Ремонт ходовой части гусеничных тракторов
РЕМОНТ ХОДОВОЙ ЧАСТИ КОЛЕСНЫХ ТРАКТОРОВ, КОМБАЙНОВ И АВТОМОБИЛЕЙ
Основными составными частями ходовой части колесных машин являются: подвеска (рессоры, амортизаторы), рулевой механизм, тормозная система, передние оси или мосты (не ведущие), колеса с пневматическими шинами.
Ремонт рессор и амортизаторов. Наиболее частыми дефектами рессор являются: уменьшение стрелы прогиба, трещины и поломки листов, разрывы центровых болтов, износ втулок, пальцев, серег, срыв или забитость резьбы стремянок. Чаще всего наблюдаются изломы коренных листов у ушков или под стремянками. Листы рессоры, имеющие трещины или изломы, заменяют. Допускается переделка длинных листов на более короткие при такой же толщине.
При уменьшении стрелы прогиба листов рессор их правят на стенде по схеме, изображенной на рисунке. Лист лежит на двух ведущих роликах, которые его перемещают. Необходимую стрелу прогиба задают нажимным роликом, который перемещается винтом. Контроль величины прогиба осуществляется с помощью указателя и шкалы. Лист рессоры автоматически перемещается в обе стороны изменением направления вращения роликов. Правку листов можно проводить и вручную, ударами молотка по вогнутой поверхности. Лист рессоры при этом укладывают на подставку, имеющую выемку соответствующего радиуса.
Рессорные листы, утратившие свою форму, можно также восстанавливать, подвергая их отжигу, гибке по шаблону для придания нужной стрелы прогиба, закалке и отпуску. Осадку и испытание рессор проводят на специальных стендах.
|
|
Вместо изношенной или сорванной резьбы стремянки рессоры нарезают вручную уменьшенную резьбу при помощи лерки, установленной в специальную державку, или на токарном станке.
У амортизаторов обычно наблюдаются следующие неисправности: просачивание смазки через сальники, износ втулок проушин и втулок осей рычагов у рычажных амортизаторов, неплотность клапанов, износ поверхностей поршней и цилиндров. Возможно также заедание поршня в цилиндре.
При ремонте амортизатор разбирают и тщательно промывают керосином. Обезличивание поршней не допускается. Изношенную ось рычагов у рычажных амортизаторов шлифуют до выведения следов износа, а втулки развертывают под размер оси. При неплотной посадке клапанов прошлифовывают их посадочную поверхность или заменяют. Посадочные поверхности гнезд исправляют, затем в зависимости от конструкции клапанов притирают их к гнездам или доводят поверхности клапана и гнезд притиркой на плите. Изношенные поршень и цилиндр заменяют. Возможно восстановление цилиндров притиркой, А Поршней — электролитическими покрытиями. Собранные амортизаторы испытывают, измеряя у рычажных амортизаторов усилие, необходимое для поворота рычага на заданный угол, а у телескопических амортизаторов — для перемещения поршня на определенное расстояние.
|
|
Ремонт рулевого механизма. У этих механизмов колесных тракторов и автомобилей наблюдаются трещины, изломы и повреждения резьбы у картеров и их крышек, износы поверхности рулевого вала и вала сошки в месте сопряжения со втулками или подшипниками качения, износ втулок и подшипников, винтовой поверхности червяка, его подшипников, ролика или зубьев сектора сошки, оси ролика и подшипника, повреждение рулевого колеса, износы и нарушения регулировок в гидроусилителях рулевого управления.
Картеры и их крышки при наличии трещин и обломов выбраковывают. Поврежденные резьбы правят метчиком или рассверливают отверстия и нарезают резьбу увеличенного размера. Шейки вала сошки, сопряженные со втулками (ЗИЛ-130, ГАЗ-53А), могут быть прошлифованы до выведения следов износов с постановкой втулок с отверстиями уменьшенного диаметра. Шейки вала сошки, сопряженные с подшипниками качения (у тракторов), могут быть восстановлены железнением. У рулевых валов при износе шпоночной канавки фрезеруют новую канавку, смещенную на 90° относительно старой. Шейки рулевого вала, изношенные в сопряжении с подшипниками (втулками), можно восстановить хромированием или железнением. Сорванную резьбу восстанавливают вибродуговой наплавкой с последующим нарезанием резьбы нормального размера. Рулевые валы и валы сошки, имеющие трещины, скручивание и повреждение шлицев, выбраковывают. Беговые дорожки червяка при износе поверхности под ролики конических подшипников и при наличии на них мелких раковин шлифуют. Изменение размеров конической поверхности компенсируют постановкой регулировочных колец за наружным кольцом подшипника.
|
|
При износе торцов ролика червяка их шлифуют до выведения следов износа и при сборке ставят утолщенные упорные шайбы.
