Назначение прессо-выдувного оборудования.
Данное задание необходимо выслать 2020г
Тема 1.30. Выдувные и прессовыдувные стеклоформующие
Источники : В.С.Севостьянов и др. стр.244 — 259
Задания
Внимательно прочитать текст лекции и разобраться со схемами и рисунками. Материал лекции скачать в электронный конспект.
2. Ответить на контрольные вопросы в конце лекции в печатном виде и выслать их на проверку.
Лекция
ВЫДУВНЫЕ И ПРЕССВЫДУВНЫЕ СТЕКЛОФОРМУЮЩИЕ МАШИНЫ
Выдувные и прессвыдувные стеклоформующие машины предназначены для изготовления из бесцветного и цветного стекла изделий бытового назначения (стаканов, вазочек, салатниц, тарелок, пепельниц, рюмок и др.).
Формование стеклянных изделий может осуществляться на ручных, полуавтоматических и автоматических прессах в металлических формах.
Наибольшее распространение получили полуавтоматические и автоматические прессы, которые снабжаются стекломассой с помощью питателей, работающих синхронно с прессами..
По способу питания стекломассой формующие машины делятся на машины с капельным и вакуумным питанием.
По характеру источника движения машины бывают пневматические, в которых привод машины и ее основных рабочих органов осуществляется сжатым воздухом, и механические, работающие от электродвигателей и механических устройств (рычагов, слайдеров и т. д.).
По способу изготовления изделий машины делятся на прессовые, вырабатывающие изделия в один прием — прессованием, прессовыдувные, в которых пулька оформляется прессованием, а изделие из нее — выдуванием, выдувные, в которых пулька и изделие из нее выдуваются сжатым воздухом.
|
|
По расположению и направлению технологического процесса выработки машины бывают трех типов: карусельные, секционные и конвейерные.
Полуавтоматический пресс ПСП 2
Однопозиционный полуавтоматический пресс ПСП-2 (рис. 1) состоит из литой станины 2, расположенной на четырех колесах станины 7, на которой установлены две вертикальные стойки 8.
Рис1.Полуавтоматический пресс пресс ПСП 2
Последние соединены в верхней части траверсой 7, на которой закреплен прессующий цилиндр 6. На штоке цилиндра расположен механизм пуансона 9 с формовым кольцом 10.
С помощью рукоятки 3 через систему рычагов 4 и золотниковое устройство 5 происходит ручное управление прессом.
Давление сжатого воздуха перед ресивером составляет 0,4 МПа, в ресивере — 0,1—0,35 МПа, усилие на штоке поршня — 12,5— 30 кН, ход поршня — (100—350) • 10-3 м, расход воздуха, подаваемого компрессором за двойной ход поршня, — 0,1 м3/мин.
Пресс обслуживают прессовщик и наборщик стекломассы. Наборщик специальной железной трубкой набирает необходимое количество стекломассы и подает строго в центр формы с предварительно положенным на нее формовым кольцом. Прессовщик отрезает ножницами необходимую порцию стекла. Затем форму со стеклом подают под пуансон — и происходит прессование изделия.
|
|
Прессующее усилие создается за счет подачи редуцированного воздуха в цилиндр, а далее — через шток поршня и прессующий пуансон усилие передается формуемой стекломассе. Отпрессованное изделие охлаждается нагнетаемым под давлением 1800—2000 Па (180—200 мм вод. ст.) воздухом и направляется на отжиг. После прессования форма передвигается на позицию разгрузки.
При прессовании обеспечивается постоянная температура прессующего узла: формы, пуансона и кольца.
Прессовыдувание
Прессовыдувание представляет собой способ формования, в котором совмещены процессы прессования и выдувания сжатым воздухом.
Рассмотрим работу прессовыдувной машины (рис. 2).
Основные формующие элементы машины: формы — черновая 1 и чистовая 7, пуансон 3, горловое кольцо 6 и ограничительное кольцо 4. Вначале прессования (рис. 2, а) черновая форма 1 поднимается и принимает каплю стекломассы 2. На следующем этапе (рис. 2, б) пуансон 3 с ограничительным кольцом 4 опускается и выпрессовывает пульку 5. Далее черновая форма опускается, а пулька остается висеть в горловом кольце 6 (рис. 2, в). Затем чистовая форма 7 смыкается, охватывая пульку 5 (рис. 2, г), после чего опускается дутьевая головка 8 и происходит выдувание изделия (рис. 2, д). Наконец, раскрывается чистовая форма, готовое изделие остается на поддоне чистовой формы (рис. 2, е) и затем переносится отставителем на конвейер, транспортирующий изделия в отжигательную печь.
|
|
Способом прессовыдувания изготовляют толстостенные полые изделия в основном с горлом диаметром более 30 мм. Диаметры изделий от 30 до 170 мм, высота от 50 до 290 мм, вместимость от 100 до 5000 мл.
На стекольных заводах используются преимущественно автоматические прессовыдувные машины ПВМ-12, 2ПВМ-12, 2ПВМ-3 и ЗПВМ-12 левого и правого вращения.
Автомат ПВМ-12 снабжен 12 черновыми и 12 чистовыми формами, которые расположены на вращающемся карусельном столе.
Цикл формования изделия начинается с момента падения капли стекломассы в черновую форму и затем проходит этапы, показанные на рис.2.
Автоматы ПВМ-12 выпускают в двухъячейковом исполнении (2ПВМ-12), вследствие чего их производительность возросла до 60 шт/мин.
|
|
Автоматы ЗПВМ-12 и 2ПВМ в двухъячейковом исполнении предназначаются для изготовления стеклотары вместимостью до 3 л. Производительность автоматов 20—30 изд/мин.
Рис. 2. Технологическая схема прессовыдувания: а — е — последовательность операций; 1 — черновая форма, 2 — стекломасса, 3 — пуансон, 4, 6 — кольца, 5 — пулька, 7— чистовая форма, 8 — головка
Карусельные автоматы могут быть цикличными - с прерывистым вращением столов и роторными – с непрерывным вращением столов. Особенность карусельных автоматов – подача порции стекломассы непосредственно под очком питателя. Благодаря вращению столов под очко питателя подходят последовательно все формы автоматов. Это обстоятельство делает конструкцию автоматов сравнительно компактной и даёт возможность применять её в низких зданиях машинованных цехов. Карусельные автоматы могут иметь 6, 7, 8,10 и 12 форм. Формовые комплекты выпоняются одно - или двухместными. Существенным недостатком карусельных автоматов является необходимость полного останова при неисправности одного из узлов. К стеклоформующим карусельным автоматам относятся 2ЛАМ, АБ-6, ВВ-7, ВВ-12, 2ПВМ-12А, ПВМ-12А, 2ПВМ-3, 2-ЛАМ, АБ-6 (Россия), "Линч-10" и "Линч-16В" (США), "Руаран"-R-7 и S-10 (Бельгия).
На карусельных цикличных автоматах впервые стали изготовлять бутылки. Эти автоматы эксплуатируются и сейчас (2ЛАМ, АБ-6, "Линч-10", ПВМ-12). Автоматы данного типа могут работать при одно - или двухкапельном питании с 6 или 12 формами.
Рис. 3. Схема технологического процесса на карусельных машинах цикличного действия типа АБ-6:
/ — заполнение черновой формы и прессование горла; // — поворот черновой формы и предварительное выдувание пульки; /// — передача пульки в чистовую форму; IV—VI — выдувание изделия; VII — съем изделия; 1— капля стекломассы; 2 — керн; 3 — горловое кольцо; 4 — прессующая головка; 5 — дутьевая головка
На прессовыдувных машинах вырабатывают широкогорлую стеклянную тару. Эти машины изготовляют изделия в два приема: сначала впрессовывают предварительную заготовку (пульку) и окончательно оформляют горло тары, а затем пульку раздувают сжатым воздухом до размеров и формы готового изделия.
На стекольных заводах работают автоматы ПВМ-12, 2ПВМ-12, 2ПВМ-3 и ЗПВМ-12 левого и правого вращения.
В черновую форму из питателя капля может подаваться свободным падением и по лотку. На позиции 1 (рис. 4) капля стекломассы поступает в черновую форму. Из капли после прессования в черновой форме получается пулька и оформляется горло тары (позиция 2). На позиции 3 пулька из черновой формы передается в чистовую. Уже на пути к позиции 3 Черновая форма опускается по наклонной направляющей, освобождая корпус пульки. Начиная с позиции 3, черновая форма идет понизу без стекла вплоть да позиции 12, где она поднимается для того, чтобы вступить в следующий цикл работы.
Пулька остается висеть в горловом кольце, держась в нем выступами горла. На пути между позициями 3 и 4 вокруг пульки закрывается чистовая форма. На позициях 4-6 происходит окончательное выдувание из пульки готового изделия с помощью трех дутьевых головок, которые в момент останова столов опускаются на горловые кольца и вдувают воздух в изделие. На позициях 7 и 8 закрепляется форма изделия — через открытое горло дополнительно вентилятором вдувается воздух. Между этими позициями специальная направляющая раскрывает горловое кольцо, обнажая горло изделия для охлаждения. На позиции 9 чистовая форма полностью открывается (предварительное открывание чистовой формы происходит между позициями 8 и 9).
Начиная с позиции 9, чистовая форма движется раскрытой до позиции 3 следующего цикла работы. На позиции 9 изделие вынимают из раскрытой чистовой формы отставителем и переносят на конвейер, ведущий к печи отжига.
Рис. 4. Схема последовательности технологических операций на машине ПВМ-12А правого вращения ( заштрихованной линией показан путь черновой формы,
сплошной линией — чистовой формы)
В роторных непрерывно вращающихся автоматах для выработки бутылок в отличие от автоматов цикличного действия предусмотрено двухэтажное размещение черновых и чистовых форм. Выдувные карусельные автоматы роторного типа R-7 и созданные на их базе автоматы ВВ-7 имеют по семь черновых и чистовых комплектов (рис. 5).
Рис. 5. Схема изготовления бутылки на автоматах R-7 иВВ-7:
0 -1 - подача капли в черновую форму;
2 - оформление горла с помощью вакуума; 3 - выдувание пульки;
4 - 5 - передачи в чистовую форму; 5-6 - выдувание бутылки;
7 — выдача готового изделия на охлаждающий стол
Процесс формования изделий заключается в следующем. Перед приемом капли черновую форму смазывают с помощью двух форсунок высокого давления. В момент подачи капли в горловой части черновой формы создается вакуум. Действие вакуума прекращается после выхода из горловой части металлического плунжера. За это время направляющая воронка отводится в сторону, а обращенную дном вверх черновую форму замыкает сверху донный затвор. Происходит выдувание пульки снизу вверх. Затем черновая форма открывается и пулька, повернувшись с горловыми кольцами на 180º, переходит на чистовой стол, где после раскрывания горловых колец производится выдувание изделия. Перед раскрыванием чистовой формы действие вакуума прекращается, отставитель захватывает изделие за горловую часть и устанавливает его на охлаждающий столик.
Охлаждающий столик с решеткой снизу предназначен для охлаждения изделий снаружи. В отличие от автомата он совершает прерывистое движение. На столике можно устанавливать устройства для внутреннего охлаждения изделий или для оплавления горла.
Формы автомата охлаждаются воздухом, который поступает от вентилятора в полую центральную колонну, а затем через специальные каналы подводится к регулируемым воздушным патрубкам.
Формование изделий на автомате (рис. 6) начинается с опускания черновой формы 1 с горловым кольцом в выработочную часть ванной печи. При контакте заборной части формы с расплавленной стекломассой под действием вакуума она засасывается в черновую форму. Одновременно керном выдувной головки оформляется горло изделия (позиция I). После подъема черновой формы "хвост" стекломассы отсекается ножом (позицияII) и в нее подается сжатый воздух для предварительного выдувания пульки. При раскрывании черновой формы пулька удерживается в горловом кольце (позиция III). Раскрытая чистовая форма 2 с поддоном 3 поднимается (позиция IV) и закрывается вокруг пульки, а через выдувную головку подается сжатый воздух (позиции V-VI). Затем горловые кольца раскрываются и готовое изделие в чистовой форме опускается для окончательного охлаждения. При раскрывании и подъеме чистовой формы готовое изделие попадает на приемный конвейер.
Рис.6 Формование изделий на автомате
Секционные автоматы. Секционные автоматы, состоят из отдельных секций, которые работают независимо друг от друга и представляют собой самостоятельные стеклоформующие автоматы.
Преимущества секционных автоматов перед карусельными:
• более высокий коэффициент использования: каждая секция может включаться и выключаться независимо от работы других секций;
• универсальность: при небольшой переналадке на них можно вырабатывать узко - и широкогорлую стеклянную тару, а также мелкие прессованные изделия;
• возможность одновременной выработки в каждой секции различных видов изделий одинаковой массы и с одинаковой продолжительностью формования; при этом время технологических операций в каждой секции можно регулировать в относительно широком диапазоне;
• отсутствие вращающихся столов с формами и, следовательно, исключение необходимости применения больших усилий на их вращение и торможение;
• минимальное число быстроизнашивающихся деталей;
• легкость и относительная безопасность обслуживания;
• возможность параллельной установки под одним питателем двух автоматов, что резко повышает производительность линий.
Недостатком, затрудняющим применение секционных стеклоформующих автоматов, является их большая высота. Для установки шестисекционного автомата необходимо, чтобы расстояние от пола машинного участка до уровня зеркала стекломассы в питателе составляло 3810— 4110 мм.
Способом двойного выдувания (рис. 7) вырабатывают узкогорлые изделия. В черновую форму, установленную горловой частью вниз, через направляющую воронку подается капля стекломассы (позиция I). Горловую часть формы в этот момент замыкают горловые формы и металлический плунжер. Капля стекломассы запрессовывается в горловую часть формы подаваемом сверху сжатым воздухом — происходит уплотнение пульки и формование горла (позиция II). В период выхода металлического плунжера из отверстия для начального дутья внутренняя часть горла разогревается теплом стекломассы. Подаваемый в отверстие сжатый воздух (позиция III) выдувает пульку и одновременно охлаждает металлический плунжер. После раздувания пульки черновая форма открывается и пулька, которую поддерживают закрытые горловые кольца, повернувшись на 180° (из положения горлом вниз в положение горлом вверх), подается в открытую чистовую форму (позиция IV). С момента открывания черновой формы и до момента начала выдувания в чистовой форме наружная часть пульки подогревается за счет тепла внутренних слоев стекломассы (позиции IV - V). В чистовой форме происходит окончательное чистовое выдувание изделия (возможно' применение системы вакуумного формования - позиция VI). Дутьевая головка чистового стола машины имеет устройство, которое позволяет совмещать процесс выдувания с процессом охлаждения изделия изнутри – продуванием (позиция VI). По данным некоторых зарубежных фирм, с помощью такого устройства можно повысить производительность машины на 10%. По окончании выдувания чистовая форма открывается, и отставитель хватками устанавливает изделие сначала на охлаждающий столик (позиция VII), а потом — на конвейер.
Рис. 7. Схема изготовления стеклянной тары на секционных автоматах
Конвейерные автоматы. Конвейерные автоматы относятся к новому типу высокопроизводительных машин со струйным и струйно-порционным питанием.
Формование изделий производится следующим образом. На позиции 1 (рис. 8, а) порция стекломассы подается в неразъемный стакан-поддон черновой формы. В позиции 2 закрываются половинки верхней части черновой формы, служащие для, формования плечиков пульки, и начинается прессование длинным плунжером, продолжающееся на позиции 3. К позиции 4 прессование пульки заканчивается, верхние половинки формы разводятся, и стакан-поддон опускается. Удерживаемая горловым кольцом пулька (позиция 5 к 6) переносится конвейером к столу чистовых форм. При движении пульки от стола черновых форм и столу чистовых форм происходят оттяжка и вторичный подогрев пульки. В зависимости от массы и вида вырабатываемых изделий этот путm можно удлинить или укоротить, передвигая стол чистовых форм относительно неподвижного стола черновых форм и меняя число горловых колец. На позициях 7 и 8 пулька охватывается половинками чистовой формы, после чего начинается выдувание изделия. На позиции 9 чистовая форма раскрывается, и готовое изделие переносится (позиция 10) до установки его на конвейере (позиция 11).
Рис 8. Схемы технологических процессов получения узкогорлых изделий прессовыдувным способом на машинах: а-Н.6-12; б-Н.1-2
Скорость выработки на автомате составляет 200—600 шт./мин.
Центробежное формование
В разъемную металлическую форму 1, укрепленную при помощи кольца. 2 на основании 3, подают порцию горячей стекломассы. Форма в зависимости от размеров, формуемого изделия вращается с частотой 800—1200 об/мин. Под действием центробежных сил стекломасса равномерно распределяется по стенкам формы, поднимается до верхнего ее обреза и принимает ее конфигурацию. При вращении формы внутреннюю, поверхность изделия омывает воздух, поэтому она получается гладкой и блестящей. Форма вращается до тех пор, пока стекломасса не затвердеет. При извлечении изделия кольцо снимают и форму открывают. Полученные таким путем изделия имеют дно, которое затем удаляют. Если основание формы сделать в виде конуса 4, а стекломассу направлять в пространство 5 между формой и конусом, получится тело вращения, открытое сверху и снизу.
Рис. 9. Устройство для центробежного формования: 1 — форма, 2 — кольцо, 3—основание, 4 — конус, 5 — пространство
Задание к теме 1.30
Ответьте на вопросы:
Назначение прессо-выдувного оборудования.
Дата добавления: 2020-11-23; просмотров: 277; Мы поможем в написании вашей работы! |
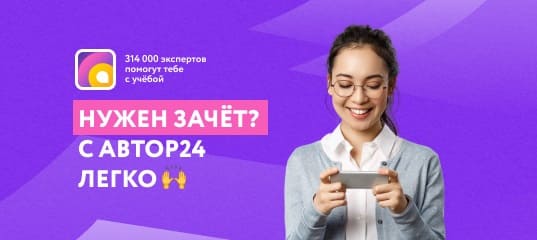
Мы поможем в написании ваших работ!