Тема 1.2 Подготовка углей к коксованию и процесс получения кокса
Раздел 1 ТОПЛИВО ДОМЕННОЙ ПЛАВКИ
Тема 1.1 Общие требования к топливу
В качестве топлива в современной доменной плавке применяют кокс, мазут, природный и коксовый газы и каменноугольную пыль. Основным видом топлива является кокс. Это единственный материал, который сохраняет форму куска в доменной печи на всем пути движения от колошника к горну. Благодаря этому обстоятельству обеспечивается прохождение газового потока через слой жидких, полужидких и твердых материалов в доменной печи. В нижней части печи раскаленный кокс образует своеобразную дренажную решетку, через которую в горн стекают жидкие продукты плавки. Высота столба шихты в современной доменной печи достигает 30 м, поэтому кокс, особенно в нижней части печи, воспринимает большие нагрузки. Отсюда вытекает основное требование, предъявляемое к коксу: высокая механическая прочность как в холодном, так и в нагретом состоянии.
Загружаемый в доменную печь кокс не должен содержать ни мелких кусков, ухудшающих газопроницаемость шихты, ни чрезмерно крупных кусков, которые, как правило, поражены трещинами и легко разрушаются в печи с образованием мелких фракций.
Кокс должен быть пористым для обеспечения хорошей горючести в горне печи и обладать высокой теплотой сгорания для получения требуемого количества тепла и необходимой температуры. Теплота сгорания кокса зависит от содержания в нем углерода, которое определяется содержанием золы, вредных примесей и летучих веществ в коксе. Чем выше содержание золы, вредных примесей и летучих веществ в коксе, тем меньше в нем углерода и меньше теплота его сгорания. Кроме того, с увеличением содержания золы и серы в коксе возрастают количество шлака, расход тепла на его расплавление и снижается механическая прочность кокса, а с увеличением содержания серы и фосфора в коксе ухудшается качество чугуна. Повышенное содержание летучих веществ в коксе свидетельствует о незавершенности процесса коксования, что приводит к снижению механической прочности кокса. Чрезмерно низкое содержание летучих в коксе, получающееся при пережоге кокса, также отрицательно сказывается на его качестве. Поэтому кокс должен содержать по возможности меньше золы, серы, фосфора и умеренное количество летучих веществ.
|
|
В коксе всегда содержится влага, поступающая в кокс при его тушении на коксохимическом заводе или из атмосферы. В связи с тем, что кокс в доменные печи загружают по массе, содержание влаги в коксе должно выдерживаться постоянным для сохранения заданного теплового режима печи.
В настоящее время расход кокса на выплавку 1 т чугуна в зависимости от условий производства колеблется в пределах 340— 640 кг и составляет 40—45% себестоимости чугуна. Это наиболее емкая статья затрат при производстве чугуна. Стоимость одной 1 тонны кокса -10000 рублей. Расход кокса уменьшают на 5—18%, применяя в качестве его заменителей природный газ, мазут и пылеугольное топливо. Важнейшими требованиями, предъявляемыми к заменителям кокса, являются их дешевизна и низкое содержание вредных примесей и золы. Применение заменителей кокса возможно лишь в ограниченных масштабах, так как ни один из них не может выполнить очень важную функцию кокса — разрыхление столба шихты и обеспечение дренажа жидких продуктов плавки.
|
|
Каменноугольный кокс
Коксом называется пористое спекшееся вещество, остающееся после удаления из каменного угля летучих веществ при нагревании его до 950—1200° С без доступа воздуха.
Характеристика углей для коксования
Для получения кокса используют только те угли, которые при нагревании способны размягчаться, вспучиваться под действием выделяющихся летучих веществ и затвердевать с образованием прочных кусков. Наилучшими для этой цели являются так называемые коксующиеся угли с выходом летучих веществ в пределах 18—27%. Угли с большим выходом летучих (газовые) или с меньшим (тощие) обычно спекаются плохо или не спекаются совсем. Для коксования применяют угли следующих марок: коксовые (К), жирные (Ж), отощенные спекающиеся (ОС) и газовые (Г).
|
|
Рис. 1. Схема процесса коксования в камере коксовой печи: / — слой сушки; 2 — слой начального разложения; 3 — пластический слой; 4 — слой полукокса; 5 — слой кокса; 6 — стенки камеры; 7 — направление выделения летучих веществ и смолы; 8 — направление выделения водяного пара и смолы
Тема 1.2 Подготовка углей к коксованию и процесс получения кокса
Основными требованиями, предъявляемыми к качеству угольной шихты, являются постоянство состава, оптимальная крупность, влажность и строго ограниченное содержание золы и серы. От качества подготовки угольной шихты в значительной мере зависит качество кокса.
Для подготовки углей к коксованию на коксохимических заводах имеются углеподготовительные отделения. Технологическая схема подготовки угольной шихты к коксованию состоит из ряда последовательных звеньев. 1.Поступающий на завод уголь различных марок подвергают предварительной шихтовке в приемных траншеях.
|
|
2.Уголь складируют в штабелях или бункерах механизированных закрытых угольных складов. При необходимости уголь направляют на обогащение для частичного удаления золы и породы, попавшей в уголь при его добыче, и частичного удаления некоторых видов серы, содержащейся в угле. При мокром обогащении концентрат подвергают обезвоживанию.
3. Обогащенные угли подвергают окончательному измельчению и направляют в угольную башню, из которой угли загружают в коксовые печи. Измельчают угли в молотковых дробилках и дезинтеграторах. Обогащение производят при помощи отсадочных машин, концентрационных столов и реожелобов. В результате обогащения получают концентрат, промежуточный продукт, вторично подвергаемый обогащению или используемый на энергетических установках, и хвосты, поступающие в отвал. Выход концентрата зависит от содержания примесей в исходном угле и применяемых способов обогащения.
4.Процесс-образования кокса протекает в камерах коксовых печей, изолированных от внешней атмосферы и соединенных лишь с аппаратами для улавливания выделяющихся при коксовании веществ. Подготовленную угольную шихту загружают в камеру шириной 350—450 мм. Стенки камеры в процессе коксования непрерывно обогреваются движущимися в вертикальных каналах продуктами сгорания газа. Тепло от стенок камеры передается угольной шихте, нагревая ее последовательно в направлении от стенок к оси камеры.
4.1Процесс образования кокса можно условно разделить на несколько стадий. В начальной стадии (при нагреве угольной шихты до 250° С) уголь подсушивается и начинает выделять летучие продукты разложения. В интервале 250—350° С выделяется легкая смола. При более высоком нагреве уголь превращается в пластическую массу, которая при температуре 500—600° С интенсивно разлагается с выделением смолы и газа, затвердевает и образует полукокс.
4.2 В следующей стадии при температуре 700° С полукокс разлагается с выделением преимущественно водорода и уплотняется. При 800° С выделение газа почти прекращается и при температуре около 1000° С происходит окончательное образование кокса.
Каждая из стадий во всей массе угольной шихты протекает неодновременно. Вначале шихта нагревается у стенок печи. По мере нагрева слой шихты претерпевает все стадии превращения в кокс. Слой готового кокса у стен постепенно увеличивается, перемещаясь в направлении к вертикальной оси камеры.
Современная коксовая печь включает камеру коксования, в которую через загрузочные люки, закрываемые крышками, загружается уголь, и отопительные простенки, в которых сжигается газ. Длина камер наибольшей коксовой батареи составляет 17000 мм, высота 7000 мм, ширина 410 мм, полезный объем 41,6 м3.
Коксовые печи выкладывают из динаса и группируют в батареи, обычно состоящие из 61—80 камер, с общими для всех печей системами подвода отопительного газа, подачи угольной шихты, отвода коксового газа, приема и тушения раскаленного кокса. Для отопления коксовой батареи используют доменный или коксовый газы или их смесь.
Тема 1.3 Принцип работы коксовой батареи
Воздух для горения газа засасывается из туннелей коксовой батареи через клапаны 1 (рис. 2) и подводные каналы 2 в регенераторы 3 и после подогрева поступает во все четные вертикальные каналы 4 отопительных простенков. Образующиеся продукты сгорания обогревают камеры коксования 5 с находящейся в них угольной шихтой и, пройдя через перевальные окна, поступают в нечетные вертикальные каналы 6 обогревательных простенков. Отдав тепло насадке регенератора 7, продукты сгорания поступают в борова по сборным каналам 8 и отводятся в атмосферу через дымовую трубу. Через каждые 20 мин путь газов в отопительной системе изменяют на противоположный и воздух начинает подогреваться в регенераторах 7, а продукты сгорания отводятся через регенераторы 3. Выделяющиеся при коксовании газообразные продукты возгонки поступают в газосборник 9 и по газопроводу коксового газа 10 направляются в химическое отделение. При отоплении батареи доменным газом часть регенераторов используют для подогрева доменного газа, который поступает по газопроводам 11. Прием раскаленного кокса, выдаваемого из камер при помощи коксовыталкивателей, и транспортировка его в башню тушения производятся тушильным вагоном. Охлажденный кокс поступает на коксосортировку.
Продолжительность процесса коксования колеблется в пределах от 12 до 16 ч Выход готового кокса зависит от содержания летучих и составляет 75—80% от массы загружаемой шихты. Производительность современной коксовой батареи достигает 1 млн. т кокса в год.
Кроме кокса, в процессе коксования получают коксовый газ и ценные химические продукты. Из 1 т угольной шихты получают 300—320 м3 коксового газа, около 33 кг каменноугольной смолы и 11 кг бензола, из которых химическим путем получают различные продукты. Коксовый газ, кроме отопления коксовых батарей используют в качестве металлургического топлива и сырья для химической промышленности.
Рисунок 2- Общий вид коксовой батареи с обслуживающими устройствами;
1- загрузочный вагон; 2 — двери камер коксования; 3 — угольная башня; 4 — башня тушения кокса; 5 — тушильный вагон; 6 — рампа для выгрузки потушенного кокса
Качество кокса
Качество кокса для доменных печей определяется химическим составом, физико-механическими и физико-химическими свойствами и зависит от свойств исходных углей; качества их подготовки к коксованию, технологии коксования и обработки готового кокса.
Кокс состоит из органических и минеральных веществ. Главной частью кокса является его органическая масса. В состав органической массы входят весь углерод кокса, большая часть серы (органическая сера) и небольшие количества водорода (Н2), кислорода (О2) и азота ( N 2 ). Минеральное вещество—зола — нежелательная, но неизбежная составляющая кокса. В состав золы входят вредные примеси: фосфор и некоторое количество серы (минеральная сера).
Более полное представление о качестве кокса по химическому составу дает технический анализ кокса. Этим анализом определяют содержание в коксе: летучих веществ V , золы А, влаги W и серы S.
Техническим анализом кокса содержание углерода в нем не определяют. Количество углерода, сгорающее в доменной печи, можно с допустимой точностью определить по разности
С = 100 — ( V + А + S ).
Зола является нежелательной примесью кокса, так как увеличивает количество шлака в доменной печи и требует увеличения расхода флюса и кокса на расплавление дополнительного количества шлака. Повышение зольности кокса связано с уменьшением содержания углерода и механической прочности кокса.
Содержание влаги в коксе зависит от способа тушения, пористости, ситового состава и степени готовности кокса. Кокс обладает низкой гигроскопичностью.
Влага в коксе при постоянном ее количестве в допустимых пределах не влияет на качество кокса и работу доменной печи. Содержание влаги в коксе зависит в основном от способа тушения кокса. При мокром тушении влажность кокса может изменяться в пределах 2—5%, иногда достигая 7—8%; при сухом тушении кокса она составляет десятые доли процента. В связи с тем что кокс в доменные печи загружают по массе, значительное колебание влажности кокса приведет к изменению количества углерода, загружаемого в печь, а следовательно, и к нарушению теплового режима доменной печи. Отсюда вытекают требование постоянства содержания влаги в коксе и необходимость текущего контроля влажности кокса перед загрузкой в доменные печи. Допустимое стандартом содержание влаги в коксе не должно превышать 5%.
Сера и фосфор — вредные примеси в чугуне. При выплавке чугуна с коксом в доменную печь вносится 80-90% серы. Перевод серы в шлак приводит к увеличению относительного выхода шлака и требует дополнительной затраты флюса и кокса, снижая производительность доменной печи. Удаление серы в процессе коксования тем полнее, чем выше выход летучих и температура коксования. Фосфор в коксе содержится в незначительном количестве, фосфористость кокса из донецких углей не превышает 0,02%, а из кузнецких и карагандинских 0,04—0,05%. Однако, учитывая, что в доменной печи фосфор полностью восстанавливается и переходит в чугун, содержание фосфора в коксе не должно превышать 0,015%. .
Физико-механические свойства кокса определяются его прочностью, термической стойкостью, газопроницаемостью, пористостью, гранулометрическим составом и насыпной массой.
Под прочностью кокса понимается способность кокса противостоять разрушающим усилиям всех видов.
Важнейшей характеристикой качества кокса является его термическая стойкость, определяемая прочностью кокса при высокой температуре в доменной печи. В нижней части печи кокс должен сохранять высокую прочность, чтобы обеспечить нормальое прохождение газов и жидких продуктов плавки.
Газопроницаемость слоя кокса оказывает большое влияние на работу доменной печи и зависит от соотношения крупных и мелких фракций в слое и от пористости кусков.
Дата добавления: 2021-01-20; просмотров: 292; Мы поможем в написании вашей работы! |
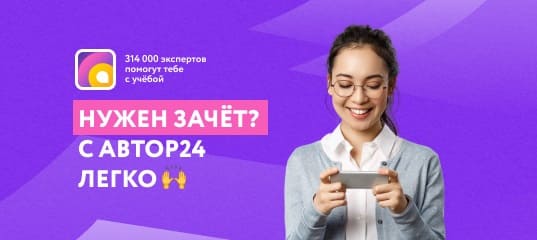
Мы поможем в написании ваших работ!