РАСЧЕТ И ТАБЛИЧНОЕ ОПРЕДЕЛЕНИЕ РЕЖИМОВ РЕЗАНИЯ ПРИ ФРЕЗЕРОВАНИИ
МИНИСТЕРСТВО ОБРАЗОВАНИЯ И НАУКИ РОССИЙСКОЙ ФЕДЕРАЦИИ
Сибирский государственный аэрокосмический университет имени академика М. Ф. Решетнева
ПРОЦЕССЫ И ОПЕРАЦИИ ФОРМООБРАЗОВАНИЯ. ЧАСТЬ 2
Методические указания (практикум) для студентов технических специальностей направления 15.03.05 «Конструкторско-технологическое обеспечение машиностроительных производств» (квалификация «бакалавр») всех форм обучения
Красноярск 2016
Практическое занятие № 5
РАСЧЕТ И ТАБЛИЧНОЕ ОПРЕДЕЛЕНИЕ РЕЖИМОВ РЕЗАНИЯ ПРИ СВЕРЛЕНИИ, ЗЕНКЕРОВАНИИ И
РАЗВЕРТЫВАНИИ
Цель работы — научиться выбирать и назначать по справочным данным параметры режима резания при сверлении, зенкеровании и развертывании, а также выбирать коэффициенты и показатели степеней для расчета мощности резания по эмпирическим формулам.
Теоретическая часть
При назначении элементов режима резания для сверления, рассверливания, зенкерования и развертывания, чтобы процесс резания был наиболее производительным и экономичным, необходимо учитывать конкретные условия обработки: материал режущей части инструмента; обрабатываемый материал и требования, предъявляемые к обрабатываемой поверхности; оборудование, на котором будет происходить процесс обработки; применяемую смазочно-охлаждающую жидкость и др.
Рассмотрим последовательность назначения режимов резания.
|
|
1. Выбирают тип сверла и его основные размеры [1, табл. 14.1 и 14.2]. Формы заточки сверл в зависимости от материала режущей части инструмента приведены в [1, табл. 14.3, 14.5, 14.7]. Геометрические параметры заточки сверл из быстрорежущей стали назначают по [1, табл. 14.4]. Углы режущей части спиральных сверл выбирают в зависимости от материала заготовки [1, табл. 14.8].
2. Определяют глубину резания t. При сверлении (рис. 1, а) отверстия в сплошном материале глубина резания, мм,
t = 0,5 D
где D — диаметр сверла, мм.
Рис. 1. Элементы режимов резания при сверлении (а), рассверливании (б), зенкеровании (в) и развертывании (г):
а — толщина срезаемого слоя; b — ширина срезаемого слоя; Sz — подана на зуб; D — диаметр сверла (зенкера, развертки); d — диаметр отверстия; φ — половина угла при вершине зенкера (развертки)
При рассверливании (рис. 1, б), зенкеровании (рис. 1, в) и развертывании (рис. 1, г) глубина резания t, мм, равная припуску на обработку h, определяется по формуле
t = D - d ,
2
где D – диаметр сверла (зенкера, развертки), мм; d – диаметр предварительно просверленного отверстия, мм.
3. Подачу S0 при сверлении выбирают в зависимости от материалов обрабатываемой детали и режущей части инструмента [1, табл. 15.8-15.12]. При сверлении отверстий, когда шероховатость и точность обработанной поверхности не являются определяющими, максимальное значение подачи S0 ограничивается прочностью и жесткостью режущего инструмента (сверла). При рассверливании отверстий подачу увеличивают в 1,5-2 раза по сравнению с табличной. При сверлении глубоких отверстий вводится поправочный коэффициент [1, с. 359]. При зенкеровании и развертывании подача S0 выбирается по справочным таблицам [1, табл. 15.15- 15.17].
|
|
4, Корректируют подачу S0 по паспортным данным станка, на котором будет проводиться обработка (берется ближайшее меньшее фактически имеющееся значение подачи на станке).
5. Назначают период стойкости сверла, зенкера и развертки [2, табл. 30 на с. 279].
6. При заданной оптимальной стойкости рассчитывают скорость главного движения резания, м/мин, допускаемую режущими свойствами резца, по эмпирической формуле
C D |
v = v K v ,
T m S y
0 |
где Сv – коэффициент, характеризующий обрабатываемый материал и условия его обработки [2, табл. 28 на с. 278]; D – диаметр сверла, мм; T — стойкость режущего инструмента, мин [2, табл. 30 на с. 279]; S0 — подача, мм/об; m — показатель относительной стойкости [2, табл. 28 на с. 278]; q, у — показатели степеней [2, табл. 28 на с. 278]; Кv — общий поправочный коэффициент на скорость резания, т. е. на измененные условия резания по отношению к тем, для которых дается значение коэффициента Cv.
|
|
Значения коэффициентов Cv и показателей степеней для рассверливания, зенкерования и развертывания являются справочными [2, табл. 29 на с. 279].
Поправочный коэффициент Kv представляет собой произведение ряда коэффициентов, важнейшими из которых являются следующие:
Kv = Kмv Kиv Klv Kпv,
где Kмv — коэффициент, учитывающий качество обрабатываемого материала [2, табл. 1 — 4 на с. 261]; Kиv — коэффициент, учитывающий качество материала инструмента [2, табл. 6 на с. 263]; Klv — коэффициент, учитывающий глубину сверления [2, табл. 31 на с. 280]; Kпv — коэффициент, отражающий состояние поверхности заготовки [2, табл. 5 на с. 263] и учитывающийся при зенкеровании и рассверливании литых и штампованных отверстий.
Упрощенная формула для определения скорости резания имеет вид
v = v табл K v
где vтабл — табличное значение скорости резания, м/мин (средние значения скорости резания при сверлении, рассверливании и зенкеровании приведены в [1, табл. 15.8, 15.9, 15.12—15.14]; Kv — поправочный коэффициент на скорость резания, учитывающий свойства обрабатываемого материала и материала режущей части инструмента, период стойкости сверла (зенкера, развертки), диаметр сверла, глубину сверления, смазочно- охлаждающие жидкости и др.
|
|
7. Определяют расчетную частоту вращения шпинделя, мин-1,
соответствующую найденной скорости резания:
n = 1000v
рас p D ,
где v — скорость резания, м/мин; D — диаметр сверла (зенкера, развертки), мм.
8. Корректируют частоту вращения шпинделя по паспортным данным станка и устанавливают действительную частоту вращения nд (Приложение 1).
9. По действительной частоте вращения определяют действительную скорость главного движения резания, м/мин:
10. Определяют эффективную мощность резания, кВт, по формуле
N = M кр v д ,
эф 9750
где Мкр — крутящий момент, Н · м.
Крутящий момент и осевую силу рассчитывают по следующим формулам: при сверлении
M кр
=10C м
D q S y K ;
P0 =10C p
D q S y K ,
0 |
0 |
мP |
p |
M кр
= 10C м
D q t x S y K ;
P0 = 10C p
D q t x S y K ,
0 |
0 |
мP |
p |
Коэффициент, учитывающий материал обрабатываемой заготовки, Кp = Кмp [2, табл. 9 и 10 на с. 264].
Крутящий момент при развертывании рассчитывают по формуле
C t x S y Dz
M = p z ,
кр 2 ×100
где Сp — коэффициент, характеризующий обрабатываемый материал и условия его обработки [2, табл. 22 на с. 273]; Sz — подача на зуб, мм/зуб; D — диаметр развертки, мм; z — число зубьев развертки; х, у — показатели степеней [2, табл. 22 на с. 273].
Подачу на зуб Sz, мм/зуб, при сверлении рассчитывают по формуле Sz = S0/2, а при зенкеровании и развертывании по формуле Sz = S0/z, где z — число зубьев развертки или зенкера.
11. Проверяют возможность обработки заготовки на выбранной модели станка. Обработка возможна, если выполняется условие
Nэф ≤ Nшп, где Nшп — мощность на шпинделе станка, кВт.
Мощность на шпинделе станка Nшп = ηNэд, где η — КПД станка; Nэд — мощность электродвигателя. Для новых станков принимают η = 0,85.
12. Определяют машинное время, мин, при сверлении (рассверливании, зенкеровании и развертывании) по формуле
L |
= l + y + D ,
n S
д 0 д 0
где L — перемещение инструмента в направлении движения подачи, мм (рис. 2); nд — частота вращения сверла, мин-1; S0 — подача, мм/об; l — глубина сверления, мм; у — врезание, мм; Δ — выход (перебег) режущего инструмента, Δ = 1...2, мм.
Врезание инструмента, мм, определяется из прямоугольного треугольника, показанного на рис. 2, д, по формуле
y= t ctgφ,
где t = D/2 — глубина резания при сверлении, мм; φ — угол заборного конуса.
При одинарной заточке 2φ = 116... 118º, у = 0,3D, а для сверл с двойной заточкой у
= 0,4D.
Рис. 2. Элементы пути, проходимого сверлом в направлении движения подачи:
а — при сквозном (на выход) сверлении; б — при глухом сверлении; в — при рассверливании;
г — при зенкеровании; д — схема врезания; D — диаметр сверла (зенкера, развертки);
d — диаметр предварительно просверленного отверстия; t — глубина резания; l — глубина сверления (зенкерования) в направлении движения подачи; у — врезание; Δ — перебег инструмента
Практическая часть
Пример 1. На вертикально-сверлильном станке серый чугун 160 НВ сверлят глухое отверстие диаметром D = 48Н12 мм на глубину 1 = 45 мм. Материал заготовки — серый чугун 160 НВ. Обработка выполняется без охлаждения.
Эскиз обработки приведен на рис. 3.
Требуется выбрать режущий инструмент, назначить режим резания и определить машинное время.
Р е ш е н и е.
А. Выбор режущего инструмента.
Для обработки серого чугуна 160 НВ [1, табл. 1.38] выбираем спиральное сверло из быстрорежущей стали Р18 диаметром D = 20 мм с коническим хвостовиком. Можно использовать сталь Р6М5. Форма заточки сверла — одинарная с подточкой поперечной кромки [1, табл. 14.3].
Параметр заточки сверла α = (11±3)º [1, табл. 14.4]. Углы спиральных сверл [1, табл. 14.8] следующие: угол в плане 2φ = 118º; угол наклона винтовой стружечной канавки, принимаемый в зависимости от диаметра сверла и обрабатываемого материала,
ω = 24...32º.
При диаметре сверла D = 20 мм угол наклона винтовой стружечной канавки ю принимаем равным 30°. Угол наклона поперечной кромки ψ = 45...55° [1, табл. 14.8]. При стандартной заточке принимаем ψ = 55°.
Обратная конусность сверла с диаметром D = 20 мм берется равной 0,05...0,10 мм на 100 мм его длины. Принимаем обратную конусность сверла равной 0,1 мм [1, с. 333].
Рис. 3. Эскиз обработки к примеру 1 | ![]() |
Б. Назначение режима резания.
1. Находим глубину резания:
t = D = 20 = 10 мм.
2 2
2. Назначаем подачу S0 [2, табл. 25 на с. 277]. Сталь 45Х с σв = 750 МПа имеет твердость 225 НВ. Для сверла с D = 20 мм при твердости стали 160...240 НВ подача S0 = 0,33...0,38 мм/об. Эти значения берутся при сверлении отверстий глубиной l ≤ 3D с точностью не выше 12-го квалитета в условиях жесткой технологической системы. В противном случае вводятся поправочные коэффициенты [2, табл. 25 на с. 277]. Принимаем среднее значение S0 = 0,35 мм/об.
