Смешивание различных марок масел не допускается.
Билеты для экзамена на военке
1.Раскрыть основные направления политики государства в области охраны труда.
обеспечение приоритета сохранения жизни и здоровья работников;
принятие и реализация федеральных законов и иных нормативных правовых актов Российской Федерации, законов и иных нормативных правовых актов субъектов Российской Федерации в области охраны труда, а также федеральных целевых, ведомственных целевых и территориальных целевых программ улучшения условий и охраны труда;
государственное управление охраной труда;
государственный надзор и контроль над соблюдением государственных нормативных требований охраны труда;
государственная экспертиза условий труда;
установление порядка проведения аттестации рабочих мест по условиям труда и порядка подтверждения соответствия организации работ по охране труда государственным нормативным требованиям охраны труда;
содействие общественному контролю над соблюдением прав и законных интересов работников в области охраны труда;
профилактика несчастных случаев и повреждения здоровья работников;
расследование и учет несчастных случаев на производстве и профессиональных заболеваний;
защита законных интересов работников, пострадавших от несчастных случаев на производстве и профессиональных заболеваний, а также членов их семей на основе обязательного социального страхования работников от несчастных случаев на производстве и профессиональных заболеваний;
|
|
установление компенсаций за тяжелую работу и работу с вредными и (или) опасными условиями труда;
координация деятельности в области охраны труда, охраны окружающей среды и других видов экономической и социальной деятельности;
(в ред. Федерального закона от 30.12.2008 N 309-ФЗ)
распространение передового отечественного и зарубежного опыта работы по улучшению условий и охраны труда;
участие государства в финансировании мероприятий по охране труда;
подготовка специалистов по охране труда и повышение их квалификации;
организация государственной статистической отчетности об условиях труда, а также о производственном травматизме, профессиональной заболеваемости и об их материальных последствиях;
обеспечение функционирования единой информационной системы охраны труда;
международное сотрудничество в области охраны труда;
проведение эффективной налоговой политики, стимулирующей создание безопасных условий труда, разработку и внедрение безопасных техники и технологий, производство средств индивидуальной и коллективной защиты работников;
установление порядка обеспечения работников средствами индивидуальной и коллективной защиты, а также санитарно-бытовыми помещениями и устройствами, лечебно-профилактическими средствами за счет средств работодателей.
|
|
(часть первая в ред. Федерального закона от 30.06.2006 N 90-ФЗ)
Реализация основных направлений государственной политики в области охраны труда обеспечивается согласованными действиями органов государственной власти Российской Федерации, органов государственной власти субъектов Российской Федерации и органов местного самоуправления, работодателей, объединений работодателей, а также профессиональных союзов, их объединений и иных уполномоченных работниками представительных органов по вопросам охраны труда.
2.Обязанности работника в области охраны труда
Работник обязан:
соблюдать требования охраны труда;
(в ред. Федерального закона от 30.06.2006 N 90-ФЗ)
правильно применять средства индивидуальной и коллективной защиты;
проходить обучение безопасным методам и приемам выполнения работ и оказанию первой помощи пострадавшим на производстве, инструктаж по охране труда, стажировку на рабочем месте, проверку знаний требований охраны труда;
(в ред. Федерального закона от 30.06.2006 N 90-ФЗ)
|
|
немедленно извещать своего непосредственного или вышестоящего руководителя о любой ситуации, угрожающей жизни и здоровью людей, о каждом несчастном случае, происшедшем на производстве, или об ухудшении состояния своего здоровья, в том числе о проявлении признаков острого профессионального заболевания (отравления);
проходить обязательные предварительные (при поступлении на работу) и периодические (в течение трудовой деятельности) медицинские осмотры (обследования), а также проходить внеочередные медицинские осмотры (обследования) по направлению работодателя в случаях, предусмотренных настоящим Кодексом и иными федеральными законами.
(в ред. Федерального закона от 30.06.2006 N 90-ФЗ)
3.Требования по безопасности при ремонте техники
3.1. Основные требования безопасности при работе личного состава на БМП и автомобилях, их обслуживании и ремонте, при проведении учений и стрельб, на занятиях по вождению, при вытаскивании и буксировке машин. Требования безопасности при работах в парках.
Перед началом работ командир (руководитель работ, контролирующее лицо) обязан лично убедиться, что для их производства созданы и обеспечены безопасные условия.
|
|
С этой целью он:
¾ проверяет укомплектованность расчетов и наличие контролирующих лиц;
¾ ставит задачу подразделениям, расчетам, номерам расчетов на проведение работ;
¾ доводит установленным порядком требования безопасности и проверяет качество их усвоения путем контрольного опроса военнослужащих (при выполнении работ с повышенной опасностью и работ на опасных объектах проводит целевой инструктаж);
¾ проверяет наличие у личного состава удостоверений на право самостоятельной работы;
¾ проверяет наличие индивидуальных средств защиты;
¾ устанавливает (контролирует) порядок и продолжительность работы в индивидуальных средствах защиты;
¾ проверяет медицинское обеспечение работ;
¾ ставит задачу начальнику аварийно-спасательной группы и проверяет ее готовность;
¾ проверяет готовность к работе ВВТ по наличию в журналах учета технического состояния и формулярах записей о проведении технического обслуживания, освидетельствования объектов гостехнадзора, поверки средств измерений и диэлектрических средств защиты;
¾ проверяет готовность и исправность систем связи, освещения, вентиляции, пожаротушения, нейтрализации, газового контроля, лифтов, а также наличия на местах плакатов и знаков безопасности, предписанных эксплуатационной документацией;
¾ принимает (контролирует) доклады от должностных лиц о готовности личного состава и ВВТ к проведению работ.
В целях строгого выполнения требований безопасности он:
а) во время работ:
¾ находится на месте проведения работ, руководит ими до полного окончания и приведения вооружения и военной техники в исходное положение;
¾ обеспечивает действенную систему контроля за выполнением операций, контролирует выполнение личным составом и представителями промышленности установленных требований безопасности;
¾ лично контролирует выполнение операций, определенных эксплуатационной документацией, и требует их полного и качественного выполнения;
¾ организует операционный контроль всего технологического цикла работ, в том числе строгий контроль наиболее ответственных и сложных операций;
¾ решительно пресекает любые несанкционированные действия личного состава и нарушения требований безопасности;
¾ в случае возникновения аварийной ситуации или неисправности подает команду "Стоп", немедленно докладывает по команде и принимает меры в соответствии с инструкциями и эксплуатационной документацией;
¾ руководит личным составом при ликвидации последствий аварий, катастроф, поломок, пожаров;
б) после окончания работ:
¾ проверяет приведение агрегатов и систем в исходное положение;
¾ проверяет наличие личного состава, выполнявшего работы;
¾ проверяет приведение рабочих мест в безопасное состояние;
¾ проверяет наличие записей в эксплуатационных документах о проведенных работах и подписей лиц, руководивших работами, исполнявших и контролировавших их;
¾ подводит итоги работ, обращает внимание на имевшиеся нарушения требований безопасности;
¾ докладывает по команде об итогах проведения работ.
Запрещается:
¾ проводить работы на ВВТ без руководства и постоянного наблюдения должностных лиц или руководителей работ;
¾ изменять объем, технологию и последовательность операций, предусмотренных эксплуатационной документацией;
¾ отключать технические средства блокировки и предупреждения об опасности;
¾ применять при работах на ВВТ нетабельное (непредусмотренные эксплуатационной документацией) оборудование, аппаратуру и инструмент;
¾ работать с помощью неисправного оборудования, аппаратуры, инструмента;
¾ применять приборы, сосуды, работающие под давлением, и грузоподъемные средства, не прошедшие положенного переосвидетельствования;
¾ пользоваться переносными электролампами с напряжением выше 36 В.
Образец ВВТ (агрегат, система) не отвечает условиям безопасности, если:
¾ имеются дефекты, выходящие за нормы браковки;
¾ на вращающихся (подвижных) и токоведущих частях узлов и механизмов отсутствуют (или неисправны) штатные ограждения и защитные устройства;
¾ неисправны приборы безопасности, предохранительные и заземляющие устройства;
¾ не укомплектован пригодными и испытанными в срок средствами защиты;
¾ эксплуатируется с истекшими сроками технического освидетельствования узлов, частей и приборов гостехнадзора и энергонадзора;
¾ хранение применяемых ядовитых технических жидкостей не отвечает требованиям руководящих документов;
¾ неисправны блокировки, световая или звуковая сигнализация;
¾ имеются другие технические нарушения и отступления от эксплуатационной документации для конкретного образца (системы, узла), представляющие угрозу для жизни и здоровья людей.
4.Мероприятия по предупреждению аварий и катастроф
¾ проведение всесторонних проверок водительского состава боевых машин и базовых шасси, отстранение от управления машинами недисциплинированных и плохо подготовленных водителей (механиков-водителей), а также по медицинским противопоказаниям;
¾ систематическое изучение личным составом опасных факторов на образцах ВВТ, механизма и условий их воздействия на организм человека;
¾ поддержание ВВТ и элементов паркового оборудования в исправном состоянии;
¾ оборудование рабочих мест, постов средствами диагностики, пожаротушения и медицинскими средствами;
¾ тщательная организация маршей, подготовка и оборудование маршрутов с учетом особенностей движения в ночное время и трудных погодных условиях;
¾ постоянное совершенствование навыков вождения у водительского состава;
¾ организация работы контрольно-технических пунктов и укомплектование их технически грамотными и требовательными специалистами;
¾ ограничение скорости и четкая организация движения в парках, при постановке (заезде) машин на места стоянки (в сооружения);
подготовка водительского и личного состава подразделений для действий в аварийных (нештатных) ситуациях.
5.Причины возникновения пожаров и способы их тушения
Пожары являются одним из видов стихийных бедствий. Возможными причинами их возникновения являются:
¾ курение в не установленных местах;
¾ нарушение правил работы с открытым огнем и газо-электросварочных работ
¾ самовоспламенение и самовозгорание своевременно не убранного мусора и др.
3.4. Средства тушения пожаров в частях, подразделениях и на технике.
.3. Первичные средства пожаротушения.
Обеспечение воинских частей пожарным инвентарем и оборудованием производится органами квартирно-эксплуатационной службы. Все пожарное оборудование, находящееся в воинской части, закрепляется за подразделениями, а в последних - за помещениями и включается в общую опись имущества. Командиры подразделений и начальники объектов несут ответственность за сохранность, содержание и постоянную готовность к действию закрепленного пожарного оборудования.
Использование пожарного инвентаря не по прямому назначению категорически запрещается.
В подразделениях и на объектах используются первичные средства пожаротушения:
¾ огнетушители;
¾ бочки с водой;
¾ песок;
¾ асбестовые покрывала;
¾ ведра;
¾ пожарный инструмент.
Огнетушитель химический пенный ОХП-10 предназначен для тушения очагов пожара из твердых материалов, а также различных горючих жидкостей, за исключением электроустановок находящихся подтоком. Они эффективно работают при температуре от 5 до 45 градусов С.
Огнетушители воздушно-пенные ОВП-5 и ОВП-10 предназначены для тушения загораний различных веществ и материалов, за исключением щелочных материалов, веществ горящих без доступа воздуха и электроустановок находящихся под током. Огнетушители можно эффективно использовать при температуре 5 - 50 градусов С. Огнетушащая эффективность этих огнетушителей в 2,5 раза выше химических пенных при одинаковой емкости.
Углекислотные огнетушители ОУ-2, ОУ-5 и ОУ-8 предназначены для тушения загораний двигателей и топливных баков боевых и транспортных машин, различных горючих жидкостей, электроустановок находящихся под напряжением, ценных документов и сгораемых материалов. Они представляют собой стальные баллоны емкостью 2,5, 5 и 8 л. Эффективное использование углекислотных огнетушителей ограничивается температурой - 25 градусов С. При более низких температурах давление в баллонах падает и истечение углекислого газа происходит медленно.
Углекислотно-бромэтиловые огнетушители ОУБ-3 и ОУБ-7 предназначены для тушения небольших очагов пожара при воспламенении различных горючих веществ, тлеющих твердых материалов (хлопка, текстиля, изоляционных материалов и др), а также электроустановок, находящихся под напряжением до 380 в. Огнетушители обеспечивают эффективное тушение пожаров при температуре от - 60 до + 55 градусов С.
Порошковый огнетушитель ОПУ-5 предназначен для тушения небольших загораний на мотоциклах, автомобилях и других машинах. Диапазон эффективного использования находится в пределах от – 50 до + 50 градусов С.
Порошковый огнетушитель ОПУ-10 предназначен для тушения небольших загораний бензина и других легко воспламеняющихся жидкостей, а также электроустановок под напряжением до 380 в. Он применяется при температуре от - 50 до + 50 градусов С.
К ручному пожарному инструменту относятся ломы, багры, топоры, лопаты, пилы и ножницы для резки проводов.
3.5. Основные правила и способы тушения пожаров, боевой техники, зданий, складов, требования безопасности при тушении пожаров.
При тушении пожара необходимо решить следующие основные задачи: спасти людей, погасить пожар, эвакуировать технику и различное имущество.
Руководитель пожара должен:
¾ правильно оценить обстановку на пожаре, быстро принять решение, четко поставить задачи личному составу и обеспечить их выполнение;
¾ организовать и поддерживать необходимые для достижения успеха условия взаимодействия между пожарной командой и подразделениями, участвующими в ликвидации пожара;
¾ определять очередность и своевременно обеспечивать быструю эвакуацию людей, боевой техники и имущества;
¾ своевременно производить вызов дополнительной помощи, подмену личного состава и оказание ему при необходимости медицинской помощи.
Вмешиваться в действия руководителя тушения пожара ЗАПРЕЩАЕТСЯ. Очередность и порядок выполнения указанных задач, их цель исходит в каждом отдельном случае из конкретной обстановки пожара, но с учетом того, что спасение людей всегда является первоочередной и главной задачей.
В первую очередь спасаются люди из помещений, которым непосредственно угрожает огнь, создается опасность возможного взрыва или обрушения конструкций, а также когда вследствие испуга находятся в состоянии паники или, потеряв сознание, не могут самостоятельно покинуть опасные места, имеется угроза распространения огня или дыма по основным путям эвакуации, предусматривается применение опасных для жизни людей огнетушащих составов и веществ.
Для спасения людей используются кратчайшие и безопасные пути: основные входы и выходы, запасные выходы, оконные проемы, люки в перекрытиях, если через них можно выйти из здания или перейти в его безопасную часть.
Основными способами спасания и эвакуации людей являются:
¾ самостоятельный выход людей в безопасное место;
¾ вывод эвакуируемых в сопровождении пожарных-спасателей;
¾ вынос людей, не имеющих возможности самостоятельно передвигаться;
¾ спуск спасаемых по стационарным и ручным пожарным лестницам, когда пути спасения отрезаны и другие способы спасения невозможны.
Порядок эвакуации техники и имущества при возникновении пожара в воинской части определяется планом противопожарной защиты.
Выбор способов и приемов прекращения огня зависит от условий и обстановки на пожаре, а также от наличия средств пожаротушения.
Успех в тушении пожара в значительной степени зависит от быстрого и своевременного ввода сил и средств на решающем направлении. Решающим направлением на пожаре считается то, на котором наиболее интенсивно распространяется огонь и наносит или может нанести наибольший ущерб, а также куда необходимо подать основные средства пожаротушения. При этом необходимо учитывать следующее:
¾ если пожар охватил отдельно стоящее здание и отсутствует угроза распространения огня на соседние, необходимо основные силы направить в места наиболее интенсивного горения;
¾ если пожар охватил часть зданий и распространяется на другие его части или соседение здания, силы и средства направляются на основные пути распространения огня;
¾ если пожар угрожает людям, то основные средства пожаротушения используются для обеспечения спасения людей;
¾ если в зоне горения находятся взрывоопасные вещества, материалы и установки, которые под воздействием температуры могут взорваться, основные силы и средства сосредотачивают на предупреждение взрыва.
При тушении пожаров в этажах казарменных, жилых и служебных зданий необходимо:
¾ произвести разведку пожара в помещениях горящего, выше и ниже расположенных этажей, а также на чердаке;
¾ установить, не осталось ли в горящих помещениях людей, и если им угрожает опасность, обеспечить их спасение;
¾ следить за состоянием горящих и соседних с ним помещений, производить контрольные вскрытия в местах, куда может проникнуть огонь;
¾ при определении очередности эвакуации имущества в первую очередь обеспечить спасение Боевого Знамени части и секретной документации, руководствуясь указаниями должностных лиц, ответственных за помещение;
¾ одновременно с эвакуацией имущества обеспечивать надежную охрану, исключающую его утрату.
Пожары боевой и автомобильной техники сопровождаются быстрым распространением огня по покрытиям зданий и машин. При тушении пожара в парке необходимо организовать выход машин своим ходом и вручную с помощью тягачей, в первую очередь, горящих машин, используя личный состав подразделений, прибывших к месту пожара.
При возникновении пожара на машине заглушить двигатель, перекрыть, если это возможно, подачу горючего и приступить к тушению огня огнетушителем, песком или кошмой. В случае возгорания двигателя и разлитого под ним топлива, вначале следует потушить горящую жидкость, а затем двигатель.
6.Технические мероприятия по поддержания БТВТ в исправности
Эксплуатация бронетанкового вооружения и техники (БТВТ) – комплекс мероприятий по использованию боевых машин, их техническому обслуживанию, хранению и транспортированию.
Эксплуатация организуется командиром воинской части, заместителем командира воинской части по вооружению и осуществляется личным составом экипажей, расчетов, эксплуатирующих машины с привлечением сил и средств технического обеспечения. Основной целью эксплуатации БТВТ в мирное и военное время является поддержание машин в постоянной готовности к боевому применению, обеспечение мероприятий боевой подготовки. В целях поддержания БТВТ в исправном состоянии в воинской части выполняется организационные и технические мероприятия.
К организационным мероприятиям относится: освежение машин; освежение шлемофонов, укрывочных брезентов, тентов, гусеничных лент, автошин, горючего, масел, смазок и специальных жидкостей в системах и агрегатах машин по истечении их гарантийных сроков службы; проведение парковых недель (дней) и парково-хозяйственных дней; организация и проведение смотров БТВТ и осмотров учебно-боевых машин; принятие мер к устранению выявленных недостатков; проведение занятий по выполнению машин в готовность к использованию по назначению (боевому применению); отработка нормативов по технической подготовке; проведение военно-технических конференций и сборов.
К техническим мероприятиям относится: своевременное, полное и качественное проведение технического обслуживания и качественная постановка машин на хранение; обеспечение работоспособности машин путем своевременного проведения на объектах боевой и строевой групп регламентированного технического обслуживание и текущего ремонта; поддержание в работоспособности состоянии паркового оборудования и средств, обеспечивающих сокращение сроков приведения машин в боевую готовность к использованию по назначению (боевому применению).
Ввод в эксплуатацию – включает прием машин воинской частью после изготовления или капитального ремонта в соответствии с установленными требованиями и закрепление этой машины за подразделением, водителем или экипажем.
Приведение объекта ВВТ в готовность к использованию по назначению означает выполнение работ по его доукомплектованию военно-техническим имуществом (например, зимними шлемофонами), боеприпасами, крепежными средствами (например, приспособлениями для крепления танков на железнодорожной платформе) и т.п., а также работ по увеличению запаса ресурса отдельных агрегатов, систем или машины в целом. Приведение машин в установленную степень готовности к использованию по назначению - заключается в проверке ее технического состояния, выполнении необходимых операций, предусмотренных эксплуатационной документацией, обеспечивающих использование машин по назначению.
Поддержание объекта ВВТ в установленной степени готовности его к использованию по назначению предусматривает выполнение как профилактических, так и восстановительных мероприятий на машинах. Поддержание машины в установленной степени готовности к использованию - состоит в выполнении установленного объема работ по техническому обслуживанию и войсковому ремонту, обеспечивающих ее исправность и работоспособность. Под готовностью машины к использованию подразумевается состояние, в котором она способна обеспечить выполнение поставленной задачи в соответствии с ее предназначением в заданное время.
Использование машин по назначению - применение ее по прямому назначению с соблюдением установленных эксплуатационной документацией норм и правил, обеспечивающих нормальную работу всех агрегатов, систем и механизмов, а также выполнение требований безопасности.
Хранение - содержание машин, прошедших специальную подготовку, в отведенных для их размещения местах в состоянии, обеспечивающем их сохранность, исправность и приведение в готовность к использованию в установленные сроки.
Транспортирование - процесс перемещения объекта ВВТ с помощью транспортных или буксировочных средств с сохранением установленной степени готовности к использованию. Он включает в себя подготовку к перевозке, перемещение с помощью различных средств к месту назначения, выгрузку и подготовку к дальнейшему использованию. В случаях длительного транспортирования на машинах могут проводиться работы профилактического и восстановительного характера, обеспечивающие поддержание их в установленной степени готовности к использованию. Транспортирование машины - включает подготовку к перевозке, доставку различными видами транспорта к месту назначения в соответствии, обеспечивающем сохранность, исправность или работоспособность, выгрузку и подготовку к дальнейшему использованию по назначению.
7. Ввод ВВТ в строй и допуск их к эксплуатации
Машины, прибывшие в часть на штатное укомплектование, вводятся в строй приказом командира части. До ввода в строй эксплуатация машин запрещается.
Готовят машину к вводу в строй экипажи (водители) под руководством командиров взвода и заместителей командиров рот по вооружению. При этом проверяются техническое состояние и укомплектованность машин и устраняются все выявленные на них недостатки. Командиры подразделений лично проверяют машины, убеждаются в их исправности и готовности. После этого отдается приказ по части о введении машин в строй. В приказе указываются: тип, марка и номер машины, в какое подразделение и в какую группу зачисляется машина, присвоенный ей номер по строевому расчету, запас ресурса до очередного среднего (капитального) ремонта на день выхода в строй, норма эксплуатации машин до конца года, звание и фамилии членов экипажа (водителя), за которыми закрепляется машина. Номер приказа и фамилии членов экипажа (водителя) заносятся в формуляр (паспорт) машины. Все члены экипажа расписываются в формуляре о принятии машины.
Машины вручаются экипажам командиром части в парке в торжественной обстановке. В боевой обстановке, а также одиночные машины в мирное время могут вручаться экипажам (водителям) командиром батальона (роты) перед строем подразделения. С этого момента ответственность за машину несет экипаж, и в первую очередь командир (водитель) машины.
Экипаж (водитель), как правило, должен всю службу проходить на одной машине. Необоснованные и невызываемые крайней необходимостью перемещения экипажа (водителя) с одной машины на другую запрещаются.
Однако в целях углубления практических навыков в использовании и обслуживании машин разрешается через год обучения менять механиков-водителей (водителей) машин учебно-боевой, учебно-строевой и транспортной группы. Смена экипажа и замена отдельных лиц отдаются приказом по части и отмечаются в формуляре. Экипажу нового состава (водителю) машина вручается командиром роты перед строем подразделения.
Эксплуатация машин осуществляется экипажами, за которыми они закреплены. При временном отсутствии механиков-водителей (водителей) к вождению машин могут допускаться другие водители, имеющие удостоверения на право вождения, о чем отдается приказ по части. К самостоятельному вождению машин допускаются лица, хорошо знающие их устройство, правила эксплуатации, имеющие достаточную практику в вождении, а также удостоверение на право вождения машин данного типа. При совершении длительного марша разрешается подмена штатного механика-водителя другим членом экипажа, имеющим удостоверение на право вождения машин данной марки. В боевой обстановке по приказанию командира подразделения или машины в случае необходимости водителя могут заменять другие военнослужащие, умеющие водить машину. Офицеры, имеющие квалификацию водителя, водят машину на занятиях по вождению в системе командирской подготовки, при обучении подчиненных и при проверке машины контрольным пробегом.
8. Единая система комплексного технического обслуживания и ремонта ВВТ включает в себя следующие виды:
а) техническое обслуживание при использовании:
- контрольный осмотр (КО);
- ежедневное техническое обслуживание (ЕТО);
- техническое обслуживание №1 (ТО-1);
- техническое обслуживание №2 (ТО-2);
- сезонное техническое обслуживание (СО);
- регламентированное техническое обслуживание (РТО);
Время и периодичность проведения технического обслуживания бронетранспортера БТР-80 при использовании представлены в таблице:
Марки машин | Продолжительность ЕТО | Техническое обслуживание №1 (ТО №1) | Техническое обслуживание №2 (ТО №2) | ||
Периодичность, км | Продолжительность, час | Периодичность, км | Продолжительность, час | ||
БТР-80 | 1,5 | 2000 | 6 | 6000 | 7 |
б) техническое обслуживание при кратковременном хранении:
- техническое обслуживание №1 при хранении (ТО-1х);
в) техническое обслуживание при длительном хранении:
- техническое обслуживание №1 при хранении (ТО-1х);
- техническое обслуживание №2 при хранении (ТО-2х);
- регламентированное техническое обслуживание (РТО).
Контрольный осмотр (КО) - проводится с целью проверки готовности к использованию систем, агрегатов, механизмов аппаратуры для обеспечения надежной работы и безопасности движения машины. КО проводится экипажами (водителями) перед выходом из парка и на марше во время остановок (привалов), перед стрельбой, занятиями и учениями.
Ежедневное техническое обслуживание (ЕТО) проводится с целью обеспечить последующую надежную работу машины при пробеге не менее 250-300 км. ЕТО проводится экипажами (водителями) с участием специалистов подразделений технического обеспечения в конце дня после каждого выхода из парка независимо от пробега (в конце суток боевых действий).ЕТО включает общий контроль технического состояния машины, дозаправку ГСМ, боеприпасами (во время боевых действий), мойку (чистку) и проверку комплектности.
Номерные ТО (ТО №1, ТО №2) проводятся с целью обеспечения надежной работы машины в пределах установленного до очередного ТО пробега (наработки). Объем, периодичность и продолжительность КО, ЕТО, ТО1 и ТО2 определяются нормативно-технической документацией (НТД) для каждого вида (типа) образца ВВТ.
Сезонное техническое обслуживание (СО) - проводится с целью подготовки машин в соответствии с условиями предстоящей эксплуатации. СО проводится экипажами (водителями) с привлечением специалистов подразделений технического обеспечения два раза в год при переводе машин на зимнюю и летнюю эксплуатацию. В объем СО входят работы номерных ТО в зависимости от наработки, а также дополнительные работы, связанные с заменой эксплуатационных материалов, предписанных НТД.
Регламентированное техническое обслуживание (РТО)_. проводится с целью поддержания боеспособности ВВТ в течении последующих 5-7 лет. РТО проводится с специально подготовленными бригадами с участием экипажей (водителей) через 5-7 лет длительного хранения ВВТ. Сущность РТО заключается в определенных технических воздействиях на механизмы, узлы, агрегаты, системы, которые содержат материалы, подверженные изменениям (старению) в процессе хранения. Номенклатура заменяемых деталей (резино-технических изделий, электронных приборов и т.д.) и технология их замены разрабатываются заводами-изготовителями машин на основе проведенных испытаний. РТО проводится под контролем и с участием представителей заводов-изготовителей.
Кроме перечисленных видов ТО на машинах проводится техническое обслуживание при подготовке к эксплуатации в особых условиях (подготовка к преодолению водных преград, эксплуатация в условиях высокогорья, подготовка вооружения к стрельбе и обслуживание после стрельбы и т. д.). Объем операций в этих случаях определяется НТД.
9.История создания БМП-2 и ее модификаций
И первыми такую потребность осознали в СССР. Приоритет в разработке и производстве самого молодого члена бронетанкового семейства принадлежит отечественным конструкторам. В США, правда, за несколько лет до запуска в серию нашего БМП-1, в ходе Вьетнамской войны, пытались создать нечто подобное, усиливая вооружение и защищенность основных армейских БТР М113 и М113А1, но ничего из этого не вышло. Как писал командир 5-й механизированной дивизии бригадный генерал Гибсон: «Личному составу приходилось постоянно напоминать, что БТР является только средством транспортировки, которое дает незначительную защиту от осколков мин и огня стрелкового оружия. 12,7 мм пулемет… предназначается для обороны или разведки огнем. Нынешний М113А1 нельзя рассматривать как штурмовую машину».
В СССР поступили по-другому. Задача перед разработчиками изначально стояла сложная: «вместить» в сравнительно небольшую массу (13 т) экипаж и десант из восьми человек, обеспечить их защиту, поставить достойное вооружение. Ко всему прочему, машина должна была быть плавающей и авиатранспортабельной. Решение нашли в новой гусеничной базе и новой компоновке: десантное отделение разместилось ближе к корме, а экипаж – в носовой части корпуса, двигатель и ходовая установка были расположены между ними.
В результате в 1966 г. из цехов Курганского машиностроительного завода вышли первые, не имеющие еще аналогов в мире, БМП-1, ознаменовав своим появлением начало нового этапа в развитии мировой бронетехники.
Боевая машина пехоты БМП-1
Эти маневренные машины с V-образным дизелем жидкостного охлаждения (специально разработанным для БМП), противопульным бронированием и малогабаритной сварной башней были по достоинству оценены в армии и пополнили вооружение войск.
Недостатки их тоже выяснились довольно быстро. Из-за того, что задачи вооружения БМП не были определены со всей четкостью, огневую мощь машины скоро признали недостаточной. Нет, конечно, основное оружие – 73-мм полуавтоматическая пушка – позволяла с уверенностью поражать на ограниченных (до 1000 м) дальностях бронированные машины, в том числе и большую часть существовавших тогда танков, но этим боевые возможности БМП, по сути, исчерпывались. В таблице представлены модификации БМП-1, выпущенных Курганским машиностроительным заводом.
Модификации БМП-1
Марка | Индекс | Принципиальные отличия |
БМП-1 | об. 765 | Сп1 и Сп2 Базовая модель. Пушка 73 мм. Масса 12,6 т (Сп1) и 13 т (Сп2) |
БМП-1 | об. 765 | Сп3 В БК введен осколочный снаряд. Масса 13,2 т |
БМП-1П | об. 765 | Сп4 ПТУР «Конкурс» вместо «Малютки», новое ППО |
БМП-1ПГ | об. 765 | Сп8 Вариант БМП-1П с автоматическим гранатометом на крыше башни |
БМП-1К | об. 773 | Командирский вариант БМП-1. Дополнительно навигационная и радиоаппаратура |
БМП-1ПК | об. 773 | Командирский вариант БМП-1П. Дополнительно навигационная и радиоаппаратура |
БМП-1Д | об. 765 | «Афганский вариант». Дополнительно АГС-17 «Пламя» и бортовые экраны |
Дальнейшим развитием концепции модернизации боевой машины пехоты стала БМП-2 – модернизированный вариант первых машин Курганского завода. 73-мм орудие сменила 30-мм автоматическая пушка, предназначенная для поражения живой силы, легкобронированных целей и вертолетов противника. Для борьбы с танками планировалось использовать ПТУРС «Конкурс».
Боевая машина пехоты БМП-2
По общей компоновке корпуса БМП-2 имеет множество сходств со своей предшественницей. Применение БМП-2, обладающей хорошей маневренностью, повышенной огневой мощью, современными средствами защиты, существенно повысило боевые возможности мотострелковых подразделений Советской Армии, с честью стоящей на защите мирных рубежей нашей Родины.
Процесс принятия БМП-2 на вооружение мог сильно затянуться. Если бы не Афганистан, эта машина могла и вовсе не увидеть свет. А когда она все-таки появилась, выяснилось, что в армии «основного противника» начинают уже поступать БМП второго поколения – американская М2 «Брэдли», английская
MCV-80 «Варриор». В таблице представлены модификации БМП-2, выпущенных Курганским машиностроительным заводом.
Модификации БМП-2
Марка | Индекс | Принципиальные отличия |
БМП-2 | об. 675 | Базовая модель. Пушка 30 мм |
БМП-2К | об. 678 | Командирский вариант БМП-2 |
БМП-2Д | «Афганский вариант». Бортовые экраны, дополнительно бронированно днище. Неплавающий. |
Ресурс модернизации БМП-1 и БМП-2 был к тому времени практически полностью исчерпан. Увеличения массы, необходимого для выполнения новых задач, поставленных перед машиной (большая огневая мощь, большая подвижность и защищенность), старая база бы просто не выдержала.
На смену БМП-2 пришла БМП-3, которую решили создавать на шасси опытного легкого плавающего танка, разработанного еще в 1975 г. для нужд воздушно-десантных войск.
Боевая машина пехоты БМП-3
Получив обозначение объект 688 (в простонародье «Чебурашка»), новая БМП была оснащена боевым модулем с 30-мм пушкой 2А42 и 2 ПУ ПТУР 9М 113 «Конкурс». Для испытаний было изготовлено два образца (заводские номера «602» и «603»). Однако к тому времени конструкторы под руководством Шипунова, возглавлявшего Тульское конструкторское бюро приборостроения, предложили абсолютно новый и достаточно оригинальный комплекс вооружения 2К23 для новой машины. В состав комплекса входит 100-мм пушка – пусковая установка 2А70 и спаренные с ней 30-мм автоматическая пушка 2А72 и 7,62-мм пулемет ПКТ. В боекомплект пушки помимо осколочно-фугасных снарядов входят противотанковые управляемые по лучу лазера ракеты 9М117 «Бастион».
На сравнительных испытаниях в Объединенных Арабских Эмиратах БМП второго поколения показали явное превосходство нашей «тройки» над американской «Брэдли» и английской «Варриор». В области боевых машин пехоты мы по-прежнему лучшие.
В таблице представлены тактико-технические характеристики боевых машин пехоты ВС РФ.
ТТХ боевых машин пехоты
Параметр | БМП-1 | БМП-2 | БМП-3 |
Полная боевая масса, т | 13 | 14 | 18,7 |
Боевой расчет, (экипаж + десант), чел. | 3+8 | 3+7 | 3+7 |
Скорость движения, км/ч – максимальная по шоссе – на плаву | 65 7 | 65 7 | 70 10 |
Запас хода по шоссе, км | 550-600 | 550-600 | 600 |
Двигатель | дизельный четырехтактный УТД-20 | дизельный четырехтактный УТД-20С1 | дизельный четырехтактный УТД-29 |
Водяной движитель | гусеничный | гусеничный | водометный |
Максимальная мощность двигателя, л.с. | 285-300 | 285-300 | 500 |
Вооружение: – пушка | 73-мм гладкоствольная 2А28 | 30-мм автоматическая пушка 2А42 | – 100-мм орудие – пусковая установка 2А70; – 30-мм автоматическая пушка 2А72 |
– пулемет, спаренный с пушкой, кол-во, калибр | 1–7,62 мм ПКТ | 1–7,62 мм ПКТ | 3–7,62 мм ПКТ |
– ПТУР | комплекс ПТУР 9М14М | комплекс ПТУР 9М111М2, 9М113 | комплекс ПТУР ПТУР 9М111М2 |
В настоящем пособии авторами затронуты вопросы назначения, технической характеристики, общего устройства и эксплуатации БМП-2. Именно эта модификация боевой машины пехоты получила всестороннее распространение не только в Вооруженных силах Российской Федерации, но и в других силовых структурах и ведомствах. Именно эта машина прошла нелегкий боевой путь в горячих точках не только нашей страны, но и всего мира, оставаясь по сей день основной боевой машиной поддержки мотострелковых подразделений.
11.Описать общие части БМП-2, их назначение, состав расчета
Боевая машина пехоты (рис. 1.1, 1.2) является гусеничной боевой машиной, имеющей вооружение, броневую защиту и высокую маневренность. Назначение машины – повысить мобильность, вооруженность и защищенность пехоты, действующей на поле боя, в условиях применения ракетно-ядерного оружия.
Рис. 1.1. Боевая машина пехоты (вид слева и спереди)
Машина вооружена 30-мм автоматической пушкой 2А42 с двухленточным питанием, стабилизированной в двух плоскостях, спаренным с пушкой 7,62-мм пулеметом ПКТ и пусковой установкой для борьбы с бронированными целями из машины и вне ее.
Рис. 1.2. Боевая машина пехоты (левый борт снят):
1 – пушка 2А42; 2 – люк механика-водителя; 3 – люк десантника; 4 – спаренный пулемет ПКТ; 5 – башня; 6 – прицел БПК-1-42; 7 – пусковая установка; 8 – укладка ПТУР;
9 – антенна радиостанции Р-123М; 10 – топливный бак; 11 – люк десанта; 12 – аккумуляторный отсек; 13 – кормовая дверь; 14 – опорный каток; 15 – магазин пушки 2А42; 16 – сиденье оператора; 17 – магазин ПКТ; 18 – сиденье десантника; 19 – сиденье механика-водителя;
20 – перегородка силового отделения; 21 – баллоны системы ППО
Вооружение, установленное в БМП, позволяет вести борьбу с различными целями, включая танки и боевые вертолеты.
На машине установлены устройства, предназначенные для защиты экипажа и оборудования внутри машины от воздействия ударной волны и проникающей радиации при взрыве ядерных боеприпасов, для защиты от химического и бактериологического оружия, а также для защиты экипажа от радиоактивной пыли при движении машины по зараженной местности. Эти устройства составляют систему защиты от оружия массового поражения.
Для постановки дымовых завес в целях маскировки машина оборудована термодымовой аппаратурой и системой пуска дымовых гранат.
Для траления мин на машину может быть установлено тралящее оборудование.
Она может преодолевать водные преграды на плаву, используя для передвижения гусеничный движитель, а также приспособлена для авиадесантирования.
Расчет машины состоит из десяти человек: экипаж три человека (командир, механик-водитель, оператор-наводчик) и семь стрелков-десантников. Десант может вести прицельный огонь из личного оружия через амбразуры машины, расположенные в десантном отделении и отделении управления.
Основными частями машины являются броневые корпус и башня, вооружение, приборы прицеливания и наблюдения, система боепитания, силовая установка, силовая передача, ходовая часть, электрооборудование и средства связи, система защиты от оружия массового поражения, пожарное оборудование, системы постановки дымовых завес и пневмооборудование.
На машине имеется возимый комплект запасных частей, инструмента и принадлежностей.
По расположению механизмов и оборудования внутри машина разделена на четыре отделения: управления, боевое, силовое и десантное.
12.Отделение управления
1.1. Отделение управления
Отделение управления расположено в носовой части корпуса машины. Оно ограничено справа перегородкой силового отделения, слева – левым бортом машины. Там расположены рабочие места механика-водителя и десантника.
Рабочее место механика-водителя оборудовано сиденьем; контрольно-измерительными приборами; приборами освещения и сигнализации; четырьмя приборами наблюдения ТНПО-170А; гирополукомпасом ГПК-59; органами управления машиной, приборами и исполнительными механизмами; аппаратом А-3 ТПУ; прибором радиационной и химической разведки; средствами пожаротушения; системой очистки приборов наблюдения.
Рабочее место десантника оборудовано сиденьем, амбразурой для стрельбы из личного оружия (в левом борту корпуса), приборами наблюдения
ТНП-165А и ТНПО-170А, аппаратом А-3 ТПУ.
Кроме того, в отделении управления расположены ФВУ, отопитель, баллон пневмосистемы, а также места для укладки ЗИП.
Общий вид отделения управления показан на рис. 1.3.
Рис. 1.3. Отделение управления
На рисунке обозначено: 1 – крыша машины; 2 – крышка люка механика-водителя; 3 – патрубок подвода воздуха из ФВУ; 4, 7, 46 – приборы
ТНПО-170А механика-водителя; 5 – кнопка звукового сигнала; 6 – центральный щиток; 8 – механизм открывания люка механика-водителя; 9 – привод жалюзи и заслонок эжектора; 10 – рукоятка привода крышки люка механика-водителя; 11 – плафон подсветки центрального щитка; 12 – переключатель поворотов ППН-45; 13 – крышка люка для доступа в силовое отделение; 14 – пульт управления дорожной сигнализации ДС; 15 – рычаг переключения передач; 16 – плафон освещения; 17 – рукоятка привода стояночного тормоза; 18 – рукоятка ручного привода подачи топлива; 19 – педаль привода подачи топлива; 20 – рукоятка удаления конденсата из влагомаслоотделителя; 21 – аптечка; 22 – рукоятка крана слива воды из двигателя; 23 – кран системы питания топливом подогревателя; 24 – клапан слива охлаждающей жидкости; 25 – рукоятка крана системы питания топливом; 26, 29 – сумки шлемофонов; 27 – сиденье десантника; 28 – баллон со сжатым воздухом; 30 – вентиль баллона; 31 – сиденье механика-водителя; 32 – педаль привода управления остановочными тормозами; 33 – педаль привода управления главным фрикционом; 34 – датчик ПРХР; 35 – рукоятка крана блокированного пневмопривода; 36 – рукоятка крана выключения главного фрикциона; 37 – гирополукомпас; 38 – рукоятка крана управления водоотражательным щитком; 39 – манометр системы пневмооборудования; 40 – рычаг включения замедленной передачи; 41 – табло ОТПУСТИ РУЧНОЙ ТОРМОЗ; 42 – бачок воздушно-жидкостной очистки; 43 – измерительный блок ПРХР; 44 – руль; 45 – блок питания прибора ТВНЕ-1ПА;
47 – замок люка механика-водителя.
13.Силовое отделение.
Силовое отделение (рис. 1.4) размещено в правой передней части корпуса и отделено от всей машины теплозвукоизоляционной перегородкой, в которой имеются люки для доступа к агрегатам.
Рис. 1.4. Силовое отделение:
1 – бортовая передача; 2 – масляный бак; 3 – расширительный бачок;
4 – маслозаправочный бачок; 5 – эжектор; 6, 7 – радиаторы
В силовом отделении расположены агрегаты силовой установки и силовой передачи с обслуживающими их системами.
Двигатель и коробка передач объединены в силовой блок, а радиатор системы охлаждения, радиатор системы смазки двигателя, радиатор системы смазки и гидроуправления силовой передачи, эжектор и воздухоочиститель – в блок охлаждения и воздухоочистки.
Справа от двигателя расположены водооткачивающий насос, маслобак с котлом подогревателя, автомат давления АДУ-2С с влагомаслоотделителем и насосный узел подогревателя.
К балкам крыши корпуса крепится блок системы охлаждения с воздухоочистителем. Кроме того, в силовом отделении размещены узлы систем, обеспечивающих работу силовой установки.
14.Боевое отделение
Боевое отделение расположено в средней части корпуса машины непосредственно за силовым отделением. Оно включает в себя башню и часть корпуса, ограниченную перегородкой силового отделения впереди и ограждениями сидений десанта сзади.
В башне в качающейся маске установлены пушка 2А42 и спаренный с ней пулемет ПКТ. На вращающемся полу смонтированы магазин ПКТ и система, обеспечивающая ленточное питание пушки бронебойно-трассирующими и осколочно-фугасными снарядами. В крыше башни между люками оператора и командира установлена пусковая установка для ПТУР. В башне оборудованы рабочие места оператора (рис. 1.5) и командира (рис. 1.6).
На рабочем месте оператора размещены: сиденье, прицел ВПК-1-42, пульт управления стабилизатором, три прибора наблюдения ТНПО-170А и один прибор ТНПТ-1, поворотный механизм башни, подъемный механизм спаренной установки, краны системы очистки прицела, аппарат А-2 ТПУ, коробка КР-60 обогрева приборов наблюдения, пульт управления системой 902В, стопор башни, баллон системы очистки приборов.
На рабочем месте командира размещены: люк командира с приборами наблюдения ТКН-3Б с осветителем ОУ-3ГА2, ТНПО-170А, ТНПТ-1; сиденье; механизм поворота люка командира; прицел 1ПЗ-3; пульт управления стабилизатора; радиостанция Р-123М; аппарат А-1 ТПУ; бачок и краны системы очистки приборов.
Кроме того, в башне установлены: блок управления и коммутации
БУ-25-2С, узлы стабилизатора, укладка ПТУР, аппаратура управления пусковой установкой 9П135М (9П135М-1).
Рис. 1.5. Место оператора
На рисунке обозначено: 1, 2, 4 – приборы наблюдения ТНПО-170А; 3 – прицел ВПК-1-42; 5 – пулемет ПКТ; 6 – кожух пушки 2А42; 7 – магазин ПКТ;
8 – пульт управления; 9 – подъемный механизм; 10 – сиденье; 11 – сумка шлемофона; 12 – поворотный механизм башни; 13 – стопор башни; 14 – указатель азимута; 15 – аппарат А-2 переговорного устройства.
В корпусе боевого отделения на правом борту установлены крепления для укладки трех ПТУР, в нише правого борта укладывается вьючное устройство пусковой установки 9П135М (9П135М-1), предусмотрены укладки для боекомплекта и ЗИП.
Рис. 1.6. Место командира
На рисунке обозначено: 1, 3 – приборы наблюдения ТНПО-170А; 2 – прибор ТКН-3Б; 4 – рукоятка привода крышки прицела 1ПЗ-3; 5 – аппарат А-1;
6 – прицел 1ПЗ-3; 7 – пульт управления; 8 – сумка для шлемофона; 9 – сиденье; 10 – уплотнение винтового рукава; 11 – уплотнение гибкого элемента; 12 – кожух пушки 2А42.
Пусковая установка 9П135М-1 – вариант исполнения 9П135М. Для обозначения обоих изделий применяется индекс 9П135М. Общий вид боевого отделения показан на рис. 1.7.
Рис. 1.7. Боевое отделение:
1 – башня; 2 – защитный колпак прицела БПК-1-42; 3 – осветитель ОУ-3ГА2; 4 – пусковая установка машины; 5 – механизм поворота люка командира; 6 – радиостанция Р-123М; 7 – ПТУР; 8 – магазин ПКТ; 9 – поворотный механизм башни; 10 – подъемный механизм спаренной установки; 11 – пушка 2А42; 12 – осветитель ОУ-3; 13 – защитная крышка прицела 1ПЗ-3; 14 – защитный колпак прибора ТКН-3Б; 15 – пусковая установка системы 902В; 16 – люк командира; 17 – люк оператора; 18 – прибор наблюдения ТНПО-170А; 19 – вентилятор отсоса газов из кожуха пушки; 20 – пулемет ПКТ; 21 – антенный ввод; 22 – фара ФГ-127;
23 – прибор наблюдения ТНПТ-1; 24 – магазин пушки 2А42
15.Десантное отделение
Десантное отделение расположено в кормовой части машины. Оно ограничено правым (рис. 1.8) и левым (рис. 1.9) бортами корпуса и разделено на две части средним топливным баком и контейнером электрооборудования.
В десантном отделении шесть рабочих мест для стрелков-десантников (по три в каждой части). Частично основанием для сидений служат боковые баки, установленные справа и слева от среднего бака. На каждом рабочем месте имеются прибор ТНПО-170А для наблюдения за местностью при движении по-боевому, амбразуры для ведения стрельбы из пулеметов ПК (передние) и автоматов АКМ (остальные), места для укладки имущества десантников.
Рис. 1.8. Десантное отделение (правый борт):
1, 3, 4 – приборы наблюдения; 2 – шаровая опора ПК; 5, 7 – шаровые опоры АКМ; 6 – труба раздачи воздуха; 8 – аппарат А-4; 9 – труба кормового водооткачивающего насоса; 10 – сумка для документов; 11 – сумка для нагрудного переключателя; 12 – трос для надевания гусеницы; 13 – кувалда; 14 – сумка с машинкой для снаряжения лент; 15 – антенна штыревая в чехле; 16, 18 – замки крепления АКМ; 17, 19 – вещевые мешки; 20 – сиденье; 21 – гильзозвеньесборник;
22 – крепление ПТУР; 23 – сумка с ЗИП двигателя; 24 – фонарь «ЗАКРОЙ ЛЮКИ»
Для выхода и входа десанта в корме машины имеются две двери. Для наблюдения за местностью в них установлены два прибора ТНПО-170А, а в левой двери еще и амбразура для стрельбы из АКМ. Над сиденьями в крыше расположены два люка для выхода десанта на плаву, для ведения огня по воздушным целям и наблюдения за местностью на марше.
В контейнере электрооборудования размещены: две аккумуляторные батареи, агрегаты электрооборудования и отопитель десантного отделения. Кроме того, в десантном отделении размещены: коробка КР-60 обогрева приборов наблюдения и стекол шаровых опор; два вентилятора отсоса пороховых газов; аппараты А-3 и А-4 ТПУ; ручной огнетушитель; водооткачивающий насос; насос ТДА; места для укладки боекомплекта (АКМ, ПК), радиостанции Р-126 (в нише правой двери) и ЗИП.
Рис. 1.9. Десантное отделение (левый борт):
1 – сумка для документов; 2 – релейная коробка КР-60 с регулятором температур РТС-27-3А;
3 – аппарат А-3 переговорного устройства; 4, 7 – шаровые опоры для автомата АКМ; 5 – труба раздачи воздуха; 6, 8, 10 – приборы наблюдения ТНПО-170А; 9 – люк; 11 – воздуховод питания двигателя воздухом; 12 – шаровая опора пулемета ПК; 13 – сумка; 14 – сумки для изделий ПГ-7В; 15 – сиденье десантное; 16 – вещевые мешки; 17 – топор; 18 – передняя рама осветителя ОУ-3ГА2; 19 – пила; 20 – крепление автомата АКМ; 21 – огнетушитель ОУ-2;
22 – сумка для нагрудных переключателей; 23 – кнопка; 24 – тренога; 25 – розетка для
переносной лампы
16.Корпус машины
Корпус является остовом, который соединяет в единое целое все агрегаты и механизмы машины, воспринимает нагрузки, возникающие при движении, преодолении препятствий и стрельбе, и, кроме того, обеспечивает необходимый запас плавучести машины. Он представляет собой коробку, сваренную из стальных броневых листов.
С внешней стороны к нижнему наклонному листу носовой части машины привариваются буксирные крюки с пружинными защелками и проушины для крепления машины при транспортировании, платики и проушины для крепления тралящего оборудования.
В верхнем наклонном листе имеется проем, который закрывается откидным ребристым листом 2 (рис. 3.1).
По бортам машины приварены ограничители 57 для уменьшения изгиба передних балансиров, отбойники 59 гусениц для исключения повреждения корпуса передних гидроамортизаторов гребнями гусениц, а также кронштейны и фланцы для крепления узлов ходовой части.
На передних наклонных листах приварены штуцера 65 для соединения пневмосистемы тралящего оборудования с пневмосистемой машины, на боковых листах – хомуты 66 для крепления штанг тралящего оборудования.
На верхних бортовых листах выполнены амбразуры для установки и ведения огня из пулеметов ПК и автоматов АКМ. Амбразуры закрываются броневыми крышками.
Крыша корпуса состоит из съемной крыши 9 и несъемных листов.
В крыше предусмотрены люки для доступа к двигателю, для входа и выхода экипажа и десанта, отверстия для заправки ГСМ и охлаждающей жидкости, для установки габаритных фонарей, воздухозаборной трубы, шахты для установки приборов наблюдения.
Днище корпуса выполнено из листов легированной стали. Для обслуживания агрегатов машины в днище имеются отверстия с пробками и лючки, закрытые крышками. Герметичность лючков и отверстий обеспечивается резиновыми прокладками. Для улучшения условий обитаемости экипажа силовое отделение изолировано от обитаемых отделений теплозвукозащитной перегородкой.
Рис. 3.1. Корпус машины:
1 – водоотражательный щиток; 2 – ребристый лист; 3 – скоба; 4 – стопор; 5 – нижний наклонный лист; 6 – пробка отверстия для заправки маслом КП; 7 – крышка люка механика-водителя; 8 – крышка люка для доступа к двигателю; 9 – съемная крыша; 10 – колпак обратного клапана выброса воды носовым откачивающим насосом; 11 – пробка отверстия для заправки масляного бака; 12 – пробка отверстия для заправки охлаждающей жидкостью;
13 – сетки над жалюзи; 14 – сетка над заслонками эжектора; 15 – перегородка силового отделения; 16 – колпак обратного клапана выброса воды из силового отделения; 17 – рукоятка лючка для выброса газов из подогревателя; 18 – днище; 19 – кольцевой воздуховод; 20 – подбашенный лист; 21 – бортовой габаритный фонарь; 22, 50 – колпаки клапанов вытяжных вентиляторов; 23, 60 – шахты для ТНПО-170А; 24 – шахта для воздухозаборной трубы; 25, 33 – пробки отверстий для заправки топливных баков; 26 – крышка люка десантного отделения; 27 – торсион; 28 – полка крыла; 29 – кормовой габаритный фонарь; 30 – колпак обратного клапана выброса воды кормовым откачивающим насосом; 31 – дверь-бак;
32 – стоп-сигнал; 34 – защитный кожух прибора ТНПО-170А; 35 – броневая крышка амбразуры для стрельбы из автомата; 36 – сектор; 37 – буксирный крюк; 38 – стопор; 39 – проушина для крепления машины при транспортировании; 40 – отбойник; 41 – отверстие для кривошипа направляющего колеса; 42 – направляющий аппарат; 43 – направляющая очистителя; 44 – задняя часть крыла; 45 – кронштейн пружинного упора; 46 – кронштейн подвески; 47 – фланец для крепления поддерживающего катка; 48, 56 – броневые крышки амбразур для стрельбы из пулемета и автоматов; 49 – кронштейн резинового упора; 51 – поручень; 52 – средние части крыла; 53 – крышка люка для доступа к ФПТ; 54 – крышка люка десантника; 55 – колпак циклона ВЗУ; 57 – ограничитель; 58 – кронштейн крепления гидроамортизатора; 59 – отбойник гусеницы; 61 – передняя часть крыла; 62 – передний габаритный фонарь; 63 – поплавок; 64 – ограждение фары; 65 – штуцера; 66 – хомут; 67, 69 – проушины; 68 – бонка;
70 – платик
В перегородке предусмотрены люки, закрытые крышками 4 (рис. 3.2), 5, 6, 11, 18 для доступа к узлам силового отделения, отверстия для тяг приводов управления, проводов электрооборудования, соединительного вала КП.
Рис. 3.2. Перегородка силового отделения:
1 – крышка для установки проходных разъемов; 2 – редуктор давления; 3 – переходная коробка; 4, 5, 6, 11, 18 – крышки люков для доступа в силовое отделение; 7 – плафон; 8 – рукоятка заслонки подогревателя; 9 – кран топливной системы; 10 – кран слива воды из двигателя; 12, 14, 15 – места прохода тяг приводов и валов; 13 – клапан слива воды из отделения управления в силовое; 16 – крышка лючка для доступа к защитной сетке воздухоочистителя;
17– защитная сетка
На перегородке со стороны боевого отделения имеется карман воздуховода, который соединен патрубком с воздухоочистителем. Патрубок закрыт сеткой 17 и крышкой 16. В нижней части кармана со стороны силового отделения имеются клапаны для слива воды, попавшей вместе с воздухом.
Кроме того, на корпусе приварены другие детали для крепления оборудования машины и детали, обеспечивающие жесткость корпуса.
17.Крылья корпуса
Крылья служат для повышения запаса плавучести, а вместе с направляющим аппаратом – для повышения скорости движения машины на плаву.
Каждое крыло состоит из трех частей 44, 52, 61 (рис. 3.1) коробчатого типа, выполненных из листов алюминиевого сплава, и поплавка 63 из стальных листов.
Для сохранения запаса плавучести машины (при повреждении или пробитии листов крыльев) внутренние полости крыльев и поплавков заполнены водонепоглощающим материалом.
Крылья крепятся к корпусу болтами с откидными шайбами, а между собой части крыльев соединяются планками и болтами.
Направляющий аппарат 42 состоит из корпуса и пяти жестко закрепленных на нем лопаток. Аппарат крепится к борту и к полке корпуса.
18.Водоотражательный щиток
Щиток предназначен для предохранения носовой части машины от заливания водой и для создания дополнительной подъемной силы при движении на плаву. Он представляет собой алюминиевый штампованный лист и крепится петлями к нижнему наклонному листу корпуса.
Подъем и опускание водоотражательного щитка (рис. 3.7) производится пневмоцилиндрами через систему рычагов, установленных на бортах машины. Воздух в пневмоцилиндры подается краном управления водоотражательным щитком. Рукоятка 38 (рис. 1.3) крана имеет два фиксированных положения – ПОДН. и ОПУЩ., соответствующих поднятому и опущенному положениям щитка.
Конструкция левого и правого рычажных механизмов управления водоотражательным щитком одинакова. При переводе рукоятки крана в положение ПОДН. воздух под давлением поступает в полость а (рис. 3.7) пневмоцилиндра 6. Поршень начинает перемещаться, шток 7 втягивается и связанная с ним рейка 8 проворачивает зубчатый сектор 10, установленный на шлицевом конце вала 12, против хода часовой стрелки.
Когда рукоятка 38 (рис. 1.3) крана будет переведена в положение ОПУЩ., воздух поступит в полость б (рис. 3.7) пневмоцилиндра, шток 7 выдвинется, рейка 8 провернет зубчатый сектор 10 по ходу часовой стрелки и рычаги 15 и 17, воздействуя на щиток, складывают его.
Рис. 3.7. Водоотражательный щиток:
1, 3 – угольники; 2, 15, 17 – рычаги; 4 – пружина; 5, 9, 19 – кронштейны; 6 – пневмоцилиндр; 7 – шток поршня; 8 – рейка; 10 – зубчатый сектор; 11 – втулка; 12 – вал; 13 – верхний наклонный лист крыши; 14 – упор; 16, 20 – пальцы; 18 – петля; 21 – накладка; 22 – водоотражательный щиток; 23 – поршень; а, б – полости пневмоцилиндров
19.Предназначение силовой установки и систем входящих в нее
Силовая установка является источником механической энергии, приводящей машину в движение. В нее входит двигатель УТД-20С1 с обслуживающими его системами: питания топливом, питания воздухом, смазки, охлаждения, подогрева и пуска.
20.Двигатель, назвачение и краткая характеристика
На БМП-2 установлен двигатель УТД-20С1 (рис. 4.1), который представляет собой шестицилиндровый V-образный четырехтактный быстроходный бескомпрессорный дизель жидкостного охлаждения со струйным распыливанием топлива. Мощность от двигателя отбирается на силовую передачу с носка коленчатого вала через маховик, а на компрессор – с противоположного конца коленчатого вала через вал отбора мощности.
На машине используется 6-цилиндровый 4-тактный бескомпрессорный дизель УТД-20С1 жидкостного охлаждения с непосредственным впрыском. Его мощность 210...221 кВт. Масса сухого двигателя около 700 кг. Общая вместимость топливных баков 460 литров. В зимнее время используется зимнее или арктическое, а летом летнее дизельное топливо. Удельный расход топлива при максимальной мощности составляет 238 г/кВт.ч. В системе смазки применяется масло МТ-16п, МТЗ-10п или М-16ИХП-3. Заправочная вместимость системы 58 л. Удельный расход масла при частоте вращения коленчатого вала 2200 об./мин не более 10,9 г/кВт.ч. Для облегчения пуска в холодное время в системе охлаждения имеется форсуночный подогреватель с жаротрубным котлом, двигатель оборудован бесфорсуночным факельным подогревателем (БФП) впускного воздуха. Основным способом пуска является пуск сжатым воздухом, дополнительным – с помощью электростартера. Предусмотрен клапанный автоматический механизм защиты двигателя от попадания воды. Клапан взводится в исходное положение ручным приводом.
Тип | Шестицилиндровый четырехтактный бескомпрессорный дизель жидкостного охлаждения, с воспламенением от сжатия, с непосредственным впрыском топлива |
Марка | УТД-20С1 |
Максимальная мощность при 2600 об/мин, кВт (л.с.) | 210-221 (285-300) |
Максимальный крутящий момент при 1500-1600 об/мин, Н.м (кгс.м) | 883-1030 (90-105) |
Степень сжатия | 15,8 |
Число цилиндров | 6 |
Расположение цилиндров | V-образное под углом 120° |
Диаметр цилиндра, мм | 150 |
Ход поршня, мм | 150 |
Порядок работы цилиндров | 1л-1пр-2л-2пр-3л-3пр |
Рабочий объем цилиндров двигателя, л | 15,9 |
Минимально устойчивые обороты на холостом ходу, об/мин. | 700 |
Максимально допустимая частота вращения коленчатого вала на хо- лостом ходу, об/мин. | 2900 |
Эксплуатационная частота враще- ния коленчатого вала, об/мин. | 1500–2600 |
Удельный расход масла при 2200 об/мин, г/кВт.ч (г/л. с-ч), не более | 10,9 (8) |
Габаритные размеры, мм: длина | 790 |
ширина | 1150 |
высота | 742 |
Масса сухого двигателя, кг | 665+5 % |
Гарантийный срок службы, ч | 500 |
21.Общее устройство УТД-20С1
В машине двигатель имеет переднее продольное расположение (маховиком вперед) и с главным фрикционом, коробкой передач и планетарными механизмами поворота образует единый силовой блок машины. Крепление силового блока к корпусу машины осуществляется на трех опорах: на двух бугелях и одной упругой опоре. Бугели расположены в передней части силового отделения и на них опираются цилиндрические картеры планетарных механизмов поворота, которые закрепляются в бугелях с помощью болтов верхними наметками.
Наименование блоков (левый и правый), а также нумерация цилиндров ведутся со стороны, противоположной маховику.
Остовом двигателя является V-образный блок-картер тоннельного типа с углом развала блоков 120°. Каждый блок состоит из трех цилиндров, которые имеют общую головку. Внутри блоков вокруг гильз цилиндров, а также внутри головок имеются полости охлаждения, сообщающиеся между собой. В головках цилиндров установлено по четыре клапана на цилиндр: два впускных с внешней стороны и два выпускных со стороны развала блоков. Клапаны приводятся в действие от распределительных валов, кулачки которых действуют непосредственно на тарелки клапанов. Механизм газораспределения каждого блока цилиндров закрывается крышкой.
Воздух поступает в цилиндры через впускные коллекторы. Продукты сгорания удаляются из цилиндров через выпускные коллекторы.
Рис. 4.1. Двигатель (вид со стороны маховика):
1, 7, 30 – трубопроводы подвода масла к механизму газораспределения; 2 – головка блока; 3 – штуцер отвода охлаждающей жидкости; 4 – выпускной коллектор; 5 – крышка головки блока; 6 – топливный фильтр тонкой очистки; 8, 19 – трубопроводы отвода топлива и воздуха; 9 – топливные шланги; 10 – топливные трубки высокого давления; 11 – топливный насос; 12 – подвод топлива к топливоподкачивающему насосу; 13 – стержень замера уровня масла в регуляторе; 14 – топливоподкачивающий насос; 15 – регулятор топливного насоса; 16 – трубопровод подвода топлива к топливному насосу; 17 – центробежный масляный фильтр; 18 – рычаг управления топливным насосом; 20 – штуцер отвода пара; 21 – крышка лючка; 22 – впускной коллектор; 23 – пробка отверстия слива масла из коллектора; 24 – шланг подвода воздуха к генератору; 25 – генератор; 26 – вентилятор генератора; 27 – трубопроводы воздухoпуска; 28 – трубопровод подвода масла к воздухораспределителю; 29 – воздухораспределитель; 31 – шестерня стартера; 32 – шпильки крепления коробки передач; 33 – маховик коленчатого вала; 34 – сапун; 35 – крышка муфты опережения угла подачи топлива; 36 – стрелка-указатель; 37 – блок-картер; 38 – крышка; 39 – шланг подвода масла к центробежному фильтру; 40 – фильтр грубой очистки масла; 41 – штуцер для подсоединения шланга агрегата консервации АКД-1; 42 – трубки объединенного слива топлива из форсунок; 43 – штуцер отвода масла к радиатору; 44 – штуцер отвода масла к фильтру; 45 – масляный насос;
46 – штуцер подвода масла из маслобака; 47 – водяной насос; 48 – кран слива охлаждающей
жидкости
22.Кривошипошатунный механизм
Коленчатый вал устанавливается в расточке блок-картера на четырех роликовых подшипниках. Со стороны механизма передач к коленчатому валу крепится маховик, с противоположной стороны с помощью шлицев соединяется вал дополнительного отбора мощности для привода воздушного компрессора машины.
На шатунных шейках коленчатого вала смонтированы вильчатые шатуны, работающие в левом блоке. На нижние головки вильчатых шатунов навешиваются внутренние шатуны, работающие в правом блоке.
Рис. 4.2. Установка силового блока в машине:
1 – двигатель; 2 – задняя опора силового блока; 3 – передняя опора силового блока;
4 – кронштейн задней опоры; 5 – коробка передач
Любой поршневой двигатель внутреннего сгорания состоит:
– из кривошипно-шатунного механизма (КШМ);
– газораспределительного механизма (ГРМ);
– механизма передач.
Особенностью двигателя УТД-20С1 (УТД-20) является наличие у него еще одного механизма – уравновешивающего.
Кривошипно-шатунный механизм служит для восприятия давления газов и преобразования возвратно-поступательного движения поршней во вращательное движение коленчатого вала.
КШМ составляет основу конструкции двигателя и состоит из блок-картера, головок блоков, коленчатого вала с маховиком, шатунных и поршневых групп, вала отбора мощности.
Блок-картер (рис. 4.3) предназначен для монтажа всех деталей, узлов и служит силовым остовом двигателя. Блок-картер отливается совместно с рубашками цилиндров с углом развала блоков 120° и представляет собой жесткую монолитную конструкцию тоннельного типа. Внутри блок-картер разделен оребренными поперечными перегородками на три цилиндровых отсека 1 и полость 2 для установки шестерен механизма передач. В тоннель, образованный расточками в перегородках, на роликовых коренных подшипниках устанавливается коленчатый вал.
В нижней части перегородок параллельно оси коленчатого вала сделаны расточки 19 для монтажа вала уравновешивающего механизма.
С левой и правой сторон блок-картера сделано по три люка 22 и 16 для монтажа шатунов.
С правой стороны блок-картера обработаны фланцы для монтажа масляного насоса и нагнетающего патрубка водяного насоса.
С левой стороны блок-картера выполнено ложе 24 для монтажа стартера. К приливу 27 монтируется генератор.
Со стороны переднего торца на блок-картере имеется фланец, на который устанавливается стакан первого коренного подшипника и передняя крышка 17.
Рис. 4.3. Блок-картер:
а – вид спереди; б – вид сзади; 1 – цилиндровый отсек; 2 – полость механизма передач;
3 – водоперепускные отверстия; 4 – сапун; 5 – шпильки крепления масляного центробежного фильтра; 6 – отверстие подвода масла в главную масляную магистраль; 7 – полукруглый прилив блок-картера; 8 – штуцер отвода масла к газораспределительному механизму; 9 – штуцер отвода масла к ТНВД и воздушному компрессору; 10 – шпильки крепления топливного фильтра; 11 – штуцер датчика манометра; 12 – главная масляная магистраль; 13 – полубугель; 14 – анкерные шпильки; 15 – прилив блок-картера для сшивных шпилек; 16, 22 – монтажный люк; 17 – передняя крышка; 18 – стакан первого коренного подшипника; 19 – опора подшипника уравновешивающего механизма; 20, 23, 25 – полости для охлаждающей жидкости; 21 – опора второго коренного подшипника; 24 – ложе для монтажа стартера; 26 – гильза цилиндра; 27 – отверстие для привода генератора; 28 – уплотняющее медное кольцо; 29 – резиновые уплотнительные кольца; 30 – опоры подшипников осей шестерен механизма передач; 31 – центрирующий фланец для картера коробки передач; 32 – шпильки крепления
картера коробки передач
Сверху по оси развала блок-картера выполнен прилив 7 с расточкой внутри. В эту расточку устанавливается муфта опережения впрыска топлива. Продолжение этой расточки является опорой корпуса. Вторая опора ТНВД – полубугель 13 с двумя резьбовыми отверстиями. На шпильках 10 крепится блок топливных фильтров. Четырьмя шпильками 5 крепится блок масляных фильтров. Через отверстие 6 поступает масло от фильтра в главную масляную магистраль 12. Сверху на приливе имеются два резьбовых отверстия 8 и 9 для отвода масла к механизму газораспределения, топливному насосу и воздушному компрессору машины. С торца прилива установлен штуцер 11 датчика манометра.
В каждом блоке выполнено по три расточки, в которые вставляются гильзы 26 цилиндров. Между наружной поверхностью гильзы и внутренней поверхностью расточки образуется кольцевая полость 25 для протока охлаждающей жидкости.
Гильзы 26 цилиндров изготовлены из высоколегированной стали. Внутренняя поверхность гильз азотируется. В верхней части гильзы имеется бурт с кольцевыми канавками для установки медного уплотнительного кольца 28 газового стыка.
Для перепуска воды из охлаждающих полостей гильз цилиндров в охлаждающую полость головок блоков на верхних плоскостях блоков выполнено по пятнадцать отверстий 3. Эти отверстия уплотняются резиновыми кольцами, надетыми на латунные трубки.
В верхние плоскости блоков ввернуто по восемь анкерных шпилек 14 для крепления головок блоков. С обеих сторон блоков имеются приливы 15 с отверстиями для сшивных шпилек головок блоков.
Сапун предназначен для сообщения внутренней полости блок-картера с атмосферой. Корпус сапуна выполнен в виде сварного цилиндра, внутри которого помещена проволочная канитель. Сапун закрыт крышкой.
На стенке заднего торца блок-картера имеется большой фигурный фланец 31 (рис. 4.3) со шпильками 32 для крепления картера коробки передач. С этой же стороны в блок-картере имеются горизонтальные расточки 30 для монтажа осей и подшипников шестерен механизма передач. В верхней части задняя стенка блок-картера переходит в коробку, связывающую блоки цилиндров.
Головка блока 14 (рис. 4.4) отливается из алюминиевого сплава. Нижняя плита вместе с верхней и боковыми стенками образует замкнутую полость, внутри которой расположены прилитые к боковым стенкам и нижней плите головки впускные 15 и выпускные 4 каналы, колодец для монтажа форсунки.
Пространство между стенками, каналами и колодцем форсунки служит водяной рубашкой охлаждения головки. Головки блоков устанавливаются на выступающие над плоскостью блок-картера бурты гильз и стягиваются с блоком восемью анкерными и двенадцатью сшивными шпильками 18 каждая.
Рис. 4.4. Головка блока:
1 – седла клапанов; 2 – уплотняющее медное кольцо; 3 – выпускной клапан; 4 – выпускное окно; 5 – пароотводной угольник; 6 – крышка головки блока; 7 – выпускной распределительный вал; 8 – крышка лючка; 9 – впускной распределительный вал; 10 – нажимной тарель клапана; 11 – замок тарели; 12 – направляющая втулка клапана; 13 – пружины клапана;
14 – головка блока; 15 – впускное окно; 16 – пусковой клапан; 17 – впускной клапан;
18 – сшивная шпилька
Стык между плоскостью головки и буртами гильз уплотняется индивидуальными медными кольцами 2. В нижней плоскости головки расточены три камеры сгорания, в каждой из которых имеются четыре отверстия, соединяющие камеру с впускными 15 и выпускными 4 каналами. В расточки этих отверстий запрессованы стальные седла 1 клапанов. К внутренним коническим поверхностям седел плотно прилегают фаски клапанов 3 и 17.
По оси каждой камеры сгорания расточены отверстия для установки форсунок. Со стороны крепления впускного коллектора, ниже окна, на оси каждого цилиндра установлены пусковые клапаны 16 системы воздушного пуска двигателя.
Охлаждающая жидкость в рубашку головки подводится снизу из рубашечного пространства блок-картера. Охлаждающая жидкость из рубашки головки отводится через штуцер, который ввернут в головку в районе третьего цилиндра, а пар – через пароотводной угольник 5.
На верхней плоскости головки установлены четыре подшипника распределительных валов газораспределительного механизма.
Головка блока закрыта сверху крышкой 6. Три люка на верхней полости крышки головки, закрываемые штампованными крышками 8, обеспечивают возможность установки и съема форсунок без снятия крышки головки. По оси штампованных крышек выполнены отверстия напротив форсунок для монтажа трубок объединенного слива топлива, просочившегося через форсунки. На боковой стенке крышки расположены три прилива с отверстиями для установки штуцеров трубопроводов высокого давления, по которым топливо подается к форсункам.
Коленчатый вал 13 (рис. 4.5) – вращающаяся часть кривошипно-шатунного механизма. В процессе работы двигателя он воспринимает нагрузки через шатун и поршень от давления газов.
Коленчатый вал – трехколенный, четырехопорный, изготовлен из высококачественной легированной стали методом штамповки.
Три шатунные шейки вала расположены под углом 120° друг относительно друга. Шатунные шейки и коренные опоры соединены между собой щеками эллиптической формы. На продолжениях первой и второй щек крепятся противовесы 3. С одной стороны к валу крепится маховик 6, а с другой в полость первой коренной опоры запрессован хвостовик 17. На первую коренную опору устанавливается упорный роликовый подшипник 1, внутреннее кольцо которого прижато к фланцу 2. На наружное кольцо подшипника надевается стакан. Наружное кольцо стопорится в стакане разрезным упругим кольцом.
Остальные три опоры вала являются беговыми дорожками для роликов коренных радиальных подшипников 4. Коленчатый вал монтируется в сборе с коренными подшипниками и передним стаканом в нагретый до 80–90 °С блок-картер.
В шатунных шейках коленчатого вала имеются полости 5, которые сообщаются между собой наклонными отверстиями.
Во внутреннюю полость коленчатого вала масло подводится от масляного фильтра двигателя через канал главной масляной магистрали и отверстия в стакане первого подшипника. Из полости стакана масло проходит внутрь коленчатого вала и по отверстиям в нем – в полости шатунных шеек.
Для подвода масла к трущимся поверхностям вкладышей шатунов в шатунных шейках выполнены отверстия 14. Со стороны носка на коленчатый вал установлена шестерня 8, от которой через механизм передач осуществляется привод узлов и агрегатов, обеспечивающих работу двигателя.
Маховик 6 предназначен: для повышения равномерности хода двигателя; прокрутки коленчатого вала во время пуска двигателя электрическим стартером; облегчения проверки и регулирования в условиях эксплуатации и ремонта машины фаз газораспределения, воздухораспределителя и угла опережения подачи топлива (с помощью градуировки). Кроме того, маховик, имеющий противовес, является одним из элементов уравновешивающего механизма.
Рис. 4.5. Коленчатый вал:
1 – подшипник первой коренной опоры; 2 – фланец; 3 – противовесы коленчатого вала; 4 – подшипники коренных опор; 5 – полости шатунных шеек; 6 – маховик; 7 – штифт; 8 – шестерня коленчатого вала; 9, 11, 16 – подшипники вала уравновешивающего механизма; 10 – шестерня-противовес; 12 – вал уравновешивающего механизма; 13 – коленчатый вал; 14 – отверстие для смазки подшипников шатунов; 15 – передний противовес; 17 – хвостовик для вала отбора мощности
Маховик изготовлен из стали. По наружному контуру маховика нарезаны зубья, а на ободе нанесена градуировка с ценой деления один градус поворота коленчатого вала. Маховик крепится к хвостовику коленчатого вала в строго определенном положении, для чего один из фиксирующих штифтов 7 расположен на большем радиусе, чем другие.
Шатун передает усилия от поршня на коленчатый вал, совершает сложное движение, так как участвует в преобразовании возвратно-поступательного движения поршня во вращательное движение коленчатого вала.
На двигателе УТД-20С1 устанавливаются шатуны центрального типа. Узел состоит из вильчатого а и внутреннего б шатунов (рис. 4.6). Верхние головки вильчатых шатунов соединяются с поршнями левого блока, а внутренних – с поршнями правого блока, нижняя головка вильчатого шатуна монтируется на шатунной шейке коленчатого вала, а по ее наружной поверхности работает нижняя головка внутреннего шатуна.
Рис. 4.6. Шатуны и поршни:
а – вильчатый шатун; б – внутренний шатун; 1, 12 – штифт; 2 – крышка вильчатого шатуна;
3 – вкладыши вильчатого шатуна; 4 – проставка; 5 – стержень вильчатого шатуна; 6 – бронзовая втулка; 7 – поршневой палец; 8 – заглушка поршневого пальца; 9, 16 – болт; 10 – гайка; 11 – шплинт; 13 – крышка внутреннего шатуна; 14 – вкладыши внутреннего шатуна; 15 – стержень внутреннего шатуна
Вкладыши являются подшипниками скольжения шатунов. Они изготавливаются из стали, внутренняя поверхность вкладышей залита тонким слоем свинцовистой бронзы и для лучшей приработки они освинцованы. Половинки вкладышей фиксируются от проворачивания штифтами 1 и 12. Окончательная расточка вкладышей производится после установки их в головки шатунов.
В верхние головки вильчатых и внутренних шатунов запрессованы бронзовые втулки 6, служащие подшипниками для поршневых пальцев 7. Палец смазывается разбрызгиванием масла через шесть отверстий в верхней головке шатуна.
Поршневая группа служит для восприятия давления газов и передачи его через шатун коленчатому валу. Поршневая группа состоит из поршня, поршневых колец, поршневого пальца и заглушек.
Поршень 1 (рис. 4.7) отштампован из алюминиевого сплава. Для уменьшения тепловой нагрузки на днище поршня нанесен гальваническим способом тонкий твердый теплоизоляционный слой.
Рис. 4.7. Поршневая группа:
а – выемка; б – маслосточные отверстия; 1 – поршень; 2 – поршневой палец;
3 – бронзовая заглушка; 4 – уплотняющие кольца; 5 – комбинированные кольца;
6 – маслосбрасывающее кольцо
Днищу поршня придана специальная форма, способствующая эффективному смесеобразованию и сгоранию впрыскиваемого топлива. С внутренней стороны на юбке поршня имеются две бобышки. В расточки бобышек при сочленении поршня с шатуном вставляется поршневой палец 2.
Для уменьшения веса поршня с внутренней и наружной сторон юбки выполнены выемки а.
По поверхности поршня проточены пять канавок, четыре из которых расположены выше отверстия под поршневой палец, а одна – ниже. Четвертая и пятая канавки имеют фаски с маслосточными отверстиями б. В канавки поршня устанавливаются поршневые кольца.
Два верхних кольца 4 – уплотняющие, стальные, трапецеидального сечения, поверхность которых покрыта хромом.
Третье и четвертое кольца 5 комбинированные, т. е. наряду с уплотнением от прорыва газов служат для удаления лишнего масла с зеркала гильз цилиндров.
Комбинированные кольца конического сечения изготовлены из специального чугуна. Кольца покрыты тонким слоем твердого хрома.
Пятое кольцо 6 – маслосбрасывающее, также изготавливается из специального чугуна.
Поршневой палец 2 – плавающего типа, стальной, цементированный по наружной поверхности, внутри пустотелый. В бобышки поршня палец устанавливается с натягом. С обеих сторон в поршневой палец устанавливаются бронзовые заглушки 3, ограничивающие его осевое перемещение и предохраняющие зеркало цилиндра от задира торцами пальца.
Вал отбора мощности служит для частичной передачи мощности от двигателя на привод воздушного компрессора машины.
Вал отбора мощности установлен со стороны переднего торца двигателя. Он соединен наружными шлицами с хвостовиком коленчатого вала, а внутренними – с валом привода компрессора. Опорами вала являются с одной стороны хвостовик коленчатого вала, с другой – радиально-упорный шариковый подшипник, установленный в проставке.
Проставка вместе с крышкой крепится к стакану первого коренного подшипника коленчатого вала.
23.Механизм газораспределения
Механизм газораспределения служит для своевременного открытия и закрытия впускных и выпускных клапанов с целью наполнения цилиндров свежим зарядом и выпуска отработавших газов в соответствии с диаграммой фаз газораспределения и порядком работы цилиндров двигателя.
Механизм газораспределения двигателя УТД-20С1 (рис. 4.8) выполнен с верхним расположением клапанов и верхним расположением распределительных валов, т.е. и клапаны, и распредвалы смонтированы на головках блоков.
Рис. 4.8. Механизм газораспределения
Механизм газораспределения состоит из клапанов впуска 17 (рис. 4.4) и выпуска 3 с тарелями 10, пружинами 13 и замками 11, распределительных валов 7 и 9 с шестернями привода и регулировочными муфтами.
На каждый цилиндр в головке блока установлено два впускных и два выпускных клапана. Клапаны впуска и выпуска отличаются один от другого размерами головок и материалами.
В стержне 1 (рис. 4.9) клапана выполнено резьбовое отверстие для ввертывания тарели 5 клапана. Резьбовое соединение позволяет устанавливать необходимый зазор между тарелью клапана и затылком кулачка распределительного вала при регулировке фаз газораспределения. Этот зазор должен быть в пределах 2,24–2,34 мм.
Положение тарели после регулирования фиксируется замком 4. Замок посажен на трехгранный конец стержня клапана.
Впускной и выпускной распределительные валы установлены в четырех подшипниках на верхней плоскости головки цилиндров.
Рис. 4.9. Клапанная группа:
а – схема расположения кулачка при замере и регулировании; 1 – стержень;
2, 3 – пружина; 4 – замок; 5 – тарель клапана
На концах распределительных валов монтируются шестерни, находящиеся между собой в зацеплении. Шестерни распределительных валов получают вращение от механизма передач. Шестерни соединены с распределительными валами регулировочными втулками и прижаты к упорным буртам валов гайками, которые фиксируются стопорными кольцами. Снаружи регулировочные втулки имеют треугольный шлиц, а внутри – прямоугольный и служат для регулировки фаз газораспределения.
Каждый распределительный вал имеет по три пары кулачков. Профили впускных и выпускных кулачков одинаковы.
Распределительные валы полые, канал внутри служит маслопроводом. Для выхода масла к подшипникам в каждой опоре и шейке вала выполнено отверстие. В затылках кулачков выполнены отверстия для смазки кулачков и тарелей клапанов.
Масло к распределительным валам подводится через канал в оси промежуточной шестерни, вертикальный канал в головке блока и каналы в упорном подшипнике.
Механизм передач (рис. 4.10) служит для передачи вращения от коленчатого вала к распределительным валам механизма газораспределения, валу уравновешивающего механизма и навесным агрегатам, обеспечивающим работу самого двигателя. Он состоит из прямозубых цилиндрических шестерен, установленных на подшипниках качения в специальной полости блок-картера. Шестерни изготовлены из легированной стали и смазываются разбрызгиванием маслом, которое сливается из-под крышек, закрывающих газораспределительные механизмы правой и левой головок блоков.
Привод всего механизма передач осуществляется от шестерни 8 коленчатого вала 9.
От этой шестерни приводится во вращение шестерня-противовес 7 вала уравновешивающего механизма с передаточным отношением, равным единице.
Рис. 4.10. Механизм передач
На рисунке обозначено: 1 – шестерни распределительных валов; 2 – промежуточные шестерни; 3 – блок шестерен датчика электрического тахометра;
4 – шестерня привода топливного насоса высокого давления; 5 – шестерни воздухораспределителя; 6 – шестерня привода генератора; 7 – шестерня-противовес вала уравновешивающего механизма; 8 – шестерня коленчатого вала; 9 – коленчатый вал; 10 – шестерня привода масляного и водяного насосов
Привод шестерни 1 распределительных валов газораспределительного механизма к блоку шестерен 5 воздухораспределителя и шестерни 4 топливного насоса высокого давления осуществляется через ряд промежуточных шестерен 2 со строго определенным передаточным отношением, равным 0,5. Такое передаточное отношение объясняется тем, что у двигателя УТД-20С1 весь рабочий цикл происходит за четыре такта, т. е. за два оборота коленчатого вала.
Привод блока шестерен 3 датчика электрического тахометра осуществляется через ряд промежуточных шестерен также с передаточным отношением 0,5.
Привод шестерни 10 масляного и водяного насосов и шестерни 6 привода генератора осуществляется через промежуточные шестерни с передаточным отношением 1,2 и 2,562 соответственно.
Для регулирования угла опережения впрыска топлива шестерня 4 соединяется с муфтой привода ТНВД с помощью регулировочной втулки. Втулка имеет такое же устройство, как и регулировочные втулки, установленные на распределительных валах газораспределительного механизма.
Уравновешивающий механизм (рис. 4.5) предназначен для частичного уравновешивания моментов от сил инерции вращающихся и возвратно-поступательно движущихся масс, появившихся в результате угла развала блок-картера в 120°.
Полного уравновешивания момента от сил инерции возвратно-поступательно движущихся масс этот уравновешивающий механизм не обеспечивает.
Подшипники дополнительного вала уравновешивающего механизма смазываются разбрызгиванием.
24.Система питания двигателя топливом
Система питания двигателя топливом (рис. 4.11) предназначена для хранения, очистки и подачи топлива в двигатель.
Техническая характеристика. В системе питания двигателя применяется следующее топливо: летом – дизельное, летнее (ДЛ-0,2-40) или керосин ТС-1; зимой – дизельное, зимнее (ДЗ-0,2 минус 35, ДЗ-0,2 минус 45), арктическое
(А-0,2) или керосин ТС-1; всесезонно – керосин Т-1, ТС-1, но при этом продолжительность работы двигателя не должна превышать 150 ч. Средний расход топлива на 100 км составляет 92 л, запас хода по топливу при движении по шоссе – 550–600 км.
Рис. 4.11. Система питания двигателя топливом:
1 – фильтр тонкой очистки топлива; 2 – двигатель; 3 – топливоподкачивающий насос; 4 – форсунка; 5 – топливный насос подогревателя; 6 – насосный узел подогревателя; 7 – фильтр грубой очистки топлива; 8 – правый топливный бак; 9, 22 – дренажные трубки; 10 – топливоподкачивающий насос (БЦН); 11 – топливный бак; 12 – дренажный клапан; 13, 18 – трубопроводы; 14 – заправочная горловина; 15 – трубопроводы дренажной системы; 16 – правый дверной топливный бак; 17 – левый дверной топливный бак; 19 – крышка лючка бака; 20, 29, 35 – пробки; 21 – левый топливный бак; 23 – топливомер; 24 – трубка; 25 – топливный кран; 26 – топливный кран подогревателя; 27 – трубки объединенного слива топлива из форсунок; 28 – клапан слива топлива из бака; 30 – пробка заправочной горловины;
31 – сетчатый фильтр; 32 – заправочная горловина; 33 – соединительный рукав; 34 – патрубок; 36 – сетчатый фильтр; 37 – корпус крана; 38, 41 – пружины; 39, 44 – уплотнительные
кольца; 40 – эксцентрик; 42 – рукоятка; 43 – шток клапана; 45 – клапан
Устройство системы: топливные баки 8, 11, 16, 17, 21, топливоподкачивающий насос 10 БЦН-1 топливных кранов 25 и 26, фильтра 7 грубой очистки, дренажной системы с клапаном 12 и топливной системы двигателя (топливоподкачивающего насоса, фильтра тонкой очистки, насоса высокого давления, всережимного регулятора, автоматической муфты угла опережения подачи топлива, форсунок и системы объединенного слива топлива из форсунок), топливомер 23.
Трубопроводы системы питания и дренажной системы окрашены в желтый цвет.
Топливные баки служат для хранения и транспортирования топлива в машине. Основной бак 11 (рис. 4.11) и дополнительные баки 8 и 21 размещены в десантном отделении. Основной топливный бак делит десантное отделение на две части. Дополнительные баки-сиденья 8 и 21 расположены с обеих сторон основного топливного бака. Полости кормовых дверей являются также дополнительными баками 16 и 17. Основной топливный бак и дверные баки имеют заправочные горловины. Дополнительные топливные баки соединены трубопроводами между собой и с основным баком. Топливные баки через дренажные трубы 9, 15, 22 и дренажный клапан 12 сообщаются с атмосферой. Общая вместимость топливных баков – 462 л.
Основной и дополнительные баки 8 и 21 сварены из алюминиевых листов. Топливные баки 8, 11 и 21 крепятся болтами к балкам днища корпуса машины через резиновые прокладки.
Забирается топливо в двигатель из основного топливного бака 11, а так как баки соединены между собой, выработка топлива производится из всех баков одновременно. Сливается топливо через клапан 28 основного топливного бака 11.
Топливомер служит для определения количества топлива в топливных баках. Он представляет собой трубку из органического стекла, которая вставлена в металлический кожух с делениями. Цена каждого деления 50 л. Топливомер находится с левой стороны передней части основного бака и соединен с ним трубопроводами.
Топливоподкачивающий насос БЦН 10 (рис. 4.12) – центробежного типа, служит для заполнения топливом питающей магистрали перед пуском двигателя, а также для удаления воздуха из этой магистрали через дренажную систему.
Рис. 4.12. Центробежный топливоподкачивающий насос БЦН
На рисунке обозначено: 1 – гайка; 2 – пропеллер; 3 – шпонка; 4 – крышка;
5 – крыльчатка; 6 – вал электродвигателя; 7 – втулка; 8 – манжета; 9 – опорный конус; 10 – корпус насоса; 11 – втулка лабиринтного уплотнения; 12 – электродвигатель; 13 – розетка разъема; 14 – пробка; 15 – отражатель; 16 – пружина манжеты; 17 – гайка.
Насос БЦН крепится на правой стороне топливного бака 11 (рис. 4.11) и состоит из электродвигателя Д-100 и центробежного насоса.
Центробежный насос состоит из корпуса 10 (рис. 4.12), крыльчатки 5, уплотнений, крышки 4 насоса и пропеллера 2.
Топливо, находящееся в баке, самотеком поступает к насосу и при работающем насосе крыльчаткой подается в топливную магистраль. Излишек топлива вместе с пузырьками воздуха вытесняется обратно в бак.
Топливные краны. На перегородке силового отделения справа от сиденья механика-водителя установлены два топливных крана: кран 25 (рис. 4.11) – для включения подачи топлива к двигателю из топливных баков, кран 26 – для подачи топлива к форсунке подогревателя. Принцип работы кранов одинаков – при переднем положении рукоятки (положение З) прерывается подача топлива к топливоподкачивающему насосу двигателя (подогревателя). При заднем положении рукоятки (положение О) топливо поступает к топливоподкачивающему насосу двигателя (подогревателя).
Топливные фильтры. Фильтр грубой очистки – щелевого типа, предназначен для предварительной очистки топлива от механических примесей перед поступлением его в топливоподкачивающий насос. Он состоит из фильтрующего элемента 6 (рис. 4.13), стакана 7, корпуса 8, крышки 3 с входным 9 и выходным 2 штуцерами. Фильтр грубой очистки установлен в силовом отделении.
Рис. 4.13. Фильтры грубой и тонкой очистки топлива
На рисунке обозначено: 1, 13 – гайки; 2, 9 – штуцера; 3, 12 – крышки фильтров; 4, 5 – уплотнения; 6 – фильтрующий элемент; 7 – стакан фильтрующего элемента; 8 – корпус фильтра грубой очистки; 10 – кронштейн крепления фильтра; 11 – прокладка; 14, 22 – уплотнительные кольца; 15 – пружина; 16 – сальник; 17 – корпус фильтра тонкой очистки; 18 – обратный клапан; 19 – входная проставка; 20 – выходная проставка; 21 – стяжной стержень; 23 – сетка; 24 – шелковый чехол; 25 – картонные фильтрующие пластины; а – фильтр грубой очистки; б – фильтр тонкой очистки.
Топливо через входной штуцер 9 поступает в полость между фильтрующим элементом и корпусом фильтра, откуда через зазоры фильтрующего элемента, очищаясь от механических частиц, поступает в выходной штуцер.
Топливный фильтр тонкой очистки служит для очистки топлива от механических примесей и отвода воздуха, попавшего в топливную систему. Фильтр расположен между блоками цилиндров двигателя. Фильтр состоит из корпуса 17, крышки 12, фильтрующего элемента 25. Полости фильтрованного и нефильтрованного топлива разобщены сальником 16 и уплотнительным кольцом 22.
Топливо поступает через входной штуцер в полость между фильтрующим элементом и корпусом фильтра. Имеющийся в топливе воздух поднимается в верхнюю часть полости фильтра и через обратный клапан 18, открывающийся под действием давления, создаваемого БЦН или топливоподкачивающим насосом при работающем двигателе, вместе с частью топлива отводится через дренажный трубопровод в топливный бак. Проходя через фильтрующий элемент топливо очищается и по каналам в стяжном стержне 21 и в корпусе фильтра поступает к выходному штуцеру.
Топливоподкачивающий насос двигателя – поршневого типа. Установлен на корпусе насоса высокого давления и приводится в действие эксцентриком кулачкового вала 2 (рис. 4.14). Насос служит для подачи топлива к топливному насосу высокого давления через фильтр тонкой очистки.
Топливный насос высокого давления – плунжерного типа, установлен вместе с регулятором оборотов и топливоподкачивающим насосом в развале блоков цилиндров двигателя.
Топливный насос (рис. 4.14) состоит из следующих основных частей: корпуса 1, кулачкового вала 2, шести секций насоса 3, регулятора оборотов 4 и привода управления. Кулачковый вал имеет три кулачка привода насосных секций и эксцентрик привода топливоподкачивающего насоса. Каждый кулачок вала приводит в действие две секции насоса. Через каждые 60° поворота кулачкового вала происходит подача топлива одной из секций насоса. В корпусе с каждой стороны просверлены по два продольных канала, из которых один – для подвода топлива к насосным секциям, а другой – для установки рейки изменения количества подаваемого топлива.
Рис. 4.14. Топливный насос высокого давления:
1 – корпус; 2 – кулачковый вал; 3 – шесть секций насоса; 4 – регулятор оборотов
Регулятор оборотов (рис. 4.15, а) – механический, всережимный, центробежного типа. Он предназначен для поддержания заданной частоты вращения коленчатого вала двигателя при различных нагрузках. Регулятор размещается в корпусе насоса на конце кулачкового вала.
Регулятор состоит из следующих основных деталей: конической тарели 1, крестовины 2 с пятью шарами 3, плоской тарели 4, рычага 5 с осью поворота 6, звеньев 8, соединенных с рейками 9, пружины 7 и рычага 10, соединенного с приводом управления.
Работа регулятора состоит в следующем. При работе двигателя вращается кулачковый вал насоса и вместе с ним вращаются крестовина и шары. При увеличении оборотов шары под действием центробежных сил отходят от центра вращения и, перемещаясь по конической тарели, отодвигают плоскую тарель. При этом рычаг, поворачиваясь по оси, перемещает зубчатые рейки в сторону уменьшения подачи топлива. Обороты двигателя снижаются до заданных, определяемых растяжением пружины при помощи привода. При уменьшении оборотов центробежные силы, действующие на шары, уменьшаются, они перемещаются под действием силы пружины к оси вращения, а зубчатые рейки при этом перемещаются в сторону увеличения подачи топлива.
Рис. 4.15. Узлы топливного насоса высокого давления:
регулятор оборотов (а): 1 – коническая тарель; 2 – крестовина; 3 – шар; 4 – плоская тарель;
5 – рычаг; 6 – ось поворота; 7 – пружина; 8 – звенья; 9 – рейка; 10 – рычаг; муфта опережения подачи топлива (б): 1 – корпус; 2 – центробежный датчик; 3 – гидравлический сервомеханизм; 4 – сервопоршень
Для предупреждения резкого изменения оборотов при внезапном изменении нагрузки пазы крестовины расположены не радиально, а под некоторым углом к направлению радиуса.
Кулачковый вал топливного насоса соединен с механизмом передач двигателя при помощи специальной автоматической муфты опережения подачи топлива. Она предназначена для изменения угла начала подачи топлива в зависимости от частоты вращения коленчатого вала. Чем больше частота вращения, тем раньше необходимо подавать топливо в цилиндры.
Муфта опережения подачи топлива (рис. 4.15, б) обеспечивает изменение угла начала подачи топлива в зависимости от числа оборотов двигателя. Кроме того, муфта передает крутящий момент от механизма передач двигателя на кулачковый вал топливного насоса. Муфта состоит из корпуса 1, центробежного датчика 2 частоты вращения коленчатого вала, гидравлического сервомеханизма 3, включающего в себе сервопоршень 4.
Форсунка – закрытого типа, с многодырчатым распылителем. Форсунки установлены в головке блока по оси цилиндров.
В корпусе имеется штуцер для подсоединения трубопровода высокого давления. Щелевой фильтр состоит из двух втулок, диаметральный зазор между которыми 0,002–0,004 мм. Подбираются втулки попарно и могут заменяться только вместе. Топливо, подведенное от насоса высокого давления, продавливается через зазор щелевого фильтра, а механические частицы задерживаются в канавках внутренней втулки.
Давление впрыска определяется регулировкой пружины форсунки. Когда давление в полости форсунки достигает 25 МПа (250 кгс/см2), игла резко поднимается вверх на 0,4-0,5 мм и топливо впрыскивается в камеру сгорания.
Привод управления подачей топлива служит для изменения количества топлива, подаваемого в цилиндры двигателя, в зависимости от дорожных условий и скорости движения машины, для быстрого прекращения подачи топлива при срабатывании систем коллективной защиты и ППО и установки постоянной подачи топлива. Управлять подачей топлива можно ручным или ножным приводом.
Ножной привод состоит из педали 3 (рис. 4.16), тяг 4, 12, 15 и 20, мостика с рычагами 21 и 24, механизма 19 остановки двигателя, вертикального валика 10 с рычагами и стойки 13 с двуплечим рычагом.
Рис. 4.16. Привод управления подачей топлива:
На рисунке обозначено: 1 – контргайка; 2 – регулировочный болт; 3 – педаль подачи топлива; 4 – тяга; 5 – тяга ручного привода; 6 – перепускной клапан; 7 – рычаг открывания клапана; 8 – стопор; 9 – рукоятка ручного управления подачей топлива; 10 – вертикальный валик привода; 11 – перегородка силового отделения; 12 – поперечная тяга; 13 – стойка с рычагом; 14 – топливный насос двигателя с регулятором; 15 – тяга к рычагу топливного насоса; 16 – рычаг топливного насоса; 17 – упор-ограничитель максимальной подачи топлива; 18 – упор-ограничитель нулевой подачи топлива; 19 – механизм остановки двигателя; 20 – тяги; 21 – рычаг; 22 – регулировочный винт; 23 – пружина привода; 24 – двуплечий рычаг; 25 – подкаблучник; 26 – пружина; 27 – штифт; 28 – тяга; 29 – шарик; 30 – пружина стопорного устройства; 51, 32 – гайки; 33 – седло;
34 – корпус стопорного устройства; Е – зазор.
Ручной привод состоит из рукоятки 9, тяги 28, корпуса 34, шарика 29, пружин 26 и 30, гайки 32. Для ограничения вращения рукоятки и исключения заклинивания при уменьшении частоты вращения установлен штифт 27.
Тяга 28 удерживается от самопроизвольного проворачивания за счет зубчатого торцевого зацепления рукоятки с корпусом.
При нажатии на педаль 3 через систему тяг и рычагов привода усилие передается на рычаг 16 регулятора топливного насоса. Рычаг 16 поворачивается, и топливный насос увеличивает подачу топлива. При этом ручной привод остается неподвижным, так как палец двуплечего рычага 24 свободно двигается по удлиненному пазу проушины тяги 5.
Положение педали 3, выжатой до упора в регулировочный болт 2, соответствует максимальной подаче топлива. При этом между рычагом 16 и упором-ограничителем 17 максимальной подачи топлива должен сохраняться зазор 0,15–0,3 мм.
При отпускании педали 3 рычаг 16 поворачивается, и подача топлива уменьшается.
При полностью отпущенной педали 3 и отсутствии зазора между рычагом 16 и упором-ограничителем 18 подача топлива прекращается (двигатель не работает), при этом между пальцем рычага 24 и проушиной тяги 5 должен быть зазор 0,5–1,0 мм.
Ручным приводом пользуются для установки минимально устойчивой частоты вращения коленчатого вала двигателя, а также при необходимости длительного поддержания постоянной частоты вращения в любом режиме.
Для изменения частоты вращения коленчатого вала двигателя ручным приводом необходимо рукоятку 9, потянув вверх, вывести из зацепления с зубьями корпуса 34 и вращать по ходу или против хода часовой стрелки, при этом тяга 5 перемещается вверх (вниз) и поворачивает двуплечий рычаг 24. Рычаг 24, поворачиваясь, воздействует через остальную систему тяг и рычагов привода на педаль 3 и на рычаг 16 регулятора топливного насоса – подача топлива уменьшается (увеличивается). При достижении требуемой частоты вращения коленчатого вала двигателя рукоятку необходимо отпустить. Воздействуя ногой на педаль 3, подачу топлива можно увеличить до максимальной, но затем уменьшить ее можно только до установленной ручным приводом.
Механизм 19 остановки двигателя (МОД) является исполнительным механизмом при срабатывании системы ППО и коллективной защиты и предназначен для остановки двигателя.
25 и 26. Заправка и слив топлива
Инструмент, принадлежности и эксплуатационные материалы: удлинитель, вороток, сменная головка 27, ключ 27x30, плоскогубцы (в ящике механика-водителя), проволока КО 1,4 (в ящике для запчастей и инструмента), ведро (под левым сиденьем в десантном отделении), воронка, фильтр, полотно (в ведре), ключ 765-93-сб159, шланг (в сумке с ЗИП двигателя), ветошь, дизельное топливо.
Для заправки топливом топливной системы необходимо:
– очистить от пыли и грязи пробки 8 и 11 (рис. 4.17) заправочных горловин;
– вывернуть пробки;
– заправить топливом основной топливный бак и топливные баки в дверях; завернуть пробки.
При заправке основного бака принять меры, исключающие попадание топлива на сетку воздухозаборной трубы.
После заправки брызги топлива удалить ветошью.
Рис. 4.17. Схема расположения люков и пробок сверху и на днище машины:
1 – пробка отверстия для щупа КП; 2 – люк над двигателем; 3, 6, 10 – отверстия для выброса воды откачивающими насосами; 4 – пробка отверстия для заправки охлаждающей жидкости; 5 – пробка отверстия для заправки маслобака; 7 – люк командира; 8, 11 – пробки заправочных горловин топливных баков; 9 – люки десантного отделения; 12 – труба забора воздуха; 13 – люк оператора; 14 – люк для доступа к ФПТ; 15 – люк десантника; 16 – люк механика-водителя; 17 – клапан отверстия слива воды из системы охлаждения; 18 – пробка отверстия слива масла из картера двигателя; 19 – двери; 20 – пробка отверстия слива воды из корпуса; 21 – пробка отверстия слива топлива; 22 – клапан отверстия слива воды из эжектора; 23 – лючок выхлопа отработавших газов из котла подогревателя; 24 – пробка отверстия слива масла из масляного бака; 25 – люк для доступа к двигателю; 26 – пробка отверстия слива
воды и масла из КП
Заливать топливо в баки до уровня заправочных горловин. Фильтры с заправочных горловин снимать лишь в тех случаях, когда механизированные средства заправки имеют свои фильтры.
При отсутствии механизированных средств заправлять топливо ведром, но обязательно через воронку с фильтром и полотно.
Для слива топлива из топливной системы необходимо:
– очистить от пыли и грязи пробку 21 в днище машины и вывернуть ее;
– очистить от пыли и грязи пробку 29 (рис. 4.11) в днище топливного бака, расконтрить и вывернуть;
– подготовить тару;
– вернуть ключ 765-93-сб159 в отверстие топливного бака, предварительно присоединив шланг к ключу 765-93-сб159;
– слить топливо в тару;
– вывернуть ключ 765-93-сб159;
– ввернуть пробку в отверстие днища топливного бака и законтрить ее проволокой;
– ввернуть пробку в отверстие днища машины.
27. Система снабжения воздухом
Система питания двигателя воздухом обеспечивает очистку от пыли воздуха, поступающего в цилиндры двигателя. Система включает в себя воздухозаборную трубу 1 (рис. 4.19), кольцевой воздуховод 5 с карманом 6, воздухоочиститель 11 с эжектором 12 отсоса пыли.
В летний период и при преодолении водных преград воздух в воздухоочиститель поступает только через воздухозаборную трубу, а в зимнее время и через лючок 9 из короба эжектора.
Рис. 4.19. Система питания двигателя воздухом:
1 – воздухозаборная труба; 2 – трубки подвода воздуха из пневмосистемы; 3 – патрубок забора воздуха в ФВУ; 4 – клапан слива воды из поддона; 5 – кольцевой воздуховод; 6 – карман воздуховода; 7 – клапаны; 8 – патрубок забора воздуха в компрессор; 9 – лючок трассы зимнего забора воздуха; 10 – патрубок забора воздуха в генератор; 11 – воздухоочиститель;
12 – эжектор отсоса пыли
4.3.1. Воздухозаборная труба
Воздухозаборная труба – выдвижная, телескопическая, находится на крыше машины между башней и люками десантного отделения. Внутри трубы установлен пневмоцилиндр 16 (рис. 4.20), с помощью которого труба выдвигается вверх для защиты от попадания воды при преодолении водных преград. Над трубой предусмотрена крышка 3 для защиты от атмосферных осадков. Для слива воды, попавшей в поддон 14 воздухозаборной трубы, предусмотрен клапан 13.
Рис. 4.20. Воздухозаборная труба:
1 – каркас сетки; 2, 8, 15 – болты; 3 – крышка; 4 – пружина; 5 – ребра жесткости верхнего колена; 6 – ограничитель; 7, 11 – рукава; 9 – трубопровод; 10 – кольцевой воздуховод; 12 – стойка; 13 – клапан; 14 – поддон; 16, 18 – пневмоцилиндры; 17, 24, 28 – гайки; 19 – крыша корпуса; 20 – полукольцо; 21 – манжета; 22, 25, 27 – колена трубы; 23 – кольцо; 26 – шток
пневмоцилиндра; 29 – сетка
4.3.2. Кольцевой воздуховод с карманом
Кольцевой воздуховод расположен вокруг погонного устройства башни.
Карман кольцевого воздуховода находится в перегородке силового отделения. Внутри кармана установлена сетка, предохраняющая от попадания посторонних предметов.
Доступ к сетке осуществляется через лючок, закрытый крышкой. В нижней части кармана расположены три клапана 7 (рис. 4.19), два из которых предназначены для слива попавшей воды, третий (средний) – для сбора твердых частиц.
4.3.3. Воздухоочиститель
Воздухоочиститель – бескассетный с автоматическим эжекционным удалением пыли из пылесборника. Он крепится к днищу короба эжектора 1
(рис. 4.21).
Рис 4.21. Воздухоочиститель:
1 – эжектор; 2 – эжектор отсоса пыли; 3 – трубка подвода отработавших газов; 4 – кронштейн; 5 – клапанная коробка; 6 – пылесборник; 7 – воздухоприточные окна циклонов; 8 – циклоны; 9 – патрубок входа воздуха в воздухоочиститель; 10 – корпус воздухоочистителя;
11, 16 – рычаги; 12 – заслонка трассы зимнего забора воздуха; 13 – маховичок заслонки;
14 – винт; 15 – каретка с шариками; 17 – валик; 18 – пружина; 19 – отверстие слива воды;
20 – инерционная решетка; 21 – перегородка; 22 – патрубки соединения воздухоочистителя с двигателем; 23 – трубки выхода очищенного воздуха из циклонов; 24 – сборник очищенного воздуха; 25 – шток пневмоцилиндра; 26 – рычаг конечного выключателя; 27 – конечный выключатель; 28 – клапан отсоса пыли; 29 – резиновая накладка; 30 – пружина клапана; 31 – трасса выпуска отработавших газов; 32 – патрубок на охлаждение компрессора; 33 – патрубок забора воздуха в генератор; 34 – пневмоцилиндр; 35 – масляный радиатор двигателя;
36 – масляный радиатор коробки передач; 37 – водяной радиатор; 38 – кольцевой воздуховод;
39 – клапан слива воды из кармана воздуховода
Основными частями воздухоочистителя являются циклонный аппарат, пылесборник 6 и сборник 24 очищенного воздуха. К корпусу воздухоочистителя приварены патрубки, которые шлангами и хомутами соединены с воздуховодом, впускными коллекторами двигателя и патрубком обдува генератора.
В корпусе воздухоочистителя имеются два отверстия 19 для слива воды.
Очистка воздуха, поступающего в цилиндры двигателя, осуществляется циклонным аппаратом, состоящим из 39 одинаковых по устройству циклонов 8. Циклон состоит из конусообразного корпуса с воздухоприточным окном 7, представляющего собой трубку, направленную тангенциально к корпусу циклона, и центральной трубки 23, вваренной в крышку циклона.
Корпус циклонного аппарата с одной стороны сообщается с пылесборником 6, а с другой стороны – со сборником 24 очищенного воздуха. На выходе из пылесборника в клапанной коробке установлен клапан 28 отсоса пыли, который в закрытом положении предотвращает попадание воды в воздухоочиститель при движении машины на плаву.
Для сигнализации положения клапана отсоса пыли на воздухоочистителе установлен конечный выключатель 27 с рычагом 26. Управление клапаном осуществляется тем же приводом, что и управление воздухозаборной трубой.
В днище эжектора установлена заслонка 12 зимнего забора воздуха, которая закрывает лючок, соединяющий подрадиаторное пространство эжектора с полостью корпуса воздухоочистителя. Заслонка управляется приводом. Привод заслонки состоит из маховичка 13, каретки 15 с шариками, винта 14, рычагов 11 и 16, валика 17 и пружины 18. В летний период и при преодолении водных преград заслонка должна быть закрыта, т.е. маховичок 13 завернут в направлении стрелки «ЗАКРЫТО», в зимний период заслонка должна быть открыта, т.е. маховичок вывернут до упора в направлении стрелки «открыто».
28. Система смазки
Система смазки двигателя (рис. 4.22) предназначена для подачи масла к трущимся поверхностям деталей двигателя в целях уменьшения трения и износа деталей, а также для отвода от них избыточного тепла и удаления продуктов износа.
Рис. 4.22. Система смазки двигателя:
1 – фильтр; 2, 13, 14 – пробки; 3 – щуп; 4, 28 – накидные гайки; 5 – сапун; 6 – перепускной клапан; 7 – заправочный бачок; 8 – масляный радиатор; 9 – центральный щиток; 10 – по-догреватель; 11 – центробежный масляный фильтр; 12 – двигатель; 15 – масляный насос двигателя; 16 – уплотнительное кольцо; 17 – фильтрующий элемент фильтра грубой очистки;
18 – обратный клапан; 19 – корпус фильтра; 20, 23, 26 – крышки; 21 – маслозаборная трубка; 22 – защитная сетка; 24 – ротор; 25 – гайка; 27 – маслозакачивающий насос МЗН-3; 29 – фильтр; 30 – масляный бак; 31, 34 – пружины; 32 – ключ Сб20-30-67; 33 – шпилька ротора;
35 – клапан
Техническая характеристика. Система смазки, комбинированная с сухим картером. Применяемое масло: основное – М-16ИХП-3, дублирующее –
МТ-16п. Полная емкость системы – 58 л. Заправочная емкость бака – 48 л. Минимально допустимое количество масла в системе – 20 л. Давление масла: нормальное 6–10 кгс/см2; минимальное – не ниже 2 кгс/см2. Температура масла: нормальная – 80–100 °С; максимально допустимая – 120 °С; минимальная – 55 °С.
Система смазки двигателя – принудительная, циркуляционная, с сухим картером. В систему смазки входят: масляный бак 30 с заправочным бачком 7, маслозакачивающий насос 27 (МЗН-3), масляный насос 15 двигателя, масляный фильтр 11, масляный радиатор 8, перепускной клапан 6 и трубопроводы (окрашены в коричневый цвет).
4.4.1. Масляный бак
Масляный бак 30 расположен в силовом отделении, установлен на опорах на днище и крепится стяжной лентой к правому борту машины. Заправочная емкость бака – 48 л.
В масляный бак вмонтирован котел подогревателя, при работе которого масло перед пуском двигателя в зимний период предварительно разогревается. На верхней части бака предусмотрена горловина, соединенная с заправочным бачком 7, а в днище – клапан 20 (рис. 4.23) слива масла из бака. На крышке бачка 7 (рис. 4.22) имеется штуцер, через который проходит указатель уровня масла (щуп 3). На штуцере щуп крепится с помощью накидной гайки 4. В пробку 2 вмонтирован сапун 5. Обратный клапан, установленный на коробе эжектора, служит для сообщения с атмосферой и предохраняет систему смазки от попадания воды и пыли.
4.4.2. Маслозакачивающий насос МЗН-3
Маслозакачивающий насос 27 МЗН-3 – шестеренчатый, с приводом от электродвигателя МН-1. МЗН-3 предназначен для подачи масла в двигатель перед его пуском, крепится к масляному баку.
В корпусе насоса смонтирован перепускной клапан на давление 10–
12 кгс/см2. Включается насос кнопкой «НАСОС» на центральном щитке.
4.4.3. Масляный насос двигателя
Масляный насос двигателя – шестеренчатый, двухсекционный. Он предназначен для подачи масла к трущимся поверхностям деталей двигателя и откачки масла из блок-картера через радиатор в масляный бак. Насос крепится внизу с правой стороны блок-картера двигателя.
Масляный насос имеет две секции – нагнетающую и откачивающую. В корпусе насоса смонтирован редукционный клапан для поддержания давления масла в главной магистрали двигателя в пределах (0,6–1,2) МПа (6–12) кгс/см2 на эксплуатационных режимах.
Рис. 4.23. Схема системы смазки двигателя:
1 – маслозаборный фильтр; 2 – воздухоотделитель; 3 – трубопровод подвода масла от маслозакачивающего насоса (МЗН-3) к двигателю; 4 – фильтрующая сетка; 5 – маслоизмерительный стержень (щуп); 6 – короб эжектора; 7 – обратный (защитный) клапан; 8 – трубопровод отвода масла от насоса двигателя в радиатор; 9 – масляный радиатор; 10 – трубопровод отвода масла из радиатора в бак; 11 – указатель электрического термометра; 12 – указатель электрического манометра; 13 – датчик давления масла; 14 – штуцер приемника электрического манометра; 15 – обратный клапан; 16 – двигатель; 17 – масляный насос двигателя; 18 – кожух обогрева трубопровода; 19 – трубопровод подвода масла от бака к насосу; 20 – клапан слива масла из бака; 21 – водозащитный рукав; 22 – перепускной клапан; 23 – маслозакачивающий насос; 24 – масляный бак
4.4.4. Масляный фильтр
Центробежный масляный фильтр предназначен для очистки масла от механических примесей. Он устанавливается в развале блоков двигателя и крепится болтами.
Масляный фильтр включает в себя ротор 24 (рис. 4.22) и последовательно включенный с ротором фильтрующий элемент 17 фильтра грубой очистки.
Ротор центробежного фильтра состоит из корпуса и крышки 20, стянутых шпильками 33. Внутри ротора установлены две маслозаборные трубки 21. В центре корпуса и крышки 20 запрессованы бронзовые подшипники, через которые проходит полый стержень, являющийся осью вращения ротора. В стержне завальцована медная трубка, которая другим концом входит в полость обратного клапана. Под ротором установлены маслоотражательный щиток и обратный клапан 18, который предотвращает перетекание масла из центрального канала двигателя в фильтр при прокачке масла насосом МЗН перед пуском двигателя. Сверху ротор закрыт крышкой 23, под которую установлена прокладка.
Фильтрующий элемент фильтра грубой очистки 17 представляет собой полый сетчатый цилиндр, надетый на стержень. Сверху фильтрующий элемент прижат пружиной и закрыт крышкой 26, которая крепится к корпусу фильтра двумя шпильками и уплотняется четырьмя резиновыми кольцами.
Во время работы двигателя масло поступает в полость фильтра, проходит через сетку фильтрующего элемента в полость стержня и далее через каналы и отверстия попадает во внутреннюю полость ротора. Часть масла через защитные сетки 22 маслозаборных трубок подводится к форсункам и, вытекая из них, вращает ротор, затем сливается через окна в маслоотражательном щитке и корпусе фильтра в канал блок-картера. Под действием центробежных сил частицы, находящиеся в масле, отбрасываются к стенке ротора и оседают. Очищенное масло попадает внутрь стержня, отжимает шарик и уходит в канал масляной магистрали для смазки узлов и механизмов двигателя.
4.4.5. Масляный радиатор
Масляный радиатор 8 – трубчато-пластинчатый, предназначен для охлаждения масла, выходящего из двигателя. Он расположен в коробе эжектора под жалюзи крыши.
Горячее масло от масляного насоса 17 по трубопроводу подводится к радиатору и, поочередно проходя через коллекторы и пакеты трубок, охлаждается потоком воздуха.
4.4.6. Работа системы смазки
Перед пуском двигателя механик-водитель включает насос МЗН-3, и масло из бака 24 (рис. 4.23) под давлением через сетчатый фильтр 1 и трубопровод 3 подается к двигателю. После пуска двигателя МЗН-3 отключают, и вступает в действие масляный насос 17 двигателя.
Масло из бака, пройдя обогреваемый в кожухе 18 трубопровод 19, подается нагнетающей секцией насоса 17 по гибкому шлангу к центробежному фильтру, где очищается и уходит в канал масляной магистрали для смазки узлов и механизмов двигателя.
Прошедшее через двигатель масло сливается в блок-картер, собирается в маслоотстойник, отсасывается откачивающей секцией масляного насоса 17, далее по трубопроводу 8 направляется в радиатор 9, где охлаждается и поступает в бак 24. Накапливающиеся в маслобаке пары масла и газы выбрасываются через обратный клапан 7 в эжектор.
4.4.7. Проверка заправки и дозаправка системы смазки двигателя
Инструмент, принадлежности и эксплуатационные материалы: ключ 27х30, вороток, удлинитель (в ящике механика-водителя), воронка с фильтром (в ведре под левым сиденьем в десантном отделении), ветошь, масло.
Очистить от пыли и грязи пробку 5 (рис. 4.17) на крыше машины и вывернуть ее. Отвернуть накидную гайку 4 (рис. 4.22), извлечь щуп 3, обтереть его чистой ветошью, вновь установить на место, затем вынуть и проверить количество масла, находящегося в баке. Проверять через 15–16 мин. после остановки двигателя.
Если уровень масла по щупу ниже верхней метки, необходимо дозаправить систему смазки маслом, для чего:
– вывернуть пробку 2;
– вынуть сетчатый фильтр;
– установить в заправочную горловину раздаточный пистолет маслозаправщика и дозаправить бак маслом до верхней метки щупа; при отсутствии маслозаправщика дозаправку производить ведром через воронку с фильтром, при этом сетчатый фильтр из заправочной горловины масляного бака не вынимать.
Установить щуп 3 и навернуть на него накидную гайку 4. Ввернуть пробку 2 заправочного бачка. Ввернуть пробку 5 (рис. 4.17) на крыше машины.
Смешивание различных марок масел не допускается.
29. Система охлаждения
Система охлаждения (рис. 4.24) предназначена для отвода тепла от деталей двигателя, соприкасающихся с горячими газами, и поддержания температуры этих деталей в допустимых пределах.
Техническая характеристика. Система охлаждения – высокотемпературная, жидкостная, закрытого типа, с принудительной циркуляцией охлаждающей жидкости. Вместимость системы – 50–52 л. Для охлаждения двигателя применяется летом вода с трехкомпонентной присадкой, зимой – низкозамерзающая жидкость марки 40 и 65. Температура охлаждающей жидкости: рекомендуемая – 80–100 °С; максимально допустимая – 120 °С; минимально допустимая температура – 55 °С.
В систему охлаждения входят: водяной насос 15 (рис. 4.24) двигателя, радиатор 2, расширительный бачок 4, паровоздушный клапан, эжектор 1, кран 12 отопителей, жалюзи 3 (рис. 4.25) и заслонки 2 эжектора, трубопроводы (окрашены в зеленый цвет).
Водяной насос 15 (рис. 4.24) размещен внизу с правой стороны блок-картера двигателя. К торцу корпуса водяного насоса крепится фланец со шлангом, по которому подводится охлаждающая жидкость.
Выходной патрубок водяного насоса непосредственно присоединен к блок-картеру. В наружный прилив на улитке насоса ввернут кран 42 для слива охлаждающей жидкости из системы и патрубок забора охлаждающей жидкости в насос подогревателя.
Рис. 4.24. Система охлаждения и подогрева двигателя:
1 – эжектор; 2 – радиатор; 3 – пробка заправочной горловины с паровоздушным клапаном;
4 – расширительный бачок; 5 – трос крана слива; 6 – рукоятка управления заслонкой подогревателя; 7 – термометр системы охлаждения и системы смазки двигателя; 8 – датчик термометра системы охлаждения двигателя; 9 – рукоятка управления краном слива охлаждающей жидкости; 10 – отопитель ФВУ; 11 – отопитель десантного отделения; 12 – кран отключения отопителей; 13 – клапан слива охлаждающей жидкости; 14 – поддон подогрева коробки передач; 15 – водяной насос двигателя; 16 – кожух обогрева маслозаборного трубопровода; 17 – ролик троса; 18 – котел подогревателя; 19 – рукоятка крышки лючка подогревателя; 20 – насосный узел подогревателя; 21 – клапан слива воды из эжектора; 22 – кран слива воды из эжектора; 23 – крышка: 24 – воздушный клапан; 25 – паровой клапан; 26 – пружина воздушного клапана; 27 – пружина парового клапана; 28 – корпус парового клапана; 29 – корпус пробки; 30 – отводящий патрубок; 31 – подводящий патрубок; 32 – корпус крана отопителя; 33 – клапан; 34 – шток; 35 – пружина; 36 – ось эксцентрика; 37 – эксцентрик; 38 – рукоятка со стопором; 39 – колпачок; 40 – пружина;
41 – шток с клапаном; 42 – кран слива охлаждающей жидкости из водяного насоса двигателя
Кран 42 слива охлаждающей жидкости через трос 5 соединен с рукояткой 9, расположенной на перегородке силового отделения.
Клапан 13 слива охлаждающей жидкости установлен справа за сиденьем механика-водителя и состоит из корпуса, штока 41 с клапаном, пружины 40 и колпачка 39. Клапан открывается нажатием на колпачок и поворотом его по ходу часовой стрелки.
4.5.1. Радиатор
Радиатор 2 – трубчато-пластинчатого типа, служит для охлаждения жидкости, выходящей из двигателя. Он расположен в коробе эжектора 1 под масляными радиаторами и крепится к коробу эжектора стяжными лентами.
Радиатор имеет два патрубка и штуцер. Один патрубок трубопроводом соединяется с головками блока цилиндров, другой – с трубопроводом водяного насоса. Пароотводная трубка, соединенная со штуцером, отводит пар в расширительный бачок 4.
4.5.2. Расширительный бачок
Расширительный бачок 4 служит резервуаром для расширяющейся при
нагревании охлаждающей жидкости, заправки системы охлаждения жидкостью, сбора и конденсации пара, отводимого от блоков цилиндров и радиатора. Бачок расположен над двигателем и крепится болтами к съемной балке корпуса.
Расширительный бачок состоит из корпуса, заливной горловины, закрываемой паровоздушным клапаном, съемного патрубка, соединенного трубопроводами с водяным насосом, и патрубка пароотводной трубки. Внутри расширительного бачка размещена контрольная линейка с гребнями для замера уровня жидкости.
4.5.3. Паровоздушный клапан
Паровоздушный клапан в пробке 3 предназначен для поддержания давления в системе (рис. 4.24). Он состоит из корпуса 29, крышки 23, штока с пружиной 27, парового клапана 25, воздушного клапана 24 с пружиной 26.
Пружина парового клапана отрегулирована на давление 200–220 кПа (2,0–2,2 кгс/см2), пружина воздушного клапана – на разрежение 2–10 кПа (0,02–0,1 кгс/см2).
С повышением температуры охлаждающей жидкости в системе повышается давление. Если сила давления пара превысит силу давления пружины 27, клапан откроется, пар через отверстия в корпусе паровоздушного клапана выйдет в атмосферу.
При остывании охлаждающей жидкости в системе создается разрежение. Если разрежение будет больше величины давления, на которую отрегулирована пружина 26, клапан 24 откроется, воздух поступит в систему и разрежение в ней уменьшится.
4.5.4. Эжектор
Эжектор предназначен для создания потока охлаждающего воздуха через радиаторы за счет использования энергии отработавших газов двигателя.
Эжектор расположен в силовом отделении и крепится к поперечным балкам корпуса. Эжектор включает в себя: короб 6 (рис. 4.25), два выпускных коллектора 12 с соплами, эжектор 28 отсоса газов из силового отделения, эжектор 7 отсоса пыли из пылесборника воздухоочистителя. Коллекторы эжектора соединены с выпускными коллекторами двигателя системой трубопроводов, шаровых компенсаторов 16 и клапанных коробок 23.
Рис. 4.25. Эжектор:
1 – уплотнительная прокладка; 2, 13 – разделительные перегородки; 3 – продольная перегородка; 4 – ручка; 5 – уплотнение от проникновения отработавших газов к радиаторам; 6 – короб эжектора; 7 – эжектор отсоса пыли; 8 – поперечная перегородка; 9 – стенка диффузора; 10 – трубка подвода отработавших газов; 11 – постель радиаторов; 12 – выпускные коллекторы эжектора; 14 – заслонка трассы зимнего забора воздуха; 15 – сопла выпуска отработавших газов; 16 – шаровые компенсаторы; 17 – труба подвода отработавших газов; 18 – крючок крепления ленты радиаторов; 19 – защитный клапан от попадания воды в силовое отделение; 20 – пружина защитного клапана; 21 – фланец установки форсунки ТДА; 22 – трубка отсоса конденсата и газов из шаровых компенсаторов; 23 – клапанная коробка; 24 – трубопровод отсоса газов из масляного бака; 25 – обратный (защитный) клапан; 26 – резиновая манжета уплотнения трубопроводов; 27 – крышка монтажного лючка; 28 – эжектор отсоса газов из силового отделения; 29 – масляный радиатор двигателя; 30 – радиатор охлаждающей жидкости; 31 – масляный радиатор коробки передач; 32 – кран слива воды из эжектора; 33 – диффузор; 34 – корпус; 35 – шток с запорным конусом; 36 – уплотнение; 37 – накидная гайка;
38 – кольцо
На коробе эжектора расположена заслонка 14 лючка для сообщения с воздухоочистителем при зимнем заборе воздуха.
Для слива попавшей в короб эжектора воды в нижней его части имеется кран 32 (рис. 4.25), соединенный трубопроводом со сливным клапаном 21 (рис. 4.24).
Для закрывания или открывания крана необходимо вращать шток за кольцо, соответственно, по ходу или против хода часовой стрелки.
Клапан слива воды 21 (рис. 4.24) из эжектора установлен на днище в переднем правом углу боевого отделения. Его конструкция аналогична конструкции клапана слива воды из системы охлаждения.
Выпускные коллекторы 12 (рис. 4.25) с соплами служат для создания разрежения за счет истечения через сопла отработавших газов с большой скоростью.
Эжектор 28 отсоса газов из силового отделения закреплен на коробе болтами. С торца эжектора установлен клапан 19, который предотвращает попадание воды в силовое отделение во время преодоления водных преград при остановке двигателя.
Привод клапана объединен с приводом клапанов защиты двигателя. Клапан закрывается автоматически вместе с клапанами защиты при остановке двигателя, а открывается вручную рукояткой 1 (рис. 4.30).
С противоположной стороны короба закреплен эжектор 7 (рис. 4.25) отсоса пыли из пылесборника воздухоочистителя.
Клапанная коробка 23 воздухоочистителя в нижней своей части имеет отверстие для слива воды, попавшей в эжектор отсоса пыли.
Эжектор отсоса газов и эжектор отсоса пыли имеют сопла, которые соединены с выпускной трассой двигателя. Газы, проходя через сопла, создают в полостях эжекторов разрежение, обеспечивая отсос газов из силового отделения и пыли из пылесборника воздухоочистителя.
4.5.5. Кран отопителей
Для включения и выключения отопителей 10 и 11 (рис. 4.24) от системы охлаждения двигателя служит кран 12, расположенный на внутренней поверхности крыши у задней стенки отсека ФВУ. Кран состоит из корпуса 32, штока 34, рукоятки 38, клапана 33 с уплотнениями и пружины 35.
Кран открывается нажатием на рукоятку 38 с переводом ее в положение О, закрывается – переводом рукоятки в положение 3.
4.5.6. Жалюзи и заслонки эжектора
Жалюзи 3 (рис. 4.26) служат для регулирования интенсивности охлаждения жидкости и масла в радиаторах. Кроме того, жалюзи и заслонки 2 эжектора защищают агрегаты силового отделения от попадания посторонних предметов и от поражения их пулями и осколками гранат. Жалюзи и заслонки закрыты сетками 1.
Рис. 4.26. Привод управления жалюзи и заслонками эжектора:
1 – сетка; 2 – заслонки эжектора; 3 – жалюзи; 4 – оси жалюзи; 5 – сектор; 6 – ось рычага ручного привода; 7 – рычаг ручного привода; 8, 14, 22, 24 – тяги; 9 – рукоятка ручного привода; 10 – защелка; 11 – кронштейн крепления ручного привода; 12, 31 – двуплечие рычаги; 13 – уплотнительный чехол; 15, 19, 30 – рычаги; 16 – электромагнит РМ6-1С; 17 – механизм отключения привода; 18 – ролик; 20 – рычаг с роликом; 21, 23, 33 – оттягивающие пружины;
25 – рычаг привода заслонок эжектора; 26 – лист крыши; 27 – переходной мостик; 28 – кронштейн мостика; 29 – кулачок; 32 – тяга поворота жалюзи: 34 – палец; 35 – наконечник; 36 – гильза; 37 – шарик; 38 – шток; 39, 45 – гайки; 40 – проушина; 41 – штифт; 42,
44 – пружина; 43 – корпус; 46 – вилка
Жалюзи, расположенные над радиаторами двигателя и КП, представляют собой решетку с подвижными и неподвижными броневыми планками, укрепленными в специальной рамке.
Заслонки эжектора 2 (рис.4.26) расположены над выпускной частью эжектора, представляют собой решетку с двумя подвижными и одной неподвижной броневыми планками в специальной рамке.
Привод управления жалюзи и заслонками эжектора обеспечивает ручное управление в обычных условиях эксплуатации и автоматическое закрывание жалюзи и заслонок эжектора при срабатывании системы защиты.
Привод состоит из рукоятки 9, двух тяг 22 и 24 с переходным мостиком 27, оттягивающих пружин 21, 23 и 33, мостика и механизма отключения 17 привода, осуществляющего автоматическое закрывание. При автоматическом закрывании жалюзи и заслонок эжектора наконечник 35 и гильза 36 механизма отключения разъединяются. Чтобы соединить наконечник и гильзу механизма отключения, т. е. привести привод управления в рабочее состояние, необходимо установить защелку 10 в вертикальное положение и перевести рукоятку в положение ЗАКРЫТО и затем в положение ОТКРЫТО, после чего защелка 10 должна быть переведена в горизонтальное положение.
Для последовательного открывания сначала заслонок 2 эжектора, а затем жалюзи 3 служит мостик, включающий кронштейн 28, рычаги 30, 19, 20 и кулачок 29.
Поворотом рукоятки 9 вправо вверх тяги и рычаги, последовательно перемещаясь, воздействуют через тягу 24 на рычаг 25, который поворачивается и открывает заслонки 2. При дальнейшем повороте рукоятки 9 рычаг 30, воздействуя на двуплечий рычаг 31 и тягу 32, открывает жалюзи.
30. – 36.
Силовая передача (рис. 5.1) – механическая, предназначена для передачи крутящего момента от коленчатого вала двигателя к ведущим колесам, для изменения величины этого момента и скорости вращения ведущих колес.
Силовая передача включает в себя: систему смазки и гидроуправления, главный фрикцион, коробку передач, два планетарных механизма поворота, остановочные тормоза, приводы управления, две бортовые передачи.
Главный фрикцион и коробка передач помещены в общий картер, к которому с двух сторон через проставки крепятся планетарные механизмы поворота. Картер посредством шпилек и гаек жестко соединен с двигателем, образуя силовой блок.
Рис. 5.1. Силовая передача (разрез):
1 – барабан остановочного тормоза; 2 – тормоз солнечной шестерни механизма поворота; 3 – планетарный ряд механизма поворота; 4 – блокировочный фрикцион механизма поворота;
5 – шестерня III передачи; 6 – шестерня II передачи; 7 – шестерня заднего хода; 8 – шестерня I передачи; 9 – ведомая коническая шестерня; 10 – ведомый вал; 11 – шестерня IV передачи; 12 – шестерня V передачи; 13 – грузовой вал; 14 – соединительный вал; 15 – ведущий вал с солнечной шестерней бортовой передачи; 16 – сателлит; 17 – корпус бортовой передачи с эпициклической шестерней; 18 – ведомый вал с водилом; 19 – ведущее колесо; 20 – синхронизатор; 21 – коленчатый вал двигателя; 22 – главный фрикцион; 23 – механизм выключения главного фрикциона; 24 – вал привода масляного насоса; 25 – ведущий вал; 26 – промежу
точная шестерня заднего хода
5.1. Главный фрикцион
Главный фрикцион представляет собой двухдисковую муфту сцепления сухого трения. Он предназначен:
– для отключения двигателя от коробки передач во время переключения передач и при экстренном торможении машины;
– обеспечения плавного трогания машины с места;
– предохранения деталей двигателя и силовой передачи от поломок при резком увеличении нагрузок на ведущих колесах.
5.1.1. Устройство главного фрикциона
Главный фрикцион состоит из ведущих частей, соединенных с маховиком двигателя, ведомых частей, соединенных с ведущим валом коробки передач, и механизма выключения.
К ведущим частям относятся опорный диск 19 (рис. 5.2), ведущий барабан 16, ведущий диск 20, нажимной диск 22, нажимные пружины 15 и детали крепления.
К ведомым частям относятся два стальных диска 21 трения с приклепанными и приклеенными к ним с обеих сторон дисками трения и ведомый барабан 23.
Рис. 5.2. Главный фрикцион
На рисунке обозначено: 1, 3 – крышки; 2 – стрелка; 4, 17, 37 – рычаги; 5 – вилка; 6, 29 – гайки; 7 – стопорная пластина; 8 – оттяжная пружина; 9 – масленка; 10 – цилиндр; 11 – поршень; 12 – подшипник; 13 – корпус подшипника; 14 – кожух; 15 – нажимная пружина; 16 – ведущий барабан; 18 – маховик; 19 – опорный диск; 20 – ведущий диск; 21 – ведомый диск; 22 – нажимной диск; 23 – ведомый барабан; 24 – шпилька; 25 – проушина; 26, 36 – контргайки; 27 – пробка; 28 – упор; 30 – педаль; 31 – шплинт; 32 – сухарь; 33 – обойма; 34, 35 – тяги; а – полость бустера; А – зазор.
Механизм выключения состоит из кольцевого цилиндра 10, поршня 11, радиально-упорного подшипника 12 в специальном корпусе 13, трех оттяжных пружин 8, трех двуплечих рычагов 4, трех вилок 5, трех регулировочных гаек
6, трех стопорных пластин 7. Для заправки смазки в подшипник служит масленка 9.
Рис. 5.3. Приводы управления остановочными тормозами и главным фрикционом
На рисунке обозначено: 1 – шток гидроцилиндра; 2 – поршень гидроцилиндра; 3 – корпус гидроцилиндра; 4 – уплотнительное кольцо; 5 – защитный чехол; 6 – упор; 7, 12, 13, 14, 17, 28, 29, 33, 34, 35, 37, 40, 47, 51, 56, 61 – рычаги; 8 – дренажные отверстия; 9 – регулировочный винт; 10, 62 – кронштейны; 11 – сигнализатор давления; 15 – золотниковая коробка; 16 – клапанная коробка; 18, 67 – оттяжные пружины; 19 – гидроцилиндр; 20 – дроссель; 21 – пробка; 22, 43 – пружины; 23 – сетчатый фильтр; 24 – шариковый клапан; 25, 42, 49 – крышки; 26 – щуп; 27 – штуцер; 30 – конечный выключатель; 31, 32, 36, 64 – тяги; 38 – педаль остановочных тормозов; 39 – планка; 41, 65 – валики; 44, 63 – упоры;
45 – педаль главного фрикциона; 46, 48 – трубы педального мостика; 50 – перепускной клапан; 52 – регулировочная гайка; 53 – тормозная лента; 54 – тормозной барабан; 55 – рукоятка стояночного тормоза; 57 – ролик; 58, 66 – проушины; 59 – гайка; 60 – корпус стопора; а, б, в – полости; г – канал; A – зазор.
5.1.2. Устройство привода управления главным фрикционом
Привод управления состоит из педали 45 (рис. 5.3) и рычага 33, смонтированных на педальном мостике, тяги 32, соединяющей рычаг 33 и рычаг 29 на переходном мостике, тяги, соединяющей рычаг 13 с рычагом 17 клапанной коробки 16, и золотника в клапанной коробке.
Для ограничения и регулирования хода педали главного фрикциона на ней крепится упор. В исходном положении педаль удерживается оттяжной пружиной 43 (рис. 5.3).
5.1.3. Работа главного фрикциона и привода управления
Под действием нажимных пружин 15 (рис. 5.2) фрикцион постоянно включен, его ведущие и ведомые части вращаются как одно целое и передают крутящий момент на ведущий вал коробки передач. При этом под действием трех оттяжных пружин 8 поршень 11 вместе с подшипником 12 оттянут в сторону коробки передач.
При нажатии на педаль главного фрикциона рычаг 33 (рис. 5.3) педального мостика, поворачиваясь, через тягу 32 и рычаги 29 и 13 переходного мостика поворачивает рычаг 17, который в свою очередь воздействует на золотник главного фрикциона. Золотник, перемещаясь, открывает канал подвода масла к бустеру механизма выключения. Масло под давлением поступает в полость а (рис. 5.2) бустера, перемещает поршень 11 и через корпус 13 подшипника воздействует на двуплечие рычаги 4. Последние, поворачиваясь вокруг своих осей, оттягивают нажимной диск 22, сжимая пружины, в результате ведущие и ведомые диски разъединяются и главный фрикцион выключается.
Для плавного включения главного фрикциона необходимо педаль отпустить на 1/2 ее хода и задержать в этом положении на короткий промежуток времени. При этом золотник, перемещаясь, открывает канал слива масла через клапан плавности. Масло из бустера главного фрикциона поступает в полость в (рис. 5.3) клапана плавности, отжимает шариковый клапан 24 и сливается в картер КП через канал г. Давление в полости быстро уменьшается, шариковый клапан под действием пружины перекрывает слив масла. Дальнейший слив масла происходит через небольшое отверстие дросселя 20, что обеспечивает плавное включение главного фрикциона.
В том случае, когда нет необходимости пользоваться клапаном плавности (например, при переключении передач), педаль отпускать сразу же на полный ход. При этом золотник возвращается в исходное положение, открывая канал слива масла.
Для выключения главного фрикциона при остановленном двигателе (например, если двигатель остановлен при включенной передаче) необходимо после нажатия на педаль главного фрикциона повернуть рукоятку крана главного фрикциона против хода часовой стрелки. В этом случае в полость а бустера поступает сжатый воздух из системы пневмооборудования.
Таким образом, выключение главного фрикциона может осуществляться двумя способами: гидравлически и с помощью сжатого воздуха.
5.1.4. Регулировка главного фрикциона
Инструмент, принадлежности и эксплуатационные материалы: ключи 10х12, 27х30, 14х17, 19х22, плоскогубцы (в ящике механика-водителя), проволока КО 1, 4, щуп (в ящике для ЗИП), приспособление для проворачивания коленчатого вала двигателя (в групповом комплекте ЗИП).
Для регулировки главного фрикциона необходимо:
– вывернуть болты крепления ребристого листа корпуса и поднять его до установки на стопор;
– вывернуть болты крепления крышки 3 (рис. 5.2) люка главного фрикциона и кожуха над стрелкой 2 и снять крышку. На ее место установить приспособление для проворачивания коленчатого вала двигателя, предварительно введя шестерню приспособления в зацепление с зубчатым венцом маховика 18;
– проворачивая приспособлением коленчатый вал двигателя, установить кожух главного фрикциона так, чтобы стакан пружины, расположенный слева от выштамповки на кожухе, находился по центру люка главного фрикциона;
– снять приспособление с люка главного фрикциона;
– расконтрить и вывернуть болты крепления стопорной пластины 7, стопорящей гайку 6;
– снять стопорную пластину 7 и отвернуть гайку 6 на 1–2 оборота;
– ввести щуп размером 6,7 мм в зазор А и, заворачивая гайку 6, отрегулировать зазор между корпусом 13 подшипника и рычагом 4 так, чтобы щуп перемещался в зазоре с незначительным люфтом;
– не выводя щупа из зазора, на гайку 6 установить стопорную пластину 7 так, чтобы отверстия в пластине совпадали с отверстиями в кожухе, и зафиксировать ее болтами, завернув их от руки;
– вывести и снова ввести щуп в зазор А, при этом щуп размером 6,7 мм должен перемещаться без усилия с незначительным люфтом, а щуп размером 7 мм – с незначительным усилием;
– закрепить стопорную пластину, завернув болты до прижатия пластины к кожуху, а затем отвернуть болты на 1–2 оборота, при этом стопорная пластина должна свободно перемещаться в пределах зазора между отверстиями и болтами. Законтрить болты попарно проволокой;
– установить приспособление и провернуть коленчатый вал двигателя так, чтобы вторая выштамповка заняла положение первой выштамповки. Снять приспособление. Отрегулировать зазор А в порядке, указанном выше;
– установить приспособление и провернуть коленчатый вал двигателя так, чтобы третья выштамповка заняла место второй выштамповки. Снять приспособление. Отрегулировать зазор А в порядке, указанном выше;
– установить крышку люка главного фрикциона и кожух над стрелкой на место и закрепить их;
– установить ребристый лист корпуса на место и закрепить его.
Методика установки щупа между рычагом и корпусом
подшипника при замере зазора А
Зазор А проверяется при положении стакана пружины слева от выштамповки на кожухе в верхней точке следующим образом:
– щуп размером 6,7 мм, а затем 7 мм подвести слева от стакана пружины к зазору А. При прокачивании щупа вдоль оси двигателя регулировочная гайка 6 должна иметь незначительное осевое перемещение, это говорит о том, что щуп находится между рычагом и корпусом подшипника;
– перевести верхний конец щупа вправо, как показано пунктиром на схеме, а затем, продвигая его вниз, ввести в зазор А между рычагом и корпусом подшипника.
5.1.5. Заправка смазки в подшипник механизма
выключения главного фрикциона
Инструмент и принадлежности: ключи 10x12, 14x17 (в ящике механика-водителя), шприц-пресс (на днище среднего отделения, справа), шланг, стержень шприц-пресса (в сумке с ЗИП двигателя), наконечник (в ящике для ЗИП) и смазка.
Для заправки смазки необходимо:
– вывернуть болты крепления ребристого листа корпуса и поднять его до установки на стопор;
– вывернуть болты крепления крышки люка главного фрикциона и снять крышку;
– повернуть рукой корпус 13 (рис. 5.2) подшипника так, чтобы масленка 9 оказалась в верхнем положении;
– соединить шланг плунжерного шприц-пресса с масленкой подшипника главного фрикциона;
– заправить смазку в подшипник механизма выключения главного фрикциона (около 60 г). Количество заправляемой смазки проверять по делениям, нанесенным на стержне шприц-пресса;
– отсоединить шланг шприц-пресса от масленки 9;
– установить крышку люка главного фрикциона на место и закрепить болтами;
– установить ребристый лист корпуса и закрепить его.
5.2. Коробка передач
Коробка передач – ступенчатая, с постоянным зацеплением шестерен, имеет пять передач переднего и одну передачу заднего хода. Она предназначена:
– для изменения крутящего момента на ведущих колесах и скорости движения машины;
– обеспечения движения машины задним ходом;
– отключения двигателя от ведущих колес.
5.2.1. Устройство коробки передач
Коробка передач состоит из следующих основных узлов: картера 1 (рис. 5.4), ведущего вала 18, изготовленного заодно с ведущей конической шестерней, ведомого вала 14, грузового вала 10 и промежуточной шестерни 28 заднего хода, закрепленной на оси 38.
Картер состоит из двух половин: нижней и верхней. Они соединяются с помощью шпилек и гаек. В нижней части картера установлены маслонасос 34 с приводом и сетчатый фильтр 36.
Для подогрева масла КП при низких температурах окружающего воздуха нижняя часть картера соединяется с системой подогрева двигателя полостями 35 и 37.
Ведущий вал установлен на роликовом и двух шарикоподшипниках. На шлицы ведущего вала установлены ведомые части главного фрикциона. Внутри ведущего вала проходит валик 19 привода к масляному насосу.
Рис. 5.4. Коробка передач:
1 – картер; 2 – ведомая шестерня III передачи; 3 – корпус синхронизатора II и III передач; 4 – кольцо синхронизатора; 5 – ведомая шестерня II передачи; 6 – ведомая шестерня заднего хода; 7 – зубчатая муфта включения I передачи и передачи заднего хода; 8 – ведомая шестерня I передачи; 9 – ведомая шестерня IV передачи; 10 – грузовой вал; 11 – ведомая шестерня V передачи; 12, 24, 25 – стопоры; 13 – зубчатая муфта с синхронизатором включения IV и V передач; 14 – ведомый вал; 15 – ведущая шестерня V передачи; 16 – ведущая шестерня IV передачи; 17 – коническая шестерня; 18 – ведущий вал; 19 – вал привода к масляному насосу; 20 – ведущая шестерня II передачи; 21 – зубчатая муфта с синхронизатором включения II и III передач; 22 – ведущая шестерня III передачи; 23 – палец; 26, 30 – рым-болты; 27 – сапун; 28 – промежуточная шестерня заднего хода; 29 – щуп; 31, 32 – шестерни; 33 – валик;
34 – масляный насос; 35, 37 – полости подогрева; 36 – сетчатый фильтр; 38 – ось
Ведомый вал установлен на трех подшипниках: двух шариковых и одном сферическом роликовом. На ведомом валу установлены шестерни 15, 16, 17, 20, 22 и муфта 13 переключения передач с синхронизатором. Шестерни 17, 20 и 22 установлены на шлицах вала, а шестерни 15 и 16 – на игольчатых подшипниках.
Грузовой вал установлен на четырех шарикоподшипниках. На грузовом валу установлены шестерни 2, 5, 6, 8, 9, 11 и две муфты 7 и 21 переключения передач. Шестерни 9 и 11 установлены на шлицах вала, а шестерни 2, 5, 6 и
8 – на игольчатых подшипниках.
Шестерня 28 закреплена на оси 38, которая, в свою очередь, установлена на двух шарикоподшипниках. Она находится в постоянном зацеплении с шестерней 6 и предназначена для обеспечения вращения грузового вала в противоположную сторону при включении передачи заднего хода. Передачи включаются перемещением подвижных зубчатых муфт, установленных на шлицах валов.
Для облегчения и бесшумности включения II, III, IV и V передач зубчатые муфты снабжены синхронизаторами инерционного типа, которые обеспечивают безударное включение зубчатых муфт благодаря уравниванию оборотов ведомых (включаемых) шестерен с оборотами ведомого и грузового валов.
5.2.2. Устройство привода управления коробкой передач
Привод служит для переключения передач в КП механиком-водителем. Он состоит из рычага 14 (рис. 5.5) переключения передач, закрепленного в корпусе 26 рулевой колонки, валика 28, поводковой коробки 33, трех тяг 34, 36 и 38, сервобустеров 1 и 2, рычага 41 (I передача и передача заднего хода) и вилок 39 и 42 переключения передач в КП. Рычаг переключения передач крепится в рамке 25 на оси 24 и своей вилкой входит в пазы валика 28. Место крепления рычага закрыто защитным чехлом 23.
Поводковая коробка состоит из корпуса 55, трех поводковых валиков 48, 50 и 58, на которых установлены поводки 45, рычага-избирателя 54 передач, шарикового замка 49 и трех пружинных стопоров с шариками 52.
Пружина 56 устанавливает валик 28 в положение, соответствующее нейтральному положению рычага переключения передач. При этом рычаг-избиратель передач входит в паз поводка валика IV и V передач.
Шариковый замок служит для исключения одновременного перемещения двух поводковых валиков, а следовательно, и одновременного включения двух передач. Он состоит из шариков и штифта 51.
Пружинные стопоры одинаковы по устройству и предназначены для фиксации поводковых валиков в нейтральном положении и положении включенной передачи. Шарики 52, входя в одну из трех канавок, имеющихся на каждом поводковом валике, фиксируют наружное положение поводкового валика.
5.2.3. Работа коробки передач и привода управления
Коробка передач и ее привод могут находиться в нейтральном положении или в положении включенной передачи.
В нейтрали рычаг 14 переключения передач занимает среднее положение, в котором удерживается пружиной 56. Поводковые валики при этом фиксируются пружинными стопорами в нейтральном положении (шарики 52 находятся в средних канавках поводковых валиков).
Рис. 5.5. Приводы управления коробкой передач и планетарными механизмами поворота
На рисунке обозначено: 1 – сервобустер IV и V передач; 2 – сервобустер II и III передач; 3 – трубопровод подвода масла к правому гидроцилиндру остановочных тормозов; 4 – трубопровод подвода масла к левому гидроцилиндру остановочных тормозов; 5, 6 – оттяжные пружины; 7 – золотниковая коробка; 8 – рычаг золотника остановочных тормозов; 9 – рычаг золотника правого поворота; 10, 37 – тяги привода управления поворотом машины; 11, 35 – тяги привода включения замедленной передачи; 12 – перегородка силового отделения; 13 – чехол уплотнения отверстия в перегородке силового отделения; 14 – рычаг переключения передач; 15, 16 – штифты; 17 – гребенка фиксации положения рычага включения замедленной передачи; 18 – рычаг включения замедленной передачи; 19 – руль; 20, 28, 30 – валики; 21, 29 – регулируемые ограничители;
22 – подвижный упор; 23 – защитный чехол; 24 – ось; 25 – рамка рычага переключения передач; 26 – корпус рулевой колонки; 27 – цапфа; 31, 32, 41 – рычаги; 33 – поводковая коробка; 34, 36, 38 – тяги привода переключения передач в коробке передач; 39, 42 – вилки переключения передач; 40 – рычаг золотника левого поворота; 43 – наконечник поводка с шаровым шарниром; 44 – стопорный болт; 45 – поводки поводковых валиков; 46 – направляющая пластина; 47 – кожух; 48 – поводковый валик II и III передач; 49 – шариковые замки; 50 – поводковый валик IV и V передач; 51 – штифт; 52 – шарик пружинного стопора; 53 – пружина стопора; 54 – рычаг-избиратель передач; 55 – корпус поводковой коробки; 56 – пружина фиксатора рычага избирателя в среднем положении;
57 – корпус фиксатора; 58 – поводковый валик I передачи и передачи заднего хода; 59 – втулка.
Муфты переключения передач с синхронизаторами и муфта переключения I передачи и передачи заднего хода находятся в среднем положении (не входят в зацепление с шестернями). Вращение от двигателя через главный фрикцион передается на ведущий вал 25 (рис. 5.1) и далее через конические шестерни – на ведомый вал 10.
Перед включением передачи выключить главный фрикцион.
Для включения I передачи необходимо рычаг 14 (рис. 5.5) переместить на себя и повернуть вверх. При перемещении рычага на себя перемещается валик 28 и рычаг-избиратель 54 входит в паз поводка 45 поводкового валика 58.
При повороте рычага вверх рычаг-избиратель перемещает поводковый валик, который через тягу 38 поворачивает рычаг 41. Вместе с рычагом 41 поворачивается вилка переключения передач и своими сухарями, перемещая зубчатую муфту 7 (рис. 5.4), вводит ее в зацепление с шестерней 8, включается передача.
Для включения передачи заднего хода рычаг 14 (рис. 5.5) необходимо переместить из нейтрального положения на себя и повернуть вниз. Через систему рычагов и тяг вилка повернется и введет зубчатую муфту 7 (рис. 5.4) в зацепление с шестерней 6.
В связи с тем, что принцип работы элементов КП при включении II, III, IV и V передач одинаков, рассмотрим работу их только при включении II передачи.
Для включения II передачи рычаг 14 (рис. 5.5) необходимо переместить от себя и повернуть вверх. При этом рычаг-избиратель входит в паз поводкового валика 48 и перемещает его. Поводковый валик через тягу 34 переместит золотник сервобустера 2 (рис. 5.5).
При перемещении золотника в первый момент поршень 36 (рис. 5.11) сервобустера не движется, так как не хватает усилия, чтобы сдвинуть рычаг 38 вилки переключения передач, пружина 33 сжимается, канал д соединяется с полостью а сервобустера. Масло давит на поршень 36, который, перемещаясь, поворачивает рычаг 38. Вилка переключения передач своими сухарями перемещает кольцо 4 (рис. 5.4) синхронизатора в сторону шестерни 5.
От кольца движение через четыре пальца 23 передается зубчатой муфте, а от нее через стопоры 25 – к корпусу синхронизатора. Корпус синхронизатора будет перемещаться до тех пор, пока своей конической частью не соприкоснется с конусным пояском шестерни 5.
Вследствие разности оборотов зубчатой муфты и включаемой шестерни между конусами появится сила трения скольжения. Под действием этой силы корпус синхронизатора увлекается включаемой шестерней и поворачивается относительно зубчатой муфты до упора стенок окон корпуса синхронизатора в выступы зубчатой муфты.
После выравнивания оборотов включаемой шестерни и синхронизатора муфта перемещается дальше и своими зубьями входит в зацепление с зубьями включаемой шестерни, включается II передача.
Масло остается в бустере, слив его в картер КП происходит при выключении передачи, когда начинает перемещаться золотник.
Для включения III передачи рычаг из нейтрального положения необходимо переместить от себя и повернуть вниз, при этом зубчатая муфта своими зубьями входит в зацепление с шестерней 2, включается III передача.
Для включения IV передачи рычаг необходимо из нейтрального положения повернуть вниз, при этом зубчатая муфта 13 своими зубьями входит в зацепление с зубьями шестерни 9, включается IV передача. Для включения V передачи рычаг необходимо повернуть вверх, при этом зубчатая муфта 13 входит в зацепление с шестерней 11, включается V передача.
5.2.4. Проверка заправки и дозаправка маслом картера коробки передач
Инструмент, принадлежности и эксплуатационные материалы: вороток, удлинитель, сменная головка 27 (в ящике механика-водителя), насадка (в ящике для ЗИП), воронка с фильтром (в ведре под левым сиденьем в десантном отделении), ветошь, масло.
Для проверки заправки и дозаправки маслом картера коробки передач необходимо:
– очистить от пыли и грязи пробку 1 (рис. 4.17) и вывернуть ее;
– очистить от пыли и грязи место вокруг щупа, извлечь щуп;
– если уровень масла по щупу находится ниже нижней метки щупа, дозаправить КП маслом, для чего:
– протереть щуп ветошью насухо;
– вставить в отверстие для щупа воронку с насадкой и фильтром;
– дозаправить масло в картер КП до верхней метки щупа. Проверять уровень масла в КП не ранее чем через 15 мин после остановки двигателя;
– установить щуп на место так, чтобы лыска на головке щупа зашла за выступ на крышке, и ввернуть пробку 1.
5.2.5. Замена масла в коробке передач
Инструмент, принадлежности и эксплуатационные материалы: вороток, удлинитель, сменная головка 27 (в ящике механика-водителя), шланг, ключ 765-93-сб159 (в сумке с ЗИП двигателя), воронка с фильтром (в ведре под левым сиденьем в десантном отделении), насадка, проволока КО 1,4 (в ящике для ЗИП), ветошь, масло.
Для замены масла в коробке передач необходимо:
– очистить от пыли и грязи пробку в днище машины и вывернуть ее;
– очистить от пыли и грязи пробку в картере КП, расконтрить и вывернуть ее;
– вывернуть пробку;
– очистить от пыли и грязи место вокруг щупа, извлечь щуп и протереть ветошью насухо;
– подготовить тару;
– ввернуть ключ 765-93-сб159 в отверстие картера КП, предварительно присоединив к нему шланг;
– слить масло в тару;
– вывернуть ключ 765-93-сб159 и положить на место;
– ввернуть пробку в картер КП и законтрить ее проволокой;
– ввернуть пробку;
– через отверстие для щупа заправить масло в КП до верхней метки щупа (около 20 л);
– при заправке масла в КП из ведра обязательно применять воронку с насадкой и фильтром;
– пустить двигатель, поработать 3–5 мин и остановить двигатель. Через 15–16 мин проверить уровень масла в КП и при необходимости дозаправить;
– установить щуп на место так, чтобы лыска на головке зашла за выступ на крышке, и ввернуть пробку.
5.2.6. Промывка гидроциклона коробки передач
Инструмент, принадлежности и эксплуатационные материалы: ключ 19х22 (в ящике механика-водителя), проволока КО1 (в ящике для ЗИП), дизельное топливо.
Для промывки гидроциклона КП необходимо:
– снять крышку люка, открыв два замка его крепления;
– вывернуть пробку 36 (рис. 5.10), предварительно расконтрив ее;
– промыть пробку в чистом дизельном топливе;
– очистить внутреннюю полость циклона чистой ветошью, смоченной в дизельном топливе;
– ввернуть пробку и законтрить проволокой. Перед завертыванием пробки убедиться в наличии резинового кольца;
– установить крышку люка и закрепить ее замками.
5.3. Планетарные механизмы поворота и тормоза
Механизмы поворота – планетарные, двухступенчатые, предназначены для передачи крутящего момента от коробки передач к бортовым передачам, осуществления поворота и для кратковременного увеличения тягового усилия на ведущих колесах без переключения передач) (включение замедленной передачи).
На машине установлены два планетарных механизма поворота с остановочными тормозами одинаковых по конструкции. Они подсоединены к коробке передач с двух сторон картера.
Остановочные тормоза – ленточные, плавающие. Они предназначены для остановки, торможения машины, осуществления крутого поворота и удержания машины в остановленном состоянии.
5.3.1. Устройство планетарных механизмов поворота
Каждый механизм поворота состоит из однорядного планетарного редуктора, блокировочного фрикциона и дискового тормоза ПМП.
Планетарный редуктор состоит из эпициклической шестерни 19 (рис. 5.6), установленной на грузовом валу КП, водила 34 с тремя сателлитами 8 на осях,
солнечной шестерни 35, которая жестко соединена с наружным барабаном 21 блокировочного фрикциона, а также деталей крепления планетарного редуктора.
Блокировочный фрикцион соединяет (блокирует) эпициклическую шестерню 19 с солнечной шестерней 35, обеспечивая прямую передачу крутящего момента от грузового вала КП к бортовой передаче, и разъединяет солнечную и эпициклическую шестерни для получения замедленной передачи.
Блокировочный фрикцион состоит из четырех ведущих дисков 18 с металлокерамическими поверхностями трения, трех ведомых дисков 17, наружного барабана 21, нажимного диска 7, нажимных пружин 20, опорного диска и внутреннего барабана (эпициклической шестерни 19). Блокировочный фрикцион – постоянно замкнутый.
Тормоз ПМП служит для остановки солнечной шестерни 35 для получения замедленной передачи в планетарном механизме поворота. Он состоит из дискового тормоза 24 (трех стальных дисков и четырех дисков с металлокерамическими поверхностями трения), наружного барабана 23, внутреннего барабана, который представляет одно целое с наружным барабаном 21 блокировочного фрикциона, нажимного диска 27, опорного диска 5, пружин 25, поршня 28. Тормоз ПМП – постоянно разомкнутый.
Рис. 5.6. Планетарный механизм поворота:
1 – наружная уплотнительная манжета; 2 – бронзовая втулка (подшипник); 3 – опорный палец; 4, 11 – прокладки; 5 – опорный диск; 6 – опора бустера; 7 – нажимной диск блокировочного фрикциона; 8 – сателлит; 9 – игольчатый подшипник; 10 – ось сателлита; 12 – игольчатый подшипник водила; 13 – грузовой вал коробки передач; 14 – шпилька крепления картера; 15 – гайка; 16 – проставка; 17 – ведомый диск блокировочного фрикциона; 18 – ведущий диск; 19 – эпициклическая шестерня планетарного ряда (внутренний барабан); 20 – пружина блокировочного фрикциона; 21 – наружный барабан; 22 – болты крепления барабана к проставке; 23 – барабан; 24 – дисковый тормоз; 25 – оттяжная пружина тормоза; 26 – тормозной барабан; 27 – нажимной диск тормоза; 28 – поршень; 29 – уплотнительные кольца; 30 – шарикоподшипник; 31 – манжета; 32 – зубчатая муфта; 33 – пробка водила; 34 – водило планет арного ряда; 35 – солнечная шестерня; 36 – внутренняя уплотнительная манжета поршня
Остановочный тормоз состоит из тормозной ленты 53 (рис. 5.3), составленной из двух половин, к внутренней поверхности которых приклепаны армированные фрикционные накладки, оттяжных пружин, которые крепятся к кронштейнам 10 и к тормозной ленте, двух гидроцилиндров 19, пружин 18, регулировочной гайки 52, рычага 7, упора 6 и тормозного барабана 54.
5.3.2. Устройство привода управления
планетарными механизмами поворота
Привод управления поворотом машины предназначен для осуществления поворота машины. Он состоит из руля 19 (рис. 5.5), расположенного в рулевой колонке, валика 20, рычагов 31 и 32, тяг 10 и 37, рычагов 9 и 40, золотников поворота левого и правого ПМП.
На валике жестко закреплен подвижной упор 22 (рис. 5.5), а к трубе рулевой колонки приварена планка, на которой имеются регулируемые ограничители 21 и 29. Подвижной упор и ограничители исключают возможность ударов золотников о корпус золотниковой коробки при отклонении руля до упора.
На валике 20 запрессованы два штифта 15 и 16, которые входят в пазы, имеющиеся на ступицах рычагов 31 и 32. При отклонении руля один штифт упирается в край паза и перемещает рычаг, а второй штифт в это время передвигается по пазу другого рычага, который удерживается пружиной и не поворачивается.
Привод замедленной передачи предназначен для одновременного выключения блокировочных фрикционов и включения тормозов обоих ПМП при прямолинейном движении, что обеспечивает увеличение крутящего момента в 1,44 раза и соответственное уменьшение скорости на каждой передаче. Он состоит из рычага 18, расположенного на рулевой колонке, валика 30 с приваренными к нему рычагами, тяг 11 и 35, шарнирно соединенных с рычагами 9 и 40 золотников поворота.
5.3.3. Работа планетарных механизмов поворота и привода управления
Привод управления планетарными механизмами может находиться в исходном положении, положении включенной замедленной передачи и в положениях, соответствующих повороту.
В исходном положении руль 19 находится в горизонтальном положении, рычаг 18 замедленной передачи – в верхнем положении, рычаги 9 и 40 золотниковой коробки пружинами 5 и 6 оттянуты в заднее крайнее положение, блокировочные фрикционы включены, а тормоза ПМП выключены. При этом солнечные шестерни ПМП сблокированы с эпициклами, они представляют собой одно целое.
При включенной передаче водила ПМП вращаются с той же скоростью, что и грузовой вал коробки передач. Машина движется со скоростью, определяемой передачей, включенной в КП.
При перемещении рычага 18 вниз через валик 30, тяги 11, 35 и рычаги 9, 40 перемещаются золотники золотниковой коробки и открывают каналы подвода масла к бустерам блокировочных фрикционов и тормозов ПМП. Под давлением масла блокировочные фрикционы выключаются, а тормоза ПМП включаются.
При включенной передаче вращение от грузового вала КП передается через сателлиты, которые обкатываясь вокруг солнечных шестерен, вращают водила. Машина движется прямолинейно со скоростью в 1,44 раза меньше скорости, определяемой передачей, включенной в КП.
Поворот машины производится поворотом руля 19 влево или вправо. Изменение радиуса поворота машины происходит плавно: чем больше угол поворота руля от исходного положения, тем с меньшим радиусом будет производиться поворот машины.
При повороте руля на небольшой угол влево через валик 20 поворачивается рычаг 32, который через тягу 37 поворачивает рычаг золотниковой коробки.
При повороте рычага 24 (рис. 5.11) золотник 26 перемещается и открывает канал подвода масла к бустеру блокировочного фрикциона левого ПМП.
Масло под воздействием постепенно увеличивающегося давления за счет скоса на золотнике начинает перемещать нажимной диск. Сила сжатия дисков уменьшается, диски пробуксовывают. По мере уменьшения силы сжатия величина крутящего момента, передаваемого к ведомым дискам блокировочного фрикциона левого ПМП, а следовательно, и к левому ведущему колесу, уменьшается, левая гусеница начинает отставать и машина с большим радиусом поворачивается влево.
При повороте руля на больший угол золотник 26, перемещаясь, открывает канал подвода масла к бустеру тормоза левого ПМП, при этом канал подвода масла к бустеру блокировочного фрикциона остается открытым. Поршень 28 (рис. 5.6) вместе с нажимным диском 27 начинает перемещаться и сжимает диски трения тормоза ПМП.
Зазор между дисками трения постепенно уменьшается, диски начинают пробуксовывать, величина крутящего момента, передаваемого к водилу планетарного ряда, увеличивается и левая гусеница будет все больше отставать от правой гусеницы, радиус поворота машины будет постепенно уменьшаться.
При полностью включенных тормозе и блокировочном фрикционе левого ПМП вращение передается через сателлиты, которые, обкатываясь вокруг заторможенной солнечной шестерни, вращают водило левого ПМП со скоростью в 1,44 раза меньше скорости вращения водила правого ПМП, машина будет поворачиваться с фиксированным радиусом поворота.
При повороте руля до упора золотник поворота левого ПМП, перемещаясь, вначале открывает канал слива масла из бустера тормоза ПМП, при этом масло сливается в картер коробки передач, а поршень тормоза возвращается в исходное положение, освобождая диски трения. Блокировочный фрикцион остается выключенным. Затем золотник поворота открывает канал подвода масла к гидроцилиндру левого остановочного тормоза.
Масло под давлением поступает в полость а (рис. 5.3), поршень 2 перемещается и своим штоком 1 нажимает на ролик рычага 7 стояночного тормоза. Рычаг поворачивается вокруг оси и затягивает тормозную ленту. Левая гусеница затормаживается, машина поворачивается на месте в левую сторону.
При установке руля в исходное положение золотник поворота левого ПМП перемещается в первоначальное положение и открывает канал слива из бустера блокировочного фрикциона, при этом масло сливается в картер КП, а блокировочный фрикцион под действием пружин включается. При включенной передаче машина будет двигаться со скоростью, определяемой передачей, включенной в КП.
5.3.4. Привод управления остановочными тормозами
Привод управления остановочными тормозами состоит из педали 38 (рис. 5.3), расположенной на педальном мостике и удерживаемой в исходном положении пружиной 43, рычага 34 на педальном мостике, рычагов 12 и 28 на переходном мостике, тяги 31, золотника остановочных тормозов, расположенного в золотниковой коробке, гидроцилиндров 19. Гидроцилиндры одинаковы по устройству и состоят из корпуса 3, поршня 2, штока 1 и штуцеров.
5.3.5. Работа остановочных тормозов и привода управления
Для торможения машины остановочными тормозами необходимо нажать на педаль 38, при этом поворачивается труба 46, жестко соединенная с педалью, и рычаг 34.
Рычаг, поворачиваясь, через тягу перемещает золотник остановочных тормозов. Золотник, перемещаясь, открывает канал подвода масла к гидроцилиндрам. Масло под давлением поступает в полость а (рис. 5.3) гидроцилиндров, перемещая поршни и затягивая тормозные ленты. Давление в гидроцилиндрах нарастает плавно в зависимости от степени нажатия на педаль благодаря наличию следящего устройства.
При отсутствии необходимого давления масла в системе гидроуправления ленты остановочных тормозов затягиваются с помощью сжатого воздуха, поступающего из пневмосистемы машины: при нажатии на педаль остановочных тормозов рычаг мостика воздействует на конечный выключатель 30 и замыкает его контакт. Напряжение через сигнализатор 19 (рис. 5.10) давления, контакт которого замыкается автоматически при падении давления в системе гидроуправления ниже 0,25 МПа (2,6 кгс/см2), и конечный выключатель подается к электропневмоклапану пневмосистемы, который открывается, и сжатый воздух по трубопроводам через штуцер поступает в полость б (рис. 5.3) гидроцилиндра. Поршень 2 перемещается и нажимает на ролик рычага 7 стояночного тормоза, ленты остановочных тормозов затягиваются.
5.3.6. Устройство привода стояночного тормоза
Привод стояночного тормоза предназначен для торможения машины при стоянке на горизонтальном участке, на спусках и подъемах и притормаживания машины при ее буксировке на суше.
Торможение машины осуществляется затягиванием ленты левого остановочного тормоза. Ввиду того, что при прямолинейном движении соединительные валы левого и правого борта жестко соединены с помощью блокировочных фрикционов ПМП с грузовым валом КП и вращаются как одно целое, то при затягивании ленты остановочного тормоза затормаживают одновременно ведущие колеса левого и правого борта.
Привод состоит из рукоятки 3 (рис. 5.7), валика 2, стопора 12, конечного выключателя 10, тяги, рычагов, мостиков, оттяжной пружины 67 (рис. 5.3) с регулировочным винтом и упора, расположенного на нижнем наклонном броневом листе корпуса.
Рис. 5.7. Схема привода управления стояночным тормозом:
1 – корпус стопора; 2 – валик; 3 – рукоятка; 4 – тяга; 5 – нижний палец тормозной ленты; 6 – верхний палец тормозной ленты; 7 – рычаг тормоза; 8 – ролик рычага; 9 – рычаг привода
стояночного тормоза; 10 – конечный выключатель; 11 – пружина; 12 – стопор
Перед сиденьем механика-водителя установлено световое табло ОТПУСТИ РУЧНОЙ ТОРМОЗ, которое загорается после затормаживания машины стояночным тормозом и предупреждает механика-водителя о необходимости снятия машины со стояночного тормоза перед началом движения.
Впереди трубы 46 педального мостика установлен дополнительный мостик, состоящий из валика 41, рычагов 37, 40 и тяги 36. Дополнительный мостик используется при длительной буксировке машины, при этом тяга 36 соединяется с рычагом 35. Порядок пользования дополнительным мостиком приведен в подразделе («Буксировка машины»).
5.3.7. Работа привода стояночного тормоза
Для затягивания ленты стояночного тормоза необходимо рукой потянуть рукоятку 55 на себя. Валик 65 через рычаги и тягу поворачивает рычаг 56, который через ролик воздействует на рычаг 7 остановочного тормоза, тормозная лента затягивается и затормаживает барабан.
Для фиксации рукоятки 55 в этом положении на валике имеются пазы, в один из которых под действием пружины 11 (рис. 5.7) входит стопор 12.
При своем движении стопор 12 нажимает на шарик, который выходит из лунки и давит на пластину конечного выключателя 10. Пластина нажимает на микровыключатель, в результате чего загорается световое табло ОТПУСТИ РУЧНОЙ ТОРМОЗ.
Для возврата рукоятки 55 (рис. 5.3) в исходное положение необходимо повернуть ее влево, не выпуская из руки довести до упора, а затем повернуть вправо вниз до вертикального положения, при этом погаснет световое табло ОТПУСТИ РУЧНОЙ ТОРМОЗ.
При соединенной тяге 36 с рычагом 35 и нажатии на педаль 38 остановочных тормозов поворачивается валик 41 дополнительного мостика и через тягу 36 и привод стояночного тормоза воздействует на тормозную ленту. При этом валик 65 с рукояткой 55 не перемещается.
5.3.8. Проверка и регулировка приводов управления
стояночного и остановочных тормозов
Инструмент и принадлежности: ключи 14x17, 13x14, сменная головка 27, вороток, удлинитель, щуп, плоскогубцы (в ящике механика-водителя).
Для проверки регулировки привода управления стояночного и остановочных тормозов:
– вытянуть на себя до отказа рукоятку стояночного тормоза. Если рукоятка 55 (рис. 5.3) выходит за корпус 60 стопора на 14 зубьев и более, отрегулировать привод стояночного и остановочных тормозов в такой последовательности:
– вывернуть болты крепления ребристого листа корпуса и поднять его до установки на стопор;
– переместить рукоятку стояночного тормоза так, чтобы рычаг 61 касался упора 63;
– затянуть гайки 52 до отказа, затем отпустить их на 8 оборотов каждую;
– проверить щупом величину зазора И между рычагом 56 и роликом рычага 7, который должен быть 0,3–1 мм. В случае отклонения отрегулировать зазор, для чего:
– расконтрить тягу 64, ослабив гайку 59;
– отсоединить проушину 58 от рычага мостика и, вворачивая (выворачивая) ее, отрегулировать длину тяги 64 так, чтобы был обеспечен зазор
И = 0,3 ± 1 мм между рычагом 56 и роликом рычага 7; соединить проушину 58 с рычагом мостика и законтрить тягу 64 гайкой 59;
– установить ребристый лист на место и закрепить его.
5.4. Бортовые передачи
Бортовая передача представляет собой одноступенчатый понижающий планетарный редуктор. Она предназначена для постоянного увеличения крутящего момента, подводимого к ведущим колесам.
Бортовые передачи крепятся к бортам корпуса в передней части машины.
5.4.1. Устройство бортовой передачи
Бортовая передача состоит из корпуса 1 (рис. 5.8), с которым заодно выполнена эпициклическая шестерня, ведущего вала 9 с солнечной шестерней, трех сателлитов 10, ведомого вала (водила) 8 и крышки 2. На ведущем валу левой бортовой передачи расположена шестерня 5 привода спидометра. Внутри ведущего вала установлен сапун 23. На крышке 2 предусмотрено отверстие для заправки маслом бортовой передачи, которое закрывается пробкой 12. Отверстие для слива масла закрывается пробкой 13. Контроль уровня масла в бортовой передаче осуществляется через заправочное отверстие. Передача крутящего момента от ПМП к бортовым передачам осуществляется муфтами 15 и валами 16 и 18.
5.4.2. Работа бортовой передачи
Крутящий момент от ПМП через валы 16 и 18 и муфты 15 передается на солнечные шестерни, жестко связанные с ведущими валами 9.
Сателлиты 10, обкатываясь по неподвижным эпициклическим шестерням, вращают водила 8.
Крутящий момент от водил передается на ведущие колеса.
Одновременно от ведущего вала 9 через ведущую шестерню 5 привода спидометра вращение передается на вал 6 привода спидометра.
5.4.3. Проверка заправки и дозаправка маслом бортовой передачи
Инструмент, принадлежности и эксплуатационные материалы: ключ 14x17, сменная головка 24, удлинитель, вороток, плоскогубцы (в ящике механика-водителя), шприц (на днище среднего отделения, справа), масло.
Для заправки маслом бортовой передачи необходимо:
– установить машину на горизонтальном участке местности;
– вывернуть болты и поднять ребристый лист;
– вывернуть пробку 12 заправочного отверстия, предварительно расконтрив ее;
– если масло не вытекает из заправочного отверстия, дозаправить бортовую передачу шприцем до появления масла из заправочного отверстия;
– ввернуть пробку заправочного отверстия и законтрить ее;
– установить ребристый лист корпуса и закрепить его.
Рис. 5.8. Бортовая передача:
1 – корпус бортовой передачи с эпициклической шестерней; 2 – крышка бортовой передачи; 3 – корпус привода спидометра; 4 – втулка с маслосгонной резьбой; 5 – ведущая шестерня привода спидометра; 6 – вал с ведомой шестерней привода спидометра и датчика пути; 7 – стопорный болт; 8 – ведомый вал (водило) планетарного ряда; 9 – ведущий вал с солнечной шестерней; 10 – сателлит; 11 – зубчатый венец муфты полужесткого соединения; 12 – пробка заправочного отверстия; 13 – пробка отверстия для слива масла; 14 – правая бортовая передача; 15 – муфты полужесткого соединения; 16 – правый соединительный вал; 17 – коробка передач; 18 – левый соединительный вал; 19 – левая бортовая передача; 20 – кольцо лабиринтного уплотнения; 21 – пробка крепления ведущего колеса; 22 – распорный конус; 23 –
сапун с набивкой; 24 – ось сателлита
5.4.4. Замена масла в бортовой передаче
Инструмент, принадлежности и эксплуатационные материалы: удлинитель, вороток, сменные головки 17, 22, 27, плоскогубцы (в ящике механика-водителя), шприц (на днище среднего отделения, справа), проволока КО1, КО1, 6 (в ящике для ЗИП), ведро, ветошь, масло.
Для заправки масла в бортовой передаче необходимо:
– установить машину на горизонтальном участке местности;
– вывернуть болты крепления ребристого листа корпуса и поднять его до установки на стопор;
– очистить от пыли и грязи пробки 12 и 13 заправочного и сливного отверстий бортовой передачи и расконтрить их;
– приготовить тару;
– вывернуть пробку 13 сливного отверстия и пробку заправочного отверстия;
– слить масло в тару;
– ввернуть пробку сливного отверстия и законтрить проволокой;
– заправить масло шприцем в бортовую передачу до кромки заправочного отверстия (примерно 2 л);
– ввернуть пробку заправочного отверстия, законтрить ее проволокой;
– установить ребристый лист корпуса и закрепить его.
37.-39. Ходовая часть
Ходовая часть состоит из гусеничного движителя и подвески.
Движитель выполнен по схеме гусеничного обвода с поддерживающими катками и с передним расположением ведущих колес. Гусеница – мелкозвенчатая с резинометаллическим шарниром. Число траков в гусенице – 85. Ширина трака – 220 мм .
6.1. Гусеничный движитель
Гусеничный движитель с передним расположением ведущих колес предназначен для сообщения машине поступательного движения как на суше, так и на воде за счет крутящего момента, подводимого от двигателя к ведущим колесам. Зацепление ведущих колес с гусеницами – цевочное. Гусеничный движитель состоит из двух гусениц 11 (рис. 6.1), двух ведущих колес 1, двенадцати опорных катков 14, шести поддерживающих катков 10, двух направляющих колес 13, двух очистителей 12, двух механизмов натяжения гусениц.
Рис. 6.1. Ходовая часть:
1 – ведущее колесо; 2 – пружинный упор; 3 – ограничитель; 4 – кронштейн крепления серьги гидроамортизатора; 5 – гидроамортизатор; 6 – резиновый упор; 7 – пробка заправочного отверстия труб балансиров; 8 – балансир; 9 – борт; 10 – поддерживающий каток; 11 – гусеница; 12 – очиститель; 13 – направляющее колесо; 14 – шестой опорный каток; 15 – скоба; 16, 21 – пальцы; 17 – резиновая втулка; 18 – трак гусеницы; 19, 20, 22 – опорные катки; 23 – шаблон;
24 – направляющая очистителя; 25, 26 – болты; А – толщина зуба
При движении машины на плаву гусеницы, перематываясь, создают своими нижними ветвями поток воды, направленный в сторону, противоположную движению, благодаря чему машина движется.
Для уменьшения вредного влияния потока воды, создаваемого верхней ветвью гусеницы, и увеличения скорости движения машины верхняя ветвь закрывается специальными крыльями. Крылья выполнены так, что поток воды, создаваемый верхней ветвью гусеницы, частично направляется назад от щитка в передней части крыльев и направляющих лопаток в кормовой части крыльев.
6.1.1. Гусеницы
Гусеницы представляют собой мелкозвенчатые ленты, состоящие каждая из 85 звеньев-траков 18, связанных между собой шарнирно с помощью обрезиненных пальцев 16, скоб 15 и болтов 26.
Трак – штампованный из высокопрочной стали, имеет две проушины для соединения траков и два гребня для предотвращения схода гусеницы с опорных катков и спадания ее с поддерживающих катков. Гладкая сторона соединенных в ленту траков (между гребнями) служит беговой дорожкой для опорных катков.
На внешней стороне трака имеются грунтозацепы, увеличивающие сцепление его с грунтом. В проушины траков запрессованы стальные пальцы с привулканизированными к ним резиновыми втулками 17, которые за счет деформации резины позволяют тракам поворачиваться на небольшой угол относительно друг друга. На концы пальцев 16 надеты скобы 15, выполненные из высокопрочной стали. Скобы закреплены с помощью болтов 26, при этом болт ввернут в скобу между лысками пальцев.
6.1.2. Ведущее колесо
Ведущие колеса, получая вращение от двигателя через агрегаты силовой передачи, перематывают находящиеся с ними в зацеплении гусеницы и сообщают корпусу машины поступательное движение.
Ведущее колесо состоит из корпуса 8 (рис. 6.2) и двух зубчатых венцов 7 для зацепления со скобами гусениц.
![]() | Рис. 6.2. Ведущее колесо: 1 – хвостовик водила; 2 – бортовая передача; 3 – контровочная проволока; 4 – пробка крепления ведущего колеса; 5, 6 – болты; 7 – зубчатые венцы; 8 – корпус |
Корпус ведущего колеса состоит из двух сваренных между собой стальных частей с фланцами для установки и крепления сменных зубчатых венцов.
Зубчатые венцы крепятся к корпусу ведущего колеса болтами. Для повышения износостойкости на рабочие поверхности зубьев наплавлен слой твердого сплава.
Ведущее колесо устанавливается на хвостовик 1 водила бортовой передачи шлицевой ступицей и крепится на водиле пробкой 4, которая стопорится болтом 5 и распорным конусом.
6.1.3. Опорный каток
Опорные катки служат для распределения веса машины на опорную поверхность гусениц. Каток выполнен полым герметичным. Он состоит из ступицы (рис. 6.3), дисков 19 и бандажа 20, сваренных между собой. На стальном бандаже привулканизирована массивная резиновая шина 21.
Рис. 6.3. Опорный каток с подвеской:
1 – труба балансира; 2 – кронштейн подвески; 3, 12 – пробки; 4 – гидроамортизатор; 5 – пружинный упор балансира; 6 – ось катка; 7 – ступица; 8 – ограничитель; 9, 26 – крышки;
10 – резиновое кольцо; 11 – стопор; 13 – лабиринтное уплотнение; 14 – крышка ступицы; 15, 28 – манжеты; 16 – роликоподшипник; 17 – уплотнительное кольцо; 18 – стопорная гайка;
19 – диск; 20 – бандаж; 21 – резиновая шина; 22 – регулировочные прокладки; 23 – балансир;
24 – ухо; 25 – болт; 27 – втулка; 29 – торсионные валы; 30 – днище
Опорные катки расположены по обе стороны бортов машины. Каток устанавливается на ось 6 на подшипниках и крепится стопорной гайкой 18, которая фиксируется стопором 11. Между подшипниками установлена распорная втулка.
К ступице катка крепится болтами крышка 9 с заправочным отверстием, закрытым пробкой 12 с алюминиевой или фибровой прокладкой. Между крышкой и ступицей имеется резиновое уплотнительное кольцо 10. С противоположной стороны ступица катка закрыта крышкой с лабиринтным уплотнением 13, резиновой манжетой 15 и уплотнительным кольцом 17.
Крышки катка установлены на сурик. Уплотнения предотвращают выброс смазки из катка, а также попадание воды и грязи в полость ступицы.
6.1.4. Поддерживающий каток
Поддерживающие катки предназначены для поддержания и направления верхних ветвей гусениц при их перематывании.
Поддерживающий каток однобандажный с привулканизированной резиновой шиной. Ступица катка изготовлена из алюминиевого сплава. В месте контакта с гребнями гусеницы в ступицу катка с обеих сторон ввернуты стальные гайки 41 (рис. 6.4).
Рис. 6.4. Направляющее колесо с механизмом натяжения
гусеницы и поддерживающий каток:
1 – шарикоподшипник; 2, 43 – крышки; 3, 25, 40, 41 – гайки; 4, 42 – пробки; 5 – стопор; 6, 12, 26, 31 – кольца; 7, 23 – болты; 8 – диски; 9 – ребро; 10, 17, 27, 30 – втулки; 11 – роликоподшипник; 13, 35 – манжеты; 14, 39 – лабиринтные уплотнения; 15 – сальник; 16 – кривошип; 18 – фланец; 19, 36 – регулировочные прокладки; 20 – червячное колесо; 21 – червяк; 22 – зубчатая муфта; 24 – стопор гайки; 28 – упорное кольцо; 29 – корпус механизма натяжения; 32, 37 – кронштейны; 33 – крышка лабиринтного уплотнения; 34 – щиток; 38 – ступица; 44 –
резиновая шина; 45 – кольцо лабиринтного уплотнения
Поддерживающий каток установлен на оси кронштейна 37 на двух шарикоподшипниках и крепится гайкой 40, которая фиксируется стопором. Между подшипниками установлены распорные втулки. К ступице катка крепится крышка 43 с заправочным отверстием, закрытым пробкой 42 с алюминиевой или фибровой прокладкой. Под крышку установлено резиновое уплотнительное кольцо. С противоположной стороны ступица катка закрыта крышкой с лабиринтным уплотнением 39, манжетой и уплотнительным кольцом. Крышки установлены на сурик.
Уплотнения предотвращают утечку масла из катка, а также попадание воды и грязи в полость ступицы.
6.1.5. Направляющие колеса и очистители
Направляющие колеса служат для направления гусениц, а вместе с механизмом натяжения – для их натяжения. Направляющее колесо сварено из двух фасонных дисков 8. Для придания жесткости между ободами колеса равномерно по периметру вварены ребра 9.
Направляющее колесо расположено в кормовой части машины на оси кривошипа 16 на шариковом и роликовом подшипниках и крепится гайкой 3, которая фиксируется стопором 5. Между подшипниками установлена распорная втулка 10.
Для предотвращения утечки смазки из ступицы, а также попадания воды и грязи внутрь ступица предохраняется крышками 2 и 33, лабиринтным уплотнением 14, самоподжимной манжетой 13, войлочным сальником 15 и уплотнительными кольцами 6 и 12.
Для заправки смазки в ступицу в центре крышки 2 имеется отверстие, закрываемое пробкой 4 с алюминиевой или фибровой прокладкой.
Очистители направляющих колес установлены на бортах машины в планках с пазами и крепятся четырьмя болтами 25 (рис. 6.1). Для наиболее эффективной очистки колес от снега между очистителем и ободом колеса устанавливается зазор 3–5 мм.
6.1.6. Механизм натяжения гусениц
Механизм натяжения гусениц состоит из кривошипа 16 (рис. 6.4), корпуса 29 механизма натяжения, кронштейна 32, червяка 21, червячного колеса 20 и стопорного устройства. Кривошип устанавливается в кронштейне и корпусе механизма натяжения на двух бронзовых втулках, выполняющих роль подшипников.
От проворачивания кривошип удерживается зубчатой муфтой 22, которая поджимается к зубцам корпуса механизма натяжения гайкой 25 и фиксируется стопором 24 с болтом 23.
Червячное колесо насажено на шлицы кривошипа и фиксируется от осевого перемещения упорным кольцом 28. Червяк установлен вертикально на двух бронзовых втулках и предохраняется от осевых перемещений буртами, выполненными на оси червяка.
При вращении шестигранной головки вала червяка вращается червячное колесо, которое поворачивает кривошип с направляющим колесом, изменяя степень натяжения гусеницы. Перед вращением червяка зубчатая муфта должна быть выведена из зацепления с корпусом механизма натяжения.
Для смазки в корпусе механизма натяжения имеется отверстие с пробкой. Уплотнительные кольца 26, 31 и манжета 35 предохраняют полость червячного механизма от попадания воды и грязи.
6.1.7. Регулировка натяжения гусениц
Инструмент и принадлежности: ключ гусеницы, ключ 14х17, вороток, удлинитель, сменная головка 24, ключ-трещотка, молоток, линейка, шплинтовыдергиватель (в ящике механика-водителя), ключ 7811-0322, приспособление для снятия скоб, нить с грузом (в ящике для ЗИП), стяжное приспособление (на днище в среднем отделении), ключ 32х36 (в сумке с ЗИП двигателя), шаблон (в групповом комплекте ЗИП), ломик (на стойке перегородки).
Регулировать натяжение гусениц только при положении оси направляющего колеса на верхней части дуги окружности, описываемой кривошипом, для чего:
– установить машину, не применяя торможения, на ровном твердом участке местности;
– расконтрить кривошип направляющего колеса – вывернуть болт 23 (рис. 6.4), снять стопор 24, ослабить гайку 25; вывести зубчатую муфту 22 из зацепления с муфтой корпуса механизма натяжения;
– на заправочные пробки первого и второго поддерживающих катков натянуть нить, при этом провисание нити не допускается.
Величина провисания гусениц определяется замером расстояния от натянутой нити до полотна трака, лежащего на первом поддерживающем катке, и до полотна трака, расположенного посередине между первым и вторым поддерживающими катками.
Величина провисания гусеницы определяется разностью полученных величин (рис. 6.1). Для регулировки провисания вращать червяк 21 (рис. 6.4) механизма натяжения ключом-трещоткой до тех пор, пока величина провисания не станет равной 6–8 мм;
– законтрить кривошип, для чего ввести зубчатую муфту 22 в зацепление с муфтой корпуса натяжного механизма, затянуть гайку 25, установить стопор 24, ввернуть болт 23 и разгрузить червяк, повернув его в обратную сторону;
– проверить величину провисания гусеницы, которая должна быть 6–8 мм, при необходимости операцию натяжения повторить.
При невозможности обеспечения требуемой величины провисания рассоединить гусеницу и удалить один трак. Для этого:
– ослабить гайки крепления очистителя 12 (рис. 6.1);
– передвинуть очиститель на максимально возможное расстояние от обода направляющего колеса;
– расконтрить кривошип направляющего колеса;
– вращать червяк механизма натяжения ключом-трещоткой до максимального ослабления гусеницы;
– очистить от грязи шестигранные отверстия и вывернуть четыре болта 7 (рис. 6.5) крепления скоб;
– очистить от грязи отверстия в пальцах демонтируемого трака с обоих концов на глубину 5–10 мм;
– расшплинтовать валик 11 и вынуть его и втулку 10 из приспособления;
– установить съемник на скобу (без втулки), после чего соединить съемник со скобой валиком и зашплинтовать валик;
Рис. 6.5. Соединение концов гусениц:
1 – пробка; 2 – ведущее колесо; 3 – ключ-трещотка; 4, 6 – пальцы трака; 5 – стяжное приспособление; 7 – болт; 8 – опорный каток; 9 – скоба; 10 – втулка; 11 – валик; 12 – шплинт; 13 – основание; 14 – упоры; 15 – винт
– вставить упоры 14 в отверстия пальцев трака и вращать винт 15 ключом-трещоткой (при необходимости с ломиком) до тех пор, пока снимаемая скоба не передвинется от торца трака на 10–15 мм, после чего с помощью этого же съемника передвинуть на такое же расстояние противоположную скобу; во избежание поломки съемника применять другие удлинители ручки ключа-трещотки, кроме ломика, запрещается;
– установить на пальцы стяжные приспособления и ключом-трещоткой вращать винты до положения, обеспечивающего свободное снятие скоб;
– с помощью съемника снять передвинутые от торца трака скобы;
– снять стяжные приспособления, предварительно отпустив винты;
– с помощью съемника снять другие две скобы и удалить трак; если усилий одного человека недостаточно для снятия скобы, несколько раз ударить молотком по торцу щеки съемника и по скобе; операцию повторять при каждом заедании скобы;
– соединить концы гусеницы (между ведущим колесом и передним опорным катком) стяжными приспособлениями, которые своими захватами надеваются на пальцы 4 и 6 соединяемых траков, и вращать винты стяжных приспособлений до положения, позволяющего установить скобы на пальцы соединяемых траков. Для предотвращения перекосов или срывов стяжных приспособлений с пальцев соединяемых траков стягивать их надо равномерно, поочередным вращением винтов стяжных приспособлений;
– надеть скобы на пальцы соединяемых траков и снять стяжные приспособления;
– установить шаблон под передний опорный каток со стороны ведущего колеса;
– медленно передвинуть машину вперед до перемещения места соединения гусеницы на шаблон и остановить машину;
– установить болты в скобы и затянуть; момент затяжки 392–470 Нм (40–48 кгс-м) или с усилием 490–588 Н (50–60 кгс) на плече 800 мм;
– переместить машину назад и убрать шаблон.
При отсутствии шаблона (в полевых условиях) болты крепления клиньев гусеницы соединяемых траков затягивать на направляющем колесе в следующем порядке:
– медленно передвинуть машину вперед до перемещения соединяемых траков на обод направляющего колеса;
– затянуть болт крепления скобы с наружной стороны гусеницы;
– медленно передвинуть машину назад до перемещения соединяемых траков на наклонный участок гусеницы между направляющим колесом и шестым опорным катком;
– затянуть болт крепления скобы с внутренней стороны гусеницы; соединение без шаблона допускается как временное с последующей перетяжкой болтов гусеницы, соединяемых по шаблону, с заменой болтов (в месте соединения), если они будут помяты;
– натянуть гусеницы и застопорить кривошип направляющего колеса;
– затянуть гайки крепления очистителя, отрегулировав расстояние между ободом направляющего колеса и очистителем 3–5 мм.
6.1.8. Замена гусениц
Инструмент и принадлежности: ключ гусеницы, вороток, удлинитель (в ящике механика-водителя), трос для надевания гусеницы (на правом борту на корме), шаблон (в групповом комплекте ЗИП), лом (на крыше десантного отделения), стяжное приспособление гусеницы (на днище в среднем отделении).
Новые гусеницы (с 85 траками) надевать на машину, а после 100–150 км пробега снять.
Поставить гусеницу на торцы пальцев так, чтобы каждый трак был повернут относительно сопрягаемого с ним трака на угол, определяемый шаблоном, и подтянуть болты крепления скоб с усилием 490–588 Н (50–60 кгс) на плече 800 мм.
Снятая с машины гусеница должна быть свернута в бухту гребнями траков внутрь, при этом диаметр отверстия бухты должен быть не менее 560 мм, что соответствует диаметру направляющего колеса. Запрещается перегибать гусеницу в каждом шарнире в любую сторону более чем на 15° от положения гусеницы в развернутом виде.
Надевать гусеницу на машину в следующем порядке:
– развернуть гусеницу впереди машины;
– пустить двигатель;
– дать звуковой сигнал;
– наехать опорными катками на гусеницу, при этом гусеницу подправлять под катки ломом, двигаться на первой передаче, пока под первым опорным катком не останется два–три трака гусеницы; если гусеницы сняты с обеих сторон, наезд производить с помощью тягача;
– затормозить машину стояночным тормозом и остановить двигатель;
– один конец троса для надевания гусеницы закрепить петлей за выступающие концы пальца трака, натянуть трос вручную и пропустить его между ободами направляющего колеса, а другой конец троса намотать на ступицу ведущего колеса, сделав три–четыре витка;
– пустить двигатель;
– дать звуковой сигнал;
– повернуть руль в левое или правое крайнее положение (в сторону, противоположную надеваемой гусенице);
– отпустить рукоятку привода стояночного тормоза;
– включить первую передачу и в момент натяжения верхнего участка гусеницы ведущим колесом нажать на педаль остановочных тормозов, одновременно выжав до упора педаль главного фрикциона, выключить передачу и перевести руль в нейтральное положение;
– затормозить машину стояночным тормозом;
– остановить двигатель;
– снять трос с пальца трака и с ведущего колеса;
– соединить и натянуть гусеницы согласно п. 6.1.7.
6.1.9. Подтяжка пробки крепления ведущего колеса
на водиле бортовой передачи
Инструмент и принадлежности: ключ 14х17, плоскогубцы, сменные головки 17, 27, удлинитель, молоток (в ящике механика-водителя), ломик (на стойке перегородки силового отделения), лом (на крыше десантного отделения), ключ для гайки крепления ведущего колеса (в групповом комплекте ЗИП), проволока КО 1,6 (в ящике для ЗИП).
Для подтяжки пробки необходимо:
– снять поплавок крыла, отвернув болты его крепления;
– снять передний лист крыла, отвернув болты его крепления;
– снять проволоку, стопорящую болт 7 (рис. 5.8);
– отвернуть на один оборот болт 7, после чего ударом молотка по головке болта сдвинуть его внутрь пробки 27 до упора;
– затянуть пробку 21 усилием 588–686 Н (60–70 кгс) на плече 1 м;
– затянуть болт 7 усилием 196–294 Н (20–30 кгс) на плече 1 м и законтрить его проволокой;
– установить передний лист и поплавок и закрепить их.
6.1.10. Использование опорного катка вместо направляющего колеса
Инструмент и принадлежности: ключ гусеницы, вороток, удлинитель, ключи 14х17, 19х22, шплинтовыдергиватель, ключ-трещотка, молоток (в ящике механика-водителя), ключ 7811-0322, приспособление для снятия скоб (в ящике для ЗИП), приспособление для снятия нижнего пальца гидроамортизатора, приспособление для снятия торсиона, домкрат (в групповом комплекте ЗИП), стяжное приспособление (на днище в среднем отделении), ломик (на стойке перегородки силового отделения).
В случае разрушения направляющего колеса или его кривошипа для продолжения движения машины можно использовать вместо направляющего колеса шестой опорный каток.
Для этого необходимо:
– разгрузить шестой опорный каток с помощью домкрата, подняв кормовую часть машины (предварительно затормозив машину) и наехав на яму;
– разъединить гусеницу и удалить из нее девять траков;
– снять гидроамортизатор с шестого опорного катка;
– вынуть с помощью приспособления торсион, предварительно вывернув болты его крепления;
– поднять шестой опорный каток до упора балансира в пружинный упор, в этом положении катка установить торсион на место и закрепить болтами;
– соединить гусеницу;
– убрать домкрат.
6.2. Подвеска
В качестве системы подрессоривания машины служит независимая торсионная подвеска. Она предназначена для смягчения толчков и ударов, воспринимаемых корпусом машины, при движении по неровной дороге или местности.
Подвеска состоит из двенадцати торсионных валов 29 (рис. 6.3), двенадцати балансиров 23, двенадцати кронштейнов 2 подвески, четырех резиновых упоров 6 (рис. 6.1), четырех пружинных упоров 2 и шести гидравлических амортизаторов 5.
6.2.1. Торсионный вал
Торсионные валы являются упругими элементами подвески. Они представляют собой длинные стальные стержни цилиндрической формы с малой и большой шлицованными головками и размещаются поперек машины над днищем. Одной головкой торсионный вал входит в шлицевое отверстие трубы балансира, а другой – в шлицевую втулку кронштейна подвески, приваренного к противоположному борту корпуса машины.
Чтобы предохранить торсионный вал от коррозии и возможных механических повреждений рабочих поверхностей, стержень его после грунтовки и покраски обвернут двойным слоем прорезиненной изоляционной ленты и покрыт сверху бакелитовым лаком.
Торсионный вал удерживается от продольного смещения в трубе балансира и в кронштейне подвески крышками 26 (рис. 6.3) и болтами 25, ввертываемыми в резьбовые отверстия на торцах торсионных валов. Отверстие в большой головке используется также для извлечения торсионного вала из кронштейна подвески и трубы балансира. Торсионные валы правых и левых опорных катков на торцах головок маркируются соответственно «Прав.» и «Лев.».
Невзаимозаменяемость торсионных валов правого и левого борта машины вызвана тем, что при работе они имеют разное направление закручивания и при изготовлении подвергаются предварительному упрочняющему закручиванию в том же направлении.
6.2.2. Балансир и кронштейн подвески
Балансир 23 выполнен из стали. Стержень, труба 1 балансира, а также ось 6 катка – пустотелые. Отверстие в стержне балансира закрыто пробкой. Внутри трубы балансира имеются устройства для соединения с торсионным валом. Труба балансира установлена на двух втулках 27, запрессованных в отверстия кронштейна подвески.
При наезде машины на препятствие балансир поворачивается и закручивает торсионный вал, вследствие чего толчки и удары, воспринимаемые корпусом машины, смягчаются. Для исключения изгиба балансира в случае сильных боковых ударов катков о препятствия на обоих бортах около передних катков приварены ограничители 8.
Балансиры имеют площадки для упора. К первым, вторым и шестым балансирам приварено по два уха 24 для соединения с гидравлическими амортизаторами.
Кронштейн 2 подвески приварен к бортовому листу и днищу машины. Во внутренней полости кронштейна имеются две расточки для запрессовки втулок и шлицы для малой головки торсионного вала. С внешней стороны в кронштейне подвески имеется выточка, в которую устанавливаются резиновые манжеты 28, предохраняющие втулку 27 от загрязнения. Для смазки втулок в кронштейнах подвески на борту машины имеются отверстия, которые закрываются пробками 3.
6.2.3. Пружинные и резиновые упоры
Пружинные упоры 2 (рис. 6.1) и резиновые упоры 6 ограничивают ход балансиров. Пружинные упоры установлены над первыми и шестыми опорными катками. Они состоят из пружины, основания, бойка, болта и стопорной шайбы. Резиновые упоры установлены над вторыми и четвертыми катками.
6.2.4. Гидравлические амортизаторы
Гидравлические амортизаторы (рис. 6.6) служат для гашения колебаний машины, возникающих при ее движении.
![]() | Рис. 6.6. Гидроамортизатор: 1 – клапан; 2 – впускной клапан; 3 – канал для прохода жидкости; 4 – регулировочные прокладки; 5 – уплотнительные кольца; 6 – клапан обратного хода; 7 – клапан прямого хода; 8 – направляющая клапана; 9 – рабочий цилиндр; 10 – опора; 11 – манжеты; 12 – шайба; 13 – защитный кожух; 14 – проушина; 15 – верхняя проушина; 16 – сферическая полость; 17 – втулка с заправочной пробкой; 18 – пружины; 19 – втулка; 20, 21, 26 – резиновое кольцо; 22 – пробка; 23 – канал для прохода жидкости; 24 – поршень; 25 – клапан для выпуска избыточной рабочей жидкости; 27 – регулировочные прокладки |
Гидравлический амортизатор устроен следующим образом. В верхнюю часть корпуса А вворачивается корпус Б уплотнения с опорой 10. Рабочий цилиндр 9 с поршнем 24 и штоком зажимаются между опорой 10 и крышкой. В нижней части выполнены каналы 3, 23 для прохода жидкости.
На конец штока наворачивается верхняя проушина 15 со сферой 16, втулкой 17 и заправочной пробкой. В поршне 24 размещены: клапан 7 прямого хода, направляющая 8 клапана, втулка с дроссельным отверстием и клапан 6 обратного хода. В клапане обратного хода имеются регулировочные прокладки 4. В канавках поршня установлены уплотнительные кольца 5. В крышке с нижней проушиной предусмотрен клапан 25 для выпуска избыточной рабочей жидкости в компенсационную камеру при прямом ходе поршня – вниз; впускной клапан 2 пропускает жидкость из компенсационной камеры при обратном ходе поршня – вверх.
Уплотнение штока состоит из шайбы 12, манжеты 11, разделенных манжеторазделителем, поджимаемым через стальное кольцо восемью пружинами 18, помещенными в отверстия втулки 19. В опоре 10 помещена резиновая манжета. Кроме того, цилиндр 9 со стороны опоры 10 и крышки уплотнен резиновыми кольцами 21 и 26. Корпус А с крышкой уплотнен резиновым кольцом 20, а с корпусом уплотнения Б – резиновым кольцом 26.
Рабочая жидкость – 760 см3 (50 % турбинного и 50 % трансформаторного масла), заправляется через пробку 22.
Защитный кожух 13, навернутый на проушину 15 и застопоренный болтом со стопорной планкой, предохраняет шток от повреждений.
40. Водооткачивающие средства
Водооткачивающие средства предназначены для удаления воды, проникшей в корпус машины при преодолении водной преграды. На машине имеются три водооткачивающих насоса:
– два водооткачивающих насоса расположены в силовом отделении: один с приводом от двигателя машины через редуктор компрессора, другой – с приводом от электродвигателя;
– третий, кормовой водооткачивающий насос с приводом от электродвигателя расположен в десантном отделении (этот электродвигатель одновременно является приводным для насоса ТДА).
Вода насосами откачивается через три обратных клапана. Для ускорения откачки воды, проникшей в отделение управления, служит клапан на перегородке силового отделения. При открытом клапане вода может перетекать из отделения управления в силовое.
8.1. Устройство водооткачивающих средств
Основными деталями водооткачивающего насоса с приводом от двигателя машины через редуктор компрессора являются корпус 2 (рис. 8.1), валик 4 привода, крыльчатка 5, жестко закрепленная на валике, сетка 6 и уплотнение 3.
![]() | Рис. 8.1. Водяной откачивающий насос с приводом от двигателя через редуктор компрессора: 1 – цапфа; 2 – корпус водяного насоса; 3 – уплотнения; 4 – валик привода водяного насоса; 5 – крыльчатка водяного насоса; 6 – сетка |
Основными деталями двух других водооткачивающих насосов с приводом от электродвигателя являются корпус 7 (рис. 8.2), крыльчатка 8, электродвигатель 6 сетки 9 и 10, самоподжимные манжеты 11 и 12.
Крыльчатка 8 в носовом водооткачивающем насосе крепится непосредственно на валу электродвигателя, а в кормовом водооткачивающем насосе – на валике 3 с конической шестерней, соединяющейся с конической шестерней валика 2, закрепленного на валу электродвигателя.
На электродвигателе установлена дренажная трубка, которая служит для предотвращения попадания воды во внутреннюю полость электродвигателя, а также для сообщения внутренней полости с атмосферой.
Рис. 8.2. Водяной откачивающий насос с приводом от электродвигателя:
1 – корпус насоса ТДА; 2, 3 – валики; 4 – корпус редуктора; 5 – вал электродвигателя;
6 – электродвигатель; 7 – корпус водяного насоса; 8 – крыльчатка водяного
насоса; 9 – сетка; 10 – нижняя сетка; 11, 12 – самоподжимные манжеты
Обратные клапаны расположены справа на корпусе машины. Все три клапана имеют одинаковое устройство. Основными деталями клапанов 1 (рис. 8.3) являются фланец 5, стержень 6 клапана, пружина 7 и втулка 8. Обратные клапаны соединены с корпусами насосов трубопроводами.
![]() | Рис. 8.3. Обратный клапан: 1 – обратный клапан; 2 – корпус машины; 3 – резиновое кольцо; 4 – уплотнительные прокладки; 5 – фланец; 6 – стержень клапана; 7 – пружина; 8 – втулка; 9 – труба |
41.Система электрооборудования
Совокупность различных электрических машин, приборов и аппаратов, объединенных общей электрической сетью, составляет единую систему – систему электрооборудования.
Электрооборудование обеспечивает электропитание всех электрических потребителей, управление и контроль за их работой. Оно включает в себя источники и потребители электрической энергии, а также приборы вспомогательного оборудования, контрольно-измерительные приборы и бортовую сеть. Общая электрическая схема системы электрооборудования БМП представлена на рис. 10.1.
Рис. 10.1. Принципиальная схема цепей источников питания машины:
ОВГ – обмотка возбуждения генератора; ОДП – обмотка дополнительных полюсов генератора; ЯГ – якорь генератора; РН-10 – регулятор напряжения; Ф – фильтр радиопомех;
ДРМ-400Т – дифференциально-минимальное реле; К – контактор включения генератора; Р1, Р2, Р3, Р4 – коммутационные реле; Р5 – дифференциальное реле; 1Р5 – обмотка дифференциального реле; 2Р5 – сериесный виток дифференциального реле; ВА – вольтамперметр;
Ш – шунт вольтамперметра; Пр8 – предохранитель; АБ – аккумуляторные батареи; ВБ –
выключатель аккумуляторных батарей; ББ1 – контактор включения батарей
К источникам электрической энергии относятся аккумуляторные батареи и генератор с регулирующей аппаратурой.
К потребителям электрической энергии относятся электрооборудование приводов наведения, блока БУ-25-2С, приборов наблюдения и прицеливания, пусковой установки 9П135М, системы коллективной защиты, системы защиты двигателя от попадания воды, радиостанции Р-123м, переговорного устройства Р-124, приборов освещения, световой и дорожной сигнализации, системы обеспечения холодного пуска двигателя.
К вспомогательному оборудованию относят: вращающееся контактное устройство ВКУ-330-2, розетка внешнего пуска, центральный щиток механика-водителя, силовой щиток, релейная коробка КР-40-1С, релейные коробки
КР-55, КР-60 с РТС-27-3А и КР-65-1С, конечные выключатели и электромагниты, фильтр радиопомех.
Контрольно-измерительные приборы предназначены для контроля за режимами работы силовой установки и систем ее обслуживающих.
10.1. Назначение, размещение приборов системы электрооборудования
10.1.1. Источники электрической энергии
Источники электрической энергии включают в себя:
1) стартерные аккумуляторные батареи марки 6СТЭН-140м – 2 ед.;
2) генератор ВГ-7500 с регулирующей аппаратурой.
Аккумуляторные батареи предназначены для питания потребителей электрической энергии.
На машине установлены две кислотные аккумуляторные батареи типа 6СТЭН-140м. Они размещены в аккумуляторном отсеке в кормовой части десантного отделения за топливным баком. Общее напряжение батарей 24 В, емкость 140 Ач, соединение – последовательное.
Генератор марки ВГ-7500 служит для питания потребителей машины электроэнергией и для зарядки аккумуляторов. Он работает в комплексе с дифференциально-минимальным реле ДМР-400Т и регулятором напряжения РН-10.
Генератор установлен на двигателе и приводится во вращение через шестерни механизма передачи и муфту привода. Генератор ВГ-7500 постоянного тока, шестиполюсной, смешанного возбуждения, с принудительным охлаждением.
Реле ДМР-400Т служит для автоматического отключения генератора от электрической сети машины, когда его напряжение ниже напряжения аккумуляторных батарей, и для включения генератора, когда его напряжение становится выше напряжения аккумуляторов.
Реле ДМР-400Т смонтировано в аккумуляторном отсеке. Особенностью работы дифференциально-минимального реле является то, что оно подключает генератор к батареям только в том случае, когда напряжение генератора превышает напряжение аккумуляторов на 0,3–0,7 В независимо от абсолютного значения напряжения генератора, как это имеет место при реле обратного тока. Отключение генератора происходит тогда, когда величина обратного тока достигает 15–35 А.
Регулятор РН-10 предназначен для поддержания в заданных пределах напряжения генератора при изменении скорости вращения его якоря. Он также защищает потребители при выходе из строя элементов регулятора при аварийных режимах.
Регулятор установлен в аккумуляторном отсеке сверху на полке. Регулятор скомпонован в алюминиевом корпусе, закрытом двумя крышками. На корпусе размещены измерительный блок и два штепсельных разъема (Ш1 и Ш2), из которых Ш1 служит для соединения регулятора с сетью, а Ш2 – для проверки электрического монтажа. На боковой стенке корпуса размещена плата с предохранителями, закрытая крышкой.
Регулятор состоит из измерительного устройства (ИУ), регулирующего устройства (РУ), обратных связей и элементов защиты.
10.1.2. Потребители электрической энергии
Основными потребителями электрической энергии являются электрический стартер, электродвигатели, электромагниты, приборы освещения и световой сигнализации.
Потребители электрической энергии включают в себя:
1) электрооборудование приводов наведения, блока БУ-25-2С, приборов наблюдения и прицеливания, пусковой установки 9П135М;
2) электрооборудование радиостанции Р-123м, переговорного устройства Р-124 (Р-174);
3) электрооборудование системы защиты двигателя от попадания воды;
4) электрооборудование системы обеспечения холодного пуска двигателя;
5) электрооборудование системы коллективной защиты;
6) электрооборудование электрического стартера, электрических двигателей, приборов освещения, световой и дорожной сигнализации.
42. 43.Источники электроэнергии, световые приборы,
Электродвигатели
Электродвигатели предназначены для приведения в действие различных приборов, агрегатов, обеспечивающих работу двигателя, систем боевой машины и электрооборудования.
Электродвигатель МВ-67 предназначен для привода нагнетателя.
На машине имеется два электродвигателя МВП-2. Один из них служит приводом переднего водооткачивающего насоса, а другой приводит в действие задний водооткачивающий насос и насос ТДА.
Включаются электродвигатели выключателями, расположенными на центральном щитке водителя ОТКАЧКА ВОДЫ-НОС, КОРМА и ТДА.
Электродвигатель МН-1 предназначен для приведения в действие маслозакачивающего насоса МЗН-3. Электродвигатель МН-1 включается кнопкой МЗН, расположенной на центральном щитке водителя.
Электродвигатель Д-100 приводит в действие подкачивающий топливный насос БЦН.
Электродвигатель МПБ-3Н служит для привода насосного узла подогревателя.
Включение электродвигателя осуществляется выключателем ОБОГРЕВ ДВИГАТ. на центральном щитке водителя.
Электродвигателей Д-55 на машине установлено четыре. Электродвигатели приводят в действие три вытяжных вентилятора корпуса и башни и вентилятор отопителя десантного отделения.
Приборы освещения, световой и дорожной сигнализации
В зависимости от места установки все приборы освещения разделяются на наружные и внутренние.
К наружному освещению относятся фары ФГ-127, ФГ-126 и ФГ-125.
Фара ФГ-127 (рис. 10.3) служит для освещения пути видимым светом при движении машины ночью с соблюдением светомаскировки. Фара установлена в носовой части корпуса у левого борта, включается выключателем СМУ на центральном щитке.
Рис. 10.3. Приборы освещения и сигнализации:
1 – светомаскировочная насадка; 2 – рассеиватель; 3 – резиновая прокладка; 4 – кольцо; 5 – ободок; 6 – резиновое кольцо; 7 – рефлектор; 8 – корпус фары; 9 – уплотнительная прокладка; 10 – винт крепления оптического элемента; 11 – штепсельная колодка; 12 – держатель кожуха; 13 – кожух; 14 – лампа с патроном; 15 – крепежный винт; 16 – винт; 17 – диск светомаскировочной насадки; 18 – прорези в диске; 19 – крышка
Светомаскировочная насадка представляет собой металлический штампованный диск с буртом. В верхней части диска имеются две щелевидные прорези, прикрытые козырьком. Снизу козырек закрыт щитком, который устраняет освещение носовой части машины.
Нижняя часть диска выполнена в виде откидывающейся кверху крышки, фиксирующейся в нижнем и верхнем положениях пружинными фиксаторами.
Светомаскировочная насадка фары обеспечивает три режима светомаскировки:
– полное затемнение, когда нижняя линза закрыта, накал нити лампы снижен (переключатель СМУ находится в положении М);
– частичное затемнение, когда нижняя линза закрыта, нить лампы горит полным накалом;
– незатемненный режим, когда нижняя линза открыта, нить лампы горит полным накалом.
Фара ФГ-126 установлена на башне и предназначена для улучшения видимости при преодолении водных преград и во время движения машины ночью. В отличие от фары ФГ-127 она не имеет светомаскировочной насадки. Включается фара выключателем ФАРА на панели управления блока БУ-25-2С. На фаре ФГ-126 установлена цифровая насадка для обозначения номера машины. Пакет цифр к цифровой насадке уложен в ЗИП. В нем имеется набор цифр: 0–9.
Фара ФГ-125 предназначена для работы ночью с прибором ТВНЕ-4Б. Она установлена в носовой части корпуса у правого борта машины. По устройству она одинакова с фарой ФГ-126, но имеет в оптическом элементе инфракрасный фильтр. Включается фара выключателем, расположенным на центральном щитке.
К приборам внутреннего освещения относятся:
1) плафоны типа ПМВ-71. Плафоны обеспечивают освещенность, необходимую для работы экипажа и десанта. На машине установлены семь плафонов ПМВ-71 (с автономными выключателями). В отделении управления – один (между механиком-водителем и десантником на перегородке). В боевом отделении – два (на наклонном листе слева от оператора и справа от командира).
В десантном отделении – четыре (около левой и правой дверей и в районе боевого отделения).
Плафоны боевого отделения и плафон, расположенный у левой двери десантного отделения, в отличие от остальных плафонов, включены в бортовую сеть по двухпроводной схеме питания от аккумуляторных батарей, минуя выключатель батарей;
2) светильники ПЛТ-50-6. Они предназначены для освещения приборов и механизмов внутри или снаружи машины при техническом обслуживании и ремонте. Подсоединяется светильник через розетки ШР-51, установленные в боевом отделении слева от оператора и в десантном отделении у левой двери. Розетки включены в бортовую сеть машины по двухпроводной схеме;
3) створчатые фонари КЛСТ-64. Фонари предназначены для подсветки центрального щитка механика-водителя. Их включение производится выключателем ОСВЕЩ. ЩИТКА в положение ДЕНЬ или НОЧЬ.
Дорожная сигнализация предназначена для обозначения габаритов машины в ночное время и прерывистой световой сигнализации при осуществлении маневров машины и при ее торможении.
В состав дорожной сигнализации входят: коробка дорожной сигнализации КДС1-2С, пульт управления дорожной сигнализации ДС, переключатель указателей поворотов ППН-45 и габаритные фонари.
Коробка КДС1-2С крепится в нише левого борта в отделении управления на трех бонках болтами и предназначена для управления режимами работы дорожной сигнализации.
Пульт ДС установлен под центральным щитком и обеспечивает переключение габаритных фонарей в режиме большого или малого света.
Переключатель поворотов ППН-45 установлен на рулевой колонке и обеспечивает включение указателей поворотов.
Габаритные фонари установлены в корпусе машины.
В передних габаритных фонарях устанавливается зеленый светофильтр, в боковых – желтый, в задних – красный. Включаются габаритные фонари выключателем ГАБАРИТ. КДС, который расположен на центральном щитке механика-водителя.
При включенном выключателе ГАБАРИТ. КДС на центральном щитке в зависимости от положения переключателей на пульте ДС система обеспечивает следующие режимы работы:
1) переключатель ГАБАРИТЫ Б-М – в положении Б, переключатель
ГАБАРИТЫ ВСЕ – ЗАДН. – в нейтральном положении:
– при нейтральном положении переключателя поворотов и отпущенной педали тормоза габаритные фонари не горят;
– при нажатой педали тормоза должны мигать задние габаритные фонари и контрольная лампа на пульте ДС;
– при включенном переключателе поворотов вправо (или влево) и отпущенной педали тормоза должны мигать правые (или левые) габаритные фонари и контрольная лампа; при нажатой педали тормоза должны мигать контрольная лампа на пульте ДС и три задних фонаря, а остальные должны погаснуть;
2) переключатель ГАБАРИТЫ Б-М – в положении Б, переключатель ГАБАРИТЫ ВСЕ – ЗАДН. – в положении ЗАДН.:
– при нейтральном положении переключателя поворотов и отпущенной педали тормоза должны гореть задние габаритные фонари;
– при нажатой педали тормоза должны мигать задние габаритные фонари и контрольная лампа на пульте ДС;
– при включенном переключателе поворотов вправо (влево) и отпущенной педали тормоза должны гореть задние средний и левый (правый) габаритные фонари, мигать правые (левые) габаритные фонари и контрольная лампа на пульте ДС; при нажатой педали тормоза должны мигать задние габаритные фонари, остальные фонари должны погаснуть;
3) переключатель ГАБАРИТЫ Б-М – в положении Б, переключатель
ГАБАРИТЫ ВСЕ – ЗАДН. – в положении ВСЕ:
– при нейтральном положении переключателя поворотов и отпущенной педали тормоза должны гореть все габаритные фонари; при нажатой педали тормоза должны гореть передние и боковые габаритные фонари, а задние и контрольная лампа на пульте ДС должны мигать;
– при включении переключателя поворотов вправо (влево) и отпущенной педали тормоза должны мигать все правые (левые) габаритные фонари и контрольная лампа, остальные габаритные фонари должны гореть; при нажатой педали тормоза должны гореть передние и боковые габаритные фонари, а задние и контрольная лампа должны мигать;
4) переключатель ГАБАРИТЫ Б-М – в положении М – функционирование системы дорожной сигнализации осуществляется как и при положении переключателя в режиме Б, на фонари подается пониженное напряжение, при этом боковые средние фонари обесточены.
При выключении выключателя ГАБАРИТ. КДС на центральном щитке не должен гореть и мигать ни один габаритный фонарь независимо от положения переключателя поворотов и педали тормоза.
Звуковой электрический сигнал С314Г установлен снаружи машины на наклонном лобовом листе слева от механика-водителя и служит для внешней звуковой сигнализации.
К световой сигнализации относятся десять фонарей ФРМ, два фонаря ОСЛТ-37 и одно световое табло ОТПУСТИ РУЧНОЙ ТОРМОЗ.
Фонари ФРМ-1 расположены на центральном щитке механика-водителя.
Световое табло ОТПУСТИ РУЧНОЙ ТОРМОЗ расположено под центральным щитком и предупреждает о том, что при трогании с места необходимо отпустить ручной тормоз.
Фонари ОСЛТ-37 расположены в нишах корпуса десантного отделения с левой и правой стороны и сигнализируют об открытых люках корпуса.
44. Аккумуляторы
Аккумуляторные батареи предназначены для питания потребителей электрической энергии:
- при неработающем двигателе (стартер, освещение и т.д.);
- при работе двигателя на малых оборотах, когда генератор еще не подключен к бортовой сети;
- для питания мощных потребителей совместно с генератором, когда потребляемый ими ток превосходит допустимую для генератора величину.
На БМП применяются две аккумуляторные батареи (АБ) типа 6СТЭН‑140м. Они располагаются в десантном отделении в контейнере и имеют следующие основные показатели:
Тип батареи | 6 СТЭН-140 м |
Номинальное напряжение, В | 12 |
Номинальная емкость (при 20-часовом режиме разрядки), Ач | 140 |
Габариты, мм | 587х238х239 |
Масса, кг | |
без электролита | 52,5 |
с электролитом | 62,0 |
Количество электролита, л | |
в батарее | 8,0 |
в аккумуляторе | 1,33 |
10.3.2. Общее устройство и работа
танковых аккумуляторных батарей
Танковая аккумуляторная батарея (рис. 10.10) состоит из шести аккумуляторов, соединенных последовательно. Номинальное напряжение батареи, состоящей из шести аккумуляторов, равно 12 В.
Аккумуляторная батарея состоит:
1) 6 последовательно соединенных аккумуляторов;
2) крышка батареи;
3) защитный клемный кожух;
4) корпус (ящик) батареи;
5) выводные зажимы;
6) межаккумуляторные соединительные перемычки;
7) мастичный слой.
Рис. 10.10. Аккумуляторная батарея 6СТЭН-140м:
1 – крышка батареи; 2 – отверстие под направляющую бонку; 3 – болт; 4 – пластмассовая защитная коробка; 5 – направляющая бонка; 6 – ящик батареи; 7 – ручка; 8 – щиток крепления пластмассовой коробки; 9 – мастика; 10 – выводные зажимы; 11 – пробка; 12 – межаккумуляторное соединение; 13 – направляющая крышки батареи; 14 – аккумуляторная крышка; 15 – стяжка аккумуляторной батареи; 16 – полюсной вывод; 17 – предохранительный щиток; 18 – свинцовые втулки; 19 – свинцовый мостик; 20 – отрицательная пластина; 21 – стопорная призма; 22 – сепаратор; 23 – положительная пластина
Маркировка АБ. На средней межаккумуляторной перемычке указывается тип батареи, товарный знак завода-изготовителя, дата изготовления (год и месяц), номер ГОСТ или ТУ, номер батареи.
Цифры и буквы типа батареи обозначают следующее:
– первая цифра указывает число аккумуляторов в батарее, соединенных последовательно;
– буквы «СТ» обозначают «стартерная»;
– буквы «ЭН» обозначают материал сосудов (бачков) аккумуляторов (эбонит) и новую серию (Н);
– цифры «140» указывают емкость батареи при 20-часовом режиме разряда;
– буква «м» – материал сепараторов (р – мипор, м – мипласт, с – стекловолокно).
Аккумулятор состоит:
1) бачок;
2) полублок положительных пластин;
3) полублок отрицательных пластин;
4) сепараторы;
5) предохранительный щиток;
6) крышка с пробкой и прокладкой.
Бачок аккумулятора изготовлен из эбонита. На дне бачка имеются ребра – призмы, на которые опираются пластины аккумулятора. Полость между призмами служит для скопления осыпающейся активной массы пластин (шлама) и исключения короткого замыкания пластин между собой.
Полублоки состоят из пластин, приваренных к общему свинцовому мостику, имеющему полюсный вывод (борн).
Пластины состоят из тонкой свинцовой решетки и вмазанной в нее активной массы.
Разноименные пластины (полублоки) собирают в блок, устанавливая между пластинами сепараторы, устраняющие возможность их соприкосновения. Сверху пластины защищают от повреждения предохранительным щитком из перфорированного хлорвинила.
Сепараторы устанавливают между пластинами так, чтобы их ребра были расположены вертикально и обращены к положительным пластинам, а гладкая сторона – к отрицательным.
При таком положении сепараторов облегчается доступ электролита в поры положительных пластин, уменьшается уплотнение отрицательных пластин, что повышает эксплуатационные качества аккумулятора.
Крышки, закрывающие собранные аккумуляторы сверху, изготавливаются из пластмассы или эбонита. Корпус крышки имеет заливное отверстие, закрываемое пробкой, и две закрепленные в корпусе при изготовлении свинцовые втулки для вывода полюсов аккумулятора.
Пробка крышки имеет вентиляционное отверстие. При сборке на заводе под пробки заливных отверстий подкладываются уплотнительные резиновые диски, придающие герметичность, необходимую при хранении батарей в сухом виде. У некоторых типов батарей герметичность обеспечивают за счет применения полиэтиленовых пробок с глухими выступами, которые при приведении аккумуляторных батарей в рабочее состояние срезаются.
При сборке крышки аккумуляторов в бачках уплотняются резиновой прокладкой и заливаются специальной мастикой.
Аккумулятор представляет собой обратимый электрохимический источник тока. Он обладает способностью за счет проходящих в нем под действием электрического тока электрохимических процессов накапливать электрическую энергию и отдавать ее во внешнюю цепь.
Процесс накапливания энергии аккумулятором называется зарядом, а процесс ее отдачи – разрядом.
Простейший кислотный аккумулятор (рис. 10.11) состоит: из двух пластин свинца, погруженных в водный раствор серной кислоты – электролит.
В результате взаимодействия на обеих пластинах образуется сернокислый свинец (сульфат свинца). Так как состав пластин одинаков, то разность потенциалов между электродами равна нулю.
Если пластины этого аккумулятора подсоединить к источнику постоянного тока, то на пластине, соединенной с положительным зажимом источника тока, образуется перекись свинца РbО2 (двуокись свинца), имеющая коричневый цвет, а на пластине, соединенной с отрицательным зажимом источника – губчатый свинец Рb, имеющий серый цвет.
Рис. 10.11. Работа простейшего аккумулятора:
а – при заряде; б – при разряде; 1 – двуокись свинца;
2 – электролит повышенной плотности; 3 – губчатый свинец;
4 – сульфат свинца; 5 – электролит низкой плотности
При заряде аккумулятора плотность электролита возрастает, так как при этом процессе образуется серная кислота. Если теперь к зажимам заряженного аккумулятора подключить какой-нибудь потребитель, то аккумулятор будет разряжаться. В этом случае ток и направление химического процесса в аккумуляторе станут протекать в обратном порядке.
При разряде аккумулятора на обеих пластинах снова образуется сернокислый свинец (РbSO4), а плотность электролита уменьшается, так как часть серной кислоты в электролите замещается водой.
Изменение удельного веса электролита при разряде и заряде аккумулятора является одним из наиболее удобных показателей его состояния. Снижение удельного веса электролита при разряде является показателем степени разряда аккумулятора, а повышение плотности электролита до величины, соответствующей плотности заряженного аккумулятора, – основным признаком окончания заряда.
45. – 46. Системы ППО и защиты от ОМП
Появление бронетанковой техники как коллективного оружия экипажа повлекло за собой создание средств коллективной защиты.
Самым первым средством коллективной зашиты экипажей явилась броневая защита боевой машины.
С развитием средств поражения развивались и развиваются средства защиты.
Так, с появлением зажигательных средств в начале ХХ века на боевых машинах начали устанавливать системы противопожарного оборудования. Одна из первых систем противопожарного оборудования (ППО), приводившаяся в действие дистанционно, была установлена на советском танке Т-35. В настоящее время на всех бронеобъектах устанавливаются автоматические системы ППО, способные без участия человека приступить к тушению пожара.
С появлением в конце Второй мировой войны ядерного оружия и, как следствие, возникновением целого комплекса оружия массового поражения (ОМП) возникла необходимость создания системы защиты от этого оружия.
Объединение различных систем боевой машины, предназначенных для защиты экипажа и систем машины общими исполнительными механизмами, привело к созданию системы коллективной защиты.
Конструктивно система коллективной защиты состоит:
- из системы противопожарного оборудования (ППО);
- системы защиты от оружия массового поражения (ОМП);
- исполнительных механизмов.
10.4.1. Система противопожарного оборудования
Пожарное оборудование машины предназначено для тушения пожара в машине и состоит из автоматической системы ППО и ручного огнетушителя.
Техническая характеристика системы ППО:
Тип системы – автоматическая двухразового действия;
Кол-во баллонов – 2 шт.;
Тип огнегасящей жидкости – хладон 114В2;
Аппаратура управления – КР-40-1С;
Способ включения – автоматический и ручной;
Количество термодатчиков – 4 шт.
Система ППО состоит из следующих основных частей:
- двух баллонов;
- трубопроводов;
- четырех штуцеров;
- четырех термодатчиков;
- релейной коробки КР-40-1С.
Баллоны емкостью по два литра каждый устанавливаются в носовой части отделения управления на опоре для крепления рулевой колонки. Баллоны заполнены хладоном 114В2. Баллоны в системе ППО подключены через штуцера и накидные гайки к трубопроводам.
Трубопроводы оканчиваются наконечниками, которые расположены против термодатчиков.
Термодатчики (термопары) реагируют на резкое повышение температуры в местах их установки и обеспечивают включение автоматики системы ППО.
Конструкция системы ППО предусматривает постоянную готовность ее к срабатыванию. Для приведения в действие системы ППО вручную помимо термодатчиков служат кнопки 1Б и 2Б, расположенные на центральном щитке механика-водителя под опломбированными крышками.
Принцип действия системы ППО (рис. 10.15)
При включении выключателя ВЫКЛ. БАТАР. загораются неполным накалом лампы 1Б и 2Б сигнализации об исправности цепей пиропатронов баллонов ППО.
Рис. 10.15. Принцип действия системы ППО
При возникновении пожара в силовом отделении один из термодатчиков выдает сигнал на усилитель релейной коробки КР-40-1С и подается питание на электромагниты исполнительных механизмов:
- закрываются жалюзи и заслонки эжектора;
- срабатывает МОД;
- закрываются клапаны вытяжных вентиляторов десантного отделения и вытяжные вентиляторы выключаются.
Срабатывает пиропатрон первого баллона, пробойник под действием газов пробивает мембрану и хладон 114В2 по трубопроводу поступает в силовое отделение, распыливается наконечниками и прекращает доступ воздуха к очагу пожара.
При срабатывании первого баллона лампа 1Б гаснет.
Если пожар не ликвидирован, термопары термодатчиков вновь нагреваются, что вызывает срабатывание второго баллона (гаснет сигнальная лампа 2Б).
При нажатии кнопки 1Б или 2Б через КР-40-1С подается напряжение на первый или второй пиропатрон и выдается сигнал на исполнительные механизмы (закрываются жалюзи и заслонки эжектора, клапаны вытяжных вентиляторов, срабатывает МОД).
Ручной огнетушитель предназначен для тушения очагов пожара в машине, в том числе различных горючих веществ и пожара электроустановок, находящихся под током. Для тушения горючих веществ, горение которых происходит без доступа воздуха (пластинчатый пироксилин, термит), огнетушитель не применяется.
Огнетушитель установлен в десантном отделении слева около кормовой двери на кронштейне.
10.4.2. Система защиты от ОМП
и обеспечения обитаемости боевого расчета
Система защиты и обеспечения обитаемости предназначена для защиты экипажа и оборудования, находящихся внутри машины, от воздействия поражающих факторов атомного взрыва, а также от воздействия радиоактивных, отравляющих веществ и бактериальных средств противника.
Кроме того, система обеспечивает вентиляцию обитаемых отделений, подогрев воздуха, подаваемого нагнетателем внутрь машины, и необходимый газовый состав воздуха в зоне работы экипажа при стрельбе из штатного оружия.
ТХ системы защиты от ОМП
Тип: коллективная, обеспечивающая защиту экипажа и внутреннего оборудования танка от ударной волны, отравляющих и радиоактивных веществ.
Датчик системы: прибор радиационной и химической разведки (ПРХР).
Источник создания избыточного давления: фильтровентиляционная установка (ФВУ).
Исполнительные устройства системы: электромеханические.
Способ включения системы: автоматический и ручной.
В систему защиты от оружия массового поражения и обеспечения обитаемости входят:
- узлы герметизации;
- фильтровентиляционная установка с системой раздачи воздуха;
- система вытяжной вентиляции;
- отопители;
- электрооборудование системы защиты;
- прибор ПРХР.
Принцип работы системы (рис. 10.16)
Защита от радиоактивной пыли, отравляющих веществ и бактериальных средств осуществляется путем герметизации и создания избыточного давления в обитаемых отделениях, а также за счет фильтрации воздуха, подаваемого в обитаемые отделения.
Рис. 10.16. Принцип работы системы по командам «Р» и «О»
Защита от воздействия ударной волны осуществляется только путем герметизации обитаемых отделений машины.
Защитой от проникающей радиации являются броня машины, а также подбой, ослабляющие действие радиации.
При обнаружении прибором ПРХР радиоактивного излучения или отравляющих веществ автоматически срабатывает система защиты.
В случае оповещения об угрозе бактериологического нападения, а также в случае неисправности или отсутствия прибора ПРХР система защиты приводится в действие вручную.
10.4.3. Исполнительные механизмы
Исполнительные механизмы системы защиты обеспечивают герметизацию машины и отключение некоторых из работающих узлов и агрегатов в момент срабатывания системы защиты.
К исполнительным механизмам системы защиты относятся:
- механизм переключения клапана ФПТ;
- механизм отключения жалюзи и заслонок эжектора;
- механизмы закрывания клапанов вытяжных вентиляторов;
- механизм остановки двигателя;
- схема отключения стабилизатора.
10.4.4. Размещение, устройство и принцип действия
приборов системы коллективной защиты
Система ППО
Термодатчики расположены в наиболее пожароопасных местах.
Термодатчик представляет собой коробчатый корпус, в котором размещена колодка с вмонтированными в нее пятнадцатью термопарами. Термопара – проволочный элемент из хромель-копелевой проволоки, состоящей из 2 спаев – холодного и горячего.
Холодные спаи находятся внутри термодатчика и залиты связующим веществом, а горячие спаи выходят наружу и при возникновении пожара охватываются пламенем. В результате этого между холодными и горячими спаями возникает термоЭДС.
Концы крайних термопар соединены с контактами штепсельного разъема. Корпус термодатчика закрыт крышкой, с помощью которой он крепится болтами к установочным кронштейнам.
Баллон ППО (рис. 10.17) имеет головку с сифонной трубкой. Головка баллона состоит: из корпуса, двух пробок, ввернутых в корпус, двух поршней с пробойниками и фиксирующими кольцами, двух мембран.
В полости пробки устанавливается пиропатрон. В корпус головки ввернут штуцер с прокладкой, закрывающий отверстие для зарядки баллона хладоном и азотом. На штуцер навинчивается заглушка. Головка ввернута в баллон штуцером с конической резьбой.
Рис. 10.17. Баллон ППО:
1 – корпус; 2 и 6 – заглушки; 3 – мембрана;
4 – пробка; 5 – штуцер; 7 – гайка; 8 – поршень с пробойником
Баллон заполнен хладоном 114В2 в количестве 1,2–1,3 кг. Хладон 114В2 представляет собой тяжелую бесцветную жидкость со специфическим запахом. Для ускорения истечения хладона в баллон добавляется азот под давлением 70 кг/см2.
Установлены баллоны в носовой части отделения управления на опоре для крепления рулевой колонки.
Управление работой системы осуществляется релейной коробкой КР-40-1С. Установлена релейная коробка рядом с баллонами ППО.
Система защиты от ОМП
Узлы герметизации машины служат для предотвращения попадания внутрь обитаемых отделений зараженного воздуха и обеспечивают защиту от действия ударной волны. Герметизация достигается за счет уплотнений лючков, люков и дверей корпуса, люков башни, уплотнений шариковых опор башни, люка командира, пусковой установки.
Люки и двери необходимо закрывать заблаговременно, а клапаны вытяжных вентиляторов, жалюзи и заслонки эжектора закрываются при срабатывании системы защиты. Крышка воздухозаборной трубы закрывается под действием ударной волны. Кроме того, проникновению зараженного воздуха в различные неплотности (при установке оружия в амбразуры и т. п.) препятствует избыточное давление воздуха внутри машины, создаваемое нагнетателем.
Фильтровентиляционная установка (ФВУ) служит для подачи воздуха внутрь машины, для создания избыточного давления, а также для очистки воздуха от пыли, радиоактивных, отравляющих веществ и бактериальных средств.
ФВУ состоит из нагнетателя, клапанной коробки, фильтра-поглотителя и магистрали раздачи чистого воздуха.
Нагнетатель и фильтр-поглотитель, соединенные между собой клапанной коробкой, располагаются в изолированном отсеке на левом борту машины.
Нагнетатель служит для подачи воздуха экипажу, для очистки его от пыли и создания в машине избыточного давления.
Клапанная коробка служит для управления потоком воздуха, выходящего из нагнетателя. Клапан в клапанной коробке может находиться в двух положениях.
В зависимости от положения клапана поток воздуха, поступающий в машину из нагнетателя, может быть направлен в раздаточную магистраль либо непосредственно через полую опору фильтра (входное окно фильтра-поглотителя закрыто клапаном, при этом рычаг клапана застопорен стопором), либо через фильтр-поглотитель, а затем через полую опору (входное окно фильтра-поглотителя открыто, а окно в полой опоре фильтра закрыто тарелкой клапана).
Фильтр-поглотитель ФПТ-200М служит для очистки воздуха от отравляющих веществ, бактериальных и радиоактивных аэрозолей. Он устанавливается на полой опоре, являющейся частью воздушной трассы ФВУ.
Раздаточная магистраль служит для подвода очищенного воздуха к местам размещения экипажа.
Раздаточная магистраль представляет собой систему трубопроводов с наконечниками. В десантном отделении раздаточная магистраль выполнена в виде поручней. Наконечники раздаточной магистрали позволяют изменять направление струи выходящего воздуха и при стрельбе должны быть установлены так, чтобы чистый воздух подавался в зону дыхания.
Фильтровентиляционная установка в зависимости от положения клапана ФПТ обеспечивает два режима работы: подача воздуха в раздаточную магистраль через фильтр ФПТ (клапан ФПТ открыт) и минуя фильтр (клапан ФПТ закрыт).
Система вытяжной вентиляции служит для удаления пороховых газов из машины. Она включает в себя три вентилятора, один из которых находится в башне, а два других – в десантном отделении в нишах правого и левого бортов; воздушные магистрали, клапанные коробки, электромагниты и конечные выключатели исполнительных механизмов закрывания клапанов вытяжных вентиляторов.
На машине установлены два отопителя: в трассе ФВУ и в десантном отделении. Отопитель в трассе ФВУ служит для подогрева нагнетаемого воздуха. Он крепится в специальном кожухе с помощью лент, затягиваемых болтами, и представляет собой трубчато-пластинчатый радиатор, в который подается горячая жидкость из системы охлаждения двигателя. Холодный воздух, проходя между горячими трубками и пластинами радиатора, нагревается и поступает внутрь машины. Отопитель в десантном отделении служит для подогрева воздуха в десантном отделении и обогрева аккумуляторных батарей. Он установлен на верхней полке аккумуляторного отсека и крепится болтами. Отопитель десантного отделения по устройству аналогичен отопителю в трассе ФВУ, но имеет вентилятор, который создает поток воздуха, просасываемый через радиатор.
Прибор ПРХР обеспечивает:
- при наличии мощного потока гамма-излучения при ядерном взрыве выдачу команды на исполнительные механизмы средств защиты со световой и звуковой сигнализацией (команда «А»);
- при воздействии гамма-излучения радиоактивно зараженной местности выдачу команды на исполнительные механизмы со световой и звуковой сигнализацией (команда «Р»);
- измерение уровня радиации внутри машины;
- при появлении в воздухе вне машины паров отравляющих веществ (0В) выдачу команды на исполнительные механизмы со световой и звуковой сигнализацией (команда «О»).
Комплект ПРХР состоит из следующих приборов и узлов:
- измерительного пульта (блок Б-1);
- датчика (блок Б-2);
- блока питания (блок Б-3);
- воздухозаборного устройства (ВЗУ) с циклоном (Ц);
- двух трубок (рис. 10.18).
Рис. 10.18. Комплект прибора радиационной защиты и химической разведки (ПРХР):
1 – измерительный пульт Б-1; 2 – датчик Б-2; 3 – блок питания Б-3; 4 – воздухозаборное
устройство с циклоном; 5 – трубки обогрева; 6 – резиновая трубка
Все блоки соединены между собой кабельными узлами, датчик (Б-2) и циклон (Ц) – трубками.
Измерительный пульт (блок Б-1) служит для измерения дозы радиации, для световой и звуковой сигнализации при наличии радиации и отравляющих веществ, для выдачи команд исполнительным механизмам системы защиты, установлен в нише левого борта.
Датчик (блок Б-2) служит для анализа поступающего снаружи воздуха.
Корпус блока Б-2 имеет сквозной канал для поступления анализируемого воздуха, который, поступая в блок Б-2 через входной штуцер, проходит через кран блока Б-2. Кран обеспечивает поступление воздуха либо через входной штуцер (при вертикальном положении РАБОТА ручки), либо через патрон с силикагелем (при горизонтальном положении УСТ. НУЛЯ ручки и вывинченной из патрона заглушке).
Блок Б-2 имеет входной ротаметр, по которому регулируется необходимый расход воздуха (2–3,2 л/мин) регулятором расхода воздуха. Поплавок ротаметра должен находиться между рисками.
Под регулятором расхода воздуха на крышке фильтра имеется стрелка, обозначенная буквами М (меньше) и Б (больше). При повороте регулятора в направлении стрелки, обозначенной буквой Б, расход воздуха, прокачиваемого через блок Б-2, увеличивается (поплавок ротаметра поднимается), а при повороте регулятора в направлении стрелки, обозначенной буквой М, расход воздуха уменьшается (поплавок ротаметра опускается).
Блок питания (блок Б-3) представляет собой преобразователь напряжения бортовой сети в напряжение, необходимое для питания схем прибора.
Воздух на анализ в блок Б-2 поступает через трубку обогрева, соединяющую блок Б-2 с циклоном, установленным слева сзади люка десантника в отверстии крыши машины.
Циклон с трубками предназначен для забора воздуха из атмосферы, очистки его от пыли, подогрева, подачи в блок Б-2 и выброса в окружающую атмосферу.
Для защиты циклона и блока Б-2 от попадания в них воды при движении машины на воде предусмотрен дополнительный лабиринт, обеспечивающий слив попавшей под крышку циклона воды.
Корпус циклона выполнен в виде цилиндра с наружной резьбой для установки на машине, в верхней части циклона имеются входное и выходное отверстия для забора и выброса анализируемого воздуха после его прохождения через блок Б-2. В нижней части циклона расположены штуцера, на которые надеваются, соответственно, трубка обогрева и трубка, соединяющая циклон с блоком Б-2. К вилке разъема подсоединяется кабель, соединяющий циклон с блоком питания.
К прибору придается ЗИП, который размещен в ЭК машины.
Принцип действия ПРХР
ПРХР имеет радиационную часть и газоанализатор. Радиационная часть прибора обеспечивает обнаружение потока гамма-излучения, измерение его мощности, выработку команд на исполнительные механизмы системы защиты и сигнализацию.
Обнаружение мощного потока гамма-излучения при ядерном взрыве осуществляется детектором – ионизационной камерой, в которой под действием гамма-излучения возникает ионизационный ток. Этот ток усиливается в усилительном устройстве до величины, необходимой для срабатывания соответствующего реле, которое включает цепи выдачи команд «А» на исполнительные механизмы и сигнализацию.
Обнаружение радиации от радиоактивно зараженной местности производится детектором – газоразрядным счетчиком, в котором под действием слабого гамма-излучения возникает ионизационный ток. Этот ток также усиливается, срабатывает соответствующее реле, которое включает цепи выдачи команды Р на исполнительные механизмы и сигнализацию.
Мощность дозы гамма-излучения измеряется рентгенметром, детектором (датчиком) которого служат четыре газоразрядных счетчика. По интенсивности ионизации, т.е. по величине ионизационного тока детекторов, измеряется мощность дозы радиоактивного излучения по шкалам указателя микроамперметра:
по верхней шкале – до 5 Р/ч;
по нижней шкале – до 150 Р/ч.
Газосигнализатор ПРХР обеспечивает обнаружение ОВ (при непрерывной прокачке через него окружающего воздуха) и выдачу команды на исполнительные механизмы и сигнализацию.
Анализируемый воздух проходит через ионизационную камеру, расположенные в датчике ПРХР и ионизируется в них двумя источниками альфа-излучения. Через камеры проходит ионизационный ток, величина которого изменяется с появлением в воздухе ОВ. Это вызывает срабатывание электрического устройства и усиление его сигнала до необходимой величины для работы реле, которое включает цепи выдачи команды «О» на исполнительные механизмы и сигнализацию.
Для стабильной работы газосигнализатора воздух подогревается и подается микронагнетателем. Расход воздуха измеряется входным ротаметром.
Размещение, устройство и работа исполнительных механизмов
Механизм отключения жалюзи заслонок эжектора состоит из электромагнита, корпуса, штока, гильзы с канавкой, наконечника, четырех шариков, удерживаемых в канавке гильзы штокоми блокирующих гильзу с наконечником.
При срабатывании системы защиты включается электромагнит и шток, перемещаясь, освобождает шарики. Шарики выходят из канавки гильзы и нарушают связь между гильзой и наконечником, в результате чего под действием пружинжалюзи и заслонки эжектора закрываются.
Действие механизма отключения восстанавливается рукояткой при выключенном выключателе ПАЗ на центральном щитке.
При срабатывании системы защиты шток электромагнита клапана ФПТ перемещает стопор и освобождает рычагклапана. Под действием пружины рычаг поворачивается, освобождается шток конечного выключателя и одновременно клапан ФПТ переводится в положение, при котором весь поток воздуха направляется через фильтр-поглотитель.
При срабатывании конечного выключателя прекращается подача электрического тока на электромагнит и одновременно загорается сигнальная лампа ОТКР. КЛАПАН ФПТ на центральном щитке.
Схема отключения стабилизатора обеспечивает отключение его при команде А (атомный взрыв), выдаваемой прибором ПРХР или вручную (при этом отключаются электромагниты подъемного и поворотного механизмов). Включается стабилизатор автоматически после прохождения команды А при выключенном выключателе ПАЗ на центральном щитке.
46-47. Эксплуатация в летний и зимний периоды
13. ОСОБЕННОСТИ ЭКСПЛУАТАЦИИ
В ЛЕТНИХ И ЗИМНИХ УСЛОВИЯХ
13.1. Особенности эксплуатации в летних условиях
Летние условия эксплуатации характеризуются устойчивой температурой окружающего воздуха 5 °С и выше.
Высокая температура окружающего воздуха вызывает повышенный нагрев агрегатов машины, испарение воды из электролита аккумуляторных батарей, а также ухудшает условия работы экипажа. При высокой температуре окружающего воздуха и больших нагрузках может перегреваться двигатель.
Во время летней эксплуатации машины в основном работают в условиях большой запыленности воздуха. Воздух с повышенным пылесодержанием, проникающий в узлы и агрегаты машины, повышает износы деталей, увеличивает усилия на педалях, рычагах, ухудшает условия их работы.
Большая запыленность воздуха резко снижает видимость через приборы прицеливания и наблюдения, особенно при движении в колонне.
13.1.1. Подготовка машины к летней эксплуатации
При подготовке машины к эксплуатации в летних условиях провести очередное техническое обслуживание № 1 или 2 в зависимости от пройденного километража и дополнительно:
- закрыть заслонку зимнего забора воздуха из короба эжектора в воздухоочиститель. Для этого открыть крышку 5 (рис. 3.2), повернуть рукоятку, расположенную на стенке воздухоочистителя, до отказа усилием руки в направлении стрелки ЗАКРЫТО и, законтрив рукоятку проволокой, установить крышку;
- заправить систему питания летним дизельным топливом, предварительно (для удаления отстоя) слить 5–6 л топлива из основного бака;
- заправить систему охлаждения водой;
- передвинуть очистители на максимально возможное расстояние от ободьев направляющих колес и закрепить;
- очистить шахты и посадочные места приборов ТНПО-170А от пыли и грязи и протереть чистой ветошью;
- залить воду в бачки воздушно-жидкостной очистки приборов наблюдения;
- проверить плотность электролита в аккумуляторных батареях согласно правилам содержания в эксплуатации стартерных свинцово-кислотных АБ;
- произвести контрольное взвешивание баллонов ППО, для чего снять их. Вес состава в каждом из баллонов должен соответствовать записи в формуляре (0,60–0,65 кгс). При необходимости отправить баллоны на заправку или заменить. Ввиду токсичности огнегасящего состава соблюдать правила техники безопасности;
- замерить величину напряжения, поддерживаемого регулятором, по показаниям вольтамперметра. Замеренная величина напряжения должна быть во всем диапазоне эксплуатационной частоты вращения в пределах 26,5–28,5 В;
- проверить у регулятора напряжения затяжку гайки разъема, болтов крепления крышек предохранителей и блока измерительного регулятора.
13.1.2. Правила эксплуатации машин в летних условиях
Для обеспечения надежной и безотказной работы машины в летних условиях необходимо:
- во время движения машины внимательно следить за показаниями контрольно-измерительных приборов;
- систематически проверять полноту заправки систем охлаждения и смазки и уровень электролита в аккумуляторных батареях;
- систему охлаждения двигателя заправлять чистой пресной (мягкой) водой с добавлением трехкомпонентной присадки, заменять воду в системе охлаждения только в случае крайней необходимости;
- обеспечивать нормальный тепловой режим работы двигателя регулированием нагрузки и частоты вращения коленчатого вала двигателя и потока охлаждающего воздуха;
- принимать меры по предупреждению попадания воды внутрь корпуса машины, в двигатель и другие агрегаты при преодолении водных препятствий;
- проверять нагрев бортовых передач и узлов ходовой части на ощупь, в случае перегрева установить причину и устранить ее;
- предохранять при хранении машин бандажи катков от воздействия солнечных лучей;
- установить очистители так, чтобы расстояние между ободом направляющего колеса и очистителем было от 3 до 5 мм;
- слить воду из бачков воздушно-жидкостной очистки приборов;
- проверить плотность электролита в аккумуляторных батареях согласно ПУС;
- замерить величину напряжения, поддерживаемого регулятором, по показанию вольтамперметра. Замеренная величина напряжения во всем диапазоне эксплуатационной частоты вращения коленчатого вала двигателя должна быть 26,5–28,5 В. Проверить у регулятора напряжения затяжку гайки разъема, болтов крепления, крышек предохранителей и блока измерительного регулятора.
13.2. Особенности эксплуатации в зимних условиях
13.2.1. Правила эксплуатации машины в зимних условиях
Для обеспечения надежной и безотказной работы машины в зимних условиях, особенно при низких температурах окружающего воздуха:
- пускать двигатель только после его разогрева подогревателем;
- пускать холодный или недостаточно разогретый двигатель (даже с буксира) при температуре окружающего воздуха ниже 5 °С запрещается;
- во время движения машины внимательно следить за показаниями КИП и поддерживать их показания в рекомендуемых пределах.
Для предотвращения запотевания и обледенения стекол и окуляра прибора 9Ш119М1 протереть их кисточкой, смоченной спирто-глицериновой смесью (стакан со спирто-глицериновой смесью и кисточку взять из ЗИП).
13.2.2. Заправка и слив охлаждающей жидкости
из системы охлаждения в зимних условиях
Зимой система охлаждения заправляется низкозамерзающей жидкостью. В исключительных случаях, при температуре окружающего воздуха от 5 °С до минус 30 °С, допускается заправка системы охлаждения водой, предварительно нагретой не ниже 80 °С. В этом случае непосредственно перед пуском двигателя систему охлаждения необходимо разогреть путем проливания через нее горячей воды с температурой 80–90 °С, при этом рукоятка крана слива воды и клапан должны быть открыты до тех пор, пока из клапана не будет вытекать горячая вода.
Закрыть сливной кран и клапан, заправить систему горячей водой. При проливе и заправке системы горячей водой и разогреве подогревателем кран отопителей должен быть закрыт.
После пуска двигателя необходимо открыть кран отопителей и дозаправить систему охлаждения.
После заправки системы горячей водой перед пуском двигателя необходимо убедиться, что температура воды в системе и давление масла, создаваемое МЗН, соответствует норме. Если температура воды и давление масла не соответствуют норме, необходимо разогреть двигатель подогревателем. При этом до включения подогревателя на обогрев поработать им без включения свечи и подачи топлива 1–2 мин (для прокачки жидкости в системе).
При длительных остановках двигателя воду из системы и поддона КП необходимо слить, прежде чем ее температура снизится до 50 °С.
После слива воды заправить в систему охлаждения 8–10 л низкозамерзающей жидкости (при закрытом сливном кране) и несколько раз провернуть коленчатый вал двигателя без подачи топлива, после чего низкозамерзающую жидкость слить, оставив сливной кран, клапан и кран отопителей открытыми.
Если машина эксплуатировалась на воде и заправляется сразу после ее слива низкозамерзающей жидкостью (машина не остывшая), необходимо после заправки системы пустить двигатель, открыть кран отопителей и дозаправить систему охлаждения.
Если в зимнее время система охлаждения по какой-либо причине заправляется низкозамерзающей жидкостью не сразу после слива воды (машина остывшая) и нет полной уверенности в том, что система проливалась низкозамерзающей жидкостью сразу после слива воды, заправку производить в следующем порядке:
- пролить и заправить систему водой, как указано выше;
- пустить двигатель и поработать 4–5 мин при частоте вращения коленчатого вала двигателя 1000–1200 об/мин;
- слить воду и заправить систему низкозамерзающей жидкостью;
- пустить двигатель, дозаправить систему полностью.
Если система после слива воды проливалась низкозамерзающей жидкостью, то последующая заправка низкозамерзающей жидкостью может производиться без пролива горячей воды.
13.2.3. Правила и порядок использования подогревателя
Разогреть двигатель системой подогрева в следующем порядке:
- открыть крышку 16 (рис. 3.2), отвернув (в правую сторону) гайку, повернув рукоятку 8 по ходу часовой стрелки до фиксации;
- прокачать топливную систему посредством кратковременного
(10–15 с) включения БЦН;
- закрыть воздушную заслонку подогревателя, установив рукоятку 8 в положение 3, если температура окружающего воздуха ниже минус 20 °С;
- включить выключатель СВЕЧА на центральном щитке;
- через 1–1,5 мин после включения свечи до отказа открыть кран питания топливом подогревателя и спустя полминуты включить выключатель ОБОГРЕВ ДВИГАТ.;
- при воспламенении топлива в котле подогревателя выключить выключатель СВЕЧА, открыть заслонку, для чего рукоятку 8 перевести в положение «О»;
- если воспламенения топлива в котле подогревателя не произошло, выключить выключатель ОБОГРЕВ ДВИГАТ. и через полминуты снова включить его. Выключатель СВЕЧА может быть непрерывно включен не более 3 мин.
Если воспламенения топлива в котле подогревателя не произошло, выключить выключатель СВЕЧА, закрыть кран питания топливом подогревателя и выключить выключатель ОБОГРЕВ ДВИГАТ., после чего повторить розжиг.
В исключительном случае при выходе свечи из строя и отсутствии запасной свечи розжиг котла подогревателя производить с помощью факела с использованием вышедшей из строя свечи.
Разогреть охлаждающую жидкость до необходимой температуры. При этом давление масла, создаваемое маслозакачивающим насосом, должно быть не менее 0,25 МПа (2,5 кгс/см2).
Если охлаждающая жидкость достигла температуры, при которой допускается пуск двигателя, а маслозакачивающий насос создает давление менее
0,25 МПа (2,5 кгс/см2), необходимо продолжить разогрев, периодически включая маслозакачивающий насос. При создании маслозакачивающим насосом давления не менее 0,25 МПа (2,5 кгс/см2) разрешается пускать двигатель.
Для прекращения работы подогревателя необходимо:
- закрыть до отказа топливный кран подогревателя;
- приблизительно через 15 с после прекращения горения топлива в котле подогревателя выключить выключатель ОБОГРЕВ ДВИГАТ.;
- закрыть лючок подогревателя, повернув рукоятку 8 (рис. 3.2) против хода часовой стрелки, и затянуть гайку.
Помнить, что при уровне масла в масляном баке менее 30 л пускать двигатель разрешается через 4–5 мин после выключения подогревателя или при открытой заправочной горловине масляного бака.
После разогрева пустить двигатель сжатым воздухом, стартером или комбинированным способом, прогреть двигатель и систему управления силовой передачей.
Для ускорения подготовки машины к движению рекомендуется после разогрева двигателя подогревателем и создания давления в системе смазки с помощью МЗН пустить двигатель и, не выключая подогреватель, прогреть двигатель.
13.2.4. Правила и порядок поддержания машины
в подогретом состоянии в полевых условиях
Для поддержания двигателя в состоянии готовности к пуску при остановках машины в зимнее время необходимо:
- выбрать площадку для стоянки машины, по возможности защищенную от ветра;
- закрыть люки и кормовые двери, а также заслонки эжектора и жалюзи;
- накрыть жалюзи над радиаторами и заслонки эжектора утеплительными ковриками;
- укрыть машину укрывочным чехлом;
- не допускать понижения температуры охлаждающей жидкости ниже 35–40 °С. При понижении температуры пустить подогреватель и нагреть охлаждающую жидкость до 80–90 °С;
- не допускать разрядки аккумуляторных батарей более чем на 25 %;
- если система охлаждения заправлена водой, то при снижении температуры воды до 60 °С пустить подогреватель и довести температуру воды до
90 °С, после чего подогреватель выключить.
13.2.5. Порядок пользования отопителями
Включать отопители для подогрева воздуха внутри машины при работающем двигателе при температуре охлаждающей жидкости не ниже 80 °С следующим образом:
- включить нагнетатель ФВУ (если он не был включен), установив выключатель НАГНЕТАТЕЛЬ на центральном щитке в положение ВКЛ., при этом фильтр ФПТ-200М должен быть закрыт;
- установить ручку крана, расположенного за отсеком ФВУ, в положение «О»;
- установить выключатель вентилятора отопителя десантного отделения, расположенный на задней стенке контейнера аккумуляторных батарей, в положение ВКЛ.
Для выключения отопителей:
- установить выключатель НАГНЕТАТЕЛЬ в положение «ВЫКЛ.»;
- установить выключатель вентилятора отопителя десантного отделения в положение «ВЫКЛ.»;
- установить ручку крана, расположенного за отсеком ФВУ, в положение «З».
13.2.6. Правила и порядок обогрева стекол приборов наблюдения
Для предотвращения запотевания и обледенения внутренних и наружных стекол приборов ТНПО-170А и ТВНЕ-1ПА, стекол амбразур, прибора ТНПТ-1, защитных стекол приборов БПК-1-42, ТКН-3Б, призмы прибора 1ПЗ-3 и окуляров прибора ТКН-3Б включить обогрев.
Во избежание разряда аккумуляторных батарей при неработающем двигателе обогрев приборов включать только в случае крайней необходимости на непродолжительное время.
Продолжительность обогрева защитных стекол БПК-1-42, ТКН-3Б приборов ТНПТ-1 и стекол амбразур при температуре воздуха минус 5 °С и ниже не ограничивается, при температуре от минус 5 до 20 °С не более 10 мин; при температуре выше 20 °С включать обогрев перечисленных приборов запрещается. Обогрев прибора 1ПЗ-3 включать только при температуре ниже 5 °С.
При температуре окружающего воздуха минус 10 °С и ниже рекомендуется включать обогрев только для выходных стекол ТНПО-170А.
Обогрев приборов ТНПО-170А механика-водителя включать на коробке КР-55, расположенной в нише слева от сиденья водителя.
Обогрев приборов ТНПО-170А и стекол амбразур десантного отделения включать на коробке КР-60, расположенной на левом борту десантного отделения.
Обогрев приборов ТНПО-170А башни, ТНПТ-1 оператора и защитного стекла прибора БПК-1-42 включать на коробке КР-60, расположенной в нише слева от сиденья оператора.
При этом для обогрева входных и выходных стекол ТНПО-170А переключатель ОБОГРЕВ ТНПО установить в положение ОБА, для обогрева выходных стекол – в положение «ВЫХОДНОЕ».
Для обогрева ТНПТ-1 оператора и защитного стекла прибора БПК-1-42 выключатель ОБОГРЕВ СТЕКЛА на КР-60 перевести в положение «ВКЛ.».
При установке прибора ТВНЕ-1ПА вместо центрального прибора механика-водителя для обогрева окуляров выключатель ВЫХОДНОЕ – ОБА перевести в положение «ВЫХОДНОЕ», а для обогрева окуляров и верхней призмы – в положение «ОБА».
Обогрев призмы и окуляра прибора 1ПЗ-3 включать выключателем ОБОГРЕВ, расположенным на этом приборе.
Обогрев защитного стекла прибора ТКН-3Б и прибора ТНПТ-1 командира включать выключателем, расположенным на нижней части прибора ТКН-3Б.
Включение обогрева окуляров прибора БПК-1-42 обеспечивается автоматически схемой прибора.
При работе зимой окуляры прибора ТКН-3Б обогреваются с помощью съемных обогревателей, электропитание которых подключается от розетки обогрева, установленной над левым окуляром прибора ТКН-3Б.
13.2.7. Розжиг котла подогревателя с помощью факела
Инструмент и принадлежности: ключ 32х36, ветошь, дизельное топливо, огнетушитель, брезентовые рукавицы.
Для розжига котла подогревателя проделать следующие операции:
– выключить выключатель батареи;
– отсоединить провод подвода питания к свече накаливания;
– вывернуть неисправную свечу;
– на всю длину спирали свечи намотать тонким слоем ветошь, с тем чтобы при вводе свечи в отверстие горелки не сбить пламя факела;
– включить выключатель батарей;
– прокачать топливную систему включением БЦН на 5–10 с;
– открыть топливный кран котла подогревателя;
– закрыть воздушную заслонку подогревателя;
– смочить ветошь дизельным топливом и поджечь факел; включить и через 5–6 с выключить выключатель ОБОГРЕВ ДВИГАТ.;
– вставить зажженный факел в отверстие горелки, не доводя резьбовую часть свечи накаливания на 5–10 мм до отверстия;
– через 3–5 с после вспышки топлива внутри горелки котла подогревателя свечу быстро ввернуть и одновременно включить выключатель ОБОГРЕВ ДВИГАТ.;
– при прослушивании характерного звука горения топлива в котле подогревателя открыть воздушную заслонку.
Меры предосторожности:
- розжиг котла подогревателя с помощью факела с использованием неисправной свечи можно производить только при слаженных отработанных действиях одновременно двух членов экипажа;
- все работы с зажженным факелом необходимо производить в брезентовых рукавицах;
- в районе горелки не должно быть никаких легковоспламеняющихся предметов;
- ручной огнетушитель должен быть готов к действию;
- если с первого раза разжечь котел подогревателя не удалось, необходимо закрыть топливный кран подогревателя и продуть полость горелки, включив на 10–15 с выключатель ОБОГРЕВ ДВИГАТ. для удаления паров топлива, и затем вновь повторить розжиг.
13.2.8. Порядок холодного пуска двигателя
Холодный пуск двигателя осуществляется по указанию командира, если температура машины и окружающего воздуха не ниже минус 20 °С, а система смазки двигателя заправлена маслом МТЗ-10п, трансмиссия ТСЗп-8 и давление воздуха в баллоне не менее 9,8 МПа (100 кгс/см2).
При температуре машины и окружающего воздуха ниже минус 20 °С и заправленной системе смазки двигателя маслом МТ-16п пуск двигателя осуществлять только после предварительного разогрева силовой установки подогревателем.
Холодный пуск двигателя осуществляется в такой последовательности:
- убедиться, что рычаг переключения передач находится в нейтральном положении, рукоятка ручного привода подачи топлива – в положении выключенной подачи, а рычаг включения замедленной передачи – в верхнем положении;
- закрыть жалюзи и накрыть их утеплительными ковриками;
- включить выключатель батарей;
- перевести рукоятку топливного крана в положение О (открыто);
- нажать кнопку ПУСК на щитке управления БФП и удерживать ее до загорания ламп СВЕЧИ 1, 2, 3, 4;
- открыть вентиль воздушного баллона;
- включить МЗН, нажав кнопку НАСОС, и создать давление в системе смазки двигателя не менее 0,25 МПа (2,5 кгс/см2);
- включить выключатель БЦН, прокачать топливную систему в течение 10–15 с и выключить БЦН;
- после загорания лампы ЭК (примерно через 90 с после нажатия кнопки ПУСК) вторично создать давление масла в системе смазки двигателя, нажав кнопку НАСОС;
- нажать кнопку СТАРТЕР и затем кнопку ПУСК ВОЗД. (комбинированный способ).
При температуре машины и окружающего воздуха до минус 10 °С пуск двигателя допускается осуществлять стартером без использования воздухопуска, для этого через 3–4 с после начала прокручивания коленчатого вала двигателя резко и полностью выжать педаль подачи топлива, а после пуска двигателя отпустить кнопки СТАРТЕР и ПУСК ВОЗД.
Кнопки СТАРТЕР и ПУСК ВОЗД. держать включенными до пуска двигателя, но не более 7 с.
Работа двигателя в течение 180 с сопровождается работой БФП. По истечении этого времени гаснут лампы ЭК и СВЕЧИ 1, 2, 3, 4.
После пуска двигателя прогреть его на режиме холостого хода с частотой вращения коленчатого вала 1000–1100 об/мин.
После достижения маслом температуры не ниже 0 °С, если двигатель работает устойчиво, без хлопков и стука, допускается начинать движение машины на низших передачах при частоте вращения коленчатого вала двигателя не более 1600 об/мин.
Дата добавления: 2020-04-25; просмотров: 106; Мы поможем в написании вашей работы! |
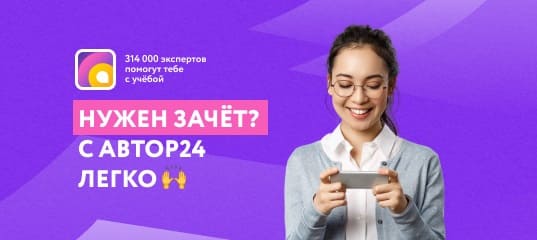
Мы поможем в написании ваших работ!