Рекомендуемый режим труда и отдыха
МИНИСТЕРСТВО ОБРАЗОВАНИЯ И НАУКИ ДОНЕЦКОЙ НАРОДНОЙ РЕСПУБЛИКИ
ГОСУДАРСТВЕННОЕ ПРОФЕССИОНАЛЬНОЕ ОБРАЗОВАТЕЛЬНОЕ УЧРЕЖДЕНИЕ
«ДОНЕЦКИЙ ТРАНСПОРТНО-ЭКОНОМИЧЕСКИЙ КОЛЛЕДЖ»
ЦИКЛОВАЯ КОМИССИЯ ГОРНО-ЭКОЛОГИЧЕСКИХ ДИСЦИПЛИН
МЕТОДИЧЕСКИЕ РЕКОМЕНДАЦИИ
ПО ВЫПОЛНЕНИЮ ПРАКТИЧЕСКИХ РАБОТ
по ПМ.04 Выполнение работ по профессии 13777 Машинист конвейера
для студентов специальности 21.02.18 Обогащение полезных ископаемых
Донецк- 2017
Содержание
Аннотация……………………………………………………………………......5
Введение………………………………………………………………………….6
Перечень практических работ…………………………………………………10
Практическая работа № 1. Освоение узлов компоновки технологического и транспортного оборудования обогатительных фабрик. Грузопотоки обогатительных фабрик.Решение ситуационных задач…………………………………………………………………………………....11
Практическая работа № 2.Расчет технико-экономической эффективности применения транспортных средств………..………………………….……………..20
Практическая работа № 3. Освоение элементов конструкции ленточных конвейеров. Конвейерный став. Конвейерная лента………………………………23
Практическая работа № 4. Освоение элементов конструкции ленточных конвейеров. Роликоопоры. Приводные и натяжные станции…………………….26
Практическая работа № 5. Освоение элементов конструкции ленточных конвейеров. Очистные устройства. Погрузочные и разгрузочные устройства ленточных конвейеров……………………………………………………………….29
|
|
Практическая работа № 6. Освоение средств автоматизации ленточного конвейера………………………………………………………………………………30
Практическая работа № 7. Эксплуатационный расчет ленточного конвейера……………………………………………… …………………………….34
Практическая работа № 8. Освоение карты организации труда на рабочем месте машиниста конвейера………………………………………………………….36
Практическая работа № 9. Предупреждение аварийных ситуаций и несчастных случаев при обслуживании ленточных конвейеров. Решение ситуационных задач…………………………………………………………………..39
Практическая работа № 10. Освоение элементов конструкции скребковых конвейеров……………………………………………………………………………..41
Практическая работа № 11. Предупреждение аварийных ситуаций и несчастных случаев при обслуживании скребковых конвейеров. Решение ситуационных задач…………………………………………………………………..45
Список литературы и Интернет – источников……………………………... 48
Аннотация
Методические рекомендации по выполнению практических работ по ПМ.04 МДК.04.01 Выполнение работ по профессии 13777 Машинист конвейера для студентов специальности 21.02.18 Обогащение полезных ископаемых содержат учебные цели, профессиональные компетенции, основные этапы выполнения работ.
|
|
Методические рекомендации способствуют более продуктивной деятельности студентов на практических занятиях, закреплению теоретических знаний, развитию пространственного мышления, творческого потенциала, позволяют учащимся выполнить практические работы с большей точностью, грамотностью и с максимальной результативностью.
ВВЕДЕНИЕ
Практические занятия являются одним из основных средств осуществления связи между теоретическим и практическим обучением.
Основное задание проведения практических работ по ПМ.04 МДК.04.01 Выполнение работ по профессии 13777 Машинист конвейера – познакомить обучающихся с технологическими процессами при обслуживании конвейерного транспорта и их закономерностями, с техническим устройством и характеристиками ленточных, скребковых, пластинчатых конвейеров, питателей разных типов через направленную преподавателем практическую деятельность самих обучающихся.
|
|
Деятельность обучающихся при выполнении практических работ должна быть творческой, близкой к исследовательской работе.
Цели и задачи практических занятий:
- убедиться в истинности приобретенных знаний, проверить результаты расчетов;
- отработать основные приемы эксплуатации различных технических транспортных устройств, изучить методы оформления технической документации;
- получить навыки самостоятельной работы по обслуживанию конвейерного транспорта;
- научиться анализировать изучаемые теоретические положения, устанавливать связь между ними и требованиями инструкции машиниста конвейера.
Для успешного решения этих задач необходимо учитывать ряд дидактических требований:
1. Каждое практическое задание должно быть тщательно подготовлено
2. Содержание его должно соответствовать уровню знаний студентов на данном этапе обучения
3. Практические работы обучающиеся должны выполнять самостоятельно после соответствующей теоретической подготовки по изучаемой теме.
При организации и проведении практических работ преподаватель должен руководствоваться следующими методическими приемами:
а) заранее тщательно и детально готовить каждое практическое занятие;
|
|
б) в обязательном порядке проводить инструктаж по охране труда перед началом практической работы, требовать от обучающихся выполнения правил безопасности;
в) раскрывать обучающимся цель каждой практической работы;
г) следить за тем, чтобы все обучающиеся, занятые практической работой, были загружены одинаково;
д) требовать своевременной сдачи отчетов;
е) сопровождать прием отчета опросом по существу практической работы и порядку ее выполнения.
Отчет оформлять необходимо в строгом соответствии с ЕСКД и требованиями ЕГР ДонТЭК.
Структура практического занятия:
- сообщение темы и цели работы;
- проведение детального инструктажа по охране труда в соответствии с темой работы;
- актуализация опорных теоретических знаний, которые необходимы для рациональной работы с транспортным оборудованием, для решения ситуационных задач, осуществления эксперимента или другой практической деятельности;
- непосредственное проведение практических работ;
- обобщение и систематизация полученных результатов, выполнение отчетов;
- подведение итогов занятия.
При подготовке и выполнении работ по Методическим рекомендациям обучающиеся получают возможность спланировать свою деятельность.
Методические рекомендации к практическим работам содержат следующие разделы:
1. Тема практической работы.
2. Цель практической работы.
3. Применяемое оборудование, аппаратура, приспособления.
4. Ход работы.
5. Контрольные вопросы.
6. Содержание отчета.
6. Список литературы и Интернет – источников.
Перечень практических работ
по МДК.04.01 Технология работ машиниста конвейера. Эксплуатация оборудования
№ п/п | Наименование работы | Кол-во часов |
1. 1 | Освоение узлов компоновки технологического и транспортного оборудования обогатительных фабрик. Грузопотоки обогатительных фабрик. Решение ситуационных задач | 2 |
2. | Расчет технико-экономической эффективности применения транспортных средств | 2 |
3. | Освоение элементов конструкции ленточных конвейеров. Конвейерный став. Конвейерная лента | 2 |
4. | Освоение элементов конструкции ленточных конвейеров. Роликоопоры. Приводные и натяжные станции | 2 |
5. | Освоение элементов конструкции ленточных конвейеров. Очистные устройства. Погрузочные и разгрузочные устройства ленточных конвейеров | 2 |
6. | Освоение средств автоматизации ленточного конвейера. Решение ситуационных задач | 2 |
7. | Эксплуатационный расчет ленточного конвейера | 2 |
8. | Освоение карты организации труда на рабочем месте машиниста конвейера | 2 |
9. | Предупреждение аварийных ситуаций и несчастных случаев при обслуживании ленточных конвейеров. Решение ситуационных задач | 2 |
10. | Освоение элементов конструкции скребковых конвейеров. Решение ситуационных задач | 2 |
11. | Предупреждение аварийных ситуаций и несчастных случаев при обслуживании скребковых конвейеров. Решение ситуационных задач | 2 |
Всего часов практических работ | 22 |
Практическая работа № 1
Тема: Освоение узлов компоновки технологического и транспортного оборудования обогатительных фабрик. Грузопотоки обогатительных фабрик. Решение ситуационных задач
Цель работы: Ознакомиться с основными типами компоновки технологического и транспортного оборудования обогатительных фабрик. Изучить грузопотоки обогатительных фабрик.
Применяемое оборудование, аппаратура, приспособления:
1. Инструкция по выполнению практической работы
2. Действующие макеты конвейерного транспорта
3. Схемы цепи аппаратов обогатительных фабрик
4. Чертежные принадлежности
Ход работы:
В зависимости от условий эксплуатации и конструктивных исполнений все средства фабричного транспорта можно классифицировать по принципу действия,
Средства рудничного транспорта |
Периодического действия |
Самоходные погрузочно-транспортные и транспортные установки |
Непрерывного действия |
Гравитационный транспорт |
Скреперные установки |
Локомотивный транспорт |
Конвейеры (вибрационные, скребковые, ленточные и др.) |
Трубопроводный гидро и пневмотранспорт |
Подвесные канатные дороги с кольцевым движением вагонеток |
Монорельсовые и канатные дороги с маятниковым движением вагонеток |
Вспомогательное оборудование |
способу перемещения груза, виду грузонесущего органа, конструкции тягового органа и способу передачи тягового усилия, времени работы на одном месте, конструктивным признакам.
По принципу действия средства внутрифабричного транспорта подразделяют на установки непрерывного действия, перемещающие грузы непрерывным потоком с загрузкой и разгрузкой при движении рабочего органа, и периодического действия, загрузку и разгрузку которых производят при полной остановке транспортных установок или на малой скорости их перемещения. Работа транспортных установок периодического действия характеризуется периодами во времени или циклами.
Транспортные устройства непрерывного действия служат для перемещения массовых грузов, идущих сплошным потоком. По способу передачи грузу движущей силы их подразделяют на конвейерные, самотечные (гравитационные) и устройства гидравлического и пневматического транспорта.
Конвейеры передают грузу движущую силу, получаемую от механического привода (например, электродвигателя). По конструктивным признакам различают конвейеры с тяговым органом и без тягового органа. К первой группе конвейеров относятся ленточные, пластинчатые, скребковые конвейеры, элеваторы и др.; ко второй — винтовые, вибрационные и др.
В самотечных (гравитационных) устройствах перемещение груза происходит под действием силы тяжести. Устройства этого типа представляют собой желоба и трубы, устанавливаемые под некоторым углом к горизонту.
В устройствах гидравлического и пневматического транспорта движущей силой являются, соответственно, струя воды и поток воздуха.
Транспортные устройства периодического действия предназначены для подъема и горизонтального перемещения на небольшие расстояния штучных грузов (деталей, машин, хозяйственных грузов и т. д.) или исходного сырья и продуктов обогащения на складах. Их называют иначе грузоподъемными машинами.
Грузоподъемные машины подразделяются на эксплуатационные и ремонтно-монтажные. К эксплуатационным относятся грейферные краны на складах углей, руд и концентратов, тельферы и т. д.
Ремонтно-монтажные устройства служат для производства различных ремонтных и монтажных работ — смены стержней или шаров в мельницах, подъема и переноски различного оборудования. К ним относятся тали, лебедки, домкраты мостовые краны и т. д.
Наряду с технологическими аппаратами и транспортными установками в общую цепь аппаратов обогатительной фабрики включен ряд вспомогательных устройств, предназначенных для временного хранения груза материала (бункера, склады) и равномерной подачи его (бункерные затворы, питатели).
По способу перемещения груза и виду грузонесущего органа различают транспортные установки, на которых груз перемещается:
по неподвижным наклонным желобам под действием силы веса или принудительным волочением;
на подвижных грузонесущих элементах, например, на ленте конвейера, в кузове вагонетки или автомобиля, ковше погрузочно-транспортной машины;
по качающимся и вибрационным желобам под действием инерции;
по неподвижным желобам или трубам в рабочей водной среде и неподвижным трубам в воздушной среде.
В транспортных установках могут применяться различные тяговые органы: гибкие (ленты, которые одновременно выполняют функции тягового и несущего органа, канаты, цепи); колеса жесткие, взаимодействующие с рельсовым путем, и эластичные, обрезиненные или с пневмошинами, взаимодействующие с почвой или дорожным покрытием; гусеничные механизмы.
В зависимости от типа и конструкции тягового органа тяговое усилие — управляемая внешняя сила, создаваемая приводом при взаимодействии с опорами и приложенная к тяговым органам — может передаваться:
трением между приводным барабаном и лентой или между приводным шкивом и канатом;
зацеплением между приводной звездочкой и тяговой цепью;
навивкой концевого каната на барабан лебедки;
сцеплением колес с рельсами или почвой; рабочей средой — в гидро- и пневмотранспортных установках;
силой гравитации—в установках, транспортирующих груз под действием его силы веса;
силой инерции — в качающихся и вибрационных конвейерах.
По виду привода и подводимой энергии различают транспортные установки с электрическим приводом, с питанием через контактный провод, гибкий кабель или от аккумуляторных батарей, дизельным, дизель-электрическим, пневматическим, гироскопическим приводом.
По времени работы внутрифабричного транспорта на одном месте различают:
самоходные установки, передвигающиеся постоянно вместе с грузом (погрузочно-транспортные машины, автосамосвалы);
передвижные, которые по условиям технологии разработки перемещают груз периодически через небольшие промежутки времени (скреперные лебедки);
полустационарные, перемещающие груз через относительно большие промежутки времени, чем передвижные;
стационарные, характеризуемые длительной эксплуатацией на одном рабочем месте (конвейерный или локомотивный транспорт).
Конструкции средств транспорта одного вида, но с разными производительностью, мощностью и габаритами характеризуются параметрическим рядом, т. е. последовательностью числовых значений основных параметров, определяющих размеры машин.
Например, в качестве основного параметра для ленточного конвейера принята ширина ленты. Ряд основных параметров одного вида машин, дополненный другими характеристиками, называется размерным рядом.
Выбор того или иного вида транспортных устройств зависит от характеристики перемещаемых грузов, требуемой дальности транспортирования и производительности установки и определяется технико-экономическим расчетом.
Объем перемещаемых грузов определяется величиной грузооборота, характеризующего мощность горно-обогатительного предприятия.
Грузооборот — количество груза (в тоннах или кубических метрах), перемещаемого в единицу времени (смену, сутки, год).
Необходимая производительность средств внутрифабричного транспорта характеризуется грузопотоком — количеством груза определенного вида (в тоннах или кубических метрах), перемещаемого в определенном направлении в единицу времени. Грузопоток на горно-обогатительном предприятии технологически увязывает комплекс обогатительных и транспортных машин.
Грузопотоки горно-обогатительных предприятий значительно изменяются во времени, что связано с неравномерностью поступления сырья на обогащение, перебоями с порожними вагонами под погрузку продуктов обогащения, простоями предприятий по различным причинам, организационными и другими факторами. Изменение грузопотока во времени характеризуется коэффициентом неравномерности
где Qmax — максимальное значение грузопотока в единицу времени, т/ч (т/мин);
Qcp — средний грузопоток за время работы в течение смены, т/ч (т/мин).
Средний грузопоток
где Qсм — сменный грузопоток, т; tcм — длительность смены, ч (мин).
Производительность выбранной транспортной машины должна превышать расчетный грузопоток на 15—20%.
Сглаживание неравномерности грузопотока, а, следовательно, увеличение производительности средств транспорта и уменьшение их простоев, обеспечивается промежуточной бункеризацией путем установки в транспортной линии аккумулирующих емкостей. На обогатительных предприятиях для аккумуляции и усреднения сырья и продуктов обогащения используются бункера различного типа и вместимости.
Система внутрифабричного транспортирования материала, в зависимости от способов размещения оборудования может быть самотечной, конвейерной или самотечно-конвейерной.
Контрольные вопросы:
1. Как делятся средства внутрифабричного транспорта в зависимости от конструктивного исполнения?
2. Какие типы транспортных средств применяются на ОФ для непрерывного транспортирования сыпучих грузов?
3. Какие бывают типы транспортных средств по способу передачи грузу движущей силы?
4. Что такое типоразмерный ряд транспортного оборудования?
5. Дайте определение грузопотока
6. Что такое грузооборот?
7. Как рассчитать коэффициент неравномерности грузопотока?
8. Поясните принцип расчета среднего грузопотока.
9. Какой берется запас при расчете среднего грузопотока.
10. Какие системы транспортных средств применяются на ОФ?
Содержание отчета:
1. Тема, цель практической работы
2. Схема транспортного узла (по варианту)
3. Расчет коэффициента неравномерности грузопотока для отделения фабрики (по варианту)
4. Выводы
Таблица 1- Варианты заданий для выполнения практической работы № 1
№ варианта | Узел технологической схемы | Максимальное значение грузопотока в единицу времени, т/ч | Длительность смены, час | Сменный грузопоток, т | Средний грузопоток, т/ч | Коэффициент неравномерности |
1,11 | Углеприем | 1000 | 8 | |||
2,12 | Углеподготовка | 1000 | 12 | |||
3,13 | Сортировка | 950 | 8 | |||
4,14 | Тяжелосредное обогащение | 500 | 12 | |||
5,15 | Отсадка крупного угля | 360 | 8 | |||
6,16 | Отсадка мелкого угля | 250 | 12 | |||
7,17 | Флотация | 200 | 8 | |||
8,18 | Фильтрация | 200 | 12 | |||
9,19 | Обезвоживание | 800 | 8 | |||
10,20 | Погрузка | 750 | 12 |
Литература:
1. Технология работ и организация труда машинистов конвейеров. Кемерово. 1989. – с. 238
2. Пухов Ю.С. Рудничный транспорт. М.: Недра, 1991.- 238 с.
3. Конспект лекций по технологии работ машиниста конвейеров. Донецк.: ГПОУ ДонТЭК, 2017. -82 с.
Практическая работа № 2
Тема: Расчет технико-экономической эффективности применения транспортных средств
Цель работы: Освоить методику расчета технико-экономической эффективности применения транспортных средств
Применяемое оборудование, аппаратура, приспособления:
1. Инструкция по выполнению практической работы
2. Действующий макет ленточного конвейера
3. Схема ленточного конвейера
4. ПК
5. Микрокалькулятор
Ход работы:
Технико-экономическая эффективность работы внутрифабричного транспорта характеризуется такими основными показателями как производительность и необходимое число транспортных машин при заданном грузообороте, расстояние транспортирования, организация движения и вспомогательных транспортных операций, производительность труда и уровень безопасности.
Обобщающим экономическим показателем технико-экономической эффективности транспорта является сумма приведенных затрат, приходящаяся на 1т или 1м3 транспортируемого груза (р/т или р/м3):
где С — себестоимость погрузки и транспортирования 1 т или 1 м3 груза, р/т (р/м3);
К — капитальные затраты, отнесенные к единице годового грузооборота (удельные капитальные затраты), р/т (р/м3);
Ен— годовой нормативный коэффициент экономической эффективности капитальных вложений (Ен = 0,15). Капитальные затраты слагаются из стоимости машин и расходов на транспортирование их к месту работы.
Для сравнения рассчитывают несколько вариантов. В качестве оптимального принимают вариант с минимальными приведенными затратами.
В себестоимость транспортирования входят: заработная плата обслуживающего персонала; начисления на заработную плату; амортизационные отчисления (стоимостное возмещение износа машин в процессе их эксплуатации) от суммы капитальных затрат; стоимость расходуемых вспомогательных материалов; стоимость электроэнергии или топлива и смазочных материалов.
Годовой экономический эффект (р.) от применения в конкретных условиях нового комплекса транспортных машин по сравнению с ранее используемым базовым комплексом
,
где С1 и С2— себестоимость транспортирования соответственно по базовому и новому вариантам комплексов, р/т (р/м3);
К1 и К2 — удельные капитальные затраты соответственно по базовому и новому комплексам, р/т (р/м3);
Qг— годовая эксплуатационная производительность нового комплекса, т (м3).
Контрольные вопросы:
1. Что является обобщающим показателем технико-экономической эффективности внутрифабричного транспорта?
2. Из каких элементов состоят капитальные затраты на транспортирование груза?
3. Чему равен годовой нормативный коэффициент экономической эффективности капитальных вложений?
4. Что входит в себестоимость транспортирования?
5. Как рассчитать годовой экономический эффект от применения в конкретных условиях нового комплекса транспортных машин по сравнению с ранее используемым базовым комплексом?
Содержание отчета:
1. Тема, цель практической работы
2. Расчет суммы приведенных затрат по базовому и проектному вариантам
3. Расчет годового экономического эффекта от применения в конкретных условиях нового комплекса транспортных машин (по вариантам). Производительность комплекса принять Qг=5 700 000 т/г
4. Выводы
Таблица 1- Варианты заданий для выполнения практической работы № 2
№ вар. | Количество оборудования, шт. | Стоимость оборудования, тыс.руб. | Себестоимость транспортирования 1 тонны, руб. | Капитальные затраты, руб. | |||||
базовый вариант | проектный вариант | базовый вариант | проектный вариант | базовый вариант | проектный вариант | базовый вариант | проектный вариант | ||
1,11 | 8 | 7 | 960 | 900 | 0,25 | 0,2 | 0,1 | 0,08 | |
2,12 | 9 | 8 | 1000 | 950 | 0,25 | 0,2 | 0,1 | 0,08 | |
3,13 | 10 | 9 | 1100 | 1000 | 0,25 | 0,2 | 0,1 | 0,08 | |
4,14 | 8 | 7 | 500 | 450 | 0,25 | 0,2 | 0,1 | 0,08 | |
5,15 | 9 | 8 | 550 | 500 | 0,25 | 0,2 | 0,1 | 0,08 | |
6,16 | 10 | 9 | 600 | 550 | 0,25 | 0,2 | 0,1 | 0,08 | |
7,17 | 8 | 7 | 400 | 350 | 0,25 | 0,2 | 0,1 | 0,08 | |
8,18 | 9 | 8 | 350 | 300 | 0,25 | 0,2 | 0,1 | 0,08 | |
9,19 | 10 | 9 | 300 | 250 | 0,25 | 0,2 | 0,1 | 0,08 | |
10,20 | 8 | 7 | 100 | 150 | 0,25 | 0,2 | 0,1 | 0,08 | |
Литература:
1. Технология работ и организация труда машинистов конвейеров. Кемерово. 1989. – с. 238
2. Пухов Ю.С. Рудничный транспорт. М.: Недра, 1991.- 238 с.
3. Конспект лекций по технологии работ машиниста конвейеров. Донецк.: ГПОУ ДонТЭК, 2017. -82 с.
Практическая работа № 3
Тема: Освоение элементов конструкции ленточных конвейеров. Конвейерный став. Конвейерная лента.
Цель работы: Усвоить знания оконструкции ленточных конвейеров, ее составных частей- конвейерном ставе и конвейерной ленте.
Применяемое оборудование, аппаратура, приспособления:
1. Инструкция по выполнению практической работы
2. Действующий макет ленточного конвейера
3. Схема ленточного конвейера
4. ПК
5. Чертежные принадлежности
Ход работы:
В ленточном конвейере транспортирование насыпных грузов осуществляется на конвейерной ленте, выполняющей функции тягового и несущего органа. Замкнутая бесконечная лента 1 (рис. 1, а) огибает головной приводной 2 и хвостовой натяжной 3 барабаны. Лента поддерживается по длине конвейера стационарными роликоопорами 4 и 5, причем расстояние между роликоопорами для верхней грузовой ветви в 2—2,5 раза меньше, чем для нижней порожней ветви. Загрузка возможна практически в любой точке по длине конвейера. Обычно ленточные конвейеры загружаются в хвостовой части через загрузочную воронку 6, а разгружаются при сходе ленты с головного барабана. Возможна разгрузка ленточного конвейера в промежуточных пунктах с помощью плужковых сбрасывателей или разгрузочных тележек. В зависимости от назначения и условий эксплуатации ленточные конвейеры оснащают дополнительными устройствами для очистки ленты и барабанов и улавливания ленты в случае ее обрыва (на наклонном конвейере). Для контроля работы и автоматизации конвейеров устанавливают различные датчики и приспособления.
Рис.1. Схемы ленточных конвейеров и их приводов
Преимуществами ленточных конвейеров являются:
Ø высокая производительность, большая длина как в одном ставе, так и всей конвейерной линии;
Ø относительная простота конструкции;
Ø значительно меньшие масса и удельная энергоемкость по сравнению со скребковыми конвейерами;
Ø высокая надежность, безопасность и возможность полной автоматизации работы.
Недостатки:
- ограничение по крупности транспортируемой горной массы (до 500 м),
- необходимость прямолинейной установки конвейера в плане,
- ограниченный угол наклона (с гладкой лентой при транспортировании вверх — до 18°, вниз — до 16°),
- высокая стоимость
- относительно небольшой срок службы конвейерной ленты.
Ленточный конвейер (рис. 2, а) включает двухбарабанную приводную станцию 2, выносной разгрузочный барабан 1, натяжную станцию 4, жесткий став 3 и загрузочное устройство 5. При ширине ленты 1200 мм и скорости движения 3,15 м/с техническая производительность конвейера составляет 1500 т/ч, суммарная мощность приводов 1000 кВт.
Рис.2. Ленточный конвейер (а) и схема запасовки ленты конвейера (б)
Основными сборочными единицами ленточного конвейера являются лента, роликоопоры и став, приводная станция, натяжное устройство, загрузочное устройство, очистные устройства и ловители ленты.
Роликовый став предназначен для поддержания верхней и нижней ветвей ленты, придания ей желобчатости и обеспечения устойчивого движения. Роликовый став выполняют либо жестким, состоящим из отдельных линейных секций (рис. 3, а), либо канатным, состоящим из двух параллельно натянутых канатов, опирающихся на стойки (рис.3, б).
Наибольшее распространение получили ленточные конвейеры с жестким ставом. Линейные секции става выполняют из швеллеров, соединенных болтами. Стойки секций крепят костылями к брусьям, расположенным на почве выработки. Для защиты нижней ветви ленты от заштыбовки и возможных попаданий горной массы с рабочей ветви ленты на нижнюю ветвь секции накрывают стальными листами.
В подземных горизонтальных выработках для транспортирования калийных руд применяют ленточные конвейеры с канатным ставом. Концы канатов через винтовые вертлюги, предназначенные для натяжения канатов, закрепляют анкерами к почве выработки. Верхние трехроликовые опоры закрепляют на канатах, а нижние — на стойках. По сравнению с жестким канатный став обладает рядом преимуществ: меньшая металлоемкость, лучшее центрирование ленты, снижение ударных нагрузок на ленту.
Рис.3 Роликовые ставы ленточных конвейеров
Лента является наиболее дорогостоящим и ответственным элементом конвейера. Стоимость ее составляет 50% от стоимости конвейера, а иногда и более. Лента состоит из каркаса, передающего тяговые усилия, верхних и нижних обкладок и бортов, предохраняющих каркас ленты от механических повреждений ипроникновения влаги. В горно-добывающей промышленности наиболее широко применяют многопрокладочные резинотканевые (рис. 4, а, б) и резинотросовые (рис. 4, в, г) ленты.
Рис.4. Конструкция конвейерных лент: 1 — прокладки; 2 — верхняя рабочая обкладка; 3 — нижняя обкладка; 4 — брекерная ткань; 5 — трос; 6 — предохранительная прокладка; 7 — резиновый наполнитель
Каркас многопрокладочных лент состоит из ряда тканевых прокладок, между которыми расположен тонкий слой резины (сквидж) толщиной 0,2—0,3 мм. Нити тканевых прокладок, направленные вдоль ленты и воспринимающие тяговые усилия, называются основными, а поперек — уточными, служащими для придания ленте поперечной жесткости. Прокладки со всех сторон защищены огнестойкой резиной. Толщина верхней обкладки составляет 6—10 мм, нижней — 2÷3,5 мм.
В многопрокладочных лентах, предназначенных для транспортирования крупнокусковых скальных грузов, под верхней обкладкой располагают защитную (брекерную) прокладку (см. рис. 4, б), обеспечивающую предохранение от пробоя прокладок каркаса крупными кусками и увеличивающую прочность связи верхней рабочей обкладки с прокладками каркаса.
Тканевые прокладки конвейерных лент изготавливают из комбинированных тканей (полиэфир/хлопок), а также на основе синтетических полиамидных волокон.
Число прокладок в ленте i = l÷6, прочность ткани прокладки по утку составляет 30—40% от прочности по основе.
Каркас резинотросовой ленты (см. рис. 4, в) состоит из ряда стальных латунированных или оцинкованных тросов диаметром 2,7—11 мм, которые расположены между двумя тканевыми защитными прокладками. В резинотросовых лентах, предназначенных для транспортирования относительно легкой горной массы, защитные прокладки отсутствуют.
Резинотросовые ленты находят все большее применение для мощных конвейеров значительной длины. По сравнению с резинотканевыми, резинотросовые ленты имеют большую прочность и малое удлинение (до 0,25%), меньшую толщину при равной прочности. Недостаток резинотросовых лент — их высокая стоимость и большая масса.
Контрольные вопросы:
1. Охарактеризуйте область применения ленточных конвейеров на ОФ
2. Назовите преимущества и недостатки ленточных конвейеров
3. Назовите основные сборочные единицы ленточного конвейера.
4. Опишите конструкции резинотканевых и резинотросовых конвейерных лент.
5. На схеме и на макете конвейера покажите основные конструктивные элементы.
6. Опишите конструкцию конвейерной ленты по схеме.
7. Приведите сравнительную характеристику резинотканевых и резинотросовых лент.
Содержание отчета:
1. Тема, цель практической работы
2. Схема ленточного конвейера с указанием основных конструктивных элементов
3. Характеристика конвейерного става
4. Схема конструкции конвейерных лент
5. Характеристика типов конвейерных лент
6. Выводы
Литература:
1. Технология работ и организация труда машинистов конвейеров. Кемерово. 1989. – с. 238
2. Пухов Ю.С. Рудничный транспорт. М.: Недра, 1991.- 238 с.
3. Конспект лекций по технологии работ машиниста конвейеров. Донецк.: ГПОУ ДонТЭК, 2017. -82 с.
Практическая работа № 4
Тема: Освоение конструкции ленточных конвейеров. Роликоопоры. Приводные и натяжные станции.
Цель работы: Усвоить знания о конструкции ленточных конвейеров, роликоопорах, приводных и натяжных станциях.
Применяемое оборудование, аппаратура, приспособления:
1. Инструкция по выполнению практической работы
2. Действующий макет ленточного конвейера
3. Схема ленточного конвейера
4. ПК
5. Чертежные принадлежности
Ход работы:
Для поддержания верхней рабочей ветви ленты по длине конвейера применяют роликоопоры, в основном, трехроликовые с углом наклона боковых роликов 30—40° (для широких лент на открытых работах применяют пятироликовые опоры).
Три ролика, образующие желоб для ленты, жестко закрепляют на кронштейнах в единую опору (рис. 1, а, б) или соединяют между собой шарнирно (рис. 1, в).
Роликоопоры с шарнирным соединением роликов, называемые гирляндными, улучшают центрирование ленты и обеспечивают ее большую желобчатость.
Рис. 1. Роликоопоры ленточного конвейера: 1,2 — ролики соответственно верхней и нижней ветвей ленты; 3 — секции става конвейера; 4 — центрирующая роликоопора нижней ветви ленты; 5 — цепи
Ролики выполняют на шарикоподшипниках с лабиринтными уплотнениями, исключающими попадание пыли в подшипниковые узлы и сохраняющими смазку в течение всего периода эксплуатации роликов (см. рис. 1, а, вид I).
На нижней (порожней) ветви устанавливают опоры: однороликовые; трехроликовые, как и на верхней ветви (см. рис. 1, а); V-образные двухроликовые с углом наклона роликов 10—15° (см. рис. 1, б), улучшающие центрирование нижней ветви ленты. С целью предотвращения налипания частиц груза нижние ролики футеруют резиновыми кольцами.
Линейные роликоопоры устанавливаются на ставе на расстоянии 1200—1400 мм друг от друга для верхней ветви ленты и2400—2800 — для нижней ветви ленты.
Кроме линейных роликоопор применяют специальные роликоопоры: центрирующие, предотвращающие боковой сход ленты; амортизирующие, располагаемые под лентой в местах подачи на нее горной массы (набор резиновых цилиндрических роликов или ролики, футерованные резиновыми кольцами).
Приводная станция ленточного конвейера включает 1,2 и, значительно реже, 3 приводных барабана, которые обеспечивают ленте необходимое тяговое усилие. На коротких конвейерах применяют однобарабанный привод, на конвейерах длиной 300—500 мм и более — двухбарабанный привод, с S-образной запасовкой ленты на барабанах.
Приводные барабаны кинематически жестко связаны с редуктором и приводятся от одного электродвигателя. Редуктор привода обычно трехступенчатый. Двигатель с редуктором соединяется эластичной муфтой. Привод вместе с выносным разгрузочным барабаном смонтирован на раме.
На коротких ленточных конвейерах возможно использование мотор-барабанов, в которых ротор и статор электродвигателя и планетарный редуктор смонтированы внутри обечайки барабана. Привод в таком исполнении компактен, но мощность его ограничена.
Обычно в приводах ленточных конвейеров малой и средней мощности используют электродвигатели с короткозамкнутым ротором.
На мощных ленточных конвейерах применяют двухбарабанный привод с запасовкой ленты, обеспечивающей обхват барабанов чистой стороной ленты. Приводная станция (рис. 2) включает в себя два отдельных блока, каждый из которых состоит из приводного 1 и отклоняющего 2 барабанов, огибаемых лентой 3. Приводной барабан 1 приводится от электродвигателя 4 через редуктор 6. Электродвигатель с редуктором соединен муфтой 5. На выходном валу редуктора установлен шкив колодочного тормоза 7, управляемого электромагнитным или электрогидравлическим приводом и служащего для затормаживания конвейера после свободного выбега. На промежуточном валу 8 смонтирован храповой останов 9, предотвращающий обратный ход ленты конвейера, загруженного и установленного под углом β>6°.
Рис. 2 Приводная станция ленточного конвейера
В мощных ленточных конвейерах применяют короткозамкнутые асинхронные электродвигатели с пусковыми гидромуфтами или электродвигатели с фазным ротором и соответствующей пусковой аппаратурой.
Натяжная станция предназначена для создания приводом тягового усилия, а также для поддержания заданного провеса ленты между роликоопорами и компенсации остаточной деформации (удлинения) ленты при ее вытяжке. По принципу действия натяжные устройства разделяют на жесткие и автоматические. В жестком натяжном устройстве натяжной барабан периодически изменяет свое положение в процессе работы конвейера, что не обеспечивает постоянного натяжения и постоянной компенсации остаточной деформации ленты.
Автоматическое натяжное устройство обеспечивает постоянное определенное соотношение натяжений в набегающей и сбегающей с привода ветвях ленты при любых нагрузках на конвейере или заданное натяжение сбегающей с привода ветви ленты — большее при пуске и меньшее при установившемся движении.
В автоматическом натяжном устройстве натяжной барабан постоянно меняет свое положение в зависимости от натяжения ленты и ее упругой вытяжки.
Автоматические натяжные устройства ввиду больших размеров и сложности конструкции не получили широкого распространения на ленточных конвейерах.
В коротких ленточных конвейерах применяют жесткое винтовое натяжное устройство с ручным управлением, установленное в хвостовой части конвейера. На горизонтальных ленточных конвейерах средней мощности в головной части конвейера у привода устанавливают жесткое натяжное устройство с электрической лебедкой, а в хвостовой секции — натяжное устройство с ручным приводом для монтажа и регулирования положения концевого барабана.
На мощных ленточных конвейерах жесткие натяжные устройства с электрическим приводом устанавливают обычно на хвостовой секции (рис. 3). Натяжная станция ленточного конвейера 2Л120А включает в себя: натяжной барабан 1, установленный на натяжной тележке 3, огибаемый лентой 2; канатную полиспастную систему 4, конец каната которой соединен с тележкой 3; электрическую лебедку 5. Периодическое подтягивание ленты производят при включении оператором электрической лебедки 5. Один из блоков полиспастной системы взаимодействует с датчиком визуального контроля натяжения ленты, который также обеспечивает блокировку конвейера от пуска при недостаточном предварительном натяжении ленты.
Puc. 3. Натяжная станция ленточного конвейера
Контрольные вопросы:
1. Для чего необходимы роликоопоры?
2. Какие типы роликоопор применяются на ленточных конвейерах?
3. На каком расстоянии должны быть установлены роликоопоры?
4. Назовите типы специальных роликоопор и их назначение
5. Каковы назначение и конструктивное исполнение приводной и натяжной станций конвейера?
6. Из каких элементов состоит приводная станция конвейера?
7. В чем особенности двухбарабанного привода?
8. Какие типы двигателей применяют обычно в приводах ленточных конвейеров?
9. Охарактеризуйте типы натяжных станций и область их применения
Содержание отчета:
1. Тема, цель практической работы
2. Сравнительная характеристика роликоопор ленточного конвейера
3. Схемы роликоопор
4. Характеристика приводных станций ленточных конвейеров
5. Характеристика натяжных станций ленточных конвейеров
6. Схемы грузовой и винтовой натяжных станций
Литература:
1. Технология работ и организация труда машинистов конвейеров. Кемерово. 1989. – с. 238
2. Пухов Ю.С. Рудничный транспорт. М.: Недра, 1991.- 238 с.
3. Конспект лекций по технологии работ машиниста конвейеров. Донецк.: ГПОУ ДонТЭК, 2017. -82 с.
Практическая работа № 5
Тема: Освоение элементов конструкции ленточных конвейеров. Очистные устройства. Погрузочные и разгрузочные устройства
Цель работы: усвоить знания оконструкции ленточных конвейеров, очистных, погрузочных и разгрузочных устройствах
Применяемое оборудование, аппаратура, приспособления:
1. Инструкция по выполнению практической работы
2. Действующий макет ленточного конвейера
3. Схема ленточного конвейера
4. ПК
5. Чертежные принадлежности
Ход работы:
Загрузочные устройства, способствующие увеличению долговечности ленты и обеспечивающие нормальный режим работы ленточных конвейеров, должны отвечать следующим основным требованиям: обеспечение минимальной высоты падения горной массы на ленту и придание грузопотоку скорости, равной или-близкой по величине и направлению к скорости движения ленты; равномерное поступление горной массы на ленту в соответствии с производительностью конвейера.
Загрузку ленточного конвейера производят обычно в его концевой части с помощью питателей, добычных или погрузочных машин, из различных бункеров с подачей груза на ленту с помощью специальных наклонных полукругового сечения: лотков и различных питателей. Под лентой в месте загрузки устанавливают амортизирующие обрезиненные ролики с шагом 0,4—0,6 м, а над лентой монтируют приемную воронку с боковыми направляющими резиновыми бортами, нижняя кромка которых соприкасается с верхней обкладкой ленты ипредохраняет от просыпей мелочи.
Очистные устройства и ловители. Для очистки рабочей обкладки ленты от прилипших частиц горной массы, которые при попадании на нижнюю ветвь загрязняют и изнашивают нижние роликоопоры и заштыбовывают пространство под нижней ветвью ленты, применяют очистные устройства. Обычно их устанавливают на нижней ветви ленты после ее сбегания с головного разгрузочного барабана. Очистные устройства могут быть выполнены в виде скребков, армированных полосовой резиной иприжимаемых к очищаемой поверхности ленты грузом или пружиной (рис. 1, а); скребков клавишного расположения (рис. 1, б); гидроочистителей, обеспечивающих гидросмыв налипших частиц с ленты. Разработаны и другие конструкции очистных устройств — щеточные (рис. 1, в) и в виде спирального ролика (рис. 1, г). Конструкция очистного устройства зависит от влажности, липкости и других свойств транспортируемой горной массы. Наибольшее распространение получили очистные устройства, выполненные в виде скребков. На мощных ленточных конвейерах, транспортирующих дробленые крепкие руды, применяют гидроочистку ленты.
Рис.1. Очистные устройства ленточных конвейеров
На наклонных мощных ленточных конвейерах устанавливают ловители для удержания рабочей ветви ленты с грузом в случае ее обрыва. На подземных конвейерах применяют ловители различных типов. Наиболее распространенные из них — ловители клинового типа, принцип действия которых следующий: при прямом ходе клиновые захваты, в которые входят края ленты, раздвигаются, а при обрыве и в начале движения ленты в обратном направлении сходятся и зажимают ленту.
Конвейерные перегружатели. Перегружатель представляет собой относительно короткий (6—25 м) передвижной ленточный конвейер с наклонной частью и горизонтальной стрелой. Перегружатели применяют при проведении выработок для передачи горной массы от погрузочной машины, проходческого комбайна или щита в нерасцепленный состав вагонеток, расположенных под горизонтальной стрелой перегружателя, или на другие транспортные средства. С помощью перегружателей обеспечивается непрерывная загрузка состава вагонеток, что позволяет значительно увеличить коэффициент использования во времени погрузочных и проходческих машин.
Перегружатели выполняют самоходными с электрическим: или пневматическим приводом или несамоходными, перемещаемыми буксировкой от погрузочной машины.
Механизм перемещения перегружателя может быть колесно-рельсовым или пневмошинным, или смонтирован на лыжах. Существуют перегружатели, перемещающиеся по монорельсу, закрепленному к кровле выработки.
Контрольные вопросы:
1. Привести назначение очистных устройств ленточного конвейера
2. Дать сравнительную характеристику очистных устройств ленточного конвейера
3. Какие механизмы и приспособления используются для загрузки ленточных конвейеров?
4. Какими способами может осуществляться разгрузка материала с конвейера?
5. Что такое конвейерные перегружатели?
Содержание отчета:
1. Тема, цель практической работы
2. Сравнительная характеристика очистных устройств ленточных конвейеров: роторных, вибрационных, скребковых
3. Схемы очистных устройств
4. Схема загрузочной течки конвейера
Литература:
1. Технология работ и организация труда машинистов конвейеров. Кемерово. 1989. – с. 238
2. Пухов Ю.С. Рудничный транспорт. М.: Недра, 1991.- 238 с.
3. Конспект лекций по технологии работ машиниста конвейеров. Донецк.: ГПОУ ДонТЭК, 2017. -82 с.
Практическая работа № 6
Тема: Освоение средств автоматизации ленточного конвейера
Цель работы: Усвоить знания о средствахавтоматизации ленточного конвейера
Применяемое оборудование, аппаратура, приспособления:
1. Инструкция по выполнению практической работы
2. Действующий макет ленточного конвейера
3. Схема ленточного конвейера
4. ПК
5. Чертежные принадлежности
Ход работы:
Автоматизация отдельных конвейеров и конвейерных линий производится по двум основным схемам:
1. дистанционное управление, при котором автоматизируются только пуск и остановка конвейера;
2. автоматизированный контроль за работой конвейера и его элементов, при которомприводные двигатели автоматически отключаются при нарушении режима работы конвейера или его отдельных элементов.
Согласно правилам безопасной эксплуатации к аппаратуре автоматизированного или дистанционного управления отдельными конвейерами или конвейерными линиями предъявляются следующие основные требования:
Ø обеспечение подачи предпускового предупредительного сигнала длительностью не менее 5 с;
Ø включение конвейеров в линию в последовательности, обратной направлению грузопотока, и обеспечение пуска последующего конвейера (против грузопотока) после разгона предыдущего;
Ø автоматическое одновременное отключение всех конвейеров в линии, транспортирующих груз на вышедший из строя конвейер;
Ø невозможность повторного включения неисправного конвейера при срабатывании электрических защит электродвигателя механической части конвейера и др.;
Ø отключение провода из любой точки по длине конвейера и наличие местной блокировки, предотвращающей пуск данного конвейера с пульта управления;
Ø возможность перехода на местное ручное управление приводами отдельных конвейеров при ремонте, осмотре и регулировании.
Аварийное отключение привода конвейера должно осуществляться при обрыве ленты, затянувшемся пуске, снижении скорости ленты до 75% от номинальной, завале перегрузочного пункта и т.д.
Между пультом управления, местом расположения приводов конвейера и пунктами загрузки конвейерной линии должна быть двухсторонняя телефонная связь или кодовая сигнализация.
Для ленточных конвейеров применяют комплекс АУК.1М, обеспечивающий выполнение основных технических требований к автоматизации конвейерных установок и предназначенный для автоматизированного управления конвейерами и контроля работы стационарных и полустационарных неразветвленных конвейерных линий с числом конвейеров до 10. Комплекс обеспечивает централизованное управление из пункта оператора, расположенного в шахте или на поверхности, и включает в себя пульт управления и блоки управления, в которые входят датчики скорости, датчики контроля схода ленты, кабель-тросовые выключатели, сирена и др.
Для контроля скорости ленты применяют тахогенераторные датчики, устанавливаемые у приводной станции между холостой и рабочей ветвями ленты. Ролик датчика прижимается пружиной к ленте. При вращении ролика тахогенератор вырабатывает ток с определенными параметрами, которые изменяются при изменении скорости ленты. Это фиксируется приборами, подающими команду на электропривод конвейера.
Датчик контроля схода ленты контролирует ее положение и при аварийном сходе ленты в сторону подает сигнал в систему дистанционного или автоматизированного управления.
Для экстренного прекращения пуска и экстренной остановки конвейеров с любого места технологической линии используют кабельно-тросовые выключатели, состоящие из гибких тяг (тросов), протянутых вдоль става конвейера, и конечных выключателей.
Для контроля состояниятросовой основы резинотросовых лент применяют устройства, обеспечивающие обнаружение поврежденных тросов в поперечном сечении ленты при ее движении, автоматическое суммирование повреждений тросовой основы по длине ленты и выдачу команды на отключение конвейера при обнаружении недопустимых повреждений.
Применяют также датчики контроля работы перегрузочных пунктов (контроля заполнения бункеров и течек в местах перегрузок горной массы с конвейера на конвейер), аппаратуру автоматизации орошения на перегрузках, предназначенную для автоматического включения и отключения системы орошения в местах перегрузки на конвейерах и др.
Важнейшее требование, предъявляемое к средствам автоматики,— их соответствие условиям работы в производственных помещениях углеобогатительных и брикетных фабрик. В связи с этим электрические средства автоматики, устанавливаемые в этих помещениях, могут быть общепромышленного исполнения либо должны быть повышенной надежности против взрыва (Н) или взрывобезопасными при любых повреждениях (О). Особенно опасными являются бункера и надбункерные помещения при переработке углей, выделяющих метан, а также помещения сушки, сухого дробления и классификации при обработке углей, дающих взрывоопасную пыль.
Высокая взрывоопасность характерна для ряда помещений брикетных фабрик. В других помещениях фабрик к средствам автоматики предъявляются жесткие требования в отношении пыле-, брызго- и влагозащищенности.
Для снижения трудоемкости, достижения удобства и простоты обслуживания целесообразна унификация:
применение однотипных средств автоматизации (использование одного типа вторичных приборов, регуляторов и т. д.);
использование аппаратуры, построенной по блочному принципу;
централизованное или групповое расположение аппаратуры и средств автоматизации.
Обогатительные процессы оценивают качественно-количественными показателями. Поэтому при наладке и эксплуатации технологии помимо контроля обогатительных процессов необходим контроль количества материала в потоках и его качественные характеристики. Количество твердых материалов (рядовой уголь и продукты обогащения) в потоках оценивается производительностью (т/ч), как и количество жидких материалов в потоках (м3/ч).
На рис. 1 показана обобщенная схема цепи технологических аппаратов углеобогатительной фабрики для обработки коксующихся углей. Рассмотрим схему с точки зрения необходимости автоматического контроля и регулирования.
Рядовой уголь в виде равномерного потока кускового материала поступает на грохоты первичной классификации 1. Поступающий рядовой уголь должен непрерывно взвешиваться (I) для определения производительности фабрики и для расчетов с поставщиком. При этом целесообразно определять его зольность (II). Поток рядового угля должен быть автоматически стабилизирован по производительности.
Надрешетный класс 100 мм ( + 100) после конвейера 2, на котором может производиться выборка посторонних предметов, и дробления в зубчатой валиковой дробилке 3 попадает вместе с подрешетным продуктом первичной классификации на классификационные грохоты 4.
Крупный машинный класс13—100 мм направляется на обогащение в тяжелосредные сепараторы 6. Здесь должно производиться определение нагрузки на сепаратор — взвешивание (I) поступающего угля.
В тяжелосредный сепаратор непрерывно подается магнетитовая кондиционная суспензия (КС), плотность которой автоматически контролируется, регистрируется и регулируется (III). Разбавленная некондиционная магнетитовая суспензия (НКС), получающаяся после ополаскивания продуктов обогащения сепаратора на грохотах 7 и 5, поступает в систему регенерации и обрабатывается на магнитных сепараторах 9. Магнитный сепаратор сбрасывает шламовую воду, которая далее сгущается в гидроциклоне 16. В емкостях с кондиционной и некондиционной суспензиями замеряются уровни, предусмотрена сигнализация. При этом желателен автоматический контроль зольности продуктов обогащения тяжелосредного сепаратора. Получаемый промпродукт поступает для раскрытия зерен в молотковую дробилку 10. Порода после ополаскивания на грохоте поступает в породный бункер 22. Подрешетный продукт—13 мм классификационных грохотов 4 поступает на дешламационные грохоты 5, где производится отмывка от него шламистых частиц крупностью <0,5 мм. Для дешламации на грохот через брызгала подается вода.
Получаемый мелкий машинный класс 0,5—13 мм поступает в отсадочные машины 11. При этом производятся стабилизация и контроль нагрузки взвешиванием (I) поступающего угля, контроль и регулирование (V) воды, подаваемой в отсадочную машину. В отсадочной машине автоматически контролируется и регулируется режим отсадки (A), контролируется и регулируется (VI) давление подаваемого сжатого воздуха. Отсадочные машины выдают концентрат и породу. Их зольность должна контролироваться (II) в целях корректирования режима отсадки. Для контроля качества продуктов отсадки обычно применяют экспресс-анализ расслоением в тяжелых жидкостях или в аппаратах ФАП.
Промпродукт отсадочной машины 11 и дробленый промпродукт тяжелосреднего сепаратора поступают на переобогащение в отсадочную машину 12. В этой отсадочной машине контролируются и регулируются те же параметры A , V , VI , что и в отсадочной машине 11. Концентраты отсадочных машин совместно обезвоживаются и ополаскиваются на грохотах 15. Затем концентрат дополнительно обезвоживается в центрифугах 14. После механического обезвоживания мелкий концентрат частично подвергается термической сушке в сушилке 21.
Подача угля (и промпродукта) в сушилку автоматически регулируется (I), так же автоматически регулируются режимы горения в топочном устройстве и процесса сушки (A). В течение сушки целесообразен автоматический контроль влажности (VII) поступающих и высушенных материалов.
Обезвоженный концентрат подается в погрузочные бункера 26. При отгрузке должны быть непрерывное взвешивание (I) и автоматический контроль влажности (VII) и зольности (II). Промпродукт отсадочной машины 12 обезвоживается в центрифугах 13 и поступает в отгрузочные бункера промпродукта 25 либо предварительно направляется на термическую сушку в сушилки 21. Необходим автоматический контроль количества (I) поступающего промпродукта и желателен автоматический контроль влажности (VII) и зольности (II).
Загрузка концентрата и промпродукта в бункера должна быть автоматизирована (А) в отношении распределения по ячейкам бункеров и выдачи информации о степени их заполнения.
Подрешетные воды дешламационных грохотов 5, шламовая вода магнитных сепараторов 9, системы регенерации магнетитовой суспензии и фугата обезвоживающих центрифуг подвергаются сгущению в гидроциклонах 16. Перед входом в гидроциклон осуществляется автоматический контроль давления (VI) поступающей водоугольной суспензии. Крупный сгущенный продукт гидроциклона возвращается на дешламационные грохоты 5. Слив гидроциклонов поступает в радиальный сгуститель 17. Слив радиального сгустителя представляет собой оборотную воду, которая возвращается в технологический процесс и используется в качестве транспортной и подрешетной воды в отсадочных машинах, подается в брызгала на грохотах и т. п. Качество оборотной воды целесообразно автоматически контролировать на содержание в ней твердого (IV).
Сгущенный продукт сгустителя поступает на обогащение во флотационные машины 19. Перед подачей во флотомашины состав (III) и количество (V) водоугольной суспензии (угольной пульпы) автоматически контролируются и регулируются. Режим флотации автоматически регулируется (А). Флотоконцентрат поступает для обезвоживания в вакуум-фильтры 20. Фильтрат возвращается во флотационный процесс. Обезвоженный флотоконцентрат направляется в бункера 24 и из них на сушку в сушилках 21. Целесообразно контролировать зольность (II) флотоконцентрата и флотохвостов. Флотохвосты сгущаются в радиальном сгустителе 18. Слив сгустителя используется в качестве оборотной воды. Осадок направляется во внешние отстойники-илонакопители. Объем (V) и содержание твердого (IV) сбрасываемых хвостов автоматически контролируются.
Для упрощения схемы на рисунке все оборудование показано в одном экземпляре; не показаны транспортное оборудование, промежуточные емкости, различное вспомогательное оборудование и приемные устройства для рядового угля, которые могут быть весьма разнообразны (приемные бункера, приемные ямы, опрокидыватели и др.).
В целом на современных углеобогатительных фабриках измеряется до 50 параметров, в том числе входные, выходные и режимные.
Серийно выпускаются совершенные конвейерные весы, действие которых основано на использовании тензометрических устройств.
Весы автоматические тензометрические конвейерные 1954АВ10-630 обеспечивают автоматическое измерение и дистанционную передачу значений текущей производительности в виде сигнала постоянного тока 0—5 мА и в дискретной форме — суммарного количества взвешиваемой массы материала, транспортируемого ленточным конвейером.
Весы состоят из устройства преобразования нагрузки, преобразователя перемещения, вторичного прибора и суммирующего отсчетного устройства.
Тензометрические весы выпускаются пятнадцати типоразмеров для конвейеров с шириной ленты от 650 до 1600 мм и скоростью движения 0,5—2,5 м/с. Класс точности весов 1,0; допускаемая погрешность текущей производительности ±0,5 % от наибольшего значения шкалы указателя производительности. Весы должны быть установлены на строго прямолинейных участках горизонтальных или наклонных конвейеров на расстоянии не менее 5 м от места загрузки и привода конвейера. Преобразователь перемещения ленты устанавливают под грузовой частью ленты после преобразователя нагрузки.
Необходимыми условиями нормальной работы конвейерных весов являются: полная техническая исправность конвейера; отсутствие порывов и клепаных швов на ленте (допускается только вулканизация); периодическая проверка установки конвейера и работы весов.
В последнее время значительное распространение получили весовые устройства, основанные на динамическом воздействии потока сыпучего материала на плоскость, лоток или другое тело, находящееся на пути движения потока (главным образом на его перепаде). Кусковой сыпучий материал каскадом ссыпается на наклонную плоскость (рис. 2), расположенную под углом к горизонтальной поверхности. Далее материал пересыпается на следующее транспортное устройство или в технологическую емкость.
Специальное измерительное устройство непрерывно измеряет динамическое воздействие падающего материала на плоскость, вычислительное устройство выдает информацию о расходе материала.
Рис. 2. Схема весового устройства фирмы «Хаслер»: 1 — конвейер; 2 — приемная плоскость; 3 — измеритель давления; 4 — вычислительный блок; 5 — блок информационный
Выход и качество продуктов обогащения зависят от зольности поступающих рядовых углей, их гранулометрического и фракционного состава. Режимы работы обогатительных аппаратов выбирают в соответствии с характеристиками рядового угля. В связи с этим для оперативного управления процессом обогащения необходимо контролировать качество углей, поступающих на фабрику. Кроме того, содержание породных фракций в рядовых углях определяет их стоимость, которую выплачивает фабрика поставщикам.
На рис. 3 показано устройство электрического влагомера, позволяющего устанавливать влажность угля непосредственно в потоке.
На коромысле 1 (рис. 3, а), установленном шарнирно непосредственно над конвейером вдоль движения угля, укреплена горизонтальная ось. На оси свободно вращается чувствительный элемент 2, представляющий собой три дисковых электрода из нержавеющей стали, которые разделены кольцевыми изоляторами из шлакоситалла. При движении ленты конвейера диски чувствительного элемента катятся по поверхности угля за счет трения. Степень нажатия дисков на уголь регулируется положением противовеса 3 на коромысле.
Контрольные вопросы:
1. Охарактеризуйте условия работы аппаратуры автоматизации на обогатительных фабриках
2. Перечислите основные требовании, предъявляемые к аппаратуре автоматизированного или дистанционного управления отдельными конвейерами и конвейерными линиями.
3. Дайте краткое описание основной аппаратуры, применяемой для автоматизации ленточных конвейеров.
4. Какие параметры необходимо контролировать при перемещении сыпучих грузов на ленточных конвейерах?
5. Какие золомеры применяются на ОФ?
6. Охарактеризуйте устройства для весового учета материала
7. Какие типы влагомеров устанавливаются на конвейерах?
Содержание отчета:
1. Тема, цель практической работы
2. Характеристика условий работы аппаратуры автоматизации
3. Требования к аппаратуре автоматизации конвейерных линий
4. Характеристика параметров контроля на ОФ по алгоритму: параметр, точка установки, средство автоматического контроля
5. Схема весового устройства фирмы «Хаслер»
6. Схема устройства электрического влагомера
Литература:
1. Технология работ и организация труда машинистов конвейеров. Кемерово. 1989. – с. 238
2. Пухов Ю.С. Рудничный транспорт. М.: Недра, 1991.- 238 с.
3. Конспект лекций по технологии работ машиниста конвейеров. Донецк.: ГПОУ ДонТЭК, 2017. -82 с.
Практическая работа № 7
Тема: Эксплуатационный расчет ленточного конвейера
Цель работы: Усвоить методику эксплуатационного расчета ленточного конвейера
Применяемое оборудование, аппаратура, приспособления:
1. Инструкция по выполнению практической работы
2. Схема ленточного конвейера
3. ПК
4. Микрокалькулятор
5. Чертежные принадлежности
Ход работы:
Исходными данными для расчета ленточного конвейера являются: расчетный грузопоток, поступающий на конвейер; плотность, гранулометрический состав и угол естественного откоса транспортируемой горной массы; максимальная длина транспортирования иугол наклона трассы; параметры конвейера в соответствии с технической характеристикой; условия эксплуатации.
Цель расчета — проверка соответствия параметров установленного конвейера условиям его эксплуатации, а именно — проверка ширины ленты по расчетному грузопотоку, определение запаса прочности ленты и мощности привода, а также возможной длины конвейера в одном ставе. Полученные расчетные параметры сравнивают с фактическими параметрами ленточного конвейера.
Техническая производительность (т/ч) ленточного конвейера
где Q — площадь поперечного сечения горной массы на ленте конвейера, м2;
k b — коэффициент снижения площади поперечного сечения горной массы на ленте в зависимости от угла наклона конвейера;
k 1 - коэффициент, учитывающий условия эксплуатации (k 1 = 1 — для стационарной установки, k 1 = 0,95 — для полустационарной).
Площадь поперечного сечения (м2) горной массы на ленте при трехроликовойопоре
где b 1 = 0,9 B—0,05 — рабочая ширина ленты, м (см. рис. 16.5,в); В — ширина ленты, м.
С достаточной точностью техническую производительность можно определить по формуле
В этой формуле значения коэффициента производительности
зависят от угла d установки боковых роликов и угла естественного откоса jд транспортируемой горной массы (табл.4).
Скорость движения ленты v для подземных ленточных конвейеров выбирают в зависимости от ширины ленты и видатранстируемогогруза из следующего ряда: 1; 1,6; 2; 2,5; 3,15;4 м/с. Для расчета производительности значение v принимают по характеристике конвейера. Если производительность задана, то по формуле (15.3) можно определить необходимую скорость ленты. При углах установки конвейера от 0 до 6° коэффициент kb=1от 6 до 180- kb=0,95
Таблица 4- Значения коэффициента производительности kп
Тип роликоопоры | Расчетный угол откоса насыпного груза | ||
15 | 20 | 25 | |
Однороликовая | 250 | 330 | 420 |
Двухроликовая с углом наклона роликов d, градус: | |||
20 | 500 | 580 | 660 |
45 | 570 | 615 | 660 |
Трехроликовая с углом наклона боковых роликов d, градус: | |||
20 | 470 | 550 | 640 |
Необходимая техническая производительность ленточного конвейера должна быть на 15—20% больше поступающего на конвейер грузопотока горной массы.
Необходимая ширина ленты (м)
Полученную ширину ленты округляют до стандартной ширины Вк и проверяют по кусковатости горной массы:
для рядового груза; содержащего куски максимальных размеров в количестве до 10% от общей массы,
Вк ≥ 2атах + 200;
для сортированного груза
Bк≥3,3аср + 200,
Таблица5 -Параметры резинотканевых конвейерных лент
Тип ткани тягового каркаса | Толщина наружных обкладок (верхней/нижней), мм | Линейная масса ленты q л кг/м) при числе тканевых прокладок | |||
3 | 4 | 5 | 6 | ||
БКНЛ-65 | 3/1 | 7,3 | 8,2 | 9,1 | 10 |
ТА-100 | 5/2 | 11,6 | 12,8 | 14 | 15,2 |
ТК-100 | 6/2 | 12,8 | 14 | 15,2 | 16,4 |
8/2 | 15,2 | 16,4 | 17,6 | 18,8 | |
ТК-200-2 | 4,5/3,5 | 14,6 | 16 | 17,2 | 18,8 |
6/2 | 13,4 | 14,8 | 16,2 | 17,6 | |
6/3,5 | 15,8 | 17,2 | 18,6 | 20 |
L ............... ³ 850 480 230 140 80 50 30 20 10
k ................ ….1,1 1,2 1,4 1,6 1,9 2,2 2,6 3,2 4,5
Натяжение ленты во всех точках конвейера определяют методом обхода контура по точкам, находят максимальное значение натяжения ленты Smax, натяжение в точке набегания ленты на приводной барабан Sнa6 и в точке сбегания Scб и сравнивают их отношение с тяговым фактором еma привода конвейера.
Запас прочности ленты т определяют по отношению разрывной прочности ленты S раз‚ установленной на конвейере, к максимальному натяжению ленты Smax, найденному методом обхода контура по точкам:
Для резинотканевых лент m = 9÷10, для резинотросовых m = 7÷9 (большие значения принимают для наклонных конвейеров). Обычно для горизонтальных и наклонных подъемных ленточных конвейеров Smax = S наб.
Контрольные вопросы:
1. Зачем необходимо производить расчет конвейеров?
2. Какие параметры расчета являются наиболее важными?
3. От чего зависит производительность конвейера?
4. Как определить ширину ленты плоской и лотковой формы по заданной производительности?
5. От чего зависит коэффициент производительности лен точного конвейера?
6. Как определяется мощность двигателя
Содержание отчета:
1. Тема, цель практической работы
2. Произвести приближенный расчет конвейера:
ü Определите ширину ленты конвейера по заданной произволдительности и по крупности транспортируемого материала.
ü Определить мощность привода на приводном валу конвейера по эмпирическим формулам
ü Определить тяговое усилие конвейера, максимальное натяжение ленты и число прокладок ленты
ü Определить диаметр барабана, выбрать двигатель и редуктор
ü Начертить схему ленточного конвейера
3. Выводы
Исходные данные для выполнения расчетов:
Технические показатели | Обозначение
| Размерность| | Вариант | ||||||||||
1 | 2 | 3 | 4 | 5 | 6 | 7 | 8 | 9 | 10 | ||||
Производительность | Q | т\ч | 620 | 550 | 600 | 480 | 360 | 500 | 650 | 570 | 420 | 390 | |
Длина | L | м | 80 | 85 | по | 50 | 100 | 65 | 70 | 75 | 100 | 55 | |
Угол наклона конвейера | β | º | 10 | 0 | 5 | 8 | 12 | 10 | 8 | 10 | 0 | 15 | |
Транспортируемый материал | - | - | Уголь | ||||||||||
Насыпная масса | т\м3 | 0,95 | 0,83 | 0,85 | 0,8 | 0,84 | 1.0 | 0,93 | 0,9 | 0,85 | 0,8 | ||
Максимальный размер куска | dmах | мм | 110 | 220 | 140 | 160 | 100 | 180 | 250 | 300 | 170 | 200 | |
Угол обхвата барабана лентой | а | º | 300 | 300 | 400 | 240 | 360 | 240 | 240 | 240 | 360 | 240 | |
Скорость ленты | V | м\с | 1,6 | 1,4 | 1,6 | 1,3 | 1,25 | 1,4 | 1.6 | 1,4 | 1.25 | 1.25 | |
Разгрузка осуществляется с концевого барабана. Материал транспортируется вверх. Атмосфера сухая. Барабан с ленточной футеровкой.
Литература:
1. Технология работ и организация труда машинистов конвейеров. Кемерово. 1989. – с. 238
2. Пухов Ю.С. Рудничный транспорт. М.: Недра, 1991.- 238 с.
3. Конспект лекций по технологии работ машиниста конвейеров. Донецк.: ГПОУ ДонТЭК, 2017. -82 с.
Практическая работа № 8
Тема: Освоение карты организации труда на рабочем месте машиниста конвейера
Цель работы: усвоить знания об организациитруда на рабочем месте машиниста конвейера
Применяемое оборудование, аппаратура, приспособления:
1. Инструкция по выполнению практической работы
2. Действующий макет ленточного конвейера
3. Схема ленточного конвейера
4. Схема организации рабочего места
5. ПК
6. Чертежные принадлежности
Ход работы:
Предметом труда машиниста конвейера является железорудная смесь, флюсы и топливо. Из подземной галереи сырьё по тракту конвейеров поступает на конвейеры перегрузочного узла №2 и далее железорудная смесь транспортируется на конвейера участка грохочения руды, а флюсы и топливо соответственно в известково-дробильное и коксо-дробильное отделение.
Форма организации труда: сменная, комплексная.
Оплата труда: сдельно-премиальная. Премия устанавливается в соответствии с действующим Положением №1 об оплате и премировании рабочих агломерационного цеха №2.
График синхронизации процесса
1 | Прием смены | ||||||||||||||||||||
2 | Выполнение операций по обслуживанию конвейеров | ||||||||||||||||||||
3 | Очистка желобов течек, каркасов | ||||||||||||||||||||
4 | Уборка участка рабочего места | ||||||||||||||||||||
5 | Замена роликов | ||||||||||||||||||||
6 | Регулировка ленты | ||||||||||||||||||||
7 | Отдых и личные надобности | ||||||||||||||||||||
8 | Сдача смены |
Оргоснастка
1.Лопота совковая.
2.Скребок.
3.Шуровка.
4.Ломик металлический.
5.Кувалда.
6.Молоток.
7.Зубило.
8.Ключи гаечные.
9.Метла.
10.Щётка.
Документация
1.Удостоверение по профессии.
2.Удостоверение стропальщика (для мужчин)
3.Карта участка с маршрутами обслуживания.
4.Карта организации труда на рабочем месте.
5.График ремонтов.
6.Инструкция по охране труда.
7.Инструкция о мерах пожарной безопасности.
8.Технологическая инструкция.
9.Инструкция по уходу, надзору и эксплуатации оборудования.
Обслуживание рабочего места
Функции обслуживания
1.Организационная: выдача задания, инструктаж по охране труда.
2.Контрольная: контроль за своевременной подачей сырья и материалов; правильной эксплуатацией оборудования.
3.Ремонтная: текущий и капитальный ремонты по графику ППР; профилактический ремонт.
Способ и режим обслуживания
1.Старший производственный мастер смены – в начале смены.
2.Старший производственный мастер смены, мастер производственного участка – в течении смены.
3.Ремонтный персонал механо- и электро- службы – в соответствии с графиком ППР. Дежурный персонал механо- и электрослужбы в течение смены.
Виды самообслуживания
1.Подготовка оборудования к ремонту и контроль качественного проведения ремонта.
2.Замена роликов.
3.Уборка просыпей и очистка течек.
4.Устранение неисправностей.
Связь
1.Телефон.
2.Селектор.
Условия труда. Факторы
Санитарно-гигиенические:
Наименование | Единица измерения | Норма |
Уровень шума | дБА | 80 |
Запылённость | мг/м3 | 4,6 |
Температура: в тёплый период в холодный период | 0С
оС ![]() | 16-27 15-21 |
Эстетические:
Окраска оборудования согласно ГОСТу
Психофизиологические
Физический труд: напряжённый, механизированный.
Рабочее положение: стоя; наклоны.
Сосредоточение внимания.
Рекомендуемый режим труда и отдыха
20 30 10 15
0 1 2 3 4 5 6 7 8 9 10 11 12
работа
отдых
Дата добавления: 2020-04-25; просмотров: 326; Мы поможем в написании вашей работы! |
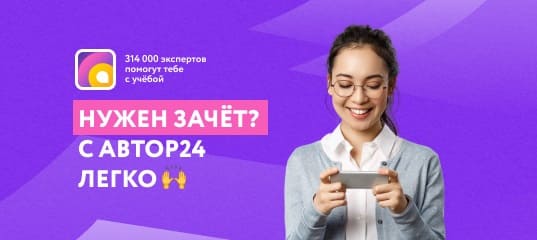
Мы поможем в написании ваших работ!