Изучение оборудования на предприятии для реализации размерной обработки
Цель работы: изучение технологических процессов ультразвуковой обработки материалов.
Задача: освоить метод ультразвуковой обработки на примере размерной обработки отверстий в металлических деталях.
Методика проведения работы
· Изучение основ технологии ультразвуковой обработки
· Изучение оборудования
· Выдача исходных данных
· Выбор оборудования
· Разработка операционного процесса
· Обработка детали
· Оценка точности и качества
Основы технологии ультразвуковой обработки
Ультразвуковая обработка материалов (УЗО) является разновидностью механической обработки. УЗО основано на использовании физического явления магнитострикции, т.е. способности ферромагнитных материалов и сплавов изменять размеры поперечного сечения и длину сердечника в переменном магнитном поле.
Эффектом магнитострикции обладают никель, железокобальтовые сплавы (пермендюр), железоалюминиевые сплавы (альфер), ферриты и другие материалы.
При возникновении электромагнитного поля с ультразвуковой частотой 16-30 кГц. Амплитуда колебаний сердечника составляет 5-10 мкм. Для увеличения амплитуды колебаний к сердечнику крепят длинный тонкий стержень-концентратор. Этот стержень является резонансным волноводом переменного поперечного сечения.
Наличие такого концентратора позволяет получить амплитуду колебаний торца сердечника до 40-60 мкм. К стержню крепят рабочий инструмент – пуансон.
|
|
Заготовки обрабатывают в ванне, заполненной суспензией, состоящей из воды и абразивного материала. Из абразивных материалов чаще используют карбиды бора и кремния, электрокорунд.
Колебательные движения пуансона передаются абразивным зернам, получающим значительные ускорения в направлении обрабатываемой поверхности заготовки. Ударяясь о поверхность обрабатываемого материала, абразивные зерна скалывают его микрочастицы. Большое число одновременно ударяющихся абразивных зерен, а также высокая частота повторения ударов (до 30 тыс. раз в сек) обуславливают интенсивный съем материала.
Кавитационные явления в жидкости способствуют интенсивному перемешиванию абразивных зерен под инструментом, замене изношенных зерен новыми, а также разрушению обрабатываемого материала. Типовая схема установки для получения отверстий в деталях из хрупкого материала представлена на рис. 1.
1 – ультразвуковой генератор (УЗГ);
2 – магнитострикционный
преобразователь;
3 – концентратор;
4 – инструмент;
5 – ванна;
6 – заготовка;
7 – кожух
Рис. 1. Схема установки для ультразвуковой обработки
Для возбуждения колебаний сердечника магнитострикционного преобразователя 2 служит ультразвуковой генератор (УЗГ) 1. Магнитострикционный преобразователь смонтирован в кожухе 7, сквозь который прокачивают воду для охлаждения сердечника. Упругие колебания от магнитострикционного преобразователя усиливаются концентратором 3, на конце которого закреплен инструмент 4, оптимальное значение упругих колебаний инструмента составляет 30 – 100 мкм. Заготовка 6 находится в ванне 5 с абразивной суспензией, состоящей из воды и абразивного материала. Из абразивных материалов используют карбид бора, карбид кремния и электрокорунд. Зернистость выбирают в зависимости от свойств обрабатываемого материала, требуемой точности и шероховатости обрабатываемой поверхности. Процесс обработки заключается в том, что торец инструмента, колеблющийся с ультразвуковой частотой, ударяет по зернам абразива, лежащим на необрабатываемой поверхности, которые скалывают частицы материала заготовки. Для нормальной работы зазор между торцом инструмента и обрабатываемой поверхностью должен быть постоянным, что обеспечивается автоматической регулировкой подачи инструмента. Абразивную суспензию в зону обработки подают под давлением по патрубку насосом.
|
|
Ультразвуковым методом обрабатывают хрупкие твердые материалы: стекло, керамику, ферриты, ситаллы, кремний, кварц, драгоценные материалы, в том числе, алмазы, твердые сплавы, титановые сплавы, вольфрам. Этим методом получают глухие и сквозные отверстия любой формы, в поперечном сечении, канавки, пазы. Ультразвуковые методы используются в технологических целях для очистки поверхностей деталей от загрязнений, пайки алюминиевых проводов, сварки тонких проводов с проводящими пленками микросхем. Точность размеров при ультразвуковой обработке составляет 0,005…0,02 мм.
|
|
Основные достоинства ультразвуковой обработки: возможность получения акустической энергии различными техническими приемами; исключительная широта диапазона технологических применений ультразвука от размерной обработки твердых материалов до неразъемного соединения (сварка, пайка и т. п.) деталей или интенсификации химико-технологических и электрохимических процессов; сравнительная несложность эксплуатации промышленных установок; возможность автоматизации и механизации. Недостатки: повышенная стоимость акустической-энергии по сравнению с другими видами энергии; необходимость изготовления специальных установок и аппаратов для генерации ультразвуковых колебаний их передачи и распределения.
|
|
Изучение ультразвуковой обработки проводится на примере размерной обработки.
Изучение оборудования на предприятии для реализации размерной обработки
На предприятии, на котором выполнялась работа, имеются три ультразвуковых станка: 4Б772, 4770, 4772.
Станок 4Б772
Станок модели 4Б772 предназначен для обработки сложно контурных отверстий постоянного сечения и полостей сложной конфигурации в заготовках из конструкционных, нержавеющих, жаропрочных, магнитных инструментальных сталей и сплавов. На станке могут изготовляться методом прошивания отверстия и плоскости различной конфигурации. Станок оснащен самостоятельным генератором ультразвуковых колебаний УЗ М-1,5 мощностью 1,5 кВт. Станок обеспечивает шероховатость обработанной поверхности 7—9-го класса чистоты.
Таблица 1. Технические характеристики станка 4Б772
Класс точности станка по ГОСТ 8-82, (Н,П,В,А,С) | Н |
Длина рабочей поверхности стола, мм | 320 |
Габариты станка Длинна Ширина Высота (мм) | 1360х1060х2080 |
Масса | 1960 |
Мощность двигателя кВт | 15 |
Пределы частоты вращения шпинделя Min/Max об/мин | 10/1250 |
Число инструментов в магазине | 30 |
Станок 4770
Станок модели 4770 предназначен Для обработки фасонных отверстий (сквозных и глухих) и наружного контура в деталях повышенной твердости из высоко легированных сталей Для ультразвуковой и электрохимической обработки деталей из твердых и хрупких материалов (кварца, рубина, графита). Ультразвуковая обработка основана на размерном разрушении изделия зернами абразива при импульсном подводе к ним механической энергии.
Таблица 2. Технические характеристики станка 4770
Пределы частоты вращения шпинделя Min об/мин | 10 |
Пределы частоты вращения шпинделя Max об/мин | 500 |
Класс точности станка по ГОСТ 8-82, (Н,П,В,А,С) | Н |
Мощность двигателя кВт | 30.6 |
Число инструментов в магазине | 30 |
Габариты станка Длинна Ширина Высота (мм) | 500х380х650 |
Масса | 171 |
Длина рабочей поверхности стола, мм | 160 |
Ширина стола, мм | 125 |
Станок 4772
Станок предназначен для обработки твердых и хрупких материалов: стекла, кремния, кварца, германия, твердых сплавов и др. На станке могут изготовляться отверстия и полости различной конфигурации методом прошивания. Станок оснащен самостоятельным генератором ультразвуковых колебаний мощностью 1,5 квт.
Таблица 3. Технические характеристики станка 4772
Оптимальный диаметр прошиваемых отверстий (мм) | 30 |
Наибольший диаметр прошиваемых отверстий (мм) | 70 |
Наибольшая глубина прошиваемых отверстий (мм) | 30 |
Наибольший рабочий ход ультразвуковой головки (мм) | 50 |
Наибольшие размеры обрабатываемых изделий (длина X ширина X высота) (мм) | 200Х150Х180 |
Наибольшая скорость съема стекла при весовой концентрации карбида бора 120 в воде 50% и площади обработки 700 мм2 (мм3/мин) | 800 |
Частота колебаний вибратора (кГц) | 20—25 |
Рабочие размеры стола (длина X ширина) (мм) | 350X250 |
Наибольшее перемещение стола (мм): | |
Продольное | 100 |
Поперечное | 150 |
Вертикальное | 150 |
Габариты станка (длина X ширина X высота) (мм) | 560Х875XI870 |
Вес станка (кг) | 700 |
Дата добавления: 2020-11-15; просмотров: 59; Мы поможем в написании вашей работы! |
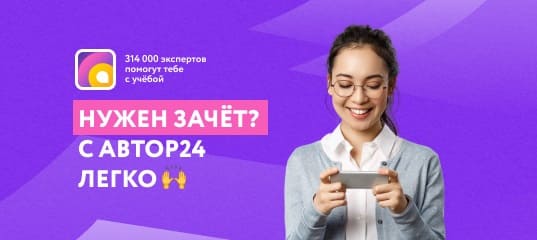
Мы поможем в написании ваших работ!