Определения габаритов, установленных ГОСТ 9238 - 83, и указать их системы для подвижного состава. Перечислить типы габаритов вагонов.
Содержание
1. Классификация и основные элементы конструкции вагонов.
2. Основные части вагона.
3. Технико-экономические параметры вагона.
4. Определения габаритов, установленных ГОСТ 9238 - 83, и указать их системы для подвижного состава. Перечислить типы габаритов вагонов.
5. Устройство колесной пары.
6. Ось
7. Назначение букс.
8. Подшипники
9. Назначение, тип и классификация рессорного подвешивания. Устройство торсионных, кольцевых и пневматических рессор.
10. Назначение тип и классификация тележек. Новые конструкции тележек пассажирских вагонов
11. Конструкция автосцепного устройства пассажирского межобластного вагона
![]() |
Классификация и основные элементы конструкции вагонов.
Классификация вагонов.
Вагоном называется единица железнодорожного подвижного состава, предназначенная для перевозки пассажиров или грузов.
Вагонный парк характеризуется сложностью и многообразием типов и конструкций. Это вызвано необходимостью удовлетворения различных требований при перевозках: защиты ряда грузов от атмосферных воздействий, сохранения качества скоропортящихся грузов, обеспечения комфорта пассажирам и др.
Вагоны классифицируются по четырем основным признакам: назначению, месту эксплуатации, осности и ширине колеи.
По назначению вагоны разделяются на две основные группы: пассажирские и грузовые.
Парк пассажирских вагонов составляют несамоходные вагоны, перемещаемые локомотивами, и самоходные, имеющие свою энергетическую установку или получающие энергию от контактной сети.
|
|
К несамоходным пассажирским вагонам относятся вагоны дальнего следования, межобластного и пригородного сообщения, вагоны-рестораны, багажные, почтовые, почтово-багажные и специальные.
Вагоны межобластного сообщения используют для перевозки пассажиров на расстояние до 700 км. Эти вагоны строятся открытого типа или купейными и оборудуются мягкими креслами для сидения.
Независимо от назначения и типа все вагоны состоят из четырех основных элементов (узлов):
- кузова 1,
- ходовых частей 4,
- ударно-тяговых устройств 2,
-
тормозного оборудования 3 .
Основные части и планировка вагона
Все пассажирские вагоны различных типов имеют общие основные элементы: кузов с рамой, ходовые части, ударно-тяговые приборы и тормозное оборудование. Основные части и общий вид пассажирского вагона показаны на рис. 1.4.
Рис. 1.4. Общий вид пассажирского (купейного) вагона:
1 — дефлектор; 2 — кузов с термоизоляцией; 3 — суфле переходных площадок;
4 — буфера; 5 — аккумуляторная батарея; 6 — ящики для белья; 7— компрессорный агрегат установки кондиционирования воздуха; 8 — конденсаторный агрегат; 9 — приборный ящик низкого напряжения; 10 — выпрямитель; 11 — трансформатор; 12 — подвагонный генератор мощностью 32 кВт; 13 — подвагонный ящик приборов высокого напряжения; 14 — привод генератора; 15 — тележка; 16 — автосцепка; 17 — междувагонное высоковольтное соединение
|
|
Все оборудование вагона подразделяется на механическое, санитарно-техническое, низковольтное электрическое (работающее на напряжении 50 или 110 В постоянного тока), высоковольтное электрическое (работающее на напряжении свыше 1000 В). По месту расположения оно в свою очередь, подразделяется на подвагонное, внугривагонное и расположенное в крышевом пространстве. Места расположения оборудования на вагонах разного типа могут различаться, это зависит от планировки вагона и его габаритов.
Все механическое оборудование находится снаружи вагона или под вагоном (тележки, все основные детали тормоза, переходные площадки и т.п.).
К низковольтному подвагонному оборудованию относятся генератор, аккумуляторная батарея, ящик с аппаратурой, умформер (до 1990 г.). К внутривагонному низковольтному оборудованию относятся
распределительный шкаф, светильники, узлы кондиционирования воздуха и др.
Высоковольтное электрическое оборудование размещено как снаружи вагона (высоковольтные междувагонные соединения, высоковольтный подвагонный ящик), так и внутри вагона в котле водяного отопления.
К санитарно-техническому оборудованию, расположенному в основном внутри вагона, относятся системы обеспечения жизнедеятельности пассажиров и проводников: холодного и горячего водоснабжения, отопления, кондиционирования воздуха. Узлы системы кондиционирования воздуха частично находятся под вагоном (компрессорный и конденсаторный агрегаты, ресивер), частично в крышевом пространстве (калориферы, воздухоохладители).
Планировка вагонов (некупейного, межобластного сообщения, купейного и габарита РИЦ) показана на рис. 1.5.
|
|
Рис. 1.5. Планировка вагонов: а — некупейного; б — межобластного сообщения; в — купейного; г — габарита РИЦ; 1 — ящик для угля; 2 — туалет; 3 — распределительный шкаф; 4 — охладитель питьевой воды; 5 — служебное отделение; 6 — система пожарной сигнализации; 7 — купе отдыха; 8 — купе пассажирское (для купейного вагона) и пассажирское отделение для вагонов некупейного и международного сообщения; 9 — стоп-кран; 10— тамбур; 11 — мусорный ящик; 12 — огнетушитель; 13 — большой коридор; 14 — косой (малый) коридор; 15 — кипятильник; 16 — котел отопления; 17 — котельное отделение
|
|
Специфичными являются оборудование и планировка вагона-ресторана, в котором имеются четыре или пять холодильников в зависимости от серии вагона и тепловое оборудование кухни, работающее на твердом или жидком (дизельном) топливе. Проводников для вагона-ресторана не предусмотрено, поэтому наблюдает за всем оборудованием и управляет его работой бригада вагона-ресторана (директор и повара)..
Отдельно следует сказать о поставляемых в Россию из Германии купейных вагонах с кондиционированием воздуха постройки с 1993 г. На этих вагонах изменена система электрооборудования, выполнена новая планировка: уменьшено число мест, предусмотрено специальное купе для инвалидов с лифтовым подъемным устройством грузоподъемностью до 300 кг. Расположение оборудования на таких вагонах показано на рис. 1.6.
Рис. 1.6. Планировка пассажирского купейного вагона с кондиционированием воздуха постройки Германии (с 1993 г.):
1 — вызывная кнопка; 2 — розетка для радио; 3 — хвостовой сигнальный фонарь; 4 — вытяжной колпак (кухонная плита); 5 — статический дефлектор системы «Кукук»; 6 — вытяжной колпак (котел отопления); 7 — вытяжной колпак (кипятильник); 8 — аккумуляторный ящик, состоящий из двух частей; 9 — аккумуляторный ящик, состоящий из трех частей; 10 — ящик для белья; 11 — компрессор; 12 — конденсатор; 13 — AEV— аппаратный ящик для трансформатора; 14 — AEV — аппаратный ящик для выпрямителя; 15 — аппаратный ящик для климатоустановки; 16 — генератор 32 кВт; 17 — высоковольтный аппаратный ящик; 18 — ступенька откидная; 19 — ящик для угля; 20 — откидной фартук подножек; 21 — туалет; 22 — умывальник; 23 — распределительный шкаф; 24 — охладитель питьевой воды; 25 — место отбора питьевой воды; 26 — стол для радиоустановки; 27 — глухое окно; 28 — оконная штора; 29 — громкоговоритель; 30 — двухламповый светильник; 31 — откидной стол; 32 — устройство поворотно-подъемное для посадки и высадки инвалидов в креслах-колясках; 33 — ящик для инвентаря; 34 — ящик для дров; 35 — ящик для мусора; 36 — гидравлический агрегат; 37— душевая установка; 38 — аварийное окно; 40— витрина для проспектов; 41 — опускное окно; 42 — отпускной клапан; 43 — одноламповый светильник; 44 — откидное сиденье; 45 — холодильник; 46 — система пожарной сигнализации; 47 — огнетушитель; 48 — кипятильник; 49 — котел отопления; 50 — плитка с бойлером; 51 — электроплитка
Принципиально система электрооборудования и основные узлы (генератор, аккумуляторная батарея, приборы регулирования, защиты, сигнализации и др.) таких вагонов не отличаются от серийно поставляемых до 1993 г. купейных вагонов с кондиционированием воздуха. Имеются, однако, некоторые дополнения: установка электроплиты в котельном отделении, перенос низковольтных междувагонных электрических соединений (аварийных) из-под вагона внутрь переходных площадок и др. Купе для инвалидов оборудовано, помимо подъемника, туалетом со специальной раздвижной дверью, умывальником, душем с возможностью подъезда к умывальнику на коляске. Гидравлический подъемный агрегат состоит из электродвигателя мощностью 1,5 кВт, работающего на напряжении 110 В постоянного тока от вагонной аккумуляторной батареи; гидравлического насоса с ручным приводом производительностью 1,2 см3 за 1 оборот; запасного масляного бака емкостью 3 л со смотровым стеклом; двухходового гидравлического клапана для подъема платформы подъемного устройства; трехходового переключающего клапана с электрическим приводом для переключения левого или правого подъемного устройства. В состав поворотно-подъемного устройства входит также предохранительный клапан максимального давления, тормозной и возвратный клапаны и блокировка, не допускающая движения вагона при включенных поворотном или подъемном узлах, исключающая падение инвалида с платформы и непоследовательное движение узлов. Управление поворотно-подъемным устройством производится со специальной панели с кнопочными выключателями.
Опыт эксплуатации купейных вагонов с поворотно-подъемным устройством показывает, что основным требованием его безопасной эксплуатации является соблюдение точной последовательности операций по подъему и впуску инвалида в вагон и его выходу из вагона. Перед включением подъемного устройства предохранительные рычаги необходимо привести в исходное положение, ограждение платформы должно находиться в откинутом вверх положении. Область поворота устройства должна быть свободна.
При наличии любых неисправностей запрещается включать поворотно-подъемное устройство. В первую очередь нужно проверить наличие напряжения и величину тока двигателя гидравлического агрегата; функционирование переключающего и гидравлического клапанов; исправность подъемного устройства и гидросистемы, особенно на отсутствие утечки масла; состояние подводящих проводов и кнопочных выключателей; положение платформы, состояние смазки, отсутствие защемления шлангов.
Основные части вагона.
Кузов вагона предназначен для размещения пассажиров или грузов. Конструкция кузова зависит от типа вагона. Все кузова имеют устройства, необходимые для обеспечения сохранности перевозимого груза или комфорта пассажиров. У большинства нагонов основанием кузова является рама.
Кузов пассажирского вагона состоит из рамы, боковых и торцовых стен, пола, крыши, дверей, окон и соответствующего внутреннего оборудования (систем электрооборудования, отопления, вентиляции, освещения, водоснабжения, диванов для лежания или сидения, багажных полок и др.).
Кузова пассажирских, изотермических и некоторых специальных грузовых вагонов имеют теплоизоляцию для поддержания необходимого температурного режима.
Ходовые части служат опорой кузова и направляют движение вагона по рельсовому пути с необходимой плавностью хода. К ходовым частям относятся тележки, состоящие из колесных пар, букс, рессорного подвешивания, рам, надрессорных балок и др.
Ударно-тяговые устройства служат для сцепления вагонов между собой и с локомотивом, а также для передачи силы тяги от локомотива к вагонам и смягчения ударов, возникающих при сцеплении или изменениях режима движения. На вагонах железных дорог России и стран СНГ в качестве ударно-тяговых приборов применяют автосцепное устройство. Его размещают в консольных частях рамы вагона.
Тормозное оборудование предназначено для уменьшения скорости движения или остановки поезда, а также удержания его на месте. Тормоза бывают ручные и автоматические. Вагоны грузового и пассажирского парков оборудованы автоматическими тормозами, а часть вагонов — дополнительно и ручными. Автоматические тормоза обычно приводятся в действие с локомотива, а в случае необходимости из вагона (стоп-краном). При разрыве состава тормоза срабатывают автоматически, без участия человека. Тормозное оборудование установлено частично на раме кузова и частично на тележках вагона.
Технико-экономические параметры вагона.
Параметрами пассажирских вагонов являются тип планировки (определяется назначением вагона), осность, населенность, масса тары, масса экипировки (вода, уголь, съемное оборудование), линейные размеры и максимальная скорость движения. Для пассажирских вагонов определяют также массу тары, приходящуюся на одно место для пассажира, массу тары на единицу длины или площади горизонтальной проекции вагона, осевую нагрузку и др.
- Грузоподъемность Р — это наибольшая масса груза, допускаемая к перевозке в вагоне. Грузоподъемность определяет провозную способность железных дорог. Поэтому стремятся создавать вагоны с максимально возможной грузоподъемностью, увеличивая габаритные размеры, повышая осевую и погонную нагрузки. Для существенного повышения грузоподъемности увеличивают число осей в вагоне. Четырехосные грузовые вагоны строятся грузоподъемностью 68-71 т, а восьмиосные — 120-132 т.
- Осевая нагрузка — нагрузка от колесной пары на рельсы. Допускаемая осевая нагрузка определяется конструкцией и прочностью верхнего строения пути и скоростью движения поездов. В настоящее время она ограничена величиной 230 кН (23,5 тс) для грузовых вагонов и 177 кН (18 тс) — для пассажирских. Ставится вопрос о дальнейшем повышении допускаемой осевой нагрузки для грузовых вагонов до 245 кН (25 тс) и более, что связано с необходимостью увеличения мощности пути по всей сети железных дорог.
- Погонная нагрузка — нагрузка от вагона на 1 м пути. Допускаемая погонная нагрузка определяется прочностью мостов и в настоящее время ограничена величиной 103 кН/м (10,5 тс/м). Четырехосные грузовые вагоны реализуют погонную нагрузку 65-72 кН/м, восьмиосные — 80-85 кН/м. Увеличение погонной нагрузки — наиболее эффективный путь повышения грузоподъемности вагона.
- Масса тары Т — собственная масса порожнего вагона. Сумма грузоподъемности и массы тары дает массу вагона брутто. Конструкция вагона должна иметь минимальную массу и необходимую прочность. Поэтому снижение массы тары - важнейшая задача вагоностроения. Ее решение позволяет уменьшить эксплуатационные затраты, связанные с передвижением тары вагонов, снизить расход материалов на изготовление вагонов и повысить грузоподъемность вагона в пределах допускаемой осевой нагрузки.
Снижения массы тары при одновременном повышении грузоподъемности и надежности вагонов, можно достигнуть путем уменьшения динамических сил, действующих на вагон за счет совершенствования ходовых частей и автосцепного устройства; выбором целесообразных конструктивных форм нагонов и их элементов; применением более прогрессивных материалов для
элементов вагонов (низколегированных сталей, сталей повышенной прочности и коррозийной стойкости, высокопрочных алюминиевых сплавов и пластмасс); совершенствованием технологии изготовления и ремонта вагонов; совершенствованием методов расчета и испытаний нагонов.
- Эффективность снижения массы грузового вагона оценивается техническим коэффициентом тары Кт = P/T
Этот коэффициент характеризует качество конструкции вагона: чем меньше Кт, тем меньше собственной массы вагона приходится на каждую тонну транспортируемого груза, а следовательно, меньше затраты на перевозку самого вагона и вагон экономически выгоднее. Поэтому при проектировании новых вагонов необходимо стремиться к снижению Кт. Для пассажирских вагонов коэффициент тары определяется как отношение массы тары к населенности вагона. - Удельный объем кузова вагона представляет собой отношение полного объема кузова V к его грузоподъемности Р. Для платформ определяется удельная площадь F как отношение площади пола к грузоподъемности. От величин удельных объемов и удельных площадей зависит использование объема и грузоподъемности вагона, а следовательно, себестоимость перевозок и приведенные затраты народного хозяйства. Поэтому при проектировании вагонов определяют оптимальные значения Vy и Fу.
- Пассажирские и грузовые вагоны характеризуются также линейными размерами (длиной, шириной, высотой и базой). Общая длина вагона 2Loб определяется расстоянием между осями сцепленных автосцепок. Длина рамы 2L вагона — расстояние между торцами концевых балок рамы, база 2l вагона — расстояние между центрами пятников кузова. Длина, ширина и высота кузова определяются заданной вместимостью и габаритом подвижного состава. Для достижения возможно большей погонной нагрузки ширину и высоту кузова обычно принимают максимальными для заданного габарита подвижного состава.
Определения габаритов, установленных ГОСТ 9238 - 83, и указать их системы для подвижного состава. Перечислить типы габаритов вагонов.
![]() |
Подвижной состав, сооружения и устройства проектируются с учетом требований соответствующих габаритов.
Одним из главных условий безопасности движения локомотивов, вагонов и иного подвижного состава является предупреждение возможности их соприкосновения со стационарными сооружениями, расположенными вблизи железнодорожного пути, или с подвижным составом, находящимся на соседнем пути. Поэтому стационарные сооружения должны располагаться на определенном расстоянии от железнодорожного пути, а подвижной состав — иметь ограниченное поперечное очертание.
Таким образом, получаются два контура: контур, ограничивающий наименьшие допускаемые размеры приближения строения и путевых устройств к оси пути — габарит приближения строений, и контур, ограничивающий наибольшие допускаемые размеры поперечного сечения подвижного состава — габарит подвижного состава. Второй контур расположен внутри первого и между ними имеется пространство (зазоры), за исключением опорных поверхностей колес, где оба контура совпадают.
ГОСТ 9238-83 устанавливает следующие определения для двух рассматриваемых разновидностей габарита.
Габаритом приближения строений железных дорог называют предельное поперечное (перпендикулярное оси пути) очертание, внутрь которого помимо подвижного состава не должны заходить никакие части сооружений и устройств, а также лежащие около пути материалы, запасные части и оборудование, за исключением частей устройств, предназначенных для непосредственного взаимодействия с подвижным составом (контактных проводов с деталями крепления, хоботов гидравлических колонок при наборе воды и др.) при условии, что положение этих устройств во внутригабаритном пространстве увязано с частями подвижного состава, с которыми они могут соприкасаться, и что они не могут вызвать соприкосновения с другими элементами подвижного состава.
Габаритом подвижного состава железных дорог называется предельное поперечное (перпендикулярное оси пути) очертание, в котором, не выходя наружу, должен помещаться установленный на прямом горизонтальном пути (при наиболее неблагоприятном положении в колее и отсутствии боковых наклонений на рессорах и динамических колебаний) как в порожнем, так и в нагруженном состоянии не только новый подвижной состав, но и подвижной состав, имеющий максимальные нормируемые износы.
Пространство между габаритами приближения строений и подвижного состава (а для двухпутных линий также между габаритами смежных подвижных составов) обеспечивает безопасные смещения подвижного состава и погруженных на нем грузов, которые возникают при его движении, а также обусловленные допустимыми отклонениями элементов пути.
Все смещения вагона могут быть сведены к следующим четырем группам:
а) вызываемые возможными отклонениями в состоянии пути — уширение колеи, упругое отжатие рельсов, перекосы и износы шпал и подкладок, упругие осадки шпал и балласта и т.п.;
б) динамические колебания вагона, возникающие при его движении;
в) обусловленные зазорами и износами ходовых частей и прогибы и осадки рессорного подвешивания от статической нагрузки;
г) выносы частей вагона в кривых. При габаритных расчетах учитывают только смещения, возможные при отклонениях, допускаемых нормами содержания вагона и пути. Поскольку размеры габарита приближения строений установлены для прямых участков пути, а в кривых имеются дополнительные уширения, выносы вагона в кривых учитывают только в размерах, превышающих имеющиеся уширения.
В зависимости от способов учета вышеуказанных смещений вагонов различают две системы габаритов подвижного состава: строительную и эксплуатационную.
Если пространство между габаритами приближения строений и подвижного состава предназначено для первых трех групп смещений (а, б и в), то устанавливаемый при такой системе учета смещений габарит подвижного состава называется строительным. Если вышеуказанное пространство предусмотрено для первых двух групп смещений (а и б), то получаемый при этом габарит называется эксплуатационным габаритом подвижного состава. Более точно данный габарит называют эксплуатационно-статическим, поскольку при этом учитывается положение подвижного состава в покое, в отличие от эксплуатационно-динамического, определяющего положение подвижного состава в движении. Последняя оценка является более совершенной. Препятствием для применения эксплуатационно-динамического габарита является сложность практического использования динамических характеристик проектируемого подвижного состава.
Следовательно, строительный габарит подвижного состава представляет собой поперечное очертание, в котором должен помещаться новый ненагруженный вагон, расположенный на прямом горизонтальном пути, когда его продольная ось совпадает с осью пути.
При проверке габаритности проектируемого вагона, называемой вписыванием вагона в габарит, в данном случае необходимо учитывать лишь смещения четвертой группы — выносы в кривых. В результате этого вписывание вагона в строительный габарит подвижного состава отличается простотой, что является достоинством данной системы. Существенным ее недостатком является то, что пространство между габаритами приближения строений и подвижного состава, установленное по одинаковой для всех вагонов величине смещений третьей группы (в), может для одних вагонов оказаться излишне большим, а для других недостаточным.
Недоиспользование межгабаритного пространства обусловливает уменьшение ширины и высоты кузова вагона, что снижает экономическую эффективность грузовых и ухудшает комфортабельность пассажирских вагонов. Такое недоиспользование свойственно большей части вагонов, поскольку при построении строительного габарита подвижного состава смещения третьей группы устанавливаются по вагонам с наибольшими разбегами и износами ходовых частей и статическими прогибами (осадками) рессорного подвешивания. Недостаточность межгабаритного пространства, возможная при проектировании вагона с еще большими нормируемыми износами или большим статическим прогибом (осадкой), чем было учтено при построении этого габарита, означает негабаритность вагона, угрожающую безопасности движения.
Недостатки строительного габарита, применявшегося до 1960 г., обусловили замену его более целесообразным эксплуатационным габаритом подвижного состава, определение которого по ГОСТ 9238-83, приведено выше.
При вписывании вагона в эксплуатационный габарит подвижного состава учитывают смещения третьей и четвертой групп (в и г).
На рис. 2.30 изображена схема построения габаритов: исходя из габарита приближения строений I и осей междупутий 2 посредством учета смещений первой и второй групп (см. а и б) определяют эксплуатационный габарит подвижного состава 3, по которому путем вписывания, учитывающим смещения третьей и четвертой групп (см. в и г), находят строительное очертание вагона 4. Проектное очертание вагона 5 отличается от строительного дополнительным учетом технологических отклонений в размерах, допускаемых при постройке вагонов.
Зная удельный объем vу , удельную площадь пола fy, и грузоподъемность вагона Р, можно определить геометрический объем кузова V, а для платформ — площадь пола F:
Внутренняя длина крытых, изотермических и полувагонов составляет
где FK — площадь поперечного сечения кузова, заполняемого грузом, м²
Внутренняя длина платформы
где 2Вв — внутренняя ширина платформы, м.
Длина платформы и полувагона выбирается с учетом существующих сортаментов длинномерных грузов. В частности, длину платформы и полувагона желательно иметь кратной величине 6,6—6,7 м, соответствующей длине распространенных лесоматериалов с учетом зазоров между штабелями и стенами вагона. Исходя из условий размещения контейнеров, внутреннюю длину платформы и полувагона целесообразно принимать кратной 2170 мм. Кроме того, длина, ширина и высота полувагона должны соответствовать размерам вагоно-опрокидывателей, однако в ряде случаев выгоднее размеры вагоноопрокидывателей приспосабливать к размерам полувагонов.Длину котла цистерны устанавливают в зависимости от диаметра котла, форм днища, колпака и других частей, определяющих объем котла.
Увеличение диаметра и уменьшение длины котла снижают его массу, но уменьшают прочность и жесткость котла. Увеличение диаметра котла повышает центр тяжести цистерны, а уменьшение длины котла обычно
сокращает базу цистерны. Все это ведет к ухудшению устойчивости и плавности хода цистерны, что существенно для четырехосных конструкций. Пределом увеличения диаметра котла является габарит подвижного состава. Размеры длины котла обычно связаны с допускаемой погонной нагрузкой вагона, которую, как указано выше, целесообразно возможно полнее использовать.
Для ориентировочного определения диаметра котла D четырехосной цистерны с учетом перечисленных факторов может быть использована формула
где V— объем котла.
Например, при объеме котла четырехосной цистерны, равном V = 73,1 м\ внутренний диаметр, вычисленный по данной формуле, D = 2,93 м близок к типовому размеру (3,0 м).
Для цистерн с большим объемом котла, например восьмиосных, диаметр, определяемый по этой формуле, превышает допустимый по условиям вписывания в габарит подвижного состава, который в данном случае является определяющим фактором. При малых колпаках, которые имеют цистерны последних лет постройки, объем котла увеличивают на 2-3 % для обеспечения расширения груза при повышении температуры.
Для достижения возможно большей погонной нагрузки внутреннюю ширину и внутреннюю высоту вагона принимают максимальными в пределах заданного габарита подвижного состава. Исходя из обычных способов размещения существующего съемного оборудования, внутреннюю ширину крытого вагона, используемого для перевозок пассажиров, принимают равной 2760 мм. Если при проектировании подобного вагона имеется возможность осуществить значительно большую ширину и тем самым повысить эффективность конструкции, то могут быть найдены иные способы использования существующего съемного оборудования.
Для обеспечения погрузки контейнеров внутреннюю ширину полувагона и платформы принимают не менее 2730—2740 мм (ширина двух контейнеров грузоподъемностью 3 т или одного грузоподъемностью 5 т с учетом зазоров между контейнерами и стенами вагона).
Чтобы обеспечить лучшее использование грузоподъемности платформ при перевозке в них сыпучих грузов, увеличивают высоту бортов. Однако при этом возрастает их масса, что затрудняет открытие и закрытие бортов. Кроме того, высота бортов выбирается с учетом возможности перевозки ряда грузов с опущенными бортами. При этом положении борта не должны выходить за пределы нижнего очертания габарита подвижного состава, а торцовые борта должны размещаться в межвагонном пространстве с учетом безопасного положения человека между бортами двух платформ.
Установив внутренние размеры кузова, определяют наружные его размеры. Наружная длина кузова
где ат — толщина торцовой стены кузова, м.
Наружная ширина кузова
где аб — толщина боковой стены, м.
В крытых вагонах учитывают также толщину боковой двери, в цистернах — наружную лестницу (если она расположена по бокам котла) и т.п.
Длина рамы кузова 2Lрм у большинства конструкций вагонов совпадает с длиной кузова.
Общая длина вагона составляет
где аа — вылет автосцепки, т.е. расстояние от оси сцепления автосцепок до концевой (буферной) балки, м.
Если выбрана длина консоли nk, то база вагона
Линейные размеры, вычисленные по формулам (2.23—2.28), уточняются путем вписывания вагона в габарит и исходя из других требований, предъявляемых к вагонам. При этом целесообразно выполнять сравнительный анализ параметров и конструктивных форм вагонов, успешно эксплуатируемых на железных дорогах России и зарубежных стран.
18 марта 1860 г. на железных дорогах нашей страны впервые в мире были установлены единые габариты приближения строений и подвижного состава. Эти габариты выгодно отличаются от габаритов зарубежных железных дорог, позволяя создавать вагоны с наибольшим объемом на единицу длины.
Действующий ГОСТ 9238-83 установил шесть единых для вагонов и локомотивов габаритов подвижного состава: Т, 1 -Т, 0-Т, 01 -Т, 02-Т, 03-Т и ввел два новых габарита — Тц и Тпp
Габарит Т (рис. 2.31), имеющий наибольшие размеры ширины и высоты, предназначен для вагонов, обращающихся по отдельным замкнутым направлениям реконструированных железных дорог СНГ, Балтии и Монгольской Народной республики, сооружения и устройства которых отвечают требованиям габарита приближения строений С (рис. 2.32).
По основному контуру, очерченному сплошными линиями, строят вагоны электропоездов, а в последние годы и некоторые грузовые вагоны. Границей размещения на вагонах сигнальных устройств, здесь, как и в других габаритах, является пунктирная линия, а неответственных выступающих частей (поручней, подлокотников, щитков и др.) — штрихпунктирная линия.
По очертаниям, показанным пунктирными линиями, вагоны могут строиться с разрешения Министерства путей сообщения после переустройства зданий, тоннелей и других искусственных сооружений, а для подвижного состава, обращающегося только на территории промышленных предприятий — по разрешению соответствующего министерства или ведомства по согласованию с МПС.
Габарит 1-Т предназначен для вагонов, допускаемых к обращению по всем железным дорогам СНГ, Балтии и МНР, а также по подъездным путям промышленных и транспортных предприятий. По контуру, показанному пунктирными линиями, вагоны могут строиться по распоряжению МПС с учетом работ по переустройству негабаритных сооружений.
Габарит 1-ВМ предусмотрен для вагонов, обращающихся по железным дорогам СНГ, Балтии и МНР, а также по отдельным реконструированным магистральным линиям других стран-участниц Организации сотрудничества железных дорог (ОСЖД), используемых для международных сообщений. Для обеспечения беспрепятственного обращения вагонов в странах-участницах ОСЖД проводилась работа по приведению железных дорог в соответствие с вводимыми едиными габаритами для этих стран.
Габарит 0-ВМ предназначен для вагонов, обращающихся по всем (кроме отдельных второстепенных участков) дорогам стран-участниц ОСЖД.
Габарит 02-ВМ (02-Т) предусмотрен для грузовых вагонов, обращающихся по всем железным дорогам стран-участниц ОСЖД, а также железным дорогам ФРГ, Австрии, Югославии, Греции, Дании, Турции и некоторых других стран Европы и Азии.
Габарит 03-ВМ предназначен для вагонов, допускаемых к обращению по дорогам всех стран Европы и Азии.
![]() |
Устройство колесной пары.
Таблица 1
Типы колесных пар вагонов
Тип колесной пары | Тип вагона | Конструкционная скорость вагона, км/час | Максимальная расчетная статистическая нагрузка от колесной пары на рельсы, кН (тс) |
РУ1Ш-957-Г | Грузовой | 120 | 230,5 (23,5) |
РУ1Ш-957-П | Пассажирский | 160 | 176,6 (18,0) |
РУ1Ш-957-Э | Немоторный электропоезда | 130 | 186,4 (19,0) |
РУ1Ш-957-Д | Немоторный дизель-поезда | ||
РВ2Ш-957-Г | Грузовой | 1200 | 245,2 (25,0) |
Номинальное расстояние между кругами катания колес 2l равно 1580 мм, а между серединами шеек 2b – 2036 мм.
Рис.3. Основные размеры колесной пары
Во избежание неравномерной передачи нагрузки на колёса и рельсы разность размеров k от торца оси до внутренней грани обода допускается не более 3 мм.Колёса, укреплённые на одной оси, не должны иметь разность диаметров D более 1 мм, что предотвращает односторонний износ гребней и не допускает повышения сопротивления движению. Чтобы снизить инерционные усилия, колесные пары скоростных вагонов подвергают динамической балансировке: для скоростей 140...160 км/ч допускается дисбаланс не более 6 Нм; для скоростей 160...200 км/ч - не более 3 Нм. Номинальная ширина обода колес всех типов колесных пар составляет 130 мм.
Ось.
Вагонная ось (рис. 1) является составной частью колёсной пары и представляет собой стальной брус круглого, переменного по длине поперечного сечения. На подступичных частях 3 оси располагаются колёса, укреплённые жёстко или подвижно, а на шейках 1 размещаются подшипники. Вагонные оси различаются между собой размерами, определяемыми в зависимости от заданной нагрузки; формой шейки оси в соответствии с применяемым типом подшипника – для подшипников качения и подшипников скольжения; формой круглого поперечного сечения – сплошные или полые; способом торцового крепления подшипников качения на шейке оси – корончатой гайкой или шайбой.
Кроме того, оси классифицируются по материалу и технологии изготовления. Между шейками 1и подступичными частями3 находятся предподступичные части 2, служащие для размещения деталей задних уплотняющих устройств букс, а также снижения концентрации напряжений в переходных сечениях от nодступичных частей к шейкам оси. В местах изменения диаметров для снижения концентрации напряжений имеются плавные сопряжения – галтели, выполненные определёнными радиусами: от шейки 1 – к предподступичной 2, от предnодступичной – к подступичной 3 и от средней 4 – к подступичной частям. Снижение концентрации напряжений, вызванных посадкой внутреннего кольца роликового подшипника, обеспечивается разгружающей канавкой, расположенной у начала задней галтели шейки оси (рис. 8, г). Оси для подшипников качения на концах шеек имеют нарезную часть К (рис.1, а) для навинчивания корончатой гайки, на торце имеется паз с двумя нарезными отверстиями для постановки и крепления двумя болтами стопорной планки.
В вагонных осях с креплением подшипников качения при помощи приставной шайбы в торцах шеек делают нарезные отверстия для болтов (рис. 1, б) в двух вариантах: при помощи трёх или четырёх болтов. На торцах всех типов осей предусмотрены центровые отверстия (рис. 1, д, е), служащие дляустановки и закрепления оси или колёсной пары в центрах при обработке на токарном станке. Форма и размеры центровых отверстий стандартизированы. Оси колёсных пар, оборудуемых дисковым тормозом, а также оси, на которых предусмотрена установка привода подвагонного генератора, имеют посадочные поверхности для установки тормозных дисков или деталей редуктора. Основные размеры и допускаемые нагрузки для стандартных типов осей вагонов широкой колеи, кроме вагонов электро- и дизель-поездов, приведены в табл. 2.
На шейки осей РУ1 и РУ1Ш устанавливают роликовые подшипники с наружным диаметром 250 мм.
У всех типов осей расстояния между центрами приложения нагрузки к шейкам одинаковы и составляют 2036 мм. Для грузовых вагонов с повышенными нагрузками от колесной пары на рельсы до 245 кН предусмотрена усиленная ось, имеющая увеличенные диаметры.
Таблица 2
Стандартные типы осей вагонов широкой колеи (ГОСТ Р50334-92)
Тип оси | Диаметр частей оси, мм | Длина шейки, мм | Общая длина оси, мм | Нагрузка от колесной пары вагонов на рельсы, кН (тс) | ||||
шейки | предподступичной | подступичной | средней | Грузовые | Пассажирские | |||
РУ1 | 130 | 165 | 194 | 165 | 176 | 2294 | 230 (23,5) | 176,5(18) |
РУ1Ш | 130 | 165 | 194 | 165 | 190 | 2216 | 230 (23,5) | 176,5(18) |
Оси проектируют в исполнении УХЛ по ГОСТ 15150. для вагонов магистральных дорог колеи 1520 мм оси изготовляют из осевой заготовки по ГОСТ 4728: для вагонов основных типов применяется сталь марки ОсВ, для вагонов электропоездов - сталь марки ОсЛ.
Химический состав:
- углерода 0,40 - 0,48;
- марганца 0,55 - 0,85;
- кремния 0,15 - 0,35;
- фосфора не более 0,04;
-
серы не более 0,045;
- хрома не более 0,3;
- меди не более 0,25 %.
В соответствии с ГОСТ 4008 гарантийный срок эксплуатации чистовых осей 8,5 лет, а срок службы - 15 лет. На торце чистовой оси предусмотрена маркировка с соответствующим расположением знаков и клейм: клеймо Госприёмки; условный номер предприятия, производившего обработку и перенесшего знаки маркировки; номер оси; две последние цифры года изготовления черновой оси; клеймо технического контроля.
Вагонные оси изготавливают поперечно–винтовой прокаткой и радиально–ротационным методом.
Процесс поперечно – винтовой прокатки ведётся на трёхвалковом стане, валки которого расположены под углом 120 градусов один к другому, что обеспечивает автоматическую деформацию заготовки по форме оси при помощи контролирующего устройства.
При радиально–ротационном способе черновая ось зажимается в шпинделе машины, где ролики обеспечивают обжатие заготовки в соответствии с требуемыми размерами.
Изготовление вагонных осей методом поперечно–винтовой прокатки и радиально–ротационным методом даёт возможность обеспечить высокую производительность и улучшить качество металла оси.
Схема изготовления осей
Технологический процесс изготовления вагонной оси включает:
- получение черновой заготовки;
- термическую обработку;
- правку;
- очистку от окалины;
- черновую и чистовую механическую обработку;
- приёмку и клеймение.
На шейке или средней части оси в горячем состоянии наносят знаки и клейма
1-номер завода изготовителя
2-дата изготовления оси
3-приемочные клейма МПС
4-номер оси
5-номер плавки.
После этого черновые оси термически обрабатывают (нормализация или нормализация с отпуском) с последующим процессом правки на прессах или штампах, а затем очистки в дробеструйных конвейерных камерах. Черновые оси проходят приемо-сдаточные испытания от каждой партии одной плавки до 150 штук.
При этом проверяют внешний вид, размеры каждой оси и проводят механические испытания образцов, вырезанных из оси, на удар и растяжение.
После механической обработки клейма, нанесённые на среднюю часть черновой оси, переносят на один из торцов.
В процессе механической обработки вагонных осей на участках, оснащенных автоматическими линиями, обрезают два конца заготовки и зацентровывают их, затем выполняют черновую обработку оси, проточку шеек под резьбу М110, фрезерование пазов под стопорную планку и сверловку отверстий под резьбу М12, с последующим нарезанием резьбы.
Обточка оси
Для повышения усталостной прочности всю поверхность вагонной оси накатывают роликами на специальных токарно-накатных станках. Сущность накатки состоит в том, что закреплёная в станке ось приводится во вращение и к её поверхности с определённым усилием прижимаются ролики, которые одновременно перемещаются с супортом вдоль оси.
Накатка шеек оси
После накатки шлифуют шейки оси и подступичные части, затем промывают водным раствором триэтаноламина в одной камере и обдувают воздухом – во второй.
У готовой оси колёсной пары автоматически контролируют размеры, потом проверяют ось магнитным дефектоскопом.
Чистовые оси
В эксплуатации ось работает при нестационарном режиме нагружения при вращении колёсной пары. Поэтому она испытывает знакопеременные напряжения с амплитудами переменной величины. Такой нестационарный режим требует применения мер по повышению предела выносливости осевой стали.
Специфика работы оси заключается в том, что при нагружении она испытывает изгибные напряжения, которые по площади поперечного сечения распределяются неравномерно, достигая наибольших значений в наружных и наименьших - во внутренних волокнах. Это обстоятельство ставит проблему замены сплошного сечения оси полым, не вызывая заметного увеличения габаритных размеров, но способствующее уменьшению массы на 100...110 кг по сравнению с осью сплошного сечения.
Опыт применения колёсных пар с полыми осями показывает, что при их создании особое внимание следует уделять обеспечению надежного соединения колеса с осью, так как в эксплуатации ослабевает их посадка – усилия распрессовки колёс оказываются ниже усилий напрессовки. Это может быть объяснено возникновением остаточных деформаций полой оси и действием других факторов, определение которых требует специальных исследований.
Назначение букс.
Практически во всех машинах и механизмах имеются как вращающиеся, так и неподвижные части. Соединение вращающихся и неподвижных частей осуществляется при помощи подшипников. Подшипник обычно состоит из четырех частей:
1. внутреннее кольцо – оно плотно надевается на вращающуюся часть (вал) и вращается вместе с ним;
2. наружное кольцо – оно устанавливается в неподвижное «посадочное место» и само остается неподвижным;
3. ролики или шарики – расположены между кольцами, они перекатываются при вращении, благодаря чему снижается трение и обеспечивается легкость вращения;
4. сепаратор ( в переводе на русский – разделитель) – это такая решетка, которая отделяет ролики друг от друга, чтобы они не наезжали один на другой и не мешали друг дружке перекатываться.
Вагоны - не исключение. Колесные пары вагонов соединяются с их тележками при помощи подшипников. Внутренние кольца закрепляются на шейках оси колесной пары, а наружные – неподвижны относительно рамы тележки.
Подшипники должны работать в смазке, причем смазка должна быть чистой. Поэтому во всех технических устройствах подшипники размещают в какой-то полости или коробке, которая заполнена смазкой и герметично отделена от окружающей среды. Собственно говоря, такие коробки с подшипниками и смазкой и называются вагонными буксами.
На фото - учебное пособие: букса со снятыми крышками и разрезанным корпусом.
Видны наружные кольца двух подшипников.
Кроме функции соединения вращающихся и неподвижных частей, буксовые узлы выполняют еще ряд важных задач.
Они обеспечивают передачу нагрузки от кузова вагона на шейки осей и ограничивают продольные и поперечные перемещения колесной пары относительно тележки. Вместе с колесными парами они являются наиболее ответственными элементами ходовых частей вагона.
Буксовый узел неподрессорен и жестко воспринимает динамические нагрузки от рельсового пути, возникающие при движении вагона. Кроме постоянно действующих нагрузок от массы брутто, буксовый узел испытывает значительные удары при прохождении колес по стыкам рельсов, от толчков во время торможения поезда или наезда колес на башмак при роспуске вагонов с горки, от действия центробежной силы при прохождении кривых участков пути и др.
Основными требованиями, предъявляемыми к буксовым узлам, являются:
- безотказность и долговечность работы в существующих условиях эксплуатации в течение установленных сроков службы;
- небольшая собственная масса;
- взаимозаменяемость и унификация деталей;
- простота выполнения монтажа и демонтажа узлов при ремонте и хорошая герметизация буксового узла.
Подшипники.
В мировой практике вагоностроения применялись буксовые узлы на подшипниках качения и подшипниках скольжения. Буксовые узлы отечественных вагонов, а также современых конструкций зарубежных вагонов, оборудованы исключительно подшипниками качения (роликовыми подшипниками). Это обусловлено тем, что роликовые подшипники обеспечивают реализацию высоких скоростей движения и осевых нагрузок, а также более надежны и экономичны в эксплуатации.
В практике вагоностроения используются три основных типа роликовых подшипников: цилиндрические однорядные — с короткими цилиндрическими роликами, сферические двухрядные — со сферическими роликами, конические одно- и двухрядные — с коническими роликами. Наибольшее распространение в отечественных и зарубежных вагонах получили цилиндрические роликовые подшипники. С 1964 г. отечественные вагоны на сферических подшипниках не выпускаются.
Внутри корпуса буксы обычно размещаются два подшипника качения. Подшипники для букс грузовых и пассажирских вагонов железных дорог МПС единые. Это роликовые цилиндрические подшипники — радиальные однорядные подшипники с короткими цилиндрическими роликами размером 130x250x80 мм.
Типы роликов: а — со скосами; б — с рациональным контактом "бомбиной"
Ролики имеют форму цилиндра, образующая которого представляет прямую линию, параллельную оси вращения подшипника и перпендикулярную радиальной нагрузке. Поэтому радиальная нагрузка распределяется по длине и хорошо воспринимается цилиндрической поверхностью тел качения, а осевая — лишь торцами роликов. Для предупреждения вредного влияния перекоса буксы и прогиба шейки оси на работу цилиндрических
подшипников ролики стали изготавливать со скосами "бомбиной".
Роликовый подшипник состоит из наружного и внутреннего колец, между которыми находятся ролики. Последние удерживаются в сепараторе на одинаковом расстоянии друг от друга.
Наружное кольцо одинаковое как для переднего, так и для заднего подшипника.Оно имеет наружный диаметр 250 мм, плотно (хотя и с небольшим зазором) входит в корпус буксы. Его внутрення поверхность имеет канавку или желобок, по которой перекатываются ролики. Края канавки не позволяют роликам сместиться ни вправо, ни влево. Кстати, на этой картиночке, которую мы не сами рисовали, а позаимствовали - явный "косяк": с одной стороны бортик нарисован, а с другой нет.
Внутреннее кольцо переднего и заднего подшипников неодинаковы. Задний подшипник выполнен с однобортовым внутренним кольцом, а передний — с безбортовым внутренним кольцом. Почему так - будет объяснено позднее.
Подшипники, имеющие один упорный борт на внутреннем кольце или оборудованные одним приставным кольцом, называются полузакрытыми. Они хорошо воспринимают радиальную нагрузку (направленную перпендикулярно оси вращения подшипников), а осевую — ограниченной величины — только со стороны борта или приставного кольца.
Передний подшипник имеет условное обозначение 232726 ГОСТ 18752, а задний — 42726 ГОСТ 18752. По этим обозначениям можно судить о размерах подшипника и его конструктивных разновидностях. Задний подшипник это тот, который ближе к колесу.
Внутреннее кольцо подшипника устанавливается на шейку оси с натягом, а наружное в корпус буксы — свободно. Вращение шейки оси вместе с внутренним кольцом подшипника вызывает вращение роликов вокруг своих осей и перекатывание по дорожкам качения между наружным и внутренним кольцами. Свободное перемещение роликов обеспечивается наличием радиального и осевого зазоров.
Радиальный зазор измеряется в свободном от нагрузки подшипнике и представляет собой сумму зазоров между дорожками качения колец и роликом. Осевой зазор измеряется между торцами роликов и бортами колец. Для новых подшипников на горячей посадке радиальный зазор 115-170 мкм, а осевой зазор 70-150 мкм. Причем меньшие значения зазоров рекомендуются для грузовых вагонов, а большие — для пассажирских.
Сепаратор представляет собой кольцо, изготовленное из латуни ЛЦ400МцЗЖ с наличием окон для установки роликов. Для удержания роликов от выпадания из сепаратора производится расчеканка его перемычек.
В мировой практике широко применяются пластмассовые сепараторы. Их важнейшие преимущества — незначительная масса, хорошие антифрикционные качества, возможность изготовления методом литья или
под давлением с незначительными затратами. При недостаточной смазке пластмассовые сепараторы проявляют свои аварийные ходовые качества. В результате они нашли широкое применение за рубежом в качестве заменителей массивных латунных сепараторов.В настоящее время разработана и принята к серийному производству рамная конструкция отечественного сепаратора из стеклонаполненного полиамида, обеспечивающая существенное повышение надежности работы буксового узла за счет устранения износов сепаратора по центрирующей поверхности и перемычкам. При этом устраняются окисление смазки, задиры торцов роликов и бортовых колец, исключается заклинивание подшипников из-за разрушения сепаратора. Новая конструкция сепаратора позволила повысить живучесть буксового узла в аварийном режиме и снизить необрессоренную массу подшипника.
Для изготовления колец и роликов применяется сталь марки ШХ4. Раньше кольца и ролики подшипников изготавливались из стали марки ШХ15СГ электрошлакового переплава. В процессе эксплуатации подшипников, изготовленных из таких сталей, проявлялась склонность к хрупкому излому особенно внутренних колец вследствие больших напряжений, возникающих от посадки колец на шейку оси при воздействии радиальной и осевой нагрузок при движении вагона. Исследования показали, что новая сталь марки ШХ4 регламентируемой прокаливаемости обладает высокой твердостью поверхностного слоя и достаточной вязкостью внутренних волокон, что обеспечивает высокую устойчивость хрупкому разрушению по сравнению со сталью ШХ15СГ.
Цилиндрические подшипники, применяемые в вагонах, выполнены разъемными: наружное кольцо, сепаратор, ролики образуют отдельный блок, который свободно снимается и надевается на внутреннее кольцо. Это хорошо видно на картинке. Такая конструкция упрощает технологию монтажа и демонтажа буксового узла, поэтому она находит широкое применение в вагоностроении.
Размер роликового подшипника для вагонных букс 130 х 250 х 80. Это - внутренний (посадочный) диаметр внутреннего кольца х наружный (посадочный) диаметр наружного кольца х ширина колец подшипника.
![]() |
Дата добавления: 2020-12-12; просмотров: 234; Мы поможем в написании вашей работы! |
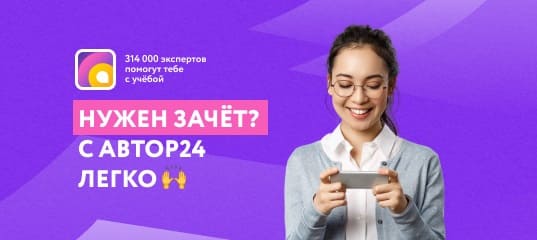
Мы поможем в написании ваших работ!