3. Корректируем подачу по паспортным данным станка 2Н135 и принимаем S0
= 0,4 мм/об (Приложение 1).
0 |
p |
P0 =10C p
D q S y K
Находим значения постоянного коэффициента Ср= 68 и показатели степеней q = 1 и у = 0,7 [2, табл. 32 на с. 281]. Поправочный коэффициент Kр на осевую составляющую силы резания, зависящий только от материала обрабатываемой заготовки, определяется выражением Kр = Kмр.
Коэффициент Kмр определяется по формуле
æ s ön р
K мр = çв ÷ .
è 750 ø
Определяем значения показателя степени np для стали и чугуна [2, табл. 9 на с.
264]: np = 0,75.
æ 750 ö0,75
K = ç ÷ =10,75 =1.
мр è 750 ø
В единицах СИ осевая составляющая силы резания
Рo = 10 · 68 · 201 · 0,40,7 · 1 = 7 025 Н.
Для выполнения обработки необходимо выполнение условия
Рo ≤ Рmax,
где Рmax — максимальная осевая сила резания, допускаемая механизмом подачи станка 2Н135 (Приложение 1), Рmax = 15 000 Н (≈ 1 500 кгс).
Так как 7 025 Н < 15 000 Н, то назначенная подача S0 = 0,4 мм/об вполне допустима.
При перегрузке механизма подачи станка в случае Рo > Рmax необходимо уменьшить подачу S0 на столько, чтобы обеспечивалось выполнение условия Рo = Рmax: откуда
y |
Pmax |
10C D q K |
p |
p |
S =
10C p
D q K
; S = .
4.
p |
5. Определяем скорость резания, м/мин, допускаемую режущими свойствами сверла, по формуле
C D q
v = v K v .
T m S y
Находим [2, табл. 28 на с. 278] значение постоянного коэффициента Cv = 9,8 и показатели степеней q = 0,4; m = 0,2; у = 0,5.
Поправочный коэффициент на скорость резания
Kv = Kмv Kиv Klv Kзv,
Коэффициент на инструментальный материал Р6М5 Kиv = 1 [2, табл. 6 на с. 263]. Коэффициент Klv, учитывающий глубину сверления до l = 3D, принимается равным
1 [2, табл. 31 на с. 280].
Коэффициент, учитывающий отрабатываемый материал, рассчитывается по формуле
æ 750 ön v
è |
s |
в ø
Здесь коэффициент, характеризующий группу стали по обрабатываемости, Кr = 1, а показатель степени nv = 0,9 [2, табл. 2 на с. 262].
Тогда
æ 750 ö0,75
K =1×ç ÷ = 10,9 =1.
мv è 750 ø
При одинарной заточке сверл из быстрорежущей стали рассчитанную скорость резания необходимо уменьшить, умножив ее на коэффициент Kзv = 0,75. Тогда
Kv = l · 1 · 1 · 0,75 = 0,75,
а скорость резания
9,8× 200,4
v = 450,2 × 0,40,5
0,75 = 18,1 м/мин.
6. Определяем частоту вращения шпинделя, соответствующую расчетной скорости резания:
n = 1000v = 1000 ×18,1 = 288,22 мин-1.
p D 3,14 × 20
7. Корректируем частоту вращения шпинделя по паспортным данным станка 2Н135 и устанавливаем действительную частоту вращения nд= 250 мин-1 (Приложение 1).
8. Определяем действительную скорость главного движения резания:
v = p Dn д = 3,14 × 2 × 250 = 15,7
м/мин.
1000 1000
9. Крутящий момент от сил сопротивления резанию при сверлении определяем по формуле
Мкр = CмDqSyKp.
Находим коэффициент См = 0,0345 и показатели степеней q = 2 и у = 0,8 [2, табл. 32 на с. 281].
Поправочный коэффициент Kp был определен в п. 3 при расчете осевой составляющей силы резания: Kp = Kмp = 1. В единицах СИ крутящий момент
Мкр = 9,81 · 0,0345 · 202 · 0,40,8 · 1 = 65,04 Н · м
10. Определяем эффективную мощность по формуле
N = M кр n д = 65,04 × 250 =1,67
кВт.
эф 9750
9750
11. Проверяем, достаточна ли мощность станка для обработки. Обработка возможна, если Nэф ≤ Nшп.
Мощность на шпинделе станка Nшп = ηNэд. У станка 2Н135 мощность электродвигателя (Приложение 1) Nэд = 4 кВт, а η = 0,8. Тогда мощность Nшп = 0,8 · 4 = 3,2 кВт.
Следовательно, условие обработки (1,67 < 3,2) выполняется, т.е. обработка возможна (станок по мощности не догружен).
В случае перегрузки станка по мощности необходимо определить коэффициент перегрузки:
K = N эф .
N |
шп
Для кратковременного резания (длительностью 1 мин) допускается перегрузка электродвигателя станка на 25 % от его номинальной мощности. Для того чтобы установить, допустима ли перегрузка, необходимо рассчитать основное время.
В. Определение машинного времени.
При глухом сверлении (см. рис. 2, б) машинное время находим по формуле
L |
= l + y + D .
n S
д 0 д 0
При одинарной заточке сверла у = 0,3D = 0,3 · 20 = 6 мм. При сверлении глухого отверстия перебег Δ = 0. Следовательно,
T м =
50 + 6
250 × 0,4
= 0,56
мин.
Задача 1. На вертикально-сверлильном станке 2Н135 сверлят глухое отверстие диаметром D на глубину l.
Варианты данных к задаче приведены в табл. 1. Эскиз обработки приведен на рис. 3.
Требуется выбрать режущий инструмент, назначить режим резания и определить машинное время.
Таблица 1 – Варианты данных к задаче 1
Номер варианта | Материал заготовки | D, мм | l, мм | Отверстие | Обработка |
1 | Сталь 45X, σв = 750МПа | 28Н12 | 60 | Глухое | С охлаждением |
2 | Серый чугун, 160 НВ | 48Н12 | 45 | Сквозное | Без охлаждения |
3 | Сталь конструкционная 40, σв = 660 МПа | 35Н12 | 25 | Глухое | С охлаждением |
4 | Сталь жаропрочная 12Х18Н9Т, 141 НВ | 45Н12 | 40 | Сквозное | С охлаждением |
5 | Серый чугун, 210 НВ | 25Н12 | 90 | Глухое | Без охлаждения |
Окончание табл. 1
Номер варианта | Материал заготовки | D, мм | l, мм | Отверстие | Обработка |
6 | Медные сплавы средней твердости, 120 НВ | 30Н12 | 50 | Сквозное | Без охлаждения |
7 | Сталь Ст3, σв = 460МПа | 15Н12 | 60 | Глухое | С охлаждением |
8 | Сталь конструкционная 40, σв = 660 МПа | 18Н12 | 70 | Глухое | Без охлаждения |
9 | Серый чугун, 190 НВ | 20Н12 | 30 | Сквозное | Без охлаждения |
10 | Сталь 45ХН, σв = 780 МПа | 26Н12 | 50 | Глухое | С охлаждением |
11 | Бронза БрАЖН 11-6-6, 200НВ | 18Н12 | 45 | Сквозное | Без охлаждения |
12 | Латунь ЛМцЖ52-4-1, 100 НВ | 25Н12 | 25 | Глухое | С охлаждением |
13 | Сталь 50, σв = 750 МПа | 35Н12 | 40 | Сквозное | С охлаждением |
14 | Серый чугун, 180 НВ | 45Н12 | 90 | Глухое | Без охлаждения |
15 | Алюминиевый сплав АЛ7,60 НВ | 14Н12 | 50 | Сквозное | Без охлаждения |
16 | Медь М3, 75 НВ | 16Н12 | 60 | Глухое | С охлаждением |
17 | Серый чугун, 220 НВ | 18Н12 | 40 | Глухое | Без охлаждения |
18 | Сталь 35, σв = 580 МПа | 24Н12 | 25 | Сквозное | Без охлаждения |
19 | Ст 5, σв = 600 МПа | 28Н12 | 45 | Глухое | С охлаждением |
20 | Латунь ЛК80-3,110 НВ | 32Н12 | 90 | Сквозное | Без охлаждения |
Пример 2. На вертикально-сверлильном станке 2Н135 зенкеруют сквозное отверстие диаметром d = 43 мм до диаметра D = 45Н11 мм на глубину l = 50 мм. Материал заготовки — сталь 40 с σв= 600 МПа (≈ 60 кгс/мм2) и твердостью 177 НВ. Заготовка из горячекатаного проката, при обработке она охлаждается эмульсией.
Эскиз обработки приведен на рис. 4.
Требуется выбрать режущий инструмент, назначить режим резания и определить машинное время.
Рис. 4. Эскиз обработки к примеру 2
Р е ш е н и е.
А. Выбор режущего инструмента.
Для обработки сквозного отверстия в стали 40 с σв = 600 МПа выбираем насадной зенкер с D = 45 мм из быстрорежущей стали Р18 (или Р6М5) с числом зубьев z = 4.
Геометрические элементы зенкера определяем по справочнику [2, табл. 48 на с. 155]: γ = 15...20º; α = 8... 10º; угол в плане φ = 60º; ω = 25...30º; f = 0,8...2 мм. Принимаем γ
= 15º, α = 8º.
Б. Назначение режима резания.
1. Определяем глубину резания:
t = D - d = 45 - 43 = 1 мм.
2 2
2. Назначаем подачу для зенкерования отверстия. В зависимости от диаметра зенкера (D = 45 мм) и материала обрабатываемой детали S0 = 1... 1,3 мм/об [2, табл. 26 на с. 277). Принимаем среднее значение S0= 1,15 мм/об.
3. Корректируем подачу по паспортным данным станка 2Н135 и принимаем S0
= 1,12 мм/об (Приложение 1).
4. Устанавливаем допустимый износ зенкеров из быстрорежущей стали Р18. При обработке заготовок из стали допустимый износ зенкеров по задней поверхности h3 = 1,2... 1,5 мм. Среднее значение периода стойкости Т для зенкера с диаметром D = 45 мм при обработке стали принимаем равным 60 мин [2, табл. 30 на с. 279].
5. Определяем скорость резания, м/мин, допускаемую режущими свойствами зенкера, по формуле
C D q
v = v K v .
T m t x S y
Постоянный коэффициент Cv = 16,3. Показатели степеней следующие: q = 0,3; m = 0,3; х = 0,2; у = 0,5 [2, табл. 29 на с. 279].
Поправочный коэффициент на скорость резания определяется по формуле
Kv = Kмv Kиv Kпv.
Здесь коэффициент на обрабатываемый материал [2, табл. 2 на с. 262]
æ 750 ön v
è |
s |
в ø
где Kr = 1 — коэффициент, характеризующий группу стали по обрабатываемости [2, табл. 2 на с. 262]; nv = 0,9 — показатель степени [2, табл. 2 на с. 262].
Следовательно,
æ 750 ö0,9
K мv = 1×ç 600 ÷
= 1,22 .
