Технологические и эксплуатационные свойства
Физические свойства
К физическим свойствам металлов и сплавов относятся:
– плотность - количество вещества, содержащегося в единице объема, г/см3;
– температура плавления - температура, при которой металл полностью переходит из твердого состояния в жидкое,°С;
– теплопроводность - это способность тел передавать с той или иной скоростью тепло при нагревании и охлаждении. Единицей измерения теплопроводности служит количество тепла (калл), распространяющегося по единице длины металла через единицу площади его поперечного сечения в единицу времени (кал/Дж);
– тепловое расширение - металлы расширяются при нагревании и сжимаются при охлаждении. Изменение линейного размера при нагреве называют линейным расширением; изменение объема тела - объемным расширением;
– удельная теплоемкость - это количество тепла, которое необходимо для повышения температуры 1 г вещества на 1°С;
– электропроводность - способность металлов проводить электрический ток. Под удельным электрическим сопротивлением р понимают сопротивление проводника длиной 1 м и площадью поперечного сечения 1 мм2;
– способность намагничиваться - это способность металла создавать собственное магнитное поле либо самостоятельно, либо под действием внешнего магнитного поля.
Химические свойства
Химические свойства - это свойства металлов и сплавов, определяющие отношение их к химическим воздействиям различных сред.
|
|
Химические воздействия среды проявляются в различных формах: металлы подвергаются атмосферной коррозии; при нагреве в закалочных печах без защитной атмосферы поверхность изделий покрывается окалиной; в кислотах металлы растворяются. Поэтому для практического использования металлов и сплавов необходимо знать их химические свойства.
Например, металлы и сплавы, стойкие против окисления при сильном нагреве (жаростойкие, окалиностойкие) применяются для изготовления различных сильно нагревающихся деталей автомобилей (выпускные коллекторы, глушители).
Механические свойства
Основными характеристиками механических свойств металлов являются: прочность, пластичность, упругость, твердость, ударная вязкость. Зная механические свойства, конструктор обоснованно выбирает соответствующий материал, обеспечивающий надежность и долговечность конструкций при их минимальной массе.
Механические свойства определяют поведение материала при деформации и разрушении от действия внешних нагрузок. Изменение формы твердого тела под действием приложенных к нему внешних сил (нагрузок) называется деформацией. По характеру действия нагрузки делятся на:
|
|
– статические, возрастающие медленно от нуля до некоторого максимального значения и далее остающиеся постоянными или меняющимися незначительно;
– динамические, возникающие в результате удара, когда действие нагрузки исчисляется долями секунды.
– повторно, переменные или циклические – нагрузка в процессе испытания многократно изменяется по величине или по величине и направлению.
Различают следующие основные виды деформации: сжатие, растяжение, кручение, сдвиг (срез), изгиб (рис. 1).
![]() |
Рисунок 1 Основные виды деформации
Сжатие - это деформация, характеризуемая уменьшением объема тела под действием сдавливающих его сил. Сжатию подвергаются строительные колонны, фундаменты машин, амортизационные подушки и др.
Растяжение - это деформация, характеризуемая увеличением длины тела, когда к обоим его концам приложены силы, равнодействующие которых направлены вдоль оси тела. Растяжению подвергаются тросы грузоподъемных машин, крепежные детали, приводные ремни и др.
Кручение - это деформация тела с одним закрепленным концом под действием пары равных, противоположно направленных сил, плоскость которых перпендикулярна к оси тела (например, валы двигателей, коробок передач и др.).
|
|
Сдвиг (срез) - когда две силы направлены друг другу навстречу и лежат не на одной прямой, но достаточно близко друг к другy, то при определенной величине сил происходит срез. На срез работают заклепки, стяжные болты и др.
Деформация, предшествующая срезу, называется сдвигом. При сдвиге соседние сечения детали смещаются одно относительно другого, оставаясь параллельными и без разрушения изделия.
Изгиб – это деформация тела под действием внешних сил, сопровождающаяся изменением кривизны деформируемого тела. Изгибу подвержены балки грузоподъемных механизмов, валы машин, рессоры и др.
Для получения сопоставимых результатов образцы и методика проведения механических испытаний регламентированы ГОСТами.
При статическом испытании на растяжение: ГОСТ 1497 получают характеристики прочности и пластичности.
