Техническое описание и принцип работы
Лабораторная работа.
Восстановление деталей плазменной наплавкой (сваркой)
Цель работы: изучить сущность процесса плазменной наплавки, ознакомиться с оборудованием и материалами, применяемыми при восстановлении деталей.
Задание
1) Ознакомиться с теоретическими положениями по технологии восстановления деталей машин с помощью плазменной наплавки;
2) ознакомиться с порядком выполнения лабораторной работы;
3) изучить принцип работы плазмотрона;
3) выполнить экспериментальную часть лабораторной работы;
5) оформить отчёт по выполненной лабораторной работе.
Оснащение рабочего места
Стол для электросварочных работ ОКС-7523 с вытяжным шкафом, портативный аппарат «Мультиплаз-3500», средства индивидуальной защиты, комплект деталей для проведения экспериментальной части работы.
Указания по технике безопасности
При проведении работ должны соблюдаться правила техники безопасности по ГОСТ 12.4.113-82 ССБТ Работы учебные лабораторные. Общие требования безопасности. ГОСТ 12.2.061-81 ССБТ Оборудование производственное. Общие требования безопасности к рабочим местам.
Меры безопасности при работе на аппарате «Мультиплаз 3500»:
Запрещается:
- Использовать аппарат для любых других целей, кроме сварки, резки, пайки, сваркопайки и пайкосварки.
- Подпускать к аппарату и допускать использование его детьми, лицами с ограниченными возможностями здоровья, а также лицами, использующими кардиостимуляторы, без предварительной консультации с врачом.
|
|
- Оставлять включенный аппарат без присмотра.
- Подключать или присоединять к блоку питания или горелке любые принадлежности, кроме рекомендуемых производителем.
- Подключать к блоку питания “Мультиплаз-3500” любые другие горелки, кроме горелки “Мультиплаз-3500”.
- Подключать горелку к любым внешним источникам рабочего тела (газовые баллоны, компрессора, емкости с жидкостью и др.).
- Заправлять горелку любыми другими жидкостями, отличными воды и водного раствора этилового спирта.
- Устанавливать блок питания и работающую горелку на поверхность с наклоном больше 10° без фиксаторов от опрокидывания.
- Работать с горелкой, когда индикатор SELV на передней панели не горит, не надев на горелку защитную насадку.
- Работать без заземления корпуса блока питания.
- Проводить работы с аппаратом без специальных защитных очков с темными стеклами.
- Работать на металлическом или сыром полу без изолирующего коврика для ног.
- Работать во влажной обуви и/или влажными ногами.
- Прикасаться к блоку питания мокрыми или влажными руками.
- Обрабатывать горелкой свежеокрашенные конструкции.
|
|
- Прикасаться к нагретым частям аппарата.
- Перемещать блок питания во время работы.
- Тянуть аппарат за сетевой кабель и обматывать сетевой кабель вокруг
аппарата.
Общие сведения
В 1923 г. американские физики Л. Тонкс и И. Ленгмюр предложили называть среду, в которой значительная часть молекул или атомов ионизирована - плазмой. Плазма является состоянием вещества, наиболее распространенном в космосе.
Физические свойства плазмы – высокие значения температур, энтальпия и электропроводность – позволяют осуществлять ряд интересных физических и технических проектов.
Плазма нашла применение в металлургии, в сварочном и ремонтном производстве.
Для технологических целей используют так называемую “низкотемпературную” плазму с температурой 103…105К, представляющую собой частично ионизированный газ.
Для получения плазмы разработаны плазмотроны или плазменные горелки.
В дуговых плазмотронах плазма с требуемыми характеристиками может быть получена при различных видах взаимодействия дуги с плазмообразующим газом: аргоном, гелием, азотом, водородом, кислородом и воздухом [1].
Плазмообразующий газ, используемый в плазмотроне, в значительной мере определяет технологические возможности плазменной струи, и его нужно выбирать в зависимости от целей процесса.
|
|
Молекулярные газы – азот, водород, кислород и воздух позволяют увеличить эффективность нагрева за счет реакций диссоциации (разложения)-ассоциации (объединения). При этом происходит дополнительное поглощение теплоты в столбе дугового разряда.
При попадании на обрабатываемую поверхность плазмообразующий газ ассоциирует (превращается из атомного в молекулярный); при этом выделяется теплота, затраченная на его диссоциацию.
Виды плазменных источников энергии.
При нагреве плазмой деталей передача энергии может осуществляться или только за счет процессов теплообмена нагретого газа с твердой или жидкой фазой (деталь электрически не связана с источником питания), или за счет суммарного действия теплообмена и электрического взаимодействия заряженных частиц плазмы с электродом-заготовкой.
В связи с этим в практике плазменной технологии сложилось три основных принципиальных схемы плазмотронов.
В двух схемах (рисунок 1а,б) для получения плазмы используют электрический дуговой разряд; в схеме (рисунок 1в) нагрев газа и образование плазмы осуществляется за счет безэлектродного (высокочастотного индукционного разряда.
|
|
Схема (а) получила название плазменной дуги, а плазмотрон для ее получения — плазмотрон прямого действия. В схеме (б) изделие 1 гальванически не связано с электродом, поэтому схема называется плазменной струей, а плазмотрон носит название плазмотрона косвенного действия.
Характеристики плазменного источника.
Основными характеристиками плазменного источника энергии является его эффективная тепловая мощность и коэффициент сосредоточенности, определяющий распределение удельного теплового потока по поверхности обрабатываемого изделия.
а – прямого действия; б – косвенного действия;
в – плазмотрон с высокочастотным индукционным разрядом
Рис. 1 — Основные схемы плазмотронов.
Для плазменной дуги эффективная тепловая мощность равна:
, Вт
где U – напряжение дуги, В;
I – сила тока дуги, А;
– эффективный КПД процесса плазменного нагрева, учитывающий потери энергии при передаче ее к изделию.
Рисунок 2 - Распределение температуры плазменной дуги (а) и плазменной струи (б) по радиусу r и по длине l
Распределение температуры плазменной дуги и плазменной струи по радиусу (r) и по длине ( ) крайне неравномерны. Максимальная температура наблюдается в центре на оси плазменного потока, причем она значительно выше, чем у открытой дуги.
Плотность теплового потока для плазменных источников энергии также выше, чем для открытой дуги, и достигает Вт/см2.
Нагрев газа в плазмотроне приводит к резкому уменьшению плотности газа. За счет этого увеличивается скорость его истечения. Скорость потока максимальна в центре, где наблюдается максимальная температура и минимальный массовый расход газа . Максимальная температура составляет 17000 °С, а максимальная скорость достигает 2 км/с.
Большая скорость потока плазмы при выходе его из плазмотрона позволяет получать значительный газодинамический напор, который растет с увеличением силы тока.
В большинстве случаев расход газа в плазмотроне превышает 1 л/с и течение горячего газа носит турбулентный характер.
Уменьшение расхода газа до значений менее 0,1 л/с позволяет получать ламинарные плазменные струи, которые отличаются большей длиной (до 0,4 м) и высокой стабильностью.
В потоке плазмы можно получить практически любое вещество в молекулярной или паровой фазе. Плазменный нагрев позволяет получать в паровой фазе нитриды и карбиды, оксиды тугоплавких металлов и неметаллы высокой чистоты. При этом можно значительно увеличить выход продуктов реакции по сравнению с другими способами проведения химических реакций.
Примером таких процессов может служить плазмохимическое получение абразивных материалов на основе бора, осаждение на рабочей поверхности металлорежущего инструмента нитрида титана и т.д.
Содержание работы
Занятие 1. Плазменная наплавка используется для нанесения на обрабатываемые заготовки поверхностных слоев (чаще всего из металлов и сплавов, отличных по составу от материала подложки) с целью повышения эксплуатационных свойств деталей. Для наплавки обычно применяют материалы со специальными свойствами (высокой твердостью, повышенной износостойкостью, коррозионной и термостойкостью).
Наплавка позволяет получать изделия из дешевых конструкционных материалов с рациональным распределением свойств по отдельным элементам. При этом значительно снижается расход дорогостоящих легирующих материалов. Толщина наплавленных за 1 проход слоев может достигать 4…5 мм; возможна многослойная наплавка.
Наплавку проводят плазменной струей, что дает возможность регулировать глубину проплавления основного металла посредством изменения расстояния между горелкой и заготовкой. Чтобы обеспечить защиту ванны расплавленного металла от взаимодействия с атмосферными газами, в качестве плазмообразующих газов используют аргон и водород.
С помощью плазменной наплавки в ремонтных целях восстанавливают дорогостоящие узлы и детали.
Существует две основные разновидности процесса:
- подача материала в плазмотрон в виде прутка или проволоки;
- подача материала в плазмотрон в виде порошка (оксиды, нитриды, карбиды).
На рис. 3 показана принципиальная схема установки для плазменного напыления порошковых материалов.
1 – электрод, 2 – источник питания, 3 – регулируемое сопротивление, 4 – охлаждающая вода, 5 – плазменная головка, 6 – плазменный факел, 7 – деталь, 8 – порошок, 9 – дуга
Рис. 3 - Схема плазменного напыления порошковыми материалами.
Для напыления материалов разработано несколько моделей плазменных установок. Промышленность серийно выпускает установки марок УМП-4 конструкции ВНИИАВТОГЕНмаш и УПУ-3М конструкции НИАТ.
Установки УМП-4-64 и УМП-5-68 состоят из трех самостоятельных узлов: плазменной горелки, порошкового питателя и пульта управления.
Технические характеристики плазменных установок приведены в таблице 1.
Для питания электроэнергией плазмотронов из выпускаемого сейчас оборудования наиболее пригодны машинные генераторы и полупроводниковые выпрямители.
Питание плазменных установок можно производить от двух последовательно соединенных преобразователей ПСО-500 или двух полупроводниковых выпрямителей ВКС-500 или от выпрямителя ИПН-160/600, обеспечивающих рабочее напряжение 90—100 В.
Баллоны с рабочими газами (азот, аргон и водород для плазменного напыления) следует устанавливать в соответствии с существующими правилами обращения с баллонами для сжатых газов.
Таблица 1 - Техническая характеристика плазменных установок
Параметр | Установка | ||
УМП-4-64 | УМП-5-68 | УПУ-3 | |
Мощность установки, кВа рекомендуемая / максимальная | 30/40 | 30/40 | 30/35 |
Производительность по напыленному материалу, кг/ч: вольфраму / окиси алюминия/ двуокиси циркония | 4/3/1,7 | 5/4/3 | -/3,5/- |
Масса, кг: установки в целом / горелки | 43/0,45 | 120/0,7 | 900/- |
Расход охлаждающей воды, дм3/мин | 3 | 3,5 | 10 |
Кислородные баллоны и баллоны с горючими газами при большом объеме работ также целесообразнее устанавливать в рампы.
Непосредственно на баллоне следует устанавливать редукторы для снижения давления газов до рабочего и поддержания этого давления постоянным.
Для подготовки поверхности в мастерской или на участке устанавливается пескоструйный шкаф (при небольших размерах изделий) или пескоструйная камера.
Технологический процесс ремонта деталей плазменной наплавкой состоит из трех этапов: подготовки поверхностей деталей к наплавке, нанесения покрытия и обработки деталей после наплавки. Подготовка поверхностей деталей к плазменной наплавке является очень важным этапом, так как от него зависит качество сцепления покрытия с металлом детали.
Подготовка поверхности деталей к плазменной наплавке состоит из следующих операций: очистки и обезжиривания деталей от грязи, влаги, окислов и жира; создания шероховатости; защиты поверхностей, не подлежащих наплавке. Очистка и обезжиривание деталей могут быть осуществлены пескоструйной обработкой.
Создание шероховатости на металлизируемой поверхности детали может быть выполнено следующими способами: обработкой стальной крошкой (металлическим песком) или дробью, нарезанием рваной резьбы и др. Обработка стальной крошкой является наиболее эффективным способом подготовки. На поверхность детали наносят струей сжатого воздуха под давлением 5 - 6 кгс/см2 стальную крошку (0,8 - 1,5 мм). Для этой цели могут быть использованы металлоструйные установки, предназначенные для удаления старой краски и очистки деталей от ржавчины. Поверхности деталей цилиндрической формы с небольшим износом перед созданием шероховатости протачивают для получения правильной геометрической формы и обеспечения минимально допустимой толщины покрытия. Для получения прочного сцепления с основным металлом толщина покрытия деталей диаметром от 25 до 100 мм не должна быть менее 0,5 - 0,8 мм.
Поверхности деталей, не подлежащие металлизации, защищают плотной бумагой, картоном или кожухами из листовой стали.
Время между подготовкой поверхности и плазменной наплавки не должно превышать 2 ч.
Нанесение покрытия. Цилиндрические поверхности деталей металлизируют на токарных станках, плоские — в камерах.
При металлизации на токарных станках деталь, закрепленная в патроне или установленная в центрах, получает вращательное движение с окружной скоростью от 15 до 20 м/мин, а плазмотрон, закрепленный на суппорте токарного станка, совершает продольное движение подачи от 1 до 10 мм/об.
Большое влияние на износостойкость и твердость покрытия оказывают режимы наплавки.
При плазменной наплавке, благодаря высокой температуре плазменной струи и большой кинетической энергии напыляемых частиц, покрытие получается плотное и беспористое. Прочность сцепления покрытия с основным металлом почти в 2 раза превышает прочность сцепления при газовой металлизации. Для уменьшения растягивающих напряжений в наносимом слое и предотвращении образования трещин ремонтируемую деталь рекомендуется предварительно подогревать в печи до температуры 150° С, после металлизации деталь медленно охлаждается в термостате.
Обработка деталей после плазменной наплавки. Наплавленные цилиндрические поверхности деталей обрабатывают на токарных и шлифовальных станках, плоские поверхности – на станках или вручную.
Плазменная наплавка успешно может быть использована для создания покрытий, имеющих разнообразные защитные свойства (жаростойких, износостойких и др.), путем нанесения тугоплавких металлов (вольфрама, молибдена), твердых сплавов (типа сормайт) или окислов металлов (Аl2О3, М2О и др.), а также неметаллических материалов с высокой температурой плавления.
К достоинствам процесса плазменной наплавки нужно отнести следующие: возможно напыление любых металлов и сплавов независимо от материала ремонтируемой детали (сталь, стекло), толщина покрытий может достигать 10—15 мм, что позволяет ремонтировать детали с большим износом. Высокая температура плазменной струи позволяет расплавлять и наносить самые тугоплавкие материалы.
Способом металлизации ремонтируют трубы полуосей заднего моста (шейки под подшипники), поворотные цапфы (шейки под подшипники) и другие детали.
Занятие 2.
Техническое описание и принцип работы
Портативный плазменный аппарат «Мультиплаз-3500» рис. 4 является генератором низкотемпературной плазмы, полученной путём нагрева до температуры ионизации паров рабочей жидкости, заливаемой в горелку перед проведением работ. Аппарат рассчитан на непрерывную работу (коэффициент рабочего цикла ПВ=100%). Аппарат состоит из плазменной горелки и блока питания.
Рис. 4 – Общий вид блока питания
2.2 Горелка. Горелка является основной частью аппарата, генерирующей низкотемпературную плазму. Горелка состоит из частей представленных на рис. 5.
Рис. 5 – Горелка «Мультиплаз-3500»
Принцип работы горелки. Оператор, после заправки горелки рабочей жидкостью, включения блока питания и подачи напряжения на катод (нажатие кнопки “ВКЛ” (”ON”)) для возбуждения дуги. При этом происходит замыкание катода и сопла горелки. В момент отпускания стартовой кнопки между катодом и соплом возникает электрическая дуга.
Энергия дуги разогревает сопло, сопло разогревает испаритель, испаритель разогревает рабочую жидкость, превращая её в пар. Пар под действием внутреннего давления (0,4-1,2 атм.) устремляется к кратковременно нажимает стартовую кнопку горелки выходному отверстию в сопле. Выходя из отверстия в сопле, пар сжимает электрическую дугу. Сжатие электрической дуги приводит к повышению её температуры. Сжатая электрическая дуга нагревает пар до температуры ионизации.
Аппарат работает в двух режимах.
Режим дуги косвенного действия РЕЖИМ I (MODE I). Электрическая дуга горит между катодом и соплом. Переносчиком энергии на обрабатываемый материал является только плазменная струя.
Режим дуги прямого действия РЕЖИМ II (MODE II). В цепь режущего (сварочного) тока включен обрабатываемый электропроводный материал, и электрическая дуга горит между ним и катодом внутри плазменной струи. За счет этого тепловая энергия, поступающая на обрабатываемый материал, существенно увеличивается.
Аппарат оснащается двумя горелками, которые конструктивно одинаковы, но горелка с зеленой меткой изначально оснащена соплом для резки, горелка с красной меткой соплом для сварки. Эти горелки взаимозаменяемы при условии замены сопла, установки необходимого заглубления катодного узла и замены рабочей жидкости. Мы рекомендуем для Вашего удобства при возможности соблюдать соответствие между маркировкой горелки и ее назначением.
Дата добавления: 2020-12-22; просмотров: 100; Мы поможем в написании вашей работы! |
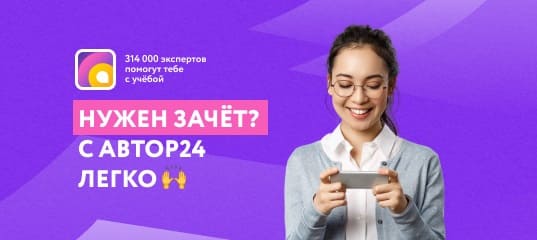
Мы поможем в написании ваших работ!