Причины изменения технического состояния
Понятие о техническом состоянии автомобиля
Автомобиль представляет собой сложную техническую систему, предназначенную для осуществления транспортной деятельности и характеризуемую множеством параметров, определяющих технические и эксплуатационные показатели данной системы Под системой понимается упорядоченная совокупность совместно действующих элементов, предназначенных для выполнения заданных функций. По отношению к автомобилю элементами являются агрегаты, узлы, механизмы и детали — объекты или изделия.
Все элементы автомобиля (агрегаты, узлы, механизмы, детали) имеют различные характеристики устойчивости к потере работоспособного состояния, на которые влияют как внутренние конструктивные факторы, зависящие от назначения и свойств элемента, так и совокупность внешних факторов, определяемых как условия эксплуатации автомобиля. Так, современный автомобиль состоит из 15...20 тыс. деталей, из которых 7...9 тыс. теряют свои первоначальные свойства при работе, причем около 3...4 тыс. деталей имеют срок службы меньший, чем у автомобиля в целом. Из них 80... 100 деталей влияют на безопасность движения, а 150... 300 деталей, ≪критических≫ по надежности, чаще других требуют замены, вызывают наибольшие простои автомобилей, ресурсные затраты в эксплуатации.
Работоспособность элементов автомобиля определяется его техническим состоянием. Техническое состояние представляет собой совокупность изменяющихся в процессе эксплуатации свойств объекта, характеризуемых в определенный момент признаками, установленными технической документацией. Техническое состояние автомобиля и его элементов определяется количественными показателями конструктивных параметров: y1; у2 ; у3, ..., уп.
|
|
Например, для двигателя это размеры деталей цилиндропоршневой группы и кривошипно-шатунного механизма, для тормозов — толщина тормозных накладок, диаметров тормозных барабанов и зазоров между ними.
Возможность непосредственного измерения конструктивных параметров многих изделий без частичной или полной разборки узла чаще всего ограничена. Для этих изделий при определении технического состояния пользуются косвенными величинами, так называемыми диагностическими параметрами, связанными с кон-структивными параметрами и дающими о них определенную информацию. Например, о техническом состоянии двигателя можно судить по изменению его мощности, расходу масла на угар, компрессии, содержанию продуктов износа в масле.
В процессе работы автомобиля показатели его технического состояния изменяются от начальных ун, соответствующих новому изделию, до предельно допустимых у'пд, а затем и до предельных уп. Значение уп соответствует предельному состоянию, при котором его дальнейшее применение по назначению недопустимо или нецелесообразно (рис. 1.1).
|
|
Продолжительность работы изделия, измеряемая в часах или километрах пробега, а в ряде случаев в единицах выполненной работы, называется наработкой Іі,. Наработка до предельного состояния, оговоренного технической документацией, называется ресурсом Ір. Тогда в интервале пробега 0 ≤ , Іі ≤ Ір при ун < уі, < уп (зона работоспособности) изделие считается исправным и может выполнять свои функции.
Если изделие удовлетворяет требованиям нормативно-технической документации по всем показателям, то оно считается исправным. Если параметры изделия, характеризующие его способность выполнять заданные функции, соответствуют установленным нормативно-технической документацией требованиям, то онопризнается работоспособным. Отсюда следует, что когда автомобиль может выполнять свои основные функции, но не отвечает всем требованиям технической документации (например, помято крыло), он работоспособен, но неисправен.
Рис. 1.1. Изменение состояния элемента в зависимости от значений
|
|
параметров состояний__
Если продолжать эксплуатировать автомобиль до состояния у, > уп, то наступит отказ, т.е. событие, заключающееся в нарушенииработоспособности.
В этом случае прекращается транспортный процесс (остановка на линии, преждевременный возврат с линии).
Роль предельно допустимого значения параметра заключается в том, чтобы своевременно обнаруживать (предупреждать) приближение момента отказа для принятия соответствующих мер.
Для своевременного предупреждения отказа элемента автомобиля необходимо иметь представление о причинах изменения его технического состояния и о факторах, определяющих проявление этих причин, а также их влиянии на интенсивность изменения технического состояния элементов автомобиля.