Червяки с изношенной винтовой поверхностью, ролики с изношенной внутренней поверхностью и поверхностью сопряжения с червяком, оси и изношенные игольчатые подшипники ролика не восстанавливают и при износах, более допустимых, выбраковывают.
У тракторов зубчатые секторы сошек при износе зубьев и внутренних шлицев заменяют.
Ремонт Передних мостов (не ведущих). У автомобилей наблюдается изгиб и скручивание балки передней оси. Такие балки правят под прессом или на специальных стендах, вхолодную.
|
|
Деформированные и выпрямленные оси контролируют при помощи специального приспособления, схема которого изображена на рисунке.
При изгибе балки передней оси стрелки вилок отклоняются от нулевого положения на шкале, соответствующего нормальному наклону шкворней. Шкалы укреплены на трубах. Труба входит внутрь трубы. Под действием пружины трубы раздвигаются, благодаря чему призмы вилок прижимаются к калибрам-шкворням.
Скрученность оси определяют по шкале. Приспособление настраивают и проверяют по прилагаемому эталону. Например, нормальный продольный Наклон Шкворня у автомобиля ГАЗ-53А составляет 2° 40', поперечный наклон — 8°. Изгиб балки в горизонтальной плоскости должен быть не более ±1,5°, в вертикальной плоскости ±30', А Допустимые скручивания ±1,5°.
У колесных тракторов Т-25, Т-40, Т-40А, МТЗ-80, где передняя ось представляет собой стальную литую балку, телескопически соединенную с выдвижными трубами поворотных цапф, изнашиваются отверстия под ось качания. Ремонт может быть проведен рассверливанием и развертыванием отверстий под увеличенную ось качания или под промежуточную втулку.
Износы поверхностей в соединении передней балки с выдвижными трубами устраняются расточкой отверстий в балке до выведения следов износа с наращиванием выдвижных труб железнением или вибродуговой наплавкой и последующей механической обработкой.
Остальные дефекты передних мостов колесных тракторов и автомобилей аналогичны.
При износе отверстий в передних балках под шкворни или под втулки вала поворотных цапф их растачивают или рассверливают и развертывают под переходные стальные втулки. Втулки запрессовывают с натягом 0,2 мм, растачивают или рассверливают в сборе с балкой и развертывают под номинальный размер. Балку передней оси устанавливают на стол станка со специальным установочным приспособлением (или кондуктором при сверлении), которое обеспечивает необходимый наклон оси отверстия под шкворень.
Отверстие во втулках под шкворень в поворотной цапфе автомобиля (или втулки в кронштейнах труб передних осей колесных тракторов) совместно развертывают или обрабатывают протягиванием. Несоосность отверстий допускается не более 0,01 мм. Изношенные отверстия под стопорные клинья шкворней развертывают под клинья увеличенного размера. При износе площадок под рессоры их подвергают фрезерованию.
У поворотных цапф изнашиваются посадочные места под внутренние обоймы подшипников, отверстия во втулках под шкворень, резьба под гайку. Для восстановления деталей ходовой части и, в частности, поворотных цапф следует применять железнение или электромеханическую обработку (ЭМО). Таким способом восстанавливают посадочные места под подшипники у поворотных цапф, шкворни, оси качания и т. д.
Поврежденную резьбу на цапфах восстанавливают вибродуговой наплавкой.
У валов поворотных цапф колесных тракторов изнашиваются шлицы. Для восстановления шлицевой конец цапфы протачивают, из стали 45 изготавливают шлицевую втулку, закаливают и напрессовывают ее на поворотную цапфу. Оба конца втулки приваривают к цапфе.
Сферические пальцы, пробки и пружины сочленений рулевых тяг при их износе заменяют. Рулевые тяги, имеющие изгиб, должны быть выпрямлены.
Ремонт тормозных систем. У тормозных систем тракторов и автомобилей наблюдаются следующие основные дефекты: износы поверхностей трения тормозных барабанов или дисков, фрикционных накладок колодок, дисков или лент (в зависимости от конструкции тормоза), шеек тормозных рычагов, осей колодок, пальцев, а также сопряженных с ними отверстий в корпусах и в кронштейнах разжимных кулаков; износы и повреждения цилиндров, поршней, манжет, штоков, диафрагм, клапанов у механического и гидравлического приводов тормозов; повреждения и разрывы шлангов, трубопроводов, неисправности компрессора (К-700, К-701, Т-150К, ЗИЛ-130).