è ø
Коэффициент на инструментальный материал Р6М5 [2, табл. 6 на с. 263].
При рассверливании и зенкеровании литых и штампованных отверстий дополнительно вводится поправочный коэффициент на скорость резания, т.е. скорость резания уменьшают, умножая ее на коэффициент Kпv = 0,9 [2, табл. 5 на с. 263].
Тогда коэффициент
а скорость резания
Kv= 1,22 · 1 · 0,9 = 1,1,
16,3× 450,3
v = 1,1 = 15,52
600,3 ×10,2 ×1,120,5
м/мин.
6. Определяем частоту вращения шпинделя, соответствующую найденной скорости резания:
n = 1000v = 1000 ×15,52 = 109,88 мин-1.
p D 3,14 × 45
7. Корректируем частоту вращения по паспортным данным станка 2Н135 и устанавливаем действительную частоту вращения nд= 90 мин-1 (Приложение 1).
8. Определяем действительную скорость главного движения резания:
v = p Dn д д 1000
= 3,14× 45×90 = 12,7 м/мин.
1000
При обработке зенкерами из быстрорежущей стали мощность, затрачиваемая на резание, незначительная (по сравнению с мощностью, затрачиваемой при сверлении и рассверливании), поэтому режимы резания по мощности привода станка не проверяем.
В. Определение машинного времени (см. рис. 2, г). Используем формулу
L |
= l + y + D .
n S
д 0 д 0
Здесь перемещение зенкера L = l + y + Δ. Врезание (см. рис. 2, д) у = tctgφ = 1 · ctg45º = 1. Перебег Δ = 1... 3 мм, принимаем Δ = 3 мм.
Тогда
L = l + y+ Δ = 50 + 1 + 3 = 54 мм.
Следовательно,
T = 50 +1+ 3 = 0,536
м 90 ×1,12
мин.
Задача 2. На вертикально-сверлильном станке 2Н135 зенкеруют отверстие диаметром d до диаметра D на глубину l.
Варианты данных к задаче приведены в табл. 2. Эскиз обработки приведен на рис. 4.
Требуется выбрать режущий инструмент, назначить режим резания и определить основное время.
Таблица 2 – Варианты данных к задаче 2
Номер варианта | Материал заготовки | D, мм | d, мм | l, мм | Отверстие | Обработка |
1 | Сталь 65 Г, σв = 850 МПа | 28Н11 | 18 | 30 | Глухое | С охлаждением |
2 | Серый чугун, 150 НВ | 30Н11 | 28,4 | 40 | Сквозное | Без охлаждения |
3 | Сталь конструкционная углеродистая 35, σв = 600 МПа | 35Н11 | 33,6 | 55 | Сквозное | С охлаждением |
4 | Сталь Ст5, σв = 600МПа | 34,8Н11 | 33 | 40 | Глухое | С охлаждением |
5 | Серый чугун, 230 НВ | 48Н11 | 45,6 | 70 | Сквозное | Без охлаждения |
6 | Алюминиевый сплав АК7ч, 50 НВ | 30Н11 | 27 | 50 | Глухое | Без охлаждения |
7 | Сталь 50, σв = 750 МПа | 30Н12 | 15 | 40 | Сквозное | С охлаждением |
8 | Медь М3, 75 НВ | 60Н12 | 40 | 50 | Сквозное | Без охлаждения |
9 | Сталь 45Х, σв = 750 МПа | 40Н12 | 15 | 70 | Сквозное | С охлаждением |
10 | Серый чугун, 170 НВ | 40Н12 | 20 | 55 | Глухое | Без охлаждения |
11 | Сталь Ст3, σв = 460МПа | 44,7Н11 | 43 | 25 | Глухое | С охлаждением |
Окончание табл. 2
Номер варианта | Материал заготовки | D, мм | d, мм | l, мм | Отверстие | Обработка |
12 | Сталь конструкционная 40, σв = 660 МПа | 45Н11 | 42 | 45 | Сквозное | Без охлаждения |
13 | Серый чугун, 190 НВ | 20Н11 | 18 | 70 | Сквозное | С охлаждением |
14 | Сталь 45ХН, σв = 780 МПа | 29,8Н11 | 28 | 35 | Глухое | С охлаждением |
15 | Бронза БрАЖН 11-6-6, 200НВ | 34,7Н11 | 33 | 60 | Сквозное | Без охлаждения |
16 | Латунь ЛМцЖ52-4-1, 100 НВ | 30Н11 | 27,6 | 15 | Глухое | Без охлаждения |
17 | Сталь 50, σв = 750 МПа | 35Н11 | 32,5 | 50 | Сквозное | С охлаждением |
18 | Серый чугун, 180 НВ | 29,8Н11 | 28 | 55 | Сквозное | Без охлаждения |
19 | Алюминиевый сплав АЛ7, 60 НВ | 16Н11 | 14 | 30 | Сквозное | С охлаждением |
20 | Сталь 38ХМЮА, σв = 750МПа | 20Н11 | 18 | 50 | Глухое | Без охлаждения |
Пример 3. На вертикально-сверлильном станке 2Н135 зенкеруют предварительно обработанное сквозное отверстие диаметром d = 44,4 мм до диаметра D = 46,7 мм на глубину l = 70 мм (под последующую обработку одной разверткой). Материал заготовки
— бронза БрОЦ4-3 твердостью 70 НВ. Заготовка — отливка. Обработка выполняется с охлаждением.
Эскиз обработки приведен на рис. 4.
Требуется выбрать режущий инструмент, назначить режим резания и определить машинное время.
Р е ш е н и е.
А. Выбор режущего инструмента.
Для обработки сквозного отверстия в цветных металлах и их сплавах с твердостью 70 НВ выбираем [2, табл. 3 на с. 116] насадной зенкер с D = 46,7 мм, с пластинами из твердого сплава ВК8 и с числом зубьев z = 4.
Геометрические элементы зенкера из твердого сплава ВК8 принимаем по справочнику [2, табл. 48 на с. 155]: γ = 10...20º; α = 10º; угол в плане φ = 60º; ω = 10...20º; f
= 0,8...2 мм. Принимаем γ = 15º, ω = 10º. Б. Назначение режима резания.
1. Определяем глубину резания:
t = D - d= 46,7 - 44,4 = 1,15
мм.
2 2
мм/об.
2. Назначаем подачу [2, табл. 26 на с. 277]. Для D = 46,7 мм подача S0 = 1,6...2
Принимаем среднее значение S0 = 1,8 мм/об.
3. Корректируем подачу по паспортным данным станка и принимаем S0= 1,6
мм/об (Приложение 1).
4. Устанавливаем допустимый износ зенкеров. Зенкеры из твердых сплавов в основном изнашиваются по задней поверхности: h3 = 1... 1,6 мм. Среднее значение периода стойкости зенкера Т [2, табл. 30 на с. 279] для диаметра D = 46,7 мм при обработке медных сплавов составляет 60 мин.
5. Определяем скорость резания, м/мин, допускаемую режущими свойствами зенкера:
C D q
v = v K v .
T m t x S y
Здесь постоянный коэффициент Cv = 143, а показатели степеней следующие: q = 0,4; m = 0,4; х = 0,15; у = 0,45 [2, табл. 29 на с. 279]. Диаметр зенкера D = 46,7 мм. Глубина резания t = 1,15 мм. Подача S = S0 = 1,6 мм/об.
Поправочный коэффициент на скорость резания определяется по формуле
Kv = Kмv Kиv Klv Kпv.
Поправочный коэффициент Kмv на обрабатываемый материал, учитывающий влияние физико-механических свойств медных и алюминиевых сплавов, находим по [2, табл. 4 на с. 263]. Для стали и чугуна коэффициент Kмv = 1 [2, табл. 1—4 на с. 261—263]. На инструментальный материал ВК8 коэффициент Kиv = 1 [2, табл. 6 на с. 263].
При рассверливании и зенкеровании литых и штампованных отверстий дополнительно вводится поправочный коэффициент на скорость резания, т.е. скорость резания уменьшают, умножая ее на коэффициент Kпv = 0,9 [2, табл. 5 на с. 263].
Тогда коэффициент
а скорость резания
Кv = 1 · 1 · 0,9 = 0,9,
143 × 46,70,4
v = 600,4 ×1,150,15 ×1,60,45 0,9 = 92,11 м/мин.
6. Определяем частоту вращения шпинделя, соответствующую найденной скорости резания:
n = 1000v = 1000 × 92,11 = 628,16 мин-1.
p D 3,14 × 46,7
7. Корректируем частоту вращения по паспортным данным станка 2Н135 и устанавливаем действительную частоту вращения nд = 500 мин-1 (Приложение 1).
8. Определяем действительную скорость главного движения резания
v = p Dn д д 1000
= 3,14 × 46,7 × 500 = 73,32 м/мин.
1000
При обработке зенкерами из быстрорежущей стали мощность, затрачиваемая на резание, незначительная (по сравнению с мощностью, затрачиваемой при сверлении и рассверливании), поэтому режимы резания по мощности привода станка не проверяем.
В. Определение машинного времени. Используем формулу
L |
= l + y + D .
n S
д 0 д 0
Здесь L = l + у + Δ. Глубина зенкерования l = 70 мм. Врезание у = t ctg φ = 1,15 · ctg60° = 1,15 · 0,5774 = 0,66. Перебег Δ = 1... 3 мм, принимаем Δ = 3 мм.
Тогда
T = 70 + 0,66 + 3 = 0,1 мин.
м 500 ×1,6
Задача 3. На вертикально-сверлильном станке 2Н135 зенкеруют отверстие диаметром d до диаметра D на глубину l под последующую обработку одной разверткой.
Варианты данных к задаче приведены в табл. 3. Эскиз обработки приведен на рис. 4.
Требуется выбрать режущий инструмент, назначить режим резания и определить основное время.
