Характеристики физических свойств.
Характеристики физических свойств измеряют при испытаниях, при которых образцы исключается приложение силы и образцы не испытывают необратимой деформации и не разрушаются.
Модуль нормальной упругости - Е (ГПа) характеризует жёсткость материала: чем выше Е, тем жёстче материал и меньше упругая деформация, получаемая при одном и том же напряжении. Модуль сдвига – модуль упругости при деформации сдвигом.
Плотность – ρ(т/м3, Мг/м³) используетсядля оценки веса деталей и конструкций. Материалы и с пониженной плотностью пригодны для применения в движущихся конструкциях (авиастроение, ракетостроение, скоростной автомобильный транспорт).
Теплопроводность – λ (вт/(м·град) используют для оценки работоспособности материала в условиях резких теплосмен, а также при создании сварных конструкций.
Коэффициент термического линейного расширения – α (1/град)необходим для оценки величины зазоров между деталями в конструкциях.
Характеристики химических свойств.
Химические свойства характеризуют способность материала к взаимодействию с внешней средой. Скорость коррозии – Vкор (мм/год, г/м2час) – оценивает потери материала в результате коррозионных процессов на поверхности
Характеристики технологических свойств.
Технологические свойства представляют комплекс свойств, определяющих возможность проведения технологического процесса изготовления изделий, например, их способность к деформированию, к сварке, к обработке резанием, к получению плотных бездефектных отливок.
|
|
Ковкость – способность материала деформироваться и принимать необходимые форму и размеры под воздействием внешней нагрузки.
Свариваемость – способность материала образовывать качественные неразъёмные соединения с требуемыми свойствами.
Обрабатываемость резанием – способность при точении резцом образовывать мелкую стружку и обеспечивать низкую шероховатость поверхности.
Хорошие литейные свойства – жидкотекучесть, плотные отливки.
Эти испытания дают только первичную информацию о возможностях материала. Для пригодности материала к конкретным условиям эксплуатации необходимо изучить и эксплуатационные характеристики, в том числе характеристики конструкционной прочности.
К способам управления строением и свойствами металлов и сплавов относятся: выбор химического состава; кристаллизация; пластическая деформация; термическая обработка; термомеханическая обработка; обработка поверхности: химико-термическая обработка, обработка лазером, поверхностное пластическое деформирование и другие.
Пластическая деформация
|
|
Пластическая деформация (или пластическое деформирование) – технологическая операция,в процессе которой изменяются размеры и форма материала без изменения его массы («технологическая» формулировка).
Пластическая деформация – это результатданной технологической операции – остаточная деформация, полученная материалом (формулировка «сопротивления материалов»).
Пластическая деформация – процесс изменения структуры металла или сплава, происходящий во время данного технологического цикла («материаловедческая» формулировка).
Пластическое деформирование используется как способ изменения размеров и формы деталей; способ упрочнения материала; способ получения определенного структурного состояния в металлах и сплавах с особыми физическими свойствами.
Пластической деформации подвергают 80 % литых металлов и сплавов (слитки, заготовки, полученные непрерывной разливкой); гранулированные и порошковые материалы; аморфные материалы; полимерные материалы.
Пластическую деформацию подразделяют на несколько видов в соответствии с различными признаками.
В зависимости от объема, в котором сохраняется остаточная деформация, различают процессы объемной и поверхностной деформации.
|
|
Объемная обработка давлением, при которой деформируется все сечение полуфабриката, применяется для получения заготовок или изделий и включает такие технологические операции как прокатка, волочение, штамповка, прессование, ковка и др.
Поверхностное пластическое деформирование (ППД), при котором деформируется поверхностный слой глубиной до 0,5 – 1 мм, применяется для упрочнения поверхности готовых деталей, в качестве финишной операции, и включает дробеструйный наклеп, обдувку дробью, алмазное выглаживание и др.
В зависимости от температуры различают процессы холодной и горячей деформации.
Способность материала к пластической деформацииопределяется совокупностью физико - механических свойств, главным из которых является пластичность.
Различают технологическую пластичность и пластичность.
Технологическая пластичность проявляется во время деформации. Для оценки технологической пластичности используются такие характеристики, как коэффициент вытяжки и др.
Испытание металла после окончания процесса деформации (на растяжение, изгиб, кручение и т.п.) позволяет определять величины относительного удлинения и относительного сужения. Эти характеристики являются «структурно чувствительными», т.е. на них оказывает влияние изменение строения исходного металла в процессе деформации.
|
|
Процесс пластической деформации под влиянием внешних усилий осуществляется посредством сдвигаодних частей кристалла относительно других. Элементарный акт пластической деформации в кристалле – это сдвиг одной части кристалла относительно другой на расстояние, не превышающее межатомное. Этот сдвиг в материале может осуществляться путем скольжения, двойникования, межзёренного перемещения.
Основным способом реализации сдвига в металлах и сплавах при пластической деформации является скольжение, которое происходит путём передвижения дислокаций. Этот механизм называется сдвигово –дислокационным, который заключается в смещении одной части кристалла относительно другой, путем последовательного перемещения дислокаций.
Для поликристаллических металлов последовательность процессов изменения структуры при холодной пластической деформации рассмотрена применительно к случаю, когда сплав в исходном состоянии имеет структуру, близкую к равновесной. В технологическом цикле изготовления деталей такое состояние достигается при термической обработке, называемой отжигом.
Для поликристаллических сплавов после отжига характерна структура сзернами равноосной формы; произвольно ориентированными в пространстве полуфабриката и с минимальной плотностью дислокаций внутри зерен. Такая структура обуславливает пониженную прочность, повышенную пластичность и изотропность механических свойств.
В результате холодной пластической деформации в поликристалле происходят следующие изменения зеренной структуры:
1. Форма зерна становится анизотропной, так как зёрна вытягиваются в направлении приложенной нагрузки, появляется так называемая «волокнистая» структура (рис. 2.14).
Рис. 2.14. Зёренная структура металла: а – до деформации; б – после холодной
пластической деформации [С.В. Грачёв, В.Р. Бараз и др.]
2. Границы зерен вытягиваются, потому что увеличивается площадь поверхности раздела зёрен при неизменном объёме; Такое изменение структуры в деформированном металле приводит к значительным остаточным упругим напряжениям по границам зёрен.
Кроме изменения формы зерен и состояния границ, в результате пластической деформации в поликристалле происходят следующие изменения структуры: значительное повышение плотности дислокаций – до 1011 - 1012 см-2; повышение плотности вакансий; появление кристаллографической текстуры при значительных степенях деформации.
Кристаллографическая текстура – идентичность в пространственной ориентации кристаллических решеток зеренотносительно внешних сил.
Результатом холодной пластической деформации сплавов является изменение свойств: повышается прочностность (рис. 2.15, а), что приводит к снижению пластичности; появляется анизотропия свойств, т.е. σвдол ≠ σвпоп≠ σввыс; изменяются физические и химические свойства (рис. 2.15, б).
| |
а | б |
Рис. 2.15. Схема изменения механических (а) и физических (б) свойств сплавов
в зависимости от степени холодной деформации: ρ – удельное электросопротивление;Ηс – коэрцитивная сила; μ – магнитная проницаемость; с.к. – сопротивление коррозии
Упрочнение сплава в результате холодной пластической деформации называется наклепом.
Причиной наклепа и сопутствующего ему сниженияпластичности являются следующие структурные изменения: повышение плотности дислокаций, а, следовательно, уменьшение их подвижности;ориентированная зеренная структура; кристаллографическая текстура.
Определённые вклад в упрочнение вносят и остаточные напряжения.
В некоторых сплавах при степени деформации более 50 - 70 % временное сопротивление разрыву (в продольном направлении) и твердость увеличиваются в полтора-два раза, а предел текучести – в 3 – 5 раз. Упрочнение сопровождается резким снижением пластичности: относительное удлинение снижается в 10 – 20, а иногда в 30 – 40 раз.
Причинами анизотропии механических свойствявляются кристаллографическая текстура при больших степенях деформации; и ориентированная зеренная структура при меньших степенях деформации.
Дальнейшее поведение холоднодеформированного сплава может быть двоякой. Если холодная деформация является завершающим этапом получения изделия, то повышенная прочность сохраняется. Если холодная деформация должна быть продолжена, а полуфабрикат так упрочнен, что имеет пониженную пластичность (иногда даже нулевую), то необходимо произвести разупрочнение металла. Это осуществляется при нагреве металла до высоких температур, выше 0,4 Тпл. При нагреве холоднодеформированных металлов происходят структурные изменения, приводящие к изменению механических свойств.
Нагрев проводится для снятия остаточных напряжений и наклепа, т.е. «восстановления» пластичности сплава. Такое изменение свойств возможно вследствие увеличения диффузионной подвижности атомов, вакансий и дислокаций при повышении температуры. В зависимости от температуры в холоднодеформированном металле протекают различные структурные процессы, стадии развития которых, называются возвратом и рекристаллизацией.
Возврат -стадия, при которой происходит перераспределение и уменьшение концентрации точечных дефектов, а также перераспределение и частичная аннигиляция дислокаций.
Незначительное уменьшение плотности дислокаций при возврате приводит к незначительному повышению пластичности и снижению прочности.
Зёренная структура при возврате не меняется. Возврат делится на две стадии:
1. Отдых – первая стадия возврата, при которой происходит уменьшение концентрации вакансий и незначительное перераспределение дислокаций без образования малоугловых границ. При отдыхе уменьшаются остаточные напряжения.
2. Полигонизация – стадия возврата, при которой происходит перестройка дислокационной структуры с образованием малоугловых границ.Области кристалла, отделенные этими границами, свободны от дислокаций, и представляют собой полигоны. Изменения механических свойств, зависящих от плотности дислокаций, не превышает 10 - 15 %.
Рекристаллизация – процесс формирования и роста в деформированном сплаве новых зерен с пониженной плотностью дислокаций, разделенных большеугловыми границами.Стадия, в результате которой все деформированные зёрна заменяются на равноосные называется первичной рекристаллизацией.
В результате изменения структуры при первичной рекристаллизации значительно снижается прочность и твёрдость металла и повышается пластичность (рис. 2.16).
Рис. 2.16. Изменение механических свойств и микроструктуры в зависимости от
Дата добавления: 2020-01-07; просмотров: 183; Мы поможем в написании вашей работы! |
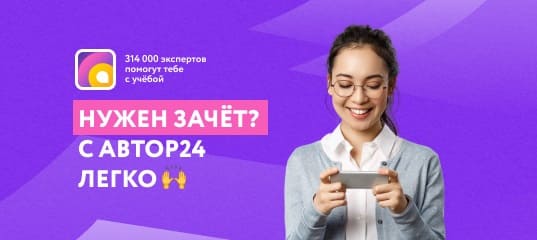
Мы поможем в написании ваших работ!