Тормозные барабаны и диски при неравномерном износе рабочей поверхности, сопрягаемой с фрикционными накладками колодок, дисков или лент, или при задирах глубиной более 0,5 мм протачивают на токарном станке до выведения следов износа. Барабан протачивают в сборе со ступицей, установив его в центры станка на конусной оправке. Тормозные барабаны тракторов при зазоре между барабаном и колодками более 3 мм следует восстанавливать расточкой и постановкой промежуточных колец с приваркой их по окружности.
Неплотность прилегания накладок к тормозным колодкам и лентам допускается до 0,5 мм. Накладки тормозных колодок, дисков или лент, изношенные до предельной толщины, а также имеющие другие дефекты (выкрашивания, трещины, отрывы от заклепок), заменяют, приклепывая новые с помощью полых медных заклепок или винтов с гайками (тракторы К-700, Т-150К) или наклеиванием клеем ВС-ЮТ с помощью приспособления. Заклепки ставят головками к накладкам. Неравномерно изношенные и имеющие задиры поверхности тормоза барабана и шкива протачивают. При протачивании между колодкой и фрикционной накладкой устанавливают прокладку, толщина которой должна быть равна половине разности диаметров проточенного и нового барабанов. Приклепанные или приклеенные накладки тормозных колодок для лучшей прилегаемости к барабану следует обтачивать снаружи. После приклепывания и обточки накладок головки заклепок или винтов должны утопать в накладках на 2...3 мм. У работавших накладок головки заклепок должны утопать не менее чем на 0,5 мм. При меньшем утопании заклепки осаживают.
Изношенные оси колодок и разжимных кулаков шлифуют на ремонтный размер либо восстанавливают железнением или вибродуговой наплавкой высокоуглеродистыми проволоками с последующим шлифованием на номинальный или увеличенный размер. Изношенные отверстия в корпусах и кронштейнах развертывают под оси и пальцы увеличенного размера либо рассверливают для постановки промежуточной втулки с отверстием номинального или уменьшенного размера. Пневматические приводы тормозов тракторов К-700, К-701, Т-150К и Автомобиля ЗИЛ-130. Основными составными частями пневматических приводов является: компрессор, баллоны, тормозной кран, тормозные камеры колес. Технология ремонта компрессора во многом аналогична ремонту двигателей внутреннего сгорания. Обкатку и испытание компрессора проводят на специальном стенде при частоте вращения вала компрессора 1200... 1350 об/мин. Давление подводимого к компрессору масла должно быть 0,12...0,25 МПа при температуре 40...50°С.
При частоте вращения коленчатого вала 1200... 1350 об/мин и сообщении баллона с атмосферой через калиброванное отверстие диаметром 1,6 мм манометр должен показывать давление в баллоне не менее 0,58 МПа. Количество масла, вытекающего через сливное отверстие крышки картера компрессора при открытом калиброванном отверстии), должно быть не более 500 г в течение 5 мин.
У комбинированного тормозного крана могут быть следующие дефекты: повреждения диафрагмы, неплотная посадка клапанов, поломка или потеря упругости пружин, износ уплотнений, отсутствие герметичности соединений, нарушение регулировок.
Свободный ход рычага крана и рычага ручного привода, который должен быть 1...2 мм, регулируется болтами.
Рабочий ход штока секции тормозного крана прицепа должен быть не более 5 мм, регулируется болтом. Рабочий ход впускных клапанов устанавливается при помощи прокладок в пределах 2,5...3,0 мм. После сборки проводят испытание тормозного крана на специальной установке. При закрытом вентиле и резком нажатии до отказа на рычаг показания манометра должны возрасти от нуля до показания второго манометра, а на манометре давление должно упасть до нуля. Показания манометров 1 и 2 в течение 1 минуты не должны изменяться. При резком отпускании рычага давление по манометру 2 должно резко упасть до нуля, а по манометру 1 резко подняться до 0,46...0,53 МПа. При иной величине давления проводят регулировку, вращая направляющую штока. Контакты стоп-сигнала должны включаться при давлении 0,019...0,078 МПа, что определяется по контрольной лампе и манометру 2. Предохранительный клапан регулируют на давление 0,87.. .0,92 МПа. Регулятор должен включаться при повышении давления в пневматической системе до 0,68...0,72 МПа, при этом компрессор прекращает подачу воздуха в пневмосистему. При давлении 0,54...0,65 МПа подача воздуха в систему должна возобновиться.