Таблица 3 – Варианты данных к задаче 3
Номер варианта | Материал заготовки | D, мм | d, мм | l, мм | Отверстие | Обработка |
1 | Сталь 38ХМЮА, σв = 750 МПа | 28Н11 | 26 | 30 | Глухое | С охлаждением |
2 | Серый чугун, 150 НВ | 30Н11 | 28,4 | 40 | Сквозное | Без охлаждения |
3 | Сталь 65Г, σв = 850 МПа | 29,8Н11 | 28 | 35 | Сквозное | Без охлаждения |
4 | Сталь Ст5, σв = 600 МПа | 33,8Н11 | 31 | 60 | Глухое | С охлаждением |
5 | Серый чугун, 160 НВ | 46Н11 | 43,6 | 30 | Сквозное | Без охлаждения |
6 | Алюминиевый сплав АК7ч, 50 НВ | 20,8Н11 | 19 | 70 | Глухое | Без охлаждения |
7 | Сталь 38ХМЮА, σв = 750 МПа | 20Н11 | 18 | 30 | Глухое | С охлаждением |
8 | Серый чугун, 180 НВ | 35Н11 | 32,5 | 50 | Глухое | Без охлаждения |
9 | Латунь ЛК80-3, 110 НВ | 44,7Н11 | 43 | 25 | Сквозное | Без охлаждения |
10 | Силумин АЛ4, 50 НВ | 19,8Н11 | 18 | 70 | Глухое | Без охлаждения |
11 | Сталь Ст3, σв = 460МПа | 28Н11 | 26 | 30 | Глухое | С охлаждением |
12 | Серый чугун, 150 НВ | 30Н11 | 28,4 | 40 | Сквозное | Без охлаждения |
13 | Сталь конструкционная углеродистая 35, σв = 600 МПа | 29,8Н11 | 28 | 35 | Сквозное | Без охлаждения |
14 | Сталь Ст5, σв = 600МПа | 33,8Н11 | 31 | 60 | Глухое | С охлаждением |
15 | Серый чугун, 230 НВ | 46Н11 | 43,6 | 30 | Сквозное | Без охлаждения |
16 | Бронза БрАЖН 11-6-6, 200НВ | 20,8Н11 | 19 | 70 | Глухое | Без охлаждения |
17 | Сталь 50, σв = 750 МПа | 20Н11 | 18 | 30 | Глухое | С охлаждением |
18 | Медь М3, 75 НВ | 35Н11 | 32,5 | 50 | Глухое | Без охлаждения |
19 | Сталь 45Х, σв = 750 МПа | 44,7Н11 | 43 | 25 | Сквозное | Без охлаждения |
20 | Серый чугун, 170 НВ | 19,8Н11 | 18 | 70 | Глухое | Без охлаждения |
Пример 4. На вертикально-сверлильном станке 2Н135 развертывают сквозное отверстие диаметром d = 19,8 мм до диаметра D = 20Н9 мм на глубину l = 30 мм. Материал заготовки — сталь 45 с σв = 700 МПа (≈ 70 кгс/мм2). Параметр шероховатости обработанной поверхности Ra 2 мкм. Обработка выполняется с охлаждением.
Эскиз обработки приведен на рис. 5.
Требуется выбрать режущий инструмент, назначить режим резания и определить машинное время.
Р е ш е н и е
А. Выбор режущего инструмента.
Для обработки стали 45 с σв = 700 МПа выбираем [2, табл. 3 на с. 116] машинную насадную развертку диаметром D = 20 мм с коническим хвостовиком, оснащенную
пластинами из твердого сплава Т15К6 для окончательной обработки конструкционной стали.
Рис. 5. Эскиз обработки к примеру 4
Геометрические элементы развертки из твердого сплава принимаем следующие [2, табл. 53 на с. 160]: γ = 0º; α = 8º. Угол в плане φ = 45º [2, табл. 51 на с. 159], форма заточки I.
Б. Назначение режима резания.
1. Определяем глубину резания:
t = D - d = 20 -19,8 = 0,1 мм.
2 2
2. Назначаем подачу S0 [2, табл. 27 на с. 278]. Для развертывания отверстия диаметром D = 2 0 мм принимаем S 0 табл = 1 мм/об. При чистовом развертывании отверстия в один проход по 9-му квалитету точности и с параметром шероховатости поверхности Ra 2 мкм вводим поправочный коэффициент на подачу K nS = 0,8. Поправочный коэффициент на подачу, учитывающий материал рабочей части инструмента (твердый сплав Т15К6), принимаем KиS = 0,7.
Тогда
S0 = S 0 табл KNs КиS = 1 · 0,8 · 0,7 = 0,56 мм/об.
3. Корректируем подачу по паспортным данным станка 2Н135 и принимаем S0
= 0,56 мм/об (Приложение 1).
4. Устанавливаем допустимый износ заборного конуса по задней поверхности для твердосплавных разверток h 3 = 0,4...0,7 мм.
Среднее значение периода стойкости Т для диаметра развертки D = 20 мм при обработке стали принимаем равным 30 мин [2, табл. 30 на с. 279).
5. Определяем скорость резания, допускаемую режущими свойствами развертки:
C D q
v = v K v .
T m t x S y
Здесь постоянный коэффициент Сv = 100,6 [2, табл. 29 на с. 279]. Показатели
степеней следующие: q = 0,3; m = 0,4; х = 0; у = 0,65 [2, табл. 29 на с. 279].
Поправочный коэффициент на скорость резания определяется по формуле
Kv = Kмv Kиv Klv Kпv.
Здесь коэффициент на обрабатываемый материал [2, табл. 1—4 нас. 261—263]
æ 750 ön v
è |
s |
в ø
где nv = 1 — показатель степени [2, табл. 2 на с. 262].
Коэффициент, характеризующий группу стали по обрабатываемости, Кr = 1 [2, табл. 2 на с. 262]. Следовательно,
æ 750 ö1
K мv = 1×ç 750 ÷
= 1,07 .
è ø
Коэффициент на инструментальный материал Kиv = 1 [2, табл. 6 нас. 263].
Коэффициент, учитывающий глубину развертывания, Klv = 1 [2, табл. 31 на с. 280].
Тогда коэффициент
а скорость резания
Kv = 1,07 · 1 · 1 = 1,07,
100,6 × 200,3
v = 300,4 × 0,10 × 0,560,65 1,07 = 98,26
м/мин.
6. Определяем частоту вращения шпинделя, соответствующую найденной скорости резания:
n = 1000v = 1000 × 98,26 =1564,7 мин-1.
p D 3,14 × 20
7. Корректируем частоту вращения по паспортным данным станка и устанавливаем действительную частоту вращения nд = = 1 400 мин-1 (Приложение 1).
8. Находим действительную скорость главного движения резания:
v = pDn д = 3,14 × 20 ×1400 = 87,9 м/мин.
д 1000
1000
Установленные режимы резания по мощности привода станка не проверяем, поскольку потребность мощности для обработки незначительная.
В. Определение машинного времени. Используем формулу
L |
= l + y + D .
n S
д 0 д 0
Здесь путь, проходимый инструментом в направлении подачи, L = l + у + Δ. Глубина развертывания l = 30 мм.
Врезание у = t ctg φ = 0,1 · ctg45º = 0,1 мм. Перебег Δ = 1...3 мм, принимаем Δ = 3 мм. Следовательно,
T = 30 + 0,1+ 3 = 0,042
м 1400 × 0,56
мин.
Задача 4. На вертикально-сверлильном станке 2Н135 развертывают отверстие диаметром d до диаметра D на глубину l. Параметр шероховатости обработанной поверхности Ra 2 мкм.
Варианты данных к задаче приведены в табл. 4. Эскиз обработки приведен на рис. 5.
Требуется выбрать режущий инструмент, назначить режим резания и определить машинное время.
Таблица 4 – Варианты данных к задаче 4
Номер варианта | Материал заготовки | D, мм | d, мм | l, мм | Отверстие | Обработка |
1 | Сталь 45, σв = 700 МПа | 28Н9 | 27,8 | 30 | Глухое | С охлаждением |
2 | Серый чугун, 180 НВ | 20Н9 | 19,6 | 60 | Сквозное | Без охлаждения |
3 | Сталь 40Х, σв = 700 МПа | 30Н9 | 29,8 | 35 | Сквозное | С охлаждением |
4 | Сталь 30ХН3А, σв = 800 МПа | 42Н9 | 41,8 | 60 | Глухое | С охлаждением |
5 | Серый чугун, 160 НВ | 46Н9 | 45,7 | 70 | Глухое | Без охлаждения |
6 | Алюминиевый сплав АК2, σв = 400 МПа | 35Н9 | 20,5 | 25 | Сквозное | С охлаждением |
7 | Серый чугун, 170 НВ | 22Н9 | 21,8 | 55 | Сквозное | Без охлаждения |
8 | Серый чугун, 190 НВ | 25Н9 | 24,8 | 75 | Глухое | Без охлаждения |
9 | Сталь 30ХН3А, σв = 800 МПа | 40Н9 | 39,7 | 45 | Сквозное | С охлаждением |
10 | Серый чугун, 230 НВ | 45Н9 | 44,7 | 70 | Глухое | Без охлаждения |
11 | Сталь Ст3, σв = 460МПа | 26Н9 | 25,8 | 30 | Сквозное | Без охлаждения |
12 | Сталь конструкционная 40, σв = 660 МПа | 18Н9 | 17,6 | 60 | Сквозное | С охлаждением |
13 | Серый чугун, 220 НВ | 28Н9 | 27,8 | 35 | Глухое | С охлаждением |
14 | Сталь 45ХН, σв = 780 МПа | 40Н9 | 39,8 | 60 | Глухое | Без охлаждения |
15 | Бронза БрАЖН 11-6-6, 200НВ | 44Н9 | 43,7 | 70 | Сквозное | С охлаждением |
16 | Латунь ЛМцЖ52-4-1, 100 НВ | 32Н9 | 31,5 | 25 | Сквозное | Без охлаждения |
17 | Сталь 50, σв = 750 МПа | 20Н9 | 19,8 | 55 | Глухое | Без охлаждения |
18 | Серый чугун, 180 НВ | 24Н9 | 23,8 | 75 | Сквозное | С охлаждением |
19 | Алюминиевый сплав АЛ7, 60 НВ | 38Н9 | 37,7 | 45 | Глухое | Без охлаждения |
20 | Сталь 38ХМЮА, σв = 750МПа | 42Н9 | 41,7 | 70 | Глухое | Без охлаждения |
Библиографические ссылки
1. Вереина Л.И. Справочник станочника: учебное пособие. – М.: Академия, 2008. – 560 с.
2. Справочник технолога-машиностроителя: в 2-х томах – Т.2 / под ред. А.Г. Косиловой и Р.К. Мещеряковой. – М.: Машиностроение, 1986. – 496 с.
Практическое занятие № 6
РАСЧЕТ И ТАБЛИЧНОЕ ОПРЕДЕЛЕНИЕ РЕЖИМОВ РЕЗАНИЯ ПРИ ФРЕЗЕРОВАНИИ
Цель работы — научиться выбирать и назначать по справочным данным параметры режима резания при фрезеровании, а также выбирать коэффициенты и показатели степеней для расчета мощности резания по эмпирическим формулам.
Теоретическая часть
Фрезерование — это один из высокопроизводительных методов обработки металлов резанием с помощью фрезы.
Фреза — многолезвийный инструмент, представляющий собой тело вращения, на образующей поверхности которого, а иногда и на торце, имеются режущие зубья.
Выбор типа фрезы зависит от видов используемого оборудования и обрабатываемой поверхности. При цилиндрическом фрезеровании ось фрезы параллельна обрабатываемой поверхности, а зубья располагаются на цилиндрической поверхности. При торцовом фрезеровании ось фрезы перпендикулярна обработанной поверхности, а зубья располагаются как на торцовой, так и на цилиндрической поверхностях.
Рис. 1. Схемы встречного (а) и попутного (б) фрезерования: ψк — угол контакта фрезы;
Sz — подача на зуб; t — глубина резания; аmах — максимальная толщина стружки
Различают две схемы цилиндрического и торцового фрезерования (рис. 1):
§ встречное фрезерование (рис. 1, а) — когда направление движения подачи Ds противоположно направлению вращения фрезы Dr При встречном фрезеровании нагрузка на зуб фрезы увеличивается постепенно и снятие стружки начинается в точке 1, а заканчивается в точке 2 с наибольшей толщиной срезаемого слоя аmах. Встречное фрезерование применяется при черновой обработке заготовок, а также при наличии корки или окалины;
§ попутное фрезерование (рис. 1, б) — когда направление вращения фрезы Dr и направление движения подачи Ds совпадают, при этом каждый зуб фрезы начинает снимать стружку с наибольшей толщиной срезаемого слоя аmах в точке 2, а заканчивает в точке 1. Попутное фрезерование применяется при чистовой обработке, когда требуется высокая точность обработки, а также при обработке тонких заготовок.
