Подкладочные скрепления подразделяются на раздельные, нераздельные и смешанные.
Дата 20.10.2020г Группа 3СПХ-3-18
МДК.03.01 Устройство железнодорожного пути
Преподаватель Слободчикова С.В.
Тема: Промежуточные рельсовые скрепления.
Назначение, виды и конструкция для деревянных шпал.
Цель занятия:
1. Образовательная: изучить основные понятия, формирование теоретических знаний, умений систематизировать и применять знания, формирование навыков упрочнения знаний и умений;
2. Воспитательная: воспитание самостоятельности, внимательности, коллективного сотрудничества; формирование ориентации студентов на высокий уровень профессиональной подготовки специалистов среднего звена;
3. Развивающая: развитие познавательного интереса к дисциплине, активности, памяти, способности выражать мысли.
Вопросы к рассмотрению:
1.Назначение, виды, требования.
2. Конструкция промежуточных рельсовых скреплений для деревянных шпал
1 Назначение, виды, требования.
Скрепления служат для прикрепления рельсов к подрельсовому основанию, восприятия нагрузок от подвижного состава вместе с другими элементами верхнего строения пути.
ТРЕБОВАНИЯ К ПРОМЕЖУТОЧНЫМ СКРЕПЛЕНИЯМ
- стабильность ширины колеи;
Требование обеспечения стабильности ширины колеи важно и очевидно, оно прямо связано с обеспечением безопасности движения поездов из условия недопущения провала колес.
|
|
- прижатие рельсов к основанию, исключающее отрыв и угон рельсов;
Нарушение требования по обеспечению достаточности прижатия рельсов к основанию приводит к отрыву рельсов от шпал при укладке или разборке пути, а также при его подъемке при проведении выправочных работ. Обусловлено это гниением деревянных шпал, разрушением дюбелей, недостаточной прочностью и коррозией прикрепителей на железобетонных основаниях.
Угон рельсов приводит к изменению их напряженно-деформированного состояния, что может вызвать выброс пути при повышении температуры и разрыв стыков при ее понижении. Угон пути приводит к смещению и перекосу шпал, выпадению подрельсовых прокладок. Ликвидация последствий угона рельсов сопряжена с выполнением сложных и трудоемких работ по регулировке зазоров и разрядке температурных напряжений в рельсовых плетях.
- оптимальные условия температурной работы рельсов;
Требование оптимизации температурной работы рельсов также связано с величиной усилий прижатия их к основанию. Исключить температурные деформации рельсов очень сложно, так как это вызывает усложнение конструкции пути, удорожание рельсовых скреплений. Недостаточное же прижатие рельсов к основанию вызывает чрезмерные деформации концевых участков рельсовых плетей, усложнение конструкции стыковых скреплений, быстрый износ промежуточных скреплений, нарушение равноупругости основания из-за перемещения шпал.
|
|
- проведение регулировки положения рельсов по высоте и ширине колеи, замену деталей скреплений без перерывов в движении поездов;
Проведение регулировки положения рельсов по высоте особенно важно на железобетонных подрельсовых основаниях и в зимнее время. В условиях высокой грузонапряженности в пути быстро накапливаются остаточные деформации, происходит нарушение проектного положения рельсов. Выправка пути с применением шпалоподбивочной техники сложна в организации, требует перерывов в движении поездов, поэтому использование регулировочных прокладок для выправки пути весьма целесообразно. В зимнее время на участках пучинообразования применение регулировочных прокладок является единственным способом исправления пути по уровню и в профиле.
- механизированную сборку и содержание узлов скреплений;
В современных условиях, когда сборка и разборка рельсошпальной решетки ведется на базах с применением поточных линий, требование о необходимости механизации работ по сборке и разборке узлов скреплений совершенно справедливо. Необходимость механизации работ по смене рельсов, замене изношенных элементов скреплений, регулировке натяжения прикрепителей при текущем содержании пути также не вызывает сомнений.
|
|
- рациональную пространственную упругость и вибростойкость узлов скреплений;
Обеспечение рациональной пространственной упругости рельсовых скреплений чрезвычайно необходимо для того, чтобы упруго перерабатывать динамические воздействия колес подвижного состава на рельсы, гасить высокочастотные вибрации, расстраивающие путь и особенно его болтовые соединения, а также для того, чтобы создавать равноупругость подрельсового основания.
Упругость, создаваемая скреплениями, отделяет массу рельса от подрельсового основания аналогично тому, как рессоры отделяют кузов экипажа от его ходовых частей. Это существенно снижает силы инерции, образующиеся при движении колес по неровностям пути. Однако при большой вертикальной и горизонтальной упругости опор увеличивается статический изгиб рельсовых нитей под колесной нагрузкой, увеличивается также поворот поперечных сечений рельсов, создающий угоняющий эффект. Этим и объясняется существование понятия оптимальной пространственной упругости пути, при которой взаимодействие пути и подвижного состава будет наилучшим, а напряжения, деформации и накопления последних будут минимальными. Кроме того, неизменная упругая связь элементов скреплений с рельсами, подрельсовыми опорами и друг с другом с заданным натяжением необходима для обеспечения нормальной работы скреплений, предотвращения неупругих колебаний элементов и связанных с этим расстройств узлов скреплений.
|
|
Передача боковых сил на бетон должна осуществляться через упругие амортизаторы (прокладки, подклеммники), обеспечивая при этом величины удельных давлений на них в допускаемых пределах: при нашпальных прокладках из резины усилие прижатия подкладки к железобетонной шпале должно быть не менее 20 кН на один болт.
Скрепления железобетонных шпал должны обеспечивать возможность регулировки положения рельсов по высоте в пределах 10-20мм. Прокладки-регуляторы должны изготавливаться из жестких материалов. Их типоразмеры должны обеспечивать уклоны отводов при исправлении пути в соответствии с действующими нормативами.
Для использования в бесстыковом пути рельсовые скрепления должны создавать монтажное натяжение прикрепителей, обеспечивающее погонное сопротивление продольным перемещениям рельсов не менее 25 кН/м.
На звеньевом пути в целях предотвращения угона рельсов необходимо, чтобы погонное сопротивление продольным перемещениям было не менее 15 кН/м. Если сила прижатия рельса с учетом коэффициента трения между рельсом и основанием недостаточна, то необходимо предусматривать дополнительные противоугонные устройства (противоугоны).
- электроизоляцию рельсов от основания:
На участках с автоблокировкой скрепления для железобетонных шпал должны обеспечивать электрическую изоляцию рельсов от шпал с сопротивлением не ниже 1 Ом на километр пути.
- экономическую эффективность конструкции верхнего строения пути.
Требование к скреплениям о необходимости обеспечения экономической эффективности конструкций пути очевидно.
Скрепления должны способствовать достижению высоких сроков службы всех элементов пути (в частности, они сильно влияют на сроки службы деревянных шпал) и оптимальных условий их эксплуатации.
КЛАССИФИКАЦИЯ ПРОМЕЖУТОЧНЫХ СКРЕПЛЕНИЙ
Промежуточные рельсовые скрепления по своей конструкции делятся на подкладочные и бесподкладочные (без металлических подкладок под рельсами). Подкладки обеспечивают большую площадь передачи давления от рельса на опору, подуклонку рельсов без затески деревянных шпал, объединяют все прикрепители при работе на сдвиг и имеют большое распространение на всех дорогах мира.
Промежуточные скрепления делятся еще на две группы в зависимости от того, обладают они или не обладают противоугонными свойствами.
Первая группа — это непротивоугонные скрепления, у которых прикрепители не создаютдостаточного нажатия на подошву рельса и тем самым не обеспечивают необходимой продольной связи рельса соснованием. При применении этих скреплений необходима установка на подошву рельса дополнительных приспособлений,препятствующих продольной сдвижке рельса, — противоугонов.
Ко второй группе скреплений относятся противоугонные конструкции, у которых с помощью упругих элементов создается необходимое нажатие на подошву рельса, исключающее его проскальзывание по опорам под проходящими поездами.
В свою очередь вторая группа делится на две подгруппы: болтовые и безболтовые скрепления.
В первом случае натяжение прикрепителей, а следовательно их нажатие на подошву рельса, можно регулировать подтягиванием гаек клеммных болтов. В безболтовых скреплениях монтажное нажатие закладных упругих элементов должно оставаться неизменным в течение всего периода эксплуатации.
Подкладочные скрепления подразделяются на раздельные, нераздельные и смешанные.
В раздельном скреплении рельс к подкладке и подкладка к опоре прикрепляются разными прикрепителями.
В нераздельном скреплении рельс через подкладку соединяется с опорой одними и теми же прикрепителями.
В смешанном скреплении рельс через подкладку соединяется с опорой, а подкладка, кроме того, самостоятельно прикрепляется к опоре.
2 СКРЕПЛЕНИЯ ДЛЯ ДЕРЕВЯННЫХ ШПАЛ
Одной из самых распространенных конструкций скреплений для деревянных шпал на отечественных дорогах является подкладочное костыльное скрепление смешанного типа ДО (рисунок 1,2)
Рисунок 1 - Промежуточное смешанное скрепление ДО для деревянных шпал: 1 — костыль основной; 2 — костыль обшивочный
Рисунок 2 Скрепление ДО в пут
и
К достоинствам скреплений ДО относятся:
· малодетальность,
· сравнительно небольшой расход металла,
· простота в изготовлении и эксплуатации.
Однако это скрепление не обеспечивает упругую связь рельса со шпалой и плохо сопротивляется угону пути. Основными элементами этого скрепления являются клинчатая ребордчатая подкладка и костыли, которые подразделяются на основные и обшивочные.
Основные костыли прижимают подошву рельса к подкладке и шпале, удерживают рельс от бокового сдвига и опрокидывания (на опрокидывание работает один внутренний костыль, на сдвиг, как правило, — все), а обшивочные прижимают подкладку к шпале, уменьшая ее вибрацию, и воспринимают сдвигающие усилия.
При применении скреплений ДО на прямых и в кривых радиусом более 1200 м рельсы пришивают на каждом конце промежуточной шпалы четырьмя костылями, а на стыковой — пятью. В кривых радиусом 1200 м и менее, а также на мостах, в тоннелях и на участках со скоростями движения свыше 120 км/ч на всех шпалах рельсы пришивают пятью костылями.
Расчеты и опыт эксплуатации скреплений ДО показывают, что устойчивость рельса против опрокидывания при эпюре шпал 1600 шт./км и более обеспечивается лучше, чем устойчивость на отжатие рельсовой нити. Случаи опрокидывания рельсов с выдергиванием костылей редки и происходят только при провале колес. Случаи же отжатия рельсовых нитей довольно часты, вследствие чего перешивка пути при костыльных скреплениях на деревянных шпалах является одной из распространенных путевых работ, особенно в кривых.
Нормальные костыли (рисунок 3) имеют овальную головку, а удлиненные (пучинные) — призматическую с ушками. Длина нормальных костылей — 165 мм, масса — 0,378 кг. Длина пучинных — 205, 240 и 280 мм. Сопротивление выдергиванию нормального костыля из новой сосновой шпалы равно примерно 20 кН.
Рисунок 3 Костыли
Костыль, забиваемый в шпалу без предварительного просверливания отверстия, перерубает волокна и, погружаясь в шпалу, надламывает их, вследствие чего его сопротивление выдергиванию уменьшается примерно на 30 %, а сопротивление отжатию — на 16 % по сравнению с сопротивлением при забивке в предварительно просверленные отверстия. Чтобы уменьшить разрушающее действие костылей, в шпалах предварительно сверлят и антисептируют отверстия глубиной 130 мм и диаметром 12,7 мм, т. е. несколько меньше поперечных размеров костыля (16x16 мм) в шпалах из мягких пород (сосна, ель, пихта) и диаметром 16 мм в шпалах из твердых пород (бук, береза, лиственница).
Ширина подкладки к рельсам Р65 и Р75 (рисунок 4, 5) меньше ширины верхней постели шпалы и составляет 170 мм. Для того чтобы уменьшить вероятность образования трещин в шпалах, костыльные отверстия смещены одно относительно другого так, что на одной прямой, параллельной продольной оси шпалы, находится не более одного костыля. Ни одно отверстие не совпадает с продольной осью шпалы. На кривых участках пути радиуса от 800 до 501 м по наружной нити укладывают несимметричные удлиненные в наружную сторону подкладки (см. рисунок 4, б), а на кривых радиуса 500 м и менее такие подкладки используют под обеими рельсовыми нитями. Делают это для большей равномерности передачи давления от рельса на шпалу, имея в виду значительные горизонтальные поперечные силы, действующие в кривых.
Более равномерная передача давления на шпалы уменьшает неравномерность износа шпал под подкладками, увеличивает
срок их службы и обеспечивает более устойчивое состояние подуклонки рельсов.
Рисунок 4- Подкладки к рельсам Р65 и Р75:
а) для прямых и пологих кривых; б) для средних и крутых кривых
Рисунок 5 - Подкладка для скрепления ДО
Во избежание перерезывания волокон древесины подкладкой, их изготавливают с закругленными краями. В углах отверстий подкладок предусмотрены закругления радиусом до 2,5 мм для уменьшения концентрации напряжений при работе подкладок и увеличения срока службы пуансонов, применяющихся при изготовлении подкладок.
Для обеспечения нормальной работы рельса вогнутость поверхности прилегания подкладки к рельсу не допускается; выпуклость допускается не более 0,5 мм.
Недостатком скреплений (ДО) является также возможность некоторого перемещения подкладки вдоль и поперек шпалы.
Это вызывается наличием неизбежных производственных допусков по толщине костылей, размерам отверстий, а также по расстоянию между ребордами. Вибрация подкладок, происходящая вследствие сотрясений от динамического воздействия колес на рельсы, усиливает механический износ шпалы под подкладкой.
Для уменьшения интенсивности износа шпал между подкладкой и шпалой укладывают прокладки толщиной от 6 до 10 мм из резины, резинокорда, гомбелита (прессованные кордные нити, пропитанные смолой). Результаты измерения износа шпал показали, что при прокладках из резины интенсивность износа снижается от 2,7 (прессованные прокладки без рифления) до 3,7 раза (рифленые прокладки).
Вторым по применимости на дорогах является раздельное скрепление Д2(КД) (рисунок 6, 7), в котором рельс прижат к подкладке двумя клеммами. Клеммы прижимаются натяжением болтов, устанавливаемых сбоку в вырезы подкладок (рисунок 8). Между гайкой болта и клеммой ставят двухвитковую шайбу (рисунок9).
Подкладка к шпале прикреплена четырьмя шурупами (рисунок 10), под головку которых иногда устанавливаются двухвитковые шайбы. Под подошву рельса укладывают упругую прокладку.
Рисунок 6 – Раздельное скрепление Д2(КД):
1- двухвитковая шайба; 2- шуруп; 3- подкладка; 4- клемный болт; 5- жесткая клемма; 6- подрельсовая прокладка; 7-нашпальная прокладка.
Рисунок 7-Скрепление Д2(КД) в пути
Рисунок 8 Скрепление Д2 (КД)
Рисунок 9 Двухвитковая шайба
Рисунок 10 Наглядное изображение скрепления Д2 (КД)
Это скрепление в отличие от костыльного смешанного скрепления обеспечивает постоянное прижатие рельса к подкладке и не требует установки противоугонов. В случае отсутствия шайб под головками шурупов быстро разрабатываются отверстия в шпалах для шурупов под движущейся нагрузкой, и изгибающиеся рельсы начинают "таскать" за собой прочно прикрепляемые к ним подкладки, которые перетирают и сминают древесину шпалы так, что она может изнашиваться в 1,5—2 раза интенсивнее, чем при смешанном костыльном скреплении.
Рисунок 10 Шуруп
Шурупы применяемые в качестве прикрепителей, благодаря винтовой нарезке сопротивляются выдергиванию в 1,5—2 раза лучше, чем костыли. Однако сопротивление шурупов отжатию меньше, чем сопротивление костылей (50—60 % от сопротивления последних). Форма головки шурупа приспособлена для применения торцовых ключей для его завинчивания и отвинчивания. Шурупы, применяемые на стрелочных переводах, на 20 мм длиннее путевых.
Скрепления Д2 (КД) дают возможность регулировки положения рельсов по высоте до 10—14 мм за счет применения прокладок различной толщины.
Желательно, чтобы подрельсовые прокладки имели две реборды, свисающие с подкладок и препятствующие их выталкиванию при ослаблении клеммных болтов. Боковое воздействие колес подвижного состава на рельс, стремящееся его сдвинуть и повернуть, воспринимается скреплениями Д2 (КД) жестко.
Значительно рациональнее использовать раздельные скрепления не с жесткими, а упругими клеммами, примером которых являются скрепления Д4 (рисунок 11)
Рисунок 11 Раздельное скрепление Д4:
1-двухвитковая шайба; 2- шуруп; 3-подкладка; 4-клеммный болт; 5- клемма; 6 – подрельсовая прокладка; 7- прокладка под подкладку
В скрепленииД4 клеммный болт заводится в фигурный вырез в подкладке. Для фиксирования положения клемм в высоких ребордах подкладки предусмотрены вырезы. Скрепление Д4 позволяет производить регулировку положения рельсов по высоте до 14 мм за счет изменения толщины подрельсовых прокладок. Во избежание смятия древесины под подкладки укладывают резиновые или резинокордовые прокладки.
К достоинствам раздельных скреплений следует отнести:
- сведение к минимуму вибраций подкладок;
- возможность регулировки положения рельсов по высоте;
- возможность смены рельсов без вывинчивания шурупов;
-сильное прижатие рельсов к подкладкам, что обеспечивает достаточное сопротивление угону и температурным деформациям рельсов.
Дата добавления: 2020-11-23; просмотров: 295; Мы поможем в написании вашей работы! |
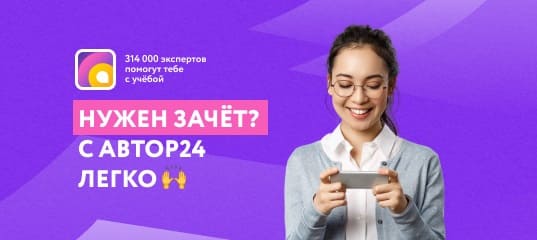
Мы поможем в написании ваших работ!