Безопасная эксплуатация автоклавов
Производство силикатного кирпича
Силикатный кирпич представляет собой искусственный безобжиговый стеновой строительный материал, изготовленный прессованием из смеси кварцевого песка и извести с последующим твердением в автоклаве.
Кварцевый песок в производстве силикатных изделий применяют немолотый или в виде смеси немолотого и тонкомолотого. Наиболее желательны кварцевые пески с зернами размером от 0,2 до 2 мм. Допускается содержание глинистых примесей не более 10%, при большем содержании увеличивается водопоглащение, снижается морозостойкость и пористость. Ограничивается содержание органических примесей. Содержание сернистых примесей допускается не более 1%, так как они могут вызвать вспучивание и понизить прочность изделий.
Состав известково-песчаной смеси для приготовления силикатного кирпича следующий: 92-95% оксида кремния, 5-8% воздушной извести и примерно 7% воды.
Технологический процесс производства силикатного кирпича включает следующие операции:
1) добычу и подачу песка и извести;
2) обжиг извести;
3) дробление и помол извести в шаровой мельнице;
4) приготовление известково-песчаной смеси;
5) прессование кирпича;
6) запаривание кирпича-сырца в автоклаве.
Производство силикатного кирпича ведут двумя спрособами барабанным и силосным (рис. 3.19), отличающимися приготовлением известково-песчаной смеси.
При барабанном способе (рис. 3.18) песок и тонкомолотая негашеная известь, получаемая измельчением в шаровой мельнице комовой извести, поступают в отдельные бункера над гасильным барабаном. Из бункеров песок, дозированный по объему, а известь по массе, периодически загружаются в гасильный барабан. Последний герметически закрывают и в течение 3-5 минут производят перемешивание сухих материалов. Затем при подаче острого пара под давлением 0,15-0,2 МПа происходит гашение извести при непрерывно вращающемся барабане. Процесс гашения извести длится до 40 минут.
|
|
|
При силосном способе (рис. 8.2.2.) предварительно перемешан
ную и увлажненную массу направляют для гашения в силосы. Гашение в силосах происходит 7-12 часов. Этот способ наиболее распространен.
В последнее время при строительстве заводов силикатного кирпича вместо силосов в технологическую схему стали вводить реакторы непрерывного действия, позволяющие организовать производство по непрерывно-поточной схеме.
|
|
Хорошо гашеную в барабане или силосе известково-песчаную массу подают в лопастной смеситель или на бегуны для дополнительного увлажнения (6-7%) и перемешивания и далее - на прессование. Прессование производят на механических прессах под давлением до 15-20 МПа, но не более 37 МПа, обеспечивающим получение плотного и прочного кирпича. После прессования прочность кирпича-сырца должна быть не ниже 0,3 МПа. Прессование (формование) производят чаще всего на трехпозиционных полуавтоматических револьверных прессах. В одной из позиций производится наполнение двух форм известково-песчаной смесью, во второй – прессование двух кирпичей, в третьей – их выталкивание.
Рис. 3.19. Технологическая схема производства силикатного кирпича по силосному способу:1 – вагонетка ; 2 - бункер песка; 3 - ленточный питатель; 4 - грохот; 5 - мешалка; 6 - плужковый сбрасыватель; 7 - силос непрерывного действия; 8 - тарельчатый питатель; 9 - пластинчатый транспортер для извести; 10 - шнековые питатели; 11 - двухкамерная мельница; 12 - шнек; 13-пресс; 14 -автомат-укладчик; 15 - запарочная вагонетка; 16 - электропередаточная тележка; 17 - реечный закатчик; 18 - проходной автоклав
|
|
Отпрессованные изделия укладывают на вагонетки автоматом-укладчиком и направляют в автоклав. Каждый автоклав вмещает 12-13 тыс. кирпичей.
Процесс запаривания, состоящий из загрузки вагонеток, закрытия крышек, выпуска пара, подъема давления 0,8…1,6 МПа, выпуска пара, открытия крышек и выпуска кирпича, продолжается 10…14 часов. После выгрузки из автоклава кирпичи укладывают в штабеля или грузят в вагоны и автомашины.
Силикатный кирпич выпускают семи марок по прочности (в кгс/см2) на сжатие: М 300, 250, 150, 125, 100, 75; по морозостойкости: F50, 35, 25, 15; плотность силикатного кирпича – 1800-2100 кг/см3 (несколько больше керамического).
Применяют силикатный кирпич там же, где керамический, но с некоторыми ограничениями. Нельзя использовать его для кладки фундаментов и цоколей, так как он менее водостоек, чем керамический, а также для кладки печей и дымовых труб, так как он менее термостоек.
По технико-экономическим показателям силикатный кирпич превосходит керамический, его себестоимость ниже на 25-35%.
Безопасная эксплуатация автоклавов
Автоклавы применяют для тепловлажностной обработки строительных материалов и конструкций. Характерными авариями при их эксплуатации являются отрыв запирающих крышек при их неудовлетворительном креплении, впуск пара в автоклав при открытых крышках, взрыв автоклава при превышении критического давления.
|
|
Для предотвращения этих аварий автоклавы оборудуют системой блокировок, исключающей впуск пара в автоклав с не полностью закрепленными крышками, а также открывания крышек при наличии давления пара в автоклаве. Имеется устройство программного регулирования режима автоклавной обработки, манометры и предохранительные клапаны.
Схема автоматической блокировки при открывании крышки автоклава ручным приводом представлена на рис. 3.20. Для контроля давления пара в автоклаве 1 используется манометр 3, а предохранительный клапан 2 служит для выпуска излишнего пара и сброса давления в аварийных случаях. Во время загрузки и выгрузки автоклава вентили впуска пара перекрываются и запираются на замок, а при ремонте автоклава на паропроводах устанавливаются заглушки.
Устройство, приведенное на рис. 3.20, не позволяет открыть крышку автоклава при наличии в нем давления пара. Из автоклава через конденсационный сосуд 8 пар поступает в реле давления 7 и, прогибая резиновую мембрану 5, приводит в движение шток 6. Последний упирается в переключатель 4 и разрывает электрическую цепь электромагнитного замка 9. В этом случае электромагнитный замок отпускает сердечник 10, который под действием пружины 11 замыкает фиксатор 12. Последний не позволяет вращать ручку 13 червячной лебедки 14 и тем самым препятствует повороту крышки 15 автоклава в затворе.
Если давление пара в автоклаве снято, то электрическая сеть замка 9 замыкается переключателем 4, сердечник 10 втягивается в электромагнит и размыкает фиксатор 12. Этим обеспечивается возможность вращения ручки 13 для открывания крышки автоклава. Имеются и другие схемы блокировки автоклава. При эксплуатации автоклавов применяют систему, при которой рабочий - пропарщик во время пропарки изделий запирает в своем шкафу жетон с номером автоклава и номером его крышки. Окончив пропарку и сняв давление в автоклаве, пропарщик передает жетон загрузчику-выгрузчику, который имеет право открывать и закрывать крышку автоклава. Закончив работу, лицо, обслуживающее автоклав, закрывает его крышку, и жетон под расписку возвращает пропарщику. Такая жетонная система позволяет избежать нарушение правил безопасного обслуживания автоклава и предотвратить несчастные случаи.
Контрольно-измерительные приборы. Каждый сосуд снабжается манометрами прямого действия. Он устанавливается на штуцере сосуда. Манометры имеют класс точности 1,5 при рабочем давлении 12 атм. Шкала манометра 25 атм. К корпусу манометра прикреплена стальная пластина, окрашенная в красный цвет и плотно прилегающая к стеклу манометра. Он устанавливается так, что его показания четко видны обслуживающему персоналу. Диаметр корпуса манометра равен 100 мм.
Разрешение на пуск автоклава в работу дает мастер после личной проверки готовности автоклава. Перед пуском пара в автоклав нужно закрыть крышку на замок и проверить герметичность прокладки путем подачи пара в кольцевой паз под уплотнительной прокладкой. Запрещается открывать паровпускные вентили и задвижки быстро, рывками.
В период подъема давления постоянно следить за показаниями контрольно-измерительных приборов. При подъеме давления пара в автоклаве рабочие не должны находиться в приямке перед автоклавом. После окончания подъема давления пара в автоклаве проверить исправность предохранительного клапана путем его принудительного открывания и результаты проверки записать в ведомость учета работы автоклавов. При угрозе аварии или несчастного случая отключить подвод пара и снизить давление в автоклаве. Запрещается принимать и сдавать смену при пуске автоклава в работу.
Проверка манометров с их опломбированием или клеймением проводиться не реже одного раза в 12 месяцев. Рабочие манометры, находящиеся в эксплуатации, проверяются не реже 1 раза в шесть месяцев контрольным манометром с записью результатов в журнал контрольных проверок. Трубные соединительные линии к приборам теплотехнических измерений во время эксплуатации должны систематически продуваться. Манометры не допускаются к применению в случаях когда:
- отсутствует пломба или клеймо;
- просроченный срок проверки;
- стрелка манометра при его выключении не возвращается на нулевую отметку шкалы;
- разбито стекло или имеются другие повреждения, которые могут отразиться на правильности его показаний.
Автоклавы также снабжены приборами для контроля скорости и равномерности прогрева.
Аварийная остановка автоклава. Автоклав должен быть выведен из эксплуатации в следующих аварийных случаях:
1) при повышении давления выше установленного;
2) при возникновении разности температур по верхней и нижней образующей корпуса, превышающей 45°
3) при защемлении опор;
4) при неисправности средств сигнализации, блокировочных устройств, предохранительных клапанов, манометров;
5) при обнаружении в основных элементах автоклава трещин пропуска пара и конденсата в соединениях, разрыве прокладок;
6) если не сработало сигнально-блокировочное устройство;
7) при возникновении пожара, угрожающего находящимся под давлением автоклавам.
Регистрация и техническое освидетельствование автоклавов. Автоклавы до пуска их в работу должны быть зарегистрированы в органах Ростехнадзора России. Регистрация производится на основании письменного заявления владельца автоклава. Для регистрации должны быть представлены:
- паспорт автоклава;
- удостоверение о качестве монтажа;
- схема включения сосуда с указаниями источника давления, параметров его рабочей среды, контрольно-измерительных приборов, предохранительных и блокирующих устройств, средств автоматики. Схема должна быть утверждена руководством организации;
- паспорт предохранительного устройства с расчетом его пропускной способности.
Орган Ростехнадзора обязан в течение пяти дней рассмотреть предоставленную информацию. При соответствии требований в паспорте ставит штамп о регистрации, пломбирует документы и возвращает их владельцу.
Автоклавы должны подвергаться техническому освидетельствованию после монтажа, до пуска в работу, периодически в процессе эксплуатации и в необходимых случаях - внеочередному освидетельствованию. Наружный и внутренний осмотры 1 раз в год, гидравлические испытания 1 раз в 8 лет. Цель наружного и внутреннего осмотров - при первичном освидетельствовании проверить, что сосуд установлен и оборудован в соответствии с Правилами и представленными при регистрации документами, а также что сосуд и его элементы не имеют повреждений.
Дата добавления: 2020-12-22; просмотров: 119; Мы поможем в написании вашей работы! |
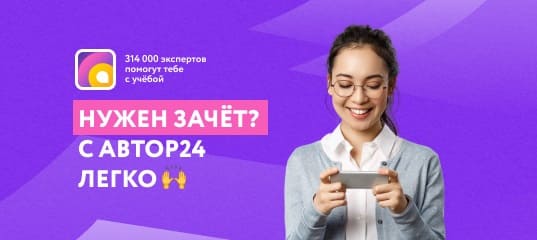
Мы поможем в написании ваших работ!