Приведем последовательность назначения режимов резания.
1. Выбирают глубину резания t, мм, тип фрезы, диаметр фрезы D, мм, и ширину фрезерования В, мм.
Диаметр фрезы D зависит от размеров обрабатываемой поверхности, глубины резания, конструктивных размеров и формы детали, а также от жесткости системы [1, табл. 17.5]. При выборе диаметра фрезы необходимо учитывать, что фрезы малого диаметра являются наиболее производительными и экономичными (в этом случае расход инструментального материала наименьший). При торцовом фрезеровании диаметр фрезы D должен быть больше ширины фрезерования В, т.е. D = (1,25... 1,50)В.
При черновой обработке для сокращения основного (машинного) времени весь припуск рекомендуется снимать за один проход. В этом случае глубина резания t равна припуску на обработку h. При повышенных требованиях к точности и шероховатости обработанной поверхности весь припуск h снимается за несколько проходов. Глубина резания t при чистовой (окончательной обработке) должна быть минимальной. При срезании повышенных припусков или при работе на маломощных станках припуск разбивается на части и удаляется за несколько проходов.
Глубина резания t — это толщина срезаемого слоя за один рабочий ход, измеряемая в направлении, перпендикулярном оси фрезы (см. рис. 1).
Ширина фрезерования В — это ширина поверхности, обрабатываемой за один рабочий ход, измеряемая в направлении, параллельном оси фрезы.
При торцовом фрезеровании понятия глубины резания и ширины фрезерования меняются местами.
Толщина срезаемого слоя а — это расстояние между поверхностями резания, образованными двумя последовательными положениями режущих кромок фрезы в радиальном направлении, нормальном к поверхности резания.
2. Выбирают инструментальный материал для режущей части фрезы [1, табл. 17.2—17.4].
3. Выбирают геометрические параметры режущей части фрезы и ее тип [1, табл. 17.6, 17.10—17.36].
4. Выбирают подачу Sz, мм/зуб, для различных фрез и условий резания [1, табл. 19.7, 19.8, 19.12, 19.13, 19.18—19.20, 19.28—19.30]. Выбор подачи при черновом фрезеровании зависит от материала обрабатываемой детали, материала режущей части фрезы, размеров обрабатываемой поверхности, жесткости системы СПИД и мощности оборудования.
При фрезеровании различают подачу на один зуб Sz, мм/зуб, и подачу на один оборот S0, мм/об, между которыми существует следующая зависимость: Sz = S0/2, мм/зуб, где z — число зубьев фрезы.
Скорость движения подачи, мм/мин, определяют по формуле
v S = S z zn , где n — частота вращения шпинделя, мин-1.
Для повышения производительности труда и уменьшения машинного времени подача должна быть по возможности максимальной. При грубом (черновом) фрезеровании, когда шероховатость и точность обработанной поверхности не являются определяющими, максимальная подача Sz ограничивается мощностью электродвигателя и жесткостью режущего инструмента.
При чистовом фрезеровании, когда качество обработанной поверхности должно быть высоким, максимальная подача S0 ограничивается требованиями шероховатости обработанной поверхности.
При выборе подачи при торцовом фрезеровании необходимо учитывать расположение заготовки относительно фрезы. При симметричной установке фрезы (рис. 2, а) подачу необходимо уменьшать в 2 раза. При обработке заготовок из конструкционных углеродистых, легированных сталей и чугуна, когда D/B = = 1,1... 1,7, рекомендуется устанавливать фрезу таким образом, чтобы режущие кромки ее зубьев были смещены относительно заготовки на значения с = (0,03...0,05)D (см. рис. 2, б).
Рис. 2. Схема симметричной (а) и смещенной (б) установки фрезы относительно детали
5. Назначают период стойкости фрезы [1, табл. 17.7].
6. Определяют скорость главного движения резания, допускаемую режущими свойствами фрезы, м/мин, по эмпирической формуле
C D q
v = v K v ,
T m t x S y B u z p
z |
где Cv — коэффициент, характеризующий обрабатываемый материал и условия его обработки [2, табл. 39 на с. 286]; D — диаметр фрезы, мм; T — стойкость режущего инструмента, мин [2, табл. 40 на с. 290]; m — показатель относительной стойкости; t — глубина резания, мм; Sz — подача на зуб, мм/зуб; х, у, q, р, u — показатели степеней [2, табл. 39 на с. 286]; В — ширина фрезерования, мм; z — число зубьев фрезы.
Общий поправочный коэффициент на скорость резания, учитывающий фактические условия резания, определяется по формуле
Kv = Kмv Kиv Kпv,
где Kмv — коэффициент, учитывающий качество обрабатываемого материала [2, табл. 1 — 4 на с. 261 —265]; Kпv — коэффициент, учитывающий состояние поверхности заготовки [2, табл. 5 на с. 263]; Kиv — коэффициент, учитывающий материал инструмента [2, табл. 5
на с. 263].
Скорость главного движения резания, м/мин, определяют по упрощенной формуле
v = v табл K v
где vтaбл — табличное значение скорости резания, м/мин [1, табл. 19.8—19.11, 19.14— 19.17, 19.21 — 19.26, 19.31 — 19.35]. Общий поправочный коэффициент на скорость резания
Kv = K1K2K3K4K5,
где K1 — K5 — поправочные коэффициенты на скорость резания при фрезеровании [1, табл. 19.8—19.11, 19.14—19.17, 19.21—19.26, 19.31—19.35], учитывающие свойства обрабатываемого материала и материала режущей части инструмента, состояние поверхности, период стойкости и число зубьев фрезы, ширину фрезерования.
7. Определяют частоту вращения шпинделя, мин-1, соответствующую найденной скорости резания:
n = 1000v .
p D
8. Корректируют частоту вращения шпинделя по паспортным данным станка и устанавливают действительную частоту вращения nд (Приложение 1).
9. По действительной частоте вращения nд, мин-1, определяют действительную скорость главного движения резания vд, м/мин:
v = p Dn д .
1000
10. Определяют скорость минутной подачи vs, мм/мин, по формуле vs = Szznд и корректируют ее значение по паспортным данным станка, т. е. устанавливают действительное значение vs.
11. Определяют эффективную мощность резания, кВт:
N эф =
P z v д .
60 ×1020
Ввиду отсутствия данных о мощности резания определяют главную составляющую силы резания при фрезеровании — окружную силу резания, Н, по формуле
= Р z |
P окр K мР ,
D q n w
где СР — коэффициент, характеризующий обрабатываемый материал и условия его обработки [2, табл. 41 на с. 291]; t — глубина резания, мм; Sz — подача на зуб, мм/зуб; В
— ширина фрезерования, мм; z — число зубьев фрезы; D — диаметр фрезы, мм; n — частота вращения шпинделя, мин-1; х, у, u, q, w — показатели степеней [2, табл. 41 на с. 291]; KмР — общий поправочный коэффициент на качество обрабатываемого материала [2, табл. 9—10, с. 264—265].
Остальные составляющие силы резания (рис. 3 и 4): горизонтальная Ргор (сила подачи), вертикальная Рверт, радиальная Ррад и осевая Рос определяются в зависимости от окружной силы Рокр.
Рис. 3. Схемы действия составляющих силы резания при встречном (а) и попутном (б) фрезеровании цилиндрической фрезой: Р — равнодействующая сил резания
При встречном фрезеровании цилиндрическими, дисковыми, угловыми и фасонными фрезами (рис. 3, а)
Ргор = (1,1...1,2)Рокр; Рверт = (0,2...0,3)Рокр; Ррад = (0,35...0,4)Рокр.
При попутном фрезеровании (рис. 3, б)
Ргор = (1,1...1,2)Рокр; Рверт = (0,7...0,9)Рокр; Ррад = (0,4...0,6)Рокр.
При фрезеровании торцовыми и концевыми фрезами:
■ при симметричном (рис. 4, а)
Ргор = (0,3...0,4)Рокр; Рверт = (0,85...0,95)Рокр; Ррад = (0,3...0,4)Рокр;
■ при несимметричном встречном (рис. 4, б)
Ргор = (0,6...0,8)Рокр; Рверт = (0,6...0,7)Рокр; Ррад = (0,3...0,4)Рокр;
■ при несимметричном попутном (рис. 4, в)
Ргор = (0,2...0,3)Рокр; Рверт = (0,9...1,0)Рокр; Ррад = (0,3...0,4)Рокр.
Осевая составляющая Рос силы резания для фрез с винтовыми зубьями определяется из соотношения
Poc = (0,2...0,4)tgω.
Рис. 4. Составляющие силы резания при торцовом фрезеровании: а — симметричном; б — несимметричном встречном: в — несимметричном попутном
Окружная сила Рокр при фрезеровании алюминиевых сплавов рассчитывается, как при фрезеровании стали: посредством введения коэффициента 0,25.
При расчете окружной силы Рокр по табличным данным не учитывается затупление фрезы. Затупление фрезы до допускаемого износа приводит к следующему увеличению окружной силы: при обработке мягкой стали (σв < 600 МПа) в 1,75—1,9 раз; во всех остальных случаях в 1,2—1,4 раза.
12. Определяют крутящий момент, Н · м, на шпинделе:
M кр
= P окр D .
2 ×100
13. Определяют эффективную мощность резания, кВт:
N эф
= P z v д .
60 ×1020
где vд — действительная скорость главного движения резания, мм/мин.
14. Проверяют возможность обработки заготовки на выбранной модели станка. Обработка возможна, если выполняется условие Nэф ≤ Nшп.
Мощность на шпинделе станка Nшп = ηNэд, где η — КПД станка (для новых моделей станков принимают η = 0,85).
15. Определяют машинное время, мин:
L |
= l + y + D ,
v
S д S д
где l — размер обработанной поверхности в направлении движения подачи, мм; у — врезание инструмента в направлении подачи, мм; Δ — выход (перебег) инструмента Δ = 1...5 мм.
При смещенном (несимметричном) фрезеровании врезание фрезы у = 0,3D.
t(D - t ) |
y = .
При черновом торцовом фрезеровании врезание инструмента
y = 0,5(D - D2 - B2 ).
При фрезеровании паза концевой фрезой врезание у = 0,5D.
Практическая часть
Пример 1. На вертикально-фрезерном станке 6Т13 производится торцовое фрезерование плоской поверхности шириной В = 100 мм и длиной l = 500 мм. Припуск на обработку h = 3,2 мм. Обрабатываемый материал заготовки — сталь 45Х с σв = 750 МПа. Заготовка представляет собой штамповку. Обработка — предварительная. Параметр шероховатости Rz 80 мкм.
Эскиз обработки приведен на рис. 5.
Требуется выбрать режущий инструмент, назначить режим резания и определить машинное время.
Рис. 5. Эскиз обработки к примеру 1.
Р е ш е н и е.
А. Выбор режущего инструмента.
1. Для предварительной обработки стали 45Х с σв = 750 МПа выбираем торцовую фрезу с вставными ножами из твердого сплава Т15К6 [1, табл. 17.3]. Диаметр торцовой фрезы выбирается в зависимости от ширины В фрезеруемой поверхности. Приблизительно диаметр фрезы D ≈ 1,6В мм, т.е. D = 1,6 · 100 мм. Выбираем стандартную фрезу диаметром D = 160 мм с числом зубьев z = 10 [1, табл. 17.15 на с. 42].