Причины изменения технического состояния
В процессе эксплуатации автомобиль взаимодействует с окружающей средой, а его элементы взаимодействуют между собой. Это взаимодействие вызывает нагружение деталей, их взаимные перемещения, вызывающие трение, нагрев, химические и другие преобразования и, как следствие, изменение в процессе работы физико-химических свойств и конструктивных параметров: состояния поверхностей, размеров деталей и их взаимного расположения, зазоров, электрических и других свойств.
|
|
Работоспособность автомобиля (и его элементов) зависит от всех видов воздействий, оказывающих влияние на его техническое состояние в каждый момент ≪жизненного≫ цикла:
механических (статические, динамические нагрузки от взаимодействия с внешней средой);
тепловых (температура окружающего воздуха, теплообразование при рабочих процессах);
электромагнитных;
химических (коррозия от продуктов сгорания топлива и других эксплуатационных материалов);
атмосферных (атмосферная коррозия).
Причины, вызывающие изменение технического состояния автомобиля, могут быть разделены на две группы: случайные и постоянного действия (рис. 1.2).
Случайные (стохастические) изменения могут возникать в результате непрогнозируемых поломок вследствие неправильной эксплуатации, некачественного хранения и обслуживания, некачественных комплектующих, а также в результате дорожно-транспортного происшествия (ДТП).
Причинами постоянного (монотонного) изменения технического состояния могут являться: износ, коррозия, старение и накопление отложений.
Рис. 1.2. Классификация причин изменения технического состояния
элементов автомобиля
Износ — степень изменения размеров и веса деталей. Он зависит от материала детали (ее физико-химических свойств), характера взаимодействия деталей (рода и вида трения, геометрии контакта, макро- и микрогеометрии поверхностей трения, посадки сопряженных деталей), нагрузки (статической, динамической), химического воздействия, продолжительности воздействия.
Структурным проявлением износа является изнашивание. Изнашиванием называются процессы постепенного изменения веса и размеров элементов автомобиля, возникающие вследствие трения сопряженных деталей.
Внешнее трение (или просто трение) есть явление сопротивления относительному перемещению, возникающему между двумя телами в зонах соприкосновения поверхностей по касательным к ним (рис. 1.3),
Изнашивание делится на механическое, молекулярно-механическое и коррозионно-механическое (рис. 1.4).
Механическое изнашивание возникает в результате механических воздействий и подразделяется на абразивное, эрозионное, кавитационное и изнашивание при фреттинге.
Абразивное изнашивание — наиболее распространенный вид механического изнашивания. Причиной абразивного изнашивания является попадание абразивных частиц на трущиеся поверхности. Абразивные частицы могут быть внешнего (песок, пыль) и внутреннего (продукты износа — стружка, сколы, механическая пыль) происхождения. Чаще обе группы частиц участвуют в процессе износа одновременно. При попадании абразивных частиц на трущиеся поверхности происходит резание, царапанье и разрушение поверхности с отделением продуктов износа, которые, в свою очередь, увеличивают интенсивность износа. Примером абразивного износа является изнашивание тормозных колодок автомобиля.
Разновидностью абразивного износа является гидро- и газоабразивное изнашивание, которое возникает в результате действия твердых частиц, взвешенных в жидкости (газе) и перемещающихся относительно изнашивающегося тела.
Другими видами механического изнашивания являются:
• эрозионное (гидро-, газоэрозионное) изнашивание материала, происходящее в результате воздействия потока жидкости и (или) газа на деталь;
• кавитационное изнашивание, происходящее при движении твердого тела относительно жидкости (разновидность гидроэрозионного изнашивания);
• изнашивание при фреттинге — вид механического изнашивания соприкасающихся тел в условиях малых относительных (колебательных) перемещений (наклеп, выкрашивание). Изнашивание при фреттинге происходит вследствие вибраций контактирующих поверхностей или периодических деформаций деталей. При этом виде коррозионно-механического изнашивания имеет место интенсивное абразивное разрушение.
Различают следующие типы коррозионных разрушений металла (рис. 1.5): равномерное (а), коррозия пятнами (б), коррозия язвами (в), коррозия точками (г), коррозионное растрескивание (д), подповерхностная коррозия (е). Для прочности деталей особо опасны коррозия точками и коррозионное растрескивание.
Молекулярно-механическое изнашивание делится на адгезионное и изнашивание при заедании.
Адгезионное изнашивание (адгезия -— взаимное сцепление контактирующих тел под действием молекулярных сил), возникающее в зонах контакта поверхностей интенсивного молекулярного (адгезионного) взаимодействия, связано с переносом материала и образованием прослоек. В результате могут произойти заедание и отказ сопряжения.
