ТОЧНОСТЬ МЕХАНИЧЕСКОЙ ОБРАБОТКИ
МЕТОДИЧЕСКИЕ УКАЗАНИЯ
Учебно-методическое пособие к выполнению практических работ и самостоятельной работе для студентов, обучающихся по направлению 21.03.01 «Нефтегазовое дело» / профиль «Сооружение и ремонт объектов систем трубопроводного транспорта» всех форм обучения при изучении дисциплины «Основы технологии машиностроения»
Рег. номер:
![]() | Ижевск 2019 |
Рецензент: Н.М. Филькин, профессор, кафедра "Автомобили и металлообрабатывающее оборудование" ИжГТУ имени М.Т. Калашникова
Составитель: Бойчук А.Е., старший преподаватель
Рекомендовано Ученым советом М факультета для использования в учебном процессе в качестве учебно-методических материалов для студентов, обучающихся по направлению 21.03.01 «Нефтегазовое дело».
(протокол №__4___ от «__20__» мая 2019 г.)
Бойчук А.Е. МЕТОДИЧЕСКИЕ УКАЗАНИЯ: Методические указания к выполнению практических работ и самостоятельной работы / сост. А.Е. Бойчук – Ижевск: ИжГТУ, 2019. – 98с. |
Методические указания предназначены для студентов, обучающихся по направлению 21.03.01 «Нефтегазовое дело» / профиль «Сооружение и ремонт объектов систем трубопроводного транспорта» всех форм обучения.
В учебно-методическом пособии приводятся требования, необходимые для выполнения практических работ и самостоятельной работы по дисциплине «Основы технологии машиностроения»
|
|
СОДЕРЖАНИЕ
ГЛАВА 1. ОСНОВЫ ПРОЕКТИРОВАНИЯ
ТЕХНОЛОГИЧЕСКИХ ПРОЕКТОВ.................................................... 4
§ 1. ПРОИЗВОДСТВЕННЫЙ И
ТЕХНОЛОГИЧЕСКИЙ ПРОЦЕССЫ................................................... 4
§ 2. ТОЧНОСТЬ МЕХАНИЧЕСКОЙ ОБРАБОТКИ................. 11
§ 3. БАЗЫ И ПРИНЦИПЫ БАЗИРОВАНИЯ............................ 17
§ 4. ТЕХНОЛОГИЧНОСТЬ КОНСТРУКЦИИ.......................... 26
§ 5. ПРИПУСКИ НА МЕХАНИЧЕСКУЮ ОБРАБОТКУ.
ОПЕРАЦИОННЫЕ РАЗМЕРЫ И ИХ ДОПУСКИ............................ 32
§ 6. ПОРЯДОК ПРОЕКТИРОВАНИЯ
ТЕХНОЛОГИЧЕСКИХ ПРОЦЕССОВ............................................... 49
§ 7. КОНТРОЛЬ КАЧЕСТВА ПРОДУКЦИИ............................ 53
§ 8. МЕТОДЫ УСТАНОВКИ ЗАГОТОВОК.
УСТАНОВОЧНЫЕ ЭЛЕМЕНТЫ ПРИСПОСОБЛЕНИЯ.................. 57
ГЛАВА 2. МЕТОДЫ ОБРАБОТКИ ОСНОВНЫХ
ПОВЕРХНОСТЕЙ ЗАГОТОВОК....................................................... 62
§ 9. ОБРАБОТКА НАРУЖНЫХ ПОВЕРХНОСТЕЙ ТЕЛ
ВРАЩЕНИЯ......................................................................................... 62
ГЛАВА 3. ТЕХНОЛОГИЯ СБОРКИ МАШИН.................................. 75
§ 10. ПРОЕКТИРОВАНИЕ ТЕХНОЛОГИЧЕСКОГО
ПРОЦЕССА СБОРКИ.......................................................................... 75
ПРИЛОЖЕНИЕ А................................................................................ 83
СПИСОК ЛИТЕРАТУРЫ.................................................................... 94
|
|
ГЛАВА 1. ОСНОВЫ ПРОЕКТИРОВАНИЯ
ТЕХНОЛОГИЧЕСКИХ ПРОЦЕССОВ
§ 1. ПРОИЗВОДСТВЕННЫЙ И ТЕХНОЛОГИЧЕСКИЙ
ПРОЦЕССЫ
При работах по проектированию технологического процесса и его реализации и при оформлении технологической документации важно уметь определять структуру технологического процесса и правильно формулировать наименование и содержание его элементов. При этой работе руководствуются ГОСТ 3.1104-81 и 3.1702-79.
Важным этапом в разработке технологического процесса является так же определение типа производства. Ориентировочно тип производства устанавливают на начальной стадии проектирования [1, с.6]. Основным критерием при этом служит коэффициент закрепления операций. Это отношение числа всех технологических операций, выполняемых в течение определенного периода, например, месяца, на механическом участке (О), и к числу рабочих мест (Р) этого участка:
Кзо = О/Р. (1.1)
Типы машиностроительных производств характеризуются следующими значениями коэффициента закрепления операций: Кзо<1 - массовое производство; 1<Кзо<10 - крупносерийное производство; 10<Кзо<20 - среднесерийное производство; 20<Кзо<40 - мелкосерийное производство; Кзо не регламентируется - единичное производство.
|
|
Формулирование наименования и содержания операции
Пример 1.1. Деталь (втулку) изготовляют в условиях серийного производства и из горячекатаного проката, разрезанного на штучные заготовки. Все поверхности обрабатываются однократно. Токарная операция выполняется согласно двум операционным эскизам по установкам (рис.1.1).
Установ А Установ Б
Рис. 1.1. Операционные эскизы |
Требуется: произвести анализ операционных эскизов и других исходных данных; установить содержание операции и сформулировать ее наименование и содержание; установить последовательность обработки заготовки в данной операции; описать содержание операции по переходам.
Решение. 1. Анализируя исходные данные, устанавливаем, что в рассматриваемой операции, состоящей из двух установок, выполняется обработка девяти поверхностей заготовки, для чего потребуется выполнить последовательно девять технологических переходов.
2. Для выполнения операции будет использован токарный или токарно-винторезный станок, и наименование операции будет «Токарная» или «Токарно-винторезная» (ГОСТ 3.0217-79). По такому же ГОСТу определяем номер группы операции (14) и номер операции (63).
|
|
Для записи содержания операции при наличии операционных эскизов может быть применена сокращенная форма записи: «Подрезать три торца», «Сверлить и расточить отверстие», «Расточить одну и точить две фаски».
3. Устанавливаем рациональную последовательность выполнения
технологических переходов по установкам, руководствуясь
операционными эскизами. В первой установке необходимо подрезать торец 4, точить поверхность 2 с образованием торца 1, точить фаску 3, сверлить отверстие 6 и расточить фаску 5. Во втором установке нужно подрезать торец 9, точить поверхность 7 и фаску 8.
|
Таблица 1.1
Исходные данные
№ перехода | Вид перехода | Содержание перехода |
1 | ПВ | Установить и закрепить заготовку |
2 | ПТ | Подрезать торец 4 |
3 | ПТ | Точить поверхность 2 с образованием торца 1 (при точении поверхности 2 производится 2 рабочих хода) |
4 | ПТ | Точить фаску 3 |
5 | ПТ | Сверлить отверстие 6 |
6 | ПТ | Расточить фаску 5 |
7 | ПВ | Переустановить заготовку |
8 | ПТ | Подрезать торец 9 |
9 | ПТ | Точить поверхность 7 |
10 | ПТ | Точить фаску 8 |
11 | ПВ | Контроль размеров деталей |
12 | ПВ | Снять деталь и уложить в тару |
4. Содержание операции в технологической документации записывается по переходам: технологическим (ПТ) и вспомогательным (ПВ). При формулировании содержания переходов используется сокращенная запись по ГОСТ 3.1702-79. В таблице 1.1 приведены записи рассматриваемого примера.
Задача 1.1. Для токарной операции разработан операционный эскиз и заданы исполнительные размеры с допусками и требования по шероховатости обрабатываемых поверхностей (рис 1.2). Обработка каждой поверхности однократная.
Рис. 1.2. Операционные эскизы
Требуется: задать тип станка; определить конфигурацию и размеры заготовки; установить схему базирования; пронумеровать на эскизе все обрабатываемые поверхности; сформулировать для записи в технологических документах наименование и содержание операции; записать содержание всех технологических переходов в технологической последовательности в полной и сокращенной формах.
Установление наименования и структуры операции и запись ее
содержания в технологической документации
Пример 1.2. На рис 1.3, который представляет собой фрагмент рабочего чертежа детали, выделен конструктивный элемент детали, подлежащий обработке в условиях серийного производства.
Рис. 1.3. Рабочий чертеж
Требуется: провести анализ исходных данных; выбрать метод обработки конструктивного типа производства; подобрать тип металлорежущего станка; установить наименование операции; записать содержание операции в полной форме; сформулировать запись содержания операции по технологическим переходам.
Решение. 1. Устанавливаем, что обработке подлежат шесть отверстий во фланце корпуса, равномерно, расположенные на окружности 0 280 мм.
2. Отверстия в сплошном материале изготовляют сверлением.
3. Для обработки выбираем радиально-сверлильный станок.
4. Наименование операции (в соответствии с типом используемого станка) - «Радиально-сверлильная».
5. Запись содержания операции в полной форме выглядит так: «Сверлить 6 сквозных отверстий 018H12 последовательно, выдерживая
d = (280 ± 0,2) мм и шероховатость поверхности Ra = 20 мкм, согласно чертежу.
6. Запись содержания переходов в полной форме такова:
1-й переход (вспомогательный). Установить заготовку в кондуктор и закрепить.
2, ..., 7-й переходы (технологические). Сверлить 6 отверстий 018H12, выдерживая размеры d = 280±0,2; Ra20 последовательно по кондуктору.
8- й переход (вспомогательный). Контроль размеров.
9- й переход (вспомогательный). Снять заготовку и уложить в тару.
Задача 1.2. Установить наименование и структуру операции в условиях серийного производства по обработке конструктивных элементов детали (рис. 1.4). Номера вариантов указаны на рисунке римскими цифрами.
Рис. 1.4. Операционные эскизы
|
Пример 1.3. На участке механического цеха имеется 18 рабочих мест. В течение месяца на них выполняется 154 разные технологические операции.
Требуется: установить коэффициент загрузки операций на
участке; определить тип производства: изложить его определение по ГОСТ 14.004-83.
Решение. 1. Коэффициент закрепления операций устанавливаем по формуле (1.1): Кзо= 154/18 = 8,56. В нашем случае это означает, что на участке за каждым рабочим местом закреплено в среднем по 8,56 операций.
2. Тип производства определяется согласно ГОСТ 3.1108-74 и 14.004-083. Поскольку 1<Кзо<10, тип производства - крупносерийное.
3. Серийное производство характеризуется ограниченной номенклатурой изделий, сравнительно большим объемом их выпуска; изготовление ведется периодически повторяющимися партиями.
Крупносерийное производство является одной из разновидностей серийного производства и по своим техническим, организационным и экономическим показателям близко к массовому производству.
Задача 1.3. Известно количество рабочих мест участка (Р) и количество технологических операций, выполняемых на них в течение месяца (О). Варианты приведены в табл. 1.2.
Требуется: определить тип производства.
Данные для расчета коэффициента закрепления операций
Таблица 1.2
№ варианта | I | II | III | IV | V | VI | VII | VIII | IX | X |
Количество рабочих мест (Р) | 42 | 29 | 31 | 17 | 18 | 35 | 7 | 19 | 27 | 49 |
Количество технологических операций (О) | 1300 | 209 | 520 | 816 | 17 | 339 | 22 | 8 | 820 | 833 |
ТОЧНОСТЬ МЕХАНИЧЕСКОЙ ОБРАБОТКИ
Одной из основных задач технологов и других участников производства в механических цехах является обеспечение необходимой точности изготовляемых деталей.
Реальные детали машин, изготовленные с помощью механической обработки, имеют параметры, отличающиеся от идеальных значений, т. е. имеют погрешности, размеры погрешностей не должны превышать допускаемых предельных отклонений (допусков). Для обеспечения заданной точности обработки должен быть правильно спроектирован технологический процесс с учетом экономической точности, достигаемой различными методами обработки. Нормы средней экономической точности приводятся в источниках [2,3]. Важно учитывать, что каждый следующий переход должен повышать точность на 1...4 квалитета.
В ряде случаев используют расчетные методы для определения возможной величины погрешности обработки. Так определяют погрешности токарной обработки, от действия сил резания, возникающих вследствие недостаточной жесткости технологической системы [1, с.11 и 12].
В ряде случаев производится анализ точности обработки партии деталей методами математической статистики [1, с.15].
Определение экономической точности, достигаемой при различных
методах обработки наружных поверхностей вращения
Пример 2.1. Поверхность ступени стального вала длиной 480 мм, изготовляемого из поковки, обрабатывается предварительно на токарном станке до диаметра 91,2 мм (рис. 2.1).
Рис. 2.1. Ступенчатый вал |
Определить: экономическую точность обработки размера 91,2; квалитет точности обрабатываемой поверхности и ее шероховатость.
Решение. Для определения экономической точности пользуются таблицами «Экономическая точность механической обработки», которые приводятся в различных справочниках [3].
В нашем случае после чернового точения точность обработанной поверхности должна быть в пределах 12...14-го квалитета (принимаем 13-й квалитет). С учетом, что при l/d = 5,3 погрешности обработки возрастают в 1,5... 1,6 раза, это соответствует снижению точности на один квалитет. Окончательно принимаем точность по 14-му квалитету.
Так как при черновом точении размер заготовки - промежуточный, то размер этот устанавливается для наружной поверхности с полем допуска основной детали 091,2h14, или 091,2-037. Шероховатость поверхности Ra = 40...20 мкм (в практике заводов при хорошо выполненных заготовках и нормальных производственных условиях достигается более высокая точность обработки).
Задача 2.1. Одна из ступеней вала подвергается механической обработке одним из указанных способом. Номера вариантов приведены в табл. 2.1.
Требуется: установить экономическую точность обработки;
выполнить операционный эскиз и указать на нем размер, квалитет точности, размер допуска и шероховатость. Принять, что поверхность рассматриваемой ступени вала имеет поле допуска основной детали (h).
Исходные данные
Таблица 2.1
№ варианта | Метод обработки и ее характер | Длина вала, мм | Диаметр ступени, мм |
I | Притирка | 106 | 20 |
II | Обтачивание получистовое | 200 | 45 |
III | Шлифование тонкое | 500 | 55 |
IV | Обтачивание однократное | 450 | 120 |
V | Суперфиниширование | 700 | 100 |
VI | Шлифование предварительное | 250 | 70 |
VII | Обтачивание тонкое | 375 | 65 |
VIII | Обтачивание окончательное | 275 | 50 |
IX | Выглаживание алмазное | 60 | 170 |
X | Шлифование окончательное | 120 | 38 |
Определение точности формы поверхностей детали при обработке
Рис. 2.2. Эскиз вала
Пример 2.2. На наружной поверхности вала (рис. 2.2) задан допуск формы, обозначенный условным знаком по СТСЭВ 368-76. Окончательную обработку этой поверхности предполагается выполнить шлифованием на круглошлифовальном станке модели ЗМ151.
Требуется: установить наименование и содержание условного обозначения указанного отклонения; установить возможность выдержать требование точности формы этой поверхности при предполагаемой обработке.
Решение. 1. По представленному эскизу точность формы
цилиндрической поверхности выражается допуском круглости и составляет 10 мкм. Согласно ГОСТ 24643-81, этот допуск соответствует 6-й степени точности формы. Под термином «Допуск крутости» понимают наибольшее допустимое значение отклонения от круглости. Частными видами отклонения от круглости являются овальность, огранка и др.
2. На круглошлифовальном станке модели ЗМ151 можно производить обработку заготовок с наибольшим диаметром до 200 мм и длиной до 700 мм. Следовательно, он пригоден для обработки данной заготовки. Отклонение от круглости при обработке на этом станке составляет 2,5 мкм [4].
На основании изложенного, делаем заключение о возможности выполнить обработку с заданной точностью.
Задача 2.2. На рис. 2.3 и в табл. 2.2 указаны варианты поверхностей с допускаемыми отклонениями формы.
Требуется: установить наименование и содержание обозначения указанных отклонений; установить возможность выполнить обработку на указанном станке, соблюдая заданную точность. Недостающими размерами задаться.
Рис. 2.3. Операционные эскизы
Исходные данные
Таблица 2.2
№ варианта | Форма поверхности | Тип станка |
I | Отверстие | Внутришлифовальный |
II | Плоскость | Плоскошлифовальный |
III | Плоскость | Плоскошлифовальный |
IV | Грань | Круглошлифовальный |
V, VI | Отверстие | Хонинговальный |
VII | Цилиндр | Токарно-винторезный |
VIII | Плоскость | Продольно-строгальный |
IX | Цилиндр | Токарный многорезцовый |
X | Цилиндр | Круглошлифовальный |
Определение точности взаимного расположения поверхностей
детали при обработке
Пример 2.3. На эскизе (рис. 2.4) обозначено техническое требование к точности взаимного расположения поверхностей детали.
Предполагается окончательную обработку верхней плоскости выполнить чистовым фрезерованием на вертикально-фрезерном станке согласно операционному эскизу, изображенному на рис. 2.5.
Рис. 2.4. Конструктивные требования Рис. 2.5. Операционный эскиз
Требуется: изложить наименование и содержание технического требования; установить по технологическим справочникам точность взаимного расположения поверхностей детали в зависимости от типа оборудования; сделать заключение о возможности выполнить указанное требование.
Решение. 1. Условным знаком на рабочем чертеже показан допуск
параллельности верхней плоскости относительно нижней плоскости, обозначенной буквой А. Под допуском параллельности понимают наибольшее допускаемое значение отклонения от параллельности. В нашем случае допуск равен 0,2 мм на площади 150 х 150 мм.
2. В таблицах технологических справочников, например [3, Т.1], находим предельные отклонения нашего случая: они равны 40...100 мкм и 25...60 мкм на длине - 300 мм, а значит, на длине 150 мм они будут равны 12,5...30 мкм. Из всех этих данных принимаем для гарантии наибольшее значение - 100 мкм, т.е. - 0,1 мм.
3. Делаем заключение - требуемая точность взаимного расположения обработанной плоскости относительно базовой плоскости А будет обеспечена.
Задача 2.3. На рис. 2.6 показаны варианты обработки поверхностей.
Требуется: расшифровать обозначение содержания допуска;
разработать технологические мероприятия, обеспечивающие выполнение этого требования.
Рис. 2.6. Варианты обработки поверхностей
§ 3. БАЗЫ И ПРИНЦИПЫ БАЗИРОВАНИЯ
Чтобы осуществить обработку заготовки на станке, ее необходимо закрепить на нем, предварительно выбрав базы. Под базированием понимают придание заготовке требуемого положения относительно станка и инструмента. От правильности базирования зависит точность обработки. При разработке схемы базирования решают вопросы выбора и размещения опорных точек. В производственных условиях всегда имеют место погрешности обработки εуст, зависящие от условий установки, т.е. от базирования εбаз, закрепления εзакр заготовки, и от неточности приспособления εпр. Погрешность установки выражается формулой:
(3.1)
Для уменьшения этих погрешностей важно соблюдать правила базирования: правило «шести точек», правило «постоянства баз», правило «совмещения баз» и др.
Значения погрешности можно определить различными методами. Табличный метод [5] позволяет определить погрешности установки в зависимости от производственных условий.
Расчетный метод определения погрешностей базирования, закрепления и вызванных неточностью приспособления выполняется с помощью формул, приводимых в литературе [3].
![]() |
При несоблюдении правила «совмещения баз» возникает необходимость в пересчете конструкторских размеров в технологические (рис.3.1). Цель пересчета состоит в определении погрешности размера замыкающего звена и сравнении ее с допуском конструкторского размера.
Рис. 3.1. Технологическая размерная цепь
Расчет размерных цепей производится в соответствии с ГОСТ 16319-80 и 16320-80 одним из указанных в них методов («максимума- минимума», вероятностным и др.). При этих расчетах пользуются формулами определения номинального размера замыкающего звена:
h = H - T, (3.2)
где Н - размер, связывающий конструкторскую и технологическую базы; Т - размер, связывающий технологическую базу с обрабатываемой поверхностью.
Погрешность размера замыкающего звена εh =εд при решении по методу «максимума-минимума» определяется по формулам:
(3.3)
где Ti - допуск на размер каждого звена цепи; ТН - допуск на размер Н установленный чертежом; ТТ - допуск на технологический размер, значение которого зависит от метода обработки и устанавливается в соответствии с нормативом средней экономической точности обработки [3,5]; n - число составляющих звеньев.
При расчете по вероятностному методу пользуются формулами
(3.4)
где t - коэффициент риска (t = 3); λi - коэффициент относительного рассеяния (для нормального закона распределения λi = 1/9).
Когда законы распределения неизвестны, принимают t = 3 и λi=1/6, следовательно
(3.5)
В результате расчета должно быть выдержано условие
(3.6)
Выбор технологической базы с учетом технических требований к
детали
![]() | |||
![]() | |||
Пример 3.1. В технологическом процессе изготовления корпуса предусмотрена операция по расточке отверстия диаметром D (рис. 3.2). При выполнении отверстия должны быть выдержаны размер, а и технические требования, касающиеся правильности взаимного расположения отверстия относительно других поверхностей детали.
Требуется: выбрать технологическую базу для рассматриваемой операции; разработать схему базирования.
Решение. 1. Одной из конструкторских баз является плоскость А основания. Ее и следует принять за технологическую установочную базу, создав под ее базирование три опорные точки 1, 2 и 3 (рис. 3.3).
Технологической направляющей базой следует принять плоскость Б с двумя опорными точками 4 и 5. Эта база позволит обработать отверстие перпендикулярно этой плоскости. Для обеспечения симметричности расположения отверстия относительно наружного контура можно использовать в качестве технологической базы поверхность В, но конструктивно легче воспользоваться для этого поверхностью Г полуцилиндра и использовать для этой цели приспособление с подвижной призмой.
На основании изложенного применим технологическую базу из трех поверхностей: А, Б и Г (рис. 3.3).
2. Схема базирования, представляющая собой расположение опорных точек на базах заготовки, представлена на рис. 3.3.
Задача 3.1. Для станочной операции по обработке указанной поверхности детали требуется выбрать технологическую базу и составить схему базирования.
Варианты приведены на рис. 3.4 и в табл. 3.1.
Рис. 3.4. Операционные эскизы
Таблица 3.1
Наименование и содержание операций
№ варианта | Наименование операции | Содержание операции |
I | Вертикально-сверлильная | Сверлить отверстие в шаре |
II | Токарная | Сверлить отверстие в шаре |
III | Токарная | Точить поверхности окончательно |
IV, V | Кругло-шлифовальная | Шлифовать указанные поверхности окончательно |
VI, VII | Горизонтально-фрезерная | Фрезеровать паз |
VIII | Вертикально-фрезерная | Фрезеровать паз |
IX | Вертикально-сверлильная | Сверлить 2 отверстия |
X | Тонкорасточная | Расточить 2 отверстия |
Определение технологической базы и составление схемы
базирования заготовки
Пример 3.2. Требуется: рассмотреть установочные элементы имеющегося приспособления (рис. 3.5) и установить поверхности заготовки, составляющие технологическую базу при закреплении заготовки в приспособлении; разработать схему базирования заготовки и сделать вывод о соблюдении правила шести точек
Решение. 1. В представленном на рисунке приспособлении выявляем его установочные элементы: плоскость корпуса 2, установочный цилиндрический палец и установочный срезанный палец 3. Технологической базой заготовки являются следующие поверхности: нижняя плоскость заготовки А и два отверстия расположенных по диагонали.
2. В соответствии с выявленными технологическими базами и использованными установочными элементами разрабатываем схему базирования (рис. 3.6): для базирования плоскости (установочной базы) образовано три опорные точки (1, 2, 3); для базирования по первому отверстию (с помощью цилиндрического пальца) образовано еще две опорные точки (4, 5), а для базирования по второму отверстию используется срезанный палец (6) образующий 6-ю точку базирования.
3. Как видно из рисунка 3.6 и приведенных рассуждений, правило базирования по шести точкам соблюдено, заготовка лишена шести степеней свободы.
Рис. 3.5. Базирование заготовки
Рис . 3.6. Схема базирования
Задача 3.2. На рис. 3.7 изображено приспособление для обработки на станке. Нужно, пользуясь рисунком, выявить технологическую базу, принятую для базирования заготовки, и представить схему базирования заготовки; сделать вывод о правильности выбора опорных точек по количеству и размещению их. Номер варианта указан на рисунке римской цифрой.
Рис. 3.7. Приспособления
Расчет линейной технологической размерной цепи
Пример 3.3. На настроенном горизонтально-фрезерном станке, работающем по наладке, окончательно обрабатывается указанная плоскость. При этом должен быть выдержан координирующий размер h = (70 ±0,05) мм (рис. 3.8). Допуск размера h = 0,1 мм.
Требуется: установить, будет ли выдержана при обработке заданная точность размера.
Рис. 3.8. Технологическая размерная цепь |
Решение. 1. Из условия примера и по операционному эскизу видно, что за технологическую базу принята нижняя плоскость А заготовки. Конструкторской и измерительной базами для контроля размера h является верхняя плоскость Б. В связи с тем, что базы не совпадают, возникла необходимость пересчета конструкторских размеров на технологические.
При этом надо рассчитать погрешность, с которой может быть выполнен размер h, и сравнить ее с допуском Th этого размера, должно быть выдержано условие εh <Th.
2. Рассматриваемая размерная цепь линейная и состоит из трех звеньев: интересующий нас размер h = 70 мм будем считать замыкающим звеном АΣ первое составляющее звено - размер А1 = 85h8(85-004) между ранее обработанными плоскостями является звеном увеличивающим; второе составляющее звено - размер А2 является технологическим, уменьшающим, и точность его обусловливается нормами экономической точности обработки на станках (см. ГОСТ 2110-72). Для нашего случая погрешность этого размера составляет 0,06 мм.
Номинальные размеры этой цепи связаны уравнением
АΣ = Ai-A2 = 85-15 = 70 мм.
3. При расчете линейной размерной цепи (рис. 3.8) методом полной взаимозаменяемости, т.е. методом максимум - минимум, определяют предельные отклонения (погрешность обработки) исходного (замыкающего) звена по формуле (3.3):
Как следует из решения, допуск по чертежу Тh = 0,1 мм меньше, чем возможная погрешность при обработке TΣ = εh = 0,114 мм, что совершенно недопустимо. Следовательно, нужно принять меры, позволяющие добиться выполнения условия εh ≤Th
Для этого, во-первых, можно поставить вопрос перед конструктором о снижении точности размера h, т.е. о расширении допуска Th до значения 0,12, тогда ТΣ = εh = (0,054 + 0,06) ≤Th.
Во-вторых, применить в качестве завершающей (финишной) обработки тонкое фрезерование или чистовое шлифование. Экономическая точность этих процессов выше и при них ТА2=0,025 мм (ГОСТ 2110-72). Тогда ТΣ = (0,054 + 0,025) = 0,079 мм. Условие TΣ <Th выдержано.
В-третьих, составляющий размер А = 85h8 получен при обработке плоскостей А и Б до рассматриваемой операции. Если предшествующую обработку выполнить точнее на один квалитет, то допуск размера будет 85h7(-0,035). Тогда погрешность обработки TΣ = (0,035 +0,06) = 0,095 мм. Условие выдержано TΣ≤Th.
В-четвертых, при расчете размерной цепи можно пользоваться
вероятностным методом по формуле ТΣ=1,2t
Тогда ТΣ = мм и выдержано условие TΣ≤Th.
В-пятых, допуск замыкающего звена рассчитывают с использованием теории вероятностей для случая рассеивания погрешностей отклонений по закону нормального распределения [6] по
формуле (3.5). В нашем случае TΣ = мм. Условие Ty≤Th выполнено.
В-шестых, при незначительном объеме выпуска деталей, т. е. в единичном или мелкосерийном производстве, можно работать не по наладке, а, например, со снятием пробных стружек. При обработке каждой детали контролируется размер h.
Задача 3.3. На рис. 3.9 и в табл. 3.2 представлены варианты операций.
Требуется: определить возможную погрешность базирования размера в результате выполнения указанной обработки.
![]() |
Рис. 3.9. Варианты для расчета размерных цепей
Исходные данные Таблица 3.2
№ варианта | Содержание операции | Размер 1, мм |
I | Строгать плоскость 1 предварительно | l1= 150+0,2 |
II | Строгать плоскость 2 окончательно | l2= 170+0,1 |
III | Подрезать торец 1 предварительно | l1=60+0,3 |
IV | Подрезать торец 2 окончательно | l2= 30+0,1 |
V | Подрезать торец 1 предварительно | l1= 100+0,2 |
VI | Подрезать торец 2 окончательно | l2= 50+0,1 |
Продолжение таблицы 3.2
VII | Шлифовать плоскость 1 предварительно | l1=75+0,1 |
VIII | Шлифовать плоскость 2 окончательно | 12= 175+0,2 |
IX | Фрезеровать плоскость 1 предварительно | l1=70+0,4 |
X | Фрезеровать плоскость 2 окончательно | 12=30+0,2 |
§ 4. ТЕХНОЛОГИЧНОСТЬ КОНСТРУКЦИИ
Успешное решение задач, которые стоят и будут в дальнейшем стоять перед машиностроением, возможно только при создании новых и совершенствовании действующих машин с целью достижения более высоких эксплуатационных характеристик при одновременном сокращении их массы, габаритов и стоимости, повышении долговечности, простоте ухода и надежности в работе. Одновременно в самом машиностроении необходимо совершенствовать технологические процессы изготовления изделий, улучшать использование всех средств технологического оснащения, внедрять в производство прогрессивные методы организации производства.
Одним из эффективных путей решения этих задач является внедрение принципов технологичности конструкций. Под этим термином понимают такое проектирование, которое при соблюдении всех эксплуатационных качеств обеспечивает минимальные трудоемкость изготовления, материалоемкость и себестоимость, а также возможность быстрого освоения выпуска изделий в заданном объеме с использованием современных методов обработки и сборки.
Технологичность - важнейшая техническая основа,
обеспечивающая использование конструкторских и технологических резервов для выполнения задач по повышению технико-экономических показателей изготовления и качества изделий. Работа по улучшению технологичности должна производиться на всех стадиях
проектирования и освоения в производстве выпускаемых изделий.
При выполнении работ, связанных с технологичностью, следует руководствоваться группой стандартов, входящих в Единую систему технологической подготовки производства (ЕСТПП), а именно ГОСТ 14.201-83...14.204-73, а также ГОСТ 2.121-73 «Технологический контроль в конструкторской документации».
Технологичность конструкции деталей обусловливается: а)
рациональным выбором исходных заготовок и материалов; б) технологичностью формы детали; в) рациональной простановкой
размеров; г) назначением оптимальной точности размеров, формы и взаимного расположения поверхностей, параметров шероховатости и технических требований.
Технологичность детали зависит от типа производства; выбранного технологического процесса, оборудования и оснастки; организации производства, а также от условий работы детали и сборочной единицы в изделии и условий ремонта.
Признаками технологичности конструкции детали, например, подкласса валов являются наличие у ступенчатых валов небольших перепадов диаметров ступеней, расположение ступенчатых поверхностей с убыванием диаметра от середины или от одного из концов, доступность всех обрабатываемых поверхностей для механической обработки, возможность применить для изготовления детали исходную заготовку прогрессивного вида, которая по форме и размерам близка к форме и размерам готовой детали, возможность применять для обработки высокопроизводительные методы.
Улучшение технологичности исходной заготовки
Пример 4.1. Выполнено два варианта конструкции исходной заготовки, полученных литьем, для изготовления корпуса опоры (рис. 4.1, а, б).
Требуется установить, какой из вариантов имеет более технологичное конструктивное оформление исходной заготовки.
Решение. Корпус (рис. 4.1, а) имеет в нижней части трубчатую полость. Для образования ее в литейной форме придется применять консольный стержень, а это будет усложнять, и удорожать изготовление отливки. Гладкое отверстие значительной длины в верхней части усложнит механическую обработку.
Корпус (рис. 4.1, б) в нижней части имеет крестовидное сечение, обладающее высокой прочностью и жесткостью и для изготовления отливки не нужен стержень. Это значительно облегчает изготовление форм для литья. Отливка симметрична относительно вертикальной плоскости и легко будет формоваться в двух опоках. Отверстие в средней части имеет выемку и поэтому длина поверхности отверстия, подлежащая механической обработке, сократилась, а это, в свою очередь, значительно облегчает и удешевляет механическую обработку. На основании изложенных соображений можно сделать заключение, что второй вариант более технологичен.
Рис. 4.1. Варианты формы отливки
Задача 4.1. При конструировании исходной заготовки или ее элементов были предложены две конструкции (варианты приведены в табл. 4.1, на рис. 4.2).
Таблица 4.1
Исходные данные
№ варианта | Наименование детали | Вид заготовки |
I; VI | Колесо зубчатое | Поковка штампованная |
II; VII | Рычаг | То же |
III; VIII | Крышка | Отливка |
IV; IX | Горловина корпуса | Сварная |
V; X | Корпус круглый | Отливка |
![]() |
Рис. 4.2. Варианты исполнения заготовок
Требуется изложить соображения по оценке технологичности конструкции каждого из вариантов исходной заготовки и установить более технологичный.
Улучшение технологичности деталей и их элементов
Пример 4.2. С целью повысить технико-экономические показатели технологического процесса предложено два варианта выполнения у детали элементов в конструкции корпуса, изготовляемого из отливок (рис. 4.3, а, б).
Требуется оценить их технологичность.
Решение. Бобышки и платики на корпусе детали (рис. 4.3, а) располагаются на разных уровнях, и обработку каждой бобышки приходится вести по индивидуальной наладке. Недостаточная жесткость верхней части детали не позволяет применить методы высокопроизводительной обработки.
В конструкции на рис. 4.3, б все обрабатываемые поверхности расположены в одной плоскости и поэтому могут обрабатываться на одном станке, например, на вертикально-фрезерном или продольнофрезерном.
![]() |
Рис. 4.3. Варианты отливок
Добавленные на внутренней стороне детали ребра увеличивают жесткость корпуса. При обработке это будет способствовать уменьшению деформации заготовки от сил резания и закрепления и позволит вести обработку с высокими режимами резания или одновременно несколькими инструментами. При этом повысится точность и качество обработанных поверхностей.
Уровень имеющихся у детали необрабатываемых поверхностей, находится ниже обработанных поверхностей. Это позволит более производительно вести обработку «на проход».
Задача 4.2. Один и тот же элемент конструкции детали машины может быть, конструктивно решен различно. Эти решения представляют двумя эскизами (варианты на рис. 4.4).
![]() |
Требуется провести анализ сравниваемых эскизов конструкций на технологичность и обосновать выбор элемента конструкции детали.
Рис. 4.4. Варианты конструкций
Определение количественных показателей технологичности
конструкции детали
Пример 4.3. Корпус массой mд = 2 кг изготовляется из чугуна марки СЧ 20 ГОСТ 1412-79. Метод получения исходной заготовки - литье в земляную форму, по I классу точности (ГОСТ 1855-55); масса заготовки m0 = 2,62 кг.
Трудоемкость механической обработки детали Ти = 45 мин при базовой трудоемкости (аналога) = 58 мин.
Технологическая себестоимости детали Ст = 2,1 руб. при базовой технологической себестоимости аналога Сб.т = 2,45 руб.
Данные конструкторского анализа детали по поверхностям представлены в табл. 4.2.
Таблица 4.2
Исходные данные
Наименование | Количество | Количество |
поверхности | поверхностей | унифицированных элементов |
Отверстие главное | 1 | 1 |
Торец фланца | 2 | — |
Фаска | 2 | 2 |
Резьбовое отверстие | 8 | 8 |
Верх основания | 2 | — |
Отверстия основания | 4 | 4 |
Низ основания | 1 | — |
Итого... | Qэ=20 | Qу.э= 15 |
Требуется определить показатели технологичности конструкции детали.
Решение. 1. К основным показателям технологичности
конструкции относятся:
• абсолютный технико-экономический показатель - трудоемкость изготовления детали Ти = 45 мин;
• уровень технологичности конструкции по трудоемкости изготовления
Ку.т = Ти/Гб.и = 45/58 = 0,775.
Деталь по этому показателю технологична, так как трудоемкость ее сравнительно с базовым аналогом ниже на 22,5%; технологическая себестоимость детали Ст = 2,1 руб.;
• уровень технологичности конструкции по технологической себестоимости
Ку.с = Ст/Сб.т = 2,1/2,45 = 0,857.
Деталь технологична, так как себестоимость ее сравнительно с базовым аналогом снизилась на 14,3%.
2. Дополнительные показатели:
• коэффициент унификации конструктивных элементов детали Ку.э= Qу.э/Qэ= 15/20 = 0,75.
По этому показателю деталь технологична, так как Ку.э>0,6 масса детали mд = 2 кг;
• коэффициент использования материала
Ки.м = mд / m0 = 2/2,62 = 0,76.
Для исходной заготовки этого типа такой показатель свидетельствует об удовлетворительном использовании материала.
Задача 4.3. О рассматриваемой детали, ее исходной заготовке и о ее базовом аналоге или прототипе известны; основные данные, приведенные в табл. 4.3 для десяти вариантов.
Требуется определить показатели технологичности конструкции детали.
Таблица 4.3
Исходные данные
№ варианта | Количество поверхностей детали Qэ | Количество унифицированных элементов Qy.3 | Масса, кг | Трудоемкость, мин | Себестоимость, руб. | ||||
Детали шд | Исходной заготовки ш0 | ||||||||
Детали Ти | Базового аналога Тб.и | Детали Ст | Базового аналога Сб.т | ||||||
I; VI | 19 | 12 | 0,8 | 1,1 | 28 | 31 | 1,7 | 2,1 | |
II; VII | 28 | 17 | 0,3 | 0,4 | 16 | 24 | 0,9 | 1,3 | |
III;VIII | 73 | 45 | 3,1 | 3,8 | 78 | 86 | 3,4 | 4,1 | |
IV; IX | 41 | 27 | 0,2 | 0,4 | 31 | 39 | 1,2 | 1,4 | |
V; X | 55 | 40 | 4,8 | 5,5 | 68 | 89 | 4,8 | 5,3 |
§ 5. ПРИПУСКИ НА МЕХАНИЧЕСКУЮ ОБРАБОТКУ.
ОПЕРАЦИОННЫЕ РАЗМЕРЫ И ИХ ДОПУСКИ
При рассмотрении элементарной поверхности исходной заготовки и соответствующей ей поверхности готовой детали общий припуск на механическую обработку определяется сравнением их размеров: это - разность размеров соответствующей поверхности на исходной заготовке и готовой детали. При рассмотрении наружной поверхности вращения (слева на рис. 5.1) общий припуск:
(5.1)
у внутренней поверхности вращения (в центре на рис. 5.1) общий припуск:
2ПобщD = Dд-Do; (5.2)
у плоской поверхности (справа на рис. 5.1) общий припуск на сторону:
, (5.3)
где d0, D0, h0 - размеры исходной заготовки;
dд, Dд, - соответствующие размеры готовой детали;
2Побщd и 2ПобщD - общие припуски на диаметр, наружной поверхности и отверстия;
П - общий припуск на сторону (торец, плоскость).
Припуск на механическую обработку удаляется обычно последовательно за несколько переходов и поэтому для поверхностей вращения и для плоских поверхностей
2Побщd= Σ2Пi; 2ПобщD=Σ2Пi; Побщh =Σ2Пi (5.4)
![]() | |||||
![]() | ![]() | ||||
где ni - промежуточные припуски, выполняемые в течение i-ro перехода, причем на каждом следующем переходе размер промежуточного припуска меньше, чем на предыдущем, а также с каждым последующим переходом увеличивается точность и уменьшается шероховатость обрабатываемой поверхности.
Рис. 5.1. Виды припуска под механическую обработку
Важной и ответственной работой при проектировании технологических процессов механической обработки деталей является установление оптимального для данного перехода промежуточного припуска, после чего можно определить очень важные в технологии обработки детали параметры - промежуточные размеры заготовки, которые фигурируют в технологической документации, в зависимости
от которых исполнители подбирают режущие и измерительные инструменты.
Промежуточные припуски на каждый переход можно установить двумя методами:
• опытно-статистическим методом, пользуясь таблицами в
ГОСТах,
в технологических справочниках, ведомственных руководящих технологических материалах и других источниках. В этих источниках часто отсутствуют таблицы для определения операционных припусков на первый черновой переход. Операционный припуск на черновой переход определяют расчетом по формуле
П1 - Побщ -(П2 + Пз+... + Пп),
где Побщ - общий припуск на механическую обработку,
установленный при проектировании заготовки;
П1, П2;..., Пп - промежуточные припуски соответственно на 1-й, 2й, ..., n-й переходы;
• расчетно-аналитическим методом по специальным формулам, с учетом многих факторов обработки. При расчете по этому методу операционные припуски получаются меньше, чем выбранные по таблицам, что позволяет экономить металл, снизить себестоимость обработки. Этот метод применяют при проектировании технологических процессов обработки деталей с большим годовым объемом выпуска. В технологической документации и в практике обработки используют промежуточные номинальные размеры с допускаемыми отклонениями. Как видно на схеме (рис. 5.2)
расположения припусков и допусков при обработке, номинальные промежуточные размеры зависят от номинальных припусков, которые находят по формуле
(5.6)
где Ti-1 - допуск на промежуточный размер на предыдущем переходе.
![]() | ![]() | ||
Для различных поверхностей используют следующие формулы: для поверхностей вращения, кроме случая обработки в центрах:
для поверхностей вращения при обработке в центрах:
для плоских поверхностей
nHOMi - 2(RZi-i+ hi-i+ ASi_i +Si) + Ti-i; (5.9)
для двух противолежащих плоских поверхностей при одновременной их обработке:
Пн^ - 2(Rzi-i+ hi-i+ ASi-i +Si) + Ti-i, (5. i0)
где RZi-i - высота микронеровностей на поверхности после предшествующего перехода [3,5];
hi-i - толщина (глубина) дефектного слоя, полученная на предшествующем смежном переходе, например, литейная корка, обезуглероженный или наклепанный слой (это слагаемое не учитывается для чугунных деталей, начиная со второго перехода, и для деталей после термообработки [3,5]);
![]() | ![]() | ![]() | |||||
![]() | |||||||
Asi-i - суммарное значение пространственных отклонений взаимосвязанных поверхностей от правильной формы (коробление, эксцентричность и др.), оставшихся после выполнения предшествующего перехода (суммарное значение пространственных отклонений уменьшается с каждым следующим переходом: Azi - 0,06 AS0; AS2= 0,05 ASi; AS3 - 0,04 AS2. При нежестком закреплении заготовки или инструмента, например, в качающихся или плавающих державках Asi-i - 0); si - погрешность установки заготовки на станке при выполнении рассматриваемого перехода:
где Ss^, s^p, SppHOT - соответственно погрешности базирования, закрепления и приспособления (при установке в центрах si - 0, при обработке на многопозиционных операциях при смене позиции учитывают погрешность индексации s^ - 50 мкм по формуле si - 0,06
si-i + sинд);
Ti-i - допуск на промежуточный размер (при определении припуска на первый черновой переход для наружных поверхностей учитывается лишь минусовая его часть T0-, а для внутренних поверхностей - плюсовая часть допуска исходной заготовки).
Промежуточные размеры при обработке наружных поверхностей вращения (валов) устанавливаются в порядке, обратном ходу
технологического процесса обработки этой поверхности, т.е. от размера готовой детали к размеру заготовки путем последовательного прибавления к наибольшему предельному размеру готовой поверхности детали (исходному расчетному размеру) припусков Пном4; Пном3; Пном2; Пном1. Допуски этих размеров устанавливаются по системе вала с полем допуска h соответствующего квалитета.
За исходный расчетный размер берется наибольший предельный размер готовой поверхности. Округление промежуточных размеров производится в сторону увеличения промежуточного припуска до того же знака, что и допуск этого размера.
Особенности расчета промежуточных припусков и размеров для внутренних поверхностей состоят в следующем:
а) допуски промежуточных (межоперационных) размеров устанавливаются по системе отверстия с полем допуска H соответствующего квалитета;
б) номинальные размеры и номинальные припуски, на всех переходах, кроме первого, связаны зависимостью
Пном1= Пт1т +Тм, (5.12)
![]() | ![]() | ![]() | |||
а номинальный припуск для первого (чернового) перехода определяется по формуле
где Т( - плюсовая часть допуска заготовки;
в) промежуточные размеры устанавливаются в порядке, обратном ходу выполнения технологического процесса от размера готового отверстия к размеру заготовки путем вычитания из наименьшего предельного размера готового отверстия (исходный размер) припусков Пном3; Пном2; Пном1. Допуски их ставятся по системе отверстия с полем допуска Н;
г) за исходный расчетный размер принимают наименьший предельный размер готового отверстия.
Схема полей допусков наружной поверхности детали, заготовок на всех стадиях обработки и исходной заготовки и полей припусков общего и промежуточных представлены на рис. 5.2.
![]() |
Выбор промежуточных припусков при обработке вала из проката и
расчет промежуточных размеров
![]() |
Пример 5.1. Ступенчатый вал длиной Ьд = 480 мм (рис. 5.3) изготовляется в условиях мелкосерийного производства из стального круглого горячекатаного проката обычной точности диаметром d0=100 мм. Наибольшая по диаметру ступень вала 090h10(90-0,35) с шероховатостью поверхности Ra5 (Rz20) обрабатывается двукратно: предварительным и окончательным точением. Требуется: установить общий припуск на механическую обработку диаметрального размера; установить промежуточные припуски на оба перехода обработки статистическим методом; рассчитать промежуточный размер.
Решение. 1. Общий припуск на механическую обработку на диаметр определяем по формуле 5.1:
2Побща = 100-90 = 10 мм.
2. Промежуточный припуск на диаметр при чистовом точении вала [4].
2П2табл 1,2 мм.
Для мелкосерийного характера производства припуск увеличивается, для чего вводится коэффициент К = 1,3, т. е. 2П2расч = 1,2-1,3 = 1,56 мм ~ 1,6мм.
Так как указания относительно размера операционного припуска на диаметр при черновом точении в технологических справочниках отсутствуют, определяем его расчетом, используя формулу (5.4):
2П1 = 2Побща-2П2расч = 10-1,6 = 8,4 мм.
Итак, исходный расчетный размер диаметра (наибольший предельный размер) равен dHCX = 90 мм, операционный припуск на чистовое точение 2П2 = 1,6 мм. Диаметр заготовки после чернового точения равен d1 = dHra + 2П2 = 91,6; он же с допуском: d1 = 91,6h12, или d1 = 91,6-035; шероховатость поверхности Ra20.
В технологической документации выполняются операционные эскизы на оба перехода (рис. 5.4, а, б)
![]() |
5)
Задача 5.1. Для изготовления ступенчатого вала (рис. 5.5) в качестве заготовки использован стальной круглый горячекатаный прокат обычной точности диаметром d0. Наибольшая по диаметру ступень этого вала диаметром dд изготовляемая с точностью по 11-му квалитету и шероховатостью поверхности Ra10, обрабатывается
дважды предварительным и окончательным точением. Варианты задачи приведены в табл. 5.1.
| 4 _ |
Рис. 5.5. Заготовка - круг
|
Исходные данные Таблица 5.1
|
|
Требуется: установить с помощью таблиц общий и
промежуточный припуски; рассчитать промежуточный размер и выполнить операционные эскизы.
Установление статистическим методом (по таблицам)
промежуточных припусков на каждый переход и расчет
промежуточных размеров заготовки
Пример 5.2. Многоступенчатый вал (рис. 5.6) изготовляется из штампованной поковки повышенной точности (I класс). Заготовка прошла фрезерно-центровальную обработку, в результате которой были подрезаны торцы и созданы центровые отверстия.
|
| |||||
iS- | с\|' | |||||
■s~4 0\ | ||||||
4 | 08 * |
Рис. 5.6. Заготовка - поковка
|
Наружная цилиндрическая поверхность одной ступени вала имеет диаметр d д = 85p6(s5;)* шероховатостью Ra1,25. Ступень
исходной заготовки (см. пример П1.2) имеет диаметр d0 = 91,2;07 и шероховатость Rz250 (Ra60).
Принятая последовательность обработки указанной поверхности приведена в табл. 5.2.
Требуется: провести анализ исходных данных; установить
статистическим методом (по таблицам) операционные припуски на каждый переход; рассчитать промежуточные размеры для выполнения каждого технологического перехода.
Решение. 1. Общий припуск на механическую обработку на диаметр составляет 6,2 мм. Коэффициент ужесточения размера обрабатываемой поверхности составляет
Кужест.р. = To/Тд = 2000/22 = 91.
Таблица 5.2 Исходные данные
|
|
Заметим, что допускаемое отклонение диаметра исходной заготовки соответствует примерно 16-му квалитету точности (IT16), а готовой детали - 6-му квалитету точности (IT6). Таким образом, точность при обработке увеличивается примерно на десять квалитетов. Такой перепад точности можно достичь за четыре этапа обработки, так как каждый этап обработки увеличивает точность размера в среднем на 2...3 квалитета.
2. Выбор операционных припусков на диаметр выполняем по таблицам [4].
Общий припуск 2Побщ = 6,2 мм. Табличное значение операционного припуска на диаметр при шлифовании составляет 0,5 мм, распределяем его на шлифование предварительное и окончательное (примерно в отношении 3:1) и получаем 2П3 = 0,375 мм и 2П4 = 0,125 мм. Округленно принимаем 2П3 = 0,4; 2П4 = 0,1. Припуск на точение под шлифование 2П2=1,2 мм. Отсюда находим припуск на черновое точение:
2П1 = 2Побщ-2П2-2П3-2П4 = 4,5 мм.
Параметры поверхности после механической обработки для каждого перехода представлены в табл. 5.3.
По данным табл. 5.3 можно сделать следующие выводы:
а) общий припуск делится по переходам в отношении 72,5%,
19,5%, 6,5% и 1,5%, что соответствует правилам технологии
механической обработки;
б) после каждого перехода точность повышается в такой последовательности (по квалитетам): 16-13-10-8-6 и соответственно допуск размера уменьшается (происходит ужесточение допуска) в 4,3; 3,8; 2,6 и 2,1 раза;
Таблица 5.3
Исходные данные
|
|
в) после каждого перехода происходит уменьшение параметров шероховатости сначала в 3.. .4 раза, а затем в 2 раза.
3. Расчет промежуточных размеров для выполнения каждого технологического перехода ведется по методике, изложенной в начале в § 5. Его результаты сведены в табл. 5.4.
4.
![]() | ![]() | ![]() | |||
Операционные эскизы для каждого перехода представлены на рис. 5.7, а, б, в, г.
о)
г)
Рис. 5.7. Промежуточные размеры Исходные данные
Таблица 5.4
|
|
1 | Точить поверхность предварительно | dl = d2 + 2П2 di=85,56+1,2 d1=86,76 | d1 = 86,76hl3 (86,76-0,054) | Rа20 |
0 | Диаметр поверхности исходной заготовки (поковка) | d0=d1 + 2П1 d0 = 86,76 + + 4,44 = 91,2 | +1,3 d0 = 91,2-07 | Ra80 |
|
Задача 5.2. Четырехступенчатый вал изготовляется из штампованной поковки повышенной точности (I класс). У этой заготовки подрезаны и зацентрованы торцы (рис. 5.8). Наружная цилиндрическая поверхность одной ступени вала имеет диаметр da с шероховатостью Ra1,25. Ступень исходной заготовки имеет диаметр do и ее шероховатость Ra60 (Rz250).
|
Заготовку обрабатывают в такой последовательности:
1. Точить предварительно (поле допуска h11...h12, Rа 20).
2. Точить окончательно (поле допуска h11...h10, Ra5).
3. Шлифовать предварительно (поле допуска h9...h8, Ra2,5).
4. Шлифовать окончательно (поле допуска IT6, Ra1,25).
Требуется: выбрать операционные припуски; рассчитать
промежуточные размеры для выполнения каждого из четырех переходов; выполнить операционные эскизы (варианты заданий приведены в табл. 5.5).
Исходные данные
Таблица 5.5
|
|
Определение промежуточных припусков расчетно-аналитическим
методом и расчет промежуточных размеров
Пример 5.3. Ступенчатый вал (см. рис. 5.8) в условиях
крупносерийного производства изготовляется из штампованной поковки I класса точности.
Масса заготовки то = 23 кг; диаметр рассматриваемой
поверхности исходной заготовки 91,2 -0,37 шероховатость ее Rz250;
допуски: на смещение штампа Дсм = 0,9 мм; на коробление - Дкор =0,5 мм (половина допуска на биение). Остальные данные имеются в примерах П1.2 и 5.2.
Требуется для средней ступени диаметром dд = 85р6 +0037,
имеющей шероховатость Rа1,25, определить промежуточные припуски на все переходы расчетно-аналитическим методом.
Решение. 1. Сбор дополнительных исходных данных для
выполнения расчета промежуточных припусков производится по литературе [10; 21, Т. 1]; допуски на промежуточные размеры - по СТ СЭВ 144-75. Последовательность обработки, число переходов и достигаемые результаты по точности и шероховатости такие же, как в примере 5.2.
Расчет отклонений формы штамповки, подготовленной к токарной обработке (подрезаны торцы и выполнена зацентровка) производится по формуле
+ А2
Исходные данные Таблица 5.6
|
|
В нашем случае ДЦ = 0,25 д/Т 2к.ш +1,
где Т0к.ш = 2 мм - допуск на диаметр крайних ступеней штамповки, т.е. ДЦ = 0,56 мм.
Отсюда
А 0 =V (0,92 + 0,52 + 0,562) = 1,172 = 1172 мкм.
Пространственные отклонения заготовки в ходе обработки уменьшаются: As = 0,06-Д0 = 0,06-1172 = 70 мкм; Д2 = 0,05-Ai =3,5 мкм; Дз = Д4= 0. Все исходные данные сведены в табл. 5.6.
2. Расчет номинальных операционных припусков производим по формуле (5.8). Номинальный промежуточный припуск на диаметр на черновое точение равен
2Пном = 2(250 + 250 + 1172) + 700 = 4044 мкм.
Номинальные припуски на диаметр на остальные три перехода по обработке этой же поверхности составят:
2Пном2 = 2(80 + 50 + 70) + 540 = 940 мкм;
2Пном3 = 2(20 + 25 + 3,5) + 140 = 237 мкм;
2Пном1 = 2(10 + 20 + 54) = 114 мкм.
3. Расчет промежуточных номинальных размеров с допусками и
обозначениями параметров шероховатости, необходимый для
исполнения детали, ведут от расчетного размера ступени - наибольшего предельного размера готовой детали - последовательно прибавляя к нему значения номинальных припусков (2Пнош) в порядке, обратном ходу технологического процесса. Округление промежуточных размеров производится в сторону увеличения припусков до той же значащей цифры, как в допуске промежуточного размера (табл. 5.7).
Таблица 5.7
Результаты расчетов
|
|
Номинальный припуск на диаметр при предварительном шлифовании | 2Пном3 | 0,237 | — |
Расчетный диаметр поверхности после получистового точения брасч2 б-3+2Пном3 | ^-расч2 | 85,4h10 (85,41 -0,14) | Ra5 |
Диаметр после получистового точения (округленный) | d2 | 85,4h10 | — |
Номинальный припуск на диаметр при получистовом точении | 2Пном2 | 0,94 мм | — |
Расчетный диаметр после чернового точения ^расч1 d2 + 2 Пном2 | брасч1 | 86,35h13 (85,35-0,54) | Ra20 |
Диаметр после чернового точения (округленный) | d1 | 86,35hl3 | — |
Номинальный припуск на диаметр при черновом точении | 2Пном1 | 4,044 | — |
Расчетный диаметр заготовки брасч0 d1 + 2Пном1 | dрасч0 | +1,3 90,394-07 | — |
Диаметр заготовки с допуском (округленный) | d0 | +1,3 90,4-07 | Rа60 (Rz250) |
|
4. Общий припуск на механическую обработку этой поверхности составит: 2Побща = 4044 + 940 + 237 + 114 = 5335 мкм.
При определении операционных припусков расчетно
аналитическим методом диаметр заготовки может быть принят 85 + 5,335 = 90,4 мм вместо 91,2, как это было рассчитано при проектировании штамповки (см. пример 5.3). Экономия составит по диаметру 0,8 мм, по массе - около 0,5 кг, или 2,5% массы исходной заготовки. Отсюда вытекает, что использование расчетно
аналитического метода открывает в ряде случаев возможность значительной экономии металла заготовок, чем при расчете по табличному методу.
Задача 5.3. Четырехступенчатый вал изготовляется из штампованной поковки повышенной точности (I класс).
Требуется для ступени этого вала, имеющей диаметр da с шероховатостью Ra1,25 определить промежуточные припуски на все переходы расчетно-аналитическим способом.
Исходные данные для решения задачи по вариантам даны в табл. 5.3; 5.6; 5.8 и на рис. 5.4. Задачу выполнять в объеме примера 5.3.
Исходные данные Таблица 5.8
|
|
§ 6. ПОРЯДОК ПРОЕКТИРОВАНИЯ ТЕХНОЛОГИЧЕСКИХ
ПРОЦЕССОВ
Определение количества технологических переходов при
механической обработке для достижения заданной точности
размера поверхности
Пример 6.1. Элементарная поверхность ступени вала диаметром 085р6(85+00з7) изготовляется из штампованной поковки повышенной точности диаметром 0 91,2(-0,37)
Требуется: проанализировать исходные данные; определить
количество технологических переходов для достижения заданной точности размера рассматриваемой ступени; установить точность промежуточных размеров.
Решение. 1. При анализе устанавливаем, что в процессе
механической обработки рассматриваемой поверхности допуск размера диаметра исходной заготовки Td0 = 2 мм уменьшается до допуска размера диаметра детали ТДд = 0,022 мм (соответственно возрастает точность размера). При этом общий коэффициент ужесточения точности размера вычисляется по формуле Куж.р.общ. = Тао/Тад = 2/0,022 = 90.
2. Количество потребных технологических переходов определяется по формуле
lgK уж.р.общ 1,9542
0,46 0,46
Принимаем n=4.
3. Допуск размера диаметра заготовки ТД0 = 2 мм соответствует примерно, 16-му квалитету точности, а допуск размера детали - 6-му квалитету. Следовательно, точность повышается на 16-6 = 10
квалитетов. По принятым четырем технологическим переходам распределяем его по закону прогрессивного убывания: 10 = 4 + 3 + 2 + 1. Точность промежуточных размеров заготовки в процессе механической обработки будет соответствовать:
после 1-го перехода 12-му квалитету (h12);
» 2-го » 9-му » (h9.);
» 3-го » 7-му » (h7);
» 4-го » 6-му » (h6).
Задача 6.1. Элементарная наружная поверхность вращения детали диаметром Дд изготовляется из заготовки, имеющей диаметр do.
Требуется установить количество технологических переходов для осуществления обработки этой поверхности и изменение точности промежуточных размеров по переходам. Варианты даны в табл. 6.1.
Исходные данные Таблица 6.1
|
|
Выбор технологического оснащения при проектировании токарной
операции и оформление операционной карты
Пример 6.2. Для условий серийного производства проектируется операция обработки ступенчатого вала из горячекатаного проката, для которой разработан технологический операционный эскиз (рис. 6.1).
Требуется произвести обоснованный выбор технологического оснащения для этой операции.
Решение. 1. Как следует из операционного эскиза, для
рассматриваемой операции (заготовка установлена в центрах) требуется токарный станок, допускающий обработку над нижней частью суппорта заготовок
Рис. 6.1. Операционный эскиз |
диаметром dcyn>100 мм и с расстоянием между центрами Lu>500 мм. Пользуясь технологическими справочниками или литературой по металлорежущим станкам [3; 7], устанавливаем, что этим требованиям отвечают токарно-винторезные станки моделей 1М61 (dcyn = 160 мм; L4 = 640 мм) 16К20 (dcyn = 220 мм; L4 = 710 мм) и др.
Учитывая серийный тип производства, выбираем хорошо зарекомендованный себя универсальный станок модели 16К20.
2. Из эскиза видно, что предстоит центровая обработка и поэтому нужен комплект приспособлений: 1) патрон токарный поводковый диаметром 400 мм по ГОСТ 2572-72 для конца шпинделя с наружной резьбой (обозначение патрона 7108.ХХХХ, [8]); 2) хомутик поводковый для токарных работ по ГОСТ 2578-70 для d = 80^100 мм (обозначение 7107.ХХХХ [8]); 3) центр станочный упорный по ГОСТ 13214-79, конус Морзе 6 (обозначение 7032.ХХХХ); 4) центр станочный вращающийся по ГОСТ 8742-75, конус Морзе 5, тип А.
3. Для этой операции требуется токарный проходной отогнутый правый резец с пластинкой твердого сплава, угол ф = 45о (обозначение 2102-0031 Т15К6 по ГОСТ 18877-73).
4. Для контроля размера диаметра и шероховатости обрабатываемой поверхности соответственно нужны: штангенциркуль по ГОСТ 166-80 (код 39 3311.ХХХХ); образцы шероховатости Ra20 для цилиндрической поверхности.
Задача 6.3. Для условий серийного производства проектируется технологический процесс механической обработки втулки, изображенной на рис. 6.2. Процесс механической обработки детали из стального горячекатаного проката диаметром 105 мм представлен операционными эскизами (рис. 6.3).
Требуется для заданной операции произвести выбор технологического оснащения (варианты даны на рис. 6.4 и в табл. 6.2).
![]() | ||||
|

5 VI
У с 55 о 5 А
Шя
|
Позици.о 5
X
5 V5
У сзаноЗ Б
&Х7/
V X
|
г |
|
Исходные данные Таблица 6.2
|
|
§ 7. КОНТРОЛЬ КАЧЕСТВА ПРОДУКЦИИ
При разработке технологических процессов изготовления деталей серьезное внимание уделяется вопросам технического контроля и исходной заготовки, и заготовки в процессе ее обработки, и готовой детали. С этой целью в технологический процесс включаются контрольные операции. Оснащение этих операций производится с учетом типа производства и его организационной структуры, вида изделия, объема выпуска деталей, максимального использования стандартного контрольного оборудования и оснастки для контроля.
Показателями операций технического контроля являются: точность измерений, достоверность их, трудоемкость и стоимость контроля, а также объем, полнота, периодичность, продолжительность контрольных операций.
Средства технического контроля включают контрольное оборудование, оснастку для контрольных работ и средства автоматизации и механизации контроля.
Выбор средств контроля, регламентированный ГОСТ 14.306-73, производится с учетом типа производства, вида изделия и объема его выпуска, характера технологического процесса, максимального применения стандартных средств измерения и др.
Выбор средств контроля можно произвести по справочным материалам производственного контроля, по ведомственным
материалам и другим источникам. Для выполнения сложных контрольных операций пользуются приспособлениями, причем, если имеющиеся стандартные универсальные приспособления не подходят, прибегают к использованию специальных.
Оформление документов технического контроля производится в соответствии с ГОСТ 3.1502-74.
Выбор способов и средств контроля выполнения технических
требований
Пример 7.1. На рабочем чертеже детали «Вал ступенчатый» показаны допуски на взаимное расположение поверхностей вала (рис. 7.1).
Рис. 7.1. Требования к расположению поверхностей |
Требуется: описать содержание указанного допуска; перечислить возможные способы обработки и условия выполнения указанных требований к точности; указать способ контроля.
Решение: 1. На чертеже вала указаны допуски на биения (радиальные и торцовые) двух ступеней и двух уступов вала относительно общей оси центровых отверстии, размер допуска одинаков для всех поверхностей и составляет 0,1 мм.
2. Для достижения требуемой точности расположения поверхностей нужно, чтобы окончательная обработка каждой из этих поверхностей (чистовое точение или круглое шлифование ступеней и чистовое подрезание или шлифование уступов) производилась с использованием постоянной технологической базы - центровых отверстий и желательно с одного установа.
3. Контроль выполнения этих технических требований осуществляют на контрольных центрах 1 (рис. 7.2) с помощью измерительных головок обычного типа 2 и рычажных 3, устанавливаемых на стойках 4. Контроль осуществляется при медленном вращении вала.
1 2 4 3 1
Рис. 7.2. Способ контроля расположения поверхностей |
Задача 7.1. На рабочем чертеже заданной детали (варианты приведены на рис. 7.3) условным обозначением показан допуск формы поверхности или допуск взаимного расположения поверхностей ее.
Требуется: описать содержание указанного допуска; перечислить возможные способы обработки рассматриваемой поверхности условия для достижения указанной точности; указать способ контроля.
![]() | ![]() | ||
V x
// | 0 I | ||
| |||
* | - | ||
|
|
Рис. 7.3. Отклонения формы и расположения поверхностей
Составление схемы контроля и разработка идеи конструкции
контрольного приспособления
Пример 7.2. На эскизе детали (рис. 7.4, а) указан допуск взаимного расположения двух поверхностей детали.
Требуется: расшифровать содержание обозначенного допуска; составить схему контроля детали для определения этого отклонения; предложить идею контрольного приспособления для контроля детали.
Решение. 1. На эскизе обозначено, что непараллельность
проверяемой поверхности относительно поверхности А (базы) не должна превышать 0,2 мм.
2. Схема контроля для определения непараллельное™ этих поверхностей показана на рис. 7.4, б: проверяемая заготовка ставится базовой поверхностью А на подставку - центровик 1, а в проверяемую поверхность упирается штифт 2 индикатора. Медленно вращая заготовку, по крайним показаниям стрелки индикатора определяют значение непараллельности.
3. Приспособление может быть создано так: на плите, играющей роль корпуса приспособления, устанавливается стойка с индикатором. Для ускорения операции на столе должен быть предусмотрен быстродействующий подъемный или поворотный механизм для индикатора.
![]() |
a) В)
Задача 7.2. На эскизе детали (см. рис. 7.3) показан допуск формы или расположения поверхности детали.
Требуется: описать содержание допуска; составить схему
контроля детали для определения погрешности; предложить идею конструкции контрольного приспособления.
§ 8. МЕТОДЫ УСТАНОВКИ ЗАГОТОВОК. УСТАНОВОЧНЫЕ
ЭЛЕМЕНТЫ ПРИСПОСОБЛЕНИЯ
Установочные элементы и механизмы служат для установки и центрирования обрабатываемых заготовок в приспособлениях. От их правильного выбора и расстановки зависит точность обработки. Основные виды установочных деталей стандартизованы, что надо учитывать при их выборе [8,9].
При установке заготовок в приспособлении возникают погрешности базирования. В практике работы возникает необходимость определения этих погрешностей.
Погрешность базирования при установке заготовки, например по двум отверстиям на двух установочных пальцах (цилиндрическом и срезанном), возникает из-за зазоров в соединениях пальцев и отверстий и равна угловому смещению (перекосу) amax заготовки (рис. 8.1). Определение наибольшего возможного угла перекоса производится по формуле:
tgamax (Smax1 + Smax2 )/(2L), (8.1)
где Smaxi1 Smax2 - наибольшие зазоры в соединении отверстия и пальца в каждом из соединений;
L - расстояние между центрами отверстий (пальцев).
При таком базировании срезанный палец должен быть расположен так, чтобы его большая диагональ была перпендикулярна линии, соединяющей центры пальцев (рис. 8.1).
Рис. 8.1. Погрешность установки заготовки на пальцах |
Разработка схемы установки заготовки и выбор установочных
элементов
![]() |
Пример 8.1. На консольно-фрезерном станке производится обработка корпусной детали (рис. 8.2,а).
Требуется: выбрать технологическую базу; разработать схему установки заготовки; подобрать установочные элементы; проверить соблюдение правил шести точек; определить угловую погрешность установки.
Решение. 1. Пользуясь эскизом детали, устанавливаем, что в качестве технологической базы рационально выбрать следующие поверхности: плоскость А основания, которая является конструкторской базой детали, и два отверстия (из четырех имеющихся), расположенных диагонально, для правильной угловой ориентации в процессе обработки.
2. Схема базирования заготовки: плоскость А устанавливается на трех опорных точках, поверхность одного из отверстий создает базирование по двум точкам, а второе отверстие - по одной.
3. В качестве установочных элементов принимаем три опоры под плоскость А, расставляемые возможно дальше друг от друга, палец цилиндрический и срезанный палец.
4. Правило шести точек выполнено.
5. Наибольший угловой перекос заготовки, базирующейся по двум отверстиям, определяется расчетом по формуле (8.1) и в нашем случае
равен tgamax = Smax/L.
Если учесть, что Вотвтах =20,033 мм, а палец установочный 20d9 (20 -0067) имеет минимальный диаметр d^. min= 19,883мм, то
8тах=Оотв.тах^пал.тт= 20,033-19,883 = 0,15мм. _________
Расстояние между базовыми отверстиями L = V2502 +1602 = 296,82 мм, откуда
tg amax =0,15/296,82 = 0,0005.
При длине обрабатываемой плоскости l = 200 мм (рис. 8.2, б) линейное смещение равно
х = l-tgamax = 200-0,0005 = 0,l мм.
Задача 8.1. На станке производится обработка детали (варианты приведены на рис. 8.3 и в табл. 8.1). Требуется: составить описание операции; определить технологическую базу; разработать схему базирования; проверить соблюдение правил базирования; выбрать установочные элементы; обосновать идею приспособления.
Исходные данные Таблица 8.1
|
|
| ![]() | |||||||||||||
| ||||||||||||||
| ||||||||||||||
|
| |||||||||||||
|


Рис. 8.3. Операционные эскизы
ГЛАВА 2. МЕТОДЫ ОБРАБОТКИ ОСНОВНЫХ
ПОВЕРХНОСТЕЙ ДЕТАЛЕЙ МАШИН
Всякая деталь машины ограничена разными по форме, размерам, точности, шероховатости и другим показателям поверхностями. При проектировании технологического процесса изготовления детали для каждой ее поверхности должны быть выбраны соответственно методы обработки и установлена последовательность обработки.
Основным методом является механическая обработка, в которой участвуют элементы технологической системы (станок-
приспособление-инструмент-заготовка). Согласно требованиям,
предъявляемым к обрабатываемой поверхности, принимают такой вид обработки, технологические возможности которого обеспечивают снятие заданного припуска с соблюдением экономической точности обработки, высокую производительность и выполнение других техникоэкономических показателей.
Существенной частью работы по проектированию технологического процесса является разработка станочных операций, в ходе которой устанавливают содержание и структуру операции, выбирают тип и модель станка, технологическую оснастку, определяют режимы резания, выполняют техническое нормирование операции и производят все расчеты, подтверждающие экономическую эффективность проектируемой операции.
§ 9. ОБРАБОТКА НАРУЖНЫХ ПОВЕРХНОСТЕЙ ТЕЛ
ВРАЩЕНИЯ
Наружные поверхности тел вращения, особенно цилиндрические, вполне технологичны. Эти поверхности имеются у многих деталей машин, в частности у деталей класса 40 («Тела вращения»).
Механическая обработка таких поверхностей производится на этапах черновой и получистовой обработки точением, на этапе чистовой обработки - тонким точением или шлифованием, отделочные работы - тонким шлифованием, притиркой, суперфинишем.
В зависимости от вида заготовки и требований, предъявляемых к поверхности по точности, шероховатости и другим параметрам, меняется количество технологических переходов, необходимых для обработки.
Проектирование операции черновой обработки ступенчатого вала
из горячекатаного проката
Пример 9.1. Ступенчатый вал подвергается черновой токарной обработке в условиях мелкосерийного производства. Исходная заготовка - штучная из горячекатаного круглого проката нормальной точности 0100 (см. пример А1.1) - после разрезания была
подвергнута обработке торцов и их зацентровке. Масса заготовки тз = 29,6 кг. Материал детали - сталь 45 (5в = 700 МПа). Эскиз заготовки после токарной операции изображен на рис. 9.1.
Требуется спроектировать операцию указанной обработки.
![]() | ![]() | ![]() | ![]() | ||||
Rz 80
362,4812
408 *
Рис. 9.1. Эскиз детали
Решение. 1. По условию устанавливаем, что в проектируемой операции должны быть обработаны пять наружных цилиндрических поверхностей и четыре торцовых (на уступах) - всего 9 поверхностей. Точность размеров невысокая - по 12-му квалитету, шероховатость поверхности достаточно велика (Яа20 или Rz80).
Для получения такой точности и шероховатости достаточно провести однократную токарную обработку. При этом допускаются большие глубина резания и подача. Следует обратить внимание на большие общие припуски при обработке крайних ступеней вала, достигающие величины 100-61,65 = 38,35 мм. Такие припуски придется удалить за несколько рабочих ходов. Так как необходимо обработать все наружные поверхности (кроме наружных торцов), то операция будет выполняться в два установа.
Обращает на себя внимание характер простановки линейных размеров: все они задаются от торца уступа между ступенями с диаметрами 81,7 и 91,2 мм. Это обстоятельство повлияет на порядок обработки торцовых поверхностей. Из торцов нужно в первую очередь обработать базовый торец и от него вести отсчет и контроль линейных размеров при обработке остальных уступов заготовки.
2. Из приведенных выше соображений операция состоит из двух
установок (рис. 9.2) и девяти технологических переходов,
перечисленных в табл. 9.1.
3. Мелкосерийный тип производства определяет применение универсальной технологической оснастки.
4. Для рассматриваемого случая с учетом типа производства пригодны универсальные токарные и токарно-винторезные станки, допускающие обработку заготовок над суппортом диаметром 100 мм и более и с расстоянием между центрами 500 мм и более. К таким станкам относятся станки моделей 1П611, 1Б616, 1К62, 16К20 и др. Можно использовать, например, токарно-винторезный станок модели 16К20 (наибольший наружный диаметр; заготовки над суппортом 220 мм и расстояние между центрами 710 мм). Технические характеристики этого станка соответствуют лучшим мировым стандартам.
5. Технологическая оснастка для данной операции состоит из:
а) токарного поводкового патрона по ГОСТ 2572-72 диаметром 400 мм;
б) поводкового хомутика по ГОСТ 2578-70 для зажима заготовок диаметром 0100 и 62 мм (для двух установок);
в) упорного центра Морзе 6 по ГОСТ 2575-79 для установки в шпиндель станка;
г) вращающегося центра Морзе 5 ГОСТ 8742-75 для установки в пиноль задней бабки.
|
| 6 | |||
Г? | |||||
| 0\ | Х2 | 38,882 | ||
4 08 ' | 12582 | ||||
|
|
У стан од Б |
Выбор режущих инструментов производится по технологическим справочникам, ГОСТам и другим источникам. Так, для обтачивания поверхности в первом технологическом переходе используют токарный проходной отогнутый резец, оснащенный твердосплавной пластиной Т15К6, с углом ф = 45° по ГОСТ 18877-73, а для точения шеек с образованием торцов уступов - упорный токарный резец с такой же пластиной (ф = 90° по ГОСТ 18879-73). Размеры резцов - по размерам резцедержателя станка (по паспорту станка) - 16х20х150 мм [10].
Контроль размеров производится штангенциркулями и линейками или скобами и шаблонами.
Для контроля шероховатости обработанных поверхностей применяем образцы шероховатости Яа20 по ГОСТ 9378-75 для наружных поверхностей вращения и для плоских поверхностей.
6. В соответствии с выбранным оборудованием наименование операции «Токарно-винторезная» (ГОСТ 6.1702-79, прил. 2).
Описание содержания операции по установкам и переходам приводится в табл. 9.1.
Результаты расчетов Таблица 9.1
|
|
В результате совмещения переходов и применения при обтачивании ступеней вала упорных резцов с углом ф = 90° число технологических переходов можно уменьшить до 6 вместо 9, как установлено в п. 2.
7. Теперь надо рассчитать рациональные припуски на черновую обработку. При выполнении 2-го перехода (см. табл. 9.1) обтачивается поверхность 1 (см. рис. 9.2), припуск 2П на диаметр и глубина резания t2 при этом переходе определяются так (см. рис. 9.1):
2П = 100-91,2 = 8,8 мм; t2 = 2П/2 = 8,8/2 = 4,4 мм.
При выполнении 3-го перехода получаем
2П = 91,2-81,7 = 9,5 мм; t3 = 4,75 мм.
Для 5-го перехода
2П = 100-86,8 = 13,2 мм; t5 = 3,3 мм (при I = 2).
Для 7-го перехода
2П = 81,7-61,65 = 20,05 мм; t7 = 5мм (при t = 2).
8. Установление режимов резания производится с помощью литературы [10], для каждого i-ro технологического перехода по глубине резания t выбирают подачу 8норм , по паспортным данным станка устанавливается подача 8факт , ближайшая к значению 8норм; далее выбирают скорость резания инорм, по ней рассчитывают частоту вращения шпинделя, об/мин: прасч = 1000V/(nd3); для данного станка по паспорту находят фактическое значение Пфакт и определяют фактическую (действительную) скорость резания, м/мин: V = ndn /1000.
Разберем подробно 2-й переход:
• глубина резания t2 = 4,4 мм (см. п. 7);
• выбираем подачу 8норм = 0,5...0,7 мм/об;
• устанавливаем 8факт = 0,7мм/об;
• выбираем скорость резания ^орм = 117 м/мин (1,95 м/с);
• поправочные коэффициенты Ки = Кп = 1,
• определяем расчетную частоту вращения шпинделя
прасч = 1000-117/(3,14-100) = 372 об/мин;
• частота вращения по паспорту станка Пфакт = 315 об/мин;
• рассчитываем фактическую скорость резания
"V факт = 0,001-3,14-100-315 = 99м/мин.
Теперь нужно проверить выбранный режим резания по мощности станка. Мощность, потребная на резание, равна 8,3 кВт, поправочный коэффициент KN = 1. Мощность на шпинделе Кшп = 7,6...8 кВт. Мощность на шпинделе по слабому звену кинематической цепи N'^= 7,6...8,5 кВт. Отсюда следует, что принятый режим резания неосуществим на станке, так как потребная мощность больше, чем достижимая (8,3>7,8).
Выход из положения можно найти, перейдя на ближайшую меньшую частоту вращения Пфакт = 250 об/мин; при этом ифакт = 0,001-3,14-100-250 = 78,5 м/мин.
При этом режиме потребная мощность равна 7 кВт. Процесс резания теперь осуществим, так как выдержано условие Кпотр^шп.
Заметим, что вынужденное снижение скорости резания против нормативной увеличит стойкость инструмента, а это даст экономию режущего инструмента.
9. Техническое нормирование операции выполняется по литературе [11], и его результаты приведены в табл. 9.1:
• основное технологическое время операции ^to = 8,12 мин;
• вспомогательное время операции £tB =8 мин;
• оперативное время ton = 8,12 + 8 = 16,12 мин;
• время обслуживания рабочего места принято в размере 0,04/ tOT [11]: Wji = 0,04-16,12 = 0,65 мин;
• время перерывов на отдых и личные надобности:
W =0,04 tOT =0,04-16,12=0,65 мин;
• штучное время операции
W= ъ + tB + ^бсл + W=8,12 + 8+0,65+0,65=17,42 мин;
• подготовительно-заключительное время на партию деталей [11]
составляет ^.з. =16+7 = 23 мин;
• штучно-калькуляционное в %т.к. = 17,42 + 23/30 = 18,19 мин; при
партии пд = 30 шт.
• норма выработки в смену Нв = (480-23)/17,42 = 26 шт.
Необходимости в пересчете вспомогательного времени в
зависимости от характера серийности работ в нашем случае нет, так как суммарная продолжительность обработки партии деталей составляет 1,2 смены.
10. После завершения всей работы по проектированию операции необходимо проанализировать результаты и оценить их с точки зрения эффективности, чтобы искать пути интенсификации процесса.
Так, обращает на себя внимание значительное основное технологическое время операции. Это объясняется тем, что при использовании проката, выбранного в качестве заготовки, значительную долю металла (35%) приходится срезать в виде стружки. Выход видится в применении более рациональных, перспективных видов заготовок: штампованных поковок и особенно поковок, получаемых ротационным обжатием, при котором заготовка близка по конфигурации и размерам к готовой детали. При этом методе не используются дорогие и сложные штампы, и его можно применять при любом объеме выпуска деталей.
Но даже при применении проката в качестве заготовок можно значительно уменьшить расход металла и снизить трудоемкость работы, если подвергнуть прокат правке на соответствующем оборудовании (прессах, правильно-рихтовальных станках и др.). При применении правки штучной заготовки и расчете припусков расчетно
аналитическим методом диаметр проката должен быть взят не 100, а 95 мм. Это позволяет снизить массу заготовки на 2,9 кг (на 9,8%) и соответственно снизить трудоемкость черновой токарной обработки. При этом изменятся режимы резания 2-го и 5-го переходов (табл. 9.2).
Таблица 9.2 Результаты расчетов
|
|
Оперативное время этих двух переходов при этом снизится с 6,63 мин до 3,3 мин, т.е. на 3,33 мин, что составляет около 20,6% от оперативного времени ton.
При этом соответственно уменьшается расход режущих инструментов, электрической энергии, расходы на заработную плату станочников, на амортизацию станка и др.
Значительный эффект дает использование при токарной обработке копировальных устройств, в частности гидрокопировальных суппортов, которыми теперь оснащаются многие токарно-винторезные станки, в частности станок модели 16К20М.
Если сравнить трудоемкость этой же операции, выполняемой на токарно-винторезном станке (W.k = 18,19 мин), с трудоемкостью операции, выполняемой на токарно-винторезном станке с
использованием гидрокопировального суппорта (Wk = 13,5 мин), то сокращение нормы времени на операцию определяем по формуле
At нв = 100(t ШТ1 -1 mT2)/t ШТ1.
1819 — 135
w= —---------- -■ 100% = 25,8%.
. . 18,19
Рост производительности труда определяем по формуле:
Рп = 100AW(100-AW ).
Рп = 100-25,8/(100-25,8) = 34,8%.
Это свидетельство эффективности применения методов точения с использованием копировального устройства на станках.
Еще больший технико-экономический эффект при
рассматриваемом типе производства дает применение станков с числовым программным управлением (ЧПУ), например хорошо себя зарекомендовавшего станка модели 16К20ФЗ. Хотя режимы резания при этом не повышаются (остаются прежними), значительно сокращается вспомогательное время за счет автоматического управления станком. Особенно большой эффект по производительности труда получается благодаря внедрению на участке станков с ЧПУ многостаночного обслуживания.
Приведенные рассуждения показывают, что в механической обработке деталей имеются огромные резервы для интенсификации процессов обработки, повышения ее эффективности. Их важно вскрывать и активно внедрять в производство.
Задача 9.1. Ступенчатый вал (рис. 9.3) подвергается черновой токарной обработке в условиях мелкосерийного производства. В качестве заготовки принимается горячекатаный прокат круглого сечения нормальной точности. Исходная заготовка - штучная диаметром d0, массой m0. Токарной обработке предшествовала обработка торцов с выдерживанием размера Ьобщ и зацентровка их с двух сторон. Материал детали - сталь 40Х ГОСТ 4543-74 (5в = 700МПа).
Варианты приведены в табл. 9.3 для обозначений по рис. 9.3. Допуски на обрабатываемые размеры по h12.
Требуется спроектировать токарно-винторезную операцию на указанную обработку.
Рис. 9.3. Эскиз детали |
Таблица 9.3
Исходные данные
|
|
Задача 9.2. Ступенчатый вал, изготовляемый в условиях серийного производства из штучной заготовки из круглого горячекатаного стального проката, обрабатывался начерно на токарновинторезном станке (см. пример 9.1). В порядке усовершенствования технологии производства внесено предложение об использовании в этой операции гидрокопировального суппорта.
Требуется: разработать операцию; изложить соображения о рациональности предложения и определить показатель роста производительности труда. Варианты так же, как в задаче 9.1
Проектирование шлифовальной операции
Пример 9.2. Ступенчатый вал имеет несколько ступеней высокой точности с малой шероховатостью. Завершающим методом обработки этих поверхностей должно быть чистовое круглое шлифование.
Так, необходимо шлифовать ступень 085р6 (85 +0,°37) с
шероховатостью Ra2,5. (Расчет промежуточных размеров приведен в примере 5.2).
Требуется спроектировать операцию чистового шлифования ступени.
Решение. 1. Анализ исходных данных позволил установить, что материал детали - сталь 45 (ГОСТ 1050-74) - относиться к I группе материалов[10,ч.3] и после улучшения имеет твердость HRС35, припуск на обработку по диаметру 2П = 0,1мм, способ установки заготовки - в центрах, масса заготовки m0= 19,4кг, производство - серийное.
2. Если принять, что в операции шлифуется поверхность только одной ступени, то операция состоит из одного установа, одного технологического и четырех вспомогательных переходов (табл. 9.4).
Содержание операции
Таблица 9.4
|
|
3. На основании исходных данных по условию примера и п. 1
принимаем, что технологическое оснащение должно быть
универсальным, производительным и точным.
4. Учитывая габаритные размеры заготовки, выбираем кругло
шлифовальный полуавтомат модели ЗМ151, предназначенный для обработки заготовок с диаметром dmax =200 мм, длиной обработки Lm&x = 700 мм; мощность электродвигателя круга Ркр = 10 кВт; частота вращения круга пкр = 1590 об/мин; скорость резания Vkp = 50 м/с, частота вращения заготовки (регулирование бесступенчатое) пд = 50...500 об/мин; скорость продольного перемещения стола (регулирование бесступенчатое) Snp = 0,05...5 м/мин; периодическая подача шлифовальной бабки при реверсе стола (регулирование бесступенчатое) S tx = 0,001...0,05мм/ход.
5. Для операции необходимы:
а) приспособления - патрон поводковый (имеется у станка), хомутик для диаметра 80 мм по ГОСТ 16488-70, два упорных центра Морзе 4 по ГОСТ 13214-79;
б) шлифовальный круг, выбираемый по литературе [10,Ч.3]: для данной операции подходит круг из белого электрокорунда, с твердостью круга - С1 (средняя), керамической связкой марки К, зернистостью № 40 (размер зерна 40 мкм) средней структурой 6;
форма и размеры шлифовального круга выбираются по паспортным данным станка: круг ПП плоский прямого профиля,
размеры круга: диаметр dkp = 600 мм, ширина круга Вкр = 80 мм, диаметр отверстия Ботв = 305 мм. Маркировка круга по всем данным:
ПП 600X80X305 24А40 С1 6К ГОСТ 2424-75;
в) средства контроля: для размера диаметра - прибор активного контроля по ГОСТ 8517-70, а для шероховатости - образцы шероховатости Ra1,25. Применение активного контроля способствует повышению производительности труда, создает условия для многостаночного обслуживания и др.
6. Установление режима резания начинаем с выбора частоты вращения заготовки в зависимости от ее диаметра, твердости обрабатываемого материала и исходя из условий бесприжогового шлифования [10,Ч.3]: Пд = 123 об/мин. Скорость вращения заготовки:
Уд = л^д-пд/1000 = 0,001-3,14-85,1-123 = 32,9 м/мин = 0,55 м/с.
Определяем продольную минутную подачу [10,Ч.3]: S^.ra&i. = 4760 мм/мин. На табличное значение принимают поправочные коэффициенты в зависимости: 1) от шероховатости поверхности KSMra1 = 1,0; 2) от формы обрабатываемой поверхности KSMra2 = 0,95. Тогда
имеем: Smhk Sмин.табл 'КяминГ КЯмин2 476°'1,0'0,95 4522 мм/мин.
Поперечная подача за один ход стола Stx.Ta6ji. = 0,005 мм/ход. Поправочный коэффициент при I группе обрабатываемого материала и 6-м квалитете равен KSt1 = 1,0; коэффициенты, зависящие от: припуска на обработку Ksn<0,6; размера и скорости шлифовального круга KSt3 = 1,3; способа шлифования и контроля размера KSt4 = 1,4; формы поверхности и жесткости заготовки KSt5 = l,0; твердости круга К1 = 1,0; точности и жесткости станка Кж = 1,0. Тогда поперечная подача равна
31х ^х.табл. ’KSt1’KSt2 "KSt3 "KSt4 ’KSt5’ К1 Кж =
= 0,005 1,0-0,6-1,3 1,4 1,0-1,0-1,0 = 0,0055 мм/ход.
Определяем мощность резания: Крезтабл. =4,8 кВт. Поправочный коэффициент Кр= 1,47, тогда N^=48-1,47 = 7,1 кВт, что меньше мощности станка.
Устанавливаем бесприжоговую предельную мощность: Ny^Npe/Вф = 7,1/80=0,089 кВт/мм < Nmmax =0,125 кВт/мм.
7. Производим расчет основного (технологического) времени по формуле
t0 = КЬд2П/(8мин231х),
где К — коэффициент выхаживания (принимаем К = 1,4),
Ьд — длина хода (при наличии торца с одной стороны и выхода шлифовального круга только в одну сторону Ьд = 1д - 0,3Вкр=120 -0,3-80 = 96 мм), получаем:
to=96-0,1-1,4/(4522-2-0,0055) = 0,27 мин.
8. Число рабочих ходов, необходимых для обработки: i=2m(2Stx ) = 0,1/(2-0,0055) = 10,
а с учетом выхаживания получаем 14 рабочих ходов.
9. Техническое нормирование операции выполняется по нормативам времени аналогично тому, как это проделано в предыдущих примерах.
Задача 9.3. Ступенчатый вал (см. рис. 5.4 и табл. 5.1)
изготавливается в условиях крупносерийного производства из поковки штампованной из стали 40Х (оВ=800 МПа). Отдельные ступени вала, имеющие высокую точность и малую шероховатость, подвергаются круглому шлифованию однократному (4) или двукратному (1 и 3).
Требуется: спроектировать круглошлифовальную операцию
(варианты приведены в табл. 9.5).
Таблица 9.5 Исходные данные
|
|
ГЛАВА 3. ТЕХНОЛОГИЯ СБОРКИ МАШИН
§ 10. ПРОЕКТИРОВАНИЕ ТЕХНОЛОГИЧЕСКОГО ПРОЦЕССА
СБОРКИ
Сборка - часть технологического процесса изготовления изделия, которая состоит из работ по соединению отдельных деталей в сборочные единицы и из них готовых изделий, соответствующих своему назначению.
В технологический процесс сборки включаются также работы по регулированию, наладке и испытанию изделия. Трудоемкость сборочных работ составляет в массовом производстве до 20%, в крупносерийном - 20...25%, в серийном - 30...35%, в мелкосерийном - 40...50% от трудоемкости механической обработки.
По форме организации сборка бывает стационарной и подвижной. При более прогрессивной подвижной сборке изделие в процессе сборки перемещается от одного рабочего места к другому и на каждом рабочем месте выполняется постоянно одна и та же операция одним рабочим или бригадой. Подвижная сборка характерна для крупносерийного и массового типов производства. Дифференциация работ на ряд мелких операций оказывается высокопроизводительным и прогрессивным процессом.
В современном производстве все большее место занимает автоматическая сборка, при которой операции сборки, контроля, окраски, сушки производятся без непосредственного участия человека. При автоматической сборке используются сборочные автоматы, в конструкцию которых входят бункерно-ориентирующие устройства, накопители, устройства для скрепления собираемых деталей и контроля качества их соединения.
Автоматическая сборка, как правило, выполняется по принципу полной взаимозаменяемости, а следовательно, соединяемые детали должны быть изготовлены с малыми допусками.
Для сборки несложных сборочных единиц, а также для покрасочных и других, вредных для человека, работ, для транспортирования изделий, установки и снятия заготовок могут использоваться промышленные роботы, представляющие собой универсальные автоматы с большим числом (до 10) степеней подвижности рабочего органа и управляемые по программе.
При проектировании поточных линий сборки возникает необходимость определения такта выпуска изделий с линии. Такт выпуска изделий (мин) определяется по формуле
Тв = 60Фд.г./Дизд.г, (10.1)
где Фд.г - действительный годовой фонд времени работы сборочного конвейера с учетом заданной сменности (при двухсменной работе и с учетом времени на ремонт оборудования Фдг = 4008 ч);
Диздг - годовой объем выпуска.
Число сборочных мест определяется по формуле
Мсб = Тсб.пр/(ТвРср), (102)
где Тсб.пр - трудоемкость сборочного процесса, мин;
Рср = 1,2..1,8 - средняя плотность работы (число рабочих на одном рабочем месте).
Общее число сборочных мест с учетом контрольных (Мк) и резервных мест (Мр) составит
Мсб.общ = Мсб + Мк + Мр. (10.3)
Скорость движения конвейера при непрерывном его движении
равна
и = l/Тв. (10.4)
Здесь l - расстояние между осями двух смежных собираемых объектов, т. е. шаг рабочих мест или станций сборочного конвейера:
l = 1и + 1пр, (10.5)
где 1 - длина собираемого объекта или длина сборочного места (станции);
1пр = 0,3... 1 - расстояние между объектами сборки или между рабочими местами (станциями), м.
Рабочая длина поточной сборочной линии (конвейера)
![]() | ![]() | ![]() | |||
определяется так:
При решении ряда технологических вопросов, связанных со сборкой машин и механизмов, возникает необходимость решения задач по определению отдельных параметров плоских размерных цепей.
Достижение заданной точности замыкающего звена достигается за счет полной взаимозаменяемости, неполной взаимозаменяемости, групповой взаимозаменяемости, пригонки и регулирования.
В технологической практике чаще встречаются задачи, в которых по установленным номинальным размерам, допускам и предельным отклонениям составляющих звеньев определяют номинальный размер, допуск и предельное отклонение замыкающего звена («обратная задача»).
Последовательность решения обратной задачи методом полной взаимозаменяемости такова: 1) рассматривая сборочный чертеж или технологическую схему, выделяют размерную цепь со всеми ее звеньями и выделяют замыкающее звено, а остальные звенья разбивают на увеличивающие и уменьшающие; 2) составляют уравнение
размерной цепи и определяют номинальный размер замыкающего звена по уравнению
Z Aув -Z Aум , (10.7)
m n
где тип- число увеличивающих и уменьшающих звеньев соответственно;
3) рассчитывают среднее отклонение поля допуска замыкающего звена
Ас. - ZA с.ув = ZA су,, (10.8)
где Ас.ув и Ас.ум - средние отклонения полей допусков увеличивающих и уменьшающих звеньев соответственно; 4) рассчитывают поле допуска замыкающего звена по формуле
Т. - Z T,, (10.9)
m+п
где Т, - допуск каждого составляющего звена; 5) определяют предельные отклонения: верхнее ES. и нижнее EI. и предельные размеры замыкающего звена: наибольший A.max и наименьший Aymin:
ES. = Ac. + 0,5T.; (10.10)
|
Asmax — As + ESs; (10.12)
Aamn — As + EIs. (10.13)
Сборка деталей машин, осуществляемая по посадкам с натягом, предназначается для осуществления неподвижных соединений без дополнительных средств крепления. Этот способ соединения деталей обладает рядом достоинств (простота конструкции деталей и сборки, высокая точность центрирования и др.) и поэтому широко распространен в машиностроении.
Имеется два основных способа сборки деталей при посадке с натягом: 1) продольная запрессовка - сборка осуществляется при нормальной температуре с помощью пресса (сборка под прессом); 2) поперечная запрессовка, или «способ термических деформаций», - сборка осуществляется при предварительном нагреве охватывающей детали («отверстия») или охлаждения охватываемой детали («вала»).
В задачи технолога при разработке и реализации операции продольной запрессовки входит определение необходимой максимальной силы пресса. Она определяется по формуле
Fn — fnPmaxn-dH.C. Ф (10.14)
где fn — (l,15...1,2)f, f - коэффициент трения при запрессовке (при соединении стальных деталей f — 0,0 6...0,13, при соединении деталей
чугуна f — 0,07 0,12 и др. [2]);
![]() | ![]() | ![]() | |||
l - длина контактной поверхности соединения, м; pmax - давление на контактных поверхностях сопрягаемых деталей при максимальном натяге Nmax, мм, выражается в Па по формуле
где уш - поправка, учитывающая смятие шероховатостей контактных поверхностей деталей при их соединении, определяется через параметры шероховатости поверхностей отверстия и вала:
Уш — 1,2(Rzd + Rzd); Уш — 5(RaD + Rad), (10.16)
где dnx. - номинальный диаметр соединения, мм;
![]() | ![]() | ![]() | ![]() | ![]() | |||||
Ci и C2 - коэффициенты Ляме, соответственно для охватываемой («вал») и охватывающей («отверстие») поверхностей:
где d1 - диаметр отверстия в охватываемой («вале») детали (при d1 = 0, т.е. в сплошном вале, получаем С1 = 1-ц1;
d2 - наружный диаметр охватывающей (втулки, корпуса) детали (при массивном корпусе, когда d2^^ получаем С2 = 1 + g2);
^1 и g2 - соответственно коэффициенты Пуассона материалов деталей «вала» и «отверстия» (для стальных деталей g = 0,3, для чугунных g = 0,25; для бронзовых g = 0,35; для латунных g = 0,38;
Е1 и Е2 - модули упругости, Па, материалов соответственно деталей «вала» и «отверстия» (для стали Е= (1,96...2)1011 Па, для чугунного литья Е= (0,74...1,05)-1011 Па; для бронзы E= 0,84-1011 Па; для латуни Е = 0,78- 1011Па).
В задачи технолога при проектировании операции сборки поперечной запрессовкой входит определение температуры нагрева охватывающей детали («отверстия») или температуры охлаждения охватываемой детали («вала»):
tD = [(Nmax + 8сб)/^)]+1;сб; (10.18)
td = U-(Nmax + Зсб)/( ad), (10.19)
где Nmax - наибольший натяг соединения, мм;
Бсб - минимально необходимый зазор при сборке, мм, принимаемый равным зазору в посадке H7/g6;
a - температурный коэффициент линейного расширения материала детали (для алюминия a= (23,9...26,5)-10-6 К-1; для бронзы a= (17,6...18,2). 10-6 K-1; для латуни (17...21)-10-6К-1; для стали a= (11,5... 12)10-6 К-1 ;
d - номинальный диаметр соединения, мм;
tc6 - температура в помещении сборки, °С. Нагрев можно осуществлять в кипящей воде (tD< 100°С), масляной ванне (tD< 110 ... 130°С), газовыми горелками, в нагревательных шкафах и печах, в индукционных печах с нагревом ТВЧ и др.
Для охлаждения охватываемой детали можно применять твердый диоксид углерода (td = -79°С), его смесь со спиртом (td = -100°С), жидкий азот (td= -196°С).
Применяется также комбинированный способ одновременного температурного воздействия на обе детали соединения.
Определение основных параметров сборочного конвейера
Пример 10.1. Годовой объем выпуска изделий сборочным участком Дгод = 100000 шт.; трудоемкость сборки одного изделия Тсб = 20 мин; длина собираемого изделия 1и = 0,5 м; режим работы сборочного участка двухсменный; на конвейере производится сборка изделия и две контрольные операции; расстояние между изделиями 1пр = 1м.
Требуется определить такт сборки, количество сборочных мест на конвейере, длину конвейера и скорость его движения.
Решение 1. Определение такта выпуска изделий с линии сборки (с конвейера) ведем по формуле (10.1): ТВ = 4008-60/100000 = 2,4 мин.
2. Число сборочных мест находим по формуле (10.2):
Мсб.м = 20/(2,4-1,2) = 6,9 (принимаем Мсб.м = 7).
3. Определение общего числа мест конвейера по формуле (10.3)
равно
Мсб.общ = 7 + 2 + 3=12.
4. Определение длины конвейера производим по формуле (10.6):
1конв= 12(0,5+ 1)= 18 м.
5. Скорость движения конвейера по формуле (10.4) равна
иконв = 1,5/2,4 = 0,625 м/мин.
Задача 10.1. Сборка заданного изделия производится на конвейере (варианты режима работы указаны в табл. 10.1).
Требуется определить такт сборки, количество сборочных мест на конвейере, длину конвейера и скорость его движения.
Исходные данные Таблица 10.1
|
|
Пример 10.2. В сборочной единице промежуточного вала редуктора (рис. 10.1), состоящей из шестерни 1, корпуса 2, кольца 3 и вала 4, конструктором задано, что для нормальной работы необходим зазор Азаз =0,05...0,75 мм, т. е. допуск на размер зазора Тзаз = 0,7 мм. Известны размеры:
А1=70_о,21; А2 = 35 . Следовательно, допуски Т1 = 0,21 мм; Т2 = 0,2 мм.
Требуется определить толщину кольца 3 и допуск на нее.
Рис. 10.1. Размерная цепь |
Решение. 1. Выделяем размерную цепь (внизу на рис. 10.1). Замыкающим звеном будет кольцо 3, звено 1 - увеличивающее, а звено 2 и зазор - уменьшающие.
2. Номинальный размер замыкающего звена определяем по формуле (10.7): АЕ = А1-(А2 + Азаз) = 70-(65 + 0) = 5 мм.
3. Среднее отклонение поля допуска корпуса EC1 = 0,5[0+(-0,21)] = -0,105 мм; шестерни EC2 = 0,5 [(-0,3) + (-0,5)]= -0,4 мм; зазора EG^ = 0,5(0,75 + 0,05) = 0,4 мм.
4. Среднее отклонение поля допуска замыкающего звена EG= -0,105-(-0,4 + 0,4)= -0,105 мм.
5. Размер поля допуска замыкающего звена находим по формуле (10.9): ТЕ = -0,21-0,2 + 0,7 = 0,29 мм.
6. Предельные отклонения замыкающего звена определяем по формулам (10.10) и (10.11):
ESs = -0,105+ 0,5-0,29 = 0,04 мм; EIS = -0,105-0,5-0,29= -0,25 мм.
7. Предельные размеры замыкающего звена определяем по формулам (10.13) и (10.12): ASmax = 5 + 0,04 = 5,04 мм; Aymin = 5-0,25 = 4,75 мм.
8. Чертежный размер толщины кольца А3 = 5+0’25 мм.
Задача 10.2. Рассматривая фрагмент сборочного чертежа редуктора (рис. 10.1), определить размер толщины кольца А3 с допуском, если заданы размеры корпуса А1 шестерни - А2 и зазора Азаз (варианты - в табл. 10.2).
Исходные данные Таблица 10.2
|
|
Приложение А
ВЫБОР И КОНСТРУИРОВАНИЕ ИСХОДНЫХ ЗАГОТОВОК
Современное состояние технологии машиностроения предоставляет большие возможности для рационального выбора вида исходной заготовки и способа ее получения.
Чем больше объем выпуска деталей, тем важнее выбрать заготовку прогрессивного вида, у которой форма и размеры приближаются к форме и размерам готовой детали. Такая тенденция современной технологии позволяет исключать обдирку и черновую обработку, добиваться высокой производительности и экономного расхода металла. Правильный выбор исходной заготовки существенно влияет на технико-экономические показатели технологического процесса изготовления детали.
Серьезное внимание должно уделяться конструированию исходной заготовки, т.е. установление ее формы, размеров с допускаемыми отклонениями, припусков на механическую обработку, твердости материала и технических требований, которым она должна отвечать. Установление размеров исходной заготовки состоит в том, что к размерам наружных поверхностей детали нужно прибавить, а от размеров внутренних поверхностей отнять общие припуски на механическую обработку. Для втулки с размерами Ад, Бд, Ьд (рис. А1.1) размеры исходной заготовки определяются так:
do Ад+2Побщ(1, | (А1.1) |
Бо=Бд-2Побщв; | (А1.2) |
L о L Д+ПобщЬ1 +ПобщЬ2, | (А1.3) |
|
где ПобщА, ПобщБ, и ПобщЬ - общие припуски на механическую обработку (на сторону) наружной, внутренней и торцевой поверхностей заготовки.
Выбор общего припуска на механическую обработку заготовок из сортового проката производится по таблицам [3;12], но размер ё0расч при выборе проката необходимо корректировать по сортаменту (ГОСТ 2590-71).
![]() | ![]() | ![]() | |||
Оценка качества исходной заготовки производится также по значению коэффициента использования материала:
где тД и т0 - массы соответственно детали и заготовки.
Конструирование заготовок из стального горячекатаного проката
Пример А1.1. Из стали 45 (ГОСТ 1050-74) изготовляют вал (рис. А1.2) массой 19,4 кг в условиях мелкосерийного производства (годовой объем выпуска 150 шт.).
![]() | ![]() | ||||||||||||||||||
![]() | |||||||||||||||||||
![]() | |||||||||||||||||||
![]() | |||||||||||||||||||
![]() | |||||||||||||||||||
![]() | |||||||||||||||||||
![]() | |||||||||||||||||||
![]() | |||||||||||||||||||
![]() | |||||||||||||||||||
![]() | |||||||||||||||||||
![]() | |||||||||||||||||||
L0 200 0 10
300+0
L0 060 010
400*
Рис. А 1.2. Эскиз детали
Требуется сконструировать исходную заготовку вала из стального горячекатаного проката.
Решение. 1. Поскольку форма вала имеет относительно
небольшую разницу перепада диаметров, а также отсутствуют дополнительные требования к механическим свойствам материала, выбираем в качестве заготовки, стальной горячекатаный прокат по ГОСТ 2590-71 [5, T1. стр. 169]. Из него разрезкой будут образованы цилиндрические заготовки диаметром do и длиной L0.
2. Для заданной детали целесообразно использовать прокат круглого сечения. Из имеющихся трех категорий точности проката выбираем обычную точность (В).
3. Диаметр проката определяют, исходя из наибольшего диаметра заготовки (09Oh1O), добавляя к нему общий припуск на механическую обработку, равный 2Побщ^ В нашем случае при длине заготовки свыше 360 до 720 мм общий припуск на диаметр Поб^=10 мм [12, стр. 72]. Допуск на диаметр устанавливается по ГОСТ 2590-71 составляет +0,6...-1,7 мм. Отсюда d0 =dmax+2ПOбщd=90+10=100 мм. Такой прокат имеется в сортаменте.
4. По формуле (А1.3) устанавливаем длину штучной заготовки: ^)^Д+2Побщь где Побщ]^=4 мм [12]. Получаем ^)=48О+24=488 мм. Допуск на длину заготовки после разрезки по 10... 12-му квалитетам составляет 250...630 мкм.
5. Технические требования, предъявляемые к заготовке:
допускаемая кривизна заготовки [3] QK.M=AL=1,0-488 мкм, т.е. не более 0,5 мм; шероховатость проката RZ=200 мкм.
6. Рассчитываем массу заготовки по формуле: m0=0,001-mnM-L0=0,001-61,65-488=30,09 кг,
где тПМ=61,65 кг - масса одного полного метра проката,
L - длина заготовки, мм.
7. Коэффициент использования материала штучной заготовки
![]() | ![]() | ![]() | ![]() | ||||
равен:
Материал заготовки используется плохо всего на - 64%.
8. Определение стоимости штучной заготовки производится по формуле Со=0,001 ЦТ-т0=0,001-133-30,09; Со=4 руб., где ЦТ=133 руб. - цена одной тонны металла по прейскуранту 01 - 08 1982 г.; то = 30,03 кг - масса заготовки.
![]() |
Эскиз заготовки представлен на рис. А1.3.
Задача А1.1. Сконструировать исходную заготовку вала из горячекатаного проката стали 40Х. Варианты и эскизы приведены на рис.А1.4 и табл. А1.1.
Исходные данные
|
|
\/f ffJ
Рис. А1.4. Эскиз детали |
Конструирование стальной поковки, изготовляемой горячей
объемной штамповкой
Пример А1.2. Из стали 45 изготовляют вал массой 19,4 кг (см. рис. А1.2). Термообработка - улучшение до твердости HRC 21...26. Неуказанные радиусы - 1,5 мм, фаски - 0,5х450. Годовой объем выпуска деталей в год 4500 шт., что соответствует крупносерийному типу производства.
Требуется сконструировать исходную заготовку, изготовляемую горячей объемной штамповкой.
Решение. 1. Учитывая свойства материала детали, ее массу, форму, размеры и тип производства, поковку целесообразно выполнять в закрытом штампе на молоте. Нагрев заготовки - пламенный в печи.
2. Руководствуясь правилом, что в плоскости разъема штампа должны располагаться два небольших габаритных размера поковки, принимаем, что ось поковки находится в плоскости разъема штампа и расположена горизонтально.
3. С целью уменьшения припусков на механическую обработку принимаем поковку I класса точности (повышенная точность). По ГОСТ 7505-74 определяем группу стали Ml.
![]() | ![]() | ||
Степень сложности поковки определяем, используя данные о детали, а не о поковке, так как последние еще неизвестны. Для этого применяем формулу
где тд = 19,4 кг - масса детали;
топ.ф.д. - масса цилиндра (рис. А1.5), описанного вокруг вала, диаметром dnmax = 90 мм и длиной Ьд = 480 мм.
Масса одного метра круглой стали этого диаметра тПМ=49,94 кг [12]. Масса цилиндра в килограммах топ.ф.д = тП.М'Ьд = 0,001-49,94-480 = 24 кг.
![]() |
Отсюда С = 19,4/24 = 0,81, что соответствует степени сложности С1.
4. Для дальнейшей работы по проектированию поковки необходимо найти массу поковки. На этой стадии работы можно ограничиться ее ориентировочным значением. Для этого пользуются
m
формулой коэффициента использования металла: КИ М = ——, откуда
m
![]() |
m,
m =---------- —,
о.ор. К
КИ.М.ср
где m^p - ориентировочная масса исходной заготовки;
КИМср = 0,75...0,8 - среднее значение коэффициента использования
![]() | ![]() | ![]() | |||
металла для поковок штампованных для деталей подкласса валов. Из исходных данных получаем
5.При расчете размеров диаметров поковки с допускаемыми отклонениями пользуются таблицами ГОСТ 7505-74. В случае пламенного нагрева поковки припуск на сторону увеличивают на 1 мм в связи с угаром и обезуглероживанием поверхностного слоя металла. Результаты расчета даны в табл. А1.5.
6.При расчете длин ступеней использованы те же таблицы ГОСТ 7505-74. Результаты расчета приведены в табл. А1.6.
7.Технические требования, предъявляемые к поковке (ГОСТ 7505-74): поковка повышенной точности (I класса);
Таблица А 1.5
Исходные данные
Диаметр ступени вала, мм | Шероховатость поверхности, мкм | Общий припуск на диаметр 2Побщ, мм | Диаметр ступени на поковке, мм | Категория размера | Допуск размера поковки штампованной, мм |
80 | Ra1,25 | 2(2,9+0,5)= 6,8 | 86,8 | Н | +1,3 -0,7 |
90 | Ra20 | 2(2,6+0,5)= 6,2 | 96,2 | Н | +1,3 -0,7 |
85 | Ra2,5 | 2(2,6+0,5)= 6,2 | 91,2 | Н | +1,3 -0,7 |
80 | Ra0,63 | 2(2,9+0,5)= 6,8 | 86,8 | Н | +1,3 -0,7 |
0 | Ra1,25 | 2(2,9+0,5)= 6,8 | 66,8 | Н | +1,3 -0,7 |
|
Результаты расчета
|
|
|
Примечание.
• Допуск размера 40 мм, отнесенного к категории l, уменьшен вдвое в связи с односторонним износом штампа;
• допускаемое смещение по разъему штампа 0,9 мм;
• допускаемый заусенец по периметру среза 1,7 мм;
• внешние штамповочные уклоны 7 ;
• допускаемое радиальное биение поверхностей 091,2 и 066,8 относительно поверхностей 086,8 не более 1 мм;
• радиус закругления внешних углов R = 4 мм;
• допуски на радиусы закруглений поковки + 2 мм;
• твердость поковки после термообработки HRC 21...26;
• поковку очистить от окалины.
• Остальные технические требования по ГОСТ 8479-70.
8. Расчет массы поковки проводят, суммируя массы ее элементарных частей:
т0.фак = Z Ш01ффак = 0,001 ‘Z ШП.М.Ш ,
где тПМ. - масса погонного метра поковки, кг, круглого сечения (определяется по диаметру элементарной части поковки с учетом половины положительного предельного отклонения его). Данные о массе погонного метра приведены в технологическом справочнике [12];
li - длина элементарной части поковки, мм.
Для нашего примера
т0факт = 0,001 • (46,5 • (40 + 60 + 60) + 56,8 • 126,4 + 51,6 • 120 + 27,6 + 80) = 23 кг.
9. Расчет коэффициента использования металла ведется по
формуле (А1.4):
19 4
КИМ = —^- = 0,843.
и.м 23 ?
Коэффициент используемого металла оказался выше среднего (см. п. 4). Это свидетельствует о правильном подходе к проектированию заготовки с учетом возможности экономии металла.
10. Стоимость поковок установлена прейскурантом 25-01. В
нашем случае стоимость 1 тонны поковок составляет 232 руб. Годовому объему выпуска 4500 шт. соответствует вторая группа серийности (доплаты за серийность нет). Для принятой штамповки I класса точности доплата составляет 5%. Доплата за термообработку штамповки составляет 22 руб., а за очистку - 6 руб. за тонну. Стоимость одной тонны поковок составит: С = 232-1,05+22+6=271,6 руб.
Стоимость одной заготовки (С1) составит
С1 = 0,001-С-т0 = 0,001-271,6-23 руб.
11. Чертеж поковки должен содержать все данные, необходимые для изготовления, контроля и приемки поковки, и выполняется в соответствии с требованиями стандартов ЕСКД. В основной надписи чертежа под наименованием детали пишут «Поковка штампованная».
Для выполнения чертежа поковки используют чертеж детали или его копию. Положение заготовки на чертеже должно соответствовать ее положению в процессе штамповки. Изображение детали на этом чертеже выполняется тонкими линиями, причем резьбы, отверстия, канавки, впадины, выточки, не выполняемые в поковке, исключаются или упрощаются.
При вычерчивании поковки учитывают все припуски на механическую обработку и кузнечные напуски (штамповочные уклоны, внутренние радиусы закруглений, перемычки отверстий и др.) с указанием их размеров. Простановку размеров поковки нужно производить только от баз, принятых для механической обработки (рис. А1.6).
Рис. А 1.6. Эскиз заготовки |
12.По результатам проектирования можно сделать некоторые выводы.
Во-первых, один из резервов экономии металла заключается в повышении класса точности поковки. Так, если в рассмотренном примере принять нормальную точность поковки (II класс) вместо принятой повышенной, то припуски на сторону будут больше на 0,8 мм и масса поковки в этом случае возрастет примерно на 1 кг. В нашем случае это составит более 4%. При крупносерийном производстве это дало бы значительное увеличение расхода металла.
Во-вторых, другим резервом экономии металла является использование индукционного нагрева исходного материала перед штамповкой. В этом случае расчетный припуск уменьшается на 1 мм. Это тоже может дать экономию металла около 5%.
В-третьих, операционные припуски можно определить расчетноаналитическим методом (см. §5) и просуммировать их для каждой поверхности, получив общий припуск на механическую обработку. В ряде случаев расчет по этому методу дает заготовку меньшей массы, а, следовательно, в этом методе заложена возможность экономии металла.
В-четвертых, большие резервы экономии металла заложены в технологических возможностях кузнечного производства. Следует иметь в виду, что способами получения заготовки, формы и размеры которой близки к форме и размерам детали, являются периодический прокат, поперечный прокат, ротационный обжим и др. Наилучший
результат дает ротационный обжим. Метод применяется для проката, как в холодном состоянии, так и с предварительным подогревом. Получаемые заготовки имеют малые погрешности размеров по диаметру (±0,15...±0,3 мм) и по длине (±1 мм), малую шероховатость (Ra=0,6 мкм), высокий коэффициент использования металла (0,85...0,95). Производительность операции обжатия примерно 50...100шт/ч. При использовании таких заготовок отпадает
необходимость черновой и получистовой обработки, а, следовательно, резко уменьшаются общие припуски на механическую обработку. У таких заготовок нет заусенца по периметру среза, нет больших уклонов на торцах и поэтому механическую обработку осуществить значительно проще. Все это положительно скажется на производительности и экономичности изготовления деталей.
Задача А1.3. Сконструировать исходную заготовку - поковку, штампованную для изготовления ступенчатого вала по вариантам, приведенным на рис. А1.4 и в табл. А1.1.
Исходные данные: Материал вала - сталь 40X. Твердость после термической обработки (улучшения) HRC 24...29. Тип производства - крупносерийное.
СПИСОК ЛИТЕРАТУРЫ
1. Гельфгат Ю.И. Сборник задач и упражнений по технологии машиностроения. - М: 1975.
2. Допуски и посадки / Под ред. В.Д. Мягкова. - М., 1978.
3. Справочник технолога машиностроителя / Под ред. А.Г. Косиловой, Р.К. Мещерякова и А.П. Малова. Изд. 4-е. - М., 1985.
4. Обработка металлов резанием / Под ред. Г.А. Монахова. Изд. 3-е. - М. 1974.
5. Косилова А.Г., Мещеряков Р.К., Калинин М.А. Точность
обработки, заготовки и припуски в машиностроении. - М., 1976.
6. Лавриненко М.З. Технология машиностроения и технологические основы автоматизации. - Киев, 1982.
7. Чернов Н.Н. Металлорежущие станки. Изд. 3-е. - М., 1978.
8. Горошкин А.К. Приспособления для металлорежущих станков. Изд. 7-е. - М., 1979.
9. Станочные приспособления / Под ред. Б.Н. Вардашкина и др. - М., 1984.
10. Общемашиностроительные нормативы режимов резания для технического нормирования работ на металлорежущих станках. 3-е изд. 1974-1978.
11. Общемашиностроительные нормативы времени вспомогательного,
на обслуживание рабочего места и подготовительно
заключительного для технического нормирования станочных работ. Серийное производство. Изд. 2-е. - М., 1974.
12. Данилевский В.В. Справочник молодого машиностроителя: Изд.
3-е. - М., 1973.
Дата добавления: 2021-04-07; просмотров: 829; Мы поможем в написании вашей работы! |
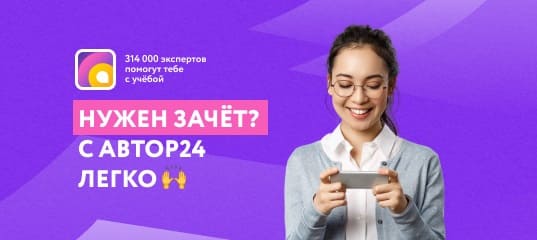
Мы поможем в написании ваших работ!