Действия машиниста при эксплуатации системы маслоснабжения цеха
Система маслоснабжения цеха. АВО масла
Назначение и состав системы маслоснабжения цеха
Система маслоснабжения компрессорного цеха должна обеспечивать: прием, хранение и контроль качества турбинного масла; очистку, подачу турбинного масла к агрегатам; аварийный слив и перелив масла из маслобаков газоперекачивающих агрегатов.
В состав системы маслоснабжения должны входить:
– склад масел вместимостью, обеспечивающей запас масла не менее трехмесячного расхода для всех потребителей;
– система маслопроводов чистого и отработанного масел цеха регенерации, а также от склада масел до потребителей;
– цех регенерации, оборудованный установками для очистки масел и насосами для подачи масла к потребителям;
– система маслопроводов, арматура и емкости, обеспечивающие аварийный слив и перелив масла из маслобаков всех ГПА.
На складе масел должны быть установлены чистые емкости под масло общей вместимостью не менее большегрузной железнодорожной цистерны - 50 м3. Дополнительные емкости выбирают исходя из необходимости обеспечения аварийного запаса.
Система маслопроводов чистого и отработанного масла должна обеспечивать следующие схемы перекачек:
– подачу чистого масла из емкости непосредственно в маслобак агрегата;
– слив отработанного масла из маслобаков в емкости для отработанного масла;
– подачу отработанного масла из маслобаков на установку очистки масла;
|
|
– слив очищенного масла в отдельную емкость;
– аварийный слив и перелив масла из маслобака агрегата при пожаре в аварийную емкость.
Кроме того в систему маслоснабжения цеха входит:
– маслобаки агрегатов;
– маслоочистительная машина типа ПСМ и стенд очистки жидкости типа (СОГ- 922, СОГ-918, СОГ-913К, СОГ-918Т);
– бак для грязного масла, который установлен рядом с маслоочистительной машиной на нулевой отметке;
– газоотделители, установленные в галерее нагнетателей;
– система подогревателей, служащая для подогрева масла непосредственно в маслобаках агрегатов и АВО масла.
Особое внимание в системе маслоснабжения цеха уделяется системе охлаждения турбинного масла, т.к. в процессе работы ГПА смазочное масло интенсивно нагревается вследствие больших тепловыделений турбины в систему смазки, так как конструктивно турбина выполнена таким образом, что многие внутренние нагревающиеся детали охлаждаются смазочным маслом. Способы охлаждения и конструкция аппаратов для охлаждения масла разные. Наиболее широкое применение получили аппараты воздушного охлаждения (АВО) масла.
Назначение и устройство АВО масла
В настоящее время на КС широко применяют систему масло-воздушного охлаждения. Эти системы более экономичны по сравнению с системами водяного охлаждения, так как исключается промежуточный контур (масло-водяной теплообменник), уменьшается суммарная длина трубопроводов. Поэтому наиболее перспективными схемами охлаждения являются двухконтурные или одноконтурные, в которых масло охлаждается в различного рода охладителях поверхностного типа.
|
|
Для охлаждения турбинного масла применяются в частности АВО Венгерского производства типа 06-10. АВО масла представляет собой группу маслоохладительных секций, из расчета одна охладительная секция на один агрегат.
Рис. 2. 9.1. Охладительная секция АВО масла
Охладительная секция состоит из следующих основных узлов (рис.2.9.1):
– одного охладительного элемента (поз. 1);
– одной обогреваемой распределительной камеры (поз.2);
– одной обогреваемой поворотной камеры (поз.3);
– двух коробок вентиляторов (поз.4);
– двух вентиляторов (поз.5);
– одного короба воздуха с жалюзи (поз.6);
– двух нижних жалюзи (поз.7);
– двух приводов нижних жалюзи (поз.8);
– одного комплекта опор (поз.9);
– одного комплекта покрывающих листов (поз.10).
· Охладительный элемент
|
|
Охладительный элемент представляет собой мелко ребристый поверхностный теплообменник типа Форго, изготовленный из алюминия холодной обработкой. Антикоррозийной защитой воздушной стороны охлаждения служит оксидный слой (химическое покрытие МБФ). Трубки охладительного элемента соединяются с камерами через маслостойкие уплотнительные кольца. Охладительный элемент имеет каркас, изготовленный из оцинкованных стальных листов и профилей.