Тормозные камеры с поврежденной диафрагмой заменяют. У тормозных камер регулируют расстояние от корпуса камеры до оси отверстия под палец в вилке штока.
Гидравлический привод тормозов автомобиля ГАЗ-53А. У автомобилей с гидроприводом тормозов изнашиваются рабочие поверхности главного тормозного и колесных цилиндров, манжета и поршни. Главный тормозной цилиндр, изношенный более допустимого, растачивают на увеличенный ремонтный размер либо растачивают и запрессовывают в него стальную или чугунную гильзу.
Изношенные тормозные цилиндры колес либо растачивают, либо обрабатывают протяжками. Алюминиевые поршни раздают при помощи пуансона и затем обтачивают, установив на специальную оправку. Поршни цилиндров также успешно восстанавливают заливкой капрона под давлением. При сборке колесных цилиндров увеличенного диаметра между резиновой манжетой и пружиной устанавливают дополнительно изготовленный алюминиевый конус. Этим достигается плотное прижатие манжеты нормального размера к цилиндру.
У главного тормозного цилиндра после сборки вращением гайки толкателя регулируют зазор между толкателем и поршнем (свободный ход толкателя), который должен быть в пределах 1,5...2,5 мм, чему соответствует свободный ход педали у автомобиля ГАЗ-53А от 8 до 14 мм. Собранные цилиндры заполняют тормозной жидкостью и испытывают на специальных стендах или приспособлениях. Плотность сопряжений должна быть обеспечена под давлением 8,7.. .9,8 МПа.
Шланги и трубопроводы тормозных систем, имеющие повреждения, заменяют.
Колеса. Изношенные посадочные места в ступицах колес под наружные кольца подшипников качения восстанавливают местным железнением или расточкой и запрессовкой промежуточных колец, которые затем растачивают на номинальный размер. Трещины в дисках колес заваривают. Изношенные отверстия диска под шпильки заваривают, рассверливают и зенкуют. Изгибы обода и диска выправляют. Шпильки колес при наличии дефектов заменяют.
Для устранения вибрации колес после ремонта проводят балансировку их в сборе с шиной на специальных стендах либо на собранном автомобиле. Дисбаланс устраняют перемещением или постановкой и снятием балансировочных грузиков.
Ремонт пневматических шин. В процессе работы (движения) и неправильного хранения у пневматических шин появляются различного рода повреждения и разрушения. К ним относятся: проколы, прорывы и разрезы покрышек и камер; износ и отслоение протектора; отслоение боковин от каркаса; разрыв и оголение проволочного сердечника борта; разрыв нитей и расслоение каркаса; повреждение вентилей. Кроме этого, у пневматических шин под воздействием солнечных лучей и высокой температуры происходит процесс старения резины — она становится более твердой и хрупкой, покрывается сеткой мелких трещин. При попадании на покрышки или камеры нефтепродуктов резина набухает и теряет механические свойства; при длительном воздействии влаги подгнивают нити корда и др.
Ремонт камер. Ремонту могут подвергаться камеры, имеющие проколы, разрывы, прорезы до величины, допускаемой техническими условиями. Например, для камер автомобиля ЗИЛ-130 допускается два разрыва длиной до 180 мм и шириной до 30 мм. Минимально допустимое расстояние между краями разрывов 1000 мм.
Камеры с явными признаками старения резины (затвердевшая, трескающаяся при изгибе) и пропитанные нефтепродуктами выбраковывают.
Для обнаружения повреждений, незаметных для глаза (проколы), камеры проверяют в ванне с водой. Наполненную воздухом камеру погружают в воду, место прокола определяют по пузырькам выходящего воздуха.
Проколы и разрыв камер обычно ремонтируют наложением заплат из сырой камерной резины либо вулканизированной резины из утильных камер, не имеющей признаков старения или разъедания нефтепродуктами. Проколы и разрывы до 30 мм рекомендуется заделывать заплатами из сырой резины, а более 30 мм — заплатами из вулканизированной резины. На прорывах закругляют ножницами острые углы, придав им овальную форму. Поверхность камеры вокруг повреждения зачищают абразивным кругом на шероховальном станке или вручную рашпилем, скашивая кромки величиной 10... 15 мм вокруг повреждения.
Заплату вырезают такого размера, чтобы она на 20...30 мм перекрывала края повреждения. Заплата из выбракованной камеры подвергается шероховке с внутренней стороны.
