Примерный расчет параметров заготовки методом литья
6.2.2. Литература
6.2.2.1. Чертеж детали
6.2.2.2. ГОСТ 26645-85
6.2.2.3."Справочник технолога-машиностроителя" т.2, Ю.А. Абрамов, В.Н. Андреев, Б.Н. Горбунов и др. (под редакцией Косиловой А.Г., Мещерякова Р.К.), М., Машиностроение 1985 г.
6.2.3. Порядок выполнения практической работы
6.2.3.1. Вычертить деталь
Рисунок 1 – Чертеж детали
6.2.3.2. Выбрать плоскость разъема модели и формы
Выбирается с учетом конфигурации детали, удобство формовки и сборки. Для указания положения плоскость разъема модели и формы рядом с проекцией детали проводится толстая сплошная линия с буквенным обозначением МФ (разъем модели, формы).Для данной детали плоскость разъема совпадает с осью детали.
6.2.3.3. Выбрать положение отливки в форме
Выбирается с учетом технологичности закрепления половин модели на модельной плите, места и способа подвода металла. Наиболее ответственные части лучше располагать в нижней полуформе. Положение отливки в форме показывается стрелками с буквенным обозначением В и Н (верх и низ формы)
6.2.3.4. Назначить квалитет точности для размеров отливки таблица 13,14,15(2.3)
6.2.3.5. Назначить припуски на механическую обработку и допускаемые отклонения на размеры отливки по ГОСТ 26645-85г. в следующем порядке, (см . примечание таблиц):
1) класс размерной точности - 9, по таблице 9
2) степень коробления выбирается в зависимости от отношения наименьшего размера к наибольшему: 10/120 0,09, степень коробления - 6, по таблице 10
|
|
3) степень точности поверхности - 10, по таблице 11
4) ряд припусков-3, по таблице 14
5) назначить допуски размеров отливки по таблице 1 в зависимости от класса размерной точности
6) допуск формы-0,4 по таблице 2
7) общий допуск по таблице 16
8) общий припуск по таблице 6
Предварительно перед пунктом 8 назначить требуемые стадии обработки из таблицы 1, карта 1 стр.35 (2.4)
6.2.3.6. Припуск, на диаметр вала, если обработка с 2-х сторон, умножить на 2
Таблица 1
Квалитет заготовки | Квалитет детали | |||||||
14 | 13-12 | 11-9 | 8-7 | |||||
Требуемые стадии обработки | ||||||||
№ стадии | Наименование стадии | № стадии | Наименование стадии | № стадии | Наименование стадии | № стадии | Наименование стадии | |
17 | 1 | Черновая | 1 2 | Черновая Получистовая | 1 2 3 | Черновая Получистовая Чистовая | 1 2 3 4 | Черновая Получистовая Чистовая Отделочная |
16 | 1 | Черновая | 1 2 | Черновая Получистовая | 1 2 3 | Черновая Получистовая Чистовая | 1 2 3 4 | Черновая Получистовая Чистовая Отделочная |
15 | 1 | Черновая | 1 2 | Черновая Получистовая | 2 3 | Получистовая Чистовая | 2 3 4 | Получистовая Чистовая Отделочная |
14 | - | - | 2 | Получистовая | 2 3 | Получистовая Чистовая | 2 3 4 | Получистовая Чистовая Отделочная |
13 | - | - | 2 | Получистовая | 3 | Чистовая | 3 4 | Чистовая Отделочная |
12 | - | - | - | - | 3 | Чистовая | 3 4 | Чистовая Отделочная |
11 | - | - | - | - | 3 | Чистовая | 4 | Отделочная |
3.7. Технологически отверстия Ф10 не выполняются
|
|
3.8. Результаты расчетов занести в таблицу 2
Таблица 2 Расчет размеров отливки
Размер,мм детали | Допуск размера,мм | Допуск формы,мм | Общий допуск мм | Квалитет | Стадии обработки | Общий припуск | Размер заготовки, мм | Окончательный размер заготовки мм |
Ø40 | 1,8 | 0,4 | 2,0 | H13 | 1,2 | 2,2 | Ø35,6±1 | Ø36±1 |
Ø60 | 2,0 | 0,4 | 2,0 | H7 | 1,2,3,4 | 2,8 | Ø54,4±1 | Ø54±1 |
Ø65 | 2,2 | 0,4 | 2,4 | H12 | 1,2 | 2,6 | Ø70,2±1,2 | Ø70±1,2 |
Ø80 | 2,2 | 0,4 | 2,4 | h9 | 1,2,3 | 2,9 | Ø85,8±1,2 | Ø86±1,2 |
Ø120 | 2,4 | 0,4 | 2,4 | H14 | 1 | 1,8 | Ø123,6±1,2 | Ø124±1,2 |
40 | 1,8 | 0,4 | 2,0 | H7 | 1,2,3,4 | 2,6-1,3=1,3 | 41,3±1 | 41,5±1 |
10 | 1,2 | 0,4 | 1,4 | H14 | 1 | 1,3 | 12,6±0,7 | 13±0,7 |
90 | 2,2 | 0,4 | 2,4 | H12 | 1,2 | 2,6 | 95,2±1,2 | 95±1,2 |
6.2.4. Назначить формовочные уклоны по ГОСТ 3212-80
6.2.5. Технические требования
- Литейные уклоны по ГОCT 3212-80
- Точность отливки 9-6-10 ГОСТ26645-85
|
|
Примерный расчет параметров заготовки поковок, изготовленных ковкой на молотах
Методические указания к выполнению работы
Расчет заготовки выполняется по ГОСТ 7505-89
6.3.1. Определение расчетной массы поковки
Расчётная масса поковки Мпр, кг, определяется исходя из её номинальных размеров.
Мпр = Мд• КР, (1)
где: Мд - масса детали, кг;
КР – расчётный коэффициент (Приложение 3, таблица 20, стр.31).
6.3.2. Определение исходного индекса
Исходный индекс для последующего назначения основных припусков, допусков и допускаемых отклонений определяется в зависимости от массы, марки стали, степени сложности и класса точности поковки (Табл.2 стр.10)
· группа стали М (Табл. 1 стр.8);
· Класс точности штамповки Т (Прил.1, стр.28);
· Степень сложности поковки С (Прил.1, стр.29-30), определяется из отношения
, (2)
где: Gп = Мпр – масса (объём) поковки;
Gф - масса (объём) геометрической фигуры, в которую вписываются формы поковки.
При определении размеров описывающей поковку геометрической фигуры допускается исходить из увеличения в 1,05 раза габаритных линейных размеров детали, определяющих положение её обработанных поверхностей.
|
|
3. Определение формы поковки
Форма поковки – пространственная фигура, определенная линейными и угловыми размерами. Геометрические параметры поковки: длина, ширина, диаметр, высота и глубина – размеры, получаемые в одной части штампа; толщина – высотный размер, получаемый в обеих частях штампа
Впадины и углубления в поковке выполняют глубиной:
· при изготовлении на молотах и прессах до 0,8 их диаметра;
· при изготовлении на горизонтально-ковочных машинах (ГКМ) – до трех диаметров.
Изготовление сквозного отверстия в поковке возможно, если диаметр отверстия в детали не менее 30 мм, а толщина поковки в месте пробивки не более диаметра пробиваемого отверстия.
6.3.4. Определение припусков на механическую обработку.
Основные припуски на механическую обработку поковок определяются в зависимости от исходного индекса, линейных размеров и шероховатости поверхности детали (Табл. 3, стр. 12-13).
Дополнительные припуски – таблица 4, таблица 5 (стр. 14)
6.3.5. Определение размеров поковки
Размеры поковки определяются как алгебраическая сумма линейных размеров поковки и припуска на данный размер. Линейные размеры поковки разрешается округлять с точностью до 0,5 мм в большую сторону для наружных поверхностей, в меньшую – для внутренних.
Расчёт размеров свести в таблицу:
6.3.6. Определение допусков на размеры
Допуски и допускаемые отклонения линейных размеров поковок назначаются в зависимости от исходного индекса и размеров поковки (Табл. 8, стр. 17-19).
6.3.7. Построение эскиза заготовки
По полученным размерам построить эскиз поковки. Правила выполнения чертежа поковки по ГОСТ 3.1126-88
6.3.7.1 Определение коэффициента использования материала
Коэффициент использования материала (Ким), определяется по формуле
(3)
где Мд – масса детали, кг;
Мз = ρ×Vз – масса заготовки, кг.
Где ρ – плотность материала заготовки, г/см3;
Vз – объём заготовки, см3.
Примечание:
· Масса детали принимается по рабочему чертежу детали и определяется в системе автоматизированного проектирования КОМПАС
· Масса заготовки определяется в системе автоматизированного проектирования КОМПАС
БИБЛИОГРАФИЧЕСКИЙ СПИСОК
7.1. Рекомендуемая литература
1. ГОСТ 2.105-95 ЕСКД
2. ГОСТ 3.1102-81 ЕСТД
3. ГОСТ Р 21.1101-2013 СПДС
4. ГОСТ 7.32-2001
5. ГОСТ 7505-89
6. ГОСТ
7. ГОСТ 26645-85
8. "Справочник технолога-машиностроителя" т.2, Ю.А. Абрамов, В.Н. Андреев, Б.Н. Горбунов и др. (под редакцией Косиловой А.Г., Мещерякова Р.К.), М., Машиностроение 1985 г.
9. Булавинцева И.А. Машиностроительное производство. Москва. Академия 2009.
10. Локтева С.Е. Станки с программным управлением и промышленные роботы.
11. Локтева С.Е. Станки с программным управлением и промышленные роботы. Москва. Машиностроение. 2010.
12. Моряков О.С. Оборудование машиностроительного производства. Москва. Академия 2009.
13. Черпаков Б.И. Вереина Л.И. Технологическое оборудование машиностроительного производства, Москва, Академия. 2010.
14. Черпаков Б.И. Альперович П.А. Металлорежущие станки. Москва. Академия 2010.
15. Шишмарев В.Ю. Автоматизация технологических процессов. Москва. Академия 2016.
Дополнительные источники:
16. Ермаков Ю.М. Фролов Б.Н. Металлорежущие станки. М. Машиностроение, 2010.
17. Роботизированные технологические комплексы и гибкие производственные системы в машиностроении под редакцией Соломенцева Ю.М. М.: .Высшая школа, 2009.
Журналы:
18. Вестник машиностроения – издатель ООО «Издательство Машиностроение», издается с 1921 г.
19. Металлургия
20. Машиностроитель – издатель ООО «Научно-техническое предприятие «Вираж-Центр», издается с 1931 г.
21. Технология машиностроения – издатель Издательский центр "Технология машиностроения», издается с 2000 г.
Дата добавления: 2020-11-29; просмотров: 1599; Мы поможем в написании вашей работы! |
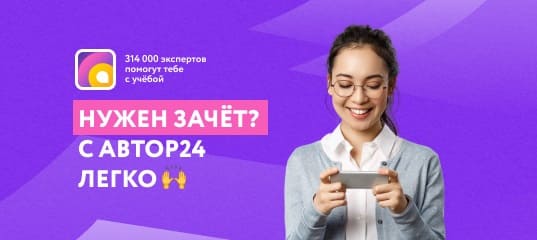
Мы поможем в написании ваших работ!