ПЕРЕЧЕНЬ ПРИМЕРНЫХ ДОПОЛНИТЕЛЬНЫХ ВОПРОСОВ, ПРЕДЛАГАЕМЫХ НА ЭКЗАМЕНЕ
Билет № 1
Вопрос 1. Преимущества и недостатки сварки перед другими способами соединения деталей, ее общая классификация и сущность.
Сварка является одним из выдающихся русских изобретений и впервые была освоена в нашей стране. Несомненно, Россия является лидером по количеству важных открытий в области науки и техники. Сейчас невозможно представить себе ни одной отрасли в хозяйстве или машиностроении, где бы не применялась сварка.
В 1802 г. русский академик Василий Владимирович Петров впервые в мире изучил и описал явление электрической дуги, возникающей при пропускании электрического тока через два стержня из угля и металла и имеющей очень высокую температуру; он также указал на возможность использования тепла электрической дуги для расплавления металлов.
Спустя 80 лет русские инженеры Николай Николаевич Бенардос и Николай Гаврилович Славянов разработали промышленные способы электрической сварки металлов.
Н.Н. Бенардос в 1882 г. изобрел способ дуговой сварки с применением угольного электрода. А после им были разработаны следующие способы сварки: дугой, горящей между двумя и несколькими электродами; в атмосфере защитного газа; контактной точечной сварки, с помощью клещей. А также изобрел ряд конструкций сварных автоматов, запатентовал много изобретений в области сварочного оборудования и процессов сварки.
Н.Г. Славянов в 1888 г. изобрел дуговую сварку плавящимся металлическим электродом. С помощью специально обученного коллектива сварщиков он исправлял дуговой сваркой брак литья, восстанавливал детали паровых машин и т. д. Он создал первый сварочный генератор и автоматический регулятор длины дуги, разработал флюсы, повышающие качество наплавленного металла.
Большой вклад в развитие сварки внес Институт электросварки имени Е.О. Патона, который в 1934 г. в Киеве организовал известный советский ученый, академик Евгений Оскарович Патон. Под его руководством коллектив института разработал новый прогрессивный метод автоматической дуговой сварки под слоем флюса, который начал применяться с 1940 г.
Сваркой называется процесс получения неразъемного соединения посредством установления межатомных связей между свариваемыми частями при их местном нагреве или пластическом деформировании, или совместным действием того и другого.
До появления сварки широко использовали клепочные и болтовые соединения. Применение сварки позволяет использовать самые разнообразные профили металла.
Межатомные связи могут устанавливаться только тогда, когда соединяемые атомы получат дополнительную энергию для преодоления существующего между ними определенного энергетического барьера. Эту энергию называют энергией активации. При сварке ее вводят извне путем нагрева (термическая активация) или пластического деформирования (механическая активация).
В зависимости от вида энергии при выполнении соединения различают два вида сварки: плавлением и давлением.
При сварке плавлением детали по соединяемым кромкам оплавляют под действием источника нагрева. Образуется общий объем жидкого металла при расплавлении двух кромок, называемый сварочной ванной. При охлаждении сварочной ванны жидкий металл затвердевает и образует сварочный шов.
Сущность сварки давлением состоит в непрерывном или прерывистом совместном пластическом деформировании материала по кромкам свариваемых деталей.
Именно вид энергии активации является основой физических признаков видов сварки, а их более 150 видов. По физическим признакам сварка классифицируется на три класса (сx. 1): термический, термомеханический, механический.
К термическому классу относят все виды сварки плавлением, осуществляемые с использованием тепловой энергии, - газовую, дуговую, электрошлаковую, электронно-лучевую, лазерную и др.
К термомеханическому классу относят все виды сварки, осуществляемые с использованием тепловой энергии и давления, - контактную, диффузионную, газо- и дугопрессовую, кузнечную и др.
К механическому классу относят все виды сварки давлением, осуществляемые с использованием механической энергии, — холодная, трением, ультразвуковая, взрывом и др.
|
|
|
|
Схема 1
|
|
Классификация сварки по физическим признакам
Сварка обладает рядом преимуществ, основные из которых следующие:
1. Экономия металла вследствие наиболее полного использования рабочих сечений элементов сварных конструкций, придания им более целесообразной формы, в соответствии с действующими нагрузками и уменьшения веса соединительных элементов.
2. Сокращение сроков работ и уменьшение стоимости изготовления конструкций за счет снижения расхода металла и уменьшения трудоемкости работ.
3. Возможность широкого использования сварки, наплавки и резки при ремонте, где эти способы обработки металла позволяют быстро и с наименьшими затратами восстанавливать изношенное, вышедшее из строя оборудование и разрушенные сооружения.
4. Возможность изготовления сварных изделий сложной формы из штамповочных и листовых элементов взамен ковки и литья.
5. Удешевление технологического оборудования, так как отпадает необходимость в дорогих сверлильных, дыропробивных станках и клепальных машинах.
6. Герметичность и надежность получаемых сварных соединений.
7. Уменьшение производственного шума и улучшение условий труда в цехах.
Сваркой можно получить сварное соединение прочностью выше основного металла. Поэтому сварку широко применяют при изготовлении ответственных конструкций, работающих при высоких давлениях и температурах, а также динамических (ударных) нагрузках, - паровых котлов, химических аппаратов высокого давления, мостов, самолетов, паровых турбин, гидросооружений, ракет, космических кораблей, искусственных спутников Земли и др.
Если говорить отдельно о газовой сварке, то недостатками ее являются:
1. Уменьшение производительности процесса с увеличением толщины свариваемого металла. Поэтому газовую сварку применяют в основном для металла толщиной до 10 мм.
2. Большая зона теплового воздействия на основной металл, что приводит к значительным короблениям свариваемых деталей.
К преимуществам газовой сварки относятся:
1. Простота способа и его универсальность.
2. Несложность оборудования.
3. Отсутствие источника электрической энергии.
|
|
Вопрос 2. Сварка трубных конструкций дуговой сваркой.
При сооружении трубопроводов сварные стыки труб могут быть поворотными, неповоротными и горизонтальными (рис. 1).
Рис. 1. Сварные стыки труб:
а – поворотный; б – неповоротный; в – горизонтальный
Перед сборкой и сваркой трубы проверяют на соответствие требованиям проекта, по которому сооружается трубопровод, и техническим условиям. Основными требованиями проекта, а также технических условий являются: наличие сертификата на трубы; отсутствие эллипсности труб; отсутствие разностенности труб; соответствие химического состава и механических свойств металла трубы требованиям, указанным в технических условиях или ГОСТах.
При подготовке стыков труб под сварку проверяют перпендикулярность плоскости реза трубы к ее оси, угол раскрытия шва и величину притупления. Угол раскрытия шва должен составлять 60-70°, а величина притупления - 2-2,5 мм (рис. 2). Фаски снимают с торцов труб механическим способом, газовой резкой или другими способами, обеспечивающими требуемую форму, размеры и качество обрабатываемых кромок.
Разностенность толщин стенок свариваемых труб и смещение их кромок не должны превышать 10% толщины стенки, но быть не более 3 мм. При стыковке труб должен обеспечиваться равномерный зазор между соединяемыми кромками стыкуемых элементов, равный 2-3 мм.
Перед сборкой кромки стыкуемых труб, а также прилегающие к ним внутренние и наружные поверхности на длине 15-20 мм очищают от масла, окалины, ржавчины и грязи.
Рис. 2. Подготовка кромок труб под сварку при толщине стенок 8-12 мм
Прихватки, являющиеся составной частью сварного шва, выполняют те же сварщики, которые будут сваривать стыки, с применением тех же электродов.
При сварке труб диаметром до 300 мм прихватка выполняется равномерно по окружности в 4 местах швом высотой 3-4 мм и длиной 50 мм каждая. При сварке труб диаметром более 300 мм прихватки располагают равномерно по всей окружности стыка через каждые 250-300 мм.
При монтаже трубопроводов необходимо стремиться к тому, чтобы по возможности больше стыков сваривалось в поворотном положении.
Количество слоев шва при дуговой сварке труб определяется толщиной стенок труб и их диаметром. При толщине труб свыше 8 мм и диаметре больше 300 мм, сварку ведут в четыре слоя (корневой, два основных, декоративный). В случае, когда толщина стенок трубы до 8 мм, сварку выполняют в два слоя сплошным швом.
По внешнему виду сварной шов должен иметь слегка выпуклую поверхность с плавным переходом к поверхности основного металла. Высота усиления шва должна быть одинаковой по всему периметру в пределах от 1 до 3 мм, ширина не должна превышать 2,5 толщины стенки труб.
Сварку труб малого диаметра и малой толщины стенки производят поворотным способом. В процессе сварки поворачивают трубу (рис. 3) в сторону, противоположную направлению сварки. Второй слой выполняют аналогично первому, но в противоположном направлении.
Сварка толстостенных труб. Трубы, толщина стенки которых составляет 8-12 мм, сваривают в три слоя плюс декоративный шов.
Рис. 3. Схема сварки стыка труб малого диаметра
Первый слой создает местный провар в корне шва и надежное сплавление кромок. Для этого необходимо, чтобы наплавленный металл образовал внутри трубы узкий ниточный валик высотой 1-1,5 мм, равномерно распределяющийся по всей окружности. Используют электроды диаметром 2-3 мм.
Для получения провара без сосулек и грата движение электрода должно быть возвратно-поступательным с непродолжительной задержкой электрода на сварочной ванне, незначительным поперечным колебанием между кромками и образованием небольшого отверстия в вершине угла скоса кромок. Отверстие получается в результате проплавления основного металла дугой. Размер его не должен превышать 2 мм – больше установленного зазора между трубами.
Второй и третий слой выполняют электродом диаметром 4-5 мм и при повышенном токе одним из следующих способов: поворотом трубы на 180° и поворотом трубы на 90°.
Поворот трубы на 180° (рис. 4).
1. Стык делят на четыре участка.
Вначале сваривают участки 1-2, после чего трубу поворачивают на 180° и заваривают участки 3 и 4 (рис. 4, а).
Рис. 4. Схема сварки стыка трубы:
а - второго слоя; б - третьего слоя
2. Трубу поворачивают еще на 90° и сваривают участки 5 и 6, затем поворачивают трубу на 180° и сваривают участки 7 и 8 (рис. 4, б).
В процессе сварки нужно следить, чтобы начало и конец шва не совпадали, перекрытие смежного слоя составляет 20-25 мм.
Поворот трубы на 90°.
Стык так же делят на 4 участка. В начале сваривают участки 1-2. Затем поворачивают трубу на 90° и сваривают участки 3-4 (рис. 5, а) После сварки 1-го слоя трубу поворачивают на 90° и сваривают участки 5-6, затем поворачивают на 90° и сваривают участки 7-8 (рис. 5, б).
Рис. 5. Схема сварки стыка трубы:
а - второго слоя; б - третьего слоя
Четвертый декоративный слой во всех рассмотренных выше способах накладывают в одном направлении при вращении трубы.
Трубы диаметром более 500 мм сваривают обратно-ступенчатым способом. Длина каждого участка зависит от диаметра трубы и составляет 150-300 мм (рис. 6).
Рис. 6. Схема сварки стыка труб большого диаметра:
а - первого слоя; б - второго слоя
3. Задача. Объясните и покажите, как проверяют работу инжектора горелки перед началом работы.
Для проверки инжектора горелки к кислородному ниппелю подсоединяют рукав от кислородного редуктора, а к корпусу горелки - наконечник. Наконечник затягивают ключом, открывают ацетиленовый вентиль и кислородным редуктором устанавливают необходимое давление кислорода соответственно номеру наконечника.
Пускают кислород в горелку, открывая кислородный вентиль. Кислород, проходя через инжектор, создает разрежение в ацетиленовых каналах и ацетиленовом ниппеле, которое можно обнаружить, приставляя палец руки к ацетиленовому ниппелю.
При наличии разрежения палец будет присасываться к ниппелю. При отсутствии разрежения необходимо закрыть кислородный вентиль, отвернуть наконечник, вывернуть инжектор и проверить, не засорено ли его отверстие.
При засорении его необходимо прочистить. При этом надо проверить также отверстия смесительной камеры и мундштука. Убедившись в их исправности, повторяют испытание на подсос (разрежение).
Билет № 2
Вопрос 1. Сварные соединения (виды, определение, достоинства, недостатки, применение).
Сварным соединением называют неразъемное соединение нескольких деталей, выполненное сваркой.
При сварке различают четыре вида соединений: стыковое, угловое, тавровое, нахлесточное.
Стыковое соединение имеет ряд преимуществ:
• неограниченная толщина свариваемых элементов;
• равномерное распределение напряжений при передаче усилий;
• минимальный расход металла на образование сварного соединения;
• удобство контроля качества шва.
Недостатки стыкового соединения: необходимость более точной сборки элементов под сварку.
Угловые и тавровые соединения используются при сварке балок, ферм, увеличивая жесткость конструкции. Они могут быть как односторонними, так и двусторонними. Угловые и тавровые двусторонние швы обладают высокой прочностью при статических нагрузках.
Нахлесточное соединение имеет преимущества перед другими соединениями:
• отсутствие скоса кромок под сварку;
• простота сборки соединения (возможность подгонки размеров за счет величины нахлестки).
Недостатки:
• повышенный расход основного металла на перекрытие в соединении. Нахлесточные соединения применяются для металла толщиной не более 6 мм. Величина нахлестки (перекрытия) должна быть не менее 3 толщин наиболее тонкого из свариваемых элементов. При сварке толщина нахлесточного соединения не должна превышать 12 мм;
• хуже работают на нагрузку;
• возможность проникновения влаги в щель между перекрытием;
• сложность определения дефектов сварки.
Вопрос 2. Сварочные редукторы (назначение, классификация, устройство, принцип действия, техника безопасности при эксплуатации).
При газовой сварке и резке металлов рабочее давление газов должно быть меньше, чем давление в баллоне или газопроводе.
Для понижения давления газа применяют редукторы.
Редуктором называется прибор, служащий для понижения давления газа, отбираемого из баллона до рабочего и для автоматического поддержания этого давления постоянным, независимо от изменения давления газа в баллоне или газопроводе.
Согласно ГОСТ 6268-78, редукторы для газопламенной обработки классифицируются:
• по принципу действия - на редукторы прямого и обратного действия;
• по назначению и месту установки - баллонный (Б), рамповый (Р), сетевой (С), центральный (Ц), универсальный высокого давления (У);
• по схеме редуцирования - одноступенчатый с механической установкой давления (О), двухступенчатый с механической установкой давления (Д), одноступенчатый с пневматической установкой давления (У);
• по роду редуцируемого газа - ацетиленовый (А), кислородный (К), пропан-бутановый (П), метановый (М).
Редукторы отличаются друг от друга цветом окраски корпуса и присоединительными устройствами для крепления их к баллону. Редукторы, за исключением ацетиленовых, присоединяются накидными гайками, резьба которых соответствует резьбе штуцера вентиля. Ацетиленовые редукторы крепят к баллонам хомутом с упорным винтом.
Принцип действия редуктора определяется его характеристикой. У редуктора прямого действия – падающая характеристика, т. е. рабочее давление по мере расхода газа из баллона несколько снижается, у редукторов обратного действия - возрастающая характеристика, т. е. с уменьшением давления газа в баллоне рабочее давление повышается.
Редукторы различаются по конструкции. Принцип действия и основные детали одинаковы для каждого редуктора.
Более удобны в эксплуатации редукторы обратного действия.
Редуктор обратного действии (рис. 7) работает следующим образом. Сжатый газ из баллона поступает в камеру высокого давления 8 и препятствует открыванию клапана 9. Для подачи газа в горелку или резак необходимо вращать по часовой стрелке регулирующий винт 2, который ввертывается в крышку 1. Винт сжимает нажимную пружину 3, которая, в свою очередь, выгибает гибкую резиновую мембрану 4 вверх. При этом передаточный диск со штоком сжимает обратную пружину 7, поднимая клапан 9, который открывает отверстие для прохода газа в камеру низкого давления 13. Открыванию клапана препятствует не только давление газа в камере высокого давления, но и пружина 7, более слабая, чем пружина 3.
Рис. 7. Схема редуктора обратного действия
Автоматическое поддержание рабочего давления на заданном уровне происходит следующим образом. Если отбор газа в горелку или резак уменьшится, то давление в камере низкого давления повысится, нажимная пружина 3 сожмется и мембрана 4 выпрямится, а передаточный диск 5 опустится, редуцирующий клапан 9 под действием пружины 7 прикроет седло клапана 10, уменьшив подачу газа в камеру низкого давления.
При увеличении отбора газа процесс будет автоматически повторяться. Давление в камере высокого давления 8 измеряется манометром 6, а в камере низкого давления 13 - манометром 11. Если давление в рабочей камере повысится сверх нормы, то с помощью предохранительного клапана 12 произойдет сброс газа в атмосферу.
В процессе эксплуатации редукторы окрашиваются в те же цвета, что и баллоны.. Необходимо следить, чтобы не произошло воспламенение редуктора из-за резкого открывания вентиля на баллоне, а также следить за техническим состоянием манометра.
3. Задача. Объясните причину и ваши действия в том случае, если при зажигании дуги она прилипает к металлу.
Прилипание дуги связано с несоответствием силы тока диаметру электрода. Сила тока мала. Необходимо правильно рассчитать силу тока и установить ее на источнике питания. Если источник питания не позволяет это сделать точно, то силу тока увеличивают опытным путем.
Билет № 3
Вопрос 1. Классификация сварных швов.
Часть сварного соединения, образовавшуюся в результате плавления кромок свариваемых металлов и электрода и непосредственно осуществляющую связь свариваемых частей, называют сварным швом.
Сварные швы классифицируют по:
• типу соединения;
• числу слоев, протяженности;
• расположению в пространстве;
• отношению к действующим усилиям (рис. 8).
Рис. 8. Виды сварных швов
По типу соединения швы делятся на стыковые и угловые.
Стыковые швы применяются при соединении частей металла встык, угловые - при выполнении тавровых, угловых и нахлесточных соединений.
Швы делятся на однослойные и многослойные. Однослойный шов выполняется за один проход, многослойный - за два прохода и более.
По протяженности сварные швы бывают непрерывные и прерывистые. Прерывистые характеризуются шагом шва.
По расположению в пространстве швы разделяют на нижние, вертикальные, горизонтальные и потолочные.
По отношению к действующим усилиям швы делятся на лобовые, фланговые, косые и комбинированные.
Вопрос 2. Контроль качества сварных швов (назначение, виды).
Внешний осмотр и обмеры сварных швов – наиболее простые и широко распространенные способы контроля их качества. Они являются первыми контрольными операциями по приемке готового сварного узла или изделия. Этим видам контроля подвергают все сварные швы независимо от того, как они будут испытаны в дальнейшем.
С помощью внешнего осмотра сварных швов выявляют наружные дефекты: непровары, наплывы, прожоги, подрезы, наружные трещины и поры, смещение свариваемых кромок деталей и т. п. Визуальный осмотр производят как невооруженным глазом, так и с применением лупы с увеличением до 10 раз.
Приступая к осмотру, сварной шов и прилегающую к нему поверхность основного металла на ширину не менее 20 мм по обе стороны шва очищают от шлака, брызг расплавленного металла, окалины и других загрязнений, которые могут затруднить проведение осмотра. Осматривать швы необходимо по всей их протяженности, а в случае недоступности – обязательно с двух сторон.
По результатам внешнего осмотра можно судить о местах расположения и характере внутренних дефектов. Например, подрез на одной из сторон шва и наплыв на другой указывают на возможный непровар по кромке. Непостоянная ширина шва часто является следствием неравномерной ширины зазора. В местах с малым зазором могут образоваться непровары, а с большим - прожоги. Перекосы и смещения кромок, а также большая высота шва могут быть причиной непроваров.
Обмеры сварных швов позволяют судить о качестве сварного соединения: недостаточное сечение шва уменьшает его прочность, слишком большое – увеличивает внутренние напряжения и деформации. Размеры сечения готового шва проверяют по его элементам в зависимости от типа соединения. У стыкового шва проверяют его ширину, высоту выпуклости и размер обратной подварки корня, в угловом шве (нахлесточное и тавровое соединения) измеряют катет. Замеренные величины должны соответствовать ТУ или ГОСТам. Размеры сварного шва контролируют обычными измерительными инструментами или специальными шаблонами. Набор шаблонов и его применение для контроля стыковых и угловых швов показаны на рис. 9. Каждый щуп набора представляет собой пластину с вырезами под определенный шов.
Внешний осмотр и обмеры сварного шва не дают возможности окончательно судить о качестве сварки. Они устанавливают только внешние дефекты шва и позволяют определить его сомнительные участки, которые могут быть проверены более точными способами.
Рис. 9. Набор шаблонов для контроля размеров сварного шва (а) и пример его применения (б):
1 - угловой шов; 2 - стыковые швы; 3 - блок
Контроль непроницаемости сварных швов и соединений.
Сварные швы и соединения ряда изделий и сооружений должны отвечать требованиям непроницаемости для различных жидкостей и газов. Это объясняется тем, что неплотности в швах снижают их прочность, уменьшают коррозионную стойкость, вызывают потерю хранимых и транспортируемых продуктов и создают ненормальные условия эксплуатации сварных конструкций. Учитывая это, во многих сварных конструкциях (резервуары, газгольдеры, трубопроводы, холодильная и вакуумная аппаратура и т. д.) сварные швы подвергают контролю на непроницаемость. Этот вид контроля производится после окончательного монтажа сварной конструкции. Дефекты, выявленные внешним осмотром (трещины, крупные видимые поры и др.), устраняются до начала испытаний. Непроницаемость сварных швов контролируют керосином, аммиаком, воздушным или гидравлическим давлением, вакуумированием или газоэлектрическими течеискателями.
Контроль керосином основан на физическом явлении капиллярности, которое заключается в способности многих жидкостей, а в первую очередь керосина, подниматься по капиллярным трубкам. Такими капиллярными трубками в сварных швах являются сквозные поры и трещины. В процессе испытания сварные швы покрывают водным раствором мела (350-450 г молотого мела на 1 л воды) или каолина с той стороны, которая более доступна для осмотра и выявления дефектов. После высыхания покрытой поверхности обратная сторона шва обильно смачивается керосином. Неплотности швов выявляют появлением жирных желтых точек или полосок керосина на меловом или каолиновом покрытии. Появление отдельных точек указывает на наличие пор и свищей, а полосок - сквозных трещин или непроваров.
Контроль аммиаком основан на изменении окраски некоторых индикаторов (спиртоводного раствора фенолфталеина или водного раствора азотнокислой ртути) под воздействием щелочей. В качестве щелочи применяется газ аммиак.
В процессе испытаний на одну сторону шва укладывают бумажную ленту или светлую ткань, пропитанную 5%-ным раствором азотно-кислой ртути, а с другой стороны обрабатывают шов смесью аммиака с воздухом под давлением.
Аммиак, проникая через неплотности сварного шва, окрашивает пропитанную индикатором бумагу или ткань в серебристо-черный цвет. При использовании в качестве индикатора спиртоводного раствора фенолфталеина его тонкой струей льют на контролируемый шов. Если в шве имеются неплотности, аммиак проходит через них и окрашивает индикатор в ярко-красный с фиолетовым оттенком цвет.
Контролю воздушным давлением (сжатым воздухом или другими газами) подвергают сосуды и трубопроводы, работающие под давлением.
Это испытание проводят с целью контроля общей непроницаемости сварного изделия.
Малогабаритные сварные изделия полностью герметизируют газонепроницаемыми заглушками и погружают в ванну с водой с таким расчетом, чтобы над изделием был слой воды в 20-40 мм. После этого в изделие через редуктор от воздушной сети или из баллона подают сжатый газ (воздух, азот, инертные газы) под давлением, на 10-20% превышающим рабочее.
Крупногабаритные сварные конструкции, которые не могут быть помещены в воду, испытывают следующим образом. Их герметизируют и создают в них испытательное давление. После этого сварные швы промазывают пенным индикатором (обычным водным раствором мыла), который пузырится в местах неплотностей.
При испытании сжатыми газами следует соблюдать правила безопасности труда: сварные сосуды необходимо испытывать в изолированном помещении с ограждениями на случай взрыва; трубопроводы испытывают отдельными изолированными участками с предупредительными знаками об опасности.
Контроль гидравлическим давлением применяют при проверке прочности и плотности различных сосудов, котлов, паро-, водо-, газопроводов и других сварных конструкций, работающих под избыточным давлением. Перед испытанием сварное изделие полностью герметизируют водонепроницаемыми заглушками. Сварные швы с наружной стороны тщательно обтирают ветошью или обдувают сжатым воздухом до получения сухой поверхности.
После полного заполнения изделия водой с помощью насоса или гидравлического пресса создают испытательное давление (обычно в 1,5-2 раза больше рабочего). Дефектные места определяют по появлению течи, просачиванию воды в виде капель, запотеванию на поверхности шва или вблизи него.
Это наиболее распространенные виды контроля качества сварных швов.
Но существует еще ультразвуковой, радиационный контроль качества сварного шва.
Сущность радиационного контроля основана на свойстве рентгеновских лучей проникать через металлические тела. После обработки рентгеновской пленки дефекты шва приобретают вид темных полос, пятен или черточек.
3. Задача. Объясните, почему для сварки ответственных конструкций преимущественно применяют источник постоянного тока.
Применение выпрямителя обеспечивает устойчивое горение электрической дуги. Это позволяет равномерно прогревать металл по всей длине шва, а также дает возможность контролировать количество тепла, поступаемого в металл при сварке за счет ранее установленной полярности дуги на источнике питания.
Билет № 4
Вопрос 1. Обозначение сварных швов на чертежах.
Согласно Единой системе конструкторской документации (ЕСК), изображения и обозначения швов сварных соединений в конструкторских документах изделий должны соответствовать ГОСТ 2.312-72 «Условные изображения и обозначения швов сварных соединений».
Изображение швов сварных соединений.
Независимо от вида сварки видимый шов сварного соединения условно изображают сплошной основной линией (рис. 10, а), а невидимый - штриховой (рис. 10, б).
Видимую одиночную сварную точку условно изображают знаком «+», невидимые одиночные точки не изображают.
Рис. 10. Изображение швов сварных соединений
От изображения шва или одиночной точки проводят линию-выноску, заканчивающуюся односторонней стрелкой (рис. 10, а, б).
На изображение сечения многопроходного шва допускается наносить контуры отдельных проходов, которые необходимо обозначать прописными буквами русского алфавита (рис. 10, в). Границы шва изображают сплошными основными линиями, а конструктивные элементы кромок в границах шва – сплошными тонкими линиями.
Шов сварного соединения, размеры конструктивных элементов которого стандартами не установлены (нестандартный шов), изображают с указанием размеров конструктивных элементов, необходимых для выполнения шва по данному чертежу (рис. 10, г).
Условные обозначения швов сварных соединений.
Структура условного обозначения стандартного шва или одиночной сварной точки приведена на рис. 10. Ниже приведены номера некоторых стандартов на типы и конструктивные элементы швов сварных соединений для различных видов сварки: ГОСТ 8713-79 «Сварка под флюсом. Соединения сварные»; ГОСТ 5264-80 «Ручная дуговая сварка. Соединения сварные»; ГОСТ 14771-76 «Дуговая сварка в защитном газе. Соединения сварные»; ГОСТ 15164-79 «Электрошлаковая сварка. Соединения сварные».
Этими стандартами в зависимости от толщины металла устанавливаются формы поперечного сечения и конструктивные элементы подготовленных кромок и выполненных швов, которым присваивают условные буквенно-цифровые обозначения.
Для обозначения сварных швов используют также вспомогательные знаки (табл. 1).
Таблица 1
Вспомогательные знаки для условного обозначения сварных швов
Если линия-выноска проведена от изображения шва с лицевой стороны, то условное обозначение шва наносят на полке линии-выноски, если с оборотной - то под полкой.
На рис. 11 показано условное обозначение шва углового соединения под тупым углом (ГОСТ 11533-75) без скоса кромок (У2), двухстороннего, выполненного автоматической сваркой под флюсом с предварительным наложением подварочного шва (Апш) по замкнутой линии.
Рис. 11. Форма поперечного сечения шва углового соединения (а) и условные обозначения шва с лицевой (б) и оборотной (в) стороны
Вопрос 2. Колебательные движения электродов (назначение, разновидности).
Для образования сварного шва электроду придается сложное движение в трех направлениях.
Первое движение - это поступательное движение электрода по направлению его оси. Оно производится со скоростью плавления электрода и обеспечивает поддержание определенной длины дуги.
Второе движение электрода направлено вдоль оси шва и производится со скоростью сварки.
В результате этих двух движений образуется узкий, шириной не более 1,5 диаметров электрода, так называемый ниточный шов. Такой шов применяется при сварке тонкого металла, а также при наложении первого шва при многослойной (многопроходной) сварке.
Третье движение - это колебание конца электрода поперек шва, которое необходимо для образования валика определенной ширины, хорошего провара кромок и замедления остывания сварочной ванны. Колебательные движения электрода поперек шва (рис. 12) могут быть различными и определяются формой, размером и положением шва в пространстве.
Рис. 12. Колебательные движения электрода поперек шва:
1,2,3 - для равномерного прогрева сварочной ванны; 4 - для усиленного прогрева корня шва; 5,6 - для усиленного прогрева кромок
3. Задача. Назовите и напишите формулу, по которой определяется сила сварочного тока.
Сила сварочного тока определяется по формуле:
I=k∙Dэл или I=(20+6Dэл)Dэл,
где k - коэффициент пропорциональности, зависящий от диаметра и типа электрода, А/мм;
Dэл - диаметр электрода, мм.
Билет № 5
Вопрос 1. Подготовка металла под сварку.
Перед сваркой после подбора металла по размерам и маркам стали необходимо выполнить следующие операции:
• правку;
• резку;
• обработку кромок и очистку под сварку.
Кромки подготавливают термическими и механическими способами.
В зависимости от толщины свариваемого металла его сварку можно вести как без разделки кромок, так и с разделкой. Разделка кромок металла начинается с 5 мм.
Существуют определенные геометрические параметры разделки кромок (рис. 13).
Обязательно в процессе сварки делают зазор b для проплавления металла на всю его толщину. Его размеры 0,5-5 мм, в зависимости от толщины свариваемого металла.
Притупление кромок с необходимо для формирования корня шва, и для того, чтобы не проплавить тонкий металл. Его размеры 2-2,5 мм.
Рис. 13. Подготовка металла под сварку
β - угол скоса кромки (15-45°);
S и S1 - толщина металла.
Разделка кромок может быть различна в зависимости от толщины металла (рис. 14).
Рис. 14. Примеры подготовки кромок:
I - высота отбортовки; R - радиус закруглений; β - угол скоса кромок; α - угол разделки кромок; S и S1 - толщина металла
Вопрос 2. Сварочные горелки (назначение, классификация, устройство, маркировка, подготовка к работе, требования техники безопасности).
Сварочная горелка служит для смешивания горючего газа или паров горючей жидкости с кислородом и получения сварочного пламени.
Сварочные горелки подразделяются следующим образом:
• по способу подачи горючего газа и кислорода в смесительную камеру - инжекторные и безынжекторные;
• по роду применяемого горючего газа - ацетиленовые, для газов-заменителей, для жидких горючих и водородные;
• по назначению - универсальные (сварка, резка, пайка, наплавка) и специализированные (выполнение одной операции).
Инжекторная горелка (рис. 15) - эта такая горелка, в которой подача горючего газа в смесительную камеру осуществляется за счет подсоса его струей кислорода, вытекающего с большой скоростью из отверстия сопла. Этот процесс подсоса газа более низкого давления струей кислорода, подводимого с более высоким давлением, называется инжекцией, а горелки данного типа - инжекторными.
Рис. 15. Конструкция инжекторной сварочной горелки:
1 - мундштук; 2 - сменный наконечник; 3 - смесительная камера; 4 - сопло инжектора; 5 - кислородный вентиль; 6 - кислородный ниппель; 7 - ацетиленовый вентиль; 8 - ацетиленовый ниппель
Для нормальной работы инжекторных горелок необходимо, чтобы давление кислорода было 0,15-0,5 МПа, а давление ацетилена значительно ниже - 0,001-0,12 МПа.
Принцип действия ее заключается в следующем. Кислород из баллона под рабочим давлением через ниппель, трубку и вентиль 5 поступает в сопло инжектора 4. Выходя из сопла инжектора с большой скоростью, кислород создает разряжение в ацетиленовом канале, в результате этого ацетилен, проходя через ниппель 6, трубку и вентиль 7, подсасывается в смесительную камеру 3.
В этой камере кислород, смешиваясь с горючим газом, образует горючую смесь. Горючая смесь, выходя через мундштук 1, поджигается и, сгорая, образует сварочное пламя. Подача газов в горелку регулируется кислородным вентилем 5 и ацетиленовым 7, расположенными на корпусе горелки. Сменные наконечники 2 подсоединяются к корпусу горелки накидной гайкой.
Безынжекторная горелка - это такая горелка, в которой горючий газ и подогревающий кислород подаются примерно под одинаковым давлением 0,05-0,1 МПа. В них отсутствует инжектор, который заменен простым смесительным соплом, ввертываемым в трубку наконечника горелки.
Правила обращения с горелками:
1. Не допускается эксплуатация неисправных горелок, так как это может привести к взрывам и пожарам, а также ожогам газосварщика.
2. Исправная горелка дает нормальное и устойчивое свариваемое пламя.
3. Для проверки инжектора горелки к кислородному ниппелю подсоединяют рукав от кислородного редуктора, а к корпусу горелки - наконечник. Наконечник затягивают ключом, открывают ацетиленовый вентиль и кислородным редуктором устанавливают необходимое давление кислорода соответственно номеру наконечника.
Пускают кислород в горелку, открывая кислородный вентиль. Кислород, проходя через инжектор, создает разрежение в ацетиленовых каналах и ацетиленовом ниппеле, которое можно обнаружить, приставляя палец руки к ацетиленовому ниппелю.
При наличии разряжения палец будет присасываться к ниппелю. При отсутствии разряжения необходимо закрыть кислородный вентиль, отвернуть наконечник, вывернуть инжектор и проверить, не засорено ли его отверстие.
При засорении его необходимо прочистить, при этом надо проверить также отверстия смесительной камеры и мундштука. Убедившись в их исправности, повторяют испытание на подсос (разрежение).
4. Величина подсоса зависит от зазора между концом инжектора и входом в смесительную камеру. Если зазор мал, то разрежение в ацетиленовых каналах будет недостаточным, в этом случае следует несколько вывернуть инжектор из смесительной камеры.
5. Вначале немного открывают кислородный вентиль горелки, создавая тем самым разрежение в ацетиленовых каналах. Затем открывают ацетиленовый вентиль и зажигают горючую смесь.
6. Пламя регулируют ацетиленовым вентилем при полностью открытом кислородном.
7. При хлопках сначала перекрывают ацетиленовый, а потом кислородный вентили.
8. Причины хлопков:
• сильный перегрев горелки;
• засорение мундштука горелки;
• если скорость истечения горючей смеси станет меньше скорости ее сгорания, то пламя проникнет в канал мундштука и произойдет обратный удар.
9. В этом случае горелку нужно погасить, охладить ее водой и прочистить мундштук иглой.
3. Задача. Быстро увеличивается начальное давление в ацетиленовом генераторе. Каковы действия сварщика в данной ситуации?
Необходимо произвести принудительный сброс давления через предохранительный клапан и сброс газа через горелку, открыв ацетиленовый вентиль.
Билет № 6
Вопрос 1. Оборудование и классификация сварочного поста электросварщика и газосварщика.
Сварочным постом называют рабочее место сварщика, оборудованное соответствующей аппаратурой и приспособлениями.
Организация рабочего места электросварщика.
Сварочные посты в зависимости от рода применяемого тока и типа источника питания дуги делятся на следующее виды:
• постоянного тока с питанием от однопостового или многопостового сварочного преобразователя или сварочного выпрямителя;
• переменного тока с питанием от сварочного трансформатора.
Сварочные посты по месту расположения могут быть стационарные и передвижные.
Стационарные посты представляют собой открытые сверху кабины для сварки изделий небольших размеров. Каркас кабины металлический. Стены окрашены в светлые тона огнестойкой краской. Окраска стен в темные тона не рекомендуется, так как она плохо поглощает ультрафиолетовые лучи сварочной дуги. Высота сварочного стола 500-600 мм; крышка стола площадью 1 м2, которую изготавливают из листовой стали толщиной около 25 мм. К нижней части крышки или ножки стола приваривают стальной болт, служащий для крепления токопроводящего кабеля от источника тока и для заземления. У стола сбоку имеется два кармана для электродов разных марок. Под ногами у сварщика должен находиться резиновый коврик.
Передвижной пост применяется в случаях сварки изделия крупных форм и необходимости проведения сварки в нестандартных условиях.
Сварочный пост устроен следующим образом (рис. 16).
От сети 1 переменный ток напряжением 220 или 380 В через рубильник 2 подается к источнику питания - сварочному трансформатору 3, где ток трансформируется до напряжения 60-70 В, и по сварочным проводам 4 через зажим 5 и электрододержатель 6 подводится к изделию 7.
Сварочный пост комплектуется:
• источником питания;
• электрододержателем;
• сварочными проводами;
• зажимами для токопроводящего провода;
• сварочным щитком с защитными светофильтрами;
• различными зачистными и мерительными инструментами.
Рис. 16. Стационарный сварочный пост
Электрододержатель - приспособление для закрепления электрода и подведения к нему тока. Среди всего многообразия применяемых электрододержателей наиболее безопасными являются пружинные, изготавливаемые по требованиям и классификации ГОСТ 14651-78Е: I типа - для тока 125 А; II типа – для тока 125-315 А; III типа - для тока 315-500 А. Электрододержатели выдерживают без ремонта 8-10 тысяч зажимов. Время замены электрода не превышает 3-4 с. Для ручной дуговой сварки существует несколько типов электрододержателей (рис. 17).
Щитки сварочные изготавливаются двух типов: ручные и головные из легких негорючих материалов по ГОСТу 12.4.035-78. Масса щитка не должна превышать 0,50 кг.
Защитные светофильтры (затемненные стекла), предназначенные для защиты глаз от излучения дуги, брызг металла и шлака, изготавливаются 13 классов или номеров по ГОСТу 12.4.080-79. Номер светофильтра подбирается в зависимости от силы сварочного тока и индивидуальных особенностей зрения сварщика (табл. 2).
Рис. 17. Типы электрододержателей
Таблица 2
Классы светофильтров
Кабели и сварочные провода необходимы для подвода тока от источника питания к электрододержателю и изделию. Электрододержатели присоединяются к гибкому (многожильному) медному кабелю марки ПРГД или ПРГДО (ГОСТ 6731-77Е). Кабель сплетен из большого числа отожженных медных проволочек диаметром 0,18-0,20 мм. Применять провод длиной более 30 м не рекомендуется, так как это вызывает значительное падение напряжения в сварочной цепи.
Токоподводящий провод соединяется с изделием через специальные зажимы. В сварочном поворотном приспособлении должны быть предусмотрены специальные клеммы. Закрепление провода должно быть надежным. Самодельные удлинители токоподводящего провода в виде кусков или обрезков металла не допускаются.
Сварщики обеспечиваются средствами личной защиты, спецодеждой.
Одежда сварщика изготавливается из различных тканей, которые должны удовлетворять двум основным требованиям:
• наружная поверхность одежды должна быть огнестойкой и термостойкой;
• внутренняя (изнаночная) поверхность одежды должна быть влагопоглощающей.
Исходя из этих требований одежду для сварщиков - куртку и брюки - шьют из брезента, сукна, замши; иногда ткани комбинируют.
При выполнении сварочных работ сварщик пользуется традиционным инструментом: металлической щеткой для зачистки кромок и удаления шлака; молотком-шлакоотделителем для удаления шлаковой корки; зубилом; рулеткой металлической, угольником, чертилкой.
Организация рабочего места газосварщика.
Для газовой сварки сварочные посты бывают стационарными и передвижными. Наибольшее применение нашел в практике передвижной сварочный пост, оснащенный:
• ацетиленовым генератором, предназначенным для получения ацетилена разложением карбида кальция водой;
• кислородным баллоном для хранения кислорода;
• шлангами для подачи газа от баллона и генератора к сварочной горелке;
• сварочной горелкой для смешивания горючего газа или паров горючего газа кислородом.
В стационарных сварочных постах подача горючего газа и кислорода происходит по трубопроводу.
Вопрос 2. Режимы дуговой сварки (назначение, сущность, принцип выбора основных и дополнительных показателей).
Под режимом сварки понимается совокупность ряда факторов (параметров) сварочного процесса, обеспечивающих устойчивое горение дуги и получение сварных швов заданных размеров, формы и качества.
При ручной дуговой сварке покрытыми электродами различают основные и дополнительные параметры режима сварки.
К основным параметрам относят:
• диаметр электрода;
• силу сварочного тока;
• напряжение дуги;
• род и полярность сварочного тока.
Дополнительные параметры:
• тип и марка электрода;
• скорость сварки;
• положение шва в пространстве;
• вылет электрода;
• предварительный подогрев и последующую термическую обработку;
• колебательные движения концом электрода.
Ниже рассматривается влияние некоторых из перечисленных факторов (параметров) на процесс сварки, а также приводятся рекомендации по их выбору.
1. Диаметр электрода при сварке в нижнем положении шва устанавливается в зависимости от толщины свариваемого металла.
Выполнение вертикальных, горизонтальных и потолочных швов независимо от толщины свариваемого металла производится электродами небольшого диаметра (до 4 мм), так как при этом легче предупредить стекание жидкого металла и шлака сварочной ванны.
При многослойной сварке для лучшего провара корня шва первый шов заваривают электродом Ø 3-4 мм, а последующие - электродами большего диаметра.
При сварке металла разной толщины диаметр выбирается по наименьшей толщине металла.
2. Сила сварочного тока (А) устанавливается в зависимости от выбранного диаметра электрода. Для сварки в нижнем положении шва она может быть приближенно определена по формуле
I=kDэл или I=(20+6Dэл)Dэл,
где k - коэффициент пропорциональности, зависящий от диаметра и типа электрода, А/мм;
Dэл - диаметр электрода, мм.
При сварке на вертикальной плоскости ток уменьшается на 10-15%, а в потолочном положении - на 15-20% против выбранного для нижнего положения шва.
3. Род тока и полярность устанавливаются в зависимости от вида свариваемого металла и его толщины. При сварке постоянным током обратной полярности на электроде выделяется больше теплоты. Исходя из этого обратная полярность применяется при сварке тонкого металла, чтобы не прожечь его, и при сварке высоколегированных сталей во избежание их перегрева. При сварке обычных углеродистых сталей применяют переменный ток, являющийся более дешевым по сравнению с постоянным.
4. Для зажигания дугового разряда нужно иметь от источника питания напряжение 30-60 В, а для горения - 20-40 В.
3. Задача. Подобрать основные параметры сварки для металла толщиной 8 мм. Сварка в нижнем положении.
1. Выбор диаметра электрода.
Диаметр выбирают по толщине свариваемого металла. В данном случае необходимы электроды двух диаметров, так как шов многослойный.
Для выполнения корневого шва выбирают электрод диаметром 2 мм, а последующие слои выполняют электродами 4 мм.
2. Силу тока рассчитывают по формуле
I=(20+6Dэл)Dэл.
Для Ø 2 мм I=(20+6Dэл)Dэл=(20+6∙2)∙2=64 А.
Для Ø 4 мм I=(20+6Dэл)Dэл=(20+6∙4)∙4=176 А.
3. Принимают переменный ток.
4. Для зажигания дугового разряда нужно иметь от источника питания напряжение 30-60 В, а для горения - 20-40 В.
Билет № 7
Вопрос 1. Сварочная дуга (определение, физическая сущность, способы зажигания, условия устойчивого горения, строение, влияние длины дуги на производительность и качества шва, окончание шва).
Если случайно или намеренно разомкнуть электрическую цепь, то в месте разрыва цепи проскакивает электрическая искра. Это явление, представляющее собой прохождение электрического тока через воздух, носит название искрового разряда.
Сварочной дугой называют дугу, представляющую собой длительный устойчивый электрический разряд в газовой среде между электродом и изделием либо между электродами, отличающуюся большим количеством тепловой энергии и сильным световым излучением.
Сварочные дуги квалифицируют по следующим признакам:
• по среде, в которой происходит дуговой разряд; на воздухе - открытая дуга, под флюсом – закрытая дуга; в среде защитных газов;
• по роду применяемого электрического тока - постоянная, переменная;
• по типу электрода - плавящаяся, неплавящаяся;
• по длительности горения - непрерывная, импульсная дуга;
• по принципу работы - прямого действия, косвенная дуга, комбинированная или трехфазная.
Для сварки металлов наиболее широко используют сварочную дугу прямого действия, в которой одним электродом служит металлический стержень (плавящийся или неплавящийся электрод), а вторым – свариваемая деталь. К электродам подведен электрический ток - постоянный или переменный.
Теплота, выделяемая сварочной дугой, не вся переходит в сварной шов. Часть теплоты теряется бесполезно на нагрев окружающего воздуха, плавление электродного покрытия.
Мощность сварочной дуги Q зависит от сварочного тока I и напряжения дуги U:
Q=I∙U (Вт).
Дугу возбуждают двумя способами - касанием или чирканьем. В обоих случаях процесс возбуждения сварочной дуги начинается с короткого замыкания. При этом в точках контакта увеличивается плотность тока, выделяется большое количество теплоты, и металл плавится. Затем электрод отводят, разрядный промежуток заполняется нагретыми частицами паров металла, и начинается горение дуги.
При отводе электрода от изделия (после короткого замыкания и мгновенного расплавления металла) жидкий мостик металла вначале растягивается, сечение его уменьшается, температура металла повышается, а затем жидкий мостик металла разрывается (рис. 18). При этом происходит быстрое испарение металла, и разрядный промежуток заполняется нагретыми ионизированными частицами паров металла, электродного покрытия и воздуха - возникает сварочная дуга.
Рис. 18. Схема возбуждения электрической дуги:
I - короткое замыкание; II - образование жидкого металла; III - образование шейки; IV - возникновение дуги.
1 - электрод; 2 - основной металл; 3 - сварочная дуга
Для повышения устойчивости горения сварочной дуги в электродное покрытие или в защитный флюс вводят элементы (калий, натрий, барий и др.), которые повышают степень ионизации и, следовательно, стабилизации сварочной дуги.
Сварочную дугу можно возбудить без касания электродом свариваемого изделия. Для этого нужно в сварочную цепь параллельно включить источник тока высокого напряжения и высокой частоты (осциллятор). При этом для возбуждения дуги достаточно приблизить конец электрода на расстояние 2-3 мм к поверхности изделия.
Дуговой промежуток подразделяется на три основные области (рис. 19):
• катодную;
• анодную;
• столб дуги.
Рис. 19. Строение электрической дуги и распределение напряжения на ее участках:
1 - катодное пятно; 2 - столб дуги; 3 - анодное пятно
Катодное пятно является источником потока свободных электронов. Температура его для стальных электродов достигает 2400-2600°С. В катодном пятне выделяется около 38% общей теплоты дуги.
Столб дуги представляет собой проводник электрического тока. В нем свободные электроны и отрицательно заряженные ионы движутся к аноду, а положительно заряженные ионы - к катоду. В целом столб дуги не имеет заряда. Он нейтрален, так как в каждом сечении столба одновременно находятся равные количества противоположно заряженных частиц.
В столбе дуги выделяется около 20% общей теплоты дуги. Температура столба дуги зависит от силы сварочного тока и достигает в ее центре 6000-7000°С и более. Температура капли на конце стального электрода приблизительно равна 2150°С, а при перелете ее через дуговой промежуток - 2350°С.
В среднем температура сварочной ванны составляет 1770°С.
Анодное пятно является местом входа и нейтрализации свободных электронов. Оно имеет примерно такую же температуру, как и катодное пятно, но в результате бомбардировки электронами на нем выделяется больше теплоты (примерно 42%), чем на катодном.
Малыми кружочками обозначены электроны, а большими - положительно и отрицательно заряженные ионы.
При работе на постоянном токе возможна прямая и обратная дуга.
При прямой полярности «+» на изделии «-» на электроде. При обратной полярности наоборот. При питании сварочной дуги постоянным током обратной полярности катодное и анодное пятна поменяются местами, т. е. катодом будет изделие, а анодом - электрод.
При переменном токе эта смена будет происходить 100 раз в секунду, поэтому дуга на переменном токе горит менее устойчиво, чем на постоянном. При сварке на переменном токе количество теплоты, выделяющиеся на электроде и изделии, будет примерно одинаковым.
Различают по длине короткую и длинную дугу.
Длиной дуги называют расстояние от конца электрода до дна кратера на поверхности металла.
Кратером называют углубление на поверхности металла в результате давления на него столба дуги.
Длина дуги определяется диаметром электрода.
Короткой называется дуга, длина которой меньше или равна диаметру электрода. Ее размеры 2 - 4 мм.
Длинная дуга та, которая больше или равна диаметру электрода.
Короткой дугой сваривают, длинной - режут металл.
Чтобы избежать кратера, применяют следующие способы:
• начинают и оканчивают шов на основном металле;
• постепенно удлиняют сварочную дугу и резко ее обрывают отводом в сторону.
В процессе горения дуги жидкий металл с конца электрода переходит в сварочную ванну в виде отдельных капель (капельный способ) и при полуавтоматической сварке струйно.
Перенос капель осуществляется под действием:
• силы тяжести;
• силы поверхностного натяжения;
• электромагнитных сил.
Характер капель зависит от силы сварочного тока. С увеличением силы тока размер капель уменьшается, а число их возрастает.
С уменьшением силы тока размер капли растет и в единицу времени капель становится меньше. Именно это свойство переноса металла и уменьшение силы тока, а также максимально короткая дуга позволяют вести сварку в вертикальном положении.
Влияние магнитных полей на дугу. Сварочная дуга является гибкой газовой вставкой между электродом и изделием и, как всякий проводник с током, взаимодействует с магнитным полем.
Отклонение столба дуги под действием магнитного поля, наблюдаемое в основном при сварке постоянным током, называется магнитным дутьем (рис. 20). Возникновение его объясняется тем, что в местах изменения направления тока создаются различные напряженности магнитного поля. Это приводит к отклонению дуги в сторону, противоположную большей напряженности.
При сварке переменным током, в связи с тем, что полярность меняется с частотой тока, это явление проявляется значительно слабее.
Магнитное дутье также имеет место при сварке вблизи ферромагнитных масс (железо и сталь). Дуга в этом случае отклоняется в сторону этих масс.
Возникновение магнитного дутья вызывает непровары и ухудшает внешний вид шва.
Рис. 20. Влияние магнитных полей и ферромагнитных масс на сварочную дугу:
а - нормальное положение дуги; б - отклонение дуги под влиянием неравномерной напряженности магнитного поля; в - отклонение дуги под влиянием ферромагнитных масс; Н1 и Н2 - напряженности магнитного поля
Устранить его можно:
• изменением места токоподвода и угла наклона электрода;
• временным размещением дополнительного ферромагнитного материала, создающего симметричное магнитное поле;
• заменой постоянного тока переменным.
Вопрос 2. Технология выполнения швов различной протяженности.
Все сварные швы в зависимости от их длины условно разбивают на три группы:
• короткие - до 250 мм;
• средней длины - от 250 до 1000 мм;
• длинные - от 1000 мм и более.
Короткие швы выполняют «на проход» в одном направлении, т. е. при движении электрода от начала шва к концу (рис. 21, а).
При выполнении швов средней длины и длинных возможно коробление изделий. Чтобы избежать этого, швы средней длины выполняют «на проход» от середины к концам (рис. 21, б) или обратноступенчатым способом (рис. 21, в), сущность которого состоит в том, что весь шов разбивают на участки длиной 100-350 мм с таким расчетом, чтобы каждый из них мог быть выполнен целым числом электродов (двумя, тремя и т. д.). При этом переход от участка к участку совмещается со сменой электрода. Каждый участок заваривается в направлении, обратном общему направлению сварки, а последний всегда заваривается «на выход».
Длинные швы выполняют от середины к концам обратноступенчатым способом (рис. 21, г). В данном случае возможно организовать работу одновременно двух сварщиков.
Рис. 21. Выполнение швов различной длины:
1-7 - последовательность наложения швов
3. Задача. Назовите цвета баллонов, в которые окрашиваются защитные и горючие газы.
Защитный газ:
Кислород - голубой.
Аргон чистый - серый.
Водород - зеленый.
Углекислота - черный.
Гелий — коричневый.
Горючий газ:
Ацетилен - белый.
Пропан, бутан, природный газ - красный.
Билет № 8
Вопрос 1. Устройство и назначение сварочного трансформатора.
Для дуговой сварки используют как переменный, так и постоянный сварочный ток. В качестве источника переменного сварочного тока применяют сварочные трансформаторы, а постоянного - сварочные выпрямители и сварочные преобразователи.
Источник питания сварочной дуги – сварочный трансформатор - обозначается следующим образом:
ТДМ-317, где:
Т - трансформатор;
Д - для дуговой сварки;
М - механическое регулирование;
31 - номинальный ток 310 А;
7 - модель.
Сварочный трансформатор служит для понижения напряжения сети с 220 или 380 В до безопасного, но достаточного для легкого зажигания и устойчивого горения электрической дуги (не более 80 В), а также для регулировки силы сварочного тока.
Трансформатор (рис. 22) имеет стальной сердечник (магнитопровод) и две изолированные обмотки. Обмотка, подключенная к сети, называется первичной, а обмотка, подключенная к электрододержателю и свариваемому изделию, - вторичной. Для надежного зажигания дуги вторичное напряжение сварочных трансформаторов должно быть не менее 60-65 В; напряжение при ручной сварке обычно не превышает 20-30 В.
8 нижней части сердечника 1 находится первичная обмотка 3, состоящая из двух катушек, расположенных на двух стержнях. Катушки первичной обмотки закреплены неподвижно. Вторичная обмотка 2, также состоящая из двух катушек, расположена на значительном расстоянии от первичной. Катушки как первичной, так и вторичной обмоток соединены параллельно. Вторичная обмотка - подвижная и может перемещаться по сердечнику при помощи винта 4, с которым она связана, и рукоятки 5, находящейся на крышке кожуха трансформатора.
Регулирование сварочного тока производится изменением расстояния между первичной и вторичной обмотками. При вращении рукоятки 5 по часовой стрелке вторичная обмотка приближается к первичной, магнитный поток рассеяния и индуктивное сопротивление уменьшаются, сварочный ток возрастает. При вращении рукоятки против часовой стрелки вторичная обмотка удаляется от первичной, магнитный поток рассеяния растет (индуктивное сопротивление увеличивается) и сварочный ток уменьшается. Пределы регулирования сварочного тока - 65-460 А. Последовательное соединение катушек первичной и вторичной обмоток позволяет получать малые сварочные токи с пределами регулирования 40-180 А. Диапазоны тока переключают выведенной на крышку рукояткой.
Рис. 22. Сварочный трансформатор:
а - внешний вид; б - схема регулирования сварочного тока
Свойства источника питания определяются его внешней характеристикой, представляющей кривую зависимости между током (I) в цепи и напряжением (U) на зажимах источника питания.
Источник питания может иметь внешнюю характеристику: возрастающую, жесткую, падающую.
Источник питания для ручной дуговой сварки имеет падающую вольт-амперную характеристику.
Напряжение холостого хода источника питания - напряжение на выходных клеммах при разомкнутой сварочной цепи.
Номинальный сварочный ток и напряжение – ток и напряжение, на которые рассчитан нормально работающий источник.
Вопрос 2. Способы заполнения шва по сечению.
По способу заполнения по сечению швы:
• однопроходные, однослойные (рис. 23, а);
• многопроходные многослойные (рис. 23, б);
• многослойные (рис. 23, в).
Рис. 23. Сварные швы по заполнению сечения шва
Если число слоев равно числу проходов дугой, то такой шов называют многослойным.
Если некоторые из слоев выполняют за несколько проходов, то шов многопроходный.
Многослойные швы чаще применяют в стыковых соединениях, многопроходные - в угловых и тавровых.
Для более равномерного нагрева металла шва по всей его длине швы выполняют:
• двойным слоем;
• каскадом;
• блоками;
• горкой.
В основу всех этих способов положен принцип обратно-ступенчатой сварки.
Сущность способа двойного слоя заключается в том, что наложение второго слоя производится по неостывшему первому после удаления сварочного шлака: сварка на длине 200-400 мм ведется в противоположных направлениях. Этим предотвращается появление горячих трещин в шве при сварке металла толщиной 15-20 мм, обладающего значительной жесткостью.
При толщине стальных листов 20-25 мм и более для предотвращения трещин применяют сварку:
• каскадом;
• блоками;
• поперечной горкой.
Заполнение многослойного шва для сварки горкой и каскадом производится по всей свариваемой толщине на определенной длине ступени. Длина ступени подбирается такой, чтобы металл в корне шва имел температуру не менее 200°С в процессе выполнения шва по всей толщине. В этом случае металл обладает высокой пластичностью, и трещин не образуется. Длина ступени при каскадной сварке равна 200-400 мм (рис. 24, а).
При сварке блоками многослойный шов сваривают отдельными ступенями, промежутки между ними заполняют по всей толщине слоями (рис. 24, б).
При соединении деталей из закаливающихся при сварке сталей рекомендуется применять сварку блоками. Из незакаливающихся (низкоуглеродистых) сталей - лучше выполнить сварку каскадом.
Рис. 24. Заполнение шва по сечению:
а - каскадом; б – блоками
Рис. 25. Сварка горкой
Таким образом, выполняют сварку (заполнение разделки) в обе стороны от центральной горки короткими швами. Каскадный метод является разновидностью метода горки.
При сварке методом горки (рис. 25) на участке 200-300 мм накладывают первый слой, после очистки его от шлака на него накладывают второй слой, по длине в 2 раза больший, чем первый. Затем, отступив от начала второго слоя на 200-300 мм, производят наплавку третьего слоя и т. д.
3. Задача. Объясните влияние серы и фосфора на качество сварного шва.
Сера и фосфор являются вредными примесями стали и чугуна. Их избыточное количество вызывает образование трещин в сварном шве. Сера вызывает трещины в горячем состоянии шва (явление красноломкости), фосфор - в холодном (явление хладноломкости).
Билет № 9
Вопрос 1. Сварочное пламя (способы получения, виды, основные характеристики, строение).
Сварочное пламя образуется при сгорании горючего газа или паров горючей жидкости в кислороде. Пламя при резке нагревает основной металл до температуры его горения.
Наибольшее применение при газовой сварке и резке нашло кислородно-ацетиленовое пламя, так как оно имеет высокую температуру (3150°С) и обеспечивает концентрированный нагрев. Однако в связи с дефицитностью ацетилена в настоящее время получили широкое распространение (особенно при резке металлов) газы - заменители ацетилена: пропан - бутан, метан, природный и городской газы.
Все горючие газы, содержащие углеводороды, образуют сварочное пламя, которое имеет ярко различимые зоны:
• ядро;
• восстановительную зону;
• факел.
Размеры ядра зависят от состава горючей смеси, ее расхода и скорости истечения.
Диаметр канала мундштука горелки определяет диаметр ядра пламени, а скорость истечения газовой смеси - его длину.
Восстановительная (средняя) зона располагается за ядром и по своему более темному цвету заметно отличается от него. Длина ее зависит от вида пламени и достигает 20 мм. Этой зоной пламени выполняют сварку. Она имеет наиболее высокую температуру - 3140ºС в точке, отстающей на 3-6 мм от конца ядра.
От состава горючей смеси, т. е. от соотношения кислорода и горючего газа, зависят внешний вид, температура и влияние сварочного пламени на расплавленный металл.
Изменяя состав горючей смеси, сварщик или газорезчик тем самым изменяет основные параметры сварочного пламени.
В зависимости от соотношения между кислородом и ацетиленом получают три основных вида сварочного пламени (рис. 26):
• нормальное (на один объем ацетилена подают несколько больше - от 1,1 до 1,3 объема кислорода);
• окислительное (получают при избытке кислорода, на один объем ацетилена более 1,3 объема кислорода);
• науглероживающее (получают при избытке ацетилена, когда на один объем ацетилена подается 0,95 и менее объема кислорода).
Рис. 26. Виды сварочного пламени:
а - нормальное; б - окислительное; в - науглероживающее
Вопрос 2. Технология и техника выполнения швов в нижнем положении.
Нижние швы являются наиболее удобными для сварки, так как в этом случае капли электродного металла под действием собственного веса легко переходят в сварочную ванну, и жидкий металл не вытекает из нее. Кроме того, наблюдение за сваркой при нижнем положении шва более удобно.
Стыковые швы применяют для получения стыковых соединений.
При выполнении стыковых швов сварку ведут в четырех направлениях: слева направо, справа налево, на себя, от себя.
Наклон электрода 15-25° от вертикали.
Угловые швы применяют для получения угловых, тавровых и нахлесточных соединений.
Сварка угловых швов может производиться наклонным электродом и в «лодочку».
При сварке углового шва, нижняя плоскость которого расположена горизонтально, возможен непровар вершины угла или одной из кромок. Непровар может образоваться на нижнем листе, если начинать сварку с вертикального листа, так как в этом случае расплавленный металл стечет на недостаточно нагретую поверхность нижнего листа. На вертикальной же полке возможно образование подрезов.
Поэтому сварку таких швов начинают, зажигая дугу на нижней плоскости в точке А, отступив от границы катета 3-4 мм. Затем дугу перемещают к вершине шва, задерживают для лучшего провара корня шва, поднимают вверх, проваривая вертикальную полку (рис. 27).
Рис. 27. Выполнение углового шва
Электрод держат под углом 45° к поверхности свариваемых деталей, слегка наклоняя его в процессе сварки то к одной, то к другой плоскости.
При сварке угловым швом в «лодочку» (рис. 28) наплавленный металл располагается в желобе, образуемом двумя полками. Это обеспечивает правильное формирование шва и хороший провар кромок металла.
Рис. 28. Выполнение углового шва в «лодочку»
3. Задача. Объясните назначение покрытия на плавящихся электродах.
1. Защита расплавленного металла от кислорода и азота воздуха при сварке. Это достигается газами, которые образуются из покрытия в зоне дуги.
2. Теплоизоляция расплавленного металла шва. Этим достигается пластичность шва.
3. Обеспечение устойчивого горения дуги, за счет введения в покрытие ионизирующих добавок.
4. Легирование металла шва.
Билет № 10
Вопрос 1. Дефекты швов сварных соединений (причины возникновения, способы их устранения).
Различные отклонения от установленных норм и технических требований, ухудшающие работоспособность сварных конструкций, называются дефектами сварных швов. Они уменьшают прочность сварных соединений и могут привести к их разрушению.
Все дефекты сварных швов могут быть разделены на три основные группы:
• дефекты формы и размеров;
• наружные и внутренние макроскопические дефекты;
• дефекты микроструктуры.
Наиболее частыми дефектами формы и размеров сварных швов являются их неполномерность, неравномерные ширина и высота, бугристость, седловины, перетяжки.
Эти дефекты швов косвенно указывают на возможность образования дефектов внутри сварного шва и околошовной зоны.
К наружным и внутренним макроскопическим дефектам относят наплывы, подрезы, прожоги, непровары, трещины, шлаковые включения и газовые поры (приложение 1).
К дефектам микроструктуры относят перегрев и пережог.
На участке перегрева металл имеет крупнозернистое строение, что ведет к хрупкости металла. Перегретый металл плохо сопротивляется ударным нагрузкам.
Наиболее опасным дефектом является пережог. Такой металл хрупок и не поддается исправлению. Причиной образования пережога является плохая защита сварочной ванны от кислорода воздуха, а также сварка на чрезмерно большом сварочном токе.
Вопрос 2. Ацетиленовый генератор (назначение, классификация, устройство, подготовка к обслуживанию, требования техники безопасности).
Ацетиленовый генератор служит для получения ацетилена разложением карбида; кальция водой.
Ацетиленовые генераторы классифицируются:
• по производительности - 1,25; 3; 5; 10, 20, 40, 80, 160; 320, 640 м3/ч;
• по способу применения - передвижные и стационарные;
• по давлению вырабатываемого ацетилена – низкого давления - до 0,02 МПа, среднего давления - от 0,02 до 0,15 МПа.
• по способу взаимодействия карбида кальция с водой - ВК (вода на карбид) и KB (карбид на воду).
Рассмотрим устройство генератора типа АСП-1,25-6 (рис. 29). Это переносной генератор производительностью 1,25 м3/ч, рабочим давлением 0,01-0,07 МПа. Генератор представляет собой вертикальный цилиндрический сосуд.
Корпус 5 состоит из трех частей:
• газообразовательной , в которой образуется ацетилен за счет взаимодействия кальция с водой;
• вытеснителъной ;
• промывательной.
Вода заливается через горловину. При достижении уровня переливной трубки 3 вода по трубке переливается в промыватель, который заполняется до уровня контрольной пробки 2.
Карбид кальция загружают в корзину 8. Уплотнение между крышкой 12 горловиной обеспечивается мембраной 11 усилием, создаваемым винтом 13 через траверсу 14.
Ацетилен, образующийся в газообразователе, по трубке 3 поступает в промыватель, барботируя через слои воды, охлаждается и промывается. Из промывателя ацетилен через вентиль предохранительного клапана 4 по шлангу 15 поступает в предохранительный затвор 7 и далее к горелке или резаку. По мере повышения давления в газообразователе пружина 10 сжимается, в результате чего корзина перемещается вверх, а вода вытесняется в вытеснитель. В результате уровень замочки карбида уменьшается, выработка ацетилена ограничивается и повышение давления прекращается. Давление ацетилена контролирует манометр 9. Ил из газообразователя и иловую воду из промывателя сливают через штуцера 6 и 1.
Рис. 29. Устройство генератора АСП-1,25-6
Подготовка генератора к работе:
• снять крышку и поддон от корзины;
• убедиться, что корпус чист и промыт;
• проверить закрепления вентиля и предохранительного клапана;
• открыть контрольные пробки в генераторе и водяном затворе;
• залить водой водяной затвор и генератор до уровня контрольной пробки;
• закрыть контрольные пробки;
• соединить шлангом вентиль и предохранительный затвор;
• загрузить карбид кальция;
• закрепить поддон на корзине и закрыть крышку;
Основные технические характеристики генератора приведены в таблице.
Основные технические характеристики генератора
Ацетиленовый генератор снабжен предохранительным затвором.
При работе с генератором необходимо соблюдать следующие правила:
• использовать размеры карбида кальция, указанные в паспорте;
• при перерывах в работе и в зимнее время нельзя допускать замерзания воды в генераторе, для чего генераторы утепляют;
• при работе нельзя оставлять возле генератора ил, его нужно относить в специальные ямы;
• нельзя подходить с огнем или зажженной горелкой к генератору, так как возможно выделение ацетилена в окружающую среду и образование взрывчатой смеси;
• работающий генератор нельзя оставлять без надзора;
• используют генераторы на открытом воздухе;
• генератор должен находиться от кислородного баллона на расстоянии 10 м, а от других источников тепла не менее 5 м.
3. Задача. Прочитайте условное обозначение электрода
Э46 - тип электрода, 460 МПа – минимальное сопротивление наплавленного металла шва на разрыв (предел прочности);
АНО-4 - марка электрода;
3,0 - диаметр электрода;
У - для сварки углеродистых сталей;
Д - толстое покрытие;
Е432 - характеристика наплавленного металла;
Р - рутиловое покрытие;
2 - для сварки во всех пространственных положениях, кроме вертикального сверху вниз;
1 - переменный ток.
Билет № 11
Вопрос 1. Понятие свариваемости металла. Классификация сталей по свариваемости.
Под свариваемостью понимается способность стали данного химического состава давать при сварке тем или иным способом высококачественное сварное соединение без трещин, пор и прочих дефектов.
На свариваемость стали влияет содержание в ней углерода и легирующих элементов.
С повышением содержания углерода в стали в ней возрастают прочностные свойства, но в то же время возрастает хрупкость и склонность к образованию трещин при сварке.
Различают физическую и технологическую свариваемость.
Физической свариваемостью обладают практически все металлы и их сплавы, т. е. способностью образовывать монолитное неразъемное соединение с установлением в нем химических связей.
Под технологической свариваемостью понимается реакция металла на воздействие конкретных условий сварки и при этом возможность образовывать соединение с требуемыми свойствами.
Для предварительного суждения о свариваемости стали известного химического состава можно подсчитывать эквивалентное содержание углерода, пользуясь формулой:
Сэкв=С+Mn/20+Ni/15+(Cr+Mo+V)/10
В целом, по признаку свариваемости все стали можно условно разделить на четыре группы (приложение 2).
Вопрос 2. Техника и технология выполнения швов в горизонтальном, вертикальном и потолочном положении.
Сварка в вертикальном положении.
Расплавленный металл под действием силы тяжести стремится стекать вниз, что затрудняет формирование шва. Поэтому вертикальные швы выполняют очень короткой дугой, при которой расстояние между каплями на электроде и жидким металлом в сварочной ванне настолько мало, что между ними возникает взаимное притяжение. Благодаря этому капли электродного металла сливаются со сварочной ванной при малейшем касании их между собой.
Объем расплавленного металла уменьшают снижением сварочного ток на 10-15% по сравнению с нижним положением, а диаметр электрода ограничивают до 5 мм.
Вертикальные швы выполняют как снизу вверх, так и сверху вниз.
В первом случае (рис. 30, а) дуга возбуждается в самой нижней точке вертикально расположенных пластин, для этого электрод устанавливают перпендикулярно поверхности свариваемого изделия (положение 1). Затем электрод немного наклоняют вниз для того, чтобы слой давления газов дуги предшествовал стеканию металла сварочной ванны (положение 2). При этом застывший металл шва образует подобие полочки, на которой удерживаются последующие капли металла.
Сварку сверху вниз применяют при малой толщине металла. В этом случае подтекающий под дугу жидкий металл уменьшает возможность образования сквозных прожогов.
В начале сварки (рис. 30, б) дуга возбуждается в самой верхней точке пластин при горизонтальном расположении электрода. После образования ванны жидкого металла электрод наклоняют на 15-20° с таким расчетом, чтобы дуга была направлена на основной и наплавленный металл. Для улучшения условий формирования шва амплитуда колебательных движений электрода должна быть небольшой, а дуга – очень короткой, чтобы капли расплавленного металла удерживались от падения концом электрода.
Рис. 30. Выполнение сварных вертикальных швов
Сварка горизонтальных швов.
Горизонтальные швы на вертикальной плоскости выполнять труднее, чем вертикальные. Для предупреждения отекания жидкого металла скос кромок обычно делается на одном верхнем листе (рис. 31, а). Дуга в этом случае возбуждается на нижней горизонтальной кромке (положение 1), а затем переносится на наклонный скос (положение 2), поднимая вверх стекающую каплю металла. Колебательные движения электродом совершают по спирали. Выполнять горизонтальными сварными швами нахлесточные соединения легче, чем стыковые, так как горизонтальная кромка нижнего листа (рис. 39, б) способствует удержанию расплавленного металла от стекания вниз. При выполнении горизонтальных швов с двумя скосами кромок устанавливают порядок их наложения (1-4 рис. 39, в), который в процессе проваривания верхней кромки позволяет избежать потолочного положения кратера с расплавленным металлом.
Рис. 31. Выполнение сварных горизонтальных швов:
а - стыковое соединение со скосом одной кромки; б - нахлесточное соединение; в – стыковое соединение со скосом двух кромок
Сварка в потолочном положении.
Сварка в потолочном положении (рис. 32) наиболее трудна, так как направление силы тяжести расплавляемого металла противоположно направлению его переноса. Это требует максимального уменьшения объема расплавляемого металла, что достигается ограничением диаметра электрода до 4 мм и снижением сварочного тока на 15-20% по сравнению с нижним положением.
Рис. 32. Сварка потолочных швов
Для сварки в потолочном положении подходят электроды, дающие небольшой шлак.
Хороший провар корня шва при потолочной сварке обеспечивается применением электродов диаметром не более 3 мм.
3. Задача. Из предложенных марок сталей выберите, которые свариваются хорошо, удовлетворительно, ограниченно, плохо. Обоснуйте свой выбор: БСт1кп; сталь 10; сталь 35; ВСт5пс; сталь 65; У7.
Свариваемость углеродистых сталей определяется процентным содержанием углерода в ней. С повышением содержания углерода свариваемость сталей ухудшается, т. е. возникает склонность к образованию трещин в шве.
БСт1кп и сталь 10 - хорошо свариваются, так как относятся к низкоуглеродистой стали (содержание углерода до 0,25%).
Сталь 35 удовлетворительно сваривается, так как относится к среднеуглеродистой (содержание углерода 0,35%).
ВСт5пс - ограниченно сваривается, так как относится к среднеуглеродистой (содержание углерода практически 0,45%).
Сталь 65 и У7 - плохо сваривается, так как содержание углерода 0,65%, т. е. высокоуглеродистая; сталь У7 - относится к инструментальной стали, углерода 0,7%. Эти стали практически не свариваются.
Билет № 12
Вопрос 1. Сварочная проволока (назначение, требования, химический состав, маркировка).
Для сварки сталей применяется специальная стальная проволока по ГОСТу 2246-70. Используется в основном низкоуглеродистая и низколегированная сталь. Предусмотрено 77 марок сварочной проволоки различного химического состава.
К сварочной проволоке предъявляются следующие требования:
• она должна расплавляться спокойно и равномерно;
• температура плавления должна быть меньше или равна температуре плавления основного металла;
• должна быть очищенной от ржавчины и грязи;
• должна по химическому составу соответствовать химическому составу свариваемого металла.
Условное обозначение проволоки рассмотрим на примере.
2Св-08А, где:
2 - диаметр проволоки 2 мм;
Св - сварочная проволока;
08 - 0,08% - содержание углерода;
А - повышенное качество металла.
В марке могут присутствовать две буквы АА (Св-08АА), что говорит о том, это материал проволоки особо качественный.
Под качеством понимается пониженное содержание в стали вредных примесей - серы и фосфора. Повышенное содержание углерода в проволоке приводит к снижению пластичности металла.
В марке проволоки могут присутствовать легирующие элементы (Св-12ГС; Св-15ГСТЮЦА):
Г - 1% марганца; С - 1% кремния.
Если после буквы, обозначающей легирующий элемент, не стоит цифра, то содержание этого элемента в стали до 1%. Цифра показывает содержание элемента в целых долях процента.
Условные обозначения легирующих элементов:
С - кремний
Н - никель
М - молибден
Т - титан
Ю - алюминий
Ц - цирконий
Г - марганец
X - хром
В - вольфрам
Ф - ванадий
Проволока различается по диаметру. Диаметр проволоки - от 1 до 12 мм.
Проволока диаметром от 1,6 до 6 мм применяется для ручной дуговой сварки (металлический стержень электрода). Проволока диаметром более 6 мм называется прутами и применяется для сварки чугуна и цветных металлов, наплавочных работ. Проволока диаметром от 2 до 5 мм - для автоматической сварки.
Диаметр проволоки для газовой сварки выбирается в зависимости от толщины металла и способа сварки.
Для сварки правым способом диаметр присадочной проволоки равен d=S/2.
Для сварки левым способом диаметр присадочной проволоки равен d=S/2+1.
Вопрос 2. Высокопроизводительные виды ручной дуговой сварки (значение, виды, техника выполнения).
Под производительностью в сварке понимают количество сварочного шва в метрах, выполненного за определенный интервал времени.
Этого можно достичь, используя различные прогрессивные приемы и усовершенствования выполнения ручной сварки (организация рабочего места сварщика, уменьшение время на переход с одной операции на другую). Все это позволяет увеличить сварщикам время горения дуги в течение рабочего времени на 10-15%, так как время смены электрода составляет 7-10% времени рабочего дня.
Чтобы увеличить производительность сварочных работ, существуют еще и специальные технические мероприятия и способы, а именно:
• сварка высокопроизводительными покрытыми электродами;
• сварка сдвоенным электродом, гребенкой электродов, трехфазной дугой;
• сварка глубоким проплавлением;
• сварка лежачим электродом;
• сварка наклонным электродом.
Рис. 33. Схема сдвоенного электрода (а), гребенки (б) и сварка трехфазным током (в, г):
1 - связка электродов; 2 - трехфазный трансформатор; 3,4 - электроды; 5 - дуга
Рассмотрим эти способы.
Сварка высокопроизводительными покрытыми электродами. Наиболее эффективны электроды с железным порошком в покрытии. Это повышает коэффициент наплавки. При сварке покрытыми электродами с железным порошком в образовании шва принимает участие не только металл электродного стержня, но и железный порошок, введенный в состав покрытия. Эти электроды должны называться высокопроизводительными.
Производительность электродов характеризуется массой электродного металла, перешедшего на изделие за единицу времени.
К этим электродам относятся электроды марок: АНО-1, ОЗС-3, АНО-19, которые при содержании 50-65% железного порошка дают 65-70 г/мин наплавленного металла (по сравнению с 23-30 г/мин для обычных электродов: АНО-4, MP-3, ОЗС-4 и др.). Однако следует учитывать, что высокопроизводительные электроды позволяют выполнять сварку только в нижнем и наклонном (угол 15-20°) положениях. Источники питания для сварки этими электродами должны иметь повышенное напряжение холостого хода.
Сварка сдвоенным электродом, гребенкой электродов, трехфазной дугой. При сварке сдвоенным электродом процесс ведут двумя стержнями, соединенными между собой контактной точечной сваркой (рис. 33, а).
Дуга переходит с одного стержня на другой, попеременно оплавляя их. Производительность сварки повышается на 20-40% по сравнению со сваркой одностержневым электродом. Это повышение достигается попеременным подогревом каждого из стержней дугой, горящей между соседними стержнями и изделием, увеличением времени горения дуги, уменьшением времени на смену электродов.
Электроды располагаются так, чтобы их общая ось совпадала с осью шва или при большой разделке кромок была перпендикулярна этой оси.
Сварочный ток составляет:
• от 100-180 А - при диаметре электродов 3+3 мм;
• 300-400 А - при диаметре 6+6 мм.
Сдвоенными электродами можно сваривать за один проход металл толщиной до 12 мм.
Электроды можно располагать по несколько стержней в ряд в виде гребенки (рис. 33, б).
Дуга возбуждается на электроде, находящемся на более близком расстоянии от свариваемого изделия. При плавлении электрода дуга переходит с одного на другой стержень и т. д.
Электродная гребенка позволяет глубоко опускаться в разделку кромок. Производительность сварки повышается вдвое по сравнению со сваркой обычным электродом.
Производительность ручной дуговой сварки можно повысить еще на большую величину, если использовать трехфазный ток (рис. 33, в).
При сварке трехфазной дугой применяют два электрода, к которым подводятся две фазы от источника питания, а третья фаза - к свариваемому изделию. В каждый данный момент в процессе изменения синусоидального тока могут гореть одна или две дуги. При этом выделяется большое количество теплоты, скорость плавления металла возрастает, и производительность сварки увеличивается на 50-60% по сравнению со сваркой однофазной дугой.
Однако при сварке трехфазной дугой сильно утяжелен электрододержатель, что ведет к утомляемости сварщика. Поэтому такую сварку лучше выполнять механизированными способами.
Сварка глубоким проплавлением. Этот вид сварки еще называют сваркой опиранием.
Для сварки применяют электроды с увеличенной толщиной покрытия. Стальной стержень электрода плавится несколько быстрее покрытия, в результате чего на конце электрода из покрытия образуется втулка (козырек). Опирая втулку электрода на поверхность изделия, сварщик перемещает дугу вдоль шва.
Образующиеся при плавлении покрытия газы своим давлением вытесняют жидкий металл из сварочной ванны, образуя валик, изделие проплавляется на большую величину, чем при сварке электродом на весу. При этом объем наплавленного металла в сварном шве значительно уменьшается без снижения прочности шва.
Этот способ сварки позволяет уменьшать глубину разделки кромок и сваривать металл значительной толщины без разделки кромок с большой скоростью. Сварку выполняют без колебательных поперечных движений электрода.
Техника сварки опиранием заключается в том, что после зажигания дуги сварщик устанавливает электрод под углом 70-80° к плоскости изделия, опускает покрытие электрода на поверхность изделия, и дуга автоматически будет перемещаться по оси шва.
Способ сварки опиранием особенно целесообразно применять при выполнении угловых швов в положении в «лодочку», используя для этого электроды марки ОЗС-3.
Сварку опиранием в вертикальном положении по направлению сверху вниз можно выполнять электродами АНО-9.
Сварка наклонным электродом (рис. 34, а).
Электрод опирается краем покрытия о свариваемый металл. Второй конец электрода зажат в обойме, которая во время сварки свободно опускается, скользя по штанге. Угол наклона электрода остается постоянным. Дуга возбуждается так же, как и при сварке лежачим электродом.
Производительность труда сварщика при использовании этих способов возрастает, так как один сварщик может работать сразу на нескольких постах.
Для сварки наклонным и лежачим электродом необходимы специальные электроды марок ОЗС-12, ОЗС-15Н (наклонный электрод), ОЗС-17Н. Электроды изготовляют диаметрами 4, 5, 6 мм и длиной от 450 до 700 мм.
Сварка лежачим электродом (рис. 34, б).
В разделку свариваемых деталей укладывают один или несколько электродов, длина которых обычно в два раза больше стандартных. От вытекания металла при выполнении стыкового шва предохраняет медная подкладка. При выполнении углового шва подкладка не требуется. Сверху электроды прижимаются к кромкам деталей медной или бронзовой колодкой. Дуга возбуждается вспомогательным электродом и затем продолжает гореть, расплавляя электрод и основной металл. Длина дуги равна толщине покрытия, составляющей 1,5-3,0 мм.
Сварку лежачим электродом можно осуществлять и под слоем флюса. Она может применяться для выполнения как прямолинейных, так и криволинейных швов, для чего необходимы специальные приспособления.
Рис. 34. Схема сварки:
а - наклонным электродом: 1 - электрод; 2 - обойма; 3 - штанга;
б - лежачим электродом: 1 - шов; 2 - дуга; 3 - лежачий электрод; 4 - свариваемый металл
3. Задача. Для сварки дан металл толщиной 8 мм. Объясните ваши действия по подготовке кромок металла к сварке.
В зависимости от толщины свариваемого металла сварка изделия может идти как с разделкой кромок, так и без. Разделка кромок металла начинается с толщины 5 мм, и она необходима для наилучшего провара металла на всю его толщину. В данном случае разделку осуществляют V-образную, хотя возможны и другие виды разделки (в зависимости от толщины металла и вида конструкции). После разделки зачищают кромки стыкуемых элементов, а также прилегающие к ним поверхности на длине 15-20 мм, очищают от масла, окалины, ржавчины и грязи, так как от состояния поверхности свариваемых изделий зависит качество сварного шва. Делают это стальной металлической щеткой.
Билет № 13
Вопрос 1. Электроды (классификация, маркировка, требования к хранению).
Электродом для дуговой сварки называют металлический или неметаллический стержень, предназначенный для подведения тока к сварочной дуге.
Для полуавтоматов и автоматов в качестве электрода применяют сварочную, порошковую и самозащитную проволоку.
Электроды подразделяются на плавящиеся и неплавящиеся.
Плавящиеся электроды выполнены из стали, чугуна, алюминия, меди и их сплавов. Они представляют собой определенных размеров металлические стержни, на поверхность которых опрессовкой или окунанием нанесено специальное покрытие.
Неплавящиеся электроды выполнены из технического вольфрама и его сплавов, угля и графита. Они предназначены для повышения температуры сварочной ванны при своем сгорании.
Назначение покрытия электродов.
1. Защита расплавленного металла от кислорода и азота воздуха при сварке. Это достигается газами, которые образуются из покрытия в зоне дуги.
2. Теплоизоляция расплавленного металла (для медленного процесса кристаллизации, что обеспечивает пластичность сварного шва). Пластичность - главное механическое свойство, которым должен обладать сварочный шов.
3. Для устойчивого горения сварочной дуги (в покрытие вводятся ионизирующие добавки).
4. Легирование металла шва.
Классификация покрытых металлических электродов.
По ГОСТу 9466-75 предусматривается следующая классификация электродов:
По назначению:
• У - для сварки углеродистых, низколегированных сталей;
• Л - для легированных конструкционных сталей;
• Н - для наплавки поверхностных слоев с особыми свойствами;
• Т - для сварки легированных теплоустойчивых сталей;
• В - для сварки высоколегированных сталей.
По толщине покрытия:
В зависимости от отношения диаметра покрытия (D) к диаметру стального стержня (d).
Такое отношение может иметь различное отношение, а, следовательно, электроды имеют различную толщину покрытия.
D/d≤1,2 - тонкое покрытие (М).
1,21,8 - особо толстое покрытие (Г).
По видам покрытия (табл. 3):
• А - кислое;
• Б - основное;
• Ц - целлюлозное;
• Р - рутиловое.
Таблица 3
Каждое покрытие имеет свой определенный состав, положительные и отрицательные свойства. Зная их, можно заранее предвидеть качество сварочного шва.
По допустимым пространственным положениям:
• 1 - для всех положений;
• 2 - для всех положений, кроме вертикального «сверху вниз»;
• 3 - для нижнего, горизонтального и вертикального «снизу вверх»;
• 4 - для нижнего и нижнего в «лодочку».
По роду и полярности сварочного тока для сварки переменным или постоянным током на прямой, обратной или любой полярности.
Электроды подразделяют на типы в соответствии с ГОСТами 9467-75, 10051-75 и 10052-75.
ГОСТ 9467-75 распространяется на металлические покрытые электроды для ручной дуговой сварки углеродистых, низколегированных и легированных конструкционных и легированных теплоустойчивых сталей. Для сварки углеродистых и легированных конструкционных сталей предусмотрено 14 типов электродов (например, Э38, Э42А, Э46 и т. д. до Э150), для сварки легированных теплоустойчивых сталей - 9 типов (например, Э-09М, Э-05Х2М, Э-09Х1МФ и т. д.).
Условное обозначение типа электрода расшифровывается так: буква Э - электрод; стоящее за ней число - временное сопротивление разрыву металла шва или наплавленного металла (так, электроды типа Э46 марок ОЗС-4, АНО-3, МР-1 и других должны обеспечить временное сопротивление разрыву не менее 46 кгс/мм2, или 460 МПа). Буква А в конце обозначения типа указывает на повышенные пластические свойства металла сварного шва.
Буквы и цифры, входящие в обозначение типов электродов для сварки легированных теплоустойчивых сталей, показывают примерный химический состав наплавленного металла.
Для каждого типа электрода разработана одна или несколько марок, характеризуемых маркой сварочной проволоки, составом покрытия, химическим составом, свойствами металла шва и др.
Электроды выпускают диаметрами 1,6; 2,0; 2,5; 3,0; 4,0; 5,0; 6,0; 8,0; 10,0 и 12,0 мм (диаметр электрода определяется диаметром металлического стержня).
В зависимости от диаметра электрода, а также марки сварочной проволоки, электроды изготовляют длиной 150-450 мм.
Упаковывают их в коробки или пачки массой не более 3 кг - для электродов диаметром до 2,5 мм; 5 кг - для электродов диаметром 3,0-4,0 мм; 8 кг - для электродов диаметром свыше 4,0 мм.
Вопрос 2. Предохранительные затворы (назначение, классификация, устройство, требования техники безопасности).
Предохранительные затворы - это устройства, предохраняющие ацетиленовые генераторы и газопроводы от попадания в них взрывной волны при обратных ударах пламени из сварочной горелки или резака.
Обратным ударом называется воспламенение горючей смеси в каналах горелки или резака и распространение пламени навстречу потоку горючей смеси.
Обратный удар характеризуется резким хлопком и гашением пламени. Горящая смесь газов устремляется по ацетиленовому каналу горелки или резака в шланг, а при отсутствии предохранительного затвора - в ацетиленовый генератор, что может привести к взрыву ацетиленового генератора и вызвать серьезные разрушения и травмы.
Ацетиленокислородная смесь сгорает с определенной скоростью. Горючая смесь вытекает из отверстия мундштука горелки или резака также с определенной скоростью, которая всегда должна быть больше скорости сгорания.
Если скорость истечения горючей смеси станет меньше скорости ее сгорания, то пламя проникает в канал мундштука и воспламенит смесь в каналах горелки или резака, произойдет хлопок и возникнет обратный удар пламени. Обратный удар может произойти от перегрева и засорения канала мундштука горелки.
Предохранительные затворы бывают жидкостные и сухие.
Жидкостные предохранительные затворы обычно заливают водой, сухие - заполняют мелкопористой металлокерамической массой.
Предохранительные затворы устанавливают между ацетиленовым генератором или ацетиленопроводом и горелкой или резаком. Если сварку или резку ведут от ацетиленового баллона, предохранительный затвор не ставят, потому что ацетилен из баллона в горелку или резак поступает с повышенным давлением, а установленный на баллоне редуктор и заполняющая баллон пористая масса надежно защищают баллон от пламени обратного удара.
Затворы делятся:
• по пропускной способности - 0,8; 1,25; 2,0; 3,2 м3/ч;
• по предельному давлению: низкого давления, в которых предельное давление ацетилена не превышает 0,01 МПа; среднего - 0,07 МПа; высокого давления - 0,15 МПа.
Предохранительные водяные затворы подразделяют на центральные, устанавливаемые на магистрали стационарных ацетиленовых генераторов, и постовые, устанавливаемые на ответвлениях трубопровода у каждого сварочного поста или у однопостовых ацетиленовых генераторов.
Конструкция предохранительных затворов должна отвечать следующим основным требованиям:
• обеспечивать наименьшее сопротивление потоку газа;
• задерживать прохождение ацетиленокислородного пламени с удалением взрывчатой смеси в атмосферу;
• обеспечивать минимальный вынос воды с проходящим через затвор газом;
• обеспечивать необходимую прочность при гидравлическом испытании на давление, равное 6 МПа;
• не допускать возможного прохождения кислорода и воздуха через затвор со стороны потребителя;
• каждый затвор должен иметь устройство для контроля за уровнем воды в нем;
• все части затвора должны быть доступны для очистки, промывки и ремонта.
На корпусе каждого затвора должны быть нанесены его паспортные данные.
Окрашивают водяные предохранительные затворы в белый цвет.
Водяной предохранительный затвор ЗСГ-1,25 (рис. 35). Этот затвор относится к затворам среднего давления; предельно допустимое давление - 0,15 МПа, пропускная способность - 1,25 м3/ч, масса - 2,5 кг.
Затвор состоит из цилиндрического корпуса 1 с верхним и нижним сферическими днищами. В нижнее днище ввернут обратный клапан, состоящий из корпуса 4, гуммированного клапана 3 и колпачка 2, ограничивающего подъем гуммированного клапана (гуммирование - покрытие резиной или эбонитом рабочей поверхности металлических деталей для предохранения от коррозии и действия агрессивных сред). Обратный клапан имеет отверстие слива воды, закрытое пробкой 6, и ниппель 7 для ввода ацетилена в затвор.
Сетка 5 предназначена для задержки частиц карбидного ила, окалины и других твердых частиц. В верхней части затвора расположен пламепреградитель 10 и штуцер 11, в нижней части - рассекатель 14.
Пробка 8 предназначена для слива воды. Вода в затвор заливается до уровня контрольной пробки 9 при вывернутой накидной гайке 12 и снятом ниппеле 13.
Ацетилен поступает в затвор по газоподводящей трубке, приподняв гуммированный клапан, проходит через слой воды, затем выходит через ниппель 13 в шланги горелки или резака.
Рис. 35.
Предохранительный затвор ЗСГ-1,25
При обратном ударе ацетиленокислородного пламени клапан прижимается давлением воды к седлу и препятствует проникновению ацетилена из генератора в затвор, а пламя гасится столбом воды.
При возникновении обратного удара в генераторе с использованием сухого затвора, ударная волна на входе в затвор разрушается пламеотбойником, и пламя гасится в порах пламегасящего элемента.
Под действием давления мембрана давит на шток, который перемещается, воздействуя на клапан, закрывая входное отверстие для доступа газа в затвор.
При использовании газов - заменителей ацетилена (кроме водорода), допускается вместо предохранительных затворов использовать обратные клапаны. При нормальной работе газ своим давлением отодвигает шарик с ножкой, проходит в корпус клапана и далее через штуцер в горелку (рис. 36).
При засорении мундштука горелки кислород, имеющий большее давление, чем горючий газ, устремляется по шлангу в клапан. Шарик давлением кислорода прижимается к седлу и перекрывает проникновение кислорода в трубопровод горючего газа (рис. 37). Перед установкой необходимо очистить детали клапанов от следов коррозии и пыли.
Рис. 36. Нормальная работа клапана
Рис. 37. Работа клапана при обратном ударе пламени
3. Задача. Расшифруйте условное обозначение электродов на этикетке
Э50А - тип электрода;
ЦУ-7 - марка электрода;
5,0 - диаметр электрода;
У - для сварки углеродистых сталей;
Д - толстое покрытие;
Е431(5) - характеристика наплавленного металла;
Б - основное покрытие;
2 - для всех пространственных положений, кроме вертикального «сверху-вниз»;
О - постоянный ток обратной полярности.
Билет № 14
Вопрос 1. Назначение и устройство сварочного выпрямителя.
Сварочные выпрямители служат для преобразования переменного тока в постоянный, предназначенный для питания сварочной дуги. С этой целью в выпрямителях используются полупроводниковые (селеновые, кремниевые или германиевые) выпрямительные элементы. Сварочный выпрямитель (рис. 38) состоит из понижающего трехфазного трансформатора 3 с подвижными катушками, выпрямительного блока 2 с охлаждающим вентилятором 1, пускорегулирующей и защитной аппаратурой, смонтированных в общем корпусе.
Рис. 38. Сварочный выпрямитель
Понижающий трехфазный трансформатор снижает напряжение сети до необходимого рабочего, а так же служит для регулирования сварочного тока изменением расстояния между первичной и вторичной обмотками. Внутри сердечника трансформатора находится ходовой винт с закрепленной на нем первичной обмоткой. Сварочный выпрямитель имеет два диапазона регулирования сварочного тока.
Сварка выпрямленным током может производиться на прямой и обратной полярности. При прямой полярности деталь подсоединяется к зажиму «+» источника, а электрод - к зажиму «-», при обратной полярности - наоборот.
На положительном полюсе в результате бомбардировки его электронами выделяется больше теплоты, чем на отрицательном. Исходя из этого, обратную полярность применяют при сварке тонколистового металла, чтобы не прожечь его, а также при сварке высоколегированных сталей во избежание их перегрева.
Обозначение выпрямителя читается следующим образом: ВД-401, где:
В - выпрямитель;
Д - для дуговой сварки;
40 - 400 А - номинальный ток;
1 - модель.
Многопостовой выпрямитель имеет маркировку ВДМ.
Вопрос 2. Защитные газы (назначение, классификация, свойства).
В качестве защитных газов при дуговой сварке плавлением применяют инертные или активные газы, а также смеси различных газов в разных пропорциях. Эти газы оттесняют воздух от сварочной ванны и тем самым предохраняют металл шва от воздействия азота и кислорода воздуха.
Инертные газы - это одноатомные газы, которые в чистом виде не вступают в химические реакции как с твердыми, так и с жидкими металлами и практически нерастворимы в большинстве из них. Из инертных газов для сварки используют аргон, гелий и их смеси.
Аргон (Аг) - это негорючий и невзрывоопасный газ без цвета и запаха. Выпускают его по ГОСТу 10157-79, согласно которому аргон предназначается для использования в качестве защитной среды при сварке, резке и плавке активных и редких металлов и сплавов на их основе, алюминия, алюминиевых и магниевых сплавов, нержавеющих хромоникелевых жаропрочных сплавов и легированных сталей различных марок.
Получают аргон из атмосферного воздуха.
В зависимости от содержания примесей аргон выпускают двух сортов: высшего - не менее 99,992% (об.) Аг и первого - не менее 99,987% (об.) Аг. Хранят и транспортируют газообразный аргон в стальных баллонах под давлением 15 МПа (150 ат.).
Гелий (Не) - это инертный газ без цвета и запаха, значительно легче воздуха. Получают его путем неоднократного сжатия и охлаждения природных газов до температур конденсации с последующим отделением примесей. В небольшом количестве гелий находится в воздухе, из которого он может быть получен в качестве побочного продукта при производстве кислорода. Гелий примерно в 10 раз легче аргона, что усложняет защиту сварочной ванны и приводит к его повышенному расходу. Стоимость гелия примерно в 5 раз выше стоимости аргона.
Чаще всего гелий используют для образования инертных газовых смесей. Обладая большей плотностью, чем гелий, такие смеси лучше защищают металл сварочной ванны от воздуха.
Наибольшее применение получила инертная газовая смесь, состоящая из 70% (об.) аргона и 30% (об.) гелия. Выпускают гелий по ТУ 51-689-75 двух сортов: особой чистоты и высокой чистоты. Хранят и транспортируют его так же, как и аргон.
Активные газы защищают зону сварки от доступа кислорода и азота воздуха, но вместе с тем химически реагируют со свариваемым металлом или физически растворяются в нем.
Из активных газов для сварки используют в основном углекислый газ. Другие активные газы, такие как кислород, водород, азот, используют, как правило, для составления защитных газовых смесей.
Углекислый газ, или диоксид углерода (С02), в нормальных условиях представляет собой бесцветный газ без запаха. Он тяжелее воздуха, что обеспечивает хорошую газовую защиту сварочной ванны, но его накапливание в зоне сварки (выше 5%) может вызвать явление кислородной недостаточности и удушья. Поэтому рабочие места сварщиков должны быть оборудованы приточно-вытяжной вентиляцией.
Получают углекислый газ из отходящих газов при производстве аммиака, спиртов, нефтепереработки, а также на базе специального сжигания топлива. При повышении давления углекислый газ переходит в жидкое (углекислота), а затем - в твердое состояние (сухой лед). При испарении 1 кг жидкого диоксида углерода образуется 509 л газообразного диоксида углерода (углекислого газа).
Выпускают углекислый газ по ГОСТу 8050-76.
В зависимости от области применения, а также по физико-химическим показателям диоксид углерода выпускают трех марок: сварочный - не менее 99,5% (об.) С02, пищевой - не менее 98,8% (об.) С02 и технический - не менее 98,5% (об.) С02.
Хранят и транспортируют его в виде жидкости в стальных баллонах под давлением 490-588 МПа. В стандартный баллон емкостью 40 л заливают 25 л жидкого диоксида углерода, при испарении которого образуется 12600 л углекислого газа.
Кислород (02) - это бесцветный газ без запаха и вкуса, поддерживающий горение. Получают его из атмосферного воздуха методом глубокого охлаждения или электролизом воды. Выпускают кислород по ГОСТу 5583-78. Хранят и транспортируют в стальных баллонах под давлением 15 МПа.
При дуговой сварке плавлением технический кислород используют при составлении защитных газовых смесей, таких как Аг+02; С02+02 и др.
Смесь аргона с 2-5% кислорода повышает устойчивость горения дуги и улучшает качество формирования сварного шва. Такие смеси рекомендуется применять при сварке плавящимся электродом легированных сталей, когда требуется струйный перенос электродного металла. При сварке низкоуглеродистых и низколегированных сталей плавящимся электродом применяют смесь углекислого газа с 20% кислорода, обеспечивающую глубокое проплавление и хорошее формирование шва, минимальное разбрызгивание, высокую плотность металла шва.
Водород (Н2) - это горючий газ, не имеющий цвета, запаха и вкуса. Смеси его с кислородом и воздухом взрывоопасны.
В зависимости от способа получения водород выпускают по ГОСТу 3022-80 трех марок - А, Б и В с содержанием от 95 до 99,99% (об.) Н2. Хранят и транспортируют в стальных баллонах под давлением 15 МПа.
Применяют водород для составления плазмообразующих смесей при плазменной сварке и резке. Так, для защиты сварочной ванны от окисления при плазменной сварке легированной стали, меди, никеля и сплавов на его основе используют смесь аргона с 5-8% водорода.
Аргоноводородную смесь, имеющую до 20% Н2, применяют при микроплазменной сварке. Наличие водорода в смеси обеспечивает сжатие столба плазмы, делает его более сконцентрированным. Кроме того, водород создает необходимую в ряде случаев восстановительную атмосферу.
Азот (N2) - это бесцветный газ без запаха плотностью 1,25 кг/м3. Получают его из атмосферного воздуха способом глубокого охлаждения. Выпускают азот по ГОСТу 9293-74 газообразным и жидким. Хранят и транспортируют его в стальных баллонах под давлением 15 МПа.
По физико-химическим показателям газообразный азот разделяют на четыре сорта: высший - не менее 99,994% (об.) N2, первый - не менее 99,6% (об.) N2, второй - не менее 99% (об.) N2, третий - не менее 97% (об.) N2.
Используют азот при составлении защитных газовых смесей. Так, смесь аргона с добавкой 10-30% (об.) азота применяют при сварке меди, а также аустенитной нержавеющей стали некоторых марок.
Для предохранения от коррозии и быстрого опознавания баллоны с защитными газами окрашивают в различные цвета и делают на них соответствующие надписи (табл. 4).
Таблица 4
Окраска баллонов для защитных газов
3. Задача. Объясните ваши действия по окончании отбора газа из баллона.
По окончании отбора газа из баллона необходимо следить за его остаточным давлением.
Баллоны для сжатых газов (кислорода) при отправке на завод-наполнитель должны иметь остаточное давление газа не менее 0,05 МПа.
Баллоны с растворенным ацетиленом должны иметь остаточное давление не менее 0,05-0,1 МПа (в зависимости от температуры). Это необходимо для того, чтобы проверить, какой газ был в баллоне, во избежание образования взрывоопасных смесей.
Билет № 15
Вопрос 1. Основные требования к сварке низко- и среднеуглеродистых сталей.
Различают:
• низкоуглеродистые стали, содержащие до 0,25% углерода;
• среднеуглеродистые, содержащие от 0,25 до 0,6% углерода;
• высокоуглеродистые, содержащие от 0,6 до 2,0% углерода.
К углеродистым относят стали, не содержащие легирующих компонентов (кроме углерода). В низкоуглеродистых сталях присутствуют марганец и кремний, однако они не считаются легирующими компонентами, если содержание марганца не превышает 1% и кремния 0,8%.
Большинство сварных конструкций изготовляется из низкоуглеродистых сталей, выпускаемых в виде листов и фасонного проката, - уголка, швеллеров, двутавровых балок и пр.
Дуговая сварка.
Для сварки низкоуглеродистых сталей применяют электроды типов Э42, Э42А, Э46 по ГОСТу 9467-60 с рутиловыми, фтористо-кальциевыми, рудно-кислыми и органическими покрытиями. Род тока, полярность и величину тока выбирают в соответствии с характером покрытия, толщиной металла, типом шва и диаметром электрода.
Низкоуглеродистые стали хорошо свариваются дуговой сваркой и другими способами.
Применяются электроды различных марок с покрытиями типов АНО, УОНИ, ОЗС, ЦМ, MP, УП, К и др.
Выбор электрода должен обеспечивать:
• равнопрочность сварного соединения с основным металлом;
• бездефектные швы;
• заданный состав металла шва.
Для особо ответственных конструкций используют электроды с основным покрытием типа Э42А марок УОНИ-13/45, УП-1/45, обеспечивающие повышенные пластические свойства и стойкость металла шва против кристаллизационных трещин.
При сварке угловых швов толстого металла и первого слоя многослойного шва, когда скорость охлаждения достаточно велика, иногда используют предварительный подогрев основного металла до 120-150ºС для предупреждения появления закалочных структур и кристаллизационных трещин.
Среднеуглеродистые стали (углерод от 0,26 до 0,45%). При их сварке применяется предварительный и сопутствующий подогрев при сварке до температуры 250-300°С.
Высокотемпературный подогрев вреден, так как вызывает появление трещин вследствие увеличения глубины провара основного металла и повышения содержания углерода в металле шва.
Лучшие результаты дает сварка постоянным током прямой полярности. Высокую стойкость металла шва против кристаллизационных трещин и необходимую прочность сварного соединения обеспечивает применение электродов УОНИ-13/55 и УОНИ-13/45.
Во избежание образования хрупких и малопластичных закалочных структур в околошовной зоне полезно медленное остывание изделия после сварки.
В ряде случаев приходится прибегать к последующей термической обработке (закалке с отпуском).
Из высокоуглеродистых сталей, как правило, не изготавливают сварные конструкции. Необходимость их сварки может возникнуть при ремонтных работах, наплавке.
В этом случае применяют те же приемы сварки и наплавки, что и для других плохо сваривающихся сталей (предварительная и последующая термообработка, предварительный и сопутствующий подогрев, соответствующие марки электродов и режимы сварки).
Газовая сварка.
Низкоуглеродистые стали свариваются газовой сваркой без особых затруднений.
Сварку ведут нормальным пламенем и, как правило, без флюса.
Наконечник горелки при левом способе сварки выбирают из расчета расхода ацетилена 100-130 дм3/ч на 1 мм толщины свариваемого металла, а при правом способе - 120-150 дм3/ч на 1 мм толщины металла.
Кромки под сварку подготавливают в зависимости от толщины свариваемого изделия. Диаметр присадочной проволоки также подбирается в зависимости от толщины свариваемого металла по следующей формуле:
• при левом способе сварки dп=S/2+1 мм;
• при правом способе сварки dп=S/2 мм,
где dп - диаметр присадочной проволоки, мм;
S - толщина свариваемого металла, мм.
Высококвалифицированные сварщики применяют пламя большой мощности, наконечник выбирают из расчета расхода ацетилена 150-200 дм3/ч на 1 мм толщины свариваемого металла, используя при этом присадочную проволоку большего диаметра; пламя горелки должно быть нормальным. Производительность сварки при этом повышается.
Для неответственных конструкций в качестве присадки применяют сварочную проволоку Св-08 и Св-08А. При сварке этими проволоками часть компонентов, таких как С, Si и Мn, выгорают, а металл шва приобретает крупнозернистую структуру. Предел прочности такого соединения ниже предела прочности основного металла.
Для получения равнопрочного с основным металлом соединения при сварке ответственных конструкций необходимо применять кремнемарганцовистую сварочную проволоку Св-08Г, Св-08ГА, Св-10ГА или Св-14ГС.
Во время сварки необходимо следить за тем, чтобы кромки свариваемого металла и конец присадочной проволоки расплавлялись одновременно. Конец присадочной проволоки должен быть погружен в ванночку расплавленного металла. Нельзя допускать, чтобы капли расплавленного металла попадали на нерасплавленные кромки основного металла, так как это приводит к непровару, что снижает механические характеристики соединения.
Если конец присадочной проволоки прилипает к свариваемым кромкам основного металла, это значит, что они недостаточно нагреты.
В процессе сварки следует избегать отклонения сварочного пламени от ванны расплавленного металла шва, так как это может привести к окислению металла шва кислородом воздуха.
Сварные швы должны иметь равномерно чешуйчатую поверхность, а также равномерную ширину и высоту наплавленного валика.
Переход от основного металла к наплавленному должен быть плавным, без подрезов. В процессе сварки горелкой производят равномерные и непрерывные колебательные и поступательные движения. Колебательные движения выбираются в зависимости от толщины свариваемого металла.
Для уплотнения и повышения пластичности наплавленного металла применяют проковку и последующую термообработку шва. Проковку рекомендуется начинать при температуре светло-красного и заканчивать при температуре темно-красного каления.
Проковка при более низкой температуре может привести к появлению микроскопических трещин в металле шва или околошовной зоне.
При сварке ответственных и толстостенных изделий применяют термическую обработку сварных соединений. В качестве горючего газа при сварке низкоуглеродистой стали применяют ацетилен или пропан-бутан; пропан-бутановым пламенем сваривают таким образом, чтобы расстояние от конца ядра пламени до свариваемой поверхности было 8-10 мм. Пропан-бутан применяется для сварки неответственных деталей.
Для сварки высокоуглеродистых сталей используются флюсы.
Вопрос 2. Сварочные автоматы (назначение, устройство, принцип действия, основные характеристики).
Общие сведения и классификация автоматов для дуговой сварки. При автоматических и механизированных способах сварки помимо источников питания дуги необходимо иметь специальное оборудование, позволяющее исключить ручное ведение сварочного процесса. При этом требуется механизировать выполнение двух основных технологических движений: подачу электрода в зону сварки и перемещение дуги вдоль свариваемых кромок.
Если при сварочном процессе оба эти движения осуществляются механизированным путем, то такой процесс рассматривается как автоматическая сварка.
Если одно из движений - подача электрода в зону сварки - осуществляется механизированным способом, а другое - перемещение дуги вдоль свариваемых кромок - вручную, то такой процесс рассматривается как механизированная (полуавтоматическая) сварка.
Если оба движения выполняются вручную сварщиком, то такой процесс называется ручной дуговой сваркой.
Сварочные аппараты, обеспечивающие автоматическое выполнение основных технологических перемещений электрода и дуги с поддержанием постоянства заданных параметров сварочного режима (напряжения дуги, сварочного тока, скорости сварки), называют автоматами.
Основной частью автоматов является сварочная головка, представляющая собой электромеханическое устройство, осуществляющее автоматическую подачу в зону дуги плавящегося электрода или присадочного металла.
Сварочную головку, закрепленную неподвижно относительно изделия, называют подвесной автоматической головкой. В подвесных головках отсутствует механизм перемещения самой головки. В этом случае относительно дуги перемещают объект сварки с помощью вспомогательного устройства или сварочного приспособления.
Если же в конструкции сварочного аппарата имеется механизм для перемещения головки, то ее называют самоходной. Перемещение самоходной головки обычно производится по специальной направляющей. Такой аппарат называют автоматом подвесного типа.
Если в конструкции автомата тележка с укрепленной на ней головкой может перемещаться непосредственно по свариваемому изделию, то такой автомат называют сварочным трактором (рис. 39).
В основе классификации автоматов лежат различные признаки: тип электрода, способ перемещения, характер защиты и др.
Рис. 39. Схема автомата для сварки плавящимся электродом:
1 - тележка; 2 - подающий механизм; 3 - кассета с электродной проволокой; 4 - горелка; 5 - пульт управления
По типу применяемого электрода автоматы подразделяют на:
• автоматы с плавящимся электродом;
• автоматы с неплавящимся (вольфрамовым) электродом.
По способу перемещения тележки различают:
• автоматы тракторного типа;
• кареточные.
По способу защиты сварочной ванны различают автоматы:
• для сварки под флюсом;
• в среде защитных газов;
• универсальные.
По пространственному выполнению сварных соединений различают автоматы для сварки швов в:
• нижнем;
• вертикальном;
• горизонтальном положениях;
• кольцевых поворотных и неповоротных стыков;
• кольцевых в горизонтальной плоскости.
По способу поддержания постоянства параметров дуги выпускают автоматы:
• с принудительным регулированием дуги;
• саморегулированием.
По числу горящих дуг различают автоматы для сварки:
• одной дугой;
• двумя дугами;
• трехфазной дугой.
Комплектование и основные узлы сварочных автоматов. Сварочные автоматы комплектуются из следующих основных узлов:
• сварочной головки;
• тележки;
• пульта управления;
• аппаратного шкафа;
• кассет со сварочной проволокой.
Основными элементами сварочной головки являются механизм подачи проволоки, подающие ролики, токоподводящий мундштук и устройства для установочных перемещений головки.
Механизм подачи состоит из электродвигателя и редуктора. При использовании электродвигателей переменного тока применяют регулируемые редукторы. Электродвигатели постоянного тока могут работать в сочетании с нерегулируемыми редукторами.
Подающие ролики расположены на выходных валах редуктора. Их назначение - стабильная подача сварочной проволоки без проскальзывания. Обычно это достигается при использовании двух пар подающих роликов.
К корпусу редуктора крепится токоведущий мундштук для обеспечения электрического контакта и направления проволоки в сварочную ванну. Мундштук должен обеспечивать минимальное блуждание торца электрода относительно сварочной ванны. Для этого иногда на головку перед мундштуком устанавливают роликовый правильный механизм для правки проволоки. Кроме того, в мундштуке должен обеспечиваться надежный электрический контакт со сварочной проволокой.
Конструкции мундштуков различны в зависимости от способа сварки, диаметра и жесткости проволоки. Для сварки электродной проволокой большого диаметра (3-5 мм) наибольшее распространение получили мундштуки с роликовым скользящим контактом.
При использовании проволок меньшего диаметра (0,8-2,5 мм) применяют трубчатые мундштуки. Скользящий контакт поддерживается за счет сменных наконечников мундштука.
Применяют также мундштуки колодочного типа, состоящие из двух подпружиненных колодок, и мундштуки сапожкового типа.
Конструкция подвески сварочной головки должна обеспечивать возможность ее установочных перемещений: вертикальное - для установления необходимого вылета электрода или угла наклона его относительно свариваемого стыка; поперечное - для установки торца электрода по центру стыка в начале и корректировки его в процессе сварки.
Тележка предназначена для перемещения головки вдоль свариваемого стыка. В большинстве автоматов тележка выполняет роль базового элемента. На ее корпусе устанавливают сварочную головку, кассету для проволоки и пульт управления автоматом. Тележка должна обеспечивать плавность хода в широком диапазоне скоростей сварки.
Различают тележки тракторного и кареточного типов.
Тележка тракторного типа перемещается с помощью бегунковых колес либо по направляющим рельсам, либо непосредственно по свариваемому изделию.
Тележка кареточного типа перемещается только по направляющим стапеля или устройства крепления самого автомата. Конструкция направляющих элементов зависит от формы свариваемого стыка.
Для сварки продольных прямолинейных швов часто применяют консольные направляющие. Автоматы консольного типа универсальны. Их можно использовать и для сварки поворотных кольцевых швов. Применяются также направляющие портального типа, смещенные относительно изделия и установленные непосредственно на приспособлениях с закрепленными в них изделиями. В автоматах для сварки неповоротных кольцевых стыков каретка перемещается по направляющим, имеющим форму окружности.
Для перемещения каретки используют механизмы с бегунковыми колесами, зубчатыми рейками, ходовыми винтами. Тележки автоматов перемещаются с помощью электродвигателей через редуктор. В автоматах с электроприводом постоянного тока скорость перемещения тележки регулируется изменением частоты вращения двигателя. В приводах переменного тока настройку скорости тележки осуществляют сменными шестернями в редукторе.
В зависимости от способов сварки сварочные автоматы могут снабжаться дополнительными устройствами. Так, при сварке под флюсом сварочные автоматы имеют специальную флюсовую аппаратуру, предназначенную для подачи флюса в зону сварки, удержания его на поверхности шва во время сварки и уборки его по окончании процесса. Такие устройства выполняются в виде съемных бункеров, в которые флюс засыпается и подается самотеком в место сварки в ходе выполнения сварного шва. Иногда применяют специальные флюсоподающие и убирающие аппараты, работающие с помощью сжатого воздуха.
В автоматах для сварки в защитных газах вместо обычного токоподводящего мундштука используется специальная сварочная горелка, в которой помимо токоподвода, имеются устройства для подачи защитного газа в зону сварки и принудительного охлаждения горелки от перегрева.
Основные принципы работы сварочных автоматов. Устойчивый процесс сварки и хорошее качество сварных швов обеспечиваются при оптимально выбранных параметрах режима сварки.
К основным параметрам режима относят:
• напряжение дуги;
• силу сварочного тока;
• скорость сварки.
Эти параметры необходимо не только правильно установить, но и поддерживать их неизменно постоянными в процессе сварки.
Наиболее часто подвержено изменениям напряжение дуги, находящееся в прямой зависимости от ее длины. При сварке плавящимся электродом постоянство длины дуги обеспечивается при равенстве скорости подачи электродной проволоки в зону сварки и скорости ее расплавления.
Если скорость подачи проволоки больше скорости ее расплавления, то произойдет уменьшение длины дуги и может возникнуть короткое замыкание электрода с изделием.
Если скорость расплавления проволоки больше скорости ее подачи, то дуга удлиняется вплоть до обрыва и прекращения процесса.
Нарушение равенства скоростей происходит по ряду причин: колебания напряжения в сети, наличие волнистости и неровностей свариваемых поверхностей деталей, неравномерность подачи электродной проволоки за счет пробуксовывания в подающих роликах, наличие прихваток по длине свариваемых кромок, воздействие магнитного дутья, отклоняющего дугу, и т. д.
Сварочная головка автомата реагирует на эти нарушения и восстанавливает нормальную (заданную) длину дуги.
В применяемых сварочных автоматах используют два принципа регулирования дуги по напряжению:
• саморегулирование дуги при постоянной скорости подачи электрода;
• принудительное регулирование, при котором скорость подачи электрода автоматически изменяется в зависимости от напряжения дуги.
На основе принципа саморегулирования дуги разработан ряд сварочных автоматов, работающих с постоянной, не зависящей от напряжения дуги скорости подачи проволоки. Они просты в устройстве и надежны в работе.
Другой вид автоматов основан на изменении скорости подачи электродной проволоки в зависимости от напряжения на дуге. Если по какой-то причине длина дуги возрастает, то возрастает и напряжение дуги. Двигатель привода подачи электродной проволоки начнет вращаться быстрее, увеличивая скорость подачи проволоки.
3. Задача. Перед вами несколько редукторов. Объясните, как определить по внешнему виду, для какого газа они предназначены.
Редукторы окрашиваются в те же цвета, что и баллоны, на которые они устанавливаются. Также кислородный редуктор имеет правую резьбу крепления, а ацетиленовый - левую, причем фиксируется еще хомутом.
Билет № 16
Вопрос 1. Флюсы (назначения, классификация, применение).
Сварочные флюсы применяют при автоматической и механизированной дуговой сварке под флюсом, при ручной дуговой сварке чугуна и цветных металлов. Они представляют собой сыпучее зернистое вещество, которое при расплавлении образует жидкий шлак, защищающий металл сварного шва от азота и кислорода воздуха.
Кроме того, назначение флюсов следующее:
• обеспечение устойчивого горения дуги;
• раскисление сварочной ванны и получение плотных швов без пор и шлаковых включений;
• легирование металла шва;
• уменьшение потерь электродного металла на угар и разбрызгивание;
• улучшение формирования шва;
• сохранение теплоты в зоне сварки, вследствие чего химические реакции между жидким металлом и шлаком проходят более полно.
По способу изготовления флюсы делят на:
• плавленые;
• неплавленые.
Плавленые флюсы изготовляют сплавлением флюсовой шихты определенного состава в электрических или пламенных печах с последующей ее грануляцией до получения крупинок (зерен) требуемого размера.
По строению зерен плавленые флюсы разделяют на:
• стекловидные;
• пемзовидные.
Стекловидный флюс представляет собой прозрачные зерна с острыми гранями, окрашенными в зависимости от состава флюса в различные цвета. Для его получения жидкий расплав флюса при 1200-1250°С тонкой струей сливают в бак с холодной проточной водой. Расплав быстро затвердевает и растрескивается на мелкие зерна.
Пемзовидный флюс представляет собой зерна пенистого материала также различных оттенков. При выливании в воду жидкого расплава флюса, нагретого до 1550-1600°С, пары воды вспенивают расплавленную массу, образуя пемзовидный флюс.
Плавленые флюсы (ГОСТ 9087-81), применяемые при автоматической и механизированной дуговой и электрошлаковой сварке и наплавке стали, выпускают 21 марки.
Размер зерен флюса - от 0,25 до 4 мм. Флюсы - стекловидный с размером зерен не более 2,5 мм и пемзовидный с размером зерен не более 4 мм – предназначены для автоматической сварки проволокой диаметром не менее 3 мм. Стекловидный флюс с размером зерен не более 1,6 мм предназначен для автоматической и механизированной сварки проволокой диаметром не более 3 мм.
Флюс упаковывают в бумажные мешки или другую тару, обеспечивающую его сохранность при транспортировании. Масса одного упаковочного места должна быть не более 50 кг.
Плавленые флюсы различных марок имеют разные области применения. Например: АН-17М, АН-43, АН-47 - для дуговой сварки и наплавки углеродистых низколегированных сталей.
Кроме плавленых широко применяют и неплавленые (керамические) флюсы, получаемые скреплением частиц флюсовой шихты без их расплавления. Они представляют собой механическую смесь тонкоизмельченных природных минералов, ферросплавов и силикатов, сцементированных жидким стеклом и гранулированных на крупинки определенных размеров. Каждое зерно (крупинка) керамического флюса состоит из прочно соединенных мелких частичек и содержит все компоненты флюса в определенном соотношении.
Керамические флюсы различных марок имеют определенные области применения, например:
АНК-35 и АНК-36 используют для сварки углеродистых сталей;
АНК-47 и АНК-48 - для сварки низколегированных сталей;
АНК-45 - для сварки высоколегированных сталей;
АНК-18, АНК-19 и АНК-40 - при наплавочных работах;
АНК-3 служит добавкой (в количестве 5-15%), применяемой в смеси с плавлеными флюсами АН-348А, ОСЦ-45, АН-60 и другими для повышения стойкости швов против образования пор. Наиболее распространенным видом флюса является вещество бура.
Керамические флюсы гигроскопичны, поэтому хранить их следует в герметически закрывающейся упаковке. Ввиду небольшой прочности зерен транспортировать керамический флюс рекомендуется в жесткой таре - металлических банках или картонных барабанах.
Вопрос 2. Способы газовой сварки (назначение, техника выполнения).
В практике различают два способа ручной газовой сварки: правый и левый.
Левым способом газовой сварки (рис. 40, а) называется такой способ, при котором сварку ведут справа налево, сварочное пламя направляют на еще несваренные кромки металла, а присадочную проволоку перемещают впереди пламени.
Левый способ наиболее распространен и применяется при сварке тонких и легкоплавких металлов. При левом способе сварки кромки основного металла предварительно подогревают, что обеспечивает хорошее перемешивание сварочной ванны. При этом способе сварщик хорошо видит свариваемый шов, поэтому внешний вид шва получается лучше, чем при правом способе.
Правый способ сварки (рис. 40, 6) - это такой способ, когда сварку выполняют слева направо, сварочное пламя направляют на сваренный участок шва, а присадочную проволоку перемещают вслед за горелкой.
Мундштуком горелки при правом способе выполняют незначительные поперечные колебания.
Так как при правом способе пламя направлено на сваренный шов, то обеспечивается лучшая защита сварочной ванны от кислорода и азота воздуха и замедленное охлаждение металла шва в процессе кристаллизации. Качество шва при правом способе выше, чем при левом. Теплота пламени рассеивается меньше, чем при левом способе.
Поэтому при правом способе сварки угол разделки шва делается не 90°, а 60-70°, что уменьшает количество наплавляемого металла и коробление изделия.
Правый способ экономичнее левого, производительность сварки при правом способе на 20-25% выше, а расход газов на 15-20% меньше, чем при левом.
Правый способ целесообразно применять при сварке деталей толщиной более 5 мм и при сварке метал лов с большой теплопроводностью. При сварке металла толщиной до 3 мм более производителен левый способ.
Рис. 40. Способы сварки: а - левый; б - правый
Мощность сварочной горелки для стали при правом способе выбирается из расчета ацетилена 120-150 дм3/ч, а при левом - 100-130 дм3/ч на 1 мм толщины свариваемого металла.
Диаметр присадочной проволоки выбирается в зависимости от толщины свариваемого металла и способа сварки.
При левом способе сварки диаметр присадочной проволоки d=S/2+1 мм, а при правом d=S/2 мм, где S - толщина свариваемого металла, мм.
3. Задача. Нужно, используя газовую сварку, соединить трубы диаметром 45 мм, толщиной стенки 3 мм. Назовите диаметр проволоки, количество слоев сварки.
Трубы сваривают в один слой поворотным способом, левым способом, так как он применяется при сварке металла толщиной до 5 мм, диаметр проволоки 2,5 мм.
Билет № 17
Вопрос 1. Металлургические процессы при сварке плавлением.
Сварка отличается от других металлургических процессов следующими особенностями: а) происходит при высокой температуре нагрева; б) протекает с большой скоростью; в) характеризуется очень малыми объемами нагретого и расплавленного металла; г) при сварке имеет место быстрый отвод тепла от расплавленного металла сварочной ванны в прилегающие к ней зоны твердого основного металла; д) на расплавленный металл в зоне сварки воздействуют окружающие его газы и шлаки.
Высокая температура при сварке сильно ускоряет процессы плавления электродного и основного металла, электродного покрытия и флюса. При этом происходит выделение газов (в основном за счет окисления углерода), испарение, разбрызгивание и окисление веществ, участвующих в химических реакциях в зоне сварки.
Молекулы кислорода, азота, водорода при высоких температурах дуги частично распадаются на атомы (диссоциируют). В атомарном состоянии эти элементы обладают высокой химической активностью. Вследствие этого окисление элементов, насыщение металла азотом, поглощение водорода в процессе сварки протекают более интенсивно, чем при обычных металлургических процессах.
Малые объемы расплавленного металла в сварочной ванне и интенсивный отвод тепла в окружающий металл обусловливают кратковременность протекающих химических реакций.
Химический состав, структура и плотность металла шва зависят от состава основного и присадочного металла, характера и состава газов, окружающих жидкий металл, режима сварки и прочих факторов.
Указанные особенности металлургических процессов при сварке затрудняют получение сварных швов высокого качества.
Рассмотрим основные реакции в зоне сварки для стали, как наиболее распространенного металла, подвергаемого сварке.
Окисление. Кислород является наиболее вредной примесью в зоне сварки, так как окисляет элементы, входящие в состав металла шва, и ухудшает его качество, образуя химические соединения - окислы.
Окисление элементов в основном происходит за счет кислорода, содержащегося в газах и шлаках сварочной зоны. В меньшей степени окисление может быть вызвано кислородом поверхностных окислов свариваемого металла (окалины, ржавчины). При случайном увеличении длины дуги капли электродного металла могут окисляться кислородом окружающего воздуха.
С железом кислород образует три окисла: FeО, Fe2О3, Fe3О4.
Наибольшее влияние на свойства стали оказывает оксид железа FeO, так как только он растворяется в железе. Растворимость оксида железа в стали зависит главным образом от содержания углерода и температуры металла. С увеличением содержания углерода в стали растворимость оксида железа снижается. При высокой температуре стали растворимость оксида железа выше, чем при низкой температуре.
Поэтому при охлаждении стали происходит выпадение из раствора оксида железа FeO. При высоких скоростях охлаждения часть оксида железа остается в растворе, образуя шлаковые прослойки между зернами металла.
При сварке стали в первую очередь окисляется железо, поскольку оно является основным элементом в стали. Другие элементы, входящие в состав стали (углерод, кремний, марганец), окисляются (выгорают) тем быстрее, чем больше химическое сродство данного элемента с кислородом.
При сварке металла, покрытого ржавчиной, содержащаяся в ней влага испаряется, пары воды разлагаются на водород и кислород, который окисляет железо в FeO.
Присутствие кислорода в металле шва в виде твердого раствора или включений окислов понижает механические свойства, снижает стойкость металла против коррозии, делает металл ломким.
Таким образом, главным условием получения наплавленного металла высокого качества является его защита от окисления кислородом окружающей среды. Это достигается созданием вокруг расплавленного металла защитной среды из газов и шлаков, а также раскислением металла шва.
Раскисление. Процесс удаления кислорода из наплавленного металла с целью повышения его качества называется раскислением. Раскисление ведется путем введения в сварочную ванну элементов - раскислителей (марганец, кремний, алюминий, титан). Раскислители входят в состав сварочной проволоки или электродных покрытий и флюсов, откуда они поступают в сварочную ванну, вступают в реакцию с оксидом железа FeO, выводя его в шлак.
Рафинирование - процесс удаления вредных примесей из сварного шва (сера, фосфор). Серу удаляют введением марганца, который образует химическое соединение (сернистый марганец), не растворимое в жидком металле, которое полностью переходит в шлак. Фосфор также в ходе химических реакций переходит в шлак.
Легирование - процесс введения в сплав элементов, придающих ему требуемые свойства. Путем легирования металла шва его пополняют элементами, содержание которых уменьшилось вследствие выгорания их при сварке. Легирующие элементы входят в состав проволоки электрода, его покрытие, во флюс. Чем лучше раскислен наплавленый металл, тем большее количество легирующего элемента им усваивается.
Рассмотрим вопрос о строении сварного шва.
Сварной шов имеет следующие зоны: основной металла, металл шва, зона сплавления, зона термического влияния.
Основной металл, который в процессе сварки нагревается и частично расплавляется. Чем выше температура нагрева, тем большие изменения будет претерпевать металл.
Металл шва образуется в результате кристаллизации расплавленных основного и электродного (присадочного) металлов. Доля электродного металла шва составляет при ручной дуговой сварке от 50 до 70%, при сварке под флюсом - от 30 до 40%.
Зона сплавления, расположенная на границе между основным и наплавленным металлом. Если зерна основного и наплавленного металла хорошо срослись и как бы проникают друг в друга, то такие швы обладают наибольшей прочностью. Зона сплавления имеет очень малую ширину и трудно различима, так как сливается с границей шва. Если между зернами основного металла и металла шва имеется пленка окислов, то в этом месте шов обладает пониженной прочностью из-за нарушения сцепления частиц основного и наплавленного металла.
Зона термического влияния. За зоной сплавления располагается участок основного металла, где он не изменяет своего первоначального химического состава. Однако структура основного металла на этом участке меняется под влиянием нагревания при сварке. Этот участок носит название зоны термического (теплового) влияния, или зоны влияния.
Здесь основной металл уже не нагревается до температуры плавления, хотя температура его достаточно высока и лежит в пределах 1100-1500°С, что вызывает значительный рост зерен на данном участке, что влияет на прочность шва.
Ширина зоны термического влияния зависит от вида, способа и режима сварки - при ручной дуговой сварке она равна 2,5-6 мм, при механизированной сварке - 2,5-4 мм, при сварке в защитных газах - 1-2,5 мм.
Вопрос 2. Ручные резаки (назначение, устройство, принцип действия, требования техники безопасности).
Резаки служат для смешения горючего газа с кислородом, образования подогревающего пламени и подачи к разрезаемому металлу струи режущего кислорода.
Ручные резаки для газовой резки классифицируются по следующим признакам:
• по роду горючего газа, на котором они работают, - для ацетилена, газов-заменителей, жидких горючих;
• по принципу смешения горючего газа и кислорода - на инжекторные и безынжекторные;
• по назначению - на универсальные и специальные;
• по виду резки - для разделительной, поверхностной, кислородно-флюсовой, копьевой.
В настоящее время щирокое применение получили универсальные резаки. К универсальным резакам предъявляют следующие основные требования: возможность резки стали толщиной от 3 до 300 мм и в любом направлении, устойчивость против обратных ударов, малая масса и удобство в обращении.
Как и сварочные горелки, резаки имеют инжекторное устройство, обеспечивающее нормальную работу при любом давлении горючего газа. Инжекторный резак отличается от инжекторной горелки тем, что имеет отдельный канал для подачи режущего кислорода и специальную головку, которая представляет собой два сменных мундштука - внутренний и наружный.
Ацетиленокислородный инжекторный резак (рис. 41) состоит из двух основных частей - ствола и наконечника.
Рис. 41. Принципиальная схема инжекторного резака
Ствол состоит из рукоятки 7 с ниппелями 5 и 6 для присоединения кислородного и ацетиленового рукавов, корпуса 8 с регулировочными кислородным 4 и ацетиленовым 9 вентилями, инжектора 10, смесительной камеры 12, трубки 13, головки резака 1 с внутренним мундштуком 14 и наружным 15, трубки режущего кислорода 2 с вентилем 3. Ствол присоединяется к корпусу 8 накидной гайкой 11.
Кислород из баллона поступает в резак через ниппель 5 и в корпусе разветвляется по двум каналам. Часть газа, проходя через вентиль 4, направляется в инжектор 10.
Выходя из инжектора с большой скоростью, струя кислорода создает разрежение и подсасывает ацетилен, образующий с кислородом в камере 12 горючую смесь, которая, проходя через зазор между наружными и внутренними мундштуками, сгорает, образуя подогревающее пламя.
Другая часть кислорода через вентиль 3 поступает в трубку 2 и, выходя через центральный канал внутреннего мундштука 14, образует струю режущего кислорода.
Основной деталью резака является мундштук, который в процессе резки быстро изнашивается. Для получения качественного реза необходимо иметь правильные размеры и необходимую чистоту каналов мундштука.
Мундштуки, которые используются в резаках, разделяются на две группы.
К первой группе относятся цельные неразборные мундштуки (рис. 42, а).
Ко второй группе относятся составные мундштуки, состоящие из двух самостоятельных мундштуков. Они имеют кольцевую щель для выхода горючей смеси (рис. 42, б). Горючая смесь поступает по кольцевому зазору между внутренним и наружным мундштуками. По центральному каналу внутреннего мундштука подается режущий кислород.
Конструкции многосопловых составных мундштуков изображены на рис. 42, в, г. Составные резаки с кольцевой щелью легче изготовлять и заменять. Перед началом работы необходимо ознакомиться с инструкцией по эксплуатации резака и убедиться в его исправности.
Рис: 42. Схемы конструкций мундштуков:
а - неразборные; б - составные; в, г - многосопловые
Прежде чем начать работу, проверяют правильность присоединения шлангов к резаку (кислородный шланг присоединяют к штуцеру с правой резьбой, шланг с горючим газом - к штуцеру с левой резьбой), инжекцию в каналах горючего газа, герметичность всех разъемных соединений.
Резак зажигают в такой последовательности.
1. Открывают на 1-4 оборота вентиль подогрева кислорода и создают разрежение в газовых каналах, затем открывают вентиль для газа и зажигают горючую смесь.
2. Подогревающее пламя регулируют кислородным и газовым вентилями.
После этого приступают к резке. Металл нагревают подогревающим пламенем до соломенного цвета, открывают вентиль режущего кислорода и выполняют резку.
3. Если нужно погасить пламя, то в первую очередь перекрывают вентиль горючего газа, а затем - кислородный.
В процессе резки по мере нагрева мундштука необходимо регулировать подогревающее пламя до нормального. При сильном нагреве наконечника его охлаждают водой.
4. Чтобы вода не попадала в каналы резака, закрывают только газовый вентиль, оставляя кислородный открытым.
5. При засорении каналов мундштуков их прочищают медной или алюминиевой иглой. При разборке резаков сначала отсоединяют ствол от корпуса, затем из корпуса вывертывают кислородный и газовый вентили, инжектор и снимают наружный и внутренний мундштуки.
6. При резке могут возникнуть следующие неисправности: отсутствие подсоса в канале горючего газа, вентили не перекрывают подсоса в канале горючего газа, частые хлопки пламени, утечка газа в соединениях и др.
Отсутствие подсоса в газовом канале возникает из-за засорения инжектора, смесительной камеры и каналов мундштука, плохой затяжки инжектора и накидной гайки смесительной камеры.
Частые хлопки пламени возникают при засорении мундштука, инжектора и смесительной камеры, при перегреве мундштука или недостаточном давлении подогревающего кислорода.
Утечка газа в соединениях вызывается ослаблением соединений и износом прокладок. Все мелкие неисправности - перекос мундштуков, негерметичность соединений, прочистка инжектора и каналов мундштуков, снятие нагара и брызг с поверхности мундштука и др. резчик устраняет во время работы. Более сложный ремонт, требующий специального инструмента, выполняется с разрешения руководства предприятия.
3. Задача. Назовите максимально допустимое рабочее давление, которое может быть при работе с кислородным баллоном, ацетиленовым баллоном, ацетиленовым переносным генератором.
Кислородный баллон рассчитан на рабочее давление 15 МПа, ацетиленовый - максимальное давление 3 МПа, ацетиленовый генератор - низкого давления до 0,02 МПа, среднего - от 0,02 до 0,15 МПа.
Билет № 18
Вопрос 1. Устройство и назначение сварочного преобразователя.
Сварочный преобразователь (рис. 43) представляет собой машину, служащую для преобразования переменного тока в постоянный сварочный ток.
Он состоит из сварочного генератора постоянного тока и приводного трехфазного асинхронного электродвигателя 8, сидящих на одном валу и смонтированных в общем корпусе. Сварочный генератор состоит из корпуса 11 с укрепленными на нем магнитными полюсами 10 и приводимого во вращение якоря 12.
Рис. 43. Сварочный преобразователь
Тело якоря набрано из отдельных лакированных пластин электротехнической стали. В продольных пазах его уложены витки обмотки. Рядом с якорем находится коллектор, состоящий из большого числа изолированных друг от друга медных пластинок 1, к которым припаяны начала и концы каждой группы витков якоря.
Магнитное поле внутри генератора создается магнитными полюсами обмоток возбуждения, которые питаются постоянным током от щеток 2 самого генератора. В распределительном устройстве 4 размещены пакетный выключатель, регулировочный реостат 3, вольтметр 6, доски зажимов 5 высокого и низкого напряжения и другая аппаратура. При включении электродвигателя якорь начинает вращаться в магнитном поле и в витках его возникает переменный ток, который с помощью коллектора преобразуется в постоянный.
К коллектору прижимаются угольные щетки 2, с помощью которых постоянный ток снимается с коллектора и подводится к зажимам 5 («+» и «-»). К этим же зажимам присоединяют сварочные провода, подводящие сварочный ток к электроду и изделию. Для охлаждения преобразователя во время его работы на валу имеется вентилятор 7.
Ходовая часть преобразователя состоит из переднего поворотного колеса с тягой 9 и двух задних колес, сидящих на одной оси. Это позволяет передвигать его на небольшое расстояние. Для подъема и перемещения преобразователя предусмотрены два рым-болта.
Сварочный ток регулируется с помощью маховичка 3 реостата: при вращении его по часовой стрелке сварочный ток увеличивается, и наоборот.
Вопрос 2. Наплавочные работы (виды, назначение, технология, материалы).
Наплавка деталей и восстановление изношенных деталей наплавкой - эффективный и экономичный способ продления срока службы деталей и машин.
Наплавку выполняют с помощью сварки, преимущественно дуговой, для наложения необходимого слоя металла на поверхность детали с целью повышения ее стойкости против истирания, повышенных температур, абразивного изнашивания, коррозии и других видов разрушения.
Наплавку применяют для восстановления размеров изношенных деталей и создания слоя металла и поверхности детали, отличающегося по своим свойствам от основного металла детали повышенной износостойкостью, антикоррозионностью, жаростойкостью и другими свойствами.
Наиболее распространены ручная дуговая наплавка покрытыми электродами, наплавка неплавящимися угольным или вольфрамовым электродом в среде защитного газа, наплавка в углекислом газе, под слоем флюса, вибродуговая наплавка.
По степени механизации процесса различают наплавку:
• ручную дуговую покрытыми электродами;
• полуавтоматическую;
• автоматическую.
Материалы для наплавки. Сплавы, применяемые для дуговой наплавки, можно подразделить на:
• литые (сормайт);
• порошкообразные или зернистые (вокар, висхром-9);
• плавленые карбиды и спеченные (карбиды вольфрама и титана).
Для ручной и механизированной наплавки выпускают большое количество различных наплавочных материалов (проволок, лент, электродов, флюсов и др.) различных химических составов и свойств. При выборе наплавляемого металла учитывают химический состав металла наплавляемой детали, условия работы, характер и вид нагрузки, износ, требуемую износостойкость.
Особое внимание при наплавке под флюсом уделяют свойствам флюсов: способствуют ли они формированию наплавленного металла, стабильности горения дуги, какой склонностью обладают к образованию пор в наплавленном металле, какие содержат легирующие элементы.
Наплавку выполняют покрытыми, проволочными и ленточными электродами. При этом ленточный и проволочный электроды могут быть сплошными или в виде порошковой ленты или порошковой проволоки.
Порошковый электрод представляет собой стержень из порошковой проволоки, имеющий толстое основное покрытие. На свойства и состав наплавленного металла влияют изменения состава порошкового наполнителя.
Порошковые электроды более производительные, чем стержневые.
При наплавке порошковым электродом создается защита легирующих элементов за счет более быстрого плавления наполнителя по сравнению со скоростью плавления оболочки электрода.
Наплавку высоколегированных сталей рекомендуется вести под низколегированными флюсами ФЦЛ-2 и АН-20, под бескислородными флюсами БКФ-1, ВКФ-2, под флюсами 48-ОФ-7 и АН-70.
Технология и способы наплавки. Сущность процесса наплавки заключается в использовании теплоты для расплавления присадочного материала и его соединения с основным металлом детали.
Используя возможности дуговой наплавки, на поверхности детали можно получить наплавленный слой любой толщины, любого химического состава с разнообразными свойствами.
Наплавка может производиться на:
• плоские;
• цилиндрические;
• конические;
• сферические и другие формы поверхности в один или несколько слоев.
Толщина слоя наплавки может изменяться в широких пределах - от долей миллиметра до сантиметров. При наплавке поверхностных слоев с заданными свойствами, как правило, химический состав наплавленного металла существенно отличается от химического состава основного металла.
Поэтому при наплавке должен выполняться ряд технологических требований.
1. В первую очередь таким требованием является минимальное разбавление наплавленного слоя основным металлом, расплавляемым при наложении валиков. Поэтому в процессе наплавки необходимо получение наплавленного слоя с минимальным проплавлением основного металла, так как в противном случае возрастает доля основного металла в формировании наплавленного слоя. Это приводит к ненужному разбавлению наплавленного металла расплавляемым основным.
2. При наплавке необходимо обеспечение минимальной зоны термического влияния и минимальных напряжений и деформаций.
Это требование обеспечивается за счет уменьшения глубины проплавления, регулированием параметров режима, погонной энергии, увеличением вылета электрода, применением широкой электродной ленты и другими технологическими приемами.
Технология наплавки различных поверхностей предусматривает ряд приемов нанесения наплавленного слоя:
• ниточными валиками с перекрытием один другого на 0,3-0,4 их ширины;
• широкими валиками, полученными за счет поперечных к направлению оси валика колебаний электрода, электродными лентами и др.
Расположение валиков с учетом их взаимного перекрытия характеризуется шагом наплавки (рис. 44).
Рис. 44. Схема наплавки слоев:
В, hн, hпр - соответственно ширина валика, высота наплавки, глубина проплавления; Sн - шаг наплавки
Наплавку криволинейных поверхностей тел вращения выполняют тремя способами (рис. 45):
• наплавкой валиков вдоль образующей тела вращения;
• по окружностям;
• по винтовой линии.
Рис. 45. Наплавка тел вращения:
а - по образующей; б - по окружности; в - по винтовой линии
Наплавку по образующей выполняют отдельными валиками так же, как при наплавке плоских поверхностей.
Наплавка по окружности также выполняется отдельными валиками до полного замыкания начального и конечного участков со смещением их на определенный шаг вдоль образующей.
При винтовой наплавке деталь вращают непрерывно, при этом источник нагрева перемещается вдоль тела со скоростью, при которой одному обороту детали соответствует смещение источника нагрева, равное шагу наплавки.
При наплавке тел вращения необходимо учитывать возможность стекания расплавленного металла в направлении вращения детали. В этом случае источник нагрева смещают в сторону, противоположную направлению вращении (рис. 46).
Рис. 46. Смещение электрода при наплавке тел вращения:
а - наклонно расположенным электродом; б - с вертикальным расположением электрода
Предварительный подогрев наплавляемой детали до температуры 200-250°С уменьшает склонность наплавленного металла к образованию трещин.
Все дефекты в наплавленном металле можно подразделить на наружные и внутренние.
К последним относятся непровар (несплавление наплавленного металла с основным), пористость, трещины и шлаковые включения. Наружные дефекты, к которым относятся раковины и трещины, выявляют визуально.
Режимы наплавки характеризуются следующими параметрами:
• при ручной наплавке покрытым электродом в технологии указывают марку электрода, его диаметр, род тока, сварочный ток;
• при автоматической наплавке - тип электродного материала (проволока, лента: сплошного сечения, порошковая), ток, напряжение дуги, длину дуги, скорость наплавки;
• при наплавке в защитном газе дополнительно указывают защитный газ;
• при наплавке под флюсом - марку флюса.
Выбирая способ наплавки, вначале оценивают возможность его применения в данном конкретном случае, затем определяют возможность обеспечения технических требований, предъявляемых к наплавленному материалу, и, наконец, оценивают экономическую эффективность наплавки. При оценке экономической эффективности способа наплавки общую стоимость ручной дуговой наплавки принимают за 100% наплавку под слоем флюса - 74%, а вибродуговую наплавку - 82%.
3. Задача. По условному обозначению на стволах горелок Г1, Г2, ГЗ, Г4 охарактеризуйте их, расшифровав это обозначение.
Г1 - горелка безынжекторная микромощности; Г2 - горелка инжекторная малой мощности; ГЗ - горелка инжекторная средней мощности; Г4 - горелка инжекторная большой мощности.
Билет № 19
Вопрос 1. Напряжения и деформации при сварке (понятия, виды, классификация, причины их возникновения, способы борьбы).
Деформацией называется изменение формы и размеров твердого тела под действием усилия.
Если форма тела восстанавливается после прекращения действия силы, то деформация является упругой.
Если тело не принимает первоначальной формы, то оно получило остаточную, или пластическую деформацию.
Напряжением называется сила, отнесенная к единице поверхности или к единице площади поперечного сечения тела. В зависимости от направления действующих усилий могут возникать напряжения растяжения, сжатия, изгиба, среза и кручения. Напряжение, при котором происходит разрушение, называется пределом усталости. Главной причиной пониженной усталостной прочности сварных соединений является сосредоточение напряжений. Причинами концентрации напряжений являются:
1. Дефекты швов - острый надрез, непровар, трещина и другие, расположенные поперек действия растягивающих напряжений.
2. Неправильные очертания сварного шва, например, швы с большой выпуклостью и неплавным переходом от наплавленного металла к основному.
3. Нерациональная конструкция сварных соединений.
В местах концентрации напряжений суммарная величина их может превысить временное сопротивление разрыву наплавленного металла, что вызовет начало разрушения сварного шва. А в отдельных случаях приводит к разрушению сварной конструкции в целом. Причинами возникновения напряжений и деформаций при сварке являются: неравномерное нагревание металла, литейная усадка расплавленного металла, структурные превращения в металле.
Для борьбы с деформациями принимаются следующие меры.
Мероприятия, выполняемые до сварки.
Рациональное конструирование сварных изделий. В процессе конструирования необходимо: ограничивать количество наплавленного металла уменьшением катетов швов или угла скоса кромок; не допускать пересечения большого количества швов; не располагать сварные швы там, где действуют максимальные напряжения от внешних нагрузок, и размещать их симметрично; применять преимущественно стыковые швы и т. п.
Правильная сборка деталей с учетом возможных деформаций. При этом наиболее часто применяют метод обратных деформаций (рис. 47). Зная, что шов после охлаждения всегда сокращается в размерах, можно заранее предугадать характер возможных напряжений и деформаций и произвести предварительный выгиб свариваемых деталей и противоположную сторону. Величина обратного выгиба определяется расчетным или опытным путем.
Рис. 47. Обратные деформации и положения элементов изделия после сварки:
а - стыковое соединение двух пластин; б - тавровая балка; в - полка таврового соединения
При сборке деталей следует избегать прихваток, которые создают жесткое закрепление деталей и способствуют возникновению значительных остаточных напряжений. Лучше применять сборочные приспособления, допускающие некоторое перемещение деталей при усадке металла.
Мероприятия, выполняемые в процессе сварки.
Рациональная последовательность наложения сварных швов. Сварные конструкции следует изготовлять так, чтобы замыкающие швы, создающие жесткий контур, заваривались в последнюю очередь. Сварку нужно вести от середины конструкции к ее краям, как бы сгоняя при этом внутренние напряжения наружу. Каждый последующий шов при многослойной сварке рекомендуется накладывать в направлении, обратном направлению предыдущего шва.
При сварке полотнищ из отдельных листов (рис. 48, а) в первую очередь нужно выполнять поперечные швы отдельных поясов, чтобы обеспечить их свободную усадку, а затем сваривать пояса между собой продольными швами. В противном случае возможно образование трещин в местах пересечения поперечных и продольных швов.
При сварке двутавровых балок (рис. 48, б) в первую очередь выполняют стыковые соединения стенок и полок, а затем - угловые поясные швы.
При сварке цилиндрических сосудов из нескольких обечаек (рис. 48, в) сначала выполняют продольные швы обечаек, а затем обечайки сваривают между собой кольцевыми швами. При ручной и механизированной сварке швы большой протяженности рекомендуется накладывать в обратноступенчатом порядке.
Рис. 48. Последовательность наложения швов (1-8) при сварке:
а - полотнища из отдельных листов; б - двутавровой балки; в - цилиндрического сосуда
Уравновешивание деформаций. В этом случае (рис. 49) швы выполняют в такой последовательности, при которой последующий шов вызывает деформации обратного направления по сравнению с деформациями от предыдущего шва. Этот способ может быть использован при симметричном расположении швов.
Жесткое закрепление деталей при сварке. В этом случае детали закрепляют в сборочно-сварочных приспособлениях, обладающих значительной жесткостью. После сварки в таких приспособлениях короблений деталей почти не будет, но в сварных швах возрастут внутренние напряжения.
Мероприятия, выполняемые после сварки. В тех случаях, когда деформации все же произошли и величины их выходят за пределы допустимых, применяют правку сварных изделий различными способами.
Механическая правка. В этом случае с помощью молотов, домкратов, винтовых прессов или других устройств создается ударная или статическая нагрузка, которую обычно прилагают со стороны наибольшего выгиба. Изделия из тонколистового металла можно править прокатыванием их между валками.
Термическая правка заключается в местном нагреве небольших участков металла деформированной конструкции. Нагрев, как правило, производят сварочными горелками большой мощности. Ведут его быстро и только до пластического состояния верхних волокон на выпуклой стороне изделия. При охлаждении нагретых участков последние сжимаются и выпрямляют изделие.
Рис.49. Уравновешивание деформации:
а - при изготовлении сварной двутавровой балки; б - при выполнении сварного стыкового многослойного шва; в - при наплавке валика продольными швами: 1-6 - последовательность наложения швов
Термомеханическая правка заключается в сочетании местного нагрева с приложением статической нагрузки, изгибающей исправляемый элемент конструкции в нужном направлении. Такой способ обычно применяют для правки жестких сварных узлов.
Методы уменьшения внутренних напряжений. Существует несколько методов уменьшения внутренних напряжений.
Наиболее часто применяют:
• предварительный или сопутствующий подогрев при сварке;
• проковку или прокатку сварных швов;
• статическое нагружение сварной конструкции;
• отпуск после сварки.
Предварительный или сопутствующий подогрев применяют при сварке сталей, склонных к закалке и образованию трещин. Температуру подогрева выбирают в зависимости от марки стали и жесткости конструкции (обычно в пределах 100-600°С). Подогрев, производимый многопламенными горелками, индукторами или в печах, уменьшает пластические деформации сжатия, что значительно снижает остаточные напряжения. Кроме того, в ряде случаев он благоприятно влияет на структуру металла шва и околошовной зоны.
Послойную проковку швов выполняют пневматическим зубилом с закругленным бойком непосредственно после сварки по горячему металлу (горячая проковка) или после полного его остывания (холодная проковка). Благодаря осадке металла в направлении удара происходит его раздача в разные стороны, что снижает растягивающие напряжения. Проковка рекомендуется при многослойной сварке металла большой толщины, причем во избежание трещин и надрывов первый и последний слои многослойного шва не проковывают. Швы на металле, склонном к закалке, проковывать нельзя. Преимущество проковки состоит в ее простоте и маневренности.
Прокатку шва выполняют при сварке тонколистового металла.
В процессе прокатки растягивающие напряжения уменьшаются. Преимущество ее перед проковкой состоит в статическом характере приложения давления и возможности плавного его регулирования.
Статическое нагружение элементов сварной конструкции возможно в процессе сварки или чаще всего после полного остывания шва. В качестве такого нагружения применяют растяжение или изгиб с образованием растягивающих напряжений в зонах, где остаточные напряжения максимальны. Это приводит к пластическим деформациям и значительному уменьшению остаточных напряжений.
Отпуск после сварки, обычно применяемый для выравнивания структуры шва и околошовной зоны, также снижает внутренние напряжения. Отпуск может быть общим, когда нагревается все изделие, и местным, когда нагревается лишь часть его в зоне сварного соединения. Преимущество общего отпуска состоит в том, что снижение напряжений происходит во всей сварной конструкции независимо от ее сложности.
Наиболее часто применяют высокий отпуск при температуре нагрева 550-680ºС. Операция отпуска состоит из четырех стадий: нагрев; выравнивание температуры по длине и сечению изделия; выдержка при температуре отпуска; охлаждение. Выдержка независимо от толщины металла обычно составляет около 3 ч, после чего происходит естественное охлаждение. По частоте применения отпуск сварных конструкций значительно превосходит все методы снятия внутренних напряжений (рис. 50).
Рис. 50. Стадии отпуска сварных конструкций:
1- поверхность изделия; 2 - внутренние зоны металла
Вопрос 2. Технология и техника кислородной резки (основные условия резки металлов, назначение, сущность).
Основные условия резки металлов. Кислородной резке подвергаются только те металлы и сплавы, которые удовлетворяют следующим основным условиям:
1. Температура воспламенения металла в кислороде должна быть ниже температуры его плавления. Лучше всех металлов и сплавов этому требованию удовлетворяют низкоуглеродистые стали, температура воспламенения которых в кислороде около 1300°С, а температура плавления около 1500ºС. Увеличение содержания углерода в стали сопровождается повышением температуры воспламенения в кислороде с понижением температуры плавления. Поэтому с увеличением содержания углерода кислородная резка сталей ухудшается.
2. Температура плавления окислов металлов, образующихся при резке, должна быть ниже температуры плавления самого металла, в противном случае тугоплавкие окислы не будут выдуваться струей режущего кислорода, что нарушит нормальный процесс резки. Этому условию не удовлетворяют высокохромистые стали и алюминий. При резке высокохромистых сталей образуются тугоплавкие окислы с температурой плавления 2000°С, а при резке алюминия - оксид с температурой плавления около 2050°С. Кислородная резка их невозможна без применения специальных флюсов.
3. Количество теплоты, которое выделяется при сгорании металла в кислороде, должно быть достаточно большим, чтобы поддерживать непрерывный процесс резки. При резке стали около 70% теплоты выделяется при сгорании металла в кислороде и только 30% общей теплоты поступает от подогревающего пламени резака.
4. Образующиеся при резке шлаки должны быть жидкотекучими и легко выдуваться из места реза.
5. Теплопроводность металлов и сплавов не должна быть слишком высокой, так как теплота, сообщаемая подогревающим пламенем и нагретым шлаком, будет интенсивно отводиться от места реза, вследствие чего процесс резки будет неустойчивым и в любой момент может прерваться. При резке стали сгорание железа в кислороде протекает по реакциям.
При проведении кислородно-ацетиленовой резки присутствует два вида пламени: подогревающее и режущая струя кислорода.
В начале газовой резки подогрев осуществляется только подогревающим пламенем до температуры воспламенения. Мощность подогревающего пламени зависит от толщины и химического состава разрезаемого металла и сплава.
Максимальная температура пламени находится на расстоянии 2-3 мм от конца ядра, поэтому для наиболее эффективного нагрева расстояние от конца ядра до поверхности разрезаемого металла должно составлять 2-3 мм. Подогревающее пламя надо регулировать на несколько повышенное содержание кислорода, так как слегка окислительное пламя обеспечивает интенсивный нагрев и улучшает качество реза.
Сжигание металла и удаление продуктов сгорания из реза осуществляется струей режущего кислорода. Количество кислорода, проходящего через сопло мундштука, зависит от конструкции сопла, давления кислорода и скорости истечения струи.
При газовой резке требуется определенное количество кислорода. Недостаток его приводит к неполному сгоранию железа и неполному удалению оксидов, а избыток кислорода охлаждает металл. Количество кислорода, необходимое для полного окисления разрезаемого металла, определяется количеством сжигаемого металла и средним расходом на его сжигание.
Основными параметрами режима кислородной резки являются:
• мощность подогревающего пламени;
• давление режущего кислорода;
• скорость резки.
Мощность подогревающего пламени характеризуется расходом горючего газа в единицу времени и зависит от толщины разрезаемого металла. Она должна обеспечивать быстрый подогрев металла в начале резки до температуры воспламенения и необходимый нагрев его в процессе резки. Для резки металла толщиной до 300 мм применяют нормальное пламя. При резке металла больших толщин лучшие результаты получают при использовании пламени с избытком горючего (науглероживающее пламя). При этом длина видимого факела пламени (при закрытом вентиле кислорода) должна быть больше толщины разрезаемого металла.
Выбор давления режущего кислорода зависит от толщины разрезаемого металла, размера режущего сопла и чистоты кислорода.
При увеличении давления кислорода увеличивается его расход. Давление кислорода выбирается в зависимости от толщины металла: чем чище кислород, тем меньше его расход на 1 пог. метр реза.
Скорость перемещения резака должна соответствовать скорости горения металла. От скорости резки зависят устойчивость процесса и качество вырезаемых деталей. Малая скорость приводит к оплавлению разрезаемых кромок (рис. 51, а), а большая - к появлению непрорезанных до конца участков реза (рис. 51, в). Скорость резки зависит от толщины и свойств участков реза. Скорость резки зависит от толщины свойств разрезаемого металла, вида резки, метода резки. Поэтому допустимую скорость резки определяют опытным путем. Скорость резки перемещения резака считают нормальным, если пучок искр будет выходить почти параллельно кислородной струе (рис. 51, б).
Большое влияние на качество реза и производительность резки оказывает подготовка металла под резку.
Рис. 51. Характер выброса шлака:
а - скорость резки мала; б - оптимальная скорость; в - скорость велика
Перед началом резки листы подают на рабочее место и укладывают на подкладки так, чтобы обеспечить беспрепятственное удаление шлаков из зоны реза. Зазор между полом и нижним листом должен быть менее 100-150 мм. Поверхность металла перед резкой должна быть очищена. На практике окалину, ржавчину, краску и другие загрязнения удаляют с поверхности металла нагревом зоны резки газовым пламенем с последующей зачисткой стальной щеткой.
Перед началом резки газорезчик должен установить необходимое давление газов на ацетиленовом и кислородном редукторах, подобрать нужные номера наружного и внутреннего мундштуков в зависимости от вида и толщины разрезаемого металла.
Процесс резки начинают с нагрева металла в начале реза до температуры воспламенения металла в кислороде. Затем пускают режущий кислород (происходит непрерывное окисление металла по всей толщине) и перемещают резак по линии реза.
Для обеспечения высокого качества реза расстояние между мундштуком и поверхностью разрезаемого металла необходимо поддерживать постоянным. Для этой цели резаки комплектуются направляющими тележками.
Процесс кислородной резки основан на свойстве металлов и их сплавов сгорать в струе чистого кислорода.
Процесс резки включает в себя следующие стадии:
• нагрев начального участка резки до температуры воспламенения металла в кислороде;
• сгорание металла в струе кислорода;
• расплавление образующихся окислов и выдувание их из места разреза;
• нагрев соседних слоев металла в кислороде и перемещение резака вдоль линии реза.
Резку начинают с края детали. При необходимости резки с середины пробивают отверстие (при толщине металла до 50 мм) пламенем вертикально стоящего резака, разогревая место резки и плавно открывая вентиль режущего кислорода по мере углубления отверстия.
Угол наклона резака 20-45° в сторону, обратную направлению резки. При криволинейной резке резак держат вертикально.
3. Задача. Назовите ваши действия в случае обратного удара пламени при работе с ацетиленовым генератором при сварке металла.
Перекрыть ацетиленовый вентиль горелки и распределительный вентиль на генераторе. Охладить горелку.
Билет № 20
Вопрос 1. Кислородно-флюсовая резка металла.
Высоколегированные хромистые, хромоникелевые стали, чугун и цветные металлы не могут подвергаться обычной кислородной резке, так как они не удовлетворяют основным условиям резки.
Хромистые и хромоникелевые нержавеющие стали на поверхности реза образуют тугоплавкие оксиды хрома с температурой плавления около 2000°С, которые препятствуют нормальному протеканию процесса резки. Поэтому кислородная резка этих сталей требует применения особых способов.
Чугун имеет температуру плавления ниже температуры воспламенения, поэтому при обычной резке чугун будет плавиться, а не сгорать в кислороде. Содержащийся в чугуне кремний образует тугоплавкую окись кремния, которая также препятствует резке.
Цветные металлы (медь, алюминий, латунь, бронза) имеют большую теплопроводность, образуют тугоплавкие окислы и также не поддаются обычной газовой резке. Удалить тугоплавкие окислы можно либо переводом их в легкоплавкие, либо введением в зону реза дополнительной теплоты.
Резку высоколегированных сталей можно обеспечить наложением вдоль линии реза низкоуглеродистой стальной полосы, при сгорании которой выделившаяся теплота, а также переходящее в шлак расплавленное железо и его оксиды способствуют разжижению оксидов хрома. Этим способом можно резать нержавеющие стали толщиной до 20 мм, однако при этом рез получается широким, а скорость резки низкая.
Для резки хромистых, хромоникелевых нержавеющих сталей, чугуна и цветных металлов применяют способ кислородно-флюсовой резки. Сущность его заключается в том, что в разрез вместе с режущим кислородом вводится порошкообразный флюс, при сгорании которого выделяется дополнительная теплота и повышается температура в зоне реза.
Кроме того, продукты сгорания флюса, взаимодействуя с тугоплавкими оксидами, образуют жидкотекучие шлаки, которые легко удаляются из зоны реза, не препятствуя нормальному протеканию процесса.
Основным компонентом порошкообразных флюсов, применяемых при кислородно-флюсовой резке металлов, является железный порошок. Железный порошок при сгорании выделяет большое количество теплоты - около 1380 кДж/кг.
При выборе железного порошка необходимо иметь в виду, что процесс резки зависит от его химического состава и его грануляции. При использовании порошков, содержащих до 0,4% углерода и до 0,6% кислорода, процесс резки нержавеющей стали протекает устойчиво. Дальнейшее увеличение содержания углерода и кислорода в порошке приводит к увеличению расхода порошка и ухудшению качества поверхности реза.
При резке нержавеющих сталей содержание кислорода в порошке не должно превышать 6%. Кислород присутствует в порошке в виде оксидов, которые замедляют процесс резки, так как требуют дополнительной теплоты для их нагрева.
Основными критериями при выборе грануляции железного порошка являются обеспечение его наилучшей транспортировки и регулирование расхода. Опытами установлено, что лучшие результаты при кислородно-флюсовой резке дает железный порошок с размерами частичек от 0,07 до 0,16 мм. Опытами также установлено, что лучшие результаты при резке нержавеющих хромоникелевых сталей достигаются при добавлении к железному порошку 10-15% алюминиевого порошка. Смесь железного и алюминиевого порошков дает жидкотекучий шлак, температура плавления второго не превышает 1300ºС. Для резки нержавеющих сталей применяется алюминиевый порошок марки АПВ.
Основная задача флюса при резке чугуна состоит в разбавлении флюса железом в области реза, снижении в сплаве содержания углерода, а также разжижения шлака, в котором содержится повышенное содержание кислорода. В состав флюсов для резки чугуна входят железный и алюминиевый порошок, кварцевый песок и феррофосфор.
Цветные металлы и сплавы подвергают только кислородно-флюсовой резке с применением флюсов.
Установки для кислородно-флюсовой резки состоят из двух основных частей: флюсопитателя и резака (ручного или машинного).
По конструкции флюсопитатели подразделяются на инжекторные, циклонные и с механической подачей.
Применяют три схемы установок для кислородно-флюсовой резки: с внешней подачей флюса, с однопроводной подачей флюса под высоким давлением и с механической подачей флюса.
По первой схеме подачи флюса флюс из бачка инжектируется кислородом и подается к резаку, укомплектованному специальной головкой. Газофлюсовая смесь, выходящая из отверстий специальной головки, засасывается струей режущего кислорода и в смеси с ним поступает в зону реза. При эксплуатации установки с внешней подачей флюса работают устойчиво и экономично (рис. 52, а).
Однопроводная схема подачи флюса под высоким давлением. В этом случае железный порошок из бачка флюсопитателя инжектируется непосредственно струей, режущего кислорода. Смесь флюса с кислородом по рукаву подводится к резаку через центральный канал мундштука и поступает к разрезаемому металлу (рис. 52, б).
По схеме с механической подачей флюса флюс, состоящий из смеси алюминиево-магниевого порошка, из бачка с помощью специального устройства подается к головке резака, где .увлекается струей режущего кислорода (рис. 52, в).
Рис. 52. Схема подачи флюса:
а - с внешней подачей; б - однопроводная под высоким давлением; в - с механической подачей;
1 - газофлюсовая смесь; 2 - флюс; 3 - флюсонесущий газ; 4 - кислородно-флюсовая смесь; 5 – режущий кислород
Вопрос 2. Баллоны для сжатых и сжиженных газов (типы, давление, окраска, надписи на баллонах, требования техники безопасности).
Для хранения и транспортировки сжатых, сжиженных и растворенных газов, находящихся под давлением, применяют стальные баллоны. Баллоны имеют различную вместимость - от 0,4 до 55 дм3.
Баллоны представляют собой стальные цилиндрические сосуды, в горловине которых имеется конусное отверстие с резьбой, куда ввертывается запорный вентиль. Для каждого газа разработаны свои конструкции вентилей, что исключает установку кислородных вентилей на ацетиленовый баллон, и наоборот.
На горловину плотно насаживают кольцо с наружной резьбой для навертывания предохранительного колпака, который служит для предохранения вентиля баллонов от возможных ударов при транспортировке.
Баллоны для сжатых, сжиженных и растворенных газов изготовляют из бесшовных труб углеродистой и легированной стали. Для сжиженных газов при рабочем давлении не свыше 3 МПа допускается применение сварных баллонов. Требования к баллонам регламентируют правила Гостехнадзора России.
В зависимости от рода газа, находящегося в баллоне, баллоны окрашивают снаружи в условные цвета, а также соответствующей каждому газу краской наносят название газа.
Например, кислородные баллоны окрашивают в голубой цвет, а надпись делают черной краской, ацетиленовый - в белый и красной краской, водородные - в темно-зеленый и красной краской, пропан - в красный и белой краской.
Часть верхней сферической части баллона не окрашивают и выбивают на ней паспортные данные баллона: тип и заводской номер баллона, товарный знак завода-изготовителя, масса порожнего баллона, вместимость, рабочее давление и дату следующего испытания.
Баллоны периодически через каждые пять лет подвергают осмотру и испытанию.
Кислородные баллоны. Для газовой сварки и резки кислород доставляют в стальных кислородных баллонах.
Кислородный баллон (рис. 53, а) представляет собой стальной цельнотянутый цилиндрический сосуд 3, имеющий выпуклое днище 1, на которое напрессовывается башмак 2. Вверху баллон заканчивается горловиной 4.
Рис. 53. Баллоны:
а - кислородный; б - ацетиленовый
В горловине имеется конусное отверстие, куда ввертывается запорный вентиль 5.
На горловину для защиты вентиля навертывается предохранительный колпак 6.
Наибольшее распространение при газовой сварке и резке получили баллоны вместимостью 40 дм3.
Эти баллоны имеют размеры:
• наружный диаметр - 219 мм;
• толщина стенки - 7 мм;
• высота - 1 390 мм;
• масса баллона без газа - 67 кг.
Они рассчитаны на рабочее давление 15 МПа, а испытательное - 22,5 МПа.
На сварочном посту кислородный баллон устанавливают в вертикальном положении и закрепляют цепью или хомутом. Для подготовки кислородного баллона к работе отвертывают колпак и заглушку штуцера, осматривают вентиль, чтобы установить, нет ли на нем жира или масла, осторожно открывают вентиль баллона и продувают его штуцер, после чего перекрывают вентиль, осматривают накидную гайку редуктора, присоединяют редуктор к вентилю баллона, устанавливают рабочее давление кислорода регулировочным винтом редуктора.
По окончании отбора газа из баллона необходимо следить, чтобы остаточное давление в нем было не меньше 0,05-0,1 МПа.
При обращении с кислородными баллонами необходимо строго соблюдать правила эксплуатации и техники безопасности, что обусловлено высокой химической активностью кислорода и высоким давлением.
При транспортировке баллонов к месту сварки необходимо твердо помнить, что запрещается перевозить кислородные баллоны вместе с баллонами горючих газов.
При замерзании вентиля кислородного баллона его надо отогревать ветошью, смоченной в горячей воде.
Причинами взрыва кислородных баллонов могут быть попадание на вентиль жира или масла, падение или удары баллонов, появление искры при слишком большом отборе газа (электризуется горловина, баллона), нагрев баллона каким-либо источником тепла, в результате чего давление газа в баллоне станет выше допустимого.
Ацетиленовые баллоны. Питание постов газовой сварки и резки ацетиленом от ацетиленовых генераторов связано с рядом неудобств, поэтому в настоящее время большое распространение получило питание постов непосредственно от ацетиленовых баллонов.
Они имеют те же размеры, что и кислородный баллон (рис. 53, б).
Ацетиленовый баллон заполняют пористой массой из активированного древесного угля (290-320 г на 1 дм3 вместимости баллона) или смесью угля, пемзы и инфузорной земли. Массу в баллоне пропитывают ацетоном (225-300 г на 1 дм3 вместимости баллона), в котором хорошо растворяется ацетилен.
Ацетилен, растворяясь в ацетоне и находясь в порах пористой массы, становится взрывобезопасным и его можно хранить в баллоне под давлением 2,5-3 МПа. Пористая масса должна иметь максимальную пористость, вести себя инертно по отношению к металлу баллона, ацетилену и ацетону, не давать осадка в процессе эксплуатации. В настоящее время в качестве пористой массы применяют активированный древесный дробленый уголь (ГОСТ 6217-74) с размером зерен от 1 до 3,5 мм.
Ацетон (химическая формула СН3СОСН3) является одним из лучших растворителей ацетилена, он пропитывает пористую массу и при наполнении баллонов ацетиленом растворяет его. Ацетилен, доставляемый потребителям в баллонах, называется растворенным ацетиленом.
Максимальное давление ацетилена в баллоне составляет 3 МПа. Давление ацетилена в полностью наполненном баллоне изменяется при изменении температуры окружающей среды (табл. 6).
Таблица 6
Давление наполненных баллонов не должно превышать при 20ºС 1,9 МПа.
При открывании вентиля баллона ацетилен выделяется из ацетона и в виде газа поступает через редуктор и шланг в горелку или резак. Ацетон остается в порах пористой массы и растворяет новые порции ацетилена при последующих наполнениях баллона газом.
Для уменьшения потерь ацетона во время работы ацетиленовые баллоны необходимо держать в вертикальном положении. При нормальном атмосферном давлении и 20°С в 1 кг (л) ацетона растворяется 28 кг (л) ацетилена. Растворимость ацетилена в ацетоне увеличивается примерно прямо пропорционально с увеличением давления и уменьшается с понижением температуры.
Для полного использования емкости баллона порожние ацетиленовые баллоны рекомендуется хранить в горизонтальном положении, так как это способствует равномерному распределению ацетона по всему объему, и с плотно закрытыми вентилями. При отборе ацетилена из баллона он уносит часть ацетона в виде паров. Это уменьшает количество ацетилена в баллоне при следующих наполнениях. Для уменьшения потерь ацетона из баллона ацетилен необходимо отбирать со скоростью не более 1700 дм3/ч.
Для определения количества ацетилена баллон взвешивают до и после наполнения газом и по разнице определяют количество находящегося в баллоне ацетилена (в кг). Масса пустого ацетиленового баллона складывается из массы самого баллона, пористой массы и ацетона. При отборе ацетилена из баллона вместе с газом расходуется 30-40 г ацетона на 1 м3 ацетилена. При отборе ацетилена из баллона необходимо следить за тем, чтобы в баллоне остаточное давление было не менее 0,05-0,1 МПа.
Использование ацетиленовых баллонов вместо ацетиленовых генераторов дает ряд преимуществ, а именно:
• компактность и простота обслуживания сварочной установки;
• безопасность и улучшение условий работы;
• повышение производительности труда газосварщиков.
Кроме того, растворенный ацетилен содержит меньшее количество посторонних примесей, чем ацетилен, получаемый из ацетиленовых генераторов.
Хранение и транспортировка баллонов.
1. Транспортировка баллонов разрешается только на рессорных транспортных средствах, а также на специальных ручных тележках или носилках.
2. При бесконтейнерной транспортировке баллонов должны соблюдаться следующие требования:
• на всех баллонах должны быть до отказа навернуты предохранительные колпаки;
• кислородные баллоны должны укладываться в деревянные гнезда (разрешается применять металлические подкладки с гнездами, оклеенными резиной или другими мягкими материалами);
• кислородные баллоны должны укладываться только поперек кузова машины так, чтобы предохранительные колпаки были в одной стороне; укладывать баллоны допускается в пределах высоты бортов;
• баллоны должны грузить рабочие, прошедшие специальный инструктаж.
3. Перевозка в вертикальном положении кислородных и ацетиленовых баллонов допускается только в специальных контейнерах.
4. Совместная транспортировка кислородных и ацетиленовых баллонов на всех видах транспорта запрещается, за исключением транспортировки двух баллонов на специальной тележке к рабочему месту.
5. В летнее время баллоны должны быть защищены от солнечных лучей брезентом или другими покрытиями.
6. Баллоны в пределах рабочего места разрешается перемещать кантовкой в наклонном положении.
7. На рабочих местах баллоны должны быть прочно закреплены в вертикальном положении.
3. Задача. Назовите и схематично изобразите способ сварки листовой конструкции длиной 1300 мм.
Сварочный шов относится к длинномерным, поэтому используют обратноступенчатый способ сварки. Сущность его состоит в том, что весь шов разбивают на участки длиной 100-350 мм с таким расчетом, чтобы каждый из них мог быть выполнен целым числом электродов (двумя, тремя и т. д.). При этом переход от участка к участку совмещается со сменой электрода. Каждый участок заваривается в направлении, обратном общему направлению сварки, а последний всегда заваривается «на выход».
В данном случае возможно организовать работу одновременно двух сварщиков.
Билет № 21
Вопрос 1. Сварка цветных металлов (медь и ее сплавы, алюминий, титан).
К техническим цветным металлам относятся медь и ее сплавы - латунь и бронза, алюминий и его сплавы, титан.
Особенность сварки цветных металлов обусловлена их свойствами:
1. Температура плавления невысокая, поэтому легко получить перегрев металла, что может привести к образованию пор и изменению состава сплава.
2. Способ окисляться с образованием тугоплавких оксидов затрудняет процесс сварки, снижает физико-механические свойства шва.
3. Повышенная способность расплавленного металла поглощать газы (кислород, азот, водород) приводит к пористости шва.
4. Большая теплоемкость и высокая теплопроводность вызывает необходимость повышенного теплового режима варки и предварительного нагрева изделия перед сваркой.
5. Относительно большие коэффициенты литейного расширения и литейная усадка приводят к возникновению внутренних напряжений, деформаций, к образованию трещин в металле шва и околошовной зоны.
6. Резкое уменьшение механической прочности и возрастание хрупкости металлов при нагреве могут привести к непредвиденному разрушению изделия.
При сварке необходимо учитывать свойства каждого из металлов.
Сварка меди и ее сплавов. Особенность сварки меди заключается в следующем.
1. Медь обладает высокой теплопроводностью, большой жидкотекучестью, способностью окисляться в нагретом и особенно в расплавленном состоянии.
2. Сварка меди в значительной степени зависит от наличия в металле различных примесей: висмута, мышьяка, свинца, сурьмы.
Они практически не растворяются в меди, но образуют с ней легкоплавкие химические соединения, которые располагаются по границам зерен, ослабляя межатомные связи.
Чистая медь обладает наилучшей свариваемостью.
3. Повышенная жидкотекучесть меди затрудняет ее сварку в различных пространственных положениях, кроме нижнего.
4. Водород в присутствии кислорода оказывает отрицательное действие на свойства меди. Расплавленная медь легко окисляется, образуя оксид меди Cu2О, который легко поглощает водород и оксид углерода (Cu2О+2Н=Н2О+2Си). При охлаждении в объеме металла выделяются пузырьки паров воды и углекислого газа, которые не растворяются в меди. Эти газы, расширяясь, создают большое внутреннее давление и приводят к образованию местных трещин. Это явление получило название водородной болезни меди.
Для предупреждения болезни следует снижать количество водорода в зоне сварки, прокаливать электроды, флюсы, использовать защитные газы.
5. При сварке меди покрытыми медными электродами без подогрева возможно возникновение горячих трещин.
6. При сварке с подогревом, создающим условие медленного охлаждения, водяной пар в большинстве случаев до затвердевания металла выходит наружу, но небольшая часть водяного пара остается между слоем сварочного шлака и поверхностью металла шва.
В результате этого поверхность металла шва после удаления шлака становится неровной. Этого можно избежать при очень медленном охлаждении шва.
Виды сварки меди:
• дуговая сварка угольным электродом (неплавящимся);
• дуговая сварка плавящимся электродом;
• автоматическая сварка под слоем флюса;
• ручная аргонодуговая сварка вольфрамовым электродом (сварка в защитных газах);
• газовая сварка.
Рассмотрим подробнее все эти виды сварки.
Дуговая сварка угольным электродом (неплавящимся). Применяется для малоответственных изделий. При толщине меди до 15 мм применяют угольные электроды, при больших толщинах - графитовые.
В том и другом случае в качестве присадочного материала используют прутки из меди марки М1 и БрОФ6,5-0,15.
Для предохранения меди от окисления и улучшения процесса сварки применяют флюсы, которые наносят на разделку шва и на присадочные прутки. Флюс - прокаленная бура.
Присадочный материал не погружают в ванну, а держат под углом 30° к изделию на расстоянии 5-6 мм от поверхности ванны. Электрод держат под углом 75° к изделию.
Листы толщиной до 4 мм сваривают с отбортовкой кромок без присадочного металла. При толщине более 5 мм сваривают с разделкой кромок под углом 60-90°.
Сборка под сварку должна обеспечить минимальные зазоры (до 0,5 мм), чтобы предупредить протекание расплавленного металла шва.
Рекомендуется использовать подкладки из графита, асбеста, керамики.
Сварка производится постоянным током прямой полярности.
Скорость сварки довольно большая и при возможности - за один проход.
Для электрода Ø 4...6 мм при толщине металла до 4 мм сила тока 140-320 А, для электрода Ø более 4 мм сила тока 350-500 А.
После сварки тонкие листы проковываются в холодном состоянии, а толстые (5-20 мм) - при температуре 200-400°. Подогрев до более высокой температуры не рекомендуется, так как медь становится хрупкой.
Дуговая сварка плавящимся электродом (металлическим). Подготовка кромок и обработка шва производится так же, как и при сварке угольным электродом.
При толщине металла 5-10 мм необходимы предварительный подогрев до температуры 250-300°С и Х-образная разделка.
Металлические электроды изготавливают из меди марок Ml и М2, названные «Комсомолец-100». Электроды Ø 3 мм применяются редко вследствие низкой механической прочности.
Электроды марки ЭТ Балтийского завода со стержнем из бронзы Бр.КМц3-1. Сварку ведут максимально короткой дугой.
Высокопроизводительные электроды АНЦ-1 и АНЦ-2 обеспечивают сварку без подогрева меди толщиной до 15мм.
Используют постоянный ток обратной полярности. Максимально короткая дуга, так как увеличение дуги ведет к разбрызгиванию металла и снижает механические свойства шва.
Колебательные движения отсутствуют. Сила тока определяется по формуле I=50dэ.
Ручная аргонодуговая сварка вольфрамовым электродом (сварка в защитных газах). Выполняется угольным или вольфрамовым электродом на постоянном токе прямой полярности.
Защитный газ - аргон, гелий.
Присадочная проволока марки Ml или Бр.КМц3-1.
При толщине металла более 4 мм сваривают с предварительным подогревом.
Автоматическая сварка под слоем флюса. Производится под флюсом марок ОСЦ-45, АН 348-А, АН-20. Проволока диаметром 1,6-4 мм марки Ml или Бр.КМц3-1.
Газовая сварка. Требует повышенной мощности пламени. Для листов толщиной до 10 мм мощность пламени 150 дм3/ч на 1 мм толщины металла, а свыше 10 мм - 200 дм3/ч.
Для уменьшения отвода теплоты изделие закрывают листовым асбестом.
Пламя используют строго нормальное. Избыток ацетилена вызывает образование пор и трещин, а избыток кислорода ведет к окислению металла шва.
Нагрев и плавка меди производится восстановительной зоной.
Наклон горелки - 80-90°. Сварку ведут быстро, без перерывов, за один проход.
Присадочная проволока - чистая медь или медь с раскислителем.
Диаметр проволоки от 1,5 до 8 мм, в зависимости от толщины металла.
В процессе сварки подогретый конец присадочного прута периодически обмакивают во флюс, так его переносят в сварочную ванну.
Для получения мелкозернистой структуры металл проковывают: толщиной до 5 мм - в холодном состоянии; при большой толщине - в горячем состоянии (200-300°). После производят отжиг при температуре до 550°С и охлаждают в воде. При этом шов получается более пластичным.
Сварка латуни. Латунь - это сплав меди с цинком. Сваривается теми же способами, что и медь.
Основное затруднение при сварке латуни связано с кипением и интенсивным испарением цинка, пары которого в воздухе образуют ядовитые окислы.
При дуговой сварке применяют присадочные прутки из латуни ЛМц58-2 и флюс из молотого борного шлака или буры.
При автоматической сварке используют проволоку из меди Ml и флюс АН-348А или ОСЦ-45.
При газовой сварке нормальным пламенем выделяются пары цинка, в результате чего шов получается пористым. Поэтому применяют пламя окислительное. Избыток кислорода окисляет часть цинка, и образующая на поверхности сварочной ванны оксидная пленка защищает расплавленный металл от дальнейшего окисления.
Сварка бронзы. Бронзой называется сплав меди с любым из металлов, кроме цинка. Сваривается так же, как и медь.
Сварка алюминия и его сплавов. Алюминий обладает малой плотностью, высокой тепло- и электропроводностью. Наибольшее применение получили сплавы алюминия с марганцем АМц.
Поверхность алюминия и его сплавов покрыта тугоплавкой оксидной пленкой, плавящейся при температуре 2050°С. Эта пленка очень затрудняет сплавление основного и присадочного металла. Поэтому свариваемые кромки необходимо тщательно очистить механическим или чаще всего химическим способом.
Виды сварки те же, что и меди, но используются прутки с алюминиевой основой и сварочная проволока на основе алюминия (СвА97, СвАМц).
Газовую сварку выполняют левым способом нормальным пламенем.
Сварка титановых сплавов. Титан обладает антикоррозионной стойкостью. Титан более активен по сравнению с алюминием к поглощению кислорода, азота, водорода в процессе нагрева. Поэтому при сварке технического титана необходима особо надежная защита от этих газов. Такая защита осуществляется при дуговой сварке в инертных газах и при использовании флюсов-паст, которые являются бескислородными.
Дуговая сварка титана и его сплавов покрытыми, угольными электродами и газовым пламенем не применяется. Этими видами сварки невозможно обеспечить высокое качество сварных соединений из-за слишком большой активности титана к кислороду, азоту и водороду.
Вопрос 2. Сварочные полуавтоматы (назначение, классификация, устройство, требования техники безопасности).
Общие сведения и классификация сварочных полуавтоматов. При механизированной сварке используют специальные сварочные аппараты, обеспечивающие механизированную подачу сварочной проволоки, а перемещение дуги вдоль оси шва выполняется вручную. Такие аппараты получили название полуавтоматов для дуговой сварки.
Полуавтоматы классифицированы по разным признакам:
• по способу защиты сварочной зоны - для сварки под флюсом, в среде защитных газов, открытой дугой;
• по способу регулирования дуги - в основном применяют полуавтоматы с саморегулированием дуги;
• по виду применяемой проволоки - сплошной, порошковой или комбинированной;
• по способу подачи проволоки - толкающего, тянущего и комбинированного типа;
• по конструктивному исполнению - со стационарным, передвижным и переносным подающим устройством.
Для сварки выпускают полуавтоматы, рассчитанные на номинальные токи 150-600 А, для проволоки диаметром 0,8-3,5 мм со скоростями подачи 1,0-17,0 м/мин.
В комплект полуавтоматов обычно входят:
• подающее устройство с кассетами для электродной проволоки;
• шкаф управления;
• сварочные горелки;
• провода для сварочной цепи и цепей управления;
• газовая аппаратура.
Устройство и основные узлы полуавтоматов. При механизированной сварке сварочная головка чаще всего разделена на две части - подающий механизм и держатель (при сварке в защитных газах – сварочная горелка), соединенные между собой гибким шлангом. Поэтому такие аппараты иногда называют шланговыми.
Полуавтоматы позволяют сочетать преимущества автоматической сварки с универсальностью и маневренностью ручной.
Типовая схема полуавтомата показана на рис. 54. В их состав входят узлы: держатель 1, гибкий шланг 2, механизм подачи сварочной проволоки 3, кассета со сварочной проволокой 4 и аппаратный шкаф, или шкаф управления 5.
Наиболее ответственным элементом полуавтоматов является механизм подачи проволоки. Его назначение и компоновка примерно те же, что и у сварочных головок автоматов для дуговой сварки. Обычно она состоит из электродвигателя, редуктора и системы подающих и прижимных роликов. Механизм обеспечивает подачу электродной проволоки по гибкому шлангу в зону сварки.
Рис. 54. Схема полуавтомата для дуговой сварки
Приводом могут служить двигатели переменного или постоянного тока.
Скорости подачи в первом случае изменяют ступенчато-сменными шестернями, во втором – происходит плавное регулирование за счет изменения частоты вращения двигателя.
Конструктивное оформление механизма подачи во многом зависит от назначения полуавтомата. В полуавтоматах для сварки проволокой большого диаметра механизм подачи размещен на передвижной тележке и располагается в отдельном корпусе. В полуавтоматах с проволокой малого диаметра он установлен в переносном футляре и расположен непосредственно на корпусе держателя.
Наибольшее распространение получили полуавтоматы толкающего типа. Подающий механизм подает проволоку путем проталкивания ее через гибкий шланг к горелке. Устойчивая подача в этом случае возможна при достаточной жесткости электродной проволоки.
В полуавтоматах тянущего типа механизм подачи или его подающие ролики размещены в горелке. В этом случае проволока протягивается через шланг. Такая система обеспечивает устойчивую подачу мягкой и тонкой проволоки.
Имеются полуавтоматы с двумя синхронно работающими механизмами подачи, осуществляющими одновременно проталкивание и протягивание проволоки через шланг (тянуще-толкающий тип).
Гибкий шланг в полуавтоматах предназначен для подачи электродной проволоки, сварочного тока, защитного газа, а иногда и охлаждающей воды к горелке. С этой целью применяют шланговый провод специальной конструкции.
Сварочные горелки предназначены для подвода к месту сварки электродной проволоки, сварочного тока и защитного газа или флюса, а также для ручного перемещения и манипулирования им в процессе сварки.
При этом сварщик удерживает держатель в руке и перемещает его вдоль шва. Быстро изнашивающимися частями держателя (при сварке в защитных газах - горелками) являются токоподводящий наконечник и газовое сопло, изготовляемые из меди.
При сварке под флюсом на держателе устанавливается бункер для флюса (рис. 55).
В полуавтомате используются приводы, работающие как на переменном, так и постоянном токе.
Рис. 55. Держатель полуавтомата для сварки под флюсом:
1 - наконечник; 2 - бункер для флюса; 3 - сварочная проволока; 4 - ручка; 5 - шланг
Техническое обслуживание полуавтоматов для дуговой сварки. Для обеспечения бесперебойной и длительной работы полуавтоматов, а также для своевременного устранения мелких неисправностей при их эксплуатации необходимо проводить профилактические работы.
Ежедневно перед началом работы следует:
• проверить состояние наконечника мундштука и газового сопла. При загрязнении очистить от брызг и нагара, восстановить надежный контакт;
• проверить место крепления мундштука к шланговому кабелю;
• проверить крепление сварочной, горелки к шланговому кабелю, осмотреть изоляцию проводов;
• опробовать работу полуавтомата пробными включениями пусковой пробки.
Не реже одного раза в месяц:
• проверить состояние роликов подающего механизма;
• проверять уровень смазки в редукторе подающего механизма и долить в случае необходимости;
• очищать от накопившейся грязи канал, по которому подается электродная проволока.
3. Задача. Перечислите зоны газового пламени. Назовите, какой зоной производят сварочные работы. Обоснуйте свой ответ.
Пламя имеет три ярко различимые зоны: ядро, восстановительная зона, факел.
Восстановительной зоной ведут сварку, поэтому ее называют еще рабочей. Это обусловлено тем, что эта зона имеет наиболее высокую температуру (3140°С) в точке, отстоящей на 3-6 мм от конца ядра.
Билет № 22
Вопрос 1. Особенности сварки легированных сталей.
Легированными называют стали, в состав которых специально вводят заданное количество легирующих элементов для получения требуемых свойств.
Легированные стали в зависимости от содержания в них легирующих компонентов подразделяют на:
• низколегированные (с содержанием легирующих компонентов, кроме углерода, не более 2,5%);
• среднелегированные (с содержанием легирующих компонентов, кроме углерода, 2,5-10%);
• высоколегированные (с содержанием легирующих компонентов, кроме углерода, свыше 10%).
Низколегированные стали предназначены для сварных конструкций, работающих при нормальной температуре. В качестве легирующих элементов они содержат
металлы, например марганец, кремний, хром.
Дуговая сварка. При дуговой сварке легированных сталей применяются следующие режимы:
Указанные значения тока соответствуют сварке в нижнем положении. При выполнении вертикальных и потолочных швов ток уменьшают на 10-20% и применяют электроды диаметром не более 4 мм.
Для уменьшения скорости охлаждения металла шва следует применять стыковые и бортовые соединения, так как при тавровых и нахлесточных соединениях скорость охлаждения выше. Рекомендуется избегать соединений, имеющих швы замкнутого контура; если же необходимы такие соединения, то их сваривают короткими участками, обеспечивая подогрев и замедленное охлаждение.
Сварку стыковых соединений металла толщиной до 6 мм и швов с катетом до 7 мм выполняют в один слой (однопроходную), что уменьшает скорость охлаждения.
Более толстый металл сваривают в несколько слоев длинными участками. Каждый слой должен иметь толщину 0,8-1,2 диаметра электрода. Сверху шва накладывают отжигающий валик, края которого должны располагаться на расстоянии 2-3 мм от границы проплавления основного металла. Отжигающий валик накладывают при температуре предыдущего слоя около 200°С.
Для металла толщиной до 40-45 мм применяют многослойную сварку способом горки или каскада. Длину участков (300-350 мм) выбирают с таким расчетом, чтобы предыдущий слой не успевал охладиться ниже 200°С при наложении следующего слоя.
Если сталь склонна к закалке или при сварке на морозе, перед выполнением первого шва применяют местный подогрев горелкой или индуктором до 200-250°С.
Сварку конструкционных низкоуглеродистых сталей производят электродами с фтористокальциевыми покрытиями марок УОНИ-13/45, УОНИ-13/55, УОНИ-13/65, УОНИ-13/85, ОЗС-2, ЦУ-1, ДСК-50, УП-1/55, УП-2/55, К-5А, ЦЛ-18, НИАТ-5 и другими, дающими более плотный и вязкий наплавленный металл, менее склонный к старению.
Электроды с руднокислыми покрытиями (ОММ-5, ЦМ-7 и др.) применять при сварке ответственных конструкций из низколегированных сталей не рекомендуется.
Низколегированные конструкционные стали лучше сваривать электродами типа Э42А, так как металл шва получает дополнительное легирование за счет элементов расплавляемого основного, при этом металл шва сохраняет высокую пластичность.
Сварка электродами типа Э60А дает более прочный, но менее пластичный металл шва вследствие более высокого содержания в нем углерода.
Сварка средне- и высоколегированных сталей. Сварка этих видов сталей затруднена по ряду причин:
• В процессе сварки происходит частичное выгорание легирующих примесей и углерода.
• Вследствие малой теплопроводности возможен перегрев свариваемого металла.
Эти стали отличает повышенная склонность к образованию закалочных структур, а больший, чем у низкоуглеродистых сталей, коэффициент линейного расширения может вызвать значительные деформации и напряжения, связанные с тепловым влиянием дуги. Причем, чем больше в стали углерода и легирующих примесей, тем сильнее проявляются эти свойства.
Для устранения влияния перечисленных причин на качество сварного соединения рекомендуется:
• тщательно подготавливать изделие под сварку;
• сварку вести при больших скоростях с малой погонной энергией, чтобы не допускать перегрева металла;
• применять термическую обработку для предупреждения образования закалочных структур и снижения внутренних напряжений;
применять легирование металла шва через электродную проволоку и покрытие с целью восполнения выгорающих в процессе сварки примесей.
Электроды для сварки высоколегированных сталей изготовляют из высоколегированной сварочной проволоки. Применяют покрытие типа Б.
Обозначения типов электродов состоят из индекса Э и следующих за ним цифр и букв. Две или три цифры, следующие за индексом, указывают на количество углерода в металле шва в сотых долях процента. Следующие затем буквы и цифры указывают примерный химический состав металла.
Сварку производят постоянным током обратной полярности. При этом сварочный ток выбирают из расчета 25-40 А на 1 мм диаметра электрода.
Длина дуги должна быть как можно короткой. Рекомендуется многослойная сварка малого сечения при малой погонной энергии.
Средиелегированные хромистые стали, содержащие до 2% углерода, относятся к мартенситному классу. Они свариваются удовлетворительно, но требуют подогрева до 200-300°С и последующей термической обработки.
Для сварки высоколегированных сталей и сталей с особыми свойствами применяют электроды, стержни которых выполнены из специальной проволоки, по химическому составу близкой к свариваемой стали. Также эти стали сваривают в защитных газах.
Газовая сварка низколегированных сталей производится нормальным пламенем мощностью 75-100 дм3/ч при левой и 100-130 дм3/ч при правой сварке на 1 мм толщины металла.
В качестве присадки используют проволоку Св-08, Св-08А или Св-10Г2.
Целесообразно проковывать шов при светло-красном калении с последующей нормализацией нагревом горелкой.
В качестве присадочной проволоки при сварке среднелегированных сталей используют проволоку, по химическому составу близкую к составу металла.
Рекомендуется сваривать с предварительным подогревом до 250-300°С, в связи с тем, что эти стали способны к закалке на воздухе.
Кромки свариваемого металла перед сваркой зачищают до металлического блеска.
Сварку рекомендуется вести с наименьшим числом перерывов. По окончании сварки пламя горелки медленно отводят вверх, что способствует более полному выделению газов из расплавленного металла.
Вопрос 2. Газовая сварка трубных конструкций.
Широкое применение получила газовая сварка труб небольшого диаметра (до 100 мм с толщиной стенок до 2-3 мм), особенно при монтаже систем отопления и горячего водоснабжения, водопроводов, газопроводов и других трубчатых конструкций.
Трубы сваривают чаще всего встык, так как стыковые соединения требуют наиболее простой подготовки кромок, наименьших затрат времени и расхода горючего газа.
При толщине стенок труб до 5 мм сварку проводят без разделки кромок, а стык собирают с зазором 1,5-2 мм.
При сварке труб с толщиной стенок более 5 мм применяют одностороннюю разделку кромок под углом 70-90º, оставляя притупление от 1,5 до 2,5 мм. Притупление необходимо для того, чтобы при сварке кромки не проплавлялись, и расплавленный металл не протекал внутрь трубы.
В зависимости от назначения конструкции используют и другие способы стыковки труб - без скоса кромок с подкладным кольцом, с раструбом и вставным кольцом.
Перед сваркой трубы выравнивают так, чтобы оси их совпадали, и прихватывают. Для центровки труб применяют центраторы и другие приспособления.
Сварку труб можно выполнять как левым, так и правым способами.
Газовой сваркой стыки сваривают в один слой.
Если трубу можно поворачивать, то сварку ведут в нижнем положении; неповоротный стык сваривают во всех пространственных положениях, что является наиболее трудным для сварщика.
Сварку труб большого диаметра (300 мм и более) выполняют четырьмя отдельными участками, как показано на рис. 56, а.
Рис. 56. Последовательность сварки труб большого диаметра:
а - 200-300 мм; б - 500-600 мм; в - сварка без поворота
При сварке труб диаметром 500-600 мм сварку могут вести одновременно два сварщика. Вначале заваривают верхнюю часть трубы на участках 1 и 2 (рис. 56, б), затем трубу поворачивают и также одновременно заваривают участки 3 и 4.
Если поворачивать трубу нельзя, то участки 3 и 4 сваривают в порядке, указанном на рис. 56, в, пунктирными стрелками.
3. Задача. Назовите способ, которым вы воспользуетесь, чтобы устранить трещину, видимую в металле шва.
Трещину засверливают по краям, чтобы избежать дальнейшего увеличения при последующей вырубке.
После засверливания вырубают металл около трещины до основного металла и вновь заваривают.
Билет № 23
Вопрос 1. Газовые шланги (рукава) (назначение, классификация, требования техники безопасности).
Рукава служат для подвода газа к горелке или резаку. Рукава, применяемые при газовой сварке и резке, должны обладать достаточной прочностью, выдерживать определенное давление, быть гибкими и не стеснять движений сварщика.
Согласно ГОСТу 9356-75, рукава делают из вулканизированной резины с тканевыми прокладками.
Кислородные рукава имеют внутренний и наружный слой из вулканизированной резины и несколько слоев из льняной или хлопчатобумажной ткани.
В зависимости от назначения резиновые рукава для газовой сварки и резки металлов подразделяют на следующие классы:
• I - для подачи ацетилена, городского газа, пропана и бутана под давлением до 0,63 МПа;
• II - для подачи жидкого топлива (бензина, уайт-спирита, керосина или их смеси) под давлением до 0,63 МПа;
• III - для подачи кислорода под давлением до 2 МПа.
Внутренний диаметр рукавов равен 6,3; 8,0; 9,0; 10,0; 12,0; 12,5; 16,0 мм.
Рукава поставляют длиной 10 и 14 м.
В зависимости от назначения наружный слой рукава окрашивают в следующие цвета:
• красный - рукава I класса;
• желтый - рукава II класса;
• синий - рукава III класса.
Рукава предназначаются для работы при температуре от +50 до -35°С (238°К), для более низкой температуры изготовляют рукава из морозостойкой резины, выдерживающей температуру до -65°С (208°К).
Все рукава должны иметь не менее чем трехкратный запас прочности при разрыве гидравлическим давлением. Рукава II класса должны быть бензостойкими.
Для нормальной работы горелкой или резаком длина рукавов не должна превышать 20 м, при использовании более длинных рукавов значительно снижается давление газа.
В монтажных условиях рукава можно удлинять до 40 м, на использование более длинных требуется специальное разрешение.
Для удлинения кислородных рукавов служат латунные, а ацетиленовых - стальные ниппели, снаружи закрепляющиеся специальными хомутами. Запрещается применение ниппелей для соединения рукавов, по которым проходит бензин или керосин, так как горючее может просочиться в соединение.
Количество соединений рукавов не более трех.
Рукава необходимо надежно крепить на горелках, резаках, редукторах, бачках жидкого горючего. Хранят рукава в помещении при температуре от 0 до +25°С.
Вопрос 2. Сварка чугуна (газовая, дуговая).
Чугуном называется железоуглеродистый сплав с содержанием углерода более 2,14%.
Сварка чугуна производится при ремонтно-восстановительных работах, исправлениях дефектов в чугунных отливках.
Сварка чугуна затруднена по следующим причинам:
1. При быстром охлаждении расплавленного чугуна происходит отбеливание чугуна, т. е. образование белого чугуна, очень хрупкого и твердого. Механическая обработка чугуна, имеющего отбеленные зоны, очень трудна.
2. Неравномерность нагрева в свариваемой детали приводит к появлению трещин. Поэтому необходимо замедлить процесс остывания шва и прилежащих к нему участков свариваемой детали.
3. Сварку ведут только в нижнем положении, так как чугун не имеет пластического состояния при переходе из твердого состояния в жидкое.
4. Образование пористости шва за счет интенсивного выгорания углерода и быстрого затвердевания расплавленного металла.
5. Образование пленки окислов кремния на поверхности ванны, имеющих высокую температуру плавления.
Чугун сваривается как дуговой, так и газовой сваркой. В том и другом случае возможна:
• горячая сварка с предварительным и сопутствующим подогревом изделия;
• холодная сварка без предварительного подогрева изделия.
Выбор способа сварки определяется составом чугуна, конструкцией детали, характером дефекта и условиями работы.
Материал для сварки. Используют чугунные прутки Ø 4, 6,8, 10,12,16 мм длиной 250, 350 и 450 мм.
По назначению прутки делятся на следующие марки:
• А - для горячей газовой сварки (с торца маркированы белой краской);
• Б - для газовой сварки с местным нагревом и для электродных стержней;
• НЧ-1; НЧ-3 - для низкотемпературной газовой сварки тонкостенных и толстостенных отливок.
Горячая газовая сварка чугуна.
С общим подогревом. Наиболее надежный способ, обеспечивающий лучшее качество сварного соединения. Процесс газовой сварки разбивается на ряд операций. К ним относится:
1. Подготовка детали под сварку.
2. Предварительный подогрев детали.
3. Сварка деталей.
4. Охлаждение деталей после сварки.
Трещины засверливают, разделку ведут механическим способом. При толщине свыше 5 мм выполняют разделку кромок под углом 70-90°.
Детали, подготовленные под сварку, подвергают нагреву до 500-700°С. Общий подогрев ведется в электрических и газовых печах, специальных термических печах, горнах. При отсутствии специальных печей сооружают временные печи. При этом деталь обкладывают древесным углем и закрывают асбестом. После того как деталь нагреется, ее подают на рабочее место сварщика и закрывают асбестовым листом, оставляя открытым только место сварки.
Сварку выполняют нормальным пламенем или с небольшим избытком ацетилена. В качестве присадки применяют чугунные прутки марки А. Им необходимо перемешивать сварочную ванну для облегчения выделения газа.
При горячей газовой сварке применяют флюс, способствующий улучшению процесса сварки и удалению образовавшихся окислов. В этом качестве используют буру.
Для получения качественного сварного соединения необходимо после сварки уменьшить скорость охлаждения, наплавленный металл подогревают пламенем в течение 1-1,5 мин. Массивные детали для снятия внутренних напряжений подвергают вторичному нагреву до 600-750ºС.
С местным подогревом. Применяется при сварке массивных деталей. Нагревают участок так, чтобы в детали создавались тепловые деформации, равнозначные деформациям, которые возникают на участке сварки.
Местный подогрев выполняют до 300-500° сварочными горелками или другими способами. Пламя нормальное, в качестве присадочного материала выбирают пруток марки Б.
Холодная газовая сварка чугуна. Процесс сварки без предварительного нагрева аналогичен процессу горячей сварки, но со своими особенностями.
Перед заваркой дефекта необходимо подогревать пламенем горелки участки, прилегающие к дефекту. По окончании заполнения дефекта горелку в течение 2-3 минут медленно отводят, направляя пламя на участки, прилегающие к дефекту. Деталь или часть детали, на которой находится заваренный участок, для медленного охлаждения засыпают песком или покрывают асбестом.
Дуговая сварка
Сварка стальными электродами с применением шпилек. Сталь при наплавке на чугун плохо сцепляется с ним из-за разной усадки. Кроме того, наплавленная на чугун сталь обогащается углеродом в зоне плавления, становится хрупкой, склонной к закалке, и дает при остывании трещины. Поэтому при сварке чугуна обычными стальными электродами (УОНИ-13/45 и УОНИ-13/55) для более надежного сцепления наплавленного металла с основным на кромках в шахматном порядке ставят на резьбе стальные шпильки (рис. 57, а).
При толщине стенки менее 10 мм шпильки ставят только на нескошенной части кромок. Шпильки обваривают кругом, после чего шов заполняют наплавленным металлом (рис. 57, б).
Рис. 57. Сварка чугуна с применением шпилек
Диаметр шпилек определяется по формуле:
d=(0,15-0,2)S,
где d - диаметр шпильки;
S - толщина стенки, мм.
Шпильки диаметром менее 3 мм не применяют.
Расстояние между шпильками составляет (4-6)d, глубина посадки 2d, расстояние от кромок не менее (1,5-2)d.
Электроды с покрытием типа УОНИ применяют при сварке чугуна потому, что они требуют использования постоянного тока обратной полярности. Это уменьшает перегрев детали и снижает выгорание кремния.
Для снижения внутренних напряжений сварку ведут с перерывами, не давая изделию нагреться выше 100°С. При использовании электродов диаметром 3 мм ток не должен превышать 120 А, диаметром 4 мм - 150 А, 5 мм - 220 А.
Первые слои шва и обварку шпилек целесообразно выполнять электродами (ЦЧ-4) (см. ниже), а последующие - УОНИ-13/55.
Сварка чугуна без подогрева стальными электродами с дополнительным креплением стальными шпильками и связями является вполне надежной и применяется при ремонте ответственных крупногабаритных деталей, испытывающих большие нагрузки.
Сварка специальными электродами. Для сварки и наплавки без подогрева деталей из серого и высокопрочного чугуна и заварки дефектов в отливках применяют электроды ЦЧ-4 из проволоки Св-08 с фтористокальциевым покрытием, разработанные отделом сварки ЦНИИТМАШ.
В состав покрытия введены элементы, активно вступающие в механическое соединение с углеродом свариваемого металла и образующие устойчивые карбиды, не растворимые в железе.
Сварка электродами ЦЧ-4 может вестись в нижнем и вертикальном положении. Применяется постоянный ток прямой полярности, можно использовать переменный ток.
Режимы сварки следующие:
Сварку производят небольшими участками длиной 30-60 мм. Для улучшения обрабатываемости рекомендуется на рапсе наплавленный слой накладывать отжигающий валик, не затрагивая при этом основного металла.
При сварке металла больших толщин первые слои по чугуну выполняют электродами ЦЧ-4, а затем заполняют всю разделку кромок электродами УОНИ-13/45 или УОНИ-13/55.
Для уменьшения напряжений наплавленный металл проковывают легкими ударами молотка. Сварку возобновляют после остывания металла до 50-60°. Наплавленный металл может обрабатываться твердосплавным инструментом.
Сварка медно-железными электродами ОЗЧ-1. Эти электроды с фтористо-кальциевым покрытием, содержащим железный порошок, применяют для сварки и наплавки чугуна без подогрева.
Стержень электрода выполнен из меди М-2 и М-3. В отдельных случаях при повышенных требованиях к чистоте поверхности после обработки и плотности сварного соединения электроды ОЗЧ-1 применяют в сочетании с электродами МНЧ-1 (см. ниже), которыми свариваются первые два или один последний слои шва.
Электроды ОЗЧ-1 допускают сварку в нижнем и вертикальном и полупотолочном положении.
Применяется постоянный ток обратной полярности при диаметре электрода: 3 мм - 90-110 A; 4 мм - 120-140 А, 5 мм - 160-190 А.
Сварку ведут предельно короткой дугой, участками по 30-60 мм, проковывая каждый участок сразу же после обрыва дуги и возобновляя сварку после охлаждения наплавки до 50-60 "С. Сварное соединение допускает обработку твердосплавным инструментом.
Сварка медно-никелевыми электродами МНЧ-1. Эти электроды с фтористо-кальциевым покрытием имеют проволоку из сплава НМЖМц (монель-металл) на основе меди.
Применяются для сварки и наплавки чугуна без подогрева, в сочетании с электродами ОЗЧ-1 (для сварки первого, обеспечивающего плотность, и последнего, обрабатываемого, швов). Сварку ведут так же, как и электродами ОЗЧ-1, на тех же режимах, короткими участками с проковкой металла шва. Наплавленный слой хорошо обрабатывается.
3. Задача. Объясните, что такое сталь и чугун? В чем их отличие?
Сталь и чугун относятся к железоуглеродистым сплавам. Это сплавы, в состав которых входит железо и углерод, а также другие элементы (кремний, марганец, сера, фосфор, легирующие элементы).
Различие этих сплавов в количестве углерода. Если в сплаве содержание углерода до 2,14%, то это сталь; если более 2,14% углерода, то это чугун.
Билет № 24
Вопрос 1. Наплавочные работы (виды, назначение, технология, материалы).
Наплавка деталей и восстановление изношенных деталей наплавкой - эффективный и экономичный способ продления срока службы деталей и машин.
Наплавку выполняют с помощью сварки, преимущественно дуговой, для наложения необходимого слоя металла на поверхность детали с целью повышения ее стойкости против истирания, повышенных температур, абразивного изнашивания, коррозии и других видов разрушения.
Наплавку применяют для восстановления размеров изношенных деталей и создания слоя металла и поверхности детали, отличающегося по своим свойствам от основного металла детали повышенной износостойкостью, антикоррозионностью, жаростойкостью и другими свойствами.
Наиболее распространены ручная дуговая наплавка покрытыми электродами, наплавка неплавящимися угольным или вольфрамовым электродом в среде защитного газа, наплавка в углекислом газе, под слоем флюса, вибродуговая наплавка.
По степени механизации процесса различают наплавку:
• ручную дуговую покрытыми электродами;
• полуавтоматическую;
• автоматическую.
Материалы для наплавки. Сплавы, применяемые для дуговой наплавки, можно подразделить на:
• литые (сормайт);
• порошкообразные или зернистые (вокар, висхром-9);
• плавленые карбиды и спеченные (карбиды вольфрама и титана).
Для ручной и механизированной наплавки выпускают большое количество различных наплавочных материалов (проволок, лент, электродов, флюсов и др.) различных химических составов и свойств. При выборе наплавляемого металла учитывают химический состав металла наплавляемой детали, условия работы, характер и вид нагрузки, износ, требуемую износостойкость.
Особое внимание при наплавке под флюсом уделяют свойствам флюсов: способствуют ли они формированию наплавленного металла, стабильности горения дуги, какой склонностью обладают к образованию пор в наплавленном металле, какие содержат легирующие элементы.
Наплавку выполняют покрытыми, проволочными и ленточными электродами. При этом ленточный и проволочный электроды могут быть сплошными или в виде порошковой ленты или порошковой проволоки.
Порошковый электрод представляет собой стержень из порошковой проволоки, имеющий толстое основное покрытие. На свойства и состав наплавленного металла влияют изменения состава порошкового наполнителя.
Порошковые электроды более производительные, чем стержневые.
При наплавке порошковым электродом создается защита легирующих элементов за счет более быстрого плавления наполнителя по сравнению со скоростью плавления оболочки электрода.
Наплавку высоколегированных сталей рекомендуется вести под низколегированными флюсами ФЦЛ-2 и АН-20, под бескислородными флюсами БКФ-1, ВКФ-2, под флюсами 48-ОФ-7 и АН-70.
Технология и способы наплавки. Сущность процесса наплавки заключается в использовании теплоты для расплавления присадочного материала и его соединения с основным металлом детали.
Используя возможности дуговой наплавки, на поверхности детали можно получить наплавленный слой любой толщины, любого химического состава с разнообразными свойствами.
Наплавка может производиться на:
• плоские;
• цилиндрические;
• конические;
• сферические и другие формы поверхности в один или несколько слоев.
Толщина слоя наплавки может изменяться в широких пределах - от долей миллиметра до сантиметров. При наплавке поверхностных слоев с заданными свойствами, как правило, химический состав наплавленного металла существенно отличается от химического состава основного металла.
Поэтому при наплавке должен выполняться ряд технологических требований.
1. В первую очередь таким требованием является минимальное разбавление наплавленного слоя основным металлом, расплавляемым при наложении валиков. Поэтому в процессе наплавки необходимо получение наплавленного слоя с минимальным проплавлением основного металла, так как в противном случае возрастает доля основного металла в формировании наплавленного слоя. Это приводит к ненужному разбавлению наплавленного металла расплавляемым основным.
2. При наплавке необходимо обеспечение минимальной зоны термического влияния и минимальных напряжений и деформаций.
Это требование обеспечивается за счет уменьшения глубины проплавления, регулированием параметров режима, погонной энергии, увеличением вылета электрода, применением широкой электродной ленты и другими технологическими приемами.
Технология наплавки различных поверхностей предусматривает ряд приемов нанесения наплавленного слоя:
• ниточными валиками с перекрытием один другого на 0,3-0,4 их ширины;
• широкими валиками, полученными за счет поперечных к направлению оси валика колебаний электрода, электродными лентами и др.
Расположение валиков с учетом их взаимного перекрытия характеризуется шагом наплавки (рис. 44).
Рис. 44. Схема наплавки слоев:
В, hн, hпр - соответственно ширина валика, высота наплавки, глубина проплавления; Sн - шаг наплавки
Наплавку криволинейных поверхностей тел вращения выполняют тремя способами (рис. 45):
• наплавкой валиков вдоль образующей тела вращения;
• по окружностям;
• по винтовой линии.
Рис. 45. Наплавка тел вращения:
а - по образующей; б - по окружности; в - по винтовой линии
Наплавку по образующей выполняют отдельными валиками так же, как при наплавке плоских поверхностей.
Наплавка по окружности также выполняется отдельными валиками до полного замыкания начального и конечного участков со смещением их на определенный шаг вдоль образующей.
При винтовой наплавке деталь вращают непрерывно, при этом источник нагрева перемещается вдоль тела со скоростью, при которой одному обороту детали соответствует смещение источника нагрева, равное шагу наплавки.
При наплавке тел вращения необходимо учитывать возможность стекания расплавленного металла в направлении вращения детали. В этом случае источник нагрева смещают в сторону, противоположную направлению вращении (рис. 46).
Рис. 46. Смещение электрода при наплавке тел вращения:
а - наклонно расположенным электродом; б - с вертикальным расположением электрода
Предварительный подогрев наплавляемой детали до температуры 200-250°С уменьшает склонность наплавленного металла к образованию трещин.
Все дефекты в наплавленном металле можно подразделить на наружные и внутренние.
К последним относятся непровар (несплавление наплавленного металла с основным), пористость, трещины и шлаковые включения. Наружные дефекты, к которым относятся раковины и трещины, выявляют визуально.
Режимы наплавки характеризуются следующими параметрами:
• при ручной наплавке покрытым электродом в технологии указывают марку электрода, его диаметр, род тока, сварочный ток;
• при автоматической наплавке - тип электродного материала (проволока, лента: сплошного сечения, порошковая), ток, напряжение дуги, длину дуги, скорость наплавки;
• при наплавке в защитном газе дополнительно указывают защитный газ;
• при наплавке под флюсом - марку флюса.
Выбирая способ наплавки, вначале оценивают возможность его применения в данном конкретном случае, затем определяют возможность обеспечения технических требований, предъявляемых к наплавленному материалу, и, наконец, оценивают экономическую эффективность наплавки. При оценке экономической эффективности способа наплавки общую стоимость ручной дуговой наплавки принимают за 100% наплавку под слоем флюса - 74%, а вибродуговую наплавку - 82%.
Вопрос 2. Сварка чугуна (газовая, дуговая).
Чугуном называется железоуглеродистый сплав с содержанием углерода более 2,14%.
Сварка чугуна производится при ремонтно-восстановительных работах, исправлениях дефектов в чугунных отливках.
Сварка чугуна затруднена по следующим причинам:
1. При быстром охлаждении расплавленного чугуна происходит отбеливание чугуна, т. е. образование белого чугуна, очень хрупкого и твердого. Механическая обработка чугуна, имеющего отбеленные зоны, очень трудна.
2. Неравномерность нагрева в свариваемой детали приводит к появлению трещин. Поэтому необходимо замедлить процесс остывания шва и прилежащих к нему участков свариваемой детали.
3. Сварку ведут только в нижнем положении, так как чугун не имеет пластического состояния при переходе из твердого состояния в жидкое.
4. Образование пористости шва за счет интенсивного выгорания углерода и быстрого затвердевания расплавленного металла.
5. Образование пленки окислов кремния на поверхности ванны, имеющих высокую температуру плавления.
Чугун сваривается как дуговой, так и газовой сваркой. В том и другом случае возможна:
• горячая сварка с предварительным и сопутствующим подогревом изделия;
• холодная сварка без предварительного подогрева изделия.
Выбор способа сварки определяется составом чугуна, конструкцией детали, характером дефекта и условиями работы.
Материал для сварки. Используют чугунные прутки Ø 4, 6,8, 10,12,16 мм длиной 250, 350 и 450 мм.
По назначению прутки делятся на следующие марки:
• А - для горячей газовой сварки (с торца маркированы белой краской);
• Б - для газовой сварки с местным нагревом и для электродных стержней;
• НЧ-1; НЧ-3 - для низкотемпературной газовой сварки тонкостенных и толстостенных отливок.
Горячая газовая сварка чугуна.
С общим подогревом. Наиболее надежный способ, обеспечивающий лучшее качество сварного соединения. Процесс газовой сварки разбивается на ряд операций. К ним относится:
1. Подготовка детали под сварку.
2. Предварительный подогрев детали.
3. Сварка деталей.
4. Охлаждение деталей после сварки.
Трещины засверливают, разделку ведут механическим способом. При толщине свыше 5 мм выполняют разделку кромок под углом 70-90°.
Детали, подготовленные под сварку, подвергают нагреву до 500-700°С. Общий подогрев ведется в электрических и газовых печах, специальных термических печах, горнах. При отсутствии специальных печей сооружают временные печи. При этом деталь обкладывают древесным углем и закрывают асбестом. После того как деталь нагреется, ее подают на рабочее место сварщика и закрывают асбестовым листом, оставляя открытым только место сварки.
Сварку выполняют нормальным пламенем или с небольшим избытком ацетилена. В качестве присадки применяют чугунные прутки марки А. Им необходимо перемешивать сварочную ванну для облегчения выделения газа.
При горячей газовой сварке применяют флюс, способствующий улучшению процесса сварки и удалению образовавшихся окислов. В этом качестве используют буру.
Для получения качественного сварного соединения необходимо после сварки уменьшить скорость охлаждения, наплавленный металл подогревают пламенем в течение 1-1,5 мин. Массивные детали для снятия внутренних напряжений подвергают вторичному нагреву до 600-750ºС.
С местным подогревом. Применяется при сварке массивных деталей. Нагревают участок так, чтобы в детали создавались тепловые деформации, равнозначные деформациям, которые возникают на участке сварки.
Местный подогрев выполняют до 300-500° сварочными горелками или другими способами. Пламя нормальное, в качестве присадочного материала выбирают пруток марки Б.
Холодная газовая сварка чугуна. Процесс сварки без предварительного нагрева аналогичен процессу горячей сварки, но со своими особенностями.
Перед заваркой дефекта необходимо подогревать пламенем горелки участки, прилегающие к дефекту. По окончании заполнения дефекта горелку в течение 2-3 минут медленно отводят, направляя пламя на участки, прилегающие к дефекту. Деталь или часть детали, на которой находится заваренный участок, для медленного охлаждения засыпают песком или покрывают асбестом.
Дуговая сварка
Сварка стальными электродами с применением шпилек. Сталь при наплавке на чугун плохо сцепляется с ним из-за разной усадки. Кроме того, наплавленная на чугун сталь обогащается углеродом в зоне плавления, становится хрупкой, склонной к закалке, и дает при остывании трещины. Поэтому при сварке чугуна обычными стальными электродами (УОНИ-13/45 и УОНИ-13/55) для более надежного сцепления наплавленного металла с основным на кромках в шахматном порядке ставят на резьбе стальные шпильки (рис. 57, а).
При толщине стенки менее 10 мм шпильки ставят только на нескошенной части кромок. Шпильки обваривают кругом, после чего шов заполняют наплавленным металлом (рис. 57, б).
Рис. 57. Сварка чугуна с применением шпилек
Диаметр шпилек определяется по формуле:
d=(0,15-0,2)S,
где d - диаметр шпильки;
S - толщина стенки, мм.
Шпильки диаметром менее 3 мм не применяют.
Расстояние между шпильками составляет (4-6)d, глубина посадки 2d, расстояние от кромок не менее (1,5-2)d.
Электроды с покрытием типа УОНИ применяют при сварке чугуна потому, что они требуют использования постоянного тока обратной полярности. Это уменьшает перегрев детали и снижает выгорание кремния.
Для снижения внутренних напряжений сварку ведут с перерывами, не давая изделию нагреться выше 100°С. При использовании электродов диаметром 3 мм ток не должен превышать 120 А, диаметром 4 мм - 150 А, 5 мм - 220 А.
Первые слои шва и обварку шпилек целесообразно выполнять электродами (ЦЧ-4) (см. ниже), а последующие - УОНИ-13/55.
Сварка чугуна без подогрева стальными электродами с дополнительным креплением стальными шпильками и связями является вполне надежной и применяется при ремонте ответственных крупногабаритных деталей, испытывающих большие нагрузки.
Сварка специальными электродами. Для сварки и наплавки без подогрева деталей из серого и высокопрочного чугуна и заварки дефектов в отливках применяют электроды ЦЧ-4 из проволоки Св-08 с фтористокальциевым покрытием, разработанные отделом сварки ЦНИИТМАШ.
В состав покрытия введены элементы, активно вступающие в механическое соединение с углеродом свариваемого металла и образующие устойчивые карбиды, не растворимые в железе.
Сварка электродами ЦЧ-4 может вестись в нижнем и вертикальном положении. Применяется постоянный ток прямой полярности, можно использовать переменный ток.
Режимы сварки следующие:
Сварку производят небольшими участками длиной 30-60 мм. Для улучшения обрабатываемости рекомендуется на рапсе наплавленный слой накладывать отжигающий валик, не затрагивая при этом основного металла.
При сварке металла больших толщин первые слои по чугуну выполняют электродами ЦЧ-4, а затем заполняют всю разделку кромок электродами УОНИ-13/45 или УОНИ-13/55.
Для уменьшения напряжений наплавленный металл проковывают легкими ударами молотка. Сварку возобновляют после остывания металла до 50-60°. Наплавленный металл может обрабатываться твердосплавным инструментом.
Сварка медно-железными электродами ОЗЧ-1. Эти электроды с фтористо-кальциевым покрытием, содержащим железный порошок, применяют для сварки и наплавки чугуна без подогрева.
Стержень электрода выполнен из меди М-2 и М-3. В отдельных случаях при повышенных требованиях к чистоте поверхности после обработки и плотности сварного соединения электроды ОЗЧ-1 применяют в сочетании с электродами МНЧ-1 (см. ниже), которыми свариваются первые два или один последний слои шва.
Электроды ОЗЧ-1 допускают сварку в нижнем и вертикальном и полупотолочном положении.
Применяется постоянный ток обратной полярности при диаметре электрода: 3 мм - 90-110 A; 4 мм - 120-140 А, 5 мм - 160-190 А.
Сварку ведут предельно короткой дугой, участками по 30-60 мм, проковывая каждый участок сразу же после обрыва дуги и возобновляя сварку после охлаждения наплавки до 50-60 "С. Сварное соединение допускает обработку твердосплавным инструментом.
Сварка медно-никелевыми электродами МНЧ-1. Эти электроды с фтористо-кальциевым покрытием имеют проволоку из сплава НМЖМц (монель-металл) на основе меди.
Применяются для сварки и наплавки чугуна без подогрева, в сочетании с электродами ОЗЧ-1 (для сварки первого, обеспечивающего плотность, и последнего, обрабатываемого, швов). Сварку ведут так же, как и электродами ОЗЧ-1, на тех же режимах, короткими участками с проковкой металла шва. Наплавленный слой хорошо обрабатывается.
3. Задача. Объясните, что такое сталь и чугун? В чем их отличие?
Сталь и чугун относятся к железоуглеродистым сплавам. Это сплавы, в состав которых входит железо и углерод, а также другие элементы (кремний, марганец, сера, фосфор, легирующие элементы).
Различие этих сплавов в количестве углерода. Если в сплаве содержание углерода до 2,14%, то это сталь; если более 2,14% углерода, то это чугун.
Билет № 25
Вопрос 1. Сварные соединения (виды, определение, достоинства, недостатки, применение).
Сварным соединением называют неразъемное соединение нескольких деталей, выполненное сваркой.
При сварке различают четыре вида соединений: стыковое, угловое, тавровое, нахлесточное.
Стыковое соединение имеет ряд преимуществ:
• неограниченная толщина свариваемых элементов;
• равномерное распределение напряжений при передаче усилий;
• минимальный расход металла на образование сварного соединения;
• удобство контроля качества шва.
Недостатки стыкового соединения: необходимость более точной сборки элементов под сварку.
Угловые и тавровые соединения используются при сварке балок, ферм, увеличивая жесткость конструкции. Они могут быть как односторонними, так и двусторонними. Угловые и тавровые двусторонние швы обладают высокой прочностью при статических нагрузках.
Нахлесточное соединение имеет преимущества перед другими соединениями:
• отсутствие скоса кромок под сварку;
• простота сборки соединения (возможность подгонки размеров за счет величины нахлестки).
Недостатки:
• повышенный расход основного металла на перекрытие в соединении. Нахлесточные соединения применяются для металла толщиной не более 6 мм. Величина нахлестки (перекрытия) должна быть не менее 3 толщин наиболее тонкого из свариваемых элементов. При сварке толщина нахлесточного соединения не должна превышать 12 мм;
• хуже работают на нагрузку;
• возможность проникновения влаги в щель между перекрытием;
• сложность определения дефектов сварки.
Вопрос 2. Сварочные редукторы (назначение, классификация, устройство, принцип действия, техника безопасности при эксплуатации).
При газовой сварке и резке металлов рабочее давление газов должно быть меньше, чем давление в баллоне или газопроводе.
Для понижения давления газа применяют редукторы.
Редуктором называется прибор, служащий для понижения давления газа, отбираемого из баллона до рабочего и для автоматического поддержания этого давления постоянным, независимо от изменения давления газа в баллоне или газопроводе.
Согласно ГОСТ 6268-78, редукторы для газопламенной обработки классифицируются:
• по принципу действия - на редукторы прямого и обратного действия;
• по назначению и месту установки - баллонный (Б), рамповый (Р), сетевой (С), центральный (Ц), универсальный высокого давления (У);
• по схеме редуцирования - одноступенчатый с механической установкой давления (О), двухступенчатый с механической установкой давления (Д), одноступенчатый с пневматической установкой давления (У);
• по роду редуцируемого газа - ацетиленовый (А), кислородный (К), пропан-бутановый (П), метановый (М).
Редукторы отличаются друг от друга цветом окраски корпуса и присоединительными устройствами для крепления их к баллону. Редукторы, за исключением ацетиленовых, присоединяются накидными гайками, резьба которых соответствует резьбе штуцера вентиля. Ацетиленовые редукторы крепят к баллонам хомутом с упорным винтом.
Принцип действия редуктора определяется его характеристикой. У редуктора прямого действия – падающая характеристика, т. е. рабочее давление по мере расхода газа из баллона несколько снижается, у редукторов обратного действия - возрастающая характеристика, т. е. с уменьшением давления газа в баллоне рабочее давление повышается.
Редукторы различаются по конструкции. Принцип действия и основные детали одинаковы для каждого редуктора.
Более удобны в эксплуатации редукторы обратного действия.
Редуктор обратного действии (рис. 7) работает следующим образом. Сжатый газ из баллона поступает в камеру высокого давления 8 и препятствует открыванию клапана 9. Для подачи газа в горелку или резак необходимо вращать по часовой стрелке регулирующий винт 2, который ввертывается в крышку 1. Винт сжимает нажимную пружину 3, которая, в свою очередь, выгибает гибкую резиновую мембрану 4 вверх. При этом передаточный диск со штоком сжимает обратную пружину 7, поднимая клапан 9, который открывает отверстие для прохода газа в камеру низкого давления 13. Открыванию клапана препятствует не только давление газа в камере высокого давления, но и пружина 7, более слабая, чем пружина 3.
Рис. 7. Схема редуктора обратного действия
Автоматическое поддержание рабочего давления на заданном уровне происходит следующим образом. Если отбор газа в горелку или резак уменьшится, то давление в камере низкого давления повысится, нажимная пружина 3 сожмется и мембрана 4 выпрямится, а передаточный диск 5 опустится, редуцирующий клапан 9 под действием пружины 7 прикроет седло клапана 10, уменьшив подачу газа в камеру низкого давления.
При увеличении отбора газа процесс будет автоматически повторяться. Давление в камере высокого давления 8 измеряется манометром 6, а в камере низкого давления 13 - манометром 11. Если давление в рабочей камере повысится сверх нормы, то с помощью предохранительного клапана 12 произойдет сброс газа в атмосферу.
В процессе эксплуатации редукторы окрашиваются в те же цвета, что и баллоны.. Необходимо следить, чтобы не произошло воспламенение редуктора из-за резкого открывания вентиля на баллоне, а также следить за техническим состоянием манометра.
3. Задача. Объясните причину и ваши действия в том случае, если при зажигании дуги она прилипает к металлу.
Прилипание дуги связано с несоответствием силы тока диаметру электрода. Сила тока мала. Необходимо правильно рассчитать силу тока и установить ее на источнике питания. Если источник питания не позволяет это сделать точно, то силу тока увеличивают опытным путем.
Билет № 26
Вопрос 1. Классификация сварных швов.
Часть сварного соединения, образовавшуюся в результате плавления кромок свариваемых металлов и электрода и непосредственно осуществляющую связь свариваемых частей, называют сварным швом.
Сварные швы классифицируют по:
• типу соединения;
• числу слоев, протяженности;
• расположению в пространстве;
• отношению к действующим усилиям (рис. 8).
Рис. 8. Виды сварных швов
По типу соединения швы делятся на стыковые и угловые.
Стыковые швы применяются при соединении частей металла встык, угловые - при выполнении тавровых, угловых и нахлесточных соединений.
Швы делятся на однослойные и многослойные. Однослойный шов выполняется за один проход, многослойный - за два прохода и более.
По протяженности сварные швы бывают непрерывные и прерывистые. Прерывистые характеризуются шагом шва.
По расположению в пространстве швы разделяют на нижние, вертикальные, горизонтальные и потолочные.
По отношению к действующим усилиям швы делятся на лобовые, фланговые, косые и комбинированные.
Вопрос 2. Контроль качества сварных швов (назначение, виды).
Внешний осмотр и обмеры сварных швов – наиболее простые и широко распространенные способы контроля их качества. Они являются первыми контрольными операциями по приемке готового сварного узла или изделия. Этим видам контроля подвергают все сварные швы независимо от того, как они будут испытаны в дальнейшем.
С помощью внешнего осмотра сварных швов выявляют наружные дефекты: непровары, наплывы, прожоги, подрезы, наружные трещины и поры, смещение свариваемых кромок деталей и т. п. Визуальный осмотр производят как невооруженным глазом, так и с применением лупы с увеличением до 10 раз.
Приступая к осмотру, сварной шов и прилегающую к нему поверхность основного металла на ширину не менее 20 мм по обе стороны шва очищают от шлака, брызг расплавленного металла, окалины и других загрязнений, которые могут затруднить проведение осмотра. Осматривать швы необходимо по всей их протяженности, а в случае недоступности – обязательно с двух сторон.
По результатам внешнего осмотра можно судить о местах расположения и характере внутренних дефектов. Например, подрез на одной из сторон шва и наплыв на другой указывают на возможный непровар по кромке. Непостоянная ширина шва часто является следствием неравномерной ширины зазора. В местах с малым зазором могут образоваться непровары, а с большим - прожоги. Перекосы и смещения кромок, а также большая высота шва могут быть причиной непроваров.
Обмеры сварных швов позволяют судить о качестве сварного соединения: недостаточное сечение шва уменьшает его прочность, слишком большое – увеличивает внутренние напряжения и деформации. Размеры сечения готового шва проверяют по его элементам в зависимости от типа соединения. У стыкового шва проверяют его ширину, высоту выпуклости и размер обратной подварки корня, в угловом шве (нахлесточное и тавровое соединения) измеряют катет. Замеренные величины должны соответствовать ТУ или ГОСТам. Размеры сварного шва контролируют обычными измерительными инструментами или специальными шаблонами. Набор шаблонов и его применение для контроля стыковых и угловых швов показаны на рис. 9. Каждый щуп набора представляет собой пластину с вырезами под определенный шов.
Внешний осмотр и обмеры сварного шва не дают возможности окончательно судить о качестве сварки. Они устанавливают только внешние дефекты шва и позволяют определить его сомнительные участки, которые могут быть проверены более точными способами.
Рис. 9. Набор шаблонов для контроля размеров сварного шва (а) и пример его применения (б):
1 - угловой шов; 2 - стыковые швы; 3 - блок
Контроль непроницаемости сварных швов и соединений.
Сварные швы и соединения ряда изделий и сооружений должны отвечать требованиям непроницаемости для различных жидкостей и газов. Это объясняется тем, что неплотности в швах снижают их прочность, уменьшают коррозионную стойкость, вызывают потерю хранимых и транспортируемых продуктов и создают ненормальные условия эксплуатации сварных конструкций. Учитывая это, во многих сварных конструкциях (резервуары, газгольдеры, трубопроводы, холодильная и вакуумная аппаратура и т. д.) сварные швы подвергают контролю на непроницаемость. Этот вид контроля производится после окончательного монтажа сварной конструкции. Дефекты, выявленные внешним осмотром (трещины, крупные видимые поры и др.), устраняются до начала испытаний. Непроницаемость сварных швов контролируют керосином, аммиаком, воздушным или гидравлическим давлением, вакуумированием или газоэлектрическими течеискателями.
Контроль керосином основан на физическом явлении капиллярности, которое заключается в способности многих жидкостей, а в первую очередь керосина, подниматься по капиллярным трубкам. Такими капиллярными трубками в сварных швах являются сквозные поры и трещины. В процессе испытания сварные швы покрывают водным раствором мела (350-450 г молотого мела на 1 л воды) или каолина с той стороны, которая более доступна для осмотра и выявления дефектов. После высыхания покрытой поверхности обратная сторона шва обильно смачивается керосином. Неплотности швов выявляют появлением жирных желтых точек или полосок керосина на меловом или каолиновом покрытии. Появление отдельных точек указывает на наличие пор и свищей, а полосок - сквозных трещин или непроваров.
Контроль аммиаком основан на изменении окраски некоторых индикаторов (спиртоводного раствора фенолфталеина или водного раствора азотнокислой ртути) под воздействием щелочей. В качестве щелочи применяется газ аммиак.
В процессе испытаний на одну сторону шва укладывают бумажную ленту или светлую ткань, пропитанную 5%-ным раствором азотно-кислой ртути, а с другой стороны обрабатывают шов смесью аммиака с воздухом под давлением.
Аммиак, проникая через неплотности сварного шва, окрашивает пропитанную индикатором бумагу или ткань в серебристо-черный цвет. При использовании в качестве индикатора спиртоводного раствора фенолфталеина его тонкой струей льют на контролируемый шов. Если в шве имеются неплотности, аммиак проходит через них и окрашивает индикатор в ярко-красный с фиолетовым оттенком цвет.
Контролю воздушным давлением (сжатым воздухом или другими газами) подвергают сосуды и трубопроводы, работающие под давлением.
Это испытание проводят с целью контроля общей непроницаемости сварного изделия.
Малогабаритные сварные изделия полностью герметизируют газонепроницаемыми заглушками и погружают в ванну с водой с таким расчетом, чтобы над изделием был слой воды в 20-40 мм. После этого в изделие через редуктор от воздушной сети или из баллона подают сжатый газ (воздух, азот, инертные газы) под давлением, на 10-20% превышающим рабочее.
Крупногабаритные сварные конструкции, которые не могут быть помещены в воду, испытывают следующим образом. Их герметизируют и создают в них испытательное давление. После этого сварные швы промазывают пенным индикатором (обычным водным раствором мыла), который пузырится в местах неплотностей.
При испытании сжатыми газами следует соблюдать правила безопасности труда: сварные сосуды необходимо испытывать в изолированном помещении с ограждениями на случай взрыва; трубопроводы испытывают отдельными изолированными участками с предупредительными знаками об опасности.
Контроль гидравлическим давлением применяют при проверке прочности и плотности различных сосудов, котлов, паро-, водо-, газопроводов и других сварных конструкций, работающих под избыточным давлением. Перед испытанием сварное изделие полностью герметизируют водонепроницаемыми заглушками. Сварные швы с наружной стороны тщательно обтирают ветошью или обдувают сжатым воздухом до получения сухой поверхности.
После полного заполнения изделия водой с помощью насоса или гидравлического пресса создают испытательное давление (обычно в 1,5-2 раза больше рабочего). Дефектные места определяют по появлению течи, просачиванию воды в виде капель, запотеванию на поверхности шва или вблизи него.
Это наиболее распространенные виды контроля качества сварных швов.
Но существует еще ультразвуковой, радиационный контроль качества сварного шва.
Сущность радиационного контроля основана на свойстве рентгеновских лучей проникать через металлические тела. После обработки рентгеновской пленки дефекты шва приобретают вид темных полос, пятен или черточек.
3. Задача. Объясните, почему для сварки ответственных конструкций преимущественно применяют источник постоянного тока.
Применение выпрямителя обеспечивает устойчивое горение электрической дуги. Это позволяет равномерно прогревать металл по всей длине шва, а также дает возможность контролировать количество тепла, поступаемого в металл при сварке за счет ранее установленной полярности дуги на источнике питания.
Билет № 27
Вопрос 1. Обозначение сварных швов на чертежах.
Согласно Единой системе конструкторской документации (ЕСК), изображения и обозначения швов сварных соединений в конструкторских документах изделий должны соответствовать ГОСТ 2.312-72 «Условные изображения и обозначения швов сварных соединений».
Изображение швов сварных соединений.
Независимо от вида сварки видимый шов сварного соединения условно изображают сплошной основной линией (рис. 10, а), а невидимый - штриховой (рис. 10, б).
Видимую одиночную сварную точку условно изображают знаком «+», невидимые одиночные точки не изображают.
Рис. 10. Изображение швов сварных соединений
От изображения шва или одиночной точки проводят линию-выноску, заканчивающуюся односторонней стрелкой (рис. 10, а, б).
На изображение сечения многопроходного шва допускается наносить контуры отдельных проходов, которые необходимо обозначать прописными буквами русского алфавита (рис. 10, в). Границы шва изображают сплошными основными линиями, а конструктивные элементы кромок в границах шва – сплошными тонкими линиями.
Шов сварного соединения, размеры конструктивных элементов которого стандартами не установлены (нестандартный шов), изображают с указанием размеров конструктивных элементов, необходимых для выполнения шва по данному чертежу (рис. 10, г).
Условные обозначения швов сварных соединений.
Структура условного обозначения стандартного шва или одиночной сварной точки приведена на рис. 10. Ниже приведены номера некоторых стандартов на типы и конструктивные элементы швов сварных соединений для различных видов сварки: ГОСТ 8713-79 «Сварка под флюсом. Соединения сварные»; ГОСТ 5264-80 «Ручная дуговая сварка. Соединения сварные»; ГОСТ 14771-76 «Дуговая сварка в защитном газе. Соединения сварные»; ГОСТ 15164-79 «Электрошлаковая сварка. Соединения сварные».
Этими стандартами в зависимости от толщины металла устанавливаются формы поперечного сечения и конструктивные элементы подготовленных кромок и выполненных швов, которым присваивают условные буквенно-цифровые обозначения.
Для обозначения сварных швов используют также вспомогательные знаки (табл. 1).
Таблица 1
Вспомогательные знаки для условного обозначения сварных швов
Если линия-выноска проведена от изображения шва с лицевой стороны, то условное обозначение шва наносят на полке линии-выноски, если с оборотной - то под полкой.
На рис. 11 показано условное обозначение шва углового соединения под тупым углом (ГОСТ 11533-75) без скоса кромок (У2), двухстороннего, выполненного автоматической сваркой под флюсом с предварительным наложением подварочного шва (Апш) по замкнутой линии.
Рис. 11. Форма поперечного сечения шва углового соединения (а) и условные обозначения шва с лицевой (б) и оборотной (в) стороны
Вопрос 2. Колебательные движения электродов (назначение, разновидности).
Для образования сварного шва электроду придается сложное движение в трех направлениях.
Первое движение - это поступательное движение электрода по направлению его оси. Оно производится со скоростью плавления электрода и обеспечивает поддержание определенной длины дуги.
Второе движение электрода направлено вдоль оси шва и производится со скоростью сварки.
В результате этих двух движений образуется узкий, шириной не более 1,5 диаметров электрода, так называемый ниточный шов. Такой шов применяется при сварке тонкого металла, а также при наложении первого шва при многослойной (многопроходной) сварке.
Третье движение - это колебание конца электрода поперек шва, которое необходимо для образования валика определенной ширины, хорошего провара кромок и замедления остывания сварочной ванны. Колебательные движения электрода поперек шва (рис. 12) могут быть различными и определяются формой, размером и положением шва в пространстве.
Рис. 12. Колебательные движения электрода поперек шва:
1,2,3 - для равномерного прогрева сварочной ванны; 4 - для усиленного прогрева корня шва; 5,6 - для усиленного прогрева кромок
3. Задача. Назовите и напишите формулу, по которой определяется сила сварочного тока.
Сила сварочного тока определяется по формуле:
I=k∙Dэл или I=(20+6Dэл)Dэл,
где k - коэффициент пропорциональности, зависящий от диаметра и типа электрода, А/мм;
Dэл - диаметр электрода, мм.
Билет № 28
Вопрос 1. Подготовка металла под сварку.
Перед сваркой после подбора металла по размерам и маркам стали необходимо выполнить следующие операции:
• правку;
• резку;
• обработку кромок и очистку под сварку.
Кромки подготавливают термическими и механическими способами.
В зависимости от толщины свариваемого металла его сварку можно вести как без разделки кромок, так и с разделкой. Разделка кромок металла начинается с 5 мм.
Существуют определенные геометрические параметры разделки кромок (рис. 13).
Обязательно в процессе сварки делают зазор b для проплавления металла на всю его толщину. Его размеры 0,5-5 мм, в зависимости от толщины свариваемого металла.
Притупление кромок с необходимо для формирования корня шва, и для того, чтобы не проплавить тонкий металл. Его размеры 2-2,5 мм.
Рис. 13. Подготовка металла под сварку
β - угол скоса кромки (15-45°);
S и S1 - толщина металла.
Разделка кромок может быть различна в зависимости от толщины металла (рис. 14).
Рис. 14. Примеры подготовки кромок:
I - высота отбортовки; R - радиус закруглений; β - угол скоса кромок; α - угол разделки кромок; S и S1 - толщина металла
Вопрос 2. Сварочные горелки (назначение, классификация, устройство, маркировка, подготовка к работе, требования техники безопасности).
Сварочная горелка служит для смешивания горючего газа или паров горючей жидкости с кислородом и получения сварочного пламени.
Сварочные горелки подразделяются следующим образом:
• по способу подачи горючего газа и кислорода в смесительную камеру - инжекторные и безынжекторные;
• по роду применяемого горючего газа - ацетиленовые, для газов-заменителей, для жидких горючих и водородные;
• по назначению - универсальные (сварка, резка, пайка, наплавка) и специализированные (выполнение одной операции).
Инжекторная горелка (рис. 15) - эта такая горелка, в которой подача горючего газа в смесительную камеру осуществляется за счет подсоса его струей кислорода, вытекающего с большой скоростью из отверстия сопла. Этот процесс подсоса газа более низкого давления струей кислорода, подводимого с более высоким давлением, называется инжекцией, а горелки данного типа - инжекторными.
Рис. 15. Конструкция инжекторной сварочной горелки:
1 - мундштук; 2 - сменный наконечник; 3 - смесительная камера; 4 - сопло инжектора; 5 - кислородный вентиль; 6 - кислородный ниппель; 7 - ацетиленовый вентиль; 8 - ацетиленовый ниппель
Для нормальной работы инжекторных горелок необходимо, чтобы давление кислорода было 0,15-0,5 МПа, а давление ацетилена значительно ниже - 0,001-0,12 МПа.
Принцип действия ее заключается в следующем. Кислород из баллона под рабочим давлением через ниппель, трубку и вентиль 5 поступает в сопло инжектора 4. Выходя из сопла инжектора с большой скоростью, кислород создает разряжение в ацетиленовом канале, в результате этого ацетилен, проходя через ниппель 6, трубку и вентиль 7, подсасывается в смесительную камеру 3.
В этой камере кислород, смешиваясь с горючим газом, образует горючую смесь. Горючая смесь, выходя через мундштук 1, поджигается и, сгорая, образует сварочное пламя. Подача газов в горелку регулируется кислородным вентилем 5 и ацетиленовым 7, расположенными на корпусе горелки. Сменные наконечники 2 подсоединяются к корпусу горелки накидной гайкой.
Безынжекторная горелка - это такая горелка, в которой горючий газ и подогревающий кислород подаются примерно под одинаковым давлением 0,05-0,1 МПа. В них отсутствует инжектор, который заменен простым смесительным соплом, ввертываемым в трубку наконечника горелки.
Правила обращения с горелками:
1. Не допускается эксплуатация неисправных горелок, так как это может привести к взрывам и пожарам, а также ожогам газосварщика.
2. Исправная горелка дает нормальное и устойчивое свариваемое пламя.
3. Для проверки инжектора горелки к кислородному ниппелю подсоединяют рукав от кислородного редуктора, а к корпусу горелки - наконечник. Наконечник затягивают ключом, открывают ацетиленовый вентиль и кислородным редуктором устанавливают необходимое давление кислорода соответственно номеру наконечника.
Пускают кислород в горелку, открывая кислородный вентиль. Кислород, проходя через инжектор, создает разрежение в ацетиленовых каналах и ацетиленовом ниппеле, которое можно обнаружить, приставляя палец руки к ацетиленовому ниппелю.
При наличии разряжения палец будет присасываться к ниппелю. При отсутствии разряжения необходимо закрыть кислородный вентиль, отвернуть наконечник, вывернуть инжектор и проверить, не засорено ли его отверстие.
При засорении его необходимо прочистить, при этом надо проверить также отверстия смесительной камеры и мундштука. Убедившись в их исправности, повторяют испытание на подсос (разрежение).
4. Величина подсоса зависит от зазора между концом инжектора и входом в смесительную камеру. Если зазор мал, то разрежение в ацетиленовых каналах будет недостаточным, в этом случае следует несколько вывернуть инжектор из смесительной камеры.
5. Вначале немного открывают кислородный вентиль горелки, создавая тем самым разрежение в ацетиленовых каналах. Затем открывают ацетиленовый вентиль и зажигают горючую смесь.
6. Пламя регулируют ацетиленовым вентилем при полностью открытом кислородном.
7. При хлопках сначала перекрывают ацетиленовый, а потом кислородный вентили.
8. Причины хлопков:
• сильный перегрев горелки;
• засорение мундштука горелки;
• если скорость истечения горючей смеси станет меньше скорости ее сгорания, то пламя проникнет в канал мундштука и произойдет обратный удар.
9. В этом случае горелку нужно погасить, охладить ее водой и прочистить мундштук иглой.
3. Задача. Быстро увеличивается начальное давление в ацетиленовом генераторе. Каковы действия сварщика в данной ситуации?
Необходимо произвести принудительный сброс давления через предохранительный клапан и сброс газа через горелку, открыв ацетиленовый вентиль.
Билет № 29
Вопрос 1. Оборудование и классификация сварочного поста электросварщика и газосварщика.
Сварочным постом называют рабочее место сварщика, оборудованное соответствующей аппаратурой и приспособлениями.
Организация рабочего места электросварщика.
Сварочные посты в зависимости от рода применяемого тока и типа источника питания дуги делятся на следующее виды:
• постоянного тока с питанием от однопостового или многопостового сварочного преобразователя или сварочного выпрямителя;
• переменного тока с питанием от сварочного трансформатора.
Сварочные посты по месту расположения могут быть стационарные и передвижные.
Стационарные посты представляют собой открытые сверху кабины для сварки изделий небольших размеров. Каркас кабины металлический. Стены окрашены в светлые тона огнестойкой краской. Окраска стен в темные тона не рекомендуется, так как она плохо поглощает ультрафиолетовые лучи сварочной дуги. Высота сварочного стола 500-600 мм; крышка стола площадью 1 м2, которую изготавливают из листовой стали толщиной около 25 мм. К нижней части крышки или ножки стола приваривают стальной болт, служащий для крепления токопроводящего кабеля от источника тока и для заземления. У стола сбоку имеется два кармана для электродов разных марок. Под ногами у сварщика должен находиться резиновый коврик.
Передвижной пост применяется в случаях сварки изделия крупных форм и необходимости проведения сварки в нестандартных условиях.
Сварочный пост устроен следующим образом (рис. 16).
От сети 1 переменный ток напряжением 220 или 380 В через рубильник 2 подается к источнику питания - сварочному трансформатору 3, где ток трансформируется до напряжения 60-70 В, и по сварочным проводам 4 через зажим 5 и электрододержатель 6 подводится к изделию 7.
Сварочный пост комплектуется:
• источником питания;
• электрододержателем;
• сварочными проводами;
• зажимами для токопроводящего провода;
• сварочным щитком с защитными светофильтрами;
• различными зачистными и мерительными инструментами.
Рис. 16. Стационарный сварочный пост
Электрододержатель - приспособление для закрепления электрода и подведения к нему тока. Среди всего многообразия применяемых электрододержателей наиболее безопасными являются пружинные, изготавливаемые по требованиям и классификации ГОСТ 14651-78Е: I типа - для тока 125 А; II типа – для тока 125-315 А; III типа - для тока 315-500 А. Электрододержатели выдерживают без ремонта 8-10 тысяч зажимов. Время замены электрода не превышает 3-4 с. Для ручной дуговой сварки существует несколько типов электрододержателей (рис. 17).
Щитки сварочные изготавливаются двух типов: ручные и головные из легких негорючих материалов по ГОСТу 12.4.035-78. Масса щитка не должна превышать 0,50 кг.
Защитные светофильтры (затемненные стекла), предназначенные для защиты глаз от излучения дуги, брызг металла и шлака, изготавливаются 13 классов или номеров по ГОСТу 12.4.080-79. Номер светофильтра подбирается в зависимости от силы сварочного тока и индивидуальных особенностей зрения сварщика (табл. 2).
Рис. 17. Типы электрододержателей
Таблица 2
Классы светофильтров
Кабели и сварочные провода необходимы для подвода тока от источника питания к электрододержателю и изделию. Электрододержатели присоединяются к гибкому (многожильному) медному кабелю марки ПРГД или ПРГДО (ГОСТ 6731-77Е). Кабель сплетен из большого числа отожженных медных проволочек диаметром 0,18-0,20 мм. Применять провод длиной более 30 м не рекомендуется, так как это вызывает значительное падение напряжения в сварочной цепи.
Токоподводящий провод соединяется с изделием через специальные зажимы. В сварочном поворотном приспособлении должны быть предусмотрены специальные клеммы. Закрепление провода должно быть надежным. Самодельные удлинители токоподводящего провода в виде кусков или обрезков металла не допускаются.
Сварщики обеспечиваются средствами личной защиты, спецодеждой.
Одежда сварщика изготавливается из различных тканей, которые должны удовлетворять двум основным требованиям:
• наружная поверхность одежды должна быть огнестойкой и термостойкой;
• внутренняя (изнаночная) поверхность одежды должна быть влагопоглощающей.
Исходя из этих требований одежду для сварщиков - куртку и брюки - шьют из брезента, сукна, замши; иногда ткани комбинируют.
При выполнении сварочных работ сварщик пользуется традиционным инструментом: металлической щеткой для зачистки кромок и удаления шлака; молотком-шлакоотделителем для удаления шлаковой корки; зубилом; рулеткой металлической, угольником, чертилкой.
Организация рабочего места газосварщика.
Для газовой сварки сварочные посты бывают стационарными и передвижными. Наибольшее применение нашел в практике передвижной сварочный пост, оснащенный:
• ацетиленовым генератором, предназначенным для получения ацетилена разложением карбида кальция водой;
• кислородным баллоном для хранения кислорода;
• шлангами для подачи газа от баллона и генератора к сварочной горелке;
• сварочной горелкой для смешивания горючего газа или паров горючего газа кислородом.
В стационарных сварочных постах подача горючего газа и кислорода происходит по трубопроводу.
Вопрос 2. Режимы дуговой сварки (назначение, сущность, принцип выбора основных и дополнительных показателей).
Под режимом сварки понимается совокупность ряда факторов (параметров) сварочного процесса, обеспечивающих устойчивое горение дуги и получение сварных швов заданных размеров, формы и качества.
При ручной дуговой сварке покрытыми электродами различают основные и дополнительные параметры режима сварки.
К основным параметрам относят:
• диаметр электрода;
• силу сварочного тока;
• напряжение дуги;
• род и полярность сварочного тока.
Дополнительные параметры:
• тип и марка электрода;
• скорость сварки;
• положение шва в пространстве;
• вылет электрода;
• предварительный подогрев и последующую термическую обработку;
• колебательные движения концом электрода.
Ниже рассматривается влияние некоторых из перечисленных факторов (параметров) на процесс сварки, а также приводятся рекомендации по их выбору.
1. Диаметр электрода при сварке в нижнем положении шва устанавливается в зависимости от толщины свариваемого металла.
Выполнение вертикальных, горизонтальных и потолочных швов независимо от толщины свариваемого металла производится электродами небольшого диаметра (до 4 мм), так как при этом легче предупредить стекание жидкого металла и шлака сварочной ванны.
При многослойной сварке для лучшего провара корня шва первый шов заваривают электродом Ø 3-4 мм, а последующие - электродами большего диаметра.
При сварке металла разной толщины диаметр выбирается по наименьшей толщине металла.
2. Сила сварочного тока (А) устанавливается в зависимости от выбранного диаметра электрода. Для сварки в нижнем положении шва она может быть приближенно определена по формуле
I=kDэл или I=(20+6Dэл)Dэл,
где k - коэффициент пропорциональности, зависящий от диаметра и типа электрода, А/мм;
Dэл - диаметр электрода, мм.
При сварке на вертикальной плоскости ток уменьшается на 10-15%, а в потолочном положении - на 15-20% против выбранного для нижнего положения шва.
3. Род тока и полярность устанавливаются в зависимости от вида свариваемого металла и его толщины. При сварке постоянным током обратной полярности на электроде выделяется больше теплоты. Исходя из этого обратная полярность применяется при сварке тонкого металла, чтобы не прожечь его, и при сварке высоколегированных сталей во избежание их перегрева. При сварке обычных углеродистых сталей применяют переменный ток, являющийся более дешевым по сравнению с постоянным.
4. Для зажигания дугового разряда нужно иметь от источника питания напряжение 30-60 В, а для горения - 20-40 В.
3. Задача. Подобрать основные параметры сварки для металла толщиной 8 мм. Сварка в нижнем положении.
1. Выбор диаметра электрода.
Диаметр выбирают по толщине свариваемого металла. В данном случае необходимы электроды двух диаметров, так как шов многослойный.
Для выполнения корневого шва выбирают электрод диаметром 2 мм, а последующие слои выполняют электродами 4 мм.
2. Силу тока рассчитывают по формуле
I=(20+6Dэл)Dэл.
Для Ø 2 мм I=(20+6Dэл)Dэл=(20+6∙2)∙2=64 А.
Для Ø 4 мм I=(20+6Dэл)Dэл=(20+6∙4)∙4=176 А.
3. Принимают переменный ток.
4. Для зажигания дугового разряда нужно иметь от источника питания напряжение 30-60 В, а для горения - 20-40 В.
Билет № 30
Вопрос 1. Сварочная дуга (определение, физическая сущность, способы зажигания, условия устойчивого горения, строение, влияние длины дуги на производительность и качества шва, окончание шва).
Если случайно или намеренно разомкнуть электрическую цепь, то в месте разрыва цепи проскакивает электрическая искра. Это явление, представляющее собой прохождение электрического тока через воздух, носит название искрового разряда.
Сварочной дугой называют дугу, представляющую собой длительный устойчивый электрический разряд в газовой среде между электродом и изделием либо между электродами, отличающуюся большим количеством тепловой энергии и сильным световым излучением.
Сварочные дуги квалифицируют по следующим признакам:
• по среде, в которой происходит дуговой разряд; на воздухе - открытая дуга, под флюсом – закрытая дуга; в среде защитных газов;
• по роду применяемого электрического тока - постоянная, переменная;
• по типу электрода - плавящаяся, неплавящаяся;
• по длительности горения - непрерывная, импульсная дуга;
• по принципу работы - прямого действия, косвенная дуга, комбинированная или трехфазная.
Для сварки металлов наиболее широко используют сварочную дугу прямого действия, в которой одним электродом служит металлический стержень (плавящийся или неплавящийся электрод), а вторым – свариваемая деталь. К электродам подведен электрический ток - постоянный или переменный.
Теплота, выделяемая сварочной дугой, не вся переходит в сварной шов. Часть теплоты теряется бесполезно на нагрев окружающего воздуха, плавление электродного покрытия.
Мощность сварочной дуги Q зависит от сварочного тока I и напряжения дуги U:
Q=I∙U (Вт).
Дугу возбуждают двумя способами - касанием или чирканьем. В обоих случаях процесс возбуждения сварочной дуги начинается с короткого замыкания. При этом в точках контакта увеличивается плотность тока, выделяется большое количество теплоты, и металл плавится. Затем электрод отводят, разрядный промежуток заполняется нагретыми частицами паров металла, и начинается горение дуги.
При отводе электрода от изделия (после короткого замыкания и мгновенного расплавления металла) жидкий мостик металла вначале растягивается, сечение его уменьшается, температура металла повышается, а затем жидкий мостик металла разрывается (рис. 18). При этом происходит быстрое испарение металла, и разрядный промежуток заполняется нагретыми ионизированными частицами паров металла, электродного покрытия и воздуха - возникает сварочная дуга.
Рис. 18. Схема возбуждения электрической дуги:
I - короткое замыкание; II - образование жидкого металла; III - образование шейки; IV - возникновение дуги.
1 - электрод; 2 - основной металл; 3 - сварочная дуга
Для повышения устойчивости горения сварочной дуги в электродное покрытие или в защитный флюс вводят элементы (калий, натрий, барий и др.), которые повышают степень ионизации и, следовательно, стабилизации сварочной дуги.
Сварочную дугу можно возбудить без касания электродом свариваемого изделия. Для этого нужно в сварочную цепь параллельно включить источник тока высокого напряжения и высокой частоты (осциллятор). При этом для возбуждения дуги достаточно приблизить конец электрода на расстояние 2-3 мм к поверхности изделия.
Дуговой промежуток подразделяется на три основные области (рис. 19):
• катодную;
• анодную;
• столб дуги.
Рис. 19. Строение электрической дуги и распределение напряжения на ее участках:
1 - катодное пятно; 2 - столб дуги; 3 - анодное пятно
Катодное пятно является источником потока свободных электронов. Температура его для стальных электродов достигает 2400-2600°С. В катодном пятне выделяется около 38% общей теплоты дуги.
Столб дуги представляет собой проводник электрического тока. В нем свободные электроны и отрицательно заряженные ионы движутся к аноду, а положительно заряженные ионы - к катоду. В целом столб дуги не имеет заряда. Он нейтрален, так как в каждом сечении столба одновременно находятся равные количества противоположно заряженных частиц.
В столбе дуги выделяется около 20% общей теплоты дуги. Температура столба дуги зависит от силы сварочного тока и достигает в ее центре 6000-7000°С и более. Температура капли на конце стального электрода приблизительно равна 2150°С, а при перелете ее через дуговой промежуток - 2350°С.
В среднем температура сварочной ванны составляет 1770°С.
Анодное пятно является местом входа и нейтрализации свободных электронов. Оно имеет примерно такую же температуру, как и катодное пятно, но в результате бомбардировки электронами на нем выделяется больше теплоты (примерно 42%), чем на катодном.
Малыми кружочками обозначены электроны, а большими - положительно и отрицательно заряженные ионы.
При работе на постоянном токе возможна прямая и обратная дуга.
При прямой полярности «+» на изделии «-» на электроде. При обратной полярности наоборот. При питании сварочной дуги постоянным током обратной полярности катодное и анодное пятна поменяются местами, т. е. катодом будет изделие, а анодом - электрод.
При переменном токе эта смена будет происходить 100 раз в секунду, поэтому дуга на переменном токе горит менее устойчиво, чем на постоянном. При сварке на переменном токе количество теплоты, выделяющиеся на электроде и изделии, будет примерно одинаковым.
Различают по длине короткую и длинную дугу.
Длиной дуги называют расстояние от конца электрода до дна кратера на поверхности металла.
Кратером называют углубление на поверхности металла в результате давления на него столба дуги.
Длина дуги определяется диаметром электрода.
Короткой называется дуга, длина которой меньше или равна диаметру электрода. Ее размеры 2 - 4 мм.
Длинная дуга та, которая больше или равна диаметру электрода.
Короткой дугой сваривают, длинной - режут металл.
Чтобы избежать кратера, применяют следующие способы:
• начинают и оканчивают шов на основном металле;
• постепенно удлиняют сварочную дугу и резко ее обрывают отводом в сторону.
В процессе горения дуги жидкий металл с конца электрода переходит в сварочную ванну в виде отдельных капель (капельный способ) и при полуавтоматической сварке струйно.
Перенос капель осуществляется под действием:
• силы тяжести;
• силы поверхностного натяжения;
• электромагнитных сил.
Характер капель зависит от силы сварочного тока. С увеличением силы тока размер капель уменьшается, а число их возрастает.
С уменьшением силы тока размер капли растет и в единицу времени капель становится меньше. Именно это свойство переноса металла и уменьшение силы тока, а также максимально короткая дуга позволяют вести сварку в вертикальном положении.
Влияние магнитных полей на дугу. Сварочная дуга является гибкой газовой вставкой между электродом и изделием и, как всякий проводник с током, взаимодействует с магнитным полем.
Отклонение столба дуги под действием магнитного поля, наблюдаемое в основном при сварке постоянным током, называется магнитным дутьем (рис. 20). Возникновение его объясняется тем, что в местах изменения направления тока создаются различные напряженности магнитного поля. Это приводит к отклонению дуги в сторону, противоположную большей напряженности.
При сварке переменным током, в связи с тем, что полярность меняется с частотой тока, это явление проявляется значительно слабее.
Магнитное дутье также имеет место при сварке вблизи ферромагнитных масс (железо и сталь). Дуга в этом случае отклоняется в сторону этих масс.
Возникновение магнитного дутья вызывает непровары и ухудшает внешний вид шва.
Рис. 20. Влияние магнитных полей и ферромагнитных масс на сварочную дугу:
а - нормальное положение дуги; б - отклонение дуги под влиянием неравномерной напряженности магнитного поля; в - отклонение дуги под влиянием ферромагнитных масс; Н1 и Н2 - напряженности магнитного поля
Устранить его можно:
• изменением места токоподвода и угла наклона электрода;
• временным размещением дополнительного ферромагнитного материала, создающего симметричное магнитное поле;
• заменой постоянного тока переменным.
Вопрос 2. Технология выполнения швов различной протяженности.
Все сварные швы в зависимости от их длины условно разбивают на три группы:
• короткие - до 250 мм;
• средней длины - от 250 до 1000 мм;
• длинные - от 1000 мм и более.
Короткие швы выполняют «на проход» в одном направлении, т. е. при движении электрода от начала шва к концу (рис. 21, а).
При выполнении швов средней длины и длинных возможно коробление изделий. Чтобы избежать этого, швы средней длины выполняют «на проход» от середины к концам (рис. 21, б) или обратноступенчатым способом (рис. 21, в), сущность которого состоит в том, что весь шов разбивают на участки длиной 100-350 мм с таким расчетом, чтобы каждый из них мог быть выполнен целым числом электродов (двумя, тремя и т. д.). При этом переход от участка к участку совмещается со сменой электрода. Каждый участок заваривается в направлении, обратном общему направлению сварки, а последний всегда заваривается «на выход».
Длинные швы выполняют от середины к концам обратноступенчатым способом (рис. 21, г). В данном случае возможно организовать работу одновременно двух сварщиков.
Рис. 21. Выполнение швов различной длины:
1-7 - последовательность наложения швов
3. Задача. Назовите цвета баллонов, в которые окрашиваются защитные и горючие газы.
Защитный газ:
Кислород - голубой.
Аргон чистый - серый.
Водород - зеленый.
Углекислота - черный.
Гелий — коричневый.
Горючий газ:
Ацетилен - белый.
Пропан, бутан, природный газ - красный.
ПЕРЕЧЕНЬ ПРИМЕРНЫХ ДОПОЛНИТЕЛЬНЫХ ВОПРОСОВ, ПРЕДЛАГАЕМЫХ НА ЭКЗАМЕНЕ
1. Назвать источники питания, их классификацию, преимущества и недостатки.
2. Устройство и регулировка трансформатора.
3. Устройство ацетиленового генератора.
4. Регулировка давления в ацетиленовом генераторе.
5. Устройство горелки.
6. Что такое «инжектор»? Объясните принцип его работы.
7. В чем отличие инжекторных горелок от безынжекторных?
8. Как проверить работу инжектора горелки?
9. Принцип работы газового редуктора.
10. Как отличить по внешним признакам редуктор для кислорода и ацетилена?
11. Требования техники безопасности при работе с генератором, горелкой, редуктором.
12. Можно ли, глядя на редуктор, определить давление в газовом баллоне?
13. Техника безопасности при работе с баллонами и цвета, в которые окрашивают баллоны для газов.
14. Почему при эксплуатации баллона газ используют не весь, а оставляют в нем остаточное давление?
15. Назначение покрытия на электроде.
16. Виды покрытия, их состав, преимущества и недостатки, обозначение.
17. Назначение непокрытых электродов.
18. Назначение флюсов.
19. Назвать самый распространенный флюс, используемый в практике.
20. Назначение защитных газов и их классификация
21. Что значит выбрать режим сварки?
22. Перечислить основные параметры режима сварки.
23. Перечислить дополнительные режимы сварки.
24. Какая зависимость существует между силой тока и положением в пространстве?
25. Какая зависимость существует между силой тока и напряжением?
26. Что называется магнитным дутьем? Как его избежать?
27. Назовите способы выполнения вертикальных швов. Какой наиболее часто применяется и почему?
28. Назначение зазора при сварке.
29. Правила выбора электродов при многослойной сварке.
30. Назначение корневого шва и правило его выполнения.
31. Показать положение электрода при выполнении сварочного шва в нижнем положении.
32. Назвать угол наклона электрода при выполнении сварки в различных пространственных положениях.
33. В чем заключается обратноступенчатый способ сварки? Нарисовать его схему.
34. Способы сварки швов длиной 250 мм. Нарисовать схему.
35. Способы сварки швов длиной 1000 мм. Нарисовать схему.
36. Как сварить изделие, сварочный шов которого больше метра? Нарисовать схему.
37. Перечислить способы заполнения шва по сечению, их назначение.
38. Последовательность включения сварочной горелки.
39. Назвать размеры используемого карбида кальция, дать обоснования своему ответу.
40. Перечислить причины возникновения деформаций при сварке.
41. Определение деформации.
42. Виды деформаций.
43. Назвать способы борьбы с деформациями.
44. Что такое «катет» сварочного шва?
45. Показать последовательность выполнения углового шва.
46. Зачем простукивают металл в околошовной зоне после сварки?
47. Что такое «свариваемость металла» и чем она определяется?
48. Влияние углерода на свариваемость металла.
49. Влияние серы и фосфора на качество сварного шва.
50. Режимы газовой сварки.
51. По каким параметрам выбирается диаметр присадочной проволоки и требования к ней?
52. Перечислить высокопроизводительные способы сварки.
53.Что называется сталью и чугуном?
54. Назвать способы сварки цветных металлов.
55. Перечислите условия разрезаемости металла.
56. Основные характеристики подогревающего пламени.
57. Основные характеристики режущего пламени.
58. Назовите виды пламени и структуру пламени.
59. Какой зоной пламени ведут сварку, почему?
60. Почему для газовой сварки наиболее широкое применение нашел ацетилен?
61. Перечислить методы контроля сварных швов.
62. В чем заключается метод керосиновых проб?
63. В чем отличие гидравлического способа испытания качества швов от способа давлением?
64. Перечислить способы сварки труб. От каких параметров они зависят?
65. Нарисовать схему поворотных способов сварки труб.
66. Нарисовать схему неповоротного способа сварки труб.
67. Сколько слоев шва выполняют при дуговой и газовой сварке труб?
68. Что такое «прихватки» и зачем они нужны?
69. Последовательность сварки ферм.
70. Нарисовать виды колебательных движений и объяснить их назначение.
Задачи к экзамену
1. Задача. Объясните и покажите, как проверяют работу инжектора горелки перед началом работы.
2. Задача. Объясните причину и ваши действия в том случае, если при зажигании дуги она прилипает к металлу.
3. Задача. Объясните, почему для сварки ответственных конструкций преимущественно применяют источник постоянного тока.
4. Задача. Назовите и напишите формулу, по которой определяется сила сварочного тока.
5. Задача. Быстро увеличивается начальное давление в ацетиленовом генераторе. Каковы действия сварщика в данной ситуации?
6. Задача. Подобрать основные параметры сварки для металла толщиной 8 мм. Сварка в нижнем положении.
7. Задача. Назовите цвета баллонов, в которые окрашиваются защитные и горючие газы.
8. Задача. Объясните влияние серы и фосфора на качество сварного шва.
9. Задача. Объясните назначение покрытия на плавящихся электродах.
10. Задача. Прочитайте условное обозначение электрода
11. Задача. Из предложенных марок сталей выберите, которые свариваются хорошо, удовлетворительно, ограниченно, плохо. Обоснуйте свой выбор: БСт1кп; сталь 10; сталь 35; ВСт5пс; сталь 65; У7.
12. Задача. Для сварки дан металл толщиной 8 мм. Объясните ваши действия по подготовке кромок металла к сварке.
13. Задача. Расшифруйте условное обозначение электродов на этикетке
14. Задача. Объясните ваши действия по окончании отбора газа из баллона.
15. Задача. Перед вами несколько редукторов. Объясните, как определить по внешнему виду, для какого газа они предназначены.
16. . Задача. Нужно, используя газовую сварку, соединить трубы диаметром 45 мм, толщиной стенки 3 мм. Назовите диаметр проволоки, количество слоев сварки.
17. Задача. Назовите максимально допустимое рабочее давление, которое может быть при работе с кислородным баллоном, ацетиленовым баллоном, ацетиленовым переносным генератором.
18. Задача. По условному обозначению на стволах горелок Г1, Г2, ГЗ, Г4 охарактеризуйте их, расшифровав это обозначение.
19. Задача. Назовите ваши действия в случае обратного удара пламени при работе с ацетиленовым генератором при сварке металла.
20. Задача. Назовите и схематично изобразите способ сварки листовой конструкции длиной 1300 мм.
21. Задача. Перечислите зоны газового пламени. Назовите, какой зоной производят сварочные работы. Обоснуйте свой ответ.
22. Задача. Перечислите зоны газового пламени. Назовите, какой зоной производят сварочные работы. Обоснуйте свой ответ.
23. Задача. Объясните, что такое сталь и чугун? В чем их отличие?
Дата добавления: 2020-11-23; просмотров: 138; Мы поможем в написании вашей работы! |
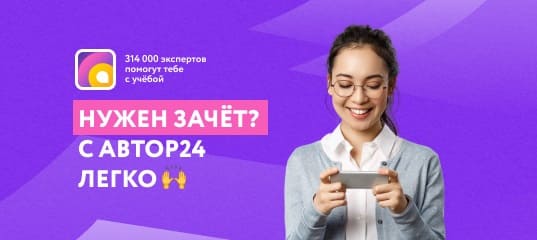
Мы поможем в написании ваших работ!