Определение отбраковочных толщин сосудов, работающих под давлением ниже 0,07 МПа и вакуумом
Министерство образования и науки Российской Федерации
Федеральное государственное бюджетное образовательное учреждение
высшего профессионального образования
«УФИМСКИЙ ГОСУДАРСТВЕННЫЙ НЕФТЯНОЙ
ТЕХНИЧЕСКИЙ УНИВЕРСИТЕТ»
Кафедра технологических машин и оборудования
Отбраковка элементов сосудов, работающих под давлением ниже 0,07 МПа и вакуумом, определение скорости коррозии основных конструктивных элементов сосуда, работающего под давлением ниже 0,07 МПа и вакуумом и периодичности технического освидетельствования
Учебно-методическое пособие
к выполнению практической работы по дисциплине
«Техническое освидетельствование технологического оборудования»
Уфа 2015
Учебно-методическое пособие предназначено для студентов очной и заочной форм обучения направлений подготовки 151000, 15.03.02 «Технологические машины и оборудование» профиля «Оборудование нефтегазопереработки».
Составители: Рубцов А.В., доцент, канд. техн. наук
Закирничная М.М., докт. техн. наук, профессор
Ковшова Ю.С., канд. техн. наук
Рецензенты: Габбасова А.Х., канд. техн. наук, доцент каф. ТМО
Хасбутдинова Е.В., канд. техн. наук, доцент каф. ТМО
© Уфимский государственный нефтяной технический университет, 2015
Содержание
С | |
Введение | 4 |
Практическая работа. Отбраковка элементов сосудов, работающих под давлением ниже 0,07 МПа и вакуумом, определение скорости коррозии основных конструктивных элементов сосуда, работающего под давлением ниже 0,07 МПа и вакуумом и периодичности технического освидетельствования | 5 |
Пример выполнения задания | 12 |
Контрольные вопросы | 18 |
Перечень вариантов к практической работе | 19 |
Список использованных источников | 19 |
Приложение А. Допускаемые напряжения для материала элемента аппарата при расчетной температуре | 21 |
Приложение Б. Требования к оформлению отчета о практической работе | 23 |
Приложение В. Пример оформления титульного листа отчета о практической работе | 24 |
ВВЕДЕНИЕ
|
|
На предприятиях нефтегазопереработки и нефтехимии эксплуатируется большое количество сосудов и аппаратов, работающих под давлением ниже 0,07 МПа и вакуумом, которые участвуют в различных технологических процессах. В процессе эксплуатации сосуды и аппараты подвергаются воздействию эксплуатационных нагрузок и рабочих сред. Это приводит к развитию различных дефектов, которые снижают эксплуатационную безопасность оборудования и могут привести к возникновению аварийных ситуаций.
|
|
Основным мероприятием по обеспечению безопасной и надежной эксплуатации сосудов и аппаратов являются периодическое техническое освидетельствование и своевременная отбраковка дефектных элементов.
Целью данного учебно-методического пособия является приобретение навыков студентами по определению отбраковочных толщин основных конструктивных элементов сосудов и аппаратов, работающих под давлением ниже 0,07 МПа и вакуумом, а также определению периодичности их технического освидетельствования по скорости коррозионного износа основных конструктивных элементов.
Практическая работа. Отбраковка элементов сосудов, работающих под давлением ниже 0,07 МПа и вакуумом, определение скорости коррозии основных конструктивных элементов сосуда, работающего под давлением ниже 0,07 МПа и вакуумом и периодичности технического освидетельствования
Цель работы:
1. Определение отбраковочных толщин основных конструктивных элементов сосудов (аппаратов) работающих под давлением ниже 0,07 МПа и вакуумом;
2. Определение периодичности технического освидетельствования сосудов давления, исходя из максимальной скорости коррозии основных элементов сосуда (аппарата).
ОБЩИЕ ПОЛОЖЕНИЯ
|
|
Определение отбраковочных толщин сосудов, работающих под давлением ниже 0,07 МПа и вакуумом
Отбраковка элементов сосудов (аппаратов) работающих под давлением ниже 0,07 МПа и вакуумом производится согласно РУА-93 «Руководящие указания по эксплуатации и ремонту сосудов и аппаратов, работающих под давлением ниже 0,07 МПа (0,7 кгс/см2) и вакуумом».
Элементы сосудов и аппаратов (в том числе и литых), определяющие их прочность, должны отбраковываться если при толщинометрии выявится, что под действием коррозии и эрозии уменьшилась толщина металла стенки (обечаек корпуса, днищ, крышек, заглушек, штуцеров и др.) до значений, определенных расчетами по действующим методикам (ГОСТ Р 52857.1¸12-2007. и др.) или по паспорту, с учетом всех действующих нагрузок (внутреннего или наружного давления, весовых, ветровых, сейсмических, температурных и пр.) без учета прибавки на коррозию (отбраковочный размер);
Если расчетная толщина стенки (без учета прибавки на коррозию) оказалась меньше величины, указанной ниже, то за отбраковочный размер принимается величина:
- для обечаек и днищ сосудов и аппаратов при диаметре 2000 мм и ниже - 3 мм, а при диаметре более 2000 мм - 4 мм;
- для патрубков - в соответствии с таблицей 1.
|
|
Таблица 1 - Минимальный отбраковочный размер для толщины стенки патрубка
Наружный диаметр, мм | £ 25 | £ 57 | £ 108(114) | £ 219 | ³ 325 |
Наименьшая допустимая толщина стенки, мм | 1,0 | 1,5 | 2,0 | 2,5 | 3,0 |
Расчетные толщины стенок элементов сосудов, работающих под давлением ниже 0,07 МПа и вакуумом, определяются по ГОСТ Р 52857.1-2007 «Сосуды и аппараты. Нормы и методы расчета на прочность. Общие требования.», ГОСТ Р 52857.2-2007 «Сосуды и аппараты. Нормы и методы расчета на прочность. Расчет цилиндрических и конических обечаек, выпуклых и плоских днищ и крышек», ГОСТ Р 52857.3-2007. «Сосуды и аппараты. Нормы и методы расчета на прочность. Укрепление отверстий в обечайках и днищах при внутреннем и внешнем давлениях. Расчет на прочность обечаек и днищ при внешних статических нагрузках на штуцер».
Для цилиндрических обечаек расчетная толщина стенки определяется по формуле (1):
, (1)
где p – расчетное внутреннее избыточное давление, МПа;
D – внутренний диаметр, мм;
[s] – допускаемое напряжение для материала, из которого изготовлен элемент, МПа. Выбирается в зависимости от материала и расчетной температуры из приложения А;
j - коэффициент сварного шва, который выбирается по таблице 2.
Таблица 2 - Коэффициенты прочности сварных швов
Вид сварного шва | Значение коэффициентов прочности сварных швов | |
Длина контролируемых швов от общей длины составляет 100 % | Длина контролируемых швов от общей длины составляет от 10 до 50 % | |
Стыковой или тавровый с двусторонним сплошным проваром, выполняемый автоматической и полуавтоматической сваркой | 1,0 | 0,9 |
Стыковой с подваркой корня шва или тавровый с двусторонним сплошным проваром, выполняемый вручную | 1,0 | 0,9 |
Стыковой, доступный сварке только с одной стороны и имеющий в процессе сварки металлическую подкладку со стороны корня шва, прилегающую по всей длине шва к основному металлу | 0,9 | 0,8 |
Втавр, с конструктивным зазором свариваемых деталей | 0,8 | 0,65 |
Стыковой, выполняемый автоматической и полуавтоматической сваркой с одной стороны с флюсовой или керамической подкладкой | 0,9 | 0,8 |
Стыковой, выполняемый вручную с одной стороны | 0,9 | 0,65 |
Для эллиптических и полусферических днищ расчетная толщина стенки определяется по формуле (2):
, (2)
где R - радиус кривизны в вершине днища, который равен:
R = D - для эллиптических днищ с Н = 0,25 D;
R = 0,5 D - для полусферических днищ с Н = 0,5 D.
Для плоских днищ расчетная толщина стенки определяется по формуле (3):
, (3)
где К- коэффициент, который в зависимости от конструкции днищ и крышек определяют по таблице 4 ГОСТ Р 52857.2-2007 «Сосуды и аппараты. Нормы и методы расчета на прочность. Расчет цилиндрических и конических обечаек, выпуклых и плоских днищ и крышек» (в данной работе принимаем К=0,53).
К0 – коэффициент, который равен 1 для днищ (крышек) без отверстий; для днищ и крышек, имеющих одно отверстие коэффициент К0 определяется по формуле (4):
, (4)
где dp – диаметр отверстия в днище или крышке;
Dр – расчетный диаметр днища (крышки), мм
В рассматриваемых вариантах Dр=D, где D – внутренний диаметр сосуда, мм.
Для штуцеров расчетная толщина стенки определяется по формуле (5):
, (5)
где p – расчетное внутреннее избыточное давление, МПа;
d – внутренний диаметр штуцера, мм;
cs – прибавка на коррозию к расчетной толщине стенки штуцера, мм. Зависит от коррозионности среды. В работе принимаем cs=1;
[s]1 – допускаемое напряжение для материала, из которого изготовлен штуцер, МПа. Выбирается в зависимости от материала и расчетной температуры из приложения А;
j1 - коэффициент сварного шва. Если ось сварного шва обечайки (днища) удалена от наружной поверхности штуцера на расстояние более чем три толщины укрепляемого элемента (3s, рисунок 1б), то коэффициент прочности этого сварного соединения при расчете укрепления отверстий следует принимать j1 = 1. В исключительных случаях, когда сварной шов пересекает отверстие или удален от наружной поверхности штуцера на расстояние менее 3s, принимают j1 £ 1в зависимости от вида и качества сварного шва.
Если плоскость, проходящая через продольный шов вальцованного штуцера и ось этого штуцера, образует угол не менее 600 с плоскостью продольного осевого сечения цилиндрической или конической обечайки (рисунок 2), то принимают j1 = 1. В остальных случаях j1 £ 1 в зависимости от вида и качества сварного шва.
Рисунок 1
Рисунок 2
Определение периодичности технического освидетельствования работающих под давлением ниже 0,07 МПа и вакуумом, исходя из максимальной скорости коррозии основных элементов сосуда (аппарата)
Для определения периодичности технического освидетельствования сосудов (аппаратов) необходимо знать скорость равномерной коррозии
Скорость равномерной коррозии а определяется по формуле (6):
, (6)
где SИ – исполнительная (проектная) толщина стенки элемента, мм;
SФ – минимальная измеренная толщина стенки элемента, мм;
- плюсовой допуск на толщину стенки, мм;
t1 - время от момента начала эксплуатации до момента обследования, лет.
Проведение периодических технических освидетельствований сосудов (аппаратов), как правило, приурочивается к планово-предупредительным ремонтам отдельных агрегатов и установок. При этом периодичность технических освидетельствований сосудов (аппаратов) не должна выходить за пределы, установленные таблицей 3.
Таблица 3- Периодичность технического освидетельствования сосудов и аппаратов, эксплуатирующихся по РУА-93
Назначение сосудов | Наружный и внутренний осмотр не реже одного раза в | Гидравлическое испытание пробным давлением не реже одного раза в |
Сосуды (аппараты) группы 5а, работающие со средой, вызывающей коррозию металла корпуса со скоростью: | ||
- не более 0,1 мм/год | 6 лет | 12 лет |
- более 0,1 мм/год до 0,3 мм/год | 2 года | 8 лет |
- более 0,3 мм/год | 1 год | 8 лет |
Сосуды (аппараты) группы 5б, работающие со средой, вызывающей коррозию металла корпуса со скоростью: | ||
- не более 0,1 мм/год | 12 лет | 12 лет |
- более 0,1 мм/год до 0,3 мм/год | 4 года | 8 лет |
- более 0,3 мм/год | 2 года | 8 лет |
Пример выполнения задания
Определение отбраковочных толщин сосудов, работающих под давлением ниже 0,07 МПа и вакуумом
Необходимо назначить отбраковочные толщины основных конструктивных элементов емкости. Необходимые исходные данные берутся из акта изучения и анализа технической документации, выдаваемого преподавателем.
Данные, которые необходимы для выполнения задания:
Срок ввода в эксплуатацию 1959 год
Расчетные параметры
Расчетное давление - 0,25 МПа
Расчетная температура - 200 0С
Внутренний диаметр
Цилиндрическая обечайка – 1000 мм
Эллиптические днища – 1000 мм
Исполнительная толщина стенки:
Цилиндрическая обечайка – 8 мм
Эллиптические днища – 8 мм
Материал, из которого изготовлен элемент:
Цилиндрическая обечайка – Ст3сп по ГОСТ 380
Эллиптические днища – Ст3сп по ГОСТ 380
Сведения о штуцерах.
Обозначение | Назначение | Ду, мм | Патрубок | ||
толщина, мм | Материал | ||||
Марка | ГОСТ | ||||
А | Вход продукта | 80 | 4,5 | сталь 10 | 1050 |
Б | Выход продукта | 40 | 3,5 | сталь 10 | 1050 |
В | Для уровнемера | 50 | 3,5 | сталь 10 | 1050 |
Г | Люк лаз | 500 | 8,0 | Ст3 | 380 |
Д | Подача ингаза | 40 | 3,5 | сталь 10 | 1050 |
Группа сосуда – 5б
Сведения о сварке:
- ручная электродуговая сварка (обечайка) электродами Э 42 ГОСТ 2523-51.
Объем контроля при изготовлении, эксплуатации и проведении экспертизы промышленной безопасности:
25 %.
Эскиз емкости приведён на рисунке А.1.
Рисунок А.1 – Эскиз емкости
По формуле (1) определим расчетные толщины стенок для цилиндрической обечайки корпуса:
По формуле (2) определим расчетные толщины стенок для эллиптических днищ:
Так как диаметр емкости равен 1000 мм, что меньше 2000 мм и расчетные толщины стенок цилиндрической обечайки и днищ получились меньше 3 мм, то за отбраковочный размер этих конструктивных элементов согласно РУА-93 принимаем толщину равную 3 мм.
Теперь по формуле (5) определяем расчетные толщины патрубков штуцеров:
Для штуцера А:
Для штуцера Б:
Для штуцера В:
Для штуцера Г:
Для штуцера Д:
Так как расчетные толщины штуцеров получились меньше указанных в таблице 4, то принимаем отбраковочные толщины для:
штуцера А Ду80– 2,0 мм;
штуцеров Б, Д Ду40– 1,5 мм;
штуцера В Ду50 – 1,5 мм;
штуцера Г Ду500 – 3,0 мм.
Определение периодичности технического освидетельствования работающих под давлением ниже 0,07 МПа и вакуумом, исходя из максимальной скорости коррозии основных элементов сосуда (аппарата).
Для емкости рассмотренной выше необходимо определить скорость коррозии для каждого конструктивного элемента и по максимальному значению определить периодичность освидетельствования.
Данные, которые необходимы для выполнения задания:
Приводятся результаты толщинометрии основных конструктивных элементов емкости, а также на рисунке А.2 схема обследования с указанием мест точек замеров. Номера точек в таблице с замерами, соответствуют номерам точек на рисунке А.2.
Определение периодичности технического освидетельствования работающих под давлением ниже 0,07 МПа и вакуумом, исходя из максимальной скорости коррозии основных элементов сосуда (аппарата).
Для емкости рассмотренной выше необходимо определить скорость коррозии для каждого конструктивного элемента и по максимальному значению определить периодичность освидетельствования.
Данные, которые необходимы для выполнения задания:
Приводятся результаты толщинометрии основных конструктивных элементов емкости, а также на рисунке А.2 схема обследования с указанием мест точек замеров. Номера точек в таблице с замерами, соответствуют номерам точек на рисунке А.2.
Дата добавления: 2020-01-07; просмотров: 1999; Мы поможем в написании вашей работы! |
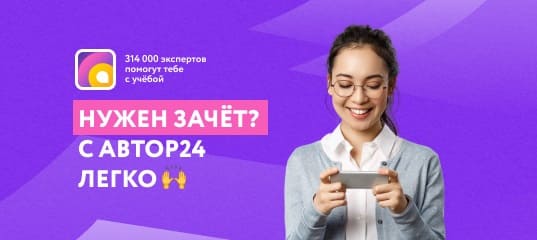
Мы поможем в написании ваших работ!