При заделке повреждения используют резиновый клей различных концентраций: 1:5; 1:8 (отношение массы клеевой резины к массе бензина). Для приготовления клея клеевую резину нарезают кусочками (12x12 мм), засыпают в герметически закрывающуюся тару и заливают бензином сорта «Калоша»; резина набухает в течение 20...24 ч. Затем добавляют бензин до требуемой концентрации и содержимое перемешивают. Срок хранения клея до одного месяца.
С шероховатых поверхностей камеры и заплаты удаляют пыль, промазывают их 2 раза клеем концентрации 1:8 с просушкой после каждой промазки в течение 25...30 мин при температуре 30...40°С в сушильной камере. После этого накладывают заплату на подготовленный участок и прокатывают роликом от середины к краям. Под заплатой не должно быть воздуха. Место вулканизации припудривают тальком или наносят мыльный раствор. Вулканизацию камер проводят на плите вулканизационного аппарата. Камеру укладывают заплатой на плиту и через деревянную накладку прижимают к плите пинолью. Края камеры не должны быть прижаты к плите. Время вулканизации 15...20 мин, температура 143...145°С.
Ремонт покрышек. Технологический процесс ремонта покрышек состоит из следующих операций: приемка в ремонт, мойка, дефектовка, вырезание поврежденных мест, сушка, шероховка, заделка повреждений, вулканизация. Не принимают в ремонт покрышки, у которых порван или оголен металлический сердечник борта, резина разрушена нефтепродуктами, а также покрышки с расслоившимся кордом, прелыми нитями корда и состарившейся резиной. Не принимаются в ремонт также покрышки при высоте рисунка протектора менее 20% номинала у тракторных и 10% у автомобильных и комбайновых покрышек.
Покрышки моют в моечных машинах или вручную водой и щетками. После мойки покрышки дефектуют и отмечают места повреждений. Для дефектовки покрышек, а также для вырезки мест повреждения и шероховки используют борторасширители.
Крупные повреждения (более 25 мм по диаметру или прямоугольники размером более 25x50 мм) вырезают. Повреждения меньших размеров только шерохуют. Повреждения вырезают обычно «наружным» конусом при несквозных повреждениях снаружи, внутренним» конусом при малом повреждении снаружи и большом внутри и «встречным» конусом при сквозном повреждении. После вырезки повреждения проводят сушку покрышки в сушильной камере.
Зашерохованный участок должен выходить за края обрезки на 15...20 мм. Шероховку проводят абразивными кругами с гибким валом, дисковыми фрезами, игольчатыми дисками, рашпилями и т. д. С шероховатой поверхности удаляют пыль.
Для заделки сквозных повреждений изготовляют манжету из выбракованной покрышки. Кромки манжеты скашивают и проводят шероховку ее поверхности. На подготовленные поверхности покрышки и манжеты наносят слой клея концентрации 1 : 8. После полного высыхания (30...40 мин) наносят второй слой клея концентрации 1 : 5 и снова дают просохнуть.
Для заделки повреждений, кроме манжеты, применяют прослоечную и протекторную резину, на которую также наносят клей концентрации 1 : 8. Схема заделки повреждения показана на рисунке.
Заделанное повреждение вулканизируют при температуре 143... 145°С. Время вулканизации от 40 до 180 мин в зависимости от характера повреждения. Вулканизацию проводят как на паровых вулканизационных аппаратах, так и на электровулканизаторах различных моделей аналогично технологии восстановления камер.
На специализированных ремонтных предприятиях у покрышек проводят замену изношенного протектора. Старый протектор срезают и на специальном станке приклеивают к покрышке и прикатывают прослоечную, а затем протекторную резину. После этого покрышку вулканизируют в паровом кольцевом вулканизаторе — в пресс-форме, востанавливающей рисунок протектора.
У гусеничных машин быстрее всего изнашиваются опорные поверхности направляющих колес, опорные катки, поддерживающие ролики и звенья гусеничной ленты.
Наружную поверхность обода направляющих колес, катков и роликов восстанавливают наплавкой под слоем флюса. Трещины на ободе и спицах колес заваривают. Изношенные посадочные места под подшипники восстанавливают наплавкой с последующей их обработкой на токарных станках под нормальный размер.
У колесных машин чаще всего повреждаются покрышки и камеры. Эти дефекты устраняют на специальном рабочем месте, оборудованном инструментом ЦКБ-6209.