· Коробка вентиляторов
Коробка вентиляторов является окрашенной сваренной из листов конструкцией, в которой расположен вентилятор. Коробка вентилятора имеет фланцы. К нижнему из них присоединяется охладительный элемент, а к верхнему - вентилятор.
· Вентилятор
Вентилятор осевой с вертикальной осью. Рабочее колесо вентилятора крепится шпонками к валу приводного электродвигателя. Направляющий аппарат вентилятора изготовлен из окрашенных сваренных стальных листов. В верхней и нижней частях корпуса вентилятора имеются фланцы, с помощью которых вентилятор крепится к коробке вентилятора и воздушному коробу. Рабочее колесо вентилятора изготовлено сваркой из стального листа. Приводной электродвигатель имеет вертикальную ось; вывод вала расположен на его верхней стороне. Двигатель закрытого исполнения, трехфазный, короткозамкнутый, с фланцевым соединением.
|
|
На корпусе вентилятора указано направление вращения вентилятора при его нормальной работе. При таком направлении вращения вентилятора поток воздуха направлен вверх. Вентилятор может вращаться и в обратном направлении.
· Короб воздуха с жалюзи
Окрашенный короб воздуха изготовлен сваркой из листа. Он служит для соединения выходных патрубков двух вентиляторов и на нем расположены верхние жалюзи охладителя. В нижней части короба имеются соединительные листы с болтами для присоединения короба к выходному патрубку вентиляторов. Короб воздуха имеет четыре подъемных ушка, которые приварены к четырем углам короба. Жалюзи расположены на коробе воздуха горизонтально, напротив выходных патрубков вентиляторов. Они служат для регулирования расхода охлаждающего воздуха.
· Нижние жалюзи
Нижние жалюзи расположены на опорной конструкции охладителя. Они служат для регулирования расхода воздуха, попадающего в охладитель.
· Привод нижних жалюзи
Привод, изготовленный из оцинкованной стали и смонтированный на тяге нижних жалюзи, служит для изменения положения жалюзийных листов и их закрепления в любом положении.
· Привод верхних жалюзи
Привод предназначен для ручного передвижения соединенных между собой верхних жалюзи и охладительной секции. Привод соединяется с жалюзи тягой. Тяги, которыми соединены передние и задние жалюзийные решетки охладительных секций, связаны соединительными элементами.
Технические данные АВО масла
Тип охладительной секции | 06-10 |
Фронтальная поверхность элемента | 11,5 м |
Тип охладительного элемента | ОН6/2 |
Число охладительных трубок | 240 |
Полезная длина трубок | 4750 мм |
Число вентиляторов | 2 |
Тип вентиляторов | АСО-125/720 |
Число оборотов | 720 об/мин |
Производительность вентилятора | 49000 м3/час |
Мощность приводного эл.двигателя | 5,5 кВт |
Расход охлаждаемой среды (турбинного масла) | 75,6 м3/час |
Давление охлаждаемой среды на выходе не более | 6 кг/см2 |
Работа охладительных секций
Охлаждаемое турбинное масло, проходящее по трубкам охладительного элемента охладительной секции охлаждается воздухом, просасываемым вентиляторами через охладитель.
При нормальном режиме работы охлаждающий воздух поступает в охладительную секцию снизу, через нижние жалюзи и выходит из нее через верхние жалюзи.
Эксплуатация АВО масла
При эксплуатации маслоохладители проверяются сменным машинистом при приеме смены и один раз в смену. При этом он визуально и на слух определяет нет ли утечек масла, во фланцевых соединениях входного и выходного коллекторов маслопровода, на задвижках и кране; повышенную вибрацию и посторонний шум. Причину ненормальной работы охладителей (утечки, вибрация, шум) следует немедленно отыскать и устранить с последующей записью в журнал дефектов и докладом сменному инженеру. Например: причиной непривычного шума или вибрации во время работы вентиляторов являются отложения грязи и льда (особенно зимой) на рабочем колесе. Вентилятор в таких случаях следует немедленно отключить и почистить рабочее колесо. При обнаружении повреждений, до их устранения вентилятор включать запрещается. Ниже мы рассмотрим эксплуатацию АВО масла в зависимости от времени года и температуры окружающей среды.
