ОБЕСПЕЧЕНИЕ КАЧЕСТВА СОЕДИНЕНИЙ В УСЛОВИЯХ ПРОИЗВОДСТВА
ЛАБОРАТОРНАЯ РАБОТА № 7
ПО ДИСЦИПЛИНЕ: «СВАРКА И ПАЙКА НЕМЕТАЛЛИЧЕСКИХ МАТЕРИАЛОВ»
Тема: «ОПРЕДЕЛЕНИЕ ДЕФЕКТОВ СВАРНЫХ СОЕДИНЕНИЙ ИЗ ПЛАСТМАСС, ВОЗМОЖНЫХ ПРИЧИН ИХ ВОЗНИКНОВЕНИЯ И СПОСОБОВ ПРЕДУПРЕЖДЕНИЯ»
Цель работы: научиться определять виды дефектов пи внешнем осмотре и устанавливать
возможные причины их возникновения.
Методическое обеспечение:
1. Методические указания по выполнению лабораторной работы.
Методические указания по выполнению лабораторной работы:
Дефекты сварных соединений подразделяются на
-наружные, выявляемые поверхностным осмотром, и
внутренние, обнаруживаемые только специальными методами контроля.
Основными дефектами в сварных швах термопластов являются
1. несоответствие шва требуемым геометрическим размерам,
2. подрезы,
3. трещины,
4. поры,
5. непровары,
6. усадочные раковины
7. участки материала, подвергнутые термоокислительиой деструкции
Несоответствие шва требуемым геометрическим размерам является в основном результатом нарушения сварщиком технических требований на размеры сварного шва.
При уменьшении размеров шва снижаются прочностные характеристики соединения; увеличение этих размеров экономически нерационально.
Подрезы — узкие, продольные углубления, образующиеся по краям шва в основном материале, максимальная глубина которых обычно составляет 1—2 мм. Трещины — наиболее опасный вид наружных и внутренних дефектов шва. Трещины в швах трудно обнаружить, так как они могут быть тонкими и находиться внутри шва.
|
|
Основная причина образования пор при сварке нагретым инструментом — длительное присутствие на воздухе оплавленных поверхностей перед их соединением и недостаточное давление осадки, неспособное выдавить поры на поверхность стыка.
Непровары — самые распространенные и опасные дефекты сварных швов, ослабляющие прочность сварного соединения. Опасность непроваров заключается в том, что по наружному виду шва нельзя установить этот дефект, так как он может находиться в любом месте шва.
Причины непровара —
1. некачественная сборка и неправильная разделка кромок;
2. нарушение технологического режима сварки (малое давление и недостаточная длительность осадки);
3. неудовлетворительная очистка присадочного материала и сварочных кромок от грязи, масла, окисленной пленки.
Непроваренные участки целиком вырезают и заваривают.
Усадочные раковины вызываются усадочными напряжениями, возникающими вследствие недостаточного давления, малой выдержки под давлением осадки и неравномерного охлаждения шва при его остывании.
|
|
Наиболее опасным дефектом сварного соединения термопластов является наличие в зоне шва участка материала, подвергнутого термоокислительной деструкции вследствие завышенной температуры сварки.
РАЗРУШАЮЩИЕ МЕТОДЫ КОНТРОЛЯ
Разрушающими методами контроля качества сварных соединений определяется механическая прочность при растяжении, сдвиге, равномерном и неравномерном отрыве, отслаивании, напряженном и ударном изгибе.
В соответствии с ГОСТ 16971—71 в качестве разрушающих методов контроля качества швов сварных применяются
1. механические испытания иа растяжение,
2. напряженный и
3. ударный изгиб.
Если изделия, выполненные методом сварки, должны эксплуатироваться в условиях агрессивных сред, швы сварных соединений необходимо выдерживать в этих средах, а затем подвергать испытаниям, при этом для испытаний отбирают не менее 20 образцов, половину из которых помещают в среду.
НЕРАЗРУШАЮЩИЕ МЕТОДЫ КОНТРОЛЯ
Для контроля качества сварных и клеевых соединений изделий из пластмасс могут применяться следующие методы неразрушающего контроли:
|
|
1.наружный осмотр и обмер
2. испытания на герметичность,
3. рентгенографический контроль,
4. ультразвуковая дефектоскопия,
5. капиллярные и другие методы контроля.
Эффективность наружного осмотра и обмера основана на том, что геометрические характеристики и внешний вид соединения связаны с технологическими параметрами процесса изготовления соединения.
Например, форма, размеры и внешний вид наплывов при стыковой сварке нагретым инструментом зависят от времени и температуры оплавления, а также давления осадки.
Поэтому
1. наличие разности высот валиков указывает на различную глубину проплавления двух сваренных изделий;
2. неоднородности валика по периметру шва — на неравномерность нагрева;
3. сдвига поверхностей — на недостаточную центровку;
4. пористый валик свидетельствует о перегреве.
В качественном сварном соединении, полученном сваркой нагретым инструментом, наплывы должны быть с обеих сторон круглыми, равномерными и одинаковыми, не должны превышать установленных размеров, впадина между ними должна быть видимой, скругленной формы, кроме того наплывы не должны иметь разрывов и других дефектов.
|
|
При наружном осмотре выявляются трещины, непровары, подрезы основного материала, смещение кромок, наружные газовые поры, неправильность геометрической формы сварного шва, несоответствие размеров сварного шва, а также недопустимые поверхностные дефекты, возникающие в результате механических повреждений (например, царапины, проколы).
Швы сварных соединений следует осматривать при хорошем освещении по возможности с обеих сторон по всей протяженности с применением увеличительных стекол с фокусным расстоянием 125—12,5 мм и увеличением в 2—20 раз. Чаще всего применяют складные обзорные лупы ЛПК-470 и ЛПК-471 двукратного увеличения.
Проверка размеров включает в себя измерение линейных и угловых размеров изделий, а также измерение линейных размеров сварочного грата. Линейные размеры изделий, указанные в спецификации, относятся к температуре + 20 °С, поэтому, если измерение производится при другой температуре, учитывается тепловое расширение материала. Измерение линейных размеров изделий, сварного шва и выявленных дефектов производится с точностью до ± 0,01 мм с помощью специальных приспособлений: измерительных линеек, циркулей, лент и др.
Испытания на герметичность проводят следующими способами:
1. обдувом,
2. химическими индикаторами,
3. воздушным давлением,
4. гидравлическим давлением,
5. наливом воды.
Способ испытаний выбирают в зависимости от конструкции изделия, его габаритных размеров и условий эксплуатации. Контроль герметичности производится после внешнего осмотра и очистки изделия от загрязнений.
При испытании обдувом струя сжатого воздуха должна быть направлена перпендикулярно к поверхности шва. Сжатый воздух под давлением до 250 «Па подают по гибкому шлангу с наконечником, причем расстояние между наконечником шланга и швом сварного соединения должно быть не более 50 мм. До обдува или одновременно с обдувом противоположную сторону шва смачивают мыльным раствором. Не герметичность шва сварного соединения определяется по появлению мыльных пузырей на смоченной раствором стороне. После испытания раствор должен быть смыт водой.
Сварные изделия с замкнутым объемом испытываются химическими индикаторами.На сварной шов накладывают бумажную ленту, пропитанную 5 %-ным водным раствором азотнокислой ртути или спирто-водным раствором фенолфталеина. После укладки и закрепления ленты на шве внутрь испытуемого изделия вводят аммиак в количестве 1 % от общего объема воздуха в изделии при давлении окружающей среды, а затем сжатым воздухом создают требуемое давление. Места не герметичности шва сварного соединения устанавливают по черным пятнам на бумажной ленте. Достоинством данного метода является высокая чувствительность и надежность контроля, а также возможность получения документации о качестве шва.
Испытание воздушным давлениемприменяется для контроля герметичности швов сварных соединений малогабаритных изделий, при этом изделие герметизируют газопроводными заглушками и погружают в воду таким образом, чтобы над изделием был слой воды 20—40 мм. Места не герметичности устанавливаются по появлению пузырьков воздуха в воде или мыльных пузырей на смоченной мыльным раствором поверхности шва. Этот способ контроля широко применяется при массовом производстве однотипных изделий.
Испытание гидравлическим давлением проводят с целью определения состояния всей сварной конструкции (различных сосудов и трубопроводов, работающих под давлением). Испытание начинают под давлением, равным рабочему. Если дефекты не обнаружены, давление увеличивают до испытательного, устанавливаемого документацией на проведение испытаний данной конструкции.
Испытания наливом воды проводят при температуре не ниже 5 °С. Изделие заполняют водой. Места негерметичности шва сварного соединения устанавливают по появлению течи.
При контроле гелиевым тече искателемв контролируемую емкость подают под небольшим избыточным давлением смесь воздуха с гелием.
Рентгенографический контроль относится к радиационным методам контроля — наиболее распространенным методам дефектоскопии
К преимуществам рентгенографического контроля относятся
1. высокая чувствительность при обнаружении мелких дефектов,
2. объективность получаемых результатов,
3. возможность определения линейных размеров и глубины залегания дефектов.
К недостаткам методе относятся
1. низкая производительность контроля, связанная с потерей времени на фото обработку,
2. высокая стоимость, связанная с расходом пленки, и необходимость в обеспечении радиационной защиты.
Для контроля сварных соединений из пластмасс наиболее применимыми методами ультразвуковой дефектоскопии являются теневой метод и импульсный эхо-метод .
Капиллярные методы дефектоскопии основаны на способности жидкости проникать в поверхностные дефектытипы поверхностных трещин, расслоений и течей в сварных соединениях пластмассовых изделий .
Электроискровой метод контроля основан на электроизоляционных свойствах пластмасс, относящихся к материалам с высокими диэлектрическими показателями. Если поместить изделие из пластмассы в пространство между электродами, к которым приложена большая разность потенциалов (15—20 кВ), то в области-дефекта в сварном соединении (непровар, трещина, пора и др.) проскакивает искра.
ОБЕСПЕЧЕНИЕ КАЧЕСТВА СОЕДИНЕНИЙ В УСЛОВИЯХ ПРОИЗВОДСТВА
Требуемое качество соединений необходимо обеспечить комплексом мероприятий, проводимых на различных стадиях:
до начала изготовления соединения — предупредительный контроль,
во время изготовления — технологический контроль
после изготовления — приемочный контроль.
Объем работы, выполняемый для обеспечения качества, зависит от требований к надежности соединений
Предупредительный контроль предусматривает контроль соответствия соединяемых изделий и вспомогательных материалов техническим требованиям нормативной документации, контроль размеров соединяемых изделий, качества подготовки соединяемых поверхностей, технического состояния применяемых инструментов и оборудования, квалификации рабочего персонала, а также контроль технологической подготовленности производства.
Технологический контроль предусматривает постадийный контроль правильности технологических параметров сварки и склеивания, влияющих на качество соединения. При этом контролируются температура сварки и склеивания, давление при нагреве свариваемых поверхностей и при охлаждении сварного шва, давление при формировании клеевой прослойки, время нагрева и охлаждения при сварке, время отверждения клеевой прослойки и другие параметры, указанные в технологической документации на производство работ по сварке и склеиванию.
Приемочный контроль предусматривает контроль качества швов соединений неразрушающими и разрушающими методами, на основе результатов которых производится отбраковка соединений. С учетом экономического фактора в производственных условиях наиболее целесообразно применение неразрушающих методов контроля, проводимого с учетом требований нормативно-технической документации на изготовление изделий и конструкций. Результаты контроля считают удовлетворительными, если установленные при контроле показатели не выходят за пределы, регламентированные данной нормативно-технической документацией.
Контрольные вопросы:
1. Назвать дефекты возникающие при сварке пластмасс.
2. Проанализировать причины их возникновения.
3. Предложить способы их предупреждения.
Дата добавления: 2021-07-19; просмотров: 147; Мы поможем в написании вашей работы! |
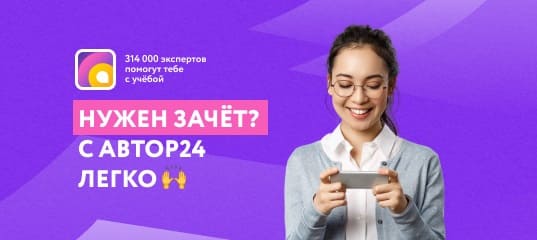
Мы поможем в написании ваших работ!