Покрышки ремонтируют в таком порядке. Поврежденные слои резины и нити каркаса вырезают. По размерам вырезанного участка готовят заплату, тщательно обрабатывают место наложения заплаты и саму заплату, затем наносят слой клея, накладывают заплату и устанавливают покрышку в вулканизационный аппарат. Температура вулканизации 140... 145 °C, а ее продолжительность в минутах определяют, умножив толщину вулканизуемого слоя на семь.
У камер чаще всего встречаются такие дефекты, как проколы, прорывы и повреждения в местах крепления вентиля.
Перед ремонтом камеру очищают от грязи и пыли и находят место повреждения. Если повреждение не удается установить при внешнем осмотре, камеру накачивают воздухом и погружают в ванну с водой. Пузырьки выходящего воздуха укажут место повреждения.
Если повреждение крупное, трещины длинные, а проколы рваные, кромки камеры обрезают ножницами, придав вырезу овальную или круглую форму. При небольших и ровных проколах камеру обрезать не следует.
Обрезанные края поврежденной камеры счищают рашпилем; поверхность камеры вокруг места повреждения зачищают рашпилем на 30 мм.
Повреждения размером до 30 мм ремонтируют сырой резиной, а при больших размерах ставят заплату из утильных камер, размеры которой должны быть такими, чтобы она перекрывала отверстие в камере на 20...25 мм и была меньше зачищенного участка на 3...5 мм со всех сторон. Поверхность заплаты надо зашероховать рашпилем с одной стороны, а края счистить.
Затем чистой тканью, смоченной бензином, протирают зашерохованную поверхность вокруг отверстия в камере и заплату и намазывают резиновым клеем. Дают клею подсохнуть, намазывают еще раз зашерохованную часть камеры и заплату и опять дают им подсохнуть. Накладывают на камеру заплату и тщательно прикатывают ее роликом.
Камеру складывают так, чтобы поврежденное место оказалось посередине; заплату и плиту электровулканизатора опудривают тальком. Камеру укладывают на плиту электровулканизатора заплатой вверх, кладут на нее электроплиту и винтом прижимают ее к плите приспособления (рис. 26.19).
Рис. 26.19. Вулканизация протектора:
- 7 - покрышка; 2 — прижимающее устройство;
- 3 — профильная алюминиевая прокладка; 4 — слой ремонтных материалов; 5 — форма для подвода тепла
При ремонте камер сырой резиной вырезают из нее заплату, чтобы она перекрывала отверстие в камере на 10... 12 мм; зашерохованную поверхность вокруг отверстия камеры и заплату протирают чистой тряпкой, смоченной бензином. Камеру складывают так, чтобы поврежденное место оказалось посередине. Затем камеру укладывают на плиту электровулканизатора повреждением вверх; на отверстие в камере накладывают заплату из сырой резины; опудривают заплату и плиту злектровулкани-затора тальком и винтом прижимают ее вместе с камерой к плите приспособления. Затем включают электроплитку и замечают время. При толщине заплаты 2 мм электроплитку выключают через 25 мин, камеру снимают с приспособления, края заплаты зачищают, камеру накачивают воздухом и проверяют ее в ванне с водой.
Небольшие покрышки снимают и надевают на колеса с помощью монтажных лопаток, а большие — приспособлением ПИМ-746.
Червяки и ролики механизма управления колесных машин, имеющие износ более установленных размеров, выбраковывают. Подшипники заменяют новыми. Шейки вала сошки восстанавливают хромированием, осталиванием или устанавливают втулку.
При сборке рулевых управлений важно обеспечить нормальный зазор в подшипниках и зацепление червяка с роликом и сходимость передних колес. Сходимость передних колес экскаватора ЭО-2626 должна обеспечиваться разностью размеров (8... 10 мм), измеренных в задней и передней частях колеса на уровне оси. Сходимость регулируют, изменяя длину поперечной тяги рулевого управления.
Ремонт ходовой части гусеничных тракторов
Детали ходовой части гусеничных тракторов подвергаются абразивному изнашиванию. Потеря массы и размеров деталей составляет значительную долю.
Ремонт и восстановление опорных катков, поддерживающих роликов и направляющих колес. Основные дефекты указанных деталей проявляются в виде износа поверхностей качения, трещин обода или спиц, износа поверхности посадочных мест под наружное кольцо подшипника качения. У поддерживающих роликов с резиновыми бандажами наблюдается разрушение бандажей. Изношенные и нарушенные резиновые бандажи заменяют.
