Современные сталеразливочные системы
Системы разливки стали и сплавов комплектуются современными шиберными затворами линейного и поворотного типа с кассетной конструкцией огнеупоров. Применение композитных материалов существенно повышает стойкость огнеупорного комплекта и сокращает время обслуживания. Исключение вторичного окисления предполагает применение различных конструкций устройств защиты, обеспечивающих наилучшее показатели даже без применения защитной трубы.
Под сталеразливочными системами следует принимать комплекс исполнительных и вспомогательных устройств, осуществляющих автоматическое дозирование расплавленного металла из технологических емкостей (ковши, печи, конвертеры и др.) и обеспечивающих для выполнения данной функциональной цели постоянный и плотный контакт рабочих поверхностей огнеупорных элементов, их самоустановку, своевременную замену расходуемых огнеупорных частей.
Наиболее ответственными расходными комплектующими сталеразливочных систем являются огнеупорные элементы (рис. 1.4), имеющие различную эксплуатационную стойкость в зависимости от физико-химического состава.
Анализ эволюции развития сталеразливочных систем, позволяет сформулировать требования к шиберным затворам нового поколения:
· многоточечный пружинный механизм равномерного прижатия огнеупорных плит,
· увеличенная долговечность узлов и деталей системы,
· наличие системы фиксации огнеупорных плит,
|
|
· минимизация человеческого фактора при эксплуатации системы,
· быстрота и удобство замены огнеупоров.
Рис. 1.4 Огнеупорный комплект шиберного затвора:
1 – гнездовой блок, 2 – ковшевой стакан, 3 – шиберные плиты в обечайке, 4 – стакан-коллектор в обечайке, 5 – уплотнительная вставка, 6 – защитная труба
Применение современных технических решений даёт возможность обеспечить достаточную равномерность приложения прижимного усилия на огнеупорные плиты, обеспечить их самоустановку, компенсировать циклические температурные расширения и износ огнеупорных и металлических деталей затвора, снизить требования к точности изготовления деталей и узлов.
Особенности производства цветных металлов
Получение меди . Медные руды бедные, содержат не более 5–6% меди, поэтому рентабельной считается руда, содержащая 1–2% меди. Основные медные руды: сульфидные (медный колчедан – халькопирит CuFeS2; халькозим – медный блеск CuS) и окисленные (куприт Cu2O; CuO) и некоторые другие.
Процесс получения меди складывается из следующих этапов:
· Обогащение руды путем флотации, основанной на смачиваемости водой породы и несмачиваемости частиц, содержащих медь. В результате получается медный концентрат, содержащий до 30% меди.
|
|
· Обжиг концентрата в пламенных или электрических печах при температуре 1200–13000С.
· Продувка штейна в конвертере воздухом для окисления сульфидов меди и железа, перевода образующихся оксидов в шлак, а серы в SO2 (газ). В результате получают черновую медь, содержащую 98–99% меди и небольшое количество золота, серебра, цинка, свинца, теллура, селена и др. Одновременно из отходящих газов извлекают серу.
· Огневое и электролитическое рафинирование с попутным извлечением золота, серебра, теллура, селена и пр.
Электролитическим рафинированием получают медь чистотой 99,90– 99,99% (марки М1, М0 и М00), огневым рафинированием чистотой 99,0–99,5 (марки М2, М3, М4).
Получение алюминия . Алюминий по распространению в природе занимает третье место после кислорода и кремния, а среди металлов – первое (в земной коре примерно 7,5% алюминия). Для получения алюминия необходимо значительное количество электроэнергии, поэтому его массовое производство стало возможным, когда появились дешевые источники электроэнергии (ГЭС). В начале прошлого века алюминий ценился дороже золота. Первый алюминиевый завод в нашей стране был пущен в 1932 г. на базе Волховской ГЭС.
|
|
Рудами алюминия являются породы, богатые глиноземом Al2O3 и залегающие крупными массами. Важнейшая руда – бокситы состоит из гидратов оксидов алюминия и железа, кремнезема, соединений кальция, магния и др.
Производство алюминия слагается из трех основных процессов:
· Получение глинозема щелочным способом: бокситы обрабатывают щелочью NaOH, фильтруют, обезвоживают обжигом при температуре 1100– 12000С. Одновременно получают криолит Na3AlF6 из плавикового шпата; его отфильтровывают и просушивают в сушильных барабанах.
· Электролиз глинозема в расплавленном криолите при температуре 930–9700С в ванне из углеродистого материала. Катодом служит расплавленный алюминий слоем 200–300 мм на дне ванны, анодом – углеродистые блоки, погруженные в электролит. Процесс идет на постоянном токе напряжением 4–4,5 вольта и силой тока 70–140 тысяч ампер. Алюминий собирается на дне ванны и периодически извлекается; на дне ванны оставляют немного алюминия (катод). В результате электролиза получается алюминий – сырец, содержащий примеси и газы.