2. Выбираем геометрические элементы фрезы [1, табл. 17.6 на с. 410]. Для стали с σв = 750 МПа угол γ = 5...-5º, принимаем γ = 5º. Задний угол α = 12...15º, принимаем α = 12º. Угол в плане φ = 45... 75º, принимаем φ = 60º. Угол φ' = 5º, а угол φ0 = 0,5φ = 0,5 · 60º = 30º.
Б. Назначение режима резания.
1. Устанавливаем глубину резания. При черновом фрезеровании припуск снимается за один рабочий ход. Следовательно, глубина резания будет равна припуску на обработку h = 3,2 мм.
2. Назначаем подачу на зуб фрезы [1, табл. 19.12]. Выбираем табличное значение подачи на зуб Sz при черновом фрезеровании по схеме, представленной на рис. 5. При обработке стали 45Х торцовыми фрезами с вставными ножами из твердого сплава Т15К6 на станке 6Т13 подача Sтабл = 0,12 мм/зуб.
При смещенном фрезеровании создаются благоприятные условия для врезания зубьев фрезы в обрабатываемую заготовку, что позволяет увеличить Sz по сравнению с Sz при симметричном фрезеровании примерно в 2 раза.
На рис. 5 показана смещенная (несимметричная) установка фрезы. В этом случае подачу Sz, мм/зуб, определяют по формуле
Sz = SzтаблKSz
Поправочный коэффициент на подачу [1, табл. 19.12]
KSz = KSzи KSzHB KSzRz KSzφ KSzф KSzB,
где KSzи =1 — коэффициент, учитывающий материал фрезы; KSzHB = 1,1 — коэффициент, учитывающий твердость материала заготовки (220 НВ) при обработке детали средней жесткости (группа стали II); KSzRz = 0,9 — коэффициент, учитывающий состояние поверхности заготовки; KSzφ =1 — коэффициент, учитывающий главный угол в плане φ = 60º; KSzф =1 — коэффициент, учитывающий конструктивные элементы фрезы с механическим креплением; KSzB =1 — коэффициент, учитывающий отношение нормативной ширины фрезерования Вн к фактической Вф.
Следовательно,
Тогда
KSz = 1 · 1,1 · 0,9 · 1 · 1 · 1 = 0,99.
Sz = 0,12 · 0,99 = 0,119 ≈ 0,12 мм/зуб.
3. Назначаем период стойкости фрезы [1, табл. 17.7]. Для торцовой фрезы из твердого сплава диаметром D = 160 мм рекомендуемый период стойкости Т = 180 мин. Допустимый износ зубьев фрезы по задней поверхности [1, табл. 17.8 на с. 413] h3 = 1,0... 1,2 мм. Принимаем h3 = 1,2 мм.
4. Определяем скорость главного движения резания, допускаемую режущими свойствами фрезы [1, табл. 19.15]. Табличное значение скорости берем для D = 160 мм при отношении B/D = 0,63, глубине резания t до 5 мм и подаче Sz = 0,12 мм/зуб: vтабл = 252 м/мин.
При расчете скорости резания вводим поправочный коэффициент на скорость при фрезеровании [1, табл. 19.15]
KV = KVм KVHB KVи KVп KVхф KVφ KVф KVo KVz KVТ KVv.
Здесь коэффициент, учитывающий марку обрабатываемого материала (сталь 45Х),
KVм =0,9.
Коэффициент, учитывающий твердость материала заготовки (220 НВ) при обработке детали средней жесткости (группа стали II), KVHB =0,9.
Коэффициент, учитывающий материал режущей части фрезы (Т15К6), KVи =1. Коэффициент, учитывающий состояние обрабатываемой поверхности (поковка),
KVп =0,9.
Коэффициент, учитывающий характер фрезерования (черновая), KVхф =1. Коэффициент, учитывающий главный угол в плане (φ = 60º), KVφ =1.
Коэффициент, учитывающий тип фрезы (фреза, оснащенная многогранными неперетачиваемыми пластинами), KVф = 1,1.
Коэффициент, учитывающий условия обработки (с охлаждением), KVo =1. Коэффициент, учитывающий число зубьев фрезы (z = 10), KVz =1.
Коэффициент, учитывающий стойкость фрезы (Т = 180 мин), KVТ = 0,86.
Коэффициент, учитывающий скорость резания принимается средним для скоростей
v = 200 и 300 м/мин (vтабл = 252 м/мин), KVv = 0,92.
Следовательно,
KV = 0,9 · 0,9 · 1 · 0,9 · 1 · 1 · 1,1 · 1 · 1 · 0,86 · 0,92 = 0,63.
Тогда
v = 252 · 0,63 = 158,76 м/мин.
5. Определяем частоту вращения шпинделя, соответствующую расчетной скорости главного движения резания:
n = 1000v = 1000 ×158,76 = 316 мин-1.
p D 3,14 ×160
6. Корректируем частоту вращения шпинделя по паспортным данным станка 6Т13 и устанавливаем действительную частоту вращения nд = 315 мин-1.
7. Находим действительную скорость главного движения резания:
v = pDn
д 1000
= 3,14 ×160 × 315 = 158,3 м/мин.
1000
8. Определяем скорость движения подачи:
vS = Szznд = 0,12 · 10 · 315 = 378 мм/мин.
9. Корректируем скорость движения подачи по паспортным данным станка и устанавливаем действительную скорость подачи v Sд = 315 мм/мин (Приложение 1).
10. Находим действительное значение подачи на зуб фрезы:
S z д
= v S д
zn д
= 315 = 0,1 мм/зуб.
10 × 315
11. Определяем главную составляющую силы резания (окружную силу) по формуле
10C t x S y B u z
P = p z K .
z D q n w мP
Определяем [2, табл. 41 на с. 291] коэффициенты и показатели степеней: Ср = 825; х
= 1; у = 0,75; u = 1,1; q = 1,3; w = 0,2.
Глубина резания t = 3,2 мм. Ширина фрезерования В = 100 мм. Число зубьев фрезы z = 10.
Поправочный коэффициент для стали 45Х, учитывающий влияние качества обрабатываемого материала на силовые зависимости,
æ s ön р
K мр = çв ÷ ,
è 750 ø
где np = 0,3 — показатель степени при обработке стали [2, табл. 9 на с. 264].
Следовательно,
æ 750 ö0,3
K = ç ÷ = 10,3 = 1.
Тогда
мр è 750 ø
P z =
10 ×825 × 3,21 × 0,10,75 ×1001,1 ×10
1601,3 × 3150,2
1 = 3250 H.
12. Определяем мощность, затрачиваемую на резание:
N эф =
P z v д
60 ×1020
= 3250 ×158,3 = 8,4 кВт.
60 ×1020
13. Проверяем, достаточна ли мощность привода станка для обработки, т. е. выполнение условия Nэф ≤ Nшп.
Мощность на шпинделе станка Nшп = ηNэд. У станка 6Т13 мощность Nэд =11 кВт, а η
= 0,8 (Приложение 1). Тогда Nшп = 0,8 · 11 = = 8,8 кВт, а так как 8,4 < 8,8, следовательно, обработка возможна. В. Определение машинного времени. Используем формулу
L |
= l + y + D .
v
S д S д
Здесь путь, проходимый инструментом в направлении подачи, L = l + у + Δ. Длина фрезерования l = 500 мм.
Врезание y = 0,5(D - D2 - B2 )= 0,5(160 - 1602 -1002 )= 17,55 мм. Перебег Δ = 1...3
мм. Принимаем Δ = 3 мм. Действительная скорость подачи v Sд = 315 мм/мин. Следовательно,
T = 500 +17,55 + 3 = 1,65
м 315
мин.
Задача 1. На вертикально-фрезерном станке 6Т13 производится торцовое фрезерование плоской поверхности шириной В и длиной l. Припуск на обработку h.
Варианты данных к задаче приведены в табл. 1. Эскиз обработки приведен на рис. 5.
Требуется выбрать режущий инструмент, назначить режим резания и определить машинное время.
Таблица 1 – Варианты данных к задаче 1
Номер варианта |
Материал заготовки |
Заготовка | Обработка, параметр шероховатости поверхности, мкм | B | l | h |
мм | ||||||
1 | Сталь Ст3, σв = 460 МПа | Поковка | Черновая | 80 | 250 | 3,5 |
2 | Серый чугун, 160 НВ | Отливка | Черновая | 60 | 350 | 4 |
3 | Сталь 45Х, σв = 700 МПа | Поковка | Получистовая окончательная, Rz 40 | 100 | 500 | 1,2 |
4 | Сталь 30ХГС, σв =750 МПа | Штамповка | Получистовая окончательная, Rz 20 | 120 | 400 | 1,6 |
5 | Серый чугун, 210 НВ | Отливка | Черновая | 70 | 320 | 3 |
6 | Сталь 12Х18Н9 в состоянии поставки, 140 НВ | Прокат | Получистовая окончательная, Rz 20 | 90 | 200 | 1,5 |
7 | Алюминий АК8, σв =490 МПа | Штамповка | Получистовая окончательная, Rz 20 | 120 | 400 | 1,5 |
Окончание табл. 1
Номер варианта |
Материал заготовки |
Заготовка | Обработка, параметр шероховатости поверхности, мкм | B | l | h |
мм | ||||||
8 | Сталь 45ХН, σв = 750 МПа | Поковка | Черновая | 75 | 360 | 3 |
9 | Серый чугун, 220 НВ | Отливка | Черновая | 130 | 380 | 3,5 |
10 | Серый чугун, 180 НВ | Отливка | Черновая | 120 | 280 | 3,5 |
11 | Сталь 30ХН3А, σв = 800 МПа | Поковка | Черновая | 80 | 250 | 3,5 |
12 | Сталь 40, σв = 660 МПа | Отливка | Черновая | 60 | 350 | 4 |
13 | Серый чугун, 180 НВ | Поковка | Получистовая окончательная, Rz 40 | 100 | 500 | 1,2 |
14 | Сталь 45, σв = 700 МПа | Штамповка | Получистовая окончательная, Rz 20 | 120 | 400 | 1,6 |
15 | Бронза БрАЖН 11-6-6, 200НВ | Отливка | Черновая | 70 | 320 | 3 |
16 | Латунь ЛМцЖ52-4-1, 100 НВ | Прокат | Получистовая окончательная, Rz 20 | 90 | 200 | 1,5 |
17 | Сталь 50, σв = 750 МПа | Штамповка | Получистовая окончательная, Rz 20 | 120 | 400 | 1,5 |
18 | Серый чугун, 180 НВ | Поковка | Черновая | 75 | 360 | 3 |
19 | Алюминиевый сплав АЛ7, 60 НВ | Отливка | Черновая | 130 | 380 | 3,5 |
20 | Сталь 38ХМЮА, σв = 750МПа | Отливка | Черновая | 120 | 280 | 3,5 |
Пример 2. На горизонтально-фрезерном станке 6Т82Г производится цилиндрическое фрезерование плоской поверхности шириной В = 85 мм и длиной l = 350 мм. Припуск на обработку h = 1,6 мм. Обрабатываемый материал заготовки — серый чугун СЧ твердостью 180 НВ. Заготовка — отливка в кокиль. Обработка — черновая, выполняется с охлаждением.