· Пуск АВО летом
В теплый период года охладительная секция находится заполненной маслом и безвоздушной.
Перед пуском ГПА, находящимся в резерве или выводимого из ремонта, машинист обязан проверить и выполнить следующие операции на охладительной секции:
– воздушный клапан и кран на секции должны быть закрыты;
– входная и выходная задвижки на секции открыты;
– байпасная задвижка закрыта.
После чего включается маслонасос смазки.
После начала циркуляции масла необходимо убедиться в том, что рабочее колесо вентилятора вращается свободно.
Производится пуск ГПА.
Открываются жалюзи.
Пускаются вентиляторы (по необходимости).
Машинист, в зависимости от температуры окружающей среды должен отрегулировать температуру масла в пределах 35...45 °С, открывая или прикрывая верхние и нижние жалюзи, или включая вентиляторы и контролируя температуру масла после АВО по прибору на МЩУ в машинном зале. Управление вентиляторами АВО выведено на отдельные щиты в машинном зале, где расположены кнопки включения вентиляторов и сигнальные лампы. Машинист в любой момент может проконтролировать, какая группа вентиляторов или отдельные вентиляторы находятся в работе, а какие выключены.
· Особенности эксплуатации АВО масла в зимнее время
Перед тем, как заполнять систему маслом, машинист должен убедиться, что температура масла в маслобаке не ниже 40 °С и при необходимости подогреть его.
После чего включается насос масла смазки и подогретым маслом, через байпасную задвижку, медленно производится заполнение АВО маслом. При заполнении системы маслом машинист обязан:
– стравить воздух через воздушный кран;
– медленно прикрывается байпасная задвижка на 1/2 часть, тем самым увеличивается проход масла через секции маслоохладителя;
– производится пуск ГПА;
– по мере роста температуры масла закрывается байпасная задвижка и открываются жалюзи и равномерным отключением и включением вентиляторов по секциям устанавливается необходимая температура.
Действия машиниста при эксплуатации системы маслоснабжения цеха
При эксплуатации и обслуживании системы маслоснабжения цеха ее работа подразделяется как бы на несколько операций, а именно:
– Закачка чистого масла со склада ГСМ в маслобаки агрегатов;
– Откачка грязного масла из цеха;
– Очистка масла;
– Подогрев масла.
Остановимся более подробно на операциях очистки и подогрева масла.
Очистка масла
Перед заполнением пустой емкости на складе ГСМ маслом требуется обследовать ее и при необходимости очистить или промыть с составлением акта . Емкости для доставки масла на КС также должны быть тщательно очищены.
Трубопроводы маслобаков и маслосистемы перед заполнением чистым маслом должны быть тщательно очищены и промыты для предупреждения загрязнения или смешивания разных сортов масел. Для очистки турбинного масла от механических примесей и воды в маслосистеме агрегатов применяются маслоочистительные установки типа ПСМ, стенды очистки жидкости типа (СОГ- 922; СОГ- 918; СОГ- 913 К; СОГ- 918 Т и фильтр-прессы. Маслоочистительная установка (ПСМ- 3000) может работать по методу кларификации, когда грязное масло очищается от механических примесей и по методу пурификации, когда необходимо очистить масло от воды.
Вопрос о применении того или иного метода очистки решается в каждом случае отдельно, в зависимости от характеристики, старения и загрязнения масла. Как правило, масло, содержащее более 0,5% воды, очищают методом пурификации. Если же масло значительно загрязнено механическими примесями, а воды содержит меньше 0,5%, то очищать его следует методом кларификации.
Очистку турбинного масла на маслоочистительной машине проводит в основном в дневное время специально обученный персонал, основательно изучивший принцип действия маслоочитительных машин и требования «Инструкции по обслуживанию ПСМ», а также хорошо ознакомленный с общими требованиями по технике безопасности. Так как маслоочистительная машина ПСМ- 3000 является высокоскоростной, развивающей большие инерционные усилия машиной, поэтому неумелое и халатное ее обслуживание может привести к серьезным последствиям. Сменному машинисту вменяется в обязанность отключение маслоочистительной машины, если в дневную смену обслуживающий персонал не успел очистить достаточное количество масла. При этом при отключении ПСМ сменный машинист должен строго следовать пунктам «Инструкции по обслуживанию ПСМ».
