Основные теоретические сведения
1. Определение числа пролетов
Число пролетов уточняют на основе наиболее рациональной специализации располагаемых в них сборочно-сварочных работ, планировки оборудования, характеристики программы годового выпуска сварных изделий для различных типов серийного производства (по материалам норм технологического проектирования).
и Типовая схема компоновки цеха с продольным направлением производственного потока. В этой схеме процессы как узловой, так и общей сборки и сварки каждого изделия расположены в одних тех же продольных пролетах, специализация осуществляется по производству отдельных типов заданных для изготовления изделий.
Б. Типовая схема компоновки цеха со смешанным направлением производственного потока. В рассматриваемой планировке сборочно-сварочных отделений поперечный пролет специализирован по выполнению общей сборки и сварки изготовляемого изделия, а продольные пролеты отделения узловой сварки и сборки специализированы по производству отдельных видов сборочных единиц того же изделия.
Необходимое число пролетов определяется:
hпр = hпоз /Rпоз, (1)
где Rпоз – среднее число позиций процесса общей сборки и сварки (в пределах 1-2); hпоз – предусматриваемое число позиций процесса общей сборки и сварки.
В. Типовая схема компоновки цеха с продольно-поперечным направлением производственного потока. Специализация осуществляется по производству отдельных типов заданных для изготовления изделий, число пролетов зависит от количественного соотношения заданных к производству изделий различных типов. Схему применяют для единичного и мелкосерийного производства крупных сложных узлов.
|
|
Г. Типовая схема с волновым расположением производственного потока, как правило, включает по одному пролету в каждом отделении цеха. Схему применяют для единичного и серийного производства сложных узлов.
Д. Типовая схема с петлевым направлением производственного потока. По этой схеме на каждое отделение отводят один-два пролета. Схема пригодна для серийного и массового производства однотипных несложных изделий с применением горизонтально-замкнутых конвейеров.
Таблица 1 Размеры пролетов в сборочно-сварочных цехах
2. Определение ширины пролета
Ширину каждого пролета, принятую в компоновочной схеме, уточняют путем соотношения проверочных эскизов планировки рабочих мест в пролете и последующих подсчетов суммы размеров ширины рабочих мест, проходов и проездов между ними. При этом планировку оборудования, сборочно-сварочных рабочих мест и размещаемых в непосредственной близости к последним складочных мест для поступающих в сборку деталей и сборочных единиц выполняют рядами, располагаемыми вдоль пролета.
|
|
В практике проектирования чаще применяются четыре варианта расположения в пролетах линий рабочих мест с обслуживающими их проездами (рис. 1, а). В каждом пролете с возрастанием количества линий рабочих мест увеличивается его требуемая ширина bпри изменяется использование площади пролета. В зависимости отпринятого количества линий рабочих мест использование площади составляет (в %):
I................. (bл : bпр) 100 ≈ 50;
II................. (bл : bпр) 100 ≈ 67;
III................. (bл : bпр) 100 ≈ 60;
IV................. (bл : bпр) 100 ≈ 67.
а ) б)
Рисунок 1. а – варианты расположения рабочих мест и обслуживания проездов
Рисунок 1. Расположение рабочих мест: – варианты расположения рабочих мест и обслуживания проездов пролетах цеха; б – схема расположения рабочих мест для подсчетов требуемой ширины пролета с размещением складочных мест
Значение ширины пролета bпр может быть определено следующим образом:
• для варианта, показанного на Рисунок 1, а:
|
|
(bпр)min = 2(b1 + bм); | (2) | |||
• для варианта, показанного на Рисунок 1, б: |
| |||
(bпр)max = 2(b1 + b2 +bм + bскл) + bп. | (3) | |||
Числовые значения величин, входящих в приведенные выше выражения, в соответствии с требованиями норм технологического проектирования и по данным практики принимают в следующих пределах:
b1– расстояние от тыльной стороны рабочего места до оси продольного ряда колонн, обычно не менее 1 м;
b2– расстояние между рабочим местом или ограждением сварочной кабины и складочным местом для прибывающих деталей;
bм– ширина рабочего места, обусловленная шириной сборочно-сварочного устройства;
bскл– ширина складочного места, зависящая от размеров складываемых у рабочих мест деталей и сборочных единиц;
bп– ширина проезда между двумя линиями рабочих мест, расположенными в одном пролете, принимают в пределах 3–4 м.
3. Определение длины пролетов
Длину пролетов в пределах каждого отделения проектируемого сборочно-сварочного цеха устанавливают на основе проектирования планировки оборудования и рабочих мест на плане каждого пролета.
При этом шаг колонн (6×12, 12×18, 12×24 м) и ширина пролетов представляют собой основные параметры сетки колонн, служащей канвой для составления технологического плана цеха.
|
|
Планировка размещения оборудования выполняется в следующей последовательности: 1-нанесение магистральных проездов; 2-размещение основного оборудования;3-размещение вспомогательного оборудования.
Методические и нормативные материалы по проектированию сварочных и машиностроительных цехов содержат рекомендуемые обязательные размеры ширины проездов и проходов; расстояний между оборудованием; размеры рабочих зон производственных рабочих, обеспечивающих удобные и безопасные условия работы (табл. 2, 3). Примеры размещения оборудования сварочных цехов представлены на Рисунок 2-8. Поиск оптимальных вариантов планировки оборудования требует анализа большого количества вариантов.
Рисунок 2. Размещение установки электрошлаковой сварки: 1 – роликовый стенд механизированный; 2 – направляющие рельсы; 3 – установочная тележка; 4 – колонна с реечным устройством; 5 – автомат сварочный; 6 – сварочный узел; 7 – место складирования
Рисунок 3. Размещение стендов, кантователей для сварки крупногабаритных узлов: 1 – двухстоечный кантователь; 2 – стенд для сборки; 3 – место складирования; 4 – универсальная площадка для сварщика с подвижной стрелой; 5 – полукозловой кран
Рисунок 4. Размещение оборудования для электронно-лучевой сварки: 1 – моечно-сушильный агрегат; 2 – установка для размагничивания; 3 – пресс для запрессовки; 4 – монорельс; 5 – установка для электронно-лучевой сварки; 6 – подвесной грузонесущий конвейер; 7 – ограждающие элементы помещения для электронно-лучевой сварки; 8 – место складирования; 9, 10, 11 – шкафы управления и источники питания
Рисунок 5. Размещение установки велосипедной тележки для автоматической сварки продольных и кольцевых швов цилиндрических изделий: 1 – направляющий рельс; 2 – велосипедная тележка с балконом; 3 – сварочный автомат; 4 – сварочный узел; 5 – стенд роликовый механизированный; 6 – место складирования
Рисунок 6. Размещение оборудования для сварки длинномерных деталей: 1 – рольганг для подачи труб; 2 – установка для сварки труб; 3 – накопитель
Рисунок 7. Размещение установок автоматической сварки и резки поворотными колоннами и самоходными порталами: 1 – портал самоходный; 2 – автомат сварочный или резак; 3 – универсальный цепной кантователь или стол термической резки; 4 – место складирования; 5 – стенд; 6 – роликовый стенд; 7 – кантователь; 8 – поворотная колонна
Рисунок 8. Размещение источников питания (рекомендуемое): 1 – однопостовой источник питания; 2 – многопостовой источник питания; 3 – ограждение сетчатое
Определение необходимости применения мостовых кранов Мостовые электрические краны применяют в тех цехах, где производят грузоподъемные работы по разгрузке металла, укладке его штабеля, подаче к режущим агрегатам, подаче на тележку при передаче металла из пролета в пролет.
Мостовые электрические нормальные краны грузоподъемностью 5;10 и 15 т имеют пролеты длиной 11; 14; 17; 20; 23; 26; 29 и 32 м, краны грузоподъемностью 20/5, 30/5, 50/10 и 80/10 т имеют пролеты 10,5; 13,5; 16,5; 19,5; 22,5; 25,5; 28,5 и 31,3 м.
Число мостовых кранов определяют из расчета один кран на каждые 60 м длины пролета, но в каждом конкретном случае количество кранов уточняется.
Таблица 2- Допускаемые пределы минимальных расстояний между оборудованием (рабочими местами), складочными местами элементами здания (по материалам норм технологического проектирования)
Примечание.Меньшие значения указанных допустимых расстояний относятся малогабаритным, а большие – к крупногабаритным (в плане) станкам, стендам и складочным местам.
5. Определение высоты пролетов
Рисунок 9. Поперечное сечение пролетов цеха для подсчетов требуемой их высоты: а – при отсутствии верхнего транспорта (кранов); – при наличии последнего в сборочно-сварочном отделении; – то же в заготовительном отделении
Высота пролетов сборочно-сварочного проектируемого цеха обусловлена размерами подлежащих изготовлению в них сборочных единиц, габаритными размерами производственного оборудования применением верхнего транспорта (Рисунок 9).
В случае отсутствия верхнего транспорта высота пролета (Нн) определяется так:
Нн> = h1 + h2> = 4,5 м, | (10) |
где h1 – наибольшая в рассматриваемом пролете высота производственного оборудования, стеллажей, стендов (но не менее 2,3 м); h2– расстояние между наивысшей точкой указанного оборудованиялибо стеллажей и наиболее низкой точкой выступающих конструкционных частей перекрытия (обычно 0,4–1 м).
Согласно нормам технологического проектирования высота производственных помещений от пола до потолка должна составлять не менее 4,5 м.
При наличии верхнего транспорта (Нн) высота пролета определяется так:
Нн> = h1 + h3+ h4+ h5 +6; | (11) |
H3> = Hп + h7+ h8, | (12) |
где Нп – высота пролета цеха от пола до уровня поверхности головки рельса подкрановых путей, м; Н3 – высота пролета цеха от пола до нижнего уровня затяжки стропил перекрытия, м; h3 – расстояние от уровня поверхности головки рельса подкрановых путей до наиболее низкой точки подъемного крюка в его наиболее высоком положении (но не менее 0,75 м); h4 – расстояние между наиболее низкой точкой транспортируемого груза (не менее 1 м); h5 – наибольшая высота грузов, транспортируемых в данном пролете при помощи верхнего транспорта, м; h6 – расстояние между наиболее низкой точкой поднятых грузов и наивысшей точкой установленного в этом же пролете оборудования (0,5–1 м); h7 – расстояние от уровня поверхности головки рельса подкранового пути до высшей точки оборудования тележки мостового крана, м; h8 – расстояние между высшей точкой оборудования тележки крана и нижним уровнем затяжки стропил перекрытия (0,6–1,2 м).
Таблица 3 -Нормы ширины проходов и проездов в пролетах сборочно-сварочного цеха (по материалам норм технологического проектирования)
6. Чертеж технологической планировки сборочно-сварочного цеха
После проведения всех подсчетов и установления на основе указанных выше соображений рационального взаимного расположения пролетов цехов приступают к нанесению на бумагу в принятом масштабе сетки колонн проектируемого цеха и размещения в его пролетах оборудования и рабочих мест.
Порядок выполнения работы
5.1. Необходимо иметь следующие данные:
a. Количество рабочих мест
b. Количество сборочных мест
c. Количество сварочных мест
d. Размеры элементов производства в плане (длина, ширина и размеры высот)
5.2.Количество подъемно-транспортных средств (общецеховых и межоперационных).
5.3. Ширина пролета уточняется по схеме, представленной на рисунке 1, и выбирается необходимая по таблице 1.
5.4. Масштаб берется 1:100, 1:200, 1:50.
5.5. На листе наносится сетка колонн в принятом масштабе, соблюдая условия прямоточности и выдерживая условные обозначения элементов производства.
5.6. С первой попытки невозможно получить оптимальный вариант планировки рабочих мест и оборудования на участке, поэтому допускается перестановка элементов.
5.7. После вычерчивания плана участка делается поперечный его разрез. Условное обозначение подъемно-транспортных средств и элементов здания.
Форма отчета о работе
6.1. Название работы.
6.2. Цель работы.
6.3. Эскиз плана участка цеха
6.4. Вывод.
Контрольные вопросы и задания
7.1. Как определяется число пролетов?
7.2. Как определяется ширину пролета?
7.3. Как определяется длину пролета?
7.4.Как производится определение необходимости применения мостовых кранов?
Рекомендуемая литература
1. Куркин С. А., Николаев Г. А. Сварные конструкции. – М.: Высшая школа, 1991.
2. Красовский А. И. Основы проектирования сварочных цехов. – М. Машиностроение. 1965.
3. Цумарев Ю.А., Проектирование сварочных цехов:учебн. пособие/Ю.А. Цумарев.- Мн:РИПО,2019
Приложение А
Дата добавления: 2021-07-19; просмотров: 159; Мы поможем в написании вашей работы! |
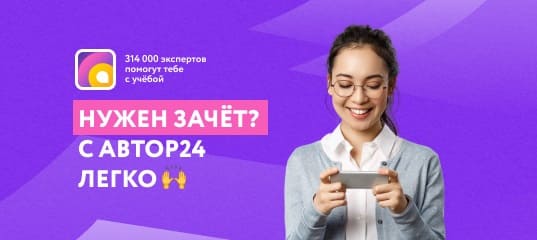
Мы поможем в написании ваших работ!