Эскиз обработки приведен на рис. 6.
Требуется выбрать режущий инструмент и назначить режим резания с использованием нормативных таблиц.
Рис. 6. Эскиз обработки к примеру 2.
Р е ш е н и е.
А. Выбор режущего инструмента.
Выбираем фрезу (1, табл. 17.2) и устанавливаем ее геометрические элементы. Берем для обработки серого чугуна стандартную цилиндрическую фрезу из быстрорежущей стали Р6М5 с крупным зубом. При ширине фрезерования В = 85 мм и припуске на обработку h = 1,6 мм диаметр фрезы D = 80 мм [1, табл. 17.5], z = 10 [1, табл. 17.10].
Принимаем геометрические элементы фрезы. Передний угол γ = 10º [1, табл. 17.6]. Задний угол α = 12... 16º [3, табл. 16 на с.225], берем α = 16º. Угол наклона винтовой стружечной канавки для фрез с крупным зубом ω = 40º [1, табл. 17.10].
Б. Назначение режима резания.
1. Устанавливаем глубину резания. При черновом фрезеровании припуск снимается за один проход. Следовательно, глубина резания будет равна припуску на обработку t = h = 1,6 мм.
2. Назначаем подачу на один зуб фрезы Sz [2, табл. 34 на с. 283]. При фрезеровании по схеме, приведенной на рис. 6, при обработке серого чугуна цилиндрическими фрезами с крупным зубом из быстрорежущей стали Р6М5 на станке 6Т82Г подачу выбираем в зависимости от мощности двигателя станка (Nэд = 7,5 кВт) при средней жесткости системы Szтабл = 0,2...0,3 мм/зуб. Принимаем среднее значение подачи Szтабл = 0,25 мм/зуб.
Тогда
Sz = Szтабл K Sz.
Поправочный коэффициент на подачу при фрезеровании определяется следующим произведением [1, табл. 19.6 на с. 473]:
K Sz = KSzHB KSzl KSzZ KSzм.
Здесь коэффициент, учитывающий твердость материала заготовки (180 НВ), KSzHB
= 1,15.
Коэффициент, учитывающий длину оправки (l = 200 мм), KSzl = 1. Коэффициент, учитывающий крупные зубья фрезы, KSzZ = 1.
Коэффициент, учитывающий обрабатываемый материал, KSzм = 0,8. Следовательно,
Тогда
K Sz = 1,15 · 1 · 1 · 0,8 = 0,92.
Sz = 0,25 · 0,92 = 0,23.
3. Назначаем период стойкости фрезы [1, табл. 17.7]. Для цилиндрических фрез из быстрорежущей стали диаметром D = 80 мм рекомендуется период стойкости Т = 180 мин. Допустимый износ зубьев фрезы по задней поверхности при черновой обработке [1, табл. 17.8] h3 = 0,5...0,8 мм. Принимаем h3 = 0,8 мм.
4. Определяем скорость главного движения резания, м/мин, допускаемую режущими свойствами фрезы [1, табл. 19.9] при подаче Sz = 0,23 мм/зуб, отношении t/D = 0,02 и vтабл = 36 м/мин:
1,25.
v = vтабл KV.
Поправочный коэффициент на скорость резания определяем по формуле
KV = KVHB KVl KVп KVD KVz KVB KVT.
Здесь коэффициент, учитывающий твердость материала заготовки (180 НВ), KVHB =
Коэффициент, учитывающий длину оправки (1 – 200 мм), KVl =1.
Коэффициент, учитывающий состояние обрабатываемой поверхности (с коркой),
Куп = 0,7.
Коэффициент, учитывающий диаметр фрезы (D = 80 мм), KVD = 0,95. Коэффициент, учитывающий число зубьев фрезы (z = 10), KVz = 1.
Коэффициент, учитывающий ширину фрезерования (В = 85 мм), KVB = 0,85. Коэффициент, учитывающий стойкость фрезы, KVT = 1.
Следовательно,
KV = 1,25 · 1 · 0,7 · 0,95 · 1 · 0,85 · 1 = 0,71.
Тогда скорость резания
v = 36 · 0,71 = 25,6 м/мин.
5. Определяем частоту вращения шпинделя, соответствующую расчетной скорости главного движения резания:
n = 1000v = 1000 × 25,6 = 101,75
мин-1.
p D 3,14 ×80
6. Корректируем частоту вращения шпинделя по паспортным данным станка 6Т82Г и устанавливаем действительную частоту вращения nд = 100 мин-1.
7. Рассчитываем действительную скорость главного движения резания:
v = p Dn д д 1000
= 3,14 ×80 ×100 = 25,12
1000
м/мин.
8. Определяем скорость движения подачи:
vS = Sм = Szznд = 0,23 · 10 · 100 = 230 мм/мин.
9. Корректируем скорость подачи по паспортным данным станка 6Т82Г и устанавливаем действительную скорость подачи v Sд = 200 мм/мин (Приложение 1).
10. Находим действительное значение подачи на зуб фрезы:
S z д
= v S д
zn д
= 200 = 0,2
10 ×100
м/зуб
11. Определяем главную составляющую силы резания (окружную силу):
10C t x S y B u z
P = p z K .
z D q n w мP
Постоянный коэффициент СР и показатели степеней следующие [2, табл. 41 на с.
291]: СР = 30; х = 0,83; у = 0,65; u = 1,0; q = 0,83; w = 0.
Ширина фрезерования В = 85 мм. Глубина резания t = 1,6 мм.
Число зубьев фрезы z = 10. Диаметр фрезы D = 80 мм. Подача на зуб Szд = 0,2 мм/зуб.
Поправочный коэффициент для серого чугуна, учитывающий влияние качества обрабатываемого материала на силовые зависимости,
æ H B ön р
K мр = ç190 ÷ ,
è ø
где n p = 0,55 — показатель степени при обработке чугуна [2, табл. 9 на с. 264].
Следовательно,
æ180 ö0,55
К мР = ç190 ÷
= 0,97 .
è ø
Тогда сила
P z =
10 × 30 ×1,60,83 × 0,20,65 ×851,0 ×10
800,83 ×1000
0,97 = 3366,6 H.
12. Определяем эффективную мощность резания:
N эф
= P z v д
60 ×1020
= 3366,6 × 25,12 = 1,38 кВт.
60 ×1020
13. Проверяем, достаточна ли мощность привода станка для обработки. Обработка возможна, если выполняется условие Nэф ≤ Nшп.
Мощность на шпинделе станка Nшп = ηNэд. У станка 6Т82Г мощность Nэд = 11 кВт, а η = 0,8. Тогда Nшп = 0,8 · 11 = 8,8 кВт. Поскольку 1,38 < 8,8, следовательно, обработка возможна.
В. Определение машинного времени Тм. Используем формулу
L |
= l + y + D ,
v
S д S д
t(D - t) |
1,6(80 -1,6) |
Тогда
y = =
=11,2 мм.
T = 350 +11,2 + 3 = 1,82 мин.
м 200
Задача 2. На горизонтально-фрезерном станке 6Т82Г производится цилиндрическое фрезерование плоской поверхности шириной В и длиной l. Припуск на обработку h.
Варианты данных к задаче приведены в табл. 2. Эскиз обработки приведен на рис. 6.
Требуется выбрать режущий инструмент и назначить режим резания с использованием нормативных таблиц.
Таблица 2 – Варианты данных к задаче 2
Номер варианта |
Материал заготовки |
Заготовка | Обработка, параметр шероховатости поверхности, мкм | B | l | h |
мм | ||||||
1 | Алюминиевый сплав АК7ч, 60 НВ | Отливка | Получистовая окончательная без охлаждения, Rа 2,0 | 55 | 200 | 2,5 |
2 | Серый чугун, 150 НВ | Отливка | Получистовая окончательная, Rа 2,0 | 45 | 150 | 1,2 |
3 | Сталь 35, σв = 600 МПа | Прокат | Черновая с охлаждением | 80 | 180 | 4 |
4 | Сталь 45Х, σв =750 МПа | Поковка | Получистовая окончательная, Ra 3,2 | 90 | 280 | 1,6 |
Продолжение табл. 2
Номер варианта |
Материал заготовки |
Заготовка | Обработка, параметр шероховатости поверхности, мкм | B | l | h |
мм | ||||||
5 | Бронза БрАЖ9-4, 120 НВ | Отливка | Черновая с коркой без охлаждения, Ra 12,5 | 70 | 370 | 4,5 |
6 | Сталь 12Х18Н9 в состоянии поставки, 140 НВ | Штамповка | Получистовая окончательная, Ra 3,2 | 90 | 400 | 1,5 |
7 | Латунь ЛК80-3, 110 НВ | Отливка | Получистовая окончательная, без охлаждения Rа 2,0 | 45 | 130 | 1 |
8 | Серый чугун, 220 НВ | Отливка | Черновая по корке без охлаждения | 70 | 350 | 5 |
9 | Сталь Ст5, σв = 600 МПа | Поковка | Черновая с охлаждением | 65 | 100 | 3 |
10 | Сталь 40ХНМА, σв = 850 МПа | Штамповка | Получистовая окончательная, без охлаждения Rа 2,0 | 85 | 400 | 1,5 |
11 | Сталь Ст3, σв = 460 МПа | Штамповка | Черновая с коркой без охлаждения, Ra 12,5 | 55 | 200 | 2,5 |
12 | Серый чугун, 160 НВ | Отливка | Черновая по корке без охлаждения | 45 | 150 | 1,2 |
13 | Сталь 45Х, σв = 700 МПа | Отливка | Получистовая окончательная, Ra 3,2 | 80 | 180 | 4 |
14 | Сталь 30ХГС, σв =750 МПа | Поковка | Черновая с коркой без охлаждения, Ra 12,5 | 90 | 280 | 1,6 |
15 | Серый чугун, 210 НВ | Отливка | Получистовая окончательная, Rа 2,0 | 70 | 370 | 4,5 |
16 | Сталь 12Х18Н9 в состоянии поставки, 140 НВ | Штамповка | Получистовая окончательная, Rа 2,0 | 90 | 400 | 1,5 |
17 | Алюминий АК8, σв =490 МПа | Отливка | Получистовая окончательная без охлаждения, Rа 2,0 | 45 | 130 | 1 |
Окончание табл. 2
Номер варианта |
Материал заготовки |
Заготовка | Обработка, параметр шероховатости поверхности, мкм | B | l | h |
мм | ||||||
18 | Сталь 45ХН, σв = 750 МПа | Штамповка | Получистовая окончательная, Rа 2,0 | 70 | 350 | 5 |
19 | Серый чугун, 220 НВ | Отливка | Получистовая окончательная, Rа 2,0 | 65 | 100 | 3 |
20 | Серый чугун, 180 НВ | Отливка | Черновая по корке без охлаждения | 85 | 400 | 1,5 |
Пример 3. На вертикально-фрезерном станке 6Т12 концевой фрезой фрезеруют сквозной паз шириной В = 20 мм, глубиной h = 12 мм и длиной l = 150 мм. Обрабатываемый материал — сталь 40 с σв = 650 МПа и твердостью 190 НВ. Заготовка представляет собой прокат. Обработка — получистовая с охлаждением. Параметр шероховатости Ra 3,2 мкм.