В последнее время для очистки масла применяются стенды очистки жидкостей СОГ- 922; СОГ- 918; СОГ- 913 К; СОГ- 918 Т.
Стенды очистки жидкостей
Стенд очистки жидкостей предназначен для очистки жидкостей на нефтяной основе (масла, СОЖ, рабочие жидкости для гидросистем машин и оборудования), от механических и жидких примесей, плотность которых больше плотности очищаемых жидкостей.
Стенд может применяться для обеспечения чистоты при производстве, ремонте и обслуживании турбоагрегатов, автотракторной технике, летательных аппаратов, двигателей станков и другого технологического оборудования с целью повышения надежности и долговечности гидромаслянных систем и узлов, качества обрабатываемой поверхности, увеличения срока службы рабочих жидкостей и масел, улучшения экологической обстановки.
Стенд может работать в режиме накопления выделенных механических и жидких примесей на колпаке центрифуги и периодически их сбросе в грязеотстойник стенда при остановке центрифуги и в режиме накопления механических загрязнений на колпаке с одновременном выводом жидких примесей (например воды) из центрифуги с расходом до 3 л/мин в процессе очистки. Режим работы выбирается в зависимости от степени обводнения очищаемых масел, времени непрерывной работы стенда, объема очищаемой жидкости .
Стенд не предназначен для очистки легковоспламеняющихся, токсичных и агрессивных к алюминиевым сплавам, некоррозийностойким сталям и маслостойкой резине жидкостей.
· Условия эксплуатации
Температура окружающего воздуха, °С | от 1 до 40 |
Температура очищаемых жидкостей, °С | до 70 |
Исходная концентрация механических загрязнений жидкости, класс чистоты по ГОСТ 17216-17 (процент по массе), не более | 17 (0,063) |
Напряжение сети переменного трехфазного тока частотой (5±1 Гц), В | 380 |
Давление жидкости на входе в стенд (при подключении к внешним системам), МПа (кГ/см2), не более | 0,05 (0,5) |
· Технические характеристики
Производительность в зависимости от вязкости жидкости должна быть не менее указанной
Наименование параметра | Вязкость жидкости , мм2/c | |||
5±2 | 15±5 | 50±10 | 300±50 | |
Производительность, л/мин, не менее | 60 | 40 | 20 | 5 |
Обобщенная производительность, л/мин х мм2/с | до 400 | 400-800 | 800-1200 | 1200-17500 |
Тонкость очистки жидкости плотностью не более 0,9 г/см3 и обобщенной производительностью не более 1000 л/мин х мм2/с от абразивных загрязнений плотностью не менее 2,5 г/см3, должна быть не более 5 мкм.
Степень очистки жидкостей плотностью не более 0,9 г/см3 от абразивных загрязнений плотностью не менее 2,5 г/см3 при исходной концентрации загрязнений до 17-го класса чистоты по ГОСТ 17216-71 в зависимости от вязкости жидкости и производительность, должна соответствовать указанной в таблице.
Вязкость жидкости, мм2/с | Производительность, л/мин, не более | Обобщенная производительность, л/мин х мм2/с | Степень очитки, класс точности по ГОСТ 172116-71 |
5 ± 2 | 60 | до 400 | 7 |
15 ± 5 | 40 | 400-800 | 9 |
50 ± 10 | 20 | 800-1200 | 10 |
300 ± 50 | 5 | свыше 1200 | не нормир. |
Степень обезвоживания масел - не менее 0,05% по массе при исходной обезводненности до 1,0% по массе при обобщенной производительности до 1000 (л/мин х мм2).
