ВЫВЕРКА, ЗАКРЕПЛЕНИЕ И ИСПЫТАНИЯ СМОНТИРОВАННОГО ОБОРУДОВАНИЯ
Монтаж теплообменной аппаратуры
Теплообменные аппараты поставляют, как правило, в полностью собранном виде после испытаний на прочность и плотность. Монтаж проводят либо на открытых площадках, либо на междуэтажных перекрытиях технологических цехов. В качестве грузоподъемных механизмов преимущественно используют самоходные стреловые краны, в некоторых случаях – трубоукладчики, мачты и порталы, а также простейшие грузоподъемные механизмы (полиспасты, тали), прикрепленные к металлоконструкциям. В зависимости от условий монтажа (высота и расположение фундаментов, размеры монтажной площадки), размеров и массы аппаратов возможны различные схемы подъема одним краном на открытой площадке (рис.1). По схеме, представленной на рис. 1а, аппарат перед подъемом располагают таким образом, чтобы положение центра масс аппарата соответствовало проектному. Стрела крана имеет минимальный вылет, и грузоподъемность крана максимальна. После подъема аппарат поворачивают на растяжках в проектное положение вокруг вертикальной оси и устанавливают на опоры. Если перед подъемом удается расположить аппарат рядом с фундаментом параллельно проектному положению, то монтаж осуществляют по схеме, показанной на рис. 1б. После подъема аппарата над фундаментом кран перемещают до установки аппарата в проектное положение. Если передвижение крана между фундаментами невозможно, то применяют схему подъема, изображенную на рис.1в.
|
|
а)
б)
г) в)
При недостаточной грузоподъемности одного крана устанавливают спаренные краны (рис. 4.1г). Для контроля равномерного распределения нагрузки на краны часто применяют балансирные траверсы. В технологических цехах теплообменные аппараты монтируют в соответствии с совмещенным графиком строительно-монтажных работ в период возведения здания, фундаментов до сооружения располагаемых выше перекрытий.
Такая технология значительно ускоряет производство строительно-монтажных работ. При несоблюдении указанной последовательности работ приходится монтировать аппараты под перекрытиями (рис..2). Возможна схема монтажа с применением вертикальной мачты и полиспастов, прикрепленных к строительным конструкциям (рис. 2а). Менее трудоемок монтаж с использованием качающейся мачты (рис.2б), оснащенной двумя полиспастами – передним и задним. Подъем выполняют обоими полиспастами до необходимой отметки, затем наклоном мачты аппарат передним торцом заводят на площадку, после чего передний полиспаст и строп освобождают. Дальнейшее перемещение аппарата осуществляют полиспастом, прикрепленным к строительным конструкциям. На рис.2 в представлена схема монтажа теплообменников с помощью электротали.
|
|
Рис.4.2. Схемы монтажа теплообменных аппаратов под перекрытием а – с помощью вертикальной мачты; б – с помощью качающейся мачты; в – с помощью электротали
а)
б)
в)
При выверке теплообменных аппаратов отклонения от проектных осей и отметок, а также от горизонтальности и вертикальности составляют: главных осей аппарата в плане 10 мм; фактической высотной отметки аппарата 10 мм; оси вертикального аппарата от вертикали 3 мм на 1 м, но не более 35 мм; горизонтального аппарата от горизонтали 0,5 мм на 1 м.
Для компенсации температурных деформаций корпуса горизонтальных теплообменников одну из опор (как правило, у подвижной трубной решетки аппарата) выполняют подвижной.
Аппараты снабжаются специальными устройствами, служащими для строповки: крюк, ушки, монтажный (ложный) штуцер.
Устройства в форме крюка удобны при подъеме аппарата в несколько этапов, когда после завершения первых этапов подъема требуется провести расстроповку. В этом случае захватное устройство крана под действием собственного веса выводится из крючков, приваренных на корпусе аппарата (рис. 18.3, а).
|
|
Ушки используются при строповке аппарата за крышку, количество ушек обычно равно трем (рис. 18.3, б).
Ложный штуцер (рис. 18.3, в) не имеет входного отверстия в аппарат и служит только для монтажа и демонтажа аппарата. Обойма вращается вместе со стропом, предохраняя его от истирания. Для лучшего вращения обоймы под нее набивается солидол. Фланец предохраняет строп от соскальзывания. На аппарате обычно устанавливается два ложных штуцера.
Рис. 3. Устройства для строповки аппаратов:
а – крюк; б – ушко; в – монтажный (ложный) штуцер;
1 – стенка аппарата; 2 – обрезок трубы; 3 – обойма;
4 – фланец; 5 – косынка; 6 – ребра жесткости
При отсутствии на аппарате монтажных цапф используется установка на корпусе аппарата хомута (бандажа), снабженного устройствами для строповки.
ВЫВЕРКА, ЗАКРЕПЛЕНИЕ И ИСПЫТАНИЯ СМОНТИРОВАННОГО ОБОРУДОВАНИЯ
Машины и оборудование после сборки и монтажа тщательно проверяют по нормам точности с помощью различных контрольно-измерительных инструментов и оптико-геодезических приборов. Отклонения установленного оборудования от проектного положения не должны превышать допусков, указанных в заводской технической документации и в инструкциях на монтаж отдельных видов оборудования. При установке оборудования на фундамент проверяют соблюдение следующих требований: отклонения оборудования по высоте и в плане (привязка к осям здания или строительных конструкций); горизонтальность или вертикальность оборудования; соосность валов машин; прямолинейность и взаимное расположение плоскостей; параллельность и перпендикулярность осей и плоскостей.
|
|
Выверку горизонтального положения оборудования производят с помощью уровня (рис. 4д), гидростатического уровня (рис. 5) или нивелира по базовым поверхностям или по контрольным площадкам на собранном оборудовании. Вертикальность проверяют с помощью отвеса или теодолита; при этом используют приспособления, изображенные на рис. 5.3.
Пакеты металлических подкладок (рис. 5.3а) применяются в качестве постоянных (несущих) и временных (выверочных) опорных элементов. Пакеты набирают из стальных или чугунных подкладок толщиной 5мм и более. Проектный уровень установки оборудования достигают в процессе его предварительного закрепления с помощью регулировочных подкладок толщиной 0,55мм. В состав пакета, кроме плоских, могут входить клиновые и другие регулируемые по высоте подкладки. Число подкладок в пакете должно быть минимальным и не превышать пяти.
Для выверки оборудования инвентарными домкратами могут быть использованы винтовые (рис. 5.3б), клиновые (рис. 5.3в), гидравлические или реечные домкраты, обеспечивающие требуемую точность выверки, безопасность и удобство регулировки. Домкраты, размещенные на подготовленных фундаментах, предварительно регулируют по высоте с погрешностью не более 2мм. Затем на домкраты опускают оборудование
и выполняют окончательную выверку.
.
Рис.5.1. Инструменты для контроля точности сборки и монтажа:
а – штангенциркуль; б – штангенглубиномер; в – штангенциркуль с индикатором;
г – микрометрический нутромер (штихмасс); д – слесарный уровень
Рис.5. Гидростатический уровень:
1 – резервуар; 2 – микрометрическая головка; 3, 4 – прозрачные шланги
для воды и воздуха; 5 – микрометрический уровнемер
а) б) в) г)
Рис.5. Приспособления для выверки вертикальности аппаратов:
а – подкладки; б – винтовой домкрат; в – клиновой домкрат; г – отжимной болт; 1 – корпус приспособления; 2 – регулирующий винт; 3 – клин; 4 –винт; 5 –стопорная шайба; 6 опорная пластина; 7 – контргайка; 8 – отжимной болт; 9 – фундаментный болт
При выверке с помощью отжимных регулировочных болтов (рис. 5.г) опорные пластины 6 устанавливают на фундамент в соответствии с расположением регулировочных винтов в опорной части оборудования. Места расположения опорных пластин на фундаментах выравнивают по горизонтали с отклонением не более 10 мм на 1 м. Перед установкой оборудования на фундаменте размещают вспомогательные опоры, на которые опускают оборудование. При опускании оборудования на фундамент без вспомогательных опор регулировочные болты должны выступать ниже установочной поверхности оборудования на одинаковую величину, но не более чем на 20 мм. Положение оборудования по высоте и горизонтали следует регулировать поочередно всеми отжимными болтами, не допуская в процессе выверки отклонения оборудования от горизонтали более чем 10 мм на 1 м. После завершения выверки оборудования положения регулировочных болтов необходимо зафиксировать стопорными гайками.
Проверку соосности валов машин производят по струне или по полумуфтам. В последнем случае соосность проверяют в два приема: выполняют предварительную проверку с помощью линейки и щупа; окончательную проверку с помощью специальных скоб и индикаторов.
Прямолинейность плоскостей проверяют следующими методами:
По краске с использованием поверочной линейки с широкой рабочей поверхностью. На рабочую поверхность линейки наносят тонкий слой краски, затем накладывают линейку на поверяемую поверхность и перемещают по ней. О прямолинейности судят по оставшемуся количеству и расположению пятен краски на проверяемой поверхности.
Поверочной линейкой и щупом. Линейку накладывают на проверяемую поверхность в разных направлениях и щупом определяют зазоры между ними.
Лекальной линейкой по световой щели. Линейку укладывают острой кромкой на проверяемую поверхность и помещают сзади линейки источник света. Просвечивание мест сопряжений линейки с поверхностью свидетельствует об отклонениях от прямолинейности.
Натянутой струной диаметром 0,30,5 мм и штихмассом (рис.5.г).
Гидростатическим уровнем (рис. 5.2) с микрометрической головкой, работающим по принципу сообщающихся сосудов. Один из резервуаров 1 устанавливают на проверяемую поверхность и оставляют его неподвижным, а второй, связанный с первым гибкими прозрачными шлангами 3 и 4 для воды и воздуха, переставляют на разные места поверхности. После каждой перестановки измеряют уровень воды в обоих резервуарах и по разности замеров определяют отклонения по вертикали каждого места от базовой горизонтальной поверхности.
Проверку параллельности в большинстве случаев выполняют путем непосредственного измерения расстояний между точками, расположенными на контролируемых поверхностях, различными инструментами (рис. 5.): штангенциркулем, нутромером (штихмассом), глубиномером, штангенрейсмусом и т.д. Проверку перпендикулярности плоскостей выполняют угольниками, размеры и тип которых выбирают в зависимости от конфигурации и размеров контролируемых деталей, узлов и расположения плоскостей. Применяют также индикаторы на штативе, штангенрейсмусы, штихмассы.
Смонтированное оборудование подвергают испытаниям: гидравлическим или пневматическим на прочность и плотность (для сосудов и аппаратов); вхолостую и под нагрузкой (для машин, механизмов и аппаратов с приводом).
Аппараты, поставляемые на место монтажа в полностью собранном виде, испытывают на прочность и плотность на заводе-изготовителе. Повторным испытаниям на месте монтажа такие аппараты подвергают в случаях: истечения гарантийного срока хранения; повреждения оборудования при транспортировке к месту установки; монтажа аппарата с применением сварки, пайки или вальцовки элементов, работающих под давлением. При поставке оборудования блоками или отдельными деталями его испытывают после сборки и сварки в монтажных условиях.
Температуру воды при гидравлическом испытании поддерживают не ниже 5 0С и не выше 40 0С. Перепад температур окружающей среды и воды, применяемой для гидравлического испытания, не должен превышать 5 0С.
Продолжительность испытаний пробным давлением составляет: 10 мин при толщине стенки аппарата до 50 мм; 20 мин при толщине стенки 50-100 мм; 30 мин при толщине стенки более 100 мм; 60 мин для литых и многослойных сосудов независимо от толщины стенки. По истечении указанного времени давление постепенно уменьшают до рабочего и тщательно осматривают все соединения и сварные швы (обстукивают молотком). Во время осмотра поддерживают рабочее давление. Замеченные дефекты исправляют после полного сброса давления и вывода воды из аппарата. Оборудование считают выдержавшим гидравлическое испытание, если давление в течение всего периода испытаний не уменьшается и при осмотре не обнаружено признаков разрыва, течи в сварных соединениях, а также видимых остаточных деформаций.
После испытаний аппарата на прочность и плотность его термоизолируют и футеруют. Нанесение на поверхность аппарата и трубопроводов защитных и термоизоляционных покрытий относится к специальным строительным работам и выполняется специализированными строительно-монтажными организациями. До нанесения теплоизоляции монтажная организация устанавливает крепежные изделия и приспособления на аппаратах (штыри, крючки, подвески
и др.), если эти работы не выполнены на заводах-изготовителях. В качестве изоляции чаще всего используют маты из минеральной ваты, которыми покрывают корпус аппарата снаружи; швы матов стягивают отожженной стальной проволокой диаметром 1-2 мм. Затем снаружи минеральную вату укрепляют крупноячеистой проволочной сеткой, поверхность которой штукатурят. После высыхания слой штукатурки оклеивают тканью и окрашивают алюминиевой или другой устойчивой краской.
В качестве изоляции применяют также стекловату, стеклоткань, а для защиты теплоизоляции – асбошиферные плиты и полуцилиндры, тонкие листы из алюминиевого сплава, а также оцинкованное железо.
Термоизоляционные работы проводят только при положительной температуре окружающей среды и термоизоляционных материалов (не ниже 5оС). Термоизоляционную футеровку аппаратов выполняют из огнеупорного кирпича или асбоцементной массы. Наиболее распространена термоизоляция асбоцементом благодаря его достаточной механической прочности, незначительной теплопроводности и невысокой стоимости. После нанесения термоизоляции и футеровки аппарата составляют соответствующий акт.
После завершения строительно-монтажных работ объект готовят к сдаче заказчику. Перед сдачей аппараты подвергают гидравлическим или пневматическим испытаниям, а машины, механизмы и аппараты с приводами испытывают вхолостую и под нагрузкой.
Испытания вхолостую включают: пробные пуски с остановками для проверки работы всех узлов оборудования и устранения неполадок; непрерывные испытания вхолостую.
Испытания под нагрузкой состоят из следующих операций: пробные испытания с постепенным увеличением давления и остановками для осмотра; проверка работы всех узлов и устранение неполадок; непрерывное испытание под нагрузкой; устранение дефектов, обнаруженных в процессе испытания; заключительное контрольное испытание под нагрузкой.
После контрольного испытания оборудования под нагрузкой составляют акт о готовности оборудования к комплексному опробованию. При сдаче смонтированного оборудования в комплексное опробование предъявляют следующие документы: акт готовности фундамента и акт приемки оборудования в монтаж; акты о выявленных дефектах оборудования; акты проверки правильности установки оборудования на фундамент; акты испытаний смазочной, гидравлической и пневматической систем, испытаний на прочность и плотность, испытаний вхолостую и под нагрузкой; монтажные и сборочные формуляры; комплект рабочих чертежей на монтаж оборудования с подписью ответственного представителя монтажной организации; акт о соответствии выполненных
работ этим чертежам или об изменениях, внесенных в процессе монтажа.
Дата добавления: 2021-04-15; просмотров: 81; Мы поможем в написании вашей работы! |
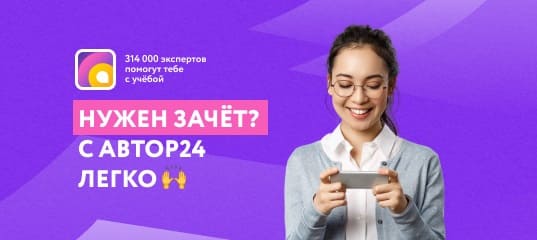
Мы поможем в написании ваших работ!