Толщина антикора для надежной защиты должна быть не менее 250 мкм, так как слой меньшей толщины плохо справляется с функцией защиты от коррозии, а толстый легко отслаивается.
И еще – после антикоррозионной обработки днища не следует использовать транспортное средство в течение 24 часов.
Одни автомобилисты считают, что современные машины не нуждаются в усилении заводской защиты, другие уверяют, что, при езде по нашим дорогам без защиты колесных арок, уже через пару лет рискуешь обнаружить следы ржавчины. Этому спору много лет. Но, в конечном счете, каждый автовладелец решает сам, как ему поступить. Попробуем взглянуть на проблему с точки зрения физики.
Для чего нужна защита колёсных арок? С первого дня эксплуатации любой автомобиль подвергается разрушающим факторам, таким как атмосферные осадки, сезонные перепады температур, плохое состояние дорожного покрытия, случайные или умышленные неправильные действия водителя. Влияние этих факторов на кузов и подвеску ускоряет процесс старения ТС и его постепенного разрушения. Первый удар принимают на себя колесные арки. Они страдают не столько от воды и грязи, снега и льда, сколько от ударов летящих из-под колес гравия и песка. Подобная гравийно-пескоструйная атака – серьезная проблема для кузова. Она вызывает: - повреждение лакокрасочного покрытия кромок колесных арок; - коррозию в скрытых полостях кузовных деталей от попадания в них грязи и песка, смешанных с агрессивными противогололёдными препаратами, а также повышает вероятность повреждения заводского и дополнительного антикоррозионного покрытия. Жидкие подкрылки Минимальные защитные средства от подобных поражений, как правило, устанавливаются на автомобиль еще на заводе, в частности – карманы кузова прикрываются щитками. К сожалению, такой вариант не обеспечивает полноценную защиту колесных арок и может рассматриваться лишь как временный.
|
|
Существует несколько способов дополнительной защиты колесных арок автомобиля: - пластиковые подкрылки; - жидкие подкрылки; - обработка специальным материалом; - защита кромок колесных арок и порогов бронирующей пленкой. Рассмотрим преимущества и недостатки каждого из вариантов.
Алюминиевые локеры. Подкрылки, которые были популярны в советское время, изготавливались из алюминия и оцинкованной стали. Помимо главного их предназначения — защиты колёсной арки, они имеют ряд недостатков, среди которых: - резиновый уплотнитель, который обрамлял локер, со временем стирал защитные покрытия колёсной арки, подвергая её коррозии. - незащищенные боковые поверхности. - быстроразрушающиеся материалы — сталь и алюминий. - небезопасность использования (могли лопнуть во время движения, создав аварийную ситуацию). - при деформации металлические локеры могли вырвать крепёж и повредить кузов. Со временем металлические подкрылки ушли в прошлое и на смену им появились пластиковые локеры.
|
|
Пластиковые локеры . Пластиковые подкрылки Этот вид защиты очень популярен уже много лет. Подкрылки, или локеры, – специально отформованные пластиковые кожухи, которые изготавливаются как для отечественных моделей автомобилей, так и для большинства распространенных в странах СНГ иномарок. Изготавливаются они из высококачественного экологически чистого полиэтилена низкого давления (ПНД) специальной марки. Это эластичный износостойкий материал, который в наилучшей степени соответствует реалиям отечественных дорог и отличается стабильностью характеристик даже при экстремальных температурах. Несомненными преимуществами использования пластиковых подкрылков являются: - надежная защита кузова автомобиля от пескоструйного эффекта и негативного влияния агрессивных антигололедных реагентов; - защита нанесенного на колесные арки антикоррозийного покрытия; - долговечность, высокая прочность и сохранение начальной формы; - стабильность физико-механических характеристик в самых сложных климатических условиях (диапазон рабочих температур от -50° до +50° С). Многие автомобилисты считают серьезным недостатком пластиковых подкрылков их крепление в колесных арках с помощью саморезов, так как это, по их мнению, чревато возникновением коррозионного поражения в местах сверления дополнительных отверстий. Это не совсем так. При профессиональной установке места крепления обрабатываются антикором, и используются только оцинкованные саморезы, что сводит риск коррозии к нулю. Причем эти меры, скорее, профилактические, так как производители все технологические отверстия делают совпадающими со штатными местами крепления в колесной арке той модели автомобиля, для которой данные подкрылки предназначены. Для каждой модели автомобиля следует использовать соответствующую модель подкрылков.
|
|
Жидкие подкрылки . Препараты с условным названием «жидкие подкрылки» есть в ассортиментном ряду практически всех производителей антикоррозионных материалов. Возьмем для примера Мercasol 4. В его состав входит гранулированное стекло, благодаря чему препарат обладает чрезвычайно высокой стойкостью к внешним механическим воздействиям. Кроме того, материал улучшает шумо- и термоизоляцию автомобиля. Технология применения «жидких подкрылков» проста: препарат наносится на чистую поверхность колесной арки кистью или шпателем. Жидкие подкрылки После высыхания рекомендуется нанести антикор. Основным достоинством «жидких подкрылков» является универсальность использования – состав можно наносить на колесные арки любой конфигурации независимо от возраста и состояния автомобиля. При наличии очагов коррозии на колесных арках обязательно нужно провести подготовительные работы, то есть зачистить и загрунтовать пораженные места. К недостаткам «жидких подкрылков» можно отнести сравнительно небольшой расчетный срок их службы – два года, — после чего покрытие нужно обновлять. Правда, на практике «жидкие подкрылки» исправно служат в среднем до четырех лет.
|
|
Мercasol Sound Deadening . Это шумопоглощающая мастика на основе каучука и полимеров, которая одновременно выполняет функции антигравийного покрытия, а также герметика. Перед нанесением состава обрабатываемую поверхность необходимо хорошо высушить и очистить от жира и грязи. Шумопоглощающую мастику лучше наносить при помощи распыляющего пистолета с регулируемой насадкой, либо под давлением 3–6 бар, причем следует использовать только профессиональное оборудование. Толщина слоя — 0,7–1,5 мм. У Мercasol Sound Deadening можно отметить два недостатка: первый – наносить состав можно только на поверхность, которая до этого не обрабатывалась другими препаратами, второй – нанесение средства возможно только в условиях сервиса, оснащенного специальным оборудованием.
Бронирующая плёнка. В качестве дополнительной антигравийной защиты кузова и, в частности, кромок колесных арок может использоваться бронирующая плёнка. Многие зарубежные автопроизводители еще в процессе сборки автомобилей предусматривают защиту бронирующей пленкой наиболее уязвимых деталей кузова и обвеса: порогов, фартуков и бамперов, стекол фар и фонарей. Но, как правило, на заводском конвейере оклеиваются очень небольшие участки машины. Между тем, с помощью бронирующей пленки можно защитить и кромки колесных арок, и капот, а также полностью проклеить бамперы и пороги.
Бронирующая пленка . Одни из наиболее известных – бронирующие пленки Ricochet и Llumar. Пленки отличаются толщиной, что и обусловливает места для их применения. Пленку толщиной 0,15 мм рекомендуется использовать для защиты окрашенных поверхностей автомобиля: крыльев и нижних частей дверей, края крыши над лобовым стеклом, зеркал заднего вида. Тот же перечень защищаемых поверхностей, за исключением зеркал заднего вида, рекомендуется и для пленки толщиной 0,3 мм. Пленки толщиной 0,5 мм обеспечивают более высокий уровень защиты, но они менее гибкие. Обычно их используют для бронирования капота автомобиля, крыльев и фар. Пленка толщиной 1 мм позволяет надежно защитить поверхности, подвергающиеся наиболее сильному разрушающему воздействию песка и гравия: фары, фонари, кромки арок колес, крылья. Основным преимуществом использования бронирующей пленки является ее невидимость на защищаемом участке. Недостаток – необходимость обращаться только к специалистам, причем как при установке, так и при удалении защиты.
В процессе эксплуатации кузов автомобиля подвергается воздействию нескольких видов коррозии, наиболее опасной из которых является электрохимическая. Она возникает при взаимодействии влаги с металлом кузова. Различные виды загрязнений, присутствующие в атмосфере и на поверхности дорог, противогололедные реагенты в зимний период – все это превращает влагу в электролит, в котором протекают электрохимические процессы, приводящие к коррозии металла.
Наиболее уязвимы для коррозии скрытые полости кузова. Если на открытых поверхностях влага быстро высыхает, то в скрытых полостях она остается постоянно, постепенно разъедая металл. Поэтому при антикоррозийной обработке автомобиля необходимо тщательно обработать все скрытые полости, к которым относятся замкнутые элементы кузова:
· пороги;
· лонжероны;
· стойки кузова;
· поперечины и усилители днища;
· места под молдингами и накладками;
· усилители моторного отсека.
Кроме того, на автомобиле много полостей, закрытых обшивкой и накладками:
· усилители капота;
· усилители крышки багажника;
· пространство между арками колес и крыльями;
· карманы дверей;
· места установки фар.
У многих производителей автомобилей разработаны технологические карты обработки скрытых полостей, с указанием мест их нахождения и способов доступа.
Дата добавления: 2019-11-16; просмотров: 118; Мы поможем в написании вашей работы! |
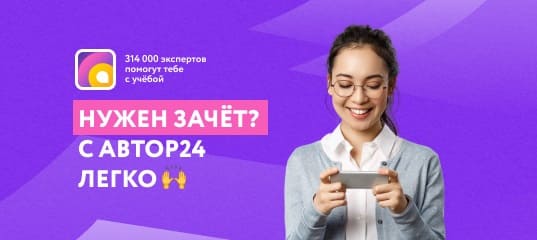
Мы поможем в написании ваших работ!