Вопросы домашней контрольной работы
1. Изобразить схему устройства кислородного конвектора и объяснить принцип его работы. Описать сущность и ход процесса производства стали в кислородном конвекторе, указать шихтовые материалы и выплавляемые стали
2. Используя технические возможности и сравнительные показатели выбрать наиболее оптимальный способ литья, если:
масса отливки 1000 кг;
серийность 900 шт.;
минимальная толщина стенки отливки 4 мм;
Обосновать свой выбор. Описать выбранный способ литья. Составить схему технологического процесса.
3. Выбрать оборудование и описать технологический процесс получения шариков из стали ШХ15. Привести схему процесса.
4. Описать технологию пайки медных трубок в условиях серийного производства. Привести схему процесса, марки флюса и припоя, режим пайки. Составить схему технологического процесса пайки. Указать метод контроля качества паяных швов.
5. Выбрать тип оборудования и изложить физическую сущность для получения отверстия квадратного сечения в технической керамике. Привести схему процесса обработки и описать ее.
6. Привести схему устройства дуговой электросталеплавильной печи, описать процесс плавки стали на углеродистой шихте и отметить основные преимущества электрических печей перед другими плавильными агрегатами.
7. Используя технические возможности и сравнительные показатели выбрать наиболее оптимальный способ литья, если:
|
|
масса отливки 2000 кг;
серийность 600 шт.;
минимальная толщина стенки отливки 2,5 мм;
Обосновать свой выбор. Описать выбранный способ литья. Составить схему технологического процесса.
1. Выбрать оборудование и описать технологию получения поковки вала из стали 50ХН массой 25 т. Поковка изготавливается из слитка. При описании технологии получения поковки перечислить применяемые операции и используемый инструмент
2. Описать технологию сварки трамвайных рельсов встык. Привести схему процесса и режим сварки. Выбрать метод контроля качества сварного соединения
3. Выбрать тип оборудования, инструмент и приспособления для отделочной обработки поверхности вала из стали 45. Привести схему процесса обработки и описать ее.
4. Выбрать оборудование и описать технологию получения алюминия. Привести способы рафинирования алюминия. Указать марки выплавляемого алюминия, их свойства и области применения.
12. Используя технические возможности и сравнительные показатели выбрать наиболее оптимальный способ литья, если:
масса отливки 100 кг;
серийность 200 шт.;
минимальная толщина стенки отливки 3 мм
Обосновать свой выбор. Описать выбранный способ литья. Составить схему технологического процесса.
|
|
13. Выбрать тип оборудования и описать технологический процесс прессования труб из латуни Л68. Какие при этом применяют инструменты и смазка? Привести схему процесса.
14. Описать технологию контактной стыковой сварки двух прутков из стали 30ХГСА. Привести схему процесса и режимы сварки. Выбрать метод контроля качества сварного шва.
15. Выбрать тип оборудования, инструмент и приспособления для получения шестерни с прямыми зубьями при начальном диаметре заготовки 280 мм. Привести схему процесса обработки и описать ее.
16. Выбрать оборудование и кратко описать технологию получения магния. Области применения магния.
17. Используя технические возможности и сравнительные показатели выбрать наиболее оптимальный способ литья, если:
масса отливки 100 кг;
серийность 1000 шт.;
минимальная толщина стенки отливки 0,5 мм;
Обосновать свой выбор. Описать выбранный способ литья. Составить схему технологического процесса.
18. Выбрать оборудование и описать технологию получения квадратной сортовой стали 30х30 мм из стали 30ХГСН2А. Привести схему процесса.
19. Описать технологию сварки кислородно-ацетиленовым пламенем трубопровода из стали марки 10. Привести схему процесса и режимы сварки. Методы контроля сварного шва.
|
|
20. Выбрать тип оборудования и изложите физическую сущность процесса прошивки отверстий в закаленной стали (HRC62). Привести схему процесса обработки и описать ее.
21. Дать схему устройства мартеновской печи и изложить принцип ее работы. Описать сущность производства стали основным скрап-рудным процессом.
22. Используя технические возможности и сравнительные показатели выбрать наиболее оптимальный способ литья, если:
масса отливки 1 кг;
серийность 1000 шт.;
минимальная толщина стенки отливки 0,5 мм;
Обосновать свой выбор. Описать выбранный способ литья. Составить схему технологического процесса.
23. Выбрать оборудование и описать технологию получения поковки шестерни из стали марки 45 при серийном производстве. Привести схему процесса.
24. Описать технологию сварки емкости из стали марки 08Х18 толщиной 10 мм. Привести схему процесса и режимы сварки. Выбрать метод контроля качества сварного соединения.
25. Выбрать тип оборудования, инструмент и приспособления для получения глухого отверстия диаметром 15 мм в корпусной детали из серого чугуна. Привести схему процесса обработки и описать ее.
26. Описать способ разливки стали в изложницы. Привести схему установки непрерывной разливки стали и описать процесс. Указать основные преимущества способа непрерывной разливки стали.
|
|
27. Используя технические возможности и сравнительные показатели выбрать наиболее оптимальный способ литья, если:
масса отливки 100000 кг;
серийность 10 шт.;
минимальная толщина стенки отливки 4 мм;
Обосновать свой выбор. Описать выбранный способ литья. Составить схему технологического процесса.
28. Выбрать оборудование и описать технологию получения арматуры из стали марки 10Г2 при серийном производстве. Привести схему процесса.
29. Описать технологию сварки листовой стали марки 12Х18Н10Т толщиной 20 мм при единичном производстве. Привести схему процесса и режимы сварки. Методы контроля сварного шва.
30. Выбрать тип оборудования, инструмент и приспособления для обработки Т-образных пазов стола вертикально - сверлильного станка, изготовленного из серого чугуна. Привести схему процесса обработки и описать ее.
31. Выбрать оборудование и описать технологию плавки губчатого титана для получения титановых слитков. Области применения титана.
32. Используя технические возможности и сравнительные показатели выбрать наиболее оптимальный способ литья, если:
масса отливки 50000 кг;
серийность 100 шт.;
минимальная толщина стенки отливки 10 мм;
Обосновать свой выбор. Описать выбранный способ литья. Составить схему технологического процесса.
33. Выбрать тип оборудования и опишите технологию получения колпачка из тонколистовой стали 08кп. Указать применяемые операции и используемый инструмент, привести их эскизы.
34. Описать технологический процесс контактной роликовой сварки листов размером 1500х1000х1 мм. Как осуществляется подготовка поверхности к сварке? Привести схему процесса и режимы сварки. Методы контроля сварного шва.
35. Выбрать тип оборудования, инструмент и приспособления для обработки направляющих станины токарного станка изготовленного из серого чугуна. Привести схему процесса обработки и описать ее.
36. Выбрать оборудование и кратко описать технологию выплавки меди. Рассмотреть способы рафинирования меди. Указать марки выплавляемой меди, их свойства и области применения
37. Используя технические возможности и сравнительные показатели выбрать наиболее оптимальный способ литья, если:
масса отливки 100 кг;
серийность 1000 шт.;
минимальная толщина стенки отливки 0,6 мм;
Обосновать свой выбор. Описать выбранный способ литья. Составить схему технологического процесса.
38. Выбрать оборудование и опишите технологический процесс получения металлических листов толщиной 2 мм из стали 08кп в рулонах от слитка до готовой продукции.
39. Описать технологию дуговой сварки под слоем флюса труб большого диаметра из стали 18ХГТ в условиях серийного производства. Привести схему процесса, состав флюсов, способ регулирования подачи электродной проволоки. Выбрать метод контроля качества сварного шва.
40. Выбрать тип оборудования, инструмент и приспособления для черной обработки торцевой части втулки диаметром 120 мм из стали марки 45. Привести схему процесса обработки и описать ее.
41. Дать определение спокойной и кипящей стали и описать процесс кристаллизации слитков в изложнице. Привести схемы строения слитков спокойной и кипящей стали и указать зоны, характеризующие кристаллическую и химическую неоднородность слитков.
42. Используя технические возможности и сравнительные показатели выбрать наиболее оптимальный способ литья, если:
масса отливки 10 кг;
серийность 1000 шт.;
минимальная толщина стенки отливки 0,5 мм;
Обосновать свой выбор. Описать выбранный способ литья. Составить схему технологического процесса.
43. Выбрать оборудование, инструмент и опишите технологию получения тонкостенных труб из латуни марки Л62. Привести схему процесса.
44. Описать технологию сварки емкостей из титанового листа толщиной 1,5 мм в условиях серийного производства. Привести схему процесса, режимы сварки. Выбрать метод контроля качества сварного шва.
45. Выбрать тип оборудования, инструмент и приспособления для получения отверстий диаметром 10мм во втулке из стали 50. Привести схему процесса обработки и описать ее.
46. Дать краткую характеристику материалам, применяемым в доменном производстве, и указать методы подготовки железных руд к плавке. Описать физико-химическую сущность процесса получения чугуна в доменной печи. Перечислить продукты доменной плавки.
47. Используя технические возможности и сравнительные показатели выбрать наиболее оптимальный способ литья, если:
масса отливки 15000 кг;
серийность 2000 шт.;
минимальная толщина стенки отливки 4 мм;
Обосновать свой выбор. Описать выбранный способ литья. Составить схему технологического процесса.
48. Выбрать тип оборудования и описать технологический процесс получения болтов М12 с шестигранной головкой при серийном производстве. Привести схему и описать принцип работы выбранного оборудования.
49. Описать технологию точечной контактной сварки кузова легкового автомобиля из стали марки 08кп. Порядок подготовки поверхности к сварке. Приведите схему процесса и режимы сварки. Методы контроля сварного шва.
50. Выбрать тип оборудования, инструмент и приспособления для получения шпоночных канавок шириной 20 мм и глубиной 12 мм в вале диаметром 200 мм. Привести схему процесса обработки и описать ее.
Приложение
Технические возможности и сравнительные показатели различных видов литья
Терминологический словарь
АБРАЗИВНАЯ ОБРАБОТКА, механическая обработка материалов при помощи абразивного инструмента и абразивных материалов. К абразивной обработке относятся: шлифование, хонингование, притирка, полирование, суперфиниш, затачивание и др.
АГЛОМЕРАЦИЯ, в металлургии — термический способ окускования мелких рудных материалов (спеканием) для улучшения их металлургических свойств.
АГРЕГАТНЫЙ СТАНОК, металлорежущий станок, собранный в основном из нормализованных (унифицированных), кинематически не связанных между собой агрегатов (т. н. силовых головок с индивидуальными приводами).
АНОДНО-МЕХАНИЧЕСКАЯ ОБРАБОТКА металлов, основанная на одновременном использовании анодного растворения и механического удаления продуктов распада. Применяется для резки, заточки резцов, шлифования и др.
БЕССЕМЕРОВСКИЙ ПРОЦЕСС, передел жидкого чугуна (с незначительным содержанием P и S) в сталь без подвода теплоты — продувкой воздухом (иногда обогащенным кислородом) в конвертере. Во 2-й пол. 20 в. вытеснен кислородно-конвертерным процессом.
БЛЮМ (англ. bloom) (блюмс, блум), полупродукт металлургического производства — стальная заготовка квадратного сечения со стороной св. 140 мм, получаемая из слитков прокаткой на блюминге или из жидкого металла на машинах непрерывного литья.
БЛЮМИНГ (англ. blooming) (блуминг), прокатный стан для обжатия стальных слитков в блюмы. Иногда используются для прокатки слябов и фасонных заготовок. Характеризуется диаметром прокатных валков в мм, который обычно проставляется рядом со словом блюминг (напр., Б. 1500).
БЛЮМИНГ-СЛЯБИНГ, комбинированный прокатный стан для обжатия крупных стальных слитков в слябы или блюмы.
ВАГРАНКА, шахтная печь, главным образом для плавки чугуна в литейных цехах. Иногда для подогрева воздуха вагранки оборудуются рекуператорами.
ВАКУУМНАЯ ПЕЧЬ, служит для нагрева и плавки металла в вакууме. Различают дуговые, индукционные, электронно-лучевые и плазменные вакуумные печи. Позволяет эффективно очистить металл от газов, примесей, неметаллических включений. Применяют для получения металла и сплавов особо ответственного назначения.
ВАЛКИ ПРОКАТНЫЕ, рабочий орган прокатного стана, выполняющий деформацию металла для придания ему требуемых размеров и формы.
ВАЛЬЦЕВАНИЕ (вальцовка), деформирование в ковочных вальцах заготовок из металла, резиновых смесей, пластмасс. С помощью вальцевания получают готовые детали, точные заготовки для штамповки и др.
ВАЛЬЦЫ (от нем. Walze — валок, каток), рабочий инструмент кузнечных, дробильных и др. машин — 2 валка, вращающиеся в противоположных направлениях, что обеспечивает захват и обработку материала, проходящего между ними. Поверхность дробильных вальцов рифленая, в ковочных вальцах имеется ручей, соответствующий конфигурации детали.
ВОЛОКА, рабочий инструмент волочильного стана; через отверстие в волоке (волочильный глазок) протягивается обрабатываемый металл.
ВОЛОЧЕНИЕ, протягивание катаных или прессованных металлических заготовок круглого или фасонного профиля (главным образом прутков, катанки, труб) через отверстие волоки для уменьшения их поперечного сечения или придания им более точных размеров и гладкой поверхности.
ВОЛОЧИЛЬНЫЙ СТАН, машина для обработки металлов волочением. Состоит из волоки и тянущего устройства. Различают станы с прямолинейным движением металла и с намоткой металла (барабанные).
ВЫРУБКА, в металлообработке — операция листовой штамповки — получение плоских деталей путем отделения материала от заготовки по замкнутому контуру в вырубном штампе (напр., круглых заготовок для штамповки кастрюль).
ВЫСАДКА, в металлообработке — кузнечная операция — создание совместных утолщений на прутковых или трубных заготовках путем уменьшения их длины (частичная осадка). Высадкой получают болты, заклепки, фланцы на трубах и т. п.
ВЫСОКОЧАСТОТНАЯ СВАРКА, сварка, при которой кромки свариваемых деталей нагревают токами высокой частоты до их размягчения или оплавления и сжимают. Ток в изделии наводится индукционным или контактным способом. Используют, напр., для сварки труб из ленты.
ВЫТЯЖКА, в металлообработке
1) кузнечная операция - увеличение длины заготовки путем уменьшения площади ее поперечного сечения (вытяжка в гладких бойках называется протяжкой); осуществляется на молотах и прессах последовательным обжатием с поворотом заготовки на 90°.
2) Операция штамповки - свертка листовой заготовки между пуансоном и матрицей в полое изделие.
3) Показатель деформации, равный отношению длин заготовки после и до операции.
ГАЗОВАЯ СВАРКА, способ сварки металлических изделий с помощью газового пламени, образованного при сгорании смеси горючего газа (ацетилена, водорода, паров бензина и др.) с кислородом. Применяют для сварки тонкостенных изделий из стали, цветных металлов и сплавов, для наплавки твердых сплавов при ремонтных работах.
ГАЗОПРЕССОВАЯ СВАРКА, соединение встык стержней, труб, фасонных профилей и т. д. нагревом мест сварки газовым пламенем до оплавления или пластичного состояния металла и последующим сжиманием (осаживанием) соединяемых частей.
ДЕЛИТЕЛЬНАЯ ГОЛОВКА, приспособление металлорежущих станков (преимущественно фрезерных) для поворота обрабатываемых деталей на определенный угол. Различают механическую и оптическую делительную головку.
ДИФФУЗИОННАЯ СВАРКА, производится нагревом (без расплавления материалов) и сдавливанием соединяемых деталей в вакууме, в результате чего происходит диффузия атомов материалов контактирующих деталей. Используют для сварки изделий из трудносвариваемых металлов, неметаллов, пластмасс.
ДОЛБЕЖНЫЙ СТАНОК, металлорежущий станок строгального типа с вертикальным возвратно-поступательным движением резца и прямолинейным (или вращательным) периодическим движением подачи, совершаемым заготовкой. Применяется для обработки труднодоступных поверхностей заготовок, пазов и канавок любой формы.
ДОМЕННАЯ ПЕЧЬ (домна), шахтная печь для выплавки чугуна. Исходные материалы (шихта ) — железорудный агломерат, окатыши, кокс, флюсы — подаются на колошник. Снизу (через фурмы) вводят нагретый воздух, жидкое, газообразное или пылевидное топливо. В доменной печи происходит восстановление железа из оксидов и насыщение его углеродом. Продукты плавки — чугун и шлак — периодически выпускаются через летки (отверстия) в нижней части доменной печи. Полезный объем наиболее крупной в Российской Федерации доменной печи 5580 м3 (1989). Кампания доменной печи (от задувки до капитального ремонта) ок. 10 лет. Первые доменные печи появились в Европе в сер. 14 в., в России — ок. 1630.
ДОМЕННОЕ ПРОИЗВОДСТВО, производство чугуна восстановительной плавкой железной руды или окускованных железорудных материалов в доменных печах. Первое основное звено в общем производственном цикле черной металлургии.
ДУГОВАЯ ПЕЧЬ, электрическая печь для плавки металлов и других материалов, в которой используется тепловой эффект электрической дуги. По способу нагрева подразделяются на печи прямого или косвенного действия и печи с закрытой дугой. Емкость наиболее крупной дуговой печи для выплавки стали 350 т (США). Разновидность дуговых печей — вакуумно-дуговые и плазменно-дуговые печи.
ДУГОВАЯ СВАРКА (электродуговая сварка), вид сварки, при которой кромки свариваемых металлических частей расплавляют дуговым разрядом между электродом и металлом в месте соединения.
ЗАТОЧНЫЙ СТАНОК, станок шлифовальной группы для заточки режущих инструментов в основном абразивными кругами. Применяются также заточные станки для безабразивного затачивания (анодно-механическими, электроискровыми, ультразвуковыми методами обработки).
ЗЕНКОВАНИЕ (от нем. senken — углублять), обработка деталей для получения конических и цилиндрических углублений, опорных плоскостей вокруг отверстий, снятия фасок центровых отверстий. Осуществляется сверлами или зенковками на сверлильных или центровочных станках.
ИНДУКЦИОННАЯ ПЕЧЬ, электрическая печь для плавки металлов, в которой используется индукционный нагрев. Различают тигельные и канальные индукционные печи. Емкость от нескольких кг до сотен т.
ИНДУКЦИОННЫЙ НАГРЕВ, нагрев токопроводящих тел путем возбуждения в них электрических токов переменным электромагнитным полем. Для создания последнего используются токи низкой (50 Гц), средней (до 10 кГц) и высокой (св. 10 кГц) частоты. Применяется для плавления металлов, поверхностной закалки деталей и т. д.
КАРУСЕЛЬНЫЙ СТАНОК, металлорежущий станок токарной группы с вертикальным расположением шпинделя для обработки крупных заготовок.
КАТАНКА, горячекатаная проволока обычно круглого сечения диаметром 5-10 мм. Получают на проволочных или проволочно-сортовых станах. Применяется главным образом для производства тонкой холоднотянутой проволоки.
КИСЛОРОДНО-КОНВЕРТЕРНЫЙ ПРОЦЕСС, передел жидкого чугуна в сталь без подвода теплоты — продувкой металла в конвертере технически чистым кислородом. Под воздействием дутья примеси чугуна (Si, Mn, C и др.) окисляются с выделением значительного количества теплоты. По окончании продувки металл раскисляют (удаляют избыточный кислород). Благодаря высокой производительности кислородно-конвертерного процесса его роль в мировой выплавке стали постоянно растет.
КЛЕТЬ прокатного стана, основная часть стана — 2 литые станины, служащие опорой для подшипников прокатных валков (рабочая клеть) или для шестеренных валков, передающих вращение от электродвигателя к прокатным валкам (шестеренная клеть).
КОКИЛЬ (франц. coquille), металлическая форма для отливки изделий.
КОНТАКТНАЯ СВАРКА, осуществляется нагревом или расплавлением металлов при прохождении электрического тока в месте контакта сдавливаемых изделий. Выполняется сжатием листовых заготовок между стержневыми электродами (точечная контактная сварка) или вращающимися роликами (шовная контактная сварка) либо прижатием торцов изделий (стыковая контактная сварка).
КООРДИНАТНО-РАСТОЧНЫЙ СТАНОК, металлорежущий станок для чистовой обработки деталей сложной формы. Обеспечивает взаимное расположение отверстий, пазов и других поверхностей детали с погрешностью до 2 мкм и 5''. Может использоваться как разметочная или измерительная машина.
КОПИРОВАЛЬНЫЙ СТАНОК, металлорежущий станок для обработки криволинейных поверхностей методом копирования. Различают копировальные станки токарные, фрезерные, шлифовальные и др. Копировальными станками называются также станки для гравирования узоров.
КУЗНЕЧНО-ПРЕССОВОЕ ПРОИЗВОДСТВО, получение металлических изделий ковкой, штамповкой или прессованием.
ЛИГАТУРА, в металлургии — вспомогательные сплавы, применяемые для введения в жидкий металл легирующих элементов (см. Легирование). Лигатурой называют также металлы (Cu, Hg и др.), вводимые в благородные металлы для придания им нужных свойств (напр., твердости) или удешевления изделий.
ЛИТЬЕ, получение отливок путем заливки обычно расплавленных материалов (металлов, горных пород и т. д.) в литейную форму. Применяется более 50 видов литья металлов.
МАРТЕНОВСКАЯ ПЕЧЬ, пламенная регенеративная печь для переработки чугуна и стального лома в сталь. Первая мартеновская печь разработана и построена П. Мартеном во Франции в 1864. В 70-е гг. 20 в. строительство мартеновских печей практически прекращено (разработан более прогрессивный кислородно-конвертерный процесс).
МАТРИЦА, в металлообработке — инструмент со сквозным отверстием (реже углублением), используемый при штамповке, прессовании и волочении для выдавливания, свертки или протягивания заготовки.
МЕТАЛЛООБРАБАТЫВАЮЩИЕ СТАНКИ, служат для обработки заготовок либо со снятием стружки (металлорежущие станки), либо пластическим деформированием (напр., для упрочнения поверхности осей, валов и др. деталей, для формообразования зубьев зубчатых колес, резьбы).
МЕТАЛЛОРЕЖУЩИЙ СТАНОК, служит для обработки заготовок в основном снятием стружки режущим инструментом. Различают металлорежущие станки: по степени специализации - ниверсальные, широкого назначения, специализированные, специальные, агрегатные; по степени автоматизации - с ручным управлением, полуавтоматические, автоматические, в т. ч. с программным управлением; по точности обработки - нормальные, повышенной, высокой, особо высокой и особой (мастер-станки) точности; по технологическому признаку или типу инструмента - токарные, сверлильные и расточные, шлифовальные и т. д.
МЕТОДИЧЕСКАЯ ПЕЧЬ, проходная печь для нагрева металлических заготовок перед прокаткой, ковкой или штамповкой. Заготовки проходят последовательно через зоны: методическую (зону предварительного подогрева), сварочную (зону нагрева) и томильную (зону выравнивания температур в заготовке).
МОЛОТ,
1) машина ударного действия для обработки давлением металлических заготовок. По назначению молоты подразделяют на ковочные и штамповочные, по виду привода — на паровоздушные, пневматические, механические, гидравлические, газовые, взрывные, электромагнитные.
2) Ручной инструмент для ковки металлов (малые молоты называются ручниками, крупные — кувалдами).
НЕПРЕРЫВНОЕ ЛИТЬЕ металлов, получение слитков-заготовок, основанное на непрерывном перемещении металла относительно зон заливки и кристаллизации. Осуществляется на машинах непрерывного литья. Разновидность непрерывного литья — непрерывная разливка стали.
ОБРАБОТКА МЕТАЛЛОВ ДАВЛЕНИЕМ, совокупность технологических процессов, в которых под действием внешних сил осуществляется пластическое формоизменение металлических заготовок без нарушения их сплошности. Основные виды: прокатка, прессование, волочение, ковка, штамповка.
ОПОКА в литейном производстве, приспособление (в виде жесткой рамы или открытого ящика) для удержания формовочной смеси при изготовлении форм, транспортировании их и заливке металлом. Изготовляют литьем, сваркой, штамповкой и другими методами из стали, чугуна, алюминиевых сплавов.
ОПРАВКА, приспособление или вспомогательный инструмент, на котором крепится заготовка или инструмент (имеющие отверстия) для обработки на металлорежущих станках. Бывают цельные и разжимные, центровые и консольные. Некоторые оправки служат для выправления смятых труб.
ОСАДКА, кузнечная операция, при которой уменьшается высота заготовки и увеличивается площадь ее поперечного сечения; обычно предшествует протяжке или прошивке.
ОТЛИВКА, заготовка или деталь, получаемая в литейной форме из расплава металла, горной породы, шлака, стекла, пластмассы и т. д.
ПАЙКА (паяние), процесс получения неразъемного соединения материалов (стали, чугуна, стекла, графита, керамики и др.), находящихся в твердом состоянии, расплавленным припоем с его последующей кристаллизацией. По механизму образования шва различают пайку готовым припоем, контактно-реактивную, реактивно-флюсовую, металлокерамическую, диффузионную и др.; по источнику нагрева — пайку паяльником, инфракрасными лучами, лазером, индукционную, газоплазменную и др.
ПЕЧНАЯ СВАРКА (кузнечная, горновая), соединение пластическим деформированием (напр., с помощью молота) металлических изделий, нагретых в печах или горнах.
ПЛАВКА,
1) переработка материалов (руд, металлов и т. д.) в плавильных печах с получением конечного продукта в жидком виде (напр., доменная или кислородно-конвертерная плавка).
2) Разовый цикл этой переработки, а также полученный в результате этого продукт.
ПЛАЗМЕННАЯ ПЕЧЬ, электрическая печь для нагрева, плавки и металлургической переработки металлов и сплавов с помощью плазмотрона. Различают плазменнодуговые и плазменные высокочастотные печи. Применяются для производства высококачественных металлов и сплавов, выращивания монокристаллов и т. д.
ПОКОВКА, промежуточная заготовка или изделие, полученное ковкой или объемной штамповкой.
ПОЛИРОВАНИЕ (полировка) (нем. Polieren, от лат. polio — делаю гладким), в машиностроении и приборостроении — обработка изделий (металлических, пластмассовых, стеклянных, керамических и др.) для получения малой шероховатости поверхности. Производится механическими (напр., обработкой абразивным инструментом, полировальной пастой, пластическим деформированием поверхности), электрохимическими и другими методами.
ПОРОШКОВАЯ МЕТАЛЛУРГИЯ, производство порошков металлов и изделий из них, их смесей и композиций с неметаллами. Порошки вырабатываются механическим измельчением или распылением жидких исходных металлов, высокотемпературным восстановлением и термической диссоциацией летучих соединений, электролизом и другими методами. Изделия получают обычно прессованием с последующей или одновременно термической, термохимической обработкой без расплавления основного компонента. Методы порошковой металлургии позволяют изготавливать изделия из материалов, получение которых другими способами невозможно (напр., из несплавляющихся металлов, композиций металлов с неметаллами) или экономически невыгодно. С помощью порошковой металлургии получают тугоплавкие и твердые материалы и сплавы, пористые, фрикционные и другие материалы и изделия из них.
ПРЕСС (франц. presse, от лат. presso — давлю, жму), машина статического (неударного) действия для обработки материалов давлением (брикетирования, получения искусственных алмазов и других целей). В металлообработке используют для ковки, штамповки, прессования (выдавливания), сборочных операций (запрессовки или распрессовки деталей) и т. д. По виду привода подразделяют на гидравлические, механические и гидромеханические. Усилие, развиваемое наиболее крупным прессом, ок. 750 МН.
ПРЕССОВАНИЕ,
1) способ обработки материалов давлением с целью их уплотнения (иногда и придания определенной формы).
2) Способ обработки металлов давлением, заключающийся в выдавливании (экструдировании) металла из замкнутой полости контейнера через канал матрицы, форма и размеры которого определяют сечение прессуемого профиля.
3) Способ производства изделий из пластмасс и резин в пресс-формах, заключающийся в размягчении материала при нагревании и фиксации формы изделия в результате выдержки под давлением. При прямом (компрессионном) прессовании материал нагревают в пресс-форме, при литьевом (трансферном) прессовании — в камере, из которой материал продавливается в пресс-форму по т. н. литниковым каналам.
ПРИБЫЛЬ, в технике —
1) верхняя часть стального слитка, где располагается усадочная раковина; при дальнейшей обработке слитка отрезается и поступает на переплав.
2) Питающий элемент литниковой системы, обычно расположенный над наиболее массивной частью отливки; удаляется после ее остывания.
ПРОКАТ, в металлургии — продукция прокатного производства: балки, рельсы, трубы, листы, полосы, ленты и т. д. Изготовляется также т. н. прецизионный прокат.
ПРОКАТКА металлов, способ обработки металлов давлением — обжатие между вращающимися валками прокатных станов. Различают продольную, поперечную и винтовую (косую) прокатку, а также поперечно-винтовую и продольно-винтовую прокатку; в зависимости от степени нагрева обрабатываемого металла — горячую, холодную и теплую прокатку. Разновидность — бесслитковая прокатка.
ПРОКАТНОЕ ПРОИЗВОДСТВО, получение из стали и других металлов путем прокатки различных изделий и полуфабрикатов, а также дополнительная обработка их с целью повышения качества. В промышленных странах прокатке подвергается более 80% выплавляемой стали.
ПРОКАТНЫЙ СТАН, в металлургии — машина или система машин для осуществления прокатки. Классифицируются по назначению (заготовочные, листовые, полосовые, сортовые, в т. ч. балочные и проволочные, трубопрокатные и деталепрокатные); по технологическому процессу (литейно-прокатные, обжимные, реверсивные, одноклетьевые, тандемы, многоклетьевые, непрерывные, холодной прокатки); по числу валков в клети — двух-(дуо), трех-(трио), четырех-(кварто) и многовалковые.
ПРОСЕЧКА, операция ковки и листовой штамповки — получение в заготовке сквозного отверстия.
ПРОТЯГИВАНИЕ (иногда называют протяжкой), обработка резанием внутренних и наружных поверхностей (цилиндрических, прямоугольных, фасонных) заготовок поступательным перемещением протяжки. Протягиванием получают шпоночные канавки, шлицы и др. Осуществляется на протяжных станках.
ПРОТЯЖКА,
1) штамповочная операция — получение полых поковок (стаканов, гильз и др.) на протяжных прессах.
2) В кузнечном производстве — то же, что вытяжка.
3) В обработке металлов резанием — то же, что протягивание.
ПРОФИЛЬ металлический, изделие, полученное прокаткой, прессованием, формовкой (гибкой) между валками. Различают профили с постоянным или переменным по длине поперечным сечением (в т. ч. периодическим) и специальные профили (бандажи, колеса, шестерни, шары и др.).
ПРОШИВКА, в металлообработке — операция обработки металлов давлением — получение полости или сквозного отверстия в заготовке сплошного сечения (напр., при штамповке деталей типа стаканов, при изготовлении трубных заготовок на косовалковых станах).
ПРУТОК, длинномерный металлический полуфабрикат — заготовка для получения деталей способами пластической деформации или обработки резанием. Сечение прутка круглое (наиболее часто), шестиугольное, прямоугольное, реже трапециевидное, овальное или сегментное. Изготовляют прокаткой, прессованием, ковкой.
ПУАНСОН (франц. poincon),
в металлообработке — одна из основных деталей инструмента, используемого при штамповке и прессовании металлов. При штамповке пуансон оказывает непосредственное давление на обрабатываемый металл. При прессовании передает давление на заготовку через пресс-шайбу; в этом случае пуансон часто называют пресс-штемпелем или шплинтоном.
РАСКИСЛЕНИЕ металлов, удаление из расплавленных металлов (главным образом стали) растворенного в них кислорода. Осуществляют введением химических элементов, образующих устойчивые соединения с кислородом. Для раскисления применяют Al, Si, Ti и др. элементы или сплавы (напр., ферросплавы) с большим сродством к кислороду, чем у основного металла.
РАСТОЧНЫЙ СТАНОК, металлорежущий станок для обработки (растачивания) вращающимся режущим инструментом предварительно полученных отверстий. Иногда используется для обтачивания торцов деталей, фрезерования плоскостей и т. п. Различают горизонтально-расточные, координатно-расточные и алмазно-расточные станки.
РАФИНИРОВАНИЕ (нем. Raffinieren, от франц. raffiner — очищать), окончательная очистка продукта от примесей в металлургической, химической, пищевой и других отраслях промышленности.
РЕАКЦИОННАЯ ПЛАВКА, способ получения металлов, основанный на идущей при нагреве химической реакции между сульфидом и оксидом или сульфатом извлекаемого металла (напр., реакционная плавка свинца: PbS + 2PbO = 3Pb + SO2 или PbS + PbSO4 = 2Pb + 2SO2).
РЕВОЛЬВЕРНЫЙ СТАНОК, металлорежущий станок обычно токарной группы с револьверной головкой (вертикальной, горизонтальной или наклонной); иногда применяются сверлильные револьверные станки.
РЕЗЬБООБРАБАТЫВАЮЩИЕ СТАНКИ, группа металлорежущих станков для образования резьб на различных заготовках. Различают резьбообрабатывающие станки: токарно-винторезные, резьбофрезерные, резьбошлифовальные, гайко-, болто-, трубо- и муфтонарезные. Образование резьб может производиться также на сверлильных, расточных и накатных станках.
РУЧЕЙ, в металлообработке —
1) углубление на поверхности валка прокатного стана для придания прокатываемой заготовке требуемой формы.
2) Часть штампа для объемной штамповки — обычно фасонная полость, поверхность которой (или часть ее) служит для получения профильной заготовки (поковки).
СВАРКА, процесс получения неразъемного соединения деталей машин, конструкций и сооружений при их местном или общем нагреве, пластическом деформировании или при совместном действии того и другого в результате установления межатомных связей в месте их соединения. Сваривают детали из металлов, керамических материалов, пластмасс, стекла и др. Существуют способы сварки, при которых материал расплавляется (дуговая, электрошлаковая, электронно-лучевая, плазменная, лазерная, газовая и др.), нагревается и пластически деформируется (контактная, высокочастотная, газопрессовая и пр.) или деформируется без нагрева (холодная, взрывом и др.); способ диффузионного соединения в вакууме. Различают также сварки: по виду используемого источника энергии — дуговая, газовая, электронно-лучевая и др.; по способу защиты материала — под флюсом, в защитных газах, вакууме и др.; по степени механизации — ручная, полуавтоматическая и автоматическая.
СВЕРЛЕНИЕ, образование сквозного или глухого цилиндрического отверстия в материале сверлом. Осуществляется вручную дрелью и др. инструментами или на сверлильных, токарных, револьверных и др. станках.
СВЕРЛИЛЬНЫЙ СТАНОК, для образования и обработки отверстий в заготовках из металлов и др. материалов сверлом. Могут выполняться следующие основные операции: сверление, зенкерование, зенкование, развертывание, растачивание, нарезание резьб. Различают сверлильные станки: вертикальные, радиальные, центровальные, многошпиндельные, агрегатные и специальные.
СЛЯБ (англ. slab, букв. — плита), полупродукт металлургического производства - стальная заготовка прямоугольного сечения с большим отношением ширины к высоте (до 15). Получают из слитков прокаткой на слябинге (иногда на блюминге или блюминге-слябинге) либо из жидкого металла на машинах непрерывного литья.
СЛЯБИНГ (англ. slabbing), высокопроизводительный прокатный стан для обжатия крупных (массой до 45 т) стальных слитков в слябы. Характеризуется диаметром горизонтальных валков в мм, который обычно проставляется рядом со словом слябинг (напр., слябинг 1150).
СОРТАМЕНТ (сортимент) (искаженное франц. assortiment, от assortir - подбирать, сортировать), состав продукции по маркам, профилям, размерам. Термин «сортамент» применяется в металлургической промышленности (преимущественно к металлопрокату), а «сортимент» - в производстве лесоматериалов.
СТРОГАЛЬНЫЙ СТАНОК, металлорежущий станок для обработки плоских и фасонных поверхностей. Главное движение (возвратно-поступательное) у поперечно-строгальных станков совершает резец вместе с суппортом и ползуном, а у продольно-строгальных — заготовка.
СУПЕРФИНИШ (суперфиниширование) (от супер... и англ. finish — отделка, обработка), тонкая отделочная обработка поверхностей деталей брусками из мелкозернистых абразивных материалов.
ТЕРМИТНАЯ СВАРКА, технологический процесс, при котором зазор между соединяемыми деталями, предварительно нагретыми до 400-700 °С, заполняется металлическим расплавом, полученным при сгорании термита. Используется для сварки проводов, труб, рельсовых стыков.
ТОКАРНЫЙ СТАНОК, предназначен для обработки заготовок из металлов и др. материалов в виде тел вращения. На токарном станке производят точение поверхностей, нарезание резьб, сверление, зенкерование, зенкование и развертывание. Главное движение (вращательное) осуществляется заготовкой, движение подачи (поступательное) — режущим инструментом. Различают токарные станки винторезные, револьверные, карусельные, многорезцовые, центровально-отрезные и специализированные.
ТОЧЕНИЕ (токарная обработка), обработка поверхностей тел вращения резанием. Характеризуется вращательным движением заготовки (главное движение) и поступательным движением инструмента — резца (подача).
УЛЬТРАЗВУКОВАЯ ОБРАБОТКА, осуществляется с помощью ультразвука. Применяется для сварки, при сверлении, шлифовании, гравировании твердых материалов, пайке и лужении, получении аэрозолей, эмульсий и суспензий, очистке деталей от загрязнений и в других процессах. Производится с помощью газо- и гидроструйных излучателей, сирен и электроакустических преобразователей.
УСАДОЧНАЯ РАКОВИНА, полость в металлическом слитке (обычно в верхней части) или фасонной отливке, образующаяся при затвердевании металла (в результате усадки).
ФИЛЬЕРА (франц. filiere, от fil — волокно, нить),
1) деталь машин в виде колпачка или пластины с отверстиями диаметром 0,06-0,8 мм для формования химических волокон.
2) Фильера в металлообработке — волока с одним отверстием.
ФЛЮС (нем. Flu, букв. — поток, течение),
1) в металлургии — материалы, вводимые в шихту для образования шлаков с заданными физическими и химическими свойствами.
2) При газовой и кузнечной сварке металлов — химикаты, растворяющие оксиды, образующиеся на свариваемых поверхностях.
3) При автоматической сварке — материалы сложного состава, под слоем которых ведется сварка.
4) При паянии — расплавляемые неметаллические вещества (канифоль, бура, хлорид цинка и др.), служащие для очистки поверхности припоя и места пайки, а также улучшения смачиваемости места пайки расплавленным припоем.
ФЛЮС (нем. Flu, букв. — поток, течение),
1) в металлургии — материалы, вводимые в шихту для образования шлаков с заданными физическими и химическими свойствами.
2) При газовой и кузнечной сварке металлов — химикаты, растворяющие оксиды, образующиеся на свариваемых поверхностях.
3) При автоматической сварке — материалы сложного состава, под слоем которых ведется сварка.
4) При паянии — расплавляемые неметаллические вещества (канифоль, бура, хлорид цинка и др.), служащие для очистки поверхности припоя и места пайки, а также улучшения смачиваемости места пайки расплавленным припоем.
ФОРМА литейная, приспособление в литейном производстве для получения отливок. Изготовляются из формовочных материалов (разовые), огнеупорной керамики (полупостоянные — выдерживают сотни отливок) или металла (постоянные — десятки тысяч отливок).
ФОРМОВКА, изготовление литейных песчаных форм. Различают формовку ручную (ямную или в опоках, по моделям или шаблону) и более распространенную — машинную (по моделям в опоках).
ФРЕЗА (от франц. fraise), режущий многолезвийный инструмент в виде тела вращения с зубьями для фрезерования. Бывают цилиндрические, торцовые, червячные и др. Материал режущей части — быстрорежущая сталь, твердый сплав или композит. В деревообработке известна фреза в виде цепи — фрезерная цепь из закаленной инструментальной стали.
ФРЕЗЕРНЫЙ СТАНОК, служит для обработки плоских и фасонных поверхностей, тел вращения, зубчатых колес и т. п. металлических и других заготовок фрезой. Различают фрезерные станки: консольные (вертикальный, горизонтальный и универсальный), бесконсольные, продольно-фрезерные, специальные и др. В деревообработке фрезерный станок используют для обработки плоскостей и фасонных поверхностей.
ФРЕЗЕРОВАНИЕ (в металлообработке), обработка материалов резанием с помощью фрезы. Фреза совершает вращательное, а заготовка - преимущественно поступательное движение. Осуществляется на фрезерных станках.
ХОЛОДНАЯ СВАРКА, сварка без нагрева (обычно при температуре ок. 20 °С) приложением давления, создающего значительную пластическую деформацию в зоне соединения. Используется для сварки материалов (в т. ч. разнородных), имеющих высокие пластические свойства (металлов, пластмасс и др.). Холодной сваркой называют также дуговую сварку чугунных деталей без предварительного нагрева.
ХОНИНГОВАНИЕ (англ. honing, от hone — точить), отделочная обработка поверхностей (в основном внутренних поверхностей цилиндрических заготовок) мелкозернистыми абразивными брусками, смонтированными на головке (хоне) хонинговального станка. Хон вращается и одновременно совершает возвратно-поступательное осевое движение.
ЦЕНТРОБЕЖНОЕ ЛИТЬЕ, способ литья в быстро вращающуюся металлическую форму. Расплавленный металл под действием центробежных сил отбрасывается к стенкам формы и затвердевает, образуя пустотелую отливку (трубку, втулку, кольцо) без стержня.
ШИХТА (нем. Schicht), смесь в определенной пропорции сырых материалов, а в некоторых случаях (напр., при выплавке чугуна в доменной печи) и топлива, подлежащая переработке в металлургических, химических и других агрегатах.
ШЛАК (от нем. Schlacke),
1) шлак металлургический — расплав оксидов (после затвердевания — камне- или стекловидное вещество), обычно покрывающий поверхность жидкого металла в плавильных печах. Формируется из пустой породы рудных материалов, из флюсов и т. д.
2) Шлак топливный — частицы золы, спекшиеся или сплавленные в куски.
ШЛИФОВАЛЬНЫЙ СТАНОК, станок для обработки материалов шлифованием. В металлообработке по кинематическим особенностям различают шлифовальные станки: кругло-, внутри-, бесцентрово- и плоскошлифовальные и планетарные. К ним относят также заточные и некоторые другие металлорежущие станки, работающие абразивным инструментом. В деревообработке различают ленточные, цилиндровые, щеточные и другие шлифовальные станки. В камнеобработке шлифовальные станки в основном аналогичны плоскошлифовальным.
ШЛИФОВАНИЕ (шлифовка) (от польск. szlifowac — точить, полировать, шлифовать), обработка поверхностей изделий из различных материалов (металлические, деревянные, стеклянные, керамические и др.) абразивным инструментом на шлифовальных станках. С помощью шлифования получают поверхности с малой шероховатостью.
ШТАМПОВКА, способ обработки давлением металлов и других материалов, при котором форма и размеры изделия определяются конфигурацией инструмента — штампа. Различают штамповку объемную и листовую, горячую и холодную, прессовую и молотовую. Штамповкой называют также изделие, полученное в результате этого процесса; иногда изделия, полученные объемной штамповкой, называют штампованной поковкой.
ЭЛЕКТРОИМПУЛЬСНАЯ ОБРАБОТКА, разновидность электроэрозионной обработки; осуществляется импульсами дугового разряда.
ЭЛЕКТРОИСКРОВАЯ ОБРАБОТКА, разновидность электроэрозионной обработки; осуществляется искровым разрядом.
ЭЛЕКТРОКОНТАКТНАЯ ОБРАБОТКА, разновидность электромеханической обработки, при которой инструмент снимает с заготовки материал, размягченный (расплавленный) при нагреве электрическим током, проходящим в месте контакта инструмента, напр. резца, с деталью.
ЭЛЕКТРОМЕХАНИЧЕСКАЯ ОБРАБОТКА, осуществляется одновременно механическим и электрическим действием на материал заготовки (напр., электроконтактная обработка) либо механическим воздействием, возникающим при преобразовании электрической энергии некоторыми физическими методами (ультразвуковая обработка и др.).
ЭЛЕКТРОННО-ЛУЧЕВАЯ ПЛАВКА, рафинирующий переплав тугоплавких металлов или высоколегированных сталей в эектронно-лучевых печах. Электронно-лучевая плавка обеспечивает высокую чистоту переплавленного материала (напр., содержание газов в металле снижается в сотни раз) и однородность его структуры.
ЭЛЕКТРОННО-ЛУЧЕВАЯ СВАРКА, сварка расплавлением материалов в месте их соединения пучком электронов с энергией до 100 кэВ. Выполняется в вакууме. Применяется для прецизионной сварки, сварки изделий из особо чистых, разнородных или тугоплавких металлов (напр., в микроэлектронике).
ЭЛЕКТРОСВАРКА, сварка, при которой свариваемые части нагреваются электрическим током. Различают электросварку дуговую и контактную.
ЭЛЕКТРОШЛАКОВАЯ СВАРКА, сварка плавлением металлов в месте соединения. Источником нагрева металла служит теплота, которая выделяется при прохождении электрического тока через расплавленный шлак, находящийся в зазоре между соединяемыми деталями.
ЭЛЕКТРОШЛАКОВОЕ ЛИТЬЕ, способ литья, при котором жидкий металл, полученный методом электрошлакового переплава, транспортируется (не соприкасаясь с воздухом) в водоохлаждаемый медный кристаллизатор, являющийся литейной формой. Отливки, полученные электрошлаковым литьем, приближаются по свойствам к поковкам. Применяется ограниченно для изготовления сравнительно несложных отливок (напр., коленчатых валов).
ЭЛЕКТРОЭРОЗИОННАЯ ОБРАБОТКА, обработка металлов, основанная главным образом на тепловом действии электрического тока между инструментом и деталью. Различают электроэрозионную обработку размерную, основанную на эрозии (разрушении материалов электрическим разрядом), и электроэрозионную обработку для упрочнения поверхности или покрытия ее защитным слоем. Разделяется на электроимпульсную и электроискровую.
Дата добавления: 2020-04-25; просмотров: 290; Мы поможем в написании вашей работы! |
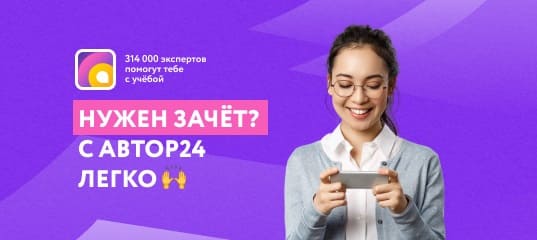
Мы поможем в написании ваших работ!