· Рафинирование первичного алюминия производят: а) продувкой хлора через расплав алюминия в закрытом ковше. Образующийся парообразный хлористый алюминий обволакивает частички примесей, которые всплывают и их удаляют. Для выделения газов из металла его выдерживают 30–45 мин. при температуре 690–7300С. Чистота алюминия составляет 99,5–99,85%; б) для получения алюминия высокой чистоты (электротехнического) применяют электролитическое рафинирование (электролит – раствор хлористых и фтористых солей; катод – пластины чистого алюминия). Можно получить алюминий чистотой 99,999%. Расход электроэнергии составляет 17–19 кВт∙ч на 1 кг алюминия.
|
|
Производство магния . Подобно алюминию магний получают электролизом из его расплавленных солей.
Основным сырьем для получения магния являются: карналлит (MgCl2∙KCl∙6H20), магнезит (MgCO3), доломит (CaCO3∙MgCO3), бишофит (MgCl2∙6H2O). Наибольшее количество магния получают из карналлита. Сначала карналлит обогащают и обезвоживают. Безводный карналлит (MgCl2∙KCl) используют для приготовления электролита.
Электролиз осуществляют в электролизере, футерованном шамотным кирпичом. Анодами служат графитовые пластины. Электролизер заполняют расплавленным электролитом состава: 10% MgCl2, 45% CaCl2, 30% NaCl, 15% KCl с небольшими добавками NaF и CaF2. Такой состав электролита необходим для понижения температуры его плавления [(720±10)0С]. Для электролитического разложения хлористого магния через электролит пропускают ток. В результате образуются ионы хлора, которые движутся к аноду. Ионы магния движутся к катоду и после разряда выделяются на поверхности, образуя капельки жидкого чернового магния. Магний имеет меньшую плотность, чем электролит, поэтому он всплывает на поверхность, откуда его периодически удаляют вакуумным ковшом.
Черновой магний содержит 5% примесей, поэтому его рафинируют переплавкой с флюсами. Для этого черновой магний и флюс, состоящий из MgCl2, KCl, BaCl2, CaF2, NaCl, CaCl2, нагревают в электропечи до температуры 700– 500С и перемешивают. При этом неметаллические примеси переходят в шлак. После этого печь охлаждают до температуры 6700С и магний разливают в изложницы на чушки.
Производство титана . Сырьем для получения титана являются титаномагнетитовые руды, из которых выделяют ильменитовый концентрат, содержащий 40–45% TiO2, ~30% FeO, 20% Fe2O3 и 5–7% пустой породы. Название этот концентрат получил по наличию в нем минерала ильменита FeO·TiO2.
Ильменитовый концентрат плавят в смеси с древесным углем, антрацитом в руднотермических печах, где оксиды железа и титана восстанавливаются. Образующееся железо науглероживается, и получается чугун, а низшие оксиды титана переходят в шлак. Чугун и шлак разливают отдельно в изложницы. Основной продукт этого процесса – титановый шлак содержит 80–90% TiO2, 2–% FeO и примеси – SiO2, Al2O3, CaO и др. Побочный продукт этого процесса – чугун используют в металлургическом производстве.
Полученный титановый шлак подвергают хлорированию в специальных печах. В нижней части печи располагают угольную насадку, нагревающуюся при пропускании через нее электрического тока. В печь подают брикеты титанового шлака, а через фурмы внутрь печи – хлор. При температуре 800–12500С в присутствии углерода образуется четыреххлористый титан, а также хлориды CaCl2, MgCl2 и другие:
TiO2 + 2C + 2Cl2 = TiCl4 + 2CO.
Четыреххлористый титан отделяется и очищается от остальных хлоридов благодаря различию температуры кипения этих хлоридов методом ректификации в специальных установках.
Титан из четыреххлористого титана восстанавливают в реакторах при температуре 950–10000С. В реактор загружают чушковый магний; после откачки воздуха и заполнения полости реактора аргоном внутрь его подают парообразный четыреххлористый титан. Между жидким магнием и четыреххлористым титаном происходит реакция:
2Mg + TiCl4 = Ti + 2MgCl2.
Твердые частицы титана спекаются в пористую массу – губку, а жидкий MgCl2 выпускают через летку реактора. Губка титана содержит 35–40% магния и хлористого магния. Для удаления из титановой губки этих примесей ее нагревают до температуры 900–9500С в вакууме.
Титановую губку плавят методом вакуумно-дугового переплава. Вакуум в печи предохраняет титан от окисления и способствует очистке его от примесей. Полученные слитки титана имеют дефекты, поэтому их вторично переплавляют, используя как расходуемые электроды. После этого чистота титана составляет 99,6–99,7%. После вторичного переплава слитки используют для обработки давлением.
Контрольные вопросы:
1. Какие этапы (переделы) различают в производстве стали?
2. Раскройте основы технологии производства чугуна в домнах.
3. Какими способами можно получить сталь?
4. Какие способы разливки стали существуют?
5. Раскройте основные способы производства цветных металлов.
Дата добавления: 2021-02-10; просмотров: 205; Мы поможем в написании вашей работы! |
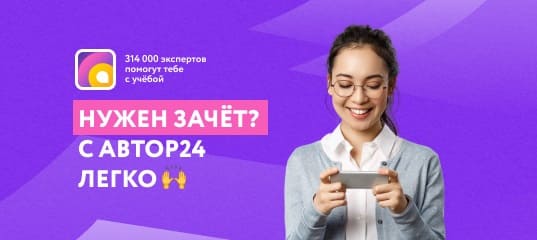
Мы поможем в написании ваших работ!