СВЕРХТВЕРДЫЕ ИНСТРУМЕНТАЛЬНЫЕ МАТЕРИАЛЫ
Компонентами сверхтвердых материалов являются: искусственные и естественные алмазы, рубины, сапфиры; не редко встречающийся кубический нитрид бора. Чаще всего, из этой группы, находят широкое применение алмаз и кубический нитрид бора, а рубин и сапфир используется редко и только для тонкого точения цветных металлов.
Алмаз, представляющий собой одну из форм строений углерода, обладает: высокой твердостью выше в 3 раза, чем у карбида титана; высокой теплопроводностью; небольшую склонность к адгезии. Однако он имеет низкую прочность как микролит. Однородная и плотная структура алмаза позволяет получить режущую кромку с малым радиусом округления, обеспечивая работу с небольшими сечениями среза. Успешное применение в тонком точении цветных металлов нашли алмазные лезвийные инструменты. Алмазы малопригодны для обработки черных металлов, из-за увеличенной хрупкости и невысокой стойкости, которая вызвана растворением алмазов в железе, при температуры более 750 градусов Цельсия. Так же алмазами оснащают торцевые фрезы и сверла.
Кубический нитрид бора синтезируется из порошка нитрида бора и, в зависимости от метода изготовления и строения кристаллической решетки, называется боразоном, эльбором, кубонитом, гексанитом, исмитом и т.п. На базе кубического нитрида бора с использованием других компонентов, например A12O4 или Si3N4, были получены композиты, превосходящих по своим свойствам основу.
|
|
Благодаря высокой твердости кубического нитрида бора (по твердости не уступает алмазу), высокой теплостойкости (1200-1500 градусов Цельсия), химической инертности по отношению к железу и углероду, позволили применять его для чистовой и тонкой обработки чугуна и стали с высокой скоростью рабочей подачи. Оснащенные инструменты на основе нитрида бора не имеют замены при обработке закаленных сталей, с твердостью до 64 HRA. Именно поэтому, их стойкость в десятки раз выше, чем у твердосплавных инструментов, а при обработки чугуна в 4-5 раз. На данный момент кубическим нитридом бора оснащают резцы и торцевые фрезы.
Со времени появления быстрорежущей стали (начало ХХ века) до современных твердых сплавов, 70-е годы прошлого века, производительность обработки, согласно документации Шведской фирмы «Coromant», увеличилась более чем в 30 раз. Так, обработка валика углеродистой стали диаметром 100 мм и длинной 500 мм составляла: 26 минут - резцами из быстрорежущей стали; 15 минут - резцами из стеллита или литые твердые сплавы; 3 минуты - резцами из современных твердых сплавов.
МАТЕРИАЛЫ ДЛЯ КОРПУСОВ ИНСТРУМЕНТОВ
Материалы для корпусов должны обладать следующими требованиями: высокая прочность и теплопроводность; соблюдать и сохранять точность размеров и формы после обработки; качественно обрабатываться и гарантировать прочное соединение с режущим элементом после сварки, наварки или напайки; обладать невысокой ценой; не должны содержать дефицитных элементов. В полной мере, этими качествами обладают конструкционные углеродистые стали – марки 40,45,50, и качественные стали – 40Х, 45Х, 40ХН.
|
|
Свое применение углеродистые стали нашли в таких сборных конструкциях, как державки резцов, корпуса сборных разверток, втулок, клиньев, винтов и т.п. Остальные корпуса составных и сборных инструментов выпускают из качественных сталей, в том числе и ножи под напайные пластины из твердых сплавов. Основной маркой качественной стали, для таких корпусов, считается 40Х, которая обладает повышенной прочностью и обеспечивает наименьшее коробление в процессе термической обработки.
В неблагоприятных условиях работы, где особенно требуется высокая твердость и износостойкость, корпуса изготавливают из инструментальных сталей У7А, У8А, 9ХС. Например, в случае, где корпус у сверл с напаянными пластинами из твердого сплава трется об обработанную часть детали с определенной скоростью резания - его изготавливают из стали 9ХС.
|
|
АБРАЗИВНЫЕ МАТЕРИАЛЫ
Абразивные материалы применяются для изготовления абразивных инструментов (кругов, брусков и пр.), а так же в форме зерен, которые являются режущими компонентами, поэтому они должны обладать высокой твердостью и теплостойкостью, нормально дробиться при затуплении, для образования новых острых кромок. Размеры зерен – в диапазоне от 2000 до 1 мкм:
· От 2000 до 160: шлифзерно;
· От 120 до 30: шлифпорошки;
· 28 и ниже: микропорошки.
Абразивные материалы, полученные естественным путем, например наждак или корунд, которые состоят из окиси алюминия A12O3, имеют большое количество посторонних примесей и обладают малой производительностью и на сегодняшний день, для изготовления промышленных абразивных инструментов применяются редко. В искусственных абразивных материалах нашли свое широкое применение электрокорунд, карбид кремния, карбид бора, синтетический алмаз и кубический нитрид бора (эльбор).
Электрокорунд включает в себя кристаллическую окись алюминия A12O3 и продукты плавки бокситов, и в зависимости от содержания окиси алюминия (от 92 до 99%) и метода изготовления делится:
|
|
· Электрокорунд нормальный: 16А…12А;
· Электрокорунд белый: 25А…22А;
· Электрокорунд хромистый: 34А…32А;
· Монокорунд: 45А…43А;
· Элетрокоруд титанистый: 37А.
Отличной режущей способностью и прочностью зерен обладают электрокорунд титанистый, хромистый и монокорунд, их применяют в долговременном режиме шлифования.
В результате спекания кварцевого песка с углеродом образуется карбид кремния (SiC) или корборунд. Выпускается в виде карбида кремния зеленого (64С…62С), с содержанием SiC не менее 98% и в виде карбида черного (55С…52С), с содержанием SiC в 95-97%.
Карбид кремния зеленый наиболее качественный и применяется для заточки твердосплавных инструментов, а карбид черный используется для шлифования материалов с низким пределом прочности, например чугуна, бронзы, латуни и других подобных материалов.
Карбид Бора (B4C) получают в процессе плавки борной кислоты и нефтяного кокса. По своей твердости он практически соответствует алмазу и изготавливается в виде порошков и паст. Предназначен для доводки твердосплавного инструмента и обработки твердых минералов – рубин, корунд, кварц.
Алмазы нормальной, повышенной и высокой прочности (в большинстве случаях искусственные) являются самыми твердыми материалами и обеспечивают самую высокую скорость обработки. Вследствие этого, именно их используют для высококачественной и производительной обработки твердых сплавов, твердых минералов, цветных металлов и их сплавов.
Кубический нитрид бора практически не уступает по своим свойствам алмазу, но применяется для обработки черных металлов или железосодержащих, потому как химически инертен к железу и углероду.
Ответить на контрольные вопросы:
1. Какие материалы применяются для производства режущих инструментов?
2. Какими свойствами должен обладать режущий инструмент?
3. Приведите примеры углеродистой режущей стали и где они применяются?
4. Как влияют легирующие добавки на свойства режущего инструмента?
5. Какие металлокерамические твердые сплавы вы знаете?
6. Какими преимуществами обладает металлокерамика при производстве режущего инструмента?
7. Назовите сверхтвердые инструментальные материалы и их преимущества перед другими твердыми сплавами.
8. Какие материалы применяются для изготовления корпусов инструментов?
9. Какие абразивные материалы применяются для заточки инструмента?
Дата добавления: 2021-01-20; просмотров: 124; Мы поможем в написании вашей работы! |
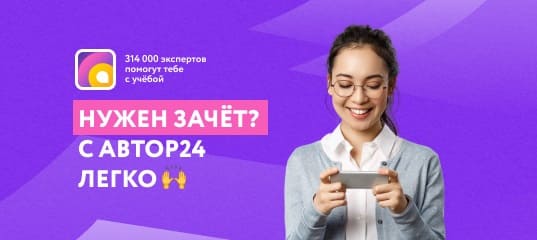
Мы поможем в написании ваших работ!