Характеристика КЦ-3 «Домбаровка»
Компрессорный цех № 3 «Домбаровка» (КЦ-3 «Домбаровка) предназначен для транспортировки газа из газопровода «Домбаровка – Оренбург» и его подачи в магистральные газопроводы «Оренбург – Новопсков», «Союз».
В состав КЦ-3 входит 5 газоперекачивающих агрегатов СТД-4000-2 производства завода «Дальэнергомаш» с приводом от электродвигателя с частотой вращения 3000 об/мин, мощностью 4 МВт и напряжением 6 кВ и нагнетателем Н-280-12-7 производительностью 13 млн. м3/сут с постоянными рабочими оборотами 8000 об/мин. Крутящий момент от двигателя передаётся к ЦБН через промежуточный редуктор, передаточное число редуктора составляет 2,66. ГПА установлены в общем здании компрессорного цеха.
Газ из магистрального газопровода «Домбаровка-Оренбург» поступает на 8 циклонных пылеуловителей производительностью 7 млн. м3/сут каждый, где очищается от жидких фракций и твердых частиц и направляется на вход ГПА.
Общие параметры КЦ-3 «Домбаровка» приведены в таблице 3.
Таблица 3 – Общие параметры КЦ-3 «Домбаровка»
Характеристика | Единица измерения | Величина |
Давление на входе КЦ, не более | кгс/см2 | 43,1 |
Давление на выходе КЦ, не более | кгс/см2 | 53 |
Температура газа на входе КЦ | 0С | -15 - +40 |
Температура газа на выходе с нагнетателя, не более | 0С | не более +90 |
Температура газа на выходе КЦ, не более | 0С | не более +45 |
Пропускная способность 1 пылеуловителя | млн. м3/сутки | 7 |
Анализ отечественной и зарубежной литературы
|
|
Анализ отечественной и зарубежной литературы выявил высокое внимание к проблеме повышения КПД газотурбинных установок и, в частности, к газоперекачивающим агрегатам с газотурбинным приводом, эксплуатируемых на компрессорных станциях по всему миру. Это объясняется тем, что колоссальное количество энергии выбрасываются в атмосферу с выхлопными газами в процессе работы ГТУ. Их температура может достигать 500°С и выше. Многие компрессорные станции нашли решение этой проблемы за счет применения ГТУ регенеративного цикла, где часть сбрасываемой в атмосферу энергии используется для дополнительного подогрева циклового воздуха после осевого компрессора. Таким образом, удалось более рационально использовать энергию продуктов сгорания ГТУ.
Схемы и типы существующих регенераторов ГТУ схожи по принципу действия, но могут отличаться друг по своей конструкции. Это зависит от начальных параметров источника тепла, стоимости оборудования и требуемого количества регенерируемой тепловой энергии. Также немаловажном фактом является достижение максимального КПД ГТУ.
Анализ существующих конструкций регенераторов, применяемых на ГТУ
|
|
В конструкциях ГТУ первоначально применялись регенераторы кожухотрубного типа, затем пластинчатого.
В первых образцах кожухотрубных регенераторов применялись конструктивные приемы, позволяющие решать характерные проблемы конструкции аппаратов и компоновки их в составе ГТУ. В каждом случае проблема выбора пространственной ориентации регенератора вертикальной (рисунок 1.1) или горизонтальной (рисунок 1.2) решается с учетом оптимальной компоновки газохода и воздуховодов с одновременной увязкой с элементами выхлопного газового тракта переходными патрубками и выхлопной трубой, с конструктивными элементами опорной рамой, системой подвески и опирания трубопроводов, а также с дополнительным оборудованием, например, таким как водяные утилизаторы теплоты.
Рисунок 1.1 – Регенератор ГТУ фирмы Броун-Бовери
Рисунок 1.2 – Регенератор газотурбинной установки ГТН-9 ЛМЗ
В некоторых случаях целесообразно направить воздух высокого давления в трубный пучок с целью разгрузки корпуса (рисунок 1.3) или, наоборот, направить выхлопные газы в трубки для облегчения их очистки (рисунок 1.4).
Рисунок 1.3 – Регенератор ГТУ танкера Auris
|
|
Рисунок 1.4 – Схема регенератора ГТУ фирмы Зульцер
С целью компенсации взаимных термических расширений корпуса и трубного пучка на корпусе размещают торообразные компенсаторы (рисунок 1.1) или применяют сальниковый компенсатор (рисунок 1.5), либо трубный пучок выполняется U-образным, что позволяет решить проблему термических перемещений (рисунок 1.6).
Рисунок 1.5 – Схема регенератора ГТУ фирмы Метрополитен-Виккерс
Рисунок 1.6 – Регенератор фирмы Роллс-Ройс
Для повышения тепловой эффективности регенератор может проектироваться с многократным перекрестным током, который производится с помощью внутренних перегородок (рисунок 1.1). Существуют также полностью противоточные регенераторы без внутренних перегородок с продольным течением теплоносителей (рисунок 1.3).
Для упрощения монтажа регенераторы иногда выполняют в виде единого крупного блока. Иногда оказывается целесообразным разделить регенератор на секции для облегчения его изготовления и транспортировки (рисунок 1.7).
Рисунок 1.7 – Четырехсекционный регенератор ГТУ фирмы Броун-Бовери
Рисунок 1.8 – Трубка с двухсторонним оребрением из гофрированной ленты фирмы Эшер-Висс
|
|
В некоторых конструкциях регенераторов трубки собраны в мини-пучки с общим подводом теплоносителя, что позволяет уменьшить размеры трубной доски (рисунок 1.9).
Рисунок 1.9 – Регенератор фирмы Роллс-Ройс с теплообменной поверхностью, собранной из мини-пучков:
а – общий вид, б – трубный пучок
Конструкция регенераторов может предусматривать традиционный для кожухотрубных теплообменников боковой подвод и отвод теплоносителей с использованием сегментных внутренних перегородок, как это показано на рисунке 1.1, или, напротив, осевой подвод и отвод теплоносителей для придания симметричности силовым и термическим нагрузкам (рисунок 1.2). Иногда одну из трубных досок регенератора выполняют не плоской, а конической для увеличения ее прочности, что позволяет уменьшить также ее толщину и массу (рисунок 1.4).
Жесткость трубного пучка и вибростойкость трубок регенераторов повышают с помощью дистанционирующих элементов: гладкой трубки, одетой поверх оребренной трубки или проволоки, вплетенной между трубками (рисунок 1.10), а также стяжного хомута.
Рисунок 1.10 – Трубный пучок регенератора ГТУ фирмы English Electric с дистанционирующей проволочной оплеткой
Для повышения компактности трубного пучка часто регенераторы изготавливаются с минимальными шагами между трубками и с трубками минимального диаметра.
Трубки в трубных досках закрепляются с помощью вальцовки, приварки, пайки, а также уплотнительными втулками
Перечисленное не исчерпывает, естественно, все множество приемов и конструктивных идей, заложенных в конструкции регенераторов.
Трубчатые регенераторы при относительной конструктивно-технологической простоте проявили два своих самых существенных недостатка: значительная масса (до 198 тонн) и значительные габариты (длина трубок до 7 м), поэтому в тех случаях, когда эти параметры были критичными, например, при необходимости транспортировки в отдаленные районы, стали применять регенераторы другого типа – пластинчатые.
Первоначально применялись пластинчатые регенераторы двух типов:
- из плоских листов с прикрепленными к ним профилированными пластинами (рисунок 1.11);
- из штампованных профильных листов с выдавленными на них канавками
В обоих случаях, когда листы собираются в пакеты, между ними образуются две системы каналов: по одной из которых движется воздух, а по другой газы. В первом варианте расстояние между листами и размеры каналов обеспечиваются распоркой в виде плоской проволочной пружины, а во втором за счет опирания друг на друга выштамповок соседних листов.
Рисунок 1.11 – Пластинчатый регенератор из плоских листов с приварным оребрением фирмы Air Preheater:
а – внешний вид регенератора, б – элементы пластинчатой поверхности теплообмена
В дальнейшем практически все пластинчатые регенераторы компоновались из профильных листов. Это связано с их большей простотой, а также с тем, что на них без особых проблем можно сформировать каналы таким образом, чтобы обеспечить противоточное движение воздуха и газов в пакете, а также тем обстоятельством, что на поверхности теплообмена могут быть выполнены дополнительные интенсификаторы в виде участков с мелким гофрированием без дополнительного усложнения технологии изготовления профильных листов. Регенераторы таких конструкций имеют меньшую массу и габариты по сравнению с трубчатыми.
Для пластинчатых регенераторов характерен ряд недостатков. Достаточно сложна технология их изготовления – необходимо формовать крупные металлические листы с большим количеством профильных канавок и гофров, а затем при сборке пакетов обеспечивать высокое качество (герметичность) большого числа сварных швов. Такие требования можно реализовать только при использовании высокопластичного, и не склонного к трещинообразованию при сварке, материала (в отечественной практике это весьма дорогостоящая нержавеющая сталь – 1Х18Н9Т). Профильные листы подвергаются воздействию перепада давления между сжатым воздухом и газами, а также термических напряжений (особенно при теплосменах), что ведет к их короблениям и при теплосменах к образованию трещин, т. е. потере герметичности воздушного тракта регенератора. Простые и надежные методы ремонта пластинчатых регенераторов так и не были выработаны, при этом отключение неисправных элементов, как это делается в трубчатых теплообменниках отглушением поврежденных труб, невозможно. Качественная чистка каналов между пластинами также практически невозможна. Тем не менее, на основе профильных листов был сконструирован ряд пластинчатых регенераторов. Примеры их конструкций показаны на рисунке 1.12.
Рисунок 1.12 – Пластинчатый регенератор турбины ГТК-5 НЗЛ
На рисунок 1.13 представлена схема трубчатого регенератора фирмы GEA (ФРГ), послужившего прототипом для многих аналогичных устройств. Рассмотрим ряд характерных черт этой конструкции, с которыми связаны ее достоинства и недостатки (как известно, наши недостатки – это продолжения наших достоинств).
Рисунок 1.13 – Схема трубчатого регенератора фирмы GEA.
1, 2 – вход и выход газов; 3, 4 – вход и выход воздуха; 5, 6 – верхняя и нижняя трубные доски; 7 – внутренние трубные перегородки; 8 – корпус; 9 – линзовый компенсатор
Рядом зарубежных фирм и отечественных предприятий были созданы трубчатые регенераторы по близким к рассмотренной конструктивным схемам.
Заключение
В данной дипломной работе выполнена разработка конструкции трубчатого регенератора тепла уходящих газов ГПА ГТК-10И. По данной теме произведены тепловой и гидравлический расчёты регенератора, расчёт гидравлических потерь в регенераторе, расчёт гидравлических потерь в подводящих и отводящих воздухопроводах, расчёт массы регенератора
В аналитическом разделе была описана общая характеристика компрессорной станции «Оренбургская», состав основного технологического оборудования компрессорного цеха «Союз», проведен анализ классификации и типов конструкций регенераторов ГТУ, их применения как в России, так и за рубежом.
В проектно-технологическом разделе произведены тепловой и гидравлический расчёты регенератора, расчёт гидравлических потерь в регенераторе, расчёт гидравлических потерь в подводящих и отводящих воздухопроводах, расчёт массы регенератора
В разделе по экологичности и безопасности, произведен анализ вредных и опасных производственных факторов. Рассмотрены меры безопасности при эксплуатации компрессорной станции и средства обнаружения утечек газа и пожаров, а также системы автоматического пожаротушения. Произведен расчет и оценка количества вредных веществ, выделяющихся в атмосферу при эксплуатации ГПА.
Разработка конструкции трубчатого регенератора тепла уходящих газов ГПА ГТК-10И, позволит предприятию:
- сократить затраты на собственные нужды (топливный газ);
- повысить показатели при использовании энергии.
Дата добавления: 2021-07-19; просмотров: 201; Мы поможем в написании вашей работы! |
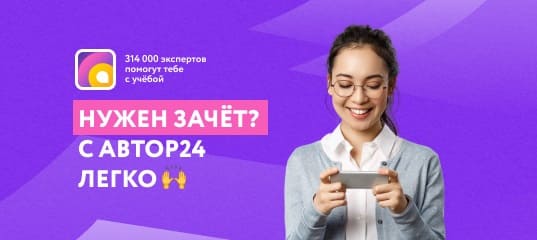
Мы поможем в написании ваших работ!