Б). Манометрические термометры.
Ю.В. Анискевич
ПРИБОРЫ И методы измерения
ТЕПЛОТЕХНИЧЕСКИХ ВЕЛИЧИН
2. Приборы и измерения давлений и сил. Классификация
2.1. Единицы измерения давлений
Давлением жидкости, газа или пара принято называть силу, действующую на какую-либо часть поверхности тела в направлении перпендикулярном этой поверхности .
В системе СИ единица давления - Паскаль Па=Н/м2.
В таблице 1 представлено соотношение между основными единицами давления.
Таблица 1.
Единицы измерения | Па | Бар | кгс/см2 | мм.вод.ст | мм.рт.ст |
1 Па | 1 | 10-5 | 1,0197∙10-5 | 0,10197 | 7,5006∙10-3 |
1 Бар | 105 | 1 | 1,0197 | 1,0197∙104 | 750,06 |
1 кгс/см2 | 9,8066∙104 | 0,98066 | 1 | 104 | 735,56 |
1 мм.вод.ст | 9,8066 | 0,98066∙10-4 | 10-4 | 1 | 7,3556∙10-2 |
1 мм.рт.ст | 133,32 | 1,3332∙10-3 | 1,3595∙10-3 | 13,595 | 1 |
При измерении давления различают: барометрическое ( ), избыточное (
) и абсолютное (
) давления:
.
Барометрическое (атмосферное) давление создается массой воздушного столба Земной атмосферы.
Барометр - прибор, измеряющий атмосферное давление.
Манометр – прибор, измеряющий избыточное давление. Показывает разность между абсолютным и атмосферным давлением.
Вакуумметр – прибор, измеряющий разряжение (давление ниже атмосферного).
С физической точки зрения давление идеального газа на твердую стенку есть результат столкновения молекул газа со стенкой. Связь между давлением, температурой и плотностью (ρ) идеального газа определяется уравнением состояния , где R – газовая постоянная.
|
|
Давление и температура полностью определяют термодинамическое состояние газа. Зная их можно определить плотность, вязкость, теплопроводность и другие физические величины, прямое измерение которых затруднено или невозможно.
2.2.1. Жидкостные приборы
Жидкостные приборы, основанные на гидростатическом принципе действия, широко применяют для измерения давления, разряжения и разности давлений. Они отличаются простотой устройства, невысокой стоимостью и относительно высокой точностью.
А). U – образный манометр.
Состоит из стеклянных измерительных трубок, соединенных внизу между собой и укрепленных на вертикальном основании. Между трубками помещена миллиметровая шкала с нулевой отметкой посередине.
Принцип действия этого прибора основан на непосредственном наблюдении разности уровней h рабочей жидкости (применяются ртуть и вода). При использовании стеклянных трубок малого диаметра вода из-за ее капиллярных свойств не применяется, а рабочим телом служит толуол или спирт.
|
|
Если одна из трубок манометра соединена с сосудом, где необходимо измерить давление, а другая остается соединенной с атмосферой, то величина измеряемого давления Р может быть определена по формуле , где Р – избыточное давление, h – разность уровней рабочей жидкости, ρ – плотность рабочей жидкости.
Если отсчет высоты столба по U – образному манометру проводят невооруженным глазом, то абсолютная погрешность оценивается в 1 мм при измерении высоты столба. Т.к. в U – образном манометре необходимо делать два отсчета, то в этом случае наибольшая абсолютная погрешность может достигать 2 мм. Для увеличения точности отсчета U – образные манометры снабжаются зеркальной шкалой, в этом случае при цене деления 1 мм отсчет высоты столба может быть произведен с погрешностью 0,25 мм. Если учесть, что измерений надо два, то общая погрешность будет не менее 0,5 мм.
Б). Чашечный манометр.
Он представляет собой U – образный манометр, у которого одно колено трубки выполнено в виде сосуда с сечением большим, чем у второго колена (рис. 2). Измеряемое давление, действуя на поверхность рабочей жидкости в широком сосуде, заставляет ее подниматься вверх по стеклянной измерительной трубке.
|
|
Рис. 2. Чашечный манометр.
Пусть под действием измеряемого давления жидкость в трубке поднимется на высоту , а в широком сосуде опустится на высоту
. Тогда высота столба, соответствующая действительному давлению равна
.
и
– площади измерительной и широкой трубок соответственно.
. Сопоставив два равенства получим:
,
где d и D– внутренние диаметры измерительной трубки и широкого сосуда.
Если ρ – плотность рабочей жидкости, то .
Основным достоинством чашечного манометра является то, что он позволяет проводить только один отсчет, т.к. разностью высот в широком сосуде можно пренебречь, или учесть с помощью введения поправки. Это вдвое повышает точность по сравнению с U – образным манометром.
Большинство чашечных приборов имеет отношение площадей . При d=4мм и D=80мм 42/802=0,25%. Следовательно, если желательно учесть изменение уровня жидкости в широком сосуде, то измеренную высоту столба жидкости в измерительной трубке надо увеличить на 0,25%.
Верхний предел измерения давления жидкостными манометрами ограничивается приемлемыми габаритными размерами приборов. На практике жидкостные приборы применяют для измерения давлений не свыше 0,2 МПа.
А). Манометры с трубчатой пружиной.
|
|
Трубчатая пружина представляет собой полую трубку плоскоовального или эллиптического сечения, согнутую по дуге окружности (рис. 4). Свободный конец пружины запаян и соединен через систему поводков со стрелкой, второй конец пружины впаян в основание манометра с ниппелем. Из измеряемого объема среда попадает в полость пружины, и она под действием давления этой среды меняет свою кривизну и через систему поводков поворачивает стрелку. Если в трубку подать газ под избыточным давлением, то кривизна трубки уменьшится, и она распрямится; при создании разряжения внутри трубки кривизна ее возрастает, и она скручивается. Перемещение свободного конца пружины а, следовательно, и угол поворота стрелки, практически будут пропорциональны созданному в ней давлению.
Рис. 4. Манометр с одновитковой трубчатой пружиной:
а – схема трубчатой пружины; б – эллиптическое поперечное сечение; в – плоскоовальное поперечное сечение.
Свойство изогнутой трубки некруглого сечения изменять величину изгиба при изменении давления в ее полости является следствием изменения формы сечения. Под действием давления внутри трубки эллиптическое или плоскоовальное сечение деформируясь, приближается к круговому сечению (малая ось эллипса или овала пружины увеличивается в размерах, а большая уменьшается). Примем допущение о том, что при деформации длина трубки остается постоянной, т.е. дуги и
сохраняют первоначальную длину.
Обозначим через значение соответствующих радиусов и угла закрутки пружины после деформации. Тогда согласно допущению
и
. Вычитая из первого уравнения второе, получим
. Но так как
и
представляют собой малые оси эллипса до и после деформации, то
. Обозначив малые оси эллипса до и после деформации через
и
, получим
, но поскольку
, то следовательно
. Таким образом под действием давления угол изгиба трубки уменьшается, т.е. трубка разгибается.
Если принять, что ,
, то получим
. Решая последнее уравнения относительно
получим:
.
Величина весьма мала по сравнению с
, поэтому можно записать:
. Из этого соотношения видно, что изменение угла изгиба трубки прямо пропорционально увеличению малой оси эллипса и первоначальному углу изгиба и обратно пропорционально величине малой оси эллипса. Следовательно, трубчатая пружина тем чувствительнее, чем меньше малая ось сечения и больше начальный угол изгиба трубки.
Трубчатая пружина может использоваться для измерения давления от 0,03 до 103 МПа, сами пружины изготавливают из латуни и стали. Недостаток – в упругом последействии. Конец пружины после снятия нагрузки приходит в начальное положение лишь через некоторый промежуток времени, а не сразу.
2.2.6. Особенности измерения давлений в движущихся средах
При изучении параметров движущихся жидкостей важное значение имеет различие между статическим и полным давлением.
Статическое давление в невозмущенном потоке определяется как давление, которое действовало бы на стенку тела, движущегося вместе с потоком, или на неподвижную стенку, расположенную параллельно вектору скорости потока.
Измеряется либо через отверстия в стенках каналов, либо с помощью введенных в поток заборных устройств – насадков. Наличие тонкого пограничного слоя в потоке газа с практически постоянным давлением поперек слоя не препятствует проникновению статического давления в приемные отверстия.
Практические ошибки, связанные с кривизной линий тока практически составляют ±1-3% при приемных отверстиях 0,5 – 1,5 мм в зависимости от диаметра канала и скорости. На точность измерений влияет качество выполнения формы отверстий: степень остроты кромки отверстия, угол наклона относительно перпендикуляра к касательной поверхности канала; каждая составляющая таких погрешностей может доходить до ±0,5 – 1,0%.
Применяются насадки двух типов:
Первого – имеют небольшую протяженность в направлении потока. Погрешность существенно зависит от чисел Re и М, а также отклонений положения приемных отверстий. Применяются, когда определяющим фактором являются малые поперечные размеры.
Второго – имеют вытянутые в направлении потока приемники. При движении вдоль приемника возмущенный поток успевает выровняться, местное давление становится равным статическому давлению набегающего потока. В этих зонах и располагаются приемные отверстия. Наибольшее применение в этой группе имеют Г – образные (типа приемника Прандтля) и дисковые.
Полное давление – давление адиабатически заторможенного потока, или давление, которое испытывает плоское тело, расположенное перпендикулярно потоку.
В потоке идеальной жидкости, движущейся с большими скоростями, давление торможения , статическое давление
и число М связаны зависимостью:
При малых значениях М это уравнение приближенно представляется в виде: .
Наибольшее расхождение между давлениями и
в случае несжимаемой вязкой жидкости вызывается изменением числа Re и формой приемника. При измерении сверхзвуковых потоков следует учитывать механические потери при прохождении потока через прямой скачек уплотнения и снижение скорости до дозвуковых значений. Потери полного давления в скачках уплотнения на скоростях до 1,25М составляют менее 1%.
Второй по значению фактор – скос потока относительно приемного отверстия. Чем больше приемное отверстие, тем чувствительность к скосу меньше. В крайнем случае, применяются экранированные насадки.
Третий – турбулентность. Влияние турбулентности невозмущенного потока на показания приемника в случаях дозвуковых потоков несжимаемой жидкости особенно существенно вблизи твердой поверхности. Оно может быть определено по формуле:
,
где – средняя величина статического давления в невозмущенном потоке,
- среднеквадратическое значение турбулентных пульсаций скорости.
4. Приборы измерения температур
4.1. Понятие температуры. Температурные шкалы.
Температурой называют величину, характеризующую тепловое состояние тела. Согласно кинетической теории температуру определяют как меру кинетической энергии поступательного движения молекул. Отсюда температура - это условная статистическая величина, прямо пропорциональная средней кинетической энергии молекул тела.
Из второго начала термодинамики понятие температуры характеризуется мерой приращения тепла, отведенного (или подведенного) от изолированной термодинамической системы в долях происходящего при этом изменения энтропии: .
Для газообразных тел, согласно кинетической теории, средняя энергия поступательного движения молекул газа связана с температурой выражением: , где k=1,38∙10-23 Дж/К – постоянная Больцмана.
В связи с исследованием высокотемпературной плазмы приходится сталкиваться с понятием электронной температуры, характеризующей поток электронов в плазме.
Возможность измерения температуры основывается на явлении теплового обмена между телами с разной степенью нагретости и на изменении физических свойств тел при их нагревании.
Принятая единица измерения температуры (1 градус) является по существу лишь мерой масштаба принятой температурной шкалы и процесс измерения температуры является определением положения на температурной шкале уровня измеренной температуры.
Температурная шкала – система последовательных числовых значений, соответствующих температурам.
Все предлагаемые эмпирические температурные шкалы (Цельсия, Реомюра, Фаренгейта) строились одинаковым путем: двум (по меньшей мере) постоянным точкам присваивались определенные числовые значения, и предполагалось, что видимое термометрическое свойство используемого в термометре вещества линейно связанно с температурой t: ,
где k – коэффициент пропорциональности; E – термометрическое свойство; D – постоянная.
Принимая для двух постоянных точек определенные значения температур, можно вычислить постоянные k, D и на этой основе построить температурную шкалу. При изменении температуры коэффициент k меняется, причем различно для разных термометрических веществ. Поэтому термометры, построенные на базе различных термометрических веществ с равномерной градусной шкалой, давали при температурах, отличающихся от температур постоянных точек, различные показания. Последние становились особенно заметными при высоких (много больших температуры кипения воды) и очень низких температурах.
Температурные шкалы, не зависящие от конкретных свойств термометрического вещества, называют термодинамическими.
А). Шкала Цельсия.
Шкала термометра между точкой таяния льда и точкой кипения воды при нормальном атмосферном давлении (760 мм рт. ст.) была разделена на 100 равных частей, считая за 00 точку таяния льда, а за 1000 точку кипения воды. В качестве рабочего тела принята ртуть.
Б). Шкалы Реомюра и Фаренгейта.
В шкале Фаренгейта. За реперные точки приняты точки плавления льда и кипения воды. При этом точка плавления льда обозначена за +320, а точка кипения воды за +2120 и промежуток между этими точками делится на 180 равных частей. В качестве рабочего тела принята ртуть. Связь между шкалой Цельсия и Фаренгейта: t(0F)=1,8t(0C)+32(0F).
В шкале Реомюра за основные реперные точки приняты точки плавления льда и кипения воды. При этом точка плавления льда обозначена за 00, а точка кипения воды за +800. В качестве рабочего тела принята смесь спирта с водой. Связь между шкалой Цельсия и Реомюра: t(0F)=0,8t(0C).
В). Термодинамическая шкала.
Не зависит от термометрического вещества. Была предложена Кельвином. В основе лежит использование термодинамического цикла Карно идеальной тепловой машины, КПД которой зависит только от термодинамической температуры. Шкала основана на одной реперной точке (0,010С) – равновесия воды (в твердой, жидкой и газообразной фазах). Ей приписано числовое значение 273,16К, нижней границей интервала шкалы принят абсолютный нуль (прекращается тепловое движение молекул). За единицу температуры принят 1 Кельвин (1К), равный 1/273,16 части термодинамической температуры тройной точки воды. Определяемая таким образом единица термодинамической шкалы 1К совпадает с величиной 10С, а переход от шкалы Цельсия к термодинамической шкале осуществляется по формуле: Т(К)=t(0C)+273,15.
Осуществить термодинамическую шкалу практически осень сложно. Поэтому обычно применяется международная практическая температурная шкала (МПТШ), которая совпадает с термодинамической с достижимой экспериментальной точностью.
4.2. Приборы измерения температуры
Существует две группы измерителей температуры по методу – контактные (термометры, терморезисторы, термопары, термокраски) и бесконтактные (пирометры, фотометры).
При измерении температуры контактным методом приходится в той или иной степени принимать во внимание особенности теплообмена между объектом, приемным преобразователем и внешней средой. Трудности создания приборов, основанных на бесконтактных методах, связаны с необходимостью определения излучательной способности объекта (реальной степени черноты), что во многих случаях невозможно сделать достаточно точно.
4.3. Контактные измерители температур
А). Термометры расширения.
Самые старые устройства для измерения температуры – жидкостные стеклянные термометры – используют термометрическое свойство теплового расширения тел. Действие термометров основано на различии коэффициентов теплового расширения термометрического вещества и оболочки, в которой она находится (термометрического стекла или реже кварца).
Показания жидкостно-стеклянного термометра зависят не только от изменения объема рабочей жидкости, но и от изменения объема стеклянного резервуара, поэтому для изготовления термометров применяются специальные сорта стекла с малым коэффициентом объемного расширения.
Жидкостный термометр состоит из стеклянных баллона 1, капиллярной трубки 3 и запасного резервуара 4 (рис. 12). Термометрическое вещество 2 заполняет баллон и частично капиллярную трубку. Свободное пространство в капиллярной трубке и в запасном резервуаре заполняется инертным газом или может находиться под вакуумом. Запасной резервуар или выступающая за верхним делением шкалы часть капиллярной трубки служит для предохранения термометра от порчи при чрезмерном перегреве.
Рис. 12. Жидкостный термометр расширения:
1 – баллон с рабочей жидкостью, 2 – рабочая жидкость, 3 – капиллярная трубка, 4- резервуар.
В качестве термометрического вещества чаще всего применяют химически чистую ртуть. Ртуть не смачивает стекла и остается жидкой в широком интервале температур. Ртутные термометры обладают наибольшей равномерностью шкалы, до 2000С шкала почти линейна. Допустимая погрешность не превышает одного деления шкалы. Кроме ртути в качестве термометрического вещества в стеклянных термометрах применяются метиловый и этиловый спирт, керосин, пентан, толуол, галлий, амальгама таллия. У таких термометров инерционность за счет большей теплоемкости выше, а точность за счет смачивания стекла ниже.
Основные достоинства стеклянных жидкостных термометров – простота употребления и достаточно высокая точность измерения даже для термометров серийного изготовления. К недостаткам стеклянных термометров можно отнести: плохую видимость шкалы (если не применять специальной увеличительной оптики) и невозможность автоматической записи показаний, передачи показаний на расстояние и ремонта.
Стеклянные жидкостные термометры имеют весьма широкое применение и выпускаются следующих основных разновидностей:
1. технические ртутные, с вложенной шкалой, с погружаемой в измеряемую среду нижней частью, прямые и угловые;
2. лабораторные ртутные, палочные или с вложенной шкалой, погружаемые в измеряемую среду до отсчитываемой температурной отметки, прямые, небольшого наружного диаметра;
3. жидкостные термометры (не ртутные);
4. повышенной точности и образцовые ртутные термометры;
5. электроконтактные ртутные термометры с вложенной шкалой, с впаянными в капиллярную трубку контактами для разрывания (или замыкания) столбиком ртути электрической цепи;
6. специальные термометры, в том числе максимальные (медицинские и другие), минимальные, метеорологические и другого назначения.
У лабораторных и других термометров, градуируемых и предназначенных для измерения при погружении в измеряемую среду до отсчитываемого деления, могут возникать систематические погрешности за счет выступающего столбика термометра. Если капиллярная трубка будет погружена в измеряемую среду не полностью, то температура выступающей части капиллярной трубки будет отличаться от температуры измеряемой среды, в результате возникнет погрешность измерения. Поправку в градусах на выступающий столбик в показания термометра можно внести по уравнению: ,
где - коэффициент видимого объемного теплового расширения термометрической жидкости в стекле
, t – действительная температура измеряемой среды 0C, tв.с. – температура выступающего столбика, измеренная с помощью вспомогательного термометра 0С, n – число градусов в выступающем столбике.
У термометров, предназначенных для работы с неполным погружением, может возникнуть аналогичная систематическая погрешность, если температура окружающей среды, а, следовательно, и выступающего столбика будут отличаться от его температуры при градуировке. Поправка, в этом случае будет ,
где - температура выступающего столбика при градуировке 0C (в первом приближении допустимо считать
),
- средняя температура выступающего столбика 0С.
Поправки могут иметь большие значения у термометров с органическими термометрическими жидкостями, для которых коэффициент примерно на порядок выше, чем у ртутных термометров.
Б). Манометрические термометры.
Действие манометрических термометров основано на использовании зависимости давления вещества при постоянном объеме от температуры. Замкнутая измерительная система манометрического термометра состоит из (рис. 13) из чувствительного элемента, воспринимающего температуру измеряемой среды, - металлического термобаллона 1, рабочего элемента манометра 2, измеряющего давление в системе, длинного соединительного металлического капилляра 3. При изменении температуры измеряемой среды давление в системе изменяется, в результате чего чувствительный элемент перемещает стрелку или перо по шкале манометра, отградуированного в градусах температуры. Манометрические термометры часто используют в системах автоматического регулирования температуры, как бесшкальные устройства информации (датчики).
Рис. 13. Манометрический термометр:
1 – термобаллон, 2 – манометр, 3 - капиляр.
Манометрические термометры подразделяют на три основных разновидности:
1. жидкостные, в которых вся измерительная система (термобаллон, манометр и соединительный капилляр) заполнены жидкостью;
2. конденсационные, в которых термобаллон заполнен частично жидкостью с низкой температурой кипения и частично – ее насыщенными парами, а соединительный капилляр и манометр – насыщенными парами жидкости или, чаще, специальной передаточной жидкостью;
3. газовые, в которых вся измерительная система заполнена инертным газом.
Достоинствами манометрических термометров являются сравнительная простота конструкции и применения, возможность дистанционного измерения температуры и возможность автоматической записи показаний. К недостаткам манометрических термометров относятся: относительно невысокая точность измерения (класс точности 1.6; 2.5; 4.0 и реже 1.0); небольшое расстояние дистанционной передачи показаний (не более 60 метров) и трудность ремонта при разгерметизации измерительной системы.
Манометрические термометры не имеют большого применения на тепловых электрических станциях. В промышленной теплоэнергетике они встречаются чаще, особенно в случаях, когда по условиям взрыво– или пожаробезопасности нельзя использовать электрические методы дистанционного измерения температуры.
Поверка показаний манометрических термометров производится теми же методами и средствами, что и стеклянных жидкостных.
Г). Термоэлектрические термометры (термопары).
Для измерения температуры в металлургии наиболее широкое распространение получили термоэлектрические термометры, работающие в интервале температур от -200 до +2500 0C и выше. Данный тип устройств характеризует высокая точность и надежность, возможность использования в системах автоматического контроля и регулирования параметра, в значительной мере определяющего ход технологического процесса в металлургических агрегатах.
Сущность термоэлектрического метода заключается в возникновении ЭДС в проводнике, концы которого имеют различную температуру (эффект Зеебека). Для того чтобы измерить возникшую ЭДС, ее сравнивают с ЭДС другого проводника, образующего с первым термоэлектрическую пару AB (рис. 15), в цепи которой потечет ток.
Рис. 15. Принципиальная схема термопары.
Результирующая термо-ЭДС цепи, состоящей из двух разных проводников A и B (однородных по длине), равна или
,
где и
- разности потенциалов проводников A и B соответственно при температурах t2 и t1, мВ.
Термо-ЭДС данной пары зависит только от температуры t1 и t2 и не зависит от размеров термоэлектродов (длины, диаметра), величин теплопроводности и удельного электросопротивления.
Спай термопары, помещаемый в измеряемую среду, называется рабочим (горячим). Термо – ЭДС меряется компенсационным методом – сведением тока в измерительной цепи к нулю, поэтому сопротивление термоэлектродов роли не играет, а их сечения могут быть малы. Отсюда вытекает одно из достоинств термопар – возможность измерения температуры в малых объемах.
Для увеличения чувствительности термоэлектрического метода измерения температуры в ряде случаев применяют термобатарею: несколько последовательно включенных термопар, рабочие концы которых находятся при температуре t2, свободные при известной и постоянной температуре t1 (термостатируют холодный спай).
Термоэлектрический термометр (ТТ) – это измерительный преобразователь, чувствительный элемент которого (термопара) расположен в специальной защитной арматуре, обеспечивающий защиту термоэлектродов от механических повреждений и воздействия измеряемой среды. На рис. 16 показана конструкция технического ТТ. Арматура включает защитный чехол 1, гладкий или с неподвижным штуцером 2, и головку 3, внутри которой расположено контактное устройство 4 с зажимами для соединения термоэлектродов 5 с проводами, идущими от измерительного прибора к термометру. Термоэлектроды по всей длине изолированы друг от друга и от защитной арматуры керамическими трубками (бусами) 6.
Рис. 16. Технический термоэлектрический термометр:
1 - защитный чехол, 2 – штуцер, 3 – крышка, 4 – контактное устройство, 5 – термоэлектроды,
6 - армированные бусы, 7 - чувствительный элемент.
Защитные чехлы выполняются из газонепроницаемых материалов, выдерживающих высокие температуры и агрессивное воздействие среды. При температурах до 10000С применяют металлические чехлы из углеродистой или нержавеющей стали, при более высоких температурах – керамические: фарфоровые, карбофраксовые, алундовые, из диборида циркония и т. п.
В качестве термоэлектродов используется проволока диаметром 0.5 мм (благородные металлы) и до 3 мм (неблагородные металлы). Спай на рабочем конце 7 термопары образуется сваркой, пайкой или скручиванием. Последний способ используется для вольфрам–рениевых и вольфрам–молибденовых термопар.
Термоэлектрические термометры выпускаются двух типов: погружаемые и поверхностные. Промышленность изготавливает устройства различных модификаций, отличающихся по назначению и условиям эксплуатации, по материалу защитного чехла, по способу установки термометра в точке измерения, по герметичности и защищенности от действия измеряемой среды, по устойчивости к механическим воздействиям, по степени тепловой инерционности и т. п.
В пределах измеряемых температур материал термопар не должен менять своих физических свойств, не окисляться, обладать высокой электропроводностью и малым температурным коэффициентом электросопротивления, для пары материалов величина термо–ЭДС должна быть достаточной для точных измерений и изменяться однозначно в зависимости от температуры (линейно).
По характеру применяемых материалов термопары можно разделить на три группы: из благородных металлов (для температур свыше 10000С и агрессивных сред), из неблагородных металлов и из металлических термоэлектродов в паре с неметаллическими.
Для измерения температур широко применяются ТТ со стандартной градуировкой (см. таблицу 4). В ряде случаев используют также ТТ с нестандартной градуировкой: медь–константановые, вольфрам–молибденовые (ТВР), некомпенсируемые и др. На рис. 17 приведены градуировочные кривые ряда термопар.
Таблица 4.
Сравнительные характеристики наиболее распространенных термопар.
Наименование и материал электродов. | Рабочий диапазон, 0С, 1000ч (100ч) | Чувствительность мВ (при t0С) | Допустимая среда. |
ТПП платинородий - платиновые 90%Pt+10%Rh – 100%Pt | -20 – 1300 (1600) | 2,31 (300) | Окислительная до 1300, 0С в восстановительной с чехлом. |
ТПР платинородий - платинородиевые 70%Pt+30%Rh-94%Pt+6%Rh | +300 – 1800 (1900) | Окислительная до 1300, 0С, в восстановительной с чехлом. | |
ТХА хромель-алюмелевые 90%Ni+10%Cr-95%Ni+5%Al,Si,Mn | -50 – 1000 (1300) | 12,21 (300) | Окислительная в восстановительной с чехлом. |
ТХК хромель-копелевые 90%NI+10%Cr – 56%Cu+44%Ni | -50 – 600 (800) | 23,1 (300) | Окислительная в восстановительной с чехлом. |
ТВР вольфрамрений - вольфрамрениевые 95%W+5%Re – 80%W+20%Re | 0 –2000 (2500) | 13 (2000) | Восстановительная, окислительная кратковременно |
НК-СА никель+кобальт – кремний+алюминий | +300 - 1000 | 20 (1000) | Окислительная и восстановительная. |
Допустимые погрешности для технических термопар типа ТПП при температуре до 3000С ±0,1 мВ, свыше 3000С - +_3∙10-5∙t мВ, где t – температура горячего спая термопары; для ТХК и ТХА при температуре до 3000С ±40С, а при температуре более 3000С ±1% от измеряемого значения термо ЭДС.
Криогенные температуры чаще всего измеряют термопарой медь–константан (100%Cu – 60%Cu+40%Ni) до –2700С или медь–копель – до –2000С.
В условиях длительной эксплуатации при высоких температурах и агрессивном воздействии сред появляется нестабильность градуировочной характеристики, которая является следствием ряда причин: загрязнения материалов термоэлектродов примесями из защитных чехлов, керамических изоляторов и атмосферы печи; испарения одного из компонентов сплава; взаимной диффузии через спай. Величина отклонения может быть значительной и резко увеличивается с ростом температуры и длительностью эксплуатации. Указанные обстоятельства необходимо учитывать при оценке точности измерения температуры в производственных условиях.
5. Приборы измерения количества и расхода
5.2. Расходомеры постоянного и переменного перепада давления
Одним из наиболее распространенных и изученных способов измерения расхода жидкостей, газов и пара является метод измерения расхода по перепаду давления в дроссельных устройствах. Последнее устанавливается в трубопроводе и создает в нем местное сужение, вследствие чего при протекании вещества повышается скорость в суженном сечении по сравнению со скоростью потока до сужения. Увеличение скорости, а, следовательно, и кинетической энергии в суженном сечении вызывают уменьшение потенциальной энергии потока в этом сечении. Соответственно статическое давление в суженном сечении будет меньше, чем в сечении до дроссельного устройства. Таким образом, при протекании вещества через дроссельное устройство создается перепад давления, зависящий от скорости потока и, следовательно, расхода жидкости. То есть, перепад давления ΔР в дроссельном устройстве, измеренный с помощью дифференциального манометра, может служить мерой расхода вещества. Численная же величина расхода может быть определена по перепаду давления расчетным путем. В качестве дроссельных устройств обычно применяют, диафрагмы, сопла и трубы Вентури.
Рис. 32. Характер потока и распределение давлений вблизи дроссельного устройства.
Характер потока и распределение давлений вблизи дроссельного устройства наглядно показаны на рис. 32. На рисунке показана диафрагма, которая представляет собой тонкий диск с отверстием круглого сечения, центр которого лежит на оси трубы. Сужение потока начинается до диафрагмы и на некотором расстоянии за диафрагмой поток достигает минимального сечения. Далее поток постепенно расширяется до полного сечения трубопровода. Сплошной линией представлена кривая, характеризующая распределение давления вдоль стенки трубопровода; кривая же, изображенная пунктирной линией, характеризует распределение давлений по оси трубопровода. Как видно из рисунка, давление за диафрагмой полностью не восстанавливается.
Значительная потеря давления при протекании вещества через диафрагму обусловлено главным образом внезапным расширением живого сечения струи после выхода потока из диафрагмы и наличием мертвых зон, заполненных вихреобразованиями, на что затрачивается значительная часть энергии. Изменение направления струек перед диафрагмой и сжатие струи после диафрагмы имеют незначительное влияние.
Улучшение характеристик точности может быть достигнуто применением двойных диафрагм.
Рис. 33. Профили сопел: А – сопло для m≤0,444; Б – для m>0,444
Сопло (рис. 33) отличается от диафрагмы тем, что при протекании вещества через него сужение струи со стороны входа частично происходит в пространстве, ограниченном профилированной частью сопла. Благодаря этому вихри перед соплом занимают меньшее место и потеря энергии соответственно меньше. Кроме того, профилированная и цилиндрическая части сопла подбираются обычно таким образом, чтобы при протекании через него вещества достигалось в достаточной степени полное сжатие струи; в этом случае площадь отверстия сопла может быть принята равной минимальному сечению струи. Кривая изменения давления имеет почти тот же характер, что и для диафрагмы.
Труба Вентури состоит из сужающейся части, аналогичной соплу, переходящей в короткий цилиндрический участок, и из расширяющейся части — диффузора. В этой форме дроссельного прибора благодаря плавному профилю сопла и в особенности наличия диффузора потеря давления δР наименьшая.
Все дроссельные устройства характеризуются модулем m. . Модуль может иметь значение для диафрагмы 0,05 – 0,7; для сопл – 0,05 – 0,65; для сопл Вентури 0,05 – 0,6
Главный недостаток расходомеров с сужающими устройствами – узкий рабочий диапазон каждого данного расходомера, что вызвано квадратичной зависимостью между расходом и перепадом давления. Отношение Qmax/Qmin не должно превышать 3 – 4, потому что с его увеличением резко возрастает погрешность измерения вблизи Qmin. Безвозвратные потери давления δР оцениваются разностью полных давлений, измеренных в сечениях 1–1 и 3–3.
Уравнение расхода для несжимаемой жидкости.
Предположим, что жидкость идеальна, скорости в сечениях 1 – 1 и 2 – 2 равны по всему сечению средней скорости и параллельны оси трубы, труба горизонтальна, тогда уравнение закона сохранения энергии имеет вид: .
Для случая несжимаемой жидкости ( ):
, (1)
где - абсолютные давления в сечениях 1–1 и 2–2; ρ – плотность жидкости;
– средние скорости в сечениях 1–1 и 2–2.
Из уравнения неразрывности следует:
.
Выразим через площадь дроссельного устройства F0:
, где
-коэффициент сужения струи. Тогда
. (2)
Совместное решение уравнений (1) и (2) дает следующее:
. (3)
Давления отнесены к сечениям 1-1 и 2-2, а в большинстве случаев давление измеряется в углах до и после сужающего устройства. Кроме того, в реальном потоке из-за вязкости и трения существуют потери энергии и скорости в различных точках течения. При переходе к действительным условиям вводят поправочный коэффициент
. Тогда уравнение (3) примет вид:
. (4)
Секундный массовый расход для несжимаемой жидкости:
,
А с учетом (4): ,
,
где - коэффициент расхода сужающего устройства.
Секундный объемный расход: ,
.
В случае измерения расхода сжимаемой жидкости (газа или пара) необходимо учесть изменение его плотности в связи с изменением давления. Считаем, что изменение состояния газа описывается уравнением адиабатического процесса: , или
, или
, где k – показатель адиабаты, С = const. С учетом этого проведя аналогичные преобразования, как и для несжимаемой жидкости, получим следующие выражения для секундных массовых и объемных расходов:
[кг/с], и
[м3/с],
где – поправочный множитель на расширение измеряемой среды.
Коэффициент расхода μ зависит от плотности вещества, его вязкости, скорости потока, площади сечения отверстия дроссельного устройства, площади самого трубопровода, шероховатости стенок трубопровода, все это можно представить в обобщенном виде: .
Для определения коэффициента расхода есть таблицы, выражающие зависимость , кроме того вводятся также поправки: k1 – на вязкость среды; k2 – на шероховатость стенок трубы; k3 – на остроту входной кромки у диафрагм (для сопл и труб Вентури k3=1). Все они затабулированы.
В случае измерения расхода газа при отношениях давлений равных или меньше критического есть возможность использовать критическую шайбу с одним замером давления перед шайбой Р1. При отношении давлений Р2/Р1 равных или меньших критического расхода газа через дроссельное устройство достигает своего максимума и остается постоянным. В этом случае расход рассчитывается по следующим формулам:
, [кг/с],
.
Расходомеры с суживающимися устройствами непригодны для измерения быстропеременных расходов, что связано с инерционностью процессов в измерителях перепада давления и соединительных магистралях.
8. Библиографический список
1. Теплотехнические измерения и приборы: учебник для вузов/ В. П. Преображенский. - 3-е изд., перераб.. - М.: Энергия, 1978. - 703 с.
2. Чистяков, С. Ф. Теплотехнические измерения и приборы: учебное пособие для вузов/ С. Ф. Чистяков, Д. В. Радун. - М.: Высш. шк., 1972. - 392 с.
3. Теплотехнические измерения и приборы: учебник для вузов/ Г. М. Иванова, Н. Д. Кузнецов, В. С. Чистяков. - М.: Энергоатомиздат, 1984. - 232 с.
4. Измерения в промышленности: справочное издание: в 3 кн.: пер. с нем./ Ред. П. Профос, Д. И. Агейкин. - М.: Металлургия, 1990 .
5. Кремлевский, П.П. Расходомеры и счётчики количества веществ: справочник : [в 2 кн.]/ П. П. Кремлёвский ; ред. Е. А. Шорников. - 5-е изд., перераб. и доп.. - СПб.: Политехника, 2002 – 2004.
Дата добавления: 2020-11-15; просмотров: 128; Мы поможем в написании вашей работы! |
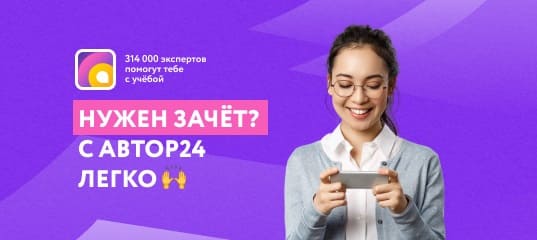
Мы поможем в написании ваших работ!