Требуется выбрать режущий инструмент и назначить режим резания с использованием нормативных таблиц.
Р е ш е н и е.
А. Выбор режущего инструмента.
Выбираем фрезу и устанавливаем ее геометрические элементы [1, табл. 17.6]. Для обработки стали 40 с σв = 650 МПа и твердостью 190 НВ выбираем стандартную концевую фрезу из быстрорежущей стали Р6М5. Диаметр фрезы принимаем равным ширине паза, т.е. D = b = 20 мм, z = 6 [1, табл. 17.19].
Геометрические элементы фрезы следующие [1, табл. 17.6]: γ = 15º, α = 20º; углы по торцу γ1 = 0, α1 = 6º, φ1 = 3º. Угол наклона винтовой стружечной канавки для фрез с нормальными зубьями ω = 30...35º [1, с. 424].
Б. Назначение режима резания.
1. Устанавливаем глубину резания. При фрезеровании пазов концевой фрезой глубиной резания считают ширину паза, т.е. в данном случае t = b = 20 мм. Глубина паза при фрезеровании его за один рабочий ход принимается за ширину фрезерования В, т.е. В
= h = 12 мм.
2. Рассчитываем подачу на зуб фрезы, мм/зуб:
Sz = Szтабл K Sz.
Поправочный коэффициент на подачу представляет собой произведение следующих составляющих [1, табл. 19.28 на с. 505]:
K Sz = KSzD KSzZ KSzп
где KSzD =1 — коэффициент, учитывающий отношение вылета фрезы к ее диаметру (до 2);
KSzZ = 1 — коэффициент, учитывающий конструкцию фрезы с нормальными зубьями; KSzп
= 0,8 — коэффициент, учитывающий форму обрабатываемой поверхности (паза).
Следовательно,
K Sz = 1 · 1 · 0,8 = 0,8.
При фрезеровании стали 40 концевой фрезой из быстрорежущей стали диаметром D = 20 мм табличное значение подачи на зуб фрезы Szтабл, мм/зуб, выбирается [1, табл. 19.29] в зависимости от предельного значения произведения t × B = 20 × 12 = 240 мм2. При обработке пазов предельное значение t × B следует уменьшить в два раза, т.е. t × B = 120 мм2. Тогда выбираем Szтабл = 0,07мм/зуб.
Следовательно,
Sz = 0,07 · 0,8 = 0,056 мм/зуб.
3. Назначаем период стойкости фрезы (1, табл. 17.7]. Для концевых фрез из быстрорежущей стали диаметром D = 20 мм рекомендуется период стойкости Т = 60 мин. Допустимый износ зубьев фрезы при получистовой обработке по задней поверхности h3 =
= 0,3...0,5 мм [1, табл. 17.8]. Принимаем h3 = 0,5 мм.
4. Определяем скорость главного движения резания, допускаемую режущими свойствами фрезы при подаче Sz = 0,056 мм/зуб и отношении t/D = 1. В этом случае скорость vтабл = 20 м/мин [1, табл. 19.31], а скорость v находится по формуле
v = vтабл Kv.
Общий поправочный коэффициент на скорость резания определяется произведением следующих составляющих [1, табл. 19.28]:
KV = KVHB KVм KVп KVD KVT KVz KVB,
где KVHB =1,1 — коэффициент, учитывающий твердость материала заготовки (190 НВ) и выбираемый интерполированием при отношении t/D = 1; KVм =1 — коэффициент, учитывающий обрабатываемый материал (сталь 40); KVп = 0,8 — коэффициент, учитывающий состояние обрабатываемой поверхности (с коркой); KVD = 1 — коэффициент, учитывающий диаметр фрезы (D = 20 мм); KVT = 1 — коэффициент, учитывающий стойкость фрезы; KVz = 1,9 — коэффициент, учитывающий число зубьев фрезы (z = 6); KVB = 0,6 — коэффициент, учитывающий ширину фрезерования (В = h = 12 мм).
Следовательно, Тогда
KV = 1,1 · 1 · 0,8 · 1 · 1 · 1,9 · 0,6= 1,0.
v = 20 · 1 =20 м/мин.
5. Определяем частоту вращения шпинделя, соответствующую расчетной скорости главного движения резания:
n = 1000v = 1000 × 20 = 318,5 мин-1.
p D 3,14 × 20
6. Корректируем частоту вращения шпинделя по паспортным данным станка 6Т12 и устанавливаем действительную частоту вращения nд = 315 мин-1.
7. Определяем действительную скорость главного движения резания:
v = p Dn д д 1000
= 3,14× 20×315 = 19,78 1000
м/мин.
8. Определяем скорость движения подачи:
vS = Sм = Szznд = 0,056 · 6 · 315 = 105,8 мм/мин.
9. Корректируем подачу по паспортным данным станка 6Т12 и устанавливаем действительную скорость подачи vSд = 100 мм/мин (Приложение 1).
10. Находим действительное значение подачи на зуб фрезы:
S z д
= v S д
zn д
= 100 = 0,053 мм/зуб.
6 × 315
11. Определяем главную составляющую силы резания (окружную силу), Н:
10C t x S y B u z
P = p z K
z D q n w мP
Значение постоянного коэффициента СР и показатели степеней следующие: СР = 68,2; х = 0,86; у = 0,72; u = 1,0; q = 0,86; w = 0 [2, табл. 41 нас. 291].
Глубина паза t = 20 мм. Ширина фрезерования В = 12 мм. Число зубьев z = 6.
Диаметр фрезы D = 20 мм.
Действительная подача на зуб Szд = 0,053 мм/зуб. Поправочный коэффициент для стали [2, табл. 9 на с. 264], учитывающий влияние качества обрабатываемого материала на силовые зависимости, определяется по формуле
æ s ön р
K мр = çв ÷
è 750 ø
где n р = 0,3 — показатель степени при обработке стали [2, табл. 9 на с. 264].
Следовательно,
æ 650 ö0,3
K мр = ç 750 ÷
= 0,96 .
è ø
Тогда сила
P z =
10 × 68,2× 200,86 × 0,0530,72 ×121,0 × 6
200,86 ×3150
0,96 = 5704 H.
12. Определяем эффективную мощность резания:
N эф
= P z v д
60×1020
= 5704 ×19,78 = 1,84 60×1020
кВт.
Проверяем, достаточна ли мощность привода станка для обработки. Обработка возможна, если выполняется условие Nэф ≤ Nшп. Мощность на шпинделе станка Nшп = ηNэд. У станка 6Т12 мощность Nэд = 7,5 кВт, а η = 0,8, т. е. Nшп = 0,8 · 7,5 = 6 кВт. Поскольку 1,84 < 6 обработка возможна.
В. Определение машинного времени. Используем формулу
L |
= l + y + D ,
v
S д S д
где L — путь, проходимый инструментом в направлении подачи, мм; l — длина фрезерования, равная 150 мм; Δ — перебег, равный 3 мм; vSд — действительная скорость подачи, равная 100 мм/мин. При фрезеровании концевой фрезой паза врезание
y = D = 20 = 10 мм.
2 2
Машинное время
T = 150 +10 + 3 = 1,63 мин.
м 100
Задача 3. На вертикально-фрезерном станке 6Т12 концевой фрезой фрезеруют сквозной паз шириной B, глубиной h и длиной l. Обработка — получистовая. Параметр шероховатости Ra 3,2 мкм.
Варианты данных к задаче приведены в табл. 3.
Требуется выбрать режущий инструмент и назначить режим резания с использованием нормативных таблиц.
Таблица 3 – Варианты данных к задаче 3
Номер варианта | Материал заготовки | Заготовка | Обработка | B | l | h |
мм | ||||||
1 | Алюминиевый сплав АК7ч, 60 НВ | Отливка | С охлаждением | 30 | 200 | 6 |
2 | Серый чугун, 150 НВ | Отливка | Без охлаждения | 35 | 480 | 15 |
3 | Сталь Ст5, σв = 600 МПа | Поковка | С охлаждением | 22 | 420 | 12 |
4 | Сталь 45Х, σв =750 МПа | Поковка | С охлаждением | 16 | 100 | 6 |
5 | Бронза БрОЦ4-3, 70 НВ | Отливка | Без охлаждения | 40 | 200 | 8 |
6 | Сталь 20ХН, σв = 600 МПа | Прокат | С охлаждением | 25 | 400 | 5 |
Окончание табл. 3
Номер варианта | Материал заготовки | Заготовка | Обработка | B | l | h |
мм | ||||||
7 | Серый чугун, 220 НВ | Отливка | Без охлаждения | 40 | 520 | 18 |
8 | Сталь 30ХМ, σв = 780 МПа | Поковка | С охлаждением | 36 | 170 | 15 |
9 | Серый чугун, 180 НВ | Отливка | Без охлаждения | 24 | 120 | 12 |
10 | Сталь 30ХН3А, σв = 800 МПа | Штамповка | С охлаждением | 28 | 420 | 10 |
11 | Сталь 30ХН3А, σв = 800 МПа | Поковка | С охлаждением | 30 | 200 | 6 |
12 | Сталь 40, σв = 660 МПа | Отливка | Без охлаждения | 35 | 480 | 15 |
13 | Серый чугун, 180 НВ | Поковка | С охлаждением | 22 | 420 | 12 |
14 | Сталь 45, σв = 700 МПа | Штамповка | С охлаждением | 16 | 100 | 6 |
15 | Бронза БрАЖН 11-6-6, 200НВ | Отливка | Без охлаждения | 40 | 200 | 8 |
16 | Латунь ЛМцЖ52-4-1, 100 НВ | Прокат | С охлаждением | 25 | 400 | 5 |
17 | Сталь 50, σв = 750 МПа | Штамповка | Без охлаждения | 40 | 520 | 18 |
18 | Серый чугун, 180 НВ | Поковка | С охлаждением | 36 | 170 | 15 |
19 | Алюминиевый сплав АЛ7, 60 НВ | Отливка | Без охлаждения | 24 | 120 | 12 |
20 | Сталь 38ХМЮА, σв = 750МПа | Отливка | С охлаждением | 28 | 420 | 10 |
560 с.
Библиографические ссылки
1. Вереина Л.И. Справочник станочника: учебное пособие. – М.: Академия, 2008. –
2. Справочник технолога-машиностроителя: в 2-х томах – Т.2 / под ред. А.Г.
Косиловой и Р.К. Мещеряковой. – М.: Машиностроение, 1986. – 496 с.
3. Прогрессивные режущие инструменты и режимы резания металлов: справочник / под общ. ред. В. И. Баранчикова. – М.: Машиностроение, 1990. – 400 с.
Дата добавления: 2021-02-10; просмотров: 4169; Мы поможем в написании вашей работы! |
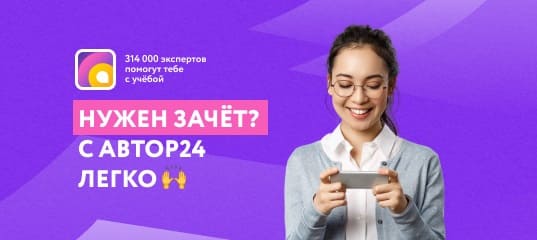
Мы поможем в написании ваших работ!