Ремонт головок блока цилиндров.
Цели работы.
1. Изучить основные дефекты головок цилиндров.
2. Ознакомиться со способами ремонта и устранения дефектов.
3. Заполнить технологическую карту ремонта ГБЦ.
Основные дефекты ГБЦ
Основными дефектами головки цилиндров являются трещины, выработки, риски и раковины на седлах выпускных и впускных клапанов, нарушение уплотнения стакана форсунки, износ отверстий в направляющих втулках клапанов, ослабление посадки направляющих втулок в головке цилиндров, трещины на поверхности прилегания головки к блоку цилиндров и коробление этой поверхности, а также погнутость и ослабление посадки шпилек на головке цилиндров или повреждение резьбы на шпильках.
Рис.1 – Схема изнашивающихся соединений ГРМ
1- Седло-фаска клапана; 2 – стержень клапана - направляющая втулка; 3- опорная поверхность коромысла – торец клапана; 4 – втулка коромысла – ось; 5 – регулировочный винт – штанга;
6 – толкатель – блок;7 – штанга – толкатель; 8 – толкатель – кулачок.
Износ соединения седло — фаска клапанного механизма
(рис. 1) приводит к уменьшению степени сжатия и
коэффициента наполнения цилиндра. При снижении степени сжатия ухудшаются пусковые качества дизеля, уменьшается наполнение цилиндров, что при неизменной цикловой подаче топлива вызывает его неполное сгорание и падение мощности двигателя.
Предельный износ деталей соединения характеризуется экономическими критериями: падением мощности двигателя, ухудшением топливной экономичности и повышенным расходом масла на угар. Их определение связано со стендовыми испытаниями двигателя, поэтому в практике ремонта используют корреляционную зависимость между этими критериями и глубиной утопания тарелки клапана относительно поверхности головки блока цилиндров. На основании экспериментальных данных и опыта эксплуатации для различных двигателей установлены допустимые глубины утопания тарелки клапана относительно поверхности головки блока, которые измеряют глубиномером с ценой деления 0,05 мм
|
|
Таблица 1 – Допустимая глубина утопания тарелки клапана
Таблица 2 - Основные регулировочные данные и показатели газораспределительного механизма и головки блока цилиндров двигателя МТЗ-82
Стержень клапана изнашивается неравномерно (больше — у краев и меньше — в середине), принимая бочкообразную форму, что характерно для впускного и выпускного клапанов. Это объясняется соответствующей кинематикой и динамикой механизма привода клапана и существованием бокового усилия, приводящего к некоторому перекосу клапана во втулке. Износ стержня клапана определяют микрометрами, а отверстия во втулке — индикаторными нутромерами. Износостойкость соединения стержень клапана — втулка влияет на долговечность клапанной группы. Износ стержня обусловливает точность посадки клапана в гнездо. Биение его рабочей фаски относительно оси
|
|
стержня приводит к неплотной посадке клапана, нарушению герметичности
пары и уменьшению наполнения цилиндра свежим зарядом.
Ремонт головок блока цилиндров.
Наличие трещин устанавливают внешним осмотром, а также при испытании головок цилиндров на герметичность водой под давлением 0,4 МПа (4 кгс/см2). Головку цилиндров заменяют при наличии трещин, проходящих через отверстия под направляющие втулки клапанов, отверстия под стаканы форсунок и гнезда под седла клапанов, и трещин на стенках рубашки охлаждения в местах, недоступных для ремонта. Трещины головок блока цилиндров заваривают без предварительного подогрева головок дуговой сваркой с помощью электрода ЦЧ-4, самозащитной проволоки ПАНЧ-11, либо заделывают фигурными вставками.
Неплоскостность (коробление) привалочной поверхности контролируют поверочной линейкой и щупом . Если неплоскостность превышает допустимое значение, а высота головки соответствует допустимому значению, то привалочную поверхность шлифуют.
|
|
Рис 1. – Проверка плоскости ГБЦ
1-поверочная линейка, 2 – головка цилиндров, 3 – щуп
При износе или срыве резьбы в отверстиях головки цилиндров нарезают резьбу ремонтного размера или ставят ввертыши.
У гнезд клапанов, износ которых меньше допустимого, фрезеруют
или зенкуют фаски. Перед обработкой выпрессовывают изношенные втулки стержня клапана, зачищают посадочное место и запрессовывают втулки
ремонтного размера с уменьшенным внутренним диаметром. Перед запрессовкой головку цилиндров нагревают до температуры 90 °С.
Изношенные рабочие фаски тарелок клапанов шлифуют до выведения следов износа на специальных станках СШК-3 или 2414. Шероховатость фаски после обработки не более ft, = 0,63 мкм, а биение относительно оси поверхности
стержня не более 0,03 мм.
Изношенный торец клапана шлифуют до выведения следов износа
на тех же станках с помощью приспособления, прилагаемого к
станку, и снимают фаску 1x45°. Неперпендикулярность торца к боковой
поверхности стержня не более 0,05 мм.
Рис. 2 – Шлифование рабочей поверхности фаски клапана
|
|
Притирка клапанов к седлам.
Перед сборкой головки цилиндров клапанную пару притирают на станках ОПР-1841А с помощью пасты различной зернистости. Притиркой достигается необходимая герметичность клапанной пары. Рекомендуются следующие
пасты: состав I (карбид бора М40 — 10 %, микрокорунд
М20 —90%), состав II (электрокорунд зернистый — 87 %, парафин
— 13 %). Состав готовят на дизельном масле. Притирают до получения
кольцевой матовой поверхности на фаске седла.
По окончании притирки клапанные гнезда и клапаны промывают
керосином до полного удаления абразивной притирочной пасты и проверяют качество обработки. Собирают клапанную группу и заливают керосин
в газораспределительные каналы. Клапанную пару собирают так. Клапаны устанавливают в гнезда, поворачивают головку нижней плитой к столу и надевают пружины. С помощью приспособления сжимают пружины и устанавливают тарелки клапанных пружин с сухарями. Последние должны
плотно сидеть в тарелке и выступать на 0,5...2,0 мм над ее поверхностью.
Зазор между ними не менее 0,5 мм. У хорошо притертых клапанов не должно быть подтекания керосина из-под их тарелок в течение 3 мин. Герметичность клапанных пар можно проверить с помощью специальных пневматических
приспособлений.
Изношенные направляющие втулки клапанов выпрессовывают, запрессовывают новые и обрабатывают их до номинального размера разверткой.
Контрольные вопросы и задания.
1. Перечислите основные дефекты ГБЦ двигателей.
2. Какие последствия в результате износа деталей ГБЦ?
3. На основе теоретического материала заполните таблицу.
Название дефекта | Способы устранения |
Дата добавления: 2021-07-19; просмотров: 83; Мы поможем в написании вашей работы! |
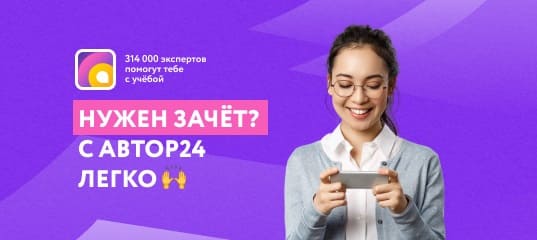
Мы поможем в написании ваших работ!