Перспективы механизации раскройного производства
Настилание материалов
Принятую из подготовительного цеха ткань предварительно нарезают на мерные полотна в соответствии с расчетом, комплектуя полотна каждого настила. При этом следят по карте расчета материала за отмеченными дефектными полотнами, которые будут обрабатывать отдельно. Иногда предварительного нарезания ткани на мерные полотна не делают, а сразу приступают к настиланию.
Так как каждый кусок ткани рассчитан для использования не в одном настиле, а в нескольких, применяют последовательное или параллельное изготовление настилов.
Последовательное изготовление настилов ткани предусматривает такую работу настильщиц, когда они сначала настилают полотна одной длины до заданной высоты настила, откладывая в сторону оставшиеся части кусков ткани, предназначенные для использования в других настилах, затем выполняют так же другие настилы один за другим.
При параллельном изготовлении настилов настильщицы настилают все настилы расчета или часть их одновременно на разных столах. Они перемещают куски ткани от стола к столу, настилая столько полотен на каждый стол, сколько указано в расчете, пока вся ткань, предназначенная для выполнения настилов, не будет израсходована. При этом способе занято столько столов, сколько настилов данного расчета настилается одновременно.
Оба способа имеют ряд недостатков. При последовательном способе приходится выбирать из многих кусков только назначенные на данный настил полотна, промеряя и откладывая остальные, что затрудняет работу. При параллельном способе настилания шесть - восемь столов долгое время оказываются занятыми неоконченными настилами, которые потом почти одновременно выходят готовыми к следующим операциям. Это создает неритмичную работу раскройного цеха.
|
|
Предварительное нарезание полотен облегчает и ускоряет последующий процесс настилания ткани, дает возможность механизировать настилание. Кроме того, такая ответственная операция, как выполнение задания, записанного в карте расчета материала, сосредоточена в одной бригаде и выполняется специально обученными рабочими. Организация предварительного нарезания полотен является предпосылкой дальнейшей механизации этой операции.
Предварительное нарезание полотен основной ткани выполняет бригада из двух человек на отдельном столе. Подкладочные и прикладные материалы сразу подают в зону их настилания.
Основную ткань настилают на столах длиной не менее 7 м и шириной 1,6 м. Высота настилочных столов 0,9 м. Поверхность стола покрыта паркетом или синтетической смолой с целью обеспечения хорошего скольжения ткани. Торцевая сторона стола может иметь ограничительную линейку для отрезания и зажимания одного конца полотна, если полотна заранее не были отрезаны (рис. 129). На другом конце стола в соответствии с длиной настила устанавливают передвижную зажимную линейку.
|
|
Подкладочные ткани настилают на более узких столах (шириной до 1,2 м).
Перед настиланием неразрезанного куска ткани у переднего конца стола закрепляют его, используя для этого кронштейны (для рулонов) или стеллажи (для куска, сложенного «книжкой»). Для лучшего перемещения полотна вдоль стола над передним концом стола устанавливают вращающиеся валики. По боковым сторонам столы имеют разметку в метрах и сантиметрах.
В раскройном цехе обычно установлено несколько настилочных столов. Количество их должно обеспечить бесперебойную работу всех технологических участков: настилания, обработки неразрезанного настила, разрезания настила на части, раскроя на ленточных машинах.
При настилании ткани полотна могут быть расположены по-разному: всгиб или вразворот. При настилании всгиб ткань складывают кромка с кромкой лицевой стороной внутрь. Такой вид расположения полотен в настиле на швейных предприятиях применяется редко, лишь для раскроя остатков.
|
|
Настилание ткани вразворот выполняют, располагая полотна «лицом вниз» или «лицом к лицу». Настилание вразворот «лицом вниз» применяют при изготовлении моделей изделий, имеющих крупные непарные или несимметричные детали, например мужских сорочек, спортивных курток и др. Для раскроя костюмов или брюк этот способ расположения полотен в настиле почти не применяют, так как детали костюмов и брюк обычно парные и симметричные. Спинки пиджаков очень редко делают неразрезными посередине. Кроме того, при настилании ткани вразворот «лицом вниз» парные детали (правые и левые) вырезают отдельно, а это может явиться причиной дефекта кроя.
Наиболее приемлемым видом расположения полотен в настиле для раскроя костюмов и брюк является настилание вразворот «лицом к лицу». В раскладке лекал используют не все детали изделия, а лишь половину всех симметричных деталей, т. е. одну полочку, часть спинки и т. д. Все детали изделия комплектуют из двух смежных полотен, лежащих лицевыми сторонами одно к другому.
