Определяем стоимости заготовки из проката
ОБЩИЕ СВЕДЕНИЯ О ПРЕДПРИЯТИИ
1.1 История предприятия
Коломенский завод стал одним из ярких символов бурного развития железнодорожного транспорта в Российской империи второй половины XIX века.
Летом 1863 года железнодорожная линия Москва – Саратов достигла Коломны. Предприимчивый и талантливый военный инженер Аманд Егорович Струве добился подряда на строительство моста через реку Оку и соорудил для этого временные мастерские на левом берегу Оки, у ее слияния с Москвой-рекой. Он приобрел в аренду более 10 десятин земли у крестьян села Боброва и получил право «производить разные постройки, как заводские, так и фабричные». Этим было положено основание одного из крупнейших в России Коломенского завода.
Коломенский завод первым в России стал строить мосты для железнодорожного и городского транспорта, прежде Россия покупала их конструкции за границей.
Аманд Струве строит первый мост, временный через Москву-реку для Московско-Казанского участка железной дороги. Вслед за мостом через Оку (1863-1864 гг.) сооружаются все мосты от Коломны до Воронежа и от Серпухова до Курска и Киева. Киевский мост через Днепр, строившийся в 1868-1870 годах, по новому способу с быками «пневматической системы», современники называли самым большим мостом в Европе: его протяженность превышала один километр. По заказу городской Думы Москвы в 60-70-х годах XIX века Коломенский завод построил Бородинский, Краснохолмский, Москворецкий и Крымский мосты. До сих пор одним из самых грандиозных и изящных сооружений считается Литейный мост, построенный в 1879 году через реку Неву в Петербурге.
|
|
Питерский Дворцовый мост (1915 г.) – крупное инженерное сооружение - последний мост Коломенского завода. Он состоит из пяти пролетов, средний из которых быстро раскрывающийся. При проектировании и постройке уделялось особое внимание его архитектуре и художественному декору.
С каждой вступавшей в строй магистралью в стране возрастала потребность в железнодорожной технике. И уже в 1865 году в Коломне было организованно производство первых товарных платформ, а затем и вагонов различного типа и началась подготовка к постройке паровозов. Локомотивостроение на Коломенском заводе ведет свою историю с 1869 года, когда из ворот предприятия вышел первый грузовой паровоз - это был один из первых паровозов, построенных в России.
1.2 Продукция, выпускаемая на предприятии
В настоящее время на Коломенском заводе производятся следующие виды продукции:
Тепловозы
ТЭП70БС
Современный пассажирский магистральный тепловоз ТЭП70БС с энергоснабжением вагонов поезда, мощностью 4000 л.с. конструкционной скоростью 160 км/ч, первый образец которого был построен в 2002 году, имеет модульную конструкцию, которая принята на предприятии как базовая для создания унифицированного ряда новых локомотивов.
|
|
ТЭП70У
Пассажирский тепловоз ТЭП70У является модификацией пассажирского тепловоза ТЭП70, выполненной для повышения его технического уровня и унифицирован по основным узлам с тепловозами ТЭП70БС, 2ТЭ70.
Предназначен для вождения пассажирских поездов на магистральных железных дорогах колеи 1520 мм на неэлектрифицированных участках железных дорог России. Возможна эксплуатация в странах СНГ и Балтии. Климатическое исполнение – У по ГОСТ 15150-69.
2ТЭ70
Современный грузовой тепловоз 2ТЭ70 с двумя шестиосными секциями мощностью 8160 л.с., конструкционной скоростью 110 км/ч, первый опытный образец которого был построен в 2004 году. Локомотив унифицирован по основным узлам с пассажирскими тепловозами ТЭП70, ТЭП70БС, ТЭП70У.
Тепловоз предназначен для вождения грузовых поездов на магистральных железных дорогах колеи 1520 мм на неэлектрифицированных участках железных дорог России. Возможна эксплуатация в странах СНГ и Балтии. Климатическое исполнение – У по ГОСТ 15150-69.
|
|
Электровозы
ЭП2К
Магистральный шестиосный электровоз постоянного тока ЭП2К
предназначен для вождения пассажирских поездов на электрифицированных (3кВ, постоянного тока) участках железных дорог. Дизели
Д49
ОАО «Коломенский завод» является разработчиком и основным производителем современных 4-х тактных среднеоборотных двигателей с газотурбинным наддувом и охлаждением наддувочного воздуха типа Д49 размерности ЧН26/26.
Двигатели ЧН26/26 выпускаются в V-образном исполнении (8, 12 и 16 цилиндров). В зависимости от частоты вращения коленчатого вала (750 ... 1100 об/мин), числа цилиндров и форсировки по среднему эффективному давлению, двигатели охватывают диапазон мощностей от 588 до 4412 кВт.
Д42
Двигатели типа Д42 размерности 30/38 – рядные, среднеоборотные,
четырехтактные, с газотурбинным наддувом и охлаждением наддувочного воздуха. Их конструкция специально разработана для применения в качестве судовой установки и удовлетворяет требованиям, предъявляемым к двигателям данного назначения.
Судовые двигатели размерностью ЧН30/38 в рядном исполнении (4, 6, 8
цилиндров), при частоте вращения коленчатого вала 360-750 об/мин могут использоваться в качестве главных и вспомогательных: для работы на винт, редуктор (в том числе встроенный), реверс-редуктор, как дизель-генератор постоянного и переменного тока.
|
|
16СД500 – флотская версия дизеля Д500 в 16-цилиндровом исполнении, есть 20-цилиндровый вариант для энергетической сферы и 12-цилиндровый для локомотивов на железной дороге. Д500 (на фото вверху) представляет собой четырехтактный комбинированный двигатель внутреннего сгорания размерностью ЧН26,5/31 с V-образным расположением цилиндров с газотурбинным наддувом и охлаждением наддувочного воздуха.
Параллельно Д500 на Коломенском заводе разработали еще один дизель нового поколения – Д300. Он относится к типоразмерному ряду ЧН26/28, и силовые установки на его базе рассчитаны для кораблей, тепловозов и электростанций дизельные двигатели Д300 и Д500 имеют мощность от 3600 до 10000 л.с.
России колеи 1520 мм. Возможна эксплуатация в странах СНГ и Балтии.
Дизель-генераторные установки для АЭС
ОАО «Коломенский завод» более 100 лет является разработчиком, изготовителем и поставщиком среднеоборотных дизельных двигателей различного назначения. Основной продукцией завода в последние годы стали дизели типа Д49 (ЧН26/26). За время изготовления выпущено более 16000 дизелей этой размерности, которые положительно зарекомендовали себя в качестве источников энергии для тепловозов, кораблей, стационарных и передвижных электростанций, как базового, так и резервного назначения. По экологическим показателям двигатели производства ОАО «Коломенский завод» соответствуют требованиям российских стандартов и директивам ЕС. На предприятии внедрена и действует сертифицированная система менеджмента качества, соответствующая требованиям ИСО 9001. Все двигатели производства ОАО «Коломенский завод» проходят сертификацию Росстандарта и, при необходимости, Ростехнадзора.
Немаловажным преимуществом является топливная экономичность и меньшая по сравнению с импортными аналогами цена как ДГУ, так и запасных частей, применяемых отечественных масел и оказываемых сервисных услуг.
Дизели типа Д49 эксплуатируются в Германии, Франции, Болгарии, Венгрии, Сирии, Польше, странах Балтии, Белоруссии, Украине, Египте, Иране, Ираке, Монголии, Корее, Кубе и других странах.
2 ИЗУЧЕНИЕ ОСНОВНЫХ ТЕХНОЛОГИЧЕСКИХ ПРОЦЕССОВ НА РАБОЧИХ МЕСТАХ ПРАКТИКИ
2.1 Продукция, выпускаемая цехом
Цех ТМ2, как отдельное подразделение на Коломенском заводе, был основан 1 октября 1965 года.
Цех ТМ2 выпускает следующие узлы и детали:
- топливные насосы;
- форсунки;
- насосфорсунки 7-Д42 (для 30ДГ);
- форсунки с принудительным охлаждением топлива (для ГДГ);
- форсуночные трубки;
- предельные выключатели различной модификации;
- гидротолкатели Д42 и Д49;
- распылители Д42 и Д49;
- сопловые наконечники различной размерности;
-мотор-вентиляторы ТЭП70.75.04.001сб;
-вентиляторы ТЭП70.85.10.001сб, ЭП2К.85.10.001сб;
- плунжерные пары.
2.2 Структура управления цехом. Участки и службы цеха и их функции
Характер производства – основное.
Вид производства – ТМ2.
Тип производства – мелкосерийное и серийное.
Структура цеха состоит из трех блоков:
· производственный блок:
ü участок прецизионных деталей, деталей форсунок и предельных выключателей;
ü участок цветных, зубчатых, корпусных деталей и деталей топливных насосов
ü шлифовально-доводочный участок;
ü участок сборочно-испытательный, гальванический и консервации;
· блок технического обслуживания:
ü группа технологической подготовки производства;
ü ремонтная служба;
ü служба инструментального хозяйства;
· административно-управленческий блок.
Начальник цеха |
Заместитель начальника цеха (по подготовке производства) |
Заместитель начальника цеха (по производству) |
Бюро технологической подготовки производства инструментального хозяйства (БТППиИХ) |
Механосборочный участок №1 |
Производственно- диспечерское бюро (ПДБ) |
Механический участок №2 |
Слесаро-сборочный участок №3 |
2.3 Виды продукции, выпускаемой на данном участке. Система контроля качества продукции
Функциями службы инструментального хозяйства являются:
- получение инструмента с Центрального инструментального склада;
- хранение и выдача инструмента;
- проверка условий эксплуатации инструмента рабочими цеха.
Для снабжения рабочих мест инструментом в цехе имеется три инструментальных кладовых:
- кладовая режущего и вспомогательного инструмента;
- кладовая измерительного инструмента;
- кладовая абразивного инструмента.
Общее количество инструмента, находящегося в цехе состоит:
- из инструмента, находящегося на рабочих местах;
- второго запасного комплекта;
- месячного запаса кладовой;
Задача СИХ – своевременное обеспечение рабочих мест необходимым инструментом. Замена инструмента производится по графику. Для учета временно выданного инструмента в цехе введена марочная система. В цехе существует склад приспособлений.
Контроль качества инструмента и приспособлений после ремонта осуществляет ОТК цеха (Отдел технического контроля).
2.4 Техника безопасности и пожарная безопасность на данном участке
Основными условиями безопасной работы кладовщика является правильная организация рабочего места, строгое соблюдение производственной дисциплины и требований безопасности.
До начала работы необходимо:
1. Надеть исправную спецодежду. Спецодежда должна быть застегнута на все пуговицы.
2. Подготовить рабочую зону для безопасной работы.
Во время работы:
1. Выполнять только ту работу, по которой прошел обучение, инструктаж и к которой допущен мастером.
2. Содержать рабочее место и помещение в чистоте.
3. Операции складирования грузов, материалов и погрузочно-разгрузочных площадках производить в соответствии с технологической планировкой, с соблюдением действующих санитарных норм и противопожарных правил.
После окончания работы:
1. Привести в порядок рабочее место.
2. Сообщить начальнику цеха или начальнику по ПП обо всех замеченных недостатках в работе.
3. Снять спецодежду и убрать ее в шкаф для рабочей одежды.
Инструкция противопожарной безопасности по участку цеха.
1. Помещение кладовой должно постоянно содержаться в чистоте.
2. Запрещается курение на участке.
3. Запрещается оставлять без присмотра включенные электронагревательные приборы.
2.5 Примеры работ, выполненные на практике
Выполнение токарных работ:
-точение наружной поверхности;
-Разработал технологическую наладку на операцию с ЧПУ;
-центрование отверстий;
- сверление отверстий;
- контроль размеров после выполненной работы;
- выполнение токарной операции обработки детали ЭП2К.31.15.011.
Я обрабатывал такие детали, как втулка, штуцер, гайка, болт и т.д.
3 ИНДИВИДУАЛЬНОЕ ЗАДАНИЕ
3.1 Деталь для практической работы
Из числа деталей, изготовляемых в цехе, подбираем деталь для практической работы. Такой деталью является деталь «Штуцер» 6ТК3.05.003 .
3.3 Назначение и конструкция детали
Деталь «Штуцер» 6ТК3.05.003 устанавливается на корпус патрубка
1-6ТК9.00.020 спг. Штуцер служит для соединения патрубка с дренажной трубкой турбокомпрессора.
Материал детали «Штуцер» сталь 40 ГОСТ 1050-2013 – сталь углеродистая конструкционная с высокой прочностью и вязкостью.
Таблица 1 - Массовая доля элементов, % по ГОСТ 1050-2013
С | Si | Mn | S | P | Cr | Ni | As | N | Cu |
0,37-0,45 | 0,17-0,37 | 0,50-0,80 | ≤ 0,040 | ≤ 0,035 | ≤ 0,25 | ≤ 0,30 | ≤ 0,08 | ≤ 0,008 | ≤ 0,30 |
Таблица 2 - Механические свойства при комнатной температуре
НД | Режим термообработки | сечение | δ 0,2 н/мм | δ в н/мм | δ % | ψ % | KCU дж/см2 | HB | ||
операция | t°С | охлаждающая среда | ||||||||
ГОСТ 1050-2013 | Нормализация | 870 | Воздух | до 80 | 335 | 570 | 19 | 45 | 59 | 217 |
3.4 Выбор заготовки
Технико – экономическое обоснование выбора заготовки для изготовления детали «Штуцер» производим учитывая металлоемкость, трудоемкость, себестоимость и конкретные производственные условия. В машиностроении основными видами заготовок для деталей машин являются стальные и чугунные отливки, отливки из цветных металлов и сплавов, штамповки и всевозможные профили проката.
Способ получения заготовок должен быть наиболее экономичным. Для изготовления детали «Штуцер» применяем два способа получения заготовки: из проката и методом горячей объемной штамповки.
Производим технико-экономическое сравнение двух вариантов изготовления заготовки.
Определяем стоимости заготовки из проката
С = 58,95 ·1,16 – (1,16-0,52) · 12645/1000 = 60,29 руб.
2) Определяем стоимости заготовки изготовленной методом горячей объемной штамповки на горизонтально-ковочной машине (ГКМ)
Сзш = 188,55·0,87-(0,87-0,52)·12645/1000=159,60 руб.
3) Определяем годовую экономию материала от выбранного варианта изготовления заготовки
Э = (1,16– 0,87) × 10000 = 2900 кг
4) Определяем экономический эффект по стоимости изготовления заготовки
Э = (159,60 – 60,29) × 10000 = 993100 руб.
Таблица 3 – Наиболее выгодный способ получения заготовки
Показатели | Вид заготовки | |
прокат | штамповка | |
1. Масса детали, кг | 0,52 | |
2. Масса заготовки, кг | 1,16 | 0,87 |
3. Коэффициент использования материала | 0,44 | 0,6 |
4. Стоимость заготовки, руб. | 60,29 | 159,60 |
5. Экономический эффект от материала заготовки, кг | 2900 | |
6. Экономический эффект от стоимости, руб. | 993100 | |
7. Наиболее выгодный способ получения заготовки | + |
3.4Маршрут обработки детали
Таблица 4– Маршрут обработки детали
№ операции | Наименование и содержание операции | Модель станка | Режущий инструмент | Приспособле ние |
1 | 2 | 3 | 4 | 5 |
005 | Отрезная | 8Г662 | ||
1. Установить и закрепить заготовку | Зажим при станке | |||
2.Отрезать заготовку в размер L=370-1,0 на 5 деталей | Пила 2254-1341 ГОСТ 2679-73 | |||
010 | Токарно-винторезная с ЧПУ | 16К20Ф3С32 | ||
1.Установить деталь, закрепить | Патрон 7100-0005 ГОСТ 2675-80 | |||
2. Подрезать торец «как чисто», точить поверхность до Ø 41,8 в размер 33-0,62, точить фаску 2х450, точить фаску 30°, обеспечивая Ø 41-0,62 по программе | Резец 2100-0563 ГОСТ 18869-73 | |||
3.Сверлить отверстие Ø15+0,43 в размер 76 | Сверло 2301-0050 ГОСТ10903 -77 | Втулка 6101-0028 ГОСТ 13793-68 |
Продолжение таблицы 4
№ операции | Наименование и содержание операции | Модель станка | Режущий инструмент | Приспособление |
010 | 4.Рассверлить отверстие до Ø21+0,52 в размер 74 |
| Сверло 2301-0073 ГОСТ10903 -77 | Втулка 6101-0028 ГОСТ 13793-68 |
5. Расточить конус с Ø21+0,52 до Ø 32Н13(+0,39) | Резец 2141-0004 ГОСТ18873-73 | |||
6. Точить канавку до Ø 34-0,62 в размер 33-0,62, образуя R1,6 | 16К20Ф3С32 | Резец 2130-0009 Т14К8 ГОСТ18884-73 | ||
5. Нарезать резьбу М42х2-6g в размер 15-0,43 | Резец 2664-0009 6 Т15К6 ГОСТ 18885-73 | |||
7. Отрезать деталь в размер 68-0,74 | Резец 2130-0009 Т14К8 ГОСТ18884-73 | |||
015 | Токарно-винторезная с ЧПУ | 16К20Ф3С32 | ||
1.Установить деталь, закрепить | Патрон 7100-0005 ГОСТ 2675-80 | |||
2. Подрезать торец в размер 24±0,2, точить поверхность под резьбу до Ǿ29,8-0,13, в размер 23±0,5 с подрезкой торца, точить фаску 2*45°, точить фаску 30° обеспечивая Ø 41-0,62 | Резец 2102-0055 Т15К6 ГОСТ 18877-73 | |||
3.Точить канавку, выдерживая b=5-0,3 и Ǿ27-0,52 | Резец канавочный специальный | |||
4. Нарезать резьбу М30х2- 6g в размер 19±0,26 | Резец 2664-0009 6 Т15К6 ГОСТ 18885-73 | |||
020 | Горизонтально-фрезерная | 6Р83Г | ||
1. Установить делительный стол с патроном на стол станка | Головка делительная 7036-0051 ГОСТ 8615-89 | |||
2. Установить деталь с оправкой в патрон и закрепить | Патрон 7100-0003 ГОСТ2675-80 Втулка резьбовая цеховая | |||
3. Установить набор фрез на размер 41h13(-0,39) | Оправка 6225-0181 ГОСТ 15068-75 |
Продолжение таблицы 4
№ операции | Наименование и содержание операции | Модель станка | Режущий инструмент | Приспособление |
020 | 4. Фрезеровать поверхности в размер 41h13(-0,39) одновременно | 6Р83Г | Фреза 2241-0010Т15К6 ГОСТ 5348-69 | |
5. Повернуть деталь на 60 °. Повторить переход 4 два раза | ||||
025 | Контрольная | ОТК | ||
1. Проверить размеры согласно чертежа. | Плита 2-2-1600х1000 ГОСТ10905-86 |
3.5 Программа обработки детали на операцию с ЧПУ
O; PROGRAMMA
T-"Проходной отогнутый резец"
G97 S630 M03 M08 F0.5
G00 X45 Z0
G01 X20
G00 X38.5 Z5
G71 U2.5 R1
G71 P10 Q20 F0.5
N10
G01 X27 Z0
X30 Z-2
Z-24
X39
A120 X41
N20
G00 X150 Z150
M05 M09
M1
T-"Канавочный резец"
G97 S630 M03 M08 F0.09
G00 X45 Z-24
X41
G01 X27
G00 X45
Z-22.5
X30
G01 X27 Z-24
G00 X150
Z150
M05 M09
M1
T-"Резьбовой резец"
G97 S500 M03 M08 F2
G00 X29 Z5
G31 Z-24 F2
G00 X32
Z5
X28
G31 Z-24 F2
G00 X32
X150 Z150
M05 M09
M30
Дата добавления: 2020-04-08; просмотров: 145; Мы поможем в написании вашей работы! |
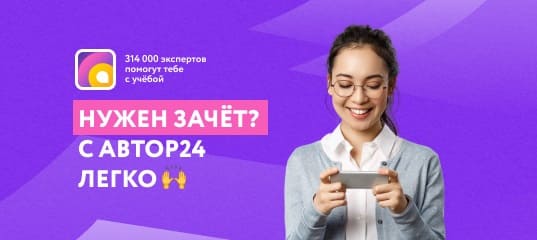
Мы поможем в написании ваших работ!