ФОРМОВОЧНЫЕ И СТЕРЖНЕВЫЕ СМЕСИ
ЛАБОРАТОРНАЯ РАБОТА 4
РАЗРАБОТКА ТЕХНОЛОГИЧЕСКОГО ПРОЦЕССА ПОЛУЧЕНИЯ ЛИТЫХ ЗАГОТОВОК
Цель работы: изучить технологию изготовления отливок в песчано-глинистых формах и разработать чертежи модели по заданному чертежу детали.
4.1. ОБЩИЕ СВЕДЕНИЯ
Литье в песчаные формы является универсальным и самым распространенным способом изготовления отливок. Этим способом изготовляют разнообразные по сложности отливки любых массы и размеров из сталей, чугунов и сплавов цветных металлов.
Литые детали (отливки) изготавливают в специальных литейных формах, в которые заливают заранее приготовленный расплав. После затвердевания расплав сохраняет очертания той полости, в которую был залит. Наиболее распространенным является способ изготовления отливок в разовых песчано-глинистых формах.
Рис. 4.1
Эскиз чертежа детали
Полость в литейной форме получают с помощью модели. Литейная модель — приспособление, при помощи которого в литейной форме получают полость с формой и размерами, близкими к конфигурации получаемой отливки. В зависимости от конструкции и способа изготовления модель может быть цельной и разъемной. В крупносерийном и массовом производстве применяют металлические модели, в единичном и мелкосерийном — деревянные. По конструкции и размерам модель отличается от получаемой по ней отливки и детали.
|
|
При конструировании модели сначала разрабатывают технологический чертеж отливки. Для этого на чертеж детали (рис. 4.1) условно наносят технологические указания (припуски, напуски, уклоны, галтели, разъемы, знаковые части), которые необходимо учесть при изготовлении модели. В соответствии с технологическим чертежом отливки изготавливают модель, размеры которой больше на величину линейной усадки сплава.
4.2. РАЗРАБОТКА ЧЕРТЕЖА МОДЕЛИ
Определение положения отливки в форме. При определении положения отливки в форме нужно руководствоваться следующими правилами:
1) наиболее ответственные рабочие части, места, подлежащие механической обработке, нужно, по возможности, располагать внизу;
2) для отливок, имеющих внутренние полости, образуемые стержнями, выбранное положение должно обеспечивать надежное крепление стержней;
3) модель должна свободно извлекаться из формы;
4) всю отливку, если позволяет ее конструкция, нужно располагать в одной полуформе в целях исключения перекосов.
От положения плоскости разъема зависит конструкция литейной формы, величина припуска на механическую обработку, расположение формовочных уклонов, расположение и конфигурация стержневых знаков и другие технологические характеристики. Разъем модели и формы на чертеже показывается линией, над которой проставляют буквенное обозначение разъема — МФ. Направление разъема изображают сплошной линией, ограниченной стрелками. Положение отливки в форме обозначают буквами. В (верх), Н (низ), проставленных у стрелок (рис. 4.2).
|
|
Рис. 4.2
Чертеж детали с элементами литейной технологии.
Примечание. Линейная усадка — 1%; класс точности 10, ряд припусков 3; деревянная модель.
После выбора плоскости разъема назначается припуск на механическую обработку, формовочные уклоны и другие элементы литейной технологии.
Припуск на механическую обработку. Отливки, как правило, подвергаются дальнейшей механической обработке с целью достижения требуемой точности размеров и необходимого качества поверхности.
Под точностью изготовления отливок понимается степень отклонения их геометрических размеров и массы от номинальных значений. Установлено шесть рядов припусков.
Припуски на механическую обработку сторон определяются в зависимости от допусков размеров отливки дифференцированно для каждого элемента.
|
|
Классы точности отливок на размер и массу, размер припуска на механическую обработку зависят от способа литья, наибольших габаритных размеров отливки, вида сплава и допуска литейных размеров отливки. Эти показатели определяют по таблицам 4.1-4.3, ГОСТ 26645-85.
Допуск — разность между наибольшими и наименьшими значениями размера отливки или между нижними и верхними предельными отклонениями.
На чертеж припуск на механическую обработку наносят сплошной тонкой линией на поверхности, где стоит знак механической обработки (V) (рис. 4.2). Для верхних частей отливок предусматривают большой припуск на механическую обработку, так как при заполнении формы расплавом неметаллические включения и газы всплывают как наиболее легкие вверх и концентрируются в слое металла, который удаляют при механической обработке отливок.
Пример. Определить припуски на механическую обработку для детали на рис. 4.2. Характеристики отливки: отливка из серого чугуна; литье в песчаные формы; габаритный размер 130 мм; единичное изготовление; средней сложности.
