СМАЗОЧНЫЕ СИСТЕМЫ, ПРИБОРЫ И ИНВЕНТАРЬ
Смазочные системы подразделяются на группы по принципу работы, схеме питания и по смазочному материалу, подаваемому ими к парам трения.
По принципу работы системы бывают:
- проточные, когда смазочный материал периодически подаётся на трущиеся поверхности и, смазав их, возвращается в систему,
- циркуляционные, когда смазочный материал непрерывно подается в пары трения, и, смазав их, возвращается в систему и вновь подается к смазываемым деталям.
По схеме питания системы подразделяются на:
- индивидуальные для обслуживания одной смазываемой точки;
- централизованные системы для подачи смазочного материала одновременно к нескольким смазываемым точкам.
По смазочному материалу, подаваемому системой, различают:
- систему для масел, ею подаётся только масло;
- систему для консистентых смазок, ею подаётся только консистентная смазка.
Для выполнения смазочных работ в соответствии с целевым назначением смазочно-заправочный инвентарь подразделяется на следующие группы:
1) инвентарь цеховой кладовой – сливные воронки, баки, насосы, раздаточные бачки.
2) инвентарь для заправки смазочных систем и приборов – масленки, шприцы, бидоны, воронки, солидолонагнетатели.
3) инвентарь для разноски масел и смазок, и для сбора отработанных масел – ведра, бидоны. Шприцы для выкачки масел.
Выбор смазочных материалов определяется видом сопряженных деталей в узлах. Смазка подшипников скольжения производится маслами и консистентными смазками. Консистентные смазки целесообразно применять в случае, если окружающая среда содержит много посторонних механических примесей,
а также, если подшипники смазываются посредством ручной системы смазки, прессмасленок и станций густой смазки. В остальных случаях следует применять масла. Выбор последних производится в зависимости от нагрузок и скоростей скольжения (табл.3.1).
|
|
Таблица 3.1
Вязкость масел для подшипников скольжения в ССТ
Удельная нагрузка, МПа | Окружная скорость вала, м/ c | ||
До 20 Lj 20 | 21…30 | 31…50 | |
До 0,5 | 10…14 | 10…14 | 4,0…5,1 |
От 0,5 до 6,5 | 38…50 | 27…33 | 17…25 |
От 6,5 до 15,0 | 55…70 | 40…60 | 30…40 |
В ряде случаев подшипники скольжения работают при температуре 200°C и выше (сушильные камеры и т.п.). В этих условиях работы может быть рекомендован для смазки коллоидный графит, который смешивается с керосином. При высокой температуре керосин испаряется, а графит, оставаясь в подшипнике, служит смазочным материалом.
Смазка подшипников качения производится как консистентной смазкой, так и маслами (табл.3.2).
|
|
Таблица 3.2
Масла для подшипников качения
Частота вращения, 1/ мин | Температура среды, ° C | ||
До 0° | 0…60 | 60…100 | |
До 1000 | Индустриальное 12 | Индустриальное 45 | Цилиндровое 11 |
1000…2500 | Индустриальное 8А | Индустриальное 30 | Индустриальное 45 |
2500…5000 | Индустриальное 8А | Индустриальное 20 | Индустриальное 20 |
5000… выше | Индустриальное 5А | Индустриальное 12 | Индустриальное 12 |
Смазка зубчатых передач различается в зависимости от вида передачи.
Для открытых зубчатых передач может быть использована, как консистентная смазка, так и жидкая.
Из консистентных применяется смазка графитная, либо литол.
Из масел для открытых передач применяются масла высокой вязкости типа цилиндрового 24 или трансмиссионного.
Закрытые зубчатые передачи смазываются всегда маслами, подаваемыми на передачи разбрызгиванием или насосами. Выбор масла определяется в основном величиной удельного давления на поверхность зуба и окружной скоростью (табл.3.3).
Таблица 3.3
|
|
Материал зубчатого колеса | Окружная скорость, м / с |
| ||||||
До 0,5 | 0,5…1,0 | 1,0…2,5 | 2,5…5,0 | 5,0…10 | 10,0…25 | Св. 25 | ||
Текстолит, чугун, бронза. | Индустриальное 20 | Индустриальное 12 | Индустриальное 8А | Индустриальное 8А | Индустриальное 5А | Индустриальное 5А | Индустри альное 5А | |
Сталь | И-30А | И-20А | И-12А | И-12А | И-8А | И-5А | И-5А |
4. МЕТОДИКА ОПРЕДЕЛЕНИЯ РЕМОНТОСЛОЖНОСТИ
ОБОРУДОВАНИЯ
По эмпирическим формулам, связывающим параметры технической характеристики (высота центров, ширина столов, частота вращения шпинделя и т.п.) станков и машин с трудоёмкостью их ремонта, может быть приближённо определена ремонтносложность оборудования.
ТОКАРНЫЕ СТАНКИ
, (4.1)
Где коэффициент конструктивных особенностей станка:
,
K Т – коэффициент класса точности (табл.4.1); KХВ – коэффициент исполнения:
без ходового винта --------- 0,9
с ходовым винтом----------- 1,0
K чт- коэффициент частоты вращения шпинделя;
K чт =1,0 при частоте вращения <2000 об/ мин;
K чт= 1,1 при частоте вращения > 2000 обмин;
K 1 , K 2 , K 3 – коэффициенты технических параметров (табл.4.2 и 4.3), d о – наибольший диаметр обрабатываемой детали, мм;
|
|
L м.ц. – расстояние между центрами, мм; n – число ступеней скорости шпинделя; Rом – ремонтносложность отдельных механизмов;
R ом = R СТ + RбТ + R сд ,
Rст – ремонтносложность суппортов,
R СТ = 0,5(Хс-1)
Хс – число суппортов; Rбт– ремонтносложность механизма бесступенчатого регулирования частоты вращения шпинделя; Rбс= 2 при d ≤ 400 мм; R бс= 4 при d > 400 мм ; Rсд– ремонтносложность механизмов, не входящих в основной комплект станка (табл. 4.4); R Г – ремонтносложность гидравлической части оборудования.
, (4.2)
Где Р – рабочее давление трёхплунжерного насоса, МПа;
Q – производительность трёхплунжерного насоса, л/мин;
C – коэффициент, учитывающий конструктивные особенности трёхплунжерного насоса; C=4;
– коэффициент, учитывающий конструктивные особенности остальных типов (табл.5.5);
QI – производительность насосов остальных типов, л/мин;
L – длина цилиндра, мм;
D – диаметр цилиндра, мм; n – число рабочих цилиндров; m – число клапанов, золотников, дросселей, реле и т.д.
Таблица 4.1
Класс точности станка | Значение K Т |
Н | 1.0 |
П | 1.17 |
В | 1,48 |
А | 1,78 |
С | 2.2 |
Таблица 4.2
Масса станка, Т | К1 | К3 |
До 10 | 0,012 | 0.2 |
10-30 | 0,016 | |
30-100 | 0,024 | 0,3 |
100-160 | 0,038 |
Таблица 4.3
L мц,мм | К2 | L мц мм | К2 |
До 2000 | 0,001 | До 6000 | 0.0018 |
До 3000 | 0,0012 | 6000-15000 | 0.0020 |
До 4000 | 0,0014 | Св. 15000 | 0.0024 |
До 5000 | 0,0016 |
Таблица 4.4
Механизм | Тип станков | Значение R сд |
Гидрокопировальный суппорт | Токарно-винторезные | 2,0 |
Механизм балансировки шлифовального круга | Круглошлифовальные Плоскошлифовальные | 4,0 |
Прибор активного контроля | Бесцентрошлифовальные Внутришлифовальные Резьбошлифовальные | 0,25 |
Механизм для торцового или внутреннего шлифования | Круглошлифовальные | 0,4 |
Таблица 4.5
Вид насосов | ![]() |
Лопастные: одинарные сдвоенные | 1.0 1.9 |
Шестеренные | 1,2 |
Поршневые | 1,5 |
ТОКАРНО-КАРУСЕЛЬНЫЕ СТАНКИ
, (4.3)
Где , здесь KТ – коэффициент класса точности (табл.4.1); КМ – коэффициент массы (табл.4.2);
К1= 0,005; К2 =0,0035; K3 = 0,42; D п- диаметр планшайбы, мм; n2- число ступеней скорости планшайбы;
Хс – см. формулу (4.1);
Rбк – ремонтносложность механизма бесступенчатого регулирования скорости планшайбы; R бк=5; R Г – см. формулу 4.2.
ТОКАРНО-РЕВОЛЬВЕРНЫЕ СТАНКИ
, (4.4)
Где , Кт – см.табл. 4.1; Кар – коэффициент автоматизации:
при ручном переключении скоростей шпинделя и подач--------1,0
при селективном и автоматическом переключении -------------- 1,3
К1=0,1 – для прутковых станков с горизонтальной осью револьверной головки;
К1=0,15 – для прутковых станков с вертикальной осью револьверной головки;
К1=0,02 –для патронных станков;
К2=0,45; dор – наибольший диаметр обрабатываемой детали (табл.4.6);
Ran = 5 – ремонтносложность механизма автоматического поворота револьверной головки; n3 – число ступеней скоростей шпинделя.
Таблица 4.6
dор, мм | K1 | dор, мм | K1 |
До 12 | 0,2 | 30 | 0.12 |
14-20 | 0,15 | 36-40 | 0,10 |
22-25 | 0,14 | 50 и более | 0,08 |
4.4 РАДИАЛЬНО-СВЕРЛИЛЬНЫЕ И ОДНОШПИНДЕЛЬНЫЕ
ВЕРТИКАЛЬНО-СВЕРЛИЛЬНЫЕ СТАНКИ
, (4.5)
Где ; K Т – см табл.4.1; Kпр – коэффициент исполнения привода (табл.4.7),
К1 = 0,1; К2 = 0,02 – для радиальных станков;
К1 = 0,08; К2 = 0,01 – для вертикальных станков;
Lвш – наибольший вылет шпинделя, мм;
R бс – см. формулу 4.1, R бс =1,5; n1 – см. формулу 4.1.
Таблица 4.7
Исполнение привода | Кпр |
С коробкой скоростей: - с ручной подачей - с механической подачей | 0,9 1,0 |
Со ступенчатым шкивом - с ручной подачей - с механической подачей | 0,8 0,9 |
Дата добавления: 2020-04-25; просмотров: 139; Мы поможем в написании вашей работы! |
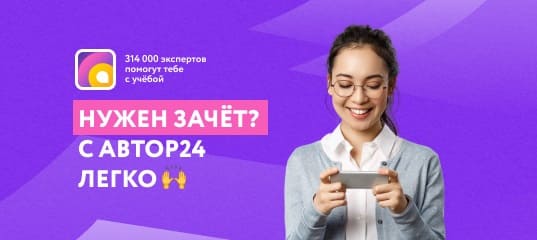
Мы поможем в написании ваших работ!