Изнашивание при заедании происходит в результате схватывания, глубинного вырывания материала, переноса его с одной поверхности трения на другую и воздействия возникших неровностей на сопряженную поверхность.
При коррозионно-механическом изнашивании вследствие окисления металла кислородом в сопряженных элементах образуется тонкий слой оксида железа (ржавчины), который затем удаляется с поверхности трения трущимися частями. Так как устойчивость окисленной поверхности (ржавчины) к износу значительно ниже, чем у неокисленной поверхности, то интенсивность изнашивания в результате постоянного контакта с окислителем (например, с водой) повышается. При трении качения и значительных деформациях в поверхностных слоях легче проникает кислород и окисляет металл.
Коррозия представляет собой агрессивное воздействие среды на детали, приводящее к окислению металла и уменьшению его прочности, изменению его характеристик и разрушению, а также ухудшению внешнего вида. Коррозия металлов (сплавов) может возникать вследствие электрохимического или химического воздействия внешней среды.
Электрохимическая коррозия возникает в водных растворах кислот, щелочей, солей и во влажной атмосфере.
Химическая коррозия возникает в результате взаимодействия металла со средой (кислородом, водородом, азотом), т. е. атомы металла (сплава) непосредственно соединяются химической связью с атомами окислителей.
К другим постоянно действующим причинам изменения технического состояния элементов автомобиля относятся старение материала и накопление отложений.
Старение материала определяется изменением его свойств от времени и потерей технических и эксплуатационных качеств в независимости от возникающих причин изменения технического состояния элемента. В большей степени это свойство относится к неметаллическим частям автомобиля.
Накопление отложений существенно влияет на ресурс работы элемента автомобиля. Отложение может проявляться в виде накипи (система охлаждения), нагара (свечи системы зажигания), наноса (система смазки), изменяя геометрию элемента и, таким образом, изменяя его технические характеристики. В некоторых случаях накопление отложений может служить причиной отказного состояния элемента.
В результате перечисленных воздействий ухудшается функционирование элементов автомобиля, утрачивается их работоспособность (поломка, износ, деформация, обрыв и т.п.). Наиболее часто нарушение работоспособности обусловлено разрушением агрегатов (узлов) и их элементов, приводящим к потере эксплуатационных качеств и работоспособности машин. Обычно повреждения возникают в том случае, когда внешние воздействия превышают допустимый уровень. Разрушения и повреждения металлических деталей и их сопряжений возникают вследствие физических и химических воздействий.
При физическом воздействии возникают следующие виды разрушений и повреждений:
• деформация — изменение форм и размеров детали под нагрузкой. При этом, если деталь после прекращения действия нагрузки вновь приобретает прежние размеры и форму, то говорят об упругой деформации, в противном случае — о пластической. Пластическая деформация происходит под действием силовых нагрузок, превышающих предел текучести (при изгибе, кручении, растяжении и смятии поверхностей);
• хрупкое разрушение происходит без предварительной деформации и вызывается нормальными напряжениями;
• вязкое разрушение происходит при значительной деформации касательными нагрузками;
• усталостное разрушение (рам, валов, пружин, рессор, шатунов и других деталей) имеет место при циклических нагрузках, связано с пластической деформацией и приводит к полной потере работоспособности элемента;
• тепловое разрушение (головки блока цилиндров, поршней, выпускных коллекторов) происходит в результате значительных нагреваний, приводя к разрушению созданной структуры материалов, т.е. к утрате первоначальных эксплуатационных свойств;
• оплавление некоторых деталей (электроды свечей, контакты прерывателей и т.д.) появляется при электромагнитных воздействиях, когда вследствие искровых разрядов частицы переносятся с анода на катод.
Дата добавления: 2021-02-10; просмотров: 166; Мы поможем в написании вашей работы! |
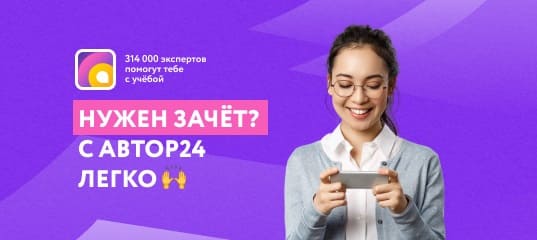
Мы поможем в написании ваших работ!