Восстановление наплавкой. Изношенные поверхности качения поддерживающих роликов, опорных катков и направляющих колес восстанавливают наплавкой электродуговыми способами — проволокой НП-ЗОХГСА под слоем керамического флюса АНК-18, порошковой проволокой ПП-АН122 или порошковой лентой ПЛ-АН 101. Опорные катки тракторов Т-4 и Т-4А обрабатывают по наружному диаметру электроконтакт-ным способом. Под действием напряжений, возникающих в результате наплавки, происходит уменьшение внутреннего диаметра отверстия под подшипники опорного катка и поддерживающего ролика. Остаточные деформации отверстий под подшипники обычно таковы, что оказываются достаточными для компенсации износа поверхности в соединении с подшипником. В таком случае отверстия растачивают, а у опорных катков трактора Т-4 обрабатывают на протяжном станке.
Бандажирование. В условиях мелкосерийного производства для восстановления поддерживающих роликов и опорных катков тракторов ДТ-75 применяют бандажирование. Рабочую поверхность катка или ролика протачивают до выведения следов износа из полосовой стали (сталь 45) толщиной 8... 10 мм, достаточной для компенсации износа, с помощью гибочного приспособления изготавливают кольцо. Стык кольца сваривают вручную электросваркой, а внутреннюю его поверхность растачивают до размера, обеспечивающего посадку кольца на ободе с натягом 0,15...0,25 мм. На обод напрессовывают кольцо при температуре последнего 300...400 °C и приваривают с двух сторон по торцу вкруговую. Износостойкость восстановленных бандажированием катков составляет 0,5...0,6 от уровня новых.
Восстановление электрошлаковой наплавкой. На специализированных предприятиях применяют восстановление ободов катков и роликов электрошлаковой наплавкой. Опорные катки, восстановленные электрошлаковой наплавкой, по износостойкости не уступают новым.
Заливка жидким металлом. Для восстановления опорных катков в условиях специализированных предприятий может быть использована заливка металлом - сталью или чугуном. Поверхность обода тщательно зачищают до металлического блеска, наносят слой специального флюса (АНШ-200, АНШ-40Э, разведенный на лаке № 302) толщиной 1...2 мм и просушивают. Каток подогревают до 400...800 °C, устанавливают в подогретый до 200...300 °C кокиль (чугунная форма) и заливают расплавленный (перегретый) металл.
Заварка трещин. Трещины на ободе и спицах опорных катков и направляющих колес устраняют сваркой.
Постановка втулки. Изношенные поверхности под подшипники в ступицах опорных катков, поддерживающих роликов и направляющих колес восстанавливают постановкой промежуточной втулки с толщиной стенки 3...4 мм или железнением.
Восстановление ведущих колес. Ведущие колеса гусеничных машин с односторонним износом зубьев при текущем ремонте переставляют на другую сторону трактора.
В условиях мелкосерийного (единичного) производства изношенные зубья ведущих колес восстанавливают наплавкой вручную.
На специализированных предприятиях восстанавливают целиком венец ведущего колеса приваркой накладок (рис. 26.20).
Рис. 26.20. Схема приварки накладок для восстановления венца ведущего колеса: 1 — накладка (сектор); 2 — сварной шов
Для этого с помощью специального копирного устройства зубчатый венец колеса обрезают плазменной или газовой горелкой. К выровненному по копиру венцу ведущего колеса приваривают компенсационные элементы. Из полосы стали 45 в специальном штампе изготовляют вкладыши и собирают их вместе с подготовленным колесом в кондукторе-манипуляторе (или прихватывают ручной сваркой). После сборки колесо сваривают с вкладышами под слоем флюса по всему контуру с двух сторон.
Восстановление гусениц. Изношенные пальцы гусеничной цепи заменяют. У звена гусеницы изнашиваются поверхности отверстий проушин (допускается до толщины стенки 3,5 мм), цевки в местах соприкосновения с зубьями ведущего колеса (допустимый износ цевки 7 мм), беговые дорожки, почвозацепы.
При восстановлении звеньев гусениц наибольшее распространение получили способы пластического деформирования, заливки жидким металлом, электродуговой наплавки. Наилучшие показатели качества восстановления обеспечивает способ пластической деформации, применяемый на специализированных линиях.
Пластическая деформация. Звенья очищают в галтовочном барабане. При галтовке с их поверхности удаляется грязь и ржавчина, выявляются трещины. Одновременно очищают партию в 60 звеньев, время обработки — 40 мин. Дефектуют звенья с помощью калибров и шаблонов. Нагревают их в два приема: сначала подогревают до температуры 350...400 °C, затем выдерживают 5 мин в расплаве соли (хлористого бария), нагретой до температуры 1000... 1050 °C в соляной электродной печи.