Прочность металла или сплава - это его способность сопротивляться деформации и разрушению под действием внешних сил (нагрузок). В зависимости от характера действия этих сил различают прочность на растяжение, сжатие, изгиб и кручение, а также усталость металлов.
|
|
Для испытания на растяжение из металла или сплава изготовляют образцы, форма и размеры которых установлены ГОСТ. Испытание прочности труб и проволоки производится в натуральном виде, т. е. без изготовления образцов.
Испытание производится на разрывных машинах. В верхний и нижний захваты закрепляют головки образца. Верхний захват закреплен неподвижно, а нижний - с помощью специального механизма медленно опускается, растягивая образец до его разрыва. Развиваемое машиной усилие достигает 50 т.
При испытании на растяжение показатели прочности могут быть получены из диаграммы растяжения, которая автоматически вычерчивается на барабане разрывной машины. Эта диаграмма характеризует поведение материала при разных нагрузках. По горизонтальной линии диаграммы откладывается абсолютное удлинение образца в миллиметрах, а по вертикальной линии - нагрузку в килограммах.
Наибольшая нагрузка Рв, когда образец металла начинает сужаться (образуется шейка), называется нагрузкой предела прочности при растяжении, а напряжение, соответствующее наибольшей нагрузке, называется пределом прочности при растяжении - в и определяется как отношение наибольшей нагрузки Рв к первоначальной площади поперечного сечения образца F0, т. е.
где Рв - наибольшая нагрузка, при которой образец разрушатся, кг;
F0 - площадь поперечного сечения образца до разрыва, мм2.
Пластичность - это способность металла, не разрушаясь, менять форму под действием нагрузки и сохранять измененную форму после снятия нагрузки.
Пластичность металлов определяется также при испытании на растяжение. По величине удлинения образца и величине уменьшения его поперечного сечения судят о пластичности материала. Чем больше удлиняется образец, тем более пластичен металл. Пластичные металлы и сплавы хорошо подвергаются обработке давлением.
Характеристикой пластичности металлов является относительное удлинение и относительное сужение.
Относительным удлинением называется отношение величины приращения длины образца после разрыва к его первоначальной длине, выраженное в процентах:
где - длина после разрыва, мм;
- первоначальная длина и расчетной части образца, мм.
Относительное сужение - отношение уменьшения площади поперечного сечения образца после испытания к первоначальной площади его поперечного сечения, выраженное в процентах:
где F0 - площадь поперечного сечения образца до начала испытания, мм2;
F1 - площадь поперечного сечения в месте paзрыва образца после испытания, мм2.
Ударная вязкость - это способность металлов и сплавов оказывать сопротивление действию ударных нагрузок.
Для испытания материала на ударную вязкость изготовляют стандартные образцы с надрезом в виде брусков с квадратные сечением и определенных размеров. Испытания проводят и специальном устройстве (маятниковый копер). Маятник с закрепленным грузом, массой 10, 15 и 30 кг поднимают на определенную высоту и закрепляют в этом положении защелкой. После освобождения маятник падает и производит удар по образцу со стороны, противоположной надрезу.
Разрушение образцов имеет различный характер. У хрупких металлов образцы разрушаются без изменения формы, у вязких, они подвергаются значительному изгибу в месте излома.
Ударная вязкость является важной характеристикой материала деталей, которые в процессе работы того или иного механизма испытывают кратковременную ударную нагрузку (например, коленчатые валы двигателей, валы и шестерни коробок (передач, полуоси колес и др.). Вязкость - свойство, противоположное хрупкости.
Твердость - это свойство металла оказывать сопротивление проникновению в него другого, более твердого тела, не получавшего остаточных деформаций.
Твердость тесно связана с такими важными характеристика металлов и сплавов, как прочность, износоустойчивость.
Технологические и эксплуатационные свойства
Под технологическими свойствами понимают способность подвергаться различным видам обработки.
Из технологических свойств наибольшее значение имеют: обрабатываемость резанием, свариваемость, ковкость, прокаливаемость и литейные свойства.
Обрабатываемость резанием - комплексное свойство металла, характеризующее способность его подвергаться обработке резанием и определяется по скорости, усилию резания и по чистоте обработки. Испытания по скорости и усилию резания производятся путем сравнения показателей, полученных при обработке данного металла, с показателями обрабатываемости эталонной марки стали (автоматная сталь марки А12). Показатель чистоты обработанной поверхности определяется измерением высоты неровностей, образующихся на поверхности металла после снятия стружки режущим инструментом.
