Электролитическое хромирование
Хромирование служит для получения мелкозернистых покрытий микротвердостью 4000.....12 000 МПа с низким коэффициентом трения и высокой сцепляемостью. Хром химически стоек против воздействия многих кислот и щелочей, жароустойчив, что обеспечивает деталям высокую износостойкость даже в тяжелых условиях эксплуатации, превышающую в 2...5 раз износостойкость закаленной стали. Наибольшая износостойкость покрытия получается при твердости 7000...9200 МПа.
Однако хромирование — энергоемкий, дорогой и малопроизводительный процесс. Его используют для следующих целей: защитно-декоративное хромирование арматуры автомобилей, Велосипедов, мотоциклов, вагонов и т. д.; увеличение износостойкости и ресурса пресс-форм, штампов, измерительных и режущих инструментов, трущихся поверхностей деталей машин (поршневых колец, штоков гидроцилиндров, плунжеров топливных насосов) и др.; восстановление малоизношенных ответственных деталей автомобилей, тракторов и различного оборудования; повышение отражательной способности при изготовлении зеркал, отражателей и рефлекторов.
Для этого процесса в отличие от других характерны следующие особенности.
1. Главным компонентом электролита служит хромовый ангидрид (СгО3), образующий при растворении в воде хромовую кислоту (СгО3 + Н2О = Н2СrO4). Главный компонент при других процессах — соль осаждаемого металла. Хром осаждается лишь при наличии в электролите определенного количества посторонних анионов, чаще всего сульфатов (SO42-) Он шестивалентен в электролите. На катоде осаждается двухвалентный металлический хром. Механизм его осаждения весьма сложен и еще недостаточно изучен.
|
|
2. Большая часть тока расходуется на побочные процессы, в том числе на разложение воды и обильное выделение водорода, в результате чего выход хрома по току мал (10...40 %). С увеличением концентрации и температуры электролита выход по току уменьшается, тогда как при осаждении других металлов, наоборот, увеличивается
3. Хромовый анод растворяется при электролизе с анодным выходом по току, в 1...8 раз превышающим выход по току на катоде. В результате концентрация ионов хрома в электролите непрерывно возрастает. Применяют нерастворимые аноды, изготовленные из свинца или из сплава свинца с 6 % сурьмы. При использовании нерастворимых анодов электролит постоянно обедняется и его необходимо периодически контролировать и корректировать, добавляя хромовый ангидрид.
Электрод, присоединенный к отрицательному полюсу источника тока (катод),а электрод, присоединенный.к положительному полюсу (анод).
На катоде выделяются металлы и водород, а анод растворяется, и на его поверхности выделяется кислород.
|
|
Химический процесс, протекающий на электродах при прохождении через электролит электрического тока, называется электролизом. Устройства, в которых за счет внешней электрической энергии совершаются химические превращения веществ, называют электролизерами или гальваническими ваннами.
Электролиз сводится в к тому, что находящиеся в электролите ионы металла разряжаются на катоде и осаждаются на нем, покрывая поверхность детали слоем металла. Анод растворяется, образуя новые ионы металла взамен выделившихся на катоде, тем самым поддерживая концентрацию электролита.
Количественно процесс электролиза подчиняется двум законам, открытым Фарадеем, названным впоследствии законами Фарадея: 1-масса вещества, выделившегося на катоде или растворившегося на аноде, прямо пропорциональна силе тока и времени его прохождения, т. е. прямо пропорциональна количеству прошедшего через электролит электричества; 2-при прохождении одного и того же количества электричества через разные электролиты массы выделившихся или растворившихся веществ пропорциональны их химическим эквивалентам.
Масса вещества, выделившегося на катоде или растворившегося на аноде при прохождении через электролит единицы количества электричества, называют электрохимическим эквивалентом. Для каждого вещества это постоянное значение, зависящее от природы вещества и определяемое делением его химического эквивалента на постоянную Фарадея.
|
|
Оба закона Фарадея в общем виде выражают формулой МТ= С* I * t 0
где МТ — масса выделившегося на катоде (растворившегося на аноде) вещества, г; С— электрохимический эквивалент вещества, г/(А-ч); I— сила тока, проходящего через электролит, А; t 0 — продолжительность электролиза, ч.
Действительная масса осажденного металла будет меньше теоретической. Отношение практически полученного на катоде количества металла МП к теоретически возможному называют катодным выходом металла по току, который выражают в процентах, т. е.
ηк=(МП/ МТ)*100= (МП/С*I*t0)*100.
Это важнейший показатель электролиза. Его физический смысл заключается в том, что он представляет собой коэффициент использования электрического тока. При хромировании ηк = 10... 18 %, а при железнении ηк = 85. ..95 %. Это означает, что при хромировании лишь 10.. .18 % затраченного на электролиз электричества полезно используется на осаждение металла, тогда как при железнении — 85...95%.
|
|
Отношение количества металла, практически растворенного на аноде, к теоретически возможному называют анодным выходом по току.
Средняя толщина осажденного на катоде покрытия в зависимости от продолжительности электролиза и время, необходимое для получения покрытия заданной толщины:
где h— толщина покрытия, мм; у — плотность осажденного металла, г/см3.
Равномерность распределения толщины покрытия зависит от природы электролита. Свойство электролита давать равномерные по толщине покрытия называют его рассеивающей способностью.
На толщину покрытий большое влияние оказывает взаимное расположение катода и анода. Для улучшения равномерности используют следующие приемы: устанавливают дополнительные и фигурные аноды, повторяющие форму покрываемых изделий так, чтобы расстояния между всеми участками катода и анода были примерно равными; применяют неметаллические (неэлектропроводные) экраны; увеличивают расстояние между покрываемыми деталями и анодами.
Помимо рассеивающей способности различают еще так называемую кроющую способность электролита. Она характеризует свойство электролита покрывать всю поверхность катода, в том числе различные углубления.
На структуру покрытий влияет режим электролиза. Повышение плотности тока и понижение температуры электролита приводят к снижению размеров кристаллов. Однако при высоких плотностях тока прикатодный слой быстро обедняется разряжающимися ионами металла, что способствует осаждению хрупких и некачественных. Чтобы повысить производительность процесса без снижения качества покрытий, необходимо увеличить допустимую плотность тока за счет роста концентрации и температуры электролита, а также его принудительным интенсивным перемешиванием (циркуляцией).
Снижение кислотности электролита ухудшает качество покрытий: они становятся темными, хрупкими и шероховатыми.
25. Коленчатый вал - одна из самых основных деталей двигателя, определяющая вместе с другими деталями цилиндропоршневой группы его ресурс. Ресурс коленвала характеризуется двумя показателями: усталостной прочностью и износостойкостью. При эксплуатации двигателя в результате действия высоких и непостоянных динамических нагрузок вал подвергается кручению и изгибу, отдельные поверхности – изнашиваются. В структуре металла накапливаются усталостные повреждения, возникают микротрещины и другие дефекты. После разборки двигателя коленчатые валы разбирают (удаляют шпонки, заглушки и пробки из масляных каналов и т.д.), тщательно очищают и дефектуют. Особенно тщательно необходимо очистить масляные каналы. При дефектации не только определяют геометрические размеры поверхностей, но и проверяют валы на наличие и расположение трещин методом магнитной дефектоскопии. В соответствии с инструкцией по дефектоскопии и восстановлению коленвалов с трещинами на шейках для тракторных двигателей считаются опасными и не допускаются следующие виды трещин, при которых валы бракуют: на галтелях коренных и шатунных шеек; на цилиндрической части шеек на расстоянии менее 6 мм от торцов щек; на кромках отверстий маслоканалов при длине трещины свыше 15 мм и расположении ее под углом более 30 град к оси шейки; находящиеся на расстоянии одна относительно другой менее 10 мм и расположенные под углом более 30 град к оси вала. Не допускается более восьми трещин длинной менее 5 мм на цилиндрической части шеек и у кромок отверстий маслоканалов, а также более трех трещин длиной свыше 5 мм. Считаются безопасными и допускаются для обработки не более трех продольных трещин длиной свыше 5 мм на поверхности каждой коренной и шатунной шейки, не выходящих на галтель, находящихся на расстоянии более 10 мм одна относительно другой и расположенных под углом менее 30 град к оси шейки. Трещины разделывают абразивным инструментом по всей длине с целью образования канавки радиусом 1,5…2 мм и глубиной 0,2…0,4 мм. Острые комки дополнительно притупляют по периметру. Канавку у разделанной трещины упрочняют виброударным наклепом в течение 6…8 с энергией удара 2,5…5 Дж. Трещины обрабатывают после шлифования шеек до ремонтного размера перед их полированием. Посадочные поверхности под шкив, шестерни, маховик, а также отверстия под штифты и шпоночные пазы чаще всего восстанавливают дуговой наплавкой проволкой 1,2Св18ХГС в среде углекислого газа с последующей механической обработкой. Основной дефект- износ коренных и шатунных шеек. Износ шеек устраняют шлифованием их под ремонтный размер. Шлифуют шейки после устранения других дефектов коленчатого вала. Для шлифования валов служат станки 3А423 или 3Б423. Овальность и конусность прошлифованных шеек не должно превышать 0,015 мм. При шлифовании оставляют припуск до 0,005 мм на последующее полирование. Полируют на специальных стендах абразивными и алмазными бесконечными лентами. После восстановления коленчатые валы подвергают динамической балансировке на машине БМ-У4. Технология и последовательность балансировки зависит от типа двигателя и конкретной конструкции коленвала и шатунов. Коренные и шатунные шейки, вышедшие за ремонтные размеры, восстанавливают наращивают различными методами: наплавкой (под слоем флюса, плазменной, в среде защитных газов и др.); гальваническими покрытиями (железнение ,хромирование); металлизацией; напеканием порошков; электроконтактной приваркой ленты и т.д.
26. Ремонт деталей ГРМ. Ремонт головок блока цилиндров. Трещины головок блока цилиндров заваривают без предварительного подогрева головок дуговой сваркой с помощью электрода ЦЧ-4, самозащитной проволки ПАНЧ-11, либо заделывают фигурными всавками. У гнезд клапанов, износ которых меньше допустимого, фрезеруют или зенкеруют фаски. Перед обработкой выпрессовываются изношенные втулки стержня клапана, зачищают посадочное место и запрессовывают втулки ремонтного размера с уменьшенным внутренним диаметром. Перед запрессовкой головку цилиндров нагревают до температуры 90 С. Затем развертывают отверстия втулок под номинальный или ремонтный размер стержня клапана так, чтобы зазор в соединении соответствовал техническим требованиям. Обработанное отверстие во втулке клапана используют в качестве технологической базы при фрезеровании или зенковании клапанных гнезд для получения необходимой соосности отверстий втулки и гнезда клапана. Гнездо фрезеруют следующим образом. Сначала его обрабатывают черновой фрезой до полного исчезновения следов износа. Потом придают фаске необходимую ширину, обрабатывая последовательно фрезами с различными углами режущей кромки. Далее окончательно обрабатывают фаску чистовой фрезой. Шероховатость поверхности фаски после фрезерования не более Ra=0.80мкм, радиальное биение фаски относительно отверстия втулки клапана – 0,05 мм. Клапанные гнезда после фрезерования упрочняют методом холодного пластического деформирования. Для этого применяют раскатки различных конструкций. Ремонт клапанов. Изношенные рабочие фаски тарелок клапанов шлифуют до выведения следов износа на специальных станках СШК-3 или 2414. Шероховатость фаски после обработки не более Ra=0.63мкм, а биение относительно оси поверхности стержня не более 0,03 мм. Изношенный торец клапана шлифуют до выведения следов износа на тех же станках с помощью приспособления, прилагаемого к станку, и снимают фаску 1*45. Неперпендикулярность торца к боковой поверхности стержня не более 0,05 мм. Стержень клапана с небольшим износом шлифуют на уменьшенный размер, а предельно изношенный восстанавливают электролитическим хромированием или железнением. Притирка клапанов к седлам. Перед сборкой головки цилиндров клапанную пару притирают на станках ОПР-1841А с помощью пасты различной зернистости. Притиркой достигается необходимая герметичность клапанной пары. Рекомендуются следующие пасты: состав I (карбид бора М40 – 10%, микрокорунд М20-90%), состав II (электрокорунд зернистый – 87%, парафин – 13%). Состав готовят на дизельном масле. Притирают до получения кольцевой матовой поверхности на фаске седла. По окончании притирки клапанные гнезда и клапаны промывают керосином или 1%-м водным раствором тринатрийфосфата до полного удаления абразивной притирочной пасты и проверяют качество обработки. Собирают клапанную группу и заливают керосин в газораспределительные каналы. У хорошо притертых клапанов не должно быть подтеканий керосина из-под тарелок в течении 3 мин. Ремонт распределительного вала. Встречаются следующие неисправности: износ опорных шеек, кулачков и посадочного места под шестерню; прогиб. Опорные шейки шлифуют под ремонтный размер. Перед обработкой проверяют и, если необходимо, устраняют прогиб вала на прессе правкой. Опорные шейки шлифуют в центрах круглошлифовального станка 3А-433 электрокорундовыми кругами зернистостью 46…60 и твердостью СМ. Овальность и конусность поверхности шеек после ремонта допускаются не более 0,03 мм. Шероховатость не более Ra=0,63 мкм. При значительном износе опорных шеек их наплавляют вибродуговым способом или проводят железнение и затем шлифуют под номинальный размер. Кулачки вала изнашиваются по высоте на рабочем участке профиля. В результате изменяются высота подъема клапанов. При износе кулачков по высоте до 0,3 мм их шлифуют на эквидистантный профиль по копиру. Если он превышает это значение, то их наплавляют ручной дуговой сваркой или вибродуговым способом с использованием копировального приспособления. Применяют порошковую проволку, электроды Т-590 и Т-620. После наплавки их шлифуют в два приема. Для шлифования используют круги твердостью СМ, СМ1, или СМ2 с зернистостью 46…60. Частота вращения шлифовального круга на станке 3А-433 равна 1033 об/мин и изделия – 32об/мин. Шероховатость поверхности шлифованных кулачков не выше Ra=0,63 мкм. Ремонт коромысел клапанолв и валиков коромысел. Изношенную поверхность бойка клапана шлифуют до выведения следов износа на станке СШК-3. Высота бойка после обработки должна соответствовать техническим требованиям. Если она меньше допустимого значения , то боек наплавляют электродом Т-590 и затем шлифуют на номинальный размер. Шероховатость поверхности после шлифования Ra=0,63 мкм и твердость HRC 50. Изношенную втулку коромысла выпресссовывают и заменяют новой. Новую втулку запрессовывают с натягом 0,01 мм. Отверстие во втулке развертывают до номинального или ремонтного размера в зависимости от размеров валика коромысел. Непараллельность рабочей поверхности бойка коромысла оси отверстия во втулке должна быть не более 0,05 мм. Изношенные валики коромысел шлифуют под ремонтный размер или восстанавливают наплавкой с последующим шлифованием до номинального размера. Ремонт стоек валиков коромысел. Изношенное отверстие под валик коромысел растачивают и ставят переходную втулку с натягом. Толщина стенки втулки должна быть не менее 1,5…2 мм. После запрессовки внутреннюю поверхность втулки, соединенную валиком, развертывают до номинального размера. Ее боковые поверхности не должны выступать за торцы стойки. Непараллельность оси отверстия втулки после обработки плоскости основания стойки не более 0,1 мм на длине 100 мм.
27. Лемех: в процессе работы изнашиваются лицевая сторона (износ по толщине), носик и лезвие (износ по ширине). При затуплении лезвия до 3-4мм тяговое сопротивление увеличивается в 3 раза, расход топлива на 6-8%. Ремонтируют изношенные лемеха кузнечной оттяжкой, приваркой нового лезвия, оттяжкой с последующей наплавкой твердого сплава (Сормайт – 1),а также заменой изношенной части приваркой вставок с последующей наплавкой твердого сплава. При оттяжке лемех нагревают до температуры 1200 град и ударами кувалды или на пневматическом молоте металл из утолщенной части разгоняют по всей длине и ширине лемеха. Оттянутый лемех затачивают с лицевой стороны под углом 25…35 град, до толщины лезвия не более 1 мм, после оттяжки и заточки лезвие лемеха нагревают на 1/3 ширины лемеха до температуры 780…820 град и закаливают в теплой подсоленной воде, опуская в нее лемех спинкой вниз, а затем отпускают на воздухе после повторного нагрева до температуры 300…350 град. Следует отметить, что закалка только режущей части – общее правило при ремонте почворежущих деталей (культиваторных лап – на 20…25 мм ширины лезвия, зубьев борон – на 35…40 мм от носка). Ремонт лемехов приваркой лезвия заключается в том, что при полном использовании запаса металла (магазина) лемеха к нему приваривают новое лезвие из выбракованных лемехов и рессор. Приваривают лезвие кузнечной, газовой или дуговой сваркой. После приварки лезвие оттягивают, затачивают и подвергают термической обработке. Для повышения их долговечности при ремонте применяют наплавку твердого сплава , получая самозатачивающиеся лемеха. Отвал: при износе или изломе носка его отрезают и приваривают носок изогнутый из стальной пластины или выбракованного отвала, в нескольких точках электродом Э-42 d=4мм. Снимают отвал со стойки и сваривают по всему шву с обеих сторон. Зачищают сварные швы с лицевой и тыльной сторон на обдирочно-шлифовальном станке. Размечают и просверливают отверстия под болты крепления отвала к стойке. Затем нагревают до температуры 800-8300 и закаливают в подогретой воде. Затем вновь нагревают до температуры 2000 и охлаждают на воздухе с целью отпуска. При незначительном износе носка наплавляют изношенный участок валиками параллельно полевому обрезу так, чтобы каждый последующий валик перекрывал предыдущий на 1/3 его ширины. Для наплавки используют наплавочные электроды типа Э80Х4С марки 13КН/ЛИВТ которые обеспечивают твердость HRC 55-62. Дисковый нож затачивают с двух сторон до толщины 0,4мм Полевую доску-поворачивают на 1800 Лапы культиваторов: лезвия лап, затупившееся до толщ 0,8мм затачивают на обдирочно-шлифовальном станке. Угол заточки 25-350, толщина лезвия после заточки 0,3-0,5мм При износе носка и лезвия до размеров менее допустимых, лапу нагревают до температуры t=830-900С и оттягивают пневматическим молотом или на наковальне вручную. Для закалки лапу нагревают в печи или кузнечном горне до температуры 8200, после чего отпускают в ванну с маслом таким образом, чтобы закаленная зона составляла 25…30мм ширины лапы. Затем лапу отпускают, для чего ее вновь нагревают до температуры 400 град и охлаждают на воздухе. Для придания лапе культиватора эффекта самозатачивания на износившееся и оттянутое лезвие с нижней стороны наплавляют слой твердого сплава толщиной 0,7-1,3 мм. Зубья борон: ремонт кузнечным способом, нагревают в горне и ударами молота или вручную восстанавливают первоначальную форму. После оттяжки зубьев закаливают:нагревают в горне до t=780-820С и охлаждают в воде, а отпускают на воздухе после нагрева до t=300-350С. Диски лущильников затачивают, а при предельном и износе по диаметру выбраковывают или заменяют изношенное лезвие. Заточку проводят на обдирачно-шлифовальном станке с использованием специального приспособления или на токарном станке. Квадратные отверстия дисков восстанавливают привариванием стальных накладок толщиной 3-4мм, в которых сделаны нормальные квадратные отверстия.
28. Предприятие технического сервиса в АПК во многом зависит от его назначения и от почвенно-климатических условий зоны, в котором оно расположено. Существует 3-х уровневая система ремонтных предприятий: 1. непосредственно эксплуатирующие технику и оборудование(ЦРМ-на центральной усадьбе; мощность зависит от численного состава МТП; производственная площадь их от 120 до 2000 м2, => отличаются по структуре и оснащению оборудованием; автогараж строят обычно на одной территории с ЦРМ, нефтесклад, передвижные средства ТО и ремонта, МТП-создают в непосредственной близости от месторасположения эксплуатации машин. Их работа находится под контролем ЦРМ). Предназначены для проведения несложного ремонта и ТО устранять неисправности и отказы. 2. ремонтно-обслуживающая база районов и фирм объединений ( мастерские общего назначения, СТОА, СТОЖ, СТОТ) выполнение сложных операций ТО, текущий и капитальный ремонт сложных машин. 3. Областные, краевые предприятия (специализированные предприятия, заводы)-восстановление ресурса сложных машин. Взаимосвязи м/у предприятиями Т.С. 1. Разборка, сборка, испытание машин - в мастерской хозяйства. Часть новых деталей поставляется из спецпредприятий. 2. Ремонт силовой части в хозяйстве, а д.в.с. в спецпредприятии. 3. Мастерские не проводят сложный ремонт у себя, а проводят его на спец предприятиях – агрегатный метод ремонта. 4. хоз-ва вообще не проводят ремонт техники, а сдают ее в ЦРМ 5. Хозяйства не проводят ремонт техники, а сдают ее в ремонт на завод изготовителя.
29.Обоснование производственной программы. Для расчета объема работ и производственной программы РОП: ожидаемый состав машинно-тракторного парка и число машин и оборудования по видам, среднегодовая наработка машин каждого вида, режимы ТО и ремонта, до ремонтный и межремонтный ресурс машин. На основании расчета общий объем работ по ТО и ремонту, распределяют по месту исполнения, выявляют недостатки или излишние мощности и делают заключение о целесообразности капиталовложений в проект и строительство новых, расширении или реконструкции существующих. Расчет объема ремонтных работ: по машинный: определение годового числа ремонта и ТО по каждой машине исходя из наработки на начало эксплуатации- Вп, планируемая годовая наработка – Вн, меж ремонтный ресурс - Вк,Вт,Вто, .=> число капит. ремонтов Nк=Вн+Вп/Вк, число текущих ремонтов Nт=Вн+Вп/Вт-Nк, и т.д. Трудоемкость определяется как произведение числа соответств видов ремонта или ТО – для всех тракторов данной марки Nтсум, Nксум и т.д. на трудоемкость этих видов ремонта и обслуживания Тк, Тт, Тто. Групповой – определение годового числа и трудоемкости ремонтно-обслуживающих работ по всей группе машин данной марки Nк=ВпN/Вк, где N-количество машин данной марки. Определение количества ремонта и ТО: граф (Y-наработка и период (кг израсходованного топлива) Х-годовой фонд времени), с использованием коэффициента цикла ηц
Nт=Nк*ηцт, метод учитывающий срок службы: Nк=(((Ваморт-Прев нар/Вк)-1)/Тс)n, вероятностный метод-Тост=Вмр-Вн, Вн=(0,1-0,3)Вп, σост=√σмр2+σн2
σмр=0,3Вмр, σн=0,3Вн, σмр=0,3Вмр.
30. Расчет основных параметров специализированного ремонтного предприятия. Такт ремонта - интервал времени, через который происходит выпуск отремонтированных объектов: общий такт ремонта τ0=ФН.Г./Wг, частный такт ремонта τЧ=ФН.Г./WnЧ, nЧ-число частей, сбор ед. входившх в обьект. Число рабочих: Рр=Т/τ0, где Т-трудоемкость данной операции, загрузка рабочих: З=(Рр/Рпр)100. Продолжительность пребывания обьекта в ремонте: -от начала первой до конца технологических операций. Зависит как от технологии так и от производственных факторов: П=Т/Ряв*Кп. Кп-коэф параллельности, Ряв-явочное количество людей, Т-трудоемкость.
При сокращении продолжительности пребывания объекта в ремонте улучшается использование оборудования, уменьшаются простои машин и повышается коэффициент эксплуатационной готовности. Фронт ремонта:-число обьектов одновременно находящихся в ремонте fр=П/τ0, чем меньше продолжительность пребывания объекта в ремонте тем меньше фронт ремонта=>требуется меньше площадь мастерской, снижаются затраты на отопление, освещение и т.д. Количество рабочих на предприятии: Рсп=Тг/Фдг; Ряв=Тг/Фнг; Рвсп=(14-17)%Рсп-крановщики кузовщики и т.д.; Рмладш.обсл.перс.= (2-3)%Рсп-уборщики;
Рскп=(3-4)%Рсп-сметно конторный персонал;
Ритр=(13-15)%Рсп.
31. Площадь рассчитывают как при проектировании новых, так и при перепланировке действующих предприятий. Площади отдельных участков, цехов и отделений определяют следующими способами.
1. По числу рабочих мест
где Fy — удельная площадь на одно рабочее место, м2; т — число рабочих мест.
2. По числу производственных рабочих
где Р — число производственных рабочих; Fр — удельная площадь на одного производственного рабочего, м2.
3. По удельной площади, отнесенной к одному станку,
где S— число станков; Fs — удельная площадь, м2 на один станок.
Данные об удельной площади на единицу оборудования даются в каталогах и справочниках.
По площади, занимаемой оборудованием, учетом переходного коэффициента
где F0 — площадь, занимаемая оборудованием, м2; δ — переходной коэффициент.
Площадь, занимаемую оборудованием, подсчитывают согласно паспортным данным.
5. По удельной годовой потребности N машины i-й марки (используют только для расчета площади ремонтно-монтажного участка центральной ремонтной мастерской хозяйств)
где fi — фронт ремонта i-й машины.
• Удельная потребность машин в площади, м2: для К-700 и К-701—30, ДТ-75М – 17, Т-150К – 9, МТЗ-80 и ЮМЗ-6КЛ – 3,15, Т-40А – 0,9, Т-25А и Т-16М – 0,3, автомобилей – 0,3 и комбайнов всех видов(в среднем) – 0,85.
6. По фронту ремонта машин (для разборочно-сборочного цеха)
где FM – удельная площадь, отнесенная к одной машине, находящейся на ремонте в разборочно-сборочном цехе, м2.
Окончательно выбирают площадь участков после проверки расчетов графическим способом по плану размещения оборудования.
7. По удельной площади fy, приходящейся на один приведенный ремонт,
где Nпр – число приведенных ремонтов.
Значения удельных площадей по каждому объекту-представителю даются в специальных справочниках.
Общую площадь распределяют следующим образом: производственная – 100%, вспомогательная, складская и конторско-бытовая – соответственно 12,8 и 6% производственной
32. Разработка компоновочного плана ремонтного предприятия. Разработка компоновочного плана выполняется для каждого отдельно стоящего здания =>на первом этапе определяют кол-во производственных и вспомогательных подраздразделений→общую площадь→форму здания. После определения размеров производственных площадей их компонуют на генеральном плане предприятия. Определяют взаимосвязь м/у подразделениями с учетом производственного процесса. При проектировании ремонтных предприятий используют различные варианты схем расположения отделений и участков (прымоточного, Г- и П- образного) в зависимости от принятого технологического процесса производства. При прямоточной схеме разборочно-моечные, дефектовочно-комплектовочные, сборочные и испытательные участки и отделения располагают последовательно один за другим. Преимущество такой схемы – ее простота, а к недостаткам относят наличие больших транспортных путей. При Г- образной схеме и наличии минимальных транспортных путей можно лучше изолировать разборочно-моечные участки от других и расположить участки восстановления деталей рядом с комплектовочными отделениями, а последнее – со сборочным, что считают весьма удобным. Недостаток данной схемы состоит в том, что из-за больших площадей участков по восстановлению базисных деталей, а также громоздких деталей затрудняется их прямолинейное перемещение к участку общей сборки машин и агрегатов. П – образная схема имеет преимущества и недостатки Г – образной. После выбора схемы определяют габаритные размеры производственного корпуса. При определении длины и ширины корпуса учитывают длину поточной линии разборки и сборки, шаг колонн, размеры и расположение площадки под строительство. Для производственных зданий промышленных предприятий габаритную схему производственного корпуса выбирают с учетом применяемого подъемно-транспортного оборудования и вида ремонтируемых объектов. Наибольшее распространение для ремонтно-обслуживающих предприятий получили здания прямоугольной формы, длина которых, м, L=F/B, где F-площадь здания ремонтного предприятия, В-ширина здания. Ширину здания принимают стандартной – 12, 18, 24, 36, 48, 54, 72 м. Отношение длины здания к его ширине не должно быть более трех.
34. Лизинг (англ. leasing — аренда) — долгосрочная аренда машин, оборудования, транспортных средств, сооружений производственного назначения, предусматривающая возможность их последующего выкупа арендатором. Лизинг осуществляется на основе долгосрочного договора между лизинговой компанией (лизингодателем), приобретающей оборудование за свой счет и сдающей его в аренду на несколько лет, и фирмой-арендатором (лизингополучателем), которая постепенно вносит арендную плату за использование лизингового имущества. После истечения срока действия договора арендатор либо возвращает имущество лизинговой компании, либо продлевает срок действия договора (заключает новый договор), либо выкупает имущество по остаточной стоимости.
Лизинг представляет собой соглашение между собственником имущества (арендодателем) и арендатором о передаче имущества в пользование на договоренный период по установленной ренте, выплачиваемой ежегодно, ежеквартально или ежемесячно.
Лизинг - это приобретение оборудования с предоставлением его в аренду организациям (лизингополучателю) в обмен на лизинговые платежи. Лизинг предусматривает возможность выкупа оборудования по истечении срока действия лизингового договора или досрочно по остаточной стоимости.
Аренда-одна из форм кредитования экспорта без передачи права собственности на товар арендатору. Аренда машин предоставляется на краткосрочный период (рентинг), среднесрочный(хайринг) и долгосрочный (лизинг). Ставка арендной платы должна обеспе чивать арендодателю получение прибыли не ниже средней нормы на вложенный капитал, а для арендатора стоимость должна быть ниже стоимости банковского кредита на приобретение машин и оборудования. Аренда машин позволяет арендатору использовать дорогостоящую технику без больших начальных затрат на капиталовложения и выплачивать арендные платежи по мере получения прибыли от эксплуатации арендуемого оборудования, а арендодателю расширить сбыт при относительном снижении риска потерь от неплатежеспособности заказчика.
Прокат-особый вид имущественного найма (аренды). По договору прооката арендодатель, осуществляющий сдачу имущества в аренду в качестве постоянной предпринимательской деятельности, обязуется предоставить арендатору движимое имущество за плату во временное владение и пользование. Имущество, предоставленное по договору проката используется для потребительских целей, если иное не предусмотрено договором или не вытекает из существа обязательства. Договор проката заключается в письменной форме и является публичным договором. Срок, на который заключается договор прооката не может превышать одного года. Правила о возобновлении договора аренды на неопределенный срок и о преимущественном праве арендатора на возобновление договора аренды к договору проката не применяются. Арендатор вправе отказаться от договора проката в любое время, письменно предупредив о своем намерении арендодателя не менее чем за десять дней.
35. Отдельные заводы создают сеть предприятий по фирменному обслуживанию своей техники. Однако не все заводы обладают такой возможностью из-за отсутствия материальных и трудовых ресурсов. Около 90% компаний изготовителей продают, проводят ТО, гарантийный ремонт, поставляют запасные части через сеть независимых дилерских пунктов, которые при работе с заказчиками руководствуются следующими основными принципами: 1. Клиент еще до начала ремонта получает точную оценку повреждений и перечень предстоящих работ; 2. Работы проводят только с согласия заказчика, который оплачивает лишь заказанные им виды работ; 3. Ремонт проводят специалисты высокой квалификации; 4. Клиент получает формуляр с указанием всех видов выполняемы работ и времени, затраченного на каждую из них; 5. Стоимость работ оплачивают по твердым расценкам, с которыми дилер знакомит заказчика. Организация фирмами-изготовителями собственных предприятий для ТО обходится дорого. Поэтому в последнее время наблюдается тенденция к сокращению числа дилеров – представителей промышленных фирм и увеличению числа независимых дилеров, которые в некоторых случаях распространяют технику нескольких поставщиков. Предприятия дилеров – это в основном семейные предприятия, которые по лицензии какой-нибудь крупной компании реализуют машины и осуществляют их сервис. При организации дилерской службы следует учитывать, во - первых, наличие уже сложившейся ремонтно-обслуживающей базы, во – вторых, климатические условия, которые оказывают влияние на эксплуатацию и хранение техники.
Дата добавления: 2020-01-07; просмотров: 157; Мы поможем в написании вашей работы! |
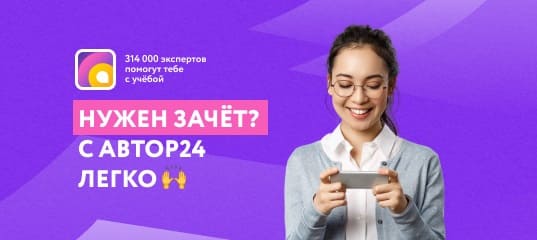
Мы поможем в написании ваших работ!