Сварочные контуры стыковых машин
Элементы контура (рис. 4.2) подводят ток от трансформатора к сваривае- мым заготовкам: гибкие шины 1 и 4, жесткие колодки 2 и 3, а также сварочные электроды – контактные губки 5. Все эти детали, так же как у машин точечной и шовной сварки, изготовляют из высокоэлектропроводных металлов – меди и бронзы. В мощных машинах элементы сварочного контура и их контакты охлаждаются проточной водой. Контактные губки стыковых машин имеют призматическую форму и кроме подвода тока выполняют еще функцию крепления свариваемых деталей. Поэтому они обычно имеют угловую или полукруглую (по окружности свариваемого стержня или трубы) канавку. При сварке деталей другой формы (полоса, уголок и пр.) применяют губки с соответствующей формой контактной поверхности. Длину губок выбирают такой, чтобы обеспечить соосность деталей и предотвратить их проскальзывание при осадке. При сварке стержней она составляет 3–4 их диаметра, а при сварке полос – не менее 10 толщин полосы. Поскольку площадь токоподвода в губках существенно больше, чем у электродов точечных машин, то допустимо их изготовление из бронз с относительно низкой электропроводностью, но с высокой твердостью, например марок БрХ или БрНБТ. Прижимные губки, входящие в состав зажимных механизмов, как правило, ток не проводят, поэтому изготавливаются из более дешевых материа- лов, например из закаленной стали 40Х. Они также могут иметь канавку по форме свариваемых заготовок, но чаще изготавливаются плоскими.
|
|
Механизмы зажатия
Зажимные устройства должны обеспечивать точную установку заготовок друг относительно друга и подвод к ним сварочного тока. Усилие зажатия Fзаж должно предупреждать проскальзывание заготовок в губках при самом боль- шом усилии сжатия. Поэтому с учетом коэффициента трения в паре «сталь – медь» Fзаж = (3–5) Fос. При сварке коротких деталей их проскальзывание можно предотвратить установкой упоров, тогда усилие зажатия можно снизить. Кон- струкции зажимных механизмов весьма разнообразны и определяются формой и размером свариваемых заготовок, необходимым усилием зажатия и характе- ром производства (рис. 4.3). В машинах малой мощности используются эксцен- триковые, рычажные и винтовые механизмы с ручным приводом, в более мощ- ных машинах – пневматические, гидравлические и электромеханические.
Эксцентриковый зажим обеспечивает небольшое усилие (не более 1 кН), но приводимый в действие вручную отличается высоким быстродействием Винтовой механизм при ручном приводе создает усилие зажатия до 40 кН. После установки на контактной губке заготовки рычаг поворачивают вокруг оси и накидывают на него замок . После этого винтовым домкратом, вращая его с помощью рукоятки, создают необходимое усилие, передаваемое прижимной губкой к заготовке. Для легкого откидывания рычага в исходное положение после сварки используется возвратная пружина.
|
|
Пневматический механизм отличается высокой скоростью действия и проектируется на усилия до 100 кН. Здесь пневмоцилиндр своим штоком поворачивает рычаг, который воздействует на прижимную губку и свариваемую заготовку. Усилие зажатия зависит от диаметра пневмоцилиндра и соотношения плеч рычага и настраивается изменением давления воздуха. Если по расчету диаметр пневмоцилиндра получается неприемлемо большим, то ис- пользуют сдвоенный пневмоцилиндр.
Гидравлический привод обеспечивает еще более значительное усилие за- жатия (до 5000 кН), но отличается большой сложностью, поскольку требует установки специальной масляной станции с насосом, баком и управляющей гидравлической аппаратурой. Поэтому обычно для экономии гидравлический 112 привод зажатия проектируется только заодно с гидравлическим приводом сжатия (оплавления и осадки). Есть, правда, возможность проектирования гидравлического привода с более дешевым преобразователем давления.
Дата добавления: 2021-07-19; просмотров: 48; Мы поможем в написании вашей работы! |
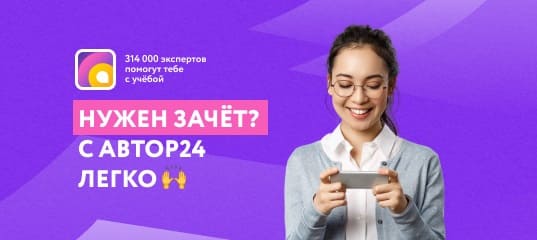
Мы поможем в написании ваших работ!