Описание процесса приготовления шихты
КОМИТЕТ ОБРАЗОВАНИЯ, НАУКИ И МОЛОДЕЖНОЙ ПОЛИТИКИ ВОЛГОГРАДСКОЙ ОБЛАСТИ
Государственное бюджетное профессиональное образовательное учреждение
«Волгоградский колледж управления и новых технологий
Имени Юрия Гагарина»
(ГБПОУ «ВКУиНТ им. Ю. Гагарина»)
КУРСОВАЯ РАБОТА
по МДК.06.02. Подготовка и ведение технологического процесса производства угольных электродов для алюминиевых электролизеров
ПМ.06Подготовка и ведение технологического процесса производства алюминия и сплавов
Разработчик (выполнил(а)):
Карандасов Михаил Владиславович
Курс 2 Группа № ЦМд-17/11
Специальность 22.02.02
Металлургия цветных металлов
Руководитель: Фетисов Сергей Александрович
Волгоград
2019 г.
Изм. |
Лист |
№ докум. |
Подпись |
Дата |
Лист |
2 |
Разраб. |
Карандасов М. |
Провер. |
Фетисов С.А. |
Лит. |
Листов |
ГБПОУ «ВКУиНТ им. Ю. Гагарина» |
|
|
Введение | 3 |
Раздел 1 Разработка транспортно-технологической схемы отделения приготовления коксовой шихты | 5 |
Раздел 2 Разработка технологического процесса смешения | 10 |
2.1Описание процесса приготовления шихты | 11 |
2.2Описание используемого дробильного оборудования | 12 |
2.3Транспортные средства | 13 |
2.4Емкости для хранения | 14 |
Заключение | 20 |
Список использованной литературы | 21 |
Приложения | 22 |
Изм. |
Лист |
№ докум. |
Подпись |
Дата |
Лист |
3 |
КР_22.02.02_ЦМд-17/11_23 |
Применение углеродистых материалов
Электродные материалы широко применяются в электролитическом производстве легких металлов , особо широкое использование получили в производстве алюминия, для изготовления анода и изделий для футеровки катодных устройств. Это объясняется их специфическими, а зачастую уникальными свойствами: высокой теплостойкостью, хорошей тепло и электропроводимостью, низким коэффициентом линейного расширения и химической инертностью, что позволяет им успешно работать в агрессивной среде ( при производстве алюминия это криолитоглиноземные расплавы).
|
|
Алюминий наиболее востребованный металл, среди всех легких металлов, поэтому производство электродов для алюминиевой промышленности занимает ведущее значение во всей электродной промышленности.
При электролизе алюминия расходуется оксид алюминия (глинозём) и углерод анода, который окисляется кислородом, выделившимся при разложении глинозёма при протекании через электролит (расплав криолита 3NaF∙AlF3) электрического тока. Это на сегодня единственный используемый способ производства алюминия и практически всех легких металлов.
В России до настоящего времени широко применяются электролизеры с самообжигающимися анодами (СА) и лишь небольшая часть алюминия производится на электролизерах с предварительно обожженными анодами (ОА). Анодная масса, используемая для формования СА, изготавливается в цехах анодной массы Братского (ЬрАЗ), Красноярского (КрАЗ), Иркутского (ИркАЗ), Волгоградского (ВгАЭ), Богословского (БАЭ), Новокузнецкого (НКАЭ) алюминиевых заводов. Обожженные аноды, используемые наСаяногорском (ОА) алюминиевом заводе, изготавливаются в цехе обожженных анодов этого же завода.
|
|
Производство электролитического алюминия в России превысило 3000 тыс. т, на производство 1 т которого расходуется 480-580 кг анодов. Таким образом, алюминиевая промышленность является крупным потребителем электродной продукции, основу которой составляет анодная масса, т.к. в
России на электролизерах СА производится более 75% всего выпускаемого алюминия.
Несмотря на многообразие электродных изделий, они изготавливаются по однотипной технологической схеме: твердые углеродные материалы в виде набора частиц различных, но определенных размеров перемешивают со связующим веществом. Полученная масса используется для формирования анода (на электролизерах с СОА) или изготовление обожженных анодов( для электролизеров с ОА)
Принципиальная технологическая схема производства анодной(электродной) массы приведена ниже.
Изм. |
Лист |
№ докум. |
Подпись |
Дата |
Лист |
4 |
КР_22.02.02_ЦМд-17/11_23 |
Изм. |
Лист |
№ докум. |
Подпись |
Дата |
Лист |
5 |
КР_22.02.02_ЦМд-17/11_23 |
|
|
Изм. |
Лист |
№ докум. |
Подпись |
Дата |
Лист |
6 |
КР_22.02.02_ЦМд-17/11_23 |
описание процесса приготовления шихты
Исходным сырьем для процесса подготовки шихты является прокаленный кокс, огарки анодов, брак обжига, уловленная пыль аспирационных систем, отходы собственного производства и другие материалы. Кокс должен быть рационально измельчен, классифицирован по крупности и распределен по соответствующим бункерам для дозирования. Назначением передела дробления, рассева и размола кокса является получение компонентов коксовой шихты (крупки, отсев, пыль), обеспечивающих заданный гранулометрический состав кокса-наполнителя анодной массы
2.2 Описание используемого дробильного оборудован
Изм. |
Лист |
№ докум. |
Подпись |
Дата |
Лист |
6 |
КР_22.02.02_ЦМд-17/11_23 |
Целью дробления является правильное и полное использование всего исходного сырья, путем получения материала всех классов крупности в необходимом соотношении.
В зависимости от крупности дробимого материала и дробленного продукта стадии дробления имеют свои названия:
- крупное дробление (куски 1000-300мм)
- среднее дробление (куски 50-5мм)
- тонкое дробление (куски 5мм и менее)
Для дробления коксов и оборотных материалов применяются:
— валковые дробилки с зубчатыми и гладкими валками,
— щековые дробилки,
— молотковые и роторные дробилки,
— конусные дробилки
Щековые дробилки используют для дробления крупногабаритных материалов (брака обожженных и «зеленых» анодов, крупных блоков, огарков и др.).
Зубчатые валковые дробилки используют на узле предварительного дробления коксов, где куски кокса могут достигать 500—700 мм.
Для среднего и тонкого дробления применяют комбинацию молотковых и валковых дробилок с гладкими валками.
Конусные дробилки универсальны.
Для получения коксовой пыли используются шаровые мельницы.
Способы дробления
Молотковые дробилки.
Изм. |
Лист |
№ докум. |
Подпись |
Дата |
Лист |
6 |
КР_22.02.02_ЦМд-17/11_23 |
Процесс дробления в молотковых дробилках происходит по принципу удара и частичного истирания материала вращающимися с большой скоростью ударными телами (молотками, билами).
По числу установленных роторов молотковые дробилки подразделяют на однороторные и двухроторные, по способу закрепления молотков — со свободно закрепленными и жестко закрепленными на роторе молотками. В зависимости от конструкции разгрузочной части различают дробилки с колосниковыми решетками и без них, с полностью открытым для выхода дробленого продукта низом.
Применяются преимущественно для среднего дробления
Производительность однороторной дробилки используется эмпирическая формула
Q =( 30÷40) DL
Q- производительность, м3/час
D - наружный диаметр окружности, описываемой молотками, м
L - длина ротора или загрузочного отверстия, м
Валковые дробилки
Материал в валковых дробилках измельчается между двумя вращающимися навстречу один другому валками путем раздавливания и частичного истирания. Измельчаемый материал увлекается силой трения в щель между валками и дробится до величины зерна, соответствующего ширине этой щели.
Различают дробилки с гладкими, зубчатыми и рифлеными валками.
По принципу действия и конструктивному оформлению валковые дробилки с зубчатыми и рифлеными валками наиболее эффективны на предварительном дроблении сырого кокса перед прокалкой.дробилки с гладкими валками наиболее приемлемы на узле среднего дробления, с установкой после молотковой дробилки.
Производительность валковой дробилки
Q=188* d * L * D * n *µ* p
d - ширина зазора между валками,м
L - длина валков, м
D - диаметр валков, м
n - частота вращения валков,об/мин
µ- коэффициент , учитывающий использования длины валка и разрыхления материалов 0,2-0,3 для крепких материалов, 0,5-0,6 для вязких и влажных материаллов
p - обьемная плотность дробимого материала , т/м3
Изм. |
Лист |
№ докум. |
Подпись |
Дата |
Лист |
6 |
КР_22.02.02_ЦМд-17/11_23 |
Подготовка сортовой пыли
Для получения тонких фракций шихты( менее 0,16мм) применяют шаровые мельницы. Исходный материал – фракции - 0,63-2 мм получаемый после рассева на грохоте при дроблении, поступают во вращающийся барабан, заполненный на 35-40% объема стальными шарами. Проходя расстояние от загрузочного устройства до разгрузочного, материал, под воздействием движущихся шаров, непрерывно истирается и раздавливается до требуемой величины (тонины помола).
Грохота
Разделение зерен различной крупности на фракции, состоящие из зерен близких по размеру , называется классификацией или грохочением( разделением). Операция заключается в пропускание смеси зерен через сита с отверстиями определенного размера.
Изм. |
Лист |
№ докум. |
Подпись |
Дата |
Лист |
6 |
КР_22.02.02_ЦМд-17/11_23 |
При просеивании не всегда зерна меньше отверстия сита проходят через сито, часть остается над ситом. Определяется это точность просеивания или КПД (h %) грохота.
h = 100* g 1 / g
g 1 –масса продукта нижнего класс, прошедших через отверстия сита
g – масса продукта нижнего класса в исходном продукте
На эффективность рассеивания влияют факторы размер и форма отверстий, угол наклона сита, скорость и длина пути перемещения материала, частота, амплитуда и направление колебаний сита.
Точность просеивания и производительность грохочения важнейшие показатели процесса, они зависят от ряда факторов.
Эффективность грохочения зависят от размера и формы частиц материала. С увеличением мелкого класса в исходном материале производительность возрастает. Пластинчатая и продолговатая форма частиц наиболее благоприятна для грохочения.
Ширина сита определяет производительность, длина определяет продолжительность или точность грохочения. Выбор отношения длины и ширины определяется требованием к грохочению.
На размер зерен нижнего продукта влияет угол наклона сита и толщина проволок, из чего плетется сито. Фактический размер зерен нижнего продукта меньше размера отверстий сита из-за нак
Изм. |
Лист |
№ докум. |
Подпись |
Дата |
Лист |
6 |
КР_22.02.02_ЦМд-17/11_23 |
На производительность грохота и точность рассева влияет равномерность подачи материала и равномерность его распределения по поверхности сита.
Для повышения производительности и точности грохочения используются схемы с предварительным отсевом и повторным дроблением крупных фракций .Схема называется дробление и классификация в замкнутом цикле.
Конструкция грохотов
При производстве электродной массы применяются грохота;
- неподвижные колосниковые
- цилиндрические
- вибрационные
При выборе оборудования для грохочения крупнокускового материала ширина течки, питателя и грохота должны быть не менее трех максимальных размеров наибольшего куска, ширина не менее двух размеров ширины грохота.
Грохоты неподвижные. К ним относятся колосниковые грохоты и горизонтальные решетки. Используются для материалов крупнее 150-200мм. Наклон не менее 350, эффективность грохочения не более 60-65%.
Грохоты цилиндрические(барабанные) представляют собой перфорированные цилиндрические или конические барабаны диаметром до2,7м и длиной до12м, с углом наклона 2-80. Эффективность грохочения 60-65%. В электродном производстве сейчас не применяются.
Грохота вибрационные. Получили наибольшую применение в электродной производстве. При просеивании получается количество продуктов на 1 больше количества установленных сит. Для очистки отверстий сит используются шары , которые располагаются под ситами на расстоянии порядка50-100мм с отверстиями более подсетового продукта. Короба виброгрохотов располагаются наклонно под углом 15-300 , сетки совершают круговые или слабо эллиптические колебания. КПД 75-80%
В настоящее время используются грохота принцип работы, которых основан на классификации материала через круто наклонные сита, с дифференцированно увеличенным размером ячеек сит. Очистка ячеек сит от материала производиться под действием амплитуды грохота, без применения дополнительных приспособлений, специальных шаров. Чистота рассева по всем фракциям не меньше 95%.±3%. Замена сит осуществляется с торца грохота без трудоемких операционных затрат.
Производительность грохота до 30т/ч. Грохота могут быть как подвесные так и установленные на полу.
Виброгрохота характеризуются ;
- площадь сита 3,1-5,6м2
-число сит от количества получаемых фракций
-угол наклона короба в основном 10-250, достигают до450
- амплитуда колебания от1-6 мм
-частота колебаний от 600 до1150мин-1
Двухсеточный грохот
Изм. |
Лист |
№ докум. |
Подпись |
Дата |
Лист |
6 |
КР_22.02.02_ЦМд-17/11_23 |

Поверхности грохочения.
Сито это поверхность грохота. В зависимости от крупности перерабатываемого материала используются сита;
Изм. |
Лист |
№ докум. |
Подпись |
Дата |
Лист |
6 |
КР_22.02.02_ЦМд-17/11_23 |
-тканые
-плетеные сита
Сетки изготовляют из специальной стали, латуни, фосфористой бронзы и пр.
В электродной промышленности используют сита из тканой проволочной сетке с квадратными или прямоугольными ячейками нормальной точности (Н) и щелевые сетки на соединительных шпильках. Для проведения ситовых анализов используются сетки повышенной точностью(П)
Характеристики сетки они зависят от размера ячейки и диаметра проволоки;
-Живое сечение сетки характеризует отношение суммарной площади отверстий к общей площади сита (Р%), зависит от отношения диаметра проволоки к размеру ячейки, выражается формулой.
Р=100/(1+ d / a )2
d -диаметр проволоки, мм
a- размер стороны квадратной ячейки ,мм
- коэффициент плотности( К%) рассчитывается по формуле
К=100-Р=100[1-а2/(а+ d )2]
К- плотности уменьшается с увеличением диаметра проволоки.
Классификация по плотности;
-малая (М) – К < 25%
-нормальная (Н) - К=25-50%
-большая (Б) – К=50-75%
- особо большая (ОБ) – К >75%
Транспортные средства
Изм. |
Лист |
№ докум. |
Подпись |
Дата |
Лист |
6 |
КР_22.02.02_ЦМд-17/11_23 |
Питателем называется механизм, при помощи которого проводится равномерная подача материала. Питатели обычно устанавливаются под разгрузочным отверстием бункеров, из которых материал транспортируют в перерабатывающие его агрегаты. Питатели перекрывают выпускное отверстие бункеров и, следовательно, выполняют одновременно функции затворов. В цехах анодной массы нашли наибольшее распространение пластинчатые, вибрационные, тарельчатые и лотковые питатели.
Ковшовые элеваторы.
Транспортные устройства, перемещающие материал в вертикальном направлении или в направлении, близком к вертикальному, называются элеваторами.
Ленточные транспортёры.
Ленточные конвейеры (транспортёры) — это машины непрерывного действия, предназначенные для транспортирования сыпучих грузов в горизонтальном или наклонном направлении.
Винтовые конвейеры –это устройства, транспортирующие материал по жёлобу при помощи вращающегося винта.
Пневматическим транспортированием называется перемещение материала по трубам воздушной струей. Частицы материала образуют с воздухом аэросмесь, которая движется под действием перепада давлений в начале и конце трубопровода.
По способу создания перепада давлений пневмотранспортные установки подразделяются на всасывающие, нагнетательные и комбинированные.
Изм. |
Лист |
№ докум. |
Подпись |
Дата |
Лист |
6 |
КР_22.02.02_ЦМд-17/11_23 |
Емкости для хранения
Изм. |
Лист |
№ докум. |
Подпись |
Дата |
Лист |
6 |
КР_22.02.02_ЦМд-17/11_23 |
Дата добавления: 2020-04-25; просмотров: 502; Мы поможем в написании вашей работы! |
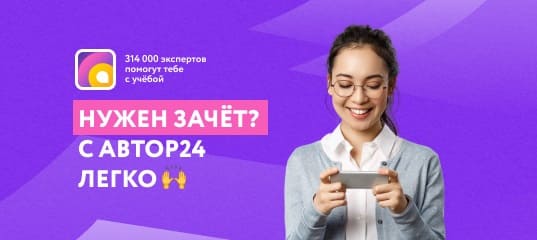
Мы поможем в написании ваших работ!