Принцип работы ректификационного аппарата
Обычно ректификационный аппарат состоит из двух частей: верхней и нижней, каждая из которых представляет собой организованную поверхность контакта фаз между паром и жидкостью.
В нижней части исходная смесь взаимодействует с паром, начальный состав которого равен составу кубового остатка. Вследствие этого из смеси извлекается НКК.
В верхней ступени пар начального состава соответствующий составу исходной смеси, взаимодействует с жидкостью, начальный состав которой равен составу дистиллята. Вследствие этого пар обогащается НКК до требуемого предела, а ВКК извлекается из паровой фазы.
Пар для питания ректификационной колонны получается многократным испарением жидкости, имеющей тот же состав, что и кубовый остаток, а жидкость – многократной конденсацией пара, имеющего состав, одинаковый с составом дистиллята.
Полученный в конденсаторе дистиллят делится на две части. Одна часть направляется обратно в колонну – флегма, другая является отбираемым продуктом – дистиллят. Отношение количества возвращенного в колонну дистиллята (флегмы) к количеству дистиллята, отобранного в виде продукта – называется флегмовым числом R.
В ректификационном аппарате снизу вверх движутся пары, а сверху подается жидкость, представляющая собой почти чистый НКК. При соприкосновении поднимающихся паров со стекающей жидкостью происходит частичная конденсация паров и частичное испарение жидкости. При этом из паров конденсируется преимущественно ВКК, а из жидкости испаряется преимущественно НКК. Таким образом, стекающая жидкость обогащается ВКК, а поднимающиеся пары обогащаются НКК, в результате чего выходящие из аппарата пары представляют собой почти чистый НКК. Эти пары поступают в конденсатор, называемый дефлегматором, и конденсируются. Часть конденсата, возвращаемая на орошение аппарата, называется флегмой, другая часть отводится в качестве дистиллята.
|
|
Как и для всех массобменных процессов эффективность ректификации зависит от поверхности контакта фаз. Для увеличения поверхности массобмена используют различные контактные устройства насадочного или барботажного типа.
Описание технологической схемы ректификационнй установки
Рассмотрим технологическую схему ректификационной установки (рис 2).
Исходная смесь из расходной емкости РЕ центробежным насосом подается в подогреватель П, где нагревается до температуры кипения и поступает на питающую тарелку ректификационной колонны РК. Стекая по тарелкам жидкость, попадает в куб, из которого поступает в кипятильник К. Из кипятильника пары жидкости поступают в нижнюю часть колонны и двигаются навстречу исходной смеси, барботируя через нее и обогащаясь низкокипящим компонентом. Выходя из колонны пары, попадают в дефлегматор Д и конденсируются. Дистиллят поступает в разделитель Р, где разделяется на два потока: одна часть в качестве флегмы возвращается в колонну и стекает по тарелкам вниз, обогащаясь при этом высококипящим компонентом, а другая часть поступает в холодильник Х1, охлаждается и попадает в приемную емкость ПЕ2. По мере работы часть жидкости из куба отводится в холодильник Х2 и поступает в приемную емкость ПЕ1 в качестве кубового остатка.
|
|
Рисунок 2 – Технологическая схема ректификационной установки
Описание конструкции ректификационной колонны
Конструкция колонны с ситчатыми тарелками
Колонны с ситчатыми тарелками (Приложение А) гораздо проще по устройству и дешевле, чем, например, колонны с колпачковыми тарелками. Колонны с ситчатыми тарелками (рисунок 3) состоят из вертикального цилиндрического корпуса 1 с горизонтальными тарелками 2, в которых равномерно по всей поверхности просверлено значительное число мелких отверстий. Для слива жидкости и регулирования её уровня на тарелке есть переливные трубки 3. нижние концы трубок погружены в стаканы 4, находящиеся на лежащих ниже тарелках, и образуют гидравлические затворы.
|
|
Рисунок 3 — Схема устройства ситчатой колонны
1 – корпус; 2 – ситчатая тарелка; 3 – переливная трубка; 4- стакан
Газ (пар) проходит в отверстия тарелки (рисунок 4) и распределяется в жидкости в виде мелких струек; лишь на некотором расстоянии от дна тарелки образуется слой пены и брызг – основная область массообмена и теплообмена на тарелке.
Рисунок 4 — Схема работы ситчатой тарелки
В определенном диапазоне нагрузок ситчатые тарелки обладают довольно большой эффективностью. Для того, чтобы КПД тарелки не уменьшалось резко, давление и скорость газа (пара), проходящего через отверстия тарелки, должны быть достаточными для того, чтобы преодолеть давление слоя жидкости на тарелке и предотвратить тем самым стекание жидкости через отверстия.
Кроме того, протекание жидкости через отверстия увеличивается с увеличением диаметра тарелки и при отклонении от строго горизонтального положения. Поэтому диаметр и число отверстий следует подбирать такими, чтобы жидкость удерживалась на тарелках и не увлекалась механически паром. Обычно принимают диаметр отверстий ситчатых тарелок 0,8-3 мм.
|
|
Очистка, промывка и ремонт ситчатых тарелок проводятся относительно удобно и легко.
Но есть и минусы. Ситчатые колонны эффективно работают только при определенных скоростях ректификации, и регулирование режима их работы. При значительных нагрузках потеря напора довольно большая. Кроме того, как указывалось ранее, тарелки должны быть расположены строго горизонтально, т.к. иначе газ (пар) будет проходить через часть отверстий, не соприкасаясь с жидкостью. А в случае внезапного прекращения поступления газа (пара) или значительно снижения его давления тарелки ситчатой колонны полностью опоражниваются от жидкости, и для достижения заданного режима процесса требуется вновь пустить колонну.
Чувствительность к колебаниям нагрузки, а также загрязнениям и осадкам, которые быстро забивают отверстия тарелки, ограничивают область использования ситчатых колонн. Но для ректификации спирта и жидкого воздуха (кислородные установки), главным образом применяют именно их.
Для повышения эффективности ситчатых тарелок увеличивают длительность контакта между жидкостью и газом (паром), например, принудительным круговым движением жидкости на тарелке при одинаковом направлении её движения на всех тарелках колонны.
Размеры и конструкции перегонного куба, дефлегматора и концевого холодильника зависят от производительности установки, физических свойств перегоняемой смеси и режима процесса (периодический или непрерывный).
Дефлегматор обычно представляет собой кожухотрубчатый теплообменник. В ряде случаев в дефлегматоре происходит конденсация всех паров, вышедших из колонны. В концевом холодильнике дистиллят охлаждается до заданной температуры.
Иногда в дефлегматоре конденсируется лишь часть паров для получения флегмы, а полная конденсация и охлаждение происходят в холодильнике.
Ректификационные установки снабжают также приборами для регулирования и контроля режима работы и нередко аппаратами для утилизации тепла.
Этанол и вода не являются коррозионно-активными веществами, рабочая температура в колонне не выше 100°С, поэтому в качестве конструкционного материала для основных деталей аппарата выбираем сталь Ст 3 ГОСТ 380 – 94: которая используется для изготовления деталей химической аппаратуры при работе с неагрессивными средами при температурах от 10 до 200 °С.
Материальный расчет колонны
Дата добавления: 2020-04-08; просмотров: 557; Мы поможем в написании вашей работы! |
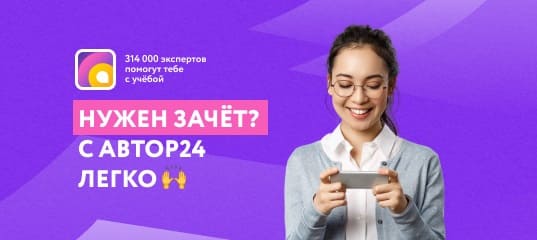
Мы поможем в написании ваших работ!