Сжигание твердого топлива в расплаве
СНИЖЕНИЕ ВРЕДНЫХ ВЫБРОСОВ В АТМОСФЕРУ ПРИ ИСПОЛЬЗОВАНИИ НОВЫХ ТЕХНОЛОГИЙ СЖИГАНИЯ
Сжигание твердого топлива в котлах с кипящим и циркулирующим кипящим слоем
Технология кипящего слоя в энергетических установках (установки тепловой мощностью 50 МВт и более) начала широко использоваться с середины 70-х годов XX в. под влиянием ужесточающихся норм на вредные выбросы. На рис. 3.63 приведены данные [3.54] о росте установленной тепловой мощности электростанций с котлами, работающими по технологии кипящего слоя. На начало 1998 г. эта технология использовалась на 606 электростанциях установленной тепловой мощностью 58 025 МВт. С середины 90-х годов рост установленной мощности с котлами кипящего слоя (КС) замедлился, а мощности установок сжигания в кипящем слое под давлением (КСД) увеличился (рис. 3.63). Из общего количества установок 51% приходится на технологию циркулирующего кипящего слоя (ЦКС) F6% по мощности), 41 % — на технологию КС B3 % по мощности), 6 % — на установки промежуточного типа и 2 % E % по мощности) — на установки КСД.
Наибольшее количество котлов размещено в Европе — 275 тепловой мощностью 24 700 МВт (из них 104 в Финляндии, 81 в Швеции и 46 в Германии), в США — 155 A8 296 МВт) и в Азии — 126 A4 231 МВт) [из них в Японии — 28C260 МВт) и в Китае — 25 B800 МВт)]. На рис. 3.64 показан рост единичной мощности котлов с кипящим слоем. Наиболее крупные котлы с кипящим слоем (в том числе под давлением) построены и сооружаются в Японии и имеют тепловую мощность 800—840 МВт. Один из крупнейших котлов с ЦКС пущен в 1996 г. во Франции на параметры пара: расход 720 т/ч, давление 16,5 МПа, температура пара 565 °С/565 °С для энергоблока 250 МВтэл, в котором успешно сжигается уголь с теплотворной способностью 3525 ккал/кг, влажностью 11 —14%, зольностью 26—32 % и содержанием серы 3,68 %.
|
|
В 2002 г. пущен самый мощный котел с ЦКС для энергоблока мощностью 300 МВт в г. Джексонвилле (США). Он предназначен для сжигания каменного угля и нефтяного кокса с содержанием серы до 8 %.
Основной характерной особенностью технологии сжигания твердых топлив в кипящем слое является наличие значительного количества инертного материала в топке. Ниже кратко описаны процессы гидродинамики и сжигания топлив в кипящем слое, а также условия образования и подавления вредных выбросов.
При скорости газа, превышающей скорость минимального псевдоожижения (сила лобового сопротивления соответствует силе тяжести), объем слоя увеличивается, образуются пузырьки газа. Этот режим соответствует пузырьковому кипящему слою. При дальнейшем росте скорости газа пузыри сливаются, частицы в надслоевом пространстве объединяются в группы с высокой концентрацией. Этот случай соответствует турбулентному кипящему слою. Если частицы улавливаются и возвращаются в слой, циркулируя по замкнутому контуру, то такой режим работы называется циркулирующим кипящим слоем. В этом случае не имеется четких границ между турбулентным слоем в нижней части топки и расположенной выше разбавленной фазой. Расход циркулирующего материала в сотни раз превышает расход газа в системе и в ряде случаев зависит от массы слоя при неизменной скорости газа и размерах частиц.
|
|
Особенностью режима ЦКС помимо собственно организации контура циркуляции считается тот факт, что скорость газа превышает скорость витания почти всех частиц слоя, т.е. практически все частицы могут быть вынесены из слоя. Однако в переходной зоне турбулентного слоя, а также в надслоевом пространстве вблизи стен существуют значительные возвратные токи, образующиеся за счет неравномерности скорости, соударения частиц, обмена энергией и образования агломератов (пакетов) частиц. Именно этот признак является решающим для отличия режимов ЦКС от других режимов псевдоожижения или движения частиц в потоке газа (например, пневмотранспорта).
Рассмотрим основные отличия процессов горения в кипящем слое и других наиболее распространенных технологий сжигания. В пылеугольной топке горение происходит в результате окислительных реакций мелких G0 % менее 200 мкм) частиц топлива, смешанных с воздухом и топочными газами. Объем факела является зоной наиболее высоких температур, которые достигают 2000 °С. При этом время пребывания частиц в топке полностью определяется временем движения газов.
|
|
В механических топках используются крупные куски угля размерами до 35 мм. Некоторые виды топлива сжигаются на движущихся решетках различных конструкций при подаче воздуха, проходящего через фиксированный слой топлива. Температура слоя достигает 1600 °С, а время пребывания в зоне горения определяется скоростью перемещения решетки.
Размеры частиц топлива, предназначенного для сжигания в кипящем слое, средние между размерами частиц топлива для пылевидного сжигания и сжигания в механических топках. Максимальный размер их зависит от реакционной способности топлива и составляет от 6 до 25 мм. Для котлов с пузырьковым кипящим слоем характерна плотность слоя около 750 кг/м3, а с циркулирующим — 550 кг/м3 при температуре слоя 820—900 °С. Поступающее топливо быстро перемешивается с материалом слоя, нагревается до температуры воспламенения и загорается. Благодаря длительному времени пребывания топлива и высокой интенсивности процессов тепломассообмена эффективность сжигания в топке с кипящим слоем довольно велика, несмотря на значительно более низкую температуру процесса, чем при пылевидном сжигании.
|
|
В пузырьковом кипящем слое наблюдается незначительный вынос частиц из топки. Время пребывания крупных кусков топлива велико, а мелких частиц примерно соответствует расчетному по скорости газа. Это часто (по крайней мере, для низкореакционных топлив) приводит к повышенному содержанию углерода в слое, в уносимых несгоревших частицах и соответственно к увеличению механического недожога. Для его уменьшения вынесенные из топки частицы улавливают и возвращают в топку. Вынос частиц из топочных камер котлов с ЦКС в несколько десятков раз больше, чем из топок с КС. Эти частицы улавливаются в сепараторах различных типов и возвращаются в топку. Время пребывания частиц в топке связано с эффективностью их улавливания в сепараторах и кратностью циркуляции золы, при этом оно существенно больше времени пребывания газа.
Концентрация топлива в слое котла с ЦКС обычно очень мала. Для высокореакционных топлив, таких как дрова, содержание углерода крайне трудно измерить. При сжигании бурых и ряда каменных углей концентрация углерода в слое меньше 1 %, для менее реакционных каменных углей и антрацита — 2 %. В отдельных случаях для крайне низкореакционных углей и отходов углеобогащения содержание углерода в слое может достигать 3 %, при этом степень конверсии его превышает 96 %.
В качестве наполнителя слоя применяют песок, известняк, который используется также для связыва- ния оксидов серы, или собственную золу слоя. По- этому удаляемая часть слоя (дренаж слоя или шлак) состоит из золы топлива, сульфата кальция и извест- няка или песка (возможно использование других на- полнителей). Как правило, доля дренажа слоя мень- ше, чем доля уносимого материала.
Сжигание в кипящем слое считается процессом, обеспечивающим низкий уровень выбросов. Однако при бесконтрольной эксплуатации таких котлов, т.е. при отсутствии специальных мер, ограничивающих выбросы, их уровень не всегда оказывается намного меньше, чем при использовании других методов сжигания. Одним из основных преимуществ сжигания в кипящем слое является возможность эффективного улавливания диоксида серы SO2 путем подачи в слой известняка. Условия в топке с кипящим слоем (температура и время пребывания частиц известняка в реакционной зоне) оказываются весьма подходящими для организации процесса абсорбции диоксида серы известняком и собственными щелочными компонентами золы. Поэтому при сжигании в кипящем слое сера улавливается гораздо эффективнее, чем при впрыскивании извести в топку с пылеугольным сжиганием.
Наиболее важными факторами, определяющими эффективность улавливания серы, являются:
• температура в слое и надслоевом пространстве. Оптимальная температура слоя составляет 840— 880 °С, причем связывание серы уменьшается как при повышении, так и при понижении температуры;
• качество извести и распределение частиц по размерам;
• содержание серы в топливе. Обычно чем больше содержится серы, тем эффективнее она связывается;
• условия подачи воздуха в топку. Чем больше доля первичного воздуха, тем выше связывание серы. Указанное обстоятельство свидетельствует о тесной взаимосвязи выбросов SO2 и NOX из котлов с топками с кипящим слоем;
• рециркуляция золы и известняка. Увеличение степени рециркуляции, по крайней мере, до 30 % повышает эффективность связывания серы.
В целом можно утверждать, что при использовании обычного промышленного известняка и умеренном отношении Ca/S A,8—2,2) обеспечивается эффективность связывания SO2 на уровне 90 %. При прочих равных условиях сжигание в циркулирующем кипящем слое позволяет добиться большего уменьшения выбросов, чем сжигание в стационарном кипящем слое.
В качестве иллюстрации к изложенному на рис. 3.65 приведены некоторые результаты отечественных исследований, выполненных на небольших пилотных установках. Следует отметить, что недостаточное время пребывания частиц в них не позволяет обеспечить высокий уровень связывания серы. Обращает на себя внимание увеличение выбросов оксидов азота при излишней подаче известняка, служащего катализатором процесса образования «топливного» NOV.
При сжигании в кипящем слое не происходит образования NOX из азота воздуха («термические» NOX практически отсутствуют). Кроме того, уровень N0^ существенно снижается за счет ступенчатой подачи воздуха. Наиболее важными факторами, определяющими концентрацию N0^ в котлах с кипящим слоем, являются:
• температура слоя, ее увеличение приводит к росту концентрации NO^ ;
• избыток воздуха на выходе из топки, его рост увеличивает концентрацию NO/,
• доля первичного воздуха, уменьшение ее доли (по крайней мере, до 40 %) способствует снижению выбросов N0^.
На рис. 3.66 приведены данные проведенных с участием ВТИ исследований, подтверждающие указанные положения. Необходимо отметить, что для топлив с умеренным выходом летучих (на уровне 20 %) выбросы NOy минимальны при прочих равных условиях. Генерация N0^ при сжигании топлив с крайне низким и очень большим выходом летучих заметно возрастает. При сжигании в пузырьковом кипящем слое концентрация оксидов азота обычно не превышает 150 мг/МДж. Более эффективное подавление NOX наблюдается в котлах с топками с циркулирующим кипящим слоем (до 70 мг/МДж).
В котлах с топками с кипящим слоем удается поддерживать выбросы оксида углерода менее 50 мг/МДж. Уровень выбросов других несгоревших газов, как правило, значительно ниже — менее 10 мг/МДж в пересчете на метан. Увеличение концентрации СО в основном связано с недостаточным временем пребывания частиц в надслоевом пространстве или низкими температурами газов в топке (что, например, было характерно для первых котлов Циркофлюид).
Рост концентрации СО может быть связан с отложениями несгоревших частиц кокса. Его можно устранить с помощью обдувки зон отложений.
В последнее время уделяется повышенное внимание исследованиям условий образования закиси азота N2O, которая может быть одной из причин возникновения глобального парникового эффекта и разрушения озонового слоя. Низкотемпературное сжигание приводит к значительной генерации N2O, которая колеблется от 20 до 100 мг/МДж [3.56] и возрастает при снижении температуры в топке. Сжигание каменных углей характеризуется наибольшими выбросами N2O. При использовании метода селективного некаталитического восстановления концентрация N2O увеличивается, особенно при замене аммиака мочевиной. На выбросы N9O могут влиять и другие условия горения, однако точные данные по этому вопросу отсутствуют.
Таким образом, основными преимуществами технологии ЦКС являются:
• возможность эффективного сжигания низкокалорийных, высокозольных топлив, а также топлив с малым выходом летучих, которая определяется стабильной температурой в топке, низким содержанием углерода в слое, длительным временем пребывания коксозольного остатка в реакционной зоне. В результате достигается значительная экономия вспомогательного топлива, так как исключается подсветка мазутом или газом;
• возможность эффективного (более 90 %) связывания оксидов серы путем относительно дешевого способа подачи известняка в топку при оптимальной температуре слоя около 870 °С и длительном времени пребывания частиц известняка в реакционной зоне;
• низкие выбросы оксидов азота (менее 200— 300 мг/нм3) без использования специальных средств азотоочистки, которые обусловлены низкой и стабильной температурой слоя и надслоевого пространства при организации ступенчатого подвода воздуха;
• возможность сжигания топлив различного качества в одном и том же котле, упрощенная схема подготовки топлива (дробление), хорошие динамические характеристики, быстрый пуск из «горячего» состояния;
• компактность котельной установки, связанная с отсутствием средств серо- и азотоочистки, что позволяет разместить котел с ЦКС в существующих котельных ячейках.
К недостаткам технологии ЦКС относятся: ус- ложнение конструкции котла (воздухораспредели- тельная решетка, специальные меры для исключения эрозии поверхностей нагрева и др.); наличие большой массы футерованных элементов и длительный пуск из «холодного» состояния с повышенным расходом пус- кового топлива для ряда модификаций; усложнение вспомогательных систем котла (дренаж слоя, возврат золы, подвод известняка и др.); повышенные расходы на собственные нужды за счет использования высоко- напорных вентиляторов (за исключением случаев с крайне высоким содержанием серы).
Производителями котлов с кипящим слоем являются 37 компаний (из них 23 производят котлы с ЦКС). Наибольшее количество котлов выпущено компаниями Foster-Wheller (Alstrem) — 96 котлов общей тепловой мощностью 14 203 МВт, ABB/Combustion Engineering (технология Лурги) — 21 котел D405 МВт), Kwarnier/Tampella — 22 котла C475 МВт), LLB (Лурги) — 12 котлов A750 МВт), EVT (технологии Альстрем, Лурги) — 11 котлов A813 МВт). В последнее время международная компания Alstom объединила производителей котлов с ЦКС в Германии, Франции и ряде других стран (ABB, EVT, Steinmuller, Combustion, Engineering).
В настоящее время за рубежом используются различные модификации технологии ЦКС (рис. 3.67). В [3.55] подробно рассмотрены схемы пяти наиболее известных модификаций ЦКС, различающихся долей тепла, полезно используемого в топке, местом установки и конструкцией золоулавливающих устройств.
Котлы ЦКС с «горячими» циклонами и зольными теплообменниками обеспечивают самый низкий уровень вредных выбросов, минимальное содержание углерода в слое, лучшие условия регулирования температуры пара (нагрузки), пригодность золошлаковых отходов для строительных целей. Котлы с ЦКС с охлаждаемыми или нефутерованными сепараторами позволяют проводить быстрый пуск из «холодного» состояния, обладают хорошими динамическими характеристиками, высокой эксплуатационной готовностью и низкими эксплуатационными затратами. Капитальные затраты современных модификаций технологии ЦКС ниже, чем традиционных технологий с использованием «горячих» циклонов.
Следует отметить, что в настоящее время самые крупные котлы с ЦКС выполнены с использованием «горячих» циклонов (технологии Альстрем и Лурги), несмотря на определенные недостатки этих технологий (высокие эксплуатационные затраты, сложность конструкции, медленный пуск из «холодного» состояния). В развитых странах (США, Германии, Японии) строятся и успешно эксплуатируются котлы всех модификаций, причем преимущества той или иной технологии с учетом всех аспектов строительства, эксплуатации и местных условий не являются очевидными. В ближайшей перспективе при сооружении новых ТЭС с котлами с ЦКС какая-либо технология не получит преимущественного развития.
Хорошо освоены и отработаны конструктивные решения по котлам с ЦКС паропроизводительностью 200—400 т/ч для сжигания широкой гаммы топлив — от антрацитов и нефтяного кокса до высокозольных шламов, торфа, отходов деревообработки. Разрабатываются конструкции котлов для энергоблоков 300 МВтэл, в том числе на высокие и сверхкритические параметры пара.
ВТИ выполнил анализ ряда зарубежных и отечественных технико-экономических исследований, связанных со сравнением пылеугольных котлов и котлов ЦКС. На рис. 3.68 приведены данные шести исследований по себестоимости электроэнергии и ее составляющим (затраты: капитальные, на топливо, на эксплуатацию и ремонт) применительно к энергоблокам мощностью 150—300 МВт с котлами с ЦКС.
За 100% приняты значения себестоимости при использовании пылеугольных котлов, оснащенных азото- и сероочисткой. В случае сжигания низкосортных топлив, требующих «мокрой» системы сероочистки, себестоимость электроэнергии, выработанной на энергоблоках с котлами с ЦКС, в среднем на 7,9 % ниже, чем на традиционных котлах. При этом затраты на эксплуатацию и ремонт примерно одинаковы. Затраты на топливо для котлов с ЦКС несколько ниже (более высокий КПД котла с ЦКС для низкореакционных топлив и отсутствие подсветки мазутом), капитальные затраты для котлов с ЦКС ниже в среднем на 7,4 %.
Таким образом, эффективность внедрения технологии ЦКС в основном определяется качеством топлива и мощностью установки при заданных ограничениях на выбросы вредных веществ. При жестких нормах на выбросы оксидов азота и серы приходится применять сложные, дорогостоящие и требующие дополнительных площадей для их установки системы азото- и сероочистки. При этом повышенное содержание серы в топливе (даже при умеренных нормах на выбросы SO7) приводит к необходимости установки «мокрой» сероочистки.
Ряд топлив нуждается в дополнительной подсветке мазутом: топлива с низким выходом летучих (АШ, тощий кузнецкий угли), высокозольные и высоковлажные угли. Использование вспомогательного топлива заметно увеличивает себестоимость электроэнергии. Некоторые твердые топлива, например, отходы углеобогащения с низкой теплотворной способностью, биомасса (древесные и сельскохозяйственные отходы), не могут сжигаться эффективно в камерных топках. Низкая цена этих топлив делает привлекательным их использование, по крайней мере, в установках промышленной энергетики. На электростанциях, использующих топлива различного качества (например, на Дальнем Востоке), имеются трудности в работе котлов (дополнительная подсветка мазутом, потери эффективности, шлакование) и вспомогательного оборудования. Применение технологии ЦКС обеспечивает минимальные потери эффективности и мощности при сжигании топлив с существенно отличающимися от проектных свойств.
Влияние качества топлива и режимных факторов на выбросы NOV и SO2 подробно рассмотрены в [3.55, 3.62, 3.63]. В табл. 3.24 приведены характеристики газовых выбросов котлов с ЦКС и пылеугольных при сжигании каменных и бурых углей по данным [3.64].
Таким образом, для каменных и высокосернистых бурых углей одинаковый уровень вредных выбросов для котлов с факельным сжиганием и с ЦКС может быть получен только при использовании мокрой сероочистки и каталитической очистки от NOX.
Некоторые аспекты влияния характеристик топлива на основные размеры и эксплуатационные показатели котлов с ЦКС были рассмотрены в [3.63]. Влияние их на конструкцию котла и его систем, термический КПД и экологические показатели приведено в табл. 3.25. Указанные в табл. 3.25 характеристики относятся в той или иной мере к любым модификациям технологии сжигания в кипящем слое. Влияние свойств угля и золы во многом аналогично такому же для традиционных пылеугольных котлов.
Интерес представляют данные по сжиганию различных видов угля по технологии Лурги. В табл. 3.26 приведены свойства топлив, которые сжигались на пилотной установке мощностью 1,5 МВт фирмы Лурги.
В табл. 3.27 приведены некоторые результаты опытного сжигания этих углей.
Было установлено, что даже у сильно забалластированных топлив достигается выгорание более 99 % углерода, связывание более 90 % диоксида серы при сравнительно низких отношениях Ca/S. При Ca/S = 1,3—2,0 и температуре горения 830—885 °С выбросы диоксида серы составляли около 200 мг/м3, оксидов азота — около 180 мг/м3. Характеристики топлива оказывают влияние на выбросы SO2 и NOX. При прочих равных условиях концентрация SO2 в дымовых газах напрямую связана с содержанием серы в топливе по зависимости
где ηso2 — эффективность связывания серы; Sr — содержание серы на рабочую массу, %; V г — объем газов на 1 кг топлива, м3/кг.
Для тощих углей и антрацитов значение Vг составляет 6—7 и уменьшается с ростом зольности. Для бурых углей это значение составляет 4—5. Эффективность связывания серы ηso2 обычно несколько возрастает с увеличением содержания серы в топливе и снижается в случае сжигания низкореакционных топлив по причине повышенной температуры в топке. При повышенном содержании щелочных составляющих собственной золы топлива может быть существенно уменьшена добавка известняка при поддержании мольного отношения Ca/S на уровне 2. При прочих равных условиях увеличение влажности топлива приводит к снижению выбросов SO2. Таким образом, при одинаковом содержании серы на рабочую массу концентрация SO2 за котлом с ЦКС будет больше для бурых углей с умеренной влажностью и высокой зольностью, а также для высокозольных низкореакционных углей.
На рис. 3.69 приведены опытные данные [3.65], основанные на сжигании 10 видов угля, включая кокс с выходом летучих 1,16%, на крупной пилотной установке. Обнаружено, что наименьшая концентрация NOX относится к углям с выходом летучих 20—25 %. Увеличение выхода летучих свыше 25 % приводит к росту выбросов NOх. для низкореакционных топлив и кокса снижение NOX в надслоевом пространстве происходит существенно слабее и концентрация N0^. в уходящих газах возрастает. Влияние температуры слоя на выбросы N0^ по данным [3.65] показано на рис. 3.69.
Данные по промышленным котлам и пилотной установке неплохо согласуются. При этом для крупных котлов концентрации NOX выше при той же температуре слоя.
В [3.65] указывается, что это обстоятельство связано с неравномерным полем температур слоя на котлах. При этом максимальные температуры выше измеряемых вблизи стен. По мнению авторов, важными являются также условия подвода вторичного воздуха (высота установки сопл от решетки, выбор их размеров и скоростей воздуха). До настоящего времени эти вопросы не получили должного освещения. Необходимо проведение специальных исследований по оптимизации условий подвода вторичного воздуха на аэродинамических моделях и огневых установках. Учитывая изложенное, при проектировании котлов следует ориентироваться на наиболее консервативные данные по эмиссии оксидов азота.
Отечественные данные по выбросам NOX при сжигании различных топлив на огневых установках (см. рис. 3.66) подтверждают данные [3.65] по влиянию выхода летучих на выбросы NO^. Максимальная концентрация NOV относится к АШ, а минимальная — к кузнецкому углю. При температуре слоя менее 900 °С, избытке воздуха менее 1,25 и доле первичного воздуха не выше 0,6 выбросы N0^. для АШ не превышают 220 мг/нм3, для подмосковного угля они составляют примерно 170 мг/нм3 и для кузнецкого угля — около 130 мг/нм3.
Дальнейшее снижение выбросов NOX связано с использованием добавки аммиака по методу селективного некаталитического восстановления. Сообщалось о снижении выбросов еще на 70 % на крупной установке с ЦКС при отношении NH3/NO равном примерно 2,5. В этом случае конечные выбросы N0^ были незначительны — менее 20 мг/МДж [3.54].
На рис. 3.70 приведены некоторые зарубежные данные [3.65—3.67] по влиянию температуры слоя, доли первичного воздуха и содержания кислорода на выходе из топки на концентрацию NОх. Увеличение температуры слоя приводит к росту эмиссии оксидов азота (рис. 3.70, я), особенно заметно проявляющемуся при температуре более 850 °С. Увеличение доли первичного воздуха также приводит к росту концентрации NОх, причем наибольший рост концентрации NОх относится к режимам с долей первичного воздуха более 70 % (рис. 3.70, б). Увеличение избытка воздуха (концентрации кислорода) на выходе из топки приводит к существенному росту концентрации NОх; при снижении нагрузки котла возможно обеспечить те же значения NОх при большем содержании кислорода.
Как указывалось ранее, мольное отношение Ca/S влияет на выбросы NОх. При сжигании АШ увеличение мольного соотношения Ca/S от 1,5 до 4 приводит к росту выбросов NОх от 150 до 250 мг/нм3. На рис. 3.71 приведены характерные показатели вредных выбросов в зависимости от мольного отношения Ca/S и нагрузки котлов Пирофлоу по данным [3.68]. Увеличение отношения Ca/S приводит к снижению концентрации SO2 и некоторому росту концентрации NОх. Эта взаимосвязь отмечена в работе финских исследователей [3.62], что указывает на необходимость разработки оптимальной стратегии регулирования процесса сжигания. В исследованиях [3.69], выполненных на установке тепловой мощностью 36 МВт, отношение Ca/S поддерживалось около 1,5, а содержание кислорода — на уровне 4 %, причем температура слоя менялась от 850 до 920 °С. При этом содержание SO2 увеличивалось с 480 до 702 мг/МДж, а содержание NОх — на 30 %. Повышение коэффициента избытка первичного воздуха от 0,8 до 1,2 снижало концентрацию SO2 на 35 мг/МДж, но повышало концентрацию NОх от 105 до 180 мг/МДж.
В [3.70] по результатам опытного сжигания на установке мощностью 2,2 МВт трех различных углей указывается, что при увеличении степени возврата частиц из горячего циклона выбросы SO2 уменьшаются. Отмечено, что при росте температуры в надслоевом пространстве более чем на 90 °С возрастает содержание SO2 при прочих равных условиях. Для известняков средней реакционной способности укрупнение частиц приводит к увеличению эффективности де- сульфуризации по сравнению с частицами мелких размеров. Последнее обстоятельство, по мнению авторов, связано с небольшой высотой установки и, возможно, недостаточной эффективностью улавливания летучих частиц в циклонах. В ряде других исследований этот эффект не обнаружен. Выбор оптимальных размеров сорбента является крайне сложной задачей, связанной с аэродинамикой топки и динамикой разложения частиц сорбента.
Сложность и взаимосвязь процессов улавливания серы и гидродинамики топки вызывают определенные трудности даже у известных фирм-поставщиков котлов с ЦКС. Например, на крупнейшем котле по технологии Пирофлоу на ТЭС Пойнт Акони (Канада) [3.71] даже при мольном отношении Ca/S = 3,2 не удавалось связать серу более чем на 90 %, что определялось высокой температурой в топке и неоптимальным фракционным составом извести.
Влияние нагрузки на экологические показатели котлов с ЦКС в Японии по данным [3.68, 3.72, 3.73] показано на рис. 3.72. Рассмотрена работа котла паро- производительностью 250 т/ч по схеме Пирофлоу при сжигании полуантрацита зольностью 10,4% при выходе летучих 15,4% и содержании серы 0,4% [3.68]. Приведены данные котла, работающего по технологии Лурги, производительностью 300 т/ч при сжигании каменного угля с содержанием серы 0,5 и 2,7 % [3.72] и результаты работы небольшого котла G0 т/ч) по схеме Мультисолид при сжигании антрацита зольностью 30 %, выходом летучих 8,4 % и содержанием серы 1,5% [3.73]. Результаты различаются по характеру влияния нагрузки на выбросы SO2, что может быть связано с особенностями поддержания режимов работы различных котлов на частичных нагрузках. Имеется тенденция к снижению концентрации NOx при работе кола на частичных нагрузках.
Как указывалось ранее, удается поддерживать выбросы монооксида углерода на уровне ниже 50 мг/МДж. Технология Циркофлюид при малой высоте надслоевого пространства и неравномерном по высоте топки полем температур в определенных случаях может не обеспечить требуемые экологические показатели. В [3.74] приведены данные по эксплуатации котла паропроизводительностью 150 т/ч на ТЭС Ремербрюкке (Германия) при сжигании углей трех месторождений. При сжигании углей марок Нейкирхен и Рейсбах-Фишбах обеспечивались допустимые значения выбросов СО, однако при сжигании угля марки Варндт выбросы СО достигали 200 мг/нм3. Указанные различия можно было бы отнести на разницу в гранулометрическом составе: уголь марки Рейсбах-Фишбах заметно тоньше, чем уголь марки Варндт (массовое содержание частиц крупностью менее 1 мм составляет 41 и 15 % соответственно). Однако специальные испытания одного и того же угля различной крупности показали, что не это является причиной изменения концентрации СО. Авторы исследования пришли к выводу, что указанное обстоятельство связано с различными скоростями реакции горения угля, причем обычная оценка реакционной способности по отношению содержания летучих к связанному углероду является недостаточно надежной.
После реконструкции котла, связанной со снижением скорости газов в надслоевом пространстве и увеличением его высоты на 2,5 м, что привело к росту времени пребывания в нем до 3,8 с, выбросы СО снизились до допустимых пределов.
Анализ опубликованных данных показывает, что до реконструкции котел работал с нагрузкой, не превышающей 125 т/ч, т.е. до 80% номинальной. Официальной причины в [3.74] не указано, однако, по- видимому, это связано с высотой надслоевого пространства. На рис. 3.73 приведены данные [3.74], из которых следует, что увеличение нагрузки приводит к росту температуры перед теплообменными поверхностями. При этом происходит снижение выбросов СО с 400 мг/нм3 при температуре около 900 °С до 200 мг/нм3 при температуре более 1000 °С. Следует отметить, что при столь высоких температурах начинают увеличиваться выбросы оксидов азота и серы даже при условии поддержания температуры слоя около 850 °С.
Необходимо отметить, что особенности схемы Циркофлюид с небольшой кратностью циркуляции, «холодным» возвратом золы и возможностью существенного отличия температур по высоте надслоевого пространства требуют специального анализа для разработки оптимальной стратегии управления экологическими показателями.
При сжигании угля в кипящем слое образуется значительно большее количество N2O, чем при пылевидном сжигании. Как правило, при сжигании битуминозного угля в ЦКС уровень выбросов колеблется от 20 до 100 мг/МДж, тогда как при пылевидном сжигании он менее 5 мг/МДж.
Механизм образования N2O пока еще недостаточно изучен. В [3.75] указывается, что образование N2O протекает по реакции между радикалами HCN + NО – Н2О + СО, а разрушение — с помощью радикалов ОН и Н. По-видимому, N2O образуется на поздних стадиях сжигания, когда из угля выделяется HCN и затем окисляется.
В Швеции [3.76] проведено комплексное изучение эмиссии NOх, SO2 в N2O с целью оптимизации уровня вредных выбросов. Испытания проводились на трех котлах с ЦКС и одном котле пузырькового слоя. Установлено, что главными факторами, оказывающими влияние на образование N2O, являются избыток воздуха и температура слоя. Существенное снижение может быть достигнуто улучшением систем подачи топлива (перемешивание в слое) и регулированием топочного процесса при пониженных избытках воздуха. Важное значение имеет повышение температуры слоя с обычного уровня 830—850 °С до примерно 900 °С.
Таким образом, управление выбросами СО и N2O также связано с поддержанием определенной температуры слоя (надслоевого пространства в схеме Циркофлюид) и избытка воздуха (регулирования расхода вторичного воздуха).
В последнее время имеется тенденция к совместному сжиганию угля и биомассы, а также к использованию технологии ЦКС для утилизации различных стоков и твердых бытовых отходов. При этом более чем в 2 раза снижаются выбросы СО2 [3.60], удается эффективно сжигать высоковлажные отходы, имеющие, как правило, низкие зольность и содержание серы, и уголь с высокой зольностью и сернистостью, что дает дополнительный природоохранный эффект и экономию невозобновляемого топлива.
В [3.77] приведены результаты совместного сжигания бурого угля и осадка сточных вод на котле с ЦКС вблизи г. Кельн (Германия). Котел с ЦКС паро- производительностью 280 т/ч (давление пара 9 МПа, температура 500 °С) был пущен в 1991 г. и рассчитан на сжигание бурых углей Рейнского бассейна.
В 1993—1995 гг. были выполнены специальные лабораторные исследования условий сжигания, а с 1998 г. началась эксплуатация этого котла со сжиганием до 35 т/ч осадка сточных вод. Осадок имеет влажность 70 %, зольность 15 % и теплоту сгорания примерно 200 ккал/кг. Теплота сгорания бурого угля примерно 2200 ккал/кг при влажности до 60 %. В осадке содержится довольно большое количество соединений хлора и фтора (более 1,5%); опасность также представляют тяжелые металлы (до 0,1 %, в том числе ртуть до 3 мг/кг).
Осадок доставляют автомобильным транспортом (в контейнерах или на самосвалах) и ковшовым погрузчиком перегружают в бункер, снабженный шнеками. Эти шнеки направляют осадок в насос с двумя плунжерами, который подает его по двум трубопроводам в котел. Течки подачи в котел размещены на линии рециркуляции золы после пневмозатворов. Эксплуатация в течение 3 лет показала, что механически отжатый осадок сточных вод отлично подается в котел в указанных ранее точках и хорошо распределяется по слою топлива. Прямая подача его в топку была не столь успешной.
По сравнению с нормальной эксплуатацией на угле при подаче 25 т/ч осадка температура в топке на 15—25° ниже; профиль температуры по высоте оставался постоянным. Совместное сжигание приводило к росту теплоты дымовых газов примерно на 10%. Такой же эффект дает рециркуляция примерно 15 % дымовых газов. За счет большого количества СаО в золе бурого угля происходит хорошее связывание серы, поэтому добавка известняка не требуется. Уменьшилось на 30 % потребление песка для заполнения слоя, так как в осадке имеется много песка. Увеличивается риск хлоридной коррозии поверхностей нагрева, особенно на «холодной» части воздухоподогревателя. Для очистки от паров ртути и других тяжелых элементов использован метод с вводом мелкоразмолотого кокса (<0,4 мм) с расходом около 80 кг/ч на 400 тыс. м3/ч дымовых газов. Кокс вводится в газоход перед электрофильтром.
Одним из наиболее важных вопросов при огневом обезвреживании отходов, содержащих полихлориды, является очистка дымовых газов от диоксинов. Наибольшее их количество образуется при сжигании муниципальных отходов. В [3.78, 3.79] приведен японский и шведский опыт сжигания этих отходов по технологии ЦКС. В [3.78] исследованы четыре вида отходов с содержанием хлоридов от 0,34 до 4,53 % на сухую массу. Показано, что при концентрации гидрохлоридов менее 70 млн долей (ррт) концентрация диоксинов в дымовых газах крайне мала (менее 0,01 мг/м3) и существенно (в 10 раз) увеличивается при росте концентрации гидрохлоридов до 700 ррт.
Увеличение температуры дымовых газов в рукавном фильтре приводит к снижению степени разложения диоксинов. При температуре ниже 180 °С степень разложения около 99 %. Увеличение времени пребывания газов в топке на 1 с приводит к связыванию 50 % диоксинов. Добавка извести в конвективную часть при температуре 400 °С также существенно снижает концентрацию диоксинов. Авторы [3.78] считают технологию ЦКС лучшей с позиции контроля за этими токсичными выбросами.
В [3.78] приведен опыт сжигания муниципальных отходов на котле с ЦКС мощностью 20 МВт в г. Сунсвальд (Швеция). Теплота сгорания отходов составляла около 3000 ккал/кг при содержании хлора на сухую массу 0,7 %. В топку подавался известняк с содержанием СаО 88 %. Кроме того, перед рукавным фильтром добавлялся Са(ОН)2 и в отдельных случаях активированный уголь (для связывания паров ртути). Показано, что при мольном отношении Ca/S в топке около 4 достигается связывание 90 % НС1. В случае добавки Са(ОН)2 эффективность связывания превышает 95 %. В результате удалось выдержать жесткие шведские нормативы по всем газовым компонентам (табл. 3.28).
Таким образом, можно заключить, что мировой опыт использования технологии ЦКС для утилизации ряда сложных по составу отходов позволяет надеяться на положительный результат ее внедрения для совместного сжигания различных отходов и стоков с углем в ряде регионов России, в особенности на целлюлозно-бумажных комбинатах.
Одним из наиболее серьезных недостатков технологии ЦКС являются трудности с использованием золошлаков ТЭС. В [3.80] указывается, что на начало 90-х годов XX в. доля используемой золы котлов ЦКС составляла всего 10%. В Европе эта доля значительно выше, однако высокие затраты на утилизацию золы снижают конкурентоспособность технологии ЦКС. В США большая часть золы ЦКС отправляется в золоотвалы с затратами не менее 4 долл/т.
В [3.80] приведены следующие направления использования золы:
• стабилизация почв; применяется в случае местной поставки на близлежащие фермы;
• стабилизация жидких стоков; пригодна вблизи крупных городов;
• покрытие отвалов;
• дорожные основы, добавки в цемент, асфальт;
• заполнение выработок и скважин; применяется при расположении ТЭС вблизи шахт;
• использование для наращивания дамб золоотвалов.
В [3.80] делается вывод о том, что в настоящее время использование золы котлов с ЦКС в США находится в том же состоянии, как это было 10—15 лет назад с золой факельного сжигания. Из-за различий в качестве топлива, возможностях золоотвалов, местных законах до сих пор не разработаны общие положения по использованию золы. Отмечается, что благодаря значительному увеличению ввода котлов с ЦКС и постоянному ужесточению норм по защите окружающей среды должны быть определены более выгодные решения, позволяющие снизить затраты на захоронение золы в золоотвалах.
ВТИ разработаны предложения по методам утилизации золошлаковых материалов котла с ЦКС Несветай ГРЭС. Отмечается, что зола АШ при сжигании в котлах с ЦКС является нетоксичной. К настоящему времени прошли экспериментальную проверку в лабораторных условиях следующие методы: изготовление безобжигового гравия и бетона на его основе, использование золы совместно с отходами угледобычи для закладки выработанных пространств и применение золы для производства мелкозернистого бетона. Перспективным представляется использование золы котлов с ЦКС для наращивания дамб существующих золоотвалов.
Сжигание твердого топлива в расплаве
Еще одним примером новой технологии использования твердого топлива, решающим проблему защиты окружающей среды, является метод газификации угля в шлаковом расплаве. Сущность этого метода, который уже несколько лет разрабатывает НИИ экологических проблем энергетики [3.81, 3.82], заключается в следующем. Твердое топливо подается в специальную камеру-газификатор, которая является составной частью энергетического котла. При пуске ванна камеры-газификатора заполняется жидким шлаком, требуемый объем которого в дальнейшем поддерживается автоматически. С помощью фурм-горелок слой шлака продувается обогащенным кислородом дутьем, благодаря чему он поддерживается в состоянии газошлаковой эмульсии. Уголь в расплав подается без какой-либо предварительной подготовки. С целью связывания серы и обеспечения определенных вязкостных характеристик расплава к углю добавляется известняк. Выходящий генераторный газ дожигается в топке котла, расположенного над камерой-газификатором (рис. 3.74).
При барботировании расплава паро-кислородсодержащим дутьем в камере-газификаторе шлак претерпевает сложные физико-химические превращения с восстановлением металлов и накоплением их в донной части камеры. Этот так называемый тяжелый шлак представляет собой чугун, или ферросилиций, в котором, как в извлекающей фазе, достигаются относительно высокие концентрации цветных и редкоземельных металлов (полиметаллоконцентрат), что делает эффективной дальнейшую переработку данного ценного сырья на предприятиях черной и цветной металлургии. Тяжелый шлак периодически сливается из камеры-газификатора в изложницы разливочной машины, где охлаждается, а затем направляется в виде отдельных чушек на склад готовой продукции. Легкий шлак, состоящий из оксидов кремния, кальция, алюминия, магния, натрия и калия, сливается из верхней части ванны камеры-газификатора и поступает на установки переработки его в товарную продукцию.
Основываясь на результатах экспериментальных исследований, проведенных на лабораторных и полупромышленных установках, авторы метода считают, что технология газификации угля в барботируемом парокислородным дутьем шлаковом расплаве имеет ряд важных преимуществ:
• возможность использования любых низкосортных и непроектных углей независимо от их марки и качества;
• реализацию максимальной концентрации технологического процесса в условиях идеального смешивания жидких, твердых и газообразных компонентов;
• безотходность по золошлакам, которая обеспечивается переводом практически всей минеральной части топлива в расплав и возможностью корректировки его состава с целью вторичной переработки;
• восстановление и вывод из расплава черных и цветных металлов;
• высокую экологическую чистоту, особенно по твердым выбросам (50 мкг/м3) и оксидам азота (100 мг/м3), снижение на 30% выбросов SO2 и на 10% выбросов СО2;
• возможность регулирования за счет изменения количества подаваемого в расплав известняка перехода сернистых соединений в газообразную (дымовые газы) или жидкую (шлаки) фазы и связывания шлаком до 90 % серы топлива;
• отсутствие громоздких систем топливоприготовления, пылеподачи и золоочистки; отсутствие золоотвала;
• широкую реализацию дефицитных попутных газов кислородной станции (азот, аргон) для нужд предприятий региона;
• высокую экономическую эффективность, в том числе за счет дальнейшего расширения ассортимента реализуемой продукции из минеральной части топлива.
Для проверки обоснованности перечисленных достоинств метода предполагается в ближайшие годы провести полномасштабный эксперимент: на Несветай ГРЭС в ОАО «Ростовэнерго» будет создана опытно-промышленная установка (ОПУ) с технологией газификации угля в шлаковом расплаве. Тепловая мощность ОПУ 200 МВт, расход пара от котельной установки с температурой 510 °С и давлением 10 МПа 220 т/ч. Основное топливо — донецкий уголь АШ с теплотой сгорания 19,82 МДж/кг.
Научный разработчик проекта — НИИ экологических проблем энергетики (ОАО НИИЭПЭ). Разработчик и изготовитель котла для ОПУ — ТКЗ «Красный котельщик», камеры-газификатора — НПО «АЛГОН» и институт «Стальпроект» (г. Москва).
Технологическая схема ОПУ включает следующие структурные элементы: систему подачи топлива и флюса; котел с камерой-газификатором; кислородную станцию; систему подготовки и подачи дутья; установки для переработки шлака в товарную продукцию; устройство приема и брикетирования полиметаллических отходов; узел подачи природного газа; систему технического водоснабжения.
Топливо и флюс со склада по существующему тракту топливоподачи Несветай ГРЭС направляются в бункер сырого угля ОПУ, а затем без дополнительной подготовки (металлоулавливания, дробления, размола и др.) подаются в камеру-газификатор. Кислород к фурмам подводится с давлением 0,3 МПа. Для производства кислорода используется серийная воздухоразделительная установка типа КААр-15. Уголь в камере благодаря высокой температуре подвергается термическому разрушению и за счет барботажа ванны равномерно распределяется по сечению. В результате в камере-газификаторе создаются идеальные условия тепло- и массообмена, обеспечивающие высокую эффективность процесса газификации угля. Теплота сгорания образующегося генераторного газа составляет 6,0—11,0 МДж/нм3 A400— 2700 ккал/нм3), что позволяет дожечь его в топке котла при умеренном температурном уровне факела. Дожигание газов производится в среде горячего воздуха. После прохождения дымовыми газами конвективных поверхностей нагрева котла и воздухоподогревателя они направляются в дымовую трубу ГРЭС.
Процесс газификации в расплаве шлака может осуществляться как при атмосферном, так и при повышенном давлении в камере-газификаторе. Опытно-промышленная установка Несветай ГРЭС, предназначенная для исследования и отработки режимов новой отечественной технологии, спроектирована по наиболее простой схеме, в которой генераторный газ из камеры-газификатора, работающей при атмосферном давлении, направляется для сжигания в топку парового котла, примыкающую непосредственно к выходному сечению камеры-газификатора. Энергетическая эффективность такого варианта использования генераторного газа определяется параметрами пара и тепловой схемой паросилового цикла. Параметры пара, принятые в проекте ОПУ, не являются оптимальными, поскольку с целью обеспечения промышленного использования ОПУ для выработки электроэнергии на ГРЭС при минимальных дополнительных капиталовложениях котельная установка ОПУ встраивается в действующий на Несветай ГРЭС паросиловой цикл с относительно низким давлением пара 10 МПа и температурой 510 °С без промежуточного перегрева.
Тепловая эффективность использования угля при данной технологии газификации резко повышается в случае применения ее в более экономичных тепловых схемах и термодинамических циклах (при сверхкритических параметрах пара котла, ПГУ с внутри- цикловой газификацией при атмосферном и высоком давлении, впрыске пара в ГТУ, термоэмиссионной надстройке и др.). Вторым этапом реализации проекта Федеральной программы является создание газификатора с аэрошлаковым расплавом под давлением. Совместно с ТКЗ «Красный котельщик» уже разработаны технические предложения стендового варианта данного газогенератора.
Рабочее давление в его реакционной камере 2 МПа, тепловая мощность 6 МВт. Газогенератор планируется установить на Несветай ГРЭС.
Освоение и применение данной технологии в электроэнергетике позволяют осуществить комплексное безотходное использование всей органической и минеральной массы угля как ценного природного сырья для производства не только энергетической, но и других пользующихся широким спросом видов товарной продукции и тем самым значительно повысить эффективность использования угля.
Дата добавления: 2020-12-22; просмотров: 79; Мы поможем в написании вашей работы! |
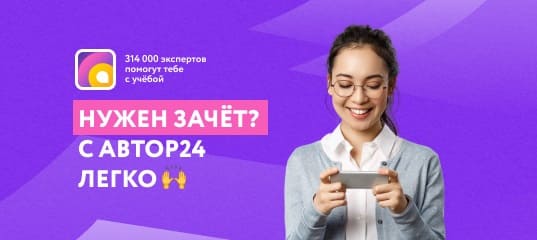
Мы поможем в написании ваших работ!