ТЕХНИЧЕСКИЕ ХАРАКТЕРИСТИКИ РАЗРАБОТКИ
Федеральное агентство Железнодорожного транспорта
Красноярский Институт Железнодорожного транспорта
Филиал ФГБОУ ВО
«Иркутский Государственный Университет Путей Сообщения»
Красноярский техникум железнодорожного транспорта
Отчет по учебной практике
Выполнил студент
Группы ЭПСв17-3: Фомин. А.А
Проверил преподаватель: Желнеров.В.И
Красноярск 2018-2019 года.
Лабораторная работа № 2
Тема: « Исследование технического состояния буксового узла»
Цель работы: систематизировать знания и приобрести навыки выявления неисправностей буксового узла на подшипниках качения путём исследования технического состояния роликовой буксы.
Оборудование: - буксовый узел на подшипниках качения в лаборатории техникума
Ход работы
1. Описать неисправности буксовых узлов и причины их возникновения;
2. Вычертить эскизы обмера буксового узла шаблоном Басалаева с описанием возможных неисправностей;
3. Охарактеризовать виды ремонта буксовых узлов и клейма, наносимые на крышку буксового узла;
4. Описать демонтаж и монтаж роликовой буксы;
|
|
5. Сделать вывод и краткий анализ о проделанной работе.
Методические указания
Для выполнения этой работы надо хорошо изучить неисправности буксовых узлов, их причины. Научиться выявлять неисправности буксовых узлов по внешним признакам при встрече поезда схода. Усвоить порядок проверки роликовых букс в эксплуатации. Изучить систему неразрушающего контроля, технологический процесс проведения ревизий роликовых букс, приёмку и приемку, и выходной контроль, а также приобретённые навыки практических занятий на полигоне. (Технология ремонта вагонов Б.В.Быков, В.Е. Пигарев, глава №3 - Ремонт колёсных пар, стр. 178-199).
1). В данном пункте я опишу основные неисправности буксовых узлов на подшипниках качения которыми являются:
· ослабление и разрушение торцевого крепления подшипников;
· трещины и разрывы внутренних колец;
· ослабление натяга (проворот) внутреннего кольца;
· износы и изломы сепараторов;
· обводнение смазки.
В настоящее время необходимо обязательно производить вихретоковый контроль сепараторов, обращая особое внимание на состояние мест перехода от перемычек к основанию. Износ и разрушение сепараторов, как правило, происходят из-за обводнения или недостаточного количества смазки в подшипниках, а также из-за механических повреждении сепараторов, не выявленных при полной ревизии буксы. Причинами попадания влаги в смазку являются неправильное ее хранение и нарушения технических требований к монтажу буксы. Не разрешается хранить смазку под открытым небом незащищенной от попадания атмосферных осадков. Во избежание попадания влаги в буксу не разрешается промывка колесных пар, подлежащих промежуточной ревизии, без специальной защиты буксового узла. При монтаже следует закладывать смазку в лабиринтное кольцо равномерно по всей окружности; необходимо заменять резиновые прокладки и кольца на новые и следить за прочностью болтовых креплений крышек.
|
|
Основная причина разрушения торцового крепления подшипников на шейке оси - нарушение требований монтажа букс: завышение зазоров между кольцами, неправильный подбор и установка гайки М 110. Следует тщательно контролировать состояние резьбы гаек и шеек осей. Проворот колец происходит из-за нарушения температурных режимов при монтаже букс, применение несовершенных измерительных приборов и инструментов или неправильной их настройки.
|
|
Все перечисленные выше неисправности приводят к повышенному нагреву букс.
Признаки неисправности буксового узла | Возможные неисправности | ||
При встрече поезда схода | |||
Наличие дыма, специфического запаха горелой смазки, пощелкивание в буксе | Разрушение подшипника | ||
Движение юзом одной из колесных пар при отжатых колодках | Заклинивание разрушенного подшипника | ||
Дребезжащий стук колеса о рельс, наличие на колесной паре нескольких ползунов | Разрушен подшипник, ролики периодически заклиниваются | ||
Выброс искр со стороны лабиринтной части | Проворот внутреннего кольца или разрушение заднего подшипника | ||
Корпус буксы грузовой тележки имеет наклон; боковая рама опирается на буксу одним краем | Проворот внутреннего кольца переднего подшипника | ||
Перемещение буксы вместе с рамой тележки вдоль оси, смещение вдоль шейки боковой рамы грузовой тележки, черный цвет крышки в зимнее время, наличие на смотровой крышке вмятин, цвета побежалости | Повреждение торцового крепления подшипников на шейке. Оборваны болты М20 или излом стопорной планки, гайка М110 сошла с резьбы, разрушен подшипник | ||
Резкий стук рычажной передачи, вертикальные перемещения буксы | Разрушение сепаратора | ||
Наличие искр между колесной парой и буксой, а также между колесной парой и рамой пассажирской тележки, слышен скрежет | Излом шейки оси | ||
При осмотре буксового узла во время стоянки поезда
| |||
Выброс смазки через лабиринтное уплотнение на детали тележки и кузов. Наличие в смазке металлических включений. Потеки смазки через крышки | Разрушение подшипника, обводнение смазки, проворот внутреннего кольца, заклинивание роликов | ||
Повышенный нагрев корпуса буксы в сравнении с другими буксами | Излишнее количество смазки, начало разрушения буксы | ||
Двойные удары или дребезжащие звуки при обстукивании смотровой крышки ниже ее середины | Повреждение торцового крепления подшипников | ||
Наличие на смотровой крышке пробоин, выпуклостей, протертостей, окалины | Повреждение торцового крепления подшипников | ||
Задняя часть корпуса нагрета больше передней | Разрушение заднего подшипника или нет зазора между лабиринтной частью корпуса буксы и лабиринтным кольцом | ||
Передняя часть корпуса буксы нагрета больше задней | Разрушен передний подшипник | ||
Разность зазоров между корпусом буксы и лабиринтным кольцом в верхней и нижней частях буксы более 1 мм при измерении специальными шаблонами | Разрушение одного из подшипников, проворот внутреннего кольца на шейке оси | ||
Смещение корпуса буксы относительно лабиринтного кольца более 1,4 мм | Повреждение торцового крепления | ||
Выделение дыма, наличие запаха из буксы (при проверке с хода и после остановки поезда) | Разрушение полиамидного сепаратора | ||
Разработка отверстия в кронштейне для валика подвески башмака, отсутствие валика, срез шплинтов его крепления, излом надбуксовой пружины, наличие ржавчины на пружинах буксового и центрального подвешивания пассажирской тележки | Разрушение одного или обоих подшипников | ||
Зазор между рамой тележки и потолком буксы менее 56 мм (для тележек КВЗ-ЦНИИ, КВЗ-5, ТВЗ-ЦНИИ-М) | Полное разрушение подшипников |
2) Вычерчиваю эскизы обмера буксового узла шаблоном Басалаева с описанием возможных неисправностей.
Проворот внутреннего кольца — нагрева буксы может не быть вообще, смазка по внешнему виду в хорошем состоянии, визуально подшипники исправны, а внутреннее кольцо заднего или переднего подшипника свободно вращается на шейке оси. На таком виде неисправности остановимся особо. Проворот внутреннего кольца вызывает ступенчатый износ шейки оси глубиной в несколько миллиметров. Такой характер износа объясняется тем, что внутреннее кольцо работает как подшипник скольжения. За счет ступенчатого износа шейки оси букса наклоняется. При провороте внутреннего кольца заднего подшипника возникает незначительный перекос корпуса буксы в сторону диска колеса. Износ шейки оси от проворота кольца переднего подшипника вызывает перекос в противоположную сторону. Ролики и дорожки качения внутренних и наружных колец перегружаются, что приводит к усталостномувыкрашиванию дорожек качения. Это особенно опасно тем, что в начальной стадии букса почти не дает нагрева. Проворот внутренних колец приводит к разрушению подшипников и шейки оси, но металлические примеси никогда не выбрасываются наружу, так как скапливаются вместе со смазкой внизу, в зазоре, образовавшемся при выработке оси. При названных неисправностях, явно угрожающих безопасности движения, крепление стопорной планки не всегда нарушается и металлические примеси в смазке могут быть незаметны.
Сама по себе прочность крепления болтов крепительной планки и чистота смазки еще не свидетельствуют об исправности узла. Система учета неисправностей показала, что чаще всего разрушается задний подшипник, так как динамическая нагрузка на него в несколько раз больше, чем на передний.
Неисправности заднего подшипника можно обнаружить по изменению посадочных зазоров между корпусом буксы и лабиринтным кольцом. Разность радиальных зазоров двух подшипников, установленных на одну шейку оси, допускается до 20 мкм, т.е. перекос корпуса буксы по отношению к лабиринтному кольцу практически невозможен. У исправной буксы зазор между корпусом буксы и лабиринтным кольцом примерно одинаково вверху и внизу и составляет суммарно 1,5 мм.
Разница зазоров вверху и внизу буксы свидетельствует о начавшемся разрушении заднего подшипника. Например, в начальной фазе разрушения заднего подшипника заднее кольцо, проворачиваясь на шейке оси, даст выработку в 1 мм. Следовательно, корпус буксы верхней частью как бы сядет на лабиринтное кольцо. Зазор между корпусом и лабиринтным кольцом в нижней части буксы увеличится на 1 мм, а в верхней — уменьшится на величину, равную выработке оси, или исчезнет совсем. При дальнейшей эксплуатации лабиринт корпуса начнет контактировать с лабиринтным кольцом. Ускорится нагрев узла и его дальнейшее разрушение.
Разрушение переднего подшипника — проворот. выработка дорожки качения и т.д., корпус буксы будет иметь наклон передней части и увеличенный зазор между корпусом и лабиринтным кольцом вверху.
Разрушение деталей крепления подшипников сопровождается сдвигом корпуса буксы по отношению к лабиринтному кольцу. Осевой разбег для двух цилиндрических подшипников в одной буксе обеспечивается ее конструкцией и составляет 0,68— 1,38 мм. Смещение корпуса на большую величину является признаком ослабления или разрушения деталей крепления на торце оси.
Повреждение торцевого крепления, проворот внутренних колец, разрушение подшипников можно выявить специальным шаблоном Басалаева
![]() | Предназначен для опрделения смещения и перекоса корпуса буксы относительно лабиринтного колца. Пределы измерений шкалы-от 0 до 10 мм. Ширина конуса щупа шаблона в месте нанесения рисок - 1+0,1; 2+0,1. Величина выступа на торце шаблона-1,5+0,2 |
Перекос буксы >1мм Шаблон Басалаева | ![]() | Клиновой выступ шаблона вводится внизу и вверху между корпусом буксы и лабиринтным кольцом. Если шаблон входит сверху и снизу на одинаковое расстояние, букса исправна. Если шаблон в верхней части входит меньше, чем в нижней, то неисправен задний подшинник.Если в верхней части входит больше, чем в нижней, то неисправен передний подшипник. |
Сдвиг буксы >1,5мм Шаблон Басалаева | ![]() | Вырезом в основании шаблона глубиной 1,7 мм проверяют смещение корпуса буксы относительно лабиринтного кольца, которое допускается не более 1,4мм. Смешение на большую величину позволяет выявить ослабление или повреждение торцевого крепления подшипников на оси. |
3) Охарактеризовать виды ремонта буксовых узлов и клейма, наносимые на крышку буксового узла
Промежуточная ревизия производится при обыкновенном освидетельствовании колесных пар, при их обточке без разборки букс, при единой технической ревизии пассажирских вагонов и по отдельным указаниям в качестве профилактической меры.
При промежуточной ревизии для контроля технического состояния буксы применяется установка для диагностирования подшипников.
Установка выявляет также такие неисправности подшипников, как отколы бортов колец и торцов роликов, усталостные и коррозийные раковины на дорожках качения колец и поверхности роликов, задиры на кольцах и роликах, ползуны на поверхности роликов, изломы упорного кольца и другие дефекты. Установка включает стенд для вращения колесной пары и диагностический блок, от которого к корпусам букс подводятся датчики. При обнаружении неисправностей буксового узла, колесная пара направляется на полную ревизию букс.
Перед производством промежуточной ревизии у выкаченных колесных пар буксы проворачивают для определения неисправностей на слух. При обнаружении толчков и ненормального шума производят полную ревизию. Контролируют надежность болтовых соединений смотровых и крепительных крышек, состояние лабиринтного уплотнения. Крышки и передние части букс протирают, снимают смотровую или крепительную крышку. Места прилегания крышек очищают от грязи и протирают, снятая крышка укладывается в закрываемый ящик внутренней стороной вверх. Из передней части буксы выбирают, смазку и перекладывают в снятую крышку для дальнейшего ее пользования. При этом необходимо соблюдать условия, исключающие попадание в крышку и буксу различных загрязнений.
При осмотре буксы определяют состояние смазки. Загрязнение смазки определяют визуально после растирания небольшого ее количества на тыльной стороне ладони. Буксы с загрязненной смазкой (стальные, латунные и другие примеси) направляют в полную ревизию. Потемнение смазки не является основанием для браковки.
Разработан прибор для определения качества проб смазки при производстве промежуточной ревизии роликовых букс. Для проверки смазки после снятия смотровых (крепительных) крышек берут из каждой буксы пробы по 4-5 грамм. Пробы смазки закладывают в прозрачный стакан емкостью 250-300 мл. В стакан наливают 100мл, предварительно нагретого в водной бане до температуры 70-900С бензина. Содержимое стакана тщательно перемешивают деревянной палочкой до получения однородной смеси. Если в смазке есть металлические частицы, они выпадают на дно стакана. Стакан с раствором помещают в отверстие в верхней части прибора (рис. 3.1) и включают прибор. Для определения содержания в смазке металлических примесей используют магнит, который вмонтирован в деревянную палочку. При перемещении палочки по дну стакана за магнитом увлекаются металлические частицы, перемещение которых наблюдают в зеркале прибора. По отражению в зеркале золотистой россыпи можно судить о наличии в смазке цветных металлов. Белый цвет смазки и её непрелипаемость к стенкам стакана свидетельствуют о наличии воды. В эксплуатации допускается наличие в смазке Л3-ЦНИИ механических примесей не более 1 %, воды - не более 1 %.
При хорошем состоянии смазки производят дальнейший осмотр переднего подшипника и деталей торцового крепления. При обнаружении трещин, изломов или других неисправностей подшипника буксу подвергают полной ревизии. При удовлетворительном состоянии подшипника контролируется стопорная планка или торцовая шайба, а также болты их крепления; ослабленные болты подтягиваются (болты стопорной планки подтягиваются в случае, если не производится обточка поверхности катания колеса). При ослаблеии болтов заменяют пружинные шайбы. Неисправную проволоку болтов стопорной планки необходимо заменить. Прочность крепления торцовой гайки проверяют ударами слесарного молотка по оправе, упираемой в шлиц гайки или в одну из граней коронки. Проверку , следует производить в обе стороны вращения гайки. Если ревизия выполняется при обыкновенном освидетельствовании колесных пар, независимо от состояния деталей крепления, снимают стопорную планку и подтягивают гайку. Колесную пару и гайку M110·4 с поврежденной резьбой к дальнейшей эксплуатации не допускают.
При торцовом креплении подшипников шайбой болты М20 освобождают от стопорения, а вращением по часовой стрелке динамометрическим ключом проверяют усилие их затяжки. При наличии хотя бы одного из болтов с крутящим моментом менее 50 Н·м, все болты откручивают и проверяют состояние резьбы болтов и резьбовых отверстий в оси. При обнаружении задиров, повреждений мест перехода от головки болта к стержню или других неисправностей болты заменяют. При обнаружении обрыва более трех первых ниток резьбы в резьбовых отверстиях оси или затруднениях при завертывании болтов крепления резьбовые отверстия разрешается исправлять мeтчиком. При повреждении более шести первых ниток резьбы в резьбовых отверстиях колесную пару не допускают к эксплуатации до специального указания. Болты, имеющие затяжку крутящим моментом более 50 Н·м, подтягивают усилием 230-250 Н·м. Затяжку производят равномерно. Завинчивание трех болтов производят дважды по периметру, а четырех - по схеме 1-2-3-4-3-4-2-1 с последующим их стопорением шайбой.
При обточке поверхности катания колес взамен снятой смотровой или крепительной крышки устанавливают временную с отверстием для прохода центра станка. После обточки колесной пары временную крышку снимают, проверяют состояние смазки надежность торцового крепления. После каждой обточки при обыкновенном освидетельствовании колесных пар под правый верхний болт крепительной крышки ставят дополнительную бирку, на которую наносят данные о месте, времени и порядковом номере обточки колесной пары.
При исправном состоянии смазки, переднего подшипника и деталей крепления в буксу закладывают ранее удаленную и при необходимости добавляют свежую смазку из расчета 1/3 свободного пространства передней части буксы, а затем ставят крышки. Между крышками ставят резиновую прокладку, новую или исправную, бывшую в употреблении. Между крепительной крышкой и корпусом устанавливают резиновое кольцо.
О проведении промежуточной ревизии на крышку буксы, предварительно очистив ее от грязи, наносят белой масляной краской надпись о времени и месте выполнения ревизии, а именно:
букву Р, месяц, две последние цифры года и присвоенный номер вагонного депо или завода.
Результаты ревизии заносятся в журнал формы ВУ-92.
Полная ревизия производится при полном освидетельствовании колесных пар, недопустимом нагреве букс, разрушении буксового узла, отсутствии бирки или неясности клейм на ней и при выполнении сварочных работ на вагоне или тележке без соблюдения требований. Ревизии подвергают обе буксы одной колесной пары.
При полной ревизии букс необходимо выполнить работы по демонтажу, промывке, осмотру и проверке деталей букс. При необходимости детали буксового узла ремонтируют или заменяют на исправные, а затем буксовые узлы вновь монтируют.
При полной ревизии буксовых узлов - а) для двух болтов, б) для одного болта. При промежуточной ревизии буксовых узлов - в) 1 - месяц, год, условный номер (клеймо) пункта, производившего полное освидетельствование колесной пары; 2 - индивидуальный номер колесной пары; 3 - знак "О", месяц, год, условный номер (клеймо) пункта, производившего обточку колесной пары без демонтажа буксовых узлов; 4 - код Государства-собственника колесной пары
После полной ревизии и монтажа букс на бирке выбивают:
- индивидуальный номер колесной пары, который включает в себя условный номер предприятия-изготовителя черновой оси, порядковый номер черновой оси и год изготовления черновой оси;
- дату полного освидетельствования (месяц и две последние цифры года);
- условный номер, присвоенный пункту, производившему освидетельствование колесной пары и монтаж букс;
- код Государства-собственника колесной пары (определяется по клейму, нанесенному на боковой поверхности ободов с наружной стороны колес).
Бирку изготавливают из листовой стали марки 10 кп толщиной 1,0—1,5 мм или оцинкованной стали толщиной 0,8—1,0 мм. Бирку устанавливают на левых верхних болтах крепительной крышки буксы правой шейки оси. Часть бирки, на которой выбита маркировка, загибают на верхнюю плоскость прилива корпуса. Бирку, укрепляемую одним болтом, не загибают. Допускается изготавливать бирки по условным штриховым линиям.
Если условный номер предприятия изготовителя черновой оси состоит из одного знака, то при написании индивидуального номера колесной пары его необходимо дополнить тремя нулями с левой стороны до четырех знаков, если из двух знаков, то дополнить двумя нулями, а если из трех — одним нулем.
Полную ревизии производят под контролем мастера, имеющего удостоверение на право производства полного освидетельствования колесных пар и полной ревизии букс.
4). В данном пункте опишу демонтаж и монтаж роликовой буксы.
Демонтаж букс с подшипниками качения выполняют на механизированной или полуавтоматической поточных линиях или ручным способом. Демонтаж букс на горячей посадке без снятия внутренних и лабиринтных колец производят при условии проверки оси специальным щупом ультразвукового дефектоскопа. Снимать внутренние и лабиринтные кольца букс на горячей посадке необходимо при их неисправностях, ремонте колесной пары со сменой элементов, а также при отсутствии соответствующих средств неразрушающего контроля.
При демонтаже буксы любым способом необходимо отвернуть болты крепительной крышки и снять ее вместе со смотровой. Из передней части буксы удалить смазку, отвинтить болты стопорной планки или тарельчатой шайбы, снять планку или шайбу. Далее с осей РУ1 отвинчивают и снимают торцовую гайку. Выкручивание болтов производят с использованием демонтажных стендов или гайковертов. Гайку снимают с помощью стенда или инерционным ключом. Снятые детали укладывают в контейнер для последующей обмывки. После удаления упорного кольца кран-балкой специальным захватом или буксосъемником снимают корпус буксы вместе с блоками подшипников (наружное кольцо с роликами и сепаратором). Из корпуса буксы пневмо- или гидропрессом удаляют блоки подшипников. При этом запрещается ударять молотком по корпусу буксы или подшипникам. При необходимости с шейки оси с помощью индукционного нагревателя снимают одно или оба внутренних кольца, а с предподступичной части оси лабиринтное кольцо.
Все детали буксового узла подают в моечные машины для промывки.
Монтаж буксовых узлов можно производить не ранее чем через 12 часов после обмывки колесных пар и через 8 часов после обмывки блоков подшипников. При этом разница температур между внутренними кольцами и блоками подшипников будет в пределах 3°С.
Монтаж буксового узла начинается с посадки лабиринтного кольца на предподступичную часть оси. Лабиринтные кольца подбираются с учетом натяга на посадку, равного 0,08…0,15 мм для новых колец и 0,02 …0,15 мм при ремонте. Для определения натяга измеряют микрометрическим или индикаторным нутромером внутренний диаметр предподступичной части оси. Эти измерения производят в двух взаимно перпендикулярных направлениях, определяя овальность посадочных поверхностей.
В настоящее время на предприятиях внедряется автоматизированная установка для подбора лабиринтных колец УПЛК-01.
Подобранные лабиринтные кольца нагревают в электропечи или масляной ванне до температуры 125…150°С и надевают на предподступичную часть оси, так чтобы оно упиралось в торец предподступичной части. Для этого на шейку оси надевают монтажную втулку, торцом которой наносят по лабиринтному кольцу удары до получения чистого металлического звука.
Перед установкой буксы на шейку оси в пазы лабиринтного кольца закладывают смазку.
Подобранные внутренние кольца нагревают в электропечи или масляной ванне до температуры 100…120°С, шейки осей перед установкой внутренних колец (если кольца нагревались в электропечи) покрывают тонким слоем веретенного АУ, индустриального 12 или трансформаторного масла.
На резьбу шейки устанавливают направляющий стакан 2 (рис.1).
Расположение приспособлений при установке внутренних колец:
а – заднего подшипника; б – переднего подшипника; 1 – монтажная втулка; 2 – направляющий стакан № 2; 3 – внутреннее кольцо заднего подшипника; 4 – лабиринтное кольцо; 5 – внутреннее кольцо переднего подшипника.
Нагретое внутреннее кольцо заднего подшипника 3 бортом вперед надевают через направляющий стакан на шейку оси и при помощи монтажной втулки 1 доводят до упора в лабиринтное кольцо 4.
После этого также устанавливают переднее внутреннее кольцо 5, обращая при этом внимание на плотность его прилегания к торцу внутреннего кольца заднего подшипника. Внутреннее кольцо переднего подшипника устанавливают так, чтобы его торец со скосом цилиндрической поверхности был обращен в сторону заднего подшипника.
После снятия направляющего стакана на шейку оси надевают упорное кольцо и либо с помощью торцовой гайки, либо тарельчатой шайбой с болтами затягивают посаженные внутренние кольца в осевом направлении.
По мере остывания внутренних колец гайку или болты подтягивают для обеспечения плотности прилегания колец друг к другу и к лабиринтному кольцу. Торцевое крепление остается затянутым до полного охлаждения колец, после чего оно разбирается. После этого производится проверка плотности прилегания внутренних колец друг к другу и к лабиринтному кольцу с помощью щупа толщиной до 0,04 мм, который может войти в зазоры между деталями на участке длиной не более1/3окружности. В подготовленный корпус буксы, посадочные поверхности которого покрыты тонким слоем масла, последовательно вставляют блок наружного кольца с роликами и сепаратором заднего подшипника маркированной стороной торца в сторону лабиринтного кольца, а блок переднего подшипника с маркированным торцом к передней части корпуса буксы.
Блоки подшипников перед установкой также смазываются жидкими маслами (цилиндровое масло марки 52 или 38).
Для облегчения установки корпуса буксы 3 с блоками подшипников 2 на шейку необходимо раздвинуть ролики втулкой 1
Корпус буксы 2 с установленными блоками подшипников и разжимной втулкой подводят к шейке оси. При этом втулка 1 надвигается на выступающую часть шейки до упора в торец внутреннего кольца, после чего корпус буксы с блоками подшипников надвигают на внутренние кольца. Разжимная втулка при перемещении буксы выходит из нее.
Далее устанавливают упорное кольцо переднего подшипника маркировкой в сторону крышки, на резьбовую часть оси навинчивают торцовую гайку, которую предварительно подбирают по резьбе шейки для обеспечения минимального зазора в соединении. Гайку затягивают до контакта с упорным кольцом переднего подшипника и дополнительно поджимают с крутящим моментом 100…150 Н·м (10…15кГс·м). Затем в паз оси устанавливают стопорную планку, не вводя ее хвостовик в шлиц гайки. Если хвостовик планки не входит в шлиц гайки, то производят дополнительную затяжку гайки до вхождения хвостовика планки в шлиц гайки. Поворот гайки в обратном направлении, т.е. ослабление затяжки гайки, запрещен.
После этого буксу необходимо слегка провернуть, чтобы убедиться в отсутствии заклинивания подшипников.
Стопорная планка крепится к торцу шейки оси с помощью двух болтов. Под болты устанавливают пружинные шайбы. Болты связываются проволокой диаметром 1,5…2 мм, проходящей через отверстия в головках.
При торцовом креплении подшипников тарельчатой шайбой после установки упорного кольца шайбу крепят к торцу шейки оси четырьмя болтами М20х60, под которые ставят специальную стопорную шайбу для закрепления одновременно четырех болтов.
На внешнюю поверхность торцовой гайки и к торцам сепаратора укладывают смазку в виде валика. Общее количество смазки, закладываемой в буксу, должно быть в пределах 0,8…1,0 кГ.
После закладки смазки устанавливают буксовую крышку. Между крепительной и смотровой крышками при их сборке ставят резиновую прокладку толщиной 3 мм. Эти крышки соединяются болтами М12 с пружинными шайбами.
На фланец крышки устанавливают новое резиновое кольцо, после чего буксу закрывают крышкой и крепят к корпусу буксы болтами М20 с пружинными шайбами. Под болт крепительной крышки буксы правой шейки с левой стороны устанавливают бирку с датой монтажа и номером пункта, производившего работу.
Буксы после монтажа окрашивают черной краской. Все данные монтажа заносят в журнал формы ВУ-90.
5). Какой можно сделать вывод и краткий анализ о проделанной работе.
В данной работе я усвоила основу для систематизирования знаний и приобретения навыков выявления неисправностей буксового узла на подшипниках качения путём исследования технического состояния роликовой буксы.
Опыт эксплуатации буксовых узлов покажет, что главными причинами выхода их из строя (отказа) являются допускаемые нарушения технологии при подборе и монтаже роликовых подшипников на шейку оси, а также несовершенства элементов корпуса буксы.
6). Литература
1. Пигарев В.Е. Технология ремонта вагонов - М.: Желдориздат, 2001.
2. Пастухов И.Ф. Конструкция вагонов: Учебник для колледжей и техникумов ж.-д. транспорта. - 2-е изд. - М.: Маршрут, 2004.
Тележка модели 18-9810 состоит из следующих узлов:
- рама тележки нежёсткого типа, состоящая из двух боковых рам 1 и надрессорной балки 2 (ОСТ 32.183);
- колесные пары марки РУ1Ш-957-Г 3 (без подшипниковых узлов) по ГОСТ 4835, на которые установлены конические двухрядные кассетные подшипники 4 закрытого типа с габаритными размерами 130х250х160 мм;
- адаптеры 5, обеспечивающие установку колёсных пар в буксовый проём;
- блокираторы 6 от вертикальных перемещений колёсных пар;
- центральное рессорное подвешивание с кусочно-линейной характеристикой, с каждой стороны тележки состоящее из комплекта 7-9 двухрядных (наружная и внутренняя) витых цилиндрических пружин (ГОСТ 1452), на две из которых опираются фрикционные клинья, а семь расположены под надрессорной балкой;
- фрикционные клинья 8, каждый из которых состоит из двух частей, образующих совместно наклонную поверхность пространственной конфигурации;
- тормозная рычажная передача 9, которая обеспечивает одностороннее нажатие тормозных колодок на колёса и оборудуется композиционными или чугунными (при особых условиях эксплуатации) тормозными колодками;
- шкворень 10;
- износостойкие элементы: износостойкое кольцо 11 упорной поверхности подпятника, износостойкий вкладыш 12 на плоскую опорную поверхность подпятника, планки 13 боковых стенок карманов надрессорной балки, вставки 14 карманов надрессорной балки, фрикционные планки 15, установленные на вертикальные стойки рессорного проёма боковой рамы, скобы 16 опорных поверхностей буксовых проёмов боковой рамы;
- боковые упругие скользуны постоянного контакта 17, состоящие из корпуса, внутрь которого вставлены два комплекта двухрядных (наружная и внутренняя) витых цилиндрических пружин, и колпака, который устанавливается сверху на пружины и входит внутрь корпуса.
ТЕХНИЧЕСКИЕ ХАРАКТЕРИСТИКИ РАЗРАБОТКИ
Тележка модели 18-9810
Наименование характеристики | Значение |
1. Масса тележки в сборе, кг | 4900, не более |
2. База тележки, мм | 1850 |
3. Конструкционная скорость движения вагона, км/ч | 120 |
4. Максимальная расчетная статическая нагрузка от колёсной пары на рельсы, кН (тс) | 230,5 (23,5) |
5. Расстояние между продольными осями боковых скользунов, мм | 1524 |
6. Расстояние между линиями приложения нагрузок к шейкам осей колёсных пар и продольными осями рессорных комплектов, мм | 2036 |
7. Назначенный срок службы, лет | 32 |
Дата добавления: 2021-01-20; просмотров: 101; Мы поможем в написании вашей работы! |
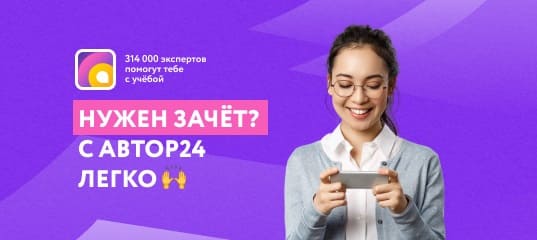
Мы поможем в написании ваших работ!