Классификация промышленных титановых сплавов
Титановые сплавы маркируют буквами и числами. Буквы («ВТ», «ОТ», «АТ», «ПТ») условно обозначают организацию, в которой разрабатывались сплавы, числа - порядковый номер сплава. Примеры марок титановых сплавов: ВТ6, ВТ14, ОТ4, АТ3 и т.п.
Сплавы классифицируют по различным признакам:
– по способу получения: деформируемые и литейные;
– по назначению: конструкционные общего назначения, жаропрочные, криогенного назначения, коррозионностойкие;
– по уровню прочности: низкопрочные (до 500 МПа), средней прочности (500 – 1000 МПа), высокопрочные (более 1000 МПа);
– по фазовому составу после термообработки (после отжига, после закалки).
Деформируемые сплавы
Одним из признаков, по которому деформируемые титановые сплавы разделяют на несколько классов, является фазовый состав после отжига:
1. α - сплавы, состоящие из твёрдого раствора на основе α - Ti (ГП).
2. Псевдо-α-сплавы, которые состоят из α-фазы и небольшого количества β – фазы (ОЦК) (не более 5 %).
3. (α+β) – сплавы.
4. Псевдо - β - сплавы (α - фазы не более 5 %) .
5. β - сплавы.
Последние два класса сплавов имеют ограниченное применение.
Класс сплава или его фазовый состав после отжига, определяется, прежде всего, легированием (табл. 3.11). В свою очередь фазовый состав влияет на механические и технологические свойства сплавов, определяет их способность к упрочняющей термической обработке.
Однофазные α - сплавы применяют и как жаропрочные, и как сплавы криогенного назначения. Они имеют следующие свойства: значительно упрочняются при холодной пластической деформации; не упрочняются при термообработке; поэтому имеют средний уровень прочности; удовлетворительно свариваются; склонны к водородной хрупкости.
|
|
Самый распространенный сплав этого класса – сплав марки ВТ5-1(Ti– 5Al – 2,5Sn) (табл. 3.11) после отжига имеет σв = 800 – 1000 МПа, удовлетворительный предел выносливости. Сплав жаропрочен до 450ºС, и в то же время сплав считается наилучшим для применения при криогенных температурах вплоть до температуры жидкого водорода.
Таблица 3.11
Химические составы и свойства после отжига титановых
Деформируемых сплавов
Класс сплав | Марка | Содержание легирующих элементов, (среднее), % | σв ,МПа (среднее) | δ, % |
α - сплавы | ВТ5 | 5Al–2,5Sn | 900 | 8 |
Псевдо - α - cплавы | ОТ4 | 5,3Al–1,4Mn | 550 | 15 |
АТ2 | 4,2Al–1,0V–0,9Mo–1,4Mn | 800 | 12…20 | |
ВТ18У | 6,5Al–0,7Mo–4Zr–2,5Sn–1Nb–0,2Si | 1050 | 10 | |
(α + β) - сплавы | BT6 | 6,1Al–4V | 1000 | 8 |
BT9 | 6,4Al–3,3Mo–1,5Zr–0,2Si | 1125 | 7 | |
BT16 | 2,8Al–4,5V–5Mo | 900 | 14 | |
BT22 | 5Al – 4,7V – 4,7Mo – 1,2Cr – 1Fe | 1170 | 8 |
Псевдо α - сплавы (1 – 5 % β - фазы) могут применяться как сплавы общего назначения, криогенные; жаропрочные, а также как сплавы повышенной технологической пластичности.
|
|
Сплавы имеют следующие свойства: высокую технологическую пластичность; способность к упрочнению при термообработке (отжиг); хорошую свариваемость всеми видами сварки; склонность к водородной хрупкости.
Сплавы системы Ti – Al - Mn (ОТ4, ОТ4-1 и др.) высокотехнологичны в холодном и горячем состояниях. Из них получают листы, ленты, полосы, трубы, а также плиты, поковки, прутки и штамповки. Применяются как сплавы общего назначения.
К псевдо α - сплавам относится и самый жаропрочный титановый сплав – ВТ18(Ti – 6,7Al – 3,2Mo – 1Nb – 4Zr – 2,5Sn – 0,2Si). Высокую жаропрочность, до температуры 600ºС, обеспечивает как присутствие тугоплавких элементов, молибдена и ниобия, так и незначительное содержание β - фазы (которая нестабильна при повышенных температурах). Детали из сплава ВТ-18 применяются в компрессорах авиационных двигателей.
Сплавы α+β имеют наилучшее сочетание механических и технологических свойств: хорошо деформируются в горячем состоянии вследствие присутствия β-фазы; упрочняются при термической обработке; относятся к высокопрочным сплавам; отличаются пониженной склонностью к водородной хрупкости.
|
|
Возможность варьирования механических свойств в широких пределах обуславливает применение сплавов этого класса как материалов разнообразного назначения (табл.3.12).
Таблица 3.12
Применение и свойства титановых деформируемых сплавов
Группы сплавов по основному свойству | Класс | ||
α -сплавы | Псевдо - α - сплавы | (α + β) - сплавы | |
Сплавы криогенного назначения | ВТ5-1 | АТ2, АТ2-1 | ВТ-6 |
Высокопрочные | - | - | ВТ16 (σв до 1250 МПа) ВТ6 (σв до 1150 МПа) ВТ22 (σв до 1350 МПа) |
Высокотехнологичные | - | ОТ4-0, ОТ4-1 | ВТ16, ВТ23 |
Жаропрочные (предельные рабочие температуры) | ВТ5-1 | ВТ20 (до 450 - 500ºС) ВТ18 (до 600ºС) | ВТ14 (до 400ºС) ВТ3-1 (400 - 450ºС) ВТ8 (450 - 500ºС) ВТ9 (до 500ºС) |
Наиболее распространённым сплавом этого класса является сплав марки ВТ6 (Ti–6Al–V): около 50 % титановых сплавов, используемых в авиакосмической промышленности в России и за рубежом, составляют сплавы – аналоги ВТ6. Из них получают трубы, прутки, поковки, штамповки, плиты, листы, предназначенные для изготовления силовых деталей и конструкций в самолетостроении. Многие из α + β - сплавов применяются как жаропрочные в компрессорах авиационных двигателей.
|
|
Литейные сплавы
Титановые сплавы имеют хорошие литейные свойства вследствие узкого интервала кристаллизации: низкая линейная усадка (менее 1 %), высокая жидкотекучесть, плотность отливок. Трудности при литье заключаются во взаимодействии сплавов со всеми известными формовочными материалами, а также с газами. В связи с этим их отливают вакууме или в нейтральном газе (аргоне).
Для фасонного литья применяют титан и его сплавы, которые по составу почти не отличаются от деформируемых аналогов: ВТ5Л, ВТ14Л, ВТ6Л и др. (буква «Л» означает – литейный сплав).
Наиболее широко используют α - сплав ВТ5Л. Отливки этого сплава имеют удовлетворительные пластичность, ударную вязкость, предел выносливости. Он предназначен для длительной работы при температуре до 400ºС.
Сплав ВТ9Л, как его деформируемый полуфабрикат ВТ9, применяется как жаропрочный, при этом рабочая температура для литых деталей выше, чем для деформируемых и составляет 550ºС.
Магниевые сплавы
Магний – щелочноземельный металл светло-серого цвета, второй группы периодической системы Д.И.Менделеева. Среди промышленных металлов он обладает наименьшей плотностью (1,74 Мг/м3) и в 1,5 раза легче алюминия. Магний имеет гексагональную кристаллическую решетку и плавится при температуре 651ºС. Магний имеет низкий модуль упругости Е= 45 ГПа и обладает невысокой прочностью и пластичностью: σв≈ 100 МПа, δ ≈ 7 % в литом состоянии и σв≈ 180 МПа, δ ≈ 15 % после деформации и отжига.
Чистый магний относится к металлам с высокой химической активностью и легко окисляется. Оксидная пленка MgO сохраняет защитные свойства лишь до 450ºС, при дальнейшем повышении температуры скорость окисления быстро возрастает, а при 623ºС магний воспламеняется на воздухе. Влажная магниевая пыль может воспламеняться при 360ºС.
Вследствие низких значений механических свойств технический магний как конструкционный материал не применяется, в технике используют магниевые сплавы.
Свойства магния значительно улучшаются при легировании. Достоинствами магниевых сплавов являются: низкая плотность; высокая удельная прочность; высокая демпфирующая способность; хорошая обрабатываемость резанием.
К основным недостаткам магниевых сплавов относятся: низкий модуль упругости Е = 45 ГПа; невысокая коррозионная стойкость; технологические трудности при литье, связанные с активностью магния; необходимость нагрева при обработке давлением.
Основными легирующими элементами в магниевых сплавах являются:
– алюминий и цинк, вызывающие твердорастворное упрочнение;
– марганец, способствующий повышению коррозионной стойкости;
– цирконий и церий, оказывающие эффективное модифицирующее действие на структуру;
– неодим и торий, повышающие жаропрочность;
– литий, значительно уменьшающий плотность.
Растворимость легирующих элементов в магниевых сплавах уменьшается при понижении температуры, что позволяет применять упрочняющую термическую обработку, состоящую из закалки с последующим старением. Низкая скорость диффузии легирующих элементов в магниевом твердом растворе облегчает фиксацию пересыщенного твердого раствора и затрудняет его распад при старении, поэтому закалку обычно проводят на воздухе и применяют только искусственное старение при сравнительно высоких температурах (до 200 – 250ºС) и более длительных выдержках (16 - 24 ч).
Прочностные свойства магниевых сплавов существенно повышаются при термомеханической обработке, состоящей в пластической деформации закаленного сплава перед старением.
По способу производства полуфабрикатов и изделий магниевые сплавы разделяют на деформируемые и литейные, которые соответственно маркируют буквами МА и МЛ с указанием условного номера сплава. Деформируемые магниевые сплавы по химическому и фазовому составу совпадают с литейными, но отличаются меньшими допусками по содержанию примесей. Магниевые сплавы принадлежат следующим основным системам легирования: Mg – Al – Zn - Mn; Mg – Zn - Zr; Mg - Nd - Zr, Mg - Li.
Магниевые сплавы широко применяются в авиастроении, автомобильной промышленности, ракетной технике, приборостроении. Из них изготавливают корпуса приборов, ракет, обтекателей, топливных баков, картеры, коробки передач, маслопомпы, диски колес и т.д.
Сплавы системы Mg – Al – Zn - Mn. Наиболее распространенным деформируемым сплавом является высокотехнологичный МА2-1, отличающийся высокой пластичностью, хорошей свариваемостью, высокой коррозионной стойкостью. Детали простой формы можно штамповать даже в холодном состоянии. Сплав не упрочняются термической обработкой и поставляется в отожженном, полунагартованном или горячекатаном состоянии.
К наиболее распространенным литейным сплавам данной системы легирования относятся MЛ5, МЛ6, обладающие хорошей жидкотекучестью, малой линейной усадкой, что позволяет изготавливать из них сложные ответственные отливки.
Сплавы системы Mg – Zn - Zr . Высокопрочные сплавы МА14, МА19 менее технологичны, чем деформируемые сплавы первой группы: деформируются в горячем состоянии, и если сплав МА 19 можно сваривать только контактной сваркой, то сплав МА14 не используется в сварных конструкциях. После упрочняющей термической обработки сплавы МА14 и МА19 имеют значения временного сопротивления 350 и 400 МПа соответственно.
Наилучшим литейным сплавом данной системы легирования является МЛ12, отличающийся высокой прочностью (σв = 230 МПа), коррозионной стойкостью, хорошими литейными свойствами.
Сплавы системы Mg - Nd - Zr относятся к группе жаропрочных за счет легирования неодимом. Неодим образует упрочняющую фазу Mg9Nd, не склонную к коагуляции при температуре эксплуатации. Сплавы МА12, МЛ9, МЛ19 имеют рабочие температуры соответственно до 200, 250 и 300ºС.
Сплавы системы Mg - Li . Сплавы МА18, МА21называют сверхлегкими: их плотность составляет 1,3-1,6 Мг/м3. Присутствие лития обеспечивает также высокую удельную жесткость сплавов, по значениям которой они превосходят даже сталь и титан. Магний-литиевые сплавы высокотехнологичны, потому что в отличие от всех других магниевых сплавов, в их структуре присутствует β – твердый раствор на основе лития с ОЦК решеткой. Листовая штамповка, гибка, вытяжка сплава М18 могут производиться в холодном состоянии. Эти сплавы хорошо свариваются и имеют удовлетворительную коррозионную стойкость.
3.5.Антифрикционные (подшипниковые) сплавы на оловянной, свинцовой и цинковой основах
![]() | Антифрикционные материалы применяют для изготовления вкладышей подшипников скольжения. Вкладыши изготавливают в виде втулок или делают разъемными (в разъемных подшипниках) (рис.3.12). Основным требованием по эксплуатационным свойствам к материалам для подшипников является – антифрикционность, т.е. способность материала обеспечивать низкий коэффициент трения (низкие потери на трение) и, следовательно, малую скорость изнашивания сопряженных деталей, а также - скольжение без заедания при любых нагрузках и скоростях. |
Критериями оценки антифрикционных материалов являются:
1. Коэффициент трения f.
2. Допустимые нагрузочно-скоростные характеристики: давление на опору p и скорость скольжения U (обозначения по ГОСТ 79034-2001).
Параметр pU (МПа м/сек) называется удельной мощностью трения. С физической точки зрения удельная мощность трения тем выше, чем выше способность материала: к снижению температуры нагрева за счет высокой теплопроводности и к снижению нагрузки в зоне контакта, при сохранении граничной смазки.
Свойства сплавов для подшипников скольжения зависят от комплекса физических, химических и механических свойств (табл. 3.13).
Таблица 3.13
Дата добавления: 2020-01-07; просмотров: 971; Мы поможем в написании вашей работы! |
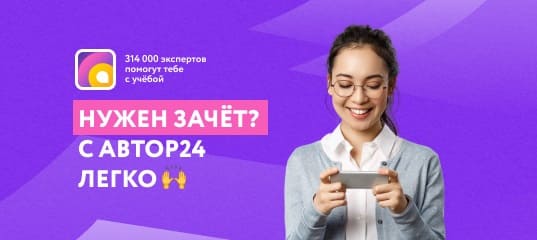
Мы поможем в написании ваших работ!