Рабочее давление на выходе из стенда в зависимости от производительности, МПа (кГс/см2) | 0,1-0,35 (1,0-3,5) |
Вакууметрическая высота всасывания на входе в центрифугу, МПа (кГс/см2), не более | 0,015 (0,15) |
Амплитуда колебания ротора центрифуги при работе стенда в режиме выгрузки шлама из центрифуги, мм | 0,5±0,2 |
Время выхода стенда после включения на режим по степени очистки, мин., не более | 30 |
Грязеемкость: | |
ротора центрифуги (при плотности загрязнение не менее 2,5 г/см3), кг, не менее | 2,0 |
грязеотстойника, кг, не менее | 40 |
Частота вращения ротора центрифуги, с-1 (об/мин) | 133±5 (8000±300) |
Максимальное давление, создаваемое ручным насосом, МПа (кГс/см2) | 0,20 (2,0) |
Производительность насоса за один ход поршня,см3, не менее | 250 |
Утечки через торцевое уплотнение, см3/ч не более | 20 |
Величина давления в напорной магистрали стенда, при котором происходит автоматическое выключение привода центрифуги, МПа (кГс/см2) | 0,05±0,02 (0,5±0,2) |
Энергетика: | |
напряжение сети переменного трехфазного тока частотой 50Гц, В | 380 |
потребляемая мощность, кВт, не более | 5,5 |
Наработка на отказ, час | 2000 |
Наименьшее количество жидкости, потребляемое для работы стенда составляет 35 л, из которых 25 л необходимы для заполнения гидросистемы стенда и не подлежат очистке.
· Устройство центрифуги
Основным узлом стенда является центрифуга (рис.2.9.3). На неподвижной оси 29 установлен ротор 28, который представляет собой узел, состоящий из втулки 9 с запрессованными крыльчаткой 12 и подшипниками 7 и 24, установленного на втулке 9 пакета конических тарелок 11, тарелкодержателя 5 и колпака 8.
Крыльчатка 12 заканчивается шкивом, с помощью которого ротор получает вращение от электродвигателя через поликлинувую передачу.
Колпак 8 фиксируется на крыльчатке 12 и тарелкодержателе 5 стопорным кольцом 22. Кольцо 22 имеет бородку, входящую в пазы колпака 8 и нижней крыльчатке 12 и предотвращающую их взаимное проворачивание.
В верхней части колпака 8, над его днищем, выполнена открытая полость 39, образованная цилиндрическим буртом 43 и съемной крышкой 40. Крышка 40 по периферии герметизируется резиновым кольцом 42 и фиксируется стопорным кольцом 41. В крышках на определенных радиусах попарно выполнены резьбовые отверстия 38, которые служат для подбора уровня слива выделенной из масла воды из полости 39.
В цилиндрическом бурте 43 встроены два клапана, каждый из которых состоит из корпуса 32, внутри которого размещены пружина 33, шарик и упор 34, патрубок 36 и шайба, фиксирующая резиновое уплотнительное кольцо внутри корпуса 32. Со стороны полости 39 по внутренней резьбе корпуса 32 вворачивается седло 35 с резьбой для заглушки, а на внешнюю часть корпуса герметично наворачивается крышка 46, которая фиксируется от отворачивания двумя стопорными винтами 47.
Рис. 2.9.3. Устройство центрифуги
Внутренняя полость ротора через отверстие 44 в днище колпака 8 и клапаны, в рабочем режиме центрифуги, сообщается с полостью 39. Винты 48 предохраняют корпус 32 от проворачивания, глушат сквозные отверстия 44 и могут вывертываться для прочистки отверстий 44 от грязи.
В средней части днища колпака ввернута пробка 1 с уплотнительным кольцом 3. В пробку встроен клапан 2 с пружиной 4 для выпуска из ротора воздуха при заполнении стенда очищаемой жидкостью.
Центрифуга закрывается кожухом 45, в котором выполнен карман 31 для сбора и отвода из стенда выделенной воды. Кожух сверху закрывается крышкой 37.
Для герметизации ротора установлено торцевое уплотнение. Оно включает в себя пару трения: кольцо 13 из закаленной стали (ХВГ) с резиновым кольцом, установленное в нижней части крыльчатки 12 ротора, а втулка 15 с приклеенным кольцом 14 из углеграфитного материала АГ-1500-С05 установлена на фланце оси.
К фланцу оси приварены всасывающий 19 и напорный 16 штуцеры для подвода в центрифугу и отвода очищаемой жидкости.
В нижнюю часть оси встроен клапан 20, который служит для перекрытия отверстия «а», соединяющего грязеотстойник с полостью ротора, при работе центрифуги в режиме очистки жидкости.
На верхнюю часть оси 19 навернут напорный диск 30, который служит для перекачки очищаемой жидкости и ограничивает максимальные перемещения ротора через подпятник 6.
Центрифуга крепиться к корпусу 18 стенда через мембрану.
· Принцип работы стенда
Очистка жидкости, находящихся в баках машин и технологического оборудования, многократной прокачкой через центрифугу производиться после погружения наконечников всасывающего 2 и нагнетающего 6 шлангов в очищаемую жидкость. Предварительно гидросистема стенда полностью заполняется жидкостью. Желательно погружение наконечников в разных местах бака. Минимальный объем жидкости в емкости - 10 л.
При очистке жидкость поступает из емкости - 9 через наконечник 2, всасывающий шланг 3, ручной насос 4 (при полностью опущенном поршне вниз) в центрифугу (рис. 2.9.4).
Допускается подсоединение стенда шланга 3 к баку 9 через вентиль. В этом случае наконечник 2 снимается.
Через штуцер 19 (рис. 2.9.4) фланца оси 29 жидкость поступает в ротор, где ребрами 25 крыльчатки 12 раскручивается и протекает по кольцевому зазору «б» между вставкой 28 и колпаком 8. В кольцевом зазоре происходит предварительная очистка от наиболее крупных частиц, отличающихся наибольшей плотностью.
При дальнейшем движении по зазорам 26 между коническими тарелками происходит доочистка жидкости. Частицы загрязнений оседают на внутренних поверхностях тарелок и затем сбрасываются с них и оседают на внутренних поверхности колпака 8, а очищенная жидкость с помощью напорного диска 30 через каналы 27, полую ось 29, штуцер 16, индикатор 23 (рис. 2.9.4), вентиль 24, напорный шланг 1 и наконечник 6 поступает под давлением в бак 9 или другую емкость.
Накопление осадка на внутренней поверхности колпака происходит до перекрытия кольцевой щели «б» между тарелкой 10 и колпаком (рис. 2.9.4).
Перекрытие кольцевой щели «б» слоем загрязнений приводит к снижению производительности и напорного давления до величины 0,5±0,2 кГ/см2 и автоматическому включению стенда датчиком давления 21.
При весьма мелкодисперсионном загрязнении малой плотности и полного перекрытия щели может не произойти из-за вторичного уноса частиц. В этом случае возникает дисбаланс и, как следствие, повышенный шум при работе стенда, что является сигналом о критическом накоплении осадка загрязнений в роторе (2кг) и необходимости выключения стенда.
После выключения стенда и остановки центрифуги осадок, обладающий слабой адгезией , сползает с поверхности колпака через окно «а» в грязесборник 14 (рис. 2.9.4).
Для интенсификации сброса осадка после остановки центрифуги включается на 1-2 мин вибратор, которой сообщает центрифуге возвратно-поступательное вертикальное движение с частотой 50 Гц и амплитудой 0,5 ± 0,2 мм.
Вибратор работает после создания в гидросистеме с помощью ручного насоса 4 давления 0,08 ± 0,02 и включения электродвигателя .
При очистке жидкостей от загрязнений, обладающих высокой адгезией (например смолистые загрязнения в отработанных моторных маслах) вибровыгрузка из ротора малоэффективна и осадок из-под колпака удаляется вручную после разборки центрифуги. В случае заиливания межтарельчатого зазора необходимо снять тарелки и удалить с их поверхности загрязнения с помощью ветоши смоченной в топливе.
Рис. 2.9.4. Гидравлическая схема стенда СОГ
При работе стенда в режиме очистки жидкости давление, создаваемое напорным диском 30 (рис. 2.9.4) воздействует на клапан 20, который перекрывает окно «а» и тем самым предотвращает подсос загрязненной жидкости из грязеотстойника и попадания загрязнений в ротор центрифуги. В режиме работы вибратора и выгрузки загрязнений клапан 20 открывает окно «а» не препятствуя сползанию загрязнений и слива воды из ротора в грязеотстойник.
Производительность стенда регулируются вентилем 24 (рис. 2.9.4) по показаниям индикатора обобщенной производительности 23.
Выделенная в роторе из масла вода по мере накопления на внутренней поверхности колпака 8 (рис. 2.9.4) перетекает через отверстие 44 и открытые клапаны в полость 39, откуда, переливаясь через отверстия 38 в крышке 40, попадает в карман 31 кожуха 45. Из кармана через патрубок вода поступает в накопительную емкость.
После остановки центрифуги некоторый объем воды с внутренней поверхности колпака стекает через окно «а» в грязесборник 14 (рис. 2.9.4).
Для предотвращения утечек масла из ротора необходимо создать водяной затвор, то есть перед включением стенда следует заполнить водой полость 39 и затем после включения стенда подливать воду до прекращения слива масла из кармана 31. Операцию создания водяного затвора следует проводить при каждом включении стенда.
При очистке масел с малым содержанием воды (< 0,05 % по массе ) или ограниченного объема масел с большой обводненностью рекомендуется режим работы стенда без непрерывного отвода воды. В этом случае клапаны (рис....) закрываются заглушками и водяной затвор не создается.
Требование мер безопасности
К работе на стенде допускаются лица не моложе 18 лет, ознакомленные с конструкцией, принципом действия и правилами эксплуатации стенда, прошедшие медицинский осмотр и инструктаж по технике безопасности в соответствии с требованиями ГОСТ 12.0.004-90.
Эксплуатацию стенда разрешается производить в помещениях оборудованных приточно - вытяжной вентиляцией, средствами пожаротушения и отвечающими другими специальными требованиями мер безопасности, указанным в нормативно - технической документации на очищаемые жидкости.
При работе стенда возможны следующие виды опасности в случае нарушения правил эксплуатации и обслуживания:
1) поражение вращающимися ротором центрифуги;
2) поражение электрическим током;
3) повышенный уровень вибрации и шума;
4) попадание очищаемой жидкости на поверхность тела, в глаза, органы дыхания;
5) загорание очищаемой жидкости или взрыв смеси ее паров с воздухом;
6) загрязнение воздуха рабочей зоны парами и аэрозолями очищаемой жидкости.
Уровень шума работающего стенда не должен превышать величин, указанных в инструкции по эксплуатации. При увеличении шума и вибрации во время работы стенд необходимо выключить.
Предельно-допустимая концентрация паров масел в воздухе рабочей зоны не должна превышать величины, указанной в ГОСТ 12.1.005.-88
· Запрещается:
1) эксплуатация стенда при отсутствии расхода жидкости из напорной магистрали свыше 2-х минут;
2) включать вибратор при вращающемся роторе центрифуги;
3) работа стенда при вращении ротора центрифуги против часовой стрелки;
4) неприрывная работа вибратора свыше 2 - х минут;
5) подключение стенда к внешним системам с давлением в подводящих магистралях более 0,05 МПа (0,5 кГ/см2);
6) допускать такую производительность, при которой «зашкаливает индикатор»
При работе стенда во избежании разлива жидкости и обеспечения безаварийной работы необходимо периодически проверять положение шлангов и крепление их к соответствующим штуцерам, а также работоспособность водяного затвора.
Использованный обтирочный материал собирать в металлический ящик с плотно закрывающейся крышкой.
Утилизацию отходов производить в установленном порядке в соответствии с санитарными правилами № 1746-77, раздел 4.
Контроль проб жидкостей
Отбор проб жидкости для анализа на тонкость и степень очистки из краника 22 (рис. 2.9.4), предварительно промытого в течении не менее 5 мин.
Пробы отбирать не менее чем через 30 мин. После включения стенда в специально подготовленную чистую стеклянную посуду с крышкой, исключающей попадание в пробу частиц из воздуха. Разрешается посуду перед отбором прополаскивать очищенной жидкостью под краном 22.
Анализ проб проводить способами, погрешность измерения которых не превышает 30%. Для получения достоверных результатов проводить анализ не менее 5 проб.
Для контроля чистоты жидкости в потоке рекомендуется применять прибор ПКЖ-904 А соединять шлангом с краном 22, выход - баком с очищаемой жидкостью.
Для контроля исходной концентрации загрязнений в очищаемой жидкости с помощью прибора ПКЖ-904А, следует прибор присоединить к штуцеру 7 (рис. 2.9.4) предварительно заполненного очищаемой жидкостью стенда, закрыть вентиль 24 и насосом создать и поддерживать в течении контроля давление 1-1,5 кГ/см2.
Фильтр-пресс
Для очистки масла от механических примесей в эксплуатации находятся фильтр - прессы. Принцип действия его следующий: загрязненное масло подается шестеренчатым насосом из маслобака агрегата в фильтр-пресс, который соединяется с последним специальным гибким маслопроводом. Рабочее давление, создаваемое насосом 4...6 кг/см2. Во время фильтрации масло проходит через фильтровальную ткань и бумагу, на поверхности которой задерживаются механические примеси и другие вещества. После фильтрации масло попадает на рифленую поверхность плитки и по бороздкам стекает в общий канал, а из него в емкость для чистого масла. При превышении давления в фильтр-прессе до 7...10 кг/см2 необходимо произвести перезарядку фильтр-пресса (очистить рамы и плиты, промыть ткани керосином, сменить фильтровальную бумагу). Отфильтрованное масло должно быть совершенно прозрачным и соответствовать государственным стандартам и техническим условиям. Отбор турбинного масла для анализа в химической лаборатории на работающих агрегатах проводится один раз в смену. После анализа в химлаборатории производится запись в журнал анализа масла, который хранится на ГЩУ. Кроме того, сменный машинист в течение смены следит за состоянием фильтров в маслобаках агрегатов и по мере необходимости производит очистку или замену фильтров.
Подогрев масла
Во время эксплуатации системы маслоснабжения цеха возникает необходимость в подогреве турбинного масла в холодное время года, особенно зимой. Подогрев масла осуществляется на двух этапах: при закачке масла из емкостей со склада ГСМ непосредственно в маслобаки агрегатов, где подогрев осуществляется подогревателями, установленными в цехе регенерации; и непосредственно в цехе, в маслобаках резервных агрегатов, подогрев ТЭНами в АВО масла. Рассмотрим более подробно последний, т.к. эти функции входят в обязанность сменного машиниста. Для поддержания температуры масла в маслобаках резервных агрегатов не менее 25°С применяются электроподогреватели (тэны), которые при помощи маслопроводов и задвижек подключены к общей системе маслоснабжения агрегатов.
Как говорилось уже выше, при описании эксплуатации АВО масла в зимних условиях, при остановке агрегата, при выводе его в резерв или в ремонт, производится обязательный слив масла с АВО в маслобак агрегата.
В течение смены машинист контролирует температуру масла в маслобаке резервных агрегатов по приборам на МЩУ, и при необходимости включает подогреватели масла. Система подогрева масла включает в себя: электроподогреватели (тэны), насос подачи подогретого масла и пульт управления, на котором установлены кнопки включения электроподогревателей и насоса, также приборы контроля давления и температуры подогретого масла. Перед включением системы подогрева машинист предварительно собирает схему, открывая и закрывая соответствующие задвижки на маслобаке, масло в котором необходимо подогреть, тем самым подключая маслобак к системе подогрева. После чего включает электроподогреватели и насос подкачки для создания необходимой циркуляции масла.
Во время подогрева масла машинист периодически контролирует температуру масла в системе подогрева и по достижении t до 40°С самостоятельно отключает подогрев и переводит систему на следующий агрегат, если в этом есть необходимость. Система подогрева снабжена защитами по Р масла и t масла по верхним пределам (на отключение).
Надо отметить, что такая система подогрева не слишком совершенна, с точки зрения экономии электроэнергии и постоянного контроля за t масла. В последнее время на КС пошли по более рациональному пути, использовав в качестве подогревателей систему водяного отопления цеха. В маслобаки агрегатов были помещены специальные теплообменники из трубы, которые были подключены к системе водяного отопления с горячей водой. Для лучшей циркуляции горячей воды имеется отдельный насос подкачки. Тем самым достигается относительно постоянная температура масла в маслобаках резервных агрегатов.
Дата добавления: 2021-04-23; просмотров: 286; Мы поможем в написании вашей работы! |
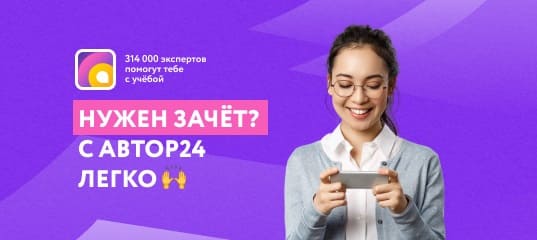
Мы поможем в написании ваших работ!