Диффузионное насыщение металлами и неметаллами (бором и кремнием)
Лекция №4
Поверхностное упрочнение металлических материалов. Классификация способов упрочнения. Химико-термическая обработка сталей: цементация, азотирование, химические покрытия. Поверхностная закалка сталей.
Классификация покрытий
В современном машиностроении применяется большое количество методов, позволяющих повысить износостойкость поверхности изделий, а также придать необходимые свойства поверхности детали.
Все известные методы нанесения покрытий подразделяются на 5 основных классов:
1) упрочнение с образованием пленки на поверхности;
К ним относят:
а) осаждение химической реакции (оксидирование, сульфидирование, фосфатирование, нанесение упрочняющего смазочного материала, осаждение из газовой фазы).
б) осаждение из паров (термическое испарение тугоплавких соединений, катодно-ионная бомбардировка, прямое электронно-лучевое испарение, реактивное электронно-лучевое испарение, электронно-химическое испарение).
в) электролитическое осаждение (хромирование, никелирование, электрофорез, никельфосфатирование, борирование, борохромирование, хромофосфатирование).
г) напыление износостойких соединений (плазменное напыление порошковых материалов, детонационное напыление, электродуговое напыление, лазерное напыление, вихревое напыление, индукционное припекание порошковых материалов).
2) Изменение химического состава поверхностного слоя;
|
|
К ним относят:
а) диффузионное насыщение (борирование, цианирование, азотирование, нитроцементация и т.п.)
б) химическое и физико-химическое воздействие (химическая обработка, ионная имплантация, электроискровая обработка и т.д.).
3) Изменением структуры поверхностного слоя;
К ним относят:
а) физико-термическая обработка (лазерная закалка, плазменная закалка);
б) электрофизическая обработка (электроконтактная, электроэрозионная, магнитная обработка);
в) механическая (упрочнение вибрацией, фрикционно-упрочняющая обработка, дробеструйная, обработка взрывом, термомеханическая, электромеханическая);
г) наплавка легированным элементом (газовым пламенем, электрической дугой, плазмой, лазерным лучом, пучком ионов и т.д.).
4) Изменение энергетического запаса поверхностного слоя;
К ним относят:
а) обработка в магнитном поле (термомагнитная обработка, импульсным магнитным полем, магнитным полем);
б) обработка в электрическом поле.
5) Изменение микрогеометрии поверхности и наклепом.
К ним относят:
а) обработка резанием (точение, шлифование, сверхскоростное резание);
б) пластическое деформирование (накатывание, обкатывание, раскатывание, выглаживание, вибронакатывание, вибровыглаживание, калибрование, центробежно-ударное упрочнение, виброударное и т.д.);
|
|
в) комбинированные методы (анодно-механическая обработка, поверхностное легирование с выглаживанием, резание с воздействием ультразвуковых колебаний, магнито-абразивная обработка и т.д.).
Химико-термической обработкой
Химико-термической обработкой называют поверхностное насыщение стали соответствующими элементами (например, углеродом, азотом, алюминием, хромом и др.) путем его диффузии в атомарном состоянии из внешней среды при высокой температуре. Химико-термическая обработка заключается в нагреве изделия до заданной температуры в твердой, газовой или жидкой среде, легко выделяющей диффундирующий элемент в атомарном состоянии, выдержке при этой температуре и последующем охлаждении. В отличие от термической обработки химико-термическая обработка изменяет не только структуру, но и химический состав поверхностных слоев, что позволяет в более широких пределах менять свойства стали.
Процесс химико-термической обработки состоит из трех элементарных стадий: 1) выделения диффундирующего элемента в атомарном состоянии в результате реакций, протекающих в насыщающей среде; 2) контактирования атомов диффундирующего элемента с поверхностью стального изделия и проникновения (растворения) в решетку железа (адсорбция); 3) диффузии атомов насыщающего элемента вглубь металла.
|
|
Скорость диффузии атомов насыщающего элемента в решетку железа неодинакова и зависит от состава и строения образующих фаз. При насыщении углеродом или азотом, составляющим с железом твердые растворы внедрения, диффузия протекает быстрее, чем при насыщении металлами, образующими твердые растворы замещения.
Толщина диффузионного слоя х в зависимости от продолжительности процесса при данной температуре обычно выражается параболической зависимостью. Следовательно, с течением времени скорость увеличения толщины слоя непрерывно уменьшается. Чем выше температура, тем больше толщина слоя за данный отрезок времени. Толщина диффузионного слоя при прочих равных условиях тем больше, чем выше концентрация диффундирующего элемента на поверхности металла.
При определении толщины диффузионного слоя, полученного при насыщении железа (стали) тем или другим элементом, обычно указывается не полная толщина слоя с измененным составом, а только глубина до определенной твердости или структуры (эффективная толщина).
|
|
Цементация стали
Цементацией называется процесс насыщения поверхностного слоя стали углеродом.
Цементацию с последующей закалкой и отпуском применяют для повышения работоспособности деталей машин (шестерни, зубчатые муфты и втулки, пальцы, ролики и т. д.), испытывающих в процессе эксплуатации статические, динамические и переменные нагрузки и подверженных изнашиванию.
Для цементации обычно используют низкоуглеродистые стали (0,1—0,18 % С). Для крупногабаритных деталей применяют стали с более высоким содержанием углерода (0,2—0,3 %). Выбор таких сталей необходим для того, чтобы сердцевина изделия, не насыщающаяся углеродом при цементации, сохраняла высокую вязкость после закалки.
Для цементации детали поступают после механической обработки нередко с припуском на шлифование 0,05—0,10 мм. Во многих случаях цементации подвергается только часть детали, тогда участки, не подлежащие упрочнению, защищают тонким слоем меди (0,02— 0,04 мм), которую наносят электролитическим способом или изолируют специальными обмазками, состоящими из смеси огнеупорной глины, песка и асбеста, замешанных на жидком стекле, и др. Цементованный слой имеет переменную концентрацию углеродов по глубине, убывающей от поверхности к сердцевине детали (рис. 98, а). В связи с этим после медленного охлаждения в структуре цементованного слоя можно различить
Рис. Схема распределении концентрации углерода по толщине цементованного слоя
(от поверхности к сердцевине) три зоны: заэвтектойдную (П+Ц2), эвтектойдную (П), доэвтектойдную (Ф+П).
За эффективную толщину цементованного слоя обычно принимают сумму заэвтектоидной, эвтектоидной и половины переходной доэвтектоидной зон — до 0,40—0,45 % С или после закалки толщину до твердости HRC 50 или HV 500—600.
Концентрация углерода в поверхностном слое может составлять 0,8—1,2 %. Более высокая концентрация углерода вызывает ухудшение механических свойств цементуемого изделия.
Цементация твердым карбюризатором. В этом процессе насыщающей средой является твердый карбюризатор — древесный уголь (дубовый или березовый) в зернах 3,5—10 мм. Для ускорения процесса цементации к древесному углю добавляют активизаторы. Температура цементации в твердом карбюризаторе 910—930 °С, выдержка составляет 6—15 ч (для слоя 0,7-1,5). В массовом производстве не применяют.
Газовая цементация. Газовую цементацию осуществляют нагревом изделия в среде газов, содержащих углерод. Ее широко применяют на заводах, изготавливающих детали массовыми партиями.
Преимущества: точное получение заданной концентрации углерода в слое; сокращается длительность процесса; обеспечивается возможность полней механизации и автоматизации процессов и значительно упрощается последующая ТО изделий, так как можно проводить закалку непосредственно из цементационной печи.
Основной реакцией, обеспечивающей науглероживание при газовой цементации, является диссоциация СО:
2СО → СО2 + Сат;
Сат → Feγ → Feγ (С) — аустенит.
При выполнении процесса в шахтных печах для цементации применяют керосин, синтин, спирты и т. д., каплями подаваемые в печь.
Для сокращения длительности процесса широко используют газовую цементацию, при которой углеродный потенциал эндотермической атмосферы вначале поддерживают высоким, обеспечивающим получение в поверхностной зоне стали 1,2—1,3 % С, а затем углеродный потенциал атмосферы снижают до 0,8 % С. В этот период концентрация углерода на поверхности снижается до 0,8 %.
Цементацию выполняют при 930—950 °С. Продолжительность цементации для получения слоя толщиной 0,7—1,5 мм при 930 С в муфельных (безмуфельных) печах непрерывного действия составляет 6—12 ч, а в шахтных 3—10 ч.
Термическая обработка стали после цементации; свойства цементованных деталей. Окончательные свойства цементованные изделия получают в результате термической обработки, выполняемой после цементации. Этой обработкой можно исправить структуру и измельчить зерно сердцевины и цементованного слоя, получить высокую твердость в цементованном слое и хорошие механические свойства сердцевины; устранить карбидную сетку в цементованном слое.
В большинстве случаев применяют закалку выше точки Ас3 (для сердцевины) при 820—850 °С.
После газовой цементации используют закалку без повторного нагрева, а непосредственно из цементационной печи после подсуживания изделий до 840—860 С. Такая обработка не исправляет структуры цементованного слоя и сердцевины и не приводит к измельчению зерна.
Иногда термическая обработка состоит из двойной закалки и отпуска. Первую закалку (или нормализацию) с нагревом до 880—900 °С назначают для исправления структуры сердцевины. Кроме того, при нагреве в поверхностном слое в аустените растворяется цементитная сетка, которая при быстром охлаждении вновь не образуется. Вторую закалку проводят с нагревом до 760—780 СС для устранения перегрева цементованного слоя и придания ему высокой твердости. Недостаток такой термической обработки заключается в сложности технологического процесса, повышенном короблении, возникающем в изделиях сложной формы, и возможности окисления и обезуглероживания.
В результате термической обработки поверхностный слой приобретает структуру мартенсита или мартенсита с небольшим количеством остаточного аустенита и избыточных карбидов в виде глобулей.
Заключительной операцией термической обработки цементованных изделий во всех случаях является низкий отпуск при 160—180 °С, переводящий мартенсит закалки в поверхностном слое в отпущенный мартенсит.
Твердость поверхностного слоя для углеродистой стали составляет HRC 60—64, а для легированной HRC58—61; снижение твердости объясняется образованием повышенного количества остаточного аустенита.
Сердцевина деталей из углеродистой стали имеет структуру сорбита, а из легированных — бейнита или низкоуглеродистого мартенсита. Низкоуглеродистый мартенсит обеспечивает повышенную прочность и достаточную вязкость сердцевины. Твердость сердцевины обычно составляет HRC 30—40.
Нитроцементация
Нитроцементацией называют процесс диффузионного насыщения поверхностного слоя стали одновременно углеродом и азотом при 840— 860 °С в газовой среде, состоящей из науглероживающего газа и аммиака. Продолжительность процесса 4—10 ч. Основное назначение нитроцементации — повышение твердости, износостойкости и предела выносливости стальных деталей.
Для нитроцементации легированных сталей рекомендуется использовать контролируемую эндотермическую атмосферу, к которой добавляют 1,5—5,5 % (объемн.) необработанного природного газа и 1,0— 3,5 % (объемн.) NH3.
После нитроцементации следует закалка непосредственно из печи, реже после повторного нагрева, применяют и ступенчатую закалку. После закалки проводят отпуск при 160—180 °С.
При оптимальных условиях насыщения структура нитроцементованного слоя должна состоять из мелкокристаллического мартенсита, небольшого количества мелких равномерно распределенных карбонитридов и 25—30 % остаточного аустенита.
Твердость слоя после закалки и низкого отпуска HRC 58—60, HV 5700—6900 МПа. Высокое содержание остаточного аустенита обеспечивает хорошую прирабатываемость.
Азотирование стали
Азотированием называют процесс диффузионного насыщения поверхностного слоя стали азотом при нагреве ее в аммиаке. Азотирование повышает твердость поверхностного слоя, его износостойкость, предел выносливости и сопротивление коррозии в таких средах, как воздух, вода, пар и т. д. Твердость азотированного слоя заметно выше, чем цементуемой стали. Азотирование широко применяется для зубчатых колес, цилиндров двигателей, деталей машин.
Процесс азотирования проводят при 500—600 °С в атмосфере частично диссоциированного аммиака:
2NH3 → 3Н2 + 2NАТ;
NАТ → Feα → Feα (N) → γ' (Fe4N) → ε (Fe2-8N).
Азотированный слой на железе состоит из нитридной зоны Fe2-3N (ε-фаза) и Fe4N (γ'-фаза) и подслоя азотистого феррита (α-фаза), в котором при охлаждении выделяется нитрид железа Fe4N. При азотировании выше 600 °С между нитридным слоем и α-фазой образуется слой азотистого аустенита (γ-фаза).
Азотированию подвергают среднеуглеродистые легированные стали, содержащие Сг, Мо, V, W и А1, которые приобретают особо высокую твердость и износостойкость.
При азотировании легированных сталей образуются нитриды Cr2N, Mo2N, VN и др., которые, выделяясь в α-фазе (т. е. азотистом феррите) в дисперсном виде, препятствуют движению дислокаций и тем самым повышают твердость азотированного слоя. Наиболее сильно повышают твердость нитриды ванадия, хрома, молибдена, а также алюминий, который растворяется в γ'-фазе.
Если главными требованиями, предъявляемыми к азотированному слою, являются высокая твердость на поверхности до HV 1200 и износостойкость, то применяют сталь 38Х2МЮА. Молибден устраняет отпускную хрупкость в стали.
Азотирование изделий сложной конфигурации рекомендуется выполнять при 500—520 °С. Продолжительность процесса зависит от требуемой толщины азотированного слоя. Чем выше температура азотирования, тем ниже твердость азотированного слоя и больше толщина слоя. Снижение твердости азотированного сдоя связано с коагуляцией частиц нитридов легирующих элементов.
Обычно при азотировании желательно иметь слой толщиной 0,3—0,6 мм. В этом случае процесс азотирования при 500—520 СС продолжается 24—90 ч.
Для ускорения процесса применяют двухступенчатое азотирование сначала при 500—520 СС, а затем при 540—560 СС, при этом сокращается продолжительность процесса при сохранении высокой твердости азотированного слоя.
Для сокращения длительности процесса применяют азотирование в плазме тлеющего разряда.
В процессе насыщения азотом изменяются размеры изделия из-за увеличения объема поверхностного слоя.
В последние годы получило распространение азотирование при 570 °С в атмосфере, содержащей 50 % (объемн.) эндогаза и 50 % NH3 или 50 % СН4 и 50 % NH3, а также в расплавленных солях [55 % (NH2) CO + 45 % Na2CO3], через которые пропускается сухой воздух (соли расплавляют в титановых тиглях). В результате такой обработки на поверхности образуется тонкий слой карбонитрида Fe2-3 (N, С), обладающий высокой твердостью (HV 600—1200) и износостойкостью. Такая обработка повышает предел выносливости.
Цианирование стали
Цианированием называют совместное насыщение поверхности стали углеродом и азотом вследствие окисления расплавленных цианистых солей.
Изделие нагревают при 820—960 °С в расплавленных солях, содержащих цианистый натрий.
Для получения слоя небольшой толщины (0,15— 0,35 мм) процесс проводят при 820—860 °С в ваннах, содержащих 20—25 % NaCN, 25—50 % NaCl и 25— 50 % Na2CO5. Продолжительность процесса определяется требуемой толщиной слоя и составляет 30—90 мин.
После цианирования закалку выполняют непосредственно из цианистой ванны и дают низкотемпературный отпуск (180—200 °С). Твердость цианированного слоя после термической обработки HRC 58—62; толщина слоя 0,15—0,3 мм. Этот вид цианирования применяют для мелких деталей.
Для получения слоя большой толщины (0,5—2,0 мм) цианирование проводят при 930—960 'С в ванне, содержащей 8 % NaCN, 82 % ВаС12 и 10 % NaCl. Зеркало ванны покрывают слоем графита для предупреждения больших потерь тепла и угара цианистых солей. Продолжительность выдержки изделий в ванне составляет 1,5—6,0 ч. При высоких температурах сталь с поверхности в большей степени насыщается углеродом (до 0,8—1,2 % С) и в меньшей степени — азотом (0,2— 0,3 % N).
После цианирования детали охлаждают на воздухе, а затем закаливают с нагревом в соляной ванне или печи и подвергают низкотемпературному отпуску. Структура цианироваиного слоя после закалки такая же, как цементованного.
Глубокое цианирование применяют на некоторых заводах вместо цементации.
Диффузионное насыщение металлами и неметаллами (бором и кремнием)
Насыщение железа (стали) металлами, а также кремнием и бором повышает жаростойкость, коррозионную стойкость, износостойкость и твердость.
Поверхностное насыщение стали металлами, а также такими элементами, как кремний и бор, проводят при температуре 900—1050 С упаковкой изделий в соответствующие порошкообразные смеси (обычно ферросплавы и 0,5—5 % NH4Cl), погружением их в расплавленный металл, или насыщением из газовой среды. При газовом методе чаще применяют летучие хлористые соединения металлов (А1Сl3, СrСl2, SiCl4 и т. д.), образующиеся при воздействии хлора на металлы или их сплавы с железом при высоких температурах. Хлориды взаимодействуют с железом, и выделяющийся в атомарном состоянии металл диффундирует в железо. Насыщение металлами (например, хромом) проводят и путем испарения диффундирующего элемента в вакууме. Продолжительность процесса обычно 6—12 ч.
Алитирование. Алитированием называется насыщение поверхности стали алюминием. В результате алитирования сталь приобретает высокую окалиностойкость (до 850— 900 °С), так как в процессе нагрева на поверхности алитированных изделий образуется плотная пленка оксида алюминия А12О3, предохраняющая металл от окисления. Алитированный слой обладает также хорошим сопротивлением коррозии в некоторых средах.
Алитированный слой представляет собой твердый раствор алюминия в α-железе. Концентрация алюминия в поверхностной части слоя составляет примерно 40 %; толщина 0,2—1,0 мм.
Хромирование стали. Хромирование, т.е. насыщение поверхности стальных изделий хромом. Обеспечивает повышенную устойчивость против газовой коррозии (окалиностойкость) до 800 °С, высокую коррозионную стойкость в таких средах, как вода, морская вода и азотная кислота. Хромирование высокоуглеродистых сталей повышает твердость и износостойкость.
Диффузионный слой, получаемый при хромировании технического железа, состоит из раствора хрома в α-железе. При хромировании стали слой состоит из карбидов хрома (Cr, Fe)7C3, (Сr, Fе)23С6. Твердость хромированного слоя, полученного хромированием железа, составляет HV 250—300, а стали HV 1200—1300. Толщина слоя не превышает 0,10—0,20 мм.
Хромированию подвергают детали паросилового оборудования, пароводяной арматуры, клапанов, вентилей, патрубков, а также деталей, работающих на износ в агрессивных средах.
Цинкование, т. е. насыщение поверхностного слоя цинком. Применяют для повышения коррозионной стойкости стали в атмосфере, пресной воде, бензине и некоторых других средах. Слой состоит из химических соединений FeZn7, FeZn3, к сердцевине прилегает α-фаза (твердый раствор цинка в α-железе). На металлургических заводах цинкованию подвергают тонкие листы, трубы, проволоку и готовые изделия (втулки, фитинги и т. д.).
Силицироеание. Силицированием называется насыщение поверхности стали (чугуна) кремнием. В результате силицирования сталь приобретает высокую коррозионную стойкость в морской воде, в азотной, серной и соляной кислотах и несколько повышенную устойчивость против износа.
Силицированиый слой представляет собой твердый раствор кремния в α-железе. Силицированный слой обладает повышенной пористостью.
Силицироваиию подвергают детали, применяемые в оборудовании химической, бумажной, нефтяной промышленности.
Борирование, т. е. насыщение поверхностного слоя бором. Создает высокую твердость (HV 1800—2000), износостойкость и устойчивость против коррозии в различных средах.
Борироваикый слой на поверхности состоит из борида FeB и ниже из борида Fe2B и α-твердого раствора.
Борирование применяют для повышения износостойкости втулок грязевых нефтяных насосов. Стойкость указанных деталей после борироваиия возрастает в 2—6 раз.
Поверхностная закалка стали
Основное назначение поверхностной закалки: повышение твердости, износостойкости и предела выносливости обрабатываемого изделия.
При поверхностной закалке, на заданную глубину, закаливается только поверхностный слой металла, тем самым приобретая износостойкую структуру и повышенную твердость, а сердцевина изделия остается незакаленной, сохраняет вязкость и воспринимает ударные нагрузки.
В практике применяют поверхностную закалку с индукционным нагревом током высокой частоты (ТВЧ) для мелких и средних деталей, а для крупных деталей применяют поверхностную закалку с нагревом газовым пламенем.
Закалка с индукционного нагрева. Индукционный нагрев происходит вследствие теплового действия тока, индуктируемого в изделии, помещенном в переменное магнитное поле.
Переменный ток, протекая через индуктор, создает переменное магнитное поле. За счет индукции в поверхностном слое возникают вихревые токи, и в слое некоторой толщины обрабатываемого изделия происходит выделение джоулева тепла. Плотность индуктированного переменного тока наибольшая в поверхностном слое (скин или поверхностный эффект. Это явление называется поверхностным эффектом. Толщину слоя x (в см), который достигнет заданной температуры за время нагрева ТВЧ можно определить по формуле:
где ρ – электросопротивление, Ом·см ;
μ – магнитной проницаемости, Гс/Э;
f – частота электрического тока, Гц.
Глубина закалки примерно равна глубине нагрева до температуры выше критической точки; глубинные слои детали нагреваются ниже критических точек и при охлаждении не упрочняются.
Глубина проникновения тока увеличивается с повышением температуры и наиболее резко возрастает при температуре, лежащей выше точки Кюри (768 °С), вследствие резкого уменьшения магнитной проницаемости при переходе стали из ферромагнитного в парамагнитное состояние. Одновременно уменьшается скорость нагрева, что нужно учитывать при установке режима нагрева. Скорость нагрева в области температур фазовых превращений (А1 и А3 для доэвтектоидной стали) составляет 30—300 °С/с.
Для закалки при поверхностном нагреве применяют сравнительно большую удельную мощность (5— 20 МВт/м2), и поэтому время нагрева незначительно 2—50 с.
С увеличением глубины закаливаемого слоя частота тока должна уменьшаться, например для получения слоя толщиной 1,0 мм частота тока составляет 50—60 кГц, для слоя 2,0 мм ~15 кГц и для слоя 4,0 мм ~4 кГц.
Толщина закаленного слоя обычно составляет от 2—3 до 5—8 мм и более. Поэтому частоту тока чаще принимают 2,5— 8 кГц. Слой толщиной до 3—5 мм можно получить и на радиочастотах путем удлинения цикла нагрева; в этом случае тепло поступает за счет теплопроводности.
Как источник электропитания эклектические генераторы разных типов (электромеханические или машинные, электронные). В зависимости от типа отличается диапазон частот и мощность. ТВЧ закалку осуществляют на специальных установках, которые обычно механизированы и автоматизированы.
Следует отметить, что при больших скоростях нагрева превращение перлита в аустенит сдвигается в область высоких температур. Поэтому температура закалки при индукционном нагреве выше, чем при нагреве в печах, где скорость нагрева не превышает 1,5—3,0 °С/с.
Так, при печном нагреве температура закалки стали с 0,4 % С составляет 840—860 °С, при индукционном нагреве со скоростью нагрева 250 °С/с 880—920 °С, а при 500 °С/с 980—1020 °С.
Охлаждающую жидкость (воду, эмульсию) для закалки обычно подают через душевое устройство — спрейер.
После закалки с индукционным нагревом изделия подвергают низкому отпуску при 160—200 °С, нередко и самоотпуску. В этом случае при закалке охлаждение проводят не до конца, и в детали сохраняется некоторое количество тепла, нагревающего закаленный слой до температур отпуска.
Для поверхностной индукционной закалки применяют стали, содержащие 0,4—0,5 % С, после закалки они имеют высокую твердость (HRC 55—60), сопротивляемость износу и не склонны к хрупкому разрушению.
В случае глубинной ТВЧ закалки нагрева до надкритических температур больше, чем глубина закалки (прокаливаемость). Детали, имеющие тонкое сечение, нагреваются насквозь. Глубина закалки, таким образом, определяется не глубиной нагрева, а прокаливаемостью стали. Поэтому для поверхностной закалки применяемая сталь должна прокаливаться на меньшую глубину, чем глубина нагрева, после закалки на поверхности образуется мартенсит (HRC 60), а в сердцевине — сорбит или троостит, что значительно упрочняет ее. Для глубинного нагрева используют специально разработанные стали пониженной и регламентированной прокаливаемости. Например сталь пониженной прокаливаемости 55ПП, содержащей 0,55—0,63 % С и — 0,5 % примесей (Si, Mn, Cr, Ni и др.) и регламентированной прокаливаемости 47ГТ содержащей (0,44—0,51 % С; 0,9—1,2 % Мп; 0,06—0,12 % Ti).
Необходимость нагрева на большую глубину требует невысокой концентрации энергии в зоне нагрева, поэтому удельная мощность составляет 0,05— 0,2 кВт/см2, скорость нагрева в области температур фазовых превращений составляет 2—10 °С/с, время нагрева 20—100 с. Частота тока 2,5—10 кГц.
После закалки с индукционного нагрева действительное зерно аустенита значительно мельче, чем при обычной закалке с печным нагревом.
При поверхностной закалке, в том числе и с глубинным нагревом, сильно повышается сопротивление усталостному разрушению. Предел выносливости повышается на 80—100 % при испытании образцов с надрезом и на 25—30 % при испытании гладких образцов.
Индукционный нагрев позволяет сократить длительность термической обработки, увеличить производительность труда, получить изделия без окалины, уменьшить деформацию и коробление. Так же индукционная закалка создает условия для автоматизации процесса и обеспечивает возможность выполнения термической обработки непосредственно в поточной линии механической обработки без разрыва технологического цикла. Закалка с индукционного нагрева находит широкое применение. Детали подвергаемые закалке с ТВЧ различные шестерни, колеса и тормозные шкивы, различные цилиндрические детали и т. д.).
Закалка с газопламенным нагревом.Этот способ закалки применяют для крупных изделий (прокатных валков, валов и т. д.). Поверхность детали нагревают газовым пламенем, имеющим высокую температуру (2400—3150 °С). Вследствие подвода значительного количества тепла поверхность изделия быстро нагревается до температуры закалки, тогда как сердцевина детали не успевает нагреться. Последующее быстрое охлаждение обеспечивает закалку поверхностного слоя.
Толщина закаленного слоя обычно составляет 2—4 мм, а его твердость HRC 50—56. В тонком поверхностном слое образуется мартенсит, а в нижележащих слоях троосто-мартенсит. Пламенная закалка вызывает меньшие деформации, чем объемная, и из-за большой скорости нагрева сохраняет более чистую поверхность.
Поверхностная закалка при нагреве лазером.Лазеры — оптические квантовые генераторы — позволяют получить очень высокую концентрацию энергии. Применение лазеров для термической обработки основано на трансформации световой энергии в тепловую. Закалка при нагреве лазером проводится при удельной мощности 103—5·104 Вт/см2 при времени воздействия на поверхность ~102 с. Используются технологические лазеры импульсного и непрерывного действия. При импульсном излучении воздействие осуществляется в точке, при непрерывном — в полосе шириной до 3 мм.
Поэтому для обработки поверхности необходимо передвигать луч с взаимным перекрытием или без перекрытия предварительно упрочненных зон. Лазерная обработка обеспечивают высокую производительность, равномерность упрочнения и позволяют обрабатывать профиль поверхности со скоростью 100—10 000 мм/мин. Толщина закаленного слоя составляет 0,3—1,0 мм. Закалка нагретых участков осуществляется путем интенсивного отвода тепла в глубь обрабатываемого изделия. Скорость охлаждения при нагреве без оплавления (5—10)-103 °С/с, а в зоне расплавления до 106 °С/с, что значительно больше скорости охлаждения при обычной закалке.
Закалка при нагреве лазером — применяется для упрочнения сложных изделий, долговечность которых лимитируется износостойкостью и усталостной прочностью, когда закалка другими методами затруднена.
Дата добавления: 2020-11-29; просмотров: 354; Мы поможем в написании вашей работы! |
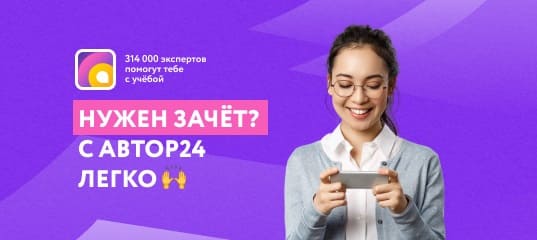
Мы поможем в написании ваших работ!