СТЫКОВАНИЕ СБОРОЧНЫХ ЭЛЕМЕНТОВ
ПМ 02 ПРОИЗВОДСТВЕННО – ТЕХНОЛОГИЧЕСКИЙ
МДК 02.01 Технологическая подготовка производства
Раздел 2 Технология сборки двигателей
Литература:
А.А.Гарькавый «Сборка авиационных двигателей»
А.И. Ильянков, М.Е. Левит «Основы сборки авиационных двигателей»
Тема: Теоретические основы технологии сборки
Технология сборки базируется на законах технологии машиностроения и является ее составной частью.
Технология сборки – это наука:
} о процессах и явлениях, протекающих при установке и закреплении деталей,
} о влиянии их на качество сборки,
} о наилучших методах и способах контроля качества изделий,
} о закономерностях хода рабочих процессов,
} о выборе оптимальных средств и параметров ведения процессов,
} о рациональных способах управления ими.
Задача сборки
Освоение производства и выпуск изделий высшей категории качества в минимальные сроки при минимальных трудовых и материальных затратах на всех стадиях создания изделий, включая опытные образцы и изделия единичного производства.
Условия и предпосылки качественной сборки
} Качественные сборочные элементы
} Неукоснительное исполнение правильной сборочной технологии
} Точные технические средства сборки
} Соответствующая квалификация сборщиков, контролёров и других работников
} Достаточные производственные помещения по площади и высоте
} Определенная температура и чистота воздуха в помещениях
|
|
} Определенная форма организации сборочных работ
Требования к сборке.
Сборка и контроль ее качества должны быть: удобными, высокопроизводительными, точными, безопасными, экономичными, несложными
Задачи конструктора при сборке
} Отыскать при проектировании наилучший вариант конструкции изделия, имеющего оптимальное число деталей, наилучшие способы их центрирования и соединения.
} Точность сборки должна обеспечиваться при минимальных затратах времени и средств.
Задачи технолога при сборке:
} Отыскание оптимальной последовательности технологического процесса сборки, включения в него прогрессивных средств сборки.
} Технологический процесс должен иметь оптимальный вариант построения операций и последовательности их выполнения.
} Для повышения производительности труда следует применять средства механизации и автоматизации.
Тема: Разновидности и структура изделий
Задание:
По тексту учебника А.А. Гарькавый «Сборка авиационных двигателей»
стр. 7-12, выполнить Практическую работу 1 Анализ специфицированных изделий (см. отдельный документ)
Тема: Явления и процессы при сборке
СОПРЯЖЕНИЯ ПРИ СБОРКЕ
|
|
У каждой детали участвующий в сборке имеются сопрягающиеся и несопрягающиеся поверхности. Несопрягающися поверхности в процессе сборки не соприкасаются с поверхностями других деталей, а сопрягающиеся - в результате их совмещения соприкасаются и образуют сопряжения.
Сопряжение представляет собой совокупность взаимосвязанных поверхностей, определенным образом взаимно расположенных после установки деталей на своё место и создающих минимум 8 связей между деталями.
Сопрягают детали между собой при взаимном центрировании, получении кинематических пар и соединений. В зависимости от способа соединения деталь может сопрягаться с одной или несколькими другими деталями. Во втором случае подобная деталь имеет соответствующее число сопрягаемых поверхностей и является звеном силового каркаса сборочной единицы, объединяющего её сборочные элементы.
В некоторых случаях наряду с получением сопряжением производят одновременно фиксирование сборочных элементов в окружном либо осевом направлениях. После получения сопряжения обычно производится закрепление сопряженных деталей.
Сопряжение поверхностей и соединение деталей могут осуществляться порознь и одновременно. Если этапы сборки выполняются порознь, то вначале производят сопряжение деталей, а затем их соединение. При сборке некоторых объектов может один из этих этапов отсутствовать. Одновременное получение сопряжений и соединение деталей наблюдается при свинчивании, запрессовке или постановке в пазы деталей, когда происходит силовое замыкание сопряжений.
|
|
В случае стыкового соединения сборочных элементов с использованием электродуговой сварки сопряжения деталей отсутствует. Детали при этом только правильно взаимно выставляются.
Сопрягаемые поверхности и их сопряжения имеют некоторые разновидности, различные свойства и параметры. В процессе выполнения сопряжения в сопрягаемых поверхностях возникают различные физические явления, влияющие на свойства сопряжения.
Сопрягаемыми называются поверхности, подготовленные для сопряжения. Сопрягаемые поверхности можно классифицировать по различным признакам: конфигурации (внешнему очертанию), назначению, взаимодействию и качеству исполнения.
По конфигурации поверхности характеризуются формами профиля и образующей, их может быть бесчисленное множество. Более распространены на деталях поверхности с постоянной прямолинейной образующей (линейчатые) и профилями, описываемыми известными математическими формулами (алгебраические). Это цилиндрические, конические, резьбовые и линейчато - фасонные (шлицевые, эвольвентные, «ёлочного» типа) поверхности.
|
|
В зависимости от назначения детали имеют один либо несколько конструктивных элементов, предназначенных для различных целей. Детали могут иметь рабочие, установочные, уплотнительные, центрирующие, соединительные, фиксирующие, балансировочные и другие элементы. Каждый конструктивный элемент детали очерчен одной либо несколькими поверхностями различной формы, образующими конфигурацию элементов и всей детали.
По назначению сопрягаемые поверхности могут быть базовыми, функциональными и упорными. Базовые поверхности, а также базовые линии или точки, называемые сборочными базами, служат для обеспечения наилучшего взаимного расположения сопрягаемых сборочных элементов в сборочной единице и сохранения при работе этой определенности положения. Обычно такими качествами обладает одна из сопрягаемых поверхностей, называемое основной базовой. Поверхность, сопрягаемая с основной базовой, называется вспомогательной базовой (присоединительной). В целях повышения точности сборки сборочными базами иногда являются установочные базы, используемые при формообразующей обработке деталей.
Функциональные (исполнительные, рабочие) поверхности служат для выполнения рабочих функций (поверхность зубьев, резьба и др.), а упорные - для обеспечения определённости осевого расположения деталей.
По взаимодействию сопрягаемые поверхности подразделяются на охватывающие и охватываемые. На деталях также имеются установочные и присоединительные поверхности предназначенные для связи изделиям с другими изделиями. Такие поверхности при сборке изделия остаются не сопряженными. Некоторые из них временно сопрягают с защитными временными деталями (крышками, заглушками и т.п.).
В процессе формирования сопряжения производится определённое взаимное расположение сопрягаемых поверхностей, введение их в соприкосновение и образование стыка, наложение связи между деталями, натяга либо зазора между не контактируемыми частями сопрягаемых поверхностей, возникают определённые контактные напряжения в поверхностных слоях и внутренние - в сопрягаемых деталях.
Определённое взаимное расположение поверхностей в сопряжении характеризуется их несоосностью, взаимным расположением вокруг и вдоль оси, наличием перекосов и их величиной. После сопряжения контактируемые поверхности могут располагаться между собой соосно или иметь некоторое взаимное смещение поперек оси по радиусу. Смещение осей по радиусу определяет несоосность поверхностей, называемую эксцентриситетом. Соосность сопрягаемых поверхностей зависит от вида посадок и формы поверхностей. При посадке с натягом сопрягаемые поверхности располагаются соосно, в сопряжениях с зазором под действием сил тяжести имеется взаимное смещение поверхностей, зависящие от величины зазоров. В осевом направлении поверхности должны сопрягаться на определенную длину и не иметь свисание.
Свисание - это часть сопрягаемых поверхностей, не вошедших в сопряжении стык. Свисание изменяет сборочные размеры собираемой сборочной пары, а также уменьшает длину сопряжения и отсюда площадь взаимного контакта, что приводит к увеличению контактных напряжений в поверхностных слоях сопрягаемых деталей и уменьшению силы трения между ними. Свисание зависит от взаимной осевой установки сопрягаемых деталей. Чтобы исключить свисание поверхностей и облегчить сборку, применяют различные способы осевого фиксирования деталей.
СТЫКОВАНИЕ СБОРОЧНЫХ ЭЛЕМЕНТОВ
Сопрягаемые поверхности твердых тел при их сборке полностью либо частично стыкуются и образуют определенного качества стык.
Стык в сопряжении образуется в месте соприкосновения между собой сопрягаемых поверхностей после установки сборочных элементов в рабочее положение. Он создает общую границу раздела соприкасающихся деталей. Стыком называется место, где две сопрягаемые поверхности при их соприкосновении стремятся слиться (объединиться) вместе и образовать одну, так называемую стыковочную поверхность. Стыковочная поверхность является общей поверхностью, принадлежащей сопрягаемым поверхностям, в которой теоретически и практически возможен их контакт. Стыковочная поверхность - это реальная либо теоретическая поверхность в пространстве, форму которой пытаются получить сопрягаемые поверхности при их силовом взаимодействии и к которой они стремятся приблизиться с целью их слияния и образование плотного стыка. Она имеет определённую форму и размеры, зависящие от конфигурации, размеров, точности и взаимной кривизны сопрягаемых поверхностей.
Стыкование – постановка одной детали на другую вплоть до соприкосновения поверхностей. Стыкование представляет собой конечный результат определенной взаимной установки сборочных элементов в осевом направлении. Стыкование не накладывает рабочих связей.
Прилегание - это контактирование сопрягаемых поверхностей вместе образования стыка. Оно зависит от качества, взаимного расположения и силового взаимодействия поверхностей и влияет на плоскость соединений, а также на силы и моменты трения, создаваемые между этими поверхностями. Прилегание различают идеальное и реальное.
Идеальное прилегание создаётся при сопряжении идеальных поверхностей, то есть поверхностей абсолютно гладких, строго определенной конфигурации и размеров. Идеальные поверхности создают идеальный стык, имеют полное прилегание друг к другу при свободном их соприкосновении. Форма и размеры идеального стыка определяются формой и размерами сопрягаемых поверхностей.
Реальные поверхности в отличие от идеальных имеют не гладкую поверхность и погрешности их формы, то есть сложный рельеф, определяемый геометрическими характеристиками: шероховатостью, волнистостью и микрогеометрией. Реальные поверхности после их сопряжения не везде сливаются (объединяются) в одно, из-за чего стык в некоторых местах, где поверхности не соприкасаются, имеют две границы раздела. На форму реального стыка, до силового взаимодействия поверхностей, влияют их кривизна, и геометрические характеристики. В результате создания при сборке силового взаимодействия поверхности в стыке деформируются, гребешки сминаются, поверхности изгибаются в местах отсутствия контактов и приближаются к друг другу вплоть до соприкосновения, что увеличивает площадь контакта. Деформация поверхностей зависит от физико-механических свойств материалов, сопрягаемых деталей и нагрузок, сжимающих стык.
В зависимости от полноты прилегания сопряженные поверхности деталей могут иметь между собой в месте стыка полный или неполный (частичный) контакт. Величина контакта влияет на величину контактных напряжений в поверхностях при работе изделия. В некоторых случаях необходимо стремиться к тому, чтобы контакт сопрягаемых поверхностей был полным по всей стыковочной поверхности. Неполный контакт сопряженных поверхностей, в процессе работы изделия, особенно в период его приработки, изменяется из-за воздействия рабочих нагрузок, приводящих к деформации и износу этих поверхностей, а также из-за воздействия рабочей среды.
Дата добавления: 2021-03-18; просмотров: 232; Мы поможем в написании вашей работы! |
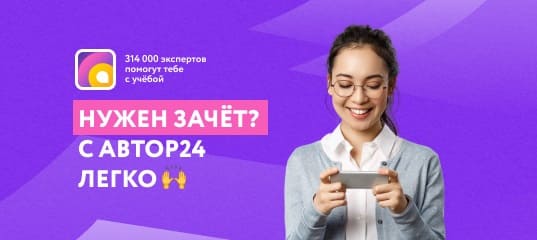
Мы поможем в написании ваших работ!