Производство нефтяных битумов
Для производства нефтяных битумов используют следующие процессы:
- концентрирование тяжелых нефтяных остатков (ТНО) под вакуумом (остаточные битумы);
- деасфальтизация тяжелых нефтяных остатков избирательными растворителями (осажденные битумы);
- окисление нефтяных остатков кислородом воздуха при высокой температуре (получение окисленных битумов);
- компаундирование остаточных битумов с окисленными битумами или с асфальтами процесса пропан–бутановой деасфальтизации (компаундированные битумы).
Обычным сырьем вакуумной перегонки является остаток атмосферной перегонки нефти – мазут.
Для получения остаточных битумов может быть использовано только сырье с большим содержанием асфальто–смолистых веществ, которые в достаточном количестве присутствуют в тяжелых высокосмолистых сернистых нефтях. Главным в процессе вакуумной перегонки является извлечение дистиллятных фракций для выработки моторных топлив (начальный этап). Побочный продукт этого процесса – гудрон соответствует требованиям на сырье в производстве битумов.
Вакуумная перегонка мазута обеспечивает снижение содержания твердых парафинов и парафино-нафтеновых углеводородов.
Количество нефтей, подходящих для производства остаточных битумов, в России ограничено, чем и объясняется тот факт, что в России до настоящего времени почти весь объем потребляемого битума вырабатывается в основном с использованием процесса окисления нефтяных остатков. За рубежом же, наоборот, основную массу вырабатываемого битума составляют остаточные битумы.
|
|
Основным аппаратом установок непрерывного действия для производства битума является либо трубчатый реактор, либо окислительная колонна. Окислительные колонны предпочтительны для производства дорожных битумов, трубчатые реактора – в производстве строительных битумов. Отдельные установки имеют в своем составе оба аппарата.
Комбинированное применение на одной битумной установке реакторов двух типов позволяет одновременно получать разные марки битумов и более полно использовать тепло реакции и отходящих потоков.
На некоторых НПЗ эксплуатируются установки, в которых применено последовательное комбинирование реакторов: сырье сначала окисляется в реакторе колонного типа, затем частично окисленный битум доокисляется в реакторе змеевикового типа
Наиболее экономичным окислительным аппаратом при производстве широкого ассортимента битумов является пустотелая колонна (обычно высотой 15–25 м и диаметром 34 м). Принципиальная схема окисления в колонне с утилизацией тепла представлена на рисунке 6.
|
|
Сырье закачивается в колонну под уровень жидкости. Внизу колонны через маточник диспергируется воздух. Битум откачивается с низа колонны, а отработанные газы выводятся с верха колонны. Холодное сырье подогревается за счет тепла реакции окисления.
При получении глубокоокисленных битумов дополнительный съем тепла осуществляется впрыском воды в газовое пространство или через маточник вместе с воздухом.
.
Рисунок 6. Принципиальная схема окисления в колонне с утилизацией тепла
1 – кипятильник; 3 – уравнительная емкость; 4 - окислительная колонна; 5 – парогенератор; 6-сепаратор с циклоном; 7 – огнепреградитель; 8 – печь дожига.
.
На рисунке 7 приведена схема непрерывно действующей битумной установки без циркуляции продукта.
Несколько вертикальных кубов расположено так, что сырье и частично окисленный продукт самотеком перетекают из одного куба в другой. Кубы снабжены маточниками для подачи воздуха. Сырье и частично окисленный продукт окисляются во всех кубах одновременно. Хотя пустотелая колонна и является наиболее экономичным окислительным аппаратом при производстве битумов, однако и она имеет существенный недостаток – невысокая степень использования кислорода воздуха и необходимость постоянного контролирования уровня сырья в колонне.
|
|
Для устранения этих недостатков было предложено проводить окисление в одной полностью заполненной сырьем колонне с перетеканием его во вторую колонну (рис. 8).
Рисунок 7. Принципиальная технологическая схема непрерывной битумной установки с кубами-окислителями:
1 – печь; 2 – вытяжная труба; 3 – конденсаторы смешения; 4 – кубы - окислители; 5 – насосы; 6 – холодильник; С – сконденсированные продукты; Р – раздаточник
На этом рисунке показана колонна с квенчинг-секцией, позволяющая поддерживать более высокую температуру процесса, высокую степень использования кислорода воздуха, а также устранить закоксовывание стенок зоны реакции окисления.
а б
Рисунок 8. Принципиальная схема окисления:
а – в заполненной колонне с отдельной секцией сепарации; б – окислительная колонна с квенчинг-секцией:
1 – насосы; 2 – первая колонна (зона реакции); 3 – вторая
колонна (зона реакции); 4 – секция квенчинга и сепарация; 5 – секция окисления; 6 – переток с регулирующим клапаном и гидравлическим затвором; 7 – разделительная тарелка
|
|
Процесс окисления с квенчинг-секцией на существующем оборудовании позволяет получить положительный эффект, но приводит к дополнительным затратам на перекачивание рециркулята. Для получения строительных и дорожных битумов было сконструировано разделение секции реакции и секции сепарации. Сырье попадает сначала в секцию сепарации, оттуда вместе с рециркулятом направляется в секцию реакции по перетоку. Благодаря разделительному устройству, реорганизованному движению потоков жидкой и газовой фаз и квенчингу сырьем поддерживаются разные температуры по высоте жидкой фазы в колонне: в секции реакции – относительно высокая, обеспечивающая полное использование кислорода воздуха; в секции сепарации – низкая, исключающая закоксовывание газового пространства.
Технико-экономические показатели процесса окисления с квенчинг-секцией превосходят соответствующие показатели, характерные для других окислительных аппаратов.
Производство окисленных битумов в кубах с механическим перемешиванием, в частности с применением турбинных мешалок, не нашло широкого применения в промышленности. Особенностью ее окислительного куба является наличие турбинной мешалки с плоскими лопастями и четырех вертикальных ребер. Исследование процесса окисления на данной установке показало возможность интенсификации процесса за счет увеличения поверхности контакта фаз, однако применение механического перемешивания связано с дополнительными энергетическими затратами, частыми поломками и выходом из строя мешалки.
Производство нефтяных пеков
Нефтяные пеки являются важным связующим компонентом электродных и анодных масс, обеспечивающим текучесть, пластичность, однородность при смешении с коксом-наполнителем и прочность, электросопротивление, реакционную способность при последующих операциях обжига изделий. Поэтому при изучении возможности производства нефтяных пеков были опробованы различные технологические приемы переработки нефтяного сырья: вакуумная переработка, термополиконденсация, окисление.
Получение нефтяного пека вакуумной перегонкой.
В качестве сырья для получения нефтяных пеков наиболее желательны остаточные нефтепродукты, обладающие высокой плотностью, ароматичностью и малым содержанием серы. Однако из-за высокой потребности в сырье такого качества для коксования ресурсы малосернистых нефтяных остатков являются ограниченными. Поэтому возникает потребность вовлечения в переработку сернистых дистиллятных крекинг-остатков, являющихся побочным продуктом процесса получения сырья для технического углерода.
Рисунок 9. Технологическая схема процесса получения пека вакуумным концентрированием
1,2 – печи; 3 – реакционная камера; 4 – испаритель высокого давления; 5 –колонна; 6 – испаритель низкого давления; 7 – вакуумная колонна;
Потоки: I – сырье; II – бензин; III – легкий газойль; IV – газы; V – тяжелый газойль; VI –пек; VII – пар.
Вакуумная перегонка крекинг-остатка при температуре 385-390°С, остаточном давлении 0,011-0,013МПа позволяет получать нефтяные пеки с температурой размягчения 82-90°С, выходом летучих 60-64%. Эти пеки имеют низкую плотность и содержат незначительное количество α-фракции (не более 8-10%). Низкая плотность и недостаточное количество α-фракции не позволяет таким пекам на равных конкурировать с каменноугольными пеками, даже с учетом экологичности данного вида продукции.
Получение нефтяных пеков методом термополиконденсации.
Термополиконденсация позволяет получать пеки с температурой размягчения 65-100°С, плотностью 1250-1300 кг/м3 при следующих условиях процесса: температура 420-430°С, продолжительность 3-5 часов. Увеличение температуры процесса до 460-510°С при снижении продолжительности процесса до 1-5 мин., и последующая выдержка в реакторе при 380-440°С в течении 1-3 часов позволяют также получить нефтяной пек для алюминиевой промышленности.
Нефтяные пеки, полученные термополиконденсацией смолы пиролиза в двух последовательно работающих реакторах и имеющие температуру размягчения 65 и 100°С соответственно, могут быть в последующем смешаны в различных пропорциях.
Рисунок 10. Технологическая схема процесса получения нефтяного волокнообразующего пека
1 - блок очистки ТСП; 2, 9 - трубчатая печь; 3 - смеситель; 4 - проточный реактор; 5 - реакционный сепаратор; 6 - вакуумная колонна; 7 - блок ультразвуковой обработки; 8 - атмосферная колонна.
Потоки: I - очищенная смола пиролиза; II - термообработанная смола пиролиза; III - реакционная масса; IV - перегретый водяной пар; V - низкоплавкий связующий пек; VI - расплав высокоплавкого пека; VII - высокоплавкий волокнообразующий пек; VIII, IX - отгон низкомолекулярных продуктов; X - вода; XI - тяжелый газойль; XII - легкий газойль; XIII - бензин; XIV - углеводородные газы.
Список литературы
1. Вержичинская С.В., Дигуров Н.Г., Синицин С.А. Химия и технология нефти и газа: учебное пособие. - М.: ФОРУМ, 2015. – 498 с.
2. Капустин В.М., Рудин М.Г. Химия и технология переработки нефти – М.: Химия, 2013. – 496 с.
3. Мановян Е.Г. Технология переработки природных энергоносителей. М.: Наука,- 2016, 435
4. Ахметов С.А. и др. Технология, экономика и автоматизация процессов переработки нефти и газа: учебное пособие - М.: Химия, 2005.
5. Воронкова Л.Б. Ведение технологического процесса на установках I и II категорий. В 2 ч. Ч. 1.: учеб. для студ. учреждений сред. проф. образования / Л.Б. Ворогкова, М.А. Руфанова. – М.: Академия, 2017. – 224 с.
6. Воронкова Л.Б. Ведение технологического процесса на установках I и II категорий. В 2 ч. Ч. 2.: учеб. для студ. учреждений сред. проф. образования / Л.Б. Ворогкова, М.А. Руфанова. – М.: Академия, 2017. – 288 с.
7. Ахметов С.А. Технология глубокой переработки нефти и газа. Уфа: «ГИЛЕМ», 2012. – 671с.;
8. Ахметов С. А. и др. Технология и оборудование процессов переработки нефти и газа: Учебное пособие / С. А. Ахметов, Т. П. Сериков, И. Р. Кузеев, М. И. Баязитов; Под ред С. А. Ахметова. – СПб.: Недра, 2016. – 868 с.
Дата добавления: 2020-12-22; просмотров: 160; Мы поможем в написании вашей работы! |
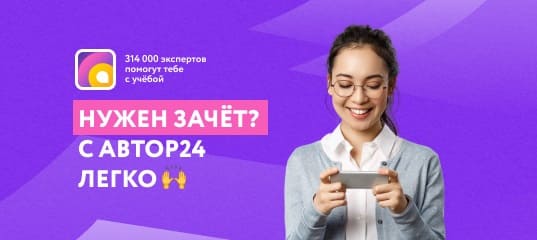
Мы поможем в написании ваших работ!