Свариваемость - способность металла давать доброкачественное соединение при сварке, характеризуется отсутствием трещин и других пороков в швах и прилегающих к шву зонах основного металла. Хорошей свариваемостью обладают конструкционные стали; значительно худшую имеют чугуны, медные и алюминиевые сплавы, которые требуют специальных технологических условий при сварке.
Ковкость - способность металлов и сплавов без разрушения менять свою форму при обработке давлением. Многие металлы и сплавы обладают достаточно хорошей ковкостью в нагретом состоянии, а в холодном состоянии - латунь и алюминиевые сплавы; пониженной ковкостью характеризуется бронза.
Прокаливаемость - способность стали воспринимать закалку на определенную глубину от поверхности. Она зависит от присутствия легирующих элементов в составе и размеров зерен структуры.
Литейные свойства металлов и сплавов характеризуются жидкотекучестью и усадкой.
Жидкотекучесть - способность металла или сплава в расплавленном состоянии заполнять литейную форму. Для повышения жидкотекучести к ним добавляют легирующие компоненты, например, фосфор — в медные сплавы и чугун, кремний - в алюминиевые сплавы.
Усадкой называется уменьшение объема расплавленного металла или сплава при его затвердевании. На степень усадки влияют многие факторы: химический состав расплава, скорость охлаждения и др.
Эксплуатационные свойства
Эксплуатационные свойства характеризуют способность материала работать в конкретных условиях.
1. Износостойкость – способность материала сопротивляться поверхностному разрушению под действием внешнего трения.
2. Коррозионная стойкость – способность материала сопротивляться действию агрессивных кислотных, щелочных сред.
3. Жаростойкость – это способность материала сопротивляться окислению в газовой среде при высокой температуре.
4. Жаропрочность – это способность материала сохранять свои свойства при высоких температурах.
5. Хладостойкость – способность материала сохранять пластические свойства при отрицательных температурах.
6. Антифрикционность – способность материала прирабатываться к другому материалу.
Эти свойства определяются специальными испытаниями в зависимости от условий работы изделий.
При выборе материала для создания конструкции необходимо полностью учитывать механические, технологические и эксплуатационные свойства
Технологические пробы
Технологическими пробами называются испытания металлов, выполняемые несложными способами и без тщательного измерения наблюдаемых свойств. Испытания имеют целью выявить способность металла к тем или иным деформациям, которым он подвергается при работе или переработке в изделие.
Качество металла по технологическим пробам определяется по внешнему виду после испытания. Отсутствие надрывов, трещин, расслоения или излома свидетельствует о том, что материал выдержал испытания.
Проба на загиб служит для определения способности металла (листов, прутков, профиля и т. п.) принимать заданный размерам и форме загиб без надрывов и трещин. Различают загиб на определенный угол, до параллельности загнутых сторон и до соприкосновения их.
Рисунок 2 Технологические пробы:
а — на загиб; 1 — загиб на определенный угол; 2 — загиб до параллельности сторон;
3 — загиб до соприкосновения сторон
б—на навивание проволоки; в — на сплющивание труб; г — на загиб труб; д — на бортование труб;
Проба на перегиб служит для определения способности металла выдерживать повторный загиб и разгибание; применяется при испытании качества полосового и листового материала, а также проволоки и прутков. Загиб образца производится попеременно в правую и левую сторону на 90°С с равномерной скоростью не более 60 перегибов в минуту до определенного числа перегибов, указанного в технических условиях.
Дата добавления: 2021-04-23; просмотров: 277; Мы поможем в написании вашей работы! |
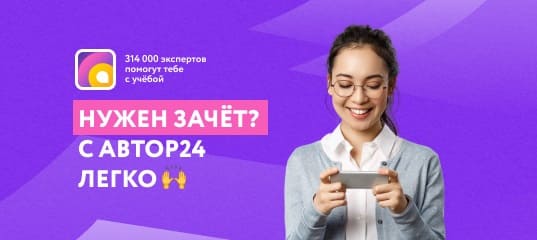
Мы поможем в написании ваших работ!