Электронно-лучевая и лазерная сварка.
Лекция 8. Диффузионная сварка
Диффузионная сварка - сварка давлением, осуществляемая за счет взаимной диффузии атомов в тонких поверхностных слоях контактирующих частей . Диффузионная сварка осуществляется при относительно длительном воздействии повышенной температуры и незначительной пластической деформации.
Диффузионные процессы протекают достаточно активно при нагреве металлов до температур рекристаллизации (0,4 Тплавления) и давлениях, необходимых для пластического деформирования и смятия микровыступов с целью обеспечения физического контакта по всей свариваемой поверхности. диффузионную сварку выполняют в вакууме (сварка химически активных металлов) или в атмосфере защитных или инертных газов.
Схема установки для диффузионной сварки показана на рис. 14.12. Свариваемые заготовки 5 устанавливают внутри камеры 3, охлаждаемой водой, подаваемой по змеевику 2. насосом 7, в камере создается вакуум (10-3…10-5 Па) (или нагнетаются защитные или инертные газы). Нагрев заготовок производится с помощью нагревателя или индуктора ТВЧ 4. Все вводы в камеру (к насосу, к генератору 8, к штоку поршня 6) герметизируются. Процесс сварки идет в две стадии. На первой стадии заготовки нагреваются, и прикладывается давление. Происходит пластическое деформирование микровыступов и разрушение тонких пленок на контактирующих поверхностях заготовок. На второй стадии заготовки выдерживаются под давлением. Под действием диффузии, образуется объемная зона взаимного соединения. Для получения качественного соединения, свариваемые поверхности заготовок необходимо предварительно очищать от окисных пленок и загрязнений.
|
|
Рис. 14.12. Схема установки для диффузионной сварки: 1 – плита; 2 – змеевик; 3 – камера; 4 – индуктор; 5 – заготовки; 6 – шток поршня; 7 – насос; 8 – генератор.
Диффузионная сварка позволяет: соединять металлы, сплавы и керамические материалы в различных сочетаниях и соединять заготовки с большой разницей по толщине. Как правило, полученные соединения не нуждаются в последующей механической обработке.
Плазменная сварка.
Плазменная сварка - сварка плавлением, при которой нагрев производится сжатой дугой.
Источником теплоты при плазменной сварке является плазменная струя – направленный поток ионизированных частиц газа, с температурой до 20000оС.
Плазму получают, пропуская поток газа через столб сжатой электрической дуги (рис.4.13). Столб дуги 2, горящий между электродом 3 и соплом 5, помещают в узкий канал 6 с охлаждаемыми стенками, и через него продувают газ. Столб дуги сжимается, что приводит к повышению в нем плотности энергии и температуры. Частые столкновения частиц продуваемого газа приводят к их высокой ионизации. Загорается плазменная дуга 1. В качестве плазмообразующего газа обычно используют аргон. Для получения более мощной дуги используют водород или азот.
|
|
Различают горелки с плазменной дугой выделенного типа (рис. 4.13, а) и с дугой невыделенного типа (рис. 4.13, б), горящей между электродом и заготовками 7.
В горелках первого типа столб дуги располагается в канале 6 корпуса горелки изолированного от электрода керамической вставкой 4. Назначение: нагрев, пайка, резка тонких (до 10 мм) заготовок, сварка.
Горелки второго типа обладают повышенной эффективной мощностью дуги, что позволяет разрезать относительно толстые (до 50 мм) заготовки.
Рис. 4.13. Схемы плазменных горелок:
а - горелка с плазменной дугой выделенного типа;
б - горелка с плазменной дугой не выделенного типа:
1 - плазменная дуга; 2 – электрическая дуга; 3 – электрод; 4 - керамическая вставка; 5 – сопло; 6 – канал; 7 – заготовки.
Плазменная дуга, являясь концентрированным источником теплоты, обладает большой проплавляющей способностью и позволяет сваривать заготовки без разделки кромок толщиной до 10 мм, а также. микроплазменную сварку заготовок толщиной 0,025…0,8 мм. Если увеличить расход плазмообразующего газа, то можно резко поднять тепловую мощность, скорость истечения и давление плазмы.
|
|
Назначение плазменной дуги:
– сварка металлов (высоколегированной стали, сплавов титана, никеля, молибдена, вольфрама) и неметаллов;
– резка всех материалов;
–наплавки;
–напыления.
Плазменная резка производится высокоскоростной плазменной дугой. В отличие от плазменных сварочных головок, плазменный резак снабжен дополнительными каналами для подачи в зону резания защитного газа.
Резка производится при величине тока 55…150А и напряжении 110…120 в. Современные установки для плазменной резки оснащены числовым программным управлением.
ХИМИЧЕСКИЕ ВИДЫ СВАРКИ
Химические способы включают в себя термитную и газовую сварку.
Газовая сварка
Газовая сварка - сварка плавлением, при которой для нагрева используется тепло пламени смеси горючих газов с кислородом, сжигаемых с помощью горелки .
Преимущества:
– простота;
– не требует сложного и дорогого оборудования;
|
|
– не требует источника электроэнергии.
При помощи газовой сварки можно сваривать почти все металлы, применяемые в технике. Такие металлы, как чугун, медь, латунь, свинец легче поддаются газовой сварке, чем дуговой.
Недостатки:
– высокая стоимость горючего газа (ацетилена) и кислорода;
– небольшая скорость нагрева металла;
– большая зона теплового воздействия на металл и взрывоопасность процесса.
Применение:
– изготовление и ремонт изделий из тонколистовой стали (сварка сосудов и резервуаров небольшой емкости, заварка трещин и т.д.);
– сварка трубопроводов малых и средних диаметров (до 100мм) и фасонных частей к ним;
– ремонтная сварке литых изделий из чугуна, бронзы и силумина (заварка литейных дефектов);
– сварка изделий из алюминия и его сплавов, меди, латуни, свинца;
– наплавка латуни на стальные и чугунные детали;
– сварка кованого и высокопрочного чугуна с применением присадочных прутков из латуни и бронзы, низкотемпературной сварке чугуна.
В газовой сварке используются горючие газы:
ацетилен, водород, метан, пропан и пары керосина.
Основным горючим газом является ацетилен.
Ацетилен - бесцветный газ, с резким запахом, ядовит, взрывоопасен. Ацетилен получают из природного газа термоокислительным пиролизом метана с кислородом (используется для снаряжения ацетиленовых баллонов) или в специальных ацетиленовых генераторах при взаимодействии карбида кальция с водой: CaC 2 +2H 2 O=C 2 H 2 +Ca(OH)+ Q.
Наиболее безопасно использовать ацетилен, поставляемый в баллонах. Ацетилен поставляется в баллонах белого цвета с красной надписью «ацетилен». Ацетиленовые баллоны, для уменьшения взрывоопасности, заполнены пористым наполнителем (гранулированный активированный уголь размером зерна 1…3,5 мм) и ацетоном. При давлении 1,5 МПа в 1 литре ацетона растворяется до 368 л ацетилена. Максимальное давление в ацетиленовых баллонах – 1.9 МПа.
Кислород поставляется в баллонах голубого цвета с черной надписью «кислород». При давлении 15 МПа, в баллоне помещается 600 л газообразного кислорода. Так как масла и жиры в атмосфере сжатого кислорода способны самовоспламеняться, то вся кислородная аппаратура не должна контактировать с этими веществами. В противном случае возможен взрыв с воронкой глубиной до 5 метров.
Для уменьшения сетевого или баллонного давления газа и обеспечения постоянного рабочего давления в газовых магистралях применяются газовые редукторы.
Горелка для газовой сварки – устройство для газовой сварки с регулируемым смешением газов и созданием направленного газового пламени. Для сварки чаще всего используются газосварочные горелки инжекторного типа (рис. 4.15, а), так как они наиболее безопасны. Под давлением 0,1…0,4 МПа, кислород поступает в горелку, через вентиль 4 и подается в кольцевой инжектор 6. Выходя с большой скоростью из узкого канала инжектора, кислород подсасывает горючий газ, поступающий через вентиль 5. В смесительной камере 3 получаем горючую смесь, которая, через мундштук 2, подается к сменному наконечнику 1. Все горючие газы, содержащие углеводороды, при сгорании образуют сварочное пламя, имеющее три отчетливо видимые зоны (рис. 4.15, б):
– ядро пламени (зона7);
– восстановительная (зона 8);
– факел (зона 9).
Ядро имеет форму закругленного ярко светящегося конуса. Оно состоит из раскаленных частиц углерода сгорающих в наружной части ядра.
Восстановительная зона в основном состоит из окиси углерода, получаемого за счет сгорания ацетилена: C 2 H 2 +O 2 =2CO 2 +2H 2 O. Эта зона имеет более темный цвет. Наибольшая температура сварочного пламени находится в этой зоне, на расстоянии 2…4 мм от ядра.
Факел имеет удлиненную конусообразную форму. Он состоит из углекислого газа и паров воды, которые получаются при сгорании окиси углерода и водорода, поступающих из восстановительной зоны и из окружающего атмосферного воздуха: 4CO+2H 2 +3O 2 =4CO 2 +2H 2 O
. Внешний вид и температура газового пламени зависит от соотношения объемов ацетилена и кислорода β=V O2 /V C2H2, где V O2 - объем подаваемого в горелку кислорода; V C2H2 - объем подаваемого в горелку ацетилена.
Рис.4.15. Газосварочная горелка и ацетилен – кислородное пламя:
а – горелка инжекторного типа; 1 – сменный наконечник; 2 – мундштук; 3 – смесительная камера; 4 - кислородный вентиль; 5 - вентиль горючего газа; 6 - кольцевой инжектор; б – нормальное пламя; в – окислительное пламя; г– восстановительное пламя; 7– ядро; 8 – восстановительная зона; 9 – факел; Т – температура.
В зависимости от величины β можно получить три вида сварочного пламени:
– нормальное;
– окислительное;
– восстановительное.
Для нормального пламени (рис. 4.15, б) (β = 1…1,3) характерно отсутствие в восстановительной зоне свободного кислорода и углерода.
Окислительное пламя (рис..15, в) получается при избытке кислорода (β = 1,5…1,7). Окислительное пламя имеет конусообразную форму бледной окраски. Все пламя приобретает синевато – фиолетовую окраску и горит с характерным шумом. Температура пламени несколько выше, чем у нормального.
Науглероживающее пламя (рис. 4.15, г) получается при избытке ацетилена (β = 0,95). Ядро пламени может иметь несколько зубчиков, теряет резкость очертаний, а на его конце появляется зеленый венчик.
Газокислородная резка металлов заключается в сжигании нагретого металла в струе чистого кислорода.
Различают два вида резки: разделительная и поверхностная.
При разделительной резке из металлического листа вырезается заготовка для дальнейшей обработки. Разделительная резка может осуществляться вручную по разметке. В серийном производстве применяется резка с использованием стационарных машин по шаблонам.
При поверхностной резке удаляется лишний металл с поверхности изделий.
Для осуществления процесса резки необходимы следующие условия:
– температура плавления металла должна быть больше температуры его горения в атмосфере кислорода. В противном случае, металл будет плавиться и переходит в жидкое состояние до резки.
– количество тепла, выделяемого при резке должно быть достаточным для поддержания непрерывности процесса.
– теплопроводность металла не должна быть слишком высокой и должна способствовать сохранению тепла на поверхности кромки реза.
Наиболее полно этому условию удовлетворяют низкоуглеродистые и низколегированные стали. При содержании в стали углерода 0,4…0,5% резка усложнена, при содержании углерода ≥ 1,2% резка невозможна. При содержании в стали марганца 4…10% резка усложняется; при содержании марганца ≥ 14% резка невозможна.
Газовый резак отличается от газовой горелки наличием дополнительного кислородного вентиля. Процесс резки осуществляется в два этапа.
- нагрев зоны резки до температуры горения металла в кислороде (характеризуется появлением большого числа искр);
- собственно резка (отключается ацетилен и кислород из основной магистрали). Дополнительным вентилем подключается кислород.
ЛУЧЕВЫЕ ВИДЫ СВАРКИ
К лучевым видам сварки относятся:
электронно-лучевая и лазерная сварка.
Электроннолучевая сварка
Электроннолучевая сварка (ЭЛС) – сварка плавлением, при которой для нагрева используется энергия ускоренных электронов. Электронный луч это сжатый поток электронов, перемещающихся с большой скоростью от катода к аноду в сильном электрическом поле. При соударении электронного потока с твердым телом до 90% кинетической энергии электронов переходит в тепловую. Температура в месте соударения достигает 5000…6000оС.
Схема формирования сварного шва показана на рис. 4.16. При сварке электронным лучом теплота выделяется непосредственно в самом свариваемом металле, вызывая плавление и частичное испарение металла. 1.
Расплавленный металл заготовок 4 вытесняется из зоны сварки давлением паров металла (парогазовый канал 2). Расплавленный металл распределяется по сварочной ванне неравномерно: фронт расплава 5 (передняя стенка канала) имеет толщину 0,05…0,5 мм, а сзади электронного луча 3, ближе к верхней части ванны, сосредоточен основной объем расплава 6. При кристаллизации этого основного объема и образуется сварной шов
Особенности ЭЛС заключающиюся в следующем: Из-за наличия зазора между свариваемыми заготовками, частичного испарения и выброса материала заготовок наблюдается занижение уровня сварного шва. Остаточные магнитные поля в деталях из ферромагнитных материалов отклоняют электронный луч от плоскости стыка заготовок. Поэтому после сборки заготовок, непосредственно перед сваркой, необходимо их размагнитить. Перед сваркой необходимо провести специальную разделку поверхностей стыка заготовок, которая обеспечит оптимальные условия формирования сварного шва и повысит точность сварки. Для защиты поверхностей свариваемых заготовок от брызг расплавленного металла необходимо использовать экраны. Обычно ЭЛС производится в вакуумных камерах при давлении 10…3Па. Вакуум обеспечивает беспрепятственное перемещение электронов и защиту от окисления катодной нити и зоны сварки.
Рис. 4.16. Схема электронно-лучевой сварки: 1 – сварной шов; 2 – парогазовый канал; 3 – электронный луч; 4 – заготовки; 5 – фронт расплавленного металла; 6 – основной объем расплавленного металла.
Высокая концентрация энергии в сфокусированном луче (до (5…7,5)104 Вт/мм2) реализует кинжальное плавление материала заготовок (отношением глубины шва к его ширине до 1: 30) с узкой з.т.в.
ЭЛС позволяет сваривать большинство токопроводящих материалов (легированные и высоколегированные стали; титановые, вольфрамовые, танталовые, ниобиевые, циркониевые, молибденовые и никелевые сплавы; некоторые керамики). Минимальная толщина свариваемых заготовок составляет 0,02 мм, максимальная – 100 мм. ЭЛС применяют для соединения малогабаритных (электроника, приборостроение, часовая промышленность) и крупногабаритных деталей (диски диаметром 50 …2300 мм; цапфы; валы; рычаги; трубные и корпусные изделия).
Лазерная сварка.
Лазерная сварка – сварка плавлением, при которой для нагрева используется энергия излучения лазера.
Лазерный луч представляет собой вынужденное монохроматическое излучение. Длина волны излучения, в зависимости от природы рабочего тела лазера, лежит в пределах от 0,1 до 10 мкм. Атомы вещества имеют определенный запас энергии и находятся в устойчивом энергетическом состоянии. Если атому дать дополнительную энергию («накачка» или «возбуждение» атома), он выйдет из равновесного состояния. Излучение возникает в результате вынужденных скачкообразных переходов атомов рабочего тела лазера на более низкие орбиты. При этом возбужденный атом стремится вернуться в устойчивое энергетическое состояние и отдает квант энергии в виде фотона.
Испускание света можно инициировать воздействием внешнего фотона, обладающего энергией, соответствующей разнице энергий атома в возбужденном и нормальном состоянии.
Схема лазерной сварки приведена на рис. 4.17. При плотностях тока ≈ 104 Вт/мм2 в пятне нагрева начинается локальное испарение металла. В расплавленном металле 2 образуется полость 3. Давление паров испаряющегося металла заготовок 1 не дает полости захлопнуться под действием гидростатических сил расплава. При соответствующей скорости перемещения (Vсв) лазерного луча 4 образовавшаяся полость приобретает динамическую устойчивость и движется вместе с лучом. Перед полостью происходит плавление металла, а позади нее – затвердевание.
При наличии полости, излучение поглощается не только поверхностью металла заготовок, но и в его глубине. После прохождения луча, полость заполняется жидким металлом и образуется узкий сварной шов 5, глубина которого значительно больше его ширины.
Рис. 4.17. Схема лазерной сварки: 1 – заготовки; 2 – расплавленный металл; 3 – полость; 4 – лазерный луч; 5 - сварной шов; Vсв - скорость перемещения лазерного луча.
Сварку малых толщин осуществляют в (непрерывном режиме шовная сварка) или в импульсном режиме (шовная или точечная сварка) с концентрацией энергии в одной точке (острая фокусировка излучения). При плотности мощности в зоне сварки 103…104 Вт/мм2 происходит только плавление металла без существенного его испарения.
Сварку с глубоким проплавлением можно осуществлять при плотностях мощности излучения более 105 Вт/мм2.
Лазерную сварку ведут с использованием вспомогательного газа (гелия или аргона), подаваемого в зону сварки через сопло под давлением. Если не использовать вспомогательный газ, то над зоной сварки образуется стационарное облако ионизированных паров испаренного металла, которой закроет поверхности заготовок от прямого действия луча. Кроме того, продувка вспомогательным газом защищает оптическую систему фокусировки от паров и брызг металла, а металл заготовок от окисления.
Преимущества. Лазерная сварка позволяет:
– соединять разнородные металлы при толщине заготовок от 0,5 до 10 мм и скорости сварки до 50 м/мин.
– обеспечивать небольшое тепловое влияние на около шовную зону и малые деформации готового изделия.
– легко автоматизировать процесс сварки.
– сваривать труднодоступные места и получать криволинейные сварные швы.
Недостатки:
– сложность оборудования
Применение:
– сварка малых толщин в электронной и радиотехнической промышленности (для сварки проводов, элементов микросхем, при ремонте вакуумных приборов и т.д.);
– сварка с глубоким проплавлением при производстве корпусных деталей, валов (в том числе карданных), осей, для сварки труб, арматурных конструкций и т.д.
– резка заготовок со сложным контуром из листовых материалов, при обработке трехмерных конструкций (резка труб, профилей …), точного раскроя листового материала (стальных листов толщиной до 25 мм), разрезания нетеплопроводных или хрупких материалов (керамик).
Сфокусированным лазерным лучом можно разрезать практически любые материалы.
Лазерная резка позволяет получать узкий и точный рез с минимальной з.т.в. Отсутствие механического воздействия на материал позволяет разрезать легкодеформируемые и нежесткие заготовки.
Дата добавления: 2020-12-22; просмотров: 64; Мы поможем в написании вашей работы! |
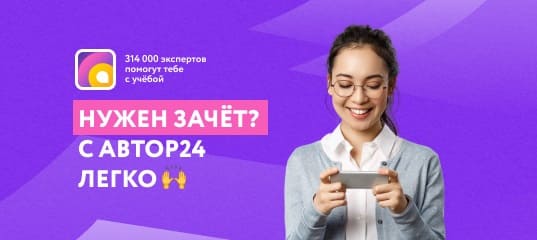
Мы поможем в написании ваших работ!