Для определения величины припуска на механическую обработку необходимо установить класс точности и ряд припусков для данной отливки. В таблице 4.1 по габаритному размеру (130 мм), типу сплава (СЧ) и способу литья (в песчаные формы) находим значение
|
|
Учитывая единичное производство и среднюю сложность отливки, выбираем класс точности 10, ряд припусков — 3.
По значению класса точности и номинальным размерам определяем допуск размеров отливки (таблица 4.2). Номинальный размер 80 мм — 2,8 мм, 30 мм — 2,2 мм.
Табл цца 4.1
Классы точности размеров и ряды припусков на механическую обработку отливок для различных способов литья (ГОСТ 26645-85)
Способ литья | Наибольший габаритный размер заливки, мм | Тип сплава | ||
Цветные сплавы (А1, Мn,
Zn), « ![]() | Цветные сплавы, серый чугун,
![]() | Ковкий, высокопрочный и легированный чугун, сталь | ||
Литье под давлением в металлические формы | до 100 | ![]() | ![]() | ![]() |
св. 100 | ![]() | ![]() | ![]() | |
Литье по выплавляемым моделям в оболочковые формы | до 100 | ![]() | ![]() | ![]() |
св. 100 | ![]() | ![]() | ![]() | |
Литье в кокиль. Литье в песчаные формы, отверждаемые в контакте с оснасткой | до 100 | ![]() | ![]() | ![]() |
100-630 | ![]() | ![]() | ![]() | |
св. 630 | ![]() | ![]() | ![]() | |
Литье в песчаные формы, сырые и сухие. Центробежное литье | до 630 | ![]() | ![]() | ![]() |
630-4000 | ![]() | ![]() | ![]() | |
св. 4000 | ![]() | ![]() | ![]() |
Примечание. В числителе указаны классы точности размеров; в знаменателе— ряды припусков. Меньшие значения относятся к простым отливкам и условиям массового производства: большие — к сложным мелкосерийно и индивидуально изготовленным отливкам; средние — к отливкам средней сложности и условиям механизированного серийного производства.
Та 6л и ца 4.2
Допуск размеров отливки, мм (ГОСТ 26645-85)
Номинальный размер, мм | ||||||||||||
Класс точности | До 4 | 4 - 6 | 6 -10 | 10 - 16 | 16 - 25 | 25 - 40 | 40-63 | 63 - 100 | 100 - 160 | 160 - 250 | 250 - 400 | > 400 |
1 | 0,06 | 0,07 | 0,08 | 0,09 | 0,1 | 0,11 | 0,12 | 0,14 | 0,16 | — | — | — |
2 | 0,08 | 0,09 | 0,10 | 0,11 | 0,12 | 0,14 | 0,16 | 0,18 | 0,20 | — | - | — |
Зт | 0,1 | 0,11 | 0,12 | 0,14 | 0,16 | 0,18 | 0,20 | 0,24 | 0,28 | 0,32 | - | — |
3 | 0,12 | 0,14 | 0,16 | 0,18 | 0,20 | 0,22 | 0,26 | 0.28 | 0,32 | 0,36 | 0,4 | _ |
4 | 0,16 | 0,18 | 0,2 | 0,22 | 0,26 | 0,28 | 0,32 | 0,36 | 0,4 | 0,44 | 0,5 | 0,56 |
5т | 0,2 | 0,22 | 0,24 | 0.28 | 0,32 | 0,36 | 0,4 | 0,44 | 0,5 | 0,56 | 0,64 | 0,7 |
5 | 0.24 | 0,28 | 0,32 | 0,36 | 0,4 | 0,44 | 0.5 | 0,56 | 0,64 | 0,7 | 0,8 | 0,9 |
6 | 0,32 | 0,36 | 0,4 | 0,44 | 0,5 | 0,56 | 0,64 | 0,7 | 0,8 | 0,9 | 1.0 | 1,1 |
7т | 0,4 | 0,44 | 0,5 | 0,56 | 0,64 | 0,7 | 0,8 | 0,9 | 1,0 | 1.1 | 1.2 | 1.4 |
7 | 0,5 | 0,58 | 0,64 | 0,7 | 0,8 | 0,9 | 1,0 | 1,1 | 1,2 | 1.4 | 1,6 | 1,8 |
8 | 0.6 | 0,7 | 0,8 | 0,9 | 1.0 | 1,1 | 1,2 | 1,4 | 1,6 | 1.8 | 2.0 | 2,2 |
9т | 0,8 | 0,9 | 1,0 | 1,1 | 1,2 | 1,4 | 1.6 | 1.8 | 2,0 | 2.2 | 2,4 | 2,8 |
9 | 1,0 | 1,1 | 1,2 | 1,4 | 1,6 | 1,8 | 2,0 | 2,2 | 2,4 | 2,8 | 3.2 | 3,6 |
10 | 1.2 | 1,4 | 1,6 | 1.8 | 2,0 | 2,2 | 2,4 | 2,8 | 3,2 | 3,6 | 4.0 | 4,4 |
11т | 1.6 | 1,8 | 2.0 | 2,2 | 2,4 | 2,8 | 3,2 | 3,6 | 4,0 | 4,4 | 5,0 | 5,6 |
11 | 2.0 | 2,2 | 2.4 | 2,8 | 3,2 | 3,6 | 4,0 | 4,4 | 5,0 | 5,6 | 6,4 | 7,0 |
12 | — | 2,8 | 3,2 | 3,6 | 4.0 | 4,4 | 5,0 | 5,6 | 6,4 | 7.0 | 8,0 | 9,0 |
13т | — | — | 4,0 | 4,4 | 5,0 | 5,5 | 6,4 | 7,0 | 8,0 | 9,0 | 10 | 11 |
13 | — | — | 5,0 | 5,6 | 6.4 | 7 | 8,0 | 3,0 | 10 | 11 | 12 | 14 |
14 | — | — | — | 7 | 8 | 9 | 10 | 11 | 12 | 14 | 16 | 18 |
15 | — | — | — | — | 10 | 11 | 12 | 14 | 16 | 18 | 20 | 24 |
16 | — | — | — | — | 12 | 14 | 16 | 18 | 20 | 22 | 24 | 28 |
По таблице 4.3 выбираем величину припуска на механическую обработку (ряд припусков 3): для допуска 2,8 мм — 3,6 мм.
На верхней части отливки принимаем величину припуска 4 мм. Припуск на механическую обработку внутренней полости с номинальным размером 30 мм и допуском 2,2 мм равен 3,2 мм.
Указываем припуски на чертеже детали с элементами литейной технологии (рис. 4.2).
Табл и ца 4.3
Припуски на механическую обработку отливок (ГОСТ 26645-85)
Допуск, мм | Ряды припусков | |||||
1 | 2 | 3 | 4 | 5 | 6 | |
До 0,12 | 0,2-0,4 | — | — | — | — | — |
0,12-0,16 | 0,3-0,5 | 0,6-0,8 | — | — | — | — |
0,16-0,20 | 0,4-0,6 | 0,7-1,0 | 1,0-1,4 | — | — | — |
0,20-0,24 | 0,5-0,7 | 0,8-1,1 | 1,1-1,5 | — | — | — |
0,24-0,30 | 0,6-0,8 | 0,9-1,2 | 1,2-1,6 | 1,8-2,2 | 2,6-3,0 | — |
0,30-0,40 | 0,7-0,9 | 1,0-1,3 | 1,4-1,8 | 1,9-2,4 | 2,8-3,2 | — |
0,40-0,50 | 0,8-1,0 | 1.1-1,4 | 1,5-2,0 | 2,0-2,6 | 3,0-3,4 | — |
0,50-0,60 | 0,9-1,2 | 1,2-1,6 | 1,6-2,2 | 2,2-2,8 | 3,2-3,6 | — |
0,60-0,80 | 1,0-1,4 | 1,3-1,8 | 1,8-2,4 | 2,4-3,0 | 3,4-3,8 | 4,4-5,0 |
0.80-1,0 | 1,1-1,8 | 1,4-2,0 | 2,0-2,8 | 2,6-3,2 | 3.6-4,0 | 4,6-5,5 |
1,0-1,2 | 1,2-2,0 | 1,8-2,4 | 2,2-3,0 | 2,8-3,4 | 3,8-4,2 | 4,8-6,0 |
1,2-1,6 | 1,6-2,4 | 2,0-2,8 | 2,4-3,2 | 3,0-3,8 | 4,0-4,6 | 5,0-6,5 |
1,6-2,0 | 2,0-2,8 | 2,4-3,2 | 2,8-3,6 | 3,4-4,2 | 4,2-5,0 | 5,5-7,0 |
2,0-2,4 | 2,4-3,2 | 2,8-3,6 | 3,2-4,0 | 3,8-4,6 | 4,6-5,5 | 6,0-7,5 |
2,4-3,0 | 2,8-3,6 | 3.2-4,0 | 3,6-4,5 | 4,2-5,0 | 5,0-6,5 | 6,5-8,0 |
3,0-4,0 | 3,4-4.5 | 3,8-5,0 | 4,2-5,5 | 5,0-6,5 | 5,5-7,0 | 7,0-9,0 |
4,0-5,0 | 4,0-5,5 | 4,4-6,0 | 5,0-6,5 | 5,5-7,5 | 6,0-8,0 | 8,0-10,0 |
5,0-6,0 | 5,0-7,0 | 5,5-7,5 | 6,0-8,0 | 6,5-8,5 | 7,0-9,5 | 9,0-11,0 |
6,0-8,0 | — | 6,5-9,5 | 7,0-10 | 7,5-10 | 8,5-12 | 10-13,0 |
8.0-10,0 | — | — | 9,0-12 | 10-13 | 11-14 | 12-15 |
10,0-12,0 | — | — | 10-13 | 11-14 | 12-15 | 13-16 |
12,0-16.0 | — | 13-15 | 14-16 | 15-17 | 16-19 |
Формовочные уклоны.
Рис. 4.3
Литейные уклоны
Формовочные уклоны служат для удобства извлечения модели из формы без ее разрушения, выполняются на вертикальных стенках моделей
в направлении извлечение модели из формы. На обрабатываемых поверхностях уклоны выполняются за счет увеличения размеров отливки сверху припуска на механическую обработку (рис. 4.3а), на необрабатываемых — за счет уменьшения размеров (рис. 4.3б), а иногда за счет увеличения в одном месте и уменьшения в другом (рис. 4.3в). Величина уклонов зависит от материала модели и высоты участка отливки (таблица 4.4). Величину уклона указывают на чертеже, а сам уклон закрашивается черным цветом (рис. 4.3).
Меньшие значения припуска устанавливают при более грубых квалитетах точности обработки, большие — при более точных.
Таблица 4.4
Формовочные уклоны (ГОСТ 3212-80)
Высота h, мм | Образующие полость формы | Образующие узкие выступы и углубления | ||
Металлическая или пластмассовая модель | Деревянная модель | Металлическая или пластмассовая модель | Деревянная модель | |
≤ 20 | 1°30' | 3° | 3° | 3° |
21-50 | Г | 1° | 2° | 2°30' |
51-100 | 0°45' | 1° | 1°30' | 1°30' |
101-200 | 0°30' | 0°45' | 0°45' | 1° |
201-300 | 0°30' | 0°30' | 0°45' | 1° |
301-800 | 0°20' | 0°30 | 0°30' | 0°45' |
801-2000 | — | 0°20' | — | 0°30' |
> 2000 | — | — | — | 0°15' |
Стержни. Для образования полостей, отверстий или иных сложных контуров в формы устанавливают стержни, которые фиксируют с помощью выступов (стержневых знаков)
Рис. 4.4
Знаки стержней:
а — вертикальный; б – горизонтальный.
Размеры и конфигурацию стержневых знаков назначают по ГОСТ 3606-80 с учетом размера стержня, способа формовки и его положения в форме (рис. 4.4).
При вертикальном расположении стержня в форме он фиксируется нижним и верхним знаками. Высоту нижних знаков стержней назначают в зависимости от их длины и диаметра (таблица 4.5). Высоту верхних вертикальных знаков принимают равной не более 0,5 высоты нижних знаков.
При горизонтальном расположении отверстия используют несколько вариантов фиксации его в форме. Длину горизонтальных стержневых знаков назначают с учетом способа формовки (таблица 4.6). Формовочные уклоны на знаковых частях назначают по ГОСТ 3606-80 (таблица 4.7) в зависимости от высоты знака.
Та б л и ца 4.5
Высота h нижних вертикальных знаков стержней для сырых, сухих форм, мм (ГОСТ 3606-80)
Размер стержня D, мм | Длина стержня L, мм | |||||
До 50 | 50-80 | 80-120 | 120-180 | 180-250 | 250-315 | |
До 30 | 20 | 30 | 30 | — | — | — |
30-50 | 20 | 35 | 35 | 35 | 50 | 60 |
50-80 | 25 | 35 | 35 | 35 | 40 | 50 |
80-120 | 25 | 35 | 35 | 35 | 40 | 50 |
120-180 | 30 | 35 | 35 | 35 | 35 | 40 |
180-250 | 30 | 35 | 35 | 35 | 35 | 40 |
250-315 | 35 | 35 | 35 | 35 | 35 | 40 |
Таблица 4.6
Длина / горизонтальных знаков стержней, мм
Размер стержня D. мм | Тип формы | Длина стержня L, мм | |||||
До 50 | 50-80 | 80-120 | 120-180 | 180-250 | 250-315 | ||
До 30 | Сырая | 20 | 25 | 30 | 35 | — | — |
Сухая | 15 | 20 | 30 | 35 | — | ||
30-50 | Сырая | 20 | 25 | 30 | 35 | 45 | 50 |
Сухая | 20 | 25 | 30 | 35 | 40 | 45 | |
50-80 | Сырая | 20 | 25 | 30 | 40 | 50 | 55 |
Сухая | 20 | 25 | 30 | 35 | 40 | 45 | |
80-120 | Сырая | 20 | 25 | 35 | 45 | 55 | 60 |
Сухая | 25 | 30 | 35 | 40 | 45 | 50 |
Таблица 4.7
Формовочные уклоны на стержневых знаках
Высота знака, мм | а | Р | Высота знака, мм | а | Р |
до 30 | 10° | 15° | 81-120 | 6° | 8° |
30-50 | 7° | 10° | 121-180 | 5° | 6° |
51-80 | 6° | 8° | 181-250 | 5° | 6° |
При литье в песчаные формы отверстия диаметром менее 20 мм целесообразно высверливать, а не получать их с помощью стержней.
Галтели. Все наружные и внутренние углы в отливке должны иметь закругления — галтели. Они облегчают извлечение модели из формы, предотвращают появление трещин в отливке, улучшают ее качество. Радиус галтелей выбирают по формуле:
где R – радиус галтели; - полусумма толщин сопрягаемых стенок отливки;
в случае, если
< 50мм;
при
Таблица 4.9
Линейная усадка сплавов
Сплав | Размер, мм | Весовая группа | Линейная усадка, % |
Серый чугун | М | I | 0,75-1,0 |
С | II | 0,5-1,0 | |
К | III, IV | 0,5-0,75 | |
Углеродистая | М | I | 1,5-2,2 |
сталь | С | II | 1,5-2,0 |
К | III, IV | 1,4-1,8 | |
Медные сплавы | М | I | 1,5-1,8 |
С | II | 1,0-1,5 | |
К | III | 0,75-1,0 | |
Алюминиевый магниевый | М | I | 1,0-1,2 |
С | II | 0,75-1,0 | |
К | III | 0,5-1,0 |
Размеры: М — до 500 мм; С — 500-1500 мм; К — свыше 1500 мм
На чертеже технологической разработки всегда указывают величину усадки сплава, которая должна быть учтена при изготовлении моделей (таблица 4.8).
Порядок выполнения работы
1. Изучить последовательность составления чертежа отливки и чертежа модели.
2. Получить эскиз детали (рис. 4.5-4.16, таблица 4.9).
Вар. | 1 | 2 |
H1 | 12 | 15 |
H2 | 60 | 120 |
H3 | 50 | 100 |
H4 | 30 | 60 |
D1 | 25 | 50 |
D2 | 30 | 55 |
D3 | 50 | 80 |
D4 | 100 | 220 |
D5 | 225 | 245 |
Рис. 4.5
Эскиз шкива
Вар. | 1 | 2 |
H1 | 100 | 210 |
H2 | 90 | 195 |
H3 | 80 | 180 |
H4 | 70 | 145 |
H5 | 20 | 30 |
H6 | 10 | 15 |
H7 | 30 | 65 |
H8 | 40 | 80 |
H9 | 60 | 130 |
D1 | 20 | 50 |
D2 | 40 | 80 |
D3 | 90 | 200 |
D4 | 100 | 220 |
D5 | 110 | 230 |
D6 | 120 | 250 |
Рис. 4.6
Эскиз барабана
Вар. | 1 | 2 |
H1 | 100 | 200 |
H2 | 90 | 180 |
H3 | 10 | 15 |
D1 | 120 | 260 |
D2 | 100 | 230 |
D3 | 80 | 200 |
D4 | 20 | 50 |
D5 | 40 | 80 |
Рис. 4.7
Эскиз стакана
Таблица 4.9
Детали для разработки технологии изготовления отливок
№ | Деталь | Вариант | Количество, шт. | Вес детали, кг |
![]() | Шкив (рис. 4.5) | 1 | 60-10000 | 2,4 |
2 | 60 | 13,0 | ||
![]() | Барабан (рис. 4.6) | 1 | 60 - 10000 | 3,6 |
2 | 60 | 21,0 | ||
![]() | Стакан (рис. 4.7) | 1 | 60 - 10 000 | 2,1 |
2 | 60 | 12,8 |
Продолжение табл. 4.9
№ | Деталь | Вариант | Количество, шт. | Вес детали, кг | |
![]() | Ролик (рис. 4.8) | 1 | 60-10 000 | 3,0 | |
2 | 60 | 21,0 | |||
![]() | Ступица (рис. 4.9) | 1 | 60-10 000 | 1,9 | |
2 | 60 | 14,2 | |||
![]() | Опора (рис. 4.10) | 1 | 60-10 000 | 1,4 | |
2 | 60 | 5,7 | |||
![]() | Гильза (рис. 4.11) | 1 | 60-10 000 | 2,1 | |
2 | 60 | 13,5 | |||
| Патрубок (рис. 4.12) | 1 | 60-10 000 | 1,7 | |
2 | 60 | 12,6 | |||
![]() | Фланец (рис. 4.13) | 1 | 60-10 000 | 2,2 | |
2 | 60 | 12,8 | |||
![]() | Переходник (рис. 4.14) | 1 | 60-10 000 | 1,4 | |
2 | 60 | 10,5 | |||
![]() | Корпус (рис. 4.15) | 1 | 60-10 000 | 1Д | |
2 | 60 | 5,6 | |||
![]() | Насадка (рис. 4.16) | 1 | 60-10 000 | 1,8 | |
2 | 60 | 13,5 |
Вар. | 1 | 2 |
H1 | 80 | 225 |
H2 | 20 | 25 |
H3 | 10 | 10 |
H4 | 90 | 240 |
H5 | 100 | 250 |
01 | 30 | 80 |
D1 | 60 | 130 |
D2 | 80 | 160 |
D3 | 100 | 200 |
Рис. 4.8
Эскиз ролика
Вар. | 1 | 2 |
Н1 | 80 | 180 |
Н2 | 50 | 95 |
Н3 | 40 | 80 |
D 1 | 100 | 220 |
D2 | 70 | 140 |
D3 | 40 | 80 |
D4 | 20 | 50 |
D 5 | 120 | 250 |
D 6 | 15 | 30 |
Рис. 4.9
Эскиз ступицы
Вар. | 1 | 2 |
Н1 | 40 | 70 |
Н2 | 50 | 85 |
Н3 | 70 | 140 |
D1 | 140 | 250 |
D2 | 100 | 190 |
D3 | 50 | 95 |
D4 | 30 | 70 |
D5 | 20 | 30 |
D6 | 30 | 40 |
D7 | 20 | 50 |
D8 | 40 | 80 |
Рис. 4.10
Эскиз опоры
Вар. | 1 | 2 |
Н1 | 120 | 250 |
Н2 | 80 | 190 |
Н3 | 40 | 60 |
Н4 | 20 | 30 |
Н5 | 10 | 15 |
D1 | 80 | 160 |
D2 | 60 | 130 |
D3 | 40 | 100 |
Рис. 4.11
Эскиз гильзы
Вар. | 1 | 2 |
H 1 | 120 | 250 |
H 2 | 110 | 235 |
H 3 , | 40 | 70 |
H4 | 40 | 90 |
H5 | 10 | 15 |
D1 | 40 | 100 |
D2 | 60 | 130 |
D 3 | 65 | 140 |
D4 | 100 | 220 |
Рис. 4.12
Эскиз патрубка
Вар. | 1 | 2 |
H1 | 100 | 200 |
H2 | 40 | 75 |
H3 | 30 | 60 |
D1 | 120 | 250 |
D2 | 100 | 220 |
D3 | 50 | 130 |
D4 | 30 | 100 |
|
Рис. 4.13
Эскиз фланца
Вар. | 1 | 2 | |
Н1 | 10 | 20 | |
Н2 | 60 | 100 | |
Н3 | 70 | 120 | |
D1 | 100 | 250 | |
D2 | 80 | 200 | |
D3 | 60 | 150 | |
D4 | 40 | 110 | |
D5 | 25 | 80 | |
D6 | 8 | 12 | |
D7 | 15 | 30 | |
D8 | 20 | 40 | |
D9 | 40 | 80 | |
| |||
Рис. 4.14
Эскиз переходника
Вар. | 1 | 2 |
Н1 | 5 | 10 |
Н2 | 60 | 100 |
Н3 | 75 | 140 |
Н4 | 80 | 150 |
D1 | 120 | 250 |
D2 | 100 | 210 |
D3 | 40 | 100 |
D4 | 5 | 15 |
D5 | 30 | 70 |
D6 | 20 | 50 |
D7 | 70 | 150 |
D8 | 80 | 170 |
Рис. 4.15
Эских корпуса
Вар. | 1 | 2 |
Н1, | 85 | 160 |
Н2 | 20 | 35 |
Н3 | 30 | 50 |
Н4 | 120 | 200 |
D1 | 120 | 250 |
D2 | 100 | 220 |
D3 | 70 | 150 |
D4 | 10 | 20 |
D5 | 30 | 50 |
S | 10 | 15 |
Рис. 4.16
Эскиз насадки
3. Определить положение отливки в форме, плоскость разъема модели, серийность. Выбрать материал модели.
4. Вычертить чертеж детали с элементами литейной технологии, показав положение модели в форме, уклоны, галтели, припуски на механическую обработку, стержневые знаки, стержни; указать линейную усадку. С целью упрощения работы величину припуска на механическую обработку поверхности с указанной шероховатостью (Rz) определить по таблицам. Чертеж выполняется на миллиметровке карандашом с соблюдением правил машиностроительного черчения и обозначений, принятых в литейном производстве.
Контрольные вопросы
1. Что называется моделью? Каковы ее назначение, конструкция, материал?
2. Что такое линейная усадка, как она учитывается при изготовлении модели, от чего зависит ее величина?
3. Для чего нужны формовочные уклоны, и от каких факторов зависит их величина?
4. На каких поверхностях назначают припуск на механическую обработку, и от чего зависит его величина?
5. Что такое галтели и как они выбираются при разработке отливки?
6. Каково назначение стержневых знаков? От чего зависит их форма?
7. Как влияет серийность производства на технологию изготовления отливок?
8. Когда применяется прибыль? Каково ее назначение?
9. В чем различие между чертежами детали, отливки, модели?
ЛАБОРАТОРНАЯ РАБОТА 5
ТЕХНОЛОГИЯ ИЗГОТОВЛЕНИЯ ОТЛИВОК В ОПОКАХ
Цель работы: изучить технологию приготовления отливок в опоках, познакомиться с составом формовочных и стержневых смесей.
5.1. ОБЩИЕ СВЕДЕНИЯ
Литье в песчаные формы является универсальным и самым распространенным способом изготовления отливок. Этим способом изготовляют разнообразные по сложности отливки любых массы и размеров из сталей, чугунов и сплавов цветных металлов.
Сущность литья в песчаные формы заключается в изготовлении отливок свободной заливкой расплавленного металла в разовую литейную форму, изготовленную из формовочной смеси с последующим затвердеванием залитого металла, охлаждением отливки в форме, извлечением ее из формы с последующей отделкой.
Для изготовления отливок используют сырые, сухие и подсушенные песчаные формы; химически твердеющие формы, изготовленные из специальных самотвердеющих смесей; формы, изготовленные по газифицируемым моделям; формы, изготовленные из песчаносмоленных смесей.
Технологический процесс изготовления отливок состоит из ряда основных и вспомогательных операций, выполняемых в определенной последовательности. Для изготовления литейных форм используют модельный комплект, формовочные и стержневые смеси и другие материалы и оборудование.
Литейным производством называется технологический процесс получения фасонных деталей или заготовок путем заливки металла в литейную форму. Расплавленный металл заливают во внутреннюю полость формы, которая по конфигурации соответствует отливке и получается с помощью модели. Литейная форма заполняется металлом через каналы, называемые литниковой системой.
Наиболее широко применяются литейные формы, изготовленные из формовочной смеси в опоках (металлических рамках).
ФОРМОВОЧНЫЕ И СТЕРЖНЕВЫЕ СМЕСИ
Формовочные материалы — это совокупность природных и искусственных материалов, используемых для приготовления формовочных и стержневых смесей. В качестве исходных материалов используют формовочные кварцевые пески и литейные формовочные глины.
Для получения отливок высокого качества формовочные и стержневые смеси, из которых делают разовые литейные формы, должны обладать определенными механическими, технологическими и физическими свойствами. К таким свойствам относятся: прочность — способность смеси обеспечивать сохранность формы без разрушения при ее изготовлении и использовании; пластичность — способность смеси воспринимать очертания модели, стержневого ящика и сохранять форму; податливость — способность смеси сокращаться в объеме под действием усадки металла; текучесть — способность смеси обтекать модели при формовке; огнеупорность — способность смеси выдерживать высокую температуру заливаемого сплава; негигроскопичность — способность не поглощать влагу из воздуха в течение длительного времени; газопроницаемость — способность пропускать газы через стенки формы; выбивае-мость — способность легко удаляться из формы и полостей отливок при их выбивке после охлаждения.
Состав формовочных смесей выбирают в зависимости от литейного сплава, массы и конфигурации отливок и других условий. Основными компонентами формовочных смесей являются кварцевый песок (> 90% Si02) и огнеупорная глина (до 10%).
Глина является связующим веществом, обеспечивающим прочность и пластичность смесей, но снижает газопроницаемость, ухудшает податливость и выбиваемость.
Различают два вида формовки в песчано-глинистые формы: в сырые формы и сухие формы. Сырые формы применяют для мелких и средних отливок, в особенности в серийном и массовом производстве. Сухие формы применяют для крупных и толстостенных отливок, для получения отливок высокого качества. Эти формы подвергаются тепловой сушке (до 24 часов) и имеют высокую прочность. Для улучшения свойств в формовочные смеси вводят добавки: противопригарные (молотый каменный уголь, пылевидный кварц, графит, мазут), повышающие податливость и газопроницаемость (древесные опилки, сульфито-спиртовая барда), коллоидные растворы органических веществ и др.
Формовочные смеси разделяют на облицовочные, наполнительные и единые.
Облицовочная смесь — это формовочная смесь, используемая для изготовления рабочего слоя формы. Такие смеси содержат повышенное количество песка и глины и имеют высокие физико-механические свойства.
Наполнительная смесь — это формовочная смесь для наполнения формы после нанесения на модель облицовочной смеси. Облицовочные и наполнительные формовочные смеси используют для изготовления крупных и сложных отливок.
Единая смесь — это формовочная смесь, применяемая одновременно в качестве облицовочной и наполнительной смеси.
Стержневые смеси. Стержни при заливке расплавленного металла испытывают значительные тепловые и механические воздействия по сравнению с формой, поэтому стержневые смеси должны иметь более высокие огнеупорность, газопроницаемость, податливость, малую газотвор-ную способность, легко выбиваться из отливок.
Специальные формовочные смеси. Использование специальных формовочных смесей для изготовления форм и стержней позволяет наиболее эффективно применять современные средства механизации и автоматизации, исключить ручной труд, сушку формы, существенно повысить производительность труда и улучшить качество отливок.
То бл и ца 5.1
Состав формовочных и стержневых смесей, %
Материал | Песчаноглинистые | Жидкостекольная с продувкой CO | Холоднотвердеющие смеси | Жидкие самотвердеющие смазки | Смеси горячего отверждения | |
сырые | сухие | |||||
Песок | 87 - 90 | 80 – 95 | 95 – 97 | 95 | 95 – 97 | 100 |
Глина | 5 – 8 | 10 – 12 | — | — | — | — |
Влага | 4 – 5 | 6 – 8 | 3,5 – 4,5 | — | 2 | — |
Жидкое стекло 100% | — | — | 3 – 7 | — | 6 – 7 | — |
Смола термореактивная | — | — | — | 2,5 | — | 3 – 4 |
Катализатор | — | — | — | 2 | — | 1 |
Нефелиновый шлак или феррохромовый | — | — | — | 1,5(свыше 100%) | — | 1 |
Пенообразователи | — | — | — | — | 0,2 | — |
Время затвердевания, мин | Сушка 8 – 24 ч | 5 – 15 | 20 – 30 | 30 – 40 | 1 – (при ![]() | |
Прочность, МПа | 30 – 50 | 80 | — | 20 – 40 | 150 - 250 |
В специальных формовочных смесях в качестве связующих используют жидкое стекло, синтетические смолы (фенолоформальдегидные, карбамидные, фурановые), в смеси вводят катализаторы.
По условиям отверждения специальные смеси можно условно разделить на следующие типы: отверждаемые при продувке С02, горячего отверждения, самоотверждающиеся на воздухе (таблица 5.1).
5.3. ЛИТНИКОВАЯ СИСТЕМА, ПРИБЫЛИ, ВЫПОРЫ
Литниковая система — система каналов для подвода жидкого металла в полость литейной формы. Правильная конструкция литниковой системы должна обеспечивать непрерывную подачу расплава в форму по кратчайшему пути, спокойное и плавное ее заполнение, улавливание шлака и других неметаллических включений, минимальный расход металла на литниковую систему, не вызывать местных разрушений формы вследствие большой скорости и неправильного направления потока металла.
Рис. 5.1
Литниковая система
Литниковая система (рис. 5.1) включает следующие элементы: литниковую чашу 2, стояк 2, шлакоуловитель 3, пи татель 4.
В зависимости от места подвода металла в форму различают горизонтальную, верхнюю, сифонную, ярусную ли тниковые системы.
Выпор — вертикальн ый канал, расположенный под самой верхней частью отливки. Выпор служит для вывода газов из формы и наблюдения за ходом заливки формы.
Прибыль — полость в форме, которая заполняется расплавом для питания массивных частей отливки, чтобы избежать образования усадочных раковин и рыхлостей.
Дата добавления: 2021-03-18; просмотров: 119; Мы поможем в написании вашей работы! |
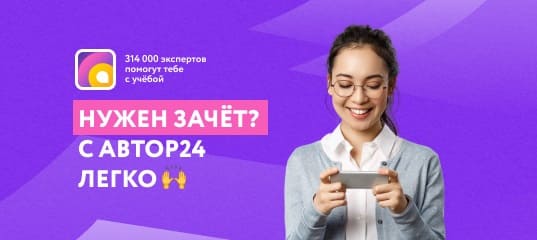
Мы поможем в написании ваших работ!