Переработка сточных вод и повторное их использование.
Лекция 1
Основные понятия. Структурная, функциональная, технологическая схемы переработки отходов. Основные принципы разработки ХТП.
Цель дисциплины- разработка химико-технологических процессов переработки отходов.
Основные понятия:
ХТП- совокупность физических и химических операций, в результате которых либо утилизируют отходы, либо обезвреживают.
ХТП- сложная система, взаимодействующая с ОС.
При разработке ХТП необходимо руководствоваться следующими основными принципами:
1. Системность.
Необходимо увязать (согласовать) разработку ХТП с экологическими вопросами защиты ОС (уровень антропогенной нагрузки, экономический ущерб и т. д.), а также связать с социальными вопросами (влияние на качество жизни, здоровье и т. д.).
2. Комплексная переработка отходов с получением индивидуальных товарных продуктов с последующей их реализацией.
3. Рациональное использование энергии (тепло химических реакций, фазовых превращений; физическое тепло, аккумулированное в отходе; тепло отходящих газов, жидкостей и твердых потоков).
4. Принцип цикличности- создание замкнутых систем водопользования, замкнутых систем газо- и воздухооборота.
Структурная схема промышленного производства.
Рис. 1.1. Структурная схема промышленного производства.
а) Основные стадии переработки отходов.
б) Схема переработки отходов.
а)
|
|
б)
Условные обозначения:
ВС- вторичное сырье- часть ВМР, к-ая может быть повторно использована.
ВМР- вторичный материальный ресурс- как потенциал для повторного использования.
На стадии пр-во и потребление образуются отходы:
Опр- отходы производства- остатки материала, полуфабрикатов, утративших полностью или частично свои потребительские свойства (пример: переработка аккумуляторов).
Опотр- изделия, материалы, утратившие свои потребительские свойства в результате физического, морального износов или контрафактная продукция.
НО- неутилизируемые отходы
Р- рассеивание
Пример 1.1. Переработка фосфогипса.
ФГ- тв. отход производства экстракционной фосфорной кислоты.
(Л.1. с. 210, рис. 4.3)
Химическая схема:
Са5F(PO4)3 + 5H2SO4 + 10H2O → 3H3PO4 + 5CaSO4∙2H2O + HF (1.1)
Реакцию 1.1 осуществляют в экстракторах. Процесс носит название: «Сернокислотное разложение апатита».
Апатит- минерал Ca5F(PO4)3
Активная часть: CaO ~45%
P2O5 ~до 42% (месторождение- Кольский п-ов, г. Апатиты)
Примеси: фтор + редкоземельные Ме до 7%
В результате сернокислотного разложения получают:
Реакционную смесь:
|
|
H3PO4- жидкость
CaSO4·2H2O – фосфогипс- тв. в-во
HF- газообразное в-во.
Реакционную смесь подвергают разделению:
карусельный вакуумфильтр: ЭФК и ФГ
жидкостная абсорбция: HF + H2Oпар
Лекция 2
Ресурсо- и энергосберегающие технологии в производстве экстракционной фосфорной кислоты.
H3PO4 – сильная кислота
2 метода:
термический метод
экстракционный метод
Термический метод основан на термическом сжигании фосфора в среде кислорода.
1 стадия. P + O2 → P2O5 (2.1)
реакция сжигания, сильно экзотермическая
2 стадия. P2O5 + 3H2O → 2H3PO4 (2.2)
Продукционная ортофосфорная кислота имеет концентрацию 85-86% масс. по P2O5 , практически без примесей.
Экстракционный метод основан на сернокислотном разложении апатитового концентрата.
Са5F(PO4)3 + 5H2SO4 + 10H2O → 3H3PO4 + 5CaSO4∙2H2O + HF (1.1)
Продукционная ЭФК с концентрацией 40% масс. по P2O5 (наличие примесей).
В зависимости от чистоты продукта различается область применения:
Чистая ортофосфорная кислота используется при фосфотировании Ме поверхностей (предварительная стадия перед окраской Ме поверхности), т. к. фосфорная кислота с добавками Zn или Mn образует на поверхности Ме защитную пленку.
|
|
В последнее время ортофосфорная кислота используется в парфюмерном пр-ве.
Область применения ЭФК:
Пр-во фосфорных и сложных концентрированных удобрений, а также получение фосфатов (кормовых), моющих и водоумягчающих средств.
Используется при крашении текстильных тканей, в реакциях органического синтеза (как катализатор).
По объему промышленного пр-ва в ассортиментной линейке занимает 3 место после серной и азотной кислот.
Некоторые характеристики водных растворов H3PO4 :
Таблица 2.1. Характеристики водных р-ров H3PO4 .
Давление атмосферное.
Конц. P2O5, % масс. | t затверд., °С | t кип., °С | Cp, кДж/(кг∙К) | ή (25°С), Па·с |
5 | 0,8 | 100,10 | 4,0737 | 0,0010 |
40 | -21,9 | 103,9 | 3,0271 | 0,0035 |
60 | -76,9 | 114,9 | 2,4995 | 0,0092 |
Как видно из табл. 2.1 с ростом концентрации изменяется t кип, t затверд,
Ср, ή.
Это объясняется строением водных растворов H3PO4 .
Согласно основным законам, установленная связь между C, t , P объясняется повышением (понижением) T фаз. превр. (кип., замерз.) за счет внутреннего строения р-ра и сил взаимодействия между растворенным в-вом и р-лем.
∆T = Tкип. р-ра - Tкип. чист. р-ля - температурная депрессия
Рис. 2.1. Зависимость температурной депрессии от концентрации.
|
|
|
|
С точки зрения технико-экономических показателей, большое преимущество имеет экстракционный способ (по сравнению с термическим).
Сравнение по минимуму приведенных затрат:
Зприв = Сб + Ен∙Куд (2.3)
Сб - себестоимость продукции, руб/т
Ен - нормативный коэффициент
Куд – уд. Капитальные затраты, руб/т
Ен = 1/Ток (2.4)
Ток – срок окупаемости
Сб = ∑Зi /ПR (2.5)
Куд = стоим. оборуд./ ПR (2.6)
∑Зi – текущие затраты
∑Зi = Зсырье + Зматер. + Зэнерг. + Зз.п. + Зремонт
ПRЭФК > ПRортофосф. к-ты (2.7)
При прочих равных условиях СбЭФК < Сбортофосф. к-ты
ЦЭФК < Цортф. к-ты
Условие (2.7) обусловлено народнохозяйственным спросом на рынке.
Сернокислотное разложение фосфатного сырья.
В основе лежит реакция (1.1).
Сырье- апатитовый концентрат
Источник- Карелия
Суть метода: извлечение (экстрагирование) H2O5 в виде H3PO4.
По этому методу природные фосфаты обрабатывают серной кислотой с последующим фильтрованием экстракционной пульпой с получением технической H3PO4 и осадка – ФГ.
Часть выделенного основного фильтрата, смешанного с промывочным раствором называют раствором разбавления, который возвращается в экстрактор для уменьшения вязкости реакционной пульпы в экстракторе.
Химическая схема процесса.
Классификация р-ции (1.1):
Гетерогенная (участники процесса находятся в разных фазах, а сам процесс протекает на границе раздела фаз).
Лимитирующей стадией является кристаллизация ФГ.
CaSO4∙2H2Oе ↔ Сае2+ + SO42- + 2H2O (2.8) ∆H< 0;
Обоснование технологического режима ТР.
ТР – такая совокупность технологических параметров (T,P,C), которая обеспечивает оптимальные условия эксплуатации оборудования.
Выбор и обоснование ТР будем проводить на основании данных о химическом равновесии и химической кинетике процесса.
Лекция 3.
Обоснование ТР производства ЭФК.
Выбор ТР на основании данных о хим. равновесии
CaSO4е ↔ Сае2+ + SO42- е; ∆H< 0 (3.1)
Анализ данных по химическому равновесию позволяет ответить на вопрос о возможности осуществления процесса.Позволяет определить равновесный состав реакционной смеси во время химического равновесия, а также позволяет управлять составом реакционной смеси в момент равновесия.
Для оценки влияния технологических параметров на состояние химического равновесия используют качественную и количественную оценки.
Изменять значение равновесной концентрации вещества в растворе- значит управлять величиной предела растворимости.
Нас интересует состояние реакционной системы, когда образуется осадок (ФГ).
Растворимое соединение выпадает в осадок при условии:
СМеn+,e∙CАm-,e > ПР/(γМеn+∙γАm-) (3.2) , где
γ- соответствующие значения коэффициентов активности ионов.
Учитывают реальные силы взаимодействия ионов по сравнению с идеальными растворами.
Таблица 3.1. Некоторые значения ПР.
соединения | СаСО3 | ZnS | PbCO3 | CdS | CaF2 | FeS |
ПР | 3.1∙10-9 | 1.6∙10-24 | 1.5∙10-13 | 1∙10-29 | 4·10-11 | 4·10-19 |
Пути управления процессом (р-ция 3.1) за счет смещения химического равновесия.
1 прием.
Добавление H2SO4 в реакционную смесь в экстракторе.
Хим. равновесие смещается влево (Сае2+ ↓) , движущая сила процесса увеличивается:
(∆ДСС)ДС = Сраб. – Сравн.
Рис. 3.1.а) Характер зависимости ССа2+,е от Т.
|

|
1- без дополнительных примесей;
2- с избытком H2SO4;
∆H< 0 , ↑Т приводит к смещению химического равновесия влево, т. е. растворимость в-ва ↓.
Рис. 3.1. б).
ССа2+,е
3- ход кривой растворимости при добавке H3PO4.
С увеличением концентрации H3PO4 в реакционной смеси, растворимость ФГ↑.
ДС = Сраб. – Се ↓.
Выбор ТР на основании данных о химической кинетике.
Химическая реакция (3.1) – гетерогенная, многостадийная.
Для описания кинетики используется модель с фронтальным перемещением зоны реакции и непрореагировавшим ядром (МФПЗРиНЯ).
Основные допущения:
Рассматривается единичная шарообразная частица ФГ в потоке жидкой реакционной смеси.
рис.3.2. Распределение концентраций веществ вблизи шарообразной частицы:
Реакционная смесь – сложная 3-х фазная система, динамическая, где тв. фаза- частицы образующегося ФГ;неразложившиеся частицы апатита;
жидкая фаза- фосфорная, серная кислоты;
газовая фаза- гидриды.
Лимитирующая стадия всего процесса – кристаллизация фосфогипса.
Условные обозначения к рис. 3.2:
ССа2+,ν, ССа2+,s, ССа2+,e – концентрация ионов Са2+ в объеме реакционной смеси, на поверхности твердой частицы ФГ и равновесная.
R- наружний радиус тв. ч-цы ФГ
δ – толщина пограничного слоя- это диффузионный слой, в котором сосредоточено основное сопротивление массопереносу.
Rсоп = 1/β или R= 1/βг (β- коэффициент массоотдачи)
Согласно МФПЗРиНЯ можно выделить основные стадии:
1. Внешняя диффузия ионов кальция из объема РС к наружней поверхности тв. ч-цы ФГ (кривая 1-2)
Wг = - 1/S·dWj/dτ (3.3)
S- поверхность раздела фаз
Уравнение (3.3) для 1 стадии:
Wг = β(ССа2+,ν – ССа2+,s) (3.4)
β≈D/δ
Пути управления скоростью на 1 стадии:
Измельчение δ↓→β↑
При этом средний размер частиц ФГ уменьшается, соотвктственно фильтрующие свойства осадка фосфогипса ухудшаются (увеличивается проскок твердых частиц через слой фильтрующего материала).
Лекция 4.
II. Поверхностная реакция.
WгII= kг*(ССа,е2+ - ССа,s2+) (4.1)
kг = [м/с] – константа скорости для гетерогенного процесса.
По уравнению Аррениуса:
kг = k0* (4.2)
Пути управления WгII:
Из уравнения (4.2) следует, что надо увеличивать температуру.
|

Окончательно выбор технологического процесса:
· Из анализа химического равновесия:
ü Размер частиц;
ü Кратность перемешивания;
ü Добавлять избыток серной кислоты на входе в реакционную смесь (больше стехиометрического значения), тогда концентрация ионов Са2+ падает – движущая сила процесса растет;
· Из кинетики:
ü При увеличении температуры константна скорости повышается, разность концентраций снижается
T↑ kг↑ ∆C↓
Анализ влияния температуры на растворимость ионов Са2+
|
|
|

Лимитирующей стадией процесса образования ФГ является поверхностная реакция. Температуру поддерживают на уровне 55-60°С не из соображений кинетики, а из-за морфологически образующегося кристалла (габитус – кристаллическая форма). При температуре 55-60°С образуется дендритная (игольчатая) форма кристалла (l>>d). А при температуре более 65°С образуется кристалл сферической формы (l≈d).
Из практики эксплуатации установок по производству фосфорной кислоты установлено, что наиболее «узким» местом, лимитирующим общую производительность установки, является процесс фильтрования. Следовательно, большие требования предъявляются при прочих равных условиях к форме кристаллов ФГ, образующего осадок на фильтрующем материале. Осадок должен обладать хорошими фильтрующими свойствами (максимальная суммарная порозность осадка). Этому будет удовлетворять структура дигидрата сульфата кальция – дендритная структура. Поэтому в основу классификации способов получения фосфорной кислоты положен вышеназванный признак. Тогда по способам получения фосфорной кислоты различают:
§ Дигидратный ФГ;
§ Полугидратный ФГ CaSO4*0,5H2O;
§ Ангидридный (безводный) ФГ CaSO4.
CaSO4 – основной компонент для вяжущих систем, используется в строительстве, медицине.
Дополнительные технологические приемы в производстве ЭФК.
Интенсифицирующие факторы делятся на:
· Экстенсивные (f);
· Интенсивные (T).
Основное уравнение массопередачи: , (4.3)
где f – поверхность массопередачи.
Для увеличения поверхности массопередачи в реакционную зону добавляют затравочные кристаллы ФГ с характеристикой fуд – отношение поверхности кристаллов к объему реакционной смеси, м2/м3. Для снижения вязкости реакционной смеси в реактор подают раствор разбавления.
Рис.4.1. Принципиальная схема получения ЭФК дигидратным методом.
Отечественные схемы производительностью 110тыс. P2O5/год реализованы на ОАО «Воскресенские минудобрения», ОАО «Череповецкий комбинат», зарубежные фирмы – «ДюПон де Немур» (Бельгия).
Сухой в виде порошка (классифицированный) апатитовый коцентрат из бункера 1 поступает на весовой дозатор 2 (класс 1А), далее – в экстрактор 4 (двухбаночный). Из емкости 3 в экстрактор поступает раствор 52% серной кислоты (тепло нейтрализации утилизируется на стадии выпаривания до концентрирования ЭФК).
Пульпа (РС) из экстрактора насосом 5 подается на карусельный вакуум-фильтр 7. Продукционную кислоты (основной фильтрат) собирают в емкости 8, промежуточный фильтрат – промывные растворы – в емкости 9.
ФГ с карусельного фильтра поступает на переработку. Раствор разбавления формируется из части продукционной кислоты и промывного раствора.
Из экстрактора 4 циркуляционная пульпа (ЦП) поступает в вакуум-испаритель 6, где происходит удаление паров фтора и воды (SiF4, HF), при этом происходит охлаждение ЦП, которая возвращается обратно в экстрактор.
Этот цикл организован для:
o Поддержания постоянной температуры в экстракторе;
o Поддержания в объеме РС необходимого количества затравочных кристаллов ФГ.
Лекция 5.
Аппаратурное оформление основных стадий ЭФК.
Рис. 5.1. Функциональная схема производства.
Стадия химических превращений.
Она осуществляется в экстракторе – емкостное оборудование, гуммированное (т.е. с внутренним антикоррозионным покрытием стенок и дна), с перемешивающими устройствами.
рис.5.2. Схема двухкаскадного экстрактора:
1-корпус; 2-внутреннее покрытие с антикоррозионным покрытием; 3-турбинная мешалка;
4,5-электромеханический привод (электродвигатель и редуктор); 6-соединительный трубопровод.
Штуцера: 7-ввода апатитового концентрата; 8- ввода серной кислоты;
9- возврата циркуляционной пульпы из вакуум-испарителя; 10-вывод циркуляционной пульпы на испаритель; 11-подача пульпы на фильтр; 12-ввод раствора разбавления.
Стадия разделения пульпы.
На этой стадии используется вакуум-фильтр с фильтрующей поверхностью от 8 до 307 м2.
Табл. 5.1. Основные типоразмеры карусельного вакуум-фильтра («Берд Прайон»).
Тип вакуум-фильтра | Общая поверхность, м2 | Рабочая поверхность, м2 | Диаметр, м |
12В | 20,6 | 15,5 | 7,7 |
18В | 46,6 | 38,7 | 11,5 |
24В | 68,2 | 60,4 | 14,6 |
30С | 157,9 | 139,4 | 20,4 |
рис.5.3. Принципиальная схема карусельного вакуум-фильтра:
Карусельный вакуум-фильтр 1 состоит из ряда фильтрэлементов 2, расположенных в одной горизонтальной плоскости и соединенных между собой таким оьразом, что при вращении стола 3 фильтрэлементы перемещаются по кругу (осуществляют круговое движение). Устройство вращения 4 позволяет создать ω=1/мин.
На рисунке 5.3 б) показано местоположение фильтраэлемента.
Преимущество карусельного вакуум-фильтра – значительная экономия площадей.
Рис. 5.4. Расчетная схема процесса фильтрования.
Пульпа после экстрактора (рис 4.1, поз. 4) поступает на основную фильтрацию (рис 5.4) с относительной влажностью ФГ 48%. Допущение: основной фильтрат не содержит ФГ и собирается в емкости 8 (рис. 4.1).
На вторую стадию фильтрации поступает ФГ с влажностью 43%, а затем поступает на третью стадию. Далее ФГ поступает на дальнейшую переработку.
Для лучшей отмывки фосфорной кислоты от ФГ на каждой стадии (основной, второй, третьей) осадок промывают промывным раствором (слабый раствор фосфорной кислоты). Это позволяет сократить потери, отмыть кислоту. Образующиеся промывные растворы используют в технологическом цикле как компонент разбавления.
Карусельный фильтр имеет корпус, внутри которого поддерживается определенное разряжение для удаления паров фтора из зоны фильтрации.
Лекция 6.
Переработка отходов (ФГ).
Табл. 6.1. Химический состав ФГ.
Фосфатное сырье | Содержание, % на сухое вещество (ангидрит) | ||||||
CaO | SO3 | P2O5 общий | P2O5 водн | R2O3 (редкозем) | F | Нерастворенный осадок | |
Хибинсткий апатитовый концентрат | 3,9-4,0 | 56-57 | 1,0-1,2 | 0,5-0,6 | 0,5-0,6 | 0,3-0,4 | 0,7-0,8 |
ФГ – это многотоннажный отход, пригодный для переработки.
Из табл. 6.1. следует, что ФГ содержит:
· значительное количество соединений Ca и SO3 – это возможность использования отхода в производстве строительных вяжущих;
· фтор – микроэлемент – фармацевтика;
· R2O3 – лантаноиды – электронная техника.
Т.е. с технико-экономической точки зрения есть полная целесообразность переработки ФГ с получением (выделением) индивидуального продукта.
Рассмотрим процесс переработки ФГ с получением строительных вяжущих.
Целесообразность переработки обусловлена не только основной задачей – получение строительных вяжущих (прибыль π1), но и сокращением затрат на транспортирование ФГ, его складирование и плату за отчуждение земли (дополнительное землепользование).
Сокращение этих затрат создает дополнительную прибыль - ∆π2. Окончательно решение о создании производства переработки твердого отхода принимается в результате:
1) оценки технико-экономической эффективности, где в общем случае доход равен
∑π = (D – P) > 0, (6.1)
где ∑π – суммарная прибыль,
D – расход,
P – доход.
2) Оценки срока окупаемости вложенных затрат:
Tокуп = [Tокуп. допуск]
Tокуп - вложенные затраты (возврат займа, прибыль по годам, рентабельность). Проходной уровень рентабельности для крупного бизнеса – 5-10%, срок окупаемости – 2,5-3 года.
Переработка ФГ – это ХТП, отражается:
§ Структурная схема;
§ Функциональная схема;
§ Химическая схема;
§ Технологическая схема.
Структурная схема – рис 1.1.б)
Рис. 6.1. Функциональная схема.
Химическая схема:
CaSO4·2H2O →T° CaSO4·0,5H2O +1,5 H2O (6.2)
CaSO4·2H2O →T° CaSO4 + 2 H2O (6.3)
Эти реакции можно записать в виде:
aA → rR +c1C (6.4)
aA → pP + c2C (6.5)
Процесс превращения сульфита кальция (А) отражается сложной параллельной химической реакцией.
Для оценки эффективности (технологической) используют критерий степень превращения:
(6.6)
Пример 6.1.
В автоклав поступает 32 кмоль вещества А (nA,0), на выходе в реакционной смеси nA,f = 8 кмоль. На входе в автоклав продукты отсутствуют. Определить степень превращения ФГ (хА) и количество образовавшегося полугидрата nr,f -?
ССС:
Целевая реакция: ∆ nA ’ = ∆ nR (6.7)
nA,0 – nA’ = - (nR,0 – nR,f) (6.8)
Побочная реакция: ∆ nA ” = ∆ nR (6.9)
nA ,0 – nA ” = - ( nR ,0 – nR , f ) (6.10)
∆nA = nR,f + nP,f
∆nA = nA,0 – nP,f = 32-8= 24 кмоль
nR,f = ∆nA - nP,f = 24-12= 12 кмоль
xA =
φ =
Проверка:
Лекция 7
рис.7.1. Схема автоклава: (Л1,стр.235 р.4.15)
Пульпа ФГ карусельного фильтра 7 (р.4.1) разбавляется технологической водой и транспортируется в виде шлама на стадии переработки. Здесь шлам подготавливают и подают в блок химических превращений, в который входит реактор автоклав. В нём осуществляются химические реакции (6.2) и (6.3). Под влиянием разности плотностей и размеров кристаллов дигидрата СК (CuSO4*2H2O) и полугидрата СК (СаSO4*½H2O).
При перемешивании пульпы (скорость несколько оборотов в минуту) создаются условия, при которых кристаллы ФГ (CaSO4*2H2O) перемещаются из верхних слоёв пульпы в нижние слои за время, достаточное для достижения степени превращения 0.8 (Х2). Полугидрат СК (СаSO4*½H2O)-ЦП выводят из нижней части автоклава по трубе 4 методом вытеснения за счёт избыточного давления в аппарате.
1-корпус аппарата (металлический);
2-тепловая рубашка.
В тепловой рубашке конденсируется пар, ∆i =2400 кДж/кг.
Перемешивающее устройство - тихоходная мешалка (лопастная).
Производительность реактора.
Пр = nr, f , (кмоль/с) (7.1)
τ
Yr = Пр , (кмоль/м³*с) (7.2)
V
Интенсивность более информативный параметр с точки зрения технико-экономических соображений, чем производительность, т.к. интенсивность включает в себя не только расходные параметры, но и коэффициенты удельной материалоёмкости.
Расчёт (пример 6.2).
Из примера 6.1 использовать исходные данные для определения интенсивности и производительности.
Sпрям.оакс=S под кривой, т.е. сделаны допущения, что все частицы пребывают 0.3 часа.
V=20 м³ (габариты реакционной зоны)
Пр=12/0.3=40 кмоль/с
Y=40/20=2 кмоль/м³*с
Пути управления процесса.
↑ Пр, ↑ Yr, τ=V/v
если τ ↑→v ↓→Ха
ССА
↑ Ха = ∆h/na0 = nr,f/na0 ↑
если побочной реакцией пренебречь
↓Пр=↑Сr*v
для непрерывных процессов
при τ ↑ => Пр ↓
РИС
τ = ∆Са =Cr , f ↑
ω ωr,a↑
Основной путь увеличения Пр-это увеличение wr.
Лекция8
Нитрозные газы.
Задача. Реакция проходит в химическом реакторе при t=700°С (предварительный нагрев до t=400°С) на алюмопалладиевом катализаторе. Оксиды азота восстанавливаются до N2 с использованием восстановителей (CH4).
Реакция восстановления: CH4 + 2O2 = CO2 + 2H2O;
CH4 + 4NO = CO2 + 2H2O + 2N2
Математическая модель реактора описывается 4 уравнениями (3 УМБ по компонентам + 1 УТБ):
1) dCO 2 = - 2F K0,1 exp( - E1 ) C1,3CH4 CO2
dl V RT
2) dCNO = -4F K0,2 exp( - E2 ) CCH4 CNO
dl V RT
![]() |
3) dCCH 4 = - F K0,3 exp(-E3) C1,3 CH4 CO2 + K0,2 exp(-E2) CCH4 CNO
dl V RT RT
4) dT = ___F__( H1K0,1 exp (- E1 ) C1,3CH4 CO2 + H2K0,2 exp (- E2) CCH4CNO )
dl VCp RT RT
где: · V – объемный расход газа, м3/ч;
· С – концентрация соответствующего компонента, % об.;
· F – площадь проходного сечения реактора,м2;
· H - тепловой эффект реакции, кДж/ моль;
· l – высота слоя контактной массы, м.
· E1=E3= 11,8 кДж/моль, E2 = 78,88 кДж/моль – энергии активации;
· Сp = 31,2 кДж/моль К – молярная теплоемкость при p=const.
газ
Исходные данные:
· Dапп.= 3,6 м;
· Vн= 82 000м3/ ч;
· Сн CH4 = 1,4 % (от общего объема);
· Сн O2 = 2,6 %;
· Сн NO = 0,13%;
· ПДК (NO) = 0,448 *10 -4 %об.;
· Hкат. = 0,6 м;
· Ск O2 =0,222 % об;
· Ск NO = 2,25 *10-5 %;
· СкCH4 = 0,178 %.
Задание: 1) составить МБ для каталитической очистки нитрозных газов;
2)определить объем контактной массы.
Решение:
1) Vк.м. = ПDапп.H/4 = 3,14 (3,6)2 0,6 = 6,1 м3
4
Состав нитрозных газов: 18% паров H2O, N2 и др. компоненты (см. ниже).
компонент | m, кг/ч | V, м3/ч | % об. | ||
вход | 1. | CH4 | 820,024 | 1 148 | 1,4 |
2. | O2 | 3 046,4 | 2 132 | 2,6 | |
3. | NO | 142,85 | 106,6 | 0,13 | |
4. | N2 | 79 861,45 | 63 853,4 | 77,87 | |
5. | H2O | 11 867,04 | 14 760 | 18 | |
å | 95 737,76 | 82 000 | 100 | ||
выход | 1. | CH4 | 103,85 | 145,38 | 0,177 |
2. | O2 | 260,12 | 182,04 | 0,222 | |
3. | NO | 0,0247 | 0,01845 | 2,25* 10-5 | |
4. | N2 | 79 928,1 | 63 942,48 | 77,979 | |
5. | H2O | 13 477,17 | 16 762,65 | 20,442 | |
6. | CO2 | 1 967,94 | 995,92 | 1,18 | |
å | 95 737,76 | 82 000 | 100 |
2) Концентрация N2 в газе на входе в аппарат:
C N2 (%) = 100-18-2,6-0,13-1,4 =77,87 %
3) Количество реагентов на входе:
а) объемные расходы
VCH4 = 82 000 1,4 = 1148 м3/ч
100
VO2 = 82 000 2,6 = 2 132 м3/ч
100
VNO = 82 000 0,13 = 106,6 м3/ч
100
VH2O= 82 000 0,18 = 14 760 м3/ч
100
VN2 = 82 000 77,87 = 63 853,4 м3/ч
100
б) массовые расходы
· rCH4 = 16 = 0,7143 кг/м3
22,4
m CH4 = V CH4 * rCH4 = 1148 * 0,7143 = 820,024 кг
· rO2 = 32 = 1,4289 кг/м3
22,4
m O2 = V O2* rO2 = 2 132 * 1,4289 = 3046,4 кг/ч
· rNO = 30 = 1,3401 кг/м3
22,4
m NO = V NO* rNO = 106,6 * 1,3401 = 142,85 кг/ч
· rN2 = 28 = 1,2507 кг/м3
22,4
m N2 = V N2* rN2 = 1,2507 * 63 853,4 = 79 861,45 кг/ч
· rH2O = 18 = 0,804 кг/м3
22,4
m H2O= V H2O * r H2O =14 760 * 0,804 = 11 867 кг/ч
· rCO2 = 44 = 1,976 кг/м3
22,4
По вычисленным с помощью ЭВМ концентрациям на выходе из аппарата, находим объемные расходы газов на выходе из контактного аппарата.
4) Объемные расходы на выходе:
VO2=82000/100·0,222=182,04 м3/ч;
VNO=82000/100·2,25·10-5= 0,01845 м3/ч;
По количеству израсходованного по уравнению реакции (1) O2, определяем количество водяных паров, СO2 и израсходованного метана:
VH2O= ∆VO2= 2132-182,04=1949,96 м3/ч;
VCO2= 1949,96/2= 974,98 м3/ч;
∆VCH4= 974,98м3/ч;
Аналогично рассчитываем количество реагентов по 2-ой реакции:
VH2O= ∆VNO/2=(1066-0,01845)/2=53,29м3/ч;
VCO2= 53,29/2= 26,64м3/ч;
∆VCH4=26.64м3/ч;
Количество СH4 на выходе из реактора:
VCH4= 82000·0,178/100=145,4 м3/ч;
VCH4=1148-(974,98+26,64) = 145,38 м3/ч;
mCH4= VCH4·ρCH4=145,38·0,7143=103,85кг/ч;
Определяем массовые расходы O2 и NO на выходе:
mO2= 182,04·1,4289=260,12 кг/ч;
mNO= 0,01845·1,3401=0,0247 кг/ч;
Количества прореагировавших в-в:
∆mNO=142,85-0,0247=142,83 кг/ч;
∆mO2= 3046,4-260,12= 2786,28 кг/ч;
По уравнениям реакций определим компоненты и просуммируем:
CH4+ 2O2= CO2+ 2H2O;
64 44 36
2786,28 X1 Y1
X1=2786,28·44/64=1915,57 кг/ч;
Y1= 2786,28·36/64= 1567,2957 кг/ч;
CH4 + 4NO= CO2+ 2H2O+ 2N2;
120 44 36 56
142,83 X2 Y2 Z2
X2= 142,83·44/120= 52,37 кг/ч;
Y2= 142,83·36/120= 42,85 кг/ч;
Z2= 142,83·56/120=66,65 кг/ч;
mCO2= X1+X2=1967,94 кг/ч;
mH2O= Y1+Y2+ 11867,04=13477,17 кг/ч;
mN2= Z2+ 79861,45= 79928,1 кг/ч;
Лекция 9
Эколого-экономичекая оценка
(эффективность производства переработки отходов) R ээ .
Rээ=Зпm*Пр* η*n*M (9.1)
Зпm - приведённые затраты (для функционирования инженерного барьерного
сооружения ИБР), руб/год;
Пр - производительность ИБС по переработанному отходу;
η - коэффициент эффективности ИБС;
n - коэффициент воздействия на ОС;
M - коэффициент использования материальных ресурсов.
Зпm= Cг+kг*εн (9.2)
Сг-годовые эксплуатационные расходы, руб/год;
kг -капитальные вложения (затраты на конструирование, документацию,
строительство, стоимостную основу оборудования (ИБС), пуск и наладочные
работы);
εн - нормативная эффективность.
εн= 1 (9.3)
Ток
Ток – срок окупаемости затрат на ИБС
Сг=Зсырьё+ Змат-я+ Зэнерг.+ Амфт+ Ззп
Пр
Амфт=0.12 ОПФ
Оценка экономической эффективности осуществляется по приведённому критерию
Зпт=(Сг+Ен+Кг)=> min
η => иногда совпадает со степенью очистки
η= С о -С1 (9.4)
С
η= ПДВ (9.5)
mотх
ПДВ – предельно допустимый выброс, год
mотх – суммарная масса отходов
ПДВ(ПДС)-массы выбросов (сбросов) вредных веществ в единицу времени от данного источника загрязнения ОС (или совокупности источников) с учётом рассеивания вредных веществ в атмосфере (ПДВ) или разбавления веществ в водной системе (ПДС), причём концентрация взвешенных веществ не превышает ПДК:
- для загрязнения атмосферы - приземная концентрация,
- для загрязнения водной системы – в створе потоков (загрязнённых сточных вод и чистой воды)
М=mцелевого продукта
mизрасход.сырья
Рис.9.1. Технологическая схема производства автоклавных (высокопрочных) гипсовых вяжущих:
Любая ХТС может быть разделена на несколько блоков.
БП – блок подготовки исходных реагентов (физические процессы-нагревание, охлаждение, отстаивание и т.п.)
БХП – это 1(несколько) реакторов, в которых получают целевой продукт, находящийся в смеси с непрореагировавшим ИР
БР – выделение ЦП из РС (физические процессы)
БК – блок кондиционирования
На рис. 9.1 представлена технологическая схема производства автоклавных высокопрочных гипсовых вяжущих на ОАО «Воскресенские минудобрения», где продукт ПГ – полугидрат СК (уравнение 6.2)
Требования к продукту:
-марка Г10 (Г19) ГОСТ 125-79 мелкокристаллический продукт (порошок),
-удельная поверхность см²/г=1 см²/г,
-предел прочности σ= 35 МПа
ФГ => 1-первичный репульп. (ФГ рис. 4.1), где его разбавляют водой и перекачивают насосом 2, далее в сборник 3. Из сборника 3 насосом 4 пульпу подают непрерывно на БВФ 5. Сточные воды поступают на нейтрализацию. ФГ направляют основной репульпатор 6, обогревают паром для защиты от коррозии, далее в пассиватор HNO3.
Далее рабочая пульпа под давлением перекачивается насосом 7 => в автоклав, где осуществляются реакции 6.2 и 6.3 (реакции дегидратации). Для модифицирования роста кристаллов вводят КМЦ (карбоксил-метил целлюлоза).
КМЦ увеличивает индукционный период образования зародышей кристаллов,
ПГ (полугидрат) способствует улучшению формы.
Лекция 10
Колонна синтеза карбонита.
1) 2NH3+СO2 <=>NH2COONH4+Q (1)
2) NH2COONH4<=>CO (NH2)2+H2O-Q (2)
∑: 2NH3+CO2<=>CO (NH2) +H2O
t=200˚C, р=20 МПа
реакции (1) и (2) идут одновременно в колонне синтеза => образуется плав
1. 34-35% CO(NH2)2
2. 18-19% NH2COONH4
3. 34-35%NH3
4. 10-11%H2O
Задача:
Составить материальный баланс синтеза карбамида при абсолютном давлении в колонне 20 МПа и t=200˚C. Источник СО2 – экспандерный газ, в котором 96%-СО2 и 4% инертные газы(N). Избыток NH3 125% (для увеличения степени превращения целевого продукта). Степень превращения NH2COONH4 70%, плав подвергают разложению и отгоняют NH3 и H2O, подвергают дистилляции и упариванию. Потери мочевины достигают 6.5%. Расчёт делаем на 1000 кг сухого продукта (мочевины).
2NH3+CO2↔CO (NH2)2+H2O
1) вычисление необходимого количества NH3 и CO2, исходя их ХР
NH3: 2*17 * 1000=566.7 кг
60
CO2: 44*1000=733 кг
60
2) количество мочевины с учётом потери 6.5 %
1000 кг – 100-6.5=93.5%
х – 100% => х=1000*100
93.5
3) определяем сколько нужно NH3 и CO2 для 1070 кг мочевины
NH3: 566.7*1.07=606.4 кг
CO2: 733*1.07=784.7 кг
4) с учётом степени превращения карбомата в мочевину (избыток NH3 =125%), Хпар=70%
NH3: 606.4*2.25 * 100=1949 кг
70
CO2: 784.7*100=1121 кг
70
5) количество инертных газов, поступающих с CO2 в колонну синтеза
1121*4=46.7 кг
96
6) по (1) находим количество образовавшегося карбомата аммония
2NH3 +CO2 ↔NH2COONH4
NH2COONH4: 1121*78=1987.2 кг
44
7) по (2) находим
NH2COONH4 →CO (NH2)2 +H2O
CO (NH2)2: 1987.2 *60*70% =1070 кг
78 100%
8) по (2) определяем воду
H2O: 1987.2 *18*0.7=321 кг
78
9) количество карбомата:
1987.2*(100-70)=596.2 кг
100
10) на образование 1987.2 кг карбомата расходуется NH3:
1987.2*(2*17)=866.2 кг
78
11) количество оставшегося NH3 (п.4):
(п.4) 1949 кг - (п.10)866.2=1082.8 кг
12) выделившаяся Н2О реагирует с остаточным NH3
H2O+NH3 →NH4OH (3)
NH4OH: 321*35=624.2 кг
18
NH3: 321*17=303.2 кг
18
13) определяем количество NH3, остающегося в газовой фазе
(п.11) 1082.8-303.2=779.6 кг
Материальный баланс получения плава мочевины
на 1 тонну готового продукта.
Приход | Расход | % | ||
NH3 | 1949 кг | мочевина CO(NH2)2 | 1070 кг | 34.4 |
CO2 | 1121 кг | карбамат аммония NH2COONH4 | 596 кг | 10.3 |
инертные газы | 46.7 кг | вода Н2О | 321 кг | 10.3 |
|
| избыточный аммиак в виде: NH3 NH4OH в газообразном виде | 1082.2 кг 303.2 кг 779.2 кг | 34.74 |
инертные газы | 467 кг | 1.5 | ||
Всего: | 3116.7 кг | 3116.7 кг | 100% |
Лекция 11
Переработка сточных вод и повторное их использование.
На 1т.100% P2О5 расходуется 200-210 м3 технологической воды.
Рис. 11.1. Схема водопользования на промышленных предприятиях.
вода с товарным продуктом
![]() |
|
|
|
![]() | ![]() | ||||
![]() | |||||
|
|

очищенная вода
1. хим. водоочистка;
2. технологические установки;
3. основные очистные сооружения;
4. дополнительные очистные сооружения;
5. локальные очистные сооружения;
6. узел оборотного водоохлаждения.
Использование воды в технологическом процессе:
1) для охлаждения (основное свойство воды - способность аккумулировать тепло за счет высокой теплоемкости Ср=4,18 кДж/кг*К)
2) как транспортирующее средство (для переноса ФГ):
· текучесть- h(H2О)= 10-3 Па*с;
· нереакционная способность- частицы воды достаточно электронейтральны (mд –дипольный момент);
3) в качестве растворителя
· диэлектрическая проницаемость воды (e=81) выше, чем у др. растворителей (фенол,CCl4)
3) как химический реагент ( с повышением t° реакционная способность воды повышается).
· NH4=H2O+NH3
Блок 1: в производственных условиях носит название цех «химводоочистки»;
· осуществляется подготовка воды;
Блок 2 : потребители воды:
1) теплообменник;
2) трубопроводы с побудителями потока;
3) емкости с перемешивающими устройствами;
4) химические реакторы (каталитические, некаталитические);
5) абсорбционная аппаратура (абсорбционно-десорбционный узел).
Блок 3: основные очистные сооружения стадии механической очистки
· отстойники (грубая очистка);
· скорые фильтры (тонкая очистка)
Блок 4 : дополнительные очистные сооружения :
1) выделение из воды ультра-, микрочастиц, спор (ультрафильтрация);
2) удаление растворенных примесей реагентным методом:
· нейтрализация (использование кислот, щелочей);
· коагуляция (флокуляция) – укрупнение частиц;
· химический реагент с переводом загрязняющего вещества из растворенного в осадок.
Согласно условиям водоотведения (или требованиям к использоанию доочищенных СВ) после блока 4 большая часть потока - a- возвращается в процесс (блок 2), а меньшая часть – водоемы (1-a).
(1-a) - регламентируемая природоохранными органами с целью поддержания постоянного водного баланса, рассматриваемого территориально-производственного комплекса. Это значит, что объемный расход (м3/ч) на входе предприятия равен объемному расходу из предприятия (n вход..= n вых., м3/ч). n вых должно удовлетворять условиям водоотведения: табл. 1 (стр.122):
1) вводоемы рыбохозяйственного назначения - ПДК {нефтепродукты}=0,05 мг/л;
2) в водоемы хозяйственно-питьевого и культурно-бытового пользования - ПДК{нефтепродукты} = 0,3 мг/л.
Требования к дочищенным СВ (см. п.1-п.5), a max =0,8, a ср. =(0,3-0,4)
Блок 5 : локальные ОС
Существуют для оперативной очистки раздельных стоков:
1) локальный отстойники;
2) нефтеловушки (плотность воды=100м3/ч, а для нефтепродуктов ~800-900м3/ч;
3) нейтрализаторы (использования известкового молока (щелочь) для уменьшения рН.
Блок 6. Замкнутая система водоснабжения (здесь сосредоточено более 10% циркулирующей воды). Вода не контактирует в реагентами.
Источники образования СВ в производстве ЭФК /рис 4.1/.
Классификация СВ.
Основные требования к созданию замкнутых водооборотных циклов заключается в разделении, сборе и переработке хозяйственно-бытовых сточных вод (ХБСВ), производственных СВ (ПСВ) и поверхностных сточных вод.
Хозяйственно-бытовые СВ:
· источники образования: административные здания (столовые);
· характеризуются повышенным содержанием минеральных примесей (в основном солей Na) и биогенных компонентов (нитриты, нитраты, фосфаты, аммонийный азот).
Табл. 11.1. Примерный состав ХБСБ:
Вещества | Содержание, масс.% |
· мыла (стеарат Na); · жирные кислоты | 18,7 4,8 |
· жиры (по кислотам): - олеиновая; - пальмитиновая; - стеариновая | 8,7 5,5 1,1 |
· карбамиды (мочевина) | 37,9 |
· креатин | 1,4 |
· кислоты: - гиппуровая | 1,4 |
· аминокислоты | 0,2 |
· лимонная к-та; · связанные жирные кис-ты; · фенол; · крахмал | 0,6 9,4 0,2 9,2 |
Табл. 11.2. Примерный состав ПСВ (направленные после производства ЭФК на стадию нейтрализации):
Вещества | Содержание |
· взвешенные вещества (г/л)* | 5-6 |
· сухой остаток (г/л) | 12-16 |
· прокаленный остаток (г/л) | 7-10 |
· содержание ионов: - SO4 2- (г/л); - F- (г/л); - фосфаты (г/л); - Si (SiO2), (г/л) | 3-4 0,7-1,0 5-7,0 2-4 |
· Ph | 1,4-1,5 |
*
1) после промывки полотен вакуум-фильтра (позиция 7) в греющих камерах выпарных аппаратов (после поз.8);
2) служит для оценки минерализации СВ;
3) зольность (остатки металлов, оксиды);
4) ионы SO4 2- (образованные по реакции 1.1) определяют кислотность (Ph)
Лекция 12
Дата добавления: 2021-01-20; просмотров: 62; Мы поможем в написании вашей работы! |
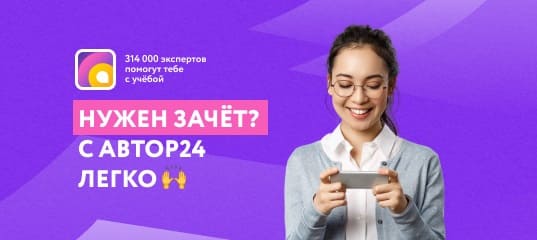
Мы поможем в написании ваших работ!