Нагретое звено подают в разъемный штамп с регулируемым рабочим объемом каждой секции. Штамп работает от двенадцатипозиционного гидравлического агрегатного пресса с общим усилием на шпинделе 60 МН. Время горячей деформации звена в штампе — 5...6 с.
Закаливают звенья холодной проточной водой.
Заливка жидким металлом. Способ используется для восстановления звена в том случае, если нет возможности реализовать пластическое деформирование. С помощью электрической дуги угольным электродом в стенке проушины звена со стороны наибольшего износа прожигают технологическое отверстие, в проушину вставляют технологический стержень и закупоривают ее с обеих сторон огнеупорной глиной. Металл расплавляют в тиглях или с помощью ТВЧ и заливают в проушины через технологические отверстия. Он заполняет изношенную полость проушины и, кристаллизуясь, образует вкладыш, удерживаемый за счет неравномерно изношенной поверхности проушины и своеобразной заклепки, образованной застывшим в технологическом отверстии металлом.
Ремонт элементов ходовой части тракторов типа Т-170. Изношенные втулки и пальцы гусениц не восстанавливают. Беговую дорожку звена восстанавливают наплавкой, поверхности под палец и втулку не восстанавливают. Изношенные почвозацепы наплавляют до нормальной высоты или приваривают к их вершинам прутки. Звенья гусениц восстанавливают только на специализированных предприятиях с программой, обеспечивающей окупаемость технологических линий в нормативные сроки.
Разборка и сборка ходовой части. Для разборки и сборки элементов ходовой части используют стенды и приспособления.
Разборка кареток. Каретки тракторов ДТ-75 устанавливают в удобное положение и начинают разборку со сжатия и снятия рессорных пружин, используя приспособления. После этого снимают катки и остальные детали, применяя съемники, прессы и т. д.
Для разборки кареток предназначены стенды ОП Р-1402М. С помощью гидроцилиндра и комплекта приспособлений можно сжимать пружины и выполнять прессовые работы: выпрессовывать и запрессовывать втулки балансиров, снимать с осей и напрессовывать на них опорные катки, напрессовывать и снимать подшипники и т. д. Повернув стол вместе с кареткой на 90°, гайковертом отвертывают и завертывают гайки крепления катков.
Сборка опорных катков. При сборке опорных катков, поддерживающих роликов и направляющих колес регулируют их продольный разбег на оси или зазор в конических роликовых подшипниках. Для регулировки ставят прокладку (направляющее колесо и опорный каток трактора ДТ-75) или вращают регулировочную гайку на оси (направляющее колесо ДТ-75, поддерживающий ролик трактора Т-4, Т-4А).
Сборка механизма натяжения гусениц. При сборке механизма натяжения гусениц пружину натяжного устройства сжимают с помощью стенда или пресса до определенной длины (640 мм для ДТ-75; 652 мм для Т-4, Т-4А). Перед навертыванием гаек резьбу стяжного болта смазывают солидоло-графитовой смазкой.
Сборка тележек. Тележку гусениц тракторов Т-4, Т-4А собирают на специальной подставке или стенде, позволяющем поворачивать ее вокруг продольной оси. Сборку начинают со сборки рамы, установки амортизатора рессоры и опорных катков. Первым, третьим и пятым по ходу трактора должны быть установлены двубортные катки, а вторым, четвертым и шестым — однобортные. После монтажа опорных катков на их беговые дорожки накладывают линейку (рейку). Зазор между линейкой и минимальным по диаметру катком не должен превышать 1,5 мм. Допускается установка прокладок под ось катка в местах ее крепления.
Сборка гусениц. Гусеницы тракторов тягового класса 3 в условиях мастерских собирают вручную на специальных подставках, а на ремонтных предприятиях с большой программой используют гидрофицированные стенды, обеспечивающие механизированную запрессовку (выпрессовку) пальцев и дискретное перемещение гусеницы на один шаг.
Дата добавления: 2021-03-18; просмотров: 213; Мы поможем в написании вашей работы! |
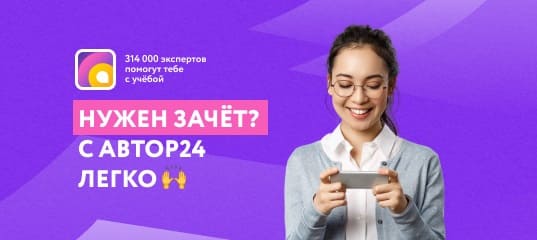
Мы поможем в написании ваших работ!