Тема 3. Система топливного, пускового и импульсного газа
Лекция: Компрессорные станции
Тема 1. Общие сведения о компрессорных станциях
Основные месторождения газа в России расположены на значительном расстоянии от крупных потребителей. Подача газа к ним осуществляется по газопроводам различного диаметра. При прохождении газа возникает трение потока о стенку трубы, что вызывает потерю давления. Поэтому транспортировать природный газ в достаточном количестве и на большие расстояния только за счет естественного пластового давления нельзя. Для этой цели необходимо строить компрессорные станции, которые устанавливаются на трассе газопровода через каждые 100–150 км.
Компрессорная станция– комплекс сооружений магистрального газопровода, предназначенный для компримирования газа.
Производственные объекты, оборудование и коммуникации КС эксплуатируют службы (участки):
– ГКС – основное и вспомогательное технологическое оборудование, системы и сооружения КЦ;
– энергоснабжения – электротехнические устройства КС, молниезащиту;
– АСУ, А и ТМ – средства автоматизации основного и вспомогательного оборудования КС, систему пожарной безопасности и контроля загазованности , систему телемеханики;
– системы тепловодоснабжения, утилизации тепла, промышленной канализации, вентиляции и кондиционирования.
Производственные задачи эксплуатационных служб, разграничение обязанностей, права и обязанности их руководителей определяют соответствующими приказами, положениями об эксплуатационных службах и должностными инструкциями.
|
|
Основными задачами эксплуатационного персонала КС являются:
– обеспечение заданного режима компримирования газа;
– обеспечение эффективной, надежной и безопасной эксплуатации оборудования и систем;
– обеспечение исправного состояния производственных зданий и сооружений, чистоты территории;
– поддержание работоспособного технического состояния оборудования и систем КС на основе системы ТО и Р, планового технического диагностирования;
– защита окружающей среды от опасных и вредных производственных факторов;
– организация работ по реконструкции и техническому перевооружению КС, модернизации основного и вспомогательного оборудования;
– обеспечение безопасных условий труда и производственной санитарии на основе соблюдения правил, норм и инструкций по охране труда и промышленной безопасности;
– оперативное выявление и устранение утечек газа.
В комплекс КС входят, как правило, следующие производственные объекты, системы и сооружения:
– один или несколько КЦ;
– диспетчерский пункт;
– АСУ ТП и система телемеханики;
|
|
– система приема, удаления и обезвреживания твердых и жидких примесей, извлеченных из транспортируемого газа;
– система электроснабжения;
– система противопожарной защиты;
– система охранной сигнализации и контроля доступа на КС;
– система производственно-хозяйственного и пожарного водоснабжения;
– система теплоснабжения;
– система маслоснабжения;
– система молниезащиты;
– система ЭХЗ;
– система связи;
– система канализации и очистные сооружения;
– система подачи газообразного азота в коммуникации КС;
–административно-хозяйственные здания и сооружения;
– склады для хранения материалов, реагентов и оборудования;
– ремонтные мастерские;
– вспомогательные объекты.
Тема 2. Технологические схемы КС
Соединенные в определенной последовательности и по определенным правилам центробежные нагнетатели, трубопроводы, пылеуловители, аппараты воздушного охлаждения, технологические краны различных диаметров образуют – технологическую схему.
Технологическая схема компрессорного цеха предназначена для:
– приема на КС технологического газа из магистрального газопровода;
– очистки технологического газа от механических примесей и капельной влаги в пылеуловителях и фильтр-сепараторах;
|
|
– распределения потоков для последующего сжатия и регулирования схемы загрузки ГПА;
– охлаждения газа после компримирования в АВО газа;
– вывода КЦ на станционное рециркуляционное «кольцо» при пуске и остановке;
– подачи газа в магистральный газопровод;
– транзитного прохода газа по магистральному газопроводу, минуя КЦ;
– для сброса газа в атмосферу из всех технологических газопроводов КЦ через свечные краны в аварийных и плановых ситуациях.
Компрессорный цех– составная часть компрессорной станции, выполняющая основные технологические функции (очистку, компримирование и охлаждение газа).
В состав КЦ входят, как правило, следующие установки, системы и сооружения:
– группа ГПА;
– узел подключения к МГ;
– входной и выходной шлейфы с границей по кранам № 7 и № 8;
– установка очистки газа с системой сбора, хранения и утилизации жидких и твердых отходов;
– установка воздушного охлаждения газа;
– установка подготовки топливного, пускового и импульсного газа;
– технологические (в том числе и межцеховые) коммуникации с ТПА;
– система электроснабжения КЦ;
– автоматизированная система управления технологическими процессами;
|
|
– вспомогательные системы и устройства (маслоснабжения, тепловодоснабжения, пожарной безопасности, контроля загазованности, отопления, вентиляции и кондиционирования воздуха, канализации, сжатого воздуха и др.).
ГПА имеют порядковый станционный номер, выполненный на видном месте.
Сосуды, работающие под давлением, и ТПА технологической обвязки КЦ, имеют станционную нумерацию в соответствии с технологической схемой и специальную табличку с содержанием в соответствии с требованиями Правилами промышленной безопасности опасных производственных объектов, на которых используется оборудование, работающее под избыточным давлением.
Система технологического газа обеспечивает:
– подачу газа к центробежным нагнетателям цеха, его транспортировку в пределах компрессорной станции и подачу в напорную линию газопровода;
– возможность загрузки и разгрузки агрегатов, их переключений для обеспечения заданного режима работы цеха, вывод нагнетателей для работы на станционное кольцо, а также стравливание газа из технологической обвязки КЦ;
– очистку транспортируемого газа и удаление конденсата;
– охлаждение газа после компримирования.
В зависимости от типа центробежных нагнетателей, различают следующие принципиальные схемы обвязок ГПА: последовательную, коллекторную, универсальную.
Схема с последовательной обвязкой, характерная для ГПА с неполнонапорными нагнетателями. Неполнонапорные нагнетатели обеспечивают отношение давления 1,23–1,25, при необходимой степени повышения давления 1,45–1,5. В этом случае ГПА соединены последовательно в группу по два агрегата.
В последовательной обвязке, схема которой представлена на рисунке 1, присутствуют технологические следующие краны:
1 – входной (входной газопровод ГПА);
2 –нагнетательный (выходной газопровод ГПА);
3, 3 бис – обводной (трубопровод между входным и выходным);
4 – наполнительный (обводной газопровод крана № 1);
5 – выпускной (выпускной газопровод (свеча) ГПА);
6– обводная линия группы или агрегата.
Рисунок 1 – Принципиальная технологическая схема КЦ
с последовательной обвязкой ГПА
Схема с коллекторной обвязкой, характерная для ГПА с полнонапорными нагнетателями. Полнонапорные нагнетатели способны обеспечить степень повышения давления до 1,45–1,5, определяемую расчетными проектными давлениями газа на входе и выходе компрессорной станции. В этом случае ГПА работают параллельно.
В коллекторной обвязке присутствуют технологические следующие краны:
1 – входной (входной газопровод ГПА);
2 – нагнетательный (выходной газопровод ГПА);
4 – наполнительный (обводной газопровод крана 1);
5 – выпускной (выпускной газопровод (свеча) ГПА);
6,6р – обводная линия группы или агрегата.
Краны № 3, № 3 бис отсутствуют, так как их функцию выполняют краны № 6,№ 6р.
Схема с коллекторной обвязкой представлена на рисунке 2.
Рисунок 2 – Принципиальная технологическая схема КЦ
с коллекторной обвязкой ГПА
Схема с универсальной обвязкой, характерная для неполнонапорных нагнетателей, но сочетает в себе и свойства коллекторной. ГПА могут работать как последовательно в группах, так и параллельно.
В последовательной обвязке присутствуют технологические следующие краны:
1 – входной (входной газопровод ГПА);
2 – нагнетательный (выходной газопровод ГПА);
3, 3 бис – обводной (трубопровод между входным и выходным);
4 – наполнительный (обводной газопровод крана 1);
5 – выпускной (выпускной газопровод (свеча) ГПА);
6 – обводная линия группы или агрегата.
Схема с универсальной обвязкой представлена на рисунке 3.
Рисунок 3 – Принципиальная технологическая схема КЦ
с универсальной обвязкой ГПА
Так для ГПА с полнонапорными нагнетателями ангарного исполнения (в индивидуальном укрытии) применяется схема с коллекторной обвязкой и индивидуальными АВО газа. При использовании такой схемы на выходном газопроводе ГПА устанавливаются два крана № 2 и № 2-1 до и после АВО газа, а так же предполагается возможность останова ГПА со стравливанием газа из АВО и без стравливания.
Схема с коллекторной обвязкой и индивидуальными АВО газа представлена на рисунке 4.
Рисунок 4 – Принципиальная технологическая схема КЦ
с коллекторной обвязкой ГПА и индивидуальными АВО газа
Узел подключения КС обеспечивает поступление газа в компрессорный цех по входному газопроводу (всасывающему шлейфу) и подачу его в газопровод после компримирования (сжатия) по выходному шлейфу.
Входные краны № 7 предназначены для подачи технологического газа в цех и его нормальное (при работающем цехе) положение – открыто.
Нагнетательные краны № 8 предназначен для подачи газа после его компримирования и охлаждения в магистральный газопровод. Перед краном
№ 8 устанавливают обратный клапан, для предотвращения обратного тока газа со стороны газопровода высокого давления при возможной неисправности крана
№ 8.
Секущий кран № 20 обеспечивает нормальную работу цеха при компримировании газа. При работе компрессорного цеха кран № 20 всегда закрыт. При открытом положении крана газ проходит транзитом, минуя компрессорный цех. При этом краны № 7 и № 8 и их обводные линии должны быть закрыты, препятствуя попаданию газа в технологические коммуникации цеха.
Свечные краны № 17и № 18 предназначены для сброса газа в атмосферу из всех технологических коммуникаций компрессорного цеха при любых аварийных остановках цеха (при этом краны № 7 и № 8 закрываются). Их также используют для продувки технологических коммуникаций при заполнении их газом.
Узел приема и запуска ВТУ предназначен для приема ВТУ, запущенного в магистральный газопровод на предыдущей КС, а также запуска ВТУ по магистральному газопроводу по ходу газа в сторону последующей КС.
Краны № 19 и № 21 носят название охранных и являются обязательными для любой КС. Размещают их в так называемой охранной зоне КС. Их назначение – отключение всей КС в аварийных ситуациях на ней.
Так как диаметры кранов № 7, № 8, № 20 более 500 мм, эти краны обводные линии малого диаметра, предназначенные для заполнения газом полости после крана, что позволяет избежать пневмоударов.
Тема 3. Система топливного, пускового и импульсного газа
Система пускового газа предназначена для подготовки и подачи газа с требуемым давлением и в необходимом количестве к пусковому устройству газотурбинных установок.
Система топливного газа обеспечивает подготовку и бесперебойную подачу газа заданного качества (давление, температура, отсутствие механических примесей и влаги) в топливную систему ГПА.
Система импульсного газа должна обеспечивать подготовку и подачу газа к узлам управления и пневмоцилиндрам для перестановки кранов технологического, топливного и пускового газа, а также к контрольно-измерительным приборам и устройствам для передачи командных импульсов.
Топливный, пусковой, импульсный газ в систему отбирается из следующих участков технологических коммуникаций компрессорного цеха:
– до и после крана № 20 узла подключения КЦ;
–из входного коллектора после пылеуловителей;
–из выходного коллектора цеха.
В зимнее время отбор газа осуществляется в основном с выходного коллектора цеха. Продувочная жидкость из сепараторов по дренажному трубопроводу направляется в емкость
После отбора газ поступает на узел подготовки топливного, пускового, импульсного газа, происходят процессы очистки, осушки подогрева, редуцирования и учета.
Узел подготовки топливного, пускового, импульсного газа включает в себя трубопроводы и коллектор импульсного газа; запорную и предохранительную арматуру, свечи для стравливания газа, устройства очистки и осушки (адсорберы, фильтры осушители, вымораживатели), узел учета, трубопроводы.
Для обеспечения бесперебойной работы в узле подготовки топливного, пускового и импульсного газа предусмотрены основная и резервные линии. Принципиальная схема узла подготовки топливного, пускового и импульсного газа показана на рисунке 1, где Ф – это фильтр-сепаратор, ПГ – подогреватель газа, РД – регулятор давления. КП – клапан предохранительный.
Рисунок 9 – Принципиальная схема узла подготовки, топливного пускового
и импульсного газа
Фильтры-сепараторы предназначены для очистки импульсного газа от механических примесей и влаги. Адсорберы предназначены для осушки импульсного газа путем поглощения воды, находящейся в газе. Поглощение осуществляется адсорбентом, находящимся в полости адсорберов. В качестве адсорбента используются силикагель или цеолит. Степень очистки и осушки импульсного газа должна исключать заедания и обмерзание работы исполнительных органов при температуре окружающего воздуха до -50°С (-60°С для районов Крайнего Севера).
Подогреватели газа предназначены для подогрева газа перед редуцированием, так как в процессе снижения давления происходит снижение температуры, и возможно обмерзание аппаратуры. Применяются подогреватели типа «газ-газ», а так же огневые подогреватели с применением промежуточного теплоносителя.
Регуляторы давления (или узел редуцирования) применяются для снижения давления газа до рабочего, так как давление в системах топливного, пускового и импульсного газа ниже давления в магистральном газопроводе.
Дата добавления: 2021-04-15; просмотров: 351; Мы поможем в написании вашей работы! |
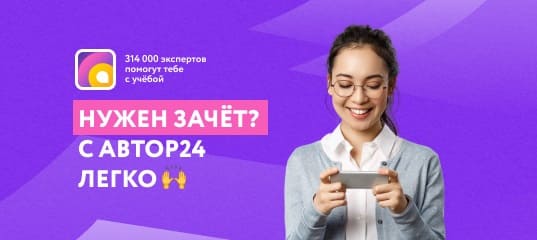
Мы поможем в написании ваших работ!