Общий подход к созданию программ для станков с ЧПУ при помощи CAM-систем
Сущность автоматизированной подготовки УП. Уровни автоматизации программирования. Системы автоматизированного программирования (САП). История развития САП. Использование CAM-систем при разработке УП. Структура CAM-системы
Существуют следующие способы подготовки УП:
1) ручная;
2) в технологическом бюро;
3) на станке с системой ЧПУ типа CNC в диалоговом режиме, и используя систему автоматизированной подготовки программы.
Ручная подготовка программ в коде ISO-7bit требует кропотливого отбора технологических решений, трудоемких геометрических расчетов, тщательного документирования отдельных этапов и может проводиться квалифицированными инженерами-технологами. Такой способ существовал только в начале развития станков с ЧПУ.
В 90-х годах основным способом подготовки управляющих программ являлась их подготовка в технологических бюро, на инструментальной ЭВМ, с использованием систем автоматизированного программирования (САП УП для станков с ЧПУ).
В настоящее время в связи с увеличением памяти МПС системы автоматизированного программирования (САП) широко встраиваются в СЧПУ. Подготовка УП ведется в диалоговом режиме на станках с СЧПУ.
Системы автоматизированного программирования УП
Совокупность математического, программного обеспечения и проблемно-ориентированного языка для записи и ввода в ЭВМ первоначальной информации при организации УП называют САП. В настоящее время разработано множество различных САП. Они различаются степенью и уровнем автоматизации этапов подготовки управляющей программы (УП).
|
|
САП – это специальное программное обеспечение, реализующее комплекс алгоритмов геометрических и технологических задач подготовки УП и содержащее проблемно-ориентированный язык, обеспечивающий запись и ввод в ЭВМ исходной информации.
САП решает следующие задачи:
¨ диалог с пользователем;
¨ синтаксический контроль исходной информации на входном языке;
¨ проектирование элементов технологического процесса обработки;
¨ расчет траектории движения инструмента;
¨ формирование и запись выходной информации на промежуточном языке;
¨ выдача диагностических сообщений о разных этапах обработки исходной информации;
¨ редактирование программ на уровнях входного, промежуточного выходного языков;
¨ формирование УП на выходном языке для конкретного станка и выдача на программоноситель;
¨ распечатка УП и сопроводительной документации;
¨ хранение и тиражирование УП.
В комплект САП входит также сопроводительная документация – руководство технологу программисту и оператору ЭВМ.
|
|
Важнейшие блоки САП, такие как: сервис, препроцессор, процессор, постпроцессор-это, как правило, файл и или несколько файлов, в которых заложена информация о конфигурации оборудования и системы ЧПУ, установленной на данное оборудование, наличии всевозможных функций. Блок сервис преобразовывает неизменную информацию о станках, материале заготовок, инструментах и др. Информация систематизируется и записывается в память ЭВМ как таблицы параметров.
Типовая структурная схема САП дана на рисунке 8.1.
Постоянная информация – библиотека операций, технологических циклов, процедур, геометрических расчетов, таблиц параметров и т.д.
Рисунок 8.1 - Типовая структурная схема САП
Исходная информация – данные о заготовке и детали.
Препроцессор – проектирует план технологических операций, перечень и последовательность переходов, выбор схем закрепления, типа инструмента и т.д., трансляцию на универсальный язык.
Процессор – выполняет геометрические и технологические расчеты (количество проходов, режимы резания, вычисления траектории).
Постпроцессор – увязывает УП с особенностями и возможностями конкретных станков (привязка к координатам станка, типу датчиков и т.д.).
|
|
На первом этапе переработка информации применяется в двух блоках, составляющих основу каждой САП, — процессоре и постпроцессоре. Процессор осуществляет геометрические и технологические расчеты «без привязки» к определенному станку и системе ЧПУ. Процессор предполагает траекторию перемещения инструмента. Данные вместе с данными о режимах резания выводятся на наружный носитель ЭВМ — диск или же магнитную ленту. Конфигурация представления этих данных называется CLDATA (от англ. CATTER Location Data — данные о расположении инструмента) и является установленным видом информации на конкретном языке.
Процессор САП состоит из трех один за другим работающих блоков: трансляции и геометрического формирования CLDATA.
Технологический блок самостоятельно делит область, подлежащую обработке, на переходы, рабочие ходы и рассчитывает оптимальные режимы резания.
Геометрический блок процессора постановляет задачи, объединенные с созданием траектории перемещения инструмента: определение точек и линий скрещивания всевозможных элементов; аппроксимация разнообразных кривых с определенным допуском; диагностика геометрических ошибок.
Блок трансляции (блок ввода и декодирования) реализовывает вытекающие функции: чтение первоначальной программы обработки изделия с наружного носителя; вывод программы на печать или же экран дисплея; изменение информации из символьной формы во внутреннее машинное представление. В препроцессоре готовятся данные для работы остальных блоков, операции подразделяются на установы и позиции, отбираются схемы крепления заготовки и оснащаются инструментальные наладки.
|
|
Блок формирования CLDATA ведет сбор сведений для работоспособности постпроцессора. Постпроцессор не прекращает переработку информации и сформировывает УП с ориентацией (т. е. с «привязкой») на конкретный станок и систему ЧПУ. Типовые функции постпроцессора: сканирование данных, которые разработаны процессором, перенос их в систему координат станка; составление команд на передвижение с учетом стоимости импульса СЧПУ и команд, обеспечивающих цикл замены инструмента; выдача в кадр значений подач и скоростей шпинделя, которые были закодированы; подача команд на включение и выключение охлаждения, зажима — разжима заготовок; выдача управляющей перфоленты и листинг (распечатки) УП; диагностика ошибок; выполнение сервисных функций. Это является вторым этапом переработки информации.
В большинстве случаев САП заключает в себе набор постпроцессоров, предоставляющие формирование УП (управляющей программы) для отдельных типов станков с ЧПУ. Вызов нужного постпроцессора выполняется автоматически по параметрам, которые технолог-программист укажет в тексте исходной программы.
Двухэтапная организация работы САП при подготовке УП содержит важное преимущество. На определенном языке САП на основе одной и той же начальной информации, имея данные CLDATA и применяя всевозможные постпроцессоры, можно получать УП для разнообразных моделей станков и УЧПУ. Кроме того, для подключения новейших моделей станков с ЧПУ к имеющейся на предприятии САП достаточно создать постпроцессор и состыковать с САП. Вместе с постпроцессором создается работа с программным блоком «редактор», который позволяет изменять УП, выводимую на экран дисплея.
В настоящее время чаще используется обозначение таких систем как CAM –системы.
Введение в CAM-системы.
Под термином Computer-aidedmanufacturing(CAM) понимают как программы, используемые технологами для подготовки управляющих программ для станков с числовым программным управлением(ЧПУ), так и сам процесс компьютеризированной подготовки производства.
Традиционно, CAM-системы представляют собой средства формирования траекторий движения инструмента на основании 2D и/или 3Dгеометрии (обычно сгенерированной в CAD-системе) и перевода (постпроцессирования) их в команды системы ЧПУ станка. Многие из программно-вычислительных комплексов совмещают в себе решение задач CAD/CAM, CAE/САМ, CAD/CAE/CAM, но существуют и узкоспециализированные CAM-системы, направленные на создание управляющих программ для специфического оборудования, например вышивальных машин, производства печатных плат и т.п.
Согласно исследованиям компании CIMdata первыми десятью компаниями по объёму выручки от CAM-систем в 2010 году были:
·Cimatron (4.1%) спродуктом GibbsCAM
·CNC Software (3.3%) спродуктом Mastercam
·C&G Systems (3.7%)
·DassaultSystèmes(18%) с продуктом CATIA
·Delcam (7.5%) спродуктом PowerMILL
·Open Mind (3.8%) спродуктом HyperMill
·Planit (6.3%) спродуктом Edgecam
·PTC(4.6%) с продуктом Pro/E·
Siemens PLM Software (12.1%) спродуктом NX
·Tebis AG (4.4%) с продуктом Tebis
История
Самые первые CAM-системы были разработаны как инструменты для внутреннего использования в компаниях автомобильной и аэрокосмической отрасли. В 1968 Пьер Безье (Pierre Beziers), инженер компании Renault разработал CAM-систему UNISURF. В первую очередь разработка CAM-систем была связана с появлением поверхностей сложной формы, о которых уже велась речь. Составление программы для обработки таких поверхностей в ручном режиме – чрезвычайно трудоёмкая и однообразная работа, однако легко алгоритмизируемая.
С ростом сложности изделий и ростом парка ЧПУ потребность в CAM-системах постепенно возрастала. Сейчас разработать программы для пятикоординатного фрезерного станка без CAM-системы не представляется возможным. Возможности CAM-систем и их рынок постоянно развиваются. Основными направлениями модернизации можно отметить следующие:
·Высокоскоростная обработка и методы оптимизации траекторий.
·Пятиосевая обработка.
·Распознавание и обработка элементов детали.
·Повышение уровня автоматизации программирования.
·Повышение простоты использования системы.
·Более глубокая интеграция с CAD/CAE/CAPP и прочими PLM системами.
Одной из веток CAM-систем является так называемое shop-floor programming, при котором визуальные средства программирования доступны непосредственно со стойки станка. Примерами являются системы ShopTurn и ShopMill компании Siemens. Такие системы обладают меньшей гибкостью, однако обычно проще в использовании, обладают большей совместимостью с конкретным системой ЧПУ и станком, а, следовательно, надёжностью программ и при производстве несложных типовых изделий позволяют перенести функции программиста ЧПУ на квалифицированного оператора станка.
Несмотря на широкие возможности и высокий уровень автоматизации подготовки управляющих программ CAM-система не может заменить человеческий труд. Особенно остро встаёт потребность в опыте и навыках квалифицированного технолога при оптимизации программ в соответствии с требованиями массового производства, при производстве изделий с высокими требованиями к точности и качеству поверхностей. CAM-система всего лишь инструмент и даже при разработке программ для изготовления типовых корпусных 2.5D деталей с использованием технологии FBM (FeatureBasedMachining) – наиболее автоматизированная на сегодняшний день задача – требуется предварительная настройка, адаптация к существующим производственным условиям, которую сможет выполнить только человек.
Коммерческая, претендующая на роль промышленной, CAM-система должна обладать следующими возможностями:
1.Импорт трехмерной геометрии.
2.Возможность создания вспомогательной геометрии.
3.Библиотеки режимов резания, материалов, станков и инструмента.
4.Наличие стратегий для 2.5D, 3D, 4х и 5ти координатной фрезерной, токарной, токарно-фрезерной, электроэрозионной обработки с гибкой настройкой параметров.
5.Возможность симуляции обработки.
6.Иметь средства для контроля траекторий на зарезы, недоработки и столкновения.
7.Постпроцессирования и генерации постпроцессоров.
Общий подход к созданию программ для станков с ЧПУ при помощи CAM-систем
Программа для станка с ЧПУ представляет собой последовательность кодов, в результате трансляции которых станок формирует траектории движения инструмента, задаёт параметры работы (подача, скорость и направление вращения шпинделя и т.п.) и выполняет вспомогательные функции (смена инструмента, подача СОЖ и т.д.).
Традиционная последовательность действий, необходимых для создания программы обработки детали для станка ЧПУ в CAM-системе, выглядит следующим образом:
1.Выбор типа обработки и кинематической схемы станка.
2.Определение управляющей геометрии.
3.Выбор стратегии и параметров обработки.
4.Вычисление траекторий движения инструмента.
5.Визуальный контроль траекторий (бэкплот) и их симуляция.
6.Постпроцессирование (перевод траекторий движения и вспомогательных операций в коды станка).
При этом предполагается, что выполнена предварительная работа по адаптации CAM-системы под имеющиеся производственные условия.
Основными работами по настройке и внедрению CAM-системы предприятия являются следующие:
1.Создание 3Dмоделей и кинематических схем станков, имеющихся на предприятии.
2.Наполнение базы данных инструмента.
3.Разработка и настройка постпроцессоров.
А также в некоторых случаях создаются и настраиваются базы данных по принятым на предприятии режимам и стратегиям обработки, настройке шаблонов операционных карт, карт наладки и другой документации.
Стадия внедрения CAM-системы очень важна и стоит уделить ей особое внимание. Обычно это большая, дорогостоящая и кропотливая работа, однако от качества её выполнения зависит дальнейшее удобство разработки, сроки разработки программ, их надежность и качество.
Под надёжностью понимается уверенность в том, что программа при её исполнении на станке с ЧПУ даст ожидаемый, в результате симуляции траекторий, результат и не приведет к поломке инструмента, станка или порче заготовки.
Под качеством программы для станка с ЧПУ будем понимать её лаконичность (отсутствие лишних инструкций, использование требуемых типов интерполяции и т.п.), наличие всех необходимых блоков и команд, возможность запуска обработки на станке без каких либо изменений оператором.
Создание моделей и схем станков, описывающих внешние габариты и поведение именно существующих на конкретном предприятии моделей станков, позволяет отследить многие ошибки (зарезы, столкновения, некорректные перемещения осей) и предотвратить потенциальные проблемы в будущем (например, выход координат в программе за пределы рабочей зоны станка). Ошибка, замеченная технологом на компьютере, не стоит ничего – ноль, тогда как ошибка, перенесенная на станок, часто обходится в цену испорченной заготовки, сломанного инструмента, а, возможно и элементов станка, например, жесткое столкновение может привести к замене шпинделя фрезерного станка. Человеческие ошибки неизбежны и различные системы симуляции призваны помочь их предотвратить, но при использовании настроек «по умолчанию» они фактически бесполезны.
Настройка постпроцессора, адаптация существующих постпроцессоров, как правило, существенно экономит время наладки программы, упрощает поиск и исправление ошибок, а также может помогать повышать скорость и качество обработки за счёт поддержки постпроцессором специфических функций, циклов и возможностей конкретного станка. Программа после правильно настроенного постпроцессора не требует редактирования формата команд и числовых данных, изменения шапки программы и прочей ручной доработки, которая неминуема при использовании стандартных, или «почти 6подходящих» постпроцессоров и может повлечь за собой привнесение дополнительных ошибок. Необходимое условие для постпроцессора –отсутствие синтаксических ошибок в генерируемых им программах.
Вышеуказанные операции строго необходимы. Без их проведения результаты работы CAM-системы могут быть некорректны и опасны. Что касается прочей адаптации системы, то она желательна и время, потраченное на неё, безусловно окупится, однако она не столь критична ,как настройка моделей станков и постпроцессора.
Современное производство характеризуется наличием большого числа станков с ЧПУ разных производителей. Каждый станок ориентирован на решение задач определенного круга и рассчитан на работу с управляющими программами, написанными в специальном формате. Большинство CAM-систем, используемых на производстве, создают файл с управляющей программой в инвариантном формате, например APT или CLDATA, не привязанной к какой-либо конкретной модели станка с ЧПУ. Для перевода инвариантной управляющей программы в программу в кодах конкретной системы с ЧПУ служат специальные интерпретаторы, называемые постпроцессорами. Наряду с универсальными постпроцессорами, предоставляемыми CAM-системами, программисты часто пишут собственные постпроцессоры, ориентированные на конкретные, часто специфичные режимы работы станка, учитывающие особенности конкретной обработки. Как следствие, с ростом производства и расширением парка станков с ЧПУ растет и количество применяемых постпроцессоров, что, в свою очередь, требует некоторой систематизации для удобства и упрощения процесса постпроцессирования управляющих программ в инвариантном коде.
Дата добавления: 2021-04-05; просмотров: 298; Мы поможем в написании вашей работы! |
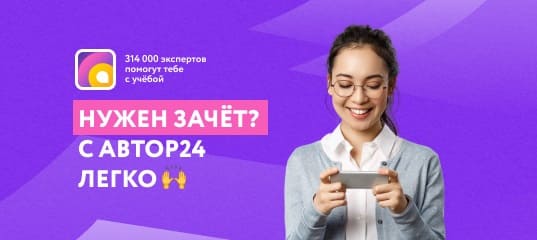
Мы поможем в написании ваших работ!