При настилании необходимо соблюдать ряд технических условий. Полотна должны располагаться без натяжения, но и без морщин, а также без перекосов. При настилании выравнивают все полотна по переднему концу настила и вдоль одной из кромок. При настилании материала с рисунком в крупную клетку или поперечную полоску способом «лицом к лицу» в парном полотне совмещают рисунок, а при настилании материалов с направленным рисунком, начесом, ворсом все полотна настилают в одном направлении. Если для настилания используют материалы разных цветов или артикулов, то сначала настилают полотна одного цвета или артикула, затем другого и т. д. Длина настила зависит от принятого количества комплектов лекал в одной рамке зарисовки, от сочетания размеров и ростов (больших или маленьких), а также от того, секционный этот настил или нет.
|
|
Секционным называют настил на несколько рамок зарисовок, одинаковых или разных по длине, у которого ряд полотен или все полотна настелены без поперечных стыков.
Секцией настила называют самостоятельную зарисовку или ее часть, которую можно отрезать от настила по поперечной прямой линии. По линии секции на столе может быть установлена передвижная секционная линейка для отрезания полотна.
По высоте настилы могут быть разные. Наиболее экономичные настилы - высокие, так как они снижают затрату времени на раскрой единицы изделия, повышают производительность труда в раскройном производстве. Это объясняется тем, что на зарисовку и раскрой настила большой и малой высоты требуется одинаковое количество труда, поэтому затраты труда на единицу продукции получаются меньше при высоком настиле.
Однако высота настила полотен может быть ограничена прежде всего высотой ножа раскройных машин, применяемых для разрезания настилов. Кроме того, на высоту настила влияют вид волокна ткани, ее толщина и характер отделки. Костюмные шерстяные и полушерстяные ткани настилают высотой 36 - 40 полотен, подкладочные шелковые - 50 - 60, хлопчатобумажные - 100 - 120, карманные хлопчатобумажные - 80 - 100, бортовые и прокладочные ткани - 40 - 50 полотен.
Прежде чем настилать не разрезанную на полотна ткань, необходимо разметить на поверхности настилочного стола длину зарисовки или трафарета. По разметке конца настила устанавливают ограничительную (прижимную) линейку. Если нужно, на продольных сторонах стола устанавливают зажимы переносной секционной линейки. Для настилания неразрезанных кусков материала при многонастильном расчете применяют полуавтоматический настилочный комплекс (ПНК), позволяющий вести настилание «лицом вниз» и «лицом к лицу» (рис. 132). Благодаря цепному конвейеру 4, расположенному под крышкой настилочного стола, и размещенным на нем рулонам ткани легко осуществляется смена рулона, из которого настелили заданное расчетом количество полотен. Каретка 2, расположенная первоначально у переднего конца стола, протягивает закрепленный в ней конец полотна до концевой линейки 3, автоматически закрепляет конец и, возвращаясь, ровняет кромку полотна. По окончании возвратного движения срабатывает автоматический останов каретки. Настеленное полотно отрезают механическим ножом 1.
На готовые настилы накладывают зарисовку, выполненную на ткани или бумаге, или трафарет. Трафарет пропудривают, т. е. протирают по всем линиям и условным обозначениям пропудривателем, наполненным мелом тонкого помола или синькой. Затем трафарет снимают с настила.
Перед разрезанием готового настила на части проверяют соблюдение технических условий настилания и правильность расхода ткани. Все нечеткие контуры деталей подмеляют с помощью лекал, уточняют расположение надсечек и других обозначений.
На верхней детали каждой пачки ставят клеймо, нашивают или приклеивают талон, на котором указаны размер и рост изделия, а на основных деталях ставят номер настила. Эта операция называется клеймением настила. Она нужна для правильного комплектования пачек деталей кроя.
Раскрой материалов
Резание материалов - это физический процесс разрушения их по заданным контурным линиям. Способов раскроя материалов много. Обычно их объединяют в четыре группы: механические, электрические, теплофизические и гидравлический. Самой многочисленной группой являются механические способы. Среди них различают резание универсальным и специальным инструментом. Наибольшее распространение в швейной промышленности получили универсальные инструменты: передвижные раскройные машины, стационарные ленточные машины и ножницы. К специальным инструментам для резания относят вырубочные прессы, катки, валики и др. К электрическим способам относят резание нагретой проволокой и электрической искрой, к теплофизическим - лучом лазера и плазмой. Гидравлический способ один - гидромониторный.
Механические универсальные инструменты позволяют вырезать детали различной конфигурации, не меняя режущего инструмента и не переналаживая машину. Но они требуют ручного труда для перемещения раскройной машины или материала, выполняют последовательное вырезание по контуру и не позволяют автоматизировать процесс выкраивания деталей. Специальные инструменты, например резаки вырубочных прессов, создают возможность для автоматизации раскроя, производят параллельное вырезание всех контуров детали, но рассчитаны для раскроя только данного контура, а при изменении модели, размера, роста требуется изготовление нового комплекта резаков.
Остальные способы раскроя как наиболее перспективные описаны далее.
Раскрой материалов универсальными инструментами заключается в следующем. Сначала настилы разрезают (рассекают) на части, из которых затем вырезают отдельные детали. Рассекание настила выполняют передвижными машинами.
Перед рассеканием срезают стороны настила по границам рамки зарисовки в целях сохранения кромки. При рассекании следят за тем, чтобы лезвие ножа проходило посередине меловых линий контуров деталей и совмещалось с контуром одной из смежных деталей. Срез должен быть вертикальным.
Перед рассеканием настила для предотвращения возможного смещения и заминов нижних слоев ткани полотна скрепляют зажимами. Настил рассекают на такие части, которыми легко можно было бы оперировать при окончательном вырезании деталей на ленточных раскройных машинах.
Одновременно с рассеканием настилов на части вырезают окончательно наиболее крупные детали изделия, имеющие простые контуры. Все остальные детали выкраивают на ленточных раскройных машинах (рис. 133). Ленточные машины наиболее производительны и обеспечивают высокое качество кроя. Однако раскрой тканей одними ленточными машинами без применения передвижных раскройных машин невозможен, так как ленточные машины установлены в цехе неподвижно.
Части настилов транспортируют к ленточным раскройным машинам разными средствами, но с одним обязательным условием: слои ткани при этом не должны быть смещены.
Для обеспечения безопасной работы на ленточных машинах, а также для увеличения точности вырезания деталей применяют вспомогательные лекала, окантованные металлической лентой. Лекало накладывают на деталь, точно совмещая края лекала с меловой линией, прижимают лекало к ткани и вырезают деталь. Надсечки на вырезанных деталях выполняют также на ленточной машине, соблюдая одинаковую их глубину (0,5 см) во всех слоях пачки деталей.
При вырезании деталей кроя без наложения лекал лента должна проходить посередине меловой линии контура детали.
Контроль качества кроя
Выкроенные детали проверяют сразу после их вырезания. Эту операцию выполняют контролеры-подрезчики. Они накладывают на соответствующее лекало поочередно верхнюю, нижнюю и среднюю детали из пачки и проверяют, нет ли обужения, укорочения или перекоса в выкроенной детали. При обнаружении неточностей пачку аккуратно складывают и ликвидируют на ленточной машине отмеченные неточности.
Массовое изготовление одежды на предприятиях основано на использовании совершенно точного кроя. Дефекты раскройного производства отрицательно сказываются на технологии изделий, а также на организации работы швейных цехов, так как дефект кроя чаще всего возникает в деталях всей пачки. Точный крой позволяет в швейных цехах не производить внутри процесса дополнительных уточнений и подрезки деталей.
Наиболее значительным дефектом кроя является обужение или укорочение деталей. При обнаружении такого дефекта в швейном цехе необходимо сообщить об этом мастеру и выяснить возможность дальнейшей обработки кроя.
Обо всех обнаруженных дефектах кроя следует сообщать мастеру и технологу раскройного цеха, чтобы предупредить дальнейшие подобные нарушения технологии производства.
Пачки кроя проверенных и уточненных деталей передают для комплектования по моделям, размерам и ростам. Полученные при настилании ткани вразворот непарные детали (верхний воротник, неразрезная спинка и др.) при комплектовании кроя раскладывают на две пачки. Все детали перевязывают по пачкам, а затем мелкие связывают вместе с крупными. Крой из полотен с текстильными дефектами, раскроенных отдельно, комплектуют с подкладкой и прикладом и присоединяют к основной пачке.
Детали скомплектованного кроя нумеруют, пришивая на машине талоны, маркируя краской или надписывая карандашом или мелом. Пачки кроя деталей из основной ткани и пачки кроя подкладки и приклада комплектуют и связывают вместе. Крой поступает на хранение на склад кроя, из которого по мере необходимости его отправляют в швейные цехи.
В раскройном цехе оформляют документ на крой - маршрутный лист.
Маршрутный лист - это документ, который сопровождает пачку кроя всех деталей из основной ткани, подкладки и приклада изделий одного размеророста от раскройного цеха до склада готовой продукции и служит отчетным документом при передаче кроя, полуфабриката и готовых изделий по участкам (цехам) производства. Маршрутный лист заполняют на основании оформленной карты расчета материала. В нем записывают все данные, характеризующие пачку кроя, указывают, кому предназначается крой, а также сообщают все выходные данные готового изделия.
Перспективы механизации раскройного производства
Совершенствование раскройного производства должно проводиться с целью получения стабильно высокого качества кроя, экономного расходования материалов и снижения затрат на единицу продукции. Эти задачи в основном определяются процессами раскладки лекал, настилания материала и вырезания из настила пачек деталей кроя.
Изготовление зарисовок на ткани верхнего полотна настила - трудоемкая ручная работа, качество которой зависит от опыта и индивидуальных способностей рабочего. Для каждого настила одного и того же сочетания размероростов и одинаковой ширины материала приходится повторно выполнять ту же зарисовку.
Механизация этой операции в настоящее время решается путем изготовления нескольких копий с помощью трафаретов, светокопий, копировальной бумаги, бумаги со специальным печатающим покрытием и др. За рубежом вместо выполнения зарисовки раскладку лекал на ткани опыляют краской. Места раскладки, не закрытые лекалами, окрашиваются и служат ориентирами при выкраивании деталей. Этот способ сокращает лишь время на обводку контуров лекал, но раскладку надо каждый раз повторять.
Долгое время ручное настилание ткани применялось потому, что каждый кусок ткани рассчитывался для использования на несколько настилов при вырезании полотен с текстильными дефектами, а также потому, что куски ткани имели до трех фактических отрезов, сделанных на текстильных фабриках. Теперь, когда на ряде предприятий применяют предварительное нарезание тканей на полотна в соответствии с расчетом и настилают уже готовые полотна, возможна дальнейшая механизация этих операций. Настилочная машина (рис. 134) перемещает полотно, не протягивая его вдоль стола, а укладывая последовательно передний край полотна на переднюю часть стола и т. д. Край полотна, закрепленный на валу машины, огибает его, и последовательно при движении машины полотно укладывается вдоль стола. При этом настил выравнивается по правой кромке. Полотна получают постоянное натяжение и не растягиваются при настилании под действием собственной массы.
Предварительное разрезание ткани на полотна и их настилание увеличивают точность кроя, сокращают расход ткани на каждое полотно, повышают производительность и облегчают условия труда.
Механизация раскроя может решаться по-разному. Например, может быть использован механический способ раскроя специальным инструментом - резаками вырубочного пресса. Резаки представляют собой тонкий стальной нож, изогнутый по контуру детали. Резаки группируют и закрепляют на металлической плите режущей кромкой вверх. При работе на вырубочном прессе на резаки настилают лист бумаги, затем полотна материала (настил) и сверху - также лист бумаги. Листы бумаги способствуют более качественному вырубанию. После такой подготовки плита с резаками и настилом автоматически подается под пресс. Вырубание выполняется по мере подачи участков настила под пресс. Вырубленные пачки деталей вынимают из гнезд резаков с помощью металлических колышков. Этот способ раскроя дает точный крой, не требующий дополнительного контроля. Благодаря параллельному способу выкраивания вырубание деталей независимо от сложности контура и его периметра производится за 1,5 - 3 с.
Кроме того, можно раскраивать материал без изготовления настилов в одно или несколько полотен при раскатывании рулона ткани валичным и катковым способами. Эти способы можно применять для раскроя деталей из прокладочных и прикладных материалов благодаря тому, что детали из этих материалов (подокатники, долевики, прокладки в низ рукавов, воротники и т. п.) достаточно мелкие, постоянные по форме независимо от модели.
Разработаны теплофизические бесконтактные способы раскроя лучом лазера и микроплазменной струей. Эти способы основаны на тепловом действии, при котором происходит сгорание ткани по заданной линии. Использование для раскроя тканей луча лазера и микроплазменной струи дает возможность применить программное управление резанием, т. е. автоматизировать процесс раскроя. Этот процесс может выполняться с помощью комплексных раскройных установок, состоящих из устройств для настилания или протягивания полотна из разматываемого рулона, раскройных комплексов и устройств для сбора кроя.
Для перемещения режущего инструмента - луча лазера или плазменного резака (плазмотрона) - над плоскостью раскройного стола, на котором располагаются ткани, применяется двухкоординатное контурное устройство. Управление этим устройством обеспечивается системой числового программного преобразователя. Сбор выкроенных деталей может быть осуществлен с помощью вакуум-присоса. Вырезанные детали присасываются к ленте конвейера, который перемещает их к сборному пункту. Точное накладывание одноименных деталей друг на друга происходит благодаря строгому расчету пути перемещения ленты конвейера и срабатыванию вакуумного устройства.
Решение проблемы механизации и автоматизации процессов подготовительно-раскройного производства позволит повысить производительность труда, резко улучшить качество в результате повышения точности кроя, более экономно расходовать швейные материалы.
Дата добавления: 2021-04-15; просмотров: 58; Мы поможем в написании вашей работы! |
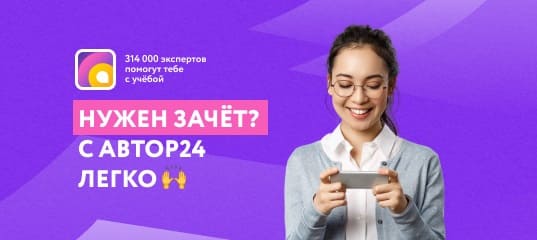
Мы поможем в написании ваших работ!