Анализ запасов товарно-материальных ценностей: ABC - метод
ABC-метод хорошо изучен применительно к задачам анализа запасов товарно-материальных ценностей (далее ТМЦ), однако полезен и при анализе мероприятий по повышению уровня качества продукции. В соответствии с ABC-методом запасы ТМЦ делятся на 3 категории по степени важности отдельных видов в зависимости от их удельной стоимости:
•категория А включает ограниченное количество наиболее ценных для работы запасов ТМЦ, обеспечивающих ее непрерывность, которые требуют постоянного и скрупулезного учета и контроля (возможно даже ежедневного). Для этих ресурсов обязателен расчет оптимального размера заказа и поставок;
•категория В составлена из тех видов ТМЦ, которые в меньшей степени важны для предприятия и которые оцениваются и проверяются при ежемесячной инвентаризации;
•категория С включает широкий ассортимент оставшихся малоценных или быстро заменяемых (закупаемых) ТМЦ, закупаемых обычно в большом количестве.
В качестве систем управления запасами используют (по степени увеличения сложности): систему удовлетворения годового спроса, «две корзины», систему цикличного заказа, систему с фиксированным уровнем заказа, адаптационную систему.
На практике компании обычно пользуются некоторым комбинированным методом, представляющим собой определенную комбинацию указанных систем.
В соответствии с ABC-методом все предметы хранения ранжируются в стоимостном выражении, после чего строится кумулятивная кривая плотности распределения. При этом оказывается, что в большинстве случаев 80% стоимости использованного запаса приходится только на 20% предметов хранения, для управления которыми можно применить адаптационную систему — возможно, с постоянным контролем. Следующие 30% предметов могут составлять 15% общей стоимости; для управления ими подойдет система цикличного заказа. Для оставшихся 50% предметов достаточно будет системы удовлетворения годового спроса или метода «двух корзин». Эти три группы методов часто обозначают как А, В и С, отсюда и название метода.
|
|
Понятие управления запасами и особенности технологии
Одним из важнейших этапов планирования деятельности предприятия является определение рационального уровня запасов.
Под запасом понимается все то, на что имеется спрос и что выключено временно из потребления. Запасы подразделяются на запасы средств производства, предназначенные для производственного потребления (сбытовые, производственные, государственные резервы и незавершенное производство), и запасы предметов потребления, предназначенные для использования в непроизводственной социально-экономической сфере и для удовлетворения потребностей людей (товарные, запасы предметов коллективного и индивидуального потребления и государственные резервы).
|
|
Основными причинами создания запасов выступает необходимость обеспечения бесперебойного снабжения производственного процесса; периодичность производства различных видов продукции поставщиками; осуществление транспортировки большинства видов продукции от поставщика к потребителю партиями; несовпадение ритма производства с ритмом потребления.
Основными причинами, побуждающими предприятия (организации) к уменьшению запасов, является плата за физическое хранение запасов, отвлечение денежных средств, вложенных в запасы; потери от естественной убыли; моральный износ.
Предметом теории управления запасами является отыскание такой организации поставок или производства, при которых суммарные затраты на функционирование системы были бы минимальными. Под организацией поставок понимается определение объемов поставок и периодичность заказов.
В планировании производства нескольких видов продукции на одном и том же оборудовании возникает задача определения размера партии и периодичности запуска продукции в производство.
|
|
В настоящее время насчитывается более 300 моделей управления запасами.
Существуют 4 основных вида затрат, которые могут оказать влияние на выбор решения по управлению запасами:
• затраты на приобретение запасов;
• затраты на организацию заказа;
• издержки хранения запасов;
• потери от дефицита.
Методы « точно вовремя»
За рубежом, особенно в Японии, нашли широкое применение системы JIT (just-in-time), известные у нас как системы «точно в срок». Родоначальником JIT была компания Toyota. В основу идеологии созданной системы были заложены две посылки:
•брак и исправление дефектов — необоснованные затраты;
•запасы — это зло, потому что они занимают пространство и связывают ресурсы.
В JIТ реализован принцип: ничего не должно быть произведено, пока в этом не возникнет необходимость.
Цель внедрения JIT — создание сбалансированной системы, при которой достигается масштабное производство, обеспечивающее выпуск высококачественной продукции при оптимальном использовании всех ресурсов.
Для достижения этой цели необходимо решить следующие задачи:
•сбои и нарушения процесса производства должны быть исключены;
•сделать производственную систему гибкой;
|
|
•достичь минимума материальных запасов;
•устранить необоснованные затраты;
•добиться минимизации времени переналадки и подготовки к производственному процессу.
Основу JIT формируют 4 блока:
•разработка изделия;
•разработка процесса;
•кадровые и организационные элементы;
•планирование и управление производством.
При разработке изделия пытаются максимально использовать следующие факторы:
•стандартные комплектующие;
•модульное проектирование;
•качество.
Производственный процесс в JIT базируется на семи особо важных факторах:
•минимальный размер производственных партий;
•сокращение времени подготовки к производству;
•производственные ячейки;
•минимизация объема незавершенного производства;
•качество;
•гибкость производства;
•снижение материально-производственных запасов.
Дата добавления: 2020-01-07; просмотров: 170; Мы поможем в написании вашей работы! |
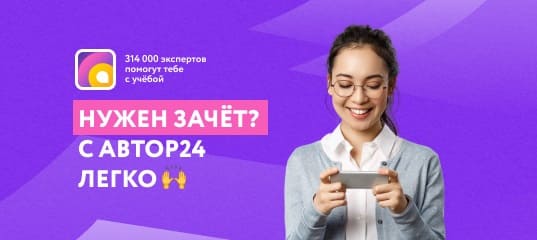
Мы поможем в написании ваших работ!