Технология ручной дуговой сварки покрытыми электродами
Содержание
Введение………………………………………………………………
Глава 1.Технологическая часть………………………………………..
1.1.Описание технологического процесса сборки и сварки………….
1.2.Оборудование и материалы, применяемые при выполнении…….
1.3.Техника безопасности и охрана труда……………………………..
Глава 2.Организационно-экономическая часть…………………………..
2.1.Организация рабочего места сварщика……………………………
2.2.Подсчет объемов работ и расхода материалов……………………
Заключение………………………………………………………………….
Список используемой литературы………………………….................
Введение
Сварка – это сложный технологический процесс, требования которого подразумевают наличие специального оборудования, материалов и квалифицированного персонала. В быту на простейшем оборудовании возможно выполнение несложных сварочных работ. Более того, в сети есть множество обучающих видео, которые можно посмотреть и сразу же приниматься за сварочные работы. Но в любом случае необходимо строжайшее соблюдение правил электро- и газобезопасности.
В современном мире процесс сваривания металла выполняют сотни тысяч людей и даже десятки тысяч роботов по всей Земле и сегодня мы знаем имена выдающихся и талантливых сварщиков, читаем интервью, смотрим обзоры работ, обучаемся. Но кем же были настоящие первооткрыватели, самые первые сварщики?
Целью выпускной квалификационной работы является технология изготовления учебного пособия по сварке труб
|
|
Исходя из цели, был рассмотрен ряд задач:
1. Изучить материал по данной теме
2. Разработать технологическую часть
3. Описать организационно-экономическую часть работы
4. Сделать чертежи
5. Сформулировать вывод исходя из полученного материала
Глава 1
Технологическая часть
1.1.Описание технологического процесса сборки и сварки
Характеристика материала конструкции
Наиболее распространённым материалом для изготовления сварных конструкций является сталь.
Сталь — это сплав железа с углеродом и другими элементами. В зависимости от химического состава сталь бывает углеродистая и легированная. Углеродистая сталь делится на низкоуглеродистую (содержание углерода до 0,25%), среднеуглеродистую (от 0,25 до 0,6%С) и высокоуглеродистую (от 0,6 до 2,0%С). Сталь, в составе которой кроме углерода имеются легирующие компоненты (хром, никель, вольфрам, ванадий и т. д.), называется легированной. Различают легированные стали: низколегированные (суммарное содержание легирующих компонентов, кроме углерода, менее 2,5%), среднелегированные (от 2,5 до 10%), высоколегированные (более 10%). Легирующие компоненты, вводимые в состав сталей, улучшают их качество: повышаются механические свойства, снижается порог хладноломкости, в результате чего создается возможность снизить массу конструкций.
|
|
По микроструктуре различают стали перлитного, мартенситного, аустенитного, ферритного и карбидного классов.
По способу производства различают стали:
· обыкновенного качества;
· качественная;
· высококачественная.
По назначению стали бывают строительные, машиностроительные (конструкционные), инструментальные и стали с особыми физическими свойствами. Рассмотренные выше стали имеют хорошую свариваемость. Технология ручной дуговой сварки таких сталей должна обеспечивать конкретный комплекс требований, к которым прежде всего относятся:
· обеспечение надежности и долговечности конструкций и особенно из термически упрочняемых сталей, как правило, используемых при изготовлении ответственных конструкций;
· обеспечение равнопрочное сварного соединения с основным металлом и отсутствие дефектов в сварном шве, поэтому механические свойства металла шва и околошовной зоны должны быть не ниже нижнего предела соответствующих свойств основного металла.
|
|
Подготовка металла к сварке
Подготовка металла под сварку заключается в правке, очистке, разметке, резке и сборке. Правкой устраняют деформацию прокатной стали. Листовой и сортовой металл правят в холодном состоянии на листоправйльных и углоправйльных вальцах и прессах. Сильно деформированный металл правят в горячем состоянии. Перенос размеров детали в натуральную величину с чертежа на металл называют разметкой. При этом пользуются инструментом: рулеткой, линейкой, угольником и чертилкой. Проще и быстрее разметка выполняется шаблоном, изготовляемым из тонкого металлического листа. При разметке заготовок учитывается укорачивание их в процессе сварки конструкции. Поэтому предусматривается припуск из расчета 1 мм на каждый поперечный стык и 0,1—0,2 мм на 1 м продольного шва.
При подготовке деталей к сварке применяют преимущественно термическую резку. Механическую резку целесообразно выполнять при заготовке однотипных деталей, главным образом с прямоугольным сечением. Часто кислородную резку, особенно машинную, сочетают со снятием угла скоса кромок. После термической резки иногда проводят механическую обработку по кромкам для удаления науглероженного металла. Перед сборкой под сварку требуется в соответствии с ГОСТом подготовить кромки свариваемых деталей.
|
|
К элементам геометрической формы подготовки кромок под сварку (см.рис.) относятся угол разделки кромок a, притупление кромок S, длина скоса листа L при наличии разности толщин металла, смещение кромок относительно друг друга б, зазор между стыкуемыми кромками а; геометрические размеры шва: в-ширина шва, h-высота шва, К-катет шва.
Сборка изделий под сварку
Трудоемкость сборки деталей под сварку составляет около 30% от общей трудоемкости изготовления изделия. Она зависит от ряда условий (серийности производства, типа изделий и др.). Для уменьшения времени сборки, а также для повышения ее точности применяют различные приспособления. Приспособления могут быть предназначены только для сборки деталей под сварку или только для сварки уже собранного изделия (например, для выполнения швов в изделии только в нижнем положении) или пользуются комбинированными сборочно-сварочными приспособлениями.
Основным назначением сборочного оборудования является фиксация и закрепление собираемого сварного узла в заданном положении. Для этой цели применяются специальные узлы и установки. Установочные и закрепляющие элементы сборочного оборудования. К первым относятся упоры, опоры, призмы, фиксаторы, шаблоны и домкраты. Закрепляющими элементами являются прижимы, которые могут быть ручными и механизированными. В качестве привода механизированных прижимов чаще всего применяются пневматические и гидравлические системы. В некоторых случаях прижим объединяют с упором или фиксатором и выполняют в виде комплексного узла. Установочные и зажимные элементы могут быть съемными и регулируемыми. Из отдельных элементов могут быть собраны приспособления и установки, в частности кондукторы и стенды. Указанные установки применяют для сборки плосколистовых и коробчатых конструкций, а также цилиндрических обечаек. При сборке осуществляют следующие операции: устанавливают все необходимые элементы конструкции на соответствующих местах с заданными зазорами и закрепляют их, совмещают кромки свариваемых элементов, при необходимости производят прихватки. В результате получают конструкцию, готовую для сварки. Для обеспечения необходимой точности сборки, сокращения времени на разметку и проверку собранной конструкции, а также облегчения процесса сварки (возможность выполнения швов в нижнем положении) целесообразно использовать при изготовлении конструкций специальный кондуктор.
Точность сборки проверяют с помощью специального инструмента.
Технология ручной дуговой сварки покрытыми электродами
При ручной дуговой сварке покрытыми металлическими электродами, сварочная дуга горит с электрода на изделие, оплавляя кромки свариваемого изделия и расплавляя металл электродного стержня и покрытие электрода (рисунок). Кристаллизация основного металла и металла электродного стержня образует сварной шов.
Достоинства способа:
· простота оборудования;
· возможность сварки во всех пространственных положениях;
· возможность сварки в труднодоступных местах;
· быстрый, по времени переход от одного вида материала к другому;
· большая номенклатура свариваемых металлов.
· Недостатки способа:
· большие материальные и временные затраты на подготовку сварщика;
· качество сварного соединения и его свойства во многом определяются субъективным фактором;
· низкая производительность (пропорциональна сварочному току, увеличение сварочного тока приводит к разрушению электродного покрытия);
· вредные и тяжёлые условия труда.
· Рациональные области применения:
· сварка на монтаже;
· сварка непротяжённых швов.
Виды трубопроводов и сварка
Трубопроводов существует огромное количество, которые используются для перемещения разных материалов и рабочих жидкостей. Отталкиваясь от их предназначения, есть следующая классификация:
· технологические;
· магистральные;
· промышленные;
· трубопроводы газоснабжения;
· водяные;
· канализационные.
При изготовлении трубопровода применяются различные материалы – керамика, пластик, бетон и различные виды металлов.
Современные сварщики для стыковки труб используют три основных способа:
· Механический осуществляется за счет взрывов в результате трения.
· Термический, который осуществляется за счет плавления, например газовой сваркой, плазменной или электро-лучевой.
· Термомеханический производится за счет магнитоуправляемой дуги посредством стыкового контактного метода.
работы плавящимся или неплавящимся электродом (аргонно-дуговая сварка). Технология сварки труб реализуется в три основных этапа:
· Подготовительный, который делится на две части – подготовка мастера и подготовка материала. К подготовке сварщика стоит отнестись очень ответственно, так как от этого зависит его безопасность. Обязательно нужно подготовить спецодежду и защитную маску для глаз, чтобы предотвратить ожог яркими искрами.
· Сварочный процесс. Когда все готово, можно начинать. Самое основное в дуговом способе ( вне зависимости вручную она проводится или инвертором) это удержать дугу. Сначала необходимо зажечь электрод и возбудить дугу. Затем полноценно производится шов. Его тип выбирается непосредственно мастером в процессе работы.
· Проверка качества работы. Когда шов готов (не стоит забывать оббивать шлак, который образуется над ним в виде валика), можно запустить коммуникацию на предмет контроля качества соединения.
· Технология сварки водопровода, газопровода и других инженерных коммуникаций практически одинаковая. Важно соблюдать последовательность действий и учитывать виды швов в разных положениях, так как от умения их варить и будет зависеть качество коммуникации.
Как состыковать трубы
Для новичка, который хочет в совершенстве овладеть сваркой, необходимо знать все тонкости этого процесса. Для сваривания двух труб существует более 30 способов. Рассмотрим самые распространенные способы сварки труб:
· в угол;
· в тавр (перпендикулярно по отношению друг к другу);
· в стык;
· внахлест.
Тип стыковки труб выбирается в зависимости от типа металла, вида сварки и характера коммуникации. Например, трубы для системы централизованного отопления чаще всего соединяются встык с помощью электросварки. Для качественного шва, главное – сделать провар по всей толщине изделия.
Сварка труб может, в зависимости от условий и масштаба работ, производиться различными способами:
Дата добавления: 2021-07-19; просмотров: 74; Мы поможем в написании вашей работы! |
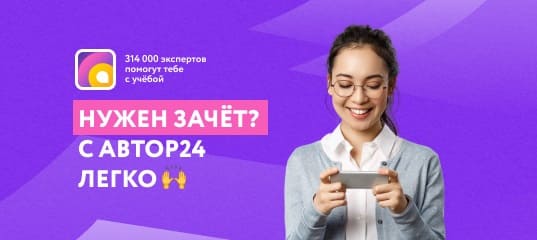
Мы поможем в написании ваших работ!