Занятие 15-16. УСТАНОВКИ ЭЛЕКТРОСТАТИЧЕСКОЙ ОКРАСКИ
ЭЛЕКТРООБОРУДОВАНИЕ УСТАНОВОК ДЛЯ НАНЕСЕНИЯ ПОКРЫТИЙ
Занятие14
ГАЛЬВАНИЧЕСКИЕ УСТАНОВКИ
Для нанесения металлических покрытий на другие металлы широко используется электролитический способ — гальваностегия. Изделие (катод) соединяется с отрицательным полюсом источника постоянного тока и погружается в ванну с электролитом — кислотным или щелочным раствором, который содержит ионы покрывающего металла. В ванну погружается электрод из покрывающего металла (анод), соединенный с положительным полюсом источника тока. В процессе электролиза металл анода переносится через электролит и осаждается на изделии. .;
Способом гальваностегии наносят антикоррозионное и декоративное покрытия металлических деталей электрических машин, для изготовления пластмассовых и миканитовых деталей коллекторов, контактных колец и т.п. . *
Количество осажденного металла пропорционально количеству прошедшего через электролит электричества с учетом, потерь из-за побочных химических реакций, утечек тока и других причин.
Наиболее распространены такие процессы нанесения покрытий, как цинкование, хромирование, никелирование, лужение, свинцевание, оксидирование. Температура электролита должна лежать в пределах от +20 до +80° С. Толщина наносимого слоя колеблется в широких пределах в зависимости от свойств покрытий, их назначения и условий эксплуатации. Например, цинковые покрытия для защиты черных металлов от коррозии имеют толщину 10—50 мкм, защитно-декоративные покрытия из хрома — до нескольких микрон. Применяются также многослойные покрытия, например медь-никель-хром. Для повышения коррозионной стойкости изделия из алюминия и его сплавов используют электролитическое утолщение оксидной пленки до 10—12 мкм. Процесс оксидирования характерен тем, что анодом служит изделие.
|
|
Электролит может иметь несколько вариантов (номеров ванн) отличающихся концентрацией компонентов. Осаждение металла сопровождается его кристаллизацией, и желательны покрытия с мелкими кристаллами (зернами). Поэтому выбирают тот вариант электролита, при котором получается мелкозернистое покрытие. Качество покрытия улучшается, если 2—6 раз в минуту менять направление тока. При повышенной температуре электролита (40—80° С) можно увеличить плотность тока и повысить производительность процесса. Обычно электролиты допускают плотность тока в пределах 102—103 ,А/м2; при подогреве и перемешивании электролита допустимы большие плотности тока.
Гальванические ванны представляют собой прямоугольные резервуары из листовой стали. Для кислотных электролитов ванны внутри футеруются материалом, не вступающим во взаимодействие с электролитом, например свинцом, винипластом, резиной. Ванны изготовляют также из полистирола.
|
|
Перед нанесением покрытий производят тщательную подготовку поверхности изделий: механическую обработку (очистку пескоструйным аппаратом, вращающимися щетками из проволоки, шлифование и полирование специальными пастами) и химическую или электрохимическую обработку. Последняя состоит из электролитического обезжиривания и травления в растворах кислот или щелочей. Изделие погружается в ванну с раствором и служит одним' из электродов. В процессе электролиза раствора выделяющиеся на поверхности изделия пузырьки газа (водорода на изделии— катоде или кислорода на изделии — аноде) отрывают от поверхности изделия капли жиров, масел, грязи и т. п. При травлении (с большими, чем при обезжиривании, плотностями тока) происходит как отрыв пленок окислов пузырьками газа, так и восстановление окислов или их электролитическое растворение. Последним этапом подготовки изделий, непосредственно перед поступлением в гальваническую ванну для нанесения покрытий, служит электрохимическое декапирование, т. е. легкое анодное травление в слабых растворах кислот.
|
|
Электрооборудование и схемы питания гальванических ванн. Для питания ванн применяют постоянный ток до нескольких тысяч ампер при напряжении 6—12 В. В качестве источников тока используют электромашинные преобразователи серии АДН с генераторами на токи от 250 до 10000 А при напряжении 6—12 или 9 В или полупроводниковые выпрямители на токи от 200 до 25 000 А при напряжении 6—28 В.
Генераторы электромашинных преобразователей на ток до 1500 А изготовляются с самовозбуждением. Более мощные генераторы имеют отдельный возбудитель с напряжением ПО В. Изменение напряжения генератора с 6 на 12 В осуществляют, переключая обмотки якоря с параллельного соединения на последовательное. При этом допустимый ток генератора уменьшается вдвоем
Полупроводниковые выпрямители в настоящее время стали основным видом источников питания гальванических установок. Выпрямители с неуправляемыми вентилями серий ВАКГ, ВАЗ и другие и тиристорные выпрямители серии ВАК выпускаются на токи от 100 до 25 000 А и напряжения от 6 до 48 В. Изготовляются также выпрямители серии ВАКР с реверсированием тока нагрузки.
На рис. 19-1 показаны упрощенные схемы источников питания гальванических ванн: электромашинного (рис. 19-1,а), неуправляемого выпрямителя (рис. 19-1,6) и тиристорного выпрямители (рис. 19-1,"в). Выпрямители с неуправляемыми вентилями построены по трехфазной схеме выпрямления с уравнительным реактором РУ и снабжены переключателем П, при помощи которого можно переключать отпайки первичной обмотки трансформатора Тр, изменяя выпрямленное напряжение. В других исполнениях выпрямителей для регулирования напряжения применены дроссели насыщения Др. Тиристорные выпрямители на токи до 600 А построены по полууправляемой трехфазной мостовой схеме выпрямления, а на большие токи — по трехфазной схеме е уравнительным реактором.
|
|
Оперативное включение и отключение источников питания производится контакторами КЛ. Напряжение генератора регулируется при помощи реостата Rper . В тиристорных выпрямителях с блоком импульсно-фазового управления БУя промежуточным усилителем ПУ применяются обратные связи по напряжению {ОН) или по току (ОТ)Т[либо по плотности тока (ОЯГ)]. Наличие переключателя обратных связей ПОС, позволяет получать внешние характеристики U = f \ I ) или U = fi (8 K ) разного вида (рис. 19-2), т. е,. обеспечивать режимы работы с автоматической стабилизацией заданного ползунком потенциометра R 3 значения напряжения либо
|
3~380 В 3-380В. 3~380В |
плотности токабкили тока/ЛБлок БТО предназначен для ограничения максимального тока выпрямителя при работе с обратной связью по ОН.
От источников тока к гальваническим ваннам ток передается по 'медным, алюминиевым, реже — латунным или стальным шинам. Когда прокладка шин невозможна, допускается применение кабелей. Сечения шин и проводов должны быть выбраны так, чтобы обеспечить минимальные потери электроэнергии.
Подвод тока к ваннам осуществляется через анодные и катодные штанги, укрепляемые на бортах ванн. Часто помещают катодную штангу между двумя анодными. В более широких ваннах укрепляют две катодные штанги с одной анодной посередине и. двумя анодными по краям. Во избежание утечки тока и нарушения режима работы ванны должна быть хорошо изолированы от
|
Рис. 19-2. Внешние характе- Рис. 19-3. Схема индивидуального ристики тиристорного вы- питания гальванической ванны, прямителя.
земли, для чего подставки ванн устанавливают на фарфоровые или резиновые прокладки. / Для ванн, потребляющих большие токи, особенно когда требуется регулировка тока, рекомендуются индивидуальные схемы питания (рис. 19-3) от источника постоянного тока ИПТ— электромашинного генератора или полупроводникового выпрямителя. При пуске электромашинного агрегата (см. рис. 19-1, а) сначала включают двигатель Д и по достижении требуемого напряжения на генераторе выключателем В (рис. 19-3) подключают ванну 1. Отключение производят в обратном порядке. При включении выпрямителя следует вначале подключить цепь ванны и только затем включить переменный ток. При выключении выпрямителя сначала выключается переменный ток, после чего можно .отключать ванну. .
Во многих гальванических цехах питание нескольких ванн осуществляется от общего источника ИПТ. На рис. 19-4 приведена схема параллельного включения гальванических ванн. В этом случае для регулирования тока в цепь каждой ванны включается реостат Rver , B >. Если для процесса покрытия требуется напряжение
большее, чем дает один источник, применяют последовательное включение нескольких источников, а при необходимости получить ток, превышающий ток одного источника, применяют параллельное включение источников.
В некоторых случаях для ванн требуется разное напряжение: для одних ванн 12 В, для других 6 В. Тогда
|
Рис. 19-4. Схема параллельного включения гальванических ванн по двухпроводной системе. |
питание ванн производится по трехпроводной схеме (рис. 19-5), дающей значительную экономию цветного металла на токопроводы.
Для механизации процессов покрытия и увеличения производительности гальванических цехов применяют полуавтоматические и автоматические установки. Они представляют собой ванны, оснащенные механизмами для непрерывного перемещения подвесных приспособлений с изделиями от места загрузки до места выгрузки.
По конструкции автоматы для нанесения гальванических покрытий могут быть прямолинейными, овальными (кольцевыми), П-образными. Прямолинейные автоматы применяются в случаях, когда поток деталей по ходу технологического процесса направлен в одну сторону. Покрываемые изделия перемещаются вдоль ванны с помощью бесконечных пластинчатых конвейерных цепей. Продолжительность процесса устанавливается в зависимости от необходимой толщины покрытия и регулируется изменением скорости. движения цепей
|
(0,1—I м/мин). У прямолинейных автоматов обслуживание двустороннее: загрузка и выгрузка изделий осуществляются с противоположных сторон ванны. В овальных, кольцевых и П-образных автоматах перемещение изделий производится также при помощи пластинчатых цепей, приводимых в движение посредством двух звездочек. Обслуживание таких автоматов, (загрузка и выгрузка) производится с одного рабочего места.
В полуавтоматических установках операции предварительной подготовки изделий и заключительные операции выполняются в стационарных ваннах. В автоматических конвейерных установках все операции, нанесения покрытий механизированы, начиная от обезжиривания и кончая сушкой деталей.
Занятие 15-16. УСТАНОВКИ ЭЛЕКТРОСТАТИЧЕСКОЙ ОКРАСКИ
На установках электростатической окраски окрашиваются различные изделия, в том числе корпуса электрических машин и аппаратов.
Сущность метода окраски распылением в электростатическом поле высокого напряжения до 140 кВ со-
стоит в том, что между заземленным окрашиваемым изделием и так называемым коронирующим электродом, находящимся под отрицательным потенциалом, создается постоянное электрическое поле, в которое вводится распыленный лакокрасочный материал. Попадая в это поле, частицы (мелкие капли) материала приобретают отрицательный заряд и движутся по линиям поля к окрашиваемому изделию.
Окраску ведут в специальной камере, которая служит для ограждения электродной системы, находящейся под высоким напряжением, а также предохраняет от запыления окрашиваемые изделия. Камера выполняется металлической, проходного типа; частично остекляется и хорошо освещается для наблюдения за процессом. Вход в камеру имеет блокировки безопасности. Размеры камеры определяются условиями производства. На рис. 19-6 представлен план электроокрасочной камеры 1 с электростатическими распылителями 7 и окрашиваемыми изделиями 6, которые движутся по заземленному конвейеру 2. В зависимости от рода и формы окрашиваемых изделий конвейер может быть-подвесным, ленточным, напольным. При окраске некоторых изделий их необходимо вращать, тогда конвейер снабжается устройством для вращения подвесок вокруг оси
в зоне электрического поля. Скорость конвейера устанавливается в зависимости от условий производства и пропускной способности сушильных камер. Обычно она равна 0,75—1 м/мин, а в некоторых случаях увеличивается до 3 м/мин и регулируется при помощи механических вариаторов.
В электроокрасочной камере предусматривается вытяжная вентиляция 3 для удаления паров растворителя краски. Движение воздуха в камере не должно нарушать движения заряженных частиц краски в зоне электрического поля, поэтому отсос воздуха производится по направлению движения распыленной краски. Скорость движения воздуха в камере обычно составляет 0,2— 0,5 м/с. В некоторых камерах устраивается еще и приточная вентиляция, которая через особые фильтры подает в камеру чистый воздух. В ряде конструкций камер предусматриваются гидрофильтры в системе вытяжной вентиляции. Камера оснащается также устройством автоматического огнетушения.; На рис. 19-7 показана принципиальная схема стационарной установки электростатической окраски. Предварительно, обезжиренные, промытые и просушенные изделия / укрепляются на конвейере 2 (в данном случав подвесном) и проходят мимо распылителей 4. Отрицательный потенциал подводится к коронирующим электродам распылителей от выпрямительного устройства высокого напряжения ВВУ, размещаемого обычно на крыше 16 электроокрасочной камеры. Краска поступает к распылителям из бачка 6 с мешалкой через дозирующее устройство 8, снабженное шестеренчатым или диафрагменным насосом. Управление всеми агрегатами установки осуществляют дистанционно с пульта 7,. вынесенного за пределы камеры. После окраски изделия поступают в сушильную камеру. Сушку ведут в специальных установках с электрическими нагревательными трубками инфракрасного (темного) излучения или излучателями с газовым подогревом.
В установках электроокраски применяют электростатические и пневматические краскораспылители и различные по форме коронирующие электроды. Электростатические распылители выполняются вращающимися центробежными с пневмо- или электроприводом, а также без подвижных элементов.
Электростатические центробежные распылители изготовляются в виде грибков, чаш, дисков. Наибольшее распространение получили чашечные и грибковые распылители. Одна из конструкций чашечного распылителя (типа ЧР-1) состоит из воздушной турбинки и сменных головок-чаш, закрепляемых на ее валу. Распылители помещаются на изолированной стойке 3 и могут быть наклонены к изделию под любым углом. Подача краски осуществляется через полый вал турбинки на внутреннюю поверхность чаши. Распыление краски с вращающейся чаши происходит за счет центробежных сил и высокого отрицательного напряжения, подаваемого на корпус чаши, которая является одновременно коронирующим электродом. Вращение чаши производится с угловой скоростью 90—150 рад/с, причем скорость регулируется давлением воздуха, который поступает от компрессора через воздухоочиститель 5. В других конструкциях чашечных распылителей, например типа ЭР-1М, вращение передается чаше от электродвигателя через механическую передачу. В грибковых распылителях с электроприводом краска подается на поверхность грибка снаружи, поэтому грибок непосредственно надевается на вал двигателя. Конструкция грибкового распылителя проще, чем чашечного, и такие распылители получают все большее распространение.
Распылители в виде грибков, чаш и дисков устанавливаются в окрасочной камере различными способами. Они крепятся на неподвижных отдельных изолированных стойках, на общей наклонной штанге между двумя стойками, подвешиваются к потолку камеры, а также помещаются на качающихся штангах или вертикальных опорах' с возвратно-поступательным движением. Механизмы перемещения распылителей приводятся в движение от электродвигателей. Применение таких механизмов позволяет сократить число распылителей в камере.
К электростатическим распылителям без подвижных элементов относятся лотки, гребенки из трубок, щелевые и другие устройства. Лакокрасочный материал в определенном количестве (от дозирующего устройства) подается на распылитель, поступает к его коронирующему краю и распыляется под действием электрического поля.
Если окраска изделий производится пневматическими распылителями (пистолетами), то в качестве коронирующих электродов используют сетки или игольчатые электроды. Распылители устанавливаются на заземленных штативах.
Электродные сетки 5 (см. рис. 19-6) применяют в тех случаях, когда распыление лакокрасочного материала производится пистолетами 4 под небольшим углом к оси конвейера. Электродные сетки изготовляют из жестких металлических трубчатых или прутковых рам без острых углов (диаметр прутков или труб 15—25 мм). На рамках через каждые 200—250 мм натягиваются коронирующие электроды из стальной или нихромовой проволоки диаметром 0,3—0,35 мм. Форма электродных сеток зависит в основном от конфигурации окрашиваемых изделий. Сетки могут быть вертикальными, горизонтальными, эллипсовидными. Длина сеток зависит от давления распыляющего воздуха; например, при давлении воздуха 90—150 кПа длина сеток составляет 1,5—2 м.
Если факел распыляемой краски необходимо направить к изделию под прямым углом, то целесообразно применять игольчатые электроды — металлические трубки со; вставленными в них остро заточенными иглами, обращенными остриями к изделию. Игольчатые электроды образуют постоянные ионизирующие точки с наибольшим скоплением электрических линий. Такие электроды менее подвержены загрязнению краской, не требуют частой чистки.
Для дистанционного управления пневматическими или электростатическими распылителями с пневмоприводом выпускается электропневматический клапан с датчиком положения (рабочее напряжение. 220/380 В).
Для электростатической окраски можно применять большинство обычных лакокрасочных материалов на основе масел, глифталевых и других смол, битумов, ас-фальтов. .Наиболее целесообразно применение электростатической окраски для наружных поверхностей изделий. Однако необходимо учитывать, что в результате неравномерности электрического поля осаждение лакокрасочного материала будет хорошо происходить на -выпуклых поверхностях и плохо — в местах углублений. В связи с этим для окраски углублений требуется дополнительная ручная подкраска (например, между ребрами корпусов электрических машин).
При окрашивании крупногабаритных изделий и изделий, выпускаемых мелкими сериями, а также для подкраски применяют ручные электростатические распылители. Схема установки для ручного электроокрашивания показана на рис. 19-8. Здесь на изделие краска, наносится при помощи электростатического распылителя-пистолета 2, который посредством шлангов и кабелей присоединен к дозатору лакокрасочного материала 4 и электростатическому генератору 5. Основные преимущества электростатической окраски заключаются в уменьшении расхода лакокрасочного материала примерно на 50% по сравнению с обычной окраской распылением и высоком качестве окраски. Вместе с тем следует иметь в виду, что экономическая и техническая эффективность метода электростатической окраски проявляется в полной мере только при комплексной механизации производства, начиная с подготовки изделий перед окраской и. кончая процессом сушки. Особенно эффективен этот метод в серийном и массовом производстве однородных изделий при использовании конвейеров.
Электрооборудование установок электростатической окраски. В качестве источников питания установок электростатической окраски применяют выпрямительные устройства высокого напряжения (например, на 140 кВ и 5 мА) и электростатические генераторы.
Принципиальная схема одной из разновидностей электростатического генератора приведена на рис. 19-9. Генератор преобразует механическую энергию в электрическую благодаря, механическому перемещению зарядов против сил электрического поля. В данном случае генератор имеет транспортер из диэлектрика. Подвижная часть генератора 1 — изоляционный транспортер зарядов, движущихся с некоторой скоростью (ротор). Элементы неподвижного статора осуществляют зарядку и разрядку поверхности транспортера. Зарядное и разрядное устройства соответственно состоят из ионизаторов 2а и За и индукторов 26 и 36.. В зарядном устройстве индуктор заземлен, в разрядном —соединен с нагрузкой 4
Если приложить между индуктором (пластиной из проводника) и ионизатором зарядного устройства напряжение возбуждения Ua , превышающее некоторое критическое значение, то на ионизаторе, представляющем собой тонкую проволоку, тонкую пластинку или ряд игл, возникнет электрический заряд. Образующиеся ионы осаждаются на поверхности транспортера и уносятся им. В разрядном устройстве (т.е. на полюсе высокого напряжения) между индуктором и ионизатором прикладывается напряжение UR противоположного знака. На ионизаторе также возникает заряд противоположного знака, благодаря чему с транспортера снимается заряд, который и .создает ток через нагрузку 4.
Чаще всего генераторы имеют цилиндрический ротор; в частности, у установки ручной электроокраски на рис. 19-8 изображен такой генератор.
Основные элементы выпрямительного устройства высокого напряжения ВВУ показаны на рис. 19-7. Повышающий трансформатор 15 установлен в бакелитовом цилиндре, заполненном трансформаторным маслом. Кенотрон 13 в кожухе располагается на трансформаторе накала 14, также установленном в бакелитовом цилиндре с маслом. Резистор 12 служит для ограничения тока на стороне высокого напряжения трансформатора при искровом разряде или к.з. В качестве ограничительного резистора обычно используется комплект радиорезисторов,, последовательно соединенных между собой и заключенных в бакелитовую трубку. Сопротивление резистора— 0,6—1 МОм. Шинопровод высокого напряжения 11 выполняют в виде стальной никелированной или хромированной трубки. Через проходной изолятор 9 подается напряжение в электроокрасочную камеру. Автоматический разрядник 10 в герметическом исполнении предназначен для автоматического снятия остаточного заряда с электродных сеток, электростатических распылителей и шинопровода после отключения высокого напряжения. Контактное устройство разрядника размещено в цилиндре полого фарфорового изолятора, заполненного маслом. Неподвижный контакт разрядника при помощи гибкого проводника присоединен к заземленным частям электроокрасочной камеры. Подвижный
контакт через систему рычагов из изолирующего материала связан с сердечником электромагнита и электрически соединен с шинопроводом 11. Если катушка электромагнита отключена, то подвижный контакт под действием пружины замкнут с неподвижным и шинопровод оказывается заземленным. При подаче питания в катушку электромагнита его сердечник втягивается, под
вижный контакт разрядника отходит от неподвижного, поэтому с шинопровода заземление снимается.
Электрическая схема устройства типа В-140-5 показана на рис. 19-10. Коронирующий электрод КЭ питается однополупериодным напряжением от "выпрямителя, состоящего из кенотрона высокого напряжения ВК типа КР-220 и повышающего трансформатора ТрВ. Первичная обмотка этого трансформатора подключена к сети 220 В через автотрансформатор AT , позволяющий плавно регулировать выпрямленное напряжение в пределах от 65 до 140 кВ. Трансформатор Тр2 накала кенотрона включен через настроечный __ реостат RH . Для контроля напряжения на коронирующём электроде служит вольтметр V , проградуированный по выпрямленному напряжению. Ток нагрузки выпрямителя высокого напряжения измеряется микроамперметром цА на 500 мкА, пределы измерения которого могут быть увеличены в 10 раз при помощи шунта #ш2 £ выключателем ВШ. Для предохранения микроамперметра от высокочастотных токов служит конденсатор С2.
Включение высокого напряжения производится при помощи главного контактора КГ после нажатия пусковой кнопки КнП. Одновременно автоматический разрядник РкА снимает заземление с отрицательного полюса цепи высокого напряжения. При перегрузках по току срабатывает максимальное реле РМ и отключает контактор КГ. Так же как и при отключении установки кнопкой КнС, в этом случае вместе с контактором КГ теряет питание электромагнит разряднику РкА, который заземляет коронирующий электрод КЭ.
В цепь высокого напряжения последовательно с ограничительным резистором R 0 включено также искропредупреждающее устройство ИПУ. Назначение ИПУ— предотвратить искровой пробой между коронирующий электродом КЭ и окрашиваемым изделием И, который может произойти в случае раскачивания изделия'на конвейере К, обрыве электродных проволок, падения изделия на коронирующий электрод и т. п. Искровой разряд в некоторых случаях вызывает загорание краски на изделии, поэтому искропредупреждающее устройство.должно быть сверхбыстродействующим. Указанное ИПУ представляет собой тиратронное реле, в аварийных случаях снимающее высокое напряжение с коронирующего электрода в течение одной миллионной доли секунды.Узел ИПУ оформлен конструктивно в виде самостоятельного блока, заключенного в бакелитовый цилиндр, заполненный маслом.
Секционированный тиратрон высокого напряжения СТ блока ИПУ включен параллельно кенотрону В К. Напряжение на коронирующий электрод поступает через пентод Л, в цепь катода которого включен резистор смещения R 1. На экранную сетку пентода подается положительный потенциал от выпрямителя Вп через сглаживающий фильтр R 3, СЗ. Питание выпрямителя Вп и цепей накала тиратрона и пентода производится от трансформатора Tpl , который в свою очередь подключен к сети 220 В через стабилизатор напряжения СИ.
Если произошло замыкание коронирующего электрода КЭ с изделием Я, увеличиваются анодный ток: пентода Л и напряжение смещения на сопротивлении R 1. Внутреннее сопротивление пентода* резко возрастает, поэтому на управляющую сетку тиратрона СТ подается отпирающий потенциал, тиратрон зажигается и шунтирует цепь высокого напряжения, снимая напряжение с коронирующего электрода. После этого реле РМ отключает контактор КГ.
Трансформатор ТрЗ служит для питания сигнальных ламп пониженным напряжением. Лампа 8ЛС контролирует наличие напряжения на схеме; лампа 7ЛС .(«светофор»), установленная при входе в окрасочную камеру, загорается при включении высокого напряжения. Остальные сигнальные лампы предназначены для контроля за работой вспомогательных устройств установки.
Кроме защиты цепи высокого напряжения от перегрузки и искрового разряда, в схеме предусмотрена защита от к. з. в трансформаторе ТрВ и на стороне низкого напряжения плавкими предохранителями Пр. Конденсаторы С1 защищают питающую сеть от радиопомех. Микроамперметр и обмотка реле РМ защищены от перенапряжений искровым промежутком ИП.
Электроаппаратура управления и защиты выпрямительного устройства высокого напряжения размещена в пульте управления, на крышке которого находятся приборы, выключатели, сигнальные лампы и кнопки КнП, КнС. Иногда применяют также дополнительные подвесные пульты управления. Приводы механизмов электроокрасочных установок выполняются от асинхронных двигателей во взрывонепроницаемом исполнении или закрытых во взрывонепроницаемых кожухах. Для привода центробежных вентиляторов применяют двигатели типа МА-143 мощностью от 3,8 до 8 кВт, а также типа ТАГ-32 мощностью 2,3—3,5 кВт. Турбинки грибковых и чашечных распылителей снабжаются двигателями серии АОЛ мощностью от 50 до 180 Вт.
Для привода насоса дозирующего устройства применяется обычно двигатель ТАГ-12/4 мощностью 0,42 кВт, для привода краскомешалки — мощностью до 0,9 кЩ Аналогичные двигатели используются и в приводах перемещения (качания) распылителей. Управление двигателями механизмов осуществляется при помощи магнитных пускателей и кнопочных станций.
Основные блокирующие устройства в схемах управления установки электростатической ожраски обеспечивают невозможность; 1) включения высокого напряжения посторонними лицами или лицами, у которых нет ключа от запирающейся пусковой кнопки; 2) пуска конвейера без предупредительного звукового сигнала и последующей выдержки времени в течение 5—15 с; 3) включения высокого напряжения в тех случаях, когда не подано напряжение на нить накала кенотрона, разомкнуты защитные вспомогательные контакты {БК.1 на рис. 19-10) на ограждении окрасочной камеры и на кабине с оборудованием высокого напряжения, регулятор высокого напряжения не находится в исходном положении (разомкнут контакт БК2); 4) включения распыления при выключенной вентиляции', неподвижном конвейере, выключенном высоком напряжении; 5) включения высокого напряжения при выключенной вентиляции.
Все элементы установки электростатической окраски, подлежащие заземлению (камера, стойки к пневматическим распылителям, конвейер, вентиляционная система и др.), заземляются согласно правилам заземления установок высокого напряжения.
Дата добавления: 2020-11-15; просмотров: 1698; Мы поможем в написании вашей работы! |
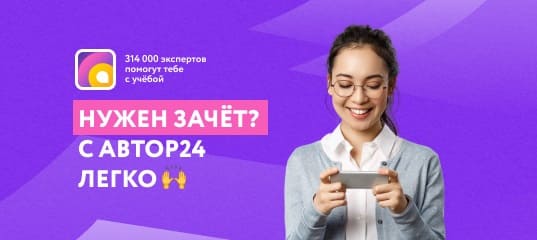
